FIELD OF THE INVENTION
[0001] The present invention relates to methods for making lithographic printing plates.
In particular, it relates to a method for directly making the lithographic printing
plates by using hydrophobic polymer latex printing, which makes it possible to produce
the lithographic plates directly from digital data output from computers, facsimiles,
or the like without using any intermediate films.
BACKGROUND OF THE INVENTION.
[0002] Digitalization of information has made a rapid progress in recent years throughout
the process from manufacturing a block copy, an upper stream process of printing,
to manufacturing a printing plate, thereby putting to practical use for example, a
photographic form system of characters, by which a block copy of manuscripts can be
readily prepared, or a scanner which directly reads picture images. With this progress,
there has arisen a demand for a direct plate-making method in which lithographic plates
can be directly prepared from digital data output from computers, facsimiles, or the
like without using a film for making printing plates.
[0003] As one example of the direct plate-making method, a method wherein an image or non-image
portion is directly formed on a substrate by ink-jet printing is known to the art.
The ink-jet printing system is a relatively rapid image output system and has a simple
construction because it does not require any complex optical system. Therefore, the
printing system makes an apparatus for making printing plates simple and the cost
for making printing plates can be reduced since the maintenance labor is largely reduced.
[0004] As examples of the methods for preparing printing plates by using the ink-jet printing
system,
Japanese Kokai Publication 113456/1981 proposes the methods for preparing printing plates wherein ink-repelling materials
(e.g. curable silicone) are printed on a printing plate by ink-let printing. The printing
plate obtained by this method is an intaglio printing plate in which the ink-repelling
material formed on the surface of the substrate serves as a non-image part. As a result,
the resolution of the printed images at shadow area or reversed lines is not so good.
Moreover, a large amount of ink is needed in this method because the ink-repelling
material must be deposited on the whole non-image part which occupies most of the
surface of the printing plate.
[0005] US-P- 5 312 654 discloses a method for making lithographic printing plates comprising: forming an
image on a substrate having an ink absorbing layer and a hydrophilized layer between
the substrate and absorbing layer by ink-jet printing using a photopolymerizable ink
composition, and exposing it to an active light in the wavelength region curing the
image. The printing endurance of said printing plates is low.
[0006] EP-A- 533 168 discloses a method for avoiding ink spreading by coating the lithographic base with
an ink absorbing layer which is removed after ink printing. This is an uneconomical
and cumbersome method.
[0007] Research Disclosure 289118 of Hay 1988 discloses a method for making printing plates with the use of an ink jet wherein
the ink is a hydrophobic polymer latex. However said printing plates have a poor ink
acceptance and a low printing endurance.
OBJECTS OF THE INVENTION
[0008] It is an object of the invention to provide a method for making lithographic printing
plates from a lithographic base having a hydrophilic surface image-wise imaged with
a hydrophobic polymer latex which yields an excellent lithographic printing plate
with a high printing endurance.
[0009] It is further an object of the present invention to provide a method for making lithographic
printing plates without a wet development of the lithographic base in a rapid , economical
and ecological way.
[0010] Further objects of the present invention will become clear from the description hereinafter.
SUMMARY OF THE INVENTION
[0011] According to the present invention there is provided a method for making a lithographic
printing plate comprising the steps of dispensing in a predetermined pattern a latex
of particles of a hydrophobic polymer onto an optionally modified hydrophilic surface
of a lithographic base, characterized in that said hydrophobic polymer and the optionally
modified hydrophilic surface of the lithographic base have mutual reactive groups.
DETAILED DESCRIPTION OF THE INVENTION
[0012] According to the present invention, the lithographic base may be an anodised aluminum
support. A particularly preferred lithographic base is an electrochemically grained
and anodised aluminum support. The anodised aluminum support may be treated to improve
the hydrophilic properties of its surface. For example, the aluminum support may be
silicated by treating its surface with sodium silicate solution at elevated temperature,
e.g. 95°C. Alternatively, a phosphate treatment may be applied which involves treating
the aluminum oxide surface with a phosphate solution that may further contain an inorganic
fluoride. Further, the aluminum oxide surface may be rinsed with a citric acid or
citrate solution. This treatment may be carried out at room temperature or may be
carried out at a slightly elevated temperature of about 30 to 50°C. A further interesting
treatment involves rinsing the aluminum oxide surface with a bicarbonate solution.
Still further, the aluminum oxide surface may be treated with polyvinylphosphonic
acid, polyvinylmethylphosphonic acid, phosphoric acid esters of polyvinyl alcohol,
polyvinylsulphonic acid, polyvinylbenzenesulphonic acid, sulphuric acid esters of
polyvinyl alcohol, and acetals of polyvinyl alcohols formed by reaction with a sulphonated
aliphatic aldehyde It is further evident that one or more of these post treatments
may be carried out alone or in combination. More detailed descriptions of these treatments
are given in
GB-A- 1 084 070, DE-A- 4 423 140, DE-A- 4 417 907, EP-A- 659 909, EP-A- 537 633, DE-A-
4 001 466, EP-A- 292 801, EP-A- 291 760 and US-P- 4 458 005.
[0013] Said anodized aluminium support has as reactive groups oxide and hydroxyl groups.
[0014] According to another mode in connection with the present invention, the lithographic
base with an optionally modified hydrophilic surface comprises a flexible support,
such as e.g. paper or plastic film, provided with a cross-linked optionally modified
hydrophilic layer. A particularly suitable cross-linked hydrophilic layer may be obtained
from a hydrophilic binder cross-linked with a cross-linking agent such as a melamine-resin,
formaldehyde, dialdehydes like glutaric dialdehyde glyoxal, polyisocyanate or a hydrolysed
tetra-alkylorthosilicate. The latter is particularly preferred.
[0015] As hydrophilic binder there may be used hydrophilic (co)polymers such as for example,
homopolymers and copolymers of vinyl alcohol with as reactive functions hydroxyl groups,
acrylamide with as reactive function an amide group, methylol acrylamide, methylol
methacrylamide, acrylic acid, methacrylic acid, hydroxyethyl acrylate, hydroxyethyl
methacrylate, all with a hydroxyl function as reactive group, maleic anhydride with
an anhydride as reactive group, maleic acid with a hydroxyl function as reactive group,
maleic anhydride/vinylmethylether copolymers anhydride with an anhydride as reactive
group. The hydrophilic binder can partially contain crosslinkable or reactive groups
e.g. silanol modified polyvinylalcohol, vinylalcohol copolymer with crosslinkable
acrylamides like N-(-methoxymethyl)-acrylamide, n-butoxymethyl acrylamide, n-butoxymethyl
methacrylamide. The hydrophilicity of the (co)polymer or (co)polymer mixture used
is preferably the same as or higher than the hydrophilicity of polyvinyl acetate hydrolyzed
to an extent of at least 60 percent by weight, preferably at least 80 percent by weight.
[0016] The amount of crosslinking agent, in particular of tetraalkyl orthosilicate, is preferably
at least 0.2 parts by weight per part by weight of hydrophilic binder, more preferably
between 0.5 and 5 parts by weight, most preferably between 1.0 parts by weight and
3 parts by weight. The amount of cross-linking agent is not so high that no hydroxyl
groups of the polyvinyl alcohol remains
[0017] A cross-linked hydrophilic layer in a lithographic base used in accordance with the
present embodiment preferably also contains substances that increase the mechanical
strength and the porosity of the layer. For this purpose colloidal silica may be used.
The colloidal silica employed may be in the form of any commercially available water-dispersion
of colloidal silica for example having an average particle size up to 40 nm, e.g.
20 nm. In addition inert particles of larger size than the colloidal silica may be
added e.g. silica prepared according to Stöber as described in J. Colloid and Interface
Sci., Vol. 26, 1968, pages 62 to 69 or alumina particles or particles having an average
diameter of at least 100 nm which are particles of titanium dioxide or other heavy
metal oxides. By incorporating these particles the surface of the cross-linked hydrophilic
layer is given a uniform rough texture consisting of microscopic hills and valleys,
which serve as storage places for water in background areas.
[0018] In a particular embodiment, the lithographic base comprises a hydrophilic binder
which comprises reactive groups selected from the group consisting of epoxides, alkoxysilanes
and reactive acrylamides which can react with hydroxyl, amino or amido functions of
the hydrophobic polymer.
[0019] The thickness of a cross-linked hydrophilic layer in a lithographic base in accordance
with this embodiment may vary in the range of 0.2 to 25 µm and is preferably 1 to
10 µm.
[0020] Particular examples of suitable cross-linked hydrophilic layers for use in accordance
with the present invention are disclosed in
EP-A- 601 240, GB-P- 1 419 512, FR-P- 2 300 354, US-P- 3 971 660, US-P- 4 284 705
and EP-A- 514 490.
[0021] As flexible support of a lithographic base in connection with the present embodiment
it is particularly preferred to use a plastic film e.g. substrated polyethylene terephthalate
film, substrated polyethylene naphthalate film, cellulose acetate film, polystyrene
film, polycarbonate film etc... The plastic film support may be opaque or transparent.
Also suitable as flexible support is glass with a thickness less than 1.2 mm and a
failure stress (under tensile stress) equal or higher than 5 x 10
7 Pa.
[0022] It is particularly preferred to use a polyester film support to which an adhesion
improving layer has been provided. Particularly suitable adhesion improving layers
for use in accordance with the present invention comprise a hydrophilic binder and
colloidal silica as disclosed in
EP-A- 619 524, EP-A- 620 502 and EP-A- 619 525. Preferably, the amount of silica in the adhesion improving layer is between 200 mg
per m
2 and 750 mg per m
2. Further, the ratio of silica to hydrophilic binder is preferably more than 1 and
the surface area of the colloidal silica is preferably at least 300 m
2 per gram, more preferably at least 500 m
2 per gram.
[0023] A latex is defined as a stable colloidal dispersion of a polymeric substance in an
aqueous medium. The polymer particles are usually approximately spherical and of typical
colloidal dimensions: particle diameters range from about 20 to 1000 nm. The dispersion
medium is usually a dilute aqueous solution containing substances such as electrolytes,
surfactants, hydrophilic polymers and initiator residues. The polymer latices are
classified in various way. By origin, they are classified as natural latices, produced
by metabolic processes occuring in the cells of certain plant species; synthetic latices,
produced by emulsion polymerization of monomers; and artificial latices, produced
by dispersing a polymer in a dispersing medium or by solvent exchange.
[0024] Preferred latices in connection with the invention are synthetic and artificial latices.
These artificial latices are rather referred to as polymer dispersions. These polymers
or oligomeric species could be dispersed in water either before their polymerization
and/or crosslinking or afterwards. The colloidal stability of the dispersion can be
improved by the addition of dispersion agents (surface-active compounds) or by ionic
groups incorporated via the monomeric species or via modification. The dispersions
of the polymers (or oligomers) can contain crosslinking agents, polymerization catalyst,
or incorporated species which can give self-crosslinking of the polymer, to obtain
sufficient mechanical strength
[0025] A hydrophobic polymer for use in the present invention has preferably a Tg below
150°C, more preferably a Tg below 120°C.
[0026] A hydrophobic polymer according to the invention is a polymer which comprises at
least one monomer with a reactive group. Examples of suitable reactive groups are
akoxysilane groups, oxazoline groups and activated carboxylic acids, e.g. carbodiimide
derivatives and preferably epoxide groups and trialkoxysilane groups. Said reactive
groups are contained in the side chain of the hydrophobic polymer. Alkoxysilane containing
monomers can contain the following polymerizable groups: acrylate, methacrylate, acrylamide,
methacrylamide, vinyl ether, styrene-derivatives.
[0027] The reactive group in the hydrophobic polymer can be introduced in the hydrophobic
polymer by copolymerization of monomers comprising said reactive groups or can be
introduced by chemical modification of said hydrophobic polymer.
[0028] Preferably said hydrophobic polymer is a copolymer containing at least a comonomer
without a reactive group.. Said hydrophobic polymer comprises a comonomer with a reactive
group in a range of 1 to 50% by weight, more preferably in a range of 3 to 30 % by
weight of the polymer.
[0029] Said hydrophobic copolymers are preferably polymers dispersed in water, prepared
by chain copolymerization of monomers like styrene, styrene derivatives, acrylates,
methacrylates, acrylamides, methacrylamides, or olefines or prepared by step polymerization
and forming polymers like polyurethanes, polyethers, polyamides, polyamic acids and
polyether imides.
[0030] Hydrophobic copolymers for use in synthetic latices according to the present invention
are, for example, polystyrene and styrenic copolymers such as styrene/butadiene/acrylic
acid copolymers, polyacrylates such as polymethyl methacrylate and polybutyl acrylate,
copolymers of butyl acrylate and methyl methacrylate, copolymers of butyl acrylate
and styrene, copolymers of butadiene and methyl methacrylate.
[0031] Hydrophobic polymers for use in artificial latices according to the present invention
are, for example polyurethanes such as the reaction product of a diisocyanate with
a hydroxyl terminated polymer or oligomer (such as polyglycol or polyester) or reaction
products of diisocyanates with amine-functional dialcohols (such as N-methyldiethanolamine,
which can be quaternized e.g. using dimethylsulphate, methyliodide or 1,4-dibromobutane).
These polymerizations are carried out in an organic solvent such as acetone, tetrahydrofurane,
The polyurethanes soluble in polar organic solvents are mixed with water, and the
organic solvent is eliminated from the aqueous-organic solutions to produce stable
polyurethane latices (e.g. as described by
D. Dieterich, Angew. Macromol. Chem., 76, 79 (1979), J. Dieterich et al., J. Oil Col. Chem. Assoc., 53, 636, (1970), V.S. Reddy, J. Diapers. Sci.Technol., 14, 417, (1993)). Stabilization of the polyurethane dispersions can also be achieved via anionic groups
such as carboxylate, sulphonate, phosphonate. Addition of a dispersion agent (surface
active compound) can give sufficient stabilization to the polyurethane latex. Diisocyanates
which could be used to produce the polyurethanes could be aliphatic or aromatic, for
example hexametylene 1,6-diisocyanate, isophorone diisocyanate, 1,6-diisocyanatotrimethylcyclohexane,
diphenylmethane 4,4'-diisocyanate, naphthalene 1,5-diisocyanate.
[0032] In order to facilitate the evaluation of the obtained lithographic plate colored
hydrophobic polymer synthetic or artificial latices can be used. For example, carbon
black or dyes or pigments can be mixed with one of the above mentioned copolymers.
Also polymer particles containing color structures in the repeating units, in particular
colored polymer particles which have obtained their color by means of a chemical reaction
based on oxidative coupling of a color coupling group in the polymer structure of
the particles with an aromatic primary amino compound, as described in
Japanese Kokai 59/30873 can be used as colored hydrophobic polymer latex.
[0033] The hydrophobic polymer synthetic or artificial latex particles have preferably a
particle size between 0.01 and 1 µm, more preferably between 0.01 µm and 0.25 µm.
[0034] The latex can contain from 1 to 70 % by weight of hydrophobic polymer, more preferably
from 2 to 40 % by weight of hydrophobic polymer, most preferably from 5 to 30 % by
weight of hydrophobic polymer.
[0035] The latex can be dispensed onto the lithographic base having a hydrophilic surface
preferably by an ink jet printer.
[0036] A volatilization preventive agent is added to the latex according to the present
invention, if necessary, to suppress evaporation of the liquid in the ink-jet nozzle
and to prevent clogging due to precipitation of the dissolved or dispersed components.
[0037] A surfactant is preferably added to the the latex used according to the present invention
to adjust the size of droplets of the latex dispersed by the ink jet nozzle, to adjust
the surface tension of the latex so that images can be formed in high resolution.
Said surfactant can be an anionic, a cationic, a nonionic or an amphoteric compound.
[0038] Other components can be further added, if necessary, to the latex used according
to the present invention. For example, heat polymerisation inhibitors, desinfectants,
anticontamination agents and anti-fungal agents can be also added. Use of buffers
and solubilizers is effective to improve the solubility or dispersibility of the polymer.
Addition of defoaming agents and foam suppressing agents are also possible to suppress
foaming of the latex in the ink-jet nozzle.
[0039] Optionally other components that enhance the latex quality can be added.
[0040] The image forming requires the following steps. On demand, microdots of the hydrophobic
polymer latex are sprayed onto the lithographic base in a predetermined pattern as
the plate passes through the printer or by a printhead shutteling over the plate.
According to one embodiment of the invention, the microdots have a diameter of about
20µm. In a following step heating may be required for the the lithographic base sprayed
with hydrophobic polymer latex. This can be done by irradiation, by convection or
by contact with a hot surface e.g.in an oven, by flash exposure, by IR-heaters or
by laser irradiation.
[0041] The image forming can also be carried out with the lithographic base already on the
printing cylinder. In that case the heating of the polymer can be effected by using
a heated printing cylinder.
[0042] The printing plate of the present invention can also be used in the printing process
as a seamless sleeve printing plate. This cylindrical printing plate has such a diameter
that it can be slided on the print cylinder. More details on sleeves are given in
"Grafisch Nieuws" ed. Keesing, 15, 1995, page 4 to 6.
[0043] The following examples illustrate the present invention without limiting it thereto.
All parts and percentages are by weight unless otherwise specified.
EXAMPLE 1
Preparation of the latices.
[0044] Seven latices were prepared all having 20% by weight in water of copolymer. Their
composition is given in table 1
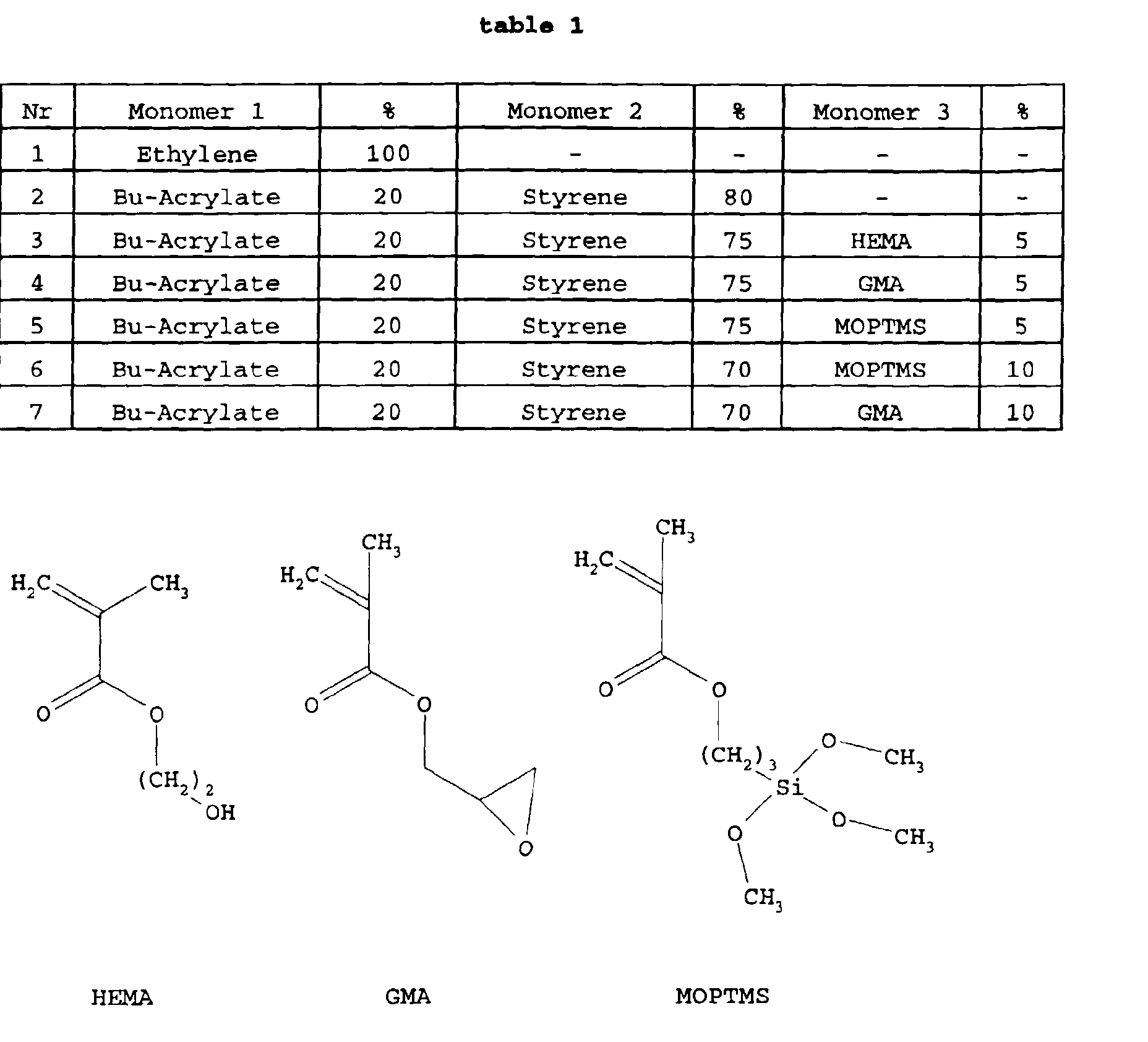
These latices were imagewise jetted on an hydrophilic support, said support being
anodized aluminum or a layer of hardened polyvinyl alcohol on polyethylene terephthalate.
These supports were prepared as follows:
Preparation of the anodized aluminum support
[0045] A 0.30 mm thick aluminum foil was degreased by immersing the foil in an aqueous solution
containing 5 g/l of sodium hydroxide at 50°C and rinsed with demineralized water.
The foil was then electrochemically grained using an alternating current in an aqueous
solution containing 4 g/l of hydrochloric acid, 4 g/l of hydroboric acid and 5 g/l
of aluminum ions at a temperature of 35°C and a current density of 1200 A/m
2 to form a surface topography with an average center-line roughness Ra of 0.5 µm.
[0046] After rinsing with demineralized water the aluminum foil was then etched with an
aqueous solution containing 300 g/l of sulfuric acid at 60°C for 180 seconds and rinsed
with demineralized water at 25°C for 30 seconds.
[0047] The foil was subsequently subjected to anodic oxidation in an aqueous solution containing
200 g/l of sulfuric acid at a temperature of 45°C, a voltage of about 10 V and a current
density of 150 A/m
2 for about 300 seconds to form an anodic oxidation film of 3.00 g/m
2 of Al
2O
3 then washed with demineralized water, posttreated with a solution containing polyvinylphosphonic
acid and subsequently with a solution containing aluminum trichloride, rinsed with
demineralized water at 20°C during 120 seconds and dried.
Preparation of a layer of hardened polyvinyl alcohol on polyethylene terephthalate
Preparation of the solution for the subbing layer.
[0048] To a solution of 11.4 g of gelatine (viscosity : 19-21 mPas) in 940 ml of water was
added 31.7 ml (11.4 g solid product) KIESELSOL 300 F (tradename for 30 % aqueous dispersion
of colloidal silica - surface area of 300 m
2 per g). Anionic wetting agents ( 0.6 g ) and biocides (1 g ) were added.
Preparation of the hydrophilic layer.
[0049] To 440 g of a dispersion containing 21.5 % TiO
2 (average particle size 0.3 to 0.5 µm) and 2.5 % polyvinyl alcohol in deionized water
were subsequently added, while stirring, 250 g of a 5 % polyvinyl alcohol solution
in water, 105 g of a hydrolyzed 22 % tetramethyl orthosilicate emulsion in water and
22 g of a 10 % solution of a wetting agent. To this mixture was then added 183g of
deionized water and the pH was adjusted to pH=4.
Preparation of the hydrophilic support
[0050] To a polyethylene terephthalate support,coated with a primer containing 170 mg/m
2 of a latex of copoly(vinylidenechloride/ methyl methacrylate/ icatonic acid) and
40 mg/m
2 of silica with a surface area of 100 m
2/g was applied the above described solution for the subbing layer at a solids coverage
of 750 mg/m
2. On top of the, subbing layer was coated the above mentioned hydrophilic layer to
a wet coating thickness of 50 g/m
2, dried at 30°C and subsequently hardened by subjecting it to a temperature of 60°C
for 1 week.
[0051] On one of those supports a sample was imaged with latex composition 1-7 and dried
at room temperature. In some cases the printing plate is afterwards treated in an
oven at 60°C for 30 minutes and then cooled to room temperature. The printing plates
are applied on a AB-Dick 360 printing press and printed with conventional ink (Van
Son rubberbase) and a commercial fountain (2% Tame). The printing results are given
in table 2.
Table 2
Nr |
Latex(table 1) |
support |
Heating temperature |
Endurance |
1 |
1 |
PTT |
22°C |
- |
2 |
1 |
PTT |
60°C |
- |
3 |
2 |
PTT |
22°C |
-- |
4 |
2 |
PTT |
60°C |
0 |
5 |
2 |
ALU |
22°C |
-- |
6 |
2 |
ALU |
60°C |
0 |
7 |
3 |
PTT |
22°C |
- |
8 |
3 |
PTT |
60°C |
0 |
9 |
3 |
ALU |
22°C |
-- |
10 |
3 |
ALU |
60°C |
- |
11 |
4 |
ALU |
60°C |
++ |
12 |
5 |
PTT |
22°C |
++ |
13 |
5 |
ALU |
22°C |
++ |
14 |
5 |
ALU |
60°C |
++ |
15 |
6 |
PTT |
60°C |
++ |
16 |
6 |
ALU |
22°C |
++ |
17 |
6 |
ALU |
60°C |
++ |
18 |
7 |
ALU |
60°C |
++ |
-Support:Alu (anodized aluminum) or PTT (polyvinyl alcohol hardened layer: Polyvinyl
alcohol-Titane dioxide- Tetramethyl orthosilicate)
-Endurance
-- very poor
- poor
0 moderate
+ good
++ very good.
It is seen from the results in table 2 that the latices with a hydrophobic polymer
containing groups which can react with the hydrophilic surface of the lithographic
base all give a printing plate with very good printing endurance , independent from
the fact if the support is anodized aluminum or a polyvinyl alcohol hardened layer
and independent from the fact if the printing plate is warmed in an oven or not.
1. A method for making a lithographic printing plate comprising the steps of dispensing
in a predetermined pattern a latex of particles of a hydrophobic polymer onto an optionally
modified hydrophilic surface of a lithographic base, characterized in that said hydrophobic
polymer and the optionally modified hydrophilic surface of the lithographic base have
mutual reactive groups.
2. A method according to claim 1 wherein said hydrophobic polymer comprises a reactive
function selected from the group consisting of epoxides, alkoxy silanes, reactive
acrylamides, oxazoline groups and activated carboxylic acids
3. A method according to claim 1 or 2 wherein said hydrophobic polymer is a polymer dispersed
in water, prepared by chain polymerization of monomers like styrene, styrene derivatives,
acrylates, methacrylates, acrylamides, methacrylamides, or olefines or prepared by
step polymerization and forming polymers like polyurethanes, polyethers, polyamides,
polyamic acids and polyether imides.
4. A method according to any of claims 1 to 3 wherein the lithographic base comprises
a hydrophilic binder which comprises reactive groups, selected from the group consisting
of epoxides, alkoxysilanes, reactive acrylamides, oxazolines and activated carboxylic
azcids.
5. A method according to any of claims 1 to 4 wherein the reactive groups are introduced
in the hydrophobic polymer by copolymerization of monomers comprising said reactive
group or are introduced by chemical modification of the polymer.
6. A method according to any of claims 1 to 5 wherein said hydrophobic polymer comprises
at least one comonomer without a reactive group.
7. A method according to any of claims 1 to 6 wherein said hydrophobic polymer comprises
a comonomer with a reactive group in a range of 1 to 50% by weight of the polymer.
8. A method according to any of claims 1 to 7 wherein the hydrophobic polymer has a Tg
below 150°C.
9. A method according to any of claims 1 to 8 wherein the lithographic base having a
hydrophilic surface is an anodized aluminum support or a flexible support provided
with a cross-linked hydrophilic layer.
10. A method according to any of claims 1 to 9 wherein said latex is dispersed by an ink
jet printer.