[0001] This invention relates to a mixture of cationic and anionic polymers useful as a
strengthening additive in papermaking processes, and to the use of the mixture in
a conventional aqueous suspension of cellulosic fibers in a process for making paper.
[0002] The production of paper of improved dry strength from pulps composed of unbleached
fibers, especially when the pulp contains black liquor, has presented a special problem
to the paper manufacturing art. Washed, unbleached pulp normally contains 1 to 10
weight percent black liquors. Most conventional dry strength polymers (both anionic
and cationic) are inadequate as dry strength additives when used with such pulps.
There is a need for new dry strength additives that improve dry strength when used
in pulps composed of unbleached fibers, particularly when the pulp contains black
liquor.
[0003] Polyacrylamides are disclosed in a number of patents to improve dry strength, and
acrylamide copolymers have been developed in attempting to provide increased dry strength
to papers made from unbleached pulps, and, more particularly, those containing black
liquor. US-A- 3,819,555 discloses autodispersible, nonionic, anionic, cationic and
amphoteric vinyl polymers containing at least 60 weight percent acrylamide linkages
and at least 5 weight percent of acrolein linkages, including anionic and cationic
polymers that are said to provide improved dry and wet strength when added to unbleached
pulps, and pulps containing black liquor. US-A- 3,840,489 discloses substantially
autodispersible vinylamide polymers comprising at least 60 weight percent of unsubstituted
vinylamide linkages as dry strengthening components and at least 5 weight percent
of hydrophobic linkages as components for improving absorptivity to cellulose. The
latter polymers may also carry a small amount of anionic or cationic substituents.
[0004] US-A- 4,167,439 discloses that a nonionic copolymer composed of 5 to 30 weight %
N-vinyl pyrrolidone, 15 to 60 weight % acrylamide, and 30 to 70 weight % methyl methacrylate
is useful as dry strength additive when used in the presence of black liquor.
[0005] Other acrylamide copolymers, disclosed to be water-insoluble or dispersible, are
stated to be useful as dry strength additives for use with unbleached pulps containing
black liquors. For instance, US-A- 3,874,994, US-A- 3,875,097, and US-A- 3,875,098
disclose use of a water-insoluble polymer containing at least about 60 weight percent
of unsubstituted acrylamide linkages, at least about 5 weight percent of hydrophobic
linkages, and at least about 2 weight percent of N-[di-(C₁₋₃alkyl)amino methyl]acrylamide.
[0006] Combinations of anionic and cationic polymers have also been described to be useful
in improving dry strength. US-A- 3,049,469 discloses that a water-soluble, carboxyl
containing polymer can be impregnated to a fibrous cellulosic material when a cationic
thermosetting polyamide-epichlorohydrin resin is added to the papermaking system.
US-A-3,332,834 discloses a complex comprised of anionic polyacrylamide, water-soluble
non-thermosetting resin and alum. And US-A- 4,002,588 discloses a polysalt that consists
essentially of an anionic acrylamide-styrene-acrylic acid interpolymer (molar ratio,
respectively, of 94-65:5-15:1-20) and a water-soluble cationic polyamine having a
molecular weight in excess of 1,000 is an efficient strengthening agent, even when
used with unbleached pulps containing black liquor.
[0007] US-A- 3,660,338 and US-A- 3,677,888 disclose a strength additive consisting essentially
of (a) an ionically self-crosslinked polysalt of a normally water-soluble polyanionic
polymer with a normally water-soluble polycationic polymer, at least one polymer of
which is a weak electrolyte having an ionization constant less than 10⁻³ and (b) a
water-soluble ionization suppressor.
[0008] South African Patent Application 78/2037 discloses water-soluble dry strength polymers,
which are asserted to be suitable for the manufacture of paper from unbleached fibers,
both in the presence of and in the absence of black liquor, comprising acrylamide
linkages and N-[di-(C₁₋₃alkyl) aminomethyl]acrylamide linkages having the specified
formulae in a mole ratio of 98:2 to 50:50, respectively. These polymers may have additional
linkages, which are nonionic, anionic or cationic, including cationic dimethyl diallyl
ammonium chloride and 2-dimethylaminoethyl acrylate linkages. They have a viscosity
of 2 to 10 mPas (centipoises (cps)), preferably 3 to 8 mPas (cps), in a 0.5% aqueous
solution at pH 11 and 25°C.
[0009] US-A- 4,347,100 discloses that addition of an anionic organic surface active agent
into mechanical or thermomechanical pulp at elevated temperature and pressure is effective
to cause dispersion of the lignin and to retard redeposition or coating of the lignin
on the fibers during defibering of the wood and during subsequent cooling of the pulp.
Useful water-soluble anionic agents are disclosed to be relatively high molecular
weight anionic organic polyelectrolytes or polymers, such as sodium lignin sulfonates,
or relatively lower molecular weight anionic detergents. The resultant pulp is disclosed
to have improved strength. Further improvement of the strength is disclosed to be
achieved by incorporating in the furnish a cationic organic polyelectrolyte or polymer
that is capable of reacting with the anionic additive to form a polysalt. Best results
are disclosed to result when starch is added with the cationic component.
[0010] Yamashita, in JP-A- 191394-82, discloses the addition of low molecular weight cationic
polymers having a charge density of at least (or more than) 3.0 meq/g, preferably
at least 5.0 meq/g, to unbleached pulp containing at least 3 percent, based on the
weight of the pulp, of lignin to improve the dry strength of the resultant paper.
This lignin is generally present in the black liquor. However, where sufficient lignin
is not present in the pulp, additional amounts may be added.
[0011] Yamashita also describes that the prior art includes use of an anionic or weakly
cationic water-soluble polymeric substance, of greater molecular weight than his cationic
polymers, in combination with lignin to improve dry strength, but that the prior art
processes do not provide improved dry strength.
[0012] CA-A- 1,110,019 discloses a process for manufacturing paper having improved dry strength
using, first, a water-soluble cationic polymer having a viscosity greater than about
5 mPas (cps) in a 10% aqueous solution at 25°C and, subsequently, a cation content
of greater than about 1.0 gram ion/kg polymer in combination with a water soluble
anionic polymer. Exemplary cationic components include a copolymer of acrylamide and
methacryloyloxyethyltrimethyl ammonium chloride having a viscosity of 9800 mPas (cps)
(10% solution) and a cationic content of 2.68 gram ion/kg polymer, a copolymer of
acrylamide and methacryloyloxyethyltrimethyl ammonium chloride having a viscosity
of 9700 mPas (cps) (10% solution) and a cationic content of 1.64 gram ion/kg polymer,
and a copolymer of acrylamide and dimethyldiallyl ammonium chloride having a viscosity
of 33 mPas (cps) and a cationic content of 2.21 gram ion/kg polymer.
[0013] Guar and its derivatives are also known as dry strength additives. For example, US-A-
3,303,184 discloses use of aminoethyl gums, such as aminoethyl ethers of guar, as
dry strength additives.
[0014] The aforementioned dry strength additives have not been found to provide suitable
results with unbleached pulps containing black liquors. There is a need for a strengthening
additive for papermaking processes that provides improved dry strength to paper products
produced using unbleached pulps, particularly those containing black liquors.
[0015] According to the invention, a mixture of water-soluble cationic and anionic polymers
useful as a strengthening additive in papermaking processes, is characterized in that
it comprises a water-soluble, linear, cationic polymer having a reduced specific viscosity
(0.05 weight % in a 2 M NaCl solution at 30°C) greater than 2 dl/g and a charge density
of 0.2 to 4 meq/g, and a water-soluble, anionic polymer having a charge density of
less than 5 meq/g that is reactable in the presence of water with the cationic polymer
to form a polyelectrolyte complex.
[0016] Also according to the invention, a process for making the mixture of cationic and
anionic polymers according to claim 14 is provided. The invention also includes a
process for improving the dry strength of paper according to claim 16.
[0017] Preferably in the said latter process, the amount of the cationic polymer is 0.2
to 3%, by dry weight of the fibers.
[0018] Also according to the invention, the use of the mixture of cationic and anionic polymers
according to the invention is characterized in that the said mixture is incorporated
into a conventional aqueous suspension of cellulosic fibers in a process for making
paper.
[0019] The polymers useful in this invention are water-soluble cationic and anionic polymers.
By "water-soluble" it is meant that the polymers form a non-colloidal 1% aqueous solution.
By "linear" it is meant that the polymers are straight-chained, with no significant
branching present. Exemplary polymers are described below.
[0020] "Charge Density" can be determined based on the known structure of the polymer by
calculating as follows:

It may also be determined by experimentation, for instance, by using the colloidal
titration technique described by L. K. Wang and W. W. Schuster in Ind. Eng. Chem.,
Prd. Res. Dev., 14(4)312 (1975).
[0021] Herein, molecular weight is expressed in terms of the polymers reduced specific viscosity
(RSV) measured in a 2 M NaCl solution containing 0.05 weight percent of the polymer
at 30°C. Under these conditions, a cationic acrylamide copolymer of molecular weight
1 x 10⁶ has a RSV of approximately 2 dl/g.
[0022] The polyelectrolyte complex that may form from the mixture of cationic and anionic
polymers may be soluble, partially soluble or insoluble in water. Thus, it forms what
may be conventionally termed a "solution", "suspension", "dispersion", etc. Herein,
to avoid confusion, the term "aqueous system" will be used to refer to the same. In
some instances the term "aqueous system" is also used with respect to aqueous solutions
of the water-soluble polymers that form the polyelectrolyte complex.
[0023] The cationic polymers of this invention have a RSV greater than 2 dl/g, preferably
in the range of about 10 to about 25 dl/g. They have a charge density in the range
of from 0.2 to 4 meq/g, preferably 0.5 to 1.5 meq/g. Optimum performance is obtained
with cationic polymers having a charge density of about 0.8 meq/g. Exemplary cationic
polymers include polysaccharides such as cationic guar (e.g., guar derivatized with
glycidyltrimethylammonium chloride) and other natural gum derivatives, and synthetic
polymers such as copolymers of acrylamide. The latter include copolymers of acrylamide
with diallyldimethylammonium chloride (DADMAC), acryloyloxyethyltrimethylammonium
chloride, methacryloyloxyethyltrimethyl ammonium methylsulfate, methacryloyloxyethyltrimethyl
ammonium chloride (MTMAC) or methacrylamidopropyltrimethylammonium chloride, etc.
Preferred are copolymers of acrylamide with DADMAC or MTMAC.
[0024] Some of the cationic polymers described above may undergo hydrolysis of their ester
linkages under conditions of high temperature, extreme pH's, or extended storage.
This hydrolysis results in the loss of cationic charge and the introduction of anionic
sites into the polymer. If sufficient hydrolysis occurs, the polymer solution may
become hazy. However, this hydrolysis has been found to have no significant effect
on the performance of the polymer so long as the net cationic charge density (sum
of cationic polymer charge density (meq. +/g) plus anionic polymer charge density
(meq. -/g)) remains within the ranges specified.
[0025] The anionic components of this invention include those normally present in unbleached
pulps such as solubilized lignins and hemicelluloses; synthetic anionic polymers;
and anionically modified natural polymers (i.e., those other than lignins and hemicelluloses).
When present in the papermaking process in sufficient quantity, the anionic polymer
normally present in unbleached pulps are preferred.
[0026] Solubilized lignins and hemicelluloses are normally present in unbleached pulps as
a result of incomplete removal of materials solubilized during manufacture of the
pulp. Such products result from both chemical and mechanical pulping.
[0027] Typically, black liquors, such as kraft black liquor or neutral sulfite brown liquor,
comprise solubilized lignin and hemicellulose. Washed, unbleached pulp normally contains
1 to 10 weight percent black liquors.
[0028] Exemplary synthetic anionic polymers and anionically modified natural polymers useful
in the present invention include copolymers of acrylamide and sodium acrylate, sodium
methacrylate and sodium-2-acrylamide-2-methylpropane sulfonate; sodium carboxymethylcellulose;
sodium carboxymethyl guar; sodium alginate; sodium polypectate; and poly-(sodium-2-acrylamide-2-methylpropane
sulfonate). They may be used by themselves or in any combination.
[0029] Also useful are anionically modified forms of lignin and hemicellulose, such as are
obtained, e.g., by oxidation, sulfonation or carboxymethylation. Oxidized and sulfonated
lignins and hemicelluloses are naturally present as by-products of the pulping process
and are normally present in unbleached pulps useful in this invention. The naturally
present lignins and hemicellulose may also be modified by synthetic processes such
as oxidation, sulfonation and carboxymethylation.
[0030] The polyelectrolyte complex of this invention provides paper having improved dry
strength in most papermaking systems. It is especially useful in the presence of the
anionic materials found in unbleached papermaking systems, i.e., black liquors, as
prior dry strength additives show reduced effectiveness in such systems.
[0031] The process for manufacturing paper comprises three principal steps: (1) forming
an aqueous suspension of cellulosic fibers; (2) adding the strengthening additive;
and (3) sheeting and drying the fibers to form the desired cellulosic web.
[0032] The first step of forming an aqueous suspension of cellulosic fibers is performed
by conventional means, such as known mechanical, chemical and semichemical, etc.,
pulping processes. After the mechanical grinding and/or chemical pulping step the
pulp is washed to remove residual pulping chemicals and solubilized wood components.
These steps are well known, for instance, as described in Casey, Pulp and Paper (New
York, Interscience Publishers, Inc. 1952).
[0033] The second step may be carried out by adding the polyelectrolyte complex, or cationic
component, or cationic and anionic components, or blends of the anionic and cationic
components directly to the papermaking system. The individual components and blends
of the components may be dry or they may be in aqueous systems. Further, this step
may be carried out by forming an aqueous system comprising the polyelectrolyte complex,
or polymer, or polymers, and adding the same to the papermaking system.
[0034] The third step is carried out according to well-known and conventional means, such
as those described in, e.g., Casey, Pulp and Paper, cited above.
[0035] The polyelectrolyte complex forms when the components are mixed in an aqueous system,
preferably under high shear. It may be formed and then added during the papermaking
process, or may be formed in the papermaking process. In the latter instance, the
cationic component may be added by itself to react with naturally present anionic
polymers or may be simultaneously or successively added with an anionic component.
When added successively, the anionic polymer is generally added prior to the cationic
polymer in order to avoid flocculating the pulp. Here, the amount of each anionic
polymer to be incorporated in the polyelectrolyte complex is reduced to take into
account the amount of that polymer already in the system.
[0036] The specific amount and type of polyelectrolyte complex that is preferable will depend
on, among other things, the characteristics of the pulp; the presence or absence of
black liquors and, where present, the amount and nature thereof; characteristics of
the polymers used to form the complex; the characteristics of the complex; the desirability
of transporting an aqueous system comprising the polyelectrolyte complex; and the
nature of the papermaking process in which the aqueous system is to be used. The polyelectrolyte
complex will typically comprise polymers in a ratio of cationic polymer(s):anionic
polymer(s) of 4:100 to 40:1, preferably 1:4 to 4:1. Aqueous systems formed prior to
addition to the pulp normally comprise 0.1 to 10 weight percent, based on the weight
of the water in the system, of the polyelectrolyte complex. Generally, the polyelectrolyte
complex is effective when added to the stock in an amount of 0.1 to 15%, preferably
0.2 to 3%, by dry weight of the pulp.
[0037] The amount of anionic polymer to be used is dependent on the source of the anionic
material. Naturally present anionic polymers are typically found at a level of 0.1
to 5%, based on the dry weight of the pulp. When anionic polymers are added to the
system, the total weight of anionic polymers generally falls in the range of 0.1 to
10%, based on the dry weight of the pulp. Preferably, the total weight of added anionic
polymers is in the range of 0.1 to 2.5%, based on the dry weight of the pulp.
[0038] The level of cationic polymer required is highly dependent on the level of anionic
material present. The level of cationic polymer is generally 0.1 to 5%, preferably
0.1 to 2.5%, based on the dry weight of the pulp.
[0039] The anionic charge fraction is indicative of the nature of the polyelectrolyte complex.
It can be determined by the following formula:

in which the total anionic charge is determined by multiplying the absolute value
of the charge density (electrostatic charge per weight of polymer, e.g., in meq/g)
of each anionic polymer forming the polyelectrolyte complex by the weight of that
polymer in the polyelectrolyte complex and adding the total charge of all of the anionic
polymers. The total cationic charge is determined by multiplying the charge density
of each cationic polymer forming the poly-electrolyte complex by the weight of that
polymer in the polyelectrolyte complex and adding the total charge of all of the cationic
polymers. Generally, the polyelectrolyte complex is completely soluble at an anionic
charge fraction of less than 0.2, colloidal at an anionic charge fraction of 0.2 to
0.4, and fibrous (in some instances as a stringy gel that precipitates from solution,
but which becomes colloidal under high shear) at an anionic charge fraction greater
than 0.4. Polyelectrolyte complexes of this invention generally have an anionic charge
fraction of 0.1 to 0.98, preferably an anionic charge fraction of 0.3 to 0.8, and
more preferably 0.45 to 0.6. All polyelectrolyte complexes per this invention provide
enhanced dry strength, particularly in the presence of black liquors. However, except
as described below, the fibrous polyelectrolyte complexes (particularly those having
the more preferred anionic charge fraction listed above) provide larger improvement
in dry strength than colloidal or water-soluble polyelectrolyte complexes prepared
from the same polymers. Under high shear in papermaking, these fibrous particles break
into colloidal particles that provide excellent dry strength properties.
[0040] Unique properties are obtained by forming the polyelectrolyte complex by mixing the
anionic and cationic components in an aqueous system at a temperature of at least
75°C and letting the mixture cool to less than about 60°C, preferably less than 50°C.
This can be achieved by adding the dry powder polymers to water heated to at least
75°C and, then, allowing the resultant aqueous system to cool to less than about 60°C.
Premixing of the polymers into a dry polymer mixture may facilitate handling. The
same properties can be obtained by preparing separate aqueous systems of the anionic
and cationic polymers, heating each of the aqueous systems to at least 75°C, mixing
them together, and, then, allowing the resultant aqueous system to cool to less than
about 60°C. Polyelectrolyte complexes prepared by these processes generally have an
anionic charge fraction of 0.1 to 0.98, preferably 0.4 to 0.9, and most preferably
0.65 to 0.85. High shear mixing aids in the rapid preparation of these polyelectrolyte
complexes, but is not necessary. Maintaining the temperature of the preparation solution,
dispersion, or slurry at above about 75°C for one hour aids in the homogenization
of the mixture.
[0041] Polyelectrolyte complexes having an anionic charge fraction of less than about 0.2
prepared by heating to at least 75°C and cooling will be water-soluble and perform
in the same manner to those having the same anionic charge fraction prepared at lower
temperatures. Polyelectrolyte complexes with anionic charge fractions of from about
0.2 to less than about 0.65 form colloidal particles that perform similar to the colloidal
and fibrous particles prepared without heating to at least 75°C and cooling.
[0042] When the anionic charge fraction is about 0.65 or higher and the polyelectrolyte
complexes are prepared by heating to at least 75°C followed by cooling, water-soluble
polyelectrolyte complexes are obtained that perform even better as dry strength additives
than the other species of this invention. These soluble polyelectrolyte complexes
are also useful as shear activated flocculants, retention aids on high speed paper
machines, viscosifiers and drag reduction agents, and in water treatment.
[0043] Such water-soluble complexes can be prepared from all of the aforementioned types
of anionic components. However, temperatures are not normally sufficiently high during
papermaking for formation of such a water-soluble polyelectrolyte complex. Therefore,
to use those anionic polymers normally present in unbleached pulps, it is necessary
to separate the anionic component from the pulp. This separation is normally carried
out in the papermaking process, making such anionic components readily available.
[0044] Water-soluble polyelectrolyte complexes can be prepared from, for example, poly(acrylamide-co-dimethyldiallyammonium
chloride) and Marasperse N-3 sodium lignin sulfonate (Reed Lignin Inc., Greenwich,
CT), or Aqualon® CMC 7M (Aqualon Company, Wilmington, DE), or southern pine black
liquor; quaternary amine modified waxy maize starch and Marasperse® N-22 sodium lignin
sulfonate (Reed Lignin Inc., Greenwich, CT); poly(acrylamide-co-methylacryloxyethyltrimethylammonium
chloride) and Marasperse® N-3 sodium lignin sulfonate; and poly(acrylamide-co-methylacryloxyethyltrimethylammonium
chloride) and Marasperse® N-3 sodium lignin sulfonate. However, some combinations
of cationic and anionic components prepared in this manner yield polyelectrolyte complexes
having anionic charge fractions of 0.65 or higher that are particulate or colloidal
and perform equivalent to their counterparts that are formed without heating to at
least 75°C and cooling.
[0045] Other additives useful in the papermaking process of this invention include sizes,
defoamers, fillers, wetting agents, optical brighteners, inorganic salts, etc.
[0046] This invention is illustrated in the following examples. All percentages, parts,
etc., are by weight, based on the weight of the dry pulp, unless otherwise indicated.
Examples 1 - 6
[0047] These examples demonstrate preparation of paper with improved dry strength according
to the process of this invention using a water-soluble, linear, high molecular weight,
low charge density, cationic polymer by itself and in combination with the water-soluble
anionic polymers that result from the manufacture of wood pulp (e.g., solubilized
lignins and hemicelluloses found in black liquor).
[0048] Handsheets were made on a Noble and Wood Sheet Machine (Noble and Wood Machine Co.,
Hoosick Falls, NY) using the following:
1. Pulp: unbleached southern kraft pulp beaten to 550 Canadian Standard Freeness (CSF)
at pH 8.
2. Standard Hard Water: Standard hard water having 50 ppm alkalinity and 100 ppm hardness
was prepared by adding CaCl₂ and NaHCO₃ to distilled water, and adjusting the pH to
6.5 with H₂SO₄.
3. Black Liquor (Union Camp Corp., Savannah, GA):
Total Solids: |
15.9% (measured by Tappi Standard T650) |
Sulfate Ash: |
8.9% |
Sodium: |
2.6% (by atomic absorption spectroscopy) |
Sulfur: |
0.7% (by x-ray fluoresence) |
Lignin: |
5.2% (by UV spectroscopy) |
Charge density (by colloidal titration): |
.057 meq/g at pH 5.5 |
.103 meq/g at pH 9.0 |
4. Defoamer: Defoamer 491A (Hercules Incorporated, Wilmington, DE).
[0049] A 3920 ml sample of 2.5 weight % stock, from a well mixed batch of beaten pulp, was
placed into a 4 liter metal beaker. Defoamer (0.025% based on cut of dry pulp) was
added to the beaker and stirring was begun. Then, black liquor was added to the beaker
in the amount listed in Table 1 below and stirring was continued for three minutes.
The stock was transferred to the proportioner and diluted to 18 liters with the pH
6.5 standard hard water described above. Next, a cationic copolymer (indicated in
the following table) was added to the stock and the pH of the stock was adjusted to
5.5 with H₂SO₄, and the stock was mixed for five minutes.
[0050] A clean thoroughly wetted screen was placed on an open deckle. The deckle was clamped
closed and then filled with the 6.5 pH standard hard water (described above), from
the white water return tank, to the bottom mark on the deckle box. A one liter aliquout
of stock was drawn from the proportioner and poured into the deckle. The stock in
the deckle was stirred using three rapid strokes of the dasher, the dasher was removed,
and the deckle was drawn into the white water return tank. The screen and retained
pulp was then transferred to the open felt at the entrance to the press.
[0051] The felted sheets were run through the press with the press weights adjusted so as
to obtain a pressed sheet having 33-34% solids. Then, the sheet and screen were placed
in the drum dryer, having an internal temperature of 116°C (240°F) and a throughput
time of 50-55 seconds, and run through two times (during the first run the sheet was
in contact with the drum and during the second run the screen was in contact with
the drum.). The sheets were conditioned at 22°C (72°F) and 50% relative humidity for
24 hours. Eight sheets were prepared in this manner, with the last five being used
for testing.
[0052] The handsheets were evaluated by way of the following tests:
Mullen Burst: Tappi Standard T403 ("Bursting Strength of Paper").
STFI Compression: Tappi Standard T826 ("Short Span Compressive Strength of Paperboard").
[0053] Results are shown in Table 1.
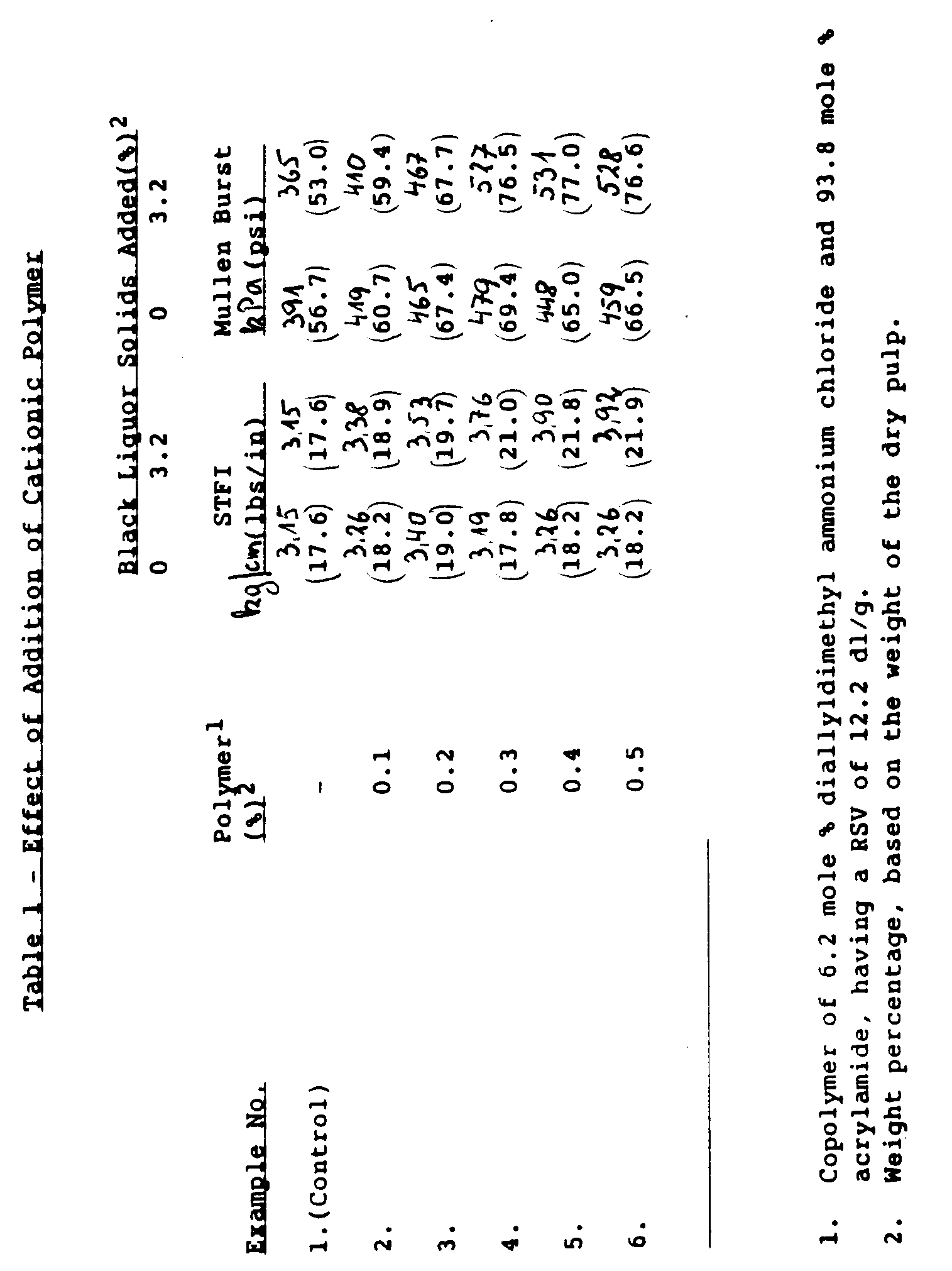
[0054] The data in Table 1 shows that improved results are obtained with respect to both
the STFI Compression Strength and Mullen Burst tests when a cationic polymer of this
invention is added to a pulp containing black liquor. Looking at the rows of data
it can be seen that best STFI Compression Strength results were obtained with samples
containing black liquor. Similarly, Mullen Burst results were better for samples containing
black liquor than samples that did not contain black liquor at polymer levels of 0.2%
or more, despite the fact that better results were obtained when the control did not
contain black liquor. Looking at the columns, it can be seen that results were significantly
better with samples containing black liquor having 0.2% or more of the cationic polymer.
Thus, this example demonstrates formation of a polyelectrolyte complex between the
cationic polymer added and the anionic polymers present in the black liquor, and that
improved dry strength is obtained with the polyelectrolyte complex of this invention.
Examples 7-9
[0055] These examples illustrate the effect of molecular weight on the performance of the
cationic polymer forming the polyelectrolyte complex. The procedure of examples 1-6
was repeated using 0.4%, by dry weight of the pulp, of the polymer used in examples
2-6 which was ultrasonically degraded in order to obtain samples of lower molecular
weight. Results, along with data for control Example No. 1 and Example No. 4 which
is included for convenience, are shown in Table 2 below.
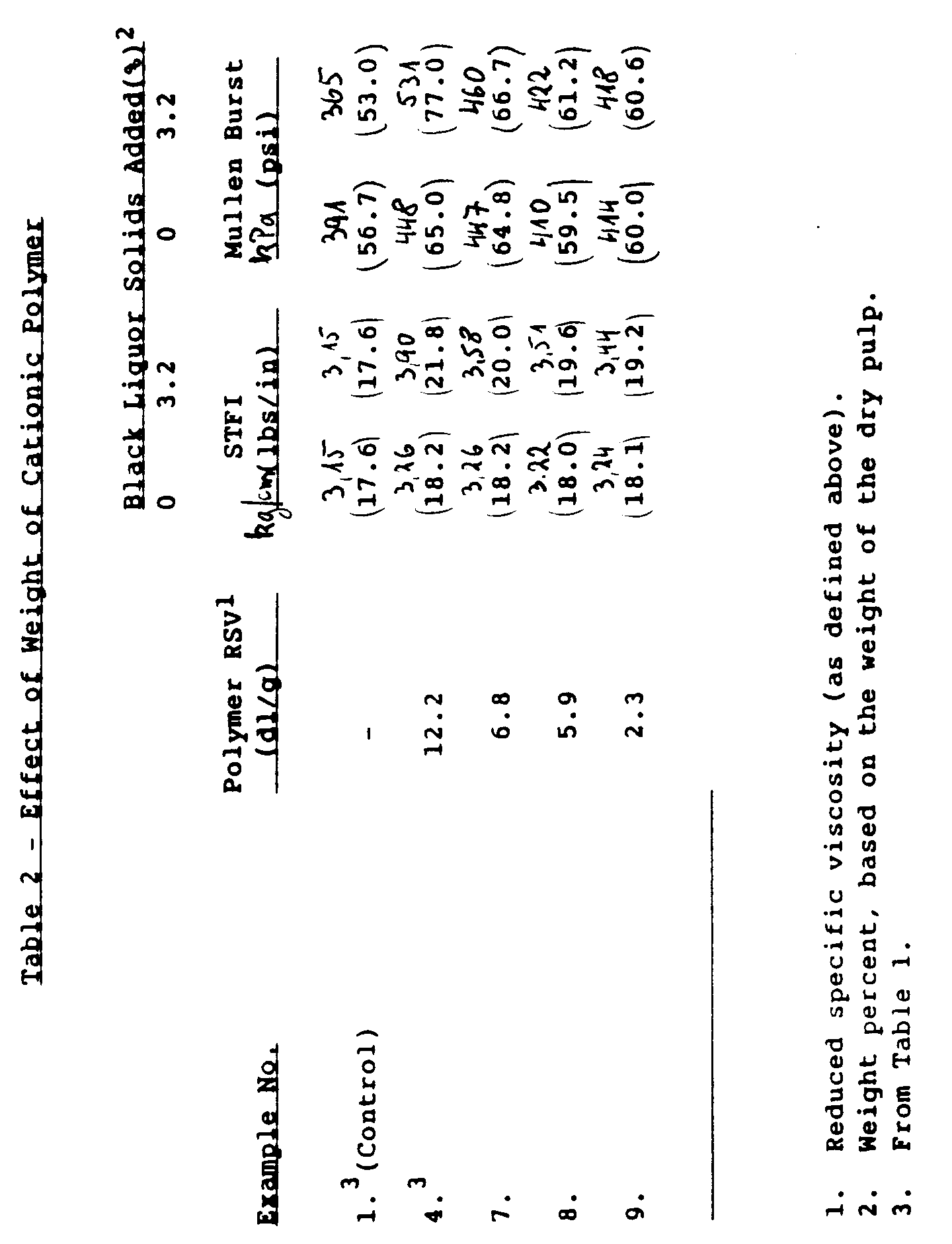
[0056] The above results show that improved results are obtained with respect to both the
STFI Compression Strength and Mullen Burst tests with the cationic polymers per this
invention having RSV's of 2 dl/g or more. Looking at the rows of data it can be seen
that better STFI Compression Strength results were obtained with samples containing
black liquor. Similarly, Mullen Burst results were better for samples containing black
liquor than samples that did not contain black liquor. This indicates formation of
a polyelectrolyte complex between the added cationic polymers and naturally present
anionic polymers of the black liquor.
[0057] Looking at the columns, it can be seen that best results were obtained with samples
having higher molecular weights (represented by higher RSV) and that significantly
better results were obtained with sample No. 4 having a RSV in the preferred range,
i.e., 12.2 dl/g, when the sample was prepared in the presence of black liquor.
Examples 10-15
[0058] These examples illustrate the effect of the charge density of the cationic polymer.
Charge density was varied by preparing acrylamide copolymers having different amounts
of diallyldimethyl ammonium chloride cationic monomer. The procedure of Examples 1-6
was repeated using the polymers described below. The polymers all had RSV's in the
range of 8-9.5 dl/g. Results are shown in Table 3, below.

[0059] Looking at the rows, in all but one instance superior results are obtained in the
presence of black liquor, indicating that a polyelectrolyte complex is being formed
by the cationic polymer and the naturally present anionic polymers. Looking at the
columns of data, it can be seen that there is a trend towards better results occurring
with polyelectrolyte complexes of lower charge density cationic polymers.
Examples 16-22
[0060] These examples demonstrate use of a number of different cationic polymers per this
invention. The procedures of Examples 1-6 was repeated using the polymers and obtaining
the results shown in Table 4, below.
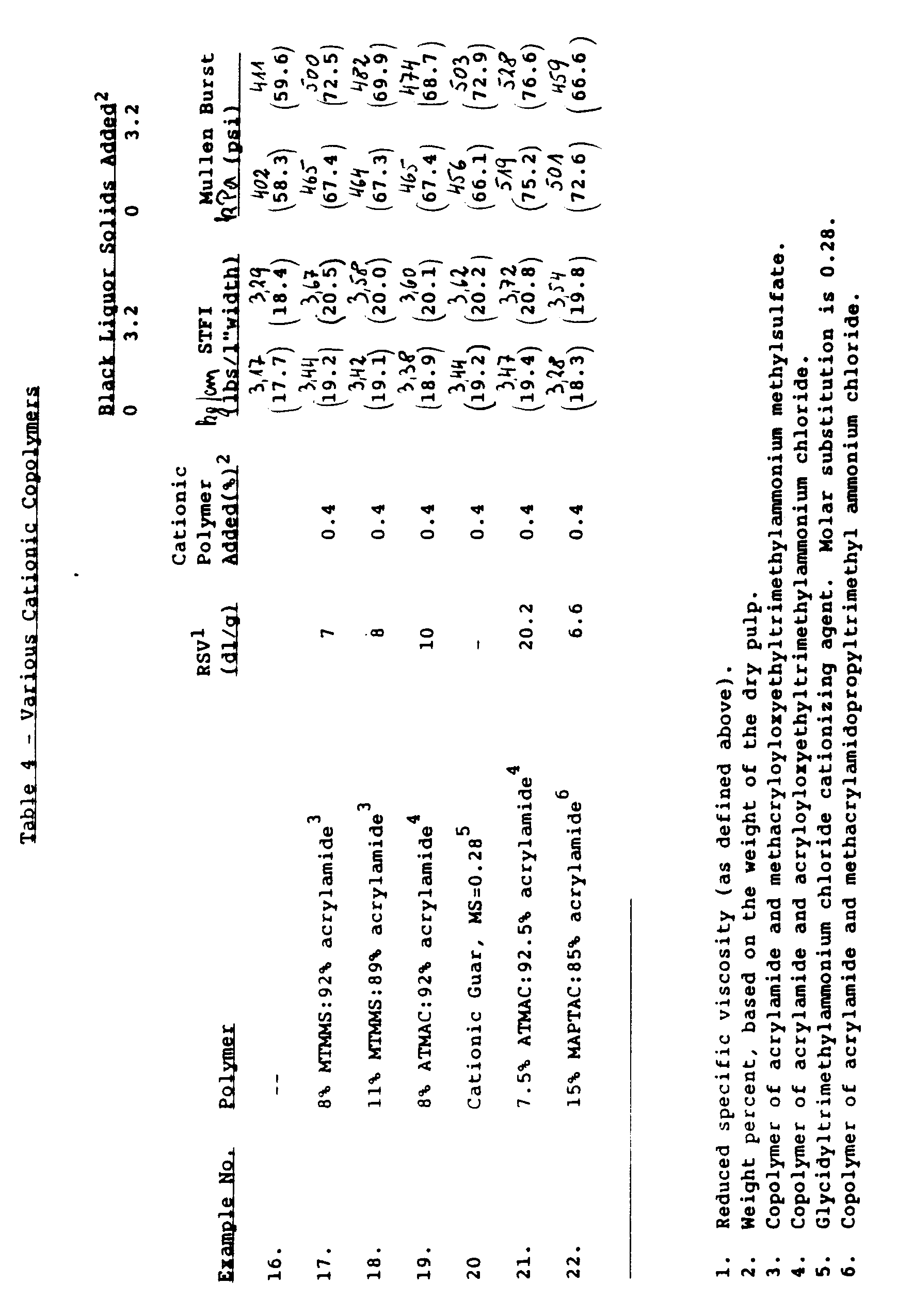
[0061] The data in Table 4 shows that improved STFI Compression Strength and Mullen Burst
results are obtained using the cationic polymers of this invention. In each instance,
the samples prepared with cationic polymers per this invention performed better than
the control sample. STFI Compression Strength was better in each instance with black
liquor. Mullen Burst results were better with the samples prepared with black liquor
than samples that were not prepared with black liquor, except with respect to sample
No. 22. Thus, the results indicate that a polyelectrolyte complex forms between the
cationic polymers of this invention and anionic polymer present in black liquors.
Examples 23-27
[0062] These examples show the effect of addition of both anionic and cationic polymers
during papermaking and the beneficial effect of addition of higher levels of anionic
component. The procedures of Example 1 were repeated using 0.5% of the cationic polymer
used in example 2-6 and the anionic polymers listed in Table 5, below. The results
are shown below in Table 5.

[0063] The data in Table 5 demonstrates that superior dry strength properties are obtained
when both an anionic and cationic polymer are added during papermaking so as to form
a polyelectrolyte complex. In addition, example 25 shows that improved results are
achieved when the amount of anionic polymer is such that the cationic and anionic
changes are nearly balanced (i.e., the charges are neutralized).
Examples 28-35
[0064] These examples illustrate the effect of using anionic polymers, other than those
resulting from the pulping operation, that fall within the scope of this invention.
Comparison samples prepared with anionic and cationic samples outside the scope of
this invention are also presented. The procedures of examples 1-6 were repeated using
0.7% of the cationic polymer of examples 2-6, except that polyamideepichlorohydrin
was used as a cationic polymer in sample No. 35. The anionic polymers were added after
the black liquor and before the cationic polymer. Results are shown in Table 6, below.
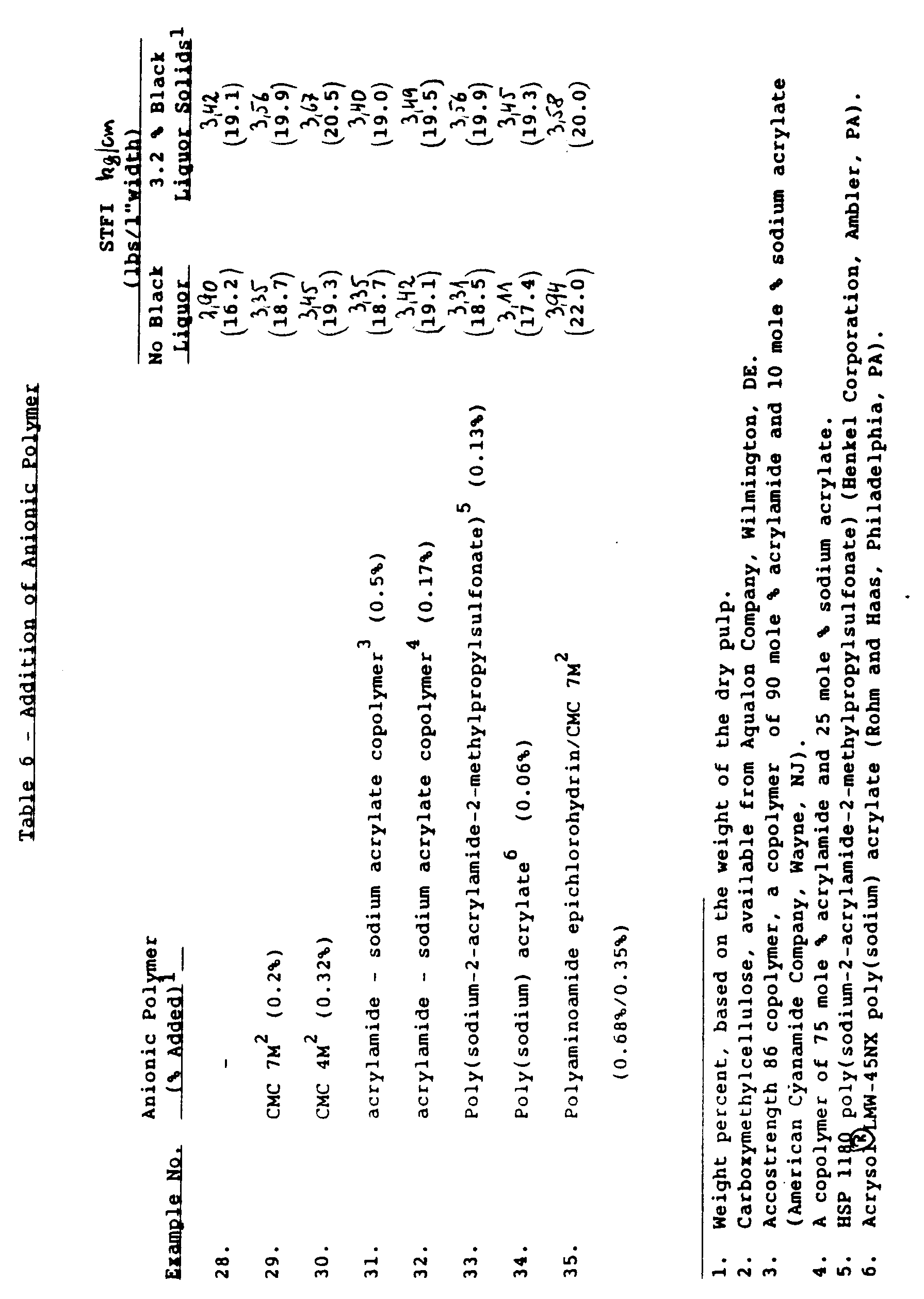
[0065] The data in Table 6 shows the superior dry strength properties of paper prepared
with the polyelectrolyte complex of this invention.
[0066] Looking at the columns, it can be seen that all of the samples prepared in the absence
of black liquor performed better than the control sample in which no anionic polymer
was used and that the samples prepared using the anionic polymers of this invention
(not present naturally) performed much better than the sample prepared only with poly(sodium
acrylate), an anionic polymer outside the scope of the instant invention.
[0067] Looking at the rows, it can be seen that in every sample, but sample No. 35, the
sample prepared with black liquor performed better than the sample prepared without
black liquor. Specifically, in Example No. 28 a polyelectrolyte complex forms with
the cationic polymers and the naturally present anionic polymers in black liquor,
providing improved dry strength. Examples 29 and 30 have superior dry strength compared
to example 28 in the absence of black liquor, indicating formation of a polyelectrolyte
complex by the cationic polymer and CMC. Similar results were found to occur with
other cationic/anionic polymer combination per this invention, in the absence of black
liquor, in examples 31 to 33. The lower STFI value achieved with poly(sodium) acrylate
(no black liquor present) indicates that additive anionic polymers per the instant
invention provide superior dry strength as compared to other additive anionic polymers.
[0068] The results obtained in example 34 in the presence of black liquor can be attributed
to formation of a polyelectrolyte complex between the cationic polymer and the anionic
polymers forming the black liquor.
[0069] Sample 35 is a comparative example showing the use of a cationic polymer outside
the scope of the instant invention. The STFI value was lower in the presence of black
liquor using this cationic polymer.
[0070] From the above, it can be seen that this invention provides superior dry strength
in the presence of black liquor than in the absence of black liquor, whereas a decrease
in dry strength occurs in the presence of black liquor using dry strength additives
outside the scope of this invention.
Examples 36-38
[0071] These examples illustrate the effect of premixing a portion of the anionic component
with the cationic polymer so as to form an aqueous system containing a polyelectrolyte
complex and adding the aqueous system to a papermaking furnish. The procedure of examples
1-6 were repeated so as to prepare a control example having no cationic polymer, example
36, and a sample prepared with a cationic copolymer comprised of 87.6 mole % acrylamide
units and 12.4% diallyldimethylammonium chloride units, Example 37.
[0072] Sample 38 was prepared using an additive composition comprising 86 parts of the aforementioned
acrylamide copolymer and 14 parts sodium lignin sulfonate, which was premixed in a
Waring blender so as to form a water-insoluble particulate polyelectrolyte complex
prior to addition to the papermaking furnish according to the following procedure.
In a Waring blender, 45g of a 20 weight percent solution of sodium lignin sulfonate
(Lignosol® XD, available from Reed Lignin Inc., Greenwich, Connecticut, having a charge
density of 0.79 meq/g at pH 6.5) was mixed into 1833 g of a 3 weight percent solution
of a copolymer comprised of 87.6 mole % acrylamide units and 12.4 mole % diallyldimethyl
ammonium chloride (RSV 13; 1.51 meq/g). This mixture was diluted with demineralized
water to form a 0.5 weight percent total solids solution that was slightly turbid.
[0073] This material was evaluated in handsheets using the procedures of examples 1 to 6.
Results are shown in Table 7.
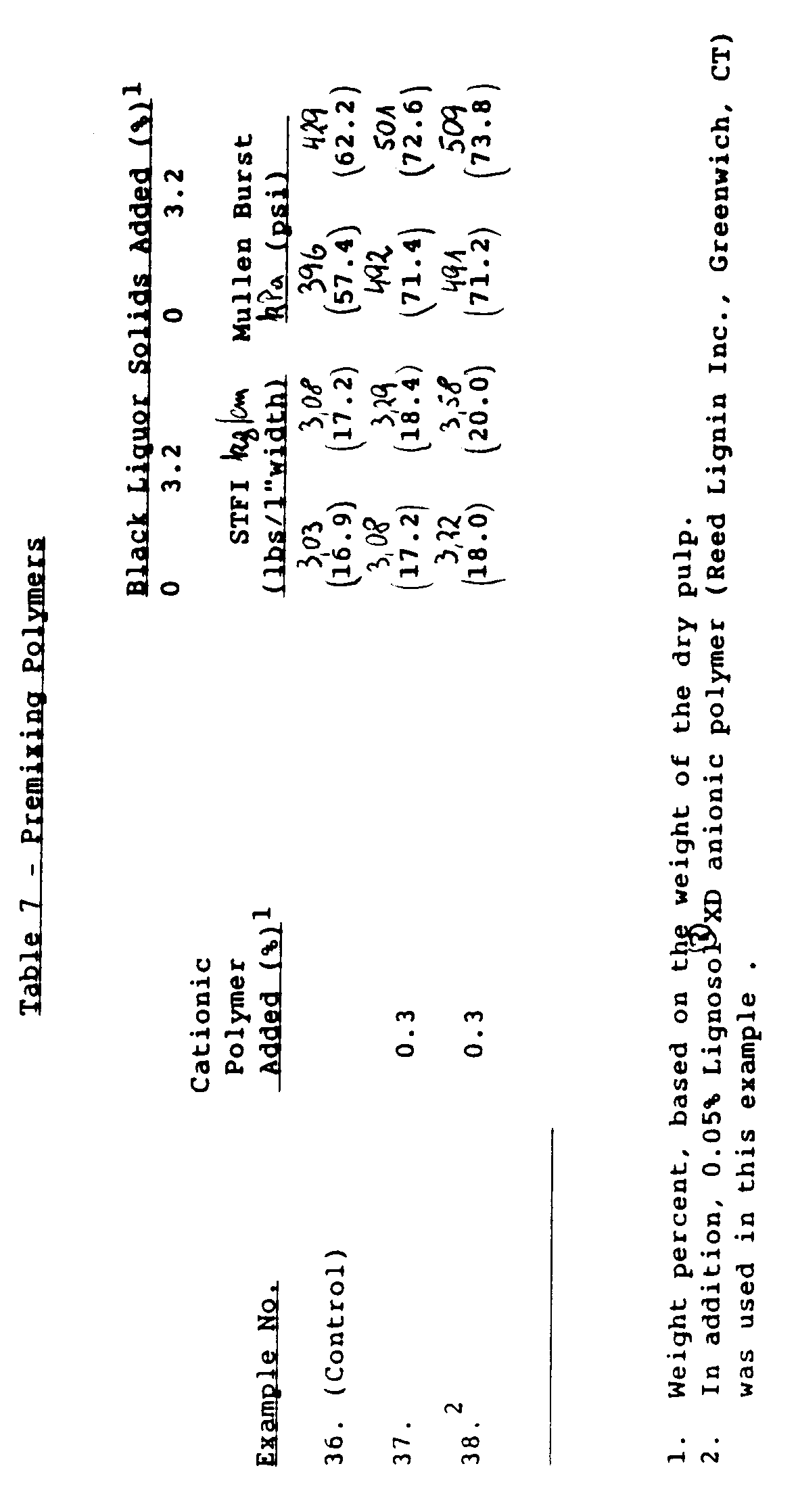
[0074] The data in Table 7 demonstrates that excellent dry strength properties are obtained
using an anionic and cationic polymer per this invention, particularly when they are
premixed to form a particulate polyelectrolyte complex prior to addition to the papermaking
process. Excellent dry strength properties occur in the presence of black liquor,
and superior performance to the cationic polymer only is shown in the absence of black
liquor.
Examples 39-46
[0075] These examples illustrates the performance of comparative polymers. The procedure
of Examples 1-6 was repeated using the following polymers: no cationic polymer, (sample
No. 39); Corcat® P600 polyethyleneimine (PEI) (Cordova Chemical Co. Muskegon, MI)
(sample No. 40); poly(diallyldimethylammonium chloride) (sample No. 41); poly(acryloyloxyethyltrimethylammonium
chloride) (sample No. 42); polyaminoamide epichlorohydrin resin (sample No. 43); copolymer
prepared from 11 mole % styrene, 5 mole % sodium acrylate and 84 mole % acrylamide,
prepared according to the procedures of Example 12 of US-A- 3,840,489) (sample No.
44); a copolymer prepared by mixing the copolymer of Example 44 with polyaminoamide
epichlorohydrin resin according to the procedures of US-A- 4,002,588 (the polymers
were mixed at an equal charge ratio) (sample No. 45); and a Mannich Reaction product
of polyacrylamide, formaldehyde and dimethylamine, 5% molar substitution (viscosity
in 0.5% solution, at pH 11, 6.5 mPas (cps)), prepared according to Example 1 of South
African Application 78/2037 (sample No. 46). Results are shown in Table 8, below.
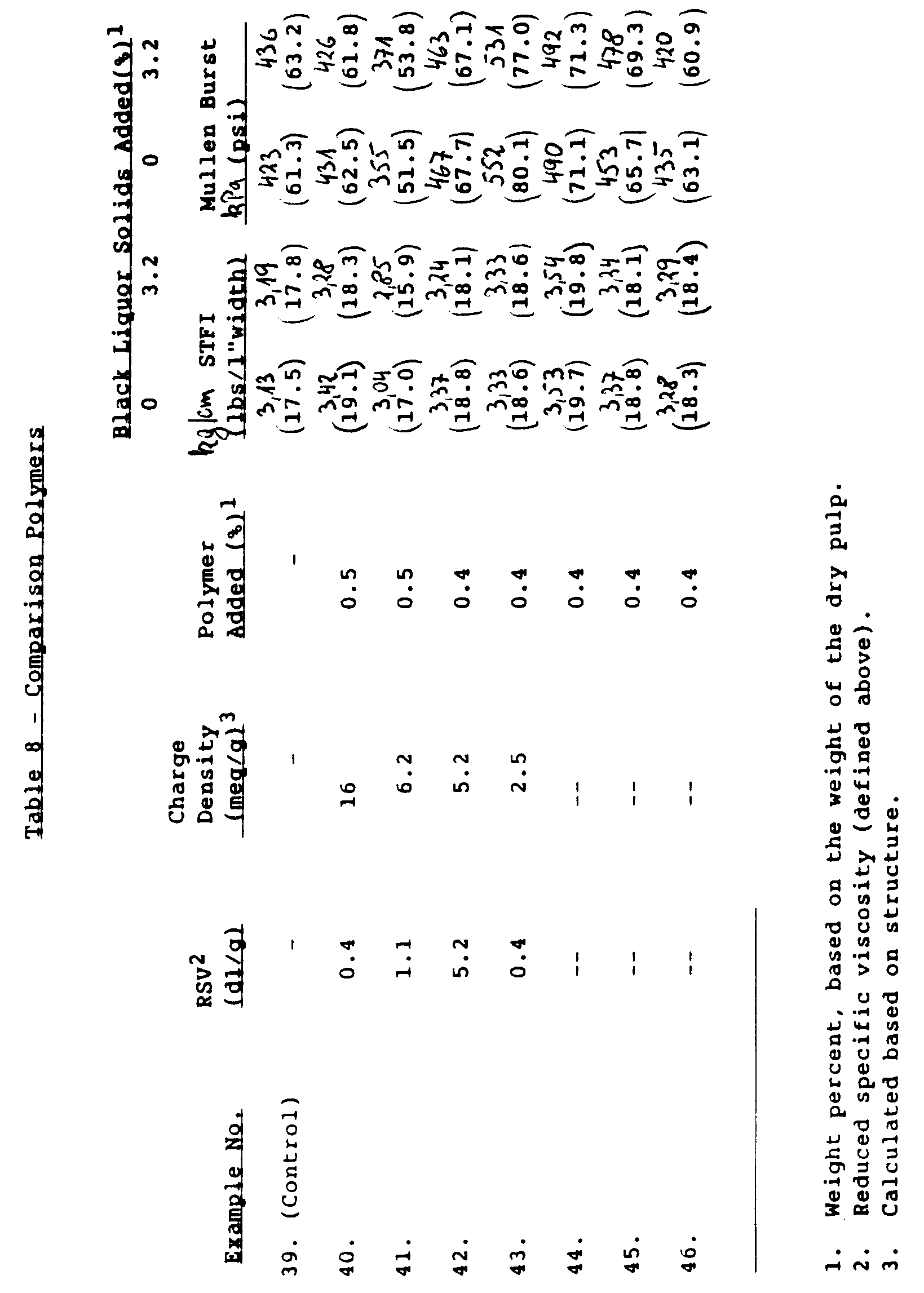
[0076] In almost every instance of using the comparative cationic polymers, either or both
of STFI and Mullen Burst properties were worse when black liquor was present during
the preparation of paper compared to when black liquor was not present; this, despite
the fact that superior results were obtained by merely adding black liquor in the
control (absence of a cationic polymer). In one instance (sample 44), negligible improvement
occurred.
Examples 47-49
[0077] The following examples demonstrate a preferred embodiment of this invention in which
two aqueous systems comprising components are prepared, heated to greater than 75°C,
mixed and cooled to less than about 60°C.
[0078] Separately, 196 g of a 0.5 weight percent solution of a copolymer of acrylamide and
diallyldimethylammonium chloride (6 mole %) and 200 g of a solution containing the
amount of Marasperse® N-3 sodium lignin sulfonate (Reed Lignin Inc., Greenwich, CT)
listed in the following table (no sodium lignin sulfonate was used in control example
47) were heated to 80°C. The two solutions were added to a baffled, heated vessel
and mixed with a Cowles disperser blade for 5 minutes at 750 rpm, while the temperature
was maintained at 80°C, and then the resulting aqueous system was allowed to cool
to room temperature. The results are shown in Table 9 below.
Table 9
Ex. |
Anionic Charge Fraction |
Sodium Lignin Sulfonate(g) |
Nature of Polyelectrolyte Complex |
Brookfield Viscosity¹ |
47 |
0 |
0 |
None formed |
37 mPas (cps) |
48 |
0.6 |
0.993 |
0.6 micrometer colloidal particle |
5.7 mPas (cps) |
49 |
0.8 |
2.648 |
soluble |
4.6 mPas (cps) |
Examples 50-54
[0079] In order to study the properties of paper prepared using the complexes of Examples
48 and 49, and complexes prepared by adding the anionic and cationic components directly
to a papermaking system, the procedures of Examples 1 - 6 were repeated using the
cationic polymer at an addition level of 0.5 weight %, by weight of dry pulp. A control
sample was prepared without using an additive. The results are shown in Table 10 below.
Table 10
Ex. |
Additive |
STFI Compression kg/cm (lbs/in) |
Mullen Burst kPa (psi) |
50 |
Control (none) |
2,67 (14.9) |
290 (42) |
51 |
Complex of Example 48 |
3,15 (17.6) |
607 (88) |
52 |
Components used in Example 48¹ |
3,26 (18.2) |
496 (72) |
53 |
Complex of Example 49 |
3,49 (19.5) |
627 (91) |
54 |
Components used in Example 49¹ |
3,20 (17.9) |
565 (82) |
1. The components were added directly to the papermaking system, as 0.5% aqueous solutions,
with the anionic component being added prior to the cationic. |
[0080] The above table shows that premixing the components at above 75°C and cooling them
to less than about 60°C does not significantly effect complex performance at an anionic
charge fraction of 0.6, but results in superior performance at a charge fraction of
0.8. Thus, this comparison demonstrates the superiority of the water-soluble polyelectrolyte
complexes of this preferred embodiment.
Examples 55-56
[0081] The following examples demonstrate a preferred embodiment of this invention.
[0082] A dry powder was prepared by mixing 0.98 g of copolymer of acrylamide and diallyldimethylammonium
chloride (6 mole %) and the amount of Marasperse® N-3 sodium lignin sulfonate (Reed
Lignin Inc., Greenwich, CT) listed in the following table. The dry powder mixture
was then added to 200 g of water that had been heated to 80°C and the mixture was
stirred using a Cowles disperser blade in a baffled, heated vessel for 5 minutes at
750 rpm, while the temperature was maintained at 80°C, and then allowed to cool to
room temperature. The results are shown in Table 11, below.
Table 11
Ex. |
Anionic Charge Fraction |
Sodium Lignin Sulfonate(g) |
Nature of Polyelectrolyte Complex |
Brookfield Viscosity¹ |
55 |
0.5 |
0.66 |
colloidal particle |
not measured |
56 |
0.8 |
2.65 |
soluble |
5 mPas (cps) |
[0083] The properties of the polyelectrolyte complex of Example 56 are similar to those
of the polyelectrolyte complex of example 49, indicating that they are essentially
the same. Therefore, performance would be similar to that of Example 53.
From all of the above examples, it can be seen that the polyelectrolyte complex of
the instant invention provides improved dry strength, particularly in papers prepared
with unbleached pulp and black liquor. Therefore, the polyelectrolyte complex of this
invention is suitable for use as dry strength additive in all types of paper and is
particularly useful as a dry strength additive for unbleached paper and paper board.
1. A mixture of water-soluble cationic and anionic polymers useful as a strengthening
additive in papermaking processes, characterized in that it comprises a linear, cationic
polymer having a reduced specific viscosity (0.05 weight % in a 2 M NaCl solution
at 30°C) greater than 2 dl/g and a charge density of 0.2 to 4 meq/g, and an anionic
polymer having a charge density of less than 5 meq/g that is reactable in the presence
of water with the cationic polymer to form a polyelectrolyte complex.
2. A mixture of cationic and anionic polymers as claimed in claim 1, further characterized
in that the cationic polymer has a reduced specific viscosity of 10 to 25 dl/g.
3. A mixture of cationic and anionic polymers as claimed in claim 1 or 2, further characterized
in that the cationic polymer has a charge density of 0.5 to 1.5 meq/g.
4. A mixture of cationic and anionic polymers as claimed in claim 1, 2, or 3, further
characterized in that the cationic polymer is selected from the group consisting of
cationic guar and copolymers of acrylamide and diallyldimethylammonium chloride, acryloyloxyethyltrimethylammonium
chloride, methacryloyloxyethyltrimethylammonium methylsulfate, methacryloyloxyethyltrimethylammonium
chloride and methacrylamidopropyltrimethylammonium chloride.
5. A mixture of cationic and anionic polymers as claimed in claim 4, further characterized
in that the cationic polymer is selected from the group consisting of copolymers of
acrylamide and diallyldimethylammonium chloride and methacryloyloxyethyltrimethyl
ammonium chloride.
6. A mixture of cationic and anionic polymers as claimed in any of the preceding claims,
further characterized in that the anionic polymer is selected from the group consisting
of copolymers of acrylamide and sodium acrylate, sodium methacrylate and sodium-2-acrylamide-2-
methylpropane sulfonate, sodium carboxymethyl cellulose, sodium carboxymethyl guar,
sodium alginate, sodium polypectate and poly(sodium-2-acrylamide-2-methylpropane sulfonate).
7. A mixture of cationic and anionic polymers as claimed in any of the preceding claims,
further characterized in that the polymer mixture is in the form of a polyelectrolyte
complex.
8. A mixture of cationic and anionic polymers as claimed in claim 7, further characterized
in that the polyelectrolyte complex has an anionic charge fraction of 0.1 to 0.98.
9. A mixture of cationic and anionic polymers as claimed in claim 7, further characterized
in that the polyelectrolyte complex has an anionic charge fraction of 0.3 to 0.8.
10. A mixture of cationic and anionic polymers as claimed in claim 7, further characterized
in that the polyelectrolyte complex has an anionic charge fraction of 0.65 to 0.85.
11. A mixture of cationic and anionic polymers as claimed in claim 7, further characterized
in that the polyelectrolyte complex has an anionic charge fraction of 0.45 to 0.6
and is fibrous.
12. A mixture of cationic and anionic polymers as claimed in any of the preceding claims,
further characterized in that the weight ratio of the cationic polymer to the anionic
polymer is 4:100 to 40:1.
13. A mixture of cationic and anionic polymers as claimed in claim 12, further characterized
in that the the weight ratio of the cationic polymer to the anionic polymer is 1:4
to 4:1.
14. A process for making the mixture of cationic and anionic polymers as claimed in any
of claims 1 to 13, whereby the cationic polymer and the anionic polymer are added
to water having a temperature of at least about 75°C and the resultant aqueous system
is cooled to less than about 60°C.
15. Use of the mixture of cationic and anionic polymers according to any of claims 1-13,
in a process for making paper whereby said mixture is incorporated into a conventional
aqueous suspension of cellulosic fibers.
16. A process for improving the dry strength of paper, wherein a water-soluble, cationic
polymer is incorporated into a conventional aqueous suspension of cellulosic fibers
in which the suspension of cellulosic fibers contains a water-soluble, anionic polymer,
whereafter the fibers are sheeted and dried to form the cellulosic web, characterized
in that the cationic polymer is a linear polymer having a reduced specific viscosity
(0.05 weight % in a 2 M NaCl solution at 30°C) greater than 2 dl/g and a charge density
of 0.2 to 4 meq/g and is incorporated into the suspension of cellulosic fibers in
an amount of 0.1 to 5 %, by dry weight of the fibers and in that the anionic polymer
has a charge density of less than 5 meq/g.
17. A process as claimed in claim 16, characterized in that the amount of the cationic
polymer is 0.2 to 3%, by dry weight of the fibers.
18. A process as claimed in claim 16, characterized in that the amount of the cationic
polymer is 0.1 to 2.5%, based on the dry weight of the fibers.
19. A process as claimed in claim 16, 17, or 18, characterized in that the amount of the
anionic polymer is 0.1 to 5%, based on the dry weight of the fibers.
20. A process as claimed in any of claims 16 to 19, characterized in that 0.1 to 5% of
the anionic polymer, based on the dry weight of the fibers, is added to the suspension
of cellulosic fibers.
21. A process as claimed in claim 16 or 17, characterized in that the anionic polymer
is selected from the group consisting of anionic polymers present in unbleached pulps,
synthetic anionic polymers and anionically modified natural polymers.
22. A process as claimed in claim 16 comprising the steps of
(1) forming an aqueous suspension of unbleached pulp fibers containing from about
0.1 to about 5%, based on the dry weight of the pulp, of anionic polymers normally
present in unbleached pulp selected from the group consisting of solubilized lignins
and hemicelluloses, said anionic polymers having a charge density of less than 5 meq/g;
(2) adding to the pulp from about 0.1 to about 5% based on the dry weight of the pulp,
of polymer consisting essentially of at least one water-soluble, linear, high molecular
weight, low charge density cationic polymer, having a reduced specific viscosity greater
than 2 dl/g and a charge density of 0.2 to 4 meq/g, in an amount such that the polyelectrolyte
complex will form with the anionic polymer normally present in said unbleached pulp,
and forming a polyelectrolyte complex from the cationic polymer and the anionic polymers
normally present in unbleached pulp; and
(3) sheeting and drying the fibers of the pulp to form the desired cellulosic web.
1. Als Verstärkungsadditiv in Papiererzeugungsverfahren geeignetes Gemisch aus wasserlöslichen
kationischen und anionischen Polymeren, dadurch gekennzeichnet, daß es ein lineares,
kationisches Polymer mit einer reduzierten spezifischen Viskosität (0,05 Gew.-% in
einer 2 M-NaCl-Lösung bei 30°C) von über 2 dl/g und einer Ladungsdichte von 0,2 bis
4 Milliäquivalenten/g und ein anionisches Polymer mit einer Ladungsdichte von weniger
als 5 Milliäquivalenten/g, das in Anwesenheit von Wasser mit dem kationischen Polymer
unter Ausbildung eines Polyelektrolytkomplexes reaktionsfähig ist, umfaßt.
2. Gemisch aus kationischen und anionischen Polymeren nach Anspruch 1, weiterhin dadurch
gekennzeichnet, daß das kationische Polymer eine reduzierte spezifische Viskosität
von 10 bis 25 dl/g aufweist.
3. Gemisch aus kationischen und anionischen Polymeren nach Anspruch 1 oder 2, weiterhin
dadurch gekennzeichnet, daß das kationische Polymer eine Ladungsdichte von 0,5 bis
1,5 Milliäquivalenten/g aufweist.
4. Gemisch aus kationischen und anionischen Polymeren nach Anspruch 1, 2 oder 3, weiterhin
dadurch gekennzeichnet, daß das kationische Polymer aus der Gruppe ausgewählt ist,
die aus kationischem Guar und Copolymeren von Acrylamid und Diallyldimethylammoniumchlorid,
Acryloyloxyethyltrimethylammoniumchlorid, Methacryloyloxyethyltrimethylammoniummethylsulfat,
Methacryloyloxyethyltrimethylammoniumchlorid und Methacrylamidopropyltrimethylammoniumchlorid
besteht.
5. Gemisch von kationischen und anionischen Polymeren nach Anspruch 4, weiterhin dadurch
gekennzeichnet, daß das kationische Polymer aus der aus Copolymeren von Acrylamid
mit Diallyldimethylammoniumchlorid und Methacryloyloxyethyltrimethylammoniumchlorid
bestehenden Gruppe ausgewählt ist.
6. Gemisch aus kationischen und anionischen Polymeren nach einem der vorstehenden Ansprüche,
weiterhin dadurch gekennzeichnet, daß das anionische Polymer aus der Gruppe ausgewählt
ist, die aus Copolymeren von Acrylamid und Natriumacrylat, Natriummethacrylat und
Natrium-2-acrylamid-2-methylpropansulfonat, Natriumcarboxymethylcellulose, Natriumcarboxymethylguar,
Natriumalginat, Natriumpolypectat und Poly(natrium-2-acrylamid-2-methylpropansulfonat)
besteht.
7. Gemisch aus kationischen und anionischen Polymeren nach einem der vorstehenden Ansprüche,
weiterhin dadurch gekennzeichnet, daß das Polymergemisch in Form eines Polyelektrolytkomplexes
vorliegt.
8. Gemisch aus kationischen und anionischen Polymeren nach Anspruch 7, weiterhin dadurch
gekennzeichnet, daß der Polyelektrolytkomplex einen anionischen Ladungsanteil von
0,1 bis 0,98 aufweist.
9. Gemisch aus kationischen und anionischen Polymeren nach Anspruch 7, weiterhin dadurch
gekennzeichnet, daß der Polyelektrolytkomplex einen anionischen Ladungsanteil von
0,3 bis 0,8 aufweist.
10. Gemisch aus kationischen und anionischen Polymeren nach Anspruch 7, weiterhin dadurch
gekennzeichnet, daß der Polyelektrolytkomplex einen anionischen Ladungsanteil von
0,65 bis 0,85 aufweist.
11. Gemisch aus kationischen und anionischen Polymeren nach Anspruch 7, weiterhin dadurch
gekennzeichnet, daß der Polyelektrolytkomplex einen anionischen Ladungsanteil von
0,45 bis 0,6 aufweist und faserig ist.
12. Gemisch aus kationischen und anionischen Polymeren nach einem der vorstehenden Ansprüche,
weiterhin dadurch gekennzeichnet, daß das Gewichtsverhältnis des kationischen Polymers
zum anionischen Polymer 4:100 bis 40:1 beträgt.
13. Gemisch aus kationischen und anionischen Polymeren nach Anspruch 12, weiterhin dadurch
gekennzeichnet, daß das Gewichtsverhältnis des kationischen Polymers zum anionischen
Polymer 1:4 bis 4:1 beträgt.
14. Verfahren zur Ausbildung des Gemisches aus kationischen und anionischen Polymeren
nach einem der Ansprüche 1 bis 13, wobei das kationische Polymer und das anionische
Polymer zu Wasser mit einer Temperatur von wenigstens etwa 75°C zugesetzt werden und
das resultierende wäßrige System auf unter etwa 60°C abgekühlt wird.
15. Verwendung des Gemisches aus kationischen und anionischen Polymeren nach einem der
Ansprüche 1 bis 13 in einem Papiererzeugungsprozeß, wobei dieses Gemisch in eine konventionelle
wäßrige Suspension von Zellulosefasern aufgenommen wird.
16. Verfahren zur Verbesserung der Trockenfestigkeit von Papier, wobei ein wasserlösliches
kationisches Polymer in eine konventionelle wäßrige Suspension von Zellulosefasern
aufgenommen wird, worin die Suspension von Zellulosefasern ein wasserlösliches anionisches
Polymer enthält, wonach die Fasern in Blattform gebracht und zur Ausbildung der Zellulosebahn
getrocknet werden, dadurch gekennzeichnet, daß das kationische Polymer ein lineares
Polymer mit einer reduzierten spezifischen Viskosität (0,05 Gew.-% in einer 2M NaCl-Lösung
bei 30°C) von über 2 dl/g und einer Ladungsdichte von 0,2 bis 4 Milliäquivalenten/g
ist und in die Suspension von Zellulosefasern in einer Menge von 0,1 bis 5 %, bezogen
auf das Trockengewicht der Fasern, eingebracht wird und daß das anionische Polymer
eine Ladungsdichte von unter 5 Milliäquivalenten/g aufweist.
17. Verfahren nach Anspruch 16, dadurch gekennzeichnet, daß die Menge des kationischen
Polymers 0,2 bis 3 %, bezogen auf das Trockengewicht der Fasern, beträgt.
18. Verfahren nach Anspruch 16, dadurch gekennzeichnet, daß die Menge des kationischen
Polymers 0,1 bis 2,5 %, bezogen auf das Trockengewicht der Fasern, beträgt.
19. Verfahren nach Anspruch 16, 17 oder 18, dadurch gekennzeichnet, daß die Menge des
anionischen Polymers 0,1 bis 5%, bezogen auf das Trockengewicht der Fasern, beträgt.
20. Verfahren nach einem der Ansprüche 16 bis 19, dadurch gekennzeichnet, daß 0,1 bis
5 % des anionischen Polymers, bezogen auf das Trockengewicht der Fasern, zu der Zellulosefasersuspension
zugesetzt werden.
21. Verfahren nach Ansopruch 16 oder 17, dadurch gekennzeichnet, daß das anionische Polymer
aus der Gruppe ausgewählt wird, die aus in ungebleichten Pulpen vorliegenden anionischen
Polymeren, synthetischen anionischen Polymeren und anionisch modifizierten natürlichen
Polymeren besteht.
22. Verfahren nach Anspruch 16, umfassend die folgenden Stufen:
(1) Ausbilden einer wäßrigen Suspension aus ungebleichten Pulpefasern mit einem Gehalt
an etwa 0,1 bis etwa 5%, bezogen auf das Trockengewicht der Pulpe, an anionischen
Polymeren, die normalerweise in ungebleichter Pulpe vorliegen,ausgewählt aus der aus
solubilisierten Ligninen und Hemizellulosen bestehenden Gruppe, welche anionischen
Polymere eine Ladungsdichte von unter 5 Milliäquivalenten aufweisen;
(2) Zusetzen von etwa 0,1 bis etwa 5 %, bezogen auf das Trockengewicht der Pulpe,
eines Polymers zu der Pulpe, welches Polymer im wesentlichen aus wenigstens einem
wasserlöslichen linearen hochmolekularen kationischen Polymer niedriger Ladungsdichte
mit einer reduzierten spezifischen Viskosität von über 2 dl/g und einer Ladungsdichte
von 0,2 bis 4 Milliäquivalenten besteht, in einer solchen Menge, daß sich mit dem
normalerweise in der ungebleichten Pulpe vorliegenden anionischen Polymer der Polyelektrolytkomplex
ausbilden wird, und Ausbilden eines Polyelektrolytkomplexes aus dem kationischen Polymer
und den normalerweise in ungebleichter Pulpe vorliegenden anionischen Polymeren; und
(3) Überführen in Blattform und Trocknen der Fasern der Pulpe zur Ausbildung der gewünschten
Zellulosebahn.
1. Mélange de polymères cationiques et anioniques hydrosolubles utiles en tant qu'additif
de renforcement dans des procédés de fabrication du papier, caractérisé en ce qu'il
comprend un polymère cationique linéaire ayant une viscosité spécifique réduite (0,05%
en poids dans une solution de NaCl 2M à 30°C) supérieure à 2 dl/g et une densité de
charge de 0,2 à 4 méq/g, et un polymère anionique ayant une densité de charge inférieure
à 5 méq/g qui peut réagir en présence d'eau avec le polymère cationique pour former
un complexe polyélectrolyte.
2. Mélange de polymères cationiques et anioniques selon la revendication 1, caractérise
de plus en ce que le polymère cationique possède une viscosité spécifique réduite
de 10 à 25 dl/g.
3. Mélange de polymères cationiques et anioniques selon la revendication 1 ou 2, caractérisé
de plus en ce que le polymère cationique possède une densité de charge de 0,5 à 1,5
méq/g.
4. Mélange de polymères cationiques et anioniques selon la revendication 1, 2 ou 3, caractérisé
de plus en ce que le polymère cationique est choisi dans le groupe formé par la gomme
guar cationique et les copolymères d'acrylamide et de chlorure de diallyldiméthylammonium,
de chlorure d'acryloyloxyéthyltriméthylammonium, de méthylsulfate de méthacryloyloxyéthyltriméthylammonium,
de chlorure de méthacryloyloxyéthyltriméthylammonium,et de chlorure de méthacrylamidopropyltriméthylammonium.
5. Mélange de polymères cationiques et anioniques selon la revendication 4, caractérisé
de plus en ce que le polymère cationique est choisi dans le groupe formé par les copolymères
d'acrylamide et de chlorure de diallyldiméthylammonium et de chlorure de méthacryloyloxyéthyltriméthylammonium.
6. Mélange de polymères cationiques et anioniques selon l'une quelconque des revendications
précédentes, caractérisé de plus en ce que le polymère anionique est choisi dans le
groupe formé par des copolymères d'acrylamide et d'acrylate de sodium, de méthacrylate
de sodium et de 2-acrylamide-2-méthylpropanesulfonate de sodium, de carboxyméthylcellulose
de sodium, de carboxyméthylguar de sodium, d'alginate de sodium, de polypectate de
sodium et de poly(2-acrylamide-2-méthylpropanesulfonate de sodium).
7. Mélange de polymères cationiques et anioniques selon l'une quelconque des revendications
précédentes, caractérisé de plus en ce que le mélange polymère est sous forme d'un
complexe polyélectrolyte.
8. Mélange de polymères cationiques et anioniques selon la revendication 7, caractérisé
de plus en ce que le complexe polyélectrolyte possède une fraction de charge anionique
de 0,1 à 0,98.
9. Mélange de polymères cationiques et anioniques selon la revendication 7, caractérisé
de plus en ce que le complexe polyélectrolyte possède une fraction de charge anionique
de 0,3 à 0,8.
10. Mélange de polymères cationiques et anioniques selon la revendication 7, caractérisé
de plus en ce que le complexe polyélectrolyte possède une fraction de charge anionique
de 0,65 à 0,85.
11. Mélange de polymères cationiques et anioniques selon la revendication 7, caractérisé
de plus en ce que le complexe polyélectrolyte possède une fraction de charge anionique
de 0,45 à 0,6 et est fibreux.
12. Mélange de polymères cationiques et anioniques selon l'une quelconque des revendications
précédentes, caractérisé de plus en ce que le rapport pondéral du polymère cationique
au polymère anionique est de 4:100 à 40:1.
13. Mélange de polymères cationiques et anioniques selon la revendication 12, caractérisé
de plus en ce que le rapport pondéral du polymère cationique au polymère anionique
est de 1:4 à 4:1.
14. Procédé pour fabriquer le mélange de polymères cationiques et anioniques selon l'une
quelconque des revendications 1 à 13, dans lequel le polymère cationique et le polymère
anionique sont ajoutés à l'eau ayant une température d'au moins environ 75°C et le
système aqueux résultant est refroidi à moins d'environ 60°C.
15. Utilisation du mélange de polymères anioniques et cationiques selon l'une quelconque
des revendications 1 à 13, dans un procédé pour fabriquer du papier consistant à incorporer
ledit mélange dans une suspension aqueuse classique de fibres cellulosiques.
16. Procédé pour améliorer la résistance à sec de papier, dans lequel un polymère cationique
hydrosoluble est incorporé dans une suspension aqueuse classique de fibres cellulosiques,
dans lequel la suspension de fibres cellulosiques contient un polymère anionique hydrosoluble,
après quoi les fibres sont mises sous forme de feuilles et séchées pour former la
toile cellulosique, caractérisé en ce que le polymère cationique est un polymère linéaire
ayant une viscosité spécifique réduite (0,05% en poids dans une solution de NaCl 2M
à 30°C) supérieure à 2 dl/g et une densité de charge de 0,2 à 4 méq/g et est incorporé
dans la suspension de fibres cellulosiques à raison de 0,1 à 5%, en poids sec des
fibres et en ce que le polymère anionique possède une densité de charge inférieure
à 5 méq/g.
17. Procédé selon la revendication 16, caractérisé en ce que la quantité du polymère cationique
est de 0,2 à 3%, en poids sec des fibres.
18. Procédé selon la revendication 16, caractérisé en ce que la quantité du polymère cationique
est de 0,1 à 2,5%, par rapport au poids sec des fibres.
19. Procédé selon la revendication 16, 17 ou 18, caractérisé en ce que la quantité du
polymère anionique est de 0,1 à 5%, par rapport au poids sec des fibres.
20. Procédé selon l'une quelconque des revendications 16 à 19, caractérisé en ce que 0,1
à 5% du polymère anionique, par rapport au poids sec des fibres,sont ajoutés à la
suspension de fibres cellulosiques.
21. Procédé selon la revendication 16 ou 17, caractérisé en ce que le polymère anionique
est choisi dans le groupe formé par les polymères anioniques présents dans des pâtes
à papier non blanchies, les polymères anioniques synthétiques et les polymères naturels
anioniquement modifiés.
22. Procédé selon la revendication 16 comprenant les étapes consistant:
(1) à former une suspension aqueuse de fibres de pâte à papier non blanchie contenant
d'environ 0,1 à environ 5%, par rapport au poids sec de la pâte à papier, de polymères
anioniques normalement présents dans la pâte à papier non blanche choisis dans le
groupe constitué des lignines solubilisées et des hémicelluloses, lesdits polymères
anioniques ayant une densité de charge inférieure à 5 méq/g;
(2) à ajouter à la pâte à papier d'environ 0,1 à environ 5% par rapport au poids sec
de la pâte à papier, de polymère constitué essentiellement d'au moins un polymère
cationique de masse moléculaire élevée, linéaire, hydrosoluble, à densité de charge
faible, ayant une viscosité spécifique réduite supérieure à 2 dl/g et une densité
de charge de 0,2 à 4 méq/g, en une quantité telle que le complexe polyélectrolyte
se formera avec le polymère anionique normalement présent dans ladite pâte à papier
non blanchie, et à former un complexe polyélectrolyte à partir du polymère cationique
et des polymères anioniques normalement présents dans la pâte à papier non blanchie;
(3) à mettre sous forme de feuilles et à sécher les fibres de la pâte à papier pour
former la toile cellulosique souhaitée.