[0001] The present invention relates to a magnetic material useful for permanent magnet,
bond magnet or other material.
[0002] As high performance rare earth permanent magnets, hitherto, Sm-Co system magnet and
Nd-Fe-B system magnet are known, and their mass production is promoted. These magnets
contain Fe and Co at high rates, and they contribute to increase of saturation magnetization.
These magnets also contain rare earth elements such as Nd and Sm, and the rare earth
elements bring about a very large magnetic anisotropy derived from the behavior of
4f electrons in the crystal field. As a result, the coercive force is increased, and
a magnet of high performance is realized. Such high performance magnets are mainly
used in electric appliances such as loudspeaker, motor and instrument.
[0003] Recently, on the other hand, intermetallic compound having ThMn₁₂ crystal structure
is noticed. This compound is small in the stoichiometric composition of rare earth
elements with respect to 3d transition elements, as compared with that of intermetallic
compounds belonging to Sm-Co magnet and Nd-Fe-B magnet such as Sm₂Co₁₇ and Nd₂Fe₁₄B,
and contains large amount of 3d transition elements. It is therefore possible to realize
a large saturation magnetization and high maximum energy product. Besides, this compound
is small in the composition ratio of expensive rare earth element and may be manufactured
at a low cost.
[0004] However, in the permanent magnet material composed iron-rich intermetallic compound
is produced large amount of impurity phase mainly of α-Fe. Therefore, the permanent
magnet is deteriorated the magnetic characteristic.
[0005] Besides, a magnetic material having a composition of introducing the intersticial
elements such as N, C, P in the crystal lattice of the principal phase has been developed.
This magnetic material is notably improved in the Curie temperature of the principal
phase, saturation magnetization and magnetic anisotropy.
[0006] In the existing magnetic material introducing the intersticial elements in the principal
phase, nevertheless, the thermal stability of the principal phase is poor, and, for
example, R₂Fe₁₇ nitrogen compound begins to decompose into α-Fe and rare earth nitride
(RN) at 600°C. RFe₁₁Ti₁ nitride having ThMn₁₂ structure begins to decompose at 450°C.
Therefore, it is very difficult to form an intersticial element containing compound
while suppressing the decomposition thereof, and a dense magnet cannot be formed by
hot pressing or sintering heating higher than the decomposition temperature of the
magnetic material.
[0007] It is an object of the present invention to provide a magnetic material which suppresses
formation of impurity phase of Fe, Co or Fe-Co alloy, possesses a stable ThMn₁₂ crystal
structure as the principal phase, and is excellent in magnetic properties and lowered
in cost.
[0008] It is other object of the present invention to provide a magnetic material which
suppresses formation of impurity phase of Fe, Co or Fe-Co alloy, possesses a ThMn₁₂
crystal structure introducing an intersticial element as the principal phase, and
is excellent in magnetic properties, enhanced in the thermal stability of the ThMn₁₂
crystal structure, improved in magnetic properties such as Curie temperature, and
lowered in cost.
[0009] It is another object of the present invention to provide a magnetic material which
suppresses formation of impurity phase of Fe, Co or Fe-Co alloy, possesses a stable
TbCu₇ crystal structure as the principal phase, and is excellent in magnetic properties
and lowered in cost.
[0010] It is a different object of the present invention to provide a magnetic material
Which suppresses formation of impurity phase of Fe, Co or Fe-Co alloy, possesses a
TbCu₇ crystal structure introducing an intersticial element as the principal phase,
and is excellent in magnetic properties, enhanced in the thermal structure of the
TbCu₇ crystal structure, improved in magnetic properties such as Curie temperature,
and lowered in cost.
[0011] To achieve the above objects, the present invention provides a magnetic material
which is expressed in a general formula:

where R1 is at least one element selected from Zr and Hf, R2 is at least one element
selected from rare earth element, M is at least one element selected from C, N and
P, T is at least one element selected from Fe and Co, x + y + z + u + v = 100, x,
y, z, u, v are atomic percent individually defined as 0.1 ≦ x ≦ 20, 2 ≦ y ≦ 20, 0.5
≦ z ≦ 20, 0 ≦ u ≦ 20, v ≧ 50), and
of which principal phase possesses a ThMn₁₂ crystal structure.
[0012] More specifically, the present invention provides a magnetic material which is expressed
in a general formula:
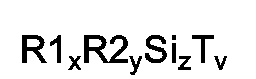
where R1 is at least one element selected from Zr and Hf, R2 is at least one element
selected from rare earth element, T is at least one element selected from Fe and Co,
x + y + z + u + v = 100, x, y, z, v are atomic percent individually defined as 0.1
≦ x ≦ 20, 2 ≦ y ≦ 20, 0.5 ≦ z ≦ 20, v ≧ 50, and of which principal phase possesses
a ThMn₁₂ crystal structure, and a magnetic material which is expressed in a general
formula:
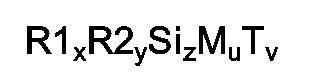
where R1 is at least one element selected from Zr and Hf, R2 is at least one element
selected from rare earth element, M is at least one element selected from C, N and
P, T is at least one element selected from Fe and Co, x + y + z + u + v = 100, x,
y, z, u, v are atomic percent individually defined as 0.1 ≦ x ≦ 20, 2 ≦ y ≦ 20, 0.5
≦ z ≦ 20, 0 < u, v ≧ 50, and of which principal phase possesses a ThMn₁₂ crystal structure.
[0013] The principal phase herein denotes the phase occupying the maximum volume out of
the crystal phases and noncrystal phases in the compound.
[0014] The components for composing the magnetic materials of the present invention are
described individually in detail below.
(1) Element R1
[0015] The element R1 is used Zr, Hf, or a mixture of Zr and Hf. Such element R1 occupies
the rare earth site of ThMn₁₂ crystal structure, and contributes to formation of this
structure excellent in phase stability. The element R1 serves to improve the thermal
stability of the compound if the element M (the intersticial element) is used as indespensable
component.
[0016] If the element R1 is less than 0.1% by atom, much α-Fe is formed, and large coercive
force is not obtained. If, on the other hand, the element R1 exceeds 20% by atom,
the content of the element T (Fe, Co) becomes relatively small, and the saturation
magnetization is extremely lowered. A more preferable content of the element R1 is
in a range of 0.5 to 6% by atom.
(2) Element R2
[0017] Rare earth element as the element R2 is La, Ce, Pr, Nd, Pm, Sm, Eu, Gd, Tb, Dy, Ho,
Er, Tm, Yb Lu, Y, which may be used either alone or in a mixture of two or more of
these elements. The element R2 is an independensable component for formation of ThMn₁₂
crystal structure, and contributes to magnetic anisotropy.
[0018] Among these rare earth elements, in particular, Sm is useful for enhancing the magnetic
properties. However, when the element M (an intersticial element) is added as an essential
component, at least one of Pr and Nd among the rare earth elements is useful for enhancing
the magnetic properties.
[0019] If the content of the element R2 is less than 2% by atom, it is difficult to form
the ThMn₁₂ crystal structure. If, on the other hand, the element R2 exceeds 20% by
atom, the content of the element T (Fe, Co) becomes relatively small, and the saturation
magnetization is extremely lowered. A more preferable content of element R2 is in
a range of 2 to 16% by atom.
[0020] Incidentally, the sum of the elements R1 and R2 is desired to be in a range of 4
to 20% by atom. By thus defining the total of the elements R1 and R2, it is possible
to obtain a magnetic material possessing both excellent magnetic anisotropy and high
coercive force. More preferably, the sum of the elements R1 and R2 is in a range of
6 to 16% by atom.
[0021] It is meanwhile allowed to replace a part of the element R2 by Ti. The replacing
amount of Ti is limited to an extent not to adversely affect the magnetic properties
of the magnetic material, for example, within 90% of the quantity of the element R1.
(3) Si
[0022] Si is an effective constituent element for forming a stable ThMn₁₂ phase. Si is also
extremely effective for enhancing the thermal stability of the ThMn₁₂ phase containing
the element M (the intersticial element).
[0023] The effect of Si is achieved by adding by 0.5% by atom or more, but when exceeding
20% by atom, the saturation magnetization is extremely lowered. A preferred content
of Si is in a range of 0.5 to 15% by atom.
(4) Element T
[0024] The element T is at least one selected from Fe and Co. The effect of the element
T is achieved when added by 50% by atom or more.
[0025] A part of the element T may be replaced by at least one type selected from Cr, V,
Mo, W, Mn, Ni, Ga, Al, so that the rate of the ThMn₁₂ phase to the whole compound
may be increased. However, if the element T is replaced too much by these elements,
the magnetic flux density is lowered, and the replacing portion may be preferred 20%
or less of the element T in percentage by atom.
(5) Element M
[0026] The element M is one or a mixture of at least two of C, N and P. By adding such element
M, principally locating at the interstitial position of the ThMn₁₂ crystal structure,
extending the crystal lattice as compared with the case not containing the element
M, and varying the energy band structure, the Curie temperature, saturation magnetization,
and magnetic anisotropy are enhanced.
[0027] If the content of element M exceeds 20% by atom, it is difficult to form ThMn₁₂ phase.
To achieve the effect of addition of the element M, the lower limit is preferably
set at 0.5% by atom.
[0028] The present invention also provides a magnetic material which is expressed in a general
formula:
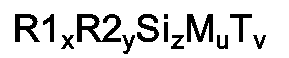
where R1 is at least one element selected from Zr and Hf, R2 is at least one element
selected from rare earth element, M is at least one element selected from C, N and
P, T is at least one element selected from Fe and Co, x + y + z + u + v = 100, x,
y, z, u, v are atomic percent individually defined as 0.1 ≦ x ≦ 20, 2 ≦ y ≦ 20, 0.5
≦ z ≦ 20, 0 ≦ u ≦ 20, v ≧ 50, and
of which principal phase possesses a TbCu₇ crystal structure.
[0029] More specifically, the present invention provides a magnetic material which is expressed
in a general formula:
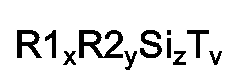
where R1 is at least one element selected from Zr and Hf, R2 is at least one element
selected from rare earth element, T is at least one element selected from Fe and Co,
x + y + z + v = 100, x, y, z, v are atomic percent individually defined as 0.1 ≦ x
≦ 20, 2 ≦ y ≦ 20, 0.5 ≦ z ≦ 20, v ≧ 50, and of which principal phase possesses a TbCu₇
crystal structure, and a magnetic material which is expressed in a general formula:

where R1 is at least one element selected from Zr and Hf, R2 is at least one element
selected from rare earth element, M is at least one element selected from C, N and
P, T is at least one element selected from Fe and Co, x + y + z + u + v = 100, x,
y, z, u, v are atomic percent individually defined as 0.1 ≦ x ≦ 20, 2 ≦ y ≦ 20, 0.5
≦ z ≦ 20, 0 < u, v ≧ 50, and of which principal phase possesses a TbCu₇ crystal structure.
[0030] The principal phase herein denotes the phase occupying the maximum volume out of
the crystal phases and noncrystal phases in the compound.
[0031] The components for composing the magnetic materials of the invention of which principal
phase possesses the TbCu₇ crystal structure are described in detail below.
[0032] The element R1 and the element R2 are added in expectation of the same actions as
mentioned above. As for the element R2, selection of Sm is useful for enhancing the
magnetic properties. However, when the element M (the intersticial element) is added
as an essential component, it is useful for enhancing the magnetic properties to use
at least one of Pr, Nd and Sm among the R2 elements.
[0033] Si is an effective element for forming a stable TbCu₇ phase. Si is also extremely
effective for enhancing the thermal stability of the TbCu₇ phase containing the element
M (the intersticial element). The content of such Si is limited owing to the same
reason as mentioned above.
[0034] The element T is one selected from Fe and Co, but a part of the element T may be
replaced at least one of Cr, V, Mo, W, Mn, Ni, Ga, Al.
[0035] The element M is principally located at the interstitial position of the TbCu₇ crystal
structure mainly, and its addition is limited owing to the same reason as above.
[0036] A manufacturing method of magnetic material of the present invention is described
below.
[0037] In the first place, an alloy powder is prepared in the following method.
(1) An alloy powder is prepared by using specified contents of the elements R1, R2,
Si, T, and adding the element M as required. In this case, the material powder is
melted by arc melting or induction melting, and cast to prepare an alloy in desired
composition, and the obtained alloy is crushed.
(2) The mixture of the elements R1, R2, Si, T, and also element M as required may
be alloyed by applying a mechanical energy, in the mechanical alloying method or mechanical
grinding method. These methods are the procedure for alloying by solid-phase reaction
of the mixture of powder or ingot containing the elements R1, R2, Si, T. Practical
methods for inducing the solid-phase reaction includes the method of applying a mechanical
impact to the powder by charging the material mixture into the planet ball mill, rotary
ball mill, attriter, vibration ball mill, screw ball mill or the like. By these methods,
the material powder is crushed to thin pieces, and different atoms diffuse mutually
on the mutually contacting positions of the thin pieces, so that the material mixture
is homogeneously unified.
(3) The alloy powder in the desired composition is prepared by liquid quenching method.
[0038] According to the results of experiment conducted by the present inventors, the ThMn₁₂
phase is likely to become the principal phase in the alloy obtained by melting by
arc melting or induction melting process.
[0039] Besides, in the alloy powder prepared by heat treatment after mechanical alloying
method or mechanical grinding method, the TbCu₇ phase is likely to be the principal
phase.
[0040] Furthermore, in the alloy powder prepared by liquid quenching method, the principal
phase may be either ThMn₁₂ phase or TbCu₇ phase depending on the cooling rate or composition.
For example, when Si is contained by 15% by atom in the alloy, if the cooling rate
is slow, the ThMn₁₂ phase becomes the principal phase, and if fast, there is a compound
in which the TbCu₇ phase is the principal phase. At a constant cooling rate, in the
alloy containing Si by 15% by atom, the ThMn₁₂ phase is the principal phase, or in
the alloy with 8% by atom, there exists a compound in which TbCu₇ phase is the principal
phase.
[0041] The obtained alloy powder is heated in inert gas atmosphere or vacuum at 300 to 1000°C
for 0.1 to 100 hours, and the coercive force is improved greatly. This heat treatment
may be omitted, however, if nitriding in the case of manufacture of, for example,
magnetic material containing nitrogen as element M as mentioned later. Furthermore,
the heat treatment may be also omitted when hot pressing or hot plastic processing
is conducted for obtaining a permanent magnet as mentioned later.
[0042] Explained next are manufacturing methods of a magnetic material containing nitrogen
as element M.
[0043] In a first method, nitrogen used as element M is introduced into the alloy powder
by heating the alloy powder in a nitrogen gas atmosphere at 0.001 to 2 atmospheric
pressures for 0.1 to 100 hours at 300 to 800°C.
[0044] The atmosphere for nitriding may be, instead of nitrogen gas, nitrogen compound gas
such as ammonia. The partial pressure of nitrogen or nitrogen compound or its mixture
gas may be preferably set in a range of 0.001 to 2 atmospheric pressures.
[0045] In nitriding treatment, it is also possible to mix other gas not containing nitrogen,
aside from nitrogen and nitrogen compound gas. When mixing oxygen, however, it is
desired to set the partial pressure of oxygen at 0.02 atmospheric pressure or less
in order to avoid deterioration of magnetic properties due to formation of oxide during
heat treatment.
[0046] The nitriding treatment may be also conducted after heat treatment employed for improving
the coercive force.
[0047] In a second method, nitrogen used as the element M is introduced into the alloy powder
by inducing solid phase reaction, using the nitride such as SiN and RN as the material
in the process of preparation of the alloy powder.
[0048] From the alloy powder (magnetic material) relating to the invention obtained in the
above methods, the following permanent magnet and bond magnet can be manufactured.
(a) A permanent magnet is manufactured by forming the alloy powder in a unified form
of high density (compressed powder) by hot press or hot immersion press (HIP). Here,
by applying a magnetic field to the formed body to align the crystal orientation,
a magnet having a high magnetic flux density may be obtained. Moreover, after hot
press or HIP, by plastic deformation processing while pressurizing at a temperature
of 300 to 700°C, the magnetic orientation may be obtained in the axis easy to magnetize.
(b) The alloy powder is bonded by using a metallic binder composed of metal such as
Al, Pb, Sn, Zn, Mg or alloy, and a permanent magnet is produced.
(c) A permanent magnetic is manufactured by sintering the alloy powder.
(d) The alloy powder is mixed with resin such as epoxy resin and nylon, and formed
to produce a bond magnet. When using the epoxy resin thermoset resin, it is preferred
to cure at a temperature of 100 to 200°C after compressive forming. When using the
nylon thermoplastic resin, it is desired to employ the injection forming method.
[0049] According to the material of the present invention, formation of impurity phase of
Fe, Co or Fe-Co alloy is suppressed, and a stable ThMn₁₂ crystal structure is formed
as the principal phase, and therefore excellent magnetic properties are exhibited,
and a lower cost is realized.
[0050] That is, in the rare earth iron intermetallic compound, the stable formation of ThMn₁₂
phase as principal phase depends greatly on the atomic radius of the element in the
rare earth site. More specifically, by reducing the atomic radius of the element occupying
the rare earth site, a stable ThMn₁₂ phase may be formed. To the contrary, when the
atomic radius of the element occupying the rare earth site exceeds 1.84 A, stable
ThMn₁₂ phase cannot be formed.
[0051] In the rare earth element, as the atomic weight is larger, the atomic radius becomes
smaller due to lanthanide contraction. For example, in the case of a rare earth iron
intermetallic compound using a light rare earth element of a smaller atomic weight
than Sm, that is, a larger atomic radius than Sm, the formation of impurity phase
mainly of α-Fe is dominant, and therefore the rare earth iron intermetallic compound
having the ThMn₁₂ phase as the principal phase cannot be obtained.
[0052] On the other hand, even in the light rare earth element of large atomic radius, by
mixing with a light rare earth element of a larger atomic weight, i.e. a light rare
earth element or heavy rare earth element of smaller atomic radius, the average atomic
radius of the entire rare earth element in the rare earth site can be reduced. As
a result, a stable ThMn₁₂ phase can be formed. However, such rare earth iron intermetallic
compound in ThMn₁₂ crystal structure is limited by the combination of specific rare
earth elements. Hence, the magnetic properties may be sacrificed by the combination
of rare earth elements.
[0053] The present invention, as indicated by the combination expressed in the general formula
R1
xR2
ySi
zT
v, can suppress the formation of impurity phase of Fe, Co or Fe-Co alloy by replacing
a part of the rare earth element of R2 by Zr or Hf of R1, so that magnetic material
having a stably formed ThMn₁₂ crystal structure as the principal phase may be obtained.
That is, since Zr and Hf are smaller in atomic radius as compared with rare earth
elements, by mixing Zr or Hf in the rare earth element, the atomic radius of the elements
occupying the rare earth site can be controlled in a wide range. As a result, without
being restricted by at least one element selected from rare earth element, by combining
with various rare earth elements Zr, and Hf, it is possible to form a stable ThMn₁₂
crystal structure as the principal phase.
[0054] Therefore, a magnetic material having a stable ThMn₁₂ crystal structure as the principal
phase and excellent in magnetic properties can be obtained. By using element T (Fe,
Co) as a part of the composition, and replacing a part of the rare earth element by
Zr or Hf as R1, the use of the expensive rare earth element may be greatly saved.
Hence, the magnetic material of low cost is obtained.
[0055] With other magnetic material of the invention, formation of impurity phase of Fe,
Co or Fe-Co alloy is suppressed, and a ThMn₁₂ crystal structure introducing the intersticial
element is formed as the principal phase for enhancing the magnetic properties, and
the thermal stability of the ThMn₁₂ crystal structure is enhanced, the Curie temperature
is improved, and the cost is lowered.
[0056] To form a stable ThMn₁₂ crystal structure in a rare earth iron intermetallic compound,
it is necessary to replace a small fraction of Fe by the elements such as Si, Cr,
V, Ti, Mo, W, Mn, Ga, Al.
[0057] On the other hand, the Th₂Zn₁₇ crystal structure and Th₂Ni₁₇ crystal structure may
be also formed in rare earth iron binary system. By introducing the intersticial elements
such as N and C in the crystal lattice of these Th₂Zn₁₇ phase and Th₂Ni₁₇ phase, it
is known effective to enhance the magnetic properties. In the ThMn₁₂ crystal structure,
when Ti, V or Mo is used as stabilizing elements, it is known that the effect by the
intersticial elements is recognized.
[0058] The present invention, having the composition expressed in the general formula R1
xR2
ySi
zM
uT
v, is capable of producing a magnetic material suppressed in the formation of impurity
phase of Fe, Co or Fe-Co alloy as mentioned above.
[0059] Moreover, as shown in the general formula, by possessing the ThMn₁₂ crystal structure
introducing the intersticial elements as the principal phase, the Curie temperature
is improved, and a magnetic material having excellent magnetic properties may be obtained.
Furthermore, by adding Si as stabilizing element, the thermal instability of the ThMn₁₂
crystal structure due to introduction of the intersticial element M can be eliminated.
In particular, the magnetic material of the invention is extremely excellent in thermal
stability as compared with the case of containing Ti, V, Mo in the specified crystal
structure phase in which the intersticial element is introduced mentioned above. By
such improvement of thermal stability, the compound containing the intersticial element
be formed more easily, and hot press can be applied. By using the denser compressed
powder prepared the hot press, a permanent magnet excellent in magnetic properties
is obtained. The element R1 serves also to improve the thermal stability of the ThMn₁₂
crystal structure which is introduced the intersticial element.
[0060] In a different magnetic material of the invention, having the composition expressed
by a general formula R1
xR2
ySi
zT
v, formation of impurity phase of Fe, Co or Fe-Co alloy is suppressed, and a stable
TbCu₇ crystal structure is formed as the principal phase, and therefore excellent
magnetic properties can be exhibited, and the cost may be lowered.
[0061] In a further different magnetic material of the present invention, having the composition
expressed in a general formula R1
xR2
ySi
zM
uT
v, formation of impurity phase of Fe, Co or Fe-Co alloy is suppressed, and a TbCu₇
crystal structure introducing the intersticial elements is formed as the principal
phase to enhance the magnetic properties, and the thermal stability of the TbCu₇ crystal
structure is enhanced, and the Curie temperature is improved, and the cost is lowered.
Hence, same as the magnetic material having the ThMn₁₂ crystal structure, hot pressing
at high temperature is possible, and using a denser compressed powder, a permanent
magnet excellent in magnetic properties may be obtained.
[0062] This invention can be more fully understood from the following detailed description
when taken in conjunction with the accompanying drawings, in which:
Fig. 1 is a diagram showing an X-ray diffraction pattern of a magnetic material in
Embodiment 1 of the invention;
Fig. 2 is a diagram showing an X-ray diffraction pattern of a magnetic material in
Control 1;
Fig. 3 is a diagram showing an X-ray diffraction pattern of a magnetic material in
Embodiment 13 of the invention;
Fig. 4 is a diagram showing an X-ray diffraction pattern of a magnetic material in
Embodiment 23 of the invention;
Fig. 5 is a diagram showing an X-ray diffraction pattern of a magnetic material in
Embodiment 28 of the invention; and
Fig. 6 is a diagram showing an X-ray diffraction pattern of a magnetic material in
Control 2.
[0063] Some of the preferred embodiments of the invention are described in detail below.
Embodiment 1
[0064] High purity Zr, Nd, Si and Fe were blended at atomic fractions of 2 atm% of Zr, 6
atm% of Nd, 16 atm% of Si, and the balance of Fe. This mixed material was melted in
arc in Ar atmosphere to obtain an ingot. Small pieces of the ingot were inserted into
a quartz tube with a nozzle (0.8 mm in diameter), and is located in vertical position,
and the ingot was melted by high frequency induction heating in Ar atmosphere. Afterward,
Ar gas was supplied at a pressure of about 300 torr to the upper side of the quartz
tube, and the molten alloy in the quartz tube was injected to a copper roll rotating
fast at a peripheral speed of 10 m/s from the nozzle to be quenched, and a rapid quenching
ribbon was obtained.
Embodiments 2 to 11
[0065] Ten rapid quenching ribbons were obtained by treating the materials in the composition
as shown in Table 1 in the same manner as in Embodiment 1.
Control 1
[0066] The raw material blending high purity Nd, Si, and Fe at atomic fractions of 8 atm%
of Nd, 16 atm% of Si, and the balance of Fe was treated in the same manner as in Embodiment
1, and a rapid quenching ribbon was obtained.
[0067] The crystal structures of the obtained ribbons of Embodiment 1 to 11 were measured
by the X-ray diffraction method. The results are shown in Table 1.

[0068] Moreover, in the ribbons obtained in Embodiment 1 and Control 1, X-ray diffraction
patterns were obtained by using CuKα radiation. The results are shown in Fig. 1 and
Fig. 2, respectively.
[0069] As clear from Table 1 and Fig. 1, it is known that the ThMn₁₂ phase is formed as
the principal phase in the ribbons of Embodiments 1 to 11. By contrast, in the ribbon
of Control 1 which is similar in composition to Embodiment 1 except that Zr is not
added, as known from Fig. 2, α-Fe is formed, and ThMn₁₂ phase is not formed at all.
Embodiment 12
[0070] High purity Zr, Sm, Si and Fe were blended at atomic fractions of 0.5 atm% of Zr,
8 atm% of Sm, 16 atm% of Si and the balance of Fe. This mixed material was melted
in arc in Ar atmosphere to obtain an ingot. Small pieces of the ingot were inserted
into a quarts tube with a nozzle (0.8 mm in diameter), and is located in vertical
position, was melted by high frequency induction heating in Ar atmosphere. Afterwards,
supplying Ar gas at a pressure of about 300 torr to the upper side of the quartz tube,
the molten alloy in the quartz tube was injected to a copper roll rotating fast at
a peripheral speed of 30 m/s from the nozzle to be quenched, and a rapid quenching
ribbon was obtained.
[0071] The crystal structure of the obtained ribbon was measured by X-ray diffraction method.
As a result, the principal phase was ThMn₁₂ phase.
[0072] After heating this ribbon in vacuum for 10 minutes at 800°C, its magnetic properties
were measured. As a result, the remanence was 5.6 kG, and the coercive force was 3.6
kOe, and extremely excellent magnetic properties were confirmed.
Embodiment 13
[0073] High purity Zr, Nd, Si and Fe were blended at atomic fractions of 4 atm% of Zr, 4
atm% of Nd, 4 atm% of Si, and the balance of Fe. This mixed material was melted in
arc in Ar atmosphere to obtain an ingot. Small pieces of the ingot were inserted into
a quarts tube with a nozzle (0.8 mm in diameter), and is located in vertical position,
and the ingot was melted by high frequency induction heating in Ar atmosphere. Afterwards,
Ar gas was supplied at a pressure of about 300 torr to the upper side of the quartz
tube, and the molten alloy in the quartz tube is injected to a copper roll rotating
fast at a peripheral speed of 30 m/s from the nozzle to be quenched, and a rapid quenching
ribbon was obtained.
Embodiments 14 to 22
[0074] Nine ribbons were obtained by treating the materials in the compositions shown in
Table 2 in the same manner as in Embodiment 13.
[0075] The crystal structures of the obtained ribbons of Embodiments 13 to 22 were measured
by the X-ray diffraction method. The results are shown in Table 2.
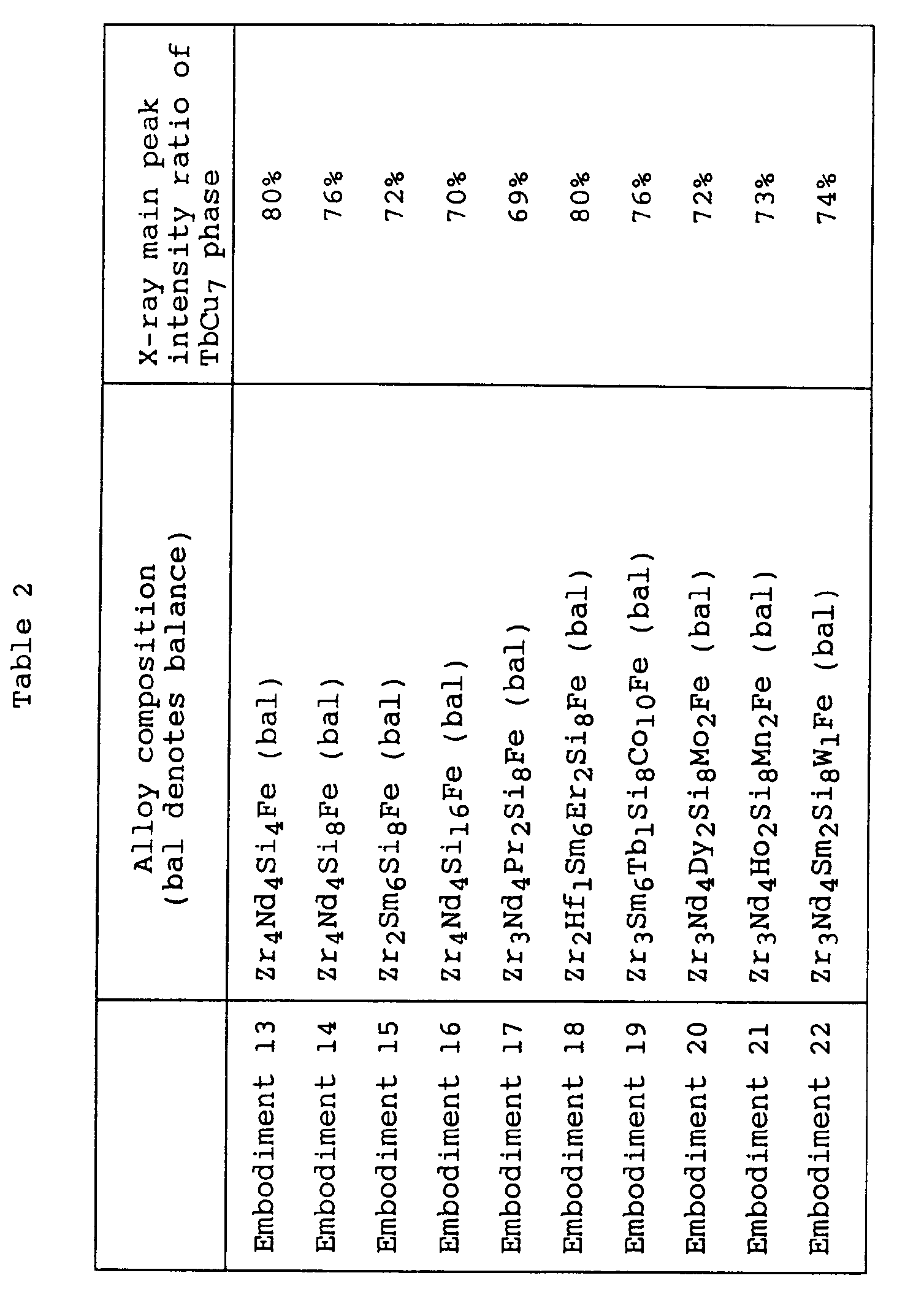
[0076] In the ribbon obtained in Embodiment 13, the X-ray diffraction pattern was determined
by using CuKα radiation. The result is shown in Fig. 3.
[0077] As clear from Table 2 and Fig. 3, in the ribbons of Embodiments 13 to 22, the TbCu₇
phase was present as the principal phase.
Embodiments 23 to 27
[0078] High purity powders of Nd, Sm, Pr, Zr, Hf, Ti, Mo, Si, W, Ga, C, Fe, Co were blended
as prescribed, and melted in arc in Ar atmosphere, and poured into a mold, and five
ingots were prepared. The ingots were ground to mean particle size of 50 to 100 µm
by using a mortar, and heated for 2 hours at temperature of 500 to 700°C in nitrogen
gas atmosphere of one atmospheric pressure, respectively. The compositions of the
specimens after heat treatment are shown in Table 3. The heat treatment temperature
in nitrogen atmosphere is also shown in Table 3.
[0079] The crystal structures of the obtained specimens of Embodiments 23 to 27 were measured
by the X-ray diffraction method. The results are also shown in Table 3.
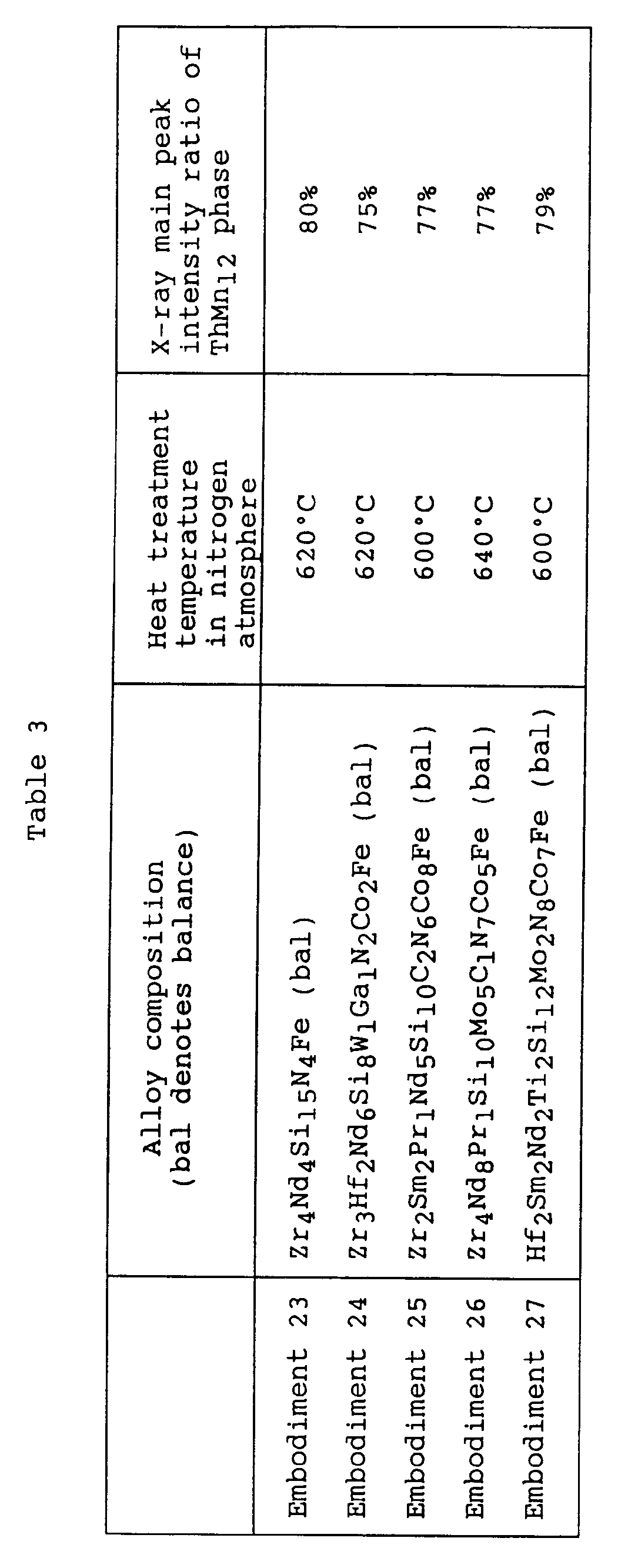
[0080] In the obtained specimen of Embodiment 23, the X-ray diffraction pattern was determined
by using CuKα radiation. The result is shown in Fig. 4.
[0081] As evident from Table 3 and Fig. 4, in all specimens of Embodiments 23 to 27, the
ThMn₁₂ phase is formed as the principal phase.
[0082] Furthermore, the specimens of Embodiments 23 to 27 were molded in magnetic field
using Zn powder as binder, and heated in Ar atmosphere at 300 to 600°C to fabricate
permanent magnets. Then, the permanent magnets were measured the coercive force and
the saturation magnetization. As a result, these permanent magnets were confirmed
to have excellent magnetic properties, with the saturation magnetization, 4πMs of
0.4 to 0.5 T, and the coercive force, iHc of 4000 to 6000 Oe.
Embodiments 28 to 32
[0083] Powders of Sm, Pr, Nd, Er, Zr, Hf having an average particle size of 0.5 mm, and
powders of Fe, Co, Cr, V, Si, Ti having an average particle size of 3 to 40 µm were
blended as prescribed to prepared five mixed powders. The mixed powders were put in
ball mill, and ground and mixed for 65 hours in Ar atmosphere, and were alloyed by
mechanical alloying. Forming dies were filled with alloy powders, and heated for 2
hours at 500 to 700°C in nitrogen gas atmosphere at one atmospheric pressure. The
compositions of specimens after heat treatment are shown in Table 4. The heat treatment
temperature in nitrogen atmosphere is also shown in Table 4.
[0084] The crystal structures of the obtained specimens in Embodiments 28 to 32 were measured
by X-ray diffraction method. The results are also shown in Table 4.

[0085] In the obtained specimen of Embodiment 28, X-ray diffraction pattern was determined
by using CuKα radiation. The result is shown in Fig. 5.
[0086] As clear from Table 4 and Fig. 5, in the specimens of Embodiments 28 to 32, the TbCu₇
phase is present as the principal phase.
[0087] Moreover, from the specimens of Embodiments 28 to 32, permanent magnets were prepared
in the same manner as in Embodiment 23, and the coercive force and the saturation
magnetization were measured. As a result, in all these permanent magnets, the saturation
magnetization, 4πMs was 0.4 to 0.5 T, and the coercive force, iHc was 4000 to 6000
Oe, and excellent magnetic properties were confirmed.
Controls 2 to 4
[0088] High purity powders of Nd, Sm, Zr, Ti, Mo, Fe and Co were blended in the composition
as shown in Table 5, and melted in arc in Ar atmosphere, and poured into molds to
prepare three ingots. The ingots were ground in an average particle size of 50 to
100 µm same as in Embodiment 23, and heated for 2 hours at 500 to 700°C in nitrogen
gas atmosphere of one atmospheric pressure. The heat treatment temperature in nitrogen
atmosphere is also shown in Table 5.
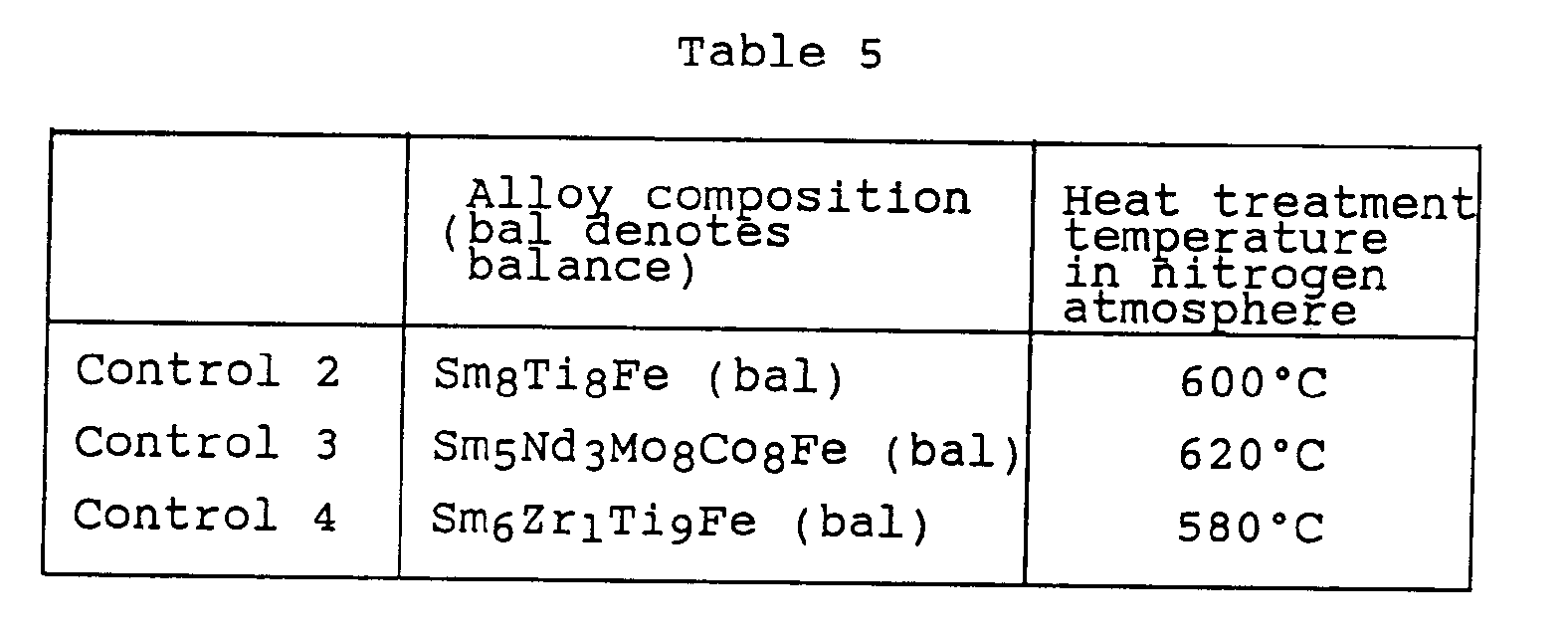
[0089] In the obtained specimen of Control 2, the X-ray diffraction pattern was determined
by using CuKα radiation. The results are shown in Fig. 6.
[0090] As clear from Fig. 6, in the specimen of Control 2, α-Fe massively precipitates into
the compound. This is because the thermal stability of the nitride is poor because
Si is not contained in the composition, and decomposition occurs at the heat treatment
temperature in Table 6. Meanwhile, as a result of determining the X-ray diffraction
pattern by using CuKα ray in the specimens of Controls 3, 4, the same X-ray diffraction
pattern as in Fig. 6 (X-ray diffraction pattern of Reference 2) was shown.
[0091] According to the present invention, as described herein, it is possible to provide
a magnetic material of low cost effective as the material for permanent magnet, bond
magnet or the like to be processed by hot press or the like, which suppresses the
formation of impurity phase of Fe, Co or Fe-Co alloy, possesses stable ThMn₁₂ crystal
structure or TbCu₇ crystal structure as the principal phase, and is characterized
by excellent magnetic properties such as saturation magnetization and the coercive
force.
1. A magnetic material which is expressed in a general formula:
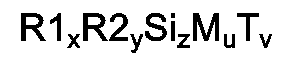
where R1 is at least one element selected from Zr and Hf, R2 is at least one element
selected from rare earth element, M is at least one element selected from C, N and
P, T is at least one element selected from Fe and Co, x + y + z + u + v = 100, x,
y, z, u, v are atomic percent individually defined as 0.1 ≦ x ≦ 20, 2 ≦ y ≦ 20, 0.5
≦ z ≦ 20, 0 ≦ u ≦ 20, v ≧ 50, and
of which principal phase possesses a ThMn₁₂ crystal structure.
2. A magnetic material of claim 1, characterized in that R1 in the general formula is
Zr.
3. A magnetic material of claim 1, characterized in that R2 in the general formula is
Sm.
4. A magnetic material of claim 1, characterized in that x and y in the general formula
are 4 ≦ x + y ≦ 20.
5. A magnetic material of claim 1, characterized in that x in the general formula is
0.5 ≦ x ≦ 6.
6. A magnetic material of claim 1, characterized in that y in the general formula is
2 ≦ y ≦ 15.
7. A magnetic material of claim 1, characterized in that z in the general formula is
0.5 ≦ z ≦ 15.
8. A magnetic material of claim 1, characterized in that T in the general formula is
Fe.
9. A magnetic material of claim 1, characterized in that u in the general formula is
u > 0.
10. A magnetic material of claim 9, characterized in that R1 in the general formula is
Zr, and R2 is at least one element selected from Pr and Nd.
11. A magnetic material which is expressed in a general formula:

where R1 is at least one element selected from Zr and Hf, R2 is at least one element
selected from rare earth element, M is at least one element selected from C, N and
P, T is at least one element selected from Fe and Co, x + y + z + u + v = 100, x,
y, z, u, v are atomic percent individually defined as 0.1 ≦ x ≦ 20, 2 ≦ y ≦ 20, 0.5
≦ z ≦ 20, 0 ≦ u ≦ 20, v ≧ 50, and
of which principal phase possesses a TbCu₇ crystal structure.
12. A magnetic material of claim 11, characterized in that R1 in the general formula is
Zr.
13. A magnetic material of claim 11, characterized in that R2 in the general formula is
Sm.
14. A magnetic material of claim 11, characterized in that x and y in the general formula
are 4 ≦ x + y ≦ 20.
15. A magnetic material of claim 11, characterized in that x in the general formula is
0.5 ≦ x ≦ 6.
16. A magnetic material of claim 11, characterized in that y in the general formula is
2 ≦ y ≦ 15.
17. A magnetic material of claim 11, characterized in that z in the general formula is
0.5 ≦ z ≦ 15.
18. A magnetic material of claim 11, characterized in that T in the general formula is
Fe.
19. A magnetic material of claim 11, characterized in that u in the general formula is
u > 0.
20. A magnetic material of claim 19, characterized in that R1 in the general formula is
Zr, and R2 is at least one element selected from Pr, Nd and Sm.
1. Magnetisches Material, ausgedrückt durch die allgemeine Formel

worin bedeuten:
R1 Zr und/oder Hf;
R2 mindestens ein Seltenerdeelement;
M mindestens ein Element, ausgewählt aus C, N und P;
T Fe und/oder Co;
x + y + zu + v = 100, wobei x, y, z, u und v für Atomprozente stehen, die einzeln
wie folgt definiert sind: 0,1 ≦ x ≦ 20; 2 ≦ y ≦ 20; 0,5 ≦ 2 ≦ 20; 0 ≦ u ≦ 20; v ≧
50, und
wobei die Hauptphase eins ThMn₁₂-Kristallstruktur aufweist.
2. Magnetisches Material nach Anspruch 1, dadurch gekennzeichnet, daß R1 in der allgemeinen
Formel für Zr steht.
3. Magnetisches Material nach Anspruch 1, dadurch gekennzeichnet, daß R2 in der allgemeinen
Formel für Sm steht.
4. Magnetisches Material nach Anspruch 1, dadurch gekennzeichnet, daß x und y in der
allgemeinen Formel wie folgt definiert sind: 4 ≦ x + y ≦ 20.
5. Magnetisches Material nach Anspruch 1, dadurch gekennzeichnet, daß x in der allgemeinen
Formel wie folgt definiert ist: 0,5 ≦ x ≦ 6.
6. Magnetisches Material nach Anspruch 1, dadurch gekennzeichnet, daß y in der allgemeinen
Formel wie folgt definiert ist: 2 ≦ y ≦ 15.
7. Magnetisches Material nach Anspruch 1, dadurch gekennzeichnet, daß z in der allgemeinen
Formel wie folgt definiert ist: 0,5 ≦ z ≦ 15.
8. Magnetisches Material nach Anspruch 1, dadurch gekennzeichnet, daß T in der allgemeinen
Formal für Fe steht.
9. Magnatisches Material nach Anspruch 1, dadurch gekennzeichnet, daß u in der allgemeinen
Formel wie folgt definiert ist: u > 0.
10. Magnetisches Material nach Anspruch 9, dadurch gekennzeichnet, daß R1 in der allgemeinen
Formel für Zr steht und R2 Pr und/oder Nd bedeutet.
11. Magnetisches Material, ausgedrückt durch die allgemeine Formel
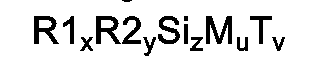
worin bedeuten:
R1 Zr und/oder Hf;
R2 mindestens ein Seltenerdeelement;
M mindestens ein Element, ausgewählt aus C, N und P;
T Fe und/oder Co;
x + y + z + u + v 100, wobei x, y, z, u und v für Atomprozente stehen, die einzeln
wie folgt definiert sind: 0,1 ≦ x ≦ 20; 2 ≦ y ≦ 20; 0,5 ≦ z ≦ 20; 0 ≦ u ≦ 20; v ≧
50, und
wobei die Hauptphase eine TbCu₇-Kristallstruktur aufweist.
12. Magnetisches Material nach Anspruch 11, dadurch gekennzeichnet, daß R1 in der allgemeinen
Formel für Zr steht.
13. Magnetisches Material nach Anspruch 11, dadurch gekennzeichnet, daß R2 in der allgemeinen
Formel für Sm steht.
14. Magnetisches Material nach Anspruch 11, dadurch gekennzeichnet, daß x und y in der
allgemeinen Formel wie folgt definiert sind: 4 ≦ x + y ≦ 20.
15. Magnetisches Material nach Anspruch 11, dadurch gekennzeichnet, daß x in der allgemeinen
Formel wie folgt definiert ist: 0,5 ≦ x ≦ 6.
16. Magnetisches Material nach Anspruch 11, dadurch gekennzeichnet, daß y in der allgemeinen
Formel wie folgt definiert ist: 2 ≦ y ≦ 15.
17. Magnetisches Material nach Anspruch 11, dadurch gekennzeichnet, daß z in der allgemeinan
Formel wie folgt definiert ist: 0,5 ≦ z ≦ 15.
18. Magnetisches Material nach Anspruch 11, dadurch gekennzeichnet, daß T in der allgemeinen
Formel für Fe steht.
19. Magnetisches Material nach Anspruch 11, dadurch gekennzeichnet, daß u in der allgemeinen
Formel wie folgt definiert ist: u > 0.
20. Magnetisches Material nach Anspruch 19. dadurch gekennzeichnet, daß R1 in der allgemeinen
Formel für Zr steht und R2 mindestens ein Element, ausgewählt aus Pr, Nd und Sm, bedeutet.
1. Matériau magnétique qui est exprimé par la formule générale :

dans laquelle R1 est au moins un élément choisi parmi Zr et Hf, R2 est au moins un
élément choisi parmi les éléments des terres rares, M est au moins un élément choisi
parmi C, N et P, T est au moins un élément choisi parmi Fe et Co, x + y + z + u +
v = 100, x, y, z, u, v étant les pourcentages atomiques définis individuellement par
0,1 ≦ x ≦ 20, 2 ≦ y ≦ 20, 0,5 ≦ 20, 0 ≦ u ≦ 20, v ≧ 50, et dont la phase principale
possède une structure de cristal de ThMn₁₂.
2. Matériau magnétique selon la revendication 1, caractérisé en ce que R1 dans la formule
générale est Zr.
3. Matériau magnétique selon la revendication 1, caractérisé en ce que R2 dans la formule
générale est Sm.
4. Matériau magnétique selon la revendication 1, caractérisé en ce que x et y dans la
formule générale sont tels que 4 ≦ x + y ≦ 20.
5. Matériau magnétique selon la revendication 1, caractérisé en ce que x dans la formule
générale est tel que 0,5 ≦ x ≦ 6.
6. Matériau magnétique selon la revendication 1, caractérisé en ce que y dans la formule
générale est tel que 2 ≦ y ≦ 15.
7. Matériau magnétique selon la revendication 1, caractérisé en ce que z dans la formule
générale est tel que 0,5 ≦ z ≦ 15.
8. Matériau magnétique selon la revendication 1, caractérisé en ce que T dans la formule
générale est Fe.
9. Matériau magnétique selon la revendication 1, caractérisé en ce que u dans la formule
générale est tel que u > 0.
10. Matériau magnétique selon la revendication 9, caractérisé en ce que R1 dans la formule
générale est Zr, et R2 est au moins un élément choisi parmi Pr et Nd.
11. Matériau magnétique qui est exprimé par la formule générale:

dans laquelle R1 est au moins un élément choisi parmi Zr et Hf, R2 est au moins un
élément choisi parmi les éléments des terres rares, M est au moins un élément choisi
parmi C, N et P, T est au moins un élément choisi parmi Fe et Co, x + y + z + u +
v = 100, x, y, z, u, v étant les pourcentages atomiques définis individuellement par
0,1 ≦ x ≦ 20, 2 ≦ y ≦ 20, 0,5 ≦ z ≦ 20, 0 ≦ u ≦ 20, v ≧ 50, et dont la phase principale
possède une structure de cristal de TbCu₇.
12. Matériau magnétique selon la revendication 11, caractérisé en ce que R1 dans la formule
générale est Zr.
13. Matériau magnétique selon la revendication 11, caractérisé en ce que R2 dans la formule
générale est Sm.
14. Matériau magnétique selon la revendication 11, caractérisé en ce que x et y dans la
formule générale sont tels que 4 ≦ x + y ≦ 20.
15. Matériau magnétique selon la revendication 11, caractérisé en ce que x dans la formule
générale est tel que 0,5 ≦ x ≦ 6.
16. Matériau magnétique selon la revendication 11, caractérisé en ce que y dans la formule
générale est tel que 2 ≦ y ≦ 15.
17. Matériau magnétique selon la revendication 11, caractérisé en ce que z dans la formule
générale est tel que 0,5 ≦ z ≦ 15.
18. Matériau magnétique selon la revendication 11, caractérisé en ce que T dans la formule
générale est Fe.
19. Matériau magnétique selon la revendication 11, caractérisé en ce que u dans la formule
générale est tel que u > 0.
20. Matériau magnétique selon la revendication 19, caractérisé en ce que R1 dans la formule
générale est Zr, et R2 est au moins un élément choisi parmi Pr, Nd et Sm.