BACKGROUND OF THE INVENTION
[0001] The invention pertains to a method of inhibiting decomposition of hydrogen peroxide
as well as to a method for pre-treating wood pulp prior to bleaching.
[0002] Hydrogen peroxide solutions are commonly used for bleaching cellulosic materials,
including paper pulps, cotton, linen, jute, etc. However, the peroxide should be stabilized
to prevent premature depletion thereof, in view of the deleterious presence of metal
ions such as iron, manganese and copper. Conventionally, sodium silicate has been
used as a peroxide bleach stabilizer, but tends to form insoluble silicates which
can be deposited onto the fibers being bleached, as well as onto the apparatus.
[0003] Similarly, prior to bleaching of pulps, a pretreatment with a chelating agent is
a standard operation in order to control the metal profile of the pulp. Chelant pre-treatment
is a key factor in achieving feasible brightness levels and viscosities upon bleaching/delignification
with peroxide. Decomposition of peroxide under alkaline conditions is greatly influenced
by the presence of certain inorganic compounds which behave as peroxide decomposition
catalysts. Transition metal ions, such as manganese, iron and copper are examples
of such catalysts, and thus should be removed prior to bleaching. Such deleterious
transition metal ions can be sequestered by the chelating agent and are subsequently
washed out of the system in a subsequent washing step.
[0004] The bleaching process with peroxide usually takes place between a pH of 10 and 11
and a temperature of 71-77°C. Under these alkaline conditions, the following reaction
occurs:

The perhydroxyl ion (OOH
-) created is what performs the bleaching. However, if transition metals are present,
the following reaction takes place:

The radicals created enhance the decomposition process. Manganese is the metal of
most concern when peroxide is the bleaching agent used.
[0005] When hydro-sulfite is the preferred bleaching agent, the metal of most concern is
iron. Hydro-sulfite bleaches pulp by a reduction reaction with the chromofors in the
pulp. If iron is present, however, the hydro-sulfite will reduce the iron before the
chromofors, hence a larger amount of bleach is needed.
[0006] Basta et al., "Reducing Levels of AOX - Part 3, Lowering of Kappa No. Prior to ClO
2 Bleaching", pgs. 23-33, discloses that pre-treatment with ethylenediaminetetraacetic
acid (EDTA) at a pH of between 5 and 7 substantially improves delignifying and brightening
action of hydrogen peroxide on oxygen predelignified softwood kraft pulp. EDTA performed
better in this regard than other chelating agents tested, namely, DTPA, TRILON ES9910
and DEQUEST 2060S. Similarly, US-A-No. 4,732,650 discloses the silicate-free bleaching
of wood pulp by the combination of a pretreatment of the pulp with a polyaminocarboxylic
acid or salt such as ethylenediaminetetraacetic acid, followed by a bleaching with
a peroxide solution together with stabilizing components.
[0007] Ethylenediaminetriacetic acid (ED3A) and its salts (such as ED3ANa
3) have applications in the field of chelating chemistry, and may be used as a starting
material in the preparation of strong chelating polymers, oil soluble chelants, surfactants
and others. Conventional routes for the synthesis of ethylenediaminetriacetic acid
were achieved via its N-benzyl derivative, which was subsequently hydrolyzed in alkaline
solutions to ED3ANa
3, thus avoiding cyclization to its 2-oxo-1,4-piperazinediacetic acid (3KP) derivative.
One example of the synthesis of ethylenediamine-N,N,N'-triacetic acid is disclosed
in
Chemical Abstracts 78, Vol. 71, page 451, no. 18369c, 1969. There it is stated that ethylenediamine
reacts with ClH
2CCO
2H in a 1:3 molar ratio in basic solution at 10°C for 24 hours to form a mixture from
which ethylenediamine-N,N,N'-triacetic acid can be separated by complexing the same
with Co(III). The resulting cobalt complexes can be isolated through ion exchange.
[0008] US-A-5,250,728 discloses a simple process for the synthesis of ED3A or its salts
in high yield. Specifically, a salt of N,N'-ethylenediaminediacetic acid (ED2AH
2) is condensed with stoichiometric amounts, preferably slight molar excesses of, formaldehyde,
at temperature between 0° and 110°C, preferably 0° to 65°C and pH's greater than 7.0
to form a stable 5-membered ring intermediate. The addition of a cyanide source, such
as gaseous or liquid hydrogen cyanide, aqueous solutions of hydrogen cyanide or alkali
metal cyanide, in stoichiometric amounts or in a slight molar excess, across this
cyclic material at temperatures between 0° and 110°C, preferably between 0° and 65°C,
forms ethylenediamine N,N'-diacetic acid-N'-cyanomethyl or salts thereof (mononitrile-diacid).
The nitrile in aqueous solutions may be spontaneously cyclized in the presence of
less than 3.0 moles base: mole ED2AH
2, the base including alkali metal or alkaline earth metal hydroxides, to form 2-oxo-1,4-piperazinediacetic
acid (3KP) or salts thereof, which is the desired cyclic intermediate. In the presence
of excess base, salts of ED3A are formed in excellent yield and purity. This patent
also discloses an alternative embodiment in which the starting material is ED2AH
aX
b, where X is a base cation, e.g., an alkali or alkaline earth metal, a is 1 to 2,
and b is 0 to 1 in aqueous solutions. The reaction mixture also can be acidified to
ensure complete formation of carboxymethyl-2-oxopiperazine (the lactam) prior to the
reaction. Formaldehyde is added, essentially resulting in the hydroxymethyl derivative.
Upon the addition of a cyanide source, 1-cyanomethyl-4-carboxymethyl-3-ketopiperazine
(mononitrile monoacid) or a salt thereof is formed. In place of CH
2O and a cyanide source, HOCH
2CN, which is the reaction product of formaldehyde and cyanide, may also be employed
in this method. Upon the addition of any suitable base or acid, this material may
be hydrolyzed to 3KP. The addition of a base will open this ring structure to form
the salt of ED3A.
[0009] In view of this relatively new technology, ethylenediaminetriacetic acid (ED3A) and
its salts now can be readily produced in bulk and high yield. Use of ED3A and ED3A
salts as chelating agents in pulp bleaching would result in a cost-effective process.
Surprisingly, the inventors of the present invention have found that ED3A and ED3A
salts actually enhance brightness and equal or outperform EDTA in such applications,
notwithstanding the presence of only three carboxylate groups in ED3A as compared
to four in EDTA.
SUMMARY OF THE INVENTION
[0010] The problems of the prior art have been overcome by the instant invention as described
in claims 1 and 5, which provides a method for metal ion chelation in aqueous solution
and in wood pulps. Extraction and removal of detrimental metal ions, preferentially
manganese, iron and copper, prior to delignification and bleaching is carried out
on pulp, preferably kraft pulp, using ethylenediaminetriacetic acid or ethylenediaminetriacetic
acid salts as the chelating agent.
BRIEF DESCRIPTION OF THE DRAWINGS
[0011]
Figure 1 is a graph of brightness gains of various chelating agents;
Figure 2 is a graph of various brightness gains of various chelating agents after
peroxide bleaching; and
Figure 3 is a graph of iron and manganese removal by various chelating agents prior
to bleaching.
DETAILED DESCRIPTION OF THE INVENTION
[0012] Suitable salts of ethylenediaminediacetic acid that are useful in the present invention
include alkali metal and alkaline earth metals, preferably sodium and potassium, and
ammonium and amine (such as triethanol amine and monoethanolamine) salts, which can
easily be prepared from ED3A acid by conventional means. For purposes of illustration,
the sodium salt will be used, although it should be understood that other salts may
be employed.
[0013] Step 1 in the overall reaction scheme for producing ED3A is the alkaline condensation of
formaldehyde with N,N'-ethylenediamine disodium acetate to form a 5-membered ring
structure, 1,3-bis(carboxymethyl)imidazolidine, and is illustrated as follows:
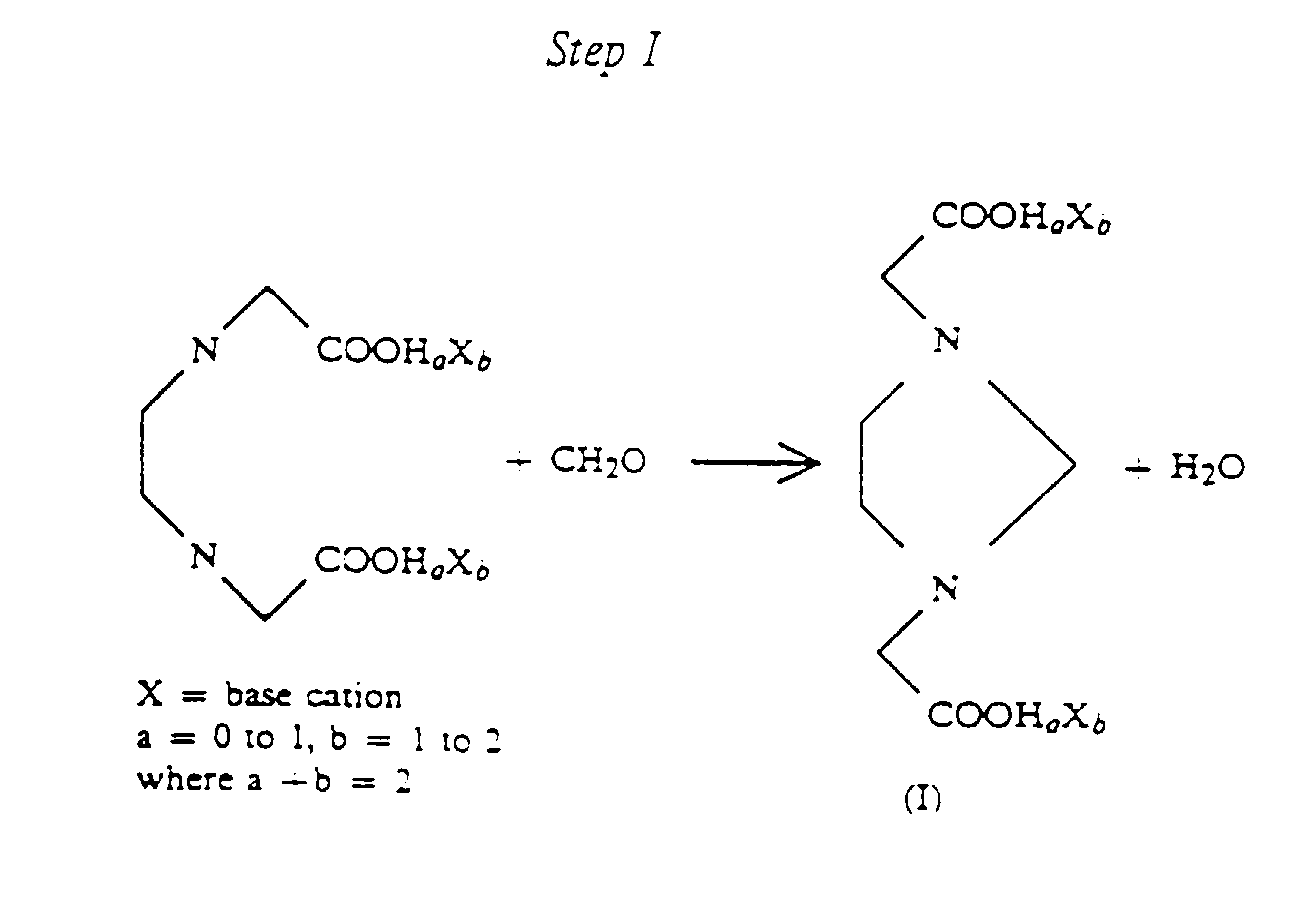
[0014] The above reaction may be carried out in the presence of additional base. Suitable
bases include alkali and alkaline earth metal hydroxides, preferably sodium and potassium
hydroxide. Compound (1) is the bridged reaction product of EDDANa
(1.0→2.0) and formaldehyde, which the is a stable intermediate in the ED3A synthesis. Compound
(I) is formed easily between 0° and 110°C. The
Step I reaction proceeds quickly and forms readily at pH's greater than about 7.0. Preferably
the temperature employed is about 0 to 65°C, most preferably 15 to 65°C, although
temperatures higher than 65°C are operable. Formaldehyde can be used in stoichiometric
amounts, although it is preferred that a slight molar excess be used, preferably 0.5%-2.0%.
Preferably the concentration of the formaldehyde is 55% or less in aqueous solution.
Paraformaldehyde also can be used.
[0015] The second step in the reaction scheme is illustrated below:

[0016] Compound (II) is readily formed at temperatures between 0° and 110°C. The reaction
should be conducted at temperatures at or below the boiling point of the solution.
Preferably the reaction is carried out at temperatures from about 0° to about 65°C,
most preferably about 15° to 65°C to enhance the reaction rate. Suitable sources of
cyanide include gaseous hydrogen cyanide, an aqueous solution of hydrogen cyanide,
or alkali metal cyanide such as sodium cyanide or potassium cyanide, etc. The cyanide
may be used in stoichiometric amounts, although slight molar excesses may be used,
preferably 0.5% - 2.0%.
[0017] Step III in the reaction sequence is the hydrolysis of compound (II) to the monoamide-diacid
compound (III) (partially hydrolyzed mononitrile diacid) and its spontaneous cyclization
to 3KP. Compound (IV) forms readily in the presence of a base such as alkali metal
or alkaline earth metal hydroxides. Preferably the base is NaOH. Mole ratios of <
3.0M base : 1M ED2AH
2 but preferably < 2.0 M base : 1M ED2AH
2 are employed. Higher concentrations of base (i.e. > 3.0 M base : M ED2AH
2) cause some disproportionation of the diacid mononitrile and some ED4A (ethylenediaminetetraacetic
acid) is formed, especially at temperatures > 65°C. In particular, the concentration
of ED4A is found to be in direct proportion to the amount of excess caustic employed,
when high temperature reactions are conducted and high molar ratios of base are employed
(> 2.0M base : 1M ED2AH
2), which may be attributed to the simultaneous hydrolysis of 3KP and disproportionation
of the mononitrile-diacid. When the mole ratio of base to ED2A is < 2.0, higher temperatures
may be used. Also, in
Step III ammonia is eliminated between an amide group and an imino group on the same molecule.
However, at lower temperatures (< 65°C) higher amounts of base may be employed (>
2.0M) and hydrolysis of compound (II) can proceed directly to ED3A without cyclization.
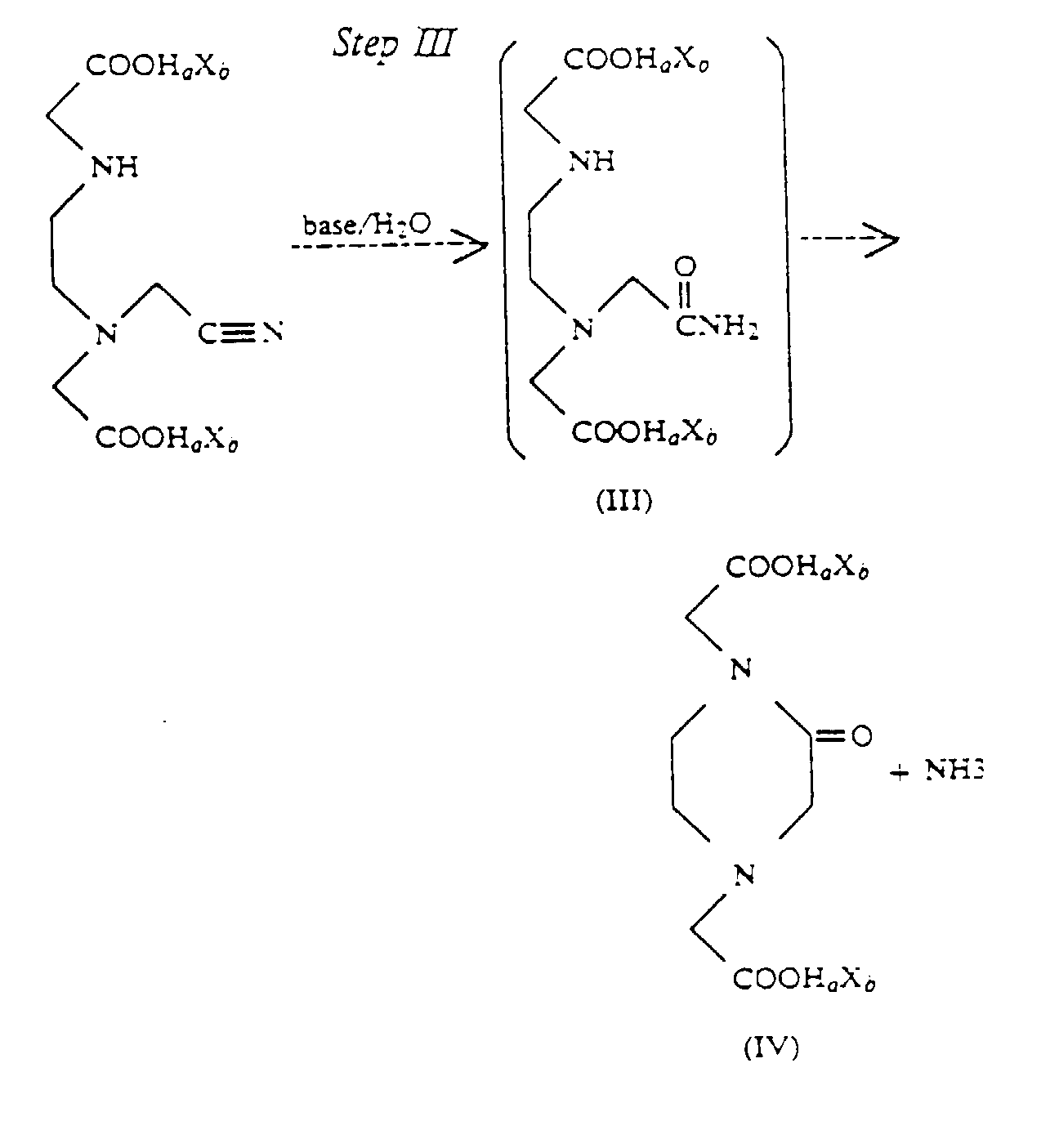
[0018] Step IV is the hydrolysis of 3KPNa
2 by at least the addition of 1 equivalent of caustic, preferably a 1 molar excess
of caustic. This amounts to approximately 5% weight excess (free) caustic in solution
on a 40% ED3ANa
3 solution. The solution is boiled under atmospheric pressure to the desired concentration.
Preferably the reaction is carried out by raising the temperature from the temperature
in
Step III to the boil over a period from about 30 minutes to about 6 hours.
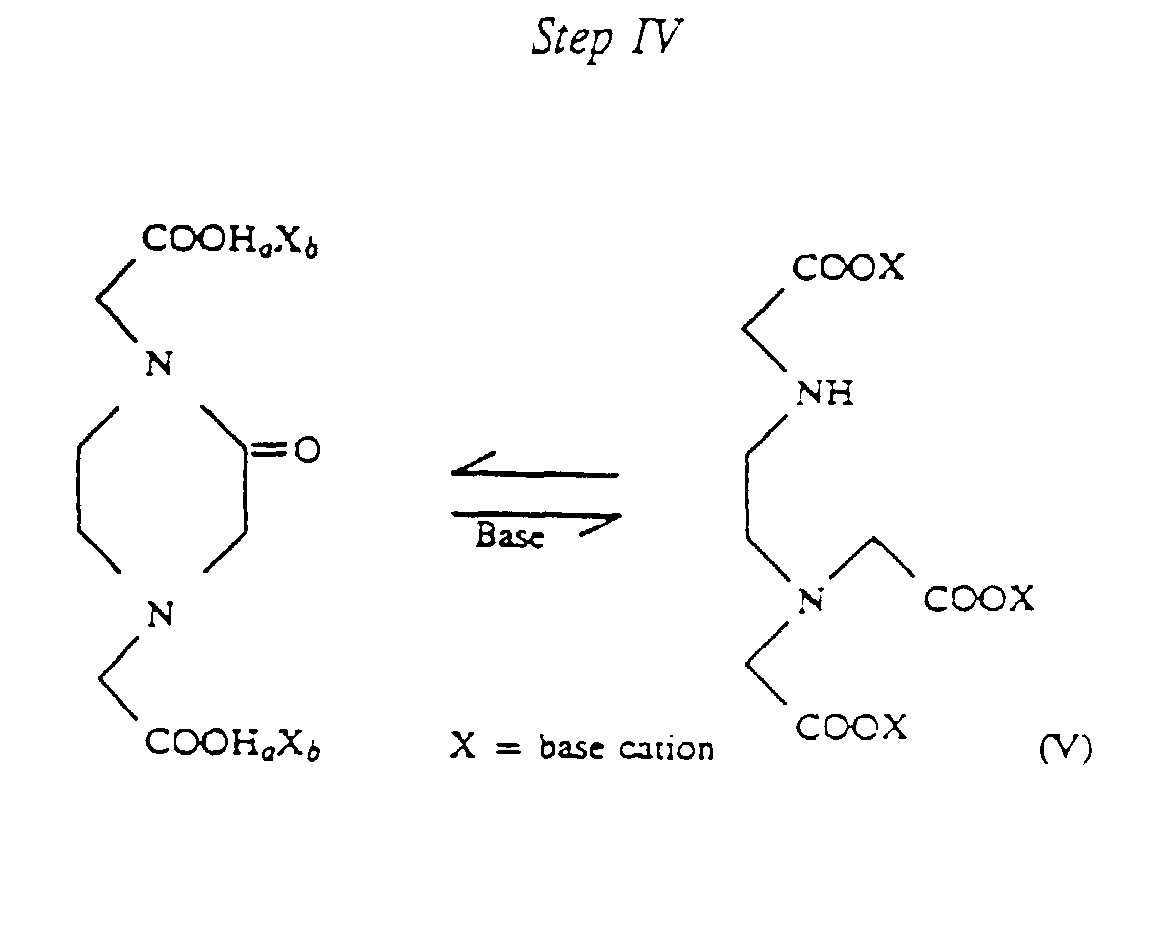
[0019] The resulting solutions typically give approximately 35-40% ED3ANa
3, with approximately 2% 3KPNa
2 remaining as an unopened ringed structure. This corresponds to about a 94% conversion
to ED3ANa
3, with the remaining 6% of mass existing as 3KPNa
2. Acidification of this mass to pH's < 6.0 to produce ED3AH
3 is not possible, as cyclization to 3KPH
2 will eventually occur.
[0020] The foregoing synthetic scheme results in conversions to ED3ANa
3 in excess of 90%, with the residual proportion being 3KPNa
2 to give a total mass balance of virtually 100%. The reactions are tolerant to a wide
pH range.
[0021] Alternatively, ED3A can be prepared using ED2AH
aX
b as the starting material, where x is a base, e.g., an alkali or alkaline earth metal,
a is 1 to 2, and b is 0 to 1 in aqueous solutions. The reaction mixture also can be
acidified with acids having pK
a's less than or equal to 3, prior to during or after the addition of a cyanide source,
to ensure complete formation of carboxymethyl-2-oxopiperazine (the lactam). Formaldehyde
is added, essentially resulting in the hydroxymethyl derivative. Upon the addition
of a cyanide source, 1-cyanomethyl-4-carboxymethyl-2-ketopiperazine or a salt thereof
is formed, and can be isolated in good yield in crystalline form by conventional means
after cooling the reaction mixture. Conversions are quantitative. In place of CH
2O and a cyanide source, HOCH
2CN, which is the reaction product of formaldehyde and cyanide, may also be employed
in this method. Upon the addition of any suitable base or acid, this material may
be hydrolyzed to 3KP. The addition of a base (> 2.0 equivalents but preferably greater
than or equal to 3.0 equivalents will open this ring structure to form the salt of
ED3A. Heating the reaction mixture will enhance the rate of reaction.
[0022] The overall reaction scheme is shown below:
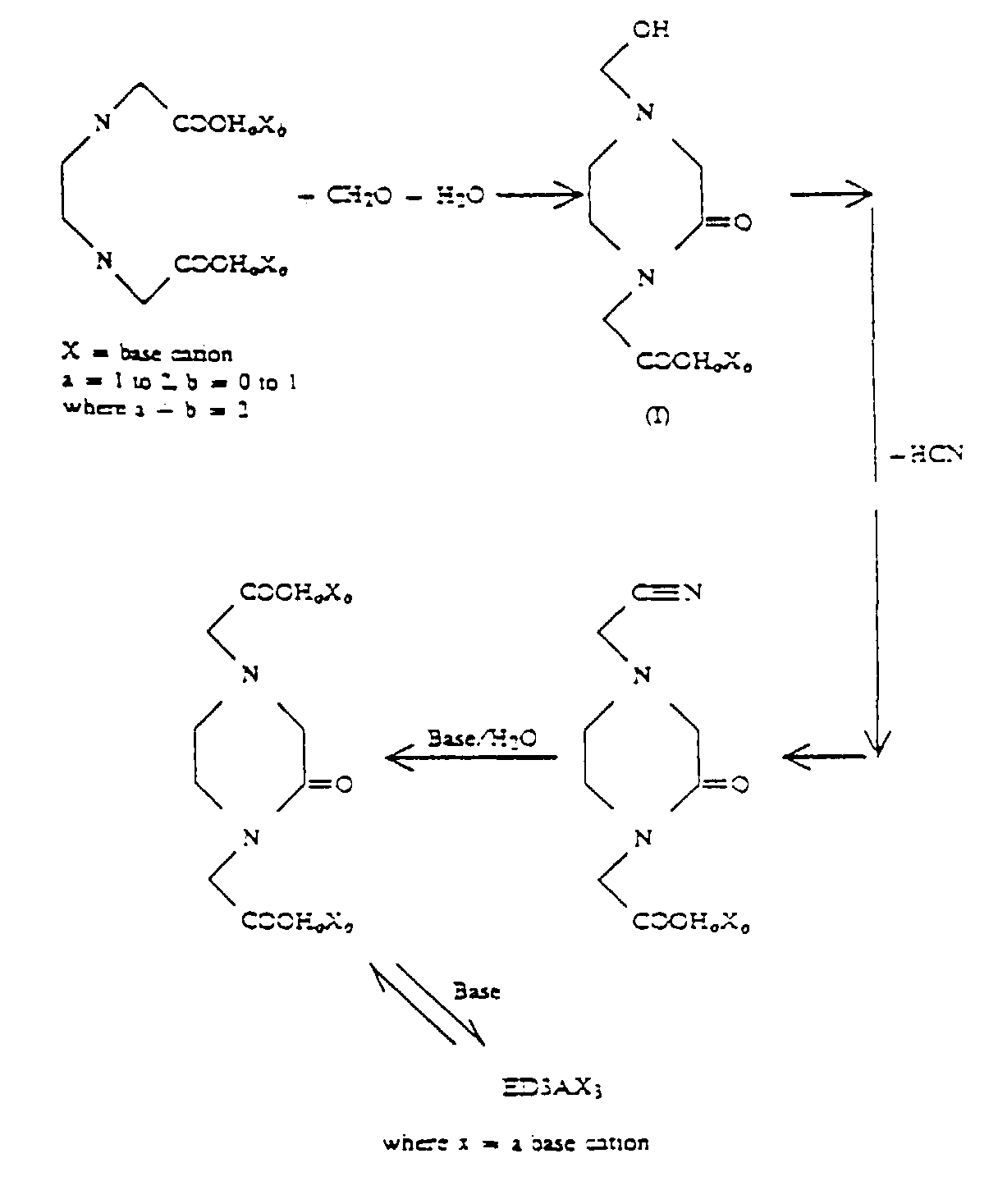
[0023] EDDA can also be allowed to form the lactam (carboxymethyl-2-oxo-piperazine) by acidification,
and the lactam is reacted with chloro or bromo acetic acid to form ED3A or 3KP.
[0024] The chelate pretreatment extraction in accordance with the present invention can
be carried out in a pH range of from about 4 to about 11, preferably 4.5-5. Operable
temperatures are from about room temperature to no higher than 100°C at atmospheric
pressure, preferably about 50°C to about 90°C. Temperatures as high as 90°C actually
improve the complexation of metals with the chelating agent.
[0025] Levels of chelating agent from about 1 to 10 kg per tonne (2 to about 20 pounds per
ton) of pulp are typical in the pulp and paper industry for enhancing peroxide bleaching
systems. The actual amount used will depend upon the level of metals present; the
amount of chelating agent being that amount effective for chelating sufficient metals
in order to achieve desired brightness and avoid undesirable peroxide decomposition.
The metal content of the pulp is typically determined by sampling the pulp and determining
its metal content by atomic adsorption. Chelates complex metals on a one-to-one molar
basis.
[0026] Preferably the pulp is pretreated with ED3A and then washed so that the complexed
metals are washed out of the system. A residence time of at least thirty minutes is
needed at this stage to allow the chelates to complex the metals present and subsequently
be washed. However, the chelate can be added to the pulp prior to bleaching (generally
at pH's of 7-9) but without subsequent washing, or can be added directly to the bleaching
process (generally pH's of 10-11), although these methods are generally less effective.
[0027] The efficiency of ethylenediaminetriacetic acid was compared along with EDTANa
4 and DTPANa
5 and no chelate in extraction of metals from two types of pulp, namely, sulfite, magnesium
base 2nd stage unbleached supplied by Wausau Paper, and a mechanical pulp, Aspen Stone
Ground Wood (SGW). The second part of the experiment was carried out to ascertain
whether there was any enhancement on brightness in peroxide bleaching on the pulp
in using chelate extraction.
Method Used for Chelate Extraction
[0028] Five grams of oven dried (OD) pulp is weighed up into a 600 ml beaker with a stirring
bar and chelate is added at the rate of 1:1 or 2:1 mole ratio of chelate to total
metal content defined as iron, manganese and copper (Fe, Mn, Cu).
[0029] Distilled water is added to the 500 ml mark, (1% consistency pulp). The pH of the
extraction slurry was 4.5 to 5.0. The sample was stirred for 1/2 hour at room temperature
and then was filtered through a Buchner funnel lined with a #4 Whatman filter paper.
[0030] The wet weight of the pulp pad was recorded to be used later in reconstituting to
10% consistency. This procedure was repeated for all the chelates that where evaluated.
Method Used for Hydrogen Peroxide Bleaching
[0031] Bleaching was carried out in zip lock bags in a water bath set at 70° C. for two
hours. A bleach liquor was made up of 2.2% NaOH as 100% based on 5 gm OD pulp, 3%
sodium silicate as 100% on 5 g OD pulp, 1% hydrogen peroxide as 100% on 5 gm OD pulp,
and water was added to make the pulp 10% consistency. The pH before bleaching was
10.5. The air was squeezed out of the bag and inserted in a water bath for 2 hours.
After the two hours in the water bath, the bleached pulp was transferred to a 600
ml beaker and the pulp was diluted to 1% consistency, the sample was mixed and the
pH was recorded. The pH was then adjusted with sulfuric acid mixed and filtered, using
a Buchner funnel with a #4 Whatman paper. The filtrate was saved for residual peroxide
titration with sodium thiosulfate and starch indicator. The pulp pad was pressed between
four absorbent pads at 6,89 · 10
6 N/m
2 (1000 psi) for one minute, then oven dried at 100°C for 1/2 hour. The pad was cooled
to room temperature and five brightness readings were taken from both sides and then
averaged.
Initial pulp analysis |
|
2nd stage unbleached |
Aspen stone ground wood |
Consistency |
36.8% |
3.6% |
Iron, ppm |
12.5 |
26.1 |
Manganese, ppm |
4.3 |
62.4 |
Copper, ppm |
0.4 |
1.3 |
Stock solutions used:
[0032]
- EDTA Na4:
- 1.1292g @ 39.5% activity, diluted to 100 mls (primary solution) then 5 mls of primary
solution diluted to 100 mls, to be used as the working solution for the experiments.
(0.565 mg EDTANa4 per ml)
- DTPA Na5:
- 1.1865g @ 41.4% activity, diluted to 100 mls (primary solution) then 5 mls of primary
solution diluted to 100 mls, to be used as the working solution for the experiments.
(0.593 mg DTPANa5 per ml)
- ED3A:
- 1.0874g @ 35% activity, diluted to 100 mls (primary solution) then 5 mls of primary
solution diluted to 100 mls, to be used as the working solution for the experiments.
(0.544 mg ED3A per ml)
- NaOH 2% :
- 8 gm of 50% diluted to 200 mls. (20.0 mg of NaOH (as 100%) per ml.)
- Hydrogen Peroxide 3%:
- 10 mls of 50% peroxide diluted to 200 mls. (30.9 mg peroxide as 100% per ml.)
- Sodium Silicate 4.51%:
- 9.02 gm of sodium silicate (41 baume) diluted to 200 mls. (45.1 mg sodium silicate
per ml.)
EXAMPLE 1
EDTANa4 (1:1) mole ratio to total Fe, Mn, Cu
Extraction:
[0033]
- pulp:
- 2nd stage (13.6 g as is) 5.0g OD
- chelate:
- 2.65 mls of working solution
- water:
- to 500 mls
Bleaching:
[0034]
- NaOH:
- 5.5 mls of working solution
- Silicate:
- 3.33 mls of working solution
- Peroxide:
- 1.62 mls of working solution
Results:
[0035]
- brightness:
- 73.5
- residual:
- 0.5% as 100%
- gain:
- 8.0 points over no chelate extraction, with bleaching
EXAMPLE 2
EDTANa4 (2:1) mole ratio to total Fe, Mn, Cu
Extraction:
[0036]
- pulp:
- 2nd stage (13.6 g as is) 5.0g OD
- chelate:
- 5.30 mls of working solution
- water:
- to 500 mls
Bleaching:
[0037]
- NaOH:
- 5.5 mls of working solution
- Silicate:
- 3.33 mls of working solution
- Peroxide:
- 1.62 mls of working solution
Results:
[0038]
- brightness:
- 73.0
- residual:
- 0.6% as 100%
- gain:
- 7.6 points over no chelate extraction, with bleaching
EXAMPLE 3
DTPANa5 (1:1) mole ratio to total Fe, Mn, Cu
Extraction:
[0039]
- pulp:
- 2nd stage (13.6 g as is) 5.0g OD
- chelate:
- 3.2 mls of working solution
- water:
- to 500 mls
Bleaching:
[0040]
- NaOH:
- 5.5 mls of working solution
- Silicate:
- 3.33 mls of working solution
- Peroxide:
- 1.62 mls of working solution
Results:
[0041]
- brightness:
- 74.4
- residual:
- 0.6% as 100%
- gain:
- 8.9 points over no chelate extraction, with bleaching
EXAMPLE 4
DTPANa5 (2:1) mole ratio to total Fe, Mn, Cu
Extraction:
[0042]
- pulp:
- 2nd stage (13.6 g as is) 5.0g OD
- chelate:
- 6.4 mls of working solution
- water:
- to 500 mls
Bleaching:
[0043]
- NaOH:
- 5.5 mls of working solution
- Silicate:
- 3.33 mls of working solution
- Peroxide:
- 1.62 mls of working solution
Results:
[0044]
- brightness:
- 73.7
- residual:
- 0.6% as 100%
- gain:
- 8.3 points over no chelate extraction, with bleaching
EXAMPLE 5
ED3A (1:1) mole ratio to total Fe, Mn, Cu
Extraction:
[0045]
- pulp:
- 2nd stage (13.6 g as is) 5.0g OD
- chelate:
- 2.39 mls of working solution
- water:
- to 500 mls
Bleaching:
[0046]
- NaOH:
- 5.5 mls of working solution
- Silicate:
- 3.33 mls of working solution
- Peroxide:
- 1.62 mls of working solution
Results:
[0047]
- brightness:
- 75.4
- residual:
- 0.6% as 100%
- gain:
- 9.9 points over no chelate extraction, with bleaching
EXAMPLE 6
ED3A (2:1) mole ratio to total Fe, Mn, Cu
Extraction:
[0048]
- pulp:
- 2nd stage (13.6 g as is) 5.0g OD
- chelate:
- 4.78 mls of working solution
- water:
- to 500 mls
Bleaching:
[0049]
- NaOH:
- 5.5 mls of working solution
- Silicate:
- 3.33 mls of working solution
- Peroxide:
- 1.62 mls of working solution
Results:
[0050]
- brightness:
- 74.3
- residual:
- 0.6% as 100%
- gain:
- 8.9 points over no chelate extraction, with bleaching
EXAMPLE 7
Blank, no chelate
Extraction:
[0051]
- pulp:
- 2nd stage (13.6 g as is) 5.0g OD
- chelate:
- none
- water:
- to 500 mls
Bleaching:
[0052]
- NaOH:
- 5.5 mls of working solution
- Silicate:
- 3.33 mls of working solution
- Peroxide:
- 1.62 mls of working solution
Results:
[0053]
- brightness:
- 65.4
- residual:
- 0.6% as 100%
- gain:
- 0
[0054] The brightness readings are graphed on Figure 1. The use of 2:1 mole ratio of chelate
to total metal (Fe, Mn, Cu) had no significant gains in brightness, compared to the
use of a 1:1 mole ratio. ED
3A brightness gain was 9.9 points over a no chelate treatment extraction of pulp, and
also showed an increase of 1.9 points over EDTANa
4 and 1.0 point increase in brightness over DTPANa
5.
[0055] The next set of experiments utilized a higher manganese pulp, aspen stone ground
wood. The same conditions used in the previous examples were used, except that the
% NaOH was increased to 2.6% instead of 2.2%, in order to achieve a higher initial
pH for bleaching.
EXAMPLE 8
EDTA Na4 (1:1) mole ratio to total Fe, Mn, Cu
Extraction:
[0056]
- pulp:
- Aspen SGW (137.4 g as is) 5.0g OD
- chelate:
- 14.3 mls of working solution
- water:
- to 500 mls
Bleaching:
[0057]
- NaOH:
- 6.5 mls of working solution
- Silicate:
- 3.33 mls of working solution
- Peroxide:
- 1.62 mls of working solution
Results:
[0058]
- brightness:
- 67.8
- residual:
- 0.2% as 100%
- gain:
- 15 points over no chelate extraction, without bleaching
EXAMPLE 9
DTPA Na5 (1:1) mole ratio to total Fe, Mn, Cu
Extraction:
[0059]
- pulp:
- Aspen SGW (137.4 g as is) 5.0g OD
- chelate:
- 17.2 mls of working solution
- water:
- to 500 mls
Bleaching:
[0060]
- NaOH:
- 6.5 mls of working solution
- Silicate:
- 3.33 mls of working solution
- Peroxide:
- 1.62 mls of working solution
Results:
[0061]
- brightness:
- 69.2
- residual:
- 0.1% as 100%
- gain:
- 16.8 points over no chelate extraction, without bleaching
EXAMPLE 10
ED3A (1:1) mole ratio to total Fe, Mn, Cu
Extraction:
[0062]
- pulp:
- Aspen SGW (137.4 g as is) 5.0g OD
- chelate:
- 12.9 mls of working solution
- water:
- to 500 mls
Bleaching:
[0063]
- NaOH:
- 6.5 mls of working solution
- Silicate:
- 3.33 mls of working solution
- Peroxide:
- 1.62 mls of working solution
Results:
[0064]
- brightness:
- 68.9
- residual:
- 0.1% as 100%
- gain:
- 16 points over no chelate extraction, without bleaching
EXAMPLE 11
ED3A (1.25:1) mole ratio to total Fe, Mn, Cu
Extraction:
[0065]
- pulp:
- Aspen SGW (137.4 g as is) 5.0g OD
- chelate:
- 16.1 mls of working solution
- water:
- to 500 mls
Bleaching:
[0066]
- NaOH:
- 6.5 mls of working solution
- Silicate:
- 3.33 mls of working solution
- Peroxide:
- 1.62 mls of working solution
Results:
[0067]
- brightness:
- 69.0
- residual:
- 0.1% as 100% %
- gain:
- 16.5 points over no chelate extraction, without bleaching
EXAMPLE 12
Blank, no chelate extraction
Extraction:
[0068]
- pulp:
- Aspen SGW (137.4 g as is) 5.0g OD
- chelate:
- 0
- water:
- to 500 mls
Bleaching:
[0069]
- NaOH:
- 6.5 mls of working solution
- Silicate:
- 3.33 mls of working solution
- Peroxide:
- 1.62 mls of working solution
Results:
[0070]
- brightness:
- 66.5
- residual:
- 0.1% as 100%
- gain:
- 13.4 points over no chelate extraction, without bleaching
[0071] The brightness gains are plotted in Figure 2, and the % iron and manganese removal
is plotted in Figure 3. ED
3A used at 1:1 mole ratio to metals had a greater brightness gain than EDTANa
4 (15 points versus 16), and when used at 25% excess, was comparable to DTPANa
5. Manganese extraction with ED
3A was greater than 91%, which was fairly comparable to EDTANa
4 and DTPANa
5 at 97+%.