(19) |
 |
|
(11) |
EP 0 407 833 B1 |
(12) |
EUROPÄISCHE PATENTSCHRIFT |
(45) |
Hinweis auf die Patenterteilung: |
|
17.02.1993 Patentblatt 1993/07 |
(22) |
Anmeldetag: 29.06.1990 |
|
|
(54) |
Deckelartiger Verschluss für schachtel- oder kassettenartige Behälter und Verfahren
zu seiner Herstellung
Cover for box-like containers and method for making it
Fermeture en forme de couvercle pour récipients similaires à des boîtes ou à des cassettes
et procédé pour sa fabrication
|
(84) |
Benannte Vertragsstaaten: |
|
AT CH DE ES FR GB IT LI NL |
(30) |
Priorität: |
10.07.1989 AT 1664/89
|
(43) |
Veröffentlichungstag der Anmeldung: |
|
16.01.1991 Patentblatt 1991/03 |
(73) |
Patentinhaber: EGO KUNSTSTOFFWERK AG |
|
CH-9450 Altstätten/SG (CH) |
|
(72) |
Erfinder: |
|
- Hasler, Kurt, Dipl.-Ing.
CH-8580 Amriswil (CH)
|
(74) |
Vertreter: Hefel, Herbert, Dipl.-Ing. |
|
Egelseestrasse 65a 6800 Feldkirch-Tosters 6800 Feldkirch-Tosters (AT) |
(56) |
Entgegenhaltungen: :
CH-A- 150 999 FR-A- 1 166 825 US-A- 1 782 110
|
DE-A- 3 608 277 GB-A- 20 640 US-A- 2 692 698
|
|
|
|
|
|
|
|
|
Anmerkung: Innerhalb von neun Monaten nach der Bekanntmachung des Hinweises auf die
Erteilung des europäischen Patents kann jedermann beim Europäischen Patentamt gegen
das erteilte europäischen Patent Einspruch einlegen. Der Einspruch ist schriftlich
einzureichen und zu begründen. Er gilt erst als eingelegt, wenn die Einspruchsgebühr
entrichtet worden ist. (Art. 99(1) Europäisches Patentübereinkommen). |
[0001] Die Erfindung bezieht sich auf einen deckelartigen Verschluß für schachteloder kassettenartige
Behälter, wobei der Verschluß randseitig in abschnittweise einen gebogenen Verlauf
aufweisenden Führungsnuten des Behälters verschiebbar geführt ist und der Verschluß
aus einer Vielzahl von mit ihren Längsseiten aneinander anliegenden, lamellenartigen
Streifen gleicher Länge besteht und auf ein Verfahren zu seiner Herstellung.
[0002] Es ist bekannt, Schränke oder größere Behälter mit sogenannten Rolladen zu verschließen.
Unter Rolladen im Sinne der gegenständlichen Erfindung werden hier flächenhafte Verschlüsse
verstanden, die in einer Ebene biegsam sind und die aus einer Vielzahl unmittelbar
nebeneinander angeordneter, lamellenartiger Leisten bestehen, die in staubdichter
Weise miteinander verbunden sind. In der Regel werden solche Rolläden aus Holzleisten
gefertigt, die auf einem festen, textilen Untergrund befestigt, beispielsweise aufgeklebt,
sind. Randseitig sind diese Rolläden in Nuten des Schrankes oder des Behälters geführt.
In diesem Zusammenhang ist beispielsweise der Rolladen nach der GB-PS 20 640 (A.D.
1913) zu nennen, der aus einzelnen, nebeneinander liegenden Holzleisten besteht, die
auf einem starken Leinengewebe aufgeklebt sind, oder der Schachtelverschluß nach der
CH-PS 150 999, wobei hier die benachbart liegenden Leisten voneinander etwas distanziert
sind. Diese Leisten sind hier mit ihrer Unterseite mit einer Folie verklebt, und darüberhinaus
ist auch an der Oberseite eine Folie vorgesehen, die jedoch der Querschnittskontur
entlang verläuft. Auch einstückige Rolladenverschlüsse für schachtelartige Behälter
sind bekannt (FR-PS 1166 825), die aus einem elastisch verformbaren Material gegossen
sind, wobei die Längsschnittkontur eines solchen Verschlusses sägezahnartig ausgestaltet
ist, und im Basisbereich dieses Verschlusses ist eine Verstärkungseinlage mit eingegossen.
Ein anderer bekannter einstückiger Verschluß (US-PS 1782 110) für einen schachtelartigen
Behälter besteht aus einem wellig geprägten Karton, der auf seiner Rückseite mit einem
dieser Prägung folgenden Verstärkungsgewebe verklebt ist. Es ist auch bekannt und
naheliegend, solche Rolläden einstückig aus Kunststoffen herzustellen, wobei dazu
Kunststoffe hoher Biegefestigkeit verwendet werden. Die einzelnen, einander benachbarten
Leisten, die einen solchen Rolladen bilden, gehen dann über ein sogenanntes Filmscharnier
ineinander über, und Scharnier und Leiste sind aus einem Material einstückig hergestellt.
Kunststoffe, die sich dafür eignen und eine hinreichend hohe Biegefestigkeit und eine
ausreichende Biegsamkeit aufweisen, sind aber nicht glasklar, ja nicht einmal lichtdurchlässig.
[0003] Es besteht jedoch Bedarf dafür, kassetten- oder schachtelartige Behälter für bestimmte
Gebrauchsgegenstände mit solchen "Rolläden" zu verschließen, jedoch besteht die Forderung,
daß diese Rolläden lichtdurchlässig, insbesondere glasklar sein müssen, damit der
im Behälter befindliche Gegenstand, auch ohne daß der Behälter geöffnet wird, beobachtet
und gesehen werden kann. Zur Herstellung solcher Rolläden eignet sich im Prinzip Acrylharz,
mit welchem glasartige Produkte herstellbar sind, doch ist dieses Material sehr spröde
und zur Fertigung von Filmscharnieren gänzlich ungeeignet. Da darüberhinaus Behälter
der hier in Rede stehenden Art relativ klein sind, sind auch die Leisten oder Streifen,
die für diesen rolladenartigen Verschluß verwendet werden, relativ dünnwandig, so
daß für die konstruktive Gestaltung von Verbindungselementen zwischen den jeweiligen
benachbarten Leisten kaum ausreichend Platz zur Verfügung steht.
[0004] Von diesem Stand der Technik und von den geschilderten Erkenntnissen geht die Erfindung
aus und zielt darauf ab, deckelartige Verschlüsse nach Rolladen-Bauart vorzuschlagen,
die die geschilderten Nachteile nicht aufweisen bzw. die die geforderten Bedingungen
erfüllen können, was erfindungsgemäß dadurch gelingt, daß die Streifen aus lichtdurchlässigem,
vorzugsweise aus glasklarem Kunststoff gefertigt sind und an ihren beiden äußeren
Rändern mittels Kunststoffdrähten miteinander verbunden sind. Da aus hochfesten Materialien
zugfeste Kunststoffdrähte von geringem Durchmesser gefertigt werden können, können
die randseitigen Bohrungen und Aussparungen für die Aufnahme und für die Durchführung
des Kunststoffdrahtes sehr klein gehalten werden.
[0005] Ist der deckelartige Verschluß ferner so aufgebaut, daß die Kunststoffdrähte in jenem
Bereich der beiden äußeren Ränder vorgesehen sind, die von den Führungsnuten des Behälters
aufgenommen sind, so liegen diese Kunststoffdrähte praktisch zur Gänze in den Führungsnuten
des Behälters und sind nicht sichtbar.
[0006] Sind die lamellenartigen Streifen sehr dünn, so ist vorgesehen, daß die lamellenartigen
Streifen an ihren Schmalseiten Zapfen tragen, welche im wesentlichen koaxial mit der
Längsmittelachse des jeweiligen Streifens liegen und die Kunststoffdrähte mit diesen
Zapfen verbunden sind, insbesondere durch diese Zapfen hindurchlaufen (Figur 2). Die
Durchmesser der Zapfen, die von den Führungen des Behälters aufgenommen werden, können
dabei ohne weiteres etwas größer gemacht werden, als es der Wandstärke der lamellenartigen
Streifen entspricht, so daß hier die Durchgangsöffnungen für die Aufnahme der Kunststoffdrähte
ohne weiteres untergebracht werden können.
[0007] Damit der deckelartige, nach Art eines Rolladens aufgebaute Verschluß auch staubdicht
ist, sind von den unmittelbar aneinander anliegenden Längsseiten benachbarter lamellenartiger
Streifen die eine Längsseite als Hohlkehle und die andere dazu korrespondierend bombiert
ausgebildet. Um die hier verwendeten Hohlkehlen und Bombierungen zu vermeiden, die
aufwendige Spritzgußformen für die Herstellung der Streifen notwendig machen, wenn
diese im Spritzgußverfahren hergestellt werden, ist als weitere Maßnahme zur Erzielung
eines staubdichten Verschlusses vorgesehen, daß die unmittelbar aneinander anliegenden
Längsseiten benachbarter lamellenartiger Streifen eine absatzartige Stufe aufweisen
und diese Stufen benachbarter lamellenartiger Streifen sich gegenseitig überlappen
(Figur 2).
[0008] Die Abmessungen solcher deckelartigen, nach Art von Rolläden aufgebauten Verschlüsse
sind klein, andererseits stellen solche Verschlüsse Massenartikel dar, so daß nach
einer einfachen und billigen Herstellungsweise getrachtet werden muß, nach einer Herstellungsweise,
nach der der Verschluß sozusagen in einem und als ganzes hergestellt werden kann.
Erfindungsgemäß ist dazu vorgesehen, daß gleichzeitig in einem Arbeitsgang mehrere
voneinander distanzierte, in einer Ebene mit ihren Längsseiten einander benachbart
liegende Streifen in einer Spritzgußform gespritzt werden, in welche die Kunststoffdrähte
vor dem Einbringen des Kunststoffes eingelegt worden sind, und die eingelegten Kunststoffdrähte
eine geschlossene, glatte, reibungsarme Oberfläche aufweisen und nach dem Öffnen der
Spritzgußform und nach dem Entformen der darin hergestellten, voneinander distanzierten,
mittels der Kunststoffdrähte randseitig verbundenen Streifen diese bei gespannten
Kunststoffdrähte gegeneinander verschoben werden (Figur 4). Eine andere zweckmäßige
Verfahrensweise besteht darin, daß gleichzeitig in einem Arbeitsgang mehrere voneinander
distanzierte, in einer Ebene mit ihren Längsseiten einander benachbart liegende Streifen
in einer Spritzgußform gespritzt werden, in welche die gummielastischen Kunststoffdrähte
unter Vorspannung vor dem Einbringen des Kunststoffes eingelegt worden sind und nach
dem Öffnen der Spritzgußform und nach dem Entformen der darin hergestellten, voneinander
distanzierten, mittels der vorgespannten, gummielastischen Kordeln randseitig verbundenen
Streifen die Kunststoffdrähte entlastet werden, wodurch die ursprünglich voneinander
getrennten Streifen sich mit ihren Längsseiten aneinanderlegen.
[0009] Nach einer weiteren zweckmäßigen Maßnahme ist vorgesehen, daß gleichzeitig in einem
Arbeitsgang mehrere voneinander distanzierte, in einer Ebene mit ihren Längsseiten
einander benachbart liegende Streifen in einer Spritzgußform gespritzt werden, in
welche die Kunststoffdrähte vor dem Einbringen des Kunststoffes eingelegt worden sind
und nach dem Abschluß des Spritzvorganges und nach dem Öffnen der Spritzgußform und
nach dem Entformen der darin hergestellten, voneinander distanzierten, mittels der
Kunststoffdrähte randseitig verbundenen Streifen die zwischen benachbarten Streifen
befindlichen Kunststoffdrahtabschnitte zur relativen Verkürzung der zwischen benachbarten
Streifen vorhandenen Abstände um die seitlichen Zapfen geschlungen werden (Figur 5,
6).
[0010] Unabhängig davon, welche Verfahrensweise vorgesehen ist, in allen Fällen ist es zweckmäßig,
darauf zu achten, daß die Schmelztemperatur des Materials für die Streifen und die
Schmelztemperatur zumindest des Oberflächenmaterials der Kunststoffdraht unterschiedlich
gewählt werden, wobei letztere höher ist als jene des Materials für die Streifen.
[0011] Anhand der Zeichnung werden Ausführungsbeispiele der Erfindung erörtert, um die Erfindung
näher zu veranschaulichen. Es zeigen:
Figur 1 in Schrägsicht einen aus Acrylglasteilen gebildeten Behälter mit einem nach
Art eines Rolladens aufgebauten, deckelartigen und durchsichtigen Verschluß;
Figur 2 drei benachbart liegende Streifen des Verschlusses in Seitensicht und in Figur
3 in Draufsicht, beide in einem gegenüber Figur 1 erheblich vergrößerten Maßstab;
Figur 4 eine Draufsicht auf eine Hälfte der Spritzgußform;
Die Figuren 5 und 6 die Ansicht und die Draufsicht auf ein weiteres Ausführungsbeispiel.
[0012] Figur 1 zeigt in Schrägsicht einen kassettenartigen Behälter 1, der aus Acrylglasteilen
hergestellt ist. Er besitzt einen Boden 2 und Seitenwände 3, 4, 5 und 6, welche miteinander
fest verbunden sind. In den beiden parallel zueinander liegenden Seitenwänden 4 und
5 ist je eine Führungsnut 7 vorgesehen, wobei jede dieser Führungsnuten zwei parallel
verlaufende, gerade Äste und einen diese Äste verbindenden Bogen aufweist. Diese Führungsnuten
nehmen die Ränder des deckelartigen, nach Art eines Rolladens aufgebauten Verschlusses
8 auf, wobei der vorderste lamellenartige Streifen dieses Verschlusses noch zusätzlich
eine Griffleiste 10 besitzt. Auch die den Verschluß bildenden, lamellenartigen Streifen
11 sind aus glasklarem Acrylglas gefertigt.
[0013] Detaildarstellungen in einem gegenüber Figur 1 stark vergrößerten Maßstab veranschaulichen
die Figuren 2 und 3, die die drei vordersten Streifen 11 des Verschlusses 8 in Seitensicht
und Draufsicht zeigen. Jeder Streifen 11 besitzt stirnseitig einen Zapfen 12, dessen
Durchmesser etwas größer ist als die Stärke des Streifens. Durch diese Zapfen 12 verlaufen
beidseitig Kunststoffdrähte 13, die die Streifen 11 zusammenhalten. An ihren Längsseiten
besitzen diese einzelnen Streifen 11 Stufungen 14, wobei sich die durch diese Stufungen
gebildeten Absätze gegenseitig überdecken, um so einen staubdichten Verschluß zu schaffen.
[0014] Um einen solchen Verschluß als Massenartikel rationell herstellen zu können, sind
folgende Verfahrensmaßnahmen vorgesehen:
In einer mindestens zweiteiligen Spritzgußform, von der in Figur 4 nur die eine
Hälfte 15 in Draufsicht dargestellt ist, sind so viele formgebende Aussparungen vorgesehen,
wie der herzustellende Deckel Streifen 11 besitzt. Diese formgebenden Aussparungen
sind voneinander um das Maß A distanziert. Bevor die Spritzgußform verschlossen wird,
werden die Kunststoffdrähte 13 spannungslos eingelegt, wobei hier Kunststoffdrähte
13 verwendet werden, die eine glatte, geschlossene und reibungsarme Oberfläche besitzen
(monofil) und deren Material einen Schmelzpunkt hat, der oberhalb des Schmelzpunktes
jenes Materials liegt, das für die Herstellung der Streifen 11 eingesetzt wird. Ist
die Spritzgußform in dieser Weise vorbereitet, so wird sie verschlossen, und das aufgeschmolzene
Material für die Herstellung der Streifen 11 wird in herkömmlicher Weise unter hohem
Druck und hoher Temperatur eingespritzt. Sobald das eingespritzte Material die Formhöhlungen
gefüllt hat und hinreichend erstarrt ist, wird die Form geöffnet, und die Streifen
werden zusammen mit den umspritzten Kunststoffdräh ten 13 aus der Form genommen. Aufgrund
der glatten, reibungsarmen Oberfläche des Kunststoffdrahtes 13 und des hohen Schmelzpunktes
des Materials, aus dem die Kunststoffdrähte bestehen, zumindest deren Oberfläche,
tritt zwischen dem Material dem Kunststoffdraht und dem zur Herstellung der Streifen
11 dienenden Material keine Bindung ein, so daß nunmehr die vorerst voneinander um
den Abstand A distanzierten Streifen zusammengeschoben werden können (Pfeil 16), bis
sie die aus den Figuren 2 und 3 ersichtliche Lage gegeneinander einnehmen. Die Pfeile
16 deuten diese Verschiebebewegung an, wobei während der Ausübung der hier notwendigen
Schubkraft die Enden der Kunststoffdrähte 13 festgehalten werden müssen, deren Enden
anschließend verknotet, verschweißt oder anderweitig abgebunden werden. Damit ist
der Verschluß sozusagen verbrauchsfertig hergestellt.
[0015] Ein anderes Verfahren sieht in diesem Zusammenhang vor, daß unter Beibehaltung der
erörterten Spritzgußform und ihrer Aufteilung der Formhöhlungen ein gummielastischer,
vorzugsweise polyfiler Kunststoffdraht 13 vor dem Verschließen der Form in diese eingelegt
wird, wobei hier der Kunststoffdraht 13 vorgespannt wird, und zwar um jenes Maß, das
der Summe der Abstände A entspricht. Wird nach dem Schließen der Spritzgußform in
der oben geschilderten Weise verfahren, so zieht nach dem Entformen der vorgespannte
und anschließend entlastete gummielastische Kunststoffdraht 13 die mit Abstand voneinander
gespritzten Streifen 11 zusammen (Figur 2 und Figur 3). Gegenüber der erstbesprochenen
Bauart (Verwendung eines Kunststoffdrahtes 13 ohne ausgeprägtes gummielastisches Verhalten)
ist hier jedoch ein gewisser Nachteil in Kauf zu nehmen, der darin besteht, daß bei
der Ausübung einer Zugkraft auf den Verschluß es unter anderem nicht vermeidbar ist,
daß zwischen benachbarten Leisten Spalte aufklaffen.
[0016] Eine weitere Verfahrensmöglichkeit veranschaulicht Figur 4 in Verbindung mit den
Figuren 5 und 6. Hier wird ein Kunststoffdraht 13 ohne ausgeprägte Dehnungseigenschaften
und ohne besondere Oberflächenbeschaffenheit (poly- oder monofil) verwendet. Die Verfahrensschritte
sind vorerst gleich jenen, wie sie oben geschildert worden sind. Nach dem Entformen
werden jedoch die einzelnen, zwischen benachbarten Zapfen 12 liegenden Kunststoffdrahtabschnitte
um jeweils einen der benachbarten Zapfen 12 gewickelt (Figur 5 und Figur 6), so daß
dadurch die Länge dieser Kunststoffdrahtabschnitte relativ verkürzt und damit die
vorerst voneinander distanzierten Streifen 11 zusammengebracht werden. Bei dieser
Verfahrensweise ist darauf zu achten, daß der Formabstand A der einzelnen Streifen
11 und die Länge 1 des Kunststoffdrahtabschnittes zwischen benachbarten Zapfen 12
entsprechend aufeinander abgestimmt werden: Durch das Umschlingen eines Zapfens 12
(Figur 5) ist der Kunststoffdrahtabschnitt um ein Maß zu verkürzen, das dem Formabstand
A der Streifen 11 entspricht. Dieses Verfahren ist aufwendig, so daß den beiden vorstehend
erörterten Verfahren wohl der Vorrang einzuräumen ist. In der Zeichnung (Fig. 5, 6)
besitzen die Zapfen 12 eine glatte Oberfläche aus Gründen der Anschaulichkeit. In
der Praxis wurden in diesem Zapfen 12 umlaufende Nuten vorgesehen, die die umschlingenden
Kunststoffdrähte aufnehmen.
Dank der geschilderten Maßnahmen ist es möglich geworden, einen deckelartigen, nach
Art eines Rolladens aufgebauten Verschluß aus glasklarem Material sozusagen in einem
Arbeitsgang zu fertigen und dennoch einen Verschluß zu erhalten, der eine ausreichende
Staubdichtheit aufweist.
[0017] Bei den gezeigten und beschriebenen Ausführungsbeispielen überlappen sich die Längsseiten
benachbarter Streifen 11 infolge der Stufung 14. Grundsätzlich ist es möglich, die
Staubdichtheit auch dadurch zu erreichen, daß von den unmittelbar aneinander anliegenden
Längsseiten benachbarter lamellenartiger Streifen die eine als Hohlkehle und die andere
dazu korrespondierend bombiert ausgebildet wird. Dies erfordert aber einen höheren
und damit kostspieligeren Formenaufwand.
1. Deckelartiger Verschluß für schachtel- oder kassettenartige Behälter (1), wobei der
Verschluß randseitig in abschnittweise einen gebogenen Verlauf aufweisenden Führungsnuten
(7) des Behälters (1) verschiebbar geführt ist und der Verschluß aus einer Vielzahl
von mit ihren Längsseiten aneinander anliegenden, lamellenartigen Streifen (11) gleicher
Länge besteht, dadurch gekennzeichnet, daß die Streifen (11) aus lichtdurchlässigem,
vorzugsweise aus glasklarem Kunststoff gefertigt sind und an ihren beiden äußeren
Rändern mittels Kunststoffdrähten (13) miteinander verbunden sind.
2. Deckelartiger Verschluß nach Anspruch 1, dadurch gekennzeichnet, daß die Kunststoffdrähte
(13) in jenem Bereich der beiden äußeren Ränder vorgesehen sind, die von den Führungsnuten
(7) des Behälters (1) aufgenommen sind.
3. Deckelartiger Verschluß nach Anspruch 1 oder 2, dadurch gekennzeichnet, daß die lamellenartigen
Streifen (11) an ihren Schmalseiten Zapfen (12) tragen, welche im wesentlichen koaxial
mit der Längsmittelachse des jeweiligen Streifens (11) liegen und die Kunststoffdrähte
(13) mit diesen Zapfen (12) verbunden sind, insbesondere durch diese Zapfen hindurchlaufen
(Figur 2).
4. Deckelartiger Verschluß nach Anspruch 3, dadurch gekennzeichnet, daß der Durchmesser
der Zapfen (12) größer ist als die Stärke der lamellenartigen Streifen (11).
5. Deckelartiger Verschluß nach Anspruch 1 oder 2, dadurch gekennzeichnet, daß von den
unmittelbar aneinander anliegenden Längsseiten benachbarter lamellenartiger Streifen
die eine Längsseite als Hohlkehle und die andere dazu korrespondierend bombiert ausgebildet
sind.
6. Deckelartiger Verschluß nach Anspruch 1 oder 2, dadurch gekennzeichnet, daß die unmittelbar
aneinander anliegenden Längsseiten benachbarter lamellenartiger Streifen (11) eine
absatzartige Stufe (14) aufweisen und diese Stufen benachbarter lamellenartiger Streifen
sich gegenseitig überdecken (Figur 2).
7. Deckelartiger Verschluß nach einem der Ansprüche 1 bis 6, dadurch gekennzeichnet,
daß die aus lichtdurchlässigem, vorzugsweise glasklarem Kunststoff gefertigten Streifen
in einem Spritzgußverfahren hergestellt sind.
8. Deckelartiger Verschluß nach Anspruch 1, dadurch gekennzeichnet, daß der Kunststoffdraht
(13) eine glatte, geschlossene, reibungsarme Oberfläche besitzt.
9. Deckelartiger Verschluß nach Anspruch 1, dadurch gekennzeichnet, daß der Kunststoffdraht
(13) gummielastisch ist.
10. Verfahren zur Herstellung des deckelartigen Verschlusses nach einem der Ansprüche
1 bis 8, dadurch gekennzeichnet, daß gleichzeitig in einem Arbeitsgang mehrere, voneinander
distanzierte, in einer Ebene mit ihren Längsseiten einander benachbart liegende Streifen
(11) in einer Spritzgußform (15) gespritzt werden, in welche die Kunststoffdrähte
(13) vor dem Einbringen des Kunststoffes eingelegt worden sind, und die eingelegten
Kunststoffdrähte (13) eine geschlossene, glatte, reibungsarme Oberfläche aufweisen
und nach dem Öffnen der Spritzgußform und nach dem Entformen der darin hergestellten,
voneinander distanzierten, mittels der Kunststoffdrähte (13) randseitig verbundenen
Streifen (11) diese bei gespannten Kunststoffdrähten (13) gegeneinander verschoben
werden, und die Schmelztemperatur des Materials für die Streifen (11) und die Schmelztemperatur
zumindest des Oberflächenmaterials des Kunststoffdrahtes (13) unterschiedlich gewählt
werden, wobei letztere höher ist als jene des Materials für die Streifen (11) (Figur
4).
11. Verfahren zur Herstellung des deckelartigen Verschlusses nach einem der Ansprüche
1 bis 8, dadurch gekennzeichnet, daß gleichzeitig in einem Arbeitsgang mehrere, voneinander
distanzierte, in einer Ebene mit ihren Längsseiten einander benachbart liegende Streifen
(11) in einer Spritzgußform gespritzt werden, in welche die gummielastischen Kunststoffdrähte
(13) unter Vorspannung vor dem Einbringen des Kunststoffes eingelegt worden sind und
nach dem Öffnen der Spritzgußform und nach dem Entformen der darin hergestellten,
voneinander distanzierten, mittels der vorgespannten, gummielastischen Kunststoffdrähte
(13) randseitig verbundenen Streifen (11) die Kunststoffdrähte (13) entlastet werden,
wodurch die ursprünglich voneinander getrennten Streifen (11) sich mit ihren Längsseiten
aneinanderlegen.
12. Verfahren zur Herstellung des deckelartigen Verschlusses nach einem der Ansprüche
1 bis 8, dadurch gekennzeichnet, daß gleichzeitig in einem Arbeitsgang mehrere, voneinander
distanzierte, in einer Ebene mit ihren Längsseiten einander benachbart liegende Streifen
(11) in einer Spritzgußform (15) gespritzt werden, in welche die Kunststoffdrähte
(13) vor dem Einbringen des Kunststoffes eingelegt worden sind und nach dem Abschluß
des Spritzvorganges und nach dem Öffnen der Spritzgußform und nach dem Entformen der
darin hergestellten, voneinander distanzierten, mittels der Kunststoffdrähte (13)
randseitig verbundenen Streifen (11) die zwischen benachbarten Streifen (11) befindlichen
Kunststoffdrahtabschnitte zur relativen Verkürzung der zwischen benachbarten Streifen
vorhandenen Abstände (A) um die seitlichen Zapfen (12) geschlungen werden (Figur 5,
6).
13. Verfahren nach Anspruch 12, dadurch gekennzeichnet, daß in dem Zapfen (12) zur Aufnahme
des ihn umschlingenden Abschnittes des Kunststoffdrahtes (13) Nuten vorgesehen sind.
14. Verfahren nach einem der Ansprüche 11 oder 12, dadurch gekennzeichnet, daß die Schmelztemperatur
des Materials für die Streifen (11) und die Schmelztemperatur zumindest des Oberflächenmaterials
des Kunststoffdrahtes (13) unterschiedlich gewählt werden, wobei letztere höher ist
als jene des Materials für die Streifen (11).
1. A cover for boxe-like or case-like containers (1), the edge of the cover being displaceably
guided in guide grooves (7) of the container (1) - part of these grooves (7) having
a curved course - and the cover being composed of a plurality of lamella-like strips
(11) of the same length whose long sides are adjacent each other, characterized in
that the strips (11) are manufactured from a light-transmitting, preferably transparent,
plastics material and are connected to one another at their two outer edges by means
of plastics wires (13).
2. A cover in accordance with Claim 1, characterized in that the plastics wires (13)
are provided in that region of the two outer edges which is received by the guide
grooves (7) of the container (1).
3. A cover in accordance with Claim 1 or 2, characterized in that the lamella-like strips
(11) carry pins (12) on their narrow sides, these pins lying substantially coaxial
with the longitudinal central axis of the respective strip (11), and the plastics
wires (13) are connected to these pins (12), in particular run through these pins
(Figure 2).
4. A cover in accordance with Claim 3, characterized in that the diameter of the pins
(12) is greater than the thickness of the lamella-like strips (11).
5. A cover in accordance with Claim 1 or 2, characterized in that of the directly adjacent
long sides of neighbouring lamella-like strips, one long side is in the form of a
channel and the other is correspondingly convex.
6. A cover in accordance with Claim 1 or 2, characterized in that the directly adjacent
long sides of neighbouring lamella-like strips (11) have a shoulder-like step (14)
and these steps of neighbouring lamella-like strips cover one another (Fig. 2).
7. A cover in accordance with any one of Claims 1 to 6, characterized in that the strips
manufactured from a light-transmitting, preferably transparent, plastics material
are manufactured in one injection moulding process.
8. A cover in accordance with Claim 1, characterized in that the plastics wire (13) has
a smooth, closed, low-friction surface.
9. A cover in accordance with Claim 1, characterized in that the plastics wire (13) is
rubber-resilient.
10. A process for the manufacture of the cover in accordance with any one of Claims 1
to 8, characterized in that simultaneously, in one working process, a plurality of
strips (11) - arranged at a distance from one another and lying in one plane with
their long sides neighbouring one another - are injection moulded in an injection
mould (15) into which the plastics wires (13) have been inserted before the introduction
of the plastics material; and the inserted plastics wires (13) have a closed smooth
low-friction surface; and after opening of the injection mould and removal therefrom
of the strips (11) - which have been manufactured therein, are at a distance from
one another and are connected at the edge by means of the plastics wires (13) - these
strips are, with tensioned plastics wires (13), displaced so as to be against one
another; and the melting temperature of the material for the strips (11) and the melting
temperature of at least the surface material of the plastics wire (13) are selected
to be different, the latter being higher than that of the material for the strips
(11) (Fig. 4).
11. A process for the manufacture of the cover in accordance with any one of Claims 1
to 8, characterized in that simultaneously, in one working process, a plurality of
strips (11) - arranged at a distance from one another and lying in one plane with
their long sides neighbouring one another - are injection moulded in an injection
mould into which the rubber-resilient plastics wires (13) have been inserted, under
pre-tension, before introduction of the plastics material; and after opening of the
injection mould and removal therefrom of the strips (11) - which have been manufactured
in the latter, are arranged at a distance from one another and are connected at the
edge by means of the prestressed rubber-resilient plastics wires (13) - the plastics
wires (13) are de-tensioned whereby the originally separated long sides of the strips
(11) come into juxtaposition.
12. A process for the manufacture of the cover in accordance with any one of Claims 1
to 8, characterized in that simultaneously, in one working process, a plurality of
strips (11) - arranged at a distance from one another and lying in one plane with
their long sides neighbouring one another - are injection moulded in an injection
mould (15) into which the plastics wires (13) have been inserted before introduction
of the plastics material; and after completion of the injection moulding process and
after opening of the injection mould and after removal therefrom of the strips (11)
- which have been manufactured therein, are arranged at a distance from one another
and are connected at the edge by means of the plastics wires - the plastics wire portions
located between neighbouring strips (11) are wound around the lateral pins (12) so
as to relatively shorten the distances (A) between neighbouring strips (Figures 5,
6).
13. A process in accordance with Claim 12, characterized in that grooves are provided
in the pin (12) to receive the plastics wire (13) portion winding therearound.
14. A process in accordance with any one of Claims 11 or 12, characterized in that the
melting temperature of the material for the strips (11) and the melting temperature
of at least the surface material of the plastics wire (13) are selected to be different,
the latter being higher than that of the material for the strips (11).
1. Fermeture en forme de couvercle pour des récipients (1) similaires à des boîtes ou
des cassettes, dans lesquels la fermeture est guidée en bordure de façon à pouvoir
coulisser dans des gorges de guidage (7) du récipient (1), qui comportent sur un tronçon
un tracé en courbe, tandis que cette fermeture est constituée par une pluralité de
bandes (11) en forme de lamelles de même longueur, s'appliquant les unes contre les
autres par leurs côtés longitudinaux, fermeture en forme de couvercle caractérisée
en ce que les bandes (11) sont fabriquées en matière synthétique laissant passer la
lumière, de préférence ayant la transparence du verre, et qui sont reliées ensemble
par des fils en matière synthétique (13) sur leurs deux bords externes.
2. Fermeture en forme de couvercle selon la revendication 1, caractérisée en ce que les
fils en matière synthétique (13) sont prévus dans la zone des deux bords externes
qui sont saisis par les gorges de guidage (7) du récipient (1).
3. Fermeture en forme de couvercle selon la revendication 1 ou la revendication 2, caractérisée
en ce que les bandes en forme de lamelles (11) portent sur leurs côtés étroits des
tétons (12) qui sont essentiellement co-axiaux à l'axe médian longitudinal de la bande
(11) considérée, et les fils en matière synthétique (13) sont reliés à ces tétons
(12), et passent notamment à travers ces tétons (figure 2).
4. Fermeture en forme de couvercle selon la revendication 3, caractérisée en ce que le
diamètre des tétons (14) est supérieur à l'épaisseur des bandes en forme de lamelles
(11).
5. Fermeture en forme de couvercle selon la revendication 1 ou la revendication 2, caractérisée
en ce que parmi les côtés longitudinaux s'appliquant directement l'un contre l'autre
de bandes voisines en forme de lamelles, l'un des côtés est réalisé sous la forme
d'une nervure creuse, tandis que l'autre côté correspondant est bombé.
6. Fermeture en forme de couvercle selon la revendication 1 ou la revendication 2, caractérisée
en ce que les côtés longitudinaux s'appliquant directement l'un sur l'autre de bandes
(11) voisines en forme de lamelles, comportent un décrochement (14) en forme de gradins
et ce décrochement de bandes voisines en forme de lamelles se recouvre réciproquement
(figure 2).
7. Fermeture en forme de couvercle selon une des revendications 1 à 6, caractérisée en
ce que les bandes fabriquées en matière synthétique laissant passer la lumière et
ayant de préférence la transparence du verre, sont fabriquées selon un procédé de
moulage par injection.
8. Fermeture en forme de couvercle selon la revendication 1, caractérisé en ce que le
fil en matière synthétique (13) a une surface lisse, fermée, avec un faible coefficient
de frottement.
9. Fermeture en forme de couvercle selon la revendication 1, caractérisée en ce que le
fil en matière synthétique (13) a l'élasticité du caoutchouc.
10. Procédé pour la fabrication de la fermeture en forme de couvercle selon une des revendications
1 à 8, procédé caractérisé en ce que simultanément en une seule opération, plusieurs
bandes (11), distancées entre elles, placées dans un plan avec leurs côtés longitudinaux
voisins les uns des autres, sont moulées par injection dans un moule, dans lequel
les fils en matière synthétique (13) ont été mis en place avant l'introduction de
la matière synthétique, et ces fils en matière synthétique (13) ainsi mis en place
ont une surface fermée, lisse, de faible coefficient de frottement, et après l'ouverture
du moule et le démoulage des bandes (11), distancées les unes des autres et reliées
sur leurs bords par des fils en matière synthétique (13) qui y ont été réalisés, ces
bandes sont poussées les unes contre les autres en maintenant les fils de matière
synthétique (13) tendus, et la température de fusion du matériau des bandes (11) est
choisie différente de la température de fusion, tout au moins du matériau superficiel
des fils en matière synthétique (13), cette dernière étant plus élevée que celle du
matériau des bandes (11) (figure 4).
11. Procédé pour la fabrication de la fermeture en forme de couvercle selon une des revendications
1 à 8, procédé caractérisé en ce que simultanément dans une seule opération, plusieurs
bandes (11), distancées les unes des autres, placées dans un plan avec leurs côtés
longitudinaux voisins les uns des autres, sont moulées par injection dans un moule
dans lequel ont été placés sous précontraintes, avant l'introduction de la matière
synthétique, les fils en matière synthétique (13) ayant l'élasticité du caoutchouc,
et après l'ouverture du moule et le démoulage des bandes (11) distancées les unes
des autres et reliées sur leurs bords par les fils (13) précontraints, en matière
synthétique ayant l'élasticité du caoutchouc, les fils en matière synthétique (13)
sont relâchés grâce à quoi les bandes (11) initialement séparées les unes des autres
viennent s'appliquer les unes contre les autres par leurs côtés longitudinaux.
12. Procédé pour la fabrication de la fermeture en forme de couvercle selon une des revendications
1 à 8, procédé caractérisé en ce que simultanément, en une seule opération, plusieurs
bandes (11), distancées les unes des autres, et se trouvant dans un plan avec leurs
côtés longidudinaux voisins les uns des autres, sont moulées par injection dans un
moule (15) dans lequel les fils en matière synthétique (13) ont été mis en place avant
l'introduction de la matière synthétique, et après l'achèvement du processus d'injection
et après l'ouverture du moule et de démoulage des bandes (11), distancées les unes
des autres et reliées sur leurs bords par les fils en matière synthétique (13), qui
y ont été réalisés, les tronçons de fils en matière synthétique se trouvant entre
les bandes (11) voisines sont enroulés autour des tétons latéraux (12) pour raccourcir
les intervalles (A) existants entre les bandes voisines (figures 5, 6).
13. Procédé selon la revendication 12, caractérisé en ce que des gorges sont prévues sur
le téton (12) pour recevoir le tronçon du fil en matière synthétique (13) qui l'entoure.
14. Procédé selon une des revendications 11 ou 12, caractérisé en ce que la température
de fusion du matériau pour les bandes (11) est choisie différente de la température
de fusion, tout au moins du matériau superficiel du fil en matière synthétique (13),
cette dernière étant plus élevée que celle du matériau pour les bandes (11).
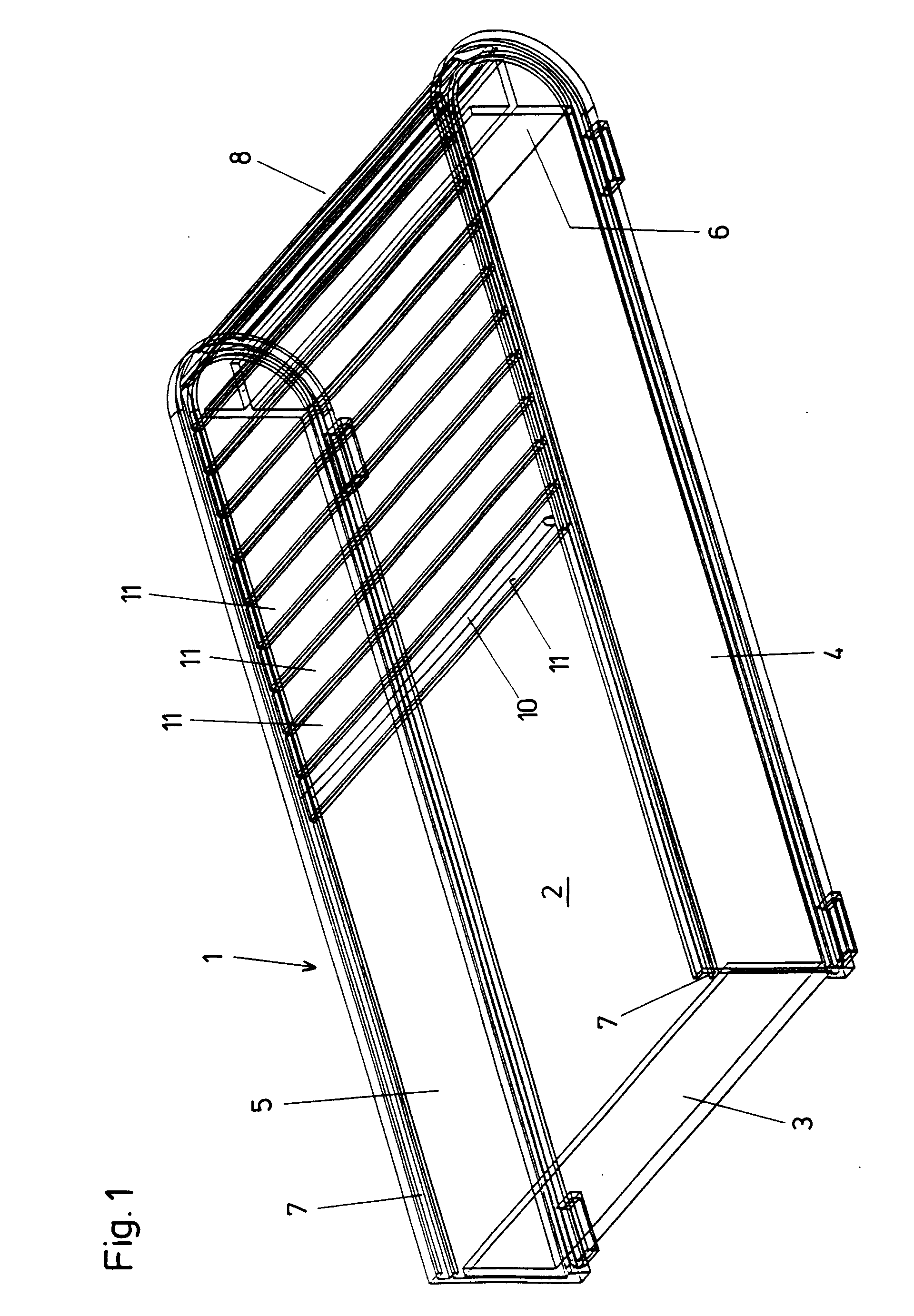
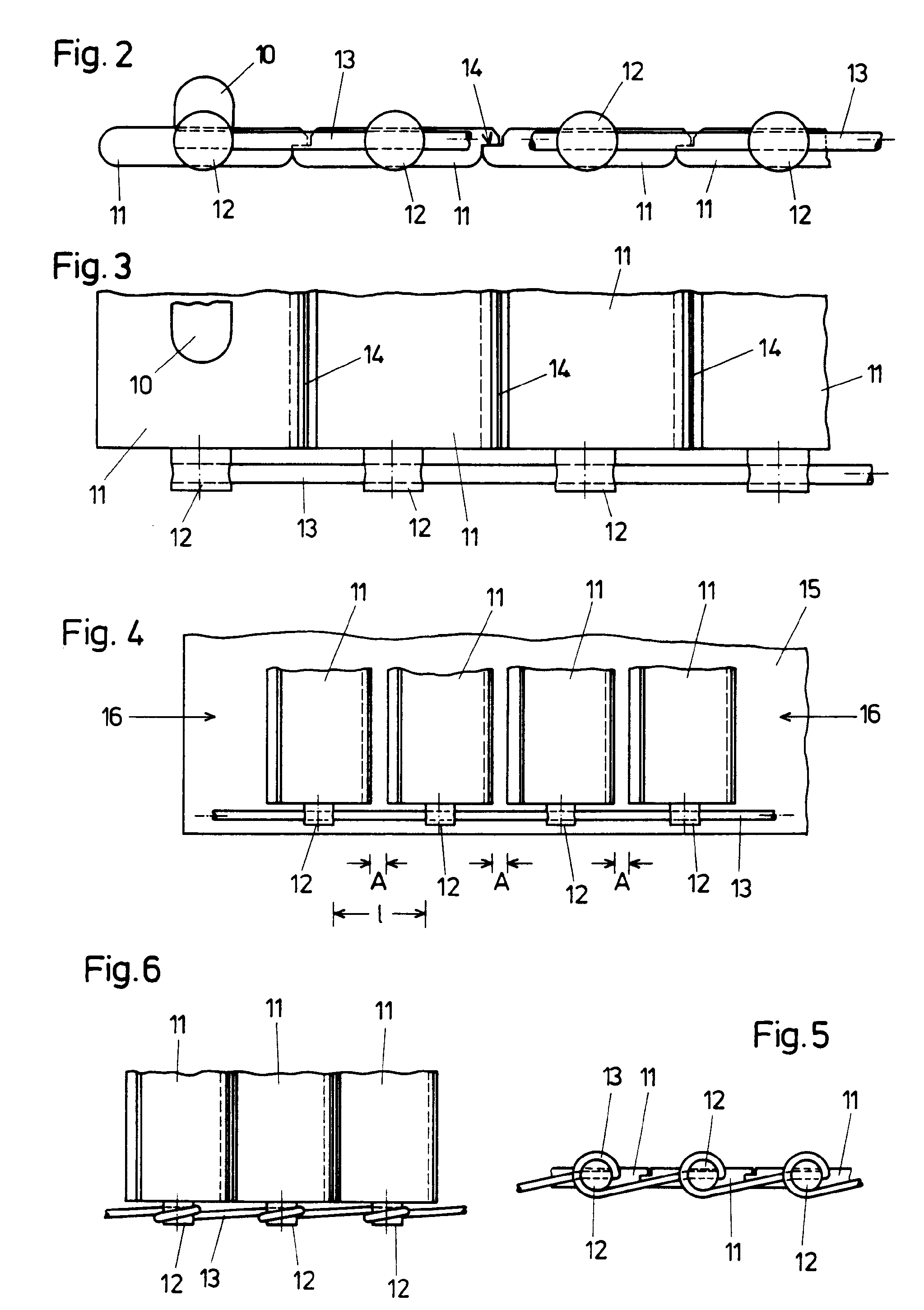