Field of the invention
[0001] This invention relates to a silver halide color photographic light-sensitive material
useful for the photographic field and, particularly, to a silver halide color photographic
light-sensitive material high in sensitivity and excellent in latent image preservability.
Background of the invention
[0002] In recent years, there has been a strong demand for a silver halide color photographic
light-sensitive material having a higher sensitivity and a superior image-quality,
because of the popularization of compact type cameras, automatically focusing type
single-lens reflex cameras and, in addition, film cartridges fitted with a lens. Therefore,
the demand for improving the characteristics of silver halide emulsions for photographic
use has been getting more serious, and there has also been a high-level demand for
improved photographic characteristics such as a higher sensitivity, an excellent graininess
and an excellent sharpness.
[0003] In response to the above-mentioned demands, US Patent Nos. 4,434,226, 4,439,520,
4,414,310, 4,433,048, 4,414,306 and 4,459,353 disclose the techniques applied with
tabular-shaped silver halide grains (hereinafter sometimes referred simply to as tabular
grains), whereby the following advantages have been known; namely, a sensitivity improvement
including a spectral-sensitization efficiency with a sensitizing dye, the improvements
in a sensitivity/graininess, a sharpness improvement made by the specific optical
characteristics of tabular-shaped grains and a covering-power improvement. However,
such a technique as mentioned above has still not been satisfactory, and performance
improvements are still needed.
[0004] For increasing sensitivity, a variety of analyses and technical developments have
been tried so far. There have been various factors of non-efficiency relating to the
sensitivity of an emulsion, such as preventing a free electron and a positive hole
from recombining. It is already known that a reduction-sensitization is effective
to prevent such a recombination as mentioned above.
[0005] As described in Journal of Photographic Science, Vol. 25, pp. 19-27, (1977) and Photographic
Science and Engineering, Vol. 23, pp. 113-117, (1979), a optimal reduction-sensitization
has been considered to contribute to a sensitization when making an exposure, through
the reactions represented by the following formulae, as described by Michell and Lowe
in Photographishe Korrespondenz, Vol. 1, pp. 20-, (1957) and Photographic Science
and Engineering, Vol. 19, pp. 49-55, (1975), respectively.



wherein h
+ and e
- represent a free positive hole and a free electron produced upon exposure; hv represents
a photon; and Ag
2 represents a reduction-sensitization nucleus. Based on assumption as above-mentioned,
it can be considered that a reduction-sensitization nucleus can prevent efficiency
deterioration due to the recombination of an electron and a positive hole so as to
contribute to an increase in sensitivity.
[0006] However, according to the description in Photographic Science and Engineering, Vol.
10, pp. 35-42, (1971) and, ibid., Vol. 23, pp. 113-117, (1979), a reduction-sensitization
nucleus has a capability of trapping not only a positive hole but also an electron.
Therefore, a sufficient explanation cannot always be made, based on only the above-mentioned
theory.
[0007] Different from a sensitivity speck inherent in silver halide grains described above,
the functions of reduction-sensitization of a spectrally sensitized silver halide
in the spectral-sensitizing region is really difficult to predict.
[0008] In a spectrally sensitized silver halide emulsion, light is absorbed by a sensitizing
dye, that is different from the case of the inherent sensitivity region. The primary
stage of a photosensitization is represented by formula (4), instead of formula (1).

[0009] Transfer of a dye positive hole (Dye
+) and an electron (e
-) as described in the right side of the formula to a silver halide grain depends greatly
upon the characteristics of the dye. Concerning a dye positive hole, it has generally
been regarded that a sensitization efficiency may become better when a dye positive
hole is not transferred to the inside of a grain.
[0010] For example, in Photographic Science and Engineering, Vol. 24, pp. 138-143, (1980),
discussions was made in relation to an oxidation potential (Eox) of a dye.
[0011] However, Abstracts of International Congress of Photographic Science, pp. 159-162,
(1978) and Photographic Science and Engineering, Vol. 17, pp. 235-244, (1973) each
suggest a sensitizing dye such as those in which a dye positive hole (Dye
+) produced upon exposure remains on the surface of the silver halide grain and, thereby,
a fog nucleus and a reduction-sensitization nucleus are bleached on the surface of
the silver halide grain. In a conventional surface-latent image type emulsion, it
may be expected that a latent image on the surface is bleached to result in a desensitization.
[0012] As described thus far, it has still been unknown, in a spectrally sensitized system,
whether it is better to reduction-sensitize the surface of a silver halide grain or
the inside thereof, and it is also still unknown what kinds of dyes are to be used
in combination so as to display the effects of the combination use.
[0013] As for the reduction-sensitization processes, the following processes have been known;
namely, a process in which a reduction-sensitization is applied to the surface of
a silver halide grain or it is applied in the course of growing silver halide grains,
or a process in which a seed crystal is reduction-sensitized in advance when making
use of the seed crystal for growing up a grain.
[0014] When making combination use of the process of applying a reduction-sensitization
to the surface of a grain and other sensitization processes (such as those in which
a gold compound or a sulfur compound is used), the level of unacceptable fog is seriously
increased so as not to be suitable for practical application. In contrast to the above,
a process of applying a reduction-sensitization in the course of growing silver halide
grains, that is to say, a process for applying a reduction-sensitization to the inside
of a grain, has not such a defect as mentioned above even if making combination use
of other sensitization processes.
[0015] Such a process as mentioned above is detailed in, for example, Japanese Patent Publication
Open to Public Inspection (hereinafter referred to as JP OPI Publication) Nos. 48-87825/1973
and 57-179835/1982. In these patents, however, there is no description of a spectrally
sensitized system, though the improvement of the inherent sensitivity of silver halide
is reported therein. It may be supposed that a dye positive hole remaining on the
surface of silver halide may destroy a latent image formed on the silver halide surface.
It is presumed that a reduction-sensitization cannot be effected, because a reduction-sensitization
nucleus present inside a grain does not effectively trap a dye positive hole on the
surface of the grain.
[0016] For the purpose of increasing the sensitivity of a surface latent image type silver
halide by making combination use of a reduction-sensitization and a gold·sulfur sensitization,
it has been known that the following problems still remain unsolved, from the standpoint
of improving a spectral sensitivity:
1. When applying a reduction-sensitization to the inside of a grain, there is mostly
no effect on spectral sensitization. When applying a reduction-sensitization to the
surface of a grain, on the other hand, there is still no positive evidence of a spectral
sensitization effect; and
2. When applying a reduction-sensitization to the surface of a grain, it is difficult
to make combination use thereof with a gold·sulfur sensitization, because of a high
fog.
[0017] In regard to the above-mentioned points, JP OPI Publication Nos. 2-105139/1990, 2-108038/1990,
2-125247/1990, 2-127636/1990, 2-130545/1990, 2-150837/1990, 2-168247/1990, 2-135043/1990,
4-232945/1992 and 4-32832/1992 disclose the techniques applicable particularly to
a spectrally sensitized silver halide emulsion, such as that for increasing sensitivity,
for improving preservability and for improving pressure resistance property.
[0018] However, the above-mentioned techniques have not been able to afford the practical
application, because the resulting desensitization has been increased after making
an exposure and then preserving under the conditions of a high temperature and a high
humidity over a long period of time.
Summary of the invention
[0019] It is an object of the invention to provide a silver halide color photographic light-sensitive
material improved in the above-mentioned problems, high in sensitivity and excellent
in latent image preservability (that is the stability of sensitivity obtained after
making an exposure and then preserving a subject under the conditions of high temperature
and high humidity for a long time).
[0020] The above-mentioned object of the invention can be achieved by the following constitution:
[0021] A silver halide color photographic light-sensitive material comprising a support
bearing thereon at least one silver halide emulsion layer comprising silver halide
grains, wherein the silver halide grain emulsion comprises tabular-shaped silver halide
grains having a even number of twinned crystal planes parallel to the major faces
thereof and an aspect ratio of less than 5, the tabular grains accounting for not
less than 50% of the total projected area of the grains contained in the layer and
satisfying the following requirements (A) to (C);
(A) A variation coefficient of grain-size distribution is to be not greater than 20%;
(B) Between a variation coefficient (x) of twin plane distances of the grains and
a variation coefficient (y) of thicknesses of the grains, there is a relation of 0.7≤y/x≤2.0;
and
(C) The grains are internally reduction-sensitized.
Detailed description of the invention
[0022] The silver halide grains contained in a silver halide emulsion of the invention are
to be tabular-shaped grains. Tabular-shaped grains are categorized crystallographically
as a twinned crystal.
[0023] A twinned crystal is a silver halide crystal having not less than one twinned crystal
planes in the grain thereof. The classifications of the twinned crystal shapes are
detailed in Klein & Moiser, Photographishe Korrespondenz, Vol. 99, p. 100 and, ibid.,
Vol. 100, p. 57, respectively.
[0024] Herein, a tabular-shaped grain has an even number of twin planes each parallel to
the major face of the grain. The twin planes can be observed through a transmission
type electron microscope. The specific observation method is as follows. First, a
sample is prepared in such a manner that a silver halide photographic emulsion containing
tabular-shaped grains is coated on a support so that the major face of the tabular-shaped
grains are oriented in parallel with the support. The resulting sample is cut and
scraped by making use of a diamond cutter into a thinned cut piece having a thickness
of the order of 0.1µm. When observing the resulting cut piece through a transmission
type electron microscope, the presence of the twinned crystal planes can be confirmed.
[0025] Herein, the twin plane distance is the shortest distance between two or more twin
planes parallel to the major face. Thus, the twin plane distance is the distance between
two twin planes in a grain when the grain has two twin planes, and it is the shortest
distance among the distances between twin planes in a grain when the grain has four
or more even-numbered twin planes.
[0026] Herein, a mean value of twin plane distances can be obtained in the following manner.
When observing a cut piece through a transmission type electron microscope as mentioned
above, not less than 1000 tabular-shaped grains having a section almost vertical to
the major face are selected at random. Among even-numbered twin planes parallel to
the major face, the shortest distance between two twinned crystal planes is obtained
from each grain, and the mean distance between twinned crystal planes of the grains
can be obtained as an arithmetic mean of the shortest distances.
[0027] The term, a variation coefficient (x) of twin plane distances, herein means a fluctuation
of the twin plane distances of tabular-shaped grains. It is expressed in terms of
a percentage obtained by dividing a standard deviation value of the twin plane distances
by a mean value of the twin plane distances.
[0028] In the emulsion of the invention, the mean twin plane distance is from 0.01µm to
0.05µm and, more preferably, from 0.013µm to 0.03µm.
[0029] The mean thickness of tabular-shaped grains useful in the emulsion of the invention
can be obtained in such a manner that the thickness of each grain is obtained by observing
the cut piece of a subject sample through a transmission type electron microscope
in the same manner as described above and the mean thickness of the grains can be
obtained by averaging out the thickness of the grains as an arithmetic mean. The mean
thickness of the tabular-shaped grains is from 0.05µm to 1.5µm and, more preferably
from 0.15µm to 1.0µm.
[0030] The term, a variation coefficient (y) of thicknesses of tabular-shaped grains, herein
means fluctuation of the thicknesses among the tabular-shaped grains. It is expressed
in terms of a percentage obtained by dividing a standard deviation of grain thickness
by a mean value of the grain thickness.
[0031] Tabular-shaped grains useful in the emulsion of the invention have the following
relations;
[0032] Between a variation coefficient (x) of distances between the twin planes and a grain-thickness
variation coefficient (y), there is a relation of 0.7≤y/x≤2.0, preferably, 0.8≤y/x≤1.6
and, most preferably, 0.9≤y/x≤1.3.
[0033] A tabular-shaped grain useful in the emulsion of the invention is defined as that
having an aspect ratio (a grain-size/a grain thickness) of lower than 5, preferably
not higher than 4.0.
[0034] Herein, the grain-size of a silver halide grain is indicated by a diameter equivalent
to that of a circle having the same area as the projected area of the silver halide
grain (i.e., a circular-equivalent diameter). It is preferably from 0.1 to 5.0µm and,
more preferably from 0.2 to 2.0µm.
[0035] A grain-size can be obtained, for example, in the following manner. A subject grain
is magnified 10,000 to 70,000 times through an electron microscope and then photographed.
The resulting diameter of the grain coming out on a print or the projected area of
the grain is practically measured, provided that the number of the grains subject
to the measurement is to be not less than 1,000 at random.
[0036] An average grain-size r is herein defined as a grain-size ri when maximizing a product
ni×ri
3 in which ni represents a frequency of grains having a grain-size ri, provided that
a significant figure is three columns and the figure in the lowest column is rounded.
[0037] A silver halide emulsion of the invention preferably comprises a monodisperse type
silver halide emulsion. As for the monodisperse type silver halide emulsions, the
weight of silver halide having a grain-size within the scope of ±20% of an average
grain-size r is to be, preferably, not less than 60% of the weight of the whole silver
halide grain, more preferably, not less than 70% and, particularly, not less than
80%.
[0038] When defining a grain-size distribution width in the following formula,
a monodispersed type emulsion of the invention has a grain-size distribution width
of not higher than 20%, more preferably not higher than 15% and, most preferably,
not higher than 12%. An average grain-size and a standard deviation are herein obtained
from the above-defined grain-size ri.
[0039] Herein, the distance between twin planes may be controlled by suitably selecting
the following various factors, which may give an influence on the supersaturated state
in the nucleation stage, including for example a gelatin concentration, a gelatin
type, a temperature, an iodide ion concentration, a pBr, a pH, an ion-supply rate,
an rpm for stirring and a combination thereof. Generally, the higher supersaturation
in the nucleation stage, the smaller becomes the distance between twin planes.
[0040] The details of the above-mentioned supersaturation factors may be referred to the
descriptions appeared in JP OPI Publication No. 63-92924/1988 or, ibid., No. 1-213637/1989.
[0041] Silver halide grains useful in the emulsion of the invention are internally reduction-sensitized,
thus, an internal portion of the grain is subjected to reduction sensitization. The
word internal portion herein means an inner portion of 90% or less and preferably
70% or less of the grain, based on the volume. In other words, silver halide grains
useful in the emulsion of the invention are subjected to reduction sensitization before
90% (preferably, 70%) of the ultimate grain volume of the grain is reached.
[0042] The above-mentioned reduction-sensitization is carried out by adding a reducing agent
to a silver halide emulsion or a mixed solution during the growth of the grains. Or,
it is carried out by ripening or grain-growing a silver halide emulsion or a mixed
solution for growing grains under the conditions of a low pAg of not higher than pAg
7 or a high pH of not lower than pH 7. A process carried out by making combination
use of the above-mentioned methods is preferred.
[0043] Preferable reducing agents include, for example, thiourea dioxide, ascorbic acid
and the derivatives thereof, and stannous salt. Other suitable reducing agents include,
for example, a borane compound, a hydrazine derivative, formamidine sulfinic acid,
a silane compound, an amine and a polyamine, and a sulfite. They may be added preferably
in an amount of from 10
-2 to 10
-8 mols per mol of silver halide used therein.
[0044] For performing a ripening treatment at a low pAg, a silver salt may be added. Among
the silver salts for this purpose, a water-soluble silver salt is preferred. Among
the water-soluble silver salts, silver nitrate is preferred. When carrying out a ripening
treatment, the pAg is suitably not higher than 7, preferably, not higher than 6 and,
particularly, from 1 to 3, provided, pAg = -log[Ag
+].
[0045] A high pH ripening treatment may be carried out, for example, by adding an alkaline
compound to a silver halide emulsion or a mixed solution for growing grains. The alkaline
compounds applicable thereto include, for example, sodium hydroxide, potassium hydroxide,
sodium carbonate, potassium carbonate and ammonia. In a process for adding an ammoniacal
silver nitrate for producing silver halide, alkaline compounds other than ammonia
may preferably be used, because the ammonia effect may be deteriorated.
[0046] As for the process of adding a silver salt or an alkaline compound for making a reduction-sensitization,
they may be rush added or may also be added by taking a given time. In the latter
instance, it may be added at a certain flow rate or may also be added by varying acceleratedly
the flow rate thereof. It is also allowed to add a necessary amount divided into several
parts for the addition. In advance of adding a soluble silver salt and/or a soluble
halide to a reaction chamber, the silver salts or an alkaline compound for a reduction-sensitization
may be made present in the reaction chamber, or they are mixed in a soluble halide
solution and then they may be added together with the halide. Besides the above, they
may further be added, separately from the soluble silver salt and soluble halide.
[0047] For preparing a silver halide emulsion of the invention, a process of growing grains
from seed grains is preferably used. To be more specific in the process an aqueous
solution containing protective colloid and seed grains are made present in a reaction
chamber in advance and silver ions, halogen ions or silver halide fine grains are
supplied thereto, so that the seed grains are grown up to final grains. Therein, the
seed grains may be prepared by a single-jet process or a controlled double-jet process,
which have been well-known in the art. Any halogen composition of the seed grains
may be used therein, including any one of silver bromide, silver iodide, silver chloride,
silver iodobromide, silver chloroiodide, silver chlorobromide and silver chloroiodobromide.
Among them, silver bromide and silver iodobromide are preferred. In the case of silver
iodobromide, the average silver iodide content thereof is preferably within the range
of from 1 mol% to 20 mol%.
[0048] To meet the afore-mentioned requirement 0.7 ≦ y/x ≦ 2.0, a value of x is preferably
as small as possible. In order to decrease the value of x , silver halide grains are
preferably grown from seed grains having narrow distance(s) between twin planes. Preferably,
the pBr of a reaction mother liquor is maintained at 2.5 or less (more preferably,
from 1.0 to 2.0) at the nucleation stage in the course of forming seed grains to decrease
the distance between twin planes of the seed grains. It is further preferable that
the resulting nucleus grains are subjected to ripening to dissolve grains other than
those having an even number of twin planes. The ripening is carried out at 30°C (preferably,
from 18 to 26°C) and in the presence of a silver halide solvent such as ammonia, thioether,
or thiocyanate. In the case when using ammonia as the solvent, the amount thereof
may be 0.10 mol/l or more, preferably from 0.2 to 2.0 mol/l. In the present invention,
x is preferably 20% or less, more preferably 15% or less.
[0049] In the process of growing crystals from seed grains, it is preferable that ripening
treatment at a low pAg is carried out by adding silver nitrate thereto, that is to
say, the ripening treatment is preferably carried out by adding silver nitrate in
the course between the point of time immediately before desalting the seed grain emulsion
and the time after completing the desalting treatment thereof. It is particularly
preferable to add silver nitrate after desalting and then ripening the seed grains.
The ripening temperature is preferably kept not lower than 40°C, more preferably from
50°C to 80°C. The ripening time is preferably taken for not shorter than 30 minutes,
more preferably from 50 to 150 minutes.
[0050] In the system of carrying out a grain growing treatment by making use of seed grains
and when carrying out ripening treatment at a high pH therein, it is necessary to
grow the grains by subjecting them to an environment having a pH of not lower than
7 at least once, before 70% of the ultimate grain volume of the grown-up grains is
reached. It is more preferable to grow up the grains by subjecting them to an environment
having a pH of not lower than 7 at least once, before 50% of the ultimate grain volume
of the grown-up grains is reached. It is particularly preferable to grow up the grains
by subjecting them to an environment having a pH of not lower than 8 at least once,
before 40% of the ultimate grain volume of the grown-up grains is reached.
[0051] An oxidizing agent may be applied to a silver halide emulsion of the invention. The
oxidizing agent applicable thereto includes, for example, the following ones:
[0052] Hydrogen peroxide (in an aqueous solution) and the adducts thereof such as H
2O
2, NaBO
2-H
2O
2-3H
2O, Na
4P
2O
7-2H
2O
2 and 2Na
2SO
4-H
2O
2-2H
2O; peroxy acid salt such as K
2S
2O
3, K
2C
2O
3, K
4P
2O
3 and K2[Ti(O
2)C
2O
4]-3H
2O; peracetic acid; ozone; iodine; bromine; and a thiosulfonic acid derivative.
[0053] The above-mentioned oxidizing agent may be added preferably in an amount of from
10
-2 to 10
-5 mols per mol of a reducing agent used therein, provided, however, that such an adding
amount thereof as mentioned above may be varied, according to the kind of reducing
agent used, the conditions of reduction-sensitization, addition time of an oxidizing
agent and the condition of adding the oxidizing agent.
[0054] The oxidizing agent may be added optimally at a time during the course of preparing
a silver halide emulsion. It is also allowed to add it in advance of adding a reducing
agent.
[0055] It is further allowed to newly add a reducible substance after adding an oxidizing
agent so that an excessive oxidizing agent may be neutralized. Such reducible substances
as mentioned above are those capable of reducing the above-mentioned oxidizing agent,
and the reducible substances include, for example, a sulfinic acid, a di- and trihydroxybenzene,
a chroman, a hydrazine and hydrazide, a p-phenylenediamine, an aldehyde, an aminophenol,
an endiol, an oxime, a reducible sugar, a phenidone, a sulfite and an ascorbic acid
derivative. These reducible substances may be added preferably in an amount of from
10
-3 to 10
3 mols per mol of an oxidizing agent used.
[0056] A silver halide grain useful in the emulsion of the invention comprises substantially
silver iodobromide. However, it is allowed to contain silver chloride therein, provided
that the effects of the invention shall not be deteriorated thereby.
[0057] It is preferable that the silver halide grains useful in the emulsion of the invention
have a silver iodobromide phase comprising not less than 5 mol% of silver iodide inside
the grain. It is more preferable that the silver halide grain has a silver iodobromide
phase comprising silver iodide in a proportion of from 10 mol% to 40 mol%. The expression,
grain have a silver iodobromide phase inside the grain, herein means an internal portion
of 90% or more inside of the grain and preferably 50% or more inside thereof, based
on the ultimate volume of the grain.
[0058] Silver halide grains useful in the emulsion of the invention are preferably the so-called
core/shell type grains comprising silver iodide localized inside the grain.
[0059] A silver halide grain useful in the emulsion of the invention is preferably comprised
of silver iodobromide having an average silver iodide content within the range of,
preferably, from 1 mol% to 20 mol% and, more preferably, from 3 to 15 mol%.
[0060] As for the means for preparing a silver halide emulsion useful in the emulsion of
the invention, a variety of means well-known in the field of the art may be used.
The following means can be used in any combination, namely, a single-jet precipitation,
a controlled double-jet precipitation, a controlled triple-jet precipitation and so
forth. However, for obtaining the highly monodisperse type grains useful in the invention,
it is essential to control the pAg in the solution in which the silver halide grains
are produced, so as to meet the silver halide grain growth rate. Such a pAg value
as mentioned above is preferably from 7.0 to 10.5, more preferably from 7.5 to 10.0
and, further preferably from 8.0 to 9.5.
[0061] In the afore-mentioned requirement, 0.7 ≦ y/x ≦ 2.0, the value of y is preferably
as small as possible to meet the requirement. To decrease y, it is essential to control
the pAg of a solution. The pAg is preferably from 7.5 to 10.0, more preferably from
8.0 to 9.5. In the present invention, y is 20% or less, preferably 15% or less.
[0062] When determining an addition rate, JP OPI Publication Nos. 54-48521/1979 and 58-49938/1983
may be referred to.
[0063] It is allowed to make present a well-known silver halide solvent such as ammonia,
thioether and thiourea, or no silver halide solvent may be used, when preparing silver
halide grains useful in the emulsion of the invention.
[0064] Silver halide grains useful in the invention may be either those capable of forming
a latent image mainly on the surface thereof, or those capable of forming a latent
image mainly inside the grain. Herein, is preferable a surface latent image-forming
silver halide emulsion.
[0065] Silver halide grains useful in the invention are prepared in the presence of a dispersion
medium, that is, in an aqueous solution containing the dispersion medium. The expression,
an aqueous solution containing a dispersion medium, herein means an aqueous solution
in which a protective colloid is formed of a substance capable of constituting hydrophilic
colloid (that is, for example, a substance capable of serving as a binder) such as
gelatin, and it also preferably means an aqueous solution containing a protective
colloidal gelatin.
[0066] When gelatin is used as the above-mentioned protective colloid, the gelatin may be
either lime-treated or acid-treated. Details of the gelatin preparation is referred
to Arthur Veis, The Macromolecular Chemistry of Gelatin, Academic Press, 1964.
[0067] Hydrophilic colloids other than gelatin, which can be used as a protective colloid,
include, for example, the following substances; namely, a protein such as a gelatin
derivative, a graft polymer of gelatin and other polymer, albumin and casein; a cellulose
derivative such as hydroxyethyl cellulose, carboxymethyl cellulose and a cellulose
sulfate; a sugar derivative such as sodium alginate and a starch derivative; and various
kinds of synthetic hydrophilic macromolecular substance such as a monomer or copolymer
of polyvinyl alcohol, polyvinyl alcohol partial acetal, poly-N-vinyl pyrrolidone,
polyacrylic acid, polymethacrylic acid, polyacrylamide, polyvinyl imidazole or polyvinyl
pyrazole.
[0068] In the case of making use of gelatin, it is preferable to make use of those having
a jelly strength of not lower than 200 in AGI's method.
[0069] Silver halide grains useful in the invention can contain a metal ion inside the grain
and/or on the surface of the grain by adding a metal ion to the grain by making use
of at least one chosen from a cadmium salt, a zinc salt, a lead salt, a thallium salt,
an iron salt, a rhodium salt, an iridium salt and an indium salt (including the complex
salts thereof), in the course of forming the grain and/or growing the grain.
[0070] A silver halide grain useful in the invention may be a grain from which any unnecessary
soluble salts are optionally removed after completing the growth of the silver halide
grain.
[0071] As in the method described in JP OPI Publication No. 60-138538/1985, a desalting
treatment can be performed at any point in the course of preparing silver halide.
When trying to remove the above-mentioned salts, they can be removed in the method
described in Research Disclosure (hereinafter abbreviated to RD) No. 17643, Article
II. To be more detailed, for removing a soluble salt from an emulsion after completing
precipitation or physical ripening, it is allowed to make use of a noodle-washing
method in which gelatin is gelled, or to make use of a flocculation method in which
an inorganic salt, an anionic surfactant, an anionic polymer (such as polystyrene
sulfonic acid) or a gelatin derivative (such as acylated gelatin and carbamoylated
gelatin) is utilized.
[0072] A silver halide grain useful in the invention can be chemically sensitized in an
ordinary method. To be more specific, a sulfur sensitization method, a selenium sensitization
method, a noble-metal sensitization method in which gold or other noble metal compound
is used, and so forth may be used alone or in combination.
[0073] Silver halide grains useful in the invention can be spectrally sensitized to any
desired wavelength region by making use of a dye that has been known as a sensitizing
dye in the photographic field. Such a sensitizing dye as mentioned above may be used
alone or in combination. It is also allowed that an emulsion is to contain, together
with a sensitizing dye, a supersensitizer capable of enhancing the sensitizing effect
of a sensitizing dye, that is a dye having no spectral sensitizing function in itself,
or, that is a compound substantially incapable of absorbing any visible rays of light.
[0074] An antifoggant or stabilizer may be added to a silver halide grain emulsion of the
invention.
[0075] As for a binder applicable to the invention, it is advantageous to use gelatin. An
emulsion layer and other hydrophilic colloidal layers may be hardened and, a plasticizer
and a water-insoluble or water-soluble synthetic polymer dispersion (so-called a latex)
may also be contained therein.
[0076] A coupler is used in an emulsion layer of a silver halide color photographic light-sensitive
material of the invention. It is also allowed to use a competing coupler having a
color correction effect and a compound capable of releasing such a photographically
useful fragment as a development accelerator, a developing agent, a silver halide
solvent, a color toner, a layer hardener, a foggant, an antifoggant, a chemical sensitizer,
a spectral sensitizer and a desensitizer, through a coupling reaction with the oxidized
product of a developing agent.
[0077] To a silver halide color photographic light-sensitive material of the invention,
an auxiliary layer such as a filter layer, an antihalation layer and an anti-irradiation
layer may be provided. In the above-mentioned layer and/or an emulsion layer, it is
also allowed to contain a dye capable of being dissolved out of a light-sensitive
material or being bleached, in the course of carrying out the development treatment.
[0078] To a silver halide color photographic light-sensitive material of the invention,
may be added a matting agent, a lubricant, an image stabilizer, a formalin scavenger,
a UV absorbent, a fluorescent whitening agent, a surfactant, a development accelerator
and a development retarder.
[0079] As for the supports useful in the material of the invention, a sheet of paper laminated
thereon with eg. polyethylene, polyethylene terephthalate film, baryta paper or cellulose
triacetate film may be used.
Examples
[0080] The invention will now be detailed with reference to the following examples. However,
the embodiments of the invention shall not be limited thereto.
Example 1
(Preparation of twinned crystal emulsion T-1)
[0081] According to the following process, a seed emulsion having two parallel twin planes
was prepared:
(Solution A) |
Ossein gelatin |
80.0 g |
Potassium bromide |
47.4 g |
A 10 wt% methanol solution of HO (CH2CH2O)m[CH(CH3)CH2O]19.8(CH2CH2O)nH (m+n=9.77) |
0.48 ml |
Add distilled water to make |
8000.0 ml |
(Solution B) |
Silver nitrate |
1200.0 g |
Add distilled water to make |
1600.0 ml |
(Solution C) |
Ossein gelatin |
32.2 g |
Potassium bromide |
790.0 g |
Potassium iodide |
70.34 g |
Add distilled water to make |
1600.0 ml |
(Solution D) |
Aqueous ammonia |
470.0 ml |
[0082] Solution A was violently stirred at 40°C and Solutions B and C were added to Solution
A in a double-jet method for 7 minutes so as to produce nuclei. During the addition
thereof, the pBr of the mixture was kept at 1.60. Thereafter, the temperature of the
mixture was lowered to be 20°C by taking 30 minutes. Further, Solution D was added
thereto by taking one minute and, successively, the mixture thereof was ripened for
5 minutes. While the mixture was being ripened, the KBr concentration and ammonia
concentration were 0.03 mols/liter and 0.66 mols/liter, respectively.
[0083] After completing the ripening treatment, the pH was adjusted to be 6.0 and a desalting
treatment was carried out in an ordinary method. To the resulting emulsion was added
an aqueous 10 wt% gelatin solution and the emulsion was then stirred to be dispersed
at 60°C for 30 minutes. Thereafter, distilled water was added thereto, so that 5360
g of an emulsion was made up.
[0084] When observing the resulting seed emulsion grains through an electron microscope,
they were proved to be tabular-shaped grains having two twin planes parallel to each
other.
[0085] It was also proved that the average grain-size of the seed emulsion grains was 0.217µm
and that the grains having two parallel crystal planes amounted to 75% (in number)
of the whole grain.
(Preparation of twinned crystal, seed grain emulsion T-2 ripened at a low pAg)
[0086] In the process for preparing seed emulsion T-1, 1884 ml of an aqueous 10 wt% gelatin
solution was added to a desalted emulsion and was then stirred the emulsion to be
dispersed at 60°C for 15 minutes. Then, 130 ml of an aqueous solution containing 21
g of silver nitrate was added thereto and the pAg value of the emulsion was then adjusted
to be 1.88. Successively, a ripening treatment was carried out by stirring the emulsion
at 60°C for 80 minutes. Thereafter, 193 ml of an aqueous solution containing 14.5
g of potassium bromide was added. The emulsion temperature was lowered to 40°C and
distilled water was added, so that 5360 g of an emulsion could be prepared.
[0087] When observing the resulting seed emulsion grains through an electron microscope,
they were proved to be the tabular-shaped grains having two twin planes parallel to
each other. It was also proved that the average grain-size of the seed emulsion grains
was 0.217µm and that the grains having two parallel crystal planes amounted to 75%
(in number) of the whole grain.
(Preparation of Emulsion EM-1 of the invention)
[0088] Tabular-shaped emulsion EM-1 of the invention was prepared by making use of the following
7 kinds of solutions, (among them, Solution A contained seed emulsion T-2 subjected
to a low pAg ripening treatment).
(Solution A) |
Ossein gelatin |
67.0 g |
Distilled water |
3176 ml |
A 10 wt% methanol solution of HO(CH2CH2O)m[CH(CH3)CH2O]19.8(CH2CH2O)nH (m+n=9.77) |
2.50 ml |
Seed emulsion (T-2) |
98.51 g |
Add distilled water to make |
3500.0 ml |
(Solution B) |
An aqueous 0.5N silver nitrate solution |
948 ml |
(Solution C) |
Potassium bromide |
52.88 g |
Ossein gelatin |
35.55 g |
Add distilled water to make |
948 ml |
(Solution D) |
An aqueous 3.5N silver nitrate solution |
4471 ml |
(Solution E) |
Potassium bromide |
1862.2 g |
Ossein gelatin |
200 g |
(Solution F) |
A fine-grain emulsion(*) comprising 3 wt% of gelatin and silver iodide grains (having
an average grain-size of 0.05µm) |
2465.5 g |
(*) The preparation process thereof will be detailed below. |
[0089] An aqueous solution containing 7.06 mols of silver nitrate and an aqueous solution
containing 7.06 mols of potassium iodide were each added in an amount of 2000ml to
5000ml of a 6.0 wt%-gelatin solution containing 0.06 mols of potassium iodide by taking
10 minutes, respectively. The pH and temperature were controlled with nitric acid
so as to be 2.0 and 40°C while the fine grains were being produced. After the grains
were formed, the pH was adjusted with an aqueous sodium carbonate solution so as to
be 6.0. The finished amount by weight was proved to be 12.53 kg.
(Solution G)
[0090] An aqueous 1.75N potassium bromide solution
[0091] Solution A was added to a reactor vessel. Solutions B through F were added thereto,
with stirring, by a double-jet method in accordance with the combination shown in
Table 1, and the seed crystals were grown up, so that a core/shell type silver halide
grain emulsion was prepared.
[0092] Therein, (1) the adding rates of Solutions (B), (C) and (F), (2) the adding rates
of Solutions (D), (E) and (F), and (3) the adding rates of Solutions (D) and (E) were
optimally controlled to meet the critical growth rate of silver halide grains so that
any small grains other than the growing seed crystal grains were neither produced
nor polydispersed in an Ostwald's ripening.
[0093] Extending over the whole region of growing crystals, the temperature and pAg of each
of the solutions were controlled to be 75°C and 8.8 in the reactor vessel, respectively.
For controlling the pAg, Solution G was added when necessary.
[0094] Table 1 shows the grain-sizes at the points of time corresponding to each of the
time of adding the solutions, and the silver iodide contents of the silver halide
phases capable of forming each of the grain surfaces.
[0095] After growing up the grains, a desalting treatment was carried out according to the
method described in JP Application No. 3-41314/1991 and a redispersion treatment was
carried out by adding gelatin. The pH and pAg of the emulsion were controlled to be
5.80 and 8.06 at 60°C, respectively. From the electronmicrograph of the resulting
emulsion grains, the resulting grains were proved to be the tabular-shaped grains
having an average grain-size of 1.23µm, an average aspect ratio of 2.0 and an average
grain-size distribution of 12.0%.
Table 1
Solution added |
Time of adding a solution (min.) |
Grain-size (µm) |
AgI content (mol%) |
(1) B,C,F |
0.00 |
0.217 |
6.0 |
(1) B,C,F |
12.50 |
0.318 |
8.4 |
(1) B,C,F |
22.83 |
0.370 |
10.8 |
(1) B,C,F |
30.98 |
0.410 |
13.2 |
(2) D,E,F |
30.99 |
0.410 |
13.2 |
(2) D,E,F |
52.82 |
0.499 |
20.4 |
(2) D,E,F |
76.69 |
0.584 |
30.0 |
(2) D,E,F |
122.33 |
0.715 |
30.0 |
(2) D,E,F |
150.56 |
0.780 |
30.0 |
(2) D,E,F |
155.12 |
0.790 |
27.5 |
(2) D,E,F |
176.38 |
0.836 |
15.1 |
(2) D,E,F |
187.90 |
0.860 |
7.7 |
(3) D,E |
188.00 |
0.862 |
0.0 |
(3) D,E |
210.46 |
0.959 |
0.0 |
(3) D,E |
224.92 |
1.062 |
0.0 |
(3) D,E |
233.55 |
1.133 |
0.0 |
(3) D,E |
243.00 |
1.230 |
0.0 |
(Preparation of emulsion EM-2 of the invention)
[0096] Emulsion EM-2 was prepared in the same manner as in the process of preparing emulsion
EM-1, except that 10 ml of an aqueous solution containing 2.0 g of potassium hydroxide
was added to seed emulsion T-1 at the point of time 65 minutes after starting the
addition of a solution for growing the crystals so that the pH of the emulsion was
adjusted to be 8.7 in a reaction system. At the point of time when completing the
addition of the reactive solution for growing the crystals, the pH of the emulsion
was lowered to be 5.8.
[0097] From the scanning type electron microscopic photograph of the resulting emulsion
grains, the grains were proved to be the tabular-shaped grains having an average grain-size
of 1.24µm, an average aspect ratio of 2.1 and a grain-size distribution of 12.5%.
[0098] Also, in the process of preparing emulsion EM-1, emulsion EM-3 for comparative use
was prepared in the same manner as in the case of emulsion EM-1, except that seed
emulsion T-1 was used and the pAg in the course of growing the crystals was controlled
to be 11.0.
[0099] Further, in the process of preparing emulsion EM-2, emulsion EM-4 for comparison
use was prepared in the same manner as in emulsion EM-2, except that potassium hydroxide
was not added in the course of growing the crystals.
[0100] Still further, Emulsions EM-5 through EM-9 were each prepared by replacing seed emulsions,
by changing the conditions for ripening the seed emulsions at a low pAg, by omitting
or applying a high-pH ripening treatment in the course of growing the crystals, by
altering the positions of adding potassium hydroxide in the course of growing the
crystals or by varying the pAg control values in the course of growing the crystals.
[0101] For determining the distance between twin planes and the grain thickness, they were
observed at a temperature of -120°C, through a transmission type electron microscope
Model JEM-2000FX manufactured by Japan Electron Co., Ltd at an acceleration voltage
of 200KV.
[0102] Table 2 collectively shows the conditions for preparing emulsions EM-1 through EM-9
and the results obtained.
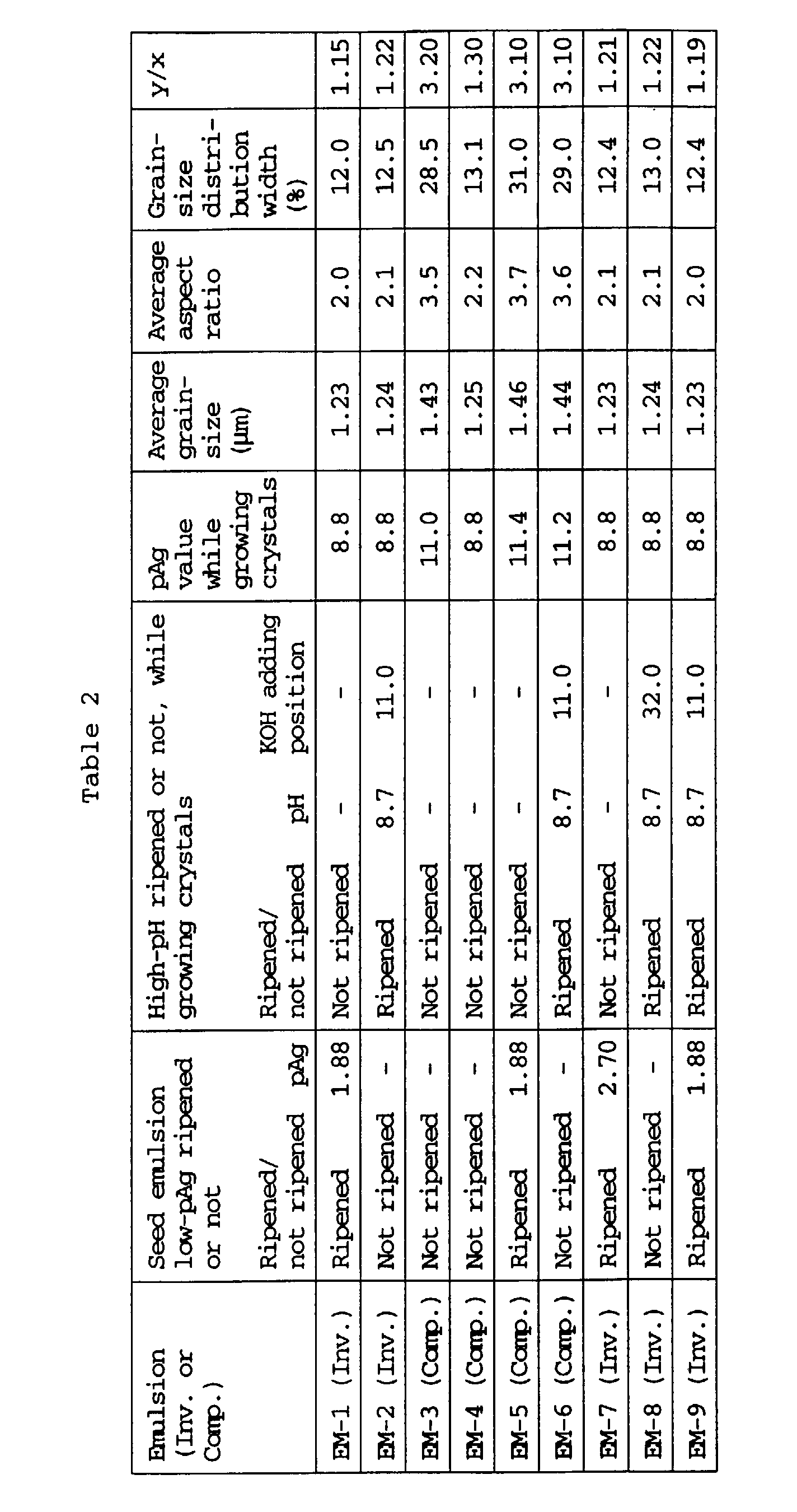
[0103] In the table, the KOH adding positions represent in terms of (the volume of a grain
at the point of time when adding KOH / the volume of the grain after growing the crystal)
× 100; and y/x represents a variation coefficient (y) of a grain thickness / a variation
coefficient (x) of a distance between twinned crystal planes.
[0104] As is obvious from Table 2, when the pAg of an emulsion was controlled to not lower
than 11.0 in the course of growing crystals, the grain-size distribution was widened
and the y/x value was increased. This fact indicates that the dispersion of the grain
thickness was increased, as well as that the grain-sizes were dispersed. On the other
hand, for an emulsion which was controlled to a pAg value of 8.8 in the course of
growing the grains, the grain-size distribution was narrowed and the y/x value was
also decreased. It was a very interesting discovery that fluctuations in the grain-size
and grain thickness depended upon the pAg value obtained when growing the grains.
Example 2 (Preparation of a silver halide color photographic light-sensitive material
sample)
[0105] A silver halide color photographic light-sensitive material of the invention was
prepared in the following manner. An optimum gold-sulfur sensitization was applied
to each of emulsions EM-1 to EM-9. By making use of the resulting emulsions, each
of the layers having the following compositions was formed on a tricetyl cellulose
support in order from the side of the support.
[0106] In every description herein given, every addition into amount of a silver halide
photographic light-sensitive material is indicated in terms of grams per sq.meter,
unless otherwise expressly stated. Amounts of silver halide and colloidal silver are
each indicated by the silver contents converted therefrom. The amount of the sensitizing
dyes is indicated in terms of mols per mol of silver halide used therein.
[0107] The constitution of silver halide color photographic light-sensitive material sample
101 of the invention (in which emulsion EM-1 of the invention was used) was as follows.
Sample 101
[0108]
Layer 1 : An antihalation layer |
Black colloidal silver |
0.16 |
UV absorbent (UV-1) |
0.20 |
High boiling solvent (OIL-1) |
0.16 |
Gelatin |
1.60 |
Layer 2 : An intermediate layer |
Compound (SC-1) |
0.14 |
High boiling solvent (OIL-2) |
0.17 |
Gelatin |
0.80 |
Layer 3 : A low-speed red-sensitive layer |
Silver iodobromide emulsion A |
0.15 |
Silver iodobromide emulsion B |
0.35 |
Sensitizing dye (SD-1) |
2.0x10-4 |
Sensitizing dye (SD-2) |
1.4x10-4 |
Sensitizing dye (SD-3) |
1.4x10-5 |
Sensitizing dye (SD-4) |
0.7x10-4 |
Cyan coupler (C-1) |
0.53 |
Colored cyan coupler (CC-1) |
0.04 |
DIR compound (D-1) |
0.025 |
High boiling solvent (OIL-3) |
0.48 |
Gelatin |
1.09 |
Layer 4 : A medium-speed red-sensitive layer |
Silver iodobromide emulsion B |
0.30 |
Silver iodobromide emulsion C |
0.34 |
Sensitizing dye (SD-1) |
1.7x10-4 |
Sensitizing dye (SD-2) |
0.86x10-4 |
Sensitizing dye (SD-3) |
1.15x10-5 |
Sensitizing dye (SD-4) |
0.86x10-4 |
Cyan coupler (C-1) |
0.33 |
Colored cyan coupler (CC-1) |
0.013 |
DIR compound (D-1) |
0.02 |
High boiling solvent (OIL-1) |
0.16 |
Gelatin |
0.79 |
Layer 5 : A high-speed red-sensitive layer |
Emulsion EM-1 |
0.95 |
Sensitizing dye (SD-1) |
1.0x10-4 |
Sensitizing dye (SD-2) |
1.0x10-4 |
Sensitizing dye (SD-3) |
1.2x10-5 |
Cyan coupler (C-2) |
0.14 |
Colored cyan coupler (CC-1) |
0.016 |
High boiling solvent (OIL-1) |
0.16 |
Gelatin |
0.79 |
Layer 6 : An intermediate layer |
Compound (SC-1) |
0.09 |
High boiling solvent (OIL-2) |
0.11 |
Gelatin |
0.80 |
Layer 7 : A low-speed green-sensitive layer |
Silver iodobromide emulsion A |
0.12 |
Silver iodobromide emulsion B |
0.38 |
Sensitizing dye (SD-4) |
4.6x10-5 |
Sensitizing dye (SD-5) |
4.1x10-4 |
Magenta coupler (M-1) |
0.14 |
Magenta coupler (M-2) |
0.14 |
Colored magenta coupler (CM-1) |
0.06 |
High boiling solvent (OIL-4) |
0.34 |
Gelatin |
0.70 |
Layer 8 : An intermediate layer |
Gelatin |
0.41 |
Layer 9 : A medium-speed green-sensitive layer |
Silver iodobromide emulsion B |
0.30 |
Silver iodobromide emulsion C |
0.34 |
Sensitizing dye (SD-6) |
1.2x10-4 |
Sensitizing dye (SD-7) |
1.2x10-4 |
Sensitizing dye (SD-8) |
1.2x10-4 |
Magenta coupler (M-1) |
0.04 |
Magenta coupler (M-2) |
0.04 |
Colored magenta coupler (CM-1) |
0.017 |
DIR compound (D-2) |
0.025 |
DIR compound (D-3) |
0.002 |
High boiling solvent (OIL-4) |
0.12 |
Gelatin |
0.50 |
Layer 10: A high-speed green-sensitive layer |
Silver iodobromide emulsion D |
0.95 |
Sensitizing dye (SD-6) |
7.1x10-5 |
Sensitizing dye (SD-7) |
7.1x10-5 |
Sensitizing dye (SD-8) |
7.1x10-5 |
Magenta coupler (M-1) |
0.09 |
Colored magenta coupler (CM-1) |
0.011 |
High boiling solvent (OIL-4) |
0.11 |
Gelatin |
0.79 |
Layer 11: A yellow filter layer |
Yellow colloidal silver |
0.08 |
Compound (SC-1) |
0.15 |
High boiling solvent (OIL-2) |
0.19 |
Gelatin |
1.10 |
Layer 12: A low-speed blue-sensitive layer |
Silver iodobromide emulsion A |
0.12 |
Silver iodobromide emulsion B |
0.24 |
Silver iodobromide emulsion C |
0.12 |
Sensitizing dye (SD-9) |
6.3x10-5 |
Sensitizing dye (SD-10) |
1.0x10-5 |
Yellow coupler (Y-1) |
0.50 |
Yellow coupler (Y-2) |
0.50 |
DIR compound (D-4) |
0.04 |
DIR compound (D-5) |
0.02 |
High boiling solvent (OIL-2) |
0.42 |
Gelatin |
1.40 |
Layer 13: A high-speed blue-sensitive layer |
Silver iodobromide emulsion C |
0.15 |
Silver iodobromide emulsion E |
0.80 |
Sensitizing dye (SD-9) |
8.1x10-5 |
Sensitizing dye (SD-11) |
3.1x10-5 |
Yellow coupler (Y-1) |
0.12 |
High boiling solvent (OIL-2) |
0.05 |
Gelatin |
0.79 |
Layer 14: A protective layer-1 |
A silver iodobromide emulsion (having an average grain-size of 0.08µm and a silver
iodide content of 1.0 mol%) |
0.40 |
UV absorbent (UV-1) |
0.065 |
High boiling solvent (OIL-1) |
0.07 |
High boiling solvent (OIL-3) |
0.07 |
Gelatin |
0.65 |
Layer 15: A protective layer-2 |
Alkali-soluble matting agent (having an average particle-size of 2µm) |
0.15 |
Polymethyl methacrylate (having an average particle-size of 3µm) |
0.04 |
Lubricant (WAX-1) |
0.04 |
Gelatin |
0.55 |
[0109] Besides the above-given compositions, there added coating aid Su-1, dispersion aid
Su-2, a viscosity controller, layer hardeners H-1 and H-2, stabilizer ST-1, antifoggants
AF-1 having an average molecular weight of 10,000 and AF-2 having an average molecular
weight of 1,100,000, and preservative DI-1, respectively.
[0111] Silver halide color photographic light-sensitive material samples 102 to 109 were
also prepared in the same manner as described above, except that emulsion EM-1 of
sample 101 was replaced by emulsions EN-2 to EM-9 as shown in Table 4:
Table 4
Sample |
102 |
103 |
104 |
105 |
106 |
107 |
108 |
109 |
Emulsion used |
EM-2 |
EM-3 |
EM-4 |
EM-5 |
EM-6 |
EM-7 |
EM-8 |
EM-9 |
[0112] Each of the resulting samples was exposed to light through an optical wedge in an
ordinary manner and were then processed in the following processing steps:
Processing steps |
1. |
Color developing |
3min.15sec. |
38.0±0.1°C |
2. |
Bleaching |
6min.30sec. |
38.0±3.0°C |
3. |
Washing |
3min.15sec. |
24°C to 41°C |
4. |
Fixing |
6min.30sec. |
38.0±3.0°C |
5. |
Washing |
3min.15sec. |
24°C to 41°C |
6. |
Stabilizing |
3min.15sec. |
38.0±3.0°C |
7. |
Drying |
|
≥50°C |
[0113] The compositions of the processing solutions used in the above-mentioned processing
steps were as follows.
<Color developer> |
4-amino-3-methyl-N-ethyl-N-(β-hydroxyethyl)aniline·sulfate |
4.75 g |
Sodium sulfite anhydride |
4.25 g |
Hydroxylamine·½sulfate |
2.0 g |
Potassium carbonate anhydride |
37.5 g |
Sodium bromide |
1.3 g |
Trisodium nitrilotriacetate (monohydrate) |
2.5 g |
Potassium hydroxide |
1.0 g |
Add water to make |
1 liter |
Adjust pH to be |
pH=10.1 |
<Bleacher> |
Iron ammonium ethylenediamine tetraacetate |
100.0 g |
Diammonium ethylenediamine tetraacetate |
10.0 g |
Ammonium bromide |
150.0 g |
Glacial acetic acid |
10.0 g |
Add water to make |
1 liter |
Adjust pH with aqueous ammonia to be |
pH=6.0 |
<Fixer> |
Ammonium thiosulfate |
175.0 g |
Sodium sulfite anhydride |
8.5 g |
Sodium metasulfite |
2.3 g |
Add water to make |
1 liter |
Adjust pH with acetic acid to be |
pH=6.0 |
<Stabilizer> |
Formalin (in an aqueous 37% solution) |
1.5 ml |
Konidux (manufactured by Konica Corp.) |
7.5 ml |
Add water to make |
1 liter |
[0114] Each of the resulting samples was exposed (for 1/200") to red light (R) through a
sensitometric wedge, and the resulting relative sensitivity and latent image preservability
of the samples were evaluated.
[0115] The results thereof will be shown in Table 5 given below.
[0116] The relative sensitivity of a fresh sample was obtained in such a manner that the
sample was color-developed within one minute after exposure and a relative value of
the reciprocal of the exposure amount capable of giving a density of Dmin (the minimum
density)+0.15 is obtained as the relative sensitivity of the sample. The sensitivity
of the sample is indicated by a value relative to the sensitivity of sample 101 that
is set to 100, (in other words, it means that the more is a value, the higher is the
sensitivity.) The latent image preservability of a sample was obtained in such a manner
that the sample was exposed to light and then allowed to stand at a relative humidity
of 80% for 7 days. Thereafter, it was color-developed and the relative sensitivity
thereof was then obtained as a value relative to the sensitivity obtained from sample
101 that was set to 100.
Table 5
Sample |
Invention or Comparison |
Red-sensitive layer |
|
|
Real-time relative sensitivity |
Relative sensitivity obtained after preserving a latent image |
101 |
Invention |
100 |
92 |
102 |
Invention |
101 |
93 |
103 |
Comparison |
77 |
42 |
104 |
Comparison |
97 |
61 |
105 |
Comparison |
75 |
65 |
106 |
Comparison |
76 |
67 |
107 |
Invention |
99 |
86 |
108 |
Invention |
100 |
88 |
109 |
Invention |
102 |
99 |
[0117] As is obvious from the results shown in Table 5, samples 101, 102 and 107 to 109
each relating to the invention, which contained an emulsion of the invention, have
a high sensitivity and are improved in latent image preservability.
[0118] Among the samples, sample 109 is particularly superior, because it uses emulsion
EM-9 satisfying the best combination of the invention.
[0119] As is apparent from Table 5, the grain-size distribution of the invention and the
y/x effect thereof are demonstrated by the sensitivity obtained with fresh samples.
[0120] On the other hand, it can be understood that the effect of the internally reduction-sensitized
grains is demonstrated by the sensitivity obtained after preserving a latent image.
As described above, the invention can provide a silver halide photographic light-sensitive
material and a silver halide color photographic light-sensitive material high in sensitivity
and excellent in latent image preservability.