[0001] The present invention concerns silver halide photographic products which are associated
with X-ray intensifying screens and used in radiography.
[0002] More precisely, the invention concerns a radiographic system containing at least
one layer of spectrally sensitised tabular grain silver halide emulsion and an intensifying
screen. The invention makes it possible to use a wide range of spectral sensitisers
whilst avoiding the problem of residual colouring, also called "dye stain" in the
art, in the areas of low exposure of the radiographic image.
[0003] In radiography, particularly in medical radiography, use is normally made of radiographic
systems comprising an intensifying screen and a silver halide photosensitive product.
[0004] The use of intensifying screens makes it possible to reduce the quantity of X-rays
required to obtain a radiograph and consequently to reduce the quantity of X-rays
absorbed by the patient.
[0005] Intensifying screens must have a maximum emission as close as possible to the sensitivity
peak of the silver halide grains making up the radiographic film.
[0006] The silver halide photosensitive products used in radiography with intensifying screens
comprise a transparent support coated on one of its faces, and preferably on both
faces, with at least one layer of spectrally sensitised silver halide emulsion.
[0007] Silver halide grains are naturally sensitive to blue light, but, by adsorbing spectral
sensitising dyes on their surface, they may have maximum absorption in the blue and/or
green and/or red regions of the visible spectrum. In practice, the spectral sensitising
dye is chosen so that the maximum absorption of the silver halide grains occurs in
the region of maximum emission of the intensifying screen.
[0008] For example a screen is used emitting in the blue region between 360 and 500 nm and
a spectral sensitising dye in the blue region having maximum absorption in this range.
[0009] It is known that tabular grain silver halide emulsions can be used in radiographic
products.
[0010] For example, US patent 4,639,411 describes a radiographic element which comprises
an emulsion consisting of tabular silver halide grains capable of forming a latent
image when it is exposed to light. This emulsion preferably consists of tabular grains
with a thickness of less than 0.5 µm and an aspect ratio higher than 5:1.
[0011] Tabular grain emulsions require a high level of sensitising dye because of the high
specific surface area of the grains. Certain spectral sensitising dyes cause, in the
radiographic image, a residual colouring in the areas which are unexposed or only
slightly exposed. For example, the image then has yellow colouring in the areas of
low density, if the dye is a spectral sensitiser in the blue region. This problem
is particularly significant with fast processing which takes place in less than a
minute and in which the time of immersion in the processing solution is very short.
[0012] In order to avoid this phenomenon, it is necessary to use a spectral sensitising
dye which does not form any residual colouring, which limits the choice thereof. This
is illustrated by US-A-5 108 887.
[0013] The invention makes it possible to use spectral sensitising dyes which, if they were
used alone in high quantities, would have caused a residual colouring in the areas
of the image of low density. According to the invention, this colouring is avoided
by associating therewith an optical brightener having special characteristics. One
advantage of the invention is that it affords a greater degree of freedom in the choice
of spectral sensitising dyes. In addition, surprisingly, the sensitometric properties
of the radiographic image are not substantially impaired by the presence of the optical
brightener according to the invention.
[0014] The optical brighteners which have been known for a long time are substances which
absorb ultraviolet light in the region of the spectrum lying between 300 and 400 nm
and which are fluorescent in the blue region of the visible spectrum.
[0015] They are used for improving the whiteness of photographic papers and in photographic
films. Research Disclosure of July 1983, No 23136, describes inter alia the use of
optical brighteners in radiographic systems.
[0016] According to this article, the presence of optical brighteners reduces the yellow
appearance of the supporting polymer when a source of ultraviolet light is used. The
optical brightener is incorporated in a layer placed on the support, or on the support
by soaking the support in a solution containing the optical brightener, for example
a developing or fixing solution or a stabilising bath.
[0017] This article does not deal with the problem of the residual colouring due to the
spectral sensitising dye.
[0018] US patent 4,232,112 describes a process for developing a colour photographic film
in which the development solution or the bleaching/fixing solution comprises a bleaching
agent which is a derivative of 4,4'-diamino-stilbene disulphonic acid and a second
compound derived from benzene sulphonic or naphthalene sulphonic acid. This process
makes it possible to avoid on the one hand the residual colouring due to oxidation
of the color developer in the bleaching/fixing solution and on the other hand the
residual colouring which is due to the accumulation of various substances on the edges
of the film.
[0019] US patent 4,587,195 describes a method for eliminating the residual colouring in
a colour image. For this purpose a development solution is used comprising a combination
of optical brighteners of the triazylstilbene type with slightly shifted absorption
peaks.
[0020] US patent 5,238,793 describes a method of processing black and white films comprising
a layer of silver halide emulsion spectrally sensitised with a cyanine dye. When the
rate of replenishment of the processing solution is low or when the level of sensitising
dye is high, the spectral sensitising dye forms in the processing solutions solid
particles which adhere to the surface of the film and form specks or blotches on the
final image.
[0021] In order to avoid this phenomenon, the exposed film is placed in contact with a processing
solution comprising a compound enabling the spectral sensitising dye to dissolve.
The solubilising compound is a stilbene derivative which is incorporated in the processing
solution in which the formation of solid particles poses a problem, but it can also
be in the photographic element. This possibility is not put into practice in this
patent, which contains no disclosure relating to the location of the solubilising
compound in the photographic element.
[0022] The problem of residual colouring resolved by the present invention is quite another
matter, since it is due not to an accumulation of solid particles in the processing
solution, but to the absorption of the residual spectral sensitising dye in the gelatin
of the radiographic product.
[0023] Thus the problem of the residual colouring which occurs in the radiographic image,
in particular after fast processing, when the emulsion contains certain spectral sensitising
dyes, is not resolved by the prior art and none of the documents cited discloses or
suggests the use of optical brighteners for resolving this problem.
[0024] Also one of the objects of the invention is a radiographic product comprising a support
and at least one photosensitive layer comprising gelatin, at least one photosensitive
silver halide tabular grain emulsion and a spectral sensitising dye in the blue region
having an emission peak between 400 and 500 nm and present in the said radiographic
product in sufficient quantity to cause, in the radiographic image, the formation
of a residual yellow colouring due to the absorption of the aggregate of the residual
dye in the gelatin, and an optical brightener
a) which is a derivative of 4,4'-diaminostilbene disulphonic acid having at least
3 anionic sulpho groups,
b) which is put in at least one of the photosensitive layers of the radiographic product
or in at least one layer of gelatin located between the photosensitive layer and the
support.
[0025] Anionic sulpho group means an ionised -SO
3- group associated with a cation balancing the ionic charge by opposition to an acid
group -SO
3H.
[0026] Another object of the invention is a radiographic system comprising at least one
X-ray intensifying screen with maximum emission between 360 and 500 nm and the radiographic
product as defined above.
[0027] In the following description, reference will be made to the drawings in which:
- Figure 1 shows the absorption spectrum between 350 and 500 nm for the RP-XOMAT® process,
the optical brightener being in the emulsion layer.
- Figure 2 shows the absorption spectrum between 350 and 500 nm for the KRA® process,
the optical brightener being in the emulsion layer.
- Figure 3 shows the optical density of the residual colouring at 440 nm for the RP-XOMAT®
process, the optical brightener being in the emulsion layer.
- Figure 4 shows the optical density of the residual colouring at 440 nm for the KRA®
process, the optical brightener being in the emulsion layer.
- Figure 5 shows the absorption spectrum between 350 and 500 nm for the RP-XOMAT® process,
the optical brightener being in a layer of gelatin between the support and the emulsion
layer.
- Figure 6 shows the absorption spectrum between 350 and 500 nm for the KRA® process,
the optical brightener being in a layer of gelatin between the support and the emulsion
layer.
- Figure 7 shows the optical density of the residual colouring at 440 nm for the RP-XOMAT®
and KRA® processes, the optical brightener being in a layer of gelatin between the
support and the emulsion layer.
- Figure 8 shows the absorption spectrum between 350 and 500 nm for the RP-XOMAT® process,
the optical brightener being in an overcoat of gelatin.
[0028] The emulsions used in the invention are emulsions with tabular grains of silver chloride,
silver bromide, silver iodide or a mixture of these halides, in a binder.
[0029] The binder is a water-permeable hydrophilic colloid such as gelatin, gelatin derivatives,
albumin, a polyvinyl alcohol, polyvinyl polymers, etc.
[0030] The emulsions may be hardened in accordance with one of the methods described in
US patent 4,425,266. The hardening agents which may be used are described in Research
Disclosure, December 1989, No 308113, Section X.
[0031] In addition to the characteristics specifically described above, the emulsions may
comprise other compounds such as anti-fogging agents, stabilisers or anti-static agents.
The radiographic film may comprise an overcoat containing matting agents. This overcoat
or the sensitive layer may contain plasticisers or lubricants. These compounds were
described in Research Disclosure, Vol 184, August 1979, No 18431.
[0032] These silver halide emulsions are preferably chemically sensitised by means of sulphur
and/or gold and/or selenium, in accordance with the conventional chemical sensitisation
methods described in Research Disclosure, December 1989, No 308119, Section III.
[0033] The emulsions are spectrally sensitised. The conventional spectral sensitisation
methods which can be used are described in Research Disclosure, December 1989, No
308119, Section IV.
[0034] The spectral sensitising dyes which can be used in the present invention are the
blue spectral dyes which are liable to produce residual colouring, such as for example
cyanine or merocyanine dyes. Cyanine dyes are described in Research Disclosure, December
1989, No 308119, Section IV A-C. Cyanine dyes which can be used according to the invention
correspond to the formula:
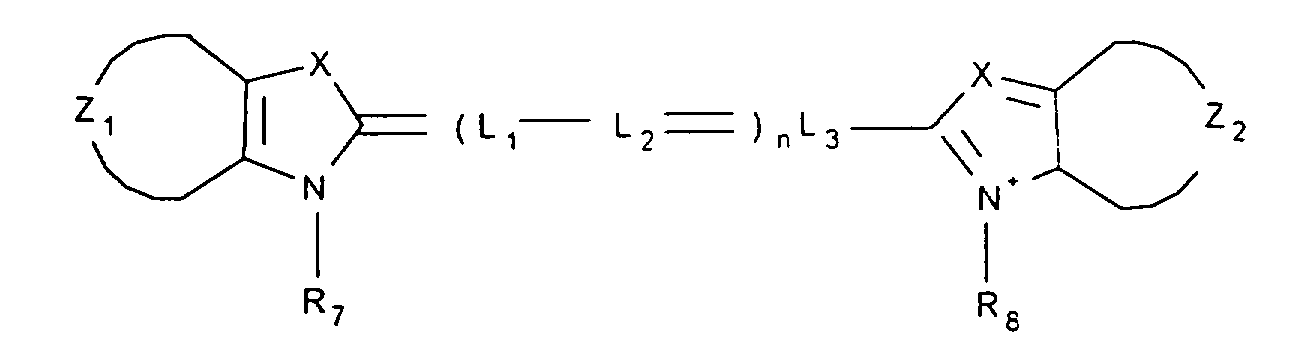
where Z
1 and Z
2 represent the atoms necessary to complete a substituted or unsubtituted aromatic
ring structure ; R
7 and R
8 each separately represent a substituted or unsubtituted alkyl radical having 1 to
12 carbon atoms, which may be substituted by a halogen, an alkoxy, aryl, aryloxy,
sulpho or carboxyl radical; L
1, L
2 and L
3 each separately represent a methine bond, substituted or unsubtituted; X is O, S,
Se, -C- or N- and n is 0, 1 or 2.
[0036] The optical brighteners which are used in the present invention must be capable of
destroying the aggregate of the residual sensitising dye in the gelatin, which reduces
the optical density corresponding to the residual colouring, giving rise to chemical
species in which the wavelength of the absorption peak lies in a region of the visible
spectrum where the sensitivity of the eye is low, preferably around the wavelengths
below 420 nm. In addition, these optical brighteners must have a sufficient number
of solubilising groups to be able to be retained in the gelatin in the layers of the
photographic product.
[0037] Examples of optical brighteners which can be used in the present invention are compounds
of the stilbene type having at least three anionic sulpho groups. For example it is
possible to use compounds having the formula:
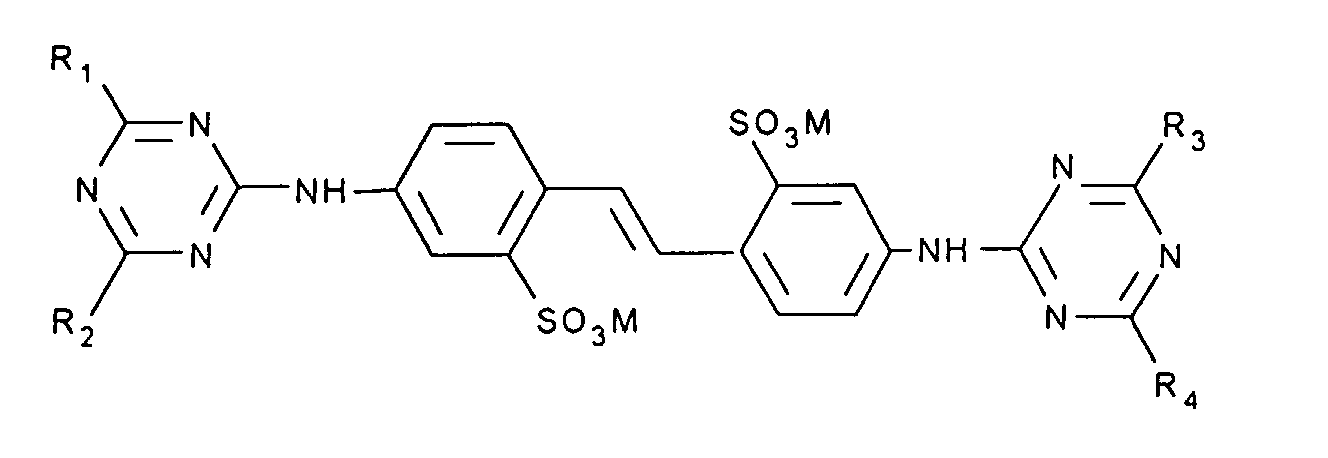
where
R1, R2, R3 and R4 are each separately chosen from the group
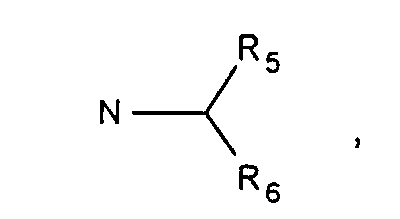
halogen, hydrogen, hydroxy, substituted or unsubstituted alkyl, substituted or unsubstituted
aryl, substituted or unsubstituted alcoxy and sulpho,
R5 and R6 are each separately chosen from amongst hydrogen, substituted or unsubstituted alkyl,
and substituted or unsubstituted aryl,
M is a cation balancing the ionic charge, with the proviso that the compound has at
least one solubilising anionic sulpho group on R1, R2, R3 or R4.
[0038] Examples of useful compounds are described in Table I in US patent 5 238 793 already
cited. Compounds which are preferred according to the invention are Phorwite® of formula:
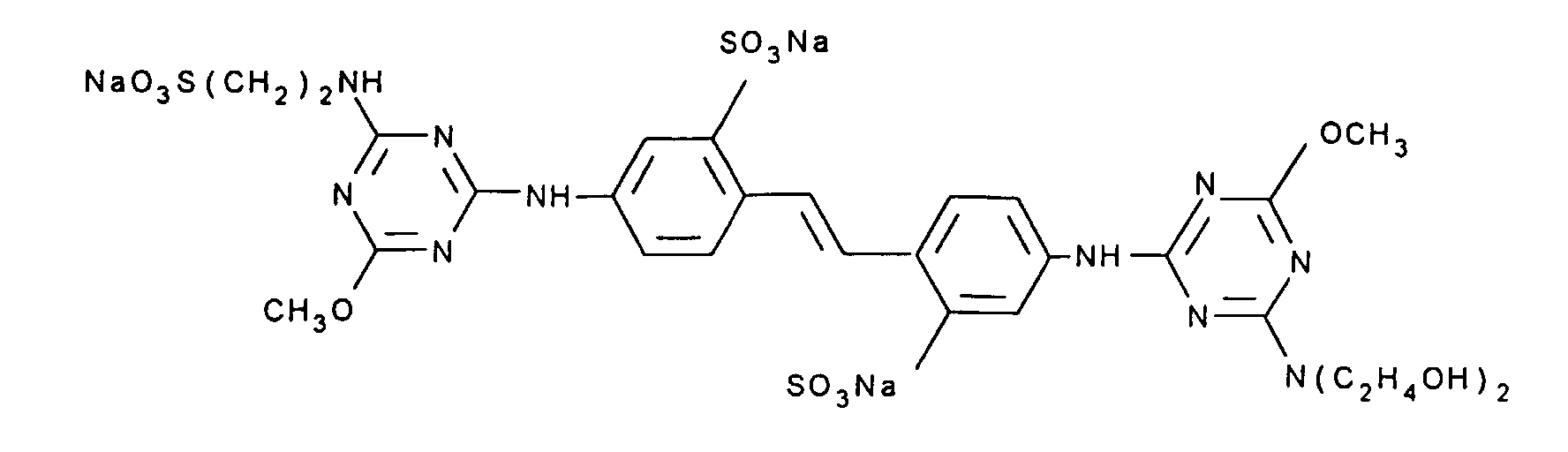
and Tinopal® of formula:

[0039] The quantity of optical brightener is determined so that the residual colouring due
to the spectral sensitising dye is highly attenuated without the sensitometric or
physical properties of the radiographic product being impaired. In particular, it
is desired that the photographic sensitivity, the reciprocity failure, the sensitivity
to pressure and the keeping during incubation (fog/speed ratio) should not be substantially
modified.
[0040] An appropriate quantity of optical brightener is between 0.05 and 2 mg/dm
2 and preferably between 0.5 and 1.5 mg/dm
2.
[0041] In addition to the radiographic film, radiographic systems generally comprise a pair
of X-ray intensifying screens situated on each side of the radiographic film.
[0042] The intensifying screens used in the invention have an emission peak in the blue
or ultraviolet region whose wavelength is between 360 and 500 nm.
[0043] The X-ray intensifying screens comprise one or more luminophores in a mixture with
a binder. The luminophore particle size is generally between 0.5 and 20 µm and preferably
between 1 and 10 µm.
[0044] Examples of luminophores emitting in the blue or ultraviolet region are calcium tungstate
CaWO
4, lanthane oxybromide LaOBr activated by terbium or thullium, gadolinium oxybromide
activated by yttrium or cerium, YTaO
4 activated by gadolinium, bismuth, lead, cerium, barium fluorochloride BaFCl activated
by europium, gadolinium, lanthanum or yttrium, or barium sulphate activated by europium
or strontium.
[0045] Usable binders are chosen from amongst the organic polymers transparent to light
radiation and to X-rays, such as vinyl alcohol and o-sulphobenzaldehyde acetal polymers,
chlorosulphonated polyethylenes, bisphenol polycarbonates, alkyl acrylate and methacrylate
copolymers and polyurethanes. Other binders which can be used within the scope of
the invention are described in US patents 2,502,529, 2,887,379, 3,617,285, 3,300,310,
3,300,311 and 3,743 833 and in Research Disclosure, Vol 154, February 1977. The preferred
binders are polyurethanes such as Estane®, Permuthane® and Cargill®,
[0046] The X-ray intensifying screens may contain, in addition to the fluorescent layer,
a protective layer and a reflective layer.
[0047] The methods of manufacturing screens and radiographic films are described in the
above-mentioned Research Disclosure No 18431.
[0048] The following examples illustrate the invention.
EXAMPLES 1-3
[0049] The films described in Examples 1-3 consist of an Estar® support coated, in the following
order, with a layer of tabular grain silver bromide emulsion having a grain equivalent
diameter of 2.14 µm and a mean grain thickness of 0.11 µm and an overcoat of gelatin.
In Example 2, the film also comprises a layer of gelatin placed between the emulsion
layer and the support. The film is hardened by means of bis(vinylsulphonylmethyl)
ether, the amount of hardening agent by weight being equal to 2.25% of the total dry
gelatin contained in the film. The emulsion is optimally chemically sensitised by
means of sulphur (150 mg KSCN per mole of Ag), gold (5.06 mg Na
3(S
2O
3)
2Au,2 H
2O per mole of Ag) and selenium (0.67 mg KSeCN per mole of Ag). The emulsion is optimally
spectrally sensitised with spectral sensitising dye A.
[0050] The samples of film are exposed to blue light simulating the exposure obtained through
an intensifying screen.
[0051] The exposed films are then processed using a conventional RP-XOMAT® process in 90
seconds and a fast KRA® process in 45 seconds.
[0052] After processing, the residual colouring levels are measured by spectrophotometry
at 440 nm (the wavelength corresponding to the absorption peak of the aggregate of
the sensitising dye in the gelatin), the reciprocity failure for an exposure of between
1/50th and 5 seconds, the spectral sensitivity between 300 and 500 nm. In this way
it is verified that no loss of sensitivity occurs in the near ultraviolet because
of the absorbance of the optical brightener.
[0053] The resistance to pressure is estimated by using a pressure roller simulating mechanical
stresses.
Example 1
[0054] In this example, the optical brightener is put in the emulsion layer of the radiographic
product.
[0055] A simplified format of radiographic product is used, as described above and comprising
a colourless Estar
R support, a tabular grain silver bromide emulsion (21 mg Ag/dm
2, 2.85 mg/dm
2 gelatin, 465 mg of spectral sensitising dye A per mole of Ag), and an overcoat of
gelatin (6.88 mg/dm
2). 0.6 mg/dm
2 of optical brightener (Tinopal® or Phorwite®) is introduced into the emulsion layer
either before spectral sensitisation (IF) or immediately after (AF). The products
are processed in automatic processors for the RP-XOMAT® and KRA® processes.
[0056] The results are given in Figures 1 and 2, where
- 1-Check represents the control product which does not contain any optical brightener
in the emulsion layer,
- 2-Phorwite® IF (or 3-Tinopal® IF) represents the product according to the invention
in which the optical brightener has been introduced into the emulsion before the sensitisation,
and
- 4-Phorwite® AF (or 5-Tinopal® AF) represents the product according to the invention
in which the optical brightener has been introduced into the emulsion after sensitisation.
[0057] Figures 1 and 2 show the absorption spectrum between 350 and 500 nm. The yellow residual
dye, due to the aggregate of the sensitising dye retained in the gelatin, corresponds
to the principal peak situated at 440 nm. A less prominent peak can be seen, corresponding
to the monomeric sensitising dye at around 410 nm.
[0058] In the presence of the optical brightener, a reduction in the height of the peak
at 440 nm is observed, and a modification of the spectrum between 420 and 350 nm,
which is explained by the destruction of the dye aggregate in the gelatin and the
formation of species resulting from the interaction between the optical brightener
and the aggregate of the dye in the gelatin.
[0059] Figures 3 and 4 show the optical density of the residual colouring at 440 nm for
the RP-XOMAT® and KRA® processes. In these figures, 1-CHECK represents the check sample.
[0060] It can be seen that the method of introducing the optical brightener (before or after
the spectral sensitising dye) is not critical.
[0061] In the fast KRA® process, the shortening of the development cycle compared with the
RP-XOMAT® process causes an aggravation of the residual colouring in the absence of
any optical brightener. The best result for both the KRA® process and the RP-XOMAT®
process is obtained with Tinopal®, this improvement being particularly noticeable
in the KRA® process.
[0062] In all cases, the presence of an optical brightener in the emulsion layer causes
a loss of sensitivity of around 0.03 to 0.06 log H (where H represents the value of
the illumination expressed in lux.sec) whilst the other parameters such as the maximum
density (Dmax), the minimum density (Dmin) and the contrast are practically unaffected.
The reciprocity failure increases, but the sensitivity to pressure and the fog of
the products when fresh or after incubation are unchanged.
[0063] The invention makes it possible to eliminate up to 82% of residual colouring in the
RP-XOMAT® process and up to 90% of residual colour in the KRA® process without excessively
impairing the sensitometric characteristics.
Example 2
[0064] In this example, the optical brightener is located in a layer placed between the
emulsion layer and the support. This arrangement may be useful where it is difficult
to introduce the optical brightener into the emulsion layer for practical reasons
or where interactions with other additives could occur.
[0065] In this example, a simplified format of radiographic product is used, comprising,
in the following order, a 20 mg/dm
2 gelatin layer between the support and the emulsion layer, a layer of tabular grain
silver bromide emulsion (21 mg Ag/dm
2, 32 mg/dm
2 gel) and an overcoat of gelatin (6.88 mg/dm
2). A quantity of optical brightener (Tinopal® or Phorwite
R) of respectively 0.3, 0.6 and 1.2 mg/dm
2 is introduced.
[0066] Figures 5 and 6 show the absorption spectrum between 360 and 450 nm. It can be seen
that the two compounds make it possible to reduce the residual colouring (lowering
of the peak at 440 nm) and are more efficacious in the KRA® process.
[0067] Figure 7 shows the optical density at 440 nm, which corresponds to the residual colouring.
CHECK represents the control. The best results are obtained with Tinopal
R at a concentration of 1.2 mg/m
2.
[0068] In all cases, the presence of an optical brightener causes no loss of sensitivity,
and the other parameters such as Dmax, Dmin and contrast are practically unaffected.
The reciprocity failure, sensitivity to pressure and fog of the product when fresh
or after incubation are unchanged.
[0069] The invention makes it possible to eliminate up to 70% of residual colouring in the
RP-XOMAT® process and up to 94% of residual colouring in the fast KRA® process without
impairing the sensitometric characteristics.
Example 3 (Comparative)
[0070] In this example, a quantity of Phorwite® of 0.4 and 0.6 mg/dm
2 respectively is introduced into the gelatin overcoat.
[0071] Figure 8 shows the absorption spectrum between 350 and 500 nm, for the RP-XOMAT®
process.
[0072] It can be seen that the effect of the optical brightener is weaker where it is put
in the overcoat since it is possible to eliminate only 15% of residual colouring.
The sensitometric characteristics are not affected.
[0073] In conclusion, the best compromise enabling the residual colouring to be reduced
without for all that modifying the sensitometric characteristics is obtained by putting
the optical brightener in the gelatin layer of the photographic product placed between
the emulsion layer and the support. In Example 2, 90% of residual colouring is eliminated
in the fast KRA® process and 67% of residual colouring in the RP-XOMAT® process with
a concentration of Tinopal® of 1.2 mg/m
2 without the sensitometric characteristics being affected.
EXAMPLES 4-5
[0074] In these examples, the normal format of radiographic film is used. On both sides
of a blue Estar® support, are coated, in the following order, a layer of tabular grain
silver bromide emulsion (32 mg/dm
2 gel, 21 mg/dm
2 Ag), an intermediate layer of gelatin (3.54 mg/dm
2 gel) and an overcoat of gelatin (3.54 mg/dm
2 gel). In Example 5, the film also comprises a layer of gelatin (14 mg/dm
2 gel) placed between the emulsion layer and the support. The film is hardened by means
of bis(vinylsulphonylmethyl) ether, the amount of hardening agent by weight being
equal to 2.35% of the total dry gelatin contained in the film. The emulsion is chemically
sensitised and spectrally sensitised with spectral sensitising dye A as in Example
1.
Example 4
[0075] In this example, 0.6 mg/dm
2 of Tinopal® is introduced into the emulsion after sensitisation.
[0076] The samples of film are exposed to blue light by means of a conventional Kodak X-Omat®
intensifying screen.
[0077] The exposed films are then processed with an RP-XOMAT® process in 90 seconds and
a KRA® process in 45 seconds, as in the previous examples.
[0078] The level of residual colouring is measured by spectrophotometry at 440 nm.
[0079] Compared with a control which does not include Tinopal®, a reduction of 70% in the
optical density at 440 nm is observed in the RP-XOMAT® process and 86.5% in the KRA®
process. A fairly large loss of sensitivity of around 0.08 to 0.1 Log H is also observed
and an increase in the reciprocity failure. The other parameters such as Dmax, Dmin
and contrast are practically unaffected. The sensitivity to pressure and the fog of
the product when fresh or after incubation are unchanged.
Example 5
[0080] In this example, 1.2 mg/dm
2 of Tinopal
R is introduced into the layer of gelatin placed between the support and the emulsion
layer.
[0081] The samples of film are exposed and processed using the RP-XOMAT® process in 90 seconds
and the KRA® process in 45 seconds, as in the previous example.
[0082] The level of residual colouring is measured by spectrophotometry at 440 nm.
[0083] Compared with a control which does not include Tinopal®, a reduction of 80% in the
optical density at 440 nm is observed in the RP-XOMAT® process and 93.5% in the KRA®
process. Neither loss of sensitivity nor increase in the reciprocity failure are observed.
The other parameters such as Dmax, Dmin and contrast are practically unaffected. The
sensitivity to pressure and the fog of the product when fresh or after incubation
are unchanged.
[0084] In conclusion, as in Examples 1 and 2, the best compromise enabling the residual
colouring to be reduced without for all that modifying the sensitometric characteristics
is obtained by placing the optical brightener in the gelatin layer of the photographic
product placed between the emulsion layer and the support. In Example 5, up to 93.5%
of residual colouring is eliminated in the fast KRA® process with a concentration
of Tinopal® of 1.2 mg/m
2 without the physical and sensitometric characteristics being affected.
1. Radiographic product comprising a support and at least one photosensitive layer comprising
gelatin, at least one photosensitive silver halide tabular grain emulsion and a spectral
sensitising dye of the visible spectrum having an emission peak between 400 and 500
nm and present in the said radiographic product in sufficient quantity to cause, in
the radiographic image, the formation of a residual yellow colouring due to the absorption
of the aggregate of the residual dye in the gelatin, and an optical brightener,
characterised in that the optical brightener
a) is a derivative of 4,4'-diaminostilbene disulphonic acid having at least 3 anionic
sulpho groups,
b) is put in at least one of the photosensitive layers of the radiographic product
or in at least one layer of gelatin located between the photosensitive layer and the
support.
2. Radiographic product according to Claim 1, wherein the optical brightener is in at
least one of the photosensitive layers.
3. Radiographic product according to Claim 1, wherein the optical brightener is in at
least one of the layers of gelatin placed between the photosensitive layer and the
support.
4. Radiographic product according to Claim 1, wherein the optical brightener has the
formula:

where
R1, R2, R3 and R4 are each separately chosen from the group

halogen, hydrogen, hydroxy, substituted or unsubtituted alkyl, substituted or unsubstituted
aryl, substituted or unsubstituted alcoxy and sulpho,
R5 and R6 are each separately chosen from amongst hydrogen, substituted or unsubstituted alkyl,
and substituted or unsubstituted aryl,
M is a cation balancing the ionic charge, with the proviso that the compound has at
least one solubilising anionic sulpho group on R1, R2, R3 or R4.
5. Radiographic product according to Claim 4, wherein the optical brightener is chosen
from amongst the following compounds:

or
6. Radiographic product according to Claim 1, wherein the amount of optical brightener
is between 0.05 and 2 mg/dm2.
7. Radiographic product according to Claim 6, wherein the amount of optical brightener
is between 0.5 and 1.5 mg/dm2.
8. Radiographic product according to Claim 1, wherein the spectral sensitising dye is
a cyanine dye.
10. Use of the radiographic product according to any one of the preceding claims in a
fast development process, the total processing time of which is less than 1 minute.
11. Radiographic system comprising at least one X-ray intensifying screen, having a maximum
emission between 360 and 500 nm, and the radiographic product according to any one
of Claims 1 to 9.
1. Radiographisches Produkt mit einem Träger und mindestens einer photosensitiven Schicht
mit Gelatine, mindestens einer photosensitiven Silberhalogenid-Tafelkornemulsion und
einem spektral sensibilisierenden Farbstoff des sichtbaren Spektrums mit einer Emissionsspitze
zwischen 400 und 500 nm, der in dem radiographischen Produkt in einer ausreichenden
Menge vorliegt, um in dem radiographischen Bild die Bildung einer restlichen Gelb-Färbung
aufgrund der Absorption des Aggregates des restlichen Farbstoffes in der Gelatine
zu bewirken, und einem optischen Aufheller,
dadurch gekennzeichnet, daß der optische Aufheller
a) ein Derivat der 4,4'-Diaminostilbendisulfonsäure mit mindestens drei anionischen
Sulfogruppen ist,
b) in mindestens eine der photosensitiven Schichten des radiographischen Produkts
eingeführt ist oder in mindestens eine Schicht aus Gelatine, die zwischen der photosensitiven
Schicht und dem Träger angeordnet ist.
2. Radiographisches Produkt nach Anspruch 1, in dem der optische Aufheller in mindestens
einer der photosensitiven Schichten vorliegt.
3. Radiographisches Produkt nach Anspruch 1, in dem der optische Aufheller in mindestens
einer der Schichten aus Gelatine zwischen der photosensitiven Schicht und dem Träger
vorliegt.
4. Radiographisches Produkt nach Anspruch 1, in dem der optische Aufheller die Formel
aufweist:

worin
R1, R2, R3 und R4 jeweils unabhängig voneinander ausgewählt sind aus der Gruppe
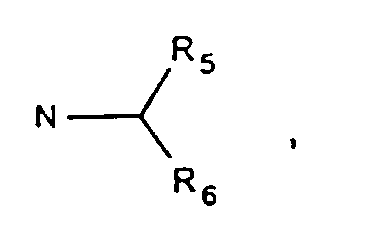
Halogen, Wasserstoff, Hydroxy, substituiertem oder unsubstituiertem Alkyl, substituiertem
oder unsubstituiertem Aryl, substituiertem oder unsubstituiertem Alkoxy und Sulfo,
R5 und R6 jeweils unabhängig voneinander ausgewählt sind aus Wasserstoff, substituiertem oder
unsubstituiertem Alkyl und substituiertem oder unsubstituiertem Aryl,
M ein Kation ist, das die ionische Ladung ausgleicht, wobei gilt, daß die Verbindung
mindestens eine löslichmachende anionische Sulfogruppe an R1, R2, R3 oder R4 aufweist.
5. Radiographisches Produkt nach Anspruch 4, in dem der optische Aufheller ausgewählt
ist aus den folgenden Verbindungen:
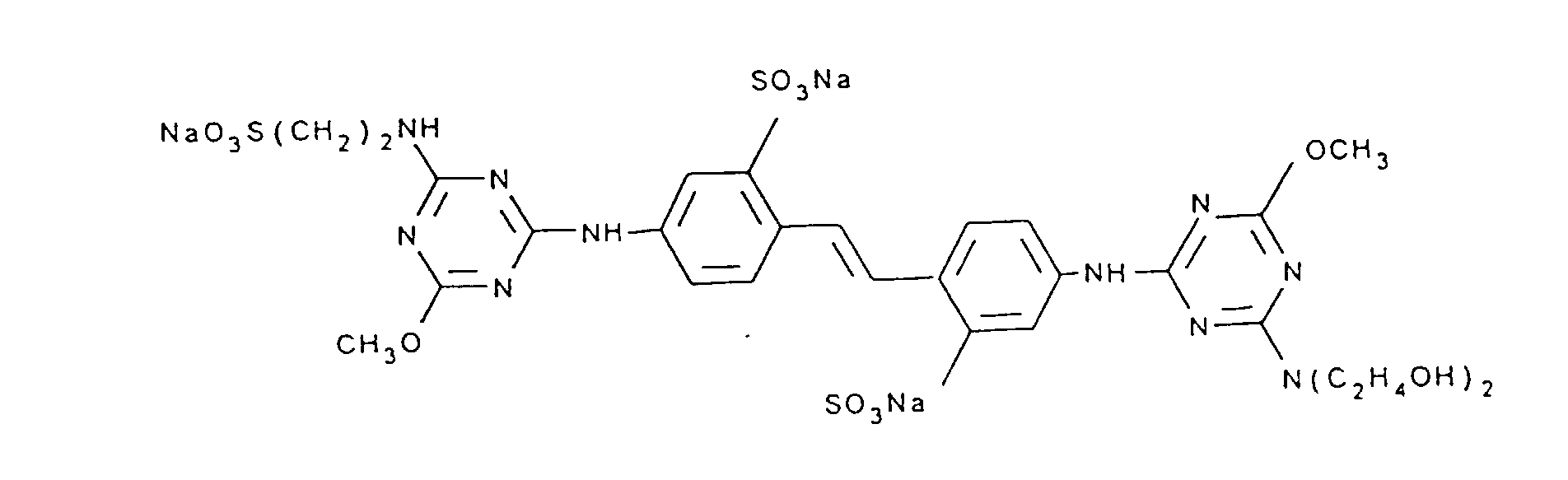
oder
6. Radiographisches Produkt nach Anspruch 1, in dem die Menge an optischem Aufheller
zwischen 0,05 und 2 mg/dm2 liegt.
7. Radiographisches Produkt nach Anspruch 6, in dem die Menge an optischem Aufheller
zwischen 0,5 und 1,5 mg/dm2 liegt.
8. Radiographisches Produkt nach Anspruch 1, in dem der spektral sensibilisierende Farbstoff
ein Cyaninfarbstoff ist.
10. Verwendung des radiographischen Produktes nach einem der vorstehenden Ansprüche im
Rahmen eines Schnell-Entwicklungsprozesses, wobei die Gesamt-Entwicklungszeit weniger
als 1 Minute beträgt.
11. Radiographisches System mit mindestens einem Röntgenstrahl-Verstärkerschirm mit einer
maximalen Emission zwischen 360 und 500 nm und dem radiographischen Produkt nach einem
der Ansprüche 1 bis 9.