[0001] The present invention relates to a method of manufacturing steel sheets having excellent
deep-drawability which may be used in manufacturing automobile bodies. In particular,
the present invention relates to a method of manufacturing hot-rolled steel sheets
having excellent deep-drawability, as well as to a method of manufacturing surface-treated
steel sheets.
Description of the Background Art
[0002] When steel sheets are prepared for deep drawing for subsequent use in manufacturing
automobile bodies, they are required to have high Lankford values (r-values) and a
high ductility (El: Elongation value). Such steel sheet has generally been prepared
as cold-rolled steel sheet, manufactured by hot rolling which is terminated at temperatures
not lower than the Ar3 transformation point, subsequently obtaining the final thickness
by cold rolling, and thereafter effecting recrystallization annealing. In recent years,
however, there have been increasing demands for the substitution of members previously
formed of cold-rolled steel sheet with those formed of hot-rolled steel sheet, in
order to reduce production costs.
[0003] Hot-rolled steel sheet for use in working has previously been prepared by terminating
rolling at temperatures not lower than the Ar3 transformation point so as to avoid
formation of non-recrystallized ferrite. In this way satisfactory working properties,
in particular ductility, are assured. However, since random orientation usually occurs
in the texture during the y to a transformation, a hot-rolled steel sheet has considerably
poor deep-drawability when compared with cold-rolled steel sheet. Hitherto, the r-value
of hot-rolled steel sheet has ranged from 0.8 to 0.9 at most.
[0004] Recently, however, several methods of obtaining hot-rolled steel sheet excellent
in deep-drawability have been proposed, in which no cold rolling is required. For
instance, Japanese Patent Laid-Open No. 226149/1984 discloses an example of a hot-rolled
steel sheet having an r-value of 1.21 which is manufactured by subjecting low-carbon
AI killed steel containing C: 0.002 %, Si: 0.02 %, Mn: 0.23 %, P: 0.009 %, S: 0.008
%, Al: 0.025 %, N: 0.0021 %, and Ti: 0.10 % to rolling at a reduction of 76 % and
at temperatures ranging from 500 to 900
° C while a lubricant is supplied, so as to obtain a steel strip having a thickness
of 1.6 mm. In this method, however, because strong lubricated rolling must be effected
during hot rolling, this inevitably involves some operational problems such as the
risk of slipping occurring in the steel blank during rolling. Japanese Patent Laid-Open
No. 192539/1987 discloses an example of a hot-rolled steel sheet having an r-value
of 1.41 which is manufactured by subjecting low-carbon AI killed steel containing
C: 0.008 %, Si: 0.04 %, Mn: 1.53 %, P: 0.015 %, S: 0.004 %, Ti: 0.068 %, and Nb: 0.024
% to rolling at a reduction of 92 % and at temperatures ranging from the Ar3 transformation
point to the Ar3 transformation point + 150 ° C. In this method, however, because
hot rolling is terminated at a temperature within the γ-phase range, and the transformed
tissue resulting from the subsequent γ to α transformation is utilized, this inevitably
has a preferred orientation of
{112}. As a result, the value of Ar that is indicative of planar anisotropy of the
r-value becomes so great that Ar = - 1.2. This is detrimental in practice.
[0005] In order to ensure excellent deep-drawability, a method must achieve an r-value of
r 1.4 at least, without involving operational problems whilst conducting hot rolling,
and without causing anisotropy.
[0006] There have recently been increasing demands for a surface-treated steel sheet having
surfaces which have been subjected to various kinds of surface treatments for use
in the manufacture of automobile bodies. Among various types of surface-treated steel
sheets, one of the more superior is hot dip galvanized sheet because it is advantageous
both in terms of its production cost and its properties.
[0007] Hot dip galvanized steel sheet is required to possess various properties, one of
the most important being excellent corrosion resistance, while deep-drawability is
another important requirement. Since outside and inside panels of automobiles are
usually formed by strong press working, the galvanized sheet must possesses both a
high Lankford value (r-value) and a high level of elongation.
[0008] A method of manufacturing such a galvanized sheet possessing excellent deep-drawability
is disclosed in, for instance, Japanese Patent Laid-Open No. 29555/1982. This patent
publication discloses attaining properties of the order of r = 2.0 and EI = 49 % by
subjecting a steel containing C: 0.006 wt % ("wt %" will hereinafter be abbreviated
to "%"), N: 0.0045 %, Si: 0.008 %, and Nb: 0.043 % to hot rolling, pickling and cold
rolling, and further subjecting the steel to recrystallization annealing and plating
in a continuous galvanizing line. Japanese Patent Laid-Open No. 74231/1984 discloses
attaining properties of the order of r = 2.1 and EI = 51 % by subjecting a steel containing
C: 0.003 %, N: 0.005 %, Si: 0.010 %, Ti: 0.012 %, and Nb: 0.007 % to hot rolling,
pickling and cold rolling, and further subjecting the steel to recrystallization annealing
and plating in a continuous galvanizing line.
[0009] Although each of these methods is successful in manufacturing a galvanized sheet
possessing excellent deep-drawability, it is still necessary to perform a long series
of processes before the final product is obtained. This means that great amounts of
energy, labour and time must be consumed in order to manufacture such galvanised sheet.
[0010] EPA 0196788 discloses a method of manufacturing formable steel sheets without the
need for cold rolling. The hot rolling of this method is performed at a draft of 35%
or more under conditions of a high strain rate and the steel sheets are made from
low carbon steel which may optionally contain B, Ti and Nb. This patent does not,
however, recognise the importance of controlling the coefficient of friction during
the rolling process.
[0011] An object of the present invention is to provide a method of obtaining a steel sheet
suitable for use in deep drawing which possesses a high Lankford value (r-value) of
r 1.4, when hot rolled.
[0012] Another object of the present invention is to provide a method of obtaining a steel
sheet suitable for use in deep drawing which does not suffer from cold-working embrittlement.
[0013] Still another object of the present invention is to provide a method of obtaining
a surface-treated steel sheet having excellent deep-drawability.
[0014] According to the present invention as set out in claim 1, there is provided a method
of manufacturing a steel sheet having excellent deep-drawability, the method including
the step of rolling a steel sheet of known thickness such that the rolling reduction
at temperatures below the Ar3 transformation point is not less than 60%, the rolling
including at least one pass in which the rolling is conducted at a temperature of
from not less than 500
° C to less than the Ar3 transformation point and in which the relationship between
the known thickness of the steel sheet before rolling t (mm), the roll radius R (mm)
and the coefficient of friction µ, satisfy the following conditions:
R 200,
R2√t ≦ 100000, and
µ ≦ - 0.2 log (R/t) + 0.55,
wherein the steel sheet contains:
not more than 0.008% by weight C,
not more than 0.5% by weight Si,
not more than 1.0% by weight Mn,
not more than 0.15% by weight P,
not more than 0.02% by weight S,
not more than 0.008% by weight N,
not less than 0.010 to not more than 0.10% by weight Al,
at least one of Ti and Nb in an amount satisfying the relationship,
1.2 (C/12 + N/14) (Ti/48 + Nb/93),
and optionally from not less than 0.0001 to not more 0.0020% by weight B and from
not less than 0.001 to not more 0.020% by weight Sb,
the balance being iron and incidental impurities. Preferred embodiments of the method
according to claim 1 are given in the dependent claims 2 to 8.
[0015] For a better understanding of the invention and to show how the same may be carried
into effect, reference will now be made by way of example only to the accompanying
drawings in which:
Fig. 1 is a graph used to explain the influence of the roll radius R on the r-value;
Fig. 2 is a graph used to explain the influence of the parameter R2 √t (t being the thickness before rolling) on the r-value;
Fig. 3 is a graph used to explain the influence of the parameter t/R4 on the r-value;
Fig. 4 is a graph used to explain the influence of the coefficient of friction on
the r-value; and
Fig. 5 is a graph used to explain the influence of the parameter log(R/t) on the r-value.
[0016] The rolling conditions, and the chemical compositions of the steels used in the present
invention, have been chosen on the basis of experimental results:
a. Conditions of Rolling at a Temperature lower than the Ar3 Transformation Point
(1) Relationship between roll radius or blank thickness with the r-value:
[0017] In a series of experiments, a hot-rolled blank having the chemical composition including
C: 0.002%, Si: 0.01%, Mn: 0.1%, P: 0.012%, S: 0.012 %, N: 0.002%, Ti: 0.04%, and Nb:
0.010% was heated and soaked at 700
° C, rolled at a reduction of 60% in one pass, and continuously subjected to self-annealing
at 700
° C for 1 hour which was effected simultaneously with coiling. The final rolling was
effected without using a lubricant. The initial thickness t was set at 1.2 mm. In
these experiments, the radius R of the rolls used in the rolling was varied from 50
to 300 mm. Fig. 1 shows the results obtained; that is, the influence on the r-value
of the resultant hot-rolled sheet by the roll radius R. As shown in Fig. 1, the r-value
changes with changes in the roll radius R. If R (mm) ≦ 200, the r-value is improved
remarkably.
[0018] In another series of experiments, a hot-rolled blank, having the same chemical composition,
was subsequently subjected to heat-soaking at 700 ° C, to 60 %-reduction rolling in
one pass, and, continuously therefrom, to coiling-simultaneous self-annealing at 700
° C for 1 hour. The final rolling was a non-lubricated rolling. In these experiments,
the radius R of the rolls used was fixed at 180 mm, while the initial thickness t
was varied from 1 to 20 mm. Fig. 2 illustrates the influence on the r-value of the
resultant hot-rolled sheet by the parameter R
2 √t where R is the roll radius and t is the initial thickness. As shown in Fig. 2,
the r-value changes with changes in R
2√t. If R
2 √t ≦ 100000, the r-value is improved remarkably.
[0019] The above-mentioned rolling conditions are specified on the basis of the following
finding: if rolling is conducted at a temperature lower than the Ar3 transformation
point while employing ordinary rolling conditions (wherein R (mm) > 300 in the case
of hot rolling), force resulting from friction between the rolls and the steel being
processed causes an additional shearing force to act on a surface layer of the steel.
As a result, the {110} orientation, which is not favorable for the achievement of
high deep-drawability, is preferred in the surface layer of the steel. In this case,
therefore, the resultant steel sheet possesses poor deep-drawability. In contrast,
it has been determined from experiments that, if the relationships of R (mm) ≦ 200
and R
2√t ≦ 100000 are satisfied, it is possible to reduce the level of occurrence of the
{110} orientation in the surface layer of the steel and, simultaneously, to increase
the level of occurrence of the {111} orientation, which is favorable to the improvement
of the r-value. For this reason, the relationships of R (mm) ≦ 200 and R
2√t ≦ 100000 are specified as rolling conditions.
[0020] In a further series of experiments, a hot-rolled blank having the chemical composition
including C: 0.002 %, Si: 0.02 %, Mn: 0.1 %, P: 0.011 %, S: 0.013 %, N: 0.002 %, Ti:
0.04 %, and Nb: 0.013 % was subjected to 60 %-reduction rolling at 700
° C in one pass, and was continuously subjected to coiling-simultaneous self-annealing
at 700 ° C for 1 hour. The final rolling was a non-lubricated rolling. In these experiments,
the initial thickness t was varied between 1 and 30 mm while the radius R of the rolls
used was varied between 100 and 350 mm. Fig. 3 shows the influence on the r-value
of the resultant hot-rolled sheet of the roll radius R and the initial thickness t.
As shown in Fig. 3, the r-value changes with changes in the parameter t/R
4. If t/R
4 ≧ 6 x 10
-10, the r-value is improved remarkably.
[0021] In a rolling mill having a plurality of stands, the roll radius R in rolls of the
downstream stands (e.g., in the rolls of the downstream 2 stands in a 6-stand mill,
or rolls of the downstream 3 stands in a 7-stand mill) may be set to satisfy R (mm)
≦ 200.
(2) Relationship between coefficient of friction and r-value:
[0022] The roll radius R (mm), the initial thickness t (mm) and the coefficient of friction
µ should satisfy the relationship of µ ≦ - 0.2 log(R/t) + 0.55.
[0023] In a series of experiments, a hot-rolled blank having the chemical composition including
C: 0.002 %, Si: 0.02 %, Mn: 0.1 %, P: 0.011 %, S: 0.013 %, N: 0.002 %, Ti: 0.04 %,
and Nb: 0.013 % was subjected to 60 %-reduction rolling at 700
° C in one pass, and it was continuously subjected to coiling-simultaneous self-annealing
at 700
° C for 1 hour. In these experiments, while the radius R of the rolls used was fixed
at 300 mm and the initial thickness t was fixed at 3 mm, the lubricating condition
during rolling was varied in such a manner that the coefficient of friction µ varied
within the range from 0.1 to 0.25. Fig. 4 illustrates the influence on the r-value
of the resultant hot-rolled sheet of the coefficient of friction u. As shown in Fig.
4, the r-value changes with changes in the coefficient of friction µ. If µ ≦ 0.15,
the r-value is improved remarkably.
[0024] Subsequently, log(R/t) was varied by changing the roll radius R and the initial thickness
t, while the coefficient of friction µ remained fixed at 0.15. Fig. 5 illustrates
the influence of log(R/t) on the r-value of the hot-rolled steel sheet after annealing.
As shown in Fig. 5, the r-value changes with changes in log(R/t). If log(R/t) ≦ 2.0,
the r-value is improved remarkably.
[0025] The results of the above-described experiments have lead to the following conclusion.
If rolling is conducted at a temperature lower than the Ar3 transformation point while
employing the condition expressed as µ > - 0.2 log(R/t) + 0.55, a problem similar
to that described before arises, in which a force resulting from friction between
the rolls and the steel being processed causes an additional shearing force to act
on a surface layer of the steel. As a result, the {110} orientation, which is undesirable
for deep-drawability, is preferred in the surface layer of the steel sheet. In this
case, therefore, the resultant steel sheet possesses poor deep-drawability. In contrast,
it has been clarified from experiments that if the relationship of µ ≦ - 0.2 log(R/t)
+ 0.55 is satisfied, it is possible to reduce the level of occurrence of the {110}
orientation in the surface layer of the steel and, simultaneously, to increase the
level of occurrence of the {111} orientation, which is favorable to the improvement
of the r-value. For this reason, the relationship of µ ≦ - 0.2 log(R/t) + 0.55 should
be satisfied.
(3) Rolling reduction at a temperature lower than the Ar3 transformation point:
[0026] If rolling is effected at a temperature lower than the Ar3 transformation point at
a total reduction of less than 60 %, the {111} orientation does not occur to a sufficient
extent during rolling and a high r-value is not therefore obtained. Preferably, the
total rolling reduction should be equal to or higher than 70 %.
(4) Summary of conditions of rolling at a temperature lower than the Ar3 transformation
point:
[0027] The following can be concluded from the above-described results. The roll radius
R (mm) must satisfy the relationship of R ≦ 200 and, simultaneously, the roll radius
R and the thickness t (mm) before rolling must satisfy the relationship of R2v1t <
100000; the coefficient of friction must satisfy the relationship in which µ ≦-0.2
log(R/t) + 0.55.
[0028] Lubricated rolling should preferably be effected. This makes it possible to achieve
further improvement in deep-drawability. In addition, the surface configuration of
the rolls used can be improved, and the rolling load can be reduced.
[0029] The roll radius R and the thickness t before rolling should preferably satisfy the
relationship of t/R4 6 6 x 10-
10. If rolling is effected while this condition is adopted, it is possible to reduce
the level of occurrence of the {110} orientation in a surface layer of the steel and,
simultaneously, to increase the level of occurrence of the {111} therein, so as to
improve the r-value.
[0030] The total reduction at which rolling is effected at a temperature lower than the
Ar3 transformation point must be equal to or higher than 60 %.
b. Effect of Chemical Composition
[0031] The following explains why the proportions of various components are used in the
steels of the present invention:
(1) Carbon
[0032] Carbon (C) should be contained in as small a proportion as possible to improve deep-drawability.
If the content of C is not more than 0.008 wt %, this will not cause much adverse
influence. Therefore, the content of C is limited to a proportion of not more than
0.008 wt %.
(2) Silicon
[0033] Since silicon (Si) acts to strengthen the steel, it is added in an amount to achieve
a desired level of strength. However, if the content of Si exceeds 0.5 wt %, this
will have an adverse influence on deep-drawability. Therefore, the content of Si is
limited to a proportion of not more than 0.5 wt %.
(3) Manganese
[0034] Since manganese (Mn) acts to strengthen the steel, it is added in an amount to achive
a desired level of strength. However, if the content of Mn exceeds 1.0 wt %, this
will have an adverse influence on deep-drawability. Therefore, the content of Mn is
limited to a proportion of not more than 1.0 wt %.
(4) Phosphorus
[0035] Since phosphorus (P) acts to strengthen the steel, it is added in an amount to achive
a desired level of strength. However, if the content of P exceeds 0.15 wt %, this
will have an adverse influence on deep-drawability. Therefore, the content of P is
limited to a proportion of not more than 0.15 wt %.
(5) Sulphur
[0036] Sulphur (S) should be limited to as small a proportion as possible for improving
deep-drawability. If the content of S is not more than 0.02 wt %, this will not have
much adverse influence. Therefore, the content of S is limited to a proportion of
not more than 0.02 wt %.
(6) Aluminum
[0037] Since aluminum (Al) acts to enable deoxidation, AI is added in accordance with necessity
in order to prevent excessive consumption of carbide and nitride forming elements.
However, if AI is added in an amount not more than 0.010 wt %, no favorable effect
is provided by the addition of AI . On the other hand, if AI is added in an amount
exceeding 0.10 wt %, no further increase occurs in the extent to which the deoxidation
action is provided. Therefore, the content of Al is limited within the range from
0.010 to 0.10 wt %.
(7) Nitrogen
[0038] Nitrogen (N) should be limited to as small a proportion as possible for improving
deep-drawability. If the content of N is not more than 0.008 wt %, this will not have
much adverse influence. Therefore, the content of N is limited to a proportion of
not more than 0.008 wt %.
(8) Titanium
[0039] Titanium (Ti) is a carbide and nitride forming element which acts to reduce the amount
of solute C or N in the steel. Therefore, Ti is added in order to ensure the preferred
occurrence of the {111} orientation which is favorable to the improvement of deep-drawability.
However, if Ti is added in an amount less than 0.01 wt %, no favorable effect is provided
by such addition. On the other hand, if Ti is added in an amount exceeding 0.20 wt
%, no further increase occurs in the extent to which the effect is provided, while
there is a risk that the surface properties of the steel will be degraded. Therefore,
the content of Ti is limited to a proportion within the range from 0.01 to 0.20 wt
%.
(9) Niobium
[0040] Niobium (Nb) is a carbide forming element which acts to reduce the amount of solute
C in the steel, and which is also helpful in making a fine grain before the final
rolling. Solute Nb acts to accumulate strain applied during rolling, thereby enabling
the preferred occurrence of the {111} orientation, hence, improving the deep-drawability.
However, if Nb is added in an amount less than 0.001 wt %, no favorable effect is
obtained. On the other hand, if Nb is added in an amount exceeding 0.040 wt %, there
is a risk that the recrystallization temperature will be raised. Therefore, the content
of Nb is limited to a proportion within the range from 0.001 to 0.040 wt %.
(10) Relation between carbon, nitrogen, titanium and niobium
[0041] If there is neither solute C nor solute N before the final rolling, the {111} orientation
preferably occurs after the rolling and the subsequent annealing, thereby improving
deep-drawability. The inventors have found that, if carbon (C), nitrogen (N), titanium
(Ti) and niobium (Nb) are added in such a manner that the relationship 1.2 (C/12 +
N/14) (Ti/48 + Nb/93) is satisfied (in other words, the total of Ti and Nb is an amount
greater than the total of C and N) neither solute C nor solute N will exist before
the final rolling. It has also been determined that, in this case, the r-value is
increased. For these reasons, the relation between the contents of C, N, Ti and Nb
should satisfy the relationship 1.2 (C/12 + N/14) ≦ (Ti/48 + Nb/93).
(11) Boron
[0042] Boron (B) acts to improve resistance to cold-working embrittlement (RSWE). However,
if B is added in an amount less than 0.0001 wt %, no favorable effect is obtained.
On the other hand, if B is added in an amount exceeding 0.0020 wt %, there is a risk
that deep-drawability will be degraded. Therefore, the content of B is limited to
a proportion within the range of from 0.0001 to 0.0020 wt %.
(12) Antimony
[0043] Antimony (Sb) acts to prevent nitridation during batch annealing. However, if Sb
is added in an amount less than 0.001 wt %, no favorable effect is obtained. On the
other hand, if Sb is added in an amount exceeding 0.020 wt %, there is a risk that
deep-drawability will be degraded. Therefore, the content of Sb is limited to a proportion
within the range of from 0.001 to 0.020 wt %.
(13) Summary of chemical composition
[0044] The steel blank must have a chemical composition including C: not more than 0.008
wt %, Si: not more than 0.5 wt %, Mn: not more than 1.0 wt %, P: not more than 0.15
wt %, S: 0.02 wt %, Al: 0.010 to 0.10 wt %, N: not more than 0.008 wt %, and at least
one of Ti and Nb in an amount satisfying the relationship 1.2 (C/12 + N/14) (Ti/48
+ Nb/93). In order to improve resistance to cold-working embrittlement, B: 0.0001
to 0.0020 wt % may also be added. In order to prevent nitridation during batch annealing,
Sb: 0.001 to 0.020 wt % may also be added. If the blank steel does not have the above-specified
chemical composition, it is not possible to achieve excellent deep-drawability.
[0045] As long as the blank to be rolled has the above-specified chemical composition, it
may be a slab or sheet prepared by means of a normal continuous casting system, or
a sheet bar prepared by means of a sheet bar caster. In order to save energy, a combination
of processes CC-DR in which continuous casting and hot rolling are continuously effected
may be effectively adopted.
c. Hot Rolling Temperature Conditions
(1) Hot rolling finish temperature and coiling temperature:
[0046] According to the present invention it is important that coiling or recrystallization
annealing after the rolling process is effected under a certain condition in which
the finish delivery temperature (FDT) in hot rolling and the coiling temperature (CT)
satisfy the relationships of (FDT) - (CT) ≦ 100 ° C and (CT) ≧ 600 ° C. In this way
a further improvement in deep drawability may be achieved.
[0047] If the final rolling is terminated at a temperature of not lower than the Ar3 transformation
point, random orientation occurs in the texture during the γ to a transformation,
thereby making it impossible to achieve excellent deep-drawability. On the other hand,
if the finish temperature of the final rolling is lowered below 500 ° C, this does
not lead to any further improvement in deep-drawability, while involving unnecessary
increase in the rolling load. Therefore, the rolling temperature is set within a range
lower than the temperature of the Ar3 transformation point but not lower than 500
° C.
(2) Roughening conditions and finish entrance temperature (FET) in the final rolling
stage of hot strip mill:
[0048] In order to achieve a further improvement in deep-drawability, the following conditions
should preferably be adopted: roughening is terminated at a temperature which is not
higher than 950
° C and which is not lower than the Ar3 transformation point, and the finish entrance
temperature (FET) is set at a temperature not higher than 800 ° C. This is for the
following reasons: if roughening is terminated at a temperature between 950
° C and the Ar3 transformation point, both inclusive, this enables the texture before
the final rolling to become fine, thereby facilitating the accumulation of strain
to be applied during the final rolling. This results in the preferred occurrence of
the {111} orientation, hence, improvement of deep-drawability. The rolling reduction
during the roughening should preferably be equal to or higher than 50 % in order to
make the grain fine. If the FET is not higher than 800 ° C, this enables the rolling
reduction within low- temperature ranges to be increased, thereby enabling an increased
amount of strain to be applied during the rolling to the grains in the {111} orientation.
This results in the preferred occurrence of the {111} orientation after recrystallization
annealing, hence, an increase in the r-value
(3) Self-annealing or recrystallization temperature:
[0049] In the case where the rolled sheet is not subjected to recrystallization annealing
after the final rolling, and it is allowed to undergo coiling-simultaneous self-annealing,
the CT is set at a temperature satisfying the relationship CT 600
° C. The reason for this requirement is that if the coiling temperature CT is lower
than 600
° C recrystallization is not completed. In order to improve deep-drawability, it is
advantageous to use a relatively low rolling temperature together with a relatively
high coiling temperature. For this purpose, the rolling should be effected under conditions
where the finish delivery temperature (FDT) and the coiling temperature CT satisfy
the relationship (FDT) - (CT) ≦ 100 ° C. In the case where the rolled sheet is subjected
to recrystallization annealing after the hot rolling (since no coiling-simultaneous
self-annealing is necessary) while the hot rolling finish temperature FDT should not
be lower than 500 ° C, the coiling temperature CT may be a relatively low temperature.
[0050] The recrystallization annealing method, which is adopted where, after the rolling,
the hot-rolled sheet is not subjected to self-annealing but is subjected to recrystallization
annealing, may be either a continuous annealing method or a box annealing method.
A suitable range of annealing temperature is from 550 to 950 ° C. The heating speed
may range from 10 ° C/hr to 50 ° C/s.
d. Conditions of Pickling, Annealing, & Galvanizing
[0051] In the present invention, since the hot rolling temperature is moderately low to
be within the range lower than the Ar3 transformation point, scale formed on the surface
of the hot-rolled sheet has a relatively small thickness of 3 mm or smaller. Therefore,
a pickling treatment may be effected using a light pickling bath provided in a galvanizing
line to effect pickling as a pretreatment, instead of passing the hot-rolled sheet
through an ordinary pickling line. If Improved pickling results may be achieved if
the pickling is effected by adopting a method including, in addition to an ordinary
pickling process, a mechanical descaling process employing a mechanical descaling
means such as shot or a leveler. Thereafter, annealing is effected at temperatures
ranging from 700 to 900
° C for 1 second to 20 minutes, and this is continuously followed by galvanizing.
[0052] If the pickling, the annealing and the galvanizing are effected continuously, the
surface of the steel sheet will be in its activated state before the galvanizing and
plating adhesion will be enhanced. On the contrary, if the hot-rolled sheet is left
standing for several hours after pickling, and it is then subjected to galvanizing,
the plating will be more or less degraded. According to the present invention, light
pickling, annealing and galvanizing may be continuously effected after the hot-rolled
sheet has been passed through an ordinary pickling line.
[0053] A conventionally known method of plating an alloy or non-alloy material can be suitably
used during the galvanizing.
(Example 1)
[0054] Steel sheets Nos. 1 to 3, shown in Table 2, were obtained in the following manner:
Steel slabs having the chemical compositions of the types 1 and 2 shown in Table 1
were heated and soaked at 1150 ° C. Thereafter, the slabs were roughened and then
subjected to final rolling. Table 2 shows the conditions adopted in these processes,
i.e., the roughening delivery temperature (RDT), the finish delivery temperature (FDT),
the rolling reduction during rolling at a temperature lower than the Ar3 transformation
point but not lower than 600
° C, the coiling temperature (CT), whether any lubricant was used or not, the radius
R (mm) of rolls on three downstream stands of the rolling mill used, and the values
of R
2√t (t being the thickness t (mm) before the final rolling). The final thickness, i.e.,
the thickness of the finished steel sheets was 1.2 mm. Properties of the hot-rolled
steel sheets after pickling are also shown in Table 2.
[0055] As shown in Table 2, steel sheets Nos. 2 and 3, which were manufactured by employing
the conditions satisfying R ≦ 200 and R2√t ≦ 100000, exhibit considerably higher r-values
than steel sheet No. 1 which is a comparison sample. In addition, since, as shown
in Table 1, the chemical composition of the steel slab used to manufacture the steel
sheet No. 2 includes B, Sample No. 2 possesses excellent resistance to cold-working
embrittlement (RSWE), as shown in Table 2.
[0056] It will be understood from these results that a hot-rolled steel sheet manufactured
by employing conditions falling within their respective ranges according to the present
invention possesses excellent deep-drawability and excellent resistance to cold-working
embrittlement.
(Example 2)
[0057] Steel sheets Nos. 1 and 2, shown in Table 3, were obtained in the following manner:
Steel slabs having the chemical compositions 1 and 2 shown in Table 1 were heated
and soaked at 1150 ° C. Thereafter, the slabs were roughened and then subjected to
final rolling. Table 3 shows the conditions adopted in these processes, i.e., the
roughening delivery temperature (RDT), the finish delivery temperature (FDT), the
rolling reduction during rolling at a temperature lower than the Ar3 transformation
point but not lower than 500
° C, the coiling temperature (CT), whether any lubricant was used or not, the radius
R (mm) of rolls on three downstream stands, and the values of R
2√t determined by the radius R and the thickness t (mm) before the final rolling. The
final thickness was 1.6 mm. After the finally rolled steel sheets were pickled, they
were subjected to box annealing at 750
° C for 5 hours.
[0058] Properties of the hot-rolled steel sheets after annealing are also shown in Table
3. It will be understood from Table 3 that hot-rolled steel sheets manufactured by
employing conditions falling within their respective ranges according to the present
invention possess excellent deep-drawability.
(Example 3)
[0059] Steel sheets Nos. 1 to 4, shown in Table 4, were obtained in the following manner:
Steel slabs having the chemical compositions 3 , 4 and 5 shown in Table 1 were heated
and soaked at 1150 ° C. Thereafter, the slabs were roughened and then subjected to
final rolling. Table 4 shows the conditions adopted in these processes, i.e., the
roughening delivery temperature (RDT), the finish delivery temperature (FDT), the
coiling temperature (CT), whether any lubricant was used or not, the radius R (mm)
of rolls on three downstream stands, and the values of t/R
4 determined by the radius R and the thickness t (mm) before the final rolling. The
final thickness was 1.2 mm.
[0060] Properties of the hot-rolled steel sheets after pickling are also shown in Table
4. As shown in Table 4, steel sheet No. 1, a comparison sample, which was manufactured
employing the conditions CT < 600
° C and (FDT) - (CT) > 100 ° C, exhibits a low r-value. The other samples manufactured
employing conditions falling within their respective ranges according to the present
invention exhibit excellent deep-drawability. It will also be understood from Table
4 that, if B is included in the chemical composition of the steel slab used, the resultant
steel sheet possesses excellent resistance to cold-working embrittlement.
(Example 4)
[0061] Steel sheets Nos. 1 and 2, shown in Table 5, were obtained in the following manner:
Steel slabs having the chemical compositions 4 and 5 shown in Table 1 were heated
and soaked at 1150 ° C. Thereafter, the slabs were roughened and then subjected to
final rolling. Table 5 shows the conditions adopted in these processes, i.e., the
roughening delivery temperature (RDT), the finish delivery temperature (FDT), the
coiling temperature (CT), whether any lubricant was used or not, the radius R (mm)
of rolls on three downstream stands, and the values of t/R
4 determined by the radius R and the thickness t (mm) before the final rolling. The
final thickness was 1.6 mm. After the finally rolled steel sheets were pickled, they
were subjected to box annealing at 750
° C for 5 hours.
[0062] Properties of the hot-rolled steel sheets after annealing are also shown in Table
5. It will be understood from Table 5 that a hot-rolled steel sheet manufactured by
employing conditions falling within their respective ranges according to the present
invention possesses excellent deep-drawability.
(Example 5)
[0063] Steel sheets Nos. 1 to 3, shown in Tables 6 (1) and 6 (2), were obtained in the following
manner: Steel slabs having the chemical compositions 6 and 7 shown in Table 1 were
heated and soaked at 1150 ° C. Thereafter, the slabs were roughened and then subjected
to final rolling. Tables 6 (1) and 6 (2) show the conditions adopted in these processes,
i.e., the roughening delivery temperature (RDT), the finish entrance temperature (FET),
the finish delivery temperature (FDT), the coiling temperature (CT), the radius R
(mm) of rolls on three stands, the thickness t (mm) before the final rolling, and
the coefficient of friction (µ). The final thickness was 1.2 mm.
[0064] Properties of the hot-rolled steel sheets after pickling or after recrystallization
annealing following pickling are shown in Table 6 (2). As shown in Table 6 (2), steel
sheet No. 3, a comparison sample, manufactured by employing a coefficient of friction
(µ) which does not satisfy the relationship of µ ≦ - 0.2 log (R/t) + 0.55, exhibits
a low r-value. The other samples manufactured employing conditions falling within
their respective ranges according to the present invention exhibit higher levels of
deep-drawability than the comparison sample.
(Example 6)
[0065] Steel sheets Nos. 1 to 4, shown in Table 7, were obtained in the following manner:
Steel slabs having the chemical compositions 8 and 9 shown in Table 1 were heated
and soaked at 1150 °C. Thereafter, the slabs were roughened and then subjected to
final rolling. Table 7 shows the conditions adopted in these processes, i.e., the
roughening delivery temperature (RDT), the finish delivery temperature (FDT), the
rolling reduction during rolling at a temperature lower than the Ar3 transformation
point but not lower than 500
° C, whether any lubricant was used or not, the radius R (mm) of rolls on three downstream
stands, and the values of R
2√t determined by the roll radius R and the thickness t (mm) before the final rolling.
The final thickness was 1.6 mm.
[0066] In this example, the hot-rolled steel sheets were subjected the continuous processes
of pickling, annealing and galvanizing. Some of the samples were not passed through
an ordinary pickling line, but they were subjected to light pickling performed as
a pretreatment in a galvanizing line, and the light pickling was continuously followed
by the processes of annealing and galvanizing. In the light pickling, mechanical descaling
was also performed. The annealing was conducted at 830
° C for 40 seconds.
[0067] Properties of the resultant galvanized steel sheets are shown in Table 7. The adhesion
of the zinc plating was evaluated in the following manner. A piece of adhesive tape
was attached to the plated surface of each steel sheet. The steel sheet was bent through
90 degrees, and was then returned to its initial position. Thereafter, the piece of
adhesive tape was removed, and the amount of Zn which peeled off with the tape was
measured utilizing fluorescent X-rays. It will be understood from the results shown
in Table 7 that hot-rolled steel sheets manufactured by employing conditions falling
within their respective ranges according to the present invention possess excellent
plating adhesion and, simultaneously, possess a high level of deep-drawability. Sample
No. 2, which was manufactured by employing a roughening delivery temperature (RDT)
exceeding 950
° C, shows a lower r-value than Sample No. 1 having the same chemical composition.
It will also be understood from Table 7 that, if B is included in the chemical composition
of the steel slab used, the resultant steel sheet exhibits excellent resistance to
cold-working embrittlement.
(Example 7)
[0068] Steel sheet No. 1, shown in Tables 8 (1) and 8 (2), was obtained in the following
manner. A steel slab having the chemical composition @ shown in Table 1 was roughened
continuously from continuous casting. Thereafter, the slab was subjected to the final
rolling (CC-DR). Tables 8 (1) and (2) show the conditions adopted in these processes,
i.e., the roughening delivery temperature (RDT), the finish entrance temperature (FET),
the finish delivery temperature (FDT), the coiling temperature (CT), the radius R
(mm) of rolls, the thickness t (mm) before the final rolling, the coefficient of friction
(µ), and whether annealing was effected or not. Properties of the steel sheet after
pickling are shown in Table 8 (2).
[0069] It will be understood from Tables 8 (1) and 8 (2) that a hot-rolled steel sheet manufactured
employing conditions falling within their respective ranges according to the present
invention possesses excellent deep-drawability.
[0070] Thus, according to the present invention, it is possible to manufacture hot-rolled
steel sheet possessing excellent deep-drawability which is as high as that of cold-rolled
steel sheet, and which suffers from no cold-working embrittlement. Furthermore, when
hot-rolled steel sheet, manufactured according to the present invention, is compared
with conventionally manufactured cold-rolled sheet, it can be seen that adoption of
the method of the present invention enables a great reduction in production costs.
Furthermore, according to the present invention, it is possible to manufacture galvanized
steel sheet which is excellent in deep-drawability, whilst omitting the process of
cold rolling or the processes of pickling and cold rolling, thereby enabling a great
reduction in production costs.
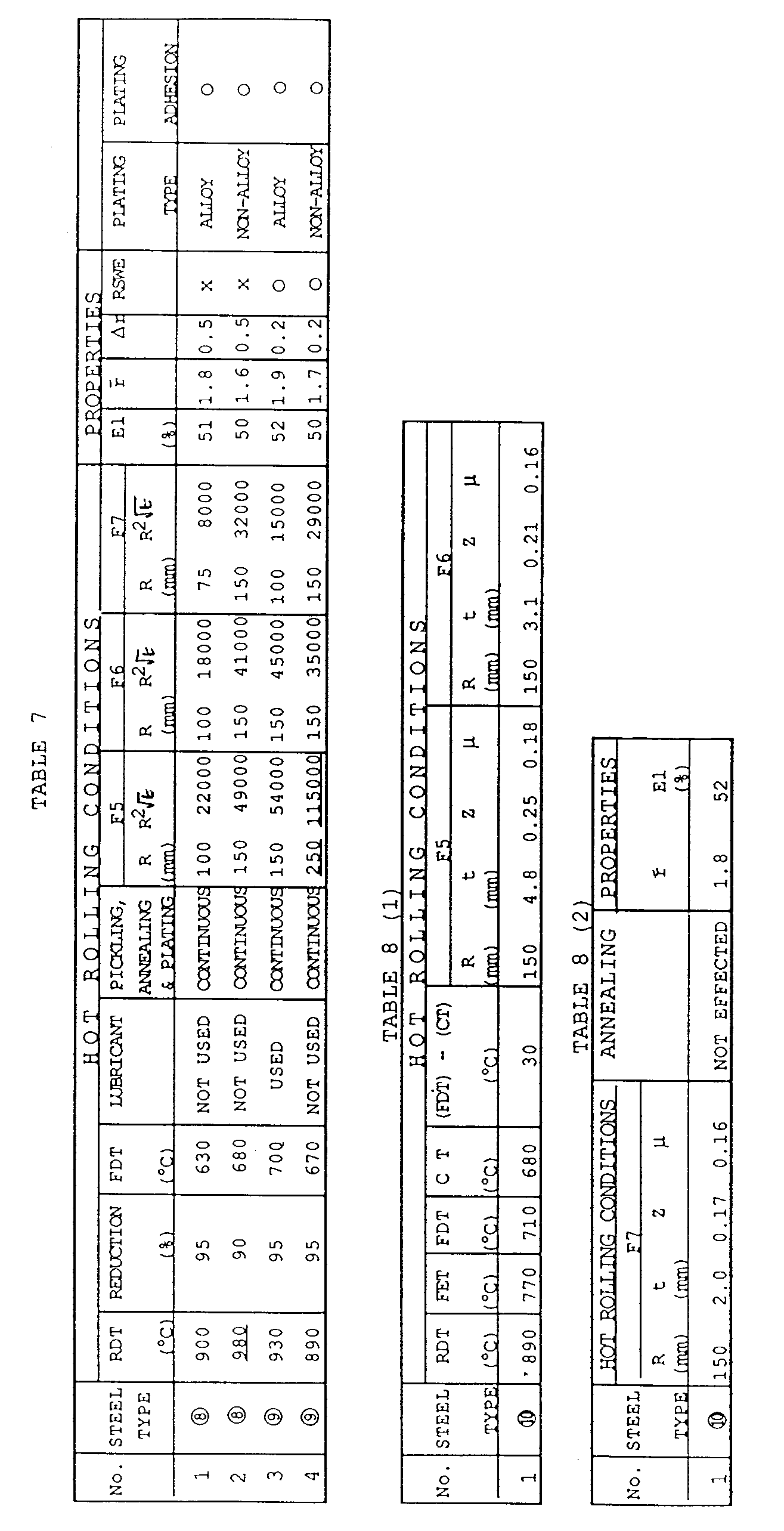