[0001] The present invention relates to a process for the manufacture of a thermal ink jet
printing head and more particularly to the production of a duct for the ink for a
thermal ink jet printing head of the type in which the nozzles, the ink expulsion
chambers and the heating elements with the corresponding electric conductors are contained
in a multi-layer plate formed by superposed layers of metals and insulating materials
fixed on a silicon support.
[0002] There are known in the art thermal ink jet printing heads in which the ink feed duct
is obtained by cutting a slit extending through the multi-layer plate for its entire
thickness by means of a jet of sand formed by particles of very hard materials, for
example alumina, with sizes of the order of 10-25 µm.
[0003] Since such a process is necessarily applied to the complete multi-layer plate, the
sand jet must cut into a relatively considerable thickness of the order of 0.5-0.7
mm. In such case, the terminal opening of the slit turns out of very inaccurate geometrical
shape, causing a large number of rejects, which make the process more costly.
[0004] Also known is the cutting of the common duct for the ink in a multi-layer plate for
an ink jet head by means of a laser beam of conventional type, for example YAG,CO₂.
Since the conventional types of laser beams operate by thermal effect, they cause
the melting of a surface layer of the sides of the cut.
[0005] When this molten layer solidifies, it becomes very fragile and, by reason of the
thermal stresses due to its cooling, is subject to extensive cracking. In consequence,
infiltration of ink will occur through these cracks during the working of the head,
with a consequent reduction in the life of the head.
[0006] Therefore, the present invention aims to provide a process for cutting the ink duct
in a multi-layer plate for a thermal ink jet printing head which is free from the
above-mentioned drawbacks.
[0007] Another aim of the invention is to produce cuts for the ink duct of geometrical form
in multi-layer plates for thermal ink jet printing heads, which are very accurate,
and have clean edges, over a greatly reduced production time.
[0008] Accordingly, the invention provides a process, which is characterised in the manner
defined in the main claim.
[0009] An embodiment of the invention will now be described by way of example only, and,
with reference to the accompanying drawings in which:
Fig. 1 represents diagrammatically a cross section of a multi-layer plate obtained
according to the invention;
Figs. 2 - 8 represent successive stages of working of the plate of Fig. 1.
[0010] Referring to Fig. 1, a multi-layer plate 1 comprisee a plurality of metal layers
and electrically insulating in which each layer is constructed by processes of vacuum
deposition and electroforming which are known in the art.
[0011] The ink is contained in chambers 4 produced in one of the layers of the plate 1 and
is expelled through nozzles 5 and 5′ disposed in two parallel rows by the effect of
the expansion of a vapour bubble generated by the rapid heating of heating elements
8 and 8′ contained in the chambers 4.
[0012] The plate 1 is used on a thermal ink jet dot printing head mounted immovably directly
on a main ink reservoir not shown in the drawings.
[0013] Each row of nozzles may contain a variable number of nozzles which is determined
on the basis of the printing requirements, such as, for example, the level of definition
of the characters.
[0014] The main reservoir communicates with the chambers 4 through a common duct 14 (Fig.
1) produced in the thickness of the plate 1 and through a plurality of feed passages
16 connecting each chamber 4 with the common duct 14.
[0015] The process for cutting the common duct 14 through the thickness of the silicon support
20 is as
[0016] A silicon support plate 20 of a thickness in the range between 400 µm and 700 µm
is passivated on both faces with a layer 22 and 24, respectively, of silicon dioxide
with a thickness, for example, of 1.5 µm, these layers performing the function of
thermal and electrical insulation. The layers 22 and 24 are covered with two protective
layers 26 and 28 of a photosensitive substance. Such photosensitive substances are
normally epoxy and/or acrylic resins polymerizable by the effect of light radiation.
After being exposed and developed, the protective layer 28 is removed by the known
photolithographic technique to form an aperture 30 (Fig. 2) of rectangular form extending
lengthwise in the direction parallel to the crystallographic orientation <110> of
the silicon support 20. Consequently, the rows of heating elements 8 and 8′ will be
aligned parallel to this direction. The aperture 30 leaves free a zone 32 (Fig.2)
of the layer 24 of silicon dioxide. The zone 32 is thereafter removed chemically with
a selective, hydrofluoric acid (HF) based solution to uncover a portion 34 of the
support 20 (Fig. 3). After removing the protective layers 26 and 28, the support 20
is immersed in an attack bath for etching the surface 34.
[0017] Since the support 20 is constituted by crystalline silicon having a standard crystallographic
orientation of < 100> , the etching action of the anisotropic attack solution develops
predominantly in accordance with the orientation of <100> and much less in accordance
with the associated orientation of <111>. With respect to the silicon support 20,
the orientation <100> corresponds to a direction X (Fig. 2) perpendicular to the outer
faces of the support 20, the orientation <100> represents a direction Y perpendicular
to X and the orientation <111> represents a direction Z perpendicular to Y and forming
with the direction X a characteristic angle α dependent on the form of the crystal
lattice of the material of the support 20. Therefore, the groove 35 (Fig. 4) which
is obtained after the etching process has in cross-section the form of a truncated
pyramid (Fig. 4) having as its greater base the surface 34 (Fig. 3) parallel to the
outer faces of the support 20 and as its smaller or truncation base a surface 36 (Fig.
4) parallel to the surface 34, the width L of which depends on the depth H₁ reached
by the etching and on the width L₁ of the zone 34. The length of the groove 35 in
the direction perpendicular to the drawing depends on the number of nozzles 5 employed
in each row. The lateral surfaces 38 and 40 have a characteristic inclination α with
respect to the greater base 34 of about 54
o, corresponding to the angle between the crystallographic orientations <100> and <111>
of the silicon support 20. The widths L, L₁ are linked to the depth H₁ of the groove
35 and to the inclination α by the equation:
L₁ = L-2H₁ cotgα 1)
[0018] The solutions most usual for anisotropic etching of silicon are the following:
A. Ethylenediamine : 750 ml
Pyrocatechol : 120 gr
Deionized water : 100 ml.
[0019] This solution, operating at a temperature of 115
oC, develops an attach gradient in accordance with the orientation <100> : G₁₀₀ = 0.75
µm/min and a ratio
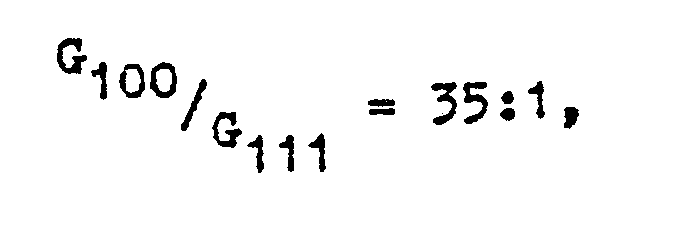
where G₁₁₁ is the anisotropic attack gradient in accordance with the orientation
<111>.
B. Ethylenediamine : 750 ml
Pyrocatechol : 120 gr
Deionized water : 240 ml
[0020] This solution, operating at a temperature of 115
oC, gives: G₁₀₀= 1.25 µm/min;
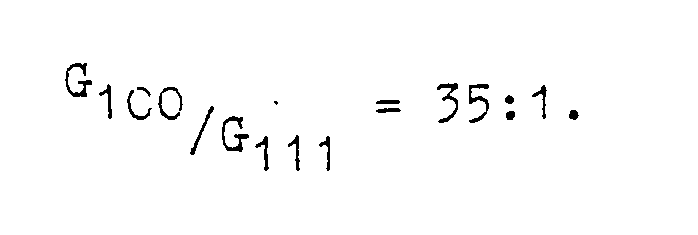
C. Potassium hydroxide: 250 gr
Isopropyl alcohol : 200 ml
(isopropanol)
Deionized water : 800 ml
[0021] This solution, operating at a temperature of 80
oC, gives G₁₀₀= 1 µm/min;
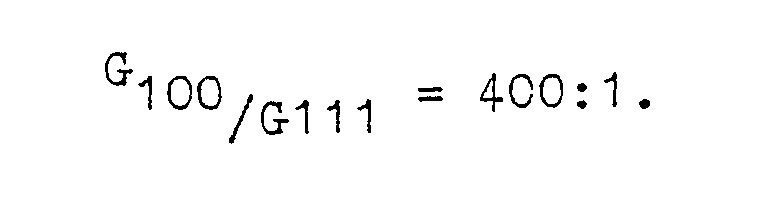
D. Hydrazine : 600 ml
Deionized water: 400 ml
[0022] This solution, operating at a temperature of 100
oC, gives G₁₀₀ = 1.8 µm/min.
[0023] The operation of etching of the groove 35 (Fig.4) is continued for an attack time
T depending on the attack gradient G₁₀₀ and until the end surface 36 reaches a depth
H₁ comprised between 60% and 90% of the thickness H of the support 20.
[0024] By way of example, with a support 20 of a thickness H = 600 µm, the depth H₁ of the
groove 35 to be etched is about 400 µm. Having fixed a width L of the surface 36 of
about 350 µm, there is obtained from the equation 1) the width L₁ of the zone 34 (Fig.
3) from which the operation of etching begins, that is L₁= 926 µm.
[0025] Using, for example, the solution A, the attack time T lasts 8 hours and 55 minutes.
After etching the groove 35 for a depth H₁, metal layers are successively deposited
under vacuum on the layer 22 of silicon dioxide by known deposition techniques to
form the heating elements 8, 8′ and the corresponding electric conductors, for example
as described in Italian Patent Application No. 67044 A/89, dated 26.1.89, in the name
of the Applicant.
[0026] More particularly, the silicon dioxide layer 22 is covered with a layer 44 (Fig.
5) between 500 and 2000 A thick of an electrically resistive metal, for example a
50/50 tantalum-aluminium alloy. The layer 44 is then etched by a known process of
dry etching under vacuum to form two pluralities of independent resistive elements
8 and 8′ for heating the ink.
[0027] The Ta-Al elements 8, 8′ are covered with a layer 46 of aluminium with a thickness
comprised between 2000 and 10,000 A. the layer 46 is then etched by a process similar
to the foregoing to obtain electric conductors 47 for supplying the heating elements
8 and 8′. On the aluminium layer 46 there are then deposited two layers 50 and 52
of electrically insulating, but thermally conductive, materials. The layer 50 in contact
with the aluminium conductors 47 is constituted by silicon nitride, while the overlying
layer 52 is constituted by silicon carbide. In total, the two layers 50 and 52 have
a thickness compsised between 2000 and 20,000 A.
[0028] A layer 56 of tantalum of a thickness between 1000 A and 10,000 A is thereafter deposited
by known techniques on the layer 52. The layer 56 is then etched under vacuum to obtain
separate and parallel strips superposed on the conductors 47.
[0029] The layer 56 has a dual function of protection of the ink of the subjacent resistive
and insulating layers and of electrical connection between the conductors 47 and connecting
terminals (not shown) towards the outside.
[0030] The layers 44, 46, 50, 52 and 56 are interrupted in an intermediate zone 60 (Fig.
5) between the two rows of the heating elements 8 and 8′, leaving free a part 62 of
the layer 22. More particularly, the tantalum layer 56 also covers the edges 58 of
the subjacent layers to protect them from possible infiltrations of acids employed
in the etching treatments and from the ink during the operation of the head.
[0031] The breaking through of the residual wall 36′, which has a thickness of H₂=H-H₁,
is thereafter carried out by a sandblasting operation.
[0032] To this end, a jet of sand formed predominantly of alumina particles of an average
size of about 20 µm is directed against the end surface 36 in a direction perpendicular
to the surface itself.
[0033] The sandblasting operation is interrupted when an opening 63 (Fig. 6) defined by
two plane and parallel walls 64 and 66 has been obtained in the surface 62. The walls
64 and 66 are connected at one end to the lateral surfaces 38 and 40, respectively,
of the groove 35 and intersect at the other end (at the top in Fig.6) the surface
62. The walls 64 and 66 and the surface 62 therefore define a parallelepipedal chamber
69 having the truncation base 36 in common with the pyramidal chamber. After completing
the cutting of the common duct 14 (Fig. 1), there is deposited on the tantalum layer
56, as described in the above-mentioned Patent Application, a layer 74 of photosensitive
material, for example Vacrel (Registered Trade Mark), in which the chambers 4 and
the feed passages 16 are obtained by a photolithographic process. Finally, a sheet
76 of gold-plated nickel bearing the nozzles 5 and 5′ is hot-soldered to the layer
74.
[0034] It remains understood that the process of construction of the thermal ink jet head
may undergo variations of modifications and that the thermal head so constructed may
be modified in form and dimensions without, however, departing from the scope of the
invention.
[0035] For example, the sandblasting process previously described may be substituted alternatively
by a process of cutting by means of a laser beam of the "excimer" (excited dimer)
type.
[0036] This type of laser is particularly suitable for machining solid materials, such as,
for example, silicon and silicon dioxide, inasmuch as the excimer laser operates
in a cold state without overheating the parts machined and without leaving traces
of melting on the surfaces struck by the laser beam.
[0037] The excimer laser beam generates a very small portion of heat, inasmuch as the energy
of the laser beam acts on the molecular bonds of the struck material, overcoming the
forces of cohesion. The removal of material therefore takes place by ablation of particles,
rather than through thermal phenomena such as melting, vaporization or sublimation.
[0038] This mechanism of ablation of particles confers on the machined parts a degree of
precision much higher than that obtainable with other conventional types of laser
beams, such as a CO₂ or YAG laser beam.
[0039] In order to construct plates for thermal ink jet heads industrially in large numbers
by the process described hereinbefore, a disc 80 (Fig.7) of silicon of circular form
with a diameter of about 100 mm and about 0.5 mm thick is normally used as the supporting
base 20. A cutaway portion 81 at the edge of the disc 80 commonly indicates the crystallographic
orientation <100> of the disc 80. On this disc there are produced at the same time
numerous identical configurations 82 of plates which, when construction has taken
place, are separated by means of crossed cuts in the support disc along intermediate
lines 83. Fig. 8 shows on an enlarged scale a part 84 of the disc 80 comprising a
slot 63 seen from the direction of the surface 62 of Fig. 6. A panel 85 in chain-dotted
lines represents the area occupied on the surface of the disc 80 by the layers 50,
52, 56 (Fig. 5) of each individual plate. In this case, the process hereinbefore described
for etching slots for feeding the ink in each individual plate finds valid application,
enabling a plurality of slots of the type of the groove 35 (Fig. 4) to be obtained
simultaneously with a single etching operation, with a considerable reduction in the
working times and costs.
1. A process for the manufacture of an ink duct in a thermal ink jet printing head
of the type in which ink expulsion chambers (4), heating (8, 8′) for heating the ink,
and
elements are produced in a plurality of superposed layers fixed on a support element
(20) defined by two opposed and parallel plane surfaces, the duct (14) being in communication
with the chambers and being formed through the thickness of the support element,
the process comprising the steps of:
a) defining an area of predetermined shape on a first of the said surfaces;
b) treating the said support element with an etching composition for a predetermined
time etch within the said area a recess extending in at least one preferred direction
and having an end wall at a pre-determined depth;
c) constructing the said plurality of superposed layers on a second of said surfaces
around the said recess; and
d) removing material of the said support element within the said recess and in the
said preferred direction between the said end wall and the said second surface.
2. A process as claimed in Claim 1, characterised in that the said support element
comprises a plate of crystalline silicon cut in accordance with a crystallographic
orientation of <100>.
3. A process as claimed in claim 2, characterised in that the said preferred direction
corresponds to the crystallographic orientation of <100> of the said support element
and is perpendicular to the said surfaces of the said element.
4. A process as in any one of the preceding claims, characterised in that the step
d) comprises the application of a sandblasting jet to the end of the said recess
in the said preferred direction.
5. Process as claimed in any one of claims 1 to 3, characterised in that the step
d) comprises the application of an excimer laser beam orientated in the said preferred
direction to the end of the said recess.
6. Process as claimed in any one of the preceding claims, characterised in that the
said etching composition comprises a mixture of ethylenediamine and pyrocatechol dissolved
in deionized water.
7. Process as claimed in any one of claims 1 to 5, characterised in that the said
etching composition comprises a mixture of potassium hydroxide and isopropanol dissolved
in deionized water.
8. Process as claimed in any one of claims 1 to 5, characterised in that the said
etching composition comprises a solution of hydrazine in deionized water.
9. Process as claimed in any one of the preceding claims, characterised in that the
said etching composition has a maximum characteristic attack gradient in the direction
<100>.
10. Process as claimed in claim 9, characterised in that the said attack time depends
on the said characteristic gradient and on the said pre-established depth.
11. Process as claimed in any one of the preceding claims, characterised in that the
said pre-established depth is comprised between 60% and 90% of the thickness of the
said support element.
12. Process as claimed in any one of the preceding claims, characterised in that the
step a) comprises the following steps:
e) applying protective layers of materials resistant to chemical agents to both the
said surfaces of the said support element; and
f) removing a part of the said protective layers on the said first surface to define
the said area of predetermined shape.
13. Process as claimed in claim 12, characterised in that the said protective layers
comprise a first layer of silicon dioxide superposed on both the said opposed surfaces
and a layer of photosensitive synthetic material resistant to chemical agents which
is superposed on the said first layer.
14. Process as claimed in claim 13, characterised in that the said photosensitive
synthetic material comprises polymerizable epoxy and/or acrylic resins.
15. Process as claimed in claim 13 or 14, characterised in that the said step f) moreover
comprises the following steps:
g) exposing an area of predetermined shape of the said photosensitive layer on the
said first surface;
h) developing the said exposed layer and completely removing the said first layer
in the portion subjacent the said area by means of a selective etching treatment.
16. Thermal ink jet printing head for a non-impact printer of the type in which ink
contained in expulsion chambers is expelled through a plurality of nozzles arranged
in two spaced, parallel rows by means of the selective heating of heating elements
contained in each chamber, and in which the nozzles, the expulsion chambers, the heating
elements and the corresponding electric supply conductors are formed in a plurality
of layers of metal and insulating materials superposed on each other and fixed on
a silicon support plate defined by two plane, parallel surfaces, each chamber communicating
with a common ink duct passing through the said plate and extending symmetrically
between and parallel to the rows of nozzles, characterised in that the duct comprises
a first chamber of substantially parellelepipedal form communicating with the said
expulsion chambers and a second chamber of substantially truncated pyramidal form
communicating with the said first chamber through a truncation base of the said second
chamber, the said truncation base being parallel to the said surfaces of the said
plate and being located in a position intermediate between the said surfaces.
17. Head as claimed in claim 16, characterised in that the said first chamber is defined
by two parallel side walls and by a base parallel and opposite to the said truncation
base, the said opposite base lying in a first of the said surfaces.
18. Head as claimed in one of claims 16 and 17, characterised in that the said second
chamber is defined by a larger base parallel and opposite to the said truncation base
and lying in a second of the said surfaces of the said plate.
19. Head as claimed in claim 17, wherein the said support plate is of crystalline
silicon cut in accordance with a crystallographic orientation of <100> , characterised
in that the said second chamber is moreover defined by two plane side walls inclined
with respect to the said larger base by a characteristic angle, the said side walls
being obtained by an etching treatment.
20. Head as claimed in any one of claims 16 to 19, characterised in that the said
first chamber is produced by means of a sandblasting operation.
21. Head as claimed in any one of claims 16 to 19, characterised in that the said
first chamber is produced by means of an excimer laser beam.