[0001] Die Erfindung betrifft eine Anspinnvorrichtung gemäß dem Oberbegriff des Anspruchs
1.
[0002] Mit steigenden Anforderungen an den Garnherstellungsprozeß werden auch an die Erzeugung
der Anspinner immer höhere Ansprüche gestellt. Der Vorgang der Bildung von Anspinnern
nach Fadenunterbrechungen, das Anspinnen, wird an den einzelnen Spinnstellen der Offenend-Rotorspinnmaschinen
üblicherweise von einer entlang der Spinnmaschine wandernden Anspinneinrichtung, dem
sogenannten Anspinnwagen, vorgenommen.
[0003] Zum Beispiel nach einem Fadenbruch, der das Anspinnen auslöst, dauert es unterschiedlich
lange, bis an der Spinnstelle wieder angesponnen wird. Beim Fadenbruch wird der Fasereinzug
abgeschaltet. Die nachlaufende Auflösewalze löst jedoch noch Fasern aus dem Faserbart
heraus. Um gleiche Bedingungen und damit eine möglichst gleiche Voreinspeisemenge
zu erreichen, wird daher vor jedem Anspinnen der Faserbart egalisiert. Das Anspinnen
beginnt mit dem Rotorstart. Aus detektierten drehzahlabhängigen Impulsen berechnet
zum Beispiel eine Mikroprozessorsteuerung die Beschleunigung für den Rotorhochlauf,
damit nach einer konstanten Zeit die eingestellte Anspinn-Rotordrehzahl erreicht wird,
und stellt aus der Beschleunigung den Startzeitpunkt für eine Voreinspeisung von Fasern
fest. In der Zeit nach der Faserbartegalisierung am vorgelegten Faserband und dem
Einschalten des Einzuges zur betriebsmäßigen Fasereinspeisung werden aus dem Faserbart
des Faserbandes wiederum Fasern ausgekämmt und über den Rotorrand des stehenden Rotors
abgesaugt. Dies ruft während des Hochlaufs der Einzugsgeschwindigkeit des Faserbandeinzuges
eine gewisse Verzögerung im Erreichen des erforderlichen Faserflusses und gegebenenfalls
eine Dünnstelle nach dem Anspinner hervor. Die Voreinspeisung erfolgt während einer
vorbestimmten Zeit und wird dann abgeschaltet. Dabei läßt sich die Menge der eingespeisten
Fasern neben der Zeitdauer der Voreinspeisung auch durch die Einstellung der Einzugsgeschwindigkeit
steuern. Nach dem Abschalten der Voreinspeisung und der Rückführung des sogenannten
Oberfadens wird die Fasereinspeisung kurz vor dem Start des Fadenabzuges wieder eingeschaltet,
um die Verzögerung auszugleichen. Diese jetzt eingespeiste Fasermenge legt sich im
Rotor auf die voreingespeiste Fasermenge ab. Der Start des Fadenabzuges geschieht
nach einer bestimmten Verweilzeit des Fadens in der Rotorrille, in der das Anspinnende
des Oberfadens Zeit hat, den Faserring aufzubrechen und sich mit den eingespeisten
Fasern zu verbinden. Die Abzugsgeschwindigkeit stellt sich auf einen Wert ein, der
der momentanen Rotordrehzahl bei Einhaltung der gewünschten Garndrehung entspricht.
Bis zum Erreichen der Betriebsrotordrehzahl folgt die Abzugsgeschwindigkeit der Erhöhung
der Rotordrehzahl. Neben dem Nachlauf des Faserflusses nach Abschalten des Einzuges
und dem verzögerten Anlauf nach Einschalten des Einzuges kann der Faserfluß auch bei
Erhöhung der Einzugsgeschwindigkeit mit Verzögerung reagieren. Das kann dazu führen,
daß der Faden während des Hochlaufs des Rotors zu dünn wird. Besonders ausgeprägt
tritt dies bei niedrigen Einzugsgeschwindigkeiten auf. Um diese unerwünschte Dickenabweichung
zu vermeiden, kann eine Einzugsaufaddierung vorgenommen werden. Dabei wird die Einzugsgeschwindigkeit
der Faserspeiseeinrichtung gegenüber einem Sollwert erhöht, um jeweils die erforderliche
Fasermenge im Rotor ankommen zu lassen. Eine Dünnstelle im Faden kann auch bei vorgenommener
Einzugsaufaddierung noch auftreten, wenn die Einzugsaufaddierung in zu geringem Umfang
erfolgt. Ist die Einzugsaufaddierung zu groß bemessen, wird eine Dickstelle im Faden
bewirkt, die ebenfalls unerwünscht ist. Es wird daher angestrebt, die Einzugsaufaddierung
von Beginn an möglichst genau zutreffend zu bemessen. Die Aufaddierung nimmt mit zunehmendem
Vorschubweg des Faserbandes ab. Nach einer Einzugslänge, die der Stapellänge entspricht,
ist die Einzugsaufaddierung beendet. Die Fasermenge wird ab diesem Zeitpunkt ohne
Aufaddierung eingespeist. Derartige Einzugsaufaddierungen während des Anspinnens sind
beispielsweise in der DE 40 30 100 A1 oder der Veröffentlichung Raasch et. al. "Automatisches
Anspinnen beim OE-Rotorspinnen", MELLIAND Textilberichte 4/1989, Seiten 251 bis 256,
beschrieben.
[0004] Mit den steigenden Anforderungen an die Garnqualität und insbesondere mit der Forderung
nach höheren Spinnverzügen und kleineren Rotoren sind die Anforderungen an die Genauigkeit
der Aufaddierungslänge merklich gestiegen. Bei einem 100fachen Verzug bewirkt ein
Fehler von 0,5 mm in der Bestimmung der Aufaddierungslänge beim Faserbandeinzug eine
auf den Faden bezogene Fehlerlänge von 50 mm. Bei einem 350fachen Verzug sind dies
bereits 175 mm. Diese Beispiele machen deutlich, wie hoch die Anforderungen an die
Genauigkeit bei der Bestimmung der Aufaddierungslänge sind.
[0005] Nach dem oben genannten Stand der Technik wird bereits der erste Anspinner mit einer
Einzugsaufaddierung erzeugt. Damit sollen Dünnstellen mit der damit verbundenen Gefahr
von Fadenbruch und Störungen beim Anpinnen vermieden werden. Zur Bestimmung der Einzugsaufaddierung
wird zunächst ein von der mittleren Stapellänge der verwendeten Fasern abhängiger
Erfahrungswert herangezogen. Während die Stapellänge bei synthetischen Garnen bekannt
ist, läßt sie sich bei Baumwoll-oder Mischgarnen nur über eine aufwendige Laborprüfung
hinreichend genau ermitteln. Da die Stapellänge proportional in die Bestimmung der
Aufaddierungslänge eingeht, führen Abweichungen zwischen der für die Berechnung eingesetzten
Stapellänge und der tatsächlichen Stapellänge zu einem Fehler bei der Bestimmung der
Aufaddierungslänge mit den oben beschriebenen Folgen, die sich besonders bei hohen
Verzügen auswirken.
[0006] Weitere Kriterien, wie zum Beispiel die Auflösewalzengarnitur, die Auflösewalzendrehzahl
und die Rotorhochlaufzeit (mit ihrem Einfluß auf die Auskämmzeit), üben Einfluß auf
den erforderlichen Umfang der Einzugsaufaddierung aus. Dieser Einfluß läßt sich aber
nur empirisch, durch Erzeugung und Auswertung einer Vielzahl weiterer Anspinner, bestimmen.
Ein ausreichend genauer Umfang der Einzugsaufaddierung für einen qualitativ zufriedenstellenden
Anspinner läßt sich somit nur nach einer relativ aufwendigen, insbesondere zeitaufwendigen,
Optimierungsphase ermitteln. Die Optimierung erfordert manuellen Einsatz des Bedienungspersonals.
Die Qualität des Ergebnisses hängt maßgeblich von der Erfahrung des Bedienungspersonals
ab.
[0007] Der Erfindung liegt die Aufgabe zugrunde, die Erzeugung von Anspinnern zu verbessern.
[0008] Diese Aufgabe wird erfindungsgemäß durch eine Vorrichtung mit den Merkmalen des Anspruchs
1 gelöst.
[0009] Vorteilhafte Ausgestaltungen der Erfindung sind Gegenstand der Unteransprüche.
[0010] Überraschend zeigt sich, daß die Optimierungsphase bei der Erzeugung von Anspinnern
durch die zusätzliche Testphase mit Testanspinnerbildung nicht verlängert, sondern
deutlich verkürzt wird.
[0011] Die Einzugsaufaddierung läßt sich dabei sehr präzise bestimmen.
[0012] Das Erzeugen von Testanspinnern ohne Einzugsaufaddierung in einer Testphase, wobei
die Länge einer dadurch in Fadenlaufrichtung gesehen nach dem Testanspinner hervorgerufenen
Dünnstelle bestimmt und der Umfang der Einzugsaufaddierung aus der ermittelten Länge
der Dünnstelle bestimmt ist, ermöglicht es, mit einer einzigen Einstellung von Anspinnerparametern
in der Testphase zu hochwertigen Anspinnern gleich ab Beginn des Spinnbetriebs zu
gelangen, die sich durch eine weitestgehende Angleichung von Oberfadendurchmesser
und Durchmesser des an den Anspinner anschließenden neu gesponnenen Fadenabschnitts
auszeichnen.
[0013] Aus dem vorgenannten Stand der Technik geht hervor, daß zum Beispiel durch Einsatz
von Erfahrungswerten bei Anspinnparametern versucht wird, bereits bei der Erzeugung
des ersten Anspinners Dünnstellen zu vermeiden oder wenigstens zu verringern und den
Faden im Anspinnerbereich zu vergleichmässigen. Dies soll der Vermeidung von Störungen
und einer Steigerung der Produktivität dienen. Mit der Testanspinnererzeugung in einer
Testphase und der anschließenden Entfernung des Testanspinners wird die Anspinneroptimierung
nicht nur deutlich beschleunigt, sondern zusätzlich enthält der im Spinnbetrieb erzeugte
Faden ausschließlich bereits hochwertige Anspinner und weist damit von Anfang an eine
erhöhte Garnqualität auf.
[0014] Mit der erfindungsgemäßen Ausführung kann der Automatisierungsgrad für automatisches
Anspinnen gesteigert werden. Das Bedienungspersonal wird dadurch entlastet und für
andere Aufgaben frei.
[0015] Der Umfang der Einzugsaufaddierung ist von der Länge der Einzugsaufaddierung abhängig.
Die Länge der Dünnstelle, von der auf die Länge der Einzugsaufaddierung geschlossen
wird, läßt sich durch Auswertung der gemessenen Fadendurchmesser ermitteln. Dazu können
die im Bereich der Dünnstelle gemessenen Fadendurchmesser mit einem aus dem Durchmesser
des Oberfadens abgeleiteten Vergleichsdurchmesser verglichen und das Ende und damit
die Länge der Dünnstelle durch das Erreichen einer Übereinstimmung ermittelt werden.
Der Vergleich kann mittels eines Komparators durchgeführt werden. Alternativ kann
der anhand der gemessenen Durchmesserwerte bestimmte Durchmesserverlauf als über die
Fadenlänge aufgetragener Kurvenverlauf dargestellt werden, der gemittelte Anstieg
des Kurvenverlaufs im Endbereich der Dünnstelle ermittelt und der Schnittpunkt von
gemitteltem Anstieg und dem vom Oberfadendurchmesser abgeleiteten Vergleichsdurchmesser
als Endpunkt der Dünnstelle bestimmt werden.
[0016] Mit einer während der Testphase wirksamen Reduzierung des Verzugs läßt sich vermeiden,
daß die Dünnstelle nach dem Testanspinner derart ausgeprägt ist, daß ein Fadenbruch
und damit der Fall droht, daß ein meßbarer Testanspinner beziehungsweise eine meßbare
Dünnstelle nicht mehr zur Verfügung stehen würde. Die Verzugsreduzierung erlaubt es
zusätzlich, daß auch bei sehr hohen Verzügen der Faden den aus der Normalfadenstärke
abgeleiteten Vergleichsdurchmesser innerhalb eines begrenzten Anspinnprüfer-Meßfensters
sicher annimmt beziehungsweise erreicht und damit ein Ausmessen der Dünnstelle in
jedem Fall erfolgen kann.
[0017] Ein Algorithmus, der die Stapellänge, die hierfür auch ohne nachteilige Folgen nur
annähernd durch Schätzung ermittelt werden kann, und einen begrenzten, vorgewählten
Meßbereich für das Messen des Fadendurchmessers berücksichtigt, läßt vorteilhaft die
einfache, schnelle und automatisierbare Bestimmung des Mindestausmaßes der Verzugsreduzierung
zu. Die Parameter können dazu der Steuerungseinrichtung oder einer damit verbundenen
Recheneinrichtung vorgegeben oder aus einem Datenspeicher abgerufen werden.
[0018] Bei Nennverzügen, bei denen zum Beispiel der Verzug zwischen 50fach und 100fach liegt,
und wobei die Verwendung des Algorithmus, der die Stapellänge und den begrenzten Meßbereich
für das Messen des Fadendurchmessers berücksichtigt, keine odei nur eine geringfügige
Verzugsreduzierung ergibt, kann der reduzierte Verzug vereinfacht durch Multiplikation
des Nennverzuges mit einem vorgegebenen Faktor, der etwas kleiner als Eins ist, bestimmt
werden.
[0019] Eine Steigerung in der Präzision des Auswerteergebnisses wird erreicht, wenn mehrere
Testanspinner mit gleichen vorgegebenen Parametern überprüft werden und daraus anschließend
oder fortlaufend ein mittleres Anspinner- beziehungsweise Dünnstellenprofil gebildet
wird. Hierdurch werden sowohl natürliche Faserband- oder Fasermischungsschwankungen
als auch Streuungen, die durch Unterschiede bei den Spinnmitteln hervorgerufen werden,
in die Bewertung einbezogen. Gleichzeitig läßt sich über die Mittelung eine Glättung
der Anspinnerprofile erzielen, wodurch das Ausmessen der Dünnstelle leichter, präziser
und sicherer erfolgen kann. Die Testanspinner können dazu an mehreren verschiedenen
Spinnstellen erzeugt werden.
[0020] Den mit steigendem Nennverzug erhöhten Anforderungen an die Genauigkeit bei der Bestimmung
der Einzugsaufaddierung und damit an die Präzision der Anspinnerprofile wird dadurch
Rechnung getragen, daß mit steigendem Nennverzug auch die Zahl der zur Mittelwertbildung
herangezogenen Testanspinner steigt.
[0021] Mit einer Einrichtung zur Visualisierung des Anspinnerprofils kann vorteilhaft eine
Kontrolle der automatischen Auswertung von Anspinnerprofilen in der Testphase durchgeführt
werden, zum Beispiel bei auftretenden Anspinnerwiederholungen oder dem Abschalten
von Spinnstellen beim Anspinnen.
[0022] Mit der vorliegenden Erfindung läßt sich die Optimierungsphase bei der Erzeugung
von Anspinnern signifikant verkürzen und das Anspinnerprofil verbessern. Die Erfindung
stellt einen Schritt in Richtung einer auf der Basis der vom Anspinnprüfer ermittelten
Qualitätsdaten sich selbst kalibrierenden und optimierenden automatischen Serviceeinrichtung,
zum Beispiel eines Anspinnwagens, dar. Die Produktivität und damit die Wirtschaftlichkeit
des Garnherstellungsprozesses wie auch die Garnqualität können mittels der Erfindung
vorteilhaft erhöht werden.
[0023] Weitere Einzelheiten der Erfindung werden anhand der Darstellung der Figuren erläutert.
[0024] Es zeigt:
- Fig. 1
- eine vereinfachte schematische Darstellung einer Spinnstelle einer Offenend-Rotorspinnmaschine,
- Fig. 2
- ein schematisches Ablaufdiagramm zur Bestimmung der Aufaddierungslänge,
- Fig. 3
- das Profil eines einzelnen Testanspinners,
- Fig. 4
- ein gemitteltes Anspinnerprofil aus einer Vielzahl von Testanspinnern,
- Fig. 5
- ein gemitteltes Anspinnerprofil aus Anspinnern mit erfindungsgemäßer Bestimmung der
Einzugsaufaddierung.
[0025] Das Ausführungsbeispiel der Fig. 1 zeigt eine Spinnstelle 1 einer Offenend-Rotorspinnmaschine.
Die Spinnstelle 1 weist eine Auflöseeinrichtung 2 auf, in die mittels einer durch
einen stufenlos regelbaren Elektromotor 3 angetriebenen Einzugswalze 4 ein Faserband
5 eingeführt wird. Das Faserband 5 wird einer sich im Gehäuse 6 drehenden Auflösewalze
vorgelegt, die das zugeführte Faserband 5 in einzelne Fasern 8 auflöst. Die vereinzelten
Faser 8 gelangen durch den Faserleitkanal 9 auf die kegelförmig ausgebildete Rutschfläche
10 des Rotors 11 und von dort in die Fasersammelrille 12. Der Rotor 11 ist auf einer
Welle 13 befestigt, die in einer Laufscheiben-Lagerung 14 gelagert und mittels eines
Tangentialriemens 15 angetrieben ist. In der Fasersammelrille 12 bildet sich der Faden
16, der durch das Fadenabzugsrohr 17 hindurch in Richtung des Pfeiles 18 mit Hilfe
einer Abzugsvorrichtung 19 abgezogen wird.
[0026] Die Abzugsvorrichtung 19 weist ein Walzenpaar auf. Während des normalen Spinnbetriebs
folgt der Faden 16' nach der Abzugsvorrichtung 19 der unterbrochenen Linie und wird
fortlaufend auf eine hier nicht dargestellte Kreuzspule aufgewickelt. Zum Anspinnen
wird den Spinnstellen jeweils eine wanderfähige Anspinneinrichtung zugestellt, die
den Anspinnvorgang durchführt. Die als Anspinnwagen (ASW) ausgebildete Anspinneinrichtung
ist hier nicht näher dargestellt.
[0027] Nach Beendigung des Anspinnvorgangs wird überprüft, ob ein ordnungsgemäßes Anspinnen
erfolgt ist. Dazu wird der Faden 16 streckenweise im Anspinnwagen geführt, was durch
die Fadenauslenkung zwischen der Abzugsvorrichtung 19 und einem Fadenführer 20 schematisch
angedeutet wird. Der Faden 16 verläuft im hier nicht näher dargestellten Anspinnwagen
zwischen zwei Fadenführern 21 und 22 vor einer Sensoreinrichtung 23, mit der das Fadenprofil
gemessen wird.
[0028] Die Prüfsignale für die längenbezogenen Fadenprofilmeßwerte werden einer Steuerungseinrichtung
24 zugeführt. Wird eine Überschreitung vorgegebener Grenzwerte festgestellt, so wird
daraus auf einen nicht mehr tolerierbaren Fehler des Fadenprofils geschlossen. Es
wird ein Schneidsignal ausgelöst, das an eine Schneideinrichtung 25 weitergegeben
wird, die den Faden 16 schneidet. Eine Unterbrechung des Fadens 16 wird spätestens
dann erkannt, wenn vor der Sensoreinrichtung kein Faden mehr detektiert wird. Ein
Fehlersignal löst daraufhin einen neuen Anspinnvorgang aus.
[0029] Die Überprüfung des Fadenprofils erfolgt am beschleunigten Faden. Nach dem Anspinnen
wird der Faden, entsprechend der sich steigernden Rotordrehzahl, mit einer zunehmenden
Geschwindigkeit aus dem Fadenabzugsrohr 17 mittels der Abzugsvorrichtung 19 abgezogen.
Damit die Meßfrequenz der Sensoreinrichtung 23 auf die sich ändernde Geschwindigkeit
des beschleunigten Fadens 16 eingestellt werden kann, werden von der von einem Antrieb
26 angetriebenen Fadenabzugswalze der Abzugsvorrichtung 19 mittels eines Sensors 27
Impulse abgegriffen. Diese Impulse geben Auskunft über die Abzugsgeschwindigkeit des
Fadens 16. Die Sensorsignale werden der Steuerungseinrichtung 24 zugeleitet, welche
die Meßfrequenz des Sensors 27 steuert und sie der Fadenabzugsgeschwindigkeit anpaßt.
Die Steuerungseinrichtung 24 ist mit einer Einrichtung 28 zur Visualisierung des Anspinnerprofils
und über die Leitung 29 mit weiteren Modulen der Spinnmaschine verbunden.
[0030] Weitere Einzelheiten derartiger Spinnstellen können beispielsweise der DE 40 30 100
A1 oder der Veröffentlichung Raasch et. al. "Automatisches Anspinnen beim OE-Rotorspinnen",
MELLIAND Textilberichte 4/1989, Seiten 251 bis 256, entnommen werden.
[0031] Bei Änderung der Spinnparameter, beispielsweise nach einem Partiewechsel, wird eine
Einzugsaufaddierung jeweils neu bestimmt.
[0032] In der nach dem bekannten Stand der Technik üblichen Praxis wird zur Bestimmung der
Einzugsaufaddierung beziehungsweise der Aufaddierungslänge L
A in einem ersten Ansatz der Nennverzug V
NENN, die mittlere Stapellänge L
ST, herangezogen und die fehlende Fasermenge dabei in Form eines Faktors, zum Beispiel
als Auskämmanteil A
A, berücksichtigt. Die Aufaddierungslänge L
AE, bezogen auf das Faserband, ergibt sich somit aus der Formel:

[0033] Zur Bestimmung der durch Auskämmen des Faserbartes fehlenden Fasermenge wird üblicherweise
ein Erfahrungswert für den Auskämmanteil A
A benutzt. Erfahrungsgemäß werden etwa 20 % der Stapellänge durch Auskämmen eingekürzt.
Bei einer Stapellänge L
ST von 25 mm ergibt sich die theoretische, zu berücksichtigende Aufaddierungslänge L
AE wie folgt:

[0034] Beginnend mit dem Anspinner wird üblicherweise ein Meßbereich von circa 600 bis 700
mm Fadenlänge nach dem Anspinner überwacht und zur Bildung eines Anspinnerprofils
herangezogen, das zum Beispiel zur Qualitätsüberwachung des Anspinners ausgewertet
wird.
[0035] Fig. 2 zeigt ein Ablaufdiagramm, nach dem eine erfindungsgemäße Bestimmung der Aufaddierungslänge
erfolgen kann. Ist die Einzugsaufaddierung, beispielsweise nach einem Partiewechsel
oder einer Änderung der Spinnparameter, neu zu bestimmen, wird ein spezielles Programm
30 verwendet.
[0036] Nach dem Start 301 des Sonderprogramms des Anspinnwagens (ASW) erfolgt zunächst die
Festlegung 302 der Anzahl der Testanspinner n
AT. Je nach Höhe des Nennverzuges V
NENN, der für den Spinnbetrieb vorgesehen ist, sollten 15 bis 50 Testanspinner in der
Testphase erzeugt werden. Mit steigendem Verzug sollte auch die Anzahl der Testanspinner
n
AT steigen. Im Ausführungsbeispiel der Fig. 2 ist bei einem Verzug V
NENN = 125 die Anzahl der Testanspinner n
AT = 22.
[0037] Anschließend erfolgt nach dem Algorithmus
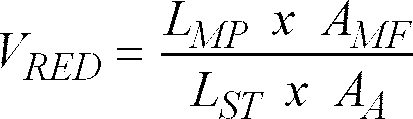
eine Berechnung und Festlegung 303 eines reduzierten Verzuges V
RED, wobei in die Berechnung die Stapellänge L
ST, der Auskämmanteil A
A, die Länge L
MF des Meßbereiches für den Testanspinner (das sogenannte Meßfenster) und ein Anteilsfaktor
A
MF des Meßbereiches am Meßfenster einfließen.
[0038] Mit dem Anteilsfaktor A
MF, der dafür unter Eins liegen muß, wird der Verzug V
RED so festgelegt, daß die Dünnstelle nach dem Testanspinner mit Sicherheit vollständig
im Meßfenster liegt und bis zu ihrem Ende ausgewertet werden kann.
[0040] Dieser reduzierte Verzug V
RED wird im Ausführungsbeispiel für die Testphase zur Erzeugung von Testanspinnern festgelegt.
Die Stapellänge muß hierbei, wenn sie nicht bekannt ist, nicht aufwendig im Labor
bestimmt werden, sondern kann geschätzt werden. Während eine fehlerhafte Stapellänge
bei einer Bestimmung der Einzugsaufaddierungslänge nach dem oben geschilderten Stand
der Technik zu unzulässigen Fehlern führt, ist dies bei der erfindungsgemäßen Bestimmung
nicht der Fall.
[0041] Anschließend erfolgt eine Festlegung 304 der Einzugsaufaddierungslänge L
A auf Null. Falls das Normalprogramm zur Erzeugung von Anspinnern eine Zusatzdrehung
DR
Z enthält, wird auch diese auf Null gesetzt. Danach erfolgt das Festlegen 305 beziehungsweise
das Aktivieren des Verzugs V
RED für die Voreinspeisung. Die Erzeugung von Testanspinnern nach dem Sonderprogramm
30 kann nunmehr durchgeführt werden.
[0042] Um einen Testanspinner zu erzeugen, erfolgt eine Anfahrt 306 des Anspinnwagens zur
nächsten Spinnstelle. Dort erfolgt der Start 307 des Anspinnvorgangs. Anschließend
erfolgt eine Überprüfung 308, ob ein Testanspinner vorhanden ist. Ergibt die Überprüfung
308, daß kein Testanspinner mit einer Dünnstelle 32 vorhanden ist, erfolgt eine Überprüfung
309, ob die Anzahl der Anspinnversuche n
AV an dieser Spinnstelle = 3 ist. Ist dies nicht der Fall, erfolgt die Einleitung 308
einer Wiederholung des Anspinnens durch den Start 307 des Anspinnvergangs an dieser
Spinnstelle.
[0043] Führt die Überprüfung 309 zu dem Ergebnis, daß die Anzahl der Anpinnversuche n
Av = 3 ist, erfolgt eine Auslösung 311 eines Alarmsignals dadurch, daß die jeweilige
Spinnstelle in Rotlicht gesetzt wird. Anschließend wird eine Anfahrt 306 zur nächsten
Spinnstelle durchgeführt.
[0044] Ergibt die Überprüfung 308, daß ein Testanspinner 33 mit Dünnstelle 32 vorhanden
ist, wird die Speicherung 312 des Anspinnerprofils und anschließend eine Unterbrechung
313 des Fadenlaufs vorgenommen.
[0045] Das Anspinnerprofil eines einzelnen Testanspinners 33 ist als Kurvenverlauf in Fig.
3 dargestellt, wobei der Fadendurchmesser D
F als Funktion der Fadenlänge L
F dargestellt ist. Der Fadendurchmesser D
F ist dabei ins Verhältnis zu einer Normalfadenstärke D
FN gesetzt und in Prozent der Normalfadenstärke D
FN angegeben. Die Fadenlänge L
F ist in mm angegeben. Die Dünnstelle 32 nach dem Testanspinner 33, innerhalb der der
Fadendurchmesser D
F die Normalfadenstärke D
FN merklich unterschreitet, ist in Fig. 3 erkennbar. Der Beginn 34 des Testanspinners
33 ist durch eine kurze Dünnstelle vor dem steilen Anstieg 35 des Fadendurchmessers
DF auf den Durchmesser des Testanspinners 33 charakterisiert.
[0046] Anschließend erfolgt die Überprüfung 314, ob die Gesamtzahl n
AG der abgespeicherten Testanspinner gleich der vorbestimmten Anzahl n
AT der Testanspinner ist. Ist dies nicht der Fall, erfolgt die Anfahrt 306 zur nächsten
Spinnstelle. Ergibt die Überprüfung 314, daß n
AG und n
AT übereinstimmen, erfolgt eine Mittelung 315 aller abgespeicherten Testanspinnerprofile.
Ein derartig gemitteltes Anspinnerprofil zeigt Fig. 4. Der Kurvenverlauf der Fig.
4 ist gegenüber dem Kurvenverlauf in Fig. 3 weitgehend geglättet und damit einer Auswertung
besser zugänglich. Die Dünnstelle 36 im gemittelten Anspinnerprofil nach dem Anspinner
37 ist in Fig. 4 deutlich ausgeprägt sichtbar.
[0047] Anschließend erfolgt das Ausmessen 316 der Dünnstelle 36 im gemittelten Anspinnerprofil.
Beim Ausmessen 316 der Dünnstelle 36, bei deren Entstehung der reduzierte Verzug V
RED aktiviert war, ist zu berücksichtigen, daß der Normalfadenstärke D
FN ein Oberfadenende als Normal zugrunde liegt, das ohne den reduzierten Verzug V
RED erzeugt ist. Daher ist das Ende 38 der Dünnstelle 36 durch Erreichen eines Vergleichsdurchmessers
D
V charakterisiert, der größer ist als die Normalfadenstärke D
FN.
[0048] Der Vergleichsdurchmesser D
V ergibt sich nach der Formel

[0049] F
FN ist ein Faktor, der aus dem Nennverzug V
NENN, der während des normalen Spinnbetriebs wirksam ist, und dem reduzierten Verzug V
RED folgendermaßen bestimmt wird:

[0050] Der Vergleichsdurchmesser D
V zur Bestimmung der Länge L
DST der Dünnstelle 36 im gemittelten Anspinnerprofil ergibt sich für das Ausführungsbeispiel
der Fig. 4 als

[0051] Damit liegt der Vergleichsdurchmesser D
V bei 111,8 % der Normalfadenstärke D
FN.
[0052] Die Länge L
DST, die zur Bestimmung der Aufaddierungslänge L
AE herangezogen wird, ist im gemittelten Anspinnerprofil als der Abstand zwischen dem
Ende 38 der Dünnstelle 36 und dem Beginn 39 des Anspinners 37 definiert. Der Beginn
39 des Anspinners 37 ist durch eine kurze Dünnstelle charakterisiert. Das Erreichen
des Vergleichsdurchmesser D
V und damit das Ende 38 der Dünnstelle 36 liegt vor, wenn der Kurvenverlauf im gemittelten
Anspinnerprofil nach dem Anspinner 37 erstmals wieder den in Fig. 4 durch eine horizontale
Linie angedeuteten Vergleichsdurchmesser D
V schneidet. Alternativ kann der anhand der gemessenen Durchmesserwerte bestimmte Kurvenverlauf
dargestellt werden, der gemittelte Anstieg 40 des Kurvenverlaufs im Endbereich der
Dünnstelle 36 ermittelt und der Schnittpunkt vom gemittelten, als strichpunktierte
Gerade dargestellten Anstieg 40 und dem als horizontale Linie angedeuteten Vergleichsdurchmesser
D
V als Endpunkt der Dünnstelle 36 bestimmt werden. Im Ausführungsbeispiel der Fig. 4
beträgt die Länge L
DST zwischen dem Beginn 39 des Anspinners 37 und dem Ende 38 der Dünnstelle 36 am Schnittpunkt
544 mm.
[0053] Für die Aufaddierungslänge L
AE, die für den normalen Spinnbetrieb beim Faserbandeinzug zu berücksichtigen ist, gilt
nun
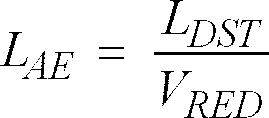
[0054] Bei


ergibt sich für das Ausführungsbeispiel

[0055] Die mit dem Rechenschritt 317 bestimmte Aufaddierungslänge L
AE beträgt demnach 5,44 mm.
[0056] In der Fig. 2 bezeichnet 318 das Einsetzen des Ergebnisses der Aufaddierungslängenbestimmung
als Parameter für den normalen Spinnbetrieb. Anschließend erfolgt eine Wiederherstellung
319 von Betriebsparametern des Anspinnwagens, die für die Erzeugung von Testanspinnern
in der Testphase geändert wurden, wie zum Beispiel der Parameter "Verzug", sowie darauffolgend
die Wiederherstellung 320 des Normalprogramms des Anspinnwagens für den Spinnbetrieb.
Für den normalen Spinnbetrieb erfolgt nunmehr der Start 31 des Normalprogramms des
Anspinnwagens.
[0057] In einer nicht dargestellten alternativen Ausbildung des speziellen Programms 30
zur Bestimmung der Aufaddierungslänge erfolgt an den Spinnstellen die Auslösung 311
eines Rotlicht-Alarmsignals nur dann, wenn kein Testanspinner zustande kommt.
[0058] In einer weiteren nicht dargestellten alternativen Ausbildung des Programms 30 erfolgt
nach der Unterbrechung 313 des Fadenlaufs keine Einleitung 310 der Wiederholung des
Anspinnens oder die Auslösung 311 des Rotlicht-Alarmsignals mehr, sondern es wird
stattdessen jeweils die Anfahrt 306 des Anspinnwagens zur nächsten Spinnstelle durchgeführt.
Durch diese beiden alternativen Ausbildungen des Programms 30 kann die Auslösung 311
von Rotlicht, das in den vorgenannten Fällen als unnötig eingestuft wird und vom Bedienungspersonal
manuell einzeln gelöscht werden müsste, vermieden werden. Die Erzeugung von Testanspinnern
kann auf möglichst viele Spinnstellen ausgedehnt werden.
[0059] Fig. 5 zeigt ein gemitteltes Anspinnerprofil aus 120 Anspinnern, bei denen die Einzugslängenoptimierung
nach der Erfindung vorgenommen wurde. Es ist deutlich eine hervorragende Übereinstimmung
zwischen dem Durchmesser im Bereich 41 des Oberfadens und dem Durchmesser des an den
Anspinner 42 anschließenden neu gesponnenen Fadenabschnitts 43 zu erkennen.
1. Anspinnvorrichtung mit einer Auswerteeinrichtung zur Ermittlung von Parametern eines
automatischen
Anspinnvorgangs, mit mindestens einer Sensoreinrichtung zum Messen des Fadendurchmessers
und zum Erfassen der Lage des jeweiligen Meßpunktes zum Anspinner,
dadurch gekennzeichnet,
daß eine Steuerungseinrichtung (24) vorhanden ist, die zunächst in einer Testphase
die Erzeugung von mindestens einem Testanspinner (33) ohne Einzugsaufaddierung und
die anschließende Entfernung des erzeugten Testanspinners (33) steuert, daß die Auswerteeinrichtung
für die Ermittlung der Länge einer dadurch jeweils in Fadenlaufrichtung gesehen nach
dem Testanspinner (33) hervorgerufenen Dünnstelle (32, 36) und die Bestimmung des
für die Kompensation der Dünnstelle (32,36) erforderlichen Umfangs der Einzugsaufaddierung
aus der ermittelten Länge der Dünnstelle (32,36) eingerichtet ist.
2. Anspinnvorrichtung nach Anspruch 1, dadurch gekennzeichnet, daß die Steuerungseinrichtung
(24) zusätzlich zur Steuerung einer während der Testphase wirksamen Reduzierung des
Verzugs eingerichtet ist.
3. Anspinnvorrichtung nach Anspruch 2, dadurch gekennzeichnet, daß das Ausmaß der Verzugsreduzierung
durch einen Algorithmus bestimmt ist, der die Stapellänge und einen begrenzten Meßbereich
für das Messen des Fadendurchmessers berücksichtigt.
4. Anspinnvorrichtung nach Anspruch 2, dadurch gekennzeichnet, daß der Verzug während
der Testphase durch Multiplikation des Nennverzuges mit einem vorgegebenen Faktor
bestimmt ist.
5. Anspinnvorrichtung nach einem der vorhergehenden Ansprüche, dadurch gekennzeichnet,
daß das Profil der Dünnstelle (36) durch Mittelwertbildung aus einer Vielzahl von
Testanspinnern (33) gebildet ist.
6. Anspinnvorrichtung nach Anspruch 5, dadurch gekennzeichnet, daß die Zahl der zur Mittelwertbildung
herangezogenen Testanspinner (33) mit steigender Höhe des Verzuges ebenfalls steigt.
7. Anspinnvorrichtung nach einem der vorhergehenden Ansprüche, dadurch gekennzeichnet,
daß eine Einrichtung (28) zur Visualisierung des Anspinnerprofils vorhanden ist.