BACKGROUND OF THE INVENTION
1. Field of the Invention
[0001] The present invention relates to a temper rolling method for steel plate and a temper
rolling mill. The present invention especially relates to a temper rolling method
for a steel plate suitable for producing a can having a highly bright appearance,
and to a temper rolling mill for carrying out the method.
2. Description of the Related Art
[0002] Temper rolling of a steel plate requiring brightness before or after plating (for
example, a steel plate for producing a can) is usually effected by a dry rolling method
using a rolling mill with two stands or more, each stand being allotted a different
role. For example, the first stand mainly serves for adjusting the quality of the
material (surface hardness and the like) and requires a dull roll having a strong
grip force in order to ensure sufficient elongation. This dull roll is usually a roll
that has been marked by dull stripes with weakly directional (or generally strongly
random) surface roughness produced by shot blasting, electro-spark machining or laser
processing. The surface roughness (Ra) is usually 0.5 µm or more.
[0003] A grinding processing roll, on the other hand, comprises a so-called mirror bright
roll for forming a specular surface appearance, and a so-called scratch bright roll
for leaving grinding traces (with a surface roughness (Ra) of about 0.15 µm or more)
behind. Some of the scratch bright rolls leave a surface roughness (Ra) of 0.5 µm
or more. However, the scratch bright roll is not used in the first stand, since it
has been considered to be insufficient for ensuring sufficient elongation.
[0004] Conventionally, the steel plate is rolled with the scratch bright roll in the second
stand of the rolling mill and thereafter for improving the brightness by alleviating
the effect of the dull stripes formed in the preceding stand. The steel plate is then
rolled with the scratch bright roll, a mirror bright roll or a dull roll having a
surface roughness corresponding to the required surface roughness of the steel plate.
[0005] While brightness is improved as the number of scratch bright to us in the intermediate
stands is increased, the facility costs and running costs are increased and a larger
installation space is required.
[0006] A two stand operation is most advantageous with respect to the production cost. As
disclosed in Japanese Unexamined Patent Publication No. 1-95803, a dull roll such
as a shot blasted dull roll is used for the front stand and a bright roll is used
for the final stand.
3. Problems to be solved by the Invention
[0007] The brightness level required with a limited surface roughness has increased in recent
years. However, it has been difficult to comply with the requirement of high brightness
in temper rolling mills having a small number of stands such as two stand mills, because
the number of rollings with the bright roll is decreased in such mills.
[0008] While it may be contemplated to apply the rolling mill twice without increasing the
number of stands by using the second stand as a pre-stand bright roll, cost increases
due to the increased number of steps can not be avoided.
SUMMARY OF THE INVENTION
[0009] Accordingly, it is an object of the present invention to solve the foregoing problems
by providing a method for improving brightness without incurring additional facilities
and production steps.
[0010] In one aspect, the present invention provides a temper rolling method for temper
rolling a steel plate using a temper rolling mill provided with plural stands, characterised
in that the steel plate contains 0.012 wt% or less of carbon (C), at least the roll
at the top front stand is a scratch bright roll having a surface roughness (Ra) of
1.2 µm or less, and at least the roll at the last stand is a bright roll having a
surface roughness (Ra) of 0.5 µm or less. Preferably, the temper rolling mill used
in the method has two stands in which case the roll at the first stand is the scratch
bright roll having a surface roughness (Ra) of 1.2 µm or less, and the roll at the
second stand is the bright roll having a surface roughness (Ra) of 0.5 µm or less.
[0011] In another aspect, the present invention provides a temper rolling mill for a steel
plate having plural stands, characterised in that at least the roll at the top front
stand is a scratch bright roll having a surface roughness (Ra) of 1.2 µm or less,
and at least the roll at the last stand is a bright roll having a surface roughness
(Ra) of 0.5 µm or less. Preferably, the temper rolling mill is provided with two stands
in which case the roll at the first stand is the scratch bright roll having a surface
roughness (Ra) of 1.2 µm or less, and the roll at the second stand is the bright roll
having a surface roughness (Ra) of 0.5 µm or less.
BRIEF DESCRIPTION OF THE DRAWINGS
[0012] Fig. 1 is a graph showing the relationship between the carbon (C) content and the
elongation of a temper rolled steel plate.
DESCRIPTION OF THE PREFERRED EMBODIMENT
[0013] The inventors of the present invention found the following facts through intensive
studies for attaining the foregoing objects:
[0014] (A) Brightness is largely deteriorated when a steel plate is compressed using a dull
roll having no directional surface roughness such as a shot blasted roll or an electro-spark
machined roll at the top front stage of the temper rolling mill.
[0015] Brightness, especially brightness after plating, of the steel plate is markedly improved
when the steel plate is rolled using a scratch bright roll, even if the surface roughness
is comparable to that obtained by other rolling methods. It is conjectured that, since
the scratch bright roll leaves unidirectional grinding traces, only a few concave
portions called dull bits, which are considered to be a main cause of deterioration
of brightness, are formed.
[0016] (B) Sufficient elongation cannot be attained when rolling general purpose low carbon
steel if a scratch bright roll is used at the top front stand. Although the reason
for this is not yet clear, it is conjectured that the surface roughness at the circumference
is so weak that the grip force is small since the grinding traces on the surface lie,
for example, in radial planes.
[0017] On the other hand, in the case of steel plate in which hardness before temper rolling
is reduced by reducing the content of carbon (C) to a certain level (so called extremely
low carbon steel), an elongation enough for obtaining a desired hardness can be ensured
even when a scratch bright roll is used at the top front stand.
[0018] The extremely low carbon steel is often excessively elongated when rolled with a
dull roll at the top front stand resulting in excess hardness. Or, the elongation
may be out of the control limit even though the hardness is not in excess, thereby
requiring a quality test to be carried out prior to shipping. On the contrary, when
a scratch bright roll is used in place of the dull roll, such excess elongation can
be avoided.
[0019] The reason why the conditions in the present invention are limited will be described
hereinafter.
[Composition of the target steel plate]
[0020] The steel plates to be subjected to the temper rolling method according to the present
invention are limited to those containing 0.012 wt% or less of carbon (C), because
a desired hardness cannot be attained by elongation using the scratch bright roll
at the top front stand when the steel plate contains more than 0.012% of C. More preferably,
the steel plate contains 0.0080 wt% or less of carbon. The preferred lower limit for
the carbon content is 0.0010 wt%, as lower contents may cause excess elongation.
[0021] FIG. 1 shows a graph indicating the relationship between the C content and the elongation
of temper rolled steel plate as a result of studies made by the inventors of the present
invention. Scratch bright rolls with a surface roughness (Ra) of 0.6 µm, scratch bright
rolls with a surface roughness (Ra) of 0.15 µm, and shot blasted dull rolls with a
surface roughness (Ra) of 0.6 µm were used as the first stand for obtaining the curves
denoted by SB 0.6, SB 0.15 and SB 0.6, respectively, in FIG. 1. Each temper rolling
mill comprised two stands, and a scratch bright roll with a surface roughness of 0.2
µm was used at the second stand. An elongation of 1.6% ± 0.2% was obtained with respect
to the steel plate containing 0.002 wt% of C under the rolling condition used.
[0022] It is apparent from FIG. 1 that elongation of the extremely low carbon steel becomes
unstable when the shot blasted dull roll was used at the first stand, (in addition
to low brightness). A desired elongation cannot be ensured, on the other hand, when
the scratch bright roll with a surface roughness (Ra) of 0.15 µm was used at the first
stand. When the scratch bright roll with a surface roughness (Ra) of 0.6 µm was used
at the first stand, on the contrary, the desired elongation could be maintained with
respect to steel plates with a C content of 0.0012 wt% or less. However, the elongation
becomes a little unstable, resulting in a decrease in elongation, in the case of steel
plates with a C content of more than 0.0080 wt%.
[0023] The steel plate preferably contains either 0.02 wt% of titanium (Ti) or 0.1 wt% of
niobium (Nb), or both of them, in order to ensure softness and machinability. Lower
limits of 0.005 wt% and 0.002 wt% are recommended with respect to Ti and Nb.
[0024] Aluminum (Al) may be present in an amount of 0.15 wt% or less for deoxidation and
stabilization of nitrogen (N).
[0025] It is preferable to contain other components within the conventional composition
range, such as 0.2 wt% or less of silicon (Si), 0.5 wt% or less of manganese (Mn);
(a content of 0.1 wt% or more is more preferable), 0.05 wt% or less of phosphorous
(P) and 0.03 wt% or less of sulfur (S). More preferable contents of Si, P and S are
0.05 wt% or less, 0.02 wt% or less and 0.02 wt% or less, respectively.
[0026] Calcium (Ca) may be added if desired and the balance is Fe and incidental element
and impurities.
(Roll at the top front stand)
[0027] In the front stand at least the top roll is a scratch bright roll with a surface
roughness (Ra) of 1.2 µm or less. Brightness before or after plating becomes poor
when a dull roll or a scratch bright roll with a surface roughness (Ra) of more than
1.2 µm is used. The preferred lower limit of the surface roughness (Ra) is 0.20 µm
or more. When the surface roughness (Ra) is less than 0.20 µm, elongation (hardness)
tends to be insufficiently developed. The more preferable surface roughness (Ra) is
in the range of 0.5 to 1.0 µm.
[0028] Although processing of the rolled surface is not especially limited, chromium (Cr)
plating may be effected in view of wear resistance.
(Roll at the last stand)
[0029] At least the roll at the last stand should be a bright roll with a surface roughness
(Ra) of 0.5 µm or less for ensuring a given level or more of brightness. A mirror
bright roll or a scratch bright roll may be used depending on the target surface roughness.
Nevertheless, a desired brightness (including after plating) cannot be ensured when
the surface roughness (Ra) exceeds 0.5 µm. However, the surface roughness is preferably
lower than the surface roughness of the roll at the final stand. The effect of the
present invention is markedly exhibited using a roll with a surface roughness (Ra)
range of about 0.15 to 0.3 µm, where requirements for brightness have not been satisfied
using a conventional roll.
[0030] Although brightness decreases as the surface roughness of the roll at the top front
stand is larger, an improvement in brightness is noticeable by using a scratch bright
roll in place of the dull roll at the top front stand even when the rolls have the
same surface roughness as each other.
[0031] Although the lower limit of the surface roughness as well as the surface treatment
after rolling is not especially limited, plating with Cr may be applied to the surface
to improve wear resistance.
(Rolls for the stands other than those described above (three stands or more))
[0032] Bright rolls are preferably used for the rolls of the stands intermediate the top
front and last stands. A roll having a surface roughness within the range of the surface
roughness of the front and last stands is especially suitable for the rolls to be
used in the stands other than the front and last stands for ensuring a required brightness.
More preferably, the surface roughness of each roll is gradually made finer in the
order of from the front roll to the succeeding rolls.
(Other conditions)
[0033] A dry rolling that requires no lubrication of the steel plate is suitable for the
temper rolling. An elongation of 3% or less is suitable, while an elongation of 1.5
±1% is more preferable and an elongation of 1.5 ±0.5% is further preferable. The target
hardness may be 50 to 60 in HR30T.
[0034] Plating methods after the temper rolling are not especially designated. Various plating
methods generally used for plating steel plates for cans such as tin plating or chromium
plating, or nickel (Ni) plating or a chromate processing on the surfaces after these
plating treatments may be applied to the target steel plate according to the present
invention.
[0035] Brightness was measured at an incident light angle of 20° using a gloss meter following
JIS Z8741 in the present invention.
[0036] The temper rolling mill according to the present invention may be applied to a production
line using the temper rolling alone, or it may installed at the outlet of a continuous
annealing furnace.
(Example)
[0037] After subjecting the cold roll steel plate having each component shown in TABLE 1
to recrystallization annealing (continuous annealing), the steel plate was temper
rolled with a temper rolling mill having two to three sands under the conditions shown
in TABLE 2, and the conditions other than those shown in TABLE 2 are the same condition
under which an elongation of 1.5 is obtained using the #1 stand SD 0.6 and #2 stand
MB 0.5 shown in No. 1 of TABLE 2. After measuring the hardness (HR30T) of each steel
plate, it was plated with tin (plating weight of 2.8 g/m
2) followed by a measurement of brightness after a reflowing treatment. Brightness
was evaluated by the following four steps:
ⓞ: 1300 to 1500
○: 1100 to less than 1300
Δ: 900 to less than 1100
×: less than 900
[0038] The results are listed in TABLE 2. It is evident from TABLE 2 that the steel plates
obtained according to the present invention had a superior brightness to that of the
steel plate in the comparative example.
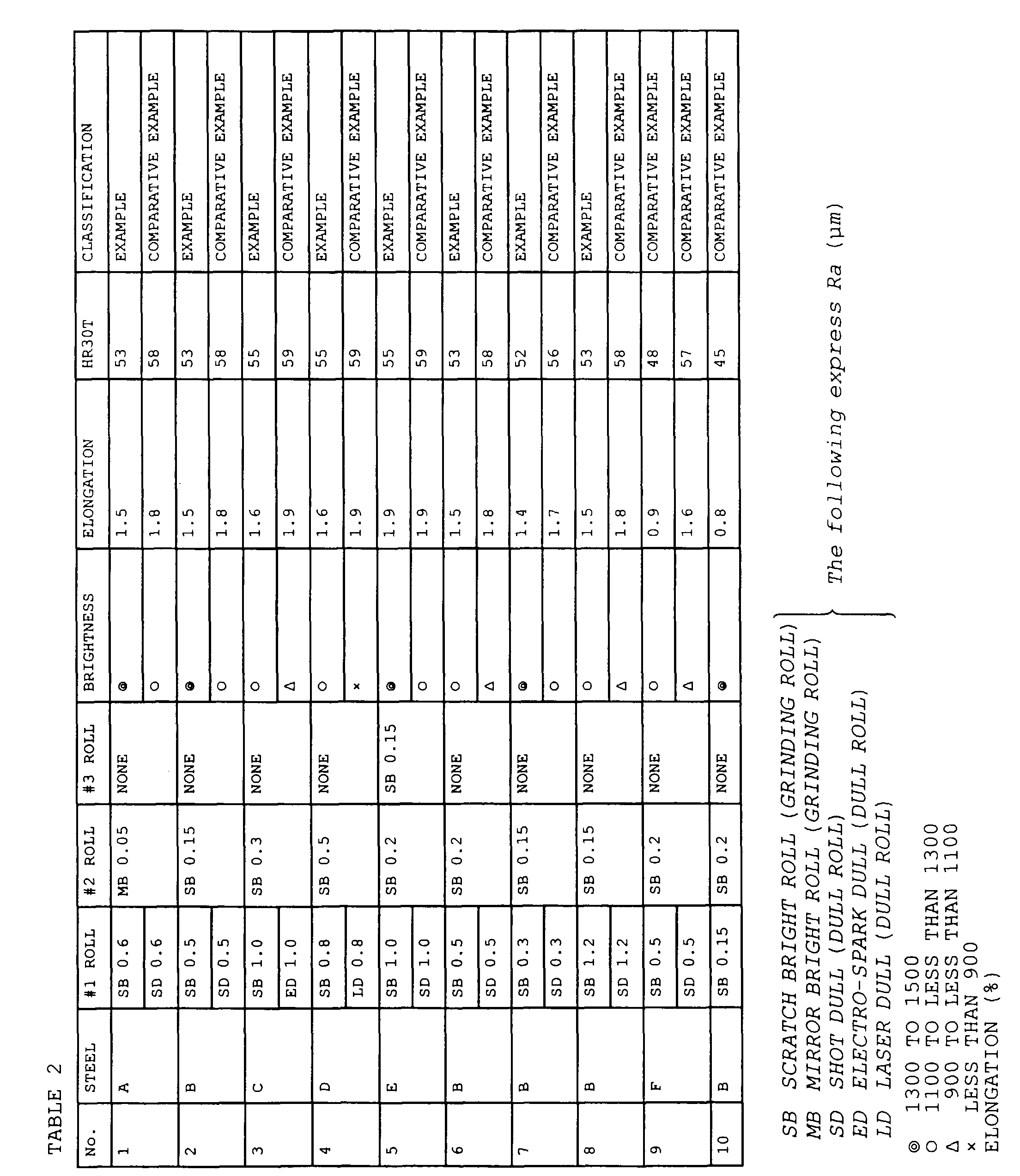
[0039] The present invention enables the production of a steel plate suitable for manufacturing,
for example, cans merely by applying unidirectional rolling using a temper rolling
mill provided with two to three stands at most.
1. A temper rolling method for temper rolling a steel plate using a temper rolling mill
provided with a plurality of roll stands characterised in that the steel plate contains
0.012 wt% or less of C, at least the roll at the top front stand is a scratch bright
roll having a surface roughness (Ra) of 1.2 µm or less, and at least the roll at the
last stand is a bright roll having a surface roughness (Ra) of 0.5 µm or less.
2. A temper rolling method according to Claim 1 wherein the temper rolling mill is a
two stand mill.
3. A temper rolling method according to Claim 1 or 2 wherein the steel plate contains
from 0.001 to 0.008 wt% of carbon.
4. A temper rolling method according to Claim 1, 2 or 3 wherein the steel plate additionally
contains from 0.005 to 0.2 wt% of Ti and/or from 0.002 to 0.1 wt% of Nb.
5. A temper rolling method according to any preceding Claim wherein the steel plate additionally
contains not more than 0.15 wt% Al, not more than 0.2 wt% Si, 0.1 to 0.5 wt% Mn, not
more than 0.05 wt% P, and not more than 0.03 wt% S.
6. A temper rolling mill for steel plate having a plurality of roll stands characterised
in that at least the roll at the top front stand is a scratch bright roll having a
surface roughness (Ra) of 1.2 µm or less, and at least the roll at the last stand
is a bright roll having a surface roughness (Ra) of 0.5 µm or less.
7. A temper rolling mill according to Claim 6 which is a two stand mill.
8. A temper rolling mill according to Claim 6 or 7 wherein the scratch bright roll of
the front stand has a surface roughness of at least 0.20 µm.
9. A temper rolling mill according to Claim 8 wherein the scratch bright roll of the
front stand has a surface roughness of 0.5 to 1.0 µm.
10. A temper rolling mill according to any one of Claims 6 to 9 wherein the bright roll
of the last stand is a mirror bright roll or a scratch bright roll having a surface
roughness of from 0.15 to 0.3 µm.