[0001] The invention refers to systems and procedures for processing of material without
removal of the same and involving a cross-sectional reduction. In the following, reference
will be made more in particular to a drawbench system.
[0002] In a drawbench, a metal wire is reduced in diameter by passing through one or more
consecutive die plates. The metal wire is drawn through the die plates by tensile
force applied by rollers or capstans set between the die plates, in particular after
each die plate. To ensure proper operation of the system, it is necessary for the
speeds of the capstans to be co-ordinated so that there is not too much slack between
one capstan and another, and at the same time there should not be an excessive tensile
force applied. The last capstan downstream dictates what should be the speed of the
capstan or capstans upstream. The control of speed of the capstans is generally entrusted,
in known systems, to a sensing device referred to as "dandy roll", which detects the
slack in the wire at a location between one capstan and another. The "dandy roll"
device comprises a feeler, generally a roller feeler, which is pushed against the
wire or sheet material of the drawing line (or generally reduced-cross section plastic
processing line). By detecting the variation in position of the feeler, which depends
upon the slack of the material, a correction is made in the speed of the capstan or
capstans upstream according to the variation detected. This type of regulation may
present some drawbacks; for example, an instability of correction or hunting, which
may even, in the case of wire, cause breaking of the wire. In addition, in the case
once again of wire, since the "dandy" device has limited extension across the wire,
it limits the possibility of filling the capstans, whereas it would be desirable to
have a greater width of filling of the latter for the purpose of cooling the wire.
Furthermore, the tension exerted by the action of the "dandy" on the wire itself may,
in some cases, cause a problem inherent slipping of the wire on the capstan, thus
leading to a limitation of the possibility of filling the capstan.
[0003] An aim of the present invention is to overcome these drawbacks of the prior art.
[0004] A further aim is to achieve a system for controlling speed of the capstans in a material-processing
line with reduction of cross section and without removal of material, in which there
is an improved stability and/or in which it is possible to exploit a greater filling
width of the capstans. These aims have been achieved with a control or regulation
process, as described in Claim 1, and with a system, as described in Claim 7.
[0005] Further characteristics and advantages of the invention are defined in the subsequent
claims.
[0006] In other words, according to the new process, a volume per unit time of material
undergoing processing is used as the control quantity to carry out regulation of capstan
speed. In particular, there is measured a volume of material per unit time that passes
in a given point or location upstream of a capstan, the speed of which it is intended
to control, and the volume per unit time that passes in a given point or location
upstream of a reference capstan (set downstream of the capstan being controlled),
and a comparison value or error signal thus obtained is used to regulate the rotational
speed of the controlled capstan. The regulation of the speed is obtained generally
using a feedback control loop of the PID (proportional-integral-differential) type.
[0007] An examplary embodiment of the invention will be described in the following, with
reference to the attached drawings, in which:
Figure 1 is a diagram of a drawing line or system with a regulation or control according
to the invention;
Figure 2 is a diagram of a drawing line or system with a variant to the proposed regulation.
[0008] With reference to Figure 1, a drawing line or system is designated by the generic
reference 10 and is illustrated as comprising a first die plate 12, upstream, a second
die plate 14, downstream, a first capstan 16, downstream of the first die plate, and
a second capstan 18, downstream of the second die plate. Capstan 16 is upstream of
capstan 18. A wire being formed on the drawing line is indicated by the letter F.
In particular, F' is a larger-section wire entering die plate 12, F'' is a wire with
intermediate cross-section between die plate 12 and die plate 14, and F''' is a reduced
cross-section wire downstream of die plate 14.
[0009] It is desired to regulate rotational speed of the upstream capstan 16, according
to the rotational speed of the downstream capstan 18. The capstan 16, then, is the
controlled member, and the capstan 18 the reference member.
[0010] According to the invention, at a location P
1 upstream of the capstan 16, and at a location P
2 upstream of the capstan 18 and downstream of the capstan 16, the volume per unit
time of wire F that passes through each of the said sections is monitored. Reference
31 is a measuring apparatus in P
1 , and reference 32 is a measuring apparatus in P
2. Unit volumes V
u1 measured in P
1 and V
u2 measured in P
2 are compared. Since the drawing operation takes place without removal of material,
for proper running of the system it should be
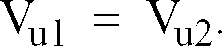
In practice, however, V
u1 is frequently different from V
u2. The comparison is used to regulate the speed of motor 22 driving the capstan 16,
preferably through a feedback loop control (not illustrated herein) of the PID type.
In the figure, reference 20 is a differential error amplifier, and reference 21 is
a driving circuit for motor 22.
[0011] The volume V
u passing per unit time in a given section may be measured in various ways. To provide
an unrestrictive example, a marking is provided at intervals along the wire, obtained
by visual means (for example, paint marks sprayed on), or electrical means, such as
magnetization. The system illustrated in Fig. 1 is particularly suited for marking
by paint-spraying, the paint being applied at a location M upstream of the die plate
12. In practice, by marking the wire F' at regular intervals upstream of the die plate
12, a marking is also obtained, at different regular intervals, of the wire F'' upstream
of the die plate 14. Counting the number of stretches of wire passing per unit time
at location P
1 and the number of stretches of wire passing per unit time at location P
2 gives the values of volume per unit time V
u1 and V
u2. Counting can be done using known means; for example, 31 and 32 may be counters of
electric pulses coming from optical (or magnetic) sensors which detect the passage
of the marks (stored in memory) on the wire.
[0012] As has been said, the system illustrated in Fig. 1 is particularly suitable when
there is a paint-type marking.
[0013] Figure 2 illustrates a system tat is particularly suited for operating with a magnetic-type
marking. In the system of Fig. 2, the same notation used in Fig. 1 for corresponding
parts has been maintained. For this reason, said parts will not be described any further.
In this case, marking is made at a location M downstream of the first die plate 12,
and the first reading of volume per unit time is made at a location P
1 downstream of the first die plate and of the marking, and upstream of the first capstan
16. The location P
2 of the second reading of unit volume is set downstream of the controlled capstan
16, i.e., upstream of the die plate 14, as in the previous drawing line.
[0014] Variants to what has been described are possible.
[0015] As far as the application of the marking and/or marking-detection devices is concerned,
it may be pointed out that it makes no difference whether they are set at the entry
point or at the exit point of the die plates, provided that they are set in the immediate
vicinity of the die plates. This possibility exists in so far as the volume of the
material coming into the die plate is exactly the same as the outgoing material.
1. A procedure for regulating the speed of rotation of a controlled capstan on the basis
of the speed of rotation of a reference capstan, in a system for the continuous plastic
processing of material by reduction of cross section, characterized in that the values
measured in the system for the regulation of the said speed consist of volumes of
material that pass per unit time at spaced locations in the system.
2. A procedure according to Claim 1, characterized in that the value of volume per unit
time is measured at a first location upstream of the controlled capstan, and the value
of volume per unit time is measured at a second location downstream of the controlled
capstan.
3. A procedure according to Claim 2, characterized in that said first location (P1) is downstream of a first piece of equipment (12) for reduction of section, and the
said second location (P2) is upstream of a second piece of equipment (14) for reduction of section.
4. A procedure according to Claim 2, characterized in that the said first location is
upstream of a first piece of equipment for reduction of section, and the said second
location is upstream of a second piece of equipment for reduction of section.
5. A procedure according to Claim 1, characterized in that the regulation of the speed
of the motor of the controlled capstan is made by means of a feed-back control loop
of the PID type.
6. A procedure according to Claim 1, characterized in that the measurement of the volume
of material per unit time that passes in a given location is made by means of marking
at intervals the moving material upstream of the said section and counting of the
marks passing per unit time at said location.
7. A system for plastic processing of material by reduction of cross section comprising
a piece of equipment (12) for reduction of section upstream, a piece of equipment
(14) for reduction of section downstream, a first drawing capstan (16) set downstream
of the first piece of equipment for reduction of section, and a second drawing capstan
(18) set downstream of the second piece of equipment for reduction of section and
of the first capstan, characterized in that it comprises two measuring apparatuses
(31, 32) for measuring volumes per unit time upstream (at location P1) and downstream (at location P2) of a said capstan (16), the speed of rotation of which is to be controlled.
8. A system according to Claim 7, characterized in that it comprises a paint-marking
device (M), and that the measuring apparatus consists of counters, the marking device
and the first measuring apparatus (31) being set upstream of the first piece of equipment
for reduction of section, the second measuring apparatus being set upstream of the
second piece of equipment for reduction of section.
9. A system according to Claim 7, characterized in that it comprises a magnetic-marking
device (M), and wherein the measuring apparatus consists of counters, the marking
device and the first counter being set downstream of the first piece of equipment
for reduction of section, the second counter being set upstream of the second piece
of equipment for reduction of section.
10. A system according to Claim 7 for a drawing line, in which the said first piece of
equipment and the said second piece of equipment are die plates.