[0001] The new method is aimed at improving and regulating the adhesion between similar
or different fibers in connection with a method for producing hydroentangled and thermobonded
fabrics from cellulose or cellulose-synthetic fiber blends.
In the method both natural and regenerated cellulose fibers and primarily polyolefin
and polyester synthetic fibers are used.
Regenerated cellulose fibers can be mixed with synthetic fibers already prior to the
thermobonding or hydroentanglement process. A fiber layer formed from short pulp cellulose
fibers, as such or as a pre-blend with a polyolefin-microfiber, is hydroentangled
into a synthetic fiber support using conventional methods, aiming at obtaining, with
respect to the cellulose, either a laminate or as good as possible degree of blending.
By improving the adhesion between the fibers in a nonwoven product, one aims at providing,
in addition to high strength characteristics, a high absorption capacity and a stable
and non-linting product structure with a high cellulose content.
[0002] Textile materials for medical applications include fibers, mono- and multifilament
threads, woven and nonwoven products and composites. The major requirements of medical
textiles are, depending on the intended application, absorbency, strength, flexibility,
softness, at times biostability or biodegradability. Cotton, pulp and silk fibers
are the most common natural materials in medical textiles. These are extensively used
in combination with regenerated cellulose fibers (
i.a. rayon viscose)in surgical, non-implantable materials and in products for health care
and hygiene. Of the synthetic materials, primarily polyesters, polyamides and polyolefins
are used in medical textiles.
The new regulation method is primarily associated with surgical textiles as well as
textiles for health care and hygiene. The former group comprises
i.a. wound dressing textiles, gauzes, band-aids, and the latter surgical dress textiles,
blankets, incontinence diapers, protective clothing, clean room wipes
etc.
Nonwoven medical textiles are manufactured primarily using two different types of
methods, that is thermobonding and hydroentanglement methods. The use of bonding polymers
or corresponding bonding agents in liquid form is avoided in medical textiles primarily
due to reasons of hygiene and also product properties. Liquid, short-chain binders
cover and encapsulate especially absorbing fibers and also prevent the formation of
semipermeable, absorbing textiles (surgical dress textiles).
Fine cellulose lint which is released from the nonwoven textile structure as a result
of the manufacturing technique is very detrimental. Lint formation is a result
i.a. of the short length of both natural and synthetic fibers, microfibrillation and other
factors. The requirements on air purity in hospital operating rooms and some special
departments put very strict limits
i.a. on particle emission from medical textiles. The USA Federal Standard 209E, 1992,
defines that the air in a clean room of the cleanliness class 100 contains particles
of a diameter d > 0.5 µm at the most 100 per cubic feet, that is 3531 per m
3. It is very difficult to reach this value for example with pulp fiber containing
hydroentangled fabrics (50 % by weight cellulose, weight 70 g/m
2) when tested with conventional test methods. In addition, a hydroentangled fabric
is, irrespective of variations in production methods, very unstable with respect to
cellulose lint release due to the shortness of the pulp cellulose fibers and their
broad length distribution, and is also especially sensitive to bending and shear.
[0003] The characteristics of the invention are disclosed in the appended claims.
[0004] The object of the invention is thus a method for improving and regulating the adhesion
strength between fibers of cellulose or cellulose-synthetic fiber blends, especially
-polyolefin fiber blends, wherein hydroentanglement and/or thermobonding processes
are used for bonding webs from gauzes and/or formats of said fibers and/or fiber blends,
according to which method, prior to the bonding process, the surface energy values
of the cellulose fiber is increased by simultaneously increasing the crystallinity
degree and long identity period of its surface layer and converting its crystal structure
from the cellulose-II- or cellulose-I- structure to the high temperature cellulose-IV-structure,
by heat treating the cellulose fiber in a polar, cellulose non-dissolving liquid,
at an elevated temperature,
prior to the bonding process, the molecular chain length is reduced in the surface
layer of the synthetic fiber used for bonding the cellulose, in order to lower the
surface energy, melt viscosity and melting point of the bonding melt formed from the
fiber surface layer during bonding, by subjecting the fiber surface during the spinning
stage thereof in a molten condition to controlled oxidative chain degradation,
prior to the bonding process, the synthetic and cellulose fibers participating in
melt bonding are intermixed using carding or some other, as such known method, and
is brought into good mutual precontact in order to ensure, during melt bonding, wetting
of the synthetic fiber partial melt and the cellulose surface, interface nucleation
and transcrystallization, which in roller bonding methods usually takes place by regulating
the linear pressure between the rollers and in hydro-entanglement processes usually
by regulating the water needling energy and/or the hydrogen bonding effect between
the cellulose fibers,
the release of short cellulose fibers from the surfaces of nonwoven laminates and
blended fabrics is prevented, besides by melt bonding, by means of a corona steam-wetting
and pressure drying process performed as an on-line process after the bonding process
which improves adhesion through hydrogen bonding.
[0005] Characteristic features for the new method are i.a. the following:
- Improvement in adhesion between the cellulose and polyolefin fibers is obtained by
increasing wetting between the molten polyolefin and the cellulose and by providing
transcrystallization in the polymer structure of the cooling contact point. Wetting
between the fiber surfaces is improved by modifying the surface structure of the polyolefin
and/or cellulose fibers. This takes place in connection with the drying process (flow-through
or suction method) of the hydroentanglement process or as a separate, but on-line
process.
- Modification of the polyolefin (especially polypropylene) fiber surface is based on
obtaining, by means of spinning oxidation (FI-application no 974169/07.11.97), large-scale
degradation of the molecular chains in the fiber surface layer and corresponding decrease
of the melting point and of the surface energy and viscosity of the molten phase formed
from the layer. This method is carried out in connection with fiber formation.
- Modification of the cellulose fiber surface is primarily based on converting the regenerated
(if necessary also the natural) cellulose crystalline structure, C-II (C-I) to the
structure, C-IV, by heat treatment of the same in a polar liquid phase. As a result
of the transformation, the surface energy value of the cellulose fiber increases.
The modification can be carried out in connection with the cellulose fiber manufacturing
process by using saturated high pressure steam or, depending on the circumstances,
as a separate heat treatment process.
- A result of the heat treatment of the cellulose fiber (C-I, C-II) in liquid phase
is, in addition to an increase in the structural crystallinity degree, which in itself
increases i.a. the free surface energy, formation of a clearly lamellar cellulose superstructure
and an increase in the structural long period. The increase in the long period and
crystallinity degree of the cellulose surface structure results in an increase in
the crystalline lamellar thickness, which in turn provides for a plane area which
exceeds the critical size needed for heterogenous nucleation which is a prerequisite
for transcrystallization (i.a. for the adherance of hydrogen atoms in the polymer chain helix facing the plane area,
to low energy sites in the cellulose structure).
- Improvement in adhesion between cellulose fibers is based on a modification of the
cellulose fiber surface by means of high-energy corona treatment for bringing about
oxidative degradation of the molecular chains in the cellulose structure and i.a. an increase in the surface area by means of mechanical working caused by bombarding
with charged ions and electrons. Wetting of the fiber blend and drying under pressure
subsequent to the corona treatment result in a very effective increase in adhesion
through hydrogen bonding. The corona and associated other treatments are carried out
on a hydroentangled dry fabric. When using the method in connection with a pulp cellulose-polyolefin
microfiber mixture, a good pre-contact is obtained (before melt wetting and transcrystallization)
in the cellulose-synthetic fiber-system. It is especially to be observed that the
effect of the corona treatment in the fabric surface extends only into a thin surface
layer, but the formation of hydrogen bridges adheres the surface fibers so that the
cellulose fibers below the surface layers are 'encapsulated' and the release of cellulose
lint ends. The absorption capacity and rate of a corona treated product fabric are
increased due to the afore mentioned mechanism. The corona and associated partial
treatments (also the wetting and transcrystallization processes) are carried out as
an on-line process to a conventional hydroentanglement process.
- Cellulose-polyolefin-fiber blends behave in thermobonding in a manner corresponding
to synthetic polymer fibers, but the participation in bonding of the cellulose in
the blend is low (that is, also the polymer melt covers a very small part of the cellulose
surface, thus without disturbing future absorption processes).
Thermobonding of fiber mixtures is regulated in a manner described in the patent FI
101087/1998.
[0006] Each partial process in the method can be regulated with respect to its effect and
thus it is possible to control the end result and the partial processes chosen to
achieve the same.
[0007] The prior art relating to the applicability of adherence and adhesion bonding between
synthetic and natural polymer fibers and the natural scientific principles relating
to adhesion bonding are shortly reviewed, as well as the use of cellulose fibers in
nonwoven products prepared from fiber mixture webs by hydro-entanglement and thermobonding
methods.
[0008] The elucidation of the natural scientific principles of adhesion bonding is here
based on the critical observations of S. Wu /1/.
The ideal strength of adhesion bonding between two phases is, expressed by means of
the adhesion work (Wa) and equilibrium distance (Zo) between the phases

wherein

are the surface energies of each phase and of their border surface.
At typical polymer variable values, a value of only approximately 104 N/mm
2 is obtained for this ideal strength. In practice, however, the strengths obtained
are an order of magnitude lower. Complete molecular contact, which is a prerequisite
for an ideal adhesion bond, is difficult to obtain in practice.
[0009] In order to clarify the new adhesion bonding method under study, in the following
three, experimentally proven partial theories which substantially affect adhesion
strength are shortly reviewed.
[0010] According to the Fractura theory, the difference between the ideal and practical
adhesion strength results from the fact that the fracture forming process is not reversible
and that there are always defects at the grain border and bulk areas. The strength
of the adhesion bond is determined by the size of the defect and the energy lost in
the irreversible deformation during the fracture forming process, that is
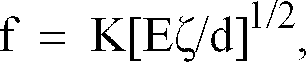
wherein E is the elastic module, d is the length of the micro-fracture, ζ is energy
at break: ζ = Wa + ψ, wherein ψ is total work of the irreversible processes (ψ >>
Wa, wherefor ζ ~ ψ).
[0011] According to the wetting-contact theory, the van der Waals forces are sufficient
to impart strong adhesion provided that there is a molecular contact between the phases
and that the contact energetics affect the extensiveness of the border surface contact
and thus adhesion strength.
It is presumed that the driving force in wetting is the spreading coefficient λ
12, that is

wherein λ
12 is the spreading coefficient of phase 1 on phase 2. If the size d of an unwetted
border surface pore relates to the spreading coefficient in accordance with the equation
d = D
o[1-(λ
12/γ
2)]
n, wherein d
o and n are constants, one obtains, by inserting into the equation /2/, the following
equation for the adhesion strength

that is, the wettability is directly proportional to the adhesion strength, which
fact has also been experimentally proven.
The rate of wetting of a border surface pore can be expressed as an exponential damping
function

wherein d and d
y are the pore sizes at time t and during an infinite time, α and τ are constants.
By inserting from the equation /2/ the adhesion strength into the equation /5/ one
obtains the change in strength at the time t. It can be seen that the increase in
adhesion strength follows first-order kinetics, which can also be experimentally shown.
[0012] According to the diffusion theory, a molecular chain or segment diffusion through
the border surface of the phases is a prerequisite for the development of a strong
adhesion bond, that is also: molecular contact to the border surface is as such not
sufficient.
A prerequisite for interdiffusion to take place is the compatibility of the components.
Most polymer pairs are, however, non-compatible. Statistical thermodynamics require
that the diffusional movements occuring in the border surface layer have to minimize
border surface energy. The thickness of the diffusional border surface layer between
polymers is indirectly proportional to the (Flory-Higgins) interaction parameter.
When the compatibility of the components increases, the interaction parameter decreases,
interpenetration increases and the thickness of the border surface layer increases.
On the other hand, the interaction parameter is proportional to the square of the
difference between the solubility parameters. It has been observed that the adhesion
strength between polymers decreases when the difference between the solubility parameters
of the phases increases.
Similar dependencies exist also in the wetting-contact theory. It is apparent that
improving the compatibility between the solubility parameters results in a decrease
of the border surface tension and thus increases the driving force behind wetting
and adhesion strength.
[0013] The diffusional kinetics for the formation of an adhesion bond is expressed by the
equation

wherein f is the adhesion strength at time t = t, V is a frequency factor, ρ is density,
M is the molecular weight, D is the diffusion constant, ϑ is the separation rate for
the adhesion bond, β is a constant (often β ≈ 1/2). According to the equation, the
adhesion strength increases when the contact time increases, the molecular weight
decreases and the testing rate increases. Diffusion can take place only in the presence
of contacts. The formation of an adhesion bond can take place at two stages, whereby
the first stage comprises wetting for the formation of border surface contact, and
the second stage comprises interdiffusion for the formation of a diffusional border
surface layer. It can experimentally be shown that the adhesion strength still continues
to grow after the formation of a complete border surface contact.
[0014] Also chemical adhesion can be added to the group of studied processes affecting adhesion
bonding. The bonding energy of a chemical bond is typically appr. 80 kcal/mol, whereas
the van der Waal attraction is to its energy only 2.5 kcal/mol. It can be experimentally
shown that the increase in adhesion bond strength can be 35-fold as a result of a
chemical bond.
In the chemical bonding of border surfaces, coupling agents based on silanes, titanates,
chromium complexes
etc. as well as functional groups, such as amino, amide, carboxyl, hydroxyl, epoxide,
isocyanate
etc. groups, are well known.
[0015] An important stage in the adhesion method according to the invention, in addition
to the polymer/solid material-contact and -wetting, is the solidification of the molten
polymer in solid material contact and the phenomena associated herewith.
Primary nucleation of spherulites induced by solid material surfaces on a precisely
defined foreign surface is termed transcrystallization. The presence of many nucleation
sites on the foreign surface prevents a lateral growth of the spherulites, whereby
crystallization can take place only in a direction perpendicular to the nucleating
surface. The formation of such a transcrystalline surface layer naturally improves
foreign surface/polymer adhesion and correspondingly the strength of the whole composite.
In this connection, factors controlling the transcrystallization process of polypropylene
will be studied, by referring to results from critical experimental studies (Goldfarb:
/2/).
[0016] The free energy of nucleation for the formation of a rectangular heterogenous cell
is

where a, b and l are the rectangular dimensions, Δg
f is the free energy of melting per unit volume, γ and γ
e are the surface free energies per unit surface for the bl- and ab-levels, ΔG is the
free total energy of cell formation and Δσ is the energy difference function

wherein γ
cs is the free energy of the crystal/support-interface per unit area, γ
cm is the free energy of the crystal/melt-interface per unit area and γ
ms is the free energy of the melt-support-interface per unit area. In the case of primary
nucleation the magnitude of the free energy barrier is obtained by differentiating
the equation /7/ with respect to the rectangular dimensions and determining from the
differentials the critical dimensions (a*, b*, l*) and introducing them into the equation
/7/, that is

wherein the free energy of melting is substituted by expressing entropy of melting
with a temperature-independent term for a material with density ρ
s, Tm is the melting point of the polymer and ΔT the degree of subcooling (Tm - Tc).
The critical variables for a given polymer are thus the variables ΔT and Δσ. The effect
of the degree of subcooling is obtained by varying the specific crystallization temperature
and the free energy difference of the support surface by varying the nucleating support.
[0017] According to measurements, crystalline and amorphous surfaces provide almost identical
nucleation densities which shows that the energy difference is of the same magnitude
on the support surfaces used in the study. This deviates from earlier studies, according
to which different supports had substantially different nucleation activities (i.a.
Schonhorn: /2/). In the study now referred to, special attention has, however, been
paid to the similarity in magnitude between the support surfaces and to the prevention
of support poisoning. The nucleation densities in the study represent the natural
nucleation potential of the used support more than its effective value.
For the estimation of the surface energy values of the components of the various supports,
the model of Fowkes /2/ is used, according to which it is assumed that only dispersion
interactions are critical in hydrocarbon/support-interaction,
i.e. as an example

wherein γ
ms is the free energy of the interface of the non-mixable phases m and s, γ
m and γ
s are the surface tensions of the phases m and s and γ
md and γ
sd are the surface tensions resulting from the dispersive component of the interface
free energy.
By inserting the component equations /10/ into the equation /8/ and assuming that
the components γ
md and γ
cd are converging, the following equation is obtained for the energy difference

The determinative part of the free energy difference of the support is formed from
the first, finite, positive constant term 2(γ
c - γ
cd), the second variable term remaining of lesser value compared to the first.
As specific and same spherulitic sites are observed after repeated meltings and crystallizations,
it must be assumed that there is a fixed number of active nucleation sites on the
support surface. As the model corresponding to the equation /7/ presupposes a planar
nucleation surface, of the size a x l units, at least these dimensions are needed
for nucleating conditions. Any material which prevents contact between the support
and the polymer melt prevents spherulitic nucleation. An impurity component preventing
wetting of the interface or changing the critical dimensions of its plane area can
destroy a nucleation site. On the other hand, active nucleation sites can be introduced
also to a 'poisoned' support (in one way or other) by increasing the degree of subcooling,
ΔT. The equation /9/ was formed from the critical dimensions, U
i corrresponding to the free energy minimum of the system:

wherein the values of c
i for the different dimensions a, l and b were respectively: 4γ, 4γ
e and 2Δγ.
According to the equation /12/ increasing ΔT reduces the planar dimensions (a, l),
which are necessary for spherulitic nucleation.
[0018] It can further be observed that in the temperature range studied, the nucleation
densities remained constant, but there were considerable differences in the nucleation
activities at different temperatures. The variations in activities were measured as
reciprocal values of the nucleation incubation times, and the measurement results
corresponded to the classical rate equation.
[0019] As a summary studied it can be observed that
- transcrystallization is a common phenomenon which takes place when there is good contact
between the support and the polymer melt
- the natural activity of the support is independent of its chemical nature
- the Fowkes equation seems to apply for a comparison of the activities of the supports
- the classical rate equation is in agreement with the measured nucleation density and
incubation time values.
[0020] There are two early studies relating to transcrystallization of polypropylene on
cellulose and graphite fiber surfaces of different qualities.
Transcrystallization of polypropylene on cellulose fiber surfaces of different qualities
(cotton, ramie, fortisan, rayon, pulp) was studied (Gray: /2/) by immersing the same
in a thin molten polypropylene film, cooling this film to the crystallization temperature
(hot table) and observing (photographing) the transcrystalline crystal growth following
surface nucleation in a polarisation microscope. The study showed that nucleation
preferentially takes place on a natural cellulose surface, whereas an unbleached cellulose
surface is, apparently due to the presence of hemicellulose and lignin components,
a poor nucleator. The surfaces of regenerated cellulose fibers and mercerized cotton
were very poor nucleation surfaces. Various physical and chemical surface treatments
did not induce nucleation on regenerated cellulose. There is no evidence in the studies
of an effect resulting from different crystal morphologies of the nucleation surfaces,
but a broad scale geometrical property of the surfaces could be controlling with respect
to transcrystallization.
[0021] One study relating to polypropylene nucleation on two PAN-based graphite fiber qualities
(Hobbs: /2/) is interesting. A poorly nucleating fiber quality consisted of small
disoriented graphite nuclei having a size of approximately 25 Å, and a well nucleating
fiber quality of broad graphite plates which were strongly oriented in the direction
of the fiber axis and of a size of over 100 Å. The big difference in nucleation properties
between these graphite qualities seems to be due to differences in size and orientation
of their structural graphite planes. Adsorption of polypropylene directly on the base
plane of the graphite support can be explained by the fact that polypropylene crystallizes
in a monoclinic lattice system, where the molecular chains form a spiral conformation
comprising three repeating units, as well as by molecular orbital calculations, which
show the priority adsorption sites for hydrogen on a graphite surface. The spiral
molecular polypropylene chain can be placed on a graphite lattice surface so that
all hydrogen atoms in contact with the surface are situated in the positions of lowest
surface energy (that is along c-c-bonds).
[0022] The use of cellulose fibers of different qualities in nonwoven products manufactured
by methods of thermobonding webs will now be studied.
[0023] The method according to the patent US 3,507,943/1970, /3/ is an early innovation
relating to productional thermobonding of nonwoven fiber webs with wide-range applicability.
In the method thermobonding is carried out using a pair of rollers, one or both rollers
of which are embossed and heatable to desired temperature. In addition to normal thermobonding,
the method comprises, in nonwoven product manufacture, impregnation, lamination, perforation,
fulling, folding
etc. The webs to be thermobonded usually contain a specified amount of bonding thermoplastic
fibers (polypropylene) and absorbing fibers (0-75 % cotton-, rayon-pulp fiber) for
absorbing wipe products. In lamination, as support materials,
i.a. nonwoven and woven products, organic film, paper, tape
etc. are used.
[0024] The patent US 3,501,369/1970, /3/ relates to a nonwoven product and a method for
its preparation. The novel non woven product with high wet and dry strength values
consists of a thermally bonded polypropylene-cellulose-fiber web, where the proportion
of cellulose fiber is 25-95 % by weight. The cellulose fibers are either short natural
fibers (
i.a. cotton) or synthetic fibers (
i.a. rayon). The method of preparation comprises making a web of the fiber mixture, subjecting
the web to heating (163-204° C) and bonding under pressure (36-360 kg/m) by hot or
cold rolling.
According to the specification, the bonding polypropylene fibers in the product are
twisted around the cellulose fibers and impart, partly intermelted, strength to the
product, that is, the bonding of the cellulose fibers is primarily mechanical. Due
to its absorbency, the product is well suited for wiping, surgical applications,
etc.
[0025] J. P. Moreau /4/ studied thermobonding of polypropylene-cotton mixtures (20, 30,
50, 75, 100 % by weight PP) as a function of temperature using a pair of rollers,
one of which was embossed and the other smooth. The bonding speed of the fiber web
was 30.5 mm/s and the linear pressure between the rollers 66 kN/m. The weights of
the bonded nonwoven fabrics were 40, 60 and 80 g/m
2.
Interblending of the cotton and polypropylene fibers proved to be difficult in the
test series. Use of a bonding polymer in the form of a film with a cotton web gave,
as compared to a fiber mixture, a better polymer-cellulose distribution. A cotton
fiber-polymer film-laminate gave, as compared to a corresponding fiber mixture product,
better longitudinal and transverse strength values. The breaking strength, elongation,
stiffness and absorbance of the products were measured and the effects of mixing levels,
product surface and temperature on the product properties were determined using statistical
analysis. It can be mentioned that the tensile strength values given in the tables
of the Moreau (/4/, 1990) publication, satisfy satisfactorily the regulation equation
for the thermobonding model according to the FI-patent application 961252/18.03.96,
/5/. The thermobonding regulation equation for the web simulating the measurement
results of the publication with respect to the MD tensile strength is

wherein σ, N is the fabric tensile strength; [PP], % by weight is the polymer content
of the fiber mixture; w, g/m
2 is the fabric weight; T, k is the oil temperature of the roller and E, cal/mol is
the dimension for the activation energy.
[0026] T. F. Gilmore et al /1992, /4/ study in their publication the advantages, use and
improvement of use of cotton in nonwoven products. Hereby thermobonding is an economical
and important alternative for hydroentanglement methods, which, as is known, best
maintain the advantageous textile properties of cotton in the product. Especially
the use of heterophilic bicomponent fibers as bonding fibers in thermobonding give
in this case products with good textile and strength properties. In the experimental
section of the publication thermobonding of a cotton web is carried out using a polypropylene-polyester-bicomponent
fiber (20 % by weight in the mixture). The thermobonding tests were carried out as
a function of the linear pressure between the rollers and the temperature, the nominal
weight of the fabrics being 85 g/m
2. In the bonding tests, both duo- and trio-rolling was used, whereby the web was transported
in the forward direction via a hot, embossed and hot, smooth roller and the pre-bonded
fabric in the return direction via the afore mentioned hot, smooth and an unheated
elastic roller. As a result of the study it was observed that trio-rolling did not
provide noticeable advantage as compared to duo-rolling. According to the publication
it is assumed that the bonding mechanism is based on mechanical attachment or encapsulation
of cotton by polypropylene.
[0027] The use of cellulose fibers in products obtainable with hydroentanglement methods
is well known. Some examples from the very broad state of the art relating to such
methods and products will be mentioned.
[0028] The method and products according to the patent US 3,485,706/1969, /3/ are often
considered to be the pioneer inventions in the productional application of liquid
needling methods. In the method, use is made of either cellulose fibers as such or
in mixture and laminates with synthetic fibers. Primarily cotton and rayon fibers
and also short pulp cellulose fibers in the form of tissue paper are used as cellulose
fibers. There is a variety of synthetic fibers (polyester, polyamide, polyacrylic,
polyolefin fibers,
etc.) homo- and copolymer fibers, either as mono- or bicomponent fibers, continuous filaments
or staple fibers.
[0029] In the hydroentanglement method according to the patent US 4,442,161/1984, /3/ nonwoven
products with improved liquid-barrier-properties are manufactured. In the method,
nozzle series that are more densely arranged than normal are used as well as a spraying
combination comprising the use of high and low pressures. In the method, polyester
fibers either in the form of continous filaments or staple fibers, and pulp fibers
primarily in the form of Harmac-paper are used. The nature of the bonding between
the cellulose and the synthetic fibers is assumed to be completely mechanical. In
the examples of the method, the "self-bonding" temperatures of the polyester qualities
are given, but apparently for the choice of drying temperatures for the products.
[0030] In the method according to the patent US 4,902,564/1988, /3/ a high-strength, well
absorbing, finished wipe product (100-270 g/m
2) is made from a fiber mixture which contains 50-75 % by weight of wood pulp and 25-50
% by weight of synthetic fibers. In the method, the wet-laid web is fed to hydroentanglement.
It is especially advantageous to use pulp fibers of a length of 3-5 mm as they perform
best in needling and the products have the best tensile and wear strengths as well
as sufficient wet strengths. In the method, polypropylene, polyamide and polyester
fibers are used as synthetic fibers. The bonding between the fibers is completely
mechanical.
[0031] The invention according to the patent US 5,459,912/1993 /3/ comprises hydroentanglement
product fabrics made from synthetic fibers and pulp fibers, as well as a method for
their preparation.
The product fabrics have very low wet and dry particle counts and good absorption
capacity. The minimum particle count as dry is given as 2.83 x 10
5 per m
3 and as wet 6.5 x 10
7 per m
3 and the minimum absorption rate and capacity as 0.1 g/(gs) and 300% respectively.
The pulp portion of the fabric product is 5-50 % by weight. Polyester, polypropylene,
polyamide and polyacrylic fibers and their combinations are used as synthetic fibers.
In a first step of the manufacturing method according to the patent a web comprising
cellulose and synthetic fiber layers is needled with the synthetic fiber layer to
the wire (maximum: 75 mesh), at a nozzle pressure range of 6.9-138 bar, the total
needling jet energy being at least 50 kJ x N/g. During needling, the fibers in the
pulp layer are intertwined hydraulically with the fibers in the synthetic fiber layer.
In a second step of the method, the obtained pre-mixed web is supported by its pulp
side on an apertured embossing means, the aperture number of which is in the range
of 40-10 mesh and is water needled using a total energy of at least 53 kJ.N/g. During
needling, the fibers are moved in the lateral and vertical direction from their initial
positions towards the apertures in the embossing means (i.e. the wire), whereby an
imprint is formed in the product fabric. The wire speed in the hydroentanglement process
is at least 18 m/min (in the range 90-180 m/min). In order to improve the absorption
properties of the product fabric, the fabrics are subjected to water removal under
subpressure in the process.
[0032] With respect to the product and methods according to the patent US 5,459,912 it can
be concluded that they do not comprise anything substantially new with respect to
prior known products or applied hydroentanglement technology. An indication of the
maximum values for the particle count for the products does not unambiguously define
the quality of the fabric with respect to the release of cellulose fibers, as the
fibers emitted by the fabric possess both a size and a weight distribution. As no
correlation is given between the used (non-standardized) particle measuring method
and other measurement methods (i.a. based on the weight change of the fabric sample),
it is impossible to carry out a comparison of the products obtained by the method
with respect to the known state of the art.
[0033] In the limited study of publications relating to bonding of cellulose and synthetic
fibers, no method or regulation method comparable to the new method was found for
improving adhesion bonding between fibers of different qualities.
Some operational principles relating to the new regulation method combination used
in the production of nonwoven products will be studied in detail in the following
examples.
Subexample 1
[0034] In the subexample 1 the structure of cellulose fibers as well as the kinetics of
the polymorphous changes in the cellulose and their effect on the fiber structures
in association with the the regulation method is studied by means of wide-angle and
low-angle x-ray scattering (WAXS and SAXS) and heating treatment tests. In the examples,
in connection with the new innovation, an increase in the energy level of the surface
layer of the cellulose fibers will be shown as a result of lattice transformation,
increase in the crystallinity degree and exceeding the critical minimum size of the
adhesion surfaces, which functions are partly interrelated.
[0035] Three polymorphous forms of the cellulose crystal structure are associated with the
present innovation, namely
- native cellulose, that is cellulose I (C-I), which is present in most natural fibers,
such as cotton, wood, ramie, linen and various hemp fibers.
- hydrate cellulose, that is cellulose II (C-II) which form is present i.a. in regenerated and mercerized cellulose.
- high temperature cellulose, that is cellulose IV (C-IV), which can be prepared at
an increased temperature, in the presence of a polar liquid phase from both native
and hydrate cellulose.
The celluloses I and II are monoclinic to their crystal lattice form, and they differ
from each other primarily with respect to the lattice constant c and the angle β of
the (a/c)-axis. The lattice form of cellulose IV has not been confirmed, but it has
been held to be tetragonal or orthorombic. The lattice constants of the cellulose
lattices C-IV and C-I are very close to each other, but the C-IV lattice lacks the
plane reflection (101). In the table 1 the lattice constants for the said cellulose
qualities have been indicated, as well as the essential plane reflections corresponding
to the Miller indices calculated therefrom. In addition to identification based on
WAXS-scattering of the cellulose lattice forms, the crystallinity degrees were determined
from the samples in the angle range of, 2θ = 10-30°, based on the scattering intensity
sum.
In order to determine the cellulose structures, WAXS-(and SAXS)-measurements were
carried out on natural fibers, raw cellulose fibers, tissue paper and regenerated
cellulose fibers made in different ways, as well as on corresponding cellulose films.
The cellulose samples differed as to their crystallinity degrees substantially from
each other, the crystallinity degree of regenerated cellulose fibers (C-II-lattice:
23 samples) being substantially lower than that of natural cellulose fibers: cotton:
68-70 %, pine, aspen cellulose: 53-65 %, xanthate based rayon: 35-40 %, NMMO based
rayon: 50-55 % and carbamate based rayon: 35-45 %.
[0036] The structural change, C-II (C-I)/C-IV, in the crystal lattice of cellulose fibers
is dependent on many factors in addition to fiber quality. Generally speaking the
transformation is more complete the lower the crystalline order is and the less energy
is needed therefore. Thus a structural change is easier for regenerated cellulose
fiber (C-II) than for mercerized or untreated natural fibers (C-I).
Rayon viscose fiber in dry form is structurally almost unchanged up to a temperature
of 300 °C, but when treated in liquids in a temperature range of 140 ° (80 °) - 300°C,
the transformation degree C-II/C-IV increases as the polarity of the liquid increases.
During mercerizing, the cellulose molecules are separated from each other under the
influence of a swelling agent, whereby during transformation the anhydroglucose molecules
are more easily rotated back to the ab-lattice level.
[0037] In the method according to the new innovation, the necessary C-II/C-IV transformation
degree is low, as the aim is to obtain a thin, cellulose IV-layer with high surface
energy on the fiber surfaces.
The crystal phase C-IV/C-II-concentration ratio was measured for viscose fibers by
means of the corresponding WAXS-intensity ratios (i.a. the (101)- plane reflexion
intensities) after both glycerol and water autoclave treatment. The following equation
was obtained for simulating the intensity ratios with sufficient accuracy (in this
connection).

wherein for the viscose fibers studied, the activation energy value was E = 4676
cal/mol, the constant F being dependant on the fiber quality. For the constant F,
for two xanthate based fiber qualities A-71 and C
s-88, the following values were obtained: F = 381.3 and 194.6. For fiber quality L-71
regenerated from a NMMO-solution, the value F = 213.4 was obtained for the constant.
The scattering intensity ratio of the (101)-planes of the fiber quality A-71 was in
glycerol, after heat treatment at a temperature of 226 °C, S = 5.05 (equation 14:S
= 4.85), which corresponds to a degree of conversion of approximately 90 % in the
crystalline part of the structure and thus a C-IV-concentration of 57.6 % in the crystalline
part (the crystallinity degrees before and after the heat treatment were 38 and 64
% respectively). The fiber quality L-71 has a scattering intensity ratio which is
lower than the previous (2.71), but its crystallinity degree is higher than the former
(before and after treatment 55 and 70 % respectively), wherefore the C-IV-concentrations
of the fiber qualities do not differ from each other much.
It is to be noted in this connection that due to the effect of the heat treatment
in a polar liquid i.a. the crystallinity degree of cellulose II increases to correspond
to the crystallinity degree of cellulose I. The crystallinity degree of cellulose
structures does not increase when heating in dry form. The effect of heat treatment
time on the C-II/C-IV-conversion was so small according to measurements (+~0.5 - 36
h) so that it does not, i.a. taking into account the crystallinity degree error, markedly
affect the intensity ratio. It is to be observed that the method used in this connection
for measuring the C-IV/C-II-concentrations, primarily gives qualitative values, as
i.a. the increase in the crystallinity degree for both crystal systems as a function of
temperature (and time) is of different magnitude, and the degree of crystallinity
is inaccurate with the fast measuring technique used.
In order to study the C-I/C-IV-lattice transformation of the crystal structure of
dry natural cotton (C-I) some heat treatment tests were carried out in glycerol (200
°C/2h). Heat treatment gave lower intensity ratios than in the afore mentioned C-II-transformation,
but from the WAXS-analysis it was easy to note a shift in the (101)-plane (C-I)scattering
intensity towards bigger 2θ-values and the disappearance of the (101)-plane (C-I)-scattering
intensity when the C-IV-lattice is formed.
[0038] The cellulose lattice C-IV is not a polymorphous form of cellulose in quite the same
proportion as the lattices C-I and C-II, but C-IV is more unstable than the said ones,
and can be held to be a defective and unorganized form of cellulose-I. On the other
hand, in the cellulose C-II/C-IV-transformation, there is a change in the cellulose
superstructure to a more organized lamellar structure, which can easily be shown with
x-ray low angle scattering measurements.
[0039] SAXS-analysis of both natural (C-I) and regenerated (C-II) cellulose fibers shows
a generally monotonicly decreasing intensity(I)/scattering angle (∈)-function. An
intermittent lamellar structure perpendicular to the fiber direction which is common
for synthetic fiber polymers is thus not often seen with cellulose fibers. The poor
formation and recognizability of the long identity period in cellulose fibers is due
to the low and density differences between the crystalline areas as well as especially
also due to the channels between the amorphous areas and microfibrils arranging themselves
in the direction of the fiber axis (
i.a. cotton and corresponding structures).
[0040] In partly disrupted (
i.a. swollen with alkali solutions) cellulose structures flexion points and points of
discontinuance can be seen in the scattering function, especially when using a Lorenz
correction (Iε
2/ε-function) for the scattering results.
[0041] In the SAXS scattering tests carried out, samples made from production fibers were
used. Thus, partly for practical reasons (crimp, preparation of sample
etc.), the scattering result does not represent cases where the radiation plane is exactly
vertical to the fiber axis, as part of the sample fibers have a completely deviating
direction.
In the SAXS-graphs of cellulose fibers in their basic state there was in the Iε
2/ε-function for both natural and regenerated fibers a more or less sharp peak or anomaly
in the scattering angle range, E = 17-19 mrad, which corresponds to the Bragg period,
L(Z) = 45-40 Å. In the SAXS graph of regenerated cellulose fiber there was, in addition
to the said line, also a definite peak, which corresponded to the scattering angle
E = 1.0 + 0.5 mrad, that is (L)Z = appr. 771 Å. In cotton fibers a weak anomaly was
detected in the scattering behaviour also in the range : ε = 9-11 mrad and L(Z) =
86-70 Å.
[0042] Cotton and rayon fibers (IS and A-71) were heat treated in a thermostat (200 °C/4h)
in a nitrogen atmosphere. The heat treatment did not introduce noticeable changes
in the WAXS-scattering angles of the lattice planes of the samples as compared to
the starting fibers. A slight increase in the crystallinity degree could be detected
in the samples: IS: 69→ 71 % and A-71: 40-42 %. In the SAXS scattering of dry heat-treated
regenerated cellulose fibers there were no essential changes as compared to the starting
fibers. The scattering function of cotton fiber showed however increased intensity,
corresponding to the scattering angle of ε = 7.5 mrad that is L(Z) = 103 Å.
[0043] As has already been stated earlier, polar liquids at increased temperatures effect
a change in the crystal structure from the C-II and C-I form to the form C-IV, and
associated herewith, a substantial increase in the crystallinity degree of especially
regenerated fibers. Simultaneously a substantial organization of the cellulose superstructure
takes place, which is indicated by a sharpening of the intensity peaks of the SAXS
scattering graphs and corresponding effectuation in the lamellar structure. When the
treatment temperature increases, the maximum values of the Iε
2/ε-functions shift towards low scattering angles and a corresponding increase in the
'long identity period', L(Z) values. As the crystallinity degree of the structure
increases substantially at the same time, the increase in the lamellar distances means
a substantial increase in the lamellar thickness. The change in the long period as
a function of temperature followed the following equation form

The value for the constant N was constant for rayon fibers within the limits of measurement
accuracy, that is N = 43390 Å/ °C. Similarly the "character" temperature ϑ
o was constant, that is ϑ
o = 414.5 °C. The value for the constant M was a function of the fiber quality (also
for cotton fibers). For the xanthate based rayon fibers A-71 the value for the constant
was, M = 110.2 Å. At the exemplary temperatures, the length of the Lorenz-corrected
long period was: L(Z), equation measurement/°C: 182.0-181.4/266, 144.3-140.2/244,
94.0-102.0/202 and 44.5-42.8/134.
As an example, the M values for three xanthate based fibers will be mentioned: 120.9/Lnz,
145.4/Cs-88 and 110.8/Cs-75. For a NMMO-solvent based rayon fiber, L-71, the value
of the constant M was, M = 150.2 Å, that is the values for the long period were substantially
lower than for the fiber A-71.
[0044] As a general result of the SAXS-analyses it can be said that especially by regulating
the heating temperature in the polar liquid (the heating time being of lesser importance),
the crystalline lamellar thickness of cellulose can be regulated, whereby the critical
dimensions of the nucleation planes for the heterogenous nucleation of the cellulose
surface can be exceeded.
Subexample 2.
[0045] In the subexample 2., the wetting of cellulose surfaces with melted polypropylene,
spreading of the contact melt and kinetics of spreading is studied in association
with the new method.
A prerequisite for a strong adhesion strength between a cellulose surface and polypropylene
is the formation of a sufficient contact surface during a sufficiently short, technically
easily realized time span. These requirements presuppose on the one hand sufficient
wetting between the cellulose surface and polymer melt, a sufficiently rapid spreading
of the melt on the contact surface and correspondingly, during polymer melt solidification,
the provision of an epitaxical "grain border crystallization" (transcrystallization).
[0046] In this connection, the level of the not very well known surface energies of the
various structural surface forms of solid cellulose, and, due to the strong polarity
of cellulose, the quality of the energies, are of importance, wherefore the measurements
are primarily directed to clarifying these.
The driving force for the spontaneous spreading of a liquid onto a solid surface is
comprised of non-equilibrium border surface forces, that is

wherein f
d is the driving force acting on a unit length of the liquid front, γ
SV is the surface tension of the solid with the saturated vapour of the liquid, γ
SL is the border surface tension between solid and liquid, γ
LV is the surface tension of the liquid and θ is the momentary contact angle.
By applying the Young equlibirium equation in the equation /16/, one obtains /1,12/:

wherein θ
e is the border angle corresponding to the equilibrium state.
Due to the additivity of the energies between the molecules formed by the non-polar
and polar components, the following equation is obtained for the formation of the
border surface energy (γ
SL)

wherefrom, by applying the Tonng equation, one obtains

where γ
Sd, γ
Ld and γ
Sp, γ
Lp are the dispersive and polar components of the solid and liquid surface tensions.
In this connection the said harmonic average (/19/: partly empirical: S. Wu) is used
in combining the dispersion and polar forces of the solid and liquid phases, as the
cellulose surface is strongly polar and the normal geometric average is thus unsuitable
for the application.
[0047] The empirical measuring quantity, that is the critical surface tension, γ
c, of wetting of a solid surface developed by Fox and Zisman /12/ is very usable. It
was observed that the function provided by homologous liquid series on a solid substrate:
cosθ/γ
LV is generally a straight line, which when extrapolated to the value, cosθ = 1 gives
a specific surface tension γ
LV, that is the said critical tension, γ
c. Thus liquids having a surface tension smaller than γ
c, spread on the solid surface.
[0048] In the studies of the subexample, glycerol, formamide, methylene iodide, tetrabromoethane,
α-bromo- and
α-chloro-naphtaline were used as organic liquids for the measurement of the surface
energy relationships for cellulose, of which liquids the two first ones are strongly
polar. The surface tensions of the liquids and their dispersive and polar components
corresponded to the values in the known literature (Wu, Toussaint-Luner:/12/).
The regenerated cellulose fibers used in the study were xanthogen and N-methyl-morpholine
oxide based (A71- and L71-type) and also purified cotton. Part of the studied fibers
were heat treated in polar liquids. The cellulose fibers were conventional, productional
qualities, from which the finishing agents had been extracted. The heat treated fibers
were surface cleaned with an ethanol-ether solution. The dynamic contact angle measurements
were done with a Cahn DCA-322-analyzer using the said liquids.
[0049] From the contact angles measured in non-polar liquids the following critical surface
energies for the cellulose fiber qualities A-71 and L-71 as well as for the natural
cotton fibers PV were obtained: γ
c, MJ/m
2: 33.5 and 39.5 as well as 39.8. The spread in measurement values was substantial
but its effect on the values for the critical surface energy is not, however, substantial.
The measurement values obtained correspond quite well to the values from literature.
The measurement values for both regenerated cellulose (C-I structure) and hemicellulose
were to their numerical values and also to their cosθ-extrapolation lines compatible
with the cellulose quality A-71 (Luner et al.: woodcast, avicel: γ
c = 35.5, cottoncast: 41.5, SW-Xylan: γ
c = 35
etc.). The values for the critical surface energy of cotton and pulp fibers (C-I-structure)
vary in literature, depending on the polarity values for the used measuring solutions.
For Douglas pulp fibers a value (Nguyen et al.) of, γ
c = 52.9 is given when measured in polar liquids, and measured in non-polar liquids
a value of, γ
c = 39.3. For cotton one obtains by computing from the γ-components (Westerlind
et al.) in non-polar liquids-the value, γ
c = 38.6 mJ/m
2.
As a result of heat treatment in polar liquids (glycerol, water) the critical surface
energy values (measured in non-polar liquids) for the samples from the test series
A-71 and L-71 increased substantially:
γ
c, MJ/m
2/γ, °C:
A-71: (CH
2)
2CH(OH)
3: 33.5/21, 37.5/200, 37.0/202, 39.5/222, 44.1/244 and H
2O: 37.8/145
L-71: (CH
2)
2CH(OH)
3: 39.5/21, 43.1/202, 41.6/222, 44.2/244 and H
2O: 39.7/145
Although one should, based on the above discussion, relate critically to the critical
surface tension, it is evident based on the test series that the surface energy of
a cellulose fiber surface increases as a result of heat treatment in polar liquids,
the magnitude of the increase being decreasing when the crystallinity degree of the
starting fiber is increasing. The critical surface energy of a regenerated cellulose
fiber thus approaches the corresponding values for natural fibers as a result of the
lattice transformation caused by the heat treatment.
[0050] When determining the critical surface energy in non-polar liquids it could be deduced
that by applying the harmonic method of Wu only part of the values for the surface
energy components obtained were comparable with the corresponding literature values.
For reasons of comparison, some calculated γ
sd- and γ
sp-values for a cellulose surface are indicated in the table 2. From the results it
can be seen that the dispersive component of the surface energy approximately corresponds
to the corresponding literature values. The polar surface energy component of the
samples studied is lower than normal, except for cotton. The low values apparently
are due to impurity components remaining on (or added to) the surfaces of technical
cellulose fibers affecting the polarity (there is often hemicellulose or lignin residues
also on natural cellulose surfaces). The Table 2. contains some surface energy values
obtained for cellulose films coated with alkyl-ketene-dimer (Toussaint et al. /12/:
1.6 - 2.1 - 2.4 µg AKD: hydroxy groups of the surface have been substituted with AKD
molecules up to 36%), from which a strong reduction in the polar energy component
as a function of "degree of coverage" of the surface can be seen, the dispersive component
remaining substantially constant.
In addition the values (mJ/m
2) for the driving force (fd) in spreading and the adhesion work (Wa) corresponding
to the measurement values given in the table 2. for a polypropylene melt/cellulose
system are given:
fd-Wa/fiber: 6.15-48.9/PV-1, 5.58-48.3/A-71-LK-200 °C, 9.23-52.0/A-71-LKA-145°C and
11.7-54.2/A-71-LK-244 °C.
[0051] Based on the surface energy measurement results it can be concluded in a general
manner that except for cotton, the surface energy values of cellulose surfaces and
polypropylene melt are so close to each other that the effect of contaminating components
has to be controlled in surface energy measurements. In a technical range, the contamination
residues or additions in cellulose can be monitored and taken advantage of in the
process control.
[0052] In addition to elucidating the surface energy relationships, an object of study in
the subexample is the rate of spreading of a polyolefin melt on cellulose surfaces,
which is of substantial importance with respect to the realization and regulation
of the adhesion process. The measurements relating to spreading of the polymer were
carried out by placing a quantity of polyolefin of appr. one milligram on cellulose
surfaces of different qualities (regenerated, grafted cellulose films and thin fiber
compressed bodies of natural cellulose) by melting the polymer and bringing it to
the desired temperature using a thermostate-regulated hot-table-protection gas oven.
The spreading of the melted drop was photograhed as a function of time and temperature
with a CCD camera, the information was loaded on magnetic tape and the measurement
of the recordings took place using image-analytical methods. The contact angle change
of the solidifying melt and the final contact angle when the polymer was in a solidified
state was measured for control reasons also with a contact angle analyzer.
The kinetic analysis of the spreading of the polymer was carried out according to
the enclosed study /1,12/. By combining the equations for the spontaneous spreading
of a liquid on a solid support and that of the retardation force resulting from the
viscosity of the liquid, the following equation can be obtained for the rate of change
of the cosine of the wetting angle of the system:

wherein θ
e is the equilibrium contact angle, γ
L is the surface energy of the liquid, η is the viscosity of the liquid and L the scaling
length.
The equation /20/ in integrated form is hereby

wherein c = γ
L/η•L and a = 1-cosθ
o/cosθ
e and θ
o is the contact angle at the starting point (t = 0).
According to the equation /21/ the rate reaction of the change of the contact angle
cosine is directly proportional to the surface tension of the wetting polymer melt
and inversely proportional to its low shear rate viscosity. The temperature dependency
of the polymer surface tension is low, wherefore the temperature dependency of the
rate coefficient under study is primarily determined by the activation energy of the
polymer melt viscosity (PP: E
~ 8000 cal/mol). The polymer surface tension is only modestly dependent on the molecular
weight, with the exception of its low values (Mn<5000). The effect of the molecular
weight on the polymer melt viscosity above the so called critical molecular weight
(PP: M
W,c
~ 5000) is rather substantial. In the area of low shear rate (D = 1s
-1) the viscosity of the polypropylene melt can be characterized with the equation η
=

[0053] By regulating the surface energy of the polymer (additives) it is possible to affect,
to a small degree, its spreading rate on a solid surface. By regulating the viscosity
of the polymer, the rate of wetting of a solid surface can be regulated to a remarkable
degree by reducing the weight average molecular weight of the wetting polymer, whereby
it is possible to simultaneously take advantage of the reduction in the polymer melting
point /14/. In practical operation it is possible to effect a degradation of the molecular
chains in the surface layer of the polyolefin fibers by molten state spinning oxidation
/15/ in connection with fiber spinning.
[0054] The spreading of a polymer melt on the surface of a solid material can be determined
by a number of structural factors of the solid or by natural or added chemical impurities
on its surface (lignins, hemicellulose, finishing agents
etc.) as well as mechanical barriers on the solid surface.
In the kinetic measurements of this subexample, specifically the behaviour of conventional,
often impure cellulose surfaces in connection with the spreading of a molten polypropylene
drop was studied. In the measurements, no primary or secondary rim films anticipating
spreading of the drop were detected. Primarily due to film impurities and irregularities
equilibrium contact angles were not looked for in the studies, but an angle was selected
for the contact angle value (θ
e) where dθ/dt seemingly became constant. For the values needed in practice, the method
cannot be significantly erroneous. Results from some spreading tests are indicated
in the table 3. Of the films in the table, the films no. 1 and 2 are cellulose-carbamate
based C-II-films. The nitrogen contents of the films are 1.6 and 0.18% respectively.
The nitrogen is situated as an isocyano acid additive in the 6-carbon of the cellulose
(CH
2O-C-NH
2:/16/). The film no 3 is a cellulose xanthogenate based C-II-film. Of the samples
in the table, the cellulose samples no. 14 and 22 are bleached and unbleached fine
cellulose fiber (C-I-structure).
In the kinetic studies the MWD-analyses of the treated polypropylene qualities are
according to the appended table. In the table, also the viscosities according to the
formula /22/ at the temperature 180 °C are indicated. The table also contains the
relative rate constant values for the wetting rate constant for the sample pair corresponding
to the bleached cellulose fiber (no. 14) of the table 3 as calculated from the viscosity
values as well as the time needed to reach the θ-value according to the rate equation
/21/.
The sample pairs no. 9 and no. 3 of the table 3. differ from each other primarily
with regards to the molecular weight distribution of the polypropylene melt. Their
rate constant ratio, C(3)/C(9) = 3.24, should thus be inversely proportional to the
ratio of the corresponding viscosities. According to the enclosed table, the viscosity
ratio is η(22)/η(21) = 4.65, there thus being a sufficient conformity between the
rate constants and the viscosities.
Sample |
MFR
g/10 min |
MWD
MW - D |
η
Pa•s |
c
min-1 |
t(70)
s |
PP 21 |
350 |
124450 - 3.86 |
207 |
0.606 |
52 |
PP 211 |
800 |
98410 - 4.44 |
91 |
2.269 |
14 |
PP 22 |
26 |
193300 - 5.53 |
960 |
0.215 |
146 |
PP 23 |
4.4 |
407500 - 7.00 |
12970 |
0.016 |
1927 |
'PP 24' |
- |
50000 |
8.6 |
24 |
1.3 |
MFR: ASTMD 1238 |
[0055] It can be mentioned that according to the table 3., the ratio between the rates of
change of the wetting angles of sample pairs no. 3 and 9 (in the point θ = 70°) and
the times needed to reach the contact angles are 4.48 and 4.14, respectively.
According to the results in the table 3., the rate coefficient of wetting for the
bleached cellulose fiber (no. 14) is slightly higher than that for the unbleached
(no. 12). In the enclosed table, the change in rate coefficient corresponding to the
bleached cellulose fiber (C-I-structure) has been calculated, when the values for
the weight average molecular weight of the wetting polymer and correspondingly for
the melt viscosity change to values which are both higher and lower than that of the
reference polymer. The molecular weights of the surface layers of peripherically oxidized
polymer fibers are /15/ in the range, M
W = 500.000 → < 10.000. Thus by regulating the molecular weights of fibers made from
conventional technical polymers or spun oxidized fibers, it is possible to regulate
the rate, degree of wetting and wetting times between a polypropylene melt and cellulose
over a very broad range, in an area of operation which is technically easy to implement.
From the results given in the table 3. it can also be seen that the carbamate based
nitrogen content of the sample films (1. and 2.) has a lowering effect on the wetting
rate constant, that is, compared to the xanthogenate based film (3) in a nitrogen
and air atmosphere:


In an air-atmosphere, the rate constants for wetting decrease in all test series
compared to the values in a nitrogen atmosphere. Another important effect of an air
atmosphere is the almost complete disappearance of the rate constant decreasing effect
of the structural nitrogen in the film (the impurity component of the film is oxidized
and evaporates, the film surface is oxidized,
etc. ). As a result of the oxygen in the air, also the value for the equilibrium contact
angle decreases in the test series samples. The effect of both the structural nitrogen
in the film and that of the atmospheric oxygen on the rate of wetting is a result
of changes in the surface energy components. By regulating the surface energy values,
it is thus possible to affect the kinetic characteristics in wetting, but apparently
to a lesser degree than by regulating the viscosity of the polymer melt.
[0056] It can still be mentioned that when the contact samples were cooled after the wetting
measurements it could be observed that the temperature of solidification was even
30 °C above the conventional solidificattion temperature (
~110-115 °C), the degree of subcooling of the polymer melt decreasing correspondingly.
This is a consequence of heterogenous nucleation of the polymer melt on the cellulose
surface. It is also to be observed that this nucleating effect of cellulose decreased
when the molecular weight of the polymer increased; for example the polymer PP 23
in the enclosed table had a melt solidification temperature (air atm.) of 113 °C,
the polymer PP 22 (N
2) 133 °C and the polymer PP 21 (N
2, no 3) 142 °C.
Subexample 3.
[0057] In the subexample 3., thermobonding of fiber mixtures from regenerated cellulose
fibers of varying quality, cotton fibers and conventional and skin-core-type polypropylene
fibers, was studied in order to elucidate the major bonding effects between the fibers.
The apparatuses and their functions, and the methods of operation, control and regulation
of the thermobonding, water needling and spin oxidation processes used in the manufacture
of the fabrics and fibers in the subexamples 3. and 4. are described in detail in
the patents FI 95153 (EP 0 667 406 A1) and FI 101087 (EP 0 799 922 A1) and the FI-patent
applications no:s 953288/030795 (EP 0 753 606 A2) and 974169/071197. For reviewing
the bonding results for the test fabrics, a bonding equation of the form (FI 101087)

was used which well simulates the measurement results, wherein Φ is a strength characteristic
of the fabric: longitudinal and transverse tensile strengths, elongation, breaking
energies
etc., T is the absolute temperature, c is a function of web velocity and weight, draw ratio
in fiber manufacture, chain orientation and molecular weight distribution of the fiber
polymer, proportion of bonding fibers in the fiber mixture
etc.
The bonding equation is satisfactorily applicable for use also in the fabric temperature
range (that is at a temperature above the temperature, T
m, corresponding to the bonding strength maximum, δ
m, where the proportion of bonding polymer partial melt is high).
[0058] The first test series (A) of the subexample 3. was carried out using a pair of steel
rollers with a point patterned and smooth roller. The results of the test series using
the bonding equations is presented in the table 4. and in the figure 1. The characteristics
of the fibers used in the test series are presented in the table 6.
In the test series (A) two different rayon-viscose qualities (R1 and R2) were used
for the bonding series, one of which was cellulose xanthogenate based and the other
a fiber regenerated from a NMMO-solution, as well as a purified cotton fiber (PV,
structure C-I). In bonding, three different polypropylene fiber qualities (PP-5, -1
and -8) were used of which PP-5 was a conventional homogenous polypropylene fiber
and the others were of skin-core type (PP-8 a peripherally highly oxidized fiber).
The results include, in addition to the fiber mixtures, also the bonding results for
the plain polypropylene fiber components. The bonding fiber proportion of the mixtures
was 50 % by weight.
When using conventional polypropylene fiber, the bonding strengths for the fiber mixtures
of both rayon fibers are substantially of the same magnitude on both sides of the
T
m -temperatures. The activation energies of the bonding processes are of the same magnitude
at temperatures below T
m and fairly close to the activation energy of bonding of plain polypropylene fiber
component. At the high temperature area the activation energy for bonding for the
rayon fiber mixtures decreases substantially below the activation energy for polypropylene
bonding, indicating simultaneously that the cellulose fibers participate in the bonding
process. In fiber mixtures corresponding to skin-core type polypropylene fibers, PP-1,
the activation energies for bonding in the temperature range, T < T
m, for cellulose fiber mixtures (R1, R3 and PV) are of the same magnitude and close
to the activation energy for the PP-1-component bonding. The bonding strengths for
the mixtures are also close to each other. The temperature (T
m) corresponding to the maximum value for the bonding strength for rayon-cellulose
mixtures increases substantially over the temperature corresponding to the bonding
fiber, the cotton mixture behaving in the opposite way. In the high temperature range
the activation energy for bonding of cellulose mixtures is below the activation energy
for the corresponding bonding fiber, which with the equation constants shows that
the cellulose participates in the bonding process. The ratios for the bonding strengths
[(R1+PP)/PP] for the corresponding polypropylene fibers were:



At a temperature of 162 °C the ratios obtainable from the equations are: 0.375/PP-5,
0.434/PP-1 and 0.453/PP-8, which order also indicates the quantitative order of participation
in cellulose bonding (at low temperatures the order is approximately the reversed).
The peripherically oxidized fiber quality (PP-8) corresponds well to its melting and
other properties to the fiber qualities obtained by the process disclosed in the FI-application
no. 974169 (subexample 1.5, p. 37-39).
[0059] It is to be observed that due to the small total area of bonding, the small contact
surface of the individual bonding points and the short delay times in bonding, the
manner of point bonding used in the tests gives a low final strength both for rayon
and cellulose mixtures (contact surface: the cellulose-PP-surface melt is low: adhesion).
The point bonding tests show, however, the mutual dependency between the main factors
in bonding, namely the own bonding system of polypropylene fibers and the bonding
system of cellulose mixtures, both with regard to the location of the maximum values
in bonding strength and to activation energies.
[0060] A second test series (B) for the subexample 3 was carried out using a roller pair
formed by a cotton and a steel roller. The results of the test series are given in
the table 5. and in figure 2. The fiber properties of the test series are given in
the table 6. From the results of the test series (B) the results corresponding to
plain polypropylene components are missing, because when using a cotton-steel roller
system the result of bonding of a polypropylene web is a polypropylene film. The temperatures
of the test series (A) and (B) do not correspond to each other. In bonding the temperature
of the unheated cotton roller increases to a value of appr. 80 ± 5°C, wherefore in
order to bring the quantity of heat needed for bonding into the system the temperature
of the steel roller is increased appr. 25 °C above the conventional temperatures for
steel rollers. In the series (A), the temperature gradient between the rollers is
appr. 5 °C, but in the series (B) appr. 90 °C. In the test series (B), two rayon viscose
qualities (R2 and R4) have been used for the preparation of the bonding mixtures,
one of which was a xanthogenate and the other a NMMO-solvent based, as well as two
polypropylene qualities (PP-3 and PP-6), one of which was of skin-core-type and the
other (PP-6) a conventional homogenous fiber. Both from the results of the table 5.
and the figure 2. it can be seen that at the low temperature range (T < T
m) the bonding strengths are approximately of the same magnitude for three mixtures,
but for one mixture (R2/PP-3) the bonding strengths are remarkably higher than for
the previous ones. When using a skin-core type polypropylene fiber, PP-3, in bonding,
the low temperature area (T < T
m) and the strength increase continue to higher temperatures as compared to a conventional
homogenous fiber.
When dissolving the cellulose from the product fabrics with phosphoric acid it can
be observed that at the low temperature area the dissolution does not remarkably affect
the strength for the fiber mixture fabrics R4/PP-6 and R4/PP-3, and thus the strength
in these fabrics is primarily due to the mutual bonding between the polypropylene
fibers. In the fiber mixture fabric R2/PP-3, the dissolution of the cellulose component
decreases substantially the fabric strength both in the low and the high temperature
bonding range, which shows that the cellulose participates in the fiber bonding in
addition to the polypropylene. In the range of high bonding temperatures, the bonding
result of the fiber mixture R4/PP-4 indicates also that the cellulose participates
in the bonding. In the high temperature range, the activation energy term of the bonding
equation for to the said mixture carries a negative sign, that is the bonding strength
increases still above the T
m-temperature. This effect disappears from the results after leaching with phosphoric
acid.
One reason for the bonding activity of the cellulose component of the R4/PP-3-mixture
is the cellulose-IV-structure, which is well visible in the WAXS analysis in the surface
layer of the cellulose fiber R4. It is also to be observed that when binding with
a cotton roller system, the bonding area is rather large and due to the plastic bonding,
the polypropylene melt spreads easily around the fiber, both factors bringing their
own contribution to the final product strength.
Subexample 4.
[0061] In the subexample 4. the improvement and regulation of the bonding between cellulose
fibers by means of corona treatment is studied.
Improvement of the adhesion between cellulose fibers is essential especially when
polyester, polyamide or similar fibers, which are inert with respect to cellulose,
comprise the binding synthetic polymer fibers for a water needled fiber fabric having
a fairly high basis weight. In order to prevent cellulose lint from being released,
hereby, if necessary, pre-mixing of polyolefin microfiber with cellulose can be used,
as well as a melt wetting-transcrystallization process for the cellulose-polyolefin
contact after the needling process. Hereby an improvement also in the cellulose-cellulose
adhesion facilitates the provision of a pre-contact in the cellulose-polyolefin mixture.
The said combined method can advantageously be used in the manufacture of absorbent
and simultaneously mecanically strong nonwoven laminate fabrics.
[0062] In the studies relating to the adhesion between cellulose fibers, a pilot scale corona
apparatus was used (Sherman High Frequency Generator: 20 ± 5 kHz, D-2 kW). The studies
relating to the release of cellulose lint were carried out using a Gelbo Flex Test
apparatus (5000 ES; EDANA 22.0-96: Linting tendency).
[0063] In this connection the adhesion between cellulose fibers is studied in a conventional
hydroentangled polyester-pulp cellulose fiber fabric (50 % by weight PES; 70 g/m
2), where the cellulose fiber format was hydroentangled against a polyester nonwoven
on top of a wire. The degree of mixing between the components was high in the product,
but the release of cellulose lint was different on both sides of the fabric (sides
A and B). For the basic comparison series the initial fabric was treated only with
the SHFG-apparatus as a function of the effect. The particle counts (N, number)/Cu.ft)
in the cellulose lint released from the product fabric increased slightly as a function
of the electrical work (W, wh/m
2) applied to the fabric,
i.e. N(A) = 1010 + 143W and N(B) = 3635 + 98W.
In order to show the effect of the corona treatment, the amount of lint released from
the initial fabric was increased by wetting the fabric with saturated water vapor
and by drying by heat rolling (115 °C, 0.1 - 40 kN/m). The results showed that the
lint quantities released from the test fabrics decreased approximately linearly as
a function of the electrical work applied thereto. The following values were obtained
for the lint quantities
N(A) = 37867-(4183-5748)W and N(B) = 20328-(1857-2713)W, where the values for the
'work coefficient' in brackets correspond to the maximum and minimum values obtained.
Lint values for the initial fabrics which were lower than those studied above behaved
correspondingly when treated in the above mentioned manner.
According to the test results, cellulose-cellulose fiber adhesion can be improved
very efficiently by means of a corona, wetting and drying treatment, and already with
a low electrical work load applied to the fabric the amount of fine cellulose lint
which is released from the fabric can be reduced practically to zero value.
[0064] The size distribution of the cellulose lint emitted from the test fabrics proved
to be practically unchanged and also independent of the lint quantity, when treating
lint of minimum size, d = 0.5 pm for five minutes. However, the lint size distributions
taken as minute average values in the test series proved to be rather substantially
different from the sum distribution, the difference in percentage as a function of
time decreasing with increased particle size. When the particle size was in the range
of 0.3 - 0.5 µm, the said difference in percentage as a function of time proved to
be the opposite with respect to the other particle size classes, which shows the special
importance of the lint classes below 0.5 pm in the distribution system. It is especially
to be observed that in the lint size classes of corona treated fabrics there appeared
no percentage spread of the above kind in the various size classes as a function of
testing time (which to its own part shows the effect of the treatment also on the
lint size distribution).
Reference literature
[0066]
/1/ S. Wu:
Polymer Interface and Adhesion, Marcel Decker,
Polymer Blends I, Ed. D.RNew York, 1982,
337-465 . Paul, S. Newman, Academic Press,
New York, 1978, 278-288
/2/ L. Goldfarb:
Makromol. Chem. 181, 1980, 1752-1762; 179, 1978, 2297-2303
H. Schonhorn, F.W. Ryan:
J. Polym. Sci., A2, 6, 1968, 231-240; 7, 1969, 105-111
Polymer Letters, 5, 1967, 919-924
D.G. Gray:
Polymer Letters Ed., 12, 1974, 509-515
S.Y. Hobbs:
Nature Phys. Sci., 234, 1971, 12-13; 239, 1972, 28-29
/3/ US 3,507,943/21.04.70: J.J. Such, A.R. Olson
US 3,501,369/13.03.70: A.H. Drelich, M.R. Fecillas
US 3,485,706/23.12.69: F.J. Evans
US 4,442,161/10.04.84: B. Kirayogly, P. Zafirogly
US 4,902,564/03.02.88: J. Israel, S.P. Suskind
US 5,459,912/24.10.93: J.M. Oathout
/4/ J.P. Moreau:
INDA J. of Nonwovens Res., 2, 1990, 14-22
T.F. Gilmore, R.K. Nayak, M. Mohammed:
INDA-TEC, '92 Proceedings, Ft-Lauderdale, FL, April 7-10, 1992, 249-259
R.A. Haldon, G. Athey:
TAPPI 1985, Nonwovens Symposium, 149-154
/5/ FI-application 961252/18.03.96: S.Mäkipirtti, E.Lampila, H. Bergholm
/6/ A. Gröbe: V, 117-118
Polymer Handbook, Ed. J.Brandrup, E.H. Immergut,
John Wiley, New York, 1989
/7/ E. Treiber:
Die Chemie der Pflanzenzellwand, Springer, Berlin, 1957, 139-223
/8/ O. Ellefsen, N. Norman:
J. Polym. Sci., 58, 1962, 769
W.J. Wellard:
J. Polym. Sci., 1954, 471
Ch. Legraud:
Compt. Rend., 233, 1951, 407
J. Chem. Phys., 48, 1951, 33
J. Polym. Sci., 7, 1951, 333
/9/ K. Hutino, I. Sakurada:
Die Naturwissenschaften, 28, 1940, 577-578
T. Kubo:
Z. Phys. Chem. (A), 187, 1940, 297
/10/ E. Ott, H.M. Spurlin, M.W. Grafflin:
Cellulose and Cellulose Derivatives, Interscience,
New York 1954, 236-247
/11/ A.N.J. Heyn:
Textile Res. J., 1949, 163-172
P.H. Hermans, D. Heikens, A. Weidinger:
J. Polym. Sci., 35, 1959, 145-165
J.S. Higgins, R.S. Stein:
J. Appl. Cryst., 11, 1978, 346-375
/12/ F.M. Fowkes:
J. Phys. Chem., 67, 1963, 2538-2541
Y. Tamai,K. Makunchi, S. Suzuki:
J. Phys. Chem., 71, 1967, 4176
S. Wu: /1/,
J. Polym. Sci., 34, 1971, 19-30
H.W. Fox, W.A. Zisman:
J. Colloid Sci., 7, 1952, 109
A.F. Toussaint, P. Luner:
Cellulose and Wood, Proceedings of the Tenth Cellulose Conference: Ed. C. Schuerch,
Wiley, 1989,
1515-1530
Contact Angle, Wettability and Adhesion: Ed. K.L.
Mittal,VSP, 1993, 383-396
P. Luner, M. Sandell:
J. Polym. Sci., C, 28, 1969, 115-142
T. Nguyen, W.E. Johns:
Wood Sci. Technol., 12, 1978, 63-74
B.S. Westerlind, G. Berg:
J. Appl. Polym. Sci., 36, 1988, 523-534
S.B. Lee, P. Luner:
TAPPI, Jan. 1972, 55, 116-121
A. Herczeg:
Forest Products J., 1965, 499-505
B.R. Ray, J.R. Anderson, J.J. Scholz:
J. Phys. Chem., 62, 1958, 1220-1230
/13/ S. Wu: /1/, 235-255
H. Schonhorn, H.L. Frisch, T.K. Kwei:
J. Appl. Phys., 37, 1966, 4967-4973
J. Colloid and Interface Sci., 28, 1968, 543-546
B.W. Cherry, C.M. Holmes:
J. Colloid and Interface Sci., 29, 1969, 174-176
/14/ M. Ahmed:
Polypropylene Fibers - Science and Technology, Elsevier, New York 1982, 146-151
H-G. Elias:
Macromolecules 1, Plenum Press, New York 1984,
400-403
/15/ FI-application no 974169/07.11.97
/16/ Neste Oy, Kulloo, Finland: Research Centre: P. Eenilä, J.I. Huttunen: 13C NMR-obs.