(57) An elevator system employing a microprocessor-based group controller communicating
with the cars (3, 4) using car position and velocity information provided by a "smart" primary position
transducer (SPPT) system to control the motion of the cars and assign them to handle
passenger demands. The SPPT includes an input shaft coupled to a primary encoder disk.
Coupled to the shaft through gearing are one or more encoder disks performing the
function of turns counting, as well as additional functions. Each disk contains multiple
tracks, and each of these tracks is sensed by a sensor, or, alternatively, the SPPT
may use two independent sensors per track. It is important to have two essentially
independent means of performing the key sensing functions. The read heads of the SPPT
are divided into primary and secondary sets with each set used to feed an independent
processor. Within each set of sensor signals, cross checks are performed to insure
the integrity of the system, which would detect a cracked or broken glass disk. In
the electronics of the SPPT system primary and secondary position signals are each
found by two methods and compared to maximize the likelihood of correct position determination,
with one method given priority over the other, depending on the circumstances. Two
independent channels for position and velocity information are maintained, using
independent parts, except for the input shafts and encoder disks. Exemplary formulae
for determining and generating the desired primary and secondary position and velocity
information are provided.
|
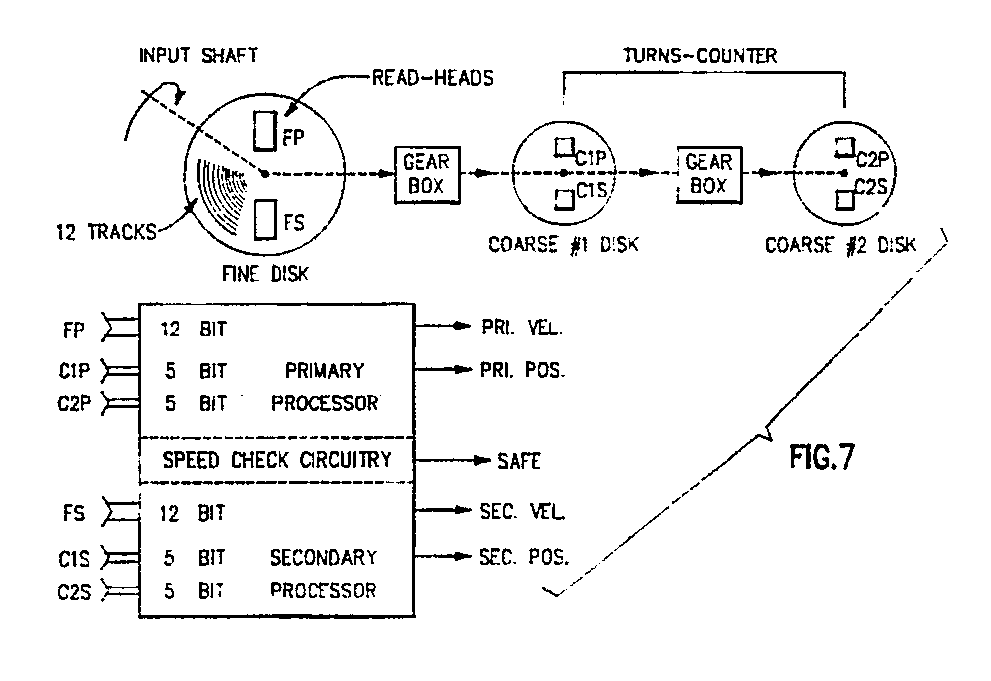
|