(19) |
 |
|
(11) |
EP 0 947 627 B1 |
(12) |
EUROPÄISCHE PATENTSCHRIFT |
(45) |
Hinweis auf die Patenterteilung: |
|
10.10.2001 Patentblatt 2001/41 |
(22) |
Anmeldetag: 13.03.1999 |
|
|
(54) |
Maschinenfilz sowie Verfahren zu dessen Herstellung
Paper-making felt and process for making the same
Feutre pour papeterie et son procédé de fabrication
|
(84) |
Benannte Vertragsstaaten: |
|
AT BE CH DE ES FI FR GB IT LI NL PT SE |
(30) |
Priorität: |
01.04.1998 DE 19814473
|
(43) |
Veröffentlichungstag der Anmeldung: |
|
06.10.1999 Patentblatt 1999/40 |
(73) |
Patentinhaber: Thomas Josef Heimbach GmbH & Co. |
|
D-52353 Düren (DE) |
|
(72) |
Erfinder: |
|
- Best, Walter, Dr.
52351 Düren (DE)
|
(74) |
Vertreter: Paul, Dieter-Alfred, Dipl.-Ing. et al |
|
Paul & Albrecht
Patentanwaltssozietät
Hellersbergstrasse 18 41460 Neuss 41460 Neuss (DE) |
(56) |
Entgegenhaltungen: :
EP-A- 0 038 276 WO-A-98/22651
|
EP-A- 0 261 488 US-A- 4 781 967
|
|
|
|
|
|
|
|
|
Anmerkung: Innerhalb von neun Monaten nach der Bekanntmachung des Hinweises auf die
Erteilung des europäischen Patents kann jedermann beim Europäischen Patentamt gegen
das erteilte europäischen Patent Einspruch einlegen. Der Einspruch ist schriftlich
einzureichen und zu begründen. Er gilt erst als eingelegt, wenn die Einspruchsgebühr
entrichtet worden ist. (Art. 99(1) Europäisches Patentübereinkommen). |
[0001] Die Erfindung betrifft einen Maschinenfilz mit wenigstens zwei Lagen von Längsfäden
aufweisenden Längsfadengelegen und einer dazwischen angeordneten Einlage sowie mit
die Außenseiten des Maschinenfilzes bedeckenden Faserschichten. Sie betrifft desweiteren
ein Verfahren zur Herstellung eines solchen Maschinenfilzes, bei dem wenigstens zwei
Längsfadengelege unter Zwischenlegung einer Einlage übereinandergelegt werden und
auf den wenigstens eine Faserschicht aufgenadelt wird.
[0002] Ein Maschinenfilz der vorgenannten Art ist in der US-A-4 781 967 beschrieben. Er
ist modulweise aufgebaut, wobei zwischen zwei Längsfadengelege ein Querfadengelege
oder ein Gewebe als Einlage angeordnet ist. Auf den Außenseiten der und zwischen den
Längsfadengelegen sind Faserschichten vorgesehen. Die einzelnen Module werden durch
Vernadelung der Faserschichten miteinander verbunden.
[0003] Maschinenfilze der vorbeschriebenen Gattung werden endlos hergestellt. Abgesehen
davon, daß die Länge solcher Maschinenfilze begrenzt ist, sie also nicht überall eingesetzt
werden können, gestaltet sich die Montage des Filzes beispielsweise in der Pressenpartie
einer Papiermaschine schwierig. Einfacher ist die Montage eines Maschinenfilzes, wenn
er in endlicher Länge vorliegt und an seinen Stirnseiten Kupplungselemente aufweist,
über die die Enden des Maschinenfilzes in der Maschine miteinander gekuppelt werden
können (vgl. EP-A-0 261 488).
[0004] Der Erfindung liegt die Aufgabe zugrunde, einen Maschinenfilz der eingangs genannten
Art so auszubilden, daß er in endlicher Form vorliegt und seine Stirnseiten miteinander
verbindbar sind.
[0005] Diese Aufgabe wird erfindungsgemäß daduch gelöst, daß zwei Lagen Längsfadengelege
gemeinsame Längsfäden aufweisen, welche über beide Seiten der Einlage gehen und die
Einlage an ihren Stirnseiten unter Ausbildung von Kupplungsösen einfassen. Grundgedanke
der Erfindung ist es also, die Längsfäden von zumindest zwei Lagen Längsfadengelege
um die Stirnseiten der Einlage herumzuführen, so daß die beiden Lagen von denselben
Längsfäden gebildet werden. Dabei bilden die Längsfäden im Bereich der Stirnseiten
der Einlage Kupplungsösen aus, die zum Zwecke der Verbindung der Stirnseiten in Überlappung
gebracht und in dieser Stellung über einen Steckdraht gekuppelt werden können. Bis
auf den Steckdraht sind keine weiteren besonderen Kupplungselemente erforderlich.
Die durch die Kupplungsnaht hervorgerufene Unstetigkeit wird hierdurch auf ein Minimum
reduziert. Außerdem ergibt sich eine einfache Herstellung des Maschinenfilzes.
[0006] In Ausbildung der Erfindung ist vorgesehen, daß jeweils zwei Lagen Längsfadengelege
durch Umklappen eines mindestens in doppelter Länge des fertigen Maschinenfilzes hergestellten
Fadengelegemoduls unter Einschluß der Einlage gebildet sind. Die Enden der Längsfäden
stoßen dann vorzugsweise in der Mitte des Maschinenfilzes aneinander. Ein solcher
Stoß wird vermieden, wenn die Längsfadengelege einen endlosen Längsfadengelegeschlauch
bilden, der die Einlage einschließt. In diesem Fall sind die Längsfäden endlos ausgebildet.
Sie können beispielsweise durch wendelförmiges Wickeln eines Längsfadens gebildet
sein.
[0007] Die Grundstruktur des erfindungsgemäßen Maschinenfilzes läßt sich auf verschiedene
Weise variieren. So besteht die Möglichkeit, daß mehr als zwei Lagen von Längsfadengelegen
dadurch gebildet werden, daß mehrere Gelegeeinheiten, bestehend jeweils aus zwei Lagen
Längsfadengelege mit gemeinsamen Längsfäden, vorgesehen sind. Dies kann beispielsweise
in der Weise geschehen, daß wenigstens zwei Gelegeeinheiten übereinander angeordnet
sind, wobei eine oder mehrere Einlagen zwischen den Lagen der Gelegeeinheiten und
auch zwischen den Gelegeeinheiten selbst vorgesehen sein können. Alternativ können
die Gelegeeinheiten auch ineinander geschachtelt angeordnet sein, wobei auch hier
die Möglichkeit besteht, mehrere Einlagen zwischen den einzelnen Lagen der Gelegeeinheiten
vorzusehen. Zur Ausbildung der Kupplungsösen können die Längsfäden nur einer Gelegeeinheit
aber auch die aller Gelegeeinheiten herangezogen werden.
[0008] Gemäß der Erfindung ist ferner vorgeschlagen, daß auf wenigstens ein Längsfadengelege
außenseitig ein Querfadengelege aufgebracht ist.
[0009] Für die Ausbildung der Einlage kommen alle bekannten Techniken in Frage. So kann
die Einlage ein Querfadengelege aufweisen. Sie kann dabei auch mehrlagig ausgebildet
sein und zusätzlich eine Faserschicht aufweisen. Auch ein Längsfadengelege kann Bestandteil
der Einlage sein. Alternativ oder in Kombination dazu kommen auch ein Gewebe, Gewirke
und/oder eine gelochte Folie oder auch ein Fadengitter in Frage. Zur Festlegung des
Längsfadengeleges sollten die Faserschichten vernadelt sein.
[0010] Ein Verfahren zur Herstellung des vorgeschriebenen Maschinenfilzes ist erfindungsgemäß
dadurch gekennzeichnet, daß wenigstens ein Längsfadenmodul in zumindest doppelter
Länge des fertigen Maschinenfilzes hergestellt wird und daß die überstehenden Abschnitte
des Längsfadenmoduls um die Stirnseiten der Einlage unter Bildung von Kupplungsösen
durch die Längsfäden herumgeklappt und fixiert werden. Um das Einführen eines Kupplungssteckdrahtes
zu erleichtern, sollte im Bereich der Kupplungsösen störendes Material entfernt werden,
beispielsweise indem wenigstens ein stirnseitiger Querfaden der Einlage entfernt wird.
Sofern dort auch Fasermaterial vorhanden ist, sollte es entfernt werden.
[0011] Ein alternatives Verfahren ist dadurch gekennzeichnet, daß ein endloser Längsfadengelegeschlauch
und getrennt davon die Einlage hergestellt werden und daß die Einlage in den von dem
Längsfadengelegeschlauch umschlossenen Raum plaziert wird, wobei die Einlage gegenüber
der Länge des Längsfadengelegeschlauches derart verkürzt ist, daß an den Stirnseiten
des Längsfadengelegeschlauches von dem Längsfadengelegeschlauch gebildete Kupplungsösen
entstehen. Der Längsfadengelegeschlauch kann dabei durch wendelförmiges Wickeln von
wenigstens einem Längsfaden in Längsrichtung und quer dazu fortschreitend hergestellt
werden. Zur Stabilisierung der Längsfadengelege sollte eine Vernadelung der Faserschichten
durchgeführt werden. Die Faserschichten können ein- oder beidseitig bei oder nach
der Herstellung der Längsfadengelege aufgelegt und befestigt werden. Auch an der Einlage
können ein- oder beidseitig Faserschichten befestigt und dann auch vernadelt werden.
[0012] In der Zeichnung ist die Erfindung anhand eines Ausführungsbeispiels näher veranschaulicht,
wobei die Darstellung schematisch und nicht maßstäblich gehalten ist. Es zeigen:
- Fig. 1
- ein Längsfadenmodul in gestreckter Stellung mit untergelegter Querfadeneinlage in
der Seitenansicht;
- Fig. 2
- die Kombination aus Längsfadenmodul und Querfadeneinlage nach Umklappen der überstehenden
Abschnitte auf die Unterseite der Querfadeneinlage in der Seitenansicht;
- Fig. 3
- einen fertigen Maschinenfilz, hergestellt ausd der Kombination gemäß Figur 2, in der
Seitenansicht;
- Fig. 4
- den Maschinenfilz gemäß Fig. 3 nach Verbinden der Stirnseiten;
- Fig. 5
- die Seitenansicht eines Längsfadengelegeschlauchs mit darin eingeschobener Querfadenlage;
- Fig. 6
- die Seitenansicht des aus der Einheit gemäß Fig. 5 hergestellten Maschinenfilzes und
- Fig. 7
- den Maschinenfilz gemäß Fig. 6 nach Kupplung von dessen Stirnseiten.
[0013] Die Figuren 1 bis 4 zeigen stufenförmig die Herstellung eines endlichen Papiermaschinenfilzes
1. Zunächst werden getrennt eine Querfadeneinlage 2 und ein Längsfadenmodul 3 hergestellt.
Die Querfadeneinlage 2 besteht aus einer Vielzahl nebeneinander angeordneter und untereinander
verbundener Querfäden - beispielhaft mit 4 bezeichnet - deren Länge der Breite des
Längsfadenmoduls 3 entsprechen. Das Längsfadenmodul 3 weist eine Vielzahl von senkrecht
zur Zeichnungsebene nebeneinander angeordnete Längsfäden 5 auf, die aneinander befestigt
sind und an deren Unterseite eine Faserschicht 6 angeklebt ist. Das Längsfadenmodul
3 ist in der gestreckten Stellung gemäß Fig. 1 doppelt so lang wie die Querfadeneinlage
2. Durch mittige Auflage des Längsfadenmoduls 3 auf die Querfadeneinlage 2 entstehen
hierdurch überstehende Abschnitte 7, 8.
[0014] In der nächsten Herstellungsstufe werden die Abschnitte 7, 8 entsprechend den Pfeilen
A und B auf die Unterseite der Querfadeneinlage 2 umgeklappt, so daß die Stirnseiten
der Abschnitte 7, 8 nahezu aneinanderstoßen. Diese Situation ist in Fig. 2 dargestellt.
Das Vorprodukt für den späteren Papiermaschinenfilz 1 hat jetzt dessen Länge, wobei
die Längsfäden 5 des Längsfadenmoduls 3 um die Stirnseiten der Querfadeneinlage 2
herumgehen. Um dort Kupplungsösen 9, 10 auszubilden, werden die außenliegenden Querfäden
11, 12 der Querfadeneinlage 2 sowie die dort vorhandene Faserschicht 6 entfernt. Hierdurch
entstehen eine Vielzahl von senkrecht zur Zeichnungsebene nebeneinanderliegenden Kupplungsösen
9, 10, welche freie Einsteckkanäle 13, 14 einschließen.
[0015] In einem weiteren Herstellungsschritt werden auf die beiden Außenseiten des Längsfadenmoduls
3 Faserschichten 16, 17 aufgebracht, und zwar auf der Oberseite mit einer größeren
Dicke als auf der Unterseite. Die Faserschichten 16, 17 und die Faserschicht 6 werden
dann in einer Nadelmaschine vernadelt, wodurch die Querfadeneinlage 2 sowie die umgeklappten
Abschnitte 7, 8 untereinander fixiert werden. Der Papiermaschinenfilz 1 ist dann fertig.
[0016] Zum Verbindung der Stirnseiten wird der Papiermaschinenfilz 1 in die aus Fig. 4 ersichtliche
Form gebracht. Dabei überlappen sich die Kupplungsösen 9, 10, so daß ein Kupplungskanal
20 entsteht, durch den ein Kupplungssteckdraht 21 gesteckt ist. Dieser verbindet die
beiden Stirnseiten. Aufgrund der Schrägen an den Stirnseiten der Faservliese 16, 17
überschneiden sich diese, so daß die Kupplungsösen 9, 10 außenseitig durch das Faservlies
16 abgedeckt sind.
[0017] In den Figuren 5 bis 7 ist die Herstellung eines anderen Papiermaschinenfilzes 22
dargestellt. In diesem Fall wird zunächst ein Längsfadenschlauch 23 durch wendelförmiges
Wickeln eines Längsfadens 24 über zwei beabstandete Walzen hergestellt. Die einzelnen
Wicklungen des Längsfadens 24 werden untereinander verbunden. Hierdurch entstehen
eine Längsfadenoberlage 25 und eine Längsfadenunterlage 26.
[0018] In den Zwischenraum zwischen Längsfadenoberlage 25 und Längsfadenunterlage 26 wird
eine Querfadeneinlage 27 eingeschoben. Sie besteht aus einer Vielzahl von nebeneinander
angeordneten und untereinander verbundenen Querfäden - beispielhaft mit 28 bezeichnet
- und einer aufgenadelten Faserschicht 29. Die Längserstreckung der Querfäden 28 entspricht
der sich senkrecht zur Zeichnungsebene erstreckenden Breite des Längsfadenschlauches
23. Die Querfadeneinlage 27 ist gegenüber der Länge des Längsfadenschlauches 23 derart
verkürzt, daß an den Stirnseiten des Längsfadenschlauches 23 Kupplungsösen 30, 31
entstehen, die von dem Längsfaden 24 gebildet werden. Die Kupplungsösen 30, 31 umschließen
freie Einsteckkanäle 32, 33. In einem darauffolgenden Verfahrensschritt werden auf
die Außenseiten von Längsfadenoberlage 25 und Längsfadenunterlage 26 Faserschicthen
34, 35 aufgelegt und untereinander und mit der Faserschicht 29 durchvernadelt. Es
liegt dann der fertige Papiermaschinenfilz 22 vor.
[0019] Um diesen Papiermaschinenfilz 22 endlos zu machen, wird der in die aus Fig. 7 ersichtliche
Form gebogen, bis die Kupplungsösen 30, 31 zur Überlappung kommen und dann einen Kupplungskanal
36 einschließen. In diesen wird anschließend ein Kupplungssteckdraht 37 eingeschoben,
der die Verbindung der Stirnseiten herstellt. Auch hier sind die Stirnseiten 38, 39
der Faserschicht 34 angeschrägt, so daß sie sich im Bereich der Kupplungsnaht überlappen.
1. Maschinenfilz (1, 22) mit wenigstens zwei Lagen (25, 26) von Längsfäden (5, 24) aufweisenden
Längsfadengelegen (3, 23) und einer dazwischen angeordneten Einlage (2, 27) sowie
mit die Außenseiten des Maschinenfilzes (1, 22) bedeckenden Faserschichten (16, 17,
34, 35), dadurch gekennzeichnet, daß zwei Längsfadengelege (25, 26) gemeinsame Längsfäden (5, 24) aufweisen, welche über
beide Seiten der Einlage (2, 27) gehen und die Einlage (2, 27) an ihren Stirnseiten
unter Ausbildung von Kupplungsösen (9, 10, 30, 31) einfassen.
2. Maschinenfilz nach Anspruch 1, dadurch gekennzeichnet, daß die jeweils zwei Lagen (25, 26) Längsfadengelege durch Umklappen eines in zumindest
doppelter Länge des fertigen Maschinenfilzes (1) hergestellten Längsfadengelegemoduls
(3) unter Einschluß der Einlage (2) gebildet sind.
3. Maschinenfilz nach Anspruch 1, dadurch gekennzeichnet, daß die Längsfadengelege einen endlosen Längsfadengelegeschlauch (23) bilden, der die
Einlage (27) einschließt.
4. Maschinenfilz nach einem der Ansprüche 1 bis 3, dadurch gekennzeichnet, daß mehr als zwei Lagen von Längsfadengelegen dadurch gebildet sind, daß mehrere Gelegeeinheiten,
bestehend jeweils aus zwei Lagen Längsfadengelege mit gemeinsamen Längsfäden, vorgesehen
sind.
5. Maschinenfilz nach Anspruch 4, dadurch gekennzeichnet, daß wenigstens zwei Gelegeeinheiten übereinander angeordnet sind.
6. Maschinenfilz nach Anspruch 4 oder 5, dadurch gekennzeichnet, daß mehrere Gelegeeinheiten ineinandergeschachtelt angeordnet sind.
7. Maschinenfilz nach einem der Ansprüche 4 bis 6, dadurch gekennzeichnet, daß die jeweils gemeinsamen Längsfäden stirnseitig Kupplungsösen ausbilden.
8. Maschinenfilz nach einem der Ansprüche 1 bis 7, dadurch gekennzeichnet, daß auf wenigstens ein Längsfadengelege außenseitig ein Querfadengelege aufgebracht ist.
9. Maschinenfilz nach einem der Ansprüche 1 bis 8, dadurch gekennzeichnet, daß die Einlage (2, 27) ein Querfadengelege aufweist.
10. Maschinenfilz nach einem der Ansprüche 1 bis 9, dadurch gekennzeichnet, daß die Einlage mehrlagig ausgebildet ist.
11. Maschinenfilz nach einem der Ansprüche 1 bis 10, dadurch gekennzeichnet, daß die Einlage (27) wenigstens eine Faserschicht (29) aufweist.
12. Maschinenfilz nach einem der Ansprüche 1 bis 11, dadurch gekennzeichnet, daß die Einlage wenigstens ein Längsfadengelege aufweist.
13. Maschinenfilz nach einem der Ansprüche 1 bis 12, dadurch gekennzeichnet, daß die Einlage ein Gewebe, Gewirke, Fadengitter und/oder eine gelochte Folie aufweist.
14. Maschinenfilz nach einem der Ansprüche 1 bis 13, dadurch gekennzeichnet, daß die Längsfadengelege (3, 25, 26) durch Vernadelung der Faserschichten (6, 16, 17,
29, 34, 35) festgelegt sind.
15. Verfahren zur Herstellung eines Maschinenfilzes (1, 22), bei dem wenigstens zwei Längsfadengelege
(3) unter Zwischenlegung einer Einlage (2) übereinandergelegt werden und wenigstens
eine Faserschicht (16, 17) aufgenadelt wird, dadurch gekennzeichnet, daß wenigstens ein Längsfadenmodul (3) in zumindest doppelter Länge des fertigen Maschinenfilzes
(1) hergestellt wird und daß die überstehenden Abschnitte (7, 8) des Längsfadenmoduls
(3) um die Stirnseiten der Einlage (2) unter Bildung von Kupplungsösen (9, 10) durch
die Längsfäden (5) herumgeklappt und fixiert werden.
16. Verfahren nach Anspruch 15, dadurch gekennzeichnet, daß im Bereich der Kupplungsösen (9, 10) störendes Material entfernt wird.
17. Verfahren nach Anspruch 16, dadurch gekennzeichnet, daß an den Stirnseiten des Maschinenfilzes (1) wenigstens ein stirnseitiger Querfaden
(11, 12) der Einlage (2) entfernt wird.
18. Verfahren nach Anspruch 16 oder 17, dadurch gekennzeichnet, daß störendes Faservliesmaterial (6) entfernt wird.
19. Verfahren zur Herstellung eines Maschinenfilzes (22), bei dem wenigstens zwei Längsfadengelege
(25, 26) unter Zwischenlegung einer Einlage (27) übereinandergelegt werden und wenigstens
eine Faserschicht (34, 35) aufgenadelt wird, dadurch gekennzeichnet, daß ein endloser Längsfadengelegeschlauch (23) und getrennt davon die Einlage (27) hergestellt
werden und daß die Einlage (27) in den von dem Längsfadengelegeschlauch (23) umschlossenen
Raum plaziert wird, wobei die Einlage (27) gegenüber der Länge des Längsfadengelegeschlauches
(23) derart verkürzt ist, daß an den Stirnseiten des Längsfadengelegeschlauches (23)
von dem Längsfadengelegeschlauch (23) gebildete Kupplungsösen (30, 31) entstehen.
20. Verfahren nach Anspruch 19, dadurch gekennzeichnet, daß der Längsfadengelegeschlauch (23) durch wendelförmiges Wickeln von wenigstens einem
Längsfaden (24) in Längsrichtung und quer dazu fortschreitend hergestellt wird.
21. Verfahren nach einem der Ansprüche 15 bis 20, dadurch gekennzeichnet, daß die Längsfadengelege (3, 23) durch Vernadeln der Faserschichten (6, 16, 17, 29, 34,
35) befestigt werden.
22. Verfahren nach einem der Ansprüche 15 bis 21, dadurch gekennzeichnet, daß bei oder nach der Herstellung der Längsfadengelege (3, 23) ein- oder beidseitig Faserschichten
(16, 17, 34, 35) befestigt werden.
23. Verfahren nach einem der Ansprüche 15 bis 22, dadurch gekennzeichnet, daß an der Einlage (27) ein- oder beidseitig Faserschichten (29) befestigt werden.
24. Verfahren nach einem der Ansprüche 15 bis 23, dadurch gekennzeichnet, daß auf wenigstens einer der beiden Längsfadengelege außenseitig wenigstens ein Querfadengelege
aufgebracht wird.
25. Verfahren nach einem der Ansprüche 15 bis 24, dadurch gekennzeichnet, daß mehr als zwei Lagen von Längsfadengelegen dadurch gebildet werden, daß mehrere Gelegeeinheiten,
bestehend jeweils aus zwei Lagen Fadengelege mit gemeinsamen Längsfäden, hergestellt
werden.
26. Verfahren nach Anspruch 25, dadurch gekennzeichnet, daß wenigstens zwei Gelegeeinheiten übereinander angeordnet werden.
27. Verfahren nach Anspruch 25, dadurch gekennzeichnet, daß die Gelegeeinheiten ineinandergeschachtelt werden.
1. Machine felt (1, 22) having a structure (3, 23) comprising at least two layers (25,
26) of longitudinal yarns (5, 24) with an intermediate layer (2, 27) disposed between
them, as well as layers of fibre (16, 17, 34, 35) covering the outermost sides of
the machine felt (1, 22), characterized in that two layers (25, 26) consisting of longitudinal yarns share common longitudinal yams
(5, 24), which extend beyond the two sides of the intermediate layer (2, 27) and enclose
the ends, thus forming coupling eyelets (9, 10, 30, 31).
2. Machine felt according to Claim 1, characterized in that the two layers (25, 26) of the structure consisting of longitudinal yams are respectively
formed by folding a longitudinal-yarn module (3), which is produced so as to be at
least twice the length of the finished machine felt (1), around the intermediate layer
(2) so as to enclose it.
3. Machine felt according to Claim 1, characterized in that the structure consisting of longitudinal yarns forms an endless tube (23), which
encloses the intermediate layer (27).
4. Machine felt according to one of Claims 1 to 3, characterized in that more than two layers of longitudinal-yarn structures are formed in that a plurality of structural units are provided, each consisting of two layers of the
longitudinal-yarn structure and sharing common longitudinal yarns.
5. Machine felt according to Claim 4, characterized in that at least two structural units are disposed one on top of the other.
6. Machine felt according to Claim 4 or 5, characterized in that a plurality of structural units are fitted one inside the other.
7. Machine felt according to one of Claims 4 to 6, characterized in that the common longitudinal yarns each form coupling eyelets at the ends.
8. Machine felt according to one of Claims 1 to 7, characterized in that a transverse-yarn structure is applied on to the outside of at least one structure
consisting of longitudinal yarns.
9. Machine felt according to one of Claims 1 to 8, characterized in that the intermediate layer (2, 27) comprises a transverse-yarn structure.
10. Machine felt according to one of Claims 1 to 9, characterized in that the intermediate layer is multilayered.
11. Machine felt according to one of Claims 1 to 10, characterized in that the intermediate layer (27) includes at least one layer of fibre (29).
12. Machine felt according to one of Claims 1 to 11, characterized in that the intermediate layer includes at least one structure consisting of longitudinal
yarns.
13. Machine felt according to one of Claims 1 to 12, characterized in that the intermediate layer includes a woven fabric, knitted fabric, yarn mesh and/or
perforated sheet.
14. Machine felt according to one of Claims 1 to 13, characterized in that the structures consisting of longitudinal yarns (3, 25, 26) are fixed by needling
of the layers of fibre (6, 16, 17, 29, 34, 35).
15. Method of manufacturing a machine felt (1, 22), in which at least two structures (3)
consisting of longitudinal yarns are placed one on top of the other with interposition
of an intermediate layer (2), and at least one layer of fibre (16, 17) is needled,
characterized in that at least one longitudinal-yarn module (3) is produced so as to be at least twice
the length of the finished machine felt (1); and in that the projecting portions (7, 8) of the longitudinal-yarn module (3) are folded round
the ends of the intermediate layer (2) and fixed in such a way that the longitudinal
yarns (5) form coupling eyelets (9, 10).
16. Method according to Claim 15, characterized in that any obstructive material in the region of the coupling eyelets (9, 10) is removed.
17. Method according to Claim 16, characterized in that, at the ends of the machine felt (1), at least one end transverse yarn (11, 12) of
the intermediate layer (2) is removed.
18. Method according to Claim 16 or 17, characterized in that any obstructive fibrous material (6) is removed.
19. Method of manufacturing a machine felt (22), in which at least two structures (25,
26) consisting of longitudinal yarns are placed one on top of the other with interposition
of an intermediate layer (27), and at least one layer of fibre (34, 35) is needled,
characterized in that an endless tube (23), consisting of longitudinal yarns, and the intermediate layer
(27) are produced separately, and in that the intermediate layer (27) is disposed in the space enclosed by the tube (23) consisting
of longitudinal yarns, the intermediate layer (27) being shortened in relation to
the length of the tube (23) in such a way that coupling eyelets (30, 31) are produced
at the ends of the longitudinal-yarn tube (23), these being formed by the longitudinal-yarn
tube (23).
20. Method according to Claim 19, characterized in that the tube (23) consisting of longitudinal yarns is progressively produced by spiral
winding of at least one longitudinal yarn (24) in longitudinal direction and at an
angle thereto.
21. Method according to one of Claims 15 to 20, characterized in that the structures (3, 23) consisting of longitudinal yarns are fixed by needling of
the layers of fibre (6, 16, 17, 29, 34, 35).
22. Method according to one of Claims 15 to 21, characterized in that, during or following manufacture of the longitudinal-yarn structures (3, 23), layers
of fibre (16, 17, 34, 35) are fixed to one or both sides.
23. Method according to one of Claims 15 to 22, characterized in that layers of fibre (29) are fixed to one or both sides of the intermediate layer (27).
24. Method according to one of Claims 15 to 23, characterized in that at least one structure consisting of transverse yarns is applied on to the outside
of at least one of the two longitudinal-yarn structures.
25. Method according to one of Claims 15 to 24, characterized in that more than two layers of longitudinal-yarn structures are formed in that a plurality of structural units are produced, each consisting of two layers of a
yarn structure sharing common longitudinal yarns.
26. Method according to Claim 25, characterized in that at least two structural units are disposed one on top of the other.
27. Method according to Claim 25, characterized in that the structural units are fitted one inside the other.
1. Feutre pour papeterie (1, 22) muni d'au moins deux couches (25, 26) de structures
de fils longitudinaux (3, 23) présentant des fils longitudinaux (5, 24) et une garniture
intermédiaire (2, 27) placée entre elles, et muni également de couches de fibres (16,
17, 34, 35) recouvrant les côtés extérieurs du feutre pour papeterie, caractérisé en ce que deux structures de fils longitudinaux (25, 26) présentent des fils longitudinaux
(5, 24) communs, lesquels dépassent des deux côtés de la garniture intermédiaire (2,
27) et bordent la garniture intermédiaire (2, 27) sur ses côtés frontaux en formant
des oeillets de couplage (9, 10, 30, 31).
2. Feutre pour papeterie selon la revendication 1, caractérisé en ce que les deux couches (25, 26) de structures de fils longitudinaux sont formées respectivement
par le rabattement d'un module de structure de fils longitudinaux (3) fabriqué au
moins du double de la longueur du feutre pour papeterie (1) fini en incluant la garniture
intermédiaire (2).
3. Feutre pour papeterie selon la revendication 1, caractérisé en ce que les structures de fils longitudinaux forment un tuyau de structure de fils longitudinaux
(23) qui inclut la garniture intermédiaire (2).
4. Feutre pour papeterie selon l'une des revendications 1 à 3, caractérisé en ce que plus de deux couches de structures de fils longitudinaux sont formées du fait que
plusieurs unités de structures sont prévues, lesquelles sont constituées respectivement
de deux couches de structures de fils longitudinaux avec des fils longitudinaux communs.
5. Feutre pour papeterie selon la revendication 4, caractérisé en ce qu'au moins deux unités de structures sont placées l'une au dessus de l'autre.
6. Feutre pour papeterie selon la revendication 4 ou 5, caractérisé en ce que plusieurs unités de structures sont emboîtées les unes dans les autres.
7. Feutre pour papeterie selon l'une des revendications 4 à 6, caractérisé en ce que les fils longitudinaux communs respectifs forment des oeillets de couplage du côté
frontal.
8. Feutre pour papeterie selon l'une des revendications 1 à 7, caractérisé en ce qu'une structure de fils transversaux est posée sur au moins une structure de fils longitudinaux
du côté de l'extérieur.
9. Feutre pour papeterie selon l'une des revendications 1 à 8, caractérisé en ce que la garniture intermédiaire (2, 27) présente une structure de fils transversaux.
10. Feutre pour papeterie selon l'une des revendications 1 à 9, caractérisé en ce que la garniture intermédiaire est formée de plusieurs couches.
11. Feutre pour papeterie selon l'une des revendications 1 à 10, caractérisé en ce que la garniture intermédiaire (27) présente au moins une couche de fibres (29).
12. Feutre pour papeterie selon l'une des revendications 1 à 11, caractérisé en ce que la garniture intermédiaire présente au moins une structure de fils longitudinaux.
13. Feutre pour papeterie selon l'une des revendications 1 à 12, caractérisé en ce que la garniture intermédiaire présente un tissu, un tissu à mailles, une grille en fils
et/ou une feuille perforée.
14. Feutre pour papeterie selon l'une des revendications 1 à 13, caractérisé en ce que les structures de fils longitudinaux (3, 25, 26) sont fixées par couture des couches
de fibres (6, 16, 17, 29, 34, 35).
15. Procédé pour la fabrication d'un feutre pour papeterie (1, 22) dans le cas duquel
au moins deux structures de fils longitudinaux (3) sont posées l'une sur l'autre,
une garniture intermédiaire (2) étant posée entre elles, et au moins une couche de
fibres (16, 17) est cousue dessus, caractérisé en ce qu'au moins un module de fils longitudinaux (3) est fabriqué dans une longueur au moins
du double du feutre pour machine (1) fini, et en ce que les sections (7, 8) du module de fils longitudinaux (3) dépassant sont repliées autour
des côtés frontaux de la garniture intermédiaire (2) et fixées en formant des oeillets
de couplage (9, 10) grâce aux fils longitudinaux (5).
16. Procédé selon la revendication 15, caractérisé en ce que dans la partie des oeillets de couplage (9, 10) on supprime le matériau gênant.
17. Procédé selon la revendication 16, caractérisé en ce qu'au moins un fil transversal (11, 12) du côté frontal de la garniture intermédiaire
(2) est supprimé sur les côtés frontaux du feutre pour papeterie (1).
18. Procédé selon la revendication 16 ou 17, caractérisé en ce que le matériau de fibres gênant (6) est supprimé.
19. Procédé pour la fabrication d'un feutre pour papeterie (22) dans le cas duquel au
moins deux structures de fils longitudinaux (25, 26) sont posées l'une sur l'autre,
une garniture intermédiaire (27) étant posée entre elles, et au moins une couche de
fibres (34, 35) est cousue dessus, caractérisé en ce qu'au moins un tuyau de structure de fils longitudinaux (23) sans fin et la garniture
intermédiaire (27) sont fabriqués, cette dernière étant séparée du premier, et en ce que la garniture intermédiaire (27) est placée dans l'espace entouré par le tuyau de
structure de fils longitudinaux (23), la garniture intermédiaire (27) étant raccourcie
par rapport à la longueur du tuyau de structure de fils longitudinaux (23) de telle
sorte que des oeillets de couplage (30, 31) formés par le tuyau de structure de fils
longitudinaux (23) sont obtenus sur les côtés frontaux du tuyau de structure de fils
longitudinaux (23).
20. Procédé selon la revendication 19, caractérisé en ce que le tuyau de structure de fils longitudinaux (23) est fabriqué par un enveloppement
de forme hélicoïdale d'au moins un fil longitudinal (24) dans le sens longitudinal
et continuant transversalement au fil longitudinal.
21. Procédé selon l'une des revendications 15 à 20, caractérisé en ce que les structures de fils longitudinaux (3, 23) sont fixées par couture des couches
de fibres (6, 16, 17, 29, 34, 35).
22. Procédé selon l'une des revendications 15 à 21, caractérisé en ce que pendant ou après la fabrication des structures de fils longitudinaux (3, 23), des
couches de fibres (16, 17, 34, 35) sont fixées sur un ou deux côtés.
23. Procédé selon l'une des revendications 15 à 22, caractérisé en ce que des couches de fibres (29) sont fixées sur un ou deux côtés de la garniture intermédiaire
(27).
24. Procédé selon l'une des revendications 15 à 23, caractérisé en ce qu'au moins une structure de fils transversaux est appliquée à l'extérieur sur au moins
l'une des deux structures de fils longitudinaux.
25. Procédé selon l'une des revendications 15 à 24, caractérisé en ce que plus de deux couches de structures de fils longitudinaux sont formées par le fait
que plusieurs unités de structure sont fabriquées, celles-ci étant composées respectivement
de deux couches de structures de fils avec des fils longitudinaux communs.
26. Procédé selon la revendication 25, caractérisé en ce qu'au moins deux unités de structures sont posées l'une sur l'autre.
27. Procédé selon la revendication 25, caractérisé en ce que les unités de structures sont emboîtées les unes dans les autres.
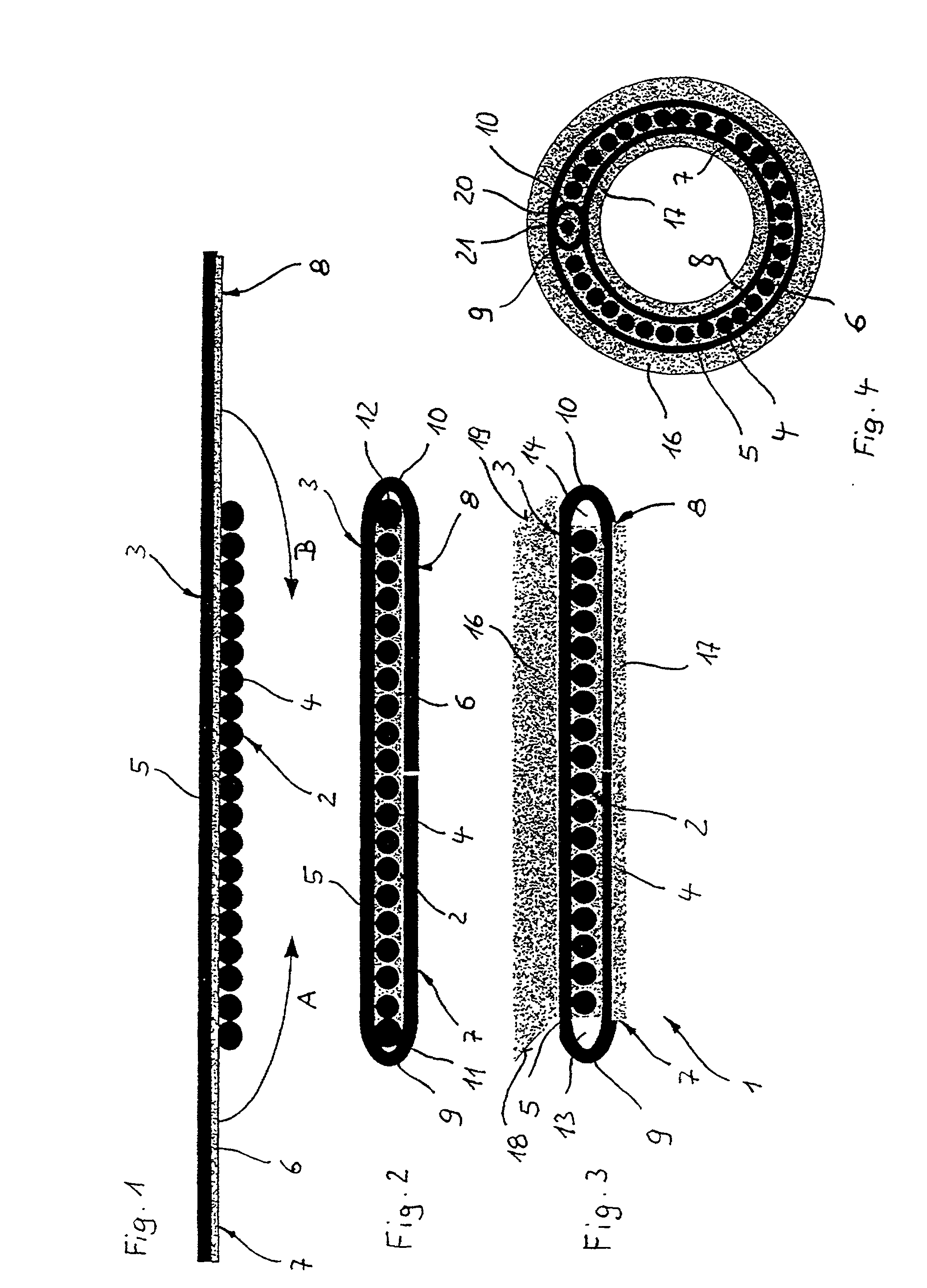
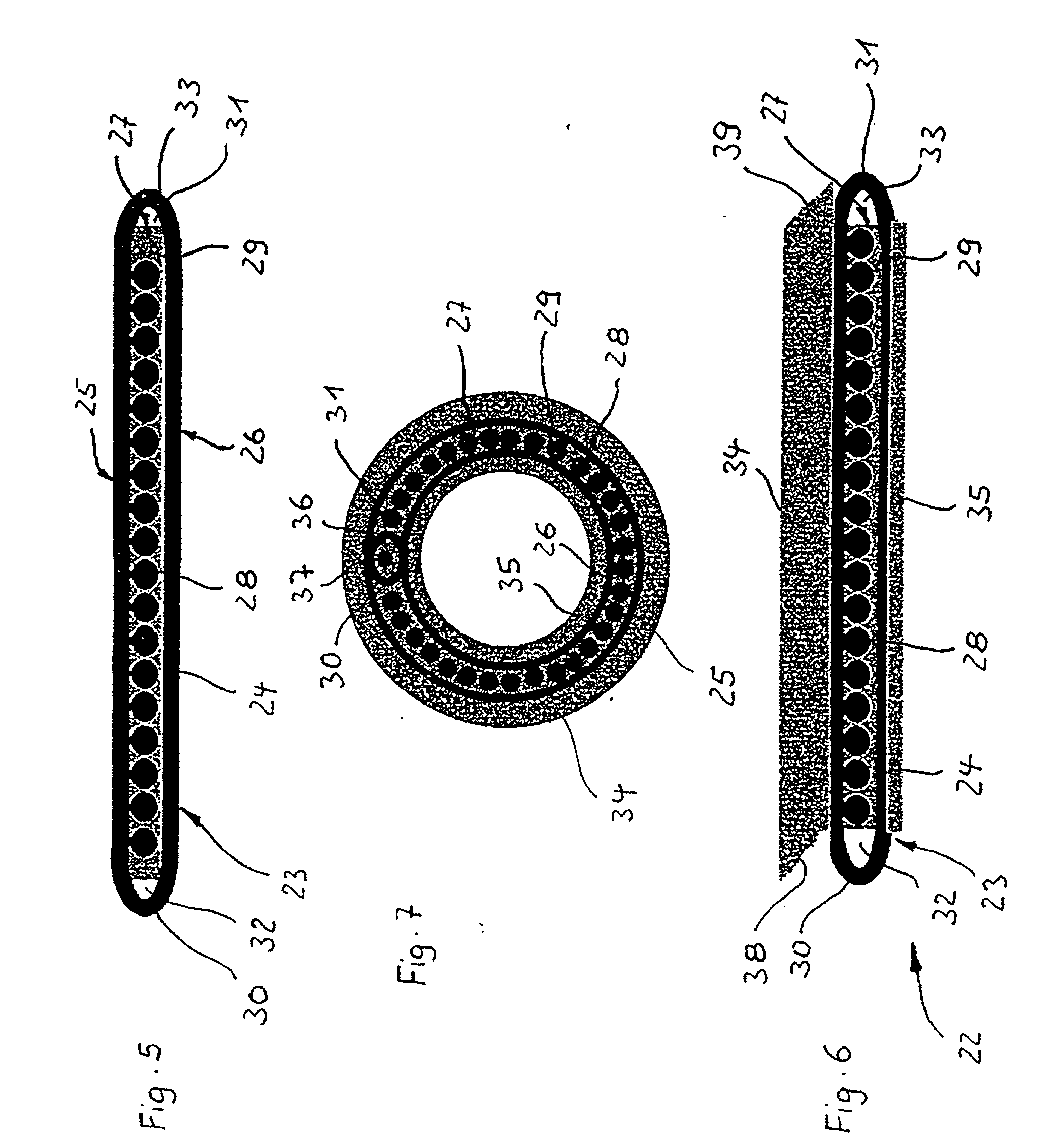