(19) |
 |
|
(11) |
EP 0 747 154 B1 |
(12) |
EUROPÄISCHE PATENTSCHRIFT |
(45) |
Hinweis auf die Patenterteilung: |
|
14.02.2001 Patentblatt 2001/07 |
(22) |
Anmeldetag: 04.06.1996 |
|
|
(54) |
Verfahren und Vorrichtung zur Herstellung von Sinterteilen
Process and apparatus for producing sintered parts
Procédé et appareil pour la fabrication des pièces frittées
|
(84) |
Benannte Vertragsstaaten: |
|
AT DE ES FR GB IT |
(30) |
Priorität: |
07.06.1995 DE 19521941
|
(43) |
Veröffentlichungstag der Anmeldung: |
|
11.12.1996 Patentblatt 1996/50 |
(73) |
Patentinhaber: |
|
- QMP Metal Powders GmbH
41069 Mönchengladbach (DE)
- BT MAGNET-TECHNOLOGIE GMBH
D-44629 Herne (DE)
|
|
(72) |
Erfinder: |
|
- Lindner, Karl-Heinz
45481 Mülheim (DE)
- Schneider, Rudolf
58730 Fröndenberg (DE)
|
(74) |
Vertreter: Meissner, Peter E., Dipl.-Ing. et al |
|
Meissner & Meissner,
Patentanwaltsbüro,
Hohenzollerndamm 89 14199 Berlin 14199 Berlin (DE) |
(56) |
Entgegenhaltungen: :
EP-A- 0 144 907 DE-A- 2 550 428 DE-A- 3 509 709
|
EP-A- 0 354 389 DE-A- 3 142 359 GB-A- 1 590 113
|
|
|
|
|
- FONDERIE, FONDEUR D'AUJOURD'HUI, Nr. 106, 1.Juni 1991, Seiten 31-39, XP000228780 FARGUES
J: "TRAITEMENT DE TREMPE ETAGEE BAINITIQUE DES FONTES"
- PATENT ABSTRACTS OF JAPAN vol. 009, no. 032 (C-265), 9.Februar 1985 & JP-A-59 177325
(SHIN NIPPON SEITETSU KK), 8.Oktober 1984,
- PATENT ABSTRACTS OF JAPAN vol. 008, no. 069 (M-286), 31.März 1984 & JP-A-58 217601
(KAWASAKI SEITETSU KK), 17.Dezember 1983,
|
|
|
|
Anmerkung: Innerhalb von neun Monaten nach der Bekanntmachung des Hinweises auf die
Erteilung des europäischen Patents kann jedermann beim Europäischen Patentamt gegen
das erteilte europäischen Patent Einspruch einlegen. Der Einspruch ist schriftlich
einzureichen und zu begründen. Er gilt erst als eingelegt, wenn die Einspruchsgebühr
entrichtet worden ist. (Art. 99(1) Europäisches Patentübereinkommen). |
[0001] Die Erfindung betrifft ein Verfahren zur Herstellung von Sinterteilen mit hoher Verschleißfestigkeit
und gleichzeitig guten dynamischen Festigkeitseigenschaften aus gepreßten Formkörpern
gemäß dem Oberbegriff des Patentanspruchs 1 sowie eine Vorrichtung zur Durchführung
dieses Verfahrens.
[0002] Mechanisch hochbeanspruchte Bauteile aus Stahl wie etwa Getriebezahnräder müssen
nicht nur eine hohe Maßgenauigkeit aufweisen, sondern müssen darüber hinaus insbesondere
auch sehr gute dynamische Festigkeitseigenschaften und gleichzeitig eine hohe Verschleißfestigkeit
zeigen. Die Herstellung derartiger Teile durch zerspanende Fertigungsverfahren mit
anschließender Einsatzhärtung erschien lange Zeit als einzig gangbarer Weg. Zur Reduzierung
des Formgebungsaufwandes ist es jedoch auch möglich, pulvermetallurgische Verfahren
anzuwenden. In diesem Zusammenhang ist es bekannt, aus einem diffusionslegierten ölhärtenden
Stahlpulver, dem Graphit in der dem gewünschten C-Gehalt entsprechenden Menge sowie
übliche Schmiermittel zugesetzt wurden, entsprechende Preßkörper als Grünlinge zu
formen, diese im Durchlaufverfahren in einem Ofen zu sintern und anschließend auf
Raumtemperatur abzukühlen. Zur Verbesserung der Maßgenauigkeit erfolgt anschließend
auf einer Kalibrierpresse ein erneuter Preßvorgang. Anschließend wird eine Einsatzhärtung
mit Abschreckung in Öl vorgenommen, dem sich eine Anlaßbehandlung anschließt. Die
so hergestellten Bauteile zeigen ein typisches Anlaßgefüge.
[0003] Ein solches Herstellverfahren liefert Bauteile mit guten statischen (Zugfestigkeit,
Härte, Verschleißfestigkeit) und gleichzeitig auch guten dynamischen Festigkeitseigenschaften.
Trotz des Aufwandes der durch einen zweiten Preßvorgang (Kalibrierung) getrieben wird,
läßt dennoch die Maßgenauigkeit und deren Gleichmäßigkeit gelegentlich Wünsche offen:
Die erreichbare Toleranzklasse beträgt etwa IT10.
[0004] Weiterhin ist es bekannt, Sinterteile aus Preßkörpern herzustellen, die aus fertiglegierten,
lufthärtenden Stahlpulvern gepreßt wurden. Hierbei wird durch Abkühlung an Luft bis
unter die Martensitstarttemperatur ein martensitisches Gefüge erzeugt. Derartige Sinterteile
zeigen wegen ihrer hohen Härte zwar gute Verschleißeigenschaften, sind jedoch aufgrund
der niedrigen Bruchdehnung für dynamische Beanspruchungsarten, wie sie bei Zahnrädern
regelmäßig auftreten, ungeeignet. Auch im Hinblick auf die erreichbare Maßgenauigkeit
(Toleranzklasse IT9) können derartig hergestellte Sinterteile vielfach nicht befriedigen.
[0005] Schließlich ist es aus der DE 40 01 899 C1 bekannt, daß zur Herstellung hochfester
Sinterteile-Grünlinge aus fertiglegiertem Stahlpulver mit einem in Form von Graphitpulver
zugesetztem Massenanteil von 0,3 bis 0,7% Kohlenstoff gepreßt, bei einer Temperatur
im Bereich von 1120 bis 1280 °C gesintert, durch Abkühlung gehärtet und anschließend
angelassen wird.
[0006] EP-A-0 354 389 offenbart ein Verfahren in dem ein Sinterstahlpulver formgepreßt und
gesintert wird. Die Sinterteile werden durch eine Erwärmung in einem Salzbad austenitisiert,
rasch auf eine Temperatur von 280 bis 450°C abgekühlt und in diesem Temperaturbereich
gehalten, um eine bainitische Mikrostruktur des Gefüges zu erreichen.
[0007] Aufgabe der Erfindung ist es, ein Verfahren der gattungsgemäßen Art so zu modifizieren,
daß bei Gewährleistung guter dynamischer Festigkeitseigenschaften und gleichzeitig
guten Verschleißeigenschaften eine deutlich verbesserte Maßhaltigkeit (engere Fertigungstoleranzen)
erreicht wird, wobei der verfahrensmäßige und der anlagentechnische Aufwand möglichst
gering bleiben sollen. Außerdem soll eine Vorrichtung zur Durchführung dieses Verfahrens
angegeben werden.
[0008] Gelöst wird diese Aufgabe durch die kennzeichnenden Merkmale des Patentanspruchs
1. Vorteilhafte Weiterbildungen ergeben sich aus den Unteransprüchen 2 bis 8. Eine
Vorrichtung zur Durchführung des erfindungsgemäßen Verfahrens weist die Merkmale des
Patentanspruchs 9 auf und ist in vorteilhafter Weise durch die in den Unteransprüchen
10 bis 12 anaeaebenen Merkmale weiter ausaestaltbar.
[0009] Nachfolgend wird die Erfindung anhand der Figuren näher erläutert. Es zeigen:
- Fig. 1
- einen schematischen Ablauf des erfindungsgemäßen Verfahrens anhand eines ZTU-Schaubildes
und
- Fig. 2 und 3
- schematische Darstellungen eines Sinterofens zur Durchführung des erfindungsgemäßen
Verfahrens.
[0010] Die Erfindung geht davon aus, daß zur Herstellung der Sinterteile ein an sich bekanntes
Vergütungsstahlpulver verwendet wird, das aus einem fertiglegierten Stahl hergestellt
ist, also (mit Ausnahme des C-Gehalts) eine gleichmäßige Verteilung der Legierungsbestandteile
aufweist. Letzteres muß also nicht erst durch entsprechend zeitlich ausgedehnte Diffusionsvorgänge
während des Sinterns angestrebt werden. Die bisher erforderliche separate Wärmebehandlung
der Sinterteile nach dem Sintern zur Einstellung der guten dynamischen Festigkeitseigenschaften
bei gleichzeitig hoher Verschleißfestigkeit entfällt. Die Einstellung dieser Eigenschaften
wird vielmehr im Zuge der Sinterbehandlung direkt durchgeführt. Hierfür ist es wesentlich,
daß das eingesetzte Stahlpulver aus einem lufthärtenden Werkstoff besteht. Dadurch
kann auf den Einsatz eines aus Umweltschutzgründen ohnehin unerwünschten Ölbades zur
Erzielung eines Abschreckeffektes verzichtet werden.
[0011] Der Kohlenstoffgehalt der Sinterteile wird in üblicher Weise separat in Form von
Graphit zugesetzt, damit das Stahlpulver zur Gewährleistung einer ausreichenden Verpreßbarkeit
weich genug bleibt. Während des Sinterprozesses diffundiert der Graphit in die sich
untereinander verbindenden Pulverpartikel hinein.
[0012] Die Erfindung sieht vor, wie Fig. 1 schematisch zeigt, im unmittelbaren Anschluß
an das Sintern (Abschnitt a) die Sinterteile von der Sintertemperatur bis auf eine
erste Haltetemperatur abzukühlen, die in einer Temperaturspanne von Ar
3 bis maximal 150 °C oberhalb Ar
3 liegt. Die Abkühlung (Abschnitt b) von der Sintertemperatur auf die erste Haltetemperatur
erfolgt zweckmäßig mit einer Abkühlgeschwindigkeit von 0,5 - 1,5 °C/s. Die Sinterteile
werden für etwa 5 - 25 min (erste Haltezeit, Abschnitt c) auf der ersten Haltetemperatur
gehalten. Dadurch wird eine kleinere Austenitkorngröße erreicht.
[0013] In der Austenitisierungsphase (Abschnitt c) empfiehlt es sich, das C-Potential in
der Schutzgasatmosphäre, die während des Sintervorgangs aufrechterhalten werden muß,
ein erhöhtes, eine Aufkohlung bewirkendes C-Potential einzustellen. Hierdurch werden
die Sinterteile in der äußeren Oberfläche mit Kohlenstoff angereichert, so daß im
Oberflächenbereich eine besonders hohe Härte erreichbar ist. Dies ist für eine gute
Verschleißfestigkeit von großer Bedeutung. Im Inneren der Sinterteile bleibt dagegen
ein niedrigerer Kohlenstoffgehalt erhalten und führt zu besonders guten dynamischen
Festigkeitseigenschaften (Härteprofil). Besonders vorteilhaft ist es, die erste Haltetemperatur
in einem Bereich von maximal 50 - 100 °C oberhalb Ar
3 zu wählen. Eine zweckmäßige Dauer der ersten Haltezeit beträgt 10 - 20 min.
[0014] Im unmittelbaren Anschluß an die erste Haltezeit erfolgt durch eine konvektive Gaskühlung
eine beschleunigte Abkühlung (Abschnitt d) bis auf eine zweite Haltetemperatur. Hierfür
empfiehlt sich eine Abkühlgeschwindigkeit im Bereich von 3 - 6°C/s. Diese zweite Haltetemperatur
ist anhand des zum jeweiligen Werkstoff gehörigen ZTU-Schaubilds so ausgewählt, daß
das Gebiet der Ferritbildung gemieden wird und sich ein bainitisches Gefüge auszubilden
beginnt. Die Haltezeit auf dieser zweiten Haltetemperatur (Abschnitt e) wird mindestens
so lange ausgedehnt, bis sich ein Gefügeanteil des Bainits von mindestens 50 % eingestellt
hat. Eine vollständige Umwandlung des Gefüges in Bainit ist jedoch im allgemeinen
nicht erwünscht. Bei maximal 95 % Bainit sollte das Halten auf der zweiten Haltetemperatur
zweckmäßigerweise spätestens beendet werden. Als besonders vorteilhaft hat sich ein
Anteil des Bainit in einer Größenordnung von 60 - 80 % erwiesen. Anschließend werden
die Sinterteile in üblicher Weise bis auf Raumtemperatur abgekühlt (Normalkühlung,
Abschnitt f).
[0015] Überraschenderweise hat sich gezeigt, daß durch die erfindungsgemäße Verfahrensweise
eine besonders gute Teilequalität gewährleistet wird. Es ergibt sich nämlich nicht
nur eine vergleichsweise hohe Maßgenauigkeit, sondern die auftretenden Toleranzen
liegen bedeutend enger als bei der herkömmlichen Herstellungsweise. Anstelle der bisher
bei Ölhärtung und Vergütung erreichbaren Güteklasse IT10 läßt sich nun die Güteklasse
IT8 erreichen. Dies ist um so überraschender, als sogar auf die Durchführung eines
separaten Kalibriervorgangs vollständig verzichtet werden kann. Dadurch wird ein kompletter
aufwendiger Arbeitsschritt eingespart. Weiterhin erübrigt sich der Energie- und Handhabungsaufwand
für ein separates Wärmebehandlungsverfahren.
[0016] In Figur 2 ist die erfindungsgemäße Vorrichtung, die als elektronisch gesteuerter
Durchlauf-Sinterofen ausgebildet ist, in ihrer einfachsten Form schematisch dargestellt.
Durch einen Pfeil an der linken Seite ist angedeutet, daß die Sinterteile in eine
erste Zone eingeführt werden, die als Aufheizzone fungiert und in der die in den Grünlingen
enthaltenen Schmierstoffe (z.B. Wachse) ausgedampft werden. Diese erste Zone wird
daher auch als Entwachszone 1 bezeichnet. Unmittelbar anschließend in Transportrichtung
ist die eigentliche Sinterzone 2 angeordnet, in der die Sinterteile auf Sintertemperatur
(mindestens 1000 °C) über eine ausreichend lange Zeit gehalten werden. Da die Sinterteile
mit einer gleichbleibenden Geschwindigkeit durch die gesamte Anlage bewegt werden,
weist die Sinterzone 2 eine entsprechende Länge auf. Um eine Oxidation der Sinterteile
zu vermeiden, wird in der gesamten Anlage eine sauerstofffreie Atmosphäre (Schutzgasatmosphäre)
aufrechterhalten. Unmittelbar an die Sinterzone 2 schließt sich eine Austenitisierungszone
3 an, in der die Sinterteile zunächst abgekühlt und auf Austenitisierungstemperatur
gehalten werden. Danach folgt eine Schroffkühlzone 4, die mit einer entsprechenden
(nicht dargestellten) Gasdusche ausgestattet ist, um eine ausreichend intensive konvektive
Gaskühlung zu bewirken. Sobald die Sinterteile die zweite Haltetemperatur erreicht
haben, treten sie in die Bainitisierungszone 7 ein und werden über eine zweite Haltezeit
ausreichend lange auf dieser Temperatur gehalten, damit sich ein mindestens 50 % betragender
Bainit-Anteil im Gefüge ausbilden kann. Hierzu weist die Bainitisierungszone 7 eine
entsprechende Länge auf. Nach ausreichender Bainitisierungszeit, möglichst vor Erreichen
eines 95 %-Anteils, treten die Sinterteile in eine abschließende Normalkühlzone 5
ein, wo sie von der Bainitisierungstemperatur bis in die Nähe der Raumtemperatur abgekühlt
werden.
[0017] In Figur 3 ist das Schema einer gegenüber Figur 2 abgewandelten Anlage dargestellt,
die sich dadurch unterscheidet, daß die in die Vorrichtung eingesetzten Grünlinge
wahlweise zwei unterschiedliche Wege durchlaufen können. Die Anordnung von der Entwachszone
1 bis zur Schroffkühlzone 4 stimmt mit der in Figur 1 dargestellten vollständig überein.
Hinter der Schroffkühlzone 4 kann die Materialflußrichtung wahlweise eingestellt werden.
Entweder treten die erzeugten Sinterteile unmittelbar in eine separate Normalkühlzone
5a ein und können die Anlage als "normal" gesinterte, also als in nicht erfindungsgemäßer
Weise hergestellte Teile verlassen; oder sie werden für die erfindungsgemäße Verfahrensfolge
nach Verlassen der Schroffkühlzone 4 über eine wahlweise zuschaltbare Quertransporteinrichtung
6, wie dies durch die eingezeichneten Pfeile angedeutet ist, in eine parallel zum
ersten Teil der gesamten Vorrichtung angeordnete Bainitisierungszone 7 eingeführt.
Zweckmäßigerweise ist die Transportrichtung hier entgegengesetzt zum ersten Teil der
Vorrichtung. Anschließend folgt wiederum eine Normalkühlzone 5b, in der die erfindungsgemäß
behandelten Teile auf Raumtemperatur abgekühlt werden. Diese abgewandelte Vorrichtung
weist also zwei Normalkühlzonen auf. Damit bietet eine solche Anlage eine besondere
Flexibilität im Hinblick auf das zu verarbeitende Produktspektrum. Selbstverständlich
wäre es möglich, die Bainitisierungszone 7 und die zweite Normalkühlzone 5b um 180°
verdreht anzuordnen, also die ursprüngliche Materialflußrichtung beizubehalten. Ebenso
wäre es ohne weiteres möglich, die Anordnung der Normalkühlzone 5a und des aus der
Bainitisierungszone 7 und der Normalkühlzone 5b gebildeten Anlagenstrangs miteinander
zu vertauschen. Die dargestellte Ausführungsform weist jedoch den Vorteil auf, daß
sie eine vergleichsweise kurze Baulänge hat.
[0018] Die Wirksamkeit der Erfindung wird anhand der nachfolgenden beiden Beispiele näher
erläutert.
Vergleichsbeispiel
[0019] Aus einem fertiglegierten Stahlpulver mit der Zusammensetzung Fe -4 Ni - 0,5 Mo,
dem elementar 1 % Cu, 0,6 % Graphit und übliche Schmiermittel zugesetzt wurden, wurden
Preßkörper mit einer Dichte von 6,80-6,90 g/cm
3 hergestellt. Die Teile wurden bei einer Temperatur von 1150 °C während einer Dauer
von 30 min gesintert. Dabei wurde eine aus Endogas bestehende Schutzgasatmosphäre
mit kontrolliertem C-Potential aufrechterhalten. Nach konvektiver Gaskühlung der Teile
(Abkühlgeschwindigkeit 3 - 6 °C/s) unter die Martensitstarttemperatur und anschließende
Normalkühlung bis auf Raumtemperatur wurden folgende Eigenschaften ermittelt:
Zugfestigkeit |
650 N/mm2 |
Härteniveau |
550 - 700 HV1 |
Bruchdehnung A3 |
0,3 - 0,6 % |
[0020] Die Maßhaltigkeit entsprach der Toleranzklasse IT9.
Erfindungsgemäßes Beispiel
[0021] Aus einem fertiglegierten Stahlpulver der Zusammensetzung Fe - 4 Ni - 0,5 Mo, dem
1 % Cu und 0,6 % Graphit sowie übliche Schmiermittel zugesetzt wurden, wurden gleichartige
Preßkörper wie im vorhergehenden Beispiel erzeugt. Die Sinterung wurde bei einer Temperatur
von 1120 °C über eine Dauer von 30 min in einer Endogasatmosphäre mit kontrolliertem
C-Potential durchgeführt. Nach der Austenitisierung erfolgte eine Schroffkühlung mit
einer Abkühlgeschwindigkeit von 3 °C/s sowie die erfindungsgemäße Bainitisierung und
eine anschließende normale Abkühlung bis auf Raumtemperatur. Dabei stellte sich in
den Bauteilen ein bainitisches Gefüge mit folgenden Eigenschaften ein:
Zugfestigkeit |
750 - 800 N/mm2 |
Härteniveau |
350 - 450 HV1 |
Bruchdehnung A3 |
bis 6 % |
[0022] Die Maßgenauigkeit der erfindungsgemäß hergestellten Teile war außerdem signifikant
besser. Sie entsprach der Toleranzklasse IT8.
[0023] Durch das erfindungsgemäße Verfahren lassen sich bei Bauteilen im Sinterzustand gleichzeit
hohe Zähigkeiten mit hohen Festigkeiten kombinieren, die sonst auch mit einer separaten
Wärmebehandlung nicht erreicht werden können, wobei eine deutlich verbesserte Maßtoleranz
gewährleistet werden kann.
1. Verfahren zur Herstellung von Sinterteilen mit hoher Verschleißfestigkeit und guten
dynamischen Festigkeitseigenschaften aus Formkörpern, die als Grünlinge aus einem
fertiglegierten lufthärtenden Vergütungsstahlpulver mit einem in Form von Graphit
zugesetzten Kohlenstoffgehalt von mindestens 0,3 % gepreßt worden sind, durch Sintern
unter Schutzgas bei einer Sintertemperatur von mindestens 1000 °C und nachfolgende
Abkühlung, wobei
- die Sinterteile unmittelbar im Anschluß an das Sintern von der Sintertemperatur
auf eine erste Haltetemperatur im Bereich von Ar3 bis maximal 150 °C oberhalb Ar3 abgekühlt und über eine erste Haltezeit von 5 - 25 min auf dieser Temperatur gehalten
werden, um die Teile zu austenitisieren,
- und die Sinterteile unmittelbar anschließend durch eine konvektive Gaskühlung beschleunigt
bis auf eine zweite Haltetemperatur abgekühlt und über eine zweite Haltezeit auf dieser
Temperatur gehalten werden, wobei die zweite Haltetemperatur in einem Temperaturbereich
liegt, in dem sich ein Bainit-Gefüge ausbildet, und die zweite Haltezeit so bemessen
wird, daß sich ein Gefügeanteil des Bainit von mindestens 50 % einstellt, und
- die Sinterteile danach auf Raumtemperatur abgekühlt werden.
2. Verfahren nach Anspruch 1,
dadurch gekennzeichnet,
daß die erste Haltetemperatur maximal 50 - 100 °C oberhalb Ar3 liegt.
3. Verfahren nach einem der Ansprüche 1 bis 2,
dadurch gekennzeichnet,
daß die erste Haltezeit 10 - 20 min beträgt.
4. Verfahren nach einem der Ansprüche 1 bis 3,
dadurch gekennzeichnet,
daß die konvektive Gaskühlung mit 3 - 6 °C/s erfolgt.
5. Verfahren nach einem der Ansprüche 1 bis 4,
dadurch gekennzeichnet,
daß die Abkühlung auf die erste Haltetemperatur mit 0,5 - 1,5 °C/s erfolgt.
6. Verfahren nach einem der Ansprüche 1 bis 5,
dadurch gekennzeichnet,
daß die zweite Haltezeit nach oben so begrenzt wird, daß der Gefügeanteil des Bainit
höchstens 95 % beträgt.
7. Verfahren nach Anspruch 6,
dadurch gekennzeichnet,
daß die zweite Haltezeit so bemessen wird, daß der Gefügeanteil des Bainit 60-80 %
beträgt.
8. Verfahren nach einem der Ansprüche 1 bis 7,
dadurch gekennzeichnet,
daß die Schutzgasatmosphäre während der Austenitisierungsphase aufrechterhalten wird
und auf ein eine Aufkohlung der Sinterteile bewirkendes C-Potential eingestellt wird.
9. Vorrichtung zur Durchführung des Verfahrens nach Anspruch 1, enthaltend einen als
Durchlaufaggregat ausgebildeten, elektronisch gesteuerten Sinterofen mit einer Sinterzone
(2), einer hinter der Sinterzone (2) angeordneten Schroffkühlzone (4) mit Gaskühlung
und mit einer hinter der Schroffkühlzone (4) angeordneten Normalkühlzone (5), wobei
zwischen der Sinterzone (2) und der Schroffkühlzone (4) eine Austenitisierungszone
(3) angeordnet ist und daß zwischen der Schroffkühlzone (4) und der Normalkühlzone
(5, 5b) eine Bainitisierungszone (7) angeordnet ist.
10. Vorrichtung nach Anspruch 9,
dadurch gekennzeichnet,
daß eine zweite Normalkühlzone (5a) vorgesehen ist, die materialflußtechnisch parallel
zu der ersten Normalkühlzone angeordnet ist, wobei eine der beiden Normalkühlzonen
(5b) über eine Quertransporteinrichtung (6) beschickbar ist und die andere Normalkühlzone
(5a) zur wahlweisen Umgehung der Bainitisierungszone (7) unmittelbar an die Schroffkühlzone
(4) angeschlossen ist.
11. Vorrichtung nach Anspruch 10,
dadurch gekennzeichnet,
daß die Quertransporteinrichtung (6) zwischen der Schroffkühlzone (4) und der Bainitisierungszone
(7) angeordnet ist.
12. Vorrichtung nach Anspruch 11,
dadurch gekennzeichnet,
daß die erste Normalkühlzone (5b) und die Bainitisierungszone (7) eine zur Transportrichtung
der Sinterzone (2), der Austenitisierungszone (3) und der Schroffkühlzone (4) entgegengesetzte
parallele Transportrichtung aufweisen.
1. Process for producing sintered parts with a high wear resistance and good dynamic
strength properties from shaped bodies, which have been compacted as green compacts
from a completely alloyed, air-hardening heat-treatable steel powder with a carbon
content, which is added in the form of graphite, of at least 0.3 %, by sintering under
protective gas at a sintering temperature of at least 1000°C and subsequent cooling,
wherein
- the sintered parts are cooled directly following sintering from the sintering temperature
to a first holding temperature in the range of Ar3 to a maximum of 150°C above Ar3 and held at this temperature over a first holding time of 5 - 25 minutes in order
to austenitize the parts,
- and the sintered parts are directly afterwards cooled in an accelerated manner by
convective gas cooling to a second holding temperature and held at this temperature
over a second holding time, wherein the second holding temperature lies in a temperature
range in which a bainite structure forms, and the second holding time is calculated
so as to produce a structural bainite fraction of at least 50 %, and
- the sintered parts are then cooled to ambient temperature.
2. Process according to Claim 1,
characterised in that the first holding temperature lies a maximum of 50 - 100°C above
Ar3.
3. Process according to any one of Claims 1 and 2,
characterised in that the first holding time is 10 - 20 minutes.
4. Process according to any one of Claims 1 to 3,
characterised in that the convective gas cooling is carried out at 3 - 6°C/s.
5. Process according to any one of Claims 1 to 4,
characterised in that the cooling to the first holding temperature is carried out
at 0.5 - 1.5°C/s.
6. Process according to any one of Claims 1 to 5,
characterised in that the second holding time has an upper limit such that the structural
bainite fraction is at most 95 %.
7. Process according to Claim 6,
characterised in that the second holding time is calculated such that the structural
bainite fraction is 60 - 80 %.
8. Process according to any one of Claims 1 to 7,
characterised in that the protective atmosphere is maintained during the austenitizing
phase and set to a C potential which causes the sintered parts to carburize.
9. Apparatus for carrying out the process according to Claim 1, comprising an electronically
controlled sintering furnace, which is formed as a continuous unit, with a sintering
zone (2), an abrupt cooling zone (4), which is disposed after the sintering zone (2),
with gas cooling, and with a normal cooling zone (5), which is disposed after the
abrupt cooling zone (4), wherein an austenitizing zone (3) is disposed between the
sintering zone (2) and the abrupt cooling zone (4), and a bainitizing zone (7) is
disposed between the abrupt cooling zone (4) and the normal cooling zone (5, 5b).
10. Apparatus according to Claim 9,
characterised in that a second normal cooling zone (5a) is provided which is disposed
parallel to the first normal cooling zone in terms of material flow, wherein one (5b)
of the two normal cooling zones can be charged by a transverse transport device (6)
and the other normal cooling zone (5a) is directly connected to the abrupt cooling
zone (4) to optionally bypass the bainitizing zone (7).
11. Apparatus according to Claim 10,
characterised in that the transverse transport device (6) is disposed between the
abrupt cooling zone (4) and the bainitizing zone (7).
12. Apparatus according to Claim 11,
characterised in that the first normal cooling zone (5b) and the bainitizing zone
(7) have a transport direction which is opposite and parallel to the transport direction
of the sintering zone (2), the austenitizing zone (3) and the abrupt cooling zone
(4).
1. Procédé pour la fabrication de pièces frittées ayant une résistance élevée à l'usure
et de bonnes propriétés de résistance mécanique dynamiques, à partir de corps moulés,
qui ont été pressés comme ébauches de compact en une poudre d'acier ayant subi un
traitement par trempe et revenu, durcie à l'air, complètement alliée, ayant une teneur
en carbone, ajoutée sous forme de graphite, d'au moins 0,3 %, par frittage sous un
gaz protecteur à une température de frittage d'au moins 1000°C et refroidissement
suivant,
- les pièces frittées étant directement refroidies, comme suite au frittage, de la
température de frittage à une première température de maintien dans la plage de Ar3 à au maximum 150°C au-dessus de Ar3 et étant maintenues, pendant un premier temps de maintien de 5 à 25 minutes, à cette
température, pour austéniser les pièces, et
- les pièces frittées étant ensuite directement refroidies, par un refroidissement
au gaz par convection de façon accélérée jusqu'à une seconde température de maintien
et maintenues pendant un second temps de maintien à cette température, la seconde
température de maintien se trouvant dans une plage de températures dans laquelle se
forme une structure de bainite, et le second temps de maintien étant tel que l'on
obtient une proportion de structure de bainite d'au moins 50 %, et
- les pièces frittées étant ensuite refroidies à la température ambiante.
2. Procédé selon la revendication 1,
caractérisé en ce que la première température de maintien vaut au maximum de 50 à
100°C au-dessus de Ar3.
3. Procédé selon une des revendications 1 à 2,
caractérisé en ce que le premier temps de maintien vaut de 10 à 20 minutes.
4. Procédé selon une des revendications 1 à 3,
caractérisé en ce que le refroidissement au gaz par convection est effectué à 3 -
6°C/s.
5. Procédé selon une des revendications 1 à 4,
caractérisé en ce que le refroidissement à la première température de maintien est
effectué à 0,5 - 1,5°C/s.
6. Procédé selon une des revendications 1 à 5,
caractérisé en ce que le second temps de maintien présente une limite supérieure telle
que la proportion de structure de bainite vaut au plus 95 %.
7. Procédé selon la revendication 6,
caractérisé en ce que le second temps de maintien est tel que la proportion de structure
de bainite vaut de 60 à 80 %.
8. Procédé selon une des revendications 1 à 7,
caractérisé en ce que l'atmosphère de gaz protecteur est conservée pendant la phase
d'austénitisation et est réglée à un potentiel C agissant sur la carburation des pièces
frittées.
9. Dispositif pour la mise en oeuvre du procédé selon la revendication 1, comportant
un four de frittage commandé électroniquement, réalisé comme appareil en continu,
ayant une zone de frittage (2), une zone de refroidissement brusque (4) à refroidissement
au gaz, agencée derrière la zone de frittage (2), et une zone de refroidissement normal
(5) agencée derrière la zone de refroidissement brusque (4), une zone d'austénitisation
(3) étant agencée entre la zone de frittage (2) et la zone de refroidissement brusque
(4), et une zone de bainitisation (7) étant agencée entre la zone de refroidissement
brusque (4) et la zone de refroidissement normal (5, 5b).
10. Dispositif selon la revendication 9,
caractérisé en ce qu'une seconde zone de refroidissement normal (5a) est prévue qui
est agencée parallèlement à la première zone de refroidissement normal par technique
de flux de matière, une des deux zones de refroidissement normal (5b) pouvant être
chargée par l'intermédiaire d'un dispositif de transport transversal (6) et l'autre
zone de refroidissement normal (5a) étant raccordée directement à la zone de refroidissement
brusque (4) pour contourner au choix la zone de bainitisation (7).
11. Dispositif selon la revendication 10,
caractérisé en ce que le dispositif de transport transversal (6) est agencé entre
la zone de refroidissement brusque (4) et la zone de bainitisation (7).
12. Dispositif selon la revendication 1 1,
caractérisé en ce que la première zone de refroidissement normal (5b) et la zone de
bainitisation (7) présentent un dispositif de transport parallèle, opposé à la direction
de transport de la zone de frittage (2), de la zone d'austénitisation (3), et de la
zone de refroidissement brusque (4).
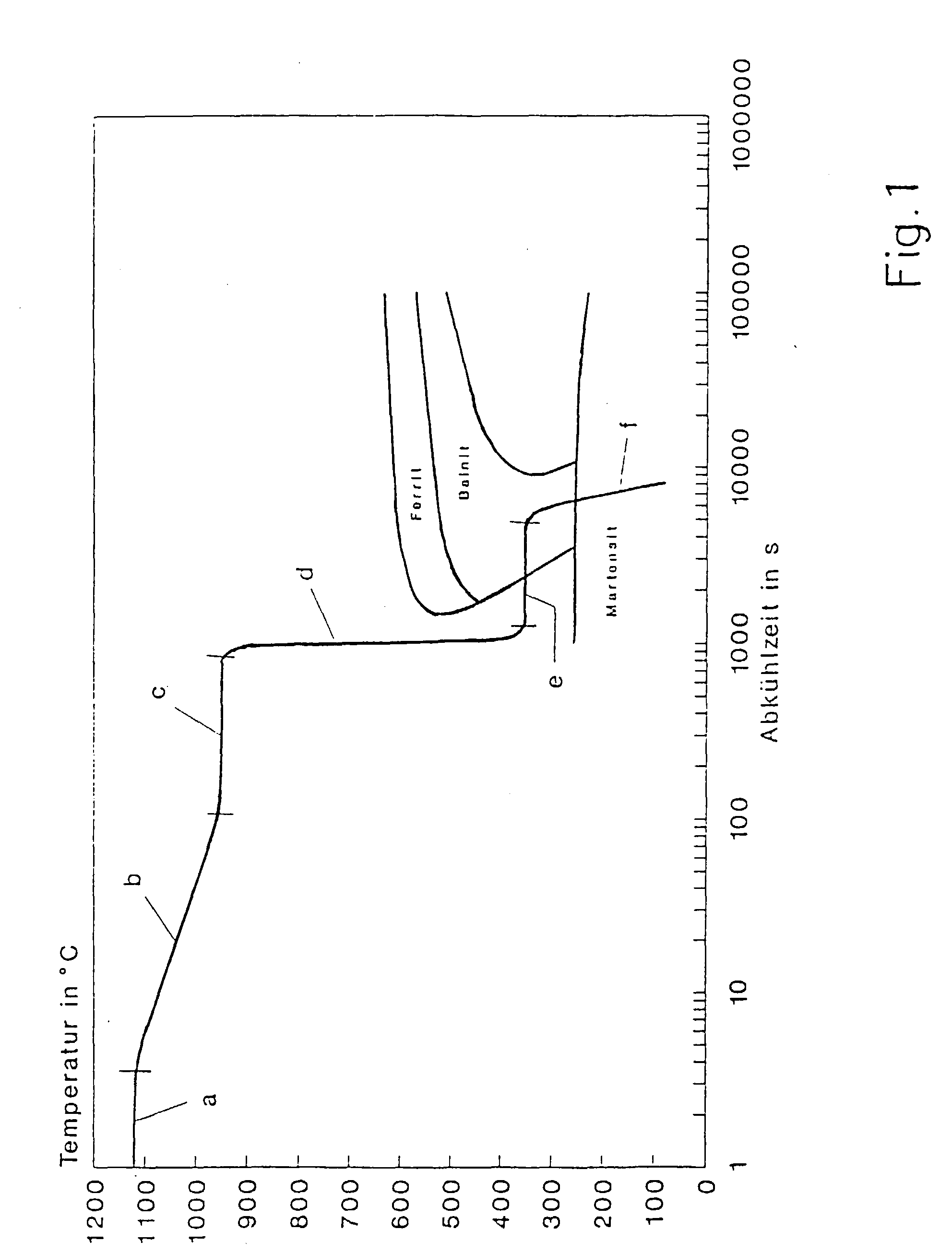
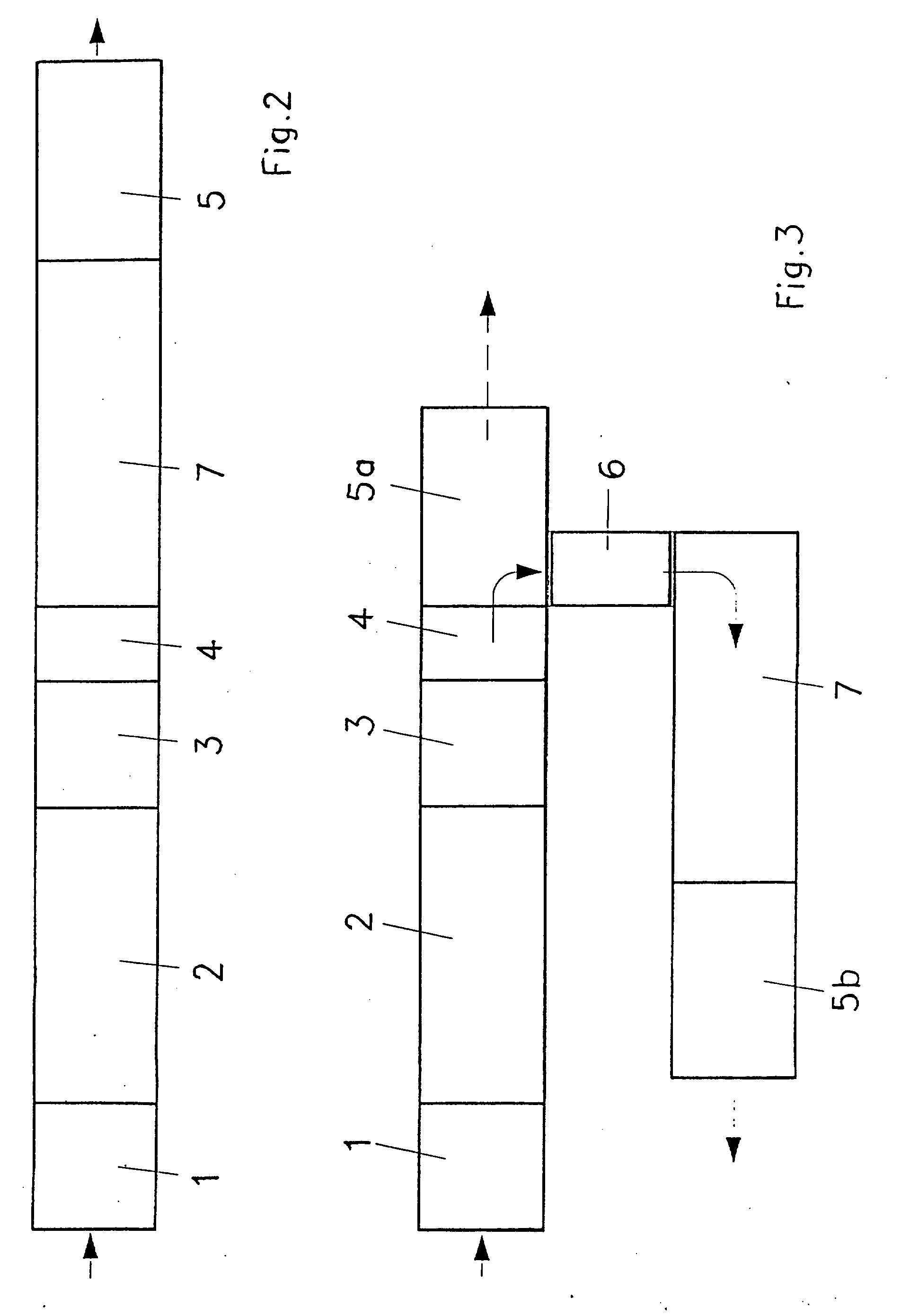