[0001] This invention relates to lyocell bleaching, particularly to the bleaching of non-fibrillating
lyocell with oxygen bleach.
[0002] Environmentally friedly, lyocell is a cellulosic fibre produced from the wood pulp
of trees grown specifically for that purpose. It is processed using an aqueous organic
solvent spinning technique in which the solvent is recycled, reducing environmental
effluents. Solvent spinning means dissolving and extruding directly into fibre without
the formation of a derivative. According to patents published by Courtaulds the solvent
may comprise N-methylmorpholine N-oxide.
[0003] Through abrasive action in a wet state, micro-fibrils can develop on the surface
of untreated Lyocell fibre and, critically, remain attached to it. The development
of micro-fibrils, known as fibre fibrillation, is one of the most important characteristics
or physical properties of Lyocell. The control and manipulation of Lyocell fibre fibrillation
can lead to a wide range of fabric aesthetics. Control and manipulation may range
from eliminating any occurrence of fibrillation to fostering its development to give
what is often described as a 'peach skin' feel or handle. Alternatively, eliminating
fibrillation will produce classically smooth fabrics.
[0004] All classes of dye used for cellulosic fabrics are applicable to Lyocell. These may
be applied using any of the normal dyeing techniques, e.g. jet, winch, beam, pad-batch.
According to Courtaulds's literature, where fibrillation control is necessary, detailed
advice should be sought. The same caution is applied to garment dyeing and washing.
[0005] A cross-linking resin finish will be necessary for classically clean (i.e. non-fibrillated)
fabrics. The use of such a cross linking resin is also recommended to maintain their
clean surfaces during domestic washing.
[0006] Lyocell fibre can be blended with other fibres to enhance yarn and fabric characteristics
in terms of performance and aesthetics. For example, the stress-strain characteristics
of Lyocell yield strength in cotton-blend yarns at all blend levels, while the resulting
fabrics benefit from increased softness.
[0007] Because of the need to control fibrillation, especially if a bleaching process is
to be used for a classically smooth non-fibrillating fabric, a variety of technologies
have been developed for treating the wet fibres during their original production to
make them less fibrillating. Among such treatments may be mentioned cross linking
for example using the processes described in US 5310424 or US 5779737. The use of
cross linker free processes, such as that described in US 5759210, is also possible.
A particularly preferred cross linker is 1,3,5-triacryloylhexahydo-1,3,5-triazine
(TAHT) which, according to US 5779737 is applied to the never dried lyocell fibre
in a continuous process as an aqueous solution which also contains an inorganic alkali,
preferably trisodium orthophosphate. The pH of the aqueous solution lies in the range
11-14 and the cross linking is achieved by heating to about 80-100°C for up to 2 minutes.
Samples of a fabric containing a fibre referred to by Courtaulds as Lyocell A100 have
been subjected to bleaching experiments to see whether its non-fibrillating properties
imported by the cross-linking can be retained by the use of a novel gentle oxygen
bleaching process.
[0008] If the bleaching conditions are too severe then the cross links can be broken. A
loss of 10-15% TAHT can be tolerated before the fibrillation protection system is
compromised. A nitrogen ring is present and measuring nitrogen levels gives an idea
of the protection. The propensity of the A100 to fibrillate is measured by performing
domestic consumer washes at 40°C. The fabric is washed using a normal commercial machine
and tumble dried. The surface is checked after 1, 3, and 5 washes for surface hairs.
At the end of the 5 washes ideally there should be no hairs on the surface. Dark shades
are a problem as hairs are more easily visible.
[0009] According to the present invention there is provided a process for the oxygen bleaching
of lyocell which has been cross linked with a nitrogen containing compound to reduce
the tendency of the lyocell to fibrillate characterised in that the oxygen bleach
comprises peracetic acid or its anion. Advantageously the oxygen bleach comprises
a major part of hydrogen peroxide and a minor part of peracetic acid or its anion
as this combines the strong oxidising capability of peracetic acid with the ability
to produce good bleaching under alkaline conditions. The peracetic acid or anion is
preferably generated by the reaction of an acetyl donating bleach activator with excess
hydrogen peroxide as this provides an easy and safe way to produce this bleaching
species either
in situ or in a nearby reaction vessel. Most preferably the bleach activator is tetraacetylethylene
diamine (TAED).
[0010] Non fibrillating Lyocell has the propensity to fibrillate if the fibre is peroxide
bleached under conditions of high alkalinity, high temperatures and long residence
times. This can be avoided through the use of TAED which enhances the performance
of peroxide in a bleach bath under mild bleaching conditions. This is achieved as
the reaction of TAED with peroxide delivers a stronger oxidising agent which is a
highly effective bleaching agent at low temperatures. The use of TAED in the bleaching
of non-fibrillating lyocell leads to improved whiteness whilst maintaining the integrity
of the fibrillation protection system. TAED provides effective bleaching, via the
production of the peracetic anion, at temperatures and residence times for which peroxide
alone would be ineffective. One mole of TAED reacts with two moles ofthe per hydroxyl
anion to form two moles of peracetic anion and one mole of DAED (Di Acetyl Ethylene
Diamine). Both TAED and the reaction product DAED are non toxic, non sensitising and
biodegrade to give carbon dioxide, water, nitrate and ammonia as end products.
[0011] It is the peracetic anion which gives better low temperature bleaching performance
and biocidal activity than use of hydrogen peroxide alone. Under alkaline conditions,
the rate of peracid release is rapid and increases with increasing temperature and
pH. Increasing the concentration of peroxide in the system also increases the rate
of formation of peracetic anion in solution Under alkaline conditions, it is advantageous
to use an excess of peroxide over TAED to ensure sufficient peroxide is available
to force the reaction to completion
[0012] To obtain the mild conditions which give the optimum bleaching with least removal
of the fibrillation protection system it is advantageous if the pH of the bleaching
process is ramped from near neutral to an alkalinity in the range about 8.5 to about
12, preferably about 9.5 to about 10.5 by adding alkali approximately 15-30 minutes
after the addition of the TAED. The alkali is conveniently sodium hydroxide.
[0013] To further increase the mildness of the bleaching conditions at least in the case
where the TAED and hydrogen peroxide are reacted
in situ it is desirable that the fabric is initially contacted with the bleach at a temperature
of less than 50°C and the temperature is raised to about 70°Cor greater before addition
of alkali.
[0014] The invention also comprises the use of peracetic acid or its anion generated by
the reaction of TAED and hydrogen peroxide in the bleaching of Lyocell, preferably
non-fibrillating Lyocell. Such non-fibrillating lyocell may have been formed by treatment
of the undried fibre with a cross-linker selected from the group comprising chemical
reagents bearing a plurality of acrylamido groups, the average number of acrylamido
groups per molecule ofthe chemical reagent in the solution being greater than 2.1.
A particularly preferred cross-linker is 1,3,5- triacryloylhexahydo-1,3,5-triazine.
[0015] It will be understood that in addition to the bleach activator, the hydrogen peroxide
and their reaction products the bleach bath may also contain such other chemicals
as are commonly used in the bleaching of fibres and fabrics. Among these chemicals
there may be mentioned: wetting agents, peroxide stabilisers, pH adjusters and buffers
and optical brightening additives.
[0016] Bleach activators may be selected from tetraacetyl ethylenediamine, tetraacetyl glycoluril,
pentaacetyl glucose, sodium nonanoyloxybenzene sulphonate, sodium lauroyloxybenzene
sulphonate, acetyl triethyl citrate and other bleach activators known to those in
the art, however TAED is preferred because of its good peracid release and its environmental
and toxicological benefits.
[0017] Wetting agents may be selected from alkylbenzenesulphonic acids, anionic preparations
of fatty alcohol adducts, alcohol ethoxylates and other wetting agents known to those
skilled in the art of textile bleaching
[0018] Stabilisers may be elected from silicates, phosphates and sequestrants, for example
Diethylenetriaminepentamethylenephosphonic acid, sodium salt (DTPMP) and organic esters,
blends of sodium carboxylate and gluconate, alcohol polyglycol ether, anionic and
other stabilisers known to those skilled in the art of textile bleaching.
[0019] Buffers and pH adjusters may be selected from, sodium sulphate, soda ash, sodium
hydroxide and potassium hydroxide, phosphates and other buffers and pH adjusters known
to those skilled in the art of textile bleaching.
[0020] OBAs may be selected from any which are stable in the presence in the presence of
strong oxidising species for example anionic stilbene derivatives and distyryl biphenyl
derivatives. The invention will now be described by way of the following non limiting
examples:
[0021] The use of TAED to bleach lyocell which had been treated with a protection system
to render it substantially non-fibrillating has been assessed. It is believed that
the treatment comprised the cross linking of the fibre while still in the wet state
by use of TAHT. The fabrics to be bleached were obtained from Courtaulds fibres and
were named Lyocell A100. Careful control of wet processing is required to ensure that
the integrity ofthe fibrillation protection system is not compromised during processing
Samples of jersey Lyocell A100 and Lyocell A100/Lycra blend (90/10) were exhaust bleached.
[0022] Table 1 shows the formulation used for bleaching. TAED was used in granulated form.
Hydrogen peroxide was used at 50% w/w. Soda ash was used to give a mildly alkaline
pH and the pH was increased with the sodium hydroxide. DTPMP is Diethylenetriaminepentamethylenephosphonic
acid, sodium salt which is a sequestrant added to prevent metal ions from catalysing
decomposition of the bleach.

Test Method for Fibrillation Index
[0023] The following method is given in US 531 0424 and was used to assess Fibrillation
Index (F.I.). A series of samples of fibre having nil and increasing amounts of fibrillation
was identified. A standard length of fibre from each sample was then measured and
the number of Fibrils (fine hairy spurs extending from the main body of the fibre)
along the standard length was counted. The length of each fibril was measured, and
an arbitrary number, being the product of the number of fibrils multiplied by the
average length of each fibril, was determined for each fibre.
[0024] The fibre exhibiting the highest value of this product was identified as being the
most fibrillated fibre and was assigned an arbitrary Fibrillation Index of 10. The
wholly non-fibrillated fibre was assigned a Fibrillation Index of zero, and the remaining
fibres were evenly ranged from 0 to 10 based on the microscopically measured arbitrary
numbers.
[0025] The measured fibres were then used to form a standard graded scale. To determine
the Fibrillation Index for any other sample offibre, five or ten fibres were visually
compared under the microscope with the standard graded fibres. The visually determined
numbers for each fibre were then averaged to give a Fibrillation Index for the sample
under test.
Processing
[0026] Batch bleaching experiments were undertaken using a laboratory wash wheel at a 10:1
liquor : goods ratio. The low temperature (70°C) bleaching process using TAED activated
peroxide involved the use of a pH ramp system during the bleaching stage. The pH ramped
bleaching system has been designed to minimise exposure of the fibres to high alkalinity
during bleaching. It is preferred to keep the pH below 10.5.
[0027] peroxide controls were undertaken at 70°C for comparative purposes at constant pH
11.
[0028] The TAED process involved increasing the temperature to 70°C over a period of 5 to
10 minutes and then bleaching at 70°C with a pH ramp midway during the bleaching sequence.
Initially the fabric and chemicals were added to produce alkaline conditions (pH 10).
The pH of the bleach batch decreased rapidly to pH 7 as the peracid was generated
from TAED. After 20 minutes the alkalinity was adjusted with sodium hydroxide. Fabric
was then bleached for a further 20 minutes. The total bleach time (excluding draining
and rinsing) was therefore about 40 minutes. After air drying, the whiteness of the
bleached samples was determined as CIE Whiteness using a Spectroflash Spectrophotometer
(D65 illumination). Final pH measurements were recorded.
Example 1 - Bleaching of Non-fibrillating Lyocell A100 & Lyocell A100 Blends
[0029] Bleaching experiments were performed on both 100% non-fibrillating Lyocell A100 and
a 90% Lyocell A100 with 10% Lycra blend. The objective was to attain target whiteness
of about 72 CIE Whiteness without compromising the fibrillation protection system.
Results for the peroxide controls are given in Table 2 and show that the target whiteness
has not been attained using a 70°C process at pH 11. This would give rise to problems
with base colour and variability of fibrillation performance. These problems could
not be overcome by raising the temperature or otherwise increasing the exposure to
hydrogen peroxide as this would give increased loss of fibrillation protection and
consequential increased fibrillation
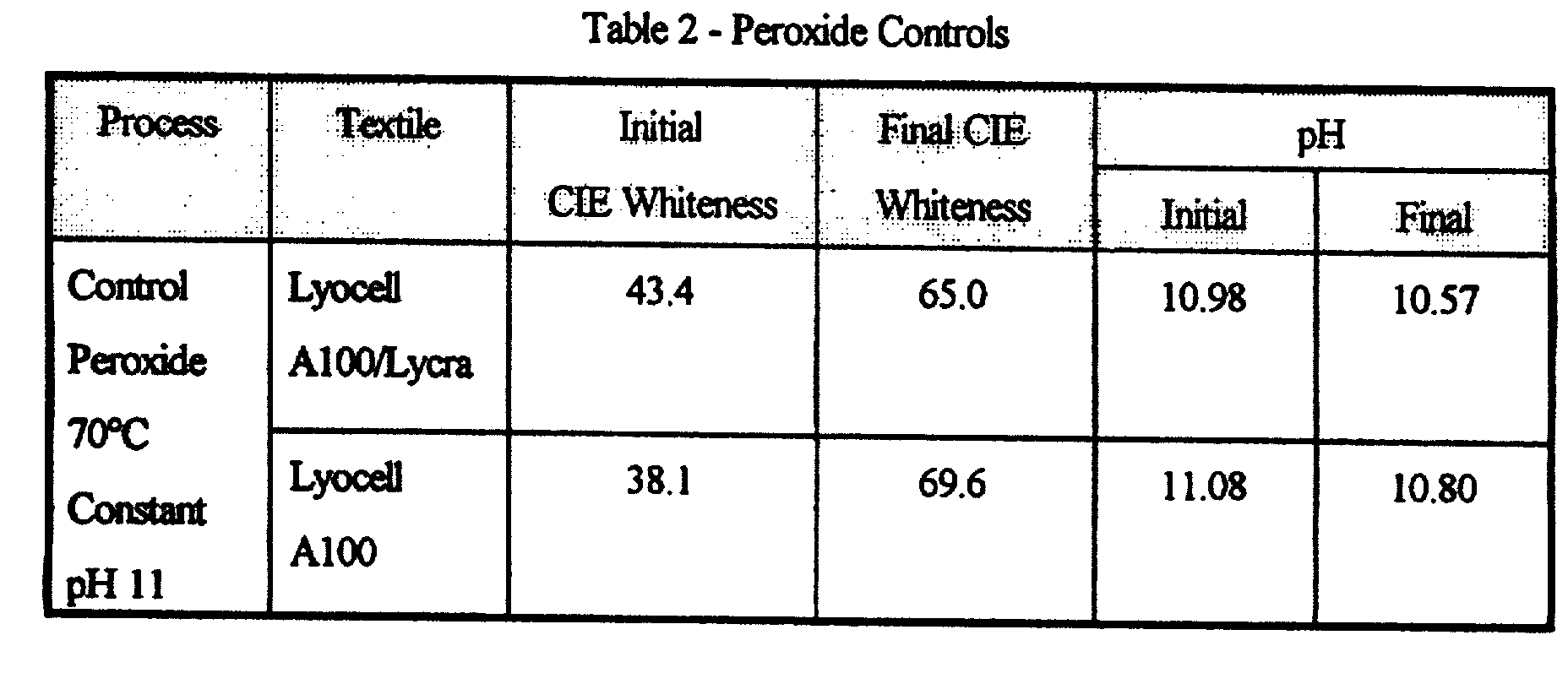
[0030] The inclusion of TAED into the bleach bath significantly increases the brightness
over that which could be attained by peroxide alone, as can be seen from Table 3.
A whiteness improvement of 5-7 units was achieved by activating the peroxide using
TAED. Table 3 also illustrates the effect of changing the alkalinity of the TAED bleaching
process for non fibrillating Lyocell A100 and Lyocell A100/Lycra blend. It seems that
the optimum pH for adjustment at the ramp stage is pH 10.5 for both Lyocell A100 and
Lyocell A100 blended with Lycra. Increasing the pH above 10.5 reduces the final whiteness.
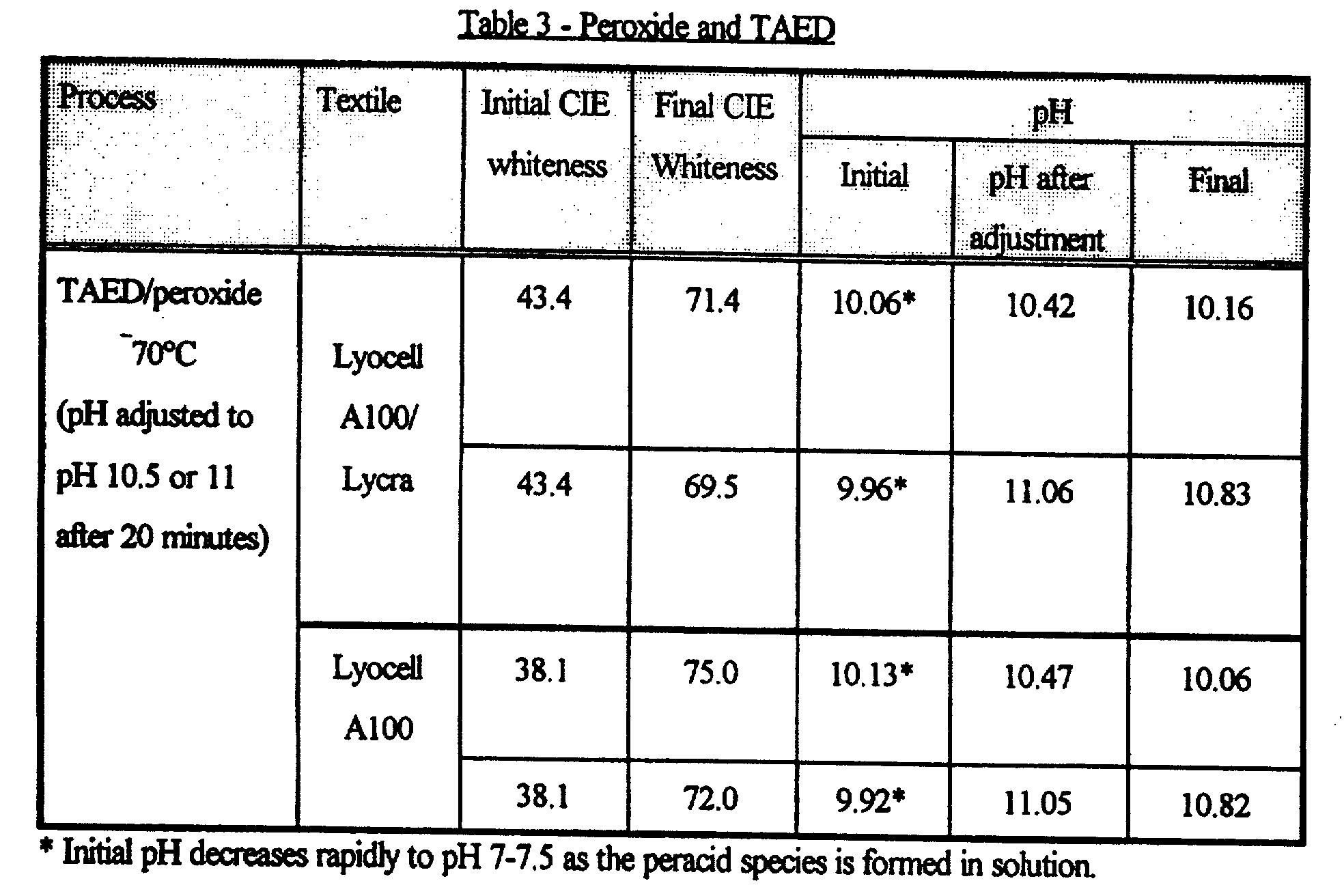
Example 2 - Effect of TAED and peroxide bleaching on fibrillation protection system
[0031] The TAED and Peroxide 70°C tests from example 2 were repeated for both the 100% non-fibrillating
lyocell and the non-fibrillating lyocell/lycra blend using the optimum adjustment
pH of 10.5.
[0032] In this example the CIE Whiteness was measured using a Macbeth reflectance spectrophotometer.
The CIE whiteness values obtained using this equipment tend to be lower than the values
obtained using the Spectroflash equipment used in example 1.
[0033] Washability was determined by measuring the fibrillation index (F.I.) according to
the test method described above after 5 x 40°C wash tumble cycles in a commercial
washing machine.
[0034] The loss of cross-link fibrillation protection system was determined by measuring
nitrogen content by Kjeldahl, a loss of 10% or less is regarded as acceptable.
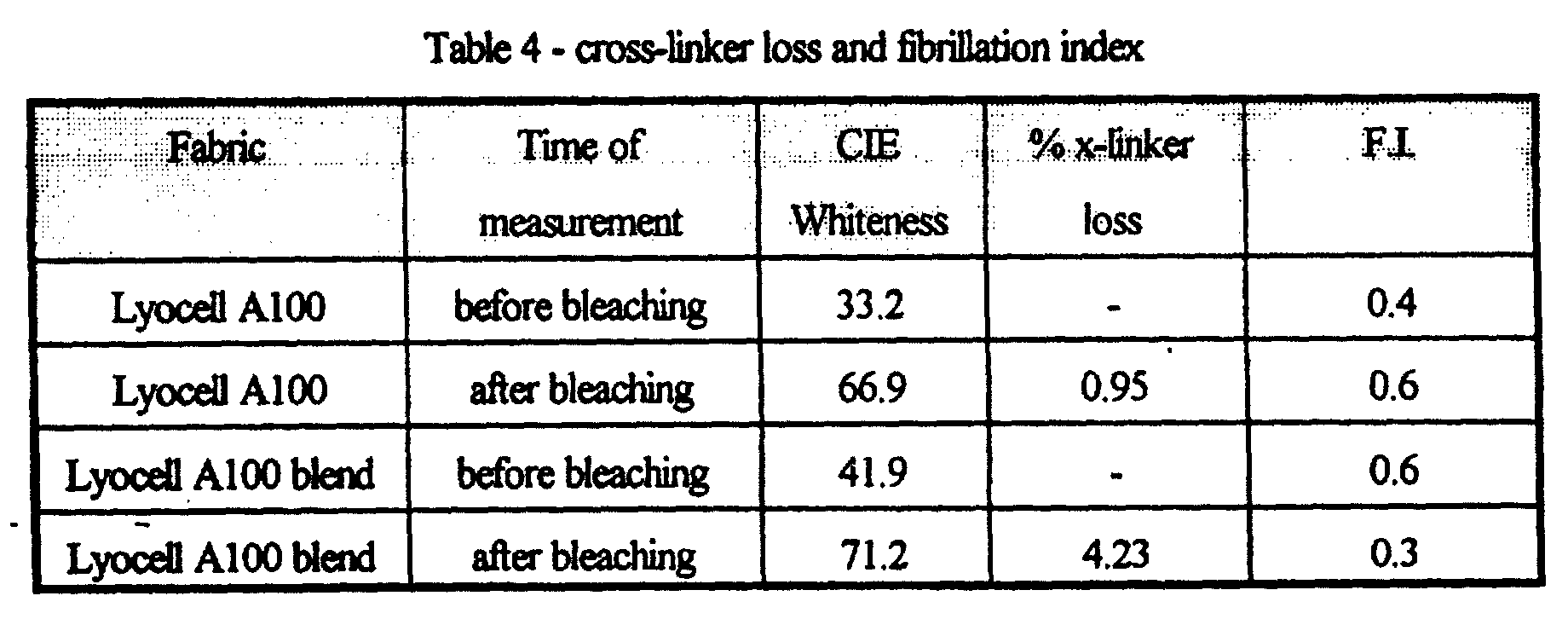
[0035] These results compare favourably with a control peroxide bleaching recipe which achieves
a whiteness of about 65 with a cross-linker loss up to 12% and a fibrillation index
of about 1.5.
1. A process for the oxygen bleaching of lyocell which has been cross linked with a nitrogen
containing compound to reduce the tendency of the lyocell to fibrillate characterised
in that the oxygen bleach comprises peracetic acid or its anion.
2. A process according to claim 1 in which the oxygen bleach comprises a major part of
hydrogen peroxide and a minor part of peracetic acid or its anion.
3. A process according to claim 2 in which the peracetic add or salt thereof is generated
by the reaction of an acetyl donating bleach activator with excess hydrogen peroxide.
4. A process according to claim 3 in which the bleach activator is TAED.
5. A process according to claim 4 in which the pH of the bleaching process is ramped
from near neutral to an alkalinity in the range about 8.5 to about 12, preferably
about 9.5 to about 10.5 by adding alkali approximately 15-30 minutes after the addition
of the TAED.
6. A process according to claim 5 in which the alkali is sodium hydroxide.
7. A process according to claim 5 or 6 in which the fabric is initially contacted with
the bleach at a temperature of less than 50°C and the temperature is raised to about
70°C or greater before addition of alkali.
8. Use of peracetic acid generated by the reaction of TAED and hydrogen peroxide in the
bleaching of Lyocell.
9. Use according to claim 8 in which the Lyocell is non-fibrillating Lyocell.
10. Use according to claim 9 in which the Lyocell has been previously treated with a cross-linker
selected from the group comprising chemical reagents bearing a plurality of acrylamido
groups, the average number of acrylamido groups per molecule ofthe chemical reagent
in the solution being greater than 2.1.
11. Use according to claim 10 in which the cross-linker is 1,3,5- triacryloylhexahydo-1,3,5-triazine.