(19) |
 |
|
(11) |
EP 0 761 826 B1 |
(12) |
EUROPÄISCHE PATENTSCHRIFT |
(45) |
Hinweis auf die Patenterteilung: |
|
23.05.2001 Patentblatt 2001/21 |
(22) |
Anmeldetag: 23.08.1996 |
|
|
(54) |
Verfahren zur Herstellung nahtloser Rohre aus ODS Werkstoffen
Method for manufacturing ODS seamless pipes
Procédé de fabrication d'un tube ODS sans soudure
|
(84) |
Benannte Vertragsstaaten: |
|
AT DE ES FR GB IT SE |
(30) |
Priorität: |
28.08.1995 AT 45795
|
(43) |
Veröffentlichungstag der Anmeldung: |
|
12.03.1997 Patentblatt 1997/11 |
(73) |
Patentinhaber: PLANSEE Aktiengesellschaft |
|
6600 Reutte, Tirol (AT) |
|
(72) |
Erfinder: |
|
- Sporer, Dieter, Dr.
6675 Tannheim (AT)
|
(74) |
Vertreter: Lohnert, Wolfgang, Dr. |
|
Plansee Aktiengesellschaft 6600 Reutte 6600 Reutte (AT) |
(56) |
Entgegenhaltungen: :
EP-A- 0 274 631 EP-A- 0 447 858 GB-A- 629 131 US-A- 4 034 588
|
EP-A- 0 398 121 EP-A- 0 456 119 GB-A- 2 036 622
|
|
|
|
|
|
|
|
|
Anmerkung: Innerhalb von neun Monaten nach der Bekanntmachung des Hinweises auf die
Erteilung des europäischen Patents kann jedermann beim Europäischen Patentamt gegen
das erteilte europäischen Patent Einspruch einlegen. Der Einspruch ist schriftlich
einzureichen und zu begründen. Er gilt erst als eingelegt, wenn die Einspruchsgebühr
entrichtet worden ist. (Art. 99(1) Europäisches Patentübereinkommen). |
[0001] Die Erfindung betrifft ein Verfahren zur Herstellung nahtloser Rohre aus Werkstoffen
gemäß dem Oberbegriff vom Anspruch 1, die durch mechanische Umformung in Kombination
mit einer rekristallisierenden Wärmebehandlung ein stark gestrecktes Grobkorngefüge
ausbilden.
[0002] Derartige Werkstoffe sind dispersionsverfestigte Metalle, Metallegierungen oder intermetallische
Phasen, die aufgrund ihrer hervorragenden mechanischen Eigenschaften bei hohen Temperaturen,
insbesondere für thermisch und mechanisch hoch beanspruchte Bauteile verwendet werden.
Eine wichtige Gruppe dieser Werkstoffe sind die sogenannten ODS-Superlegierungen auf
Eisen-, Nickel- oder Kobaltbasis, bei denen als Dispersoide Oxidteilchen verwendet
werden. Die ODS-Superlegierungen erweitern das Temperatureinsatzgebiet von hitzebeständigen
Werkstoffen bis auf etwa 1350°C.
[0003] Allen diesen Werkstoffen ist gemeinsam, daß sie ihre guten Hochtemperatureigenschaften,
insbesondere ihre gute Kriechfestigkeit, durch die Ausbildung eines langgestreckten
Grobkorngefüges erreichen. Zur Ausbildung dieses Grobkorngefüges müssen die Werkstoffe
mit einem hohen Umformgrad mechanisch umgeformt werden und einer anschließenden Glühbehandlung
zur Rekristallisation unterzogen werden. Durch diese direktionale Rekristallisation
zeigen die Werkstoffe je nach Legierung und Herstellungsart eine ziemlich ausgeprägte
Richtungsabhängigkeit der mechanischen Eigenschaften, beispielsweise der Hochtemperatur-Kriechfestigkeit.
Die besten Festigkeitseigenschaften werden immer in Richtung der Hauptumformrichtung,
also parallel zur Gefügestreckung, beobachtet. In den Richtungen orthogonal zu dieser
Hauptumformrichtung zeigen bisher auch diese Werkstoffe nur vergleichsweise ungünstige
Festigkeitswerte bei hohen Temperaturen.
[0004] Bei innendruckbeaufschlagten Rohren liegt die größte mechanische Beanspruchung in
Umfangsrichtung vor. Die Materialspannungen in Umfangrichtung sind doppelt so hoch
wie jene in Rohrlängsrichtung. Für innendruckführende Rohre, die hohen Temperaturen
ausgesetzt sind, bieten sich daher die genannten Werkstoffe mit einem gestreckten
Grobkorngefüge dann an, wenn dabei sichergestellt ist, daß die hohe,Gefügestreckung
in Rohrumfangsrichtung eingestellt wird, um das Warmfestigkeitspotential dieser Werkstoffe
voll auszunützen.
[0005] Bisher wurden nahtlose Rohre aus den genannten Werkstoffen beispielsweise durch Tieflochbohren
aus Stangenmaterial oder durch Warmstrangpressen mit oder ohne anschließendes Kaltreduzieren,
wie etwa das Rohrziehen oder Rohrpilgerschrittwalzen hergestellt. Der Nachteil dieser
Verfahren liegt jedoch darin, daß die Hauptumformrichtung in axialer Richtung des
Rohres liegt und damit auch die starke Gefügestreckung bzw. Gefügeorientierung in
dieser Richtung liegt, was mit einer relativ geringen Festigkeit in der am höchsten
beanspruchten Rohrumfangsrichtung verbunden ist.
[0006] In "Development of Ferritic ODS Tubes for Heat Exchangers Operating Above 1100°C",
B. Kazimierzak, J. M. Prignon et al., "Structural Applications of Mechanical Alloying",
ASM, Ohio (1990), Seiten 137 - 145 wird ein Heißstrangpreßverfahren zur Herstellung
von nahtlosen Rohren aus ODS-Werkstoffen beschrieben, die die gewünschte hochgestreckte
Gefügestruktur in Rohrumfangsrichtung zeigen.
Nachteilig bei diesem Verfahren ist, daß dessen erfolgreiche Anwendung von einer Vielzahl
von Parametern abhängt. Der Prozeß, vor allem die Temperaturführung, muß in sehr engen
Grenzen kontrolliert werden, um die Kornstreckung in Umfangsrichtung in reproduzierbarer
Weise zu erhalten. Dadurch wird das Verfahren aufwendig und teuer.
[0007] Darüberhinaus schränkt das Verfahren die erzeugbaren Rohrformate über die maximal
zur Verfügung stehenden Preßkräfte industrieller Strangpressen sowohl nach oben als
auch nach unten stark ein. Der wesentliche Nachteil dieses Verfahrens liegt aber darin,
daß nur relativ dickwandige Rohre hergestellt werden können, was aus Wärmeleitungsgründen
für Rohre in Rohrbündel-Wärmetauschern oder einfach aus Gründen des erhöhten Materialaufwandes
trotz optimierter Gefügestruktur häufig keine technisch oder wirtschaftlich befriedigende
Rohrfertigung erlaubt. Heute lassen sich über das Heißstrangpreßverfahren mit oder
ohne nachgeschaltete Kaltverarbeitungsverfahren Rohre mit Außendurchmessern zwischen
25 und 40 mm bei Wandstärken zwischen 2,5 und 5 mm herstellen.
[0008] Die Aufgabe der vorliegenden Erfindung ist die Bereitstellung eines Verfahrens zur
Herstellung nahtloser Rohre aus ODS Werkstoffen, bei denen ein stark gestrecktes Gefüge
in Rohrumfangsrichtung orientiert ist, das auf einfache Weise eine gute Reproduzierbarkeit
dieser Gefügestrukturen gewährleistet und mit dem auch dünnwandige Rohre mit Wandstärken
unterhalb von 2,5 mm über einen großen Durchmesserbereich hergestellt werden können.
[0009] Gelöst wird die Aufgabe durch ein Verfahren gemäß Anspruch 1.
[0010] Das napf-oder rohrförmige Ausgangsteil wird auf einer konventionellen Drückmaschine
auf einen Dorn aufgebracht und mittels einer oder vorzugsweise mehrerer Drückrollen
in einem oder mehreren Überläufen im Außendurchmesser reduziert. Dadurch wird die
Wandstärke verringert und gleichzeitig die Länge des Ausgangsnapfes bzw. der Ausgangsbüchse
erhöht, wodurch ein rohrförmiger Körper entsteht. Auf diese Art und Weise sind Rohre
mit Wandstärken zwischen 0,3 und 2,5 mm und Durchmessern im Bereich von 20 bis 450
mm herstellbar.
[0011] Die Kinematik des Zylinder-Drückwalzprozesses ist derart, daß der Materialfluß während
der Umformung fast ausschließlich in axialer Richtung erfolgt. Um Teile mit möglichst
maßgenauem Innendurchmesser zu erhalten muß der tangentiale Materialfluß (Materialfluß
in Rohrumfangsrichtung) durch Abstimmung der Abmessungen des Ausgangsteiles auf die
verwendeten Drückwalzen und die Anzahl der Überläufe auf ein Minimum reduziert werden.
[0012] Für den Fachmann völlig überraschend war es, daß es trotz der Tatsache, daß der Materialfluß
beim Zylinder-Drückwalzen hauptsächlich in axialer Richtung erfolgt, die Rohre die
nach dem erfindungsgemäßen Verfahren hergestellt werden, nach der Rekristallisationsglühung
ein hochgestrecktes Grobkorngefüge aufweisen, das in Rohrumfangsrichtung verläuft.
Dies wird durch einfache Anwendung des Zylinder-Drückwalzens innerhalb der bekannten
Verfahrensgrenzen ohne Anwendung zusätzlicher oder ohne aufwendige Optimierung einzelner
Verfahrensparameter erreicht, sodaß eine gute Reproduzierbarkeit der Rohre durch das
erfindungsgemäße Verfahren gewährleistet ist.
[0013] Das erfindungsgemäße Verfahren bietet darüberhinaus den Vorteil, daß hohe Querschnittsreduktionen
pro Drückwalzdurchgang sowie auch hohe Gesamtquerschnittsabnahmen ohne Anwärmung und
ohne Zwischenglühungsschritte erreicht werden können. Dies war insbesondere bei Anwendung
des Verfahrens bei ferritischen ODS-Werkstoffen nicht zu erwarten, da diese Werkstoffe
ein spröd-duktil Übergangsverhalten zeigen, sodaß derartige Werkstoffe für die Umformung
normalerweise stets auf mindestens 60 - 100° vorgewärmt werden müssen, um nach der
Umformung mit Sicherheit rißfreie Teile zu ergeben. Dadurch, daß das erfindungsgemäße
Verfahren praktisch bei allen Werkstoffen bei Raumtemperatur angewandt werden kann,
ohne daß Werkstück und Drückdorn aufwendig vorgewärmt werden müssen, ergibt sich eine
wirtschaftliche Herstellung und ausgezeichnete Reproduzierbarkeit der Rohre. Die gute
Reproduzierbarkeit betrifft dabei sowohl die gute Maßhaltigkeit als auch die metallurgische
Qualität im Hinblick auf das in Rohrumfangsrichtung gestreckte Grobkorngefüge nach
der Rekristallisationsglühung.
[0014] Neben der Rekristallisationsglühung können zwischen einzelnen Verformungsschritten
auch Zwischenglühungen in Form von Entspannungs- bzw. Erholungsglühungen eingelegt
werden.
[0015] Als verfestigende Teilchen haben sich insbesondere die Oxide eines oder mehrerer
Metalle aus der Gruppe Yttrium, Aluminium, Lanthan, Cer und Zirkon bewährt.
[0016] Eine Variante eines erfindungsgemäß einsetzbaren Werkstoffes ist es, die verfestigenden
Teilchen im Werkstoff derart auszubilden, daß zum Werkstoff reaktive metallische Zusätze
zugegeben werden, die während der Verarbeitung des Werkstoffes und/oder während einer
Wärmebehandlung in die entsprechenden Oxid-, Nitrid- oder Karbidteilchen umgewandelt
werden.
[0017] Als Metallegierungen haben sich insbesondere solche auf der Basis von Eisen, Nickel
oder Kobalt bewährt.
Als Eisenbasislegierungen haben sich jene mit der Zusammensetzung
6 - 30 Gew.% Cr, 0 - 10 Gew.% Al, 0 - 2 Gew.% Ti,
0 - 10 Gew.% Mo, 0 - 10 Gew.% W, 0 - 10 Gew.% Ta, 0,1 - 2 Gew.% von einem oder mehreren
Oxiden aus der Gruppe Y, Al, La, Ce und Zr, sowie Fe als Rest und als Nickelbasislegierungen
jene mit der Zusammensetzung 6 - 38 Gew.% Cr, 0,1- 7 Gew.% Al,
0 - 2 Gew.% Ti, 0 - 5 Gew.% Mo, 0 - 5 Gew.% W, 0 - 5 Gew.% Ta, 0,1 - 2 Gew.% von einem
oder mehreren Oxiden aus der Gruppe Y, Al, La, Ce und Zr, sowie Ni als Rest, insbesondere
bewährt.
[0018] Im folgenden wird die Erfindung anhand von Beispielen und Figuren näher erläutert:
[0019] Es zeigen:
- Figur 1
- Querschliff von einzelnen Abschnitten des nach Beispiel 1 hergestellten Rohres in
16-facher Vergrößerung
- Figur 2
- Querschliff von einzelnen Abschnitten des nach Beispiel 2 hergestellten Rohres in
16-facher Vergrößerung
BEISPIEL 1:
[0020] Aus einer ODS-Legierung mit der chemischen Zusammensetzung 19 Gew.% Cr, 5,5 Gew.%
Al, 0,5 Gew.% Ti, 0,5 Gew.% Y
2O
3 und Rest Fe wurde in der Schrittfolge Mechanisches Legieren der Pulverausgangsstoffe,
heißisostatisches Verdichten der Pulver, anschließende Warmumformung durch Rundschmieden,
Aufbohren des geschmiedeten Zylinders und abschließendes Überdrehen der inneren und
äußeren Mantelflächen, ein büchsenförmiger Rohling mit Innendurchmesser 60 mm und
Wandstärke 5 mm angefertigt. Dieser Rohling wurde auf einer konventionellen 3-Rollen-CNC-Drückmaschine
in nur zwei Überläufen bei gleichbleibendem Innendurchmesser von der Ausgangswandstärke
auf eine Endwandstärke von 1,25 mm umgeformt. Das so hergestellte Rohr zeigte eine
hervorragende Oberflächenqualität sowie Maßhaltigkeit. Es wurde anschließend ohne
Befund mit dem Farbeindringverfahren auf Risse untersucht. Schließlich wurde das Rohr
bei einer Temperatur von 1380 °C während einer Stunde rekristallisierend an Luft geglüht.
Während dieser Glühung bildete sich eine sehr dünne und fest anhaftende Al
2O
3-Schicht aus. Eine metallographische Untersuchung des geglühten Rohres ergab ein grobkörniges
Rekristallisationsgefüge mit hoher Gefügestreckung in Rohrumfangsrichtung entsprechend
Figur 1.
BEISPIEL 2:
[0021] Aus einer ODS-Legierung derselben Zusammensetzung wie im Beispiel 1 wurde durch Mechanisches
Legieren der Pulverausgangsstoffe, heißisostatisches Pressen und anschließendes konventionelles
Lochpressen ein Hohlformat hergestellt. Aus diesem Rohling wurde in der Folge durch
Überdrehen ein büchsenförmiger Rohling mit 60 mm Innendurchmesser und 5 mm Wandstärke
hergestellt. Der so erhaltene Rohling zeigt eine feinkörnige Gefügestruktur. Er wurde
durch Drückwalzen in nur drei Überläufen von der Ausgangswandstärke 5 mm auf eine
Endwandstärke von 0,7 mm umgeformt. Dies entspricht einem Gesamtumformgrad von 84
% relativer Querschnittsabnahme, der ohne Anwärmung und ohne Zwischenglühen erreicht
wurde.
Das Rohr wurde anschließend ohne Befund sowohl mit dem Farbeindringverfahren als auch
mit Wirbelstromprüfung auf Risse untersucht. In der Folge wurde das Rohr bei 1380
°C während einer Stunde rekristallisierend an Luft geglüht. Dabei bildete sich die
in Figur 2 dargestellte Gefügestruktur aus.
1. Verfahren zur Herstellung nahtloser Rohre mit in Rohrumfangsrichtung stark gestrecktem
Gefüge, gefertigt aus metallischen Werkstoffen, die mit Oxid- und/oder Karbidteilchen
verfestigt sind und die durch mechanische Umformung in Kombination mit einer rekristallisierenden
Wärmebehandlung ein stark gestrecktes Grobkorngefüge ausbilden,
dadurch gekennzeichnet,
dass ein napf- oder büchsenförmiges Ausgangsteil in unrekristallisiertem Zustand durch
Drückwalzen nach DIN 8583, Gruppe 2.1.1.3.2.2. mit einem Umformgrad von mindestens
30 % und bei üblichen Maßnahmen zur Minimierung des tangentialen Materialflusses in
die gewünschte Rohrform gebracht wird und dass der Werkstoff durch eine Zwischenglühung
zwischen einzelnen Verformungsschritten oder durch eine Endglühung nach Abschluss
der Verformung grobkörnig rekristallisiert wird.
2. Verfahren zur Herstellung nahtloser Rohre nach Anspruch 1, dadurch gekennzeichnet,
daß die verfestigenden Teilchen Oxide eines oder mehrerer Metalle aus der Gruppe Yttrium,
Aluminium, Lanthan, Cer und Zirkon sind.
3. Verfahren zur Herstellung nahtloser Rohre nach Anspruch 1, dadurch gekennzeichnet,
daß die verfestigenden Teilchen aus reaktiven metallischen Zusätzen gebildet werden,
die während der Verarbeitung des Werkstoffes und/oder während einer Wärmebehandlung
in die entsprechenden Oxid-, Nitrid-oder Karbidteilchen umgewandelt werden.
4. Verfahren zur Herstellung nahtloser Rohre nach Anspruch 1, dadurch gekennzeichnet,
daß als Metallegierung eine dispersionsverfestigte Legierung auf Basis Eisen, Nickel
oder Kobalt verwendet wird.
5. Verfahren zur Herstellung nahtloser Rohre nach Anspruch 4, dadurch gekennzeichnet,
daß die Legierung aus 6 - 30 Gew.% Cr, 0 - 10 Gew.% Al, 0 - 2 Gew.% Ti, 0 - 10 Gew.%
Mo, 0 - 10 Gew.% W, 0 - 10 Gew.% Ta, 0,1 - 2 Gew.% von einem oder mehreren Oxiden
der Metalle aus der Gruppe Y, Al, La, Ce und Zr, sowie Fe als Rest besteht.
6. Verfahren zur Herstellung nahtloser Rohre nach Anspruch 4, dadurch gekennzeichnet,
daß die Legierung aus 6 - 38 Gew.% Cr, 0,1 - 7 Gew.% Al, 0 - 2 Gew.% Ti, 0 - 5 Gew.%
Mo, 0 - 5 Gew.% W, 0 - 5 Gew.% Ta, 0,1 - 2 Gew.% von einem oder mehreren Oxiden der
Metalle aus der Gruppe Y, Al, La, Ce und Zr, sowie Ni als Rest besteht.
1. Method of manufacturing seamless pipes, which have an extremely elongated grain structure
in pipe circumferential direction, from metallic materials which are strengthened
with oxide and/or carbide particles and which through mechanical transformation combined
with a recrystallizing heat treatment form a coarse extremely elongated grain structure,
characterized in
that a cup- or bush-shaped starting part in a non-recrystallized state is brought
by flow-turning according to DIN 8583, Group 2.1.1.3.2.2. with a degree of transformation
of at least 30% and with conventional measures to minimize the tangential flow of
material into the desired tubular shape and that the material is recrystallized in
a coarse-grained manner by an intermediate annealing between individual deformation
steps or by a final annealing upon completion of deformation.
2. Method of manufacturing seamless pipes according to claim 1, characterized in that
the strengthening particles are oxides of one or more metals from the group yttrium,
aluminium, lanthanum, cerium and zirconium.
3. Method of manufacturing seamless pipes according to claim 1, characterized in that
the strengthening particles are formed from reactive metallic additives, which during
the processing of the material and/or during a heat treatment are converted into the
corresponding oxide, nitride or carbide particles.
4. Method of manufacturing seamless pipes according to claim 1, characterized in that,
as a metal alloy, an iron-, nickel- or cobalt-based dispersion strengthened alloy
is used.
5. Method of manufacturing seamless pipes according to claim 4, characterized in that
the alloy comprises 6 - 30 wt.% Cr, 0 - 10 wt.% Al, 0 - 2 wt.% Ti, 0 - 10 wt.% Mo,
0 - 10 wt.% W, 0 - 10 wt.% Ta, 0.1 - 2 wt.% of one or more oxides of the metals from
the group Y, Al, La, Ce and Zr, the rest being Fe.
6. Method of manufacturing seamless pipes according to claim 4, characterized in that
the alloy comprises 6 - 38 wt.% Cr, 0.1 - 7 wt.% Al, 0 - 2 wt.% Ti, 0 - 5 wt.% Mo,
0 - 5 wt.% W, 0 - 5 wt.% Ta, 0.1 - 2 wt.% of one or more oxides of the metals from
the group Y, Al, La, Ce and Zr, the rest being Ni.
1. Procédé de fabrication de tubes sans soudure, à texture fortement étirée dans ux
de formage d'au moins 30% et en prenant les dispositions habituelles pour minimiser
le flux tangentiel de matière, et en ce que la matière est recristallisée en gros
grains par un recuit intermédiaire entre étapes individuelles de formage ou par un
recuit final après la fin du formage.
2. Procédé de fabrication de tubes sans soudure selon la revendication 1, caractérisé
en ce que les particules consolidantes sont des oxydes d'un ou plusieurs des métaux
du groupe formé par l'yttrium, l'aluminium, le lantux de formage d'au moins 30% et
en prenant les dispositions habituelles pour minimiser le flux tangentiel de matière,
et en ce que la matière est recristallisée en gros grains par un recuit intermédiaire
entre étapes individuelles de formage ou par un recuit final après la fin du formage.
2. Procédé de fabrication de tubes sans soudure selon la revendication 1, caractérisé
en ce que les particules consolidantes sont des oxydes d'un ou plusieurs des métaux
du groupe formé par l'yttrium, l'aluminium, le lanthane, le cérium et le zirconium.
3. Procédé de fabrication de tubes sans soudure selon la revendication 1, caractérisé
en ce que les particules consolidantes consistent en additifs métalliques réactifs
qui sont transformés en particules correspondantes d'oxydes, de nitrures ou de carbures
pendant le formage de la matière et/ou pendant le traitement thermique.
4. Procédé de fabrication de tubes sans soudure selon la revendication 1, caractérisé
en ce qu'un alliage consolidé par dispersion à base de fer, de nickel ou de cobalt
est utilisé comme alliage métallique.
5. Procédé de fabrication de tubes sans soudure selon la revendication 4, caractérisé
en ce que l'alliage se compose de 6 à 30% en poids de Cr, de 0 à 10% en poids d'AI,
de 0 à 2% en poids de Ti, de 0 à 10% en poids de Mo, de 0 à 10% en poids de W, de
0 à 10% en poids de Ta, de 0,1 à 2% en poids d'un ou plusieurs oxydes des métaux du
groupe formé par Y, Al, La, Ce et Zr, ainsi que de Fe pour le solde.
6. Procédé de fabrication de tubes sans soudure selon la revendication 4, caractérisé
en ce que l'alliage se compose de 6 à 38% en poids de Cr, de 0,1 à 7% en poids d'AI,
de 0 à 2% en poids de Ti, de 0 à 5% en poids de Mo, de 0 à 5% en poids de W, de 0
à 5% en poids de Ta, de 0,1 à 2% en poids d'un ou plusieurs oxydes des métaux du groupe
Y, Al, La Ce ou Zr, ainsi que Ni pour le solde.
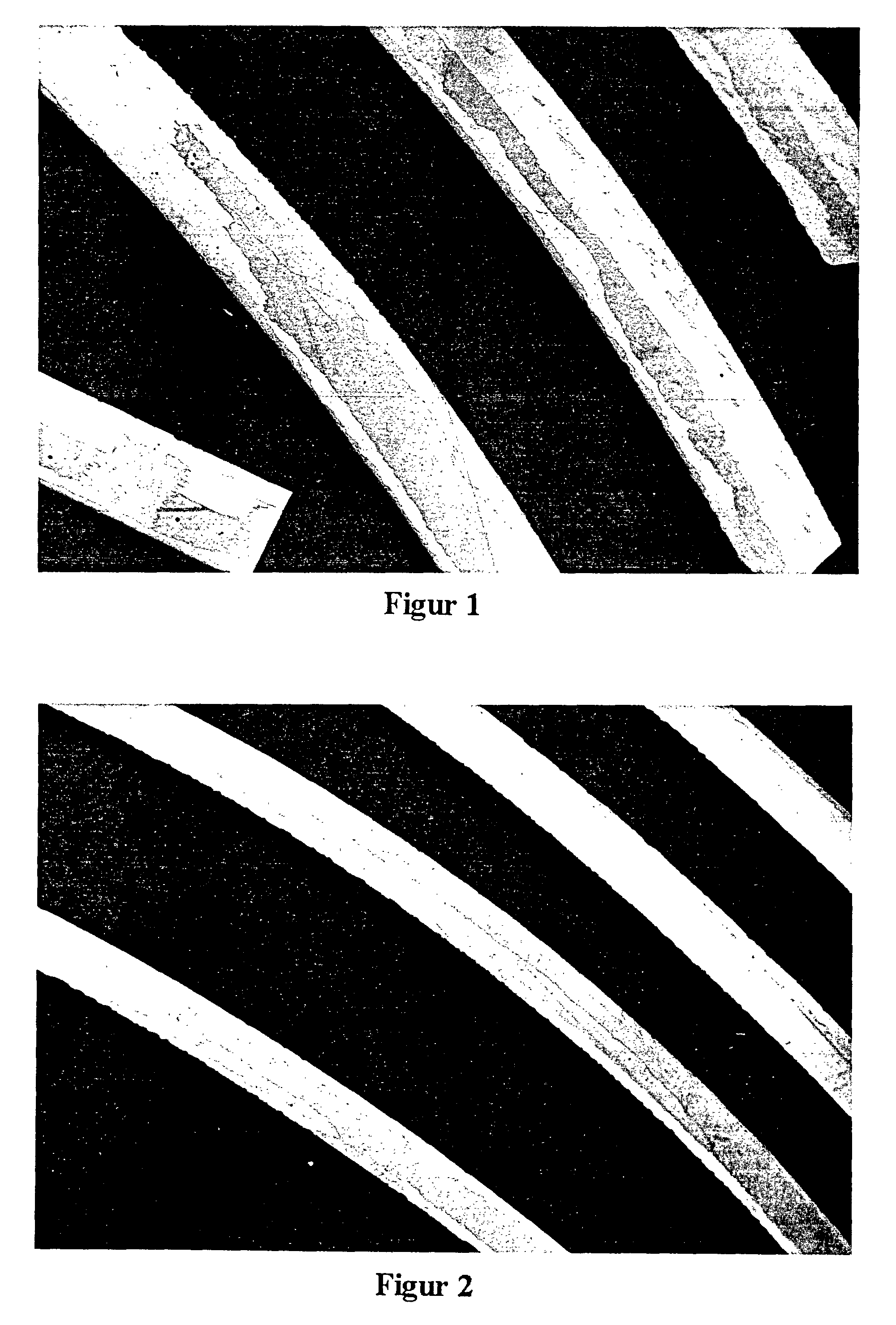