(19) |
 |
|
(11) |
EP 0 369 283 B1 |
(12) |
EUROPÄISCHE PATENTSCHRIFT |
(45) |
Hinweis auf die Patenterteilung: |
|
14.09.1994 Patentblatt 1994/37 |
(22) |
Anmeldetag: 06.11.1989 |
|
(51) |
Internationale Patentklassifikation (IPC)5: H01H 1/02 |
|
(54) |
Sinterkontaktwerkstoff für Niederspannungsschaltgeräte der Energietechnik, insbesondere
für Motorschütze
Sintered contact material for low-tension switchgear, particularly for contactors
Matériau de contact fritté pour appareillages interrupteurs à basse tension de la
technique de l'énergie, spécialement pour des contacteurs
|
(84) |
Benannte Vertragsstaaten: |
|
DE FR GB IT SE |
(30) |
Priorität: |
17.11.1988 DE 3838950
|
(43) |
Veröffentlichungstag der Anmeldung: |
|
23.05.1990 Patentblatt 1990/21 |
(73) |
Patentinhaber: SIEMENS AKTIENGESELLSCHAFT |
|
80333 München (DE) |
|
(72) |
Erfinder: |
|
- Haufe, Wolfgang
D-8521 Hessdorf (DE)
- Krause, Ralf-Dieter, Dipl.-Ing.
D-8500 Nürnberg (DE)
- Rothkegel, Bernhard
verstorben (DE)
|
(56) |
Entgegenhaltungen: :
EP-A- 0 164 664 EP-A- 0 182 386
|
EP-A- 0 170 812 DE-A- 3 232 627
|
|
|
|
|
|
|
|
|
Anmerkung: Innerhalb von neun Monaten nach der Bekanntmachung des Hinweises auf die
Erteilung des europäischen Patents kann jedermann beim Europäischen Patentamt gegen
das erteilte europäischen Patent Einspruch einlegen. Der Einspruch ist schriftlich
einzureichen und zu begründen. Er gilt erst als eingelegt, wenn die Einspruchsgebühr
entrichtet worden ist. (Art. 99(1) Europäisches Patentübereinkommen). |
[0001] Die Erfindung bezieht sich auf einen Sinterkontaktwerkstoff für Niederspannungsschaltgeräte
der Energietechnik, insbesondere für Motorschütze, mit Silber (Ag), Zinnoxid (SnO₂),
Wismutoxid (Bi₂O₃) und Kupferoxid (CuO) hergestellt aus einem inneroxidierten Legierungspulver
(IOLP) einer Silber-Zinn-Wismut-Kupfer-Ausgangslegierung, wobei das Zinnoxid in Massenanteilen
von 4 bis 12 % vorhanden ist und das Verhältnis der Massenanteile von Zinnoxid zu
Wismutoxid einerseits und von Zinnoxid zu Kupferoxid andererseits im inneroxidierten
Legierungspulver jeweils zwischen 8:1 und 12:1 beträgt.
[0002] Für den Einsatz in Niederspannungsschaltgeräten der Energietechnik, beispielsweise
in Motorschützen, aber auch in Leistungsschaltern haben sich Kontaktwerkstoffe auf
der Basis von Silber-Zinnoxid als besonders vorteilhaft erwiesen. Kontaktstücke aus
Silber-Zinnoxid erreichen in Motorschützen eine hohe Lebensdauerschaltzahl, haben
aber den Nachteil, daß sich bei Lichtbogeneinwirkung auf den Kontaktflächen thermisch
sehr stabile Oxidschichten ausbilden, die zu einem erhöhten Kontaktwiderstand führen.
Dadurch treten bei Dauerstromführung im Schaltgerät unzulässig hohe Übertemperaturen
an den Schaltgliedern auf, die insbesondere zu Schäden an den Kunststoffteilen führen
können.
[0003] In der DE-OS 33 04 637 (≙ EP-A-0 182 386), der DE-OS 34 21 758 (≙ EP-A-0 170 812)
und der DE-OS 34 21 759 (≙ EP-A-0 164 664) werden aus inneroxidierten Legierungspulvern
hergestellte Sinterkontaktwerkstoffe der Konstitution AgSnO₂Bi₂O₃CuO beschrieben,
die einerseits die heute gestellten Forderungen an die Lebensdauerschaltzahl und andererseits
an das Einschaltvermögen erfüllen. Bei diesen Werkstoffen kann ein relativ hoher Wismutoxid-Anteil
vorhanden sein, der entweder über das inneroxidierte Legierungspulver oder über eine
separate Zumischung des Wismutoxides zum inneroxidierten Legierungspulver eingebracht
wird. Allerdings erreichen diese Werkstoffe hinsichtlich der Übertemperatur nur dann
akzeptable Werte, wenn der Gesamtmassenanteil an Oxid auf 8 % bis 11 % begrenzt wird.
[0004] In der DE-A-32 32 627 sind weiterhin Werkstoffe für elektrische Kontakte auf der
Basis von AgSnO₂ beschrieben, welche zusätzlich noch einen kleinen Anteil von Verbindungen
hochschmelzender Metalle enthalten, nämlich Vanadiumoxid, Molybdänoxid oder Wismuttitanat
sowie vorzugsweise noch Molybdäncarbid oder Wolframcarbid. Solche Werkstoffe sollen
ebenso wirksam wie Wolframoxid die Kontaktstellentemperatur zu senken vermögen, diese
erniedrigte Kontaktstellentemperatur aber für eine größere Schaltspielzahl gewährleisten
als ein Silber-Zinnoxid-Wolframoxid-Werkstoff.
[0005] Aufgabe der Erfindung ist es demgegenüber, einen aus inneroxidiertem Legierungspulver
hergestellten Werkstoff der Konstitution AgSnO₂Bi₂O₃CuO weiter zu verbessern. Dabei
soll zwecks Silbereinsparung der Oxidanteil möglichst hoch und trotzdem die Übertemperatur
möglichst niedrig und bei dem die übrigen Eigenschaften in einem optimalen Verhältnis
zueinander belassen sind.
[0006] Die Aufgabe ist erfindungsgemäß bei einem Kontaktwerkstoff der eingangs genannten
Art durch Wismutzirkonat als weiteres Metalloxid, das dem inneroxidierten Legierungspulver
zugemischt ist, gelöst. Im Rahmen der Erfindung kann zusätzlich auch Wismuttitanat
vorhanden sein. Vorzugsweise liegen das Wismutzirkonat als Mischoxid 2Bi₂O₃.3ZrO₂
und das Wismuttitanat in stöchiometrischer Verbindung Bi₂Ti₂O₇ vor. Dabei beträgt
der Massenanteil an Wismutzirkonat und gegebenenfalls Wismuttitanat zwischen 0,1 und
5 %, wobei der Gesamtgehalt der Oxide in Massenanteilen maximal 20 % ist.
[0007] Zur Herstellung eines solchen Werkstoffes wird einem inneroxidierten Legierungspulver
vorgegebener Zusammensetzung Wismutzirkonatpulver und/oder Wismuttitanatpulver hinzugefügt,
wobei beim Naßmischen des inneroxidierten Legierungspulvers mit dem Pulver der Zusatzoxide
organische Lösungsmittel, insbesondere Propanol, verwendet werden.
[0008] Im Rahmen der Erfindung ergab es sich überraschenderweise, daß speziell durch den
Zusatz von Wismutzirkonatpulver und weiterhin von Wismuttitanatpulver zu einem inneroxidierten
Legierungspulver aus AgSnO₂Bi₂O₃CuO gegenüber dem Stand der Technik bei hoher Lebensdauerschaltzahl
eine Absenkung der Übertemperatur erreicht wird.
[0009] Weitere Einzelheiten und Vorteile der Erfindung ergeben sich aus der nachfolgenden
Beschreibung des Verfahrens zur Herstellung von Kontaktstücken aus dem neuen Werkstoff,
wobei auf eine Figur und weiterhin eine Tabelle mit Einzelbeispielen für unterschiedliche
Werkstoffzusammensetzungen Bezug genommen wird. Es zeigen die Figur ein typisches
Gefügebild des neuen Werkstoffes und die Tabelle Meßwerte für die Lebensdauerschaltzahl
und für die Übertemperatur.
[0010] Die Lebensdauerschaltzahl korrespondiert bekanntermaßen mit dem Volumenabbrand des
Kontaktwerkstoffes und die Übertemperatur mit dem Kontaktwiderstand. Es sind vier
Beispiele des Standes der Technik und fünf Ausführungsbeispiele der Erfindung gegenübergestellt.
[0011] Zur Herstellung der inneroxidierten Legierungspulver für die in der Tabelle angegebenen
Beispiele werden Legierungen aus AgSnBiCu bei einer Temperatur von etwa 1323 K (1050°C)
erschmolzen. Durch Zerstäuben der Schmelze mit Wasser in einer Druckverdüsungsanlage
werden daraus gleich zusammengesetzte Legierungspulver erhalten. Nach dem Trocknen
werden die Pulver auf < 300 µm abgesiebt. Dieser Anteil wird in sauerstoffhaltiger
Atmosphäre bei Temperaturen zwischen 773 K (500°C) und 873 K (600°C) quantitativ inneroxidiert,
wonach AgSnO₂Bi₂O₃CuO-Pulver folgender Zusammensetzung in Massenanteilen in Prozent
erhalten werden:

[0012] Den angegebenen AgSnO₂Bi₂O₃CuO-Pulvern werden Pulver aus Wismutzirkonat (2Bi₂O₃.3ZrO₂)
und/oder Wismuttitanat (Bi₂Ti₂O₇) durch Naßmischen in einer Rührwerkskugelmühle unter
Verwendung von Propanol und Stahlkugeln zugesetzt. Nach dem Trocknen des Gemisches
werden die Stahlkugeln von der jeweiligen Pulvermischung durch Absieben getrennt.
Die Ausgangspulver für die Kontaktstückherstellung der in der Tabelle angegebenen
Werkstoffbeispiele sind wie folgt zusammengesetzt:

[0013] Bei dieser Aufstellung bildet das inneroxidierte Legierungspulver die Basis mit 100
Massenanteilen in Prozent, zu denen die Zusatzoxide in Massenanteilen bezogen auf
100 % hinzugemischt werden. Bei der Herstellung der Kontaktstücke wird das erzeugte
Ausgangspulvergemisch mit einem Preßdruck von z.B. 600 MPa verdichtet und werden die
erhaltenen Preßkörper bei einer Temperatur zwischen 1123 K (850°C) und 1148 K (875°C)
über 2 h an Luft gesintert. Zur Erzielung einer kleinen Restporosität werden die gesinterten
Kontaktstücke bei einer Temperatur von 923 K (650°C) und einem Druck von z.B. 1000
MPa warm nachgepreßt. Eine weitere Verdichtung und Verfestigung wird durch eine zweite
Sinterung bei einer Temperatur zwischen 1123 K (850°C) und 1148 K (875°C) während
2 h erreicht. Anschließend erfolgt als letzter Herstellschritt ein Kaltkalibrieren
zur Endform bei einem Druck von z.B. 1000 MPa.
[0014] Bei obigen Werkstoffen wird nach der Sinterung ein spezifisches Gefüge mit unterschiedlichen
Oxidteilchengrößen und -formen sowie Oxidkonzentrationen erhalten, das in der Figur
in Anlehnung an ein lichtmikroskopisches Gefügebild wiedergegeben ist. Erkennbar sind
die ehemaligen Teilchen des inneroxidierten Legierungspulvers 1 mit Oxidfeinausscheidungen
2 und angelagerten gröberen Oxidausscheidungen 3. Durch die Umkörnung der Oxidausscheidungen
an den Grenzen des inneroxidierten Legierungspulvers aus AgSnO₂Bi₂O₃CuO entsteht ein
umschließendes, nahezu oxidfreies Silbernetzwerk 4, das eine hohe Sinterverdichtung
bewirkt und die es aufgrund ihrer Duktilität erlaubt, einen nahezu porenfreien Kontaktwerkstoff
durch Kaltverdichten herzustellen.
[0015] Die Umkörnung, die durch die Sintertemperatur und Sinterdauer steuerbar ist, verläuft
als Front ins Innere der AgSnO₂Bi₂O₃CuO-Pulverteilchen 1. In dieser Front besitzen
die Oxidausscheidungen 2 eine längliche, zum Teil schlierenartige Form und sind hoch
zirkonat- und/oder titanathaltig.
[0016] Überraschenderweise führt der Gefügeaufbau gemäß der Figur zu einer günstigen Beeinflussung
der elektrischen Leitfähigkeit der sich bei Lichtbogeneinwirkung auf den Kontaktflächen
ausbildenden Oxidschichten.
[0017] Zur Verwendung als Kontaktstücke in Niederspannungsschaltgeräten der Energietechnik
werden zweckmäßigerweise Zweischichten-Fertigformteile mit einer lötfähigen Reinsilberschicht
gefertigt. Diese Formteile können unmittelbar auf die Kontaktträger beispielsweise
von Motorschützen aufgelötet werden.
[0018] Mit nach obiger Vorschrift hergestellten Kontaktstücken wurden Lebensdauer- und Erwärmungsprüfungen
in Motorschützen durchgeführt. Es wurden Siemens-Schütze mit einem AC-3-Nennbetriebsstrom
von 250 A verwendet. Wesentliche Kenngrößen sind dabei die Lebensdauerschaltzahl bei
4-fachem AC-3-Nennbetriebsstrom (4 x I
e AC-3=1000 A) und die maximale Übertemperatur der Anschlußschienen des Schaltgerätes bei
Dauerführung des AC-1-Nennbetriebsstromes von I
eAC-1=300 A. Die Messungen der Übertemperatur wurden während der Lebensdauerprüfung bis
zu einer Schaltzahl von 5.10⁴ durchgeführt. Die zugehörigen Meßwerte sind in der Tabelle
angegeben.
[0019] Die vier Vergleichswerkstoffe des oben abgehandelten Standes der Technik, die durch
Sinterung von inneroxidierten Legierungspulvern hergestellt wurden, sind eingangs
aufgelistet. Die Meßwerte zeigen, daß bezüglich Übertemperatur Werkstoffe der Konstitution
AgSnO₂Bi₂O₃CuO und AgSnO₂Bi₂O₃CuO + Bi₂O₃ Werte unterhalb von 80 K nicht erreichen,
was in der Praxis in manchen Fällen als unbefriedigend angesehen wird.
[0020] Hier ergeben nun die neuen Werkstoffe, die durch Sinterung eines inneroxidierten
Legierungspulvers unter Zumischung von Wismutzirkonatpulver und/oder Wismuttitanatpulver
hergestellt wurden, insbesondere bei einem Gesamtmassenanteil von etwa 12 % Oxid,
die geforderte Verbesserung des Übertemperaturverhaltens. Es wurden Werte von 60 K
bis 70 K gemessen, wobei die Lebensdauerschaltzahl auf dem gleichen hohen Niveau des
Standes der Technik bleibt. Damit ist das Eigenschaftspektrum insgesamt verbessert,
wobei sich in jedem Fall eine Silbereinsparung ergibt.
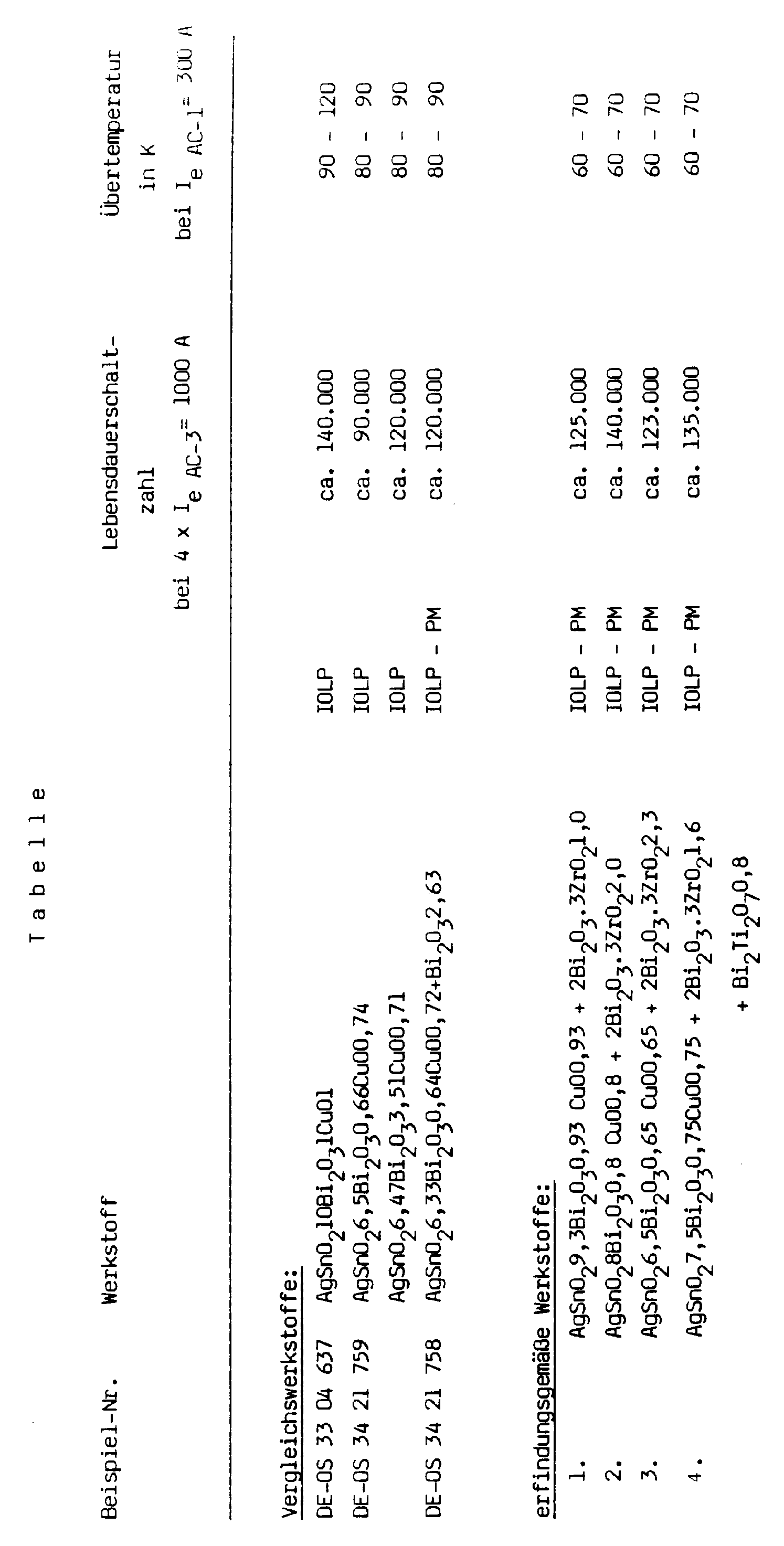
1. Sinterkontaktwerkstoff für ein Niederspannungsschaltgerät der Energietechnik, insbesondere
für ein Motorschütz, mitSilber (Ag), Zinnoxid (SnO₂), Wismutoxid (Bi₂O₃) und Kupferoxid
(CuO), hergestellt aus einem inneroxidierten Legierungspulver (IOLP) einer Silber-Zinn-Wismut-Kupfer-Ausgangslegierung,
wobei das Zinnoxid in Massenanteilen von 4 bis 12 % enthalten ist und das Verhältnis
der Massenanteile in Prozent von Zinnoxid zu Wismutoxid einerseits und von Zinnoxid
zu Kupferoxid andererseits im inneroxidierten Legierungspulver jeweils zwischen 8:1
und 12:1 beträgt, gekennzeichnet durch Wismutzirkonat (2Bi₂O₃.3ZrO₂) als weiteres Metalloxid, das dem inneroxidierten
Legierungspulver zugemischt ist.
2. Sinterkontaktwerkstoff nach Anspruch 1, dadurch gekennzeichnet, daß zusätzlich Wismuttitanat (Bi₂Ti₂O₇) vorhanden ist.
3. Sinterkontaktwerkstoff nach Anspruch 1 und Anspruch 2, dadurch gekennzeichnet, daß das Wismutzirkonat als Mischoxid und das Wismuttitanat als stöchiometrische
Verbindung vorliegen.
4. Sinterkontaktwerkstoff nach Anspruch 1 und Anspruch 2, dadurch gekennzeichnet, daß der Gesamtmassenanteil an Wismutzirkonat und Wismuttitanat zwischen 0,1 und
5 % beträgt.
5. Sinterkontaktwerkstoff nach Anspruch 3, dadurch gekennzeichnet, daß der Gesamtmassenanteil an Wismutzirkonat und Wismuttitanat zwischen 0,5 und
4 % beträgt.
6. Sinterkontaktwerkstoff nach Anspruch 4, dadurch gekennzeichnet, daß der Massenanteil an Wismutzirkonat zwischen 0,5 und 3 % beträgt.
7. Sinterkontaktwerkstoff nach Anspruch 2, dadurch gekennzeichnet, daß der Massenanteil von Wismuttitanat zwischen 0,1 und 2 % beträgt.
8. Sinterkontaktwerkstoff nach einem der vorhergehenden Ansprüche, dadurch gekennzeichnet, daß der Gesamtgehalt der Oxide in Massenanteilen maximal 20 % beträgt.
9. Sinterwerkstoff nach Anspruch 6, dadurch gekennzeichnet, daß der Massenanteil aller Oxide bei etwa 12 % liegt.
1. Sintered contact material for low voltage switchgear for power engineering, in particular
for a motor contactor, containing silver (Ag), tin oxide (SnO₂), bismuth oxide (Bi₂O₃)
and copper oxide (CuO) and produced from an internally oxidised alloy powder (IOAP)
of a silver-tin-bismuth-copper starting alloy, the tin oxide content being from 4
to 12% by weight and the ratio of tin oxide to bismuth oxide on the one hand and of
tin oxide to copper oxide on the other hand as weight percentages in the internally
oxidised alloy powder being in each case between 8:1 and 12:1, characterised by bismuth
zirconate (2Bi₂O₃.3ZrO₂) as a further metal oxide which is admixed with the internally
oxidised alloy powder.
2. Sintered contact material according to claim 1, characterised in that in addition
bismuth titanate (Bi₂Ti₂O₇) is present.
3. Sintered contact material according to claim 1 and claim 2, characterised in that
the bismuth zirconate is present as a mixed oxide and the bismuth titanate as a stoichiometric
compound.
4. Sintered contact material according to claim 1 and claim 2, characterised in that
the total amount of bismuth zirconate and bismuth titanate is between 0.1 and 5% by
weight.
5. Sintered contact material according to claim 3, characterised in that the total amount
of bismuth zirconate and bismuth titanate is between 0.5 and 4% by weight.
6. Sintered contact material according to claim 4, characterised in that the amount of
bismuth zirconate is between 0.5 and 3% by weight.
7. Sintered contact material according to claim 2, characterised in that the amount of
bismuth titanate is between 0.1 and 2% by weight.
8. Sintered contact material according to one of the preceding claims, characterised
in that the total oxide content of oxides amounts to at most 20% by weight.
9. Sintered contact material according to claim 6, characterised in that the amount of
all oxides is about 12% by weight.
1. Matériau de contact fritté pour un appareil interrupteur à basse tension en courant
fort, notamment pour un contacteur de moteur, comprenant de l'argent (Ag), de l'oxyde
d'étain (SnO₂), de l'oxyde de bismuth (Bi₂O₃) et de l'oxyde de cuivre (CuO), préparé
à partir d'une poudre d'alliage à oxydation interne (IOLP) d'un alliage de départ
d'argent, d'étain, de bismuth et de cuivre, l'oxyde d'étain étant présent en des proportions
pondérales de 4 à 12 %, et le rapport des proportions pondérales en pourcentages de
l'oxyde d'étain à l'oxyde de bismuth d'une part, et de l'oxyde d'étain à l'oxyde de
cuivre d'autre part, de la poudre d'alliage à oxydation interne étant compris respectivement
entre 8:1 et 12:1, caractérisé par du zirconate de bismuth (2Bi₂O₃·3ZrO₂) comme autre
oxyde métallique, qui est ajouté à la poudre d'alliage à oxydation interne.
2. Matériau de contact fritté suivant la revendication 1, caractérisé en ce que du titanate
de bismuth (Bi₂Ti₂O₇) est présent en plus.
3. Matériau de contact fritté suivant la revendication 1 ou 2, caractérisé en ce que
le zirconate de bismuth est présent sous la forme d'un oxyde mixte et le titanate
de bismuth sous la forme d'un composé stoechiométrique.
4. Matériau de contact fritté suivant la revendication 1 ou 2, caractérisé en ce que
la proportion pondérale totale de zirconate de bismuth et de titanate de bismuth est
comprise entre 0,1 et 5 %.
5. Matériau de contact fritté suivant la revendication 3, caractérisé en ce que la proportion
pondérale totale de zirconate de bismuth et de titanate de bismuth est comprise entre
0,5 et 4 %.
6. Matériau de contact fritté suivant la revendication 4, caractérisé en ce que la proportion
pondérale de zirconate de bismuth est comprise entre 0,5 et 3 %.
7. Matériau de contact fritté suivant la revendication 2, caractérisé en ce que la proportion
pondérale de titanate de bismuth est comprise entre 0,1 et 2 %.
8. Matériau de contact fritté suivant l'une des revendications précédentes, caractérisé
en ce que la teneur totale des oxydes en proportions pondérales est au maximum de
20 %.
9. Matériau de contact fritté suivant la revendication 6, caractérisé en ce que la proportion
pondérale de tous les oxydes est de 12 % environ.
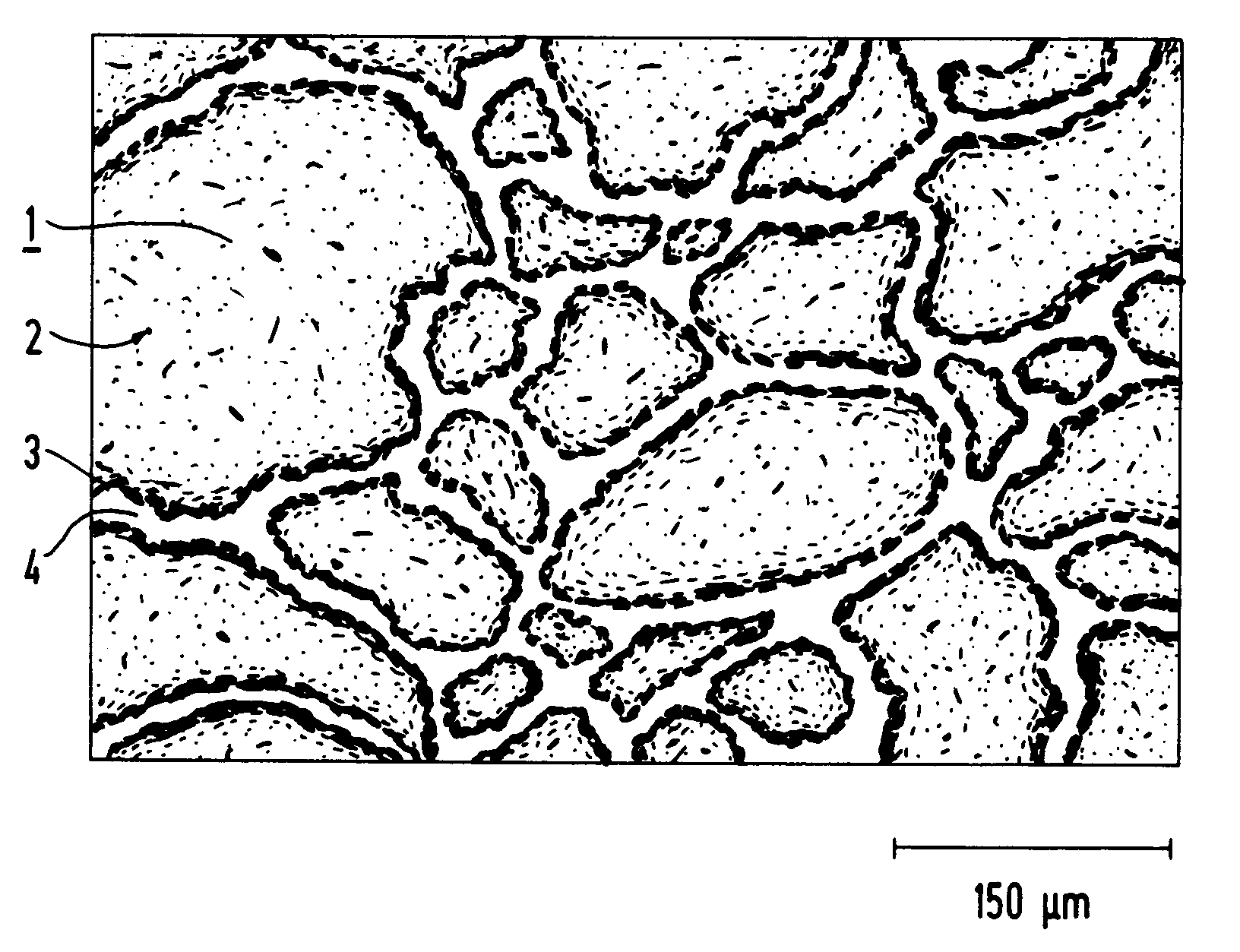