BACKGROUND OF THE INVENTION
(Field of the Invention)
[0001] This invention relates to a high-strength copper based alloy which is so excellent
in resistance to cracks caused by hot rolling (hereinafter called "hot rolling crack
resistance") that a hot rolled plate formed of the alloy is almost free of cracks,
thereby enabling to manufacture high-strength copper based alloy sheet materials from
the alloy, with a high yield.
(Prior Art)
[0002] In recent years, various electrical and electronic apparatuses have been made more
compact in size, lighter in weight and higher in performance. Accordingly, component
parts for such electrical and electronic apparatuses, such as lead frames of semiconductor
devices, terminals, and connectors, are required to be smaller in wall thickness.
To satisfy such requirement, there have been proposed or used many high-strength copper
based alloys for the manufacture of electrical and electronic parts, including one
proposed by Japanese Provisional Patent Publication (Kokai) No. 63-86838, which consists
essentially of, in percent by weight:
Ni: 0.8 - 4 %;
Si: 0.1 - 1.2 %;
Sn: 1 - 4 %; and
Cu and inevitable impurities: the balance.
[0003] However, these conventional high-strength copper based alloys are liable to have
cracks formed in lateral edges thereof (edge cracks) and cracks in upper and lower
side surfaces thereof (surface cracks) when they are hot rolled. Conventionally, attempts
have been made to prevent the formation of such cracks, e.g. by decreasing the reduction
ratio of each rolling pass, i.e. increasing the number of rolling passes. Even by
this method, the formation of cracks cannot be completely prevented, resulting in
a low yield of products.
SUMMARY OF THE INVENTION
[0004] It is the object of the invention to provide a high-strength copper based alloy which
has far more excellent hot rolling crack resistance as compared with conventional
copper based alloys, as well as strength as high as that of the conventional copper
based alloys.
[0005] To attain the above object, the present invention provides a copper based alloy having
excellent hot rolling crack resistance, which consists essentially of:
Sn: 0.4 - 2.5 %,
Ni: 0.2 - 4 %,
Si: 0.02 - 0.4 %,
Pb: 0.001 - 0.015 %,
Zn: 0.1 - 2 %,
Ni(%)/Si(%): not less than 10, and
Cu and inevitable impurities: the balance
The percentage throughout the specification is percent by weight.
[0006] The above and other objects, features, and advantages of the invention will become
more apparent from the following detailed description.
DETAILED DESCRIPTION
[0007] Under the aforesaid circumstances, the present inventors have made many studies in
order to obtain a high-strength copper based alloy having excellent hot rolling crack
resistance, and reached the following finding:
A copper based alloy consisting essentially of:
Sn: 0.4 - 2.5 %,
Ni: 0.2 - 4 %,
Si: 0.02 - 0.4 %,
Pb: 0.001 - 0.015 %,
Zn: 0.1 - 2 %,
Ni(%)/Si(%): not less than 10, and
Cu and inevitable impurities: the balance possesses high strength due to the action
of the component elements Sn, Ni, and Si, exhibits excellent workability in stamping,
press working, etc. which are indispensable for the manufacture of various electrical
and electronic parts, due to the action of the component element Pb, and at the same
time possesses excellent hot rolling crack resistance due to the action of the component
element Zn.
[0008] The present invention is based upon the above finding. The copper based alloy according
to the invention has the aforesaid chemical composition.
[0009] The reasons for specifying as above the contents of the component elements will be
described hereinbelow:
(a) Sn:
[0010] The Sn acts to enhance the strength of the copper based alloy. However, if the Sn
content is below 0.4%, the strength cannot be improved to a desired extent, whereas
if it is in excess of 2.5%, the hot rolling crack resistance will be spoiled. Therefore,
the Sn content has been limited to a range of 0.4 to 2. 5%, and preferably, 0.6 to
2.3%.
(b) Ni:
[0011] The Ni is solid-solved into the matrix to strengthen the same. Further, it is combined
with the Si to form a Ni-Si compound finely distributed in the matrix to thereby enhance
the strength. However, if the Ni content is below 0.2%, desired strength cannot be
achieved, and further, free Si can be present in the matrix, depending upon the ratio
between the Ni and Si contents. The presence of free Si in the matrix can cause edge
cracks and/or surface cracks during hot rolling of the copper based alloy. On the
other hand, if the Ni content exceeds 4%, an increased part of the Ni is solid-solved
into the matrix to lower the electric conductivity. Therefore, the Ni content has
been limited to a range of 0.2 to 4%, and preferably 0.5 to 3.5%.
(c) Si:
[0012] The Si is combined with the Ni to form a Ni-Si compound to increase the strength,
as mentioned above, and also acts to deoxize the matrix. However, if the Si content
is less than 0.02%, these actions cannot be performed to a satisfactory extent, whereas
if it is in excess of 0.4%, free Si can be present in the matrix, depending upon the
ratio between the Si and Ni contents, causing formation of cracks during hot rolling
of the copper based alloy. Therefore, the Si content has been limited to a range of
0.02 to 0.4%, and preferably 0.05 to 0.3%.
[0013] To prevent the formation of cracks due to hot rolling, it is required that the Si
should be entirely combined with the Ni to form a Ni-Si compound so that no free Si
is present in the matrix. To satisfy this requirement, the percentage ratio of Ni
to Si should be 10 or more.
(d) Pb:
[0014] The Pb acts to improve the formability of the copper based alloy such as stamping
and press working which are indispensable for the manufacture of electrical and electronic
parts from the copper based alloy. However, if the Pb content is less than 0.001%,
the above action cannot be performed to a satisfactory extent, whereas in excess of
0.015%, cracks are liable to occur during hot rolling of the alloy. Therefore, the
Pb content has been limited to a range of 0.001 to 0.015%, and preferably 0.002 to
0.01%.
(e) Zn:
[0015] The Zn acts to improve the hot rolling crack resistance under the condition that
the percentage ratio of Ni to Si is 10 or more, and hence prevent formation of edge
cracks and surface cracks in the hot rolled plate by hot rolling. However, if the
Zn content is below 0.1%, the above action cannot be performed to a satisfactory extent,
whereas if it is above 2%, there will be a degradation in the solder wettability.
Therefore, the Zn content has been limited to a range of 0.1 to 2%, and preferably
0.2 to 1.7%.
[0016] In addition, the copper based alloy according to the invention may contain, as invitable
impurities, carbon, sulfur, oxygen, hydrogen, and nitrogen. However, it is desirable
that carbon, sulfur, oxygen should each be contained in an amount of 30 ppm or less,
and hydrogen and nitrogen in an amount of 3 ppm or less.
[0017] Hot rolling to which the copper based alloy according to the invention can be subjected
should be effected under the following condition:
Starting Temperature: |
750 to 900°C, preferably 800 to 880°C |
Ending Temperature: |
400°C or more, preferably 550°C or more |
[0018] An example of the high-strength copper based alloy according to the invention will
now be described.
EXAMPLE
[0019] Molten copper based alloys having chemical compositions shown in Tables 1 and 2 were
prepared by the use of an ordinary low-frequency channel-type induction furnace, as
copper based alloys Nos. 1 - 11 according to the present invention, comparative copper
based alloys Nos. 12 - 18, and conventional copper based alloys Nos. 19 - 23. The
prepared molten alloys were cast by a conventional semi-continuous casting method,
into ingots, each having a size of 150mm in thickness, 500mm in width, and 2800mm
in length. The ingots were hot rolled over 15 rolling passes at a predetermined starting
temperature within a range of 800 to 880°C, and a predetermined ending temperature
within a range of 550 to 600, into a hot rolled plate having a thickness of 11mm.
The hot rolled plates were quenched, followed by each having its surfaces scalped
into a thickness of 10mm.
[0020] The hot rolled plates thus obtained were measured in respect of tensile strength
to evaluate the strength. Further, measurements were made of the number of edge cracks
in the opposite laterial edge portions of each hot rolled plate, the length of the
largest crack in the upper side surface (the maximum length), and the number of surface
cracks in the upper side surface. A longitudinally central portion having a length
of 20m of each hot rolled plate was subjected to the above measurements. Results of
the measurements are shown in Table 1.
[0021] The comparative Cu based alloys Nos. 12 to 18 each have the content of one of its
component elements or the percentage ratio of Ni to Si falling outside the range of
the present invention, as asterisked in Table 2.
[0022] It will be learned from the results shown in Tables 1 and 2 that the copper based
alloys Nos. 1 - 11 according to the present invention show far more excellent hot
rolling crack resistance than the conventional copper based alloys Nos. 19 - 23 and
have almost no edge crack nor surface crack formed therein after the hot rolling,
while possessing strength as high as that of the conventional copper based alloys
Nos. 19 - 23.
[0023] On the other hand, the comparative copper based alloys Nos. 12 - 18, each of which
has one of the component elements or the percentage ratio of Ni to Si falling outside
the range of the present invention, are inferior to the copper based alloys according
to the present invention in at least one of strength and hot rolling crack resistance.
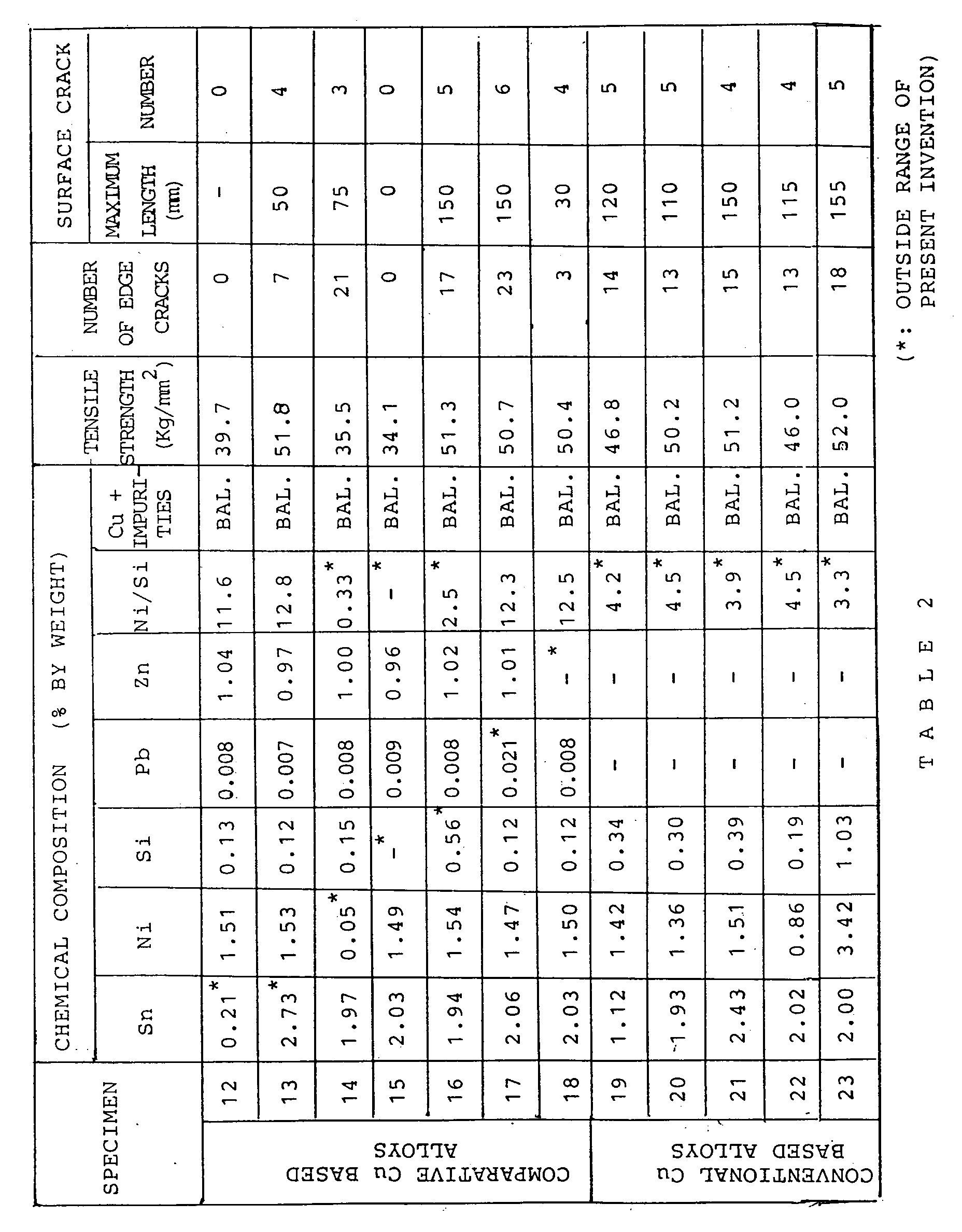
[0024] As described above, the copper based alloy according to the invention has excellent
strength, and hence enables to design various electrical and electronic parts formed
therefrom to be reduced in wall thickness, thus contributing to reduction in the size
and weight of the parts. Besides, a hot rolled plate formed of the alloy is almost
free of edge cracks and surface cracks. Therefore, the copper based alloy according
to the invention is useful to greatly improve the yield and quality of products formed
therefrom.
1. A high-strength copper based alloy having excellent resistance to cracks caused by
hot rolling, which consists essentially of:
Sn: 0.4 - 2.5 %,
Ni: 0.2 - 4 %,
Si: 0.02 - 0.4 %,
Pb: 0.001 - 0.015 %,
Zn: 0.1 - 2 %,
Ni(%)/I(%); not less than 10, and
Cu and inevitable impurities: the balance.
2. The high-strength copper based alloy as claimed in claim 1, consisting essentially
of:
Sn: 0.6 - 2.3%,
Ni: 0.5 - 3.5%,
Si: 0.05 - 0.3%,
Pb: 0.002 - 0.01%,
Zn: 0.2 - 1.7%,
Ni(%)/Si(%); not less than 10, and
Cu and inevitable impurities: the balance.