HYDROTHERMAL PROCESS FOR GROWING OPTICAL-QUALITY SINGLE CRYSTALS AND AQUEOUS MINERALIZER
THEREFOR
FIELD OF THE INVENTION
[0001] This invention relates to producing optically useful crystals of MTiOXO₄, wherein
M is selected from the group consisting of NH₄, K, Rb, Tl, mixtures thereof and mixtures
of Cs therewith, and X is selected from the group consisting cf P, As and mixtures
thereof, and more particularly to hydrothermal processes for producing such crystals.
BACKGROUND OF THE INVENTION
[0002] The need for optical quality single crystals of materials exhibiting nonlinear optical
properties is well established in the art. Potassium titanyl phosphate (i.e. KTP)
is particularly useful in nonlinear optical devices, as described, for example, in
U.S. Patent No. 3,949,323. Optical quality crystals having dimensions on the order
of one millimeter or more are particularly useful for many optical applications.
[0003] Processes for producing optical quality crystals using aqueous systems are known
generally in the art as hydrothermal processes, and processes for producing such crystals
using nonaqueous molten salt systems are known generally in the art as flux processes.
Hydrothermal processes are considered particularly advantageous relative to flux processes
for growing crystals for certain applications since hydrothermal processes often produce
crystals having better optical damage resistance and relatively lower ionic conductivity.
Typically, hydrothermal processes involve growing the crystal in a vessel having a
growth region where the crystal grows and a nutrient region containing nutrient for
growing the crystal, and employ an aqueous mineralizer solution (i.e., a mineralizer).
[0004] For example, one type of mineralizer used for hydrothermal crystal growth of KTP
uses a mineralizer containing both potassium and phosphate. A typical commercial production
of KTP crystals, described by Belt et al., SPIE Proceedings,
968, 100 (1988), uses a potassium phosphate mineralizer at a temperature in the range
of about 520°C to 560°C and a pressure in the range of about 1.72 X 10⁺⁸ Pa to 2.03
10⁺⁸ Pa (1700 to 2000 atm.). The relatively high temperature and pressure employed
in this process makes scale-up difficult and expensive. As suggested in Laudise et
al., "Solubility and P-V-T Relations and the Growth of Potassium Titanyl Phosphate",
Journal of Crystal Growth,
102, pp. 427-433 (1990) the use of more moderate conditions can lead to a problem of
the coprecipitation of anatase (TiO₂), making the process less useful. Mineralizers
rich in potassium have been used under conditions of fairly moderate temperature (e.g.,275
to 425°C) and pressure (e.g., less than 14,000 psi) as described in U.S. Patent No.
5,066,356. Although U.S. Patent No. 5,066,356 demonstrates that growth temperature
and pressure can be reduced while using certain concentrated mineralizer solutions,
the growth rate of that process is somewhat limited due to the relatively low solubility
of KTiOPO₄ in the mineralizer. U.S. Patent No. 4,305,778 discloses a hydrothermal
process for crystal growth which utilizes a stable glass composition that minimizes
the tendency of the seed crystals to dissolve in the aqueous mineralizer solution
before nutrient can migrate to the seed crystals.
[0005] Another type of mineralizer used for the hydrothermal growth of KTiOPO₄ involves
the use of potassium fluoride solutions as described, for example, in Jia et al.,
"The Solubility of KTiOPO₄ (KTP) in KF Aqueous Solution Under High Temperature and
High Pressure", Journal of Crystal Growth,
79 (1986), pp. 970-973, and in Jia et al., "Hydrothermal Growth of KTP Crystals in the
Medium Range of Temperature and Pressure", Journal of Crystal Growth,
99 (1990), pp. 900-904. Jia et al. disclose that by utilizing KF as a mineralizer relatively
lower temperature and pressure can be employed for a hydrothermal KTP crystal growth
process, and use of a pressure as low as 1000 Kg/cm (14223 psi) (i.e. 9.80 X 10⁺⁷
Pa) is exemplified. The use of pure KF mineralizer as described by Jia et al. provides
a solubility of about 2% under the stated growth conditions, but like the process
described in Laudise et al. supra, the higher solubility occurs near the phase stability
boundary (with respect to temperature, pressure and mineralizer concentration), so
the possibility of coprecipitation of an undesirable non-KTP phase exists.
[0006] A generally recognized family of KTP-type materials has the formula MTiOXO₄ where
M is selected from the group consisting of NH
4, K, Rb, Tl, mixtures thereof and mixtures of Cs therewith, and X is selected from
the group consisting of P, As and mixtures thereof. Hydrothermal processes for producing
KTiOPO₄ are well studied. A problem associated with extending these studies to hydrothermal
production of other crystals of the family involves the compositional variability
of the mineralizers most suitable for growing each of the MTiOxO₄ family of materials.
These variations make the development of new crystals, such as KTiOAsO₄, difficult
and costly, since a new set of desirable growth parameters must be found for each
of the isomorphs and their solid solutions.
SUMMARY OF THE INVENTION
[0007] This invention provides a method of increasing the rate of crystal growth in a hydrothermal
process for growing a crystal at MTiOXO₄, wherein M is selected from the group consisting
of NH4, K, Rb, Tl, mixtures thereof, and mixtures of Cs therewith and X is selected
from the group consisting of P and As and mixtures thereof. In general, the method
is used with a hydrothermal process for growing said crystal in a growth region at
elevated temperatures using a mineralizer comprising both M⁺ and X⁺⁵, and comprises
the step of employing a mineralizer further comprising F⁻ in an amount effective to
increase the solubility of MTiOXO₄ in the mineralizer.
[0008] This invention further provides an aqueous mineralizer for the hydrothermal production
of crystals of MTiOXO₄, consisting essentially of an aqueous composition (solution/mixture)
of F⁻, M⁺ and X⁺⁵ wherein F⁻ is present in an amount effective to increase the solubility
of MTiOXO₄ in the mineralizer and to provide a MTiOXO₄ solubility of at least about
1% by weight at the operating temperature and pressure for the hydrothermal production.
Optical quality crystals of at least 1 mm³ can be grown using the mineralizer of this
invention in times on the order of hours, rather than days and weeks.
[0009] It is an object of this invention to provide an improved mineralizer for use in hydrothermal
processes to improve crystal growth rates for the MTiOXO₄ family of materials by increasing
the solubility of MTiOXO₄ in the mineralizer.
[0010] It is a further object of this invention to provide mineralizer embodiments for the
growth of MTiOAsO₄ materials at relatively low temperature and pressure.
BRIEF DESCRIPTION OF THE DRAWING
[0011] Figure 1 is a ternary diagram which depicts the broad and preferred range of aqueous
mineralizer composition for the production of MTiOXO₄ at a fluoride molality of from
about 4 to 12, and from about 400°C to 600°C and from about 1.01 X 10⁺⁸ Pa to 2.03
X 10⁺⁸ Pa(1000 to 2000 atm.) pressure.
DETAILED DESCRIPTION
[0012] A hydrothermal process is provided in accordance with this invention which employs
a concentrated aqueous mineralizer solutions comprising F⁻ in addition to M⁺ and X⁺⁵
in a hydrothermal process to achieve relatively rapid, low pressure and/or low temperature
growth of crystalline materials of the formula MTiOXO₄, wherein M is selected from
the group consisting of NH₄, K, Rb, Tl, mixtures thereof and mixtures of Cs therewith
(preferably K) and X is selected from the group consisting of P and As and mixtures
thereof. An aqueous mineralizer solution is also provided in accordance with this
invention which consists essentially an aqueous composition of F⁻, M⁺ and X⁺⁵ (where
M and X are defined above). The hydrothermal process for crystal growth at elevated
temperature in a growth region, employs a growth medium comprising a mineralizer solution
containing F⁻, M⁺ and X⁺⁵, and employs either a growth region temperature from about
200°C to about 800°C or a pressure of less than 1.93 X 10⁺⁸ Pa (28,000 psi), or both,
during crystallization. Typically, growth rates greater than 1 mm/side/week can be
achieved at even the relatively lower temperatures studied in the art (i.e., 200°C
to 600°C), and at operating pressures significantly lower than 5.52 X 10⁺⁷ Pa (8000
psi) and preferably about 2.42 X 10⁺⁷Pa (3500 psi) or less. For the best combination
of effective crystal growth rate and economics of operation, the crystal growth pressure
for the present invention is commonly in the range of from 1.38 X 10⁺⁷ Pa to 9.66
X 10⁺⁷ Pa (2000 to 14000 psi). A typical temperature range is from about 250°C to
about 450°C.
[0013] The general procedure used for hydrothermal crystal growth is well known in the art
and involves conducting the crystal growth at elevated temperature and pressure in
a pressure vessel containing a means for nucleating crystal growth and a growth medium
comprising a nutrient and an aqueous mineralizer solution. The preferred means for
nucleating crystal growth are seed crystals which provide nucleation sites. In accordance
with this invention seed crystals of MTiOXO₄, as defined above, can be utilized. Typical
hydrothermal processes usually use a high pressure vessel or container in which single
crystal seeds of the desired product are hung in a relatively supersaturated zone
(i.e., a growth region) and a large quantity of polycrystalline nutrient of the same
material is maintained in an unsaturated zone (i.e. a nutrient region), all together
with an aqueous solution of mineralizer in which the nutrient is suitably soluble.
The temperatures of the growth region and the nutrient region are selected in accordance
with the slope of the solubility/temperature correlation for the specific mineralizer
used. For solutions having a positive (normal) solubility/temperature correlation,
the nutrient region is kept warmer than the growth region, while for solutions having
a negative (retrograde) solubility/temperature correlation, the growth region is kept
warmer than the nutrient region. Under steady-state growth conditions, the nutrient
dissolves in the hotter (or cooler in the case of a retrograde correlation) nutrient
zone, is transported to the cooler (or hotter in the case of a retrograde correlation)
growth zone via natural convection caused by a density gradient or by forced convection
(e.g., a rocker mechanism) and is deposited on the seed crystals. Large crystals are
thereby produced.
[0014] The aqueous solution of mineralizer in combination with a nutrient consisting of
a polycrystalline form of MTiOXO₄ or in combination with suitable precursors thereof
makes up the growth medium. The amount of nutrient is not critical, provided enough
is present to saturate the growth medium and provide sufficient material for the desired
mass increase on the seed crystal(s) . Nutrient surface area is typically 5 to 10
times the surface area of the seed crystal(s) so that the rate of nutrient dissolution
does not undesirably limit crystal growth.
[0015] The mineralizer should contain both M⁺ and X⁺⁵, as defined above and, in accordance
with this invention must contain fluoride to achieve desirable growth rates. For example,
materials such as described by Belt et al., "Nonlinear Optic Materials for Second
Harmonic Generation (KTP)", Avionics Laboratory, Air Force Wright Aeronautical Laboratories,
Air Force Systems Command, Wright-Patterson Air Force Base, Ohio (1984), formed from
the combination of MH₂XO₄ and M₂HXO₄ are suitable for use along with MF. It is noted
that the F⁻ provided for use in this invention need not be specifically added as the
compound MF, but can be added using other fluoride sources which do not interfere
with crystallization (e.g., a mixture of HF and MOH) which form MF in situ. The X⁺⁵
is generally present in the mineral or combination as an oxide (e.g., XO
4 -3), and may be provided by adding compounds such as X₂O₅, and/or MH₂XO₄. In accordance
with this invention it is preferred that the mole ratio of M⁺ to X⁺⁵ in the mineralizer
solution is from about 0.7:1 to about 2.5:1 to avoid formation of material other than
the desired MTiOXO₄, such as anatase (TiO₂). If desired, an oxidizing agent, such
as KNO₃ or H₂O₂, can be present in the growth medium in small concentrations to prevent
reduction of Ti⁺⁴ and to enhance crystal quality.
[0016] In accordance with the practice of this invention the concentration of F⁻ in the
aqueous solution of mineralizer is preferably at least about 1 molal (as F), more
preferably 2 molal or more, and is preferably 12 molal or less. The concentration
of M⁺ in the aqueous solution of mineralizer is preferably at least 1 molal (as M),
more preferably 2 molal or more, and is preferably 20 molal or less, more preferably
16 molal or less. A concentration of M⁺ from about 2 to 16 molal is considered particularly
suitable for many applications. It is recognized that concentrations of M⁺ as high
as 20 molal may not be achieved at room temperature, but can be achieved at the higher
temperatures of operation. Consequently, solid material might be added with the aqueous
solution of mineralizer, which would dissolve upon heating to provide an aqueous solution
of mineralizer of the desired concentration. The concentration of X⁺⁵ in the aqueous
solution of mineralizer is preferably at least about 0.2 molal (as X), more preferably
1 molal or more, and is preferably 12 molal or less, more preferably 8 molal or less.
The invention is considered particularly useful for growing crystals where X is As.
[0017] An aqueous mineralizer is provided in accordance with this invention for hydrothermal
production of crystals of MTiOXO₄ which consists essentially of an aqueous composition
containing F⁻, M⁺ and X⁺⁵ wherein F⁻ is present in an amount effective to increase
the solubility of MTiOXO₄ in the mineralizer and to provide MTiOXO₄ solubility of
at least about 1 percent by weight of the operating temperature and pressure of a
hydrothermal crystal growth process.
[0018] While pH of the aqueous mineralizer of the present invention is not particularly
critical to the crystal growth process
per se, the pH can be important in the construction of pressure vessels for the process.
For example, low pH (about 7 or less) and low operating temperature and pressure (e.g.,
200°C and 4.05 X 10⁺⁷ Pa (400 atm.) allows use of metal vessels with liners other
than noble metals (e.g., Teflon®).
[0019] Certain proportions of M⁺, F⁻ and X⁺⁵ are considered particularly suitable for mineralizer
compositions. Mineralizer systems of this invention may be represented on a ternary
diagram, in terms of the relative mole percent of MF, MOH and X₂O₅. Figure 1, for
example represents a ternary diagram for mineralizer used for growing MTiOXO₄, wherein
mole percentages in terms of MF, MOH and X₂O₅ are shown relative to each other (water
of aqueous mineralizer is not included). The corners of the ternary diagram labeled
MF, MOH and X₂O₅ thus represent 100 relative mole percent total of MF, MOH and X₂O₅
respectively; and each point within the diagram represents 100 mole percent total
of MF, MOH and X₂O₅. Preferably for the growth of MTiOXO₄ at about 4 to 12 molal F-¹
and at about 400 to 600°C and about 1.01 X 10⁺⁸ Pa to 2.03 X 10⁺⁸ Pa (1000 to 2000
atm.) pressure, the amounts of M, F and X are selected to provide a mineralizer compound
falling within the polygon which is defined by I II III IV V VI I; and more preferably
the amounts of M, F and X are selected to provide a mineralizer composition falling
within the polygon which is defined by A B C D E F A. The diagram is especially useful
for defining preferred ranges where M is K and X is P or As. Similar ranges apply
to other MTiOXO₄ isomorphs. At lower temperatures (e.g., less than about 300°C) and
absolute fluoride concentrations below 4 molal, these zones expanded slightly to include
the pure KF mineralizer as well.
[0020] While the practice of this invention is not bound by any theory or explanation, the
role of fluoride ion in the aqueous mineralizer of this invention is believed to be
related to the dissolution of MTiOXO₄. The dissolution can be written as follows:

In a highly concentrated solution of M⁺ and/or X⁺⁵, such as typically exists in MOH/X₂O₅-type
aqueous mineralizer solutions equilibrium is shifted to the left in accordance with
the law of mass action, favoring the precipitation of MTiOXO₄ and lowering its solubility.
To obtain high solubility, one should therefore (1) find ions which readily form water-soluble
complexes with titanium (Ti⁺⁴); and (2) reduce the absolute concentration of M⁺ and/or
X⁺⁵. In accordance with this invention, fluoride ion complexes effectively with titanium
and is believed to be primarily responsible for the high solubility of MTiOXO₄ in
the mineralizers of the present invention. As is evident in Figure 1, at high temperature
(above about 400°C) and high F⁻ concentrations (above about 4 molal), the amount of
M and/or X cannot be reduced to zero because of the MTiOXO₄-phase stability requirements.
Accordingly, the addition of M and X stabilizes the MTiOXO₄ phase field in the presence
of fluoride.
[0021] A typical hydrothermal process using aqueous mineralizer of this invention comprises
the steps of (1) providing in a vessel (a) means for nucleating growth of a crystal
at MTiOXO₄ in a growth region, (b) a growth medium comprising nutrient for growing
said crystal of MTiOXO₄ and an aqueous solution of mineralizer containing a mixture
of F, M (i.e., NH₄, K, Rb, Tl, or partial Cs) and X (i.e., As or P) in a nutrient
region, and (c) means for producing a temperature gradient between said growth region
and said nutrient region; (2) employing in said nutrient region a nutrient temperature
sufficient to effect solution of at least a portion of said nutrient; and (3) employing
in said growth region an elevated growth temperature at which the MTiOXO₄ has a lower
solubility than at said nutrient temperature and a pressure whereby growth of said
crystal proceeds.
[0022] Under the mild conditions of temperature and pressure typically employed in the practice
of this invention, the vessel chosen can be selected from a wide variety of types
and sizes which can withstand these reaction temperatures and reaction pressures.
Pressure vessel configurations typically utilize a noble metal container, or noble
metal-clad container although other inert material such as Teflon® can also be used
for lining the container. Platinum, gold and Teflon® are preferred liner materials
for the crystal growth of potassium titanyl phosphate and potassium titanyl arsenate.
A ladder-like rod configuration can be used to hang a number of seed crystals in the
growth region portion of the lined vessel and a perforated baffle plate is used to
separate the part of the container containing the growth region from the part containing
a nutrient region. (The growth region can be located either above or below the nutrient
region, depending upon the type of temperature/solubility correlation.) The baffle
plate aids in maintaining the thermal gradient during growth. Nutrient is placed in
the nutrient region, separated from the growth region by the baffle. An aqueous solution
of mineralizer is loaded into the can along with the seed crystals. The can is sealed
and typically placed in an autoclave with a sufficient amount of water to generate
a pressure on the outer wall equal to the pressure generated inside the can at the
predetermined maximum operating temperature. This "pressure balancing" approach prevents
the can from collapsing and thus enables proper crystal growth. Typically, if a noble
metal liner is used the need for the can is eliminated. Various conventional forced
convection techniques such as mechanical rockers or stirrers can also be employed
for the crystal growth process. Alternatively, a horizontal rather than vertical configuration
can be utilized.
[0023] The percentage of fill is defined as the room temperature atmospheric pressure volume
of the solution divided by the free volume of the container, i.e., the container volume
less the volume of nutrient, seed crystals, frame or ladder, and baffle. In the case
of a lined vessel, the container's volume is the volume of the vessel. Common practice
in the art has generally been to limit the percentage of fill so that excessive pressure
is not encountered at the growth temperature, and a preferred fill range from 70 to
85% has typically been used depending on mineralizer concentration. Percentages of
fill above about 85% have generally been avoided because the resulting pressure is
generally considered excessive for assuring vessel integrity. In accordance with this
invention percentages of fill of from about 60% to 95% are preferably used, with fill
percentages of from about 70% to 85% being most generally preferred.
[0024] The following non-limiting examples further illustrate practice of the invention.
EXAMPLES
[0025] Hydrothermal solubilities of MTiOXO₄ may be studied using the following standard
solution-quenching method. A mineralizer mixture consisting of typically 2 to 4 ml
of H₂O and varying amounts of MF, X₂O₅ and/or MH₂XO₄, is placed in a 0.95 cm (3/8")
gold or platinum tube along with a pre-weighed amount of excess MTiOXO₄ powder. The
two ends of the tube are then welded shut, and the tube is placed in an internally
heated pressure vessel and brought to a specified temperature and pressure. The solution
is held at this temperature and pressure until equilibrium solubility is established
(typically from 1 to 3 days). The pressure vessel is then quenched quickly (about
600°C/min.) to room temperature. Rapid cooling is used to keep all dissolved MTiOXO₄
in solution. Upon cutting-open the tube, the pH of the solution is measured and the
undissolved MTiOXO₄ powder and crystals are recovered and weighed. The MTiOXO₄ weight
loss is taken as the hydrothermal solubility at the temperature and pressure condition
used.
EXAMPLE 1
[0026] The standard solution-quenching method outlined above was used to determine the relationship
of solubility to pH at from 400°C to 600°C and from 1000 atmospheres to 2000 atmospheres.
Results for a variety of aqueous mineralizer compositions in accordance with this
invention for the production of KTiOAsO₄ are shown in Table 1.
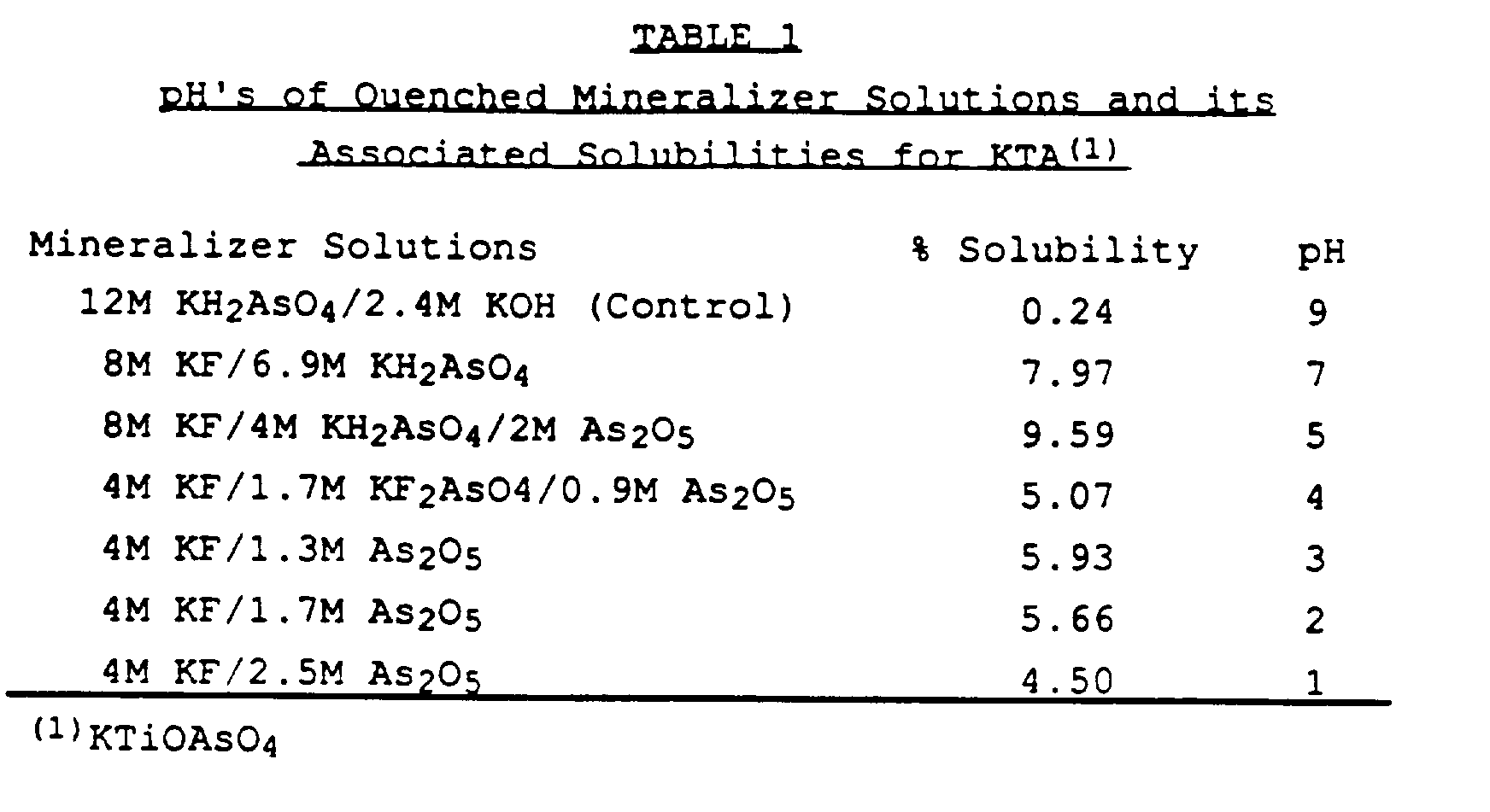
The Control mineralizer known in the art (i.e., mineralizer containing no KF) has
a very low solubility.
EXAMPLE 2
[0027] The standard solution-quenching method outlined above was used to determine the solubility
of MTiOXO₄ for a variety of isomorphs of MTiOXO₄ in the aqueous mineralizer of the
present invention. Results are shown in Table 2.
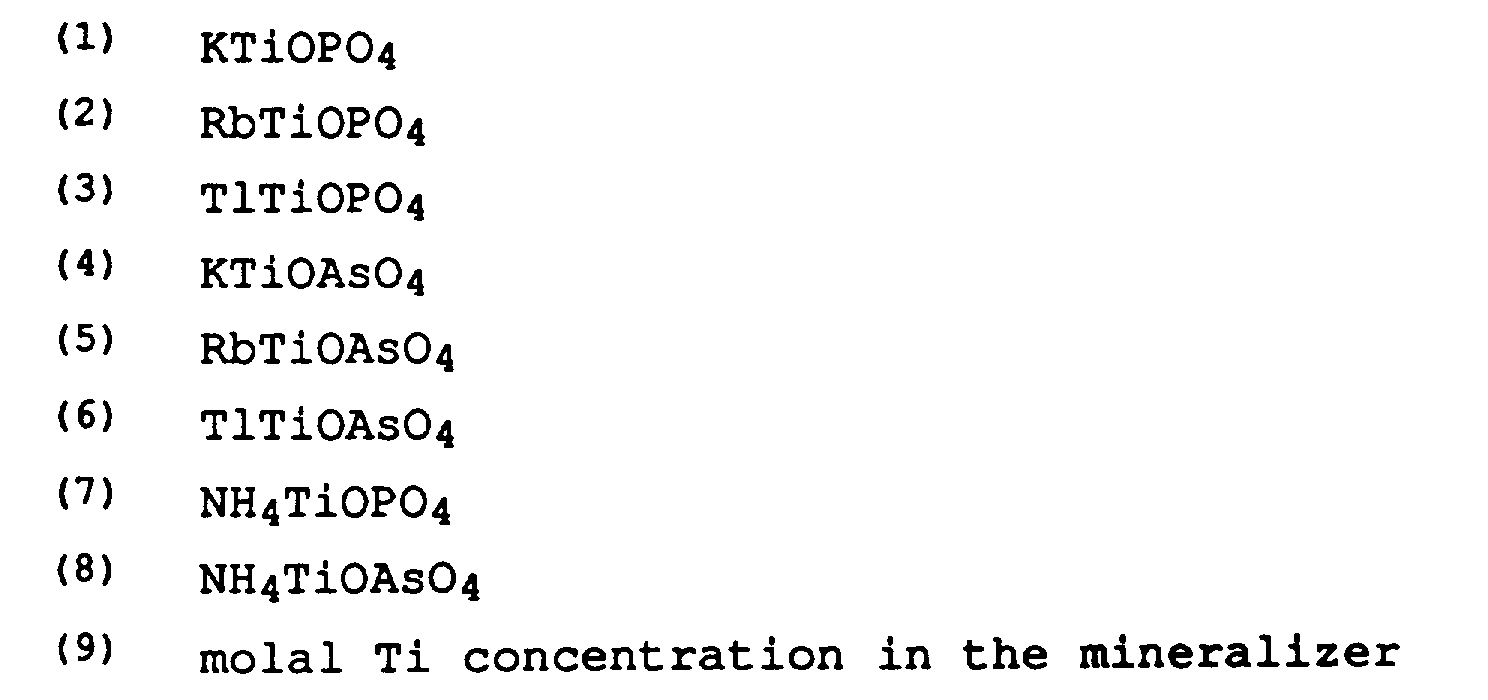
[0028] Table 2 shows that low temperature (200°C) can be used with MF/P₂O₅ or MF/As₂O₅ mineralizer,
while providing more than adequate solubility of MTiOPO₄ or MTiOAsO₄.
EXAMPLE 3
[0029] The standard solution-quenching method outlined above was used to determine the solubility
of KTiOPO₄ and KTiOAsO₄ at various operating temperatures and pressures. Results are
shown in Table 3.
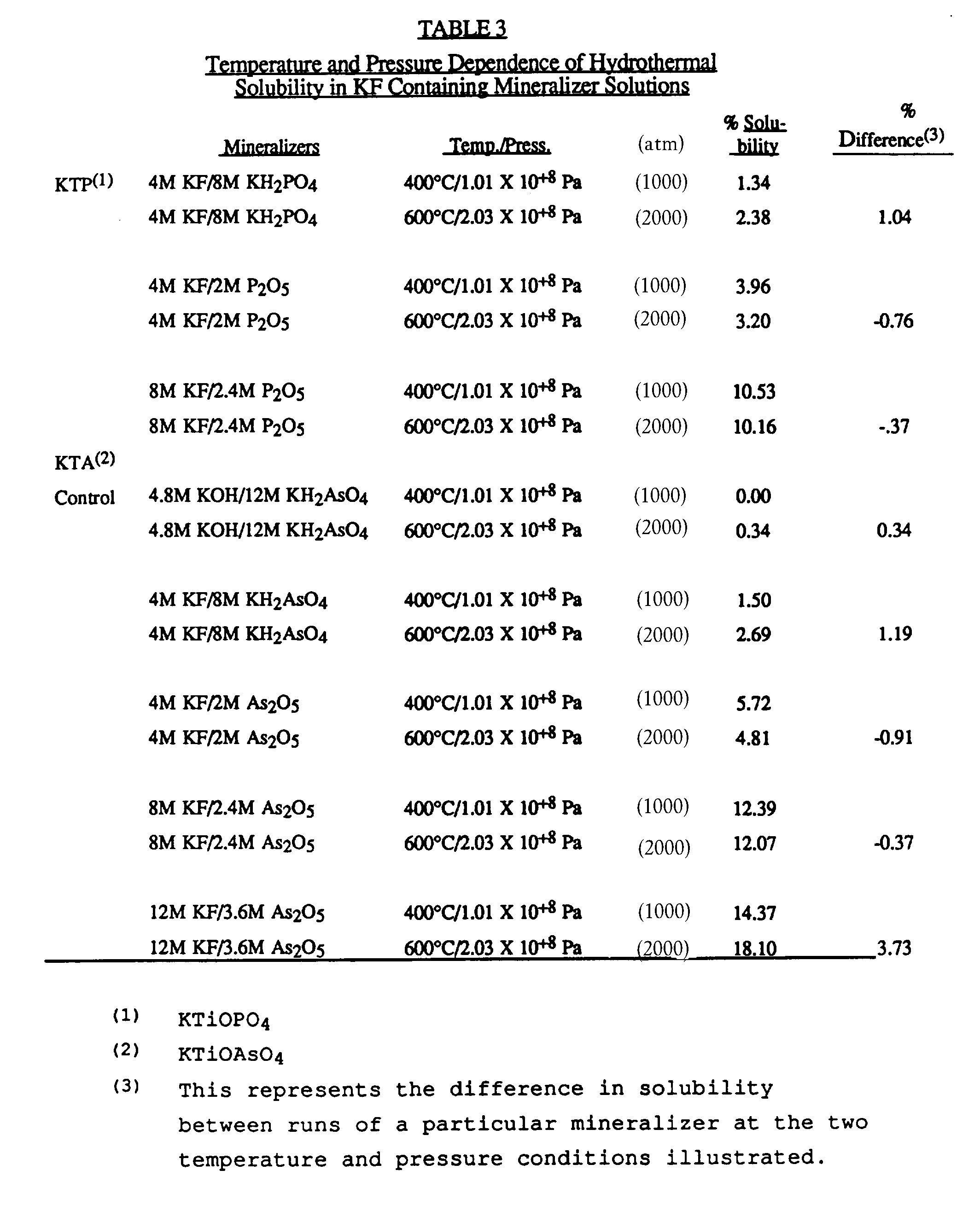
It can be seen from Table 3 that the aqueous mineralizers known in the art (Controls
containing no KF), provide very low solubility of KTiOAsO₄.
EXAMPLE 4
Growth of KTiOPO₄
[0030] A mixture consisting of 3.5 ml of H₂O, 1.63 g of KF, 1.29 g of P₂O₅ and about 1.8
g of fine (<0.5 mm³) KTiOPO₄ crystals was placed in a gold tube (0.95 cm (3/8") in
diameter and about 15.2 cm (6") long) and both ends were hermetically sealed shut.
The tube was placed in an internally heated pressure vessel which was brought to a
temperature of 600°C and 2.03 X 10⁺⁸ Pa (2000 atm.) pressure. Argon was used to pressurize
the vessel. A temperature difference of about 25°C was established between the center
of the gold tube and its two ends by cooling the two ends of the pressure vessel.
The temperature and pressure were maintained for 16 hours during which time crystallization
of KTiOPO₄ took place via temperature gradient transport. The vessel was then quenched
to room temperature and optical quality crystals of up to about 1.5 x 1 x 1mm³ were
recovered from the gold tubes.
EXAMPLE 5
Growth of KTiOAsO₄
[0031] A mixture consisting of 3.5 ml of H₂O, 1.63 g of KF, 2.09 g of As₂O₅ and about 1.8
g of fine (<0.5 mm³) KTiOAsO₄ crystals was placed in a gold tube (0.95 cm (3/8") in
diameter and about 15.2 cm (6") long) and both ends were hermetically sealed shut.
The tube was placed in an internally heated pressure vessel which was brought to a
temperature of 600°C and 2.03 X 10⁺⁸ Pa (2000 atm.) pressure. Argon was used to pressurize
the vessel. A temperature difference of about 25°C was established between the center
of the gold tube and its two ends by cooling the two ends of the pressure vessel.
The temperature and pressure were maintained for 16 hours during which time crystallization
of KTiOAsO₄ took place via temperature gradient transport. The vessel was then quenched
to room temperature and optical quality crystals of up to about 1.5 x 1 x 1 mm³ were
recovered from the gold tubes.
EXAMPLE 6
Growth of KTiOAsO₄
[0032] A mixture consisting of 3.5 ml of H₂0, 0.81 g of KF, 1.38 g of As₂O₅ and about 0.46
g of fine (<0.5 mm³) KTiOAsO₄ crystals was placed in a gold tube (0.95 cm (3/8") in
diameter and about 15.2 cm (6") long) and both ends were hermetically welded shut.
The tube was placed in an internally heated pressure vessel which was brought to a
temperature of 800°C and 2.03 X 10⁺⁸ Pa (2000 atm.) pressure. Argon was used to pressurize
the vessel. The temperature was held constant at 800°C for 1 hour, and then cooled
at a rate of 5°C per hour to a temperature of 600°C. After holding the temperature
at 600°C for two more hours, the vessel was quenched to room temperature and the gold
tube was cut open to remove the grown crystals. Optical quality KTiOAsO₄ crystals
of up to about 2.0 x 1.5 x 1.5 mm³ were recovered from the gold tubes.
EXAMPLE 7
Growth of KTiOAsO₄
[0033] A mixture of 3.5 ml H₂0, 1.63 g KF, 0.99 g As₂O₅, 1.91 g KH₂AsO₄ and about 1.33 g
of fine (<0.5 mm³) KTiOAsO₄ crystals was placed in a gold tube (0.95 cm (3/8") in
diameter and about 15.2 cm (6") long) and both ends were hermetically welded shut.
The tube was placed in an internally heated pressure vessel and brought to 400°C and
5.06 X 10⁺⁷ Pa (500 atm.) pressure. Argon was used to pressurize the vessel. The temperature
was held constant at 400°C for 5 hours, and then cooled at a rate of 5°C/hr. to 300°C.
After holding at 300°C for 8 more hours, the vessel was quenched to room temperature
and the gold tube was cut open to remove the grown crystals. Optical quality KTiOAsO₄
crystals of up to about 1x1x1mm³ were obtained.
1. A increasing the rate of crystal growth in method of a hydrothermal process for growing
a crystal of MTiOXO₄ wherein M is selected from the group consisting of NH₄, K, Rb,
Tl, mixtures thereof, and mixtures thereof with Cs, and X is selected from the group
consisting of P, As and mixtures thereof, in a growth region at elevated temperature
using a mineralizer both M⁺¹ and X⁺⁵, said hydrothermal process comprising the step
of employing a mineralizer further comprising F⁻ in an amount effective to increase
the solubility of MTiOXO₄ in the mineralizer.
2. The hydrothermal process of Claim 1 wherein X is P.
3. The hydrothermal process of Claim 1 wherein X is As.
4. The hydrothermal process of Claim 1, 2 or 3 wherein M is K.
5. The hydrothermal process of Claim 1 comprising the steps of providing in a vessel
(a) means for nucleating growth of a crystal in a growth region, (b) a growth medium
comprising nutrient for growing said crystal of MTiOXO₄ and an aqueous mineralizer
containing a mixture of F, M and X in a nutrient region, and (c) means for producing
a temperature gradient between said growth region and said nutrient region; (2) employing
in said nutrient region an elevated temperature sufficient to effect solution of at
least a portion of said nutrient; and (3) employing in said growth region an elevated
growth temperature at which the MTiOXO₄ has a lower solubility than at said nutrient
temperature and a pressure whereby growth of said crystal proceeds.
6. The hydrothermal process of Claim 5 wherein the concentration of F⁻ in the mineralizer
solution is at least 1 molal, the concentration of M⁺ is from 1 to 20 molal and the
concentration of X⁺⁵ is from 0.2 to 12 molal.
7. The hydrothermal process of Claim 5 wherein the concentration of F⁻ in the mineralizer
solution is from 2 to 8 molal, the concentration of M⁺ is from 2 to 16 molal, and
the concentration of X⁺⁵ is from 1 to 8 molal.
8. The hydrothermal process of Claim 1 or Claim 5 wherein the growth region temperature
is from about 200°C to about 800°C.
9. The hydrothermal process of Claim 8 wherein the growth region temperature is 250°C
to 600°C.
10. The hydrothermal process of Claim 1 or Claim 5 wherein the pressure is less than 1.93
x 10⁺⁸ Pa(28000 psi)
11. The hydrothermal process of Claim 10 wherein the pressure is from 1.38 x 10⁺⁷ Pa to
9.66 x 10⁺⁷ Pa (2000 to 14000 psi)
12. An aqueous mineralizer for hydrothermal production of crystals of MTiOXO₄ consisting
essentially of an aqueous mixture containing at least about 1 molal M⁺¹, where M is
selected from the group consisting of NH₄, K, Rb, Tl, mixtures thereof, and mixtures
of Cs therewith, at least about 0.2 molal X⁺⁵, where X is selected from the group
consisting of P, As and mixtures thereof, and an amount of F⁻ at least about 1 molal,
which is effective to increase the solubility of MTiOXO₄ in the mineralization and
to provide a MTiOXO₄ solubility of at least 1% by weight at the operating temperature
and pressure for the hydrothermal production.
13. The aqueous mineralizer of Claim 12 for hydrothermal production of said crystals at
about 4 to 12 molal F⁻, and at a temperature from about 400°C to 60°C and a pressure
from about 1.01 x 10⁸ to 2.03 x 10⁸ Pa (1000 atmospheres to 2000 atmospheres) wherein
the amounts of M⁺, F⁻ and X⁺⁵ are selected to produce a mineralizer composition falling
within the polygon which is defined by I II III IV V VI I in Figure 1.
14. The aqueous mineralizer of Claim 13 wherein the amounts of M⁺, F⁻ and X⁺⁵ are selected
to provide a mineralizer composition falling within the polygon which is defined by
A B C D E F A in Figure 1.
15. The aqueous mineralizer solution of Claim 12, Claim 13 or Claim 14 wherein M is K
and X is As.
16. The aqueous mineralizer solution of Claim 12, Claim 13 or Claim 14 wherein M is K
and X is P.
1. Verfahren zum Erhöhen der Geschwindigkeit des Kristallwachstums eines hydrothermalen
Verfahrens zum Züchten eines MTiOXO₄-Kristalls, worin M aus der Gruppe, bestehend
aus NH₄, K, Rb, Tl, Mischungen derselben und Mischungen derselben mit Cs ausgewählt
ist, und X aus der Gruppe, bestehend aus P, As und Mischungen derselben ausgewählt
ist, in einem Wachstumsbereich bei erhöhter Temperatur unter Verwendung eines Mineralisierungsmittels,
das sowohl M¹⁺ als auch X⁵⁺ umfaßt, wobei das hydrothermale Verfahren die Stufe der
Anwendung eines Mineralisierungsmittels umfaßt, das weiterhin F⁻ in einer Menge umfaßt,
um auf wirksame Weise die Löslichkeit von MTiOXO₄ in dem Mineralisierungsmittel zu
erhöhen.
2. Hydrothermales Verfahren gemäß Anspruch 1, worin X P ist.
3. Hydrothermales Verfahren gemäß Anspruch 1, worin X As ist.
4. Hydrothermales Verfahren gemäß Anspruch 1, 2 oder 3, worin M K ist.
5. Hydrothermales Verfahren gemäß Anspruch 1, umfassend die Stufen: (1) Bereitstellen
in einem Gefäß: (a) Mittel, um das Wachstum eines Kristalls in einem Wachstumsbereich
einzuleiten, (b) ein Wachstumsmedium, umfassend Nährstoff zum Wachstum des MTiOXO₄-Kristalls,
und ein wäßriges Mineralisierungsmittel, das eine Mischung aus F, M und X in einem
Nährstoffbereich enthält, und (c) Mittel zur Bildung eines Temperaturgradienten zwischen
dem Wachstumsbereich und dem Nährmittelbereich, (2) Anwendung einer erhöhten Temperatur
in dem Nährmittelbereich, die ausreichend ist, um das Auflösen wenigstens eines Teils
des Nährmittels zu bewirken, und (3) Anwendung einer erhöhten Wachstumstemperatur
in dem Wachstumsbereich, bei der das MTiOXO₄ eine geringere Löslichkeit als bei der
Nährmitteltemperatur und einen Druck hat, wobei das Wachstum des Kristalls fortschreitet.
6. Hydrothermales Verfahren gemäß Anspruch 5, worin die Konzentration von F⁻ in der Mineralisierungsmittel-Lösung
wenigstens 1 molal ist, die Konzentration von M⁺.1 bis 20 molal ist, und die Konzentration
von X⁵⁺ 0,2 bis 12 molal ist.
7. Hydrothermales Verfahren gemäß Anspruch 5, worin die Konzentration von F⁻ in der Mineralisierungsmittel-Lösung
2 bis 8 molal ist, die Konzentration von M⁺ 2 bis 16 molal ist, und die Konzentration
von X⁵⁺ 1 bis 8 molal ist.
8. Hydrothermales Verfahren gemäß Anspruch 1 oder 5, worin die Temperatur des Wachstumsbereichs
etwa 200°C bis etwa 800°C beträgt.
9. Hydrothermales Verfahren gemäß Anspruch 8, worin die Temperatur des Wachstumsbereichs
250°C bis 600°C ist.
10. Hydrothermales Verfahren gemäß Anspruch 1 oder 5, worin der Druck weniger als 1,93x10⁸
Pa (28 000 psi) ist.
11. Hydrothermales Verfahren gemäß Anspruch 10, worin der Druck 1,38x10⁷ Pa bis 9,66x10⁷
Pa (2000 bis 14 000 psi) ist.
12. Wäßriges Mineralisierungsmittel für die hydrothermale Herstellung von MTiOXO₄-Kristallen,
das im wesentlichen aus einer wäßrige Mischung besteht, enthaltend: wenigstens etwa
1 molales M¹⁺, worin M aus der Gruppe, bestehend aus NH₄, K, Rb, Tl, deren Mischungen,
und Mischungen von Cs mit diesen ausgewählt ist, wenigstens etwa 0,2 molales X⁵⁺,
worin X aus der Gruppe, bestehend aus P, As und deren Mischungen ausgewählt ist, und
eine Menge von wenigstens 1 molalem F⁻, das wirksam ist, um die Löslichkeit von MTiOXO₄
bei der Mineralisierung zu erhöhen und um eine MTiOXO₄-Löslichkeit von wenigstens
1 Gew.-% bei der Arbeitstemperatur und dem Druck für die hydrothermale Herstellung
bereitzustellen.
13. Wäßriges Mineralisierungsmittel gemäß Anspruch 12 für die hydrothermale Herstellung
der Kristalle bei etwa 4 bis 12 molalem F⁻ und einer Temperatur von etwa 400°C bis
600°C und einem Druck von etwa 1,01x10⁸ bis 2,03x10⁸ Pa (1000 bis 2000 Atmosphären),
worin die Mengen von M⁺, F⁻ und X⁵⁺ ausgewählt sind, um eine Mineralisierungsmittel-Zusammensetzung
herzustellen, die in das Polygon fällt, das durch I II III IV V VI I in Figur 1 definiert
ist.
14. Wäßriges Mineralisierungsmittel gemäß Anspruch 13, worin die Mengen von M⁺, F⁻ und
X⁵⁺ ausgewählt sind, um eine Mineralisierungsmittel-Zusammensetzung bereitzustellen,
die in das Polygon fällt, das durch A B C D E F A in Figur 1 definiert ist.
15. Wäßrige Mineralisierungsmittel-Lösung gemäß Anspruch 12, Anspruch 13 oder Anspruch
14, worin M K und X As ist.
16. Wäßrige Mineralisierungsmittel-Lösung gemäß Anspruch 12, Anspruch 13 oder Anspruch
14, worin M K und X P ist.
1. Un procédé pour augmenter la vitesse de croissance cristalline dans un procédé hydrothermique
pour faire croître un cristal de MTiOXO₄ où M est choisi dans le groupe formé par
NH₄, K, Rb, Tl, leurs mélanges, et leurs mélanges avec Cs, et X est choisi dans le
groupe formé par P, As et leurs mélanges, dans une zone de croissance à température
élevée en utilisant un minéralisateur comprenant à la fois M¹⁺ et X⁵⁺, ledit procédé
hydrothermique comprenant l'étape consistant à utiliser un minéralisateur comprenant,
de plus, F⁻ en une quantité efficace pour augmenter la solubilité de MTiOXO₄ dans
le minéralisateur.
2. Le procédé hydrothermique de la revendication 1, dans lequel X est P.
3. Le procédé hydrothermique de la revendication 1, dans lequel X est As.
4. Le procédé hydrothermique de la revendication 1, 2 ou 3, dans lequel M est K.
5. Le procédé hydrothermique de la revendication 1, comprenant les étapes consistant
à disposer dans un récipient (a) un moyen pour amorcer la croissance d'un cristal
dans une zone de croissance, (b) un milieu de croissance comprenant une substance
nutritive pour faire croître ledit cristal de MTiOXO₄ et un minéralisateur aqueux
contenant un mélange de F, M et X dans une zone nourricière et (c) un moyen pour établir
un gradient de température entre ladite zone de croissance et ladite zone nourricière
; (2) à utiliser dans ladite zone nourricière une température élevée suffisante pour
réaliser la dissolution d'une partie au moins de ladite substance nutritive ; et (3)
à utiliser dans ladite zone de croissance une température de croissance élevée à laquelle
le MTiOXO₄ présente une solubilité plus faible qu'à ladite température de zone nourricière
et une pression à laquelle la croissance dudit cristal progresse.
6. Le procédé hydrothermique de la revendication 5, dans lequel la concentration molale
de F⁻ dans la solution minéralisatrice est d'au moins 1, la concentration molale de
M⁺ est de 1 à 20 et la concentration molale de X⁵⁺ est de 0,2 à 12.
7. Le procédé hydrothermique de la revendication 5, dans lequel la concentration molale
de F⁻ dans la solution minéralisatrice est de 2 à 8 molale, la concentration molale
de M⁺ est de 2 à 16, et la concentration molale de X⁵⁺ est de 1 à 8.
8. Le procédé hydrothermique de la revendication 1 ou de la revendication 5, dans lequel
la température de la zone de croissance est d'environ 200°C à environ 800°C.
9. Le procédé hydrothermique de la revendication 8, dans lequel la température de la
zone de croissance est de 250°C à 600°C.
10. Le procédé hydrothermique de la revendication 1 ou de la revendication 5, dans lequel
la pression est inférieure à 1,93 × 10⁺⁸ Pa.
11. Le procédé hydrothermique de la revendication 10, dans lequel la pression est de 1,38
× 10⁺⁷ Pa à 9,66 × 10⁺⁷ Pa.
12. Un minéralisateur aqueux pour la production hydrothermique de cristaux de MTiOXO₄,
consistant essentiellement en un mélange aqueux contenant M¹⁺ à une concentration
molale d'au moins 1 environ, où M est choisi dans le groupe formé par NH₄, K, Rb,
Tl, leurs mélanges, et leurs mélanges avec Cs, X⁵⁺ à une concentration molale d'au
moins 0,2 environ, où X est choisi dans le groupe formé par P, As et leurs mélanges,
et F⁻ à une concentration molale d'au moins 1 environ, qui est efficace pour augmenter
la solubilité de MTiOXO₄ dans le minéralisateur et pour établir une solubilité de
MTiOXO₄ d'au moins 1 % en poids à la température et la pression opératoires pour la
production hydrothermique.
13. Le minéralisateur aqueux de la revendication 12, pour la production hydrothermique
desdits cristaux à une concentration molale de F⁻ d'environ 4 à 12 et à une température
d'environ 400°C à 600°C et une pression d'environ 1,01 × 10⁸ à 2,03 × 10⁸ Pa, les
quantités de M⁺, F⁻ et X⁵⁺ étant choisies pour produire une composition de minéralisateur
s'inscrivant dans le polygone qui est défini par I II III IV V VI I sur la Figure
1.
14. Le minéralisateur aqueux de la revendication 13, dans lequel les quantités de M⁺,
F⁻ et X⁵⁺ sont choisies pour produire une composition de minéralisateur s'inscrivant
dans le polygone défini par A B C D E F A sur la Figure 1.
15. La solution minéralisatrice aqueuse de la revendication 12, la revendication 13 ou
la revendication 14, dans laquelle M est K et X est As.
16. La solution minéralisatrice aqueuse de la revendication 12, la revendication 13 ou
la revendication 14, dans laquelle M est K et X est P.