BACKGROUND OF THE INVENTION
(1) Field of the Invention
[0001] This invention relates to the use as a solvent for the dye of pressure-sensitive
recording paper of a certain hydrocarbon mixture that is prepared by disproportionating
diarylalkanes or a mixture mainly containing diarylalkanes in the presence of a disproportionation
catalyst.
(2) Description of the Prior Art
[0002] Various kinds of pressure-sensitive recording papers are hitherto well known. For
example, a colorless dye, that is a dye-precursor, is dissolved in a solvent and the
obtained solution is encapsulated into microcapsules. One surface of a sheet of paper
is coated with microcapsules and the surface of another sheet of paper is coated with
clay or a polymeric material such as phenol resin (color developer) which produces
a color upon reaction with the dye-precursor. When the recording paper is used, the
treated surfaces of the above set of paper sheets are put together face to face and
local pressure is applied to the paired sheets by handwriting or any other measure,
thereby obtaining desired duplicate impressions.
[0003] The recording mechanism in the pressure-sensitive recording paper is such that the
microcapsules on the surface of a sheet of paper are ruptured by the pressure of handwriting
or else to release the dye solution from the microcapsules. The solution containing
a dye comes into contact with clay or polymeric material (color developer) on the
opposite surface of the other sheet of paper to produce a color.
[0004] The dyes for pressure-sensitive recording paper are exemplified by Crystal Violet
Lactone, Malachite Green, benzoyl Leucomethylene Blue, Rhodamine B and 3-dialkylamino-7-dialkylamino
fluoran.
[0005] As the solvents for pressure-sensitive recording paper, diarylalkanes such as diphenylmethane
and phenylxylylethane are conventionally used. Some of diarylalkanes, however, have
offensive odor due to their chemical structures, and thus are not suitable as the
solvents for pressure-sensitive recording paper.
[0006] Meanwhile, it is known that diphenylethanes are contained in the by-product oil that
is produced in a certain preparation process. However, the by-product oil usually
contains many kinds of other compounds and it is impossible to separate them simply
by distillation. For this reason, even though the diphenylethanes in the by-product
oil are not expensive, they are not widely used due to their offensive odor and for
other reasons. For example, as disclosed in Japanese Laid-Open Patent Publication
No. 56-161195, it is necessary to treat them in order to remove offensive odor and
to add some odor-masking agents.
[0007] Other aromatic hydrocarbons such as dibenzyltoluene that is heavier than diarylalkanes
are also proposed as the solvents for pressure-sensitive recording paper. Due to their
higher molecular weight, however, their pour points and viscosities are generally
high and their color developing properties are not always satisfactory. Accordingly,
heavier aromatic hydrocarbons are scarcely used as solvents for pressure-sensitive
recording paper.
[0008] JP-A-56-161195 discloses the use of an ethylbenzene heavy end fraction, that is of
the product obtained from the alkylation of benzene with ethylene, as the solvent
for the dye precursor of a pressure-sensitive material.
According to FR-A-2154207 the dye precursor of a pressure-sensitive reproduction system
is dissolved in a solvent which consists of dibenzylbenzenes, that is a compound in
which the aromatic nuclei are linked via methylene groups.
BRIEF SUMMARY OF THE INVENTION
[0009] It is, therefore, the primary object of the present invention to provide an improved
solvent for the dye of pressure-sensitive recording paper which is free from the above-described
disadvantages of the conventional art.
[0010] Another object of the present invention is to provide a solvent for the dye of pressure-sensitive
recording paper which solvent has no offensive odor though it is prepared from diarylalkanes,
shows excellent color developing property and anti-fading property, and has a sufficiently
low pour point and viscosity irrespective of its high boiling point.
[0011] A further object of the present invention is to provide a solvent for the dye of
pressure-sensitive recording paper, which solvent is inexpensive, has desirable properties
and can be prepared from a by-product oil fraction of a hydrocarbon mixture mainly
containing diarylalkanes that is obtained from a specific production process.
[0012] The present invention is directed to the use of a hydrocarbon mixture mainly containing
triaryldialkanes as a solvent for the dye of pressure sensitive recording paper, said
mixture being obtained by recovering by distillation substantially the whole fraction
boiling between 350 and 450°C from the reaction mixture obtained by the process of
disproportionating, at temperatures in the range of 20 to 500°C in the presence of
a disproportionation catalyst, the by-product oil fraction being obtained in the process
of preparing alkylated monocyclic aromatic hydrocarbons by alkylating benzene or toluene
with ethylene in the presence of an alkylation catalyst and having boiling points
in the range of 260 to 320°C.
[0013] The above-mentioned by-product oil fraction is a hydrocarbon mixture mainly containing
diarylalkanes that is obtained in the process to produce alkylated monocyclic aromatic
hydrocarbons by alkylating benzene or toluene with ethylene in the presence of an
alkylation catalyst. When the above by-product oil fraction is used as a starting
material, it is inexpensive and a fraction containing triaryldialkanes can be obtained
efficiently. In addition, it is desirable because a solvent for the dye of pressure-sensitive
recording paper which scarcely has offensive odor can be obtained.
DETAILED DESCRIPTION OF THE INVENTION
[0014] (I) and The boiling points of the above diarylalkanes or the hydrocarbon mixture
mainly containing the same are in the range of 260 to 320°C and preferably 260 to
310°C. Diarylalkanes or a hydrocarbon mixture having a boiling point higher than the
above range is not desirable because the effect of below-described disproportionation
cannot be expected.
[0015] The above diarylalkanes are used singly or in a mixture of two or more kinds.
[0016] Exemplified as the above diarylalkanes are, diphenylethane, phenyltolylethane and
ditolylethane.
[0017] Among alkylation catalysts mainly used industrially are Lewis acids such as aluminum
chloride and boron fluoride, synthetic zeolites that are typically represented by
ZSM-5 type zeolite such as ZSM-5 and ZSM-11, and protonic acids such as phosphoric
acid.
[0018] The above-mentioned alkylation is widely put into practice as preparation process
for lower alkylbenzenes such as ethylbenzene, ethyltoluene and cumene. Ethylbenzene
and ethyltoluene which are produced by alkylating benzene and toluene with ethylene,
are dehydrogenated into styrene and methylstyrene, respectively, and they are consumed
in large quantities for producing polymers.
[0019] An example of ethylbenzene preparation process will be described, in which benzene
is alkylated with ethylene in the presence of aluminum chloride catalyst.
[0020] The molar ratio of the feed of benzene to ethylene is, for example, about 10:1 to
about 3:1. In liquid phase alkylation, 0.005 to 0.030 part of catalyst is added to
one part of produced ethylbenzene. The reaction is carried out at temperatures of
90 to 150°C, pressures of 0.5 to 15 kg/cm
2 and duration of 20 minutes to 3 hours.
[0021] Through the above alkylation, unreacted benzene, aimed ethylbenzene, polyethylbenzenes
such as diethylbenzene and triethylbenzene, and the by-product oil fraction containing
diarylalkanes are obtained.
[0022] After the alkylation, the catalyst is removed by a conventional method. For example,
the catalyst is separated by sedimentation in a settler, which is followed by neutralization
and repeated water rinsing.
[0023] Then the unreacted benzene (b.p. 80°C), ethylbenzene (b.p. 136°C) and polyethylbenzene
(b.p. 176 to 250°C) are recovered by distillation from the alkylation product to obtain
the by-product oil containing diarylalkanes, as the bottoms.
[0024] The by-product oil fraction which is used for the present invention is the fraction
obtained from the process to produce ethylbenzene or ethyltoluene by alkylating benzene
or toluene with ethylene. This by-product oil fraction substantially comprises diarylalkanes
and can be obtained in large quantities at low cost. Furthermore, the effect of disproportionation
of the invention can be produced markedly. Accordingly, said by-product oil fraction
is desirable as the starting material to be used in the present invention.
[0025] In the present invention, the above-described starting material is subjected to disproportionation
in the presence of a disproportionation catalyst.
[0026] The disproportionation catalysts are exemplified by Lewis acids such as aluminum
chloride and ferric chloride, solid acids such as silica-alumina, and synthetic zeolites
represented by ZSM-5 type zeolites such as ZSM-5 and ZSM-11, heteropoly acids such
as silicotungstic acid, super strong acids such as trifluoromethane sulfonic acid,
and super strongly acidic cation exchange resin such as Nafion (trademark, made by
E.I. du Pont de Nemours). However, sulfuric acid and natural clay such as activated
clay are not preferable because the disproportionation does not proceed substantially.
[0027] The temperatures for the disproportionation can be selected in a wide range of 2O
to 5OO°C depending on the kind of the catalyst. For example, the temperature range
of 2O to 150°C is suitable for aluminum chloride; 150 to 230°C, for Nafion; and 250
to 500°C, for synthetic zeolite. The disproportionation does not occur at temperatures
lower than the above range, while side reactions such as decomposition occur at temperatures
higher than the above range, neither of which is, accordingly, desirable.
[0028] With regard to the type of reaction, any of batchwise and continuous types can be
employed.
[0029] Preferable reaction times are 20 minutes to 10 hours in batchwise reaction and 0.5
to 10 in LHSV in continuous reaction.
[0030] The pressures of disproportionation are not especially limited, however, they are
generally in the range of atmospheric pressure to 10 bar (kg/cm
2).
[0031] In the disproportionation according to the invention, monocyclic aromatic hydrocarbons,i.e.
benzene and alkylbenzene,such as toluene that are lighter than the starting hydrocarbons
and triaryldialkanes that are heavier than the starting hydrocarbons and are represented
by the following general formula (I), are produced.
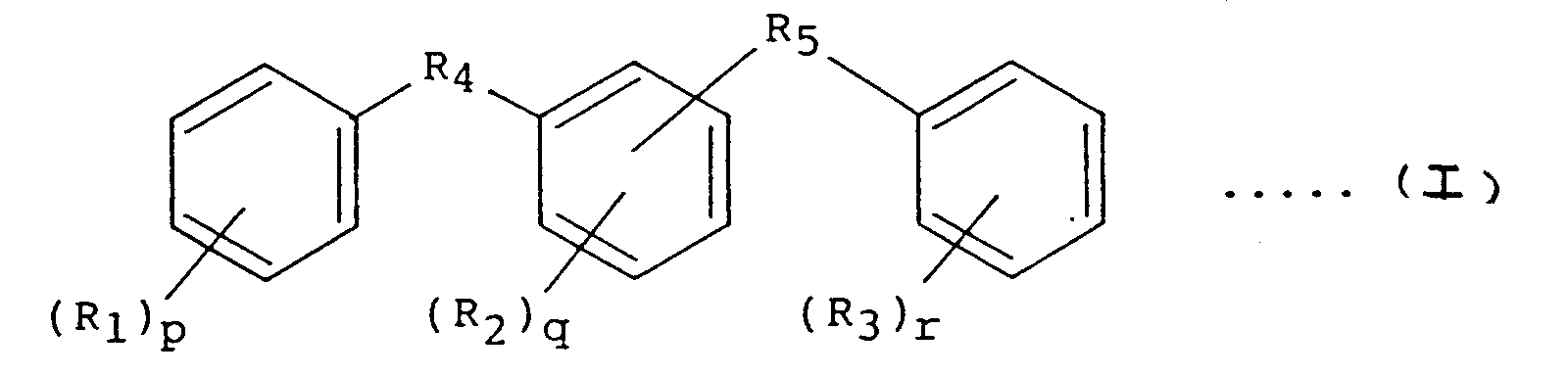
wherein each of R
1, R
2 and R
3 is a hydrogen atom or a straight chain or branched chain alkyl group; each of R
4 and R
5 is an ethylidene group; and each of p, q and r is an integer from 0 to 3.
[0032] The present invention is characterized in that the fraction mainly containing the
foregoing triaryldialkanes is used as the solvent for the dye of pressure-sensitive
recording paper. Accordingly, after the disproportionation, the catalyst is removed
by settling or filtration and the above fraction mainly containing triaryldialkanes
is obtained by distillation. The boiling temperature of the fraction that is suitable
as the solvent for the dye of pressure-sensitive recording paper is above 350°C but
not higher than 450°C, preferably below 420°C as converted to atmospheric pressure
basis. In the fraction containing triaryldialkanes having boiling points above 450°C,
the viscosity and pour point are too high which are not desirable.
[0033] As described above, since monocyclic aromatic hydrocarbons that are lighter than
the starting material are produced in the disproportionation, lighter materials can
be continuously removed outside the reaction system especially in a batchwise system.
This is desirable because the yield of the above triaryldialkanes can be improved.
[0034] The fraction mainly containing triaryldialkanes is preferable because it has no offensive
odor. In addition, in spite of its higher boiling point, the viscosity and pour point
are relatively low. Furthermore, the dissolving property (dissolving power) and color
developing property relative to the conventional dyes are also excellent. Accordingly,
the above fraction is most suitable for use as the solvent for the dye of pressure-sensitive
recording paper. Still further, when the by-product oil fraction in alkylation process
is used as a starting material, it is desirable because the solvent can be produced
at lower cost.
[0035] The solvents according to the present invention can be used singly or in a mixture
with one or more kinds of known solvents, for example, kerosene, alkylbenzenes such
as dodecylbenzene, diarylalkanes such as 1-phenyl-1-xylylethane and 1-phenyl-2-isopropylphenylethane,
alkylbiphenyls such as isopropylbiphenyl, and alkylnaphthalenes such as diisopropylnaphthalene.
[0036] Among the dyes (dye-precursors), there are typically triarylmethane type compounds,
diphenylmethane type compounds, xanthene type compounds, thiazine type compounds,
and spiropyran type compounds.
[0037] The dye-precursors of triarylmethane type compounds are exemplified by:
3,3-bis(p-dimethylaminophenyl)-6-dimethylaminophthalide (Crystal Violet Lactone);
3,3-bis(p-dimethylaminophenyl)phthalide; 3-(p-dimethylaminophenyl)-3-(1,2-dimethylindole-3-yl)-phthalide;
3-(p-dimethylaminophenyl)-3-(2-methylindole-3-yl)phthalide; 3-(p-dimethylaminophenyl)-3-(2-phenylindole-3-yl)phthalide;
3,3-bis(1,2-dimethylindole-3-yl)-5-dimethylaminophthalide; 3,3-bis(1,2-dimethylindole-3-yl)-6-dimethylaminophthalide;
3,3-bis(9-ethylcarbazole-3-yl)-5-dimethylaminophthalide; 3,3-bis(2-phenylindole-3-yl)-5-dimethylaminophthalide;
and 3-p-dimethylaminophenyl-3-(1-methylpyrrole-2-yl)-6-dimethylaminophthalide.
[0038] The dye-precursors of diphenylmethane type compounds are exemplified by:
4,4-bis-dimethylaminobenzhydrine benzyl ether;
N-halophenyl leuco Auramine; and
N-2,4,5-trichlorophenyl leuco Auramine.
[0039] The xanthene type dye-precursors are exemplified by: Rhodamine B-anilinolactam; Rhodamine
B-(p-nitroanilino)lactam; Rhodamine B-(p-chloroanilino)lactam; 3-dimethylamino-6-methoxyfluoran;
3-diethylamino-7-methoxyfluoran; 3-diethylamino-7-chloro-6-methylfluoran; 3-diethylamino-7-(acetylmethylamino)fluoran;
3-diethylamino-7-(dibenzylamino)fluoran; 3-diethylamino-7-(methylbenzylamino)fluoran;
3-diethylamino-7-(chloroethylmethylamino)fluoran; 3-diethylamino-7-(diethylamino)fluoran;
and 3-diethylamino-6-methyl-7-anilinofluoran.
[0040] The thiazine type dye-precursors are exemplified by: benzoyl leuco methylene blue
and p-nitrobenzoyl leuco methylene blue.
[0041] The spiro type dye-precursors are exemplified by: 3-methyl-spiro-dinaphthopyran;
3-ethyl-spiro-dinaphthopyran; 3,3'-dichloro-spiro-dinaphthopyran; 3-benzyl-spiro-dinaphthopyran;
3-methylnaptho-(3-methoxybenzo)spiropyran; and 3-propyl-spiro-dibenzodipyran.
[0042] The dye-precursors can be dissolved in the solvent of the invention in the same manner
as when using conventional solvents.
[0043] Among the color developer, there are clay, polymers, and aromatic carboxylic acids
or their metal salts.
[0044] The polymers are exemplified by phenol-aldehyde polymer, phenol-acetylene polymer,
maleic acid-rosin polymer, partially or completely hydrolyzed styrene-maleic anhydride
copolymer, partially or completely hydrolyzed ethylene-maleic anhydride copolymer,
carboxy polyethylene, and partially or completely hydrolyzed vinyl methyl ether-maleic
anhydride copolymer.
[0045] The aromatic carboxylic acids and their derivatives are exemplified by: 3,5-di(α-methylbenzyl)salicylic
acid; 3-(α-methylbenzyl)-5-(α,α-dimethylbenzyl)salicylic acid; 3-(4'-α',α'-dimethylbenzyl)phenyl-5-(α,α-dimethylbenzyl)salicylic
acid; 3,5-di-tert-butyl salicylic acid; 3,5-di-tert-octyl salicylic acid; 3-cyclohexyl-5-(α,α-dimethylbenzyl)salicylic
acid; 3-phenyl-5-(α,α-dimethylbenzyl)salicylic acid; and 3,5-di(α,α-dimethylbenzyl)salicylic
acid. Furthermore, their salts of polyvalent metals such as zinc, aluminum, barium,
tin, iron, calcium and lead can also be used.
[0046] As the method to prepare the microcapsules of the dye-precursor solution, which is
obtained by dissolving a dye-precursor in the solvent, there is a coacervation method
in which the fine particles of the dye-precursor solution that are dispersed in water
are coated by a protective colloidal material such as gelatin or gum arabic, thereby
obtaining the microcapsules which contain the dye-precursor solution. Another method
is the interfacial polymerization method or a in situ polymerization method in which
a monomer or a partially condensed polymerizable product is employed and a polymerization
initiator, an accelerator or a catalyst is added to cause polymerization on the surfaces
of fine particles of the dye-precursor solution, thereby preparing the microcapsules
containing the dye-precursor solution. The specific solvent of the present invention
can be used in any one of the above methods.
[0047] In the practical process for preparing microcapsules in the conventional art, an
auxiliary solvent has been used in dissolving a dye-precursor in order to control
the viscosity and volatility of the dye-precursor solution, the particle size of the
fine dispersion in microcapsule formation, the dissolving property to the polymeric
material that is coated onto the surface to be recorded, and the rate of color development.
However, the specific solvent of the present invention can satisfactorily be used
without employing such an auxiliary solvent. Nevertheless, any solvent which does
not degrade the characteristics of the solvent of the present invention may be used
as an auxiliary solvent. It should be noted also that the specific solvent of the
present invention can be used together with conventional solvents.
[0048] The present invention will be described in more detail with reference to the following
examples.
Example 1
[0049] Using aluminum chloride catalyst, alkylation was carried out by reacting batchwise
benzene with ethylene in a molar ratio (benzene:ethylene) of 5:1 at 130°C and 4.9
kg/cm
2 for 1 hour.
[0050] Unreacted benzene, ethylbenzene and polyethylbenzene were distilled off from the
above obtained reaction mixture to recover a by-product oil fraction of boiling points
260 to 310°C (converted to atmospheric pressure) that contained the following diarylalkanes.
Composition |
% by weight |
C14 - C16 diarylethane |
71 |
Others |
29 |
Total |
100 |
(Triaryldialkane was scarcely contained.) |
[0051] The above by-product oil fraction had strong offensive odor and could not be used
as a solvent.
[0052] Then, 30 g of aluminum chloride was added to 2000 ml of the above by-product oil
fraction and it was disproportionated at 80°C for 5 hours with stirring.
[0053] After the disproportionation, the catalyst was deactivated and the disproportionation
product was rinsed with water and dried. It was followed by distillation to obtain
a C
6 - C
9 monocyclic aromatic hydrocarbon fraction of 80 to 160°C in boiling points (yield:
5.0%), unreacted by-product oil fraction and heavier fraction of 351 to 400°C in boiling
points (yield: 14.8%).
[0054] It was confirmed that the above heavier fraction mainly contained triaryldialkanes
by GC-mass spectrum analysis. Furthermore, even though the fraction has high boiling
points, the pour point and viscosity of the fraction were low as follows:
Pour point |
-27.5°C |
Viscosity |
18.5 cSt (at 40°C) |
This fraction had almost no odor.
[0055] Then, 5.0 g of crystal Violet was added to 100 g of the above fraction and it was
emulsified by adding 100 g of gelatin, and water was added to make up 600 g as the
whole. The pH of the above was adjusted to 4.5 with adding an aqueous solution of
CMC and the capsule membranes were cured by glutaraldehyde to prepare microcapsule
slurry.
[0056] A paste (CMC aqueous solution) and a blocking agent were added to the above obtained
microcapsule slurry and they were mixed well. The above mixture was applied uniformly
to sheets of quality paper using a wire bar and they were dried. The coated paper
sheets were used as test papers where the the quantity of coated microcapsules was
determined by weighing the test paper that was maintained at 25 ± 1°C and 60% humidity.
[0057] This test paper was combined with another sheet of paper that was coated with acid
clay to obtain a set of pressure-sensitive recording paper. This pressure-sensitive
recording paper was applied with a load of 675 kg/cm
2 for 1 minute and color densities at 1 minute and 60 minutes after removing the load
were obtained by determining the absorbances at 610 nm. The results are shown in the
following Table 1.
[0058] For comparison purpose, 10% by weight of activated clay powder was added to the foregoing
by-product oil fraction and it was treated at 180°C for 1 hour. Meanwhile, to the
by-product oil fraction was added 5% by volume of 97 wt.% sulfuric acid and it was
shaken at room temperature for 30 minutes. The two of treated by-product oil fractions
were analyzed by GC-mass spectrum where the formation of triaryldialkane was hardly
observed. Furthermore, the odor was hardly changed after the above treatments.
Example 2
[0059] Using synthetic zeolite ZSM-5, toluene was alkylated with ethylene under the following
conditions:
Reaction temperature |
500°C |
Toluene/ethylene |
5 (molar ratio) |
WHSV |
10 |
[0060] After the alkylation, unreacted toluene, ethyltoluene and polyethyltoluene were distilled
off from the reaction mixture to obtain a heavier fraction, which had the following
property and composition:
By-Product Oil Fraction
[0061]
Boiling Point |
260 - 300°C |
Composition |
% by weight |
C14 - C15 diarylmethane |
59.1 |
C16 diarylethane |
25.9 |
Others |
15.0 |
Total |
100.0 |
(Triaryldialkane was scarcely contained) |
[0062] The odor of the by-product oil fraction obtained here was better than the by-product
oil fraction obtained in Example 1, however, it had considerable offensive odor yet.
[0063] The above by-product oil fraction (2000 ml) was disproportionated at 200°C for 3
hours under atmospheric pressure by using 50 g of strongly acidic cation exchange
resin (trademark: Nafion made by du Pont de Nemours). During the disproportionation,
the produced lighter fractions of benzene and C
7 - C
9 alkylbenzenes such as toluene were removed continuously from the reaction system.
[0064] After the disproportionation, the catalyst was filtered off and 1550 ml of the filtrate
was distilled to recover Fraction 2 containing diarylalkanes corresponding to unreacted
fraction and Fraction 3 containing heavier triaryldialkane. Incidentally, the lighter
fraction which was removed during the disproportionation was also collected, it is
also shown in the following:
Fraction |
Boiling Point |
Recovery |
Lighter fraction |
80 - 160°C |
9.9% |
Fraction 3 |
351 - 400°C |
29.5% |
[0065] It was confirmed that the above Fraction 3 mainly contained triaryldialkanes by GC-mass
spectrum analysis. This fraction had almost no odor and the properties of the fraction
were low as follows:
Pour point |
-35°C |
Viscosity |
16.8 cSt (at 40°C) |
[0066] Using the above Fraction 3, pressure-sensitive recording papers were prepared in
the like manner as Example 1 and color densities and rates of color development were
determined. The results are shown in the following Table 1.
[0067] For comparison purpose, other pressure-sensitive recording papers were prepared in
the same manner as Example 1 by using, as solvents, diisopropylnaphthalene (trademark:
KMC made by Kureha Chemical Industry) and partially hydrogenated terphenyl (trademark:
HB-40 made by Hüls), and similar tests were carried out. Their results are also shown
in Table 1.
