[0001] The present invention relates to a method for removing offensive odors from cork.
[0002] Cork has unique characteristics. It is lightweight and has a high degree of resilience.
Additionally, it has excellent gas and liquid sealing properties, and it is stable
against solvents such as alcohol. Furthermore, it is a hygienic material which is
food-safe and not harmful to human beings, and which has no intrinsic odor.
[0003] Due to the above mentioned characteristics, cork has been widely utilized as stoppers
for casings such as bottles filled with liquor such as wine, brandy or whiskey, or
casings packed with various kinds of foods.
[0004] However, despite having no intrinsic odor, offensive odor is encountered on cork
stoppers on rare occasions. This odor, when present, deteriorates the quality of the
contents of the bottles or casings sealed by the cork. Recently, by various studies,
2,4,6-trichloroanisol (TCA) has been identified as the substance which originates
the offensive odor. TCA is considered as the substance produced by moulds from 2,4,6-trichlorophenol
(TCP) which is utilized in agents conventionally used to spray cork oak. Also, in
"Journal of Agricultural and Food Chemistry", (1982) pages 359 to 362, it is presumed
that 2,4,6-trichlorophenol and other related chlorinated compounds originate from
the chlorination of liquid-related substantces during the chlorinate bleaching used
in the processing of cork and that these compounds are later extracted into the liquor,
such as wine. A similar consideration that the chlorinate agent is the source of the
odor substance has been given in "Science des Aliments" (1984), pages 81 to 93. In
the discussion, it has been pointed out that the 2,4,6-trichloroanisol is derived
from pentachlorophenol or other chrorinated pesticides applied to the tree. Further
it is considered that cork material and corks stored in premises with atmosphere polluted
by chloroanisoles may contaminate bottled wine aged in healthy cellars.
[0005] Methods for effective deodorization of cork have been studied, and the following
methods have been attempted.
(1)Dry-heating deodorization
[0006] Cork is heated and dried at 80 °C for 6 to 8 h, after which the offensive odor causing
substances are substantially evaporated. However, TCA is specifically adsorbed by
the macromolecular compounds which form cork such as cellulose, lignin and suberin,
and it is difficult to remove TCA in the dried state. The boiling point of TCA is
240 °C at 98.2 kPa (738.2 mmHg), and 132 °C at 3.7 kPa (28 mmHg). Therefore, in order
to evaporate TCA, a heating temperature must be applied which is higher than the boiling
point of TCA. However, it is difficult to raise the internal temperature of cork without
heating the surface excessively, which results in deterioration of the cork's desirable
characteristics. As such, heating is applied only to the surface of the cork, therefore
TCA in the interior cannot be removed entirely.
(2)Repetition heating deodorization
[0007] Cork is heated at 80 °C for 6 h, and is then left at room temperatures for about
a month. TCA can be removed by repeating this treatment many times. However, this
method requires long periods of treatment until the TCA is entirely removed. Therefore,
the production efficiency is low. (2 or 3 repetitions of the above treatment is insufficient
for entirely removing TCA).
(3)Citric acid deodorization
[0008] Cork is deodorized by being soaked in a 3 vol% solution of citric acid for 3 to 5
min. However, the effects of this deodorization technique are retained only for a
short period. That is, because cork resists the absorption of liquids, the citric
acid solution cannot reach the cork interior. Therefore, the deodorizing treatment
affects only the cork surface and untreated TCA within the cork is moved to the cork
surface with the lapse of time. Thus the offensive odor re-occurs.
(4)Oxidant bath deodorization
[0009] Cork is deodorized and sterilized by soaking it in a 1 vol% solution of hydroperoxide
(H₂O₂). However similar problems to those in the citric acid deodorization are caused.
(5)Alcohol steam deodorization
[0010] Cork is left and deodorized in an alcohol atmosphere at 18 to 24 °C for a month.
However, this method encounters the same problems as methods (3) and (4).
(6)Hot water washing
[0011] Cork in the grain state is washed in hot water at a temperature of 60 °C. The treatment
needs to be repeated 2 times. However, as TCA has a relatively strong affinity for
cork, it is moved to and retained in the internal portions of the cork. According
to this method, therefore, the deodorizing effect is still insufficient because the
treatment affects only the cork surface.
(7)Soxhlet extraction
[0012] TCA in the cork is extracted by a Soxhlet extractor at 45 °C for 24 hours with n-pentane.
By this method, TCA is entirely removed from both the surface and internal areas of
the cork. However, the equipment is very expensive and production costs become very
high. Furthermore, a certain degree of safety risk is encountered with this method.
(8)Dispersion
[0013] It has been considered to simply grind the cork into grains having a certain diameter,
and then forming it back into the desired form by pressing it with adhesives. However,
since TCA is merely dispersed in each grain, a high improvement cannot be expected
from this approach.
(9) Sterilization with Irradiation
[0014] "Deutsche Lebensmittel-Rundschau" (1984) Pages 204-207, is directed to the sterilization
with irradiation. Therein the mechanism of the formation of cork taint in wines is
discussed. There has been proposed to use an irradiation process for preventing microbial
conversion from TCP to TCA and thus achieving prevention of cork taint. However, this
method cannot remove TCA residing within the internal structure of the cork
(10) Sterilization with Ozone
[0015] DE-A-37 05 422 discusses that cork is sterilized with ozonized water or an ozonized
silicone emulsion, in which the ozonized concn. is 1 mg/ℓ at a temperature lower than
30°C.
[0016] However, this method encounters the same problems as methods (3) and (4).
[0017] It is therefore, the object of the present invention to provide a method for deodorizing
cork by removing substances causing offensive odors, principally TCA, from the cork
interior without deteriorating the cork's unique characteristics, and further to provide
an apparatus for carrying out this method.
[0018] According to the present invention this object is attained with a method for deodorizing
cork by removing a substance originating offensive odor from the cork comprising the
steps of:
supplying steam for generating a steam flow to said cork in a container with a temperature
of 100°C to 130°C and a pressure of at least 101.1 kPa (760 mmHg) to thereby cause
steam molecules to penetrate the internal structure of the cork thus promoting a steam
distillation within the internal structure of the cork, and
discharging the steam past the cork and containing the substance originating offensive
odor, from said container.
[0019] The substance originating offensive odors may be 2,4,6-trichloroanisole which may
be produced from 2,4,6-trichlorophenol or 2,4,6-trichlorphenol itself. It is preferred
that the method further comprises the steps of:
cutting the cork into pieces having a predetermined size,
pre-heating the cut cork to a certain temperature, and
maintaining the temperature and the pressure during deodorization.
[0020] In such case, the steam temperature is at least 100 °C; the system pressure is at
least 101.1 kPa (760 mmHg). In a preferred embodiment, the second step further comprises
supplying the steam for the cork from the bottom of the container. The second step
may further comprise agitating the container. In such case, the agitating step comprises
rotating and/or oscillating the container. The agitating step may also comprise stirring
the cork in the container.
[0021] The method may further comprise the step of cooling the cork in the container. The
cooling step may include the steps of:
maintaining the cork within the container and stopping the steam supply, thus causing
a natural cooling, generating a hot atmosphere, supplying the hot atmosphere to the
interior of the container after the cooling efficiency by the natural cooling has
been lowered.
[0022] Preferably, the container is maintained at a rotating and oscillating condition when
the hot atmosphere is supplied thereto.
[0023] According to a further aspect of the invention, there is provided an apparatus for
deodorizing cork by steam distillation comprising:
(a) a first means (1) for containing said cork,
(b) a second means (5) for supplying steam from a steam generator for forming a steam
flow from an inlet (22) to an outlet (26) of said first means (1),
(c) a third means (6) for discharging the steam along with a substance causing offensive
odor in the cork through said outlet (26) of said first means (1).
BRIEF DESCRIPTION OF THE DRAWINGS
[0024] The present invention will be understood more clearly from the preferred embodiments
described herebelow and from the appended drawings which illustrate the embodiments
of the present invention in detail.
[0025] In the drawings:
Fig. 1 is a block diagram showing a method for removing offensive odor substances
according to the present invention;
Fig. 2 is a sectional view of an apparatus for the deodorization of cork according
to the present invention;
Fig. 4 is a graph showing the relationship between the penetration of steam and the
temperature and pressure of the steam; and
Fig. 3 is a graph showing the relationship between the total amount of supplied steam
and the TCA removal ratio.
[0026] The present invention is accomplished by utilizing conventional steam distillation.
[0027] As is well known, cork has the water resistive property to prevent water molecules
from penetrating into the internal structure thereof. Therefore, though it is known
that TCA on the cork surface can be washed out by water, internally contained TCA
cannot be removed by water. To this point, it has been known that TCA has a characteristic
which is that it can be volatilized with steam. Additionally, it has a relatively
low boiling point at 3.7 kPa (28 mmHg). Therefore, if the treating temperatures are
controlled to the level at which the partial pressure of TCA becomes 3.7 kPa (28 mmHg),
TCA can be evaporated at relatively low temperatures. Taking the factors mentioned
above into consideration, the inventors became aware that steam distillation may be
effectively utilized for the deodorization of cork. Previously, steam distillation
had never been applied for cork deodorization. In various attempts made by the inventors,
it has become apparent to the inventors that the steam temperature and pressure is
a very important factor for enabling steam distillation. Particularly, according to
the invention, the steam can penerate into the internal structure of the cork for
heating the internal structure so that steam distillation is caused within the internal
structure for removing TCA residing in the inside of the cork.
[0028] It is considered that molecules of steam can be excited so as to increase their mobility
under a given temperature. Such increased mobility of steam molecules enables them
to successfully penetrate into the internal structure of the cork. The steam molecule
penetrating into the internal structure of the cork heat the inside of the cork to
the temperature at which steam distillation is internally caused. By this, TCA contained
in the internal structure of the cork can be evaporated.
[0029] Any kind of cork may be used and it is not limited to the field of its use or by
its form. For example, cork for bottle capping, wine bottle stoppers or crown disks,
for architectural use, vibration proofing or heat insulator materials may all benefit
from the treatment according to the present invention.
[0030] The shape of the first means is not specifically limited, but for effective steam
utilization, a longitudinal shape the container of which is formed with a diameter
smaller than its height is most preferred.
[0031] Any state of the cork is acceptable, but for enhancing the removal efficiency by
homogenizing steam and cork, maintaining the cork in an agitated state while supplying
steam to the first means is preferable. For agitating, moving the container per se
(e.g., oscillating or rolling) or to locating an agitating means in the container
of the first means to stir the inner materials are both acceptable.
[0032] According to the present invention the steam temperature is at least 100°C and the
pressure of the container is at least 101 kPa (760 mmHg). When the steam temperature
is lower than 100°C, the partial pressure is not high enough to cause steam distillation
within the internal organization of the cork. Also at a pressure lower than 101.1
kPa, the penetration of steam molecules into the internal structure of the cork may
not be sufficient. On the other hand, when the steam temperature is higher than 130°C,
it becomes difficult to control the temperature during the cooling process. That is,
at a high steam temperature, a significant amount of steam can penetrate the internal
structure. The steam penetrating the internal structure of the cork may lead to a
shrinkage of the cork when it is subjected to an atmospheric temperature which may
result in rapid cooling. A significant magnitude of shrinkage of the cork may degradate
the properties of the cork. Therefore, the temperature has to be maintained to be
lower than or equal to 130°C.
[0033] The cork size is not limited specifically, but a smaller size is preferred because
the TCA movement from within the cork to its surface becomes easier. This results
in an effective removal of TCA.
[0034] It should be appreciated that the specific treatment temperature, the specific system
pressure, the container configuration, the cork amount to be treated and other conditions
for the steam distillation treatment can be selected according to the required efficiency
and degree of removal of TCA.
[0035] According to the above identified steam distillation, the partial pressure of the
TCA can be reduced by the partial pressure of the steam, and the boiling point of
TCA can be lowered to about atmospheric pressure. Therefore, the deterioration of
the cork can be avoided and the deodorization of the cork (removal of TCA) can be
accomplished sufficiently.
[0036] The method for removing offensive odor in the cork according to the present invention
is described in detail referring to the appended Figures which show the processing
system for TCA removal.
[0037] Referring now to Fig. 1, a block diagram showing the method for removing offensive
odor according to the present invention is shown. A given amount of cork 2 cut to
a predetermined size is put into a treating container 1. Purified water provided from
a purified water generator 4 is supplied to a steam generator 3. Then, after steam
is generated in the generator 3, it is supplied to the container 1 via a steam supply
pipe 5. Steam distillation of the cork 2 is performed in the container 1, then steam
is discharged from the container 1 through a steam discharge pipe 6 out of the system.
Steam feeding is controlled by a supply valve 7, a flow meter 8, pressure meters 9,
and 10, a discharge valve 11, and a flow control valve 12. Temperature sensors 13,
14 and 15 are installed in the upper, middle and lower ports of container 1, respectively.
The temperature in the container 1 is monitored through these sensors by a monitor
system 16, then temperature is controlled at the constant predetermined level.
[0038] The container 1 has an outer container 17 and an inner container 18 spaced from the
outer container 17 at a constant interval as shown in Fig. 2. It may be formed as
a cylinder. In this way, the container 1 is formed as a pressure proof container having
a double-walled structure. This structure enables steam to be introduced into the
space between the outer and the inner wall after it goes through the cork 2. Therefore,
steam in the space through which the steam past the cork flows, serves for maintaining
the container temperature at the desired treatment temperature and thus for reducing
the heat loss in the steam
Referring now to Fig. 2, when amounts of cork 2 are put into the inner container
18 by opening a lid 19, they pile on a bottom plate 20. Steam is sprayed into the
interior of the container 1 through a plurality of steam pores 21 penetrating the
bottom plate 20, and runs through the piled cork 2 from bottom to top.
[0039] A steam inlet pipe 22 is connected to the center port of the container's bottom and
extends from the lower end of the outer container 17 of the container 1 to the outside
of the container. The lower edge of the inlet pipe 22 is connected to the steam supply
pipe 5 via a first rotary joint 23. Steam fluid supplied from the supply pipe 5 is
supplied to the inlet pipe 22, to the inner container 18 via the steam spraying pores
21 in the bottom plate 20 of the container 1. Then, steam supplied into the inner
container 18 rises through the cork 2 concurrently heating it, and is discharged from
steam discharging pores 24 which penetrate the upper side wall(s) of the inner container
18 into the space 25 between the outer container 17 and the inner container 18, an
outlet pipe 26 coaxially arranged surrounding the outside of the steam inlet pipe
22. Then it is discharged from the steam discharge pipe 6 connected to the outlet
pipe 26 via a second rotary joint 27. Pressure and flow of steam can be controlled
at a constant level by the discharge valve 11 and the flow control valve 12.
[0040] In order to homogenize sprayed steam and the cork 2, agitating the material in the
container 1 is effective. A central shaft 28 for rotation is located surrounding the
outlet pipe 26, and is rotatably supported by a bottom portion 30a of an oscillating
frame 30 formed in U-shape via a bearing 29. The container 1 can be rotated against
the central shaft by a rotation drive device 31 installed on the bottom portion 30a
of the oscillating frame 30 composed of a motor, rotation gear, translation gear or
so forth. Additionally, the container 1 can be oscillated by the oscillating frame
30. Then, by rotating with oscillation, the cork 2 and steam in the container 1 can
be agitated sufficiently. A pair of supporting shafts 32, and 33 are installed to
an outer surface of an upper end of side portions 30b of the oscillating frame 30.
These shafts 32, 33 are oscillatably supported by a pair of fixed frames 36, 37 via
bearings 34, 35 to be oscillated by an oscillation drive device 38.
[0041] The oscillation drive device 38 is composed of a worm wheel 39 installed on the supporting
shaft 33 and a motor 42 which rotatably operates a worm gear 40 via belt 41, where
the worm gear 40 is engaged to gear teeth of the worm wheel 39. When the motor 42
is rotated in one direction the worm gear 40 and the worm wheel 39 are rotated in
the same direction. This rotation slowly oscillates the oscillating frame 30 in one
direction. On the other hand, when the motor 42 is rotated in the other direction,
it slowly rotates the oscillating frame 30 in the other direction. In this way, the
oscillating frame 30 is oscillated.
[0042] In order to supply steam regardless of the oscillation of the oscillating frame 30,
the steam supply pipe 5 is located through the center portion of the supporting shaft
33, connected to the oscillating frame 30 via a third rotary joint 43, and further
connected to the container 1 via the first rotary joint 23. The steam discharge pipe
6 is located through the center portion of the other supporting shaft 32, connected
to the oscillating frame 30 via a forth rotary joint 44, and further connected to
the container 1 via the second rotary joint 27.
[0043] A slip ring 45 is mounted on the edge of the central shaft 28 of the container 1.
Signals, obtained from temperature sensors 13, 14 and 15, connected to the outside
portion of the oscillating frame 30 via the slip ring 45, are input to a monitoring
device 16 which is connected to the slip ring 45 (as shown in Fig. 1) allowing the
temperature in the container to be effectively monitored.
[0044] Circular frames 46 are mounted on the top of the side portion 30b of the oscillating
frame 30. Rollers 47 are installed in the inner surface of the radial frames 46 to
rotate the container 1 smoothly by supporting the outer surface of the upper port
of the container 1.
[0045] In the shown embodiment, the rotation speed of the container is preferably determined
as, at least, 10 rpm, and the incline angle is preferably determined as at least ±
60°, though they depend on conditions such as the processing amount and the cork size.
The inclination angle range of the container is not strictly limited to ± 60° but
can be selected in any way. In general, the inclination angle of the container may
be determined according to the degree of filling of the cork within the interior space
of the container. Namely, the inclination angle is selected so that the cork can be
distributed over the entire area of the steam path so that the steam cannot escape
without contacting the cork. Similarly, in the case of rolling or agitation, care
should be taken not to cause a blow off of the steam. Therefore, the driving speed
in rolling and agitation may be determined according to the amount of the cork filled
in the container.
[0046] Further to say, there is no problem processing by steam distillation in a stationary
environment (not rotated or oscillated).
[0047] In order to avoid physically changing the cork, for example, shrinking, it may be
preferable to cool the cork slowly with maintaining the same within the container
1 cork volume becomes smaller (shrunken) when it is subjected to a substantially low
temperature after the penetration of steam having a relatively high temperature. Particularly,
since the temperature of the internal structure of cork cannot be cooled like that
on the surface, a relatively long period is required for satisfactorily cooling the
internal structure of the cork This means that if cork is immediately removed from
the container to subject it to the atmosphere, a substantial magnitude of shrinkage
may be caused in the cork to make it stiff and to degrade the cork properties. On
the other hand, allowing natural cooling takes a very long time. Therefore, supplying
a hot atmosphere to the container by way of cooling may be effective. Here, rotation
and oscillation of the container 1 are continued while cooling. During natural cooling,
it has been observed that the cooling efficiency is significantly dropped at a certain
temperature. In order to accelerate cooling, the hot atmosphere is generated in a
hot atmosphere generator (not shown in the Figures), and is supplied to the container
1 by controlling the valve 7 located on the steam inlet side. As the cork 2 is wetted
by steam, the hot atmosphere supplied to the container 1 can take latent heat from
the surface of the cork 2 when steam is evaporated. This increases the cooling speed.
The results of cooling tests on cork are shown in the following Table 1.
Table 1
Repetition |
1 |
2 |
3 |
4 |
5 |
Cooling periods(min) |
47 |
48 |
47 |
50 |
46 |
Volume ratio(%) |
111.4 |
98.0 |
95.0 |
96.4 |
104.7 |

Materials are shrunken when this value becomes over 100.
[0048] Treatment indicates steam distillation.
Test conditions
[0049]
- Flow amount of steam :
- 280 l/h
- Period of treatment :
- 64 min
- Pressure (cage pressure):
- 1 kg/cm²
[0050] As shown in Table 1, shrinking of the cork was prevented.
EXAMPLE 1
[0051] In order to demonstrate the advantages accomplished by the present invention, experiments
were performed. In the experiments, natural cork of the size 10 cm x 10 cm x 5 cm
was heated in an autoclave for 60 min at respective temperatures of 100 °C, 110 °C,
120 °C and 130 °C. The pressures at the respective temperatures are shown in the following
Table 2.
TABLE 2
Temperature (°C) |
Pressure (kg/cm²) |
100 |
1.033 |
110 |
1.461 |
120 |
2.055 |
130 |
2.754 |
For checking the depth or the degree of penetration of steam into the internal structure
of the cork, the cork piece samples were cut by a knife and the dimension from the
cork surface was measured. The result of the measurement is shown in the following
Table 3 and Fig. 3.
Table 3
Temperature (°C) |
Penetration Magnitude (mm) |
100 |
0.5 |
110 |
5.0 |
120 |
10.0 |
130 |
20.0 |
[0052] As can be seen from the foregoing Table 3 and Fig. 4, the penetration degree is exponentially
increased according to rising of the steam temperature.
EXAMPLE 2
[0053] Cork capping plug recognized as corked was crushed by a known cork crushing machine
into a grain size ordinarily used for forming compressed cork, for forming sample
cork pieces. 4g of the sample cork pieces were put in a gauze bag (15 cm x 20 cm).
The sample cork containing bag was put in the mid portion of the cork burden in the
container 1. The deodorization treatment was performed utilizing the apparatus of
Fig. 2. In the treatment, the container 1 was rolled with sccessive variations of
the inclination angle. The steam was flown through the container 1 across the cork
in a flow rate of 20 l/h and 40 l/h. The deodorization treatment was performed for
30 min, 60 min and 90 min after reaching a predetermined condition, i.e. the temperature
in the container was 120 °C and the pressure was 1 kg/cm². After the treatment, the
residual TCA amount was checked. The check of residual TCA was performed by slicing
the sample cork, extracting the TCA from slices by n-pentane, and measurement by gascromatograph.
The result of measurement is shown in Table 4 and Fig. 3.
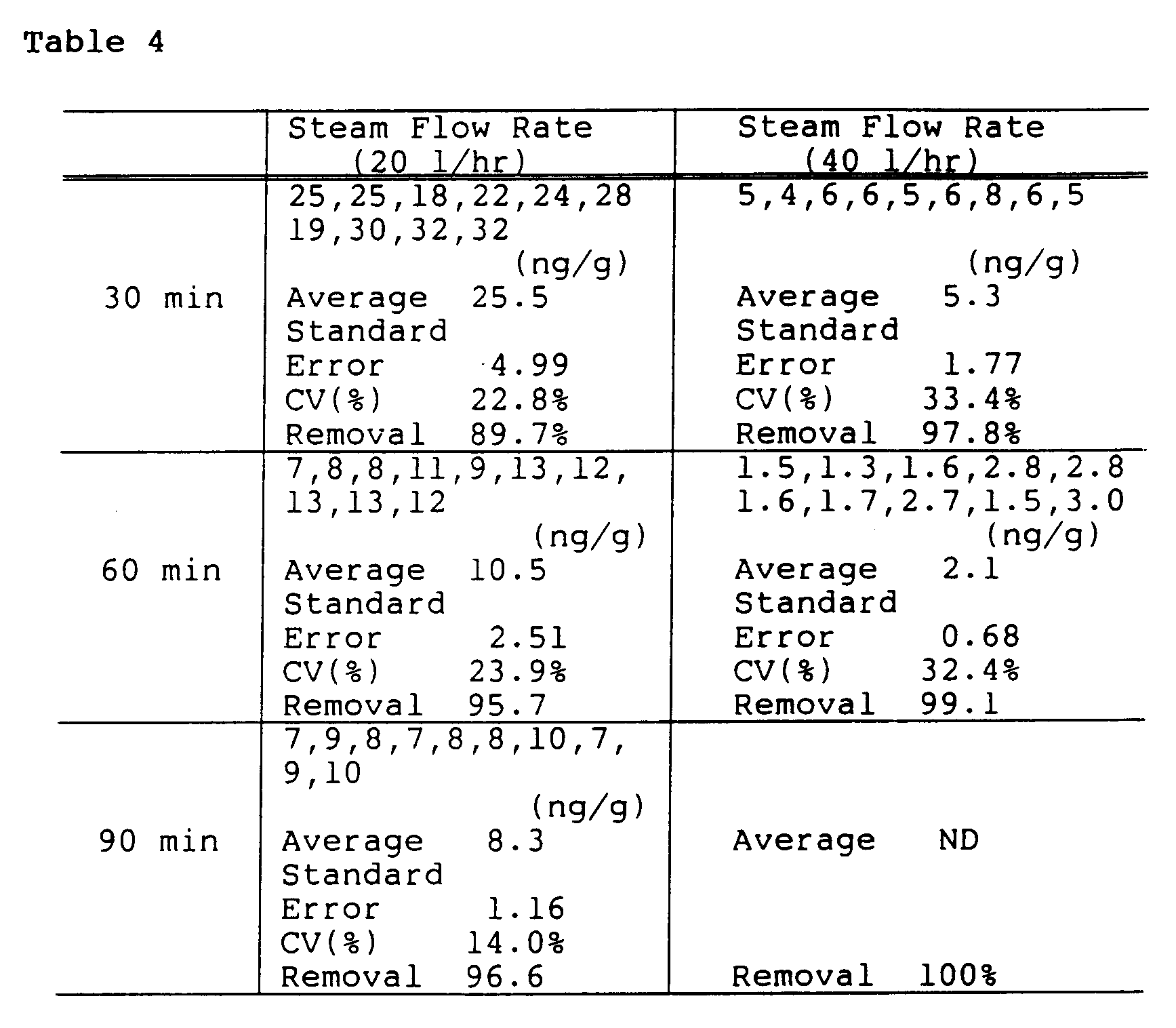
1. A method for deodorizing cork by removing a substance originating offensive odor from
the cork comprising the steps of:
supplying steam for generating a steam flow to said cork in a container with a temperature
of 100°C to 130°C and a pressure of at least 101.1 kPa (760 mmHg) to thereby cause
steam molecules to penetrate the internal structure of the cork thus promoting a steam
distillation within the internal structure of the cork, and
discharging the steam past the cork and containing the substance originating offensive
odor, from said container.
2. The method as set forth in claim 1, wherein said substance originating offensive odor
is 2,4,6-trichloroanisole.
3. The method as set forth in claim 1, wherein said substance originating offensive odor
is 2,4,6-trichlorophenol.
4. The method as set forth in claim 1, which further comprises the steps of:
cutting said cork into pieces having a predetermined size, and
pre-heating said cut cork to a temperature for deodorization treatment.
5. The method as set forth in claim 1, wherein said temperature and said pressure are
maintained during the deodorization.
6. The method as set forth in claim 1 or 4, wherein the container is agitated while supplying
the steam.
7. The method as set forth in claim 6, wherein said agitation comprises rotating and/or
oscillating said container.
8. The method as set forth in claim 6, wherein said agitation comprises stirring said
cork in said container.
9. The method as set forth in claim 1 or 4, which further comprises the step of cooling
said cork in said container.
10. The method as set forth in claim 9, wherein said cooling step comprises the steps
of:
maintaining said cork within said container after the deodorization treatment and
stopping the steam supply thus subjecting the cork to natural cooling,
generating a hot atmosphere, and
supplying said hot atmosphere to the interior of said container after the cooling
efficiency by natural cooling has decreased.
11. An apparatus for deodorizing cork by steam distillation comprising:
(a) a first means (1) for containing said cork,
(b) a second means (5) for supplying steam from a steam generator for forming a steam
flow from an inlet (22) to an outlet (26) of said first means (1),
(c) a third means (6) for discharging the steam along with a substance causing offensive
odor in the cork through said outlet (26) of said first means (1).
12. The apparatus as set forth in claim 11, wherein said first means (1) is formed in
a longitudinal shape along with the direction of steam feeding.
13. The apparatus as set forth in claim 11, wherein a means for agitating said first means
(1) is further provided.
14. The apparatus as set forth in claim 13, wherein said agitating means comprises means
for rotation (28) and/or oscillation (30) of said first means (1).
15. The apparatus as set forth in claim 13, wherein said agitating means is located in
said first means (1) and comprises a means for stirring said cork in said first means
(1).
16. The apparatus as set forth in claim 11, wherein a means for cooling said cork in said
first means (1) is further provided.
17. The apparatus as set forth in claim 16, wherein said cooling means is composed of
a means for generating a hot atmosphere, and a means for supplying said hot atmosphere
to the interior of said first means (1) while rotation and oscillation of said first
means (1) are maintained.
1. Verfahren zum Desodorieren von Kork durch Entfernen einer Substanz, welche einen unangenehmen
Geruch verursacht, aus dem Kork, welches die Schritte umfaßt:
Bereitstellen von Dampf zum Erzeugen eines Dampfflusses zu dem Kork in einem Behälter
mit einer Temperatur von 100°C bis 130°C und einem Druck von mindestens 101,1 kPa
(760 mmHg), um dadurch Dampfmoleküle dazu zu bringen, in die innere Struktur des Korks
einzudringen, wodurch eine Dampfdestillation in der inneren Struktur des Korks gefördert
wird, und
Austragen des Dampfs nach dem Kork, welcher die Substanz enthält, welche einen unangenehmen
Geruch verursacht, aus dem Behälter.
2. Verfahren nach Anspruch 1, worin die Substanz, welche einen unangenehmen Geruch verursacht,
2,4,6-Trichloranisol ist.
3. Verfahren nach Anspruch 1, worin die Substanz, welche einen unangenehmen Geruch verursacht,
2,4,6-Trichlorphenol ist.
4. Verfahren nach Anspruch 1, welches ferner die Schritte umfaßt:
Schneiden des Korks in Stücke mit einer vorbestimmten Größe, und
Vorwärmen des geschnittenen Korks auf eine Temperatur zur Desodorierungsbehandlung.
5. Verfahren nach Anspruch 1, worin die Temperatur und der Druck während der Desodorierung
aufrechterhalten werden.
6. Verfahren nach Anspruch 1 oder 4, worin der Behälter in Bewegung gehalten wird, während
der Dampf zugeführt wird.
7. Verfahren nach Anspruch 6, worin das In-Bewegung-Halten das Drehen und/oder Schwenken
des Behälters umfaßt.
8. Verfahren nach Anspruch 6, worin das In-Bewegung-Halten das Rühren des Korks in dem
Behälter umfaßt.
9. Verfahren nach Anspruch 1 oder 4, welches ferner den Schritt des Kühlens des Korks
in dem Behälter umfaßt.
10. Verfahren nach Anspruch 9, worin der Kühlungsschritt die Schritte umfaßt:
Halten des Korks in dem Behälter nach der Desodorierungsbehandlung und Abstellen der
Dampfzufuhr, womit der Kork einer natürlichen Abkühlung ausgesetzt ist,
Erzeugen einer heißen Atmosphäre, und
Zuführen der heißen Atmosphäre in das Innere des Behälters, nachdem die Kühlungswirkung
durch natürliches Abkühlen abgenommen hat.
11. Vorrichtung zum Desodorieren von Kork durch Dampfdestillation umfassend:
(a) ein erstes Mittel (1) zum Enthalten des Korks,
(b) ein zweites Mittel (5) zum Zuführen von Dampf aus einem Dampferzeuger zum Bilden
eines Dampfflusses von einem Einlaß (22) zu einem Auslaß (26) des ersten Mittels (1),
(c) ein drittes Mittel (6) zum Austragen des Dampfs zusammen mit einer Substanz, welche
einen unangenehmen Geruch in dem Kork verursacht, durch den Auslaß (26) des ersten
Mittels (1).
12. Vorrichtung nach Anspruch 11, worin das erste Mittel (1) in einer länglichen Form
entlang der Richtung der Dampfzufuhr ausgebildet ist.
13. Vorrichtung nach Anspruch 11, worin ferner ein Mittel zum In-Bewegung-Halten des ersten
Mittels (1) bereitgestellt wird.
14. Vorrichtung nach Anspruch 13, worin das Mittel zum In-Bewegung-Halten Mittel zum Drehen
(28) und/oder Schwenken (30) des ersten Mittels (1) umfaßt.
15. Vorrichtung nach Anspruch 13, worin das Mittel zum In-Bewegung-Halten in dem ersten
Mittel (1) sich befindet und ein Mittel zum Rühren des Korks in dem ersten Mittel
(1) umfaßt.
16. Vorrichtung nach Anspruch 11, worin ferner ein Mittel zum Abkühlen des Korks in dem
ersten Mittel (1) bereitgestellt wird.
17. Vorrichtung nach Anspruch 16, worin das Abkühlungsmittel zusammengesetzt ist aus einem
Mittel zum Erzeugen einer heißen Atmosphäre und einem Mittel zum Zuführen der heißen
Atmosphäre in das Innere des ersten Mittels (1), wobei das Drehen und Schwenken des
ersten Mittels (1) aufrechterhalten werden.
1. Procédé pour la désodorisation du liège par l'élimination, du liège, d'une substance
produisant une odeur gênante, comprenant les étapes de :
fournir de la vapeur pour produire un écoulement de vapeur vers ledit liège dans
un conteneur à une température de 100°C à 130°C et à une pression d'au moins 101,1
kPa (760 mmHg) pour ainsi forcer les molécules de vapeur a pénétrer dans la structure
interne du liège et ainsi favoriser une distillation à la vapeur dans la structure
interne du liège et
évacuer la vapeur ayant passé par le liège et contenant la substance produisant
une odeur désagréable, dudit conteneur.
2. Procédé selon la revendication 1 , où ladite substance produisant une odeur désagréable
est le 2,4,6-trichloroanisole.
3. Procédé selon la revendication 1, où ladite substance produisant une odeur désagréable
est le 2,4,6-trichlorophénol.
4. Procédé selon la revendication 1, qui comprend de plus les étapes de :
découper ledit liège en morceaux d'une grandeur prédéterminée et
préchauffer ledit liège découpé à une température pour son traitement de désodorisation.
5. Procédé selon la revendication 1, où ladite température et ladite pression sont maintenues
pendant la désodorisation.
6. Procédé selon la revendication 1 ou 4, où le conteneur est soumis à agitation tout
en lui fournissant de la vapeur.
7. Procédé selon la revendication 6, où ladite agitation consiste à faire tourner et/ou
osciller ledit conteneur.
8. Procédé selon la revendication 6, où ladite agitation consiste à soumettre ledit liège
à agitation dans ledit conteneur.
9. Procédé selon l'une quelconque des revendications 1 ou 4, qui comprend de plus l'étape
de refroidir ledit liège dans ledit conteneur.
10. Procédé selon la revendication 9, où ladite étape de refroidissement comprend les
étapes de :
maintenir ledit liège dans ledit conteneur après le traitement de désodorisation
et arrêter la fourniture de vapeur pour ainsi soumettre le liège à un refroidissement
naturel,
produire une atmosphère chaude et
fournir ladite atmosphère chaude à l'intérieur dudit conteneur après diminution
de l'efficacité de refroidissement par refroidissement naturel.
11. Dispositif pour désodoriser le liège par distillation à la vapeur comprenant :
(a) un premier moyen (1) pour contenir ledit liège,
(b) un second moyen (5) pour fournir de la vapeur d'un générateur de vapeur afin de
former un écoulement de vapeur d'une entrée (22) à une sortie (26) dudit premier moyen
(1),
(c) un troisième moyen (6) pour évacuer la vapeur en même temps qu'une substance provoquant
une odeur désagréable dans le liège par ladite sortie (26) dudit premier moyen (1).
12. Dispositif selon la revendication 11, où ledit premier moyen (1) est de forme longitudinale
dans la direction de l'alimentation en vapeur.
13. Dispositif selon la revendication 11, où un moyen pour agiter ledit premier moyen
(1) est de plus prévu.
14. Dispositif selon la revendication 13, où ledit moyen d'agitation comprend un moyen
pour faire tourner (28) et/ou osciller (30) ledit premier moyen (1).
15. Dispositif selon la revendication 13, où ledit moyen d'agitation est placé dans ledit
premier moyen (1) et comprend un moyen pour soumettre ledit liège à agitation dans
ledit premier moyen (1).
16. Dispositif selon la revendication 11, où un moyen pour refroidir ledit liège dans
ledit premier moyen (1) est de plus prévu.
17. Dispositif selon la revendication 16, où ledit moyen de refroidissement se compose
d'un moyen pour produire une atmosphère chaude et d'un moyen pour fournir ladite atmosphère
chaude à l'intérieur dudit premier moyen (1), tout en maintenant la rotation et l'oscillation
dudit premier moyen (1).