BACKGROUND OF THE INVENTION
Field of the Invention
[0001] The present invention relates to an invar type alloy wire and, more specifically,
to an invar type alloy wire excellent in toughness, strength and low thermal expansion
property which can be used preferably as strands for overhead conductor cables.
Description of the Related Art
[0002] An invar alloy having the composition of Fe-36 wt% Ni has been known as an alloy
having low thermal expansion property, which is used for precision parts, for example.
Meanwhile, in order to increase transmission capacity of an aluminum cable steel reinforced
(ACSR) as overhead conductor cable, a method of reducing slack of conductor cable
caused by increase in temperature during power transmission has been studied. One
method has been known in which an alloy wire having low thermal expansion property
is used as a steel core to reduce slacking. An invar type alloy wire such as disclosed
in Japanese Patent Laying-Open No. 55-119156 has been developed as such alloy wire
having low thermal expansion property.
[0003] The alloy wire developed in accordance with Japanese Patent Laying-Open No. 55-119156
is a hard material and exhibits tensile strength of 120 kg/mm
2. However, it exhibits low toughness property stability such as turns of twisting
after it has been finally subjected to zinc or zinc alloy plating, thereby reducing
production yield of conductor cables. Zinc alloy plating or the like is applied to
improve corrosion resistance of the conductor cable. However, an intermetallic compound
formed at the interface with the plating tends to lower the twisting property of the
alloy wire.
[0004] Therefore, an object of the present invention is to improve toughness of a conventionally
used invar type alloy wire having high strength, and, more particularly, to improve
twisting property of the wire in the final wire size.
[0005] Document EP 0 723 030 A1 which has the same priority date as this application discloses
a Fe-Ni-based alloy wire and a method of manufacturing such a wire. The wire shown
in this citation is prepared by processing the material in which the areal percentages
of the precipitations at the grain boundaries is up to 2% at finishing hot wire rolling.
Moreover, the average crystal grain size of the wire in the longitudinal direction
is in the range of 5-70
µm at finishing the hot wire rolling.
SUMMARY OF THE INVENTION
[0006] The invar type alloy wire in accordance with one aspect of the present invention
contains Fe and Ni as main alloy elements, and the wire has high toughness, high strength
and low thermal expansion property, wherein the average grain size in transverse direction
of said wire in a final wire size is within a range of 1 to 5
µm; wherein the areal ratio of precipitates existing at grain boundary of said wire
in said final wire size is at most 4 % and wherein impurity contained in said alloy
is at most 0.01 percent in weight of P, at most 0.004 percent by weight of S, at most
0.005 percent of weight of O and at most 0.008 percent by weight of N.
[0007] Due to the fact that the areal ratio of the precipitates existing at the grain boundary
of the wire in the processed final wire size is at most 4%, the twisting property
of the wire is improved. Especially when the areal ratio of the precipitates existing
at the grain boundary of the wire in the final wire size is at most 2%, twisting property
and reliability of the wire can be remarkably improved.
[0008] In the invar type alloy wire in accordance with the present invention, the average
grain size in the transverse direction of the wire in the processed final wire size
is 1 to 5
µm, and hence twisting property of the wire is improved.
[0009] Especially when the average grain size in the transverse direction of the wire in
the final wire size is within 1.5 to 4
µm, the twisting property and the reliability of the wire can significantly be improved.
[0010] The method of manufacturing an invar type alloy wire in accordance with the present
invention, comprises the steps of:
preparing an invar type alloy containing, as main elements, Fe and Ni, wherein impurity
contained in said alloy is at most 0.01 percent in weight of P, at most 0.004 percent
by weight of S, at most 0.005 percent of weight of O and at most 0.008 percent by
weight of N;
performing hot working and heat treatment in combination to set areal ratio of precipitates
existing at grain boundary of said alloy to be at most 2 % and to set average grain
size in longitudinal direction of a rod shape processed by said hot working and heat
treatment to be within a range of 5 to 40 µm ; and therafter, performing cold working and heat treatment in combination to set
areal ratio of precipitates existing at the grain boundary of said alloy in final
wire size of said wire to be at most 4 % and to set average grain size in transverse
direction of said wire in said final wire size to be within a range of 1 to 5 µm.
Such an invar type alloy wire has superior twisting property. Especially when the
areal ratio of the precipitates existing at the grain boundary of the alloy is set
to be at most 1 % by the combination of hot working and heat treatment, the areal
ratio of the precipitates existing at the grain boundary of the alloy in the final
wire size can be easily set to be at most 2 % by the subsequent combination of cold
working and heat treatment, and hence an invar type alloy wire having significantly
improved twisting property can be provided.
DESCRIPTION OF THE PREFERRED EMBODIMENTS
[0011] A conventionally used invar type alloy wire having high strength contains, as main
elements, Fe and Ni, and Co may partially substitute for Ni. Generally, such an invar
type alloy wire having high strength contains at least one of Mo, Cr, C, W, Nb, Ti,
V, Si or the like as strengthing element, and in addition, at least one of Mn, Al,
Mg, Ti, Ca or the like as a deoxidizer.
[0012] The inventors performed various investigations to eliminate instabilizing factors
related to the toughness of such invar type alloy wire having high strength. As a
result, it was found that crystal grain size of the wire, the amount of precipitates
at the grain boundary and amount of specific impurity elements have significant effects
on the toughness of the wire. It was also found that there is a preferable method
of processing and heat treatment for controlling the grain size and the amount of
precipitates at the grain boundary. The precipitates at the grain boundary here are
often carbide.
[0013] In order to reduce precipitates at the grain boundary in the final wire size of the
wire, any of the following methods may be used: a method in which during hot rolling,
cooling is started from solid solution temperature (cooling from the solid solution
temperature may be considered to be a kind of heat treatment); a method in which solution
heat treatment is performed prior to hot rolling; and a method in which solution heat
treatment is performed after hot rolling. No matter which of the methods is employed,
the smaller the amount of precipitates at the grain boundary after the combined hot
working and heat treatment, the smaller the amount of precipitates at the grain boundary
precipitated during subsequent cold working and heat treatment, and therefore the
smaller the amount of precipitates existing at the grain boundary in the wire in the
final wire size.
Table 1
Element |
C |
Mn |
Ni |
Co |
Cr |
Mo |
P |
S |
O |
N |
Fe |
Wt % |
0.25 |
0.30 |
35.0 |
3.01 |
0.98 |
2.01 |
0.002 |
0.001 |
0.0015 |
0.0013 |
remaining part |
[0014] As an example, an invar type alloy having such a composition as shown in Table 1
was dissolved and cast.
Table 2
Sample |
Rolling Start Temperature (°C) |
Cooling Rate (°C/sec) |
Areal Ratio of Precipitates at Grain Boundary (%) |
Average Grain size in Longitudinal Direction (µm) |
A |
1200 |
10 |
0.2 |
22 |
B |
1150 |
8 |
0.6 |
14 |
C |
1100 |
7 |
0.9 |
5 |
D |
1250 |
3 |
3.8 |
75 |
E |
1200 |
5 |
2.8 |
59 |
[0015] Table 2 shows the influence of the temperature at which rolling is started and the
rate of cooling during rolling until the temperature reaches 600°C when the invar
type alloy shown in Table 1 is subjected to hot rolling, on the average grain size
in the longitudinal direction of the rod after rolling and on the areal ratio of the
precipitates at the grain boundary. For measuring the areal ratio of the precipitates
at the grain boundary, the rolled rod was cut along the longitudinal direction, the
cut surface is polished and etched for 40 seconds by using 5 % nital solution, and
the surface was photographed with the magnification of 4000 by using a scanning type
electron microscope. The microphotograph was processed by an automatic image processing
apparatus, the areal ratio of the precipitates existing at the grain boundary was
calculated, and the average grain size in the longitudinal direction was calculated.
[0016] As is apparent from Table 2, the average grain sizes in the longitudinal direction
of samples A, B and C of which rate of cooling during hot working was relatively fast
are within the range of 5 to 40 µm, and the areal ratio of the precipitates at the
grain boundary is at most 2.0 %. Meanwhile, the grain sizes of samples D and E of
which cooling rate during hot working was slow are far greater than 40 µm, and the
areal ratio of precipitates at the grain boundary exceeds 2.0 %.
[0017] Referring to Table 2, a billet having a square cross section of about 120 x 120 mm
2 was passed through a plurality of shaping rolls and rolled to be a rod having a circular
cross section of about 12 mm in diameter.
[0018] Thereafter, all the samples A to E shown in Table 2 were subjected to first cold
working, first heat treatment, scraping, second heat treatment and second cold working.
As the first cold working, drawing with the degree of processing of about 30 % was
performed by using a plurality of dies. The first heat treatment was performed in
a non-oxidizing atmosphere such as in a decomposed ammonia gas containing 75 % by
volume of H
2 and 25 % by volume of N
2, at 650°C for 10 hours. The samples softened by the first heat treatment were peeled
by scraping dies, and then subjected to second heat treatment under the same condition
as the first heat treatment. The samples softened by the second heat treatment were
drawn to have the diameter of about 2 to 5 mm with the degree of processing of about
85 %, by passing through a plurality of dies, and thereafter the samples were dipped
in Zn-5 wt % Al alloy melt. The average grain size in the transverse direction, areal
ratio of precipitates at the grain boundary and various mechanical properties of the
wires having final wire size obtained through these steps are as shown in Table 3.
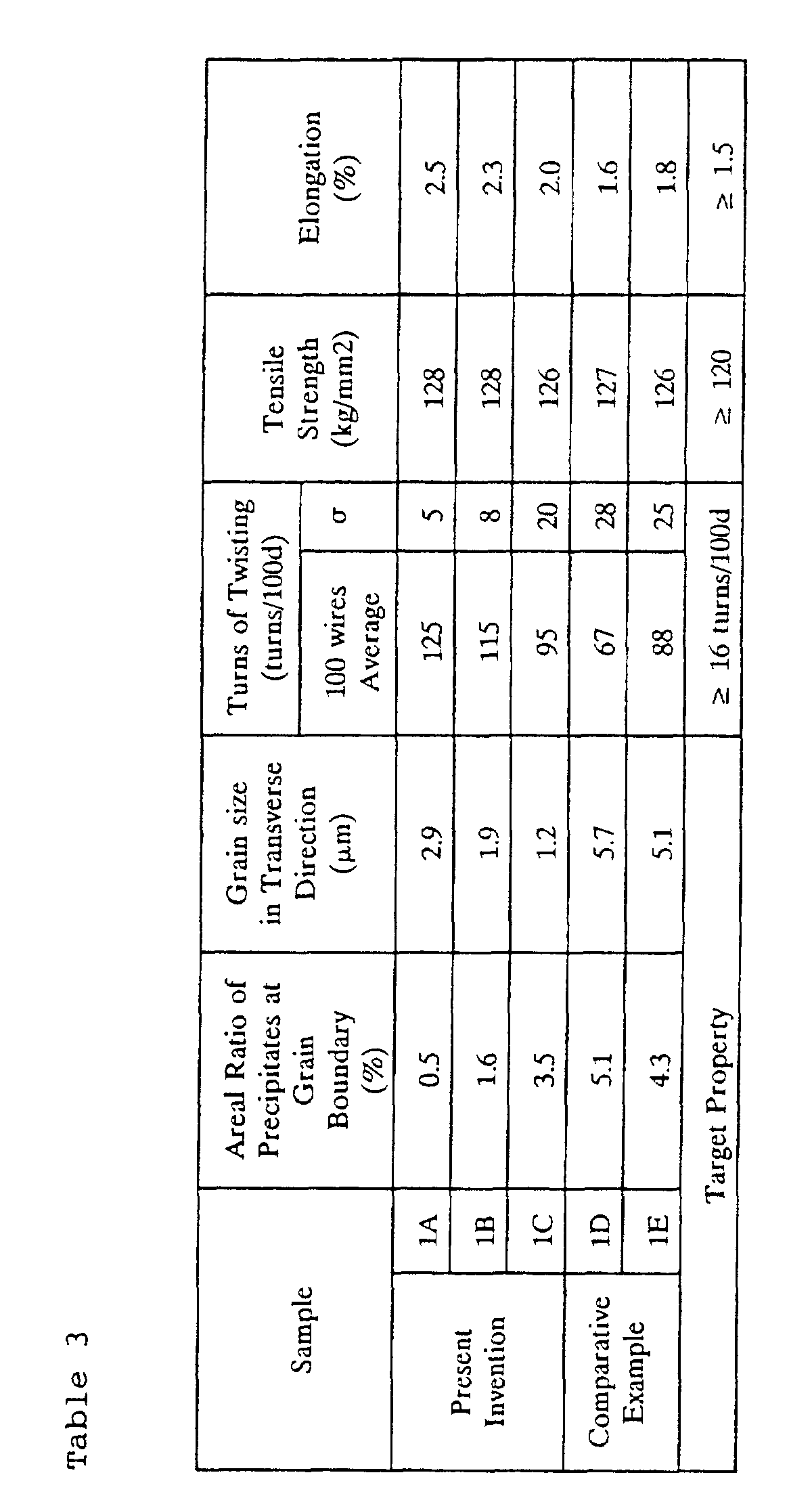
Referring to Table 3, samples 1A to 1E are the samples obtained from samples A to
E of Table 2. The samples 1A to 1E all have similar tensile strength exceeding the
target property of 120 kg/mm
2. However, comparative examples 1D and 1E are inferior in twisting property and elongation
as compared with samples 1A, 1B and 1C in accordance with the present invention.
[0019] The twisting property is represented by the number of possible twisting (turns/100d)
at about 60 rpm of a single wire having the length one hundred times the diameter
d until it breaks. The reference character σ represents standard deviation of the
turns of twisting of one hundred wires. The smaller the value σ, the higher the reliability,
as the twisting property is stable.
[0020] Referring to Table 3, the samples 1A and 1B of which areal ratio of precipitates
at the grain boundary is at most 2.0 % and average grain size in the transverse direction
is within the range of 1.5 to 4 µm have superior twisting property exceeding 100 turns,
and they have high reliability as represented by the standard deviation σ of at most
10. The sample 1C of which areal ratio of the precipitates at the grain boundary exceeds
2 % but not higher than 4 % and the grain size in the cross sectional direction is
within a range of 1 to 5 µm but not higher than 1.5 µm has slightly inferior twisting
property as compared with samples 1A and 1B. However, it can still satisfy the target
property in 3σ management. More specifically, for the sample 1C, 95-3σ=35 turns, and
hence it satisfies the required property (≥ 16 turns/100d). Meanwhile, comparative
examples 1D and 1E of which areal ratio of precipitates at the grain boundary exceeds
4 % and the grain size in the transverse direction exceeds 5 µm, the twisting property
cannot satisfy the target property, in accordance with 3σ management. Further, in
comparative examples 1D and 1E, though target elongation property (≥ 1.5 %) is satisfied,
the elongation property is inferior to the samples 1A to 1C in accordance with the
present invention. Especially, in comparative example 1D, breakage was observed during
cold working.
[0021] As already mentioned, samples 1A to 1E are obtained by performing same cold working
and heat treatment on the hot worked samples A to E of Table 2. If would be understood
that in order to obtain preferable twisting property, it is preferable that the areal
ratio of the precipitates at the grain boundary in the rod after hot working is at
most 2 % and the grain size in the longitudinal direction is within the range of 5
to 40 µm.
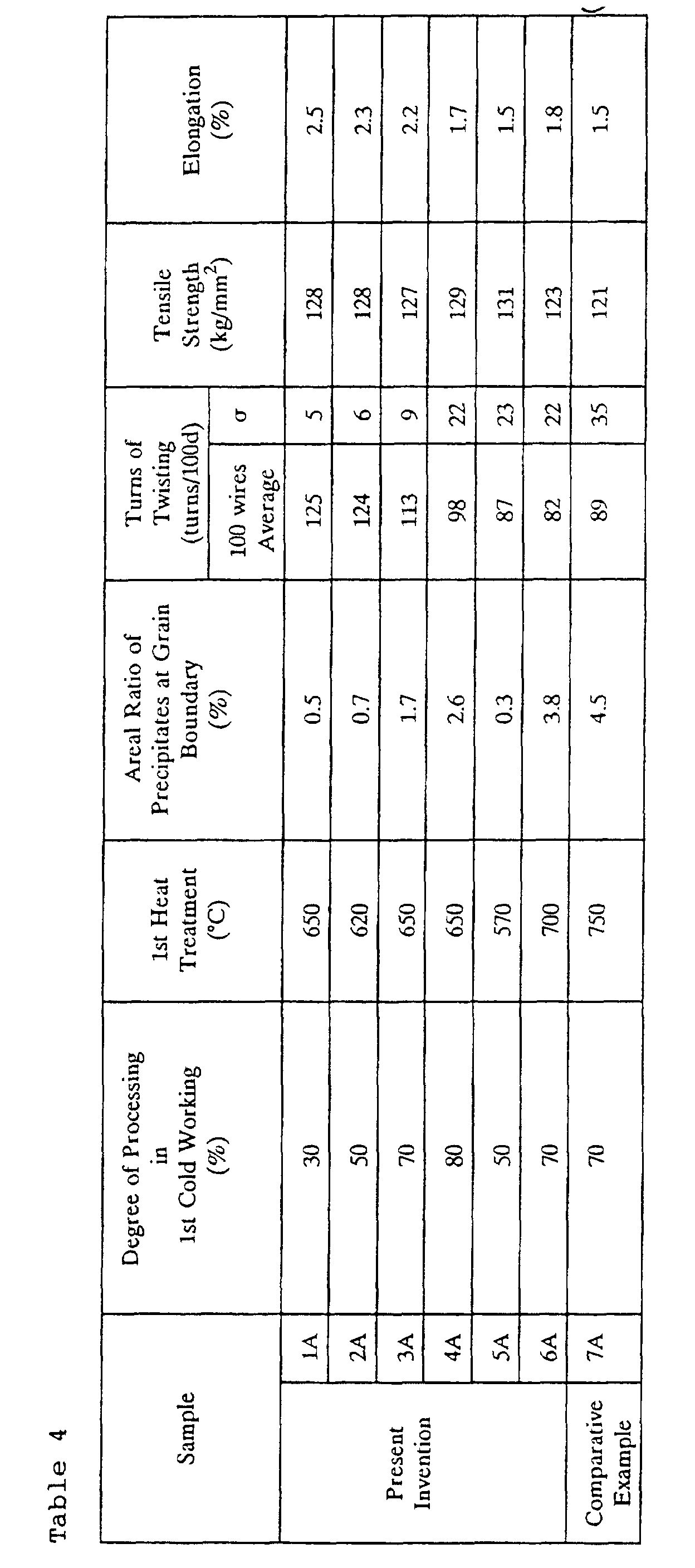
[0022] Table 4 shows influence of the degree of processing of the first cold working and
the temperature of immediately following first heat treatment on the areal ratio of
the precipitates at the grain boundary and various mechanical properties of the wires
in the final wire size. Referring to Table 4, first cold working with various degrees
of processing and first heat treatment at various temperatures were performed on sample
A of Table 2. The processes after the first heat treatment are the same as those described
with reference to Table 3. Samples 1A to 7A all have similar tensile strength higher
than the target property of 120 kg/mm
2.
[0023] However, while samples 1A to 6A belonging to the present invention of which areal
ratio of the precipitates at the grain boundary in the final state is at most 4 %
can satisfy the target value of the twisting property (≥ 16 turns/100d) even under
3σ management, the comparative example 7A of which areal ratio of the precipitates
at the grain boundary in the final state exceeds 4 % cannot satisfy the target value
of the twisting property under 3σ management (89-3σ=89-3x35<16 turns).
[0024] Now, sample 4A is processed with the degree of processing of the first cold working
being 80 %, exceeding 70 %, and hence the areal ratio of the precipitates at the grain
boundary of the final state exceeds 2 %, though not higher than 4 %. Therefore, it
is inferior to samples 1A to 3A in twisting property and elongation. In other words,
the degree of processing of the first cold working should more preferably be at most
70 %.
[0025] Further, for the sample 5A, temperature of the first heat treatment was 570°C, which
was not higher than 600°C. Therefore, the amount of precipitates at the grain boundary
was small. However, since the strain in the wire is not sufficiently removed, the
turns of twisting vary as compared with samples 1A to 3A, and as a result, average
turns of twisting is low and elongation is degraded. Namely, the temperature for the
first heat treatment should more preferably be at least 600°C.
[0026] Further, for the sample 6A, relatively large degree of processing of 70 % was set
for the first cold working, and relatively high temperature of 700°C was set for the
heat treatment. Therefore, the areal ratio of the precipitates at the grain boundary
in the final state was larger as compared with samples 1A to 1C and, as a result,
twisting property and elongation were degraded. Especially when the temperature for
the first heat treatment exceeds 700°C, the areal ratio of the precipitates at the
grain boundary in the final state exceeds 4 % as in comparative example 7A, and hence
target twisting property (≥ 16 turns/100d) cannot be satisfied. In other words, the
temperature for the first heat treatment should preferably be in the range of 600°C
to 700°C.
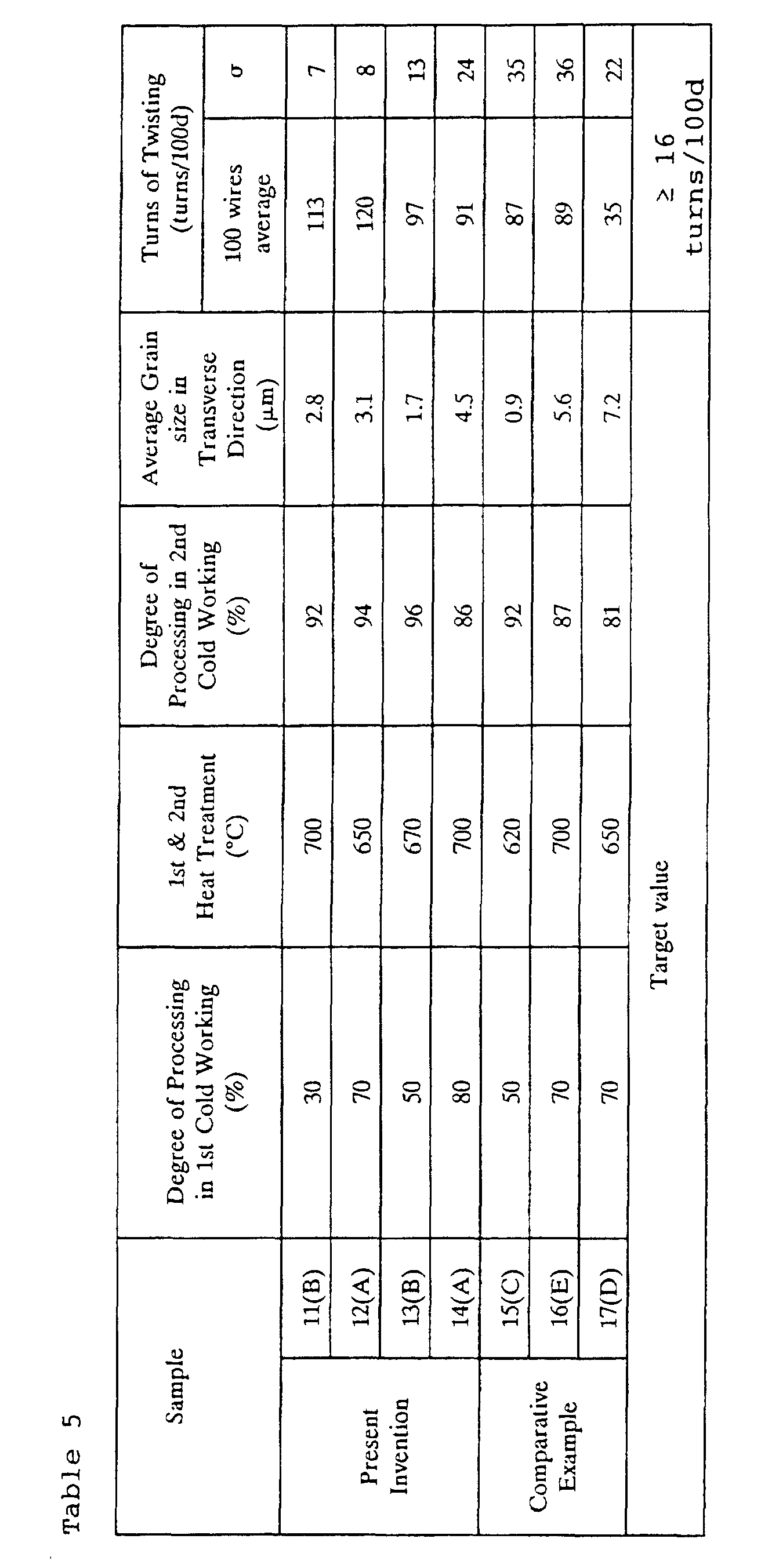
[0027] Table 5 shows influence of hot working, cold working and heat treatment on the average
grain size in the transverse direction of the wire and twisting property of the wire
in the final wire size. The alphabets (A) to (E) appended to the sample numbers of
Table 5 represent that the samples are obtained by performing first cold working,
first heat treatment, scraping, second cold working and Zn-5 wt % Al alloy plating
on the hot worked samples A to E of Table 2. For each sample of Table 5, the temperature
for the first and second heat treatments before and after scraping is set to be the
same temperature.
[0028] As can be seen from Table 5, samples 11 to 14 belonging to the present invention
of which average grain size in the transverse direction in the final wire size is
within the range of 1 to 5 µm can satisfy the target value of twisting property (≥
16 turns/100d) even at the 3σ management. By contrast, comparative examples 15 to
17 of which grain size in the transverse direction is out of the range of 1 to 5 µm
cannot satisfy the target value of twisting property at 3σ management.
[0029] Now, for sample 14, the degree of processing in the first cold working was 80 %,
which is higher than 70 %, so that the grain size in the transverse direction at the
final state exceeds 4 %, though not higher than 5 %, and twisting property is inferior
to samples 11 to 13. Therefore, the degree of processing of the first cold working
should desirably be at most 70 %.
[0030] The small grain size in the transverse direction of comparative example 15 may be
related to small grain size in the longitudinal direction of sample C in Table 2.
As compared with samples A and B, sample C has relatively large areal ratio of the
precipitates at the grain boundary, and areal ratio of the precipitates at the grain
boundary at the final wire size of sample 15 was increased to 4.4 %, even though the
temperatures for the first and second heat treatments were relatively low.
[0031] Further, in comparative example 17 having very large grain size in the transverse
direction, breakage was observed during the second cold working.
[0032] Then, alloys such as shown in Table 6 were melt and cast in order to see the influence
of impurity on the invar type alloy wire. Referring to Table 6, numerical values related
to respective elements denote percentage by weight in the alloy.
Table 7
Sample |
Twisting Property (turns/100d) |
Tensile Strength (kg/mm2) |
Elongation (%) |
|
100 wires average |
σ |
|
|
Present Invention |
21 |
125 |
5 |
127 |
2.5 |
22 |
122 |
6 |
127 |
2.5 |
23 |
115 |
11 |
127 |
2.3 |
Comparative Example |
24 |
75 |
20 |
127 |
2.0 |
25 |
96 |
27 |
126 |
2.1 |
26 |
74 |
22 |
126 |
1.9 |
27 |
48 |
25 |
125 |
1.7 |
Target Property |
≧ 16 (turns/100d) |
≧ 120 |
≧ 1.5 |
[0033] Table 7 shows various mechanical properties at the final wire size of the invar type
alloy wires having such compositions as shown in Table 6.
[0034] Of each of the samples having such compositions as shown in Table 6, a billet was
heated to 1200°C, and thereafter cooled to about 600°C at the cooling rate of 10°C/sec,
while it is rolled by shaping rolls. The obtained rolled rods were examined and it
was found that every rod has the areal ratio of the precipitates at the grain boundary
of about 0.2 % and average grain size of about 22 µm in the longitudinal direction.
[0035] The rolled rods which were hot worked were all subjected to a first cold drawing
of 22 %, scraping, heat treatment at 650°C for 10 hours, a second cold drawing of
86 % and plating with Zn-5 wt % Al alloy.
[0036] Referring to Table 7, samples 21 to 27 all have similar tensile strength exceeding
the target value of 120 kg/mm
2. However, it is apparent that comparative examples 24 to 27 are inferior in twisting
property and elongation as compared with the samples 21 to 23 belonging to the present
invention.
[0037] More specifically, samples 21 to 23 belonging to the present invention containing
P of at most 0.01 percent by weight, S of at most 0.004 percent by weight, O of at
most 0.005 percent by weight and N of at most 0.008 percent by weight have superior
twisting property. Especially, samples 21 and 22 which include P of at most 0.005
percent by weight, S of at most 0.002 percent by weight O of at most 0.003 percent
by weight and N of at most 0.006 percent by weight only as impurities have superior
twisting property and stability (that is, small a).
[0038] Comparative examples 24 to 27 all include at least one impurity of P exceeding 0.01
percent by weight, S exceeding 0.004 percent by weight O exceeding 0.005 percent by
weight N exceeding 0.008 percent by weight, so that these examples are far inferior
in twisting property to the samples 21 to 23 of the present invention, and target
value (≥ 16 turns/100d) of the twisting property cannot be achieved.
[0039] In any of the above described embodiments, various properties of the wire are hardly
influenced when Mo of the alloy element is replaced by V, and hence V can be similarly
used as Mo.
[0040] As described above, according to the present invention, toughness, especially twisting
property of an invar type alloy wire having high strength can be improved, and by
using the same, production yield of overhead conductor cables can be improved.
[0041] Although the present invention has been described and illustrated in detail, it is
clearly understood that the same is by way of illustration and example only and is
not to be taken by way of limitation, the scope of the present invention being limited
only by the terms of the appended claims.
1. An invar type alloy wire having high toughness, high strength and low thermal expansion
property, containing, as main alloy element, Fe and Ni, wherein the average grain
size in transverse direction of said wire in a final wire size is within a range of
1 to 5 µm; wherein the areal ratio of precipitates existing at grain boundary of said wire
in said final wire size is at most 4 % and wherein impurity contained in said alloy
is at most 0.01 percent in weight of P, at most 0.004 percent by weight of S, at most
0.005 percent of weight of O and at most 0.008 percent by weight of N.
2. The invar type alloy wire according to claim 1, wherein areal ratio of said precipitates
is at most 2 %.
3. The invar type alloy wire according to claim 1, wherein average grain size in transverse
direction of said wire in said final wire size is within a range of 1.5 to 4 µm.
4. The invar type alloy wire according to claim 1, wherein part of Ni in said invar type
alloy is replaced by Co.
5. The invar type alloy wire according to claim 1, wherein said invar type alloy further
contains, as strengthing element, at least one of Mo, Cr, C, W, Nb, Ti, V and Si.
6. The invar type alloy wire according to claim 1, wherein said invar type alloy further
contains, as deoxidizer, at least one of Mn, Al, Mg, Ti and Ca.
7. The invar type alloy wire according to claim 1, wherein impurity contained in said
alloy is at most 0.005 percent by weight of P, at most 0.002 percent by weight of
S, at most 0.003 percent of weight of O and at most 0.006 percent by weight of N.
8. A method of manufacturing an invar type alloy wire having high toughness, high strength
and low thermal expansion property, comprising the steps of:
preparing an invar type alloy containing, as main elements, Fe and Ni, wherein impurity
contained in said alloy is at most 0.01 percent in weight of P, at most 0.004 percent
by weight of S, at most 0.005 percent of weight of O and at most 0.008 percent by
weight of N;
performing hot working and heat treatment in combination to set areal ratio of precipitates
existing at grain boundary of said alloy to be at most 2 % and to set average grain
size in longitudinal direction of a rod shape processed by said hot working and heat
treatment to be within a range of 5 to 40 µm ; and therafter, performing cold working and heat treatment in combination to set
areal ratio of precipitates existing at the grain boundary of said alloy in final
wire size of said wire to be at most 4 % and to set average grain size in transverse
direction of said wire in said final wire size to be within a range of 1 to 5 µm.
9. The method of manufacturing an invar type alloy wire according to claim 8, wherein
areal ratio of said precipitates after said hot working and heat treatment in combination
is set to be at most 1 % and areal ratio of said precipitates in said final wire size
is set to be at most 2 %.
10. The method of manufacturing an invar type alloy wire according to claim 8, wherein
said alloy is subjected to a first cold working at a degree of processing of at most
70% after said hot working, and thereafter subjected to at least one heat treatment
at a temperature within a range of 600 to 700°C.
1. Invarlegierungsdraht mit hoher Zähigkeit, hoher Härte und niedrigem thermischen Ausdehungsvermögen,
der als Hauptlegierungselement Fe und Ni enthält, wobei die mittlere Korngröße in
Querrichtung des Drahtes in der endgültigen Drahtstärke in einem Bereich von 1 bis
5 µm liegt; wobei das Flächenverhältnis von Niederschlägen, die an der Korngrenze
des Drahtes in der endgültigen Drahtstärke vorliegen, höchstens 4 % beträgt und wobei
die Verunreinigung, die in der Legierung enthalten ist, höchstens 0,01 Gewichtsprozent
P, höchstens 0,004 Gewichtsprozent S, höchstens 0,005 Gewichtsprozent O und höchstens
0,008 Gewichtsprozent N beträgt.
2. Invarlegierungsdraht nach Anspruch 1, wobei das Flächenverhältnis der Niederschläge
höchstens 2 % beträgt.
3. Invarlegierungsdraht nach Anspruch 1, wobei die mittlere Korngröße in Querrichtung
des Drahtes in der endgültigen Drahtstärke in einem Bereich von 1,5 bis 4 µm liegt.
4. Invarlegierungsdraht nach Anspruch 1, wobei ein Teil des Ni in der Invarlegierung
durch Co ersetzt ist.
5. Invarlegierungsdraht nach Anspruch 1, wobei die Invarlegierung weiterhin zumindest
eines von Mo, Cr, C, W, Nb, Ti, V und Si als Härtungselement enthält.
6. Invarlegierungsdraht nach Anspruch 1, wobei die Invarlegierung weiterhin zumindest
eines von Mn, Al, Mg, Ti und Ca als Reduktionsmittel enthält.
7. Invarlegierungsdraht nach Anspruch 1, wobei die Verunreinigung, die in der Legierung
enthalten ist, höchstens 0,005 Gewichtsprozent P, höchstens 0,002 Gewichtsprozent
S, höchstens 0,003 Gewichtsprozent O und höchstens 0,006 Gewichtsprozent N beträgt.
8. Verfahren zur Herstellung eines Invarlegierungsdrahtes mit hoher Zähigkeit, hoher
Härte und niedrigem thermischen Ausdehnungsvermögen, umfassend die Schritte:
Herstellen einer Invarlegierung, die als Hauptelemente Fe und Ni enthält, wobei die
Verunreinigung, die in der Legierung enthalten ist, höchstens 0,01 Gewichtsprozent
P, höchstens 0,004 Gewichtsprozent S, höchstens 0,005 Gewichtsprozent O und höchstens
0,008 Gewichtsprozent N beträgt;
Durchführen von Warmformgebung und Wärmebehandlung in Kombination, um das Flächenverhältnis
der Niederschläge, die an der Korngrenze der Legierung vorliegen, auf höchstens 2
% einzustellen und um die mittlere Korngröße in Längsrichtung einer Stabform, die
durch die Warmformgebung und die Wärmebehandlung hergestellt wurde, in einem Bereich
von 5 bis 40 µm einzustellen; und danach Durchführung von Kaltformgebung und Wärmebehandlung
in Kombination, um das Flächenverhältnis der Niederschläge, die an der Korngrenze
der Legierung in der endgültigen Drahtstärke vorliegen, auf höchstens 4 % einzustellen
und um die mittlere Korngröße in Querrichtung des Drahtes in der endgültigen Drahtstärke,
in einem Bereich von 1 bis 5 µm einzustellen.
9. Verfahren zur Herstellung eines Invarlegierungsdrahtes nach Anspruch 8, wobei das
Flächenverhältnis der Niederschläge nach der Warmformgebung und Wärmebehandlung in
Kombination auf höchstens 1 % eingestellt wird und das Flächenverhältnis der Niederschläge
in der endgültigen Drahtstärke auf höchstens 2 % eingestellt wird.
10. Verfahren zur Herstellung eines Invarlegierungsdrahtes nach Anspruch 8, wobei die
Legierung einer ersten Kaltformgebung bei einem Verarbeitungsgrad von höchstens 70
% nach der Warmformgebung unterworfen wird und danach zumindest einer Warmformgebung
bei einer Temperatur in einem Bereich von 600 bis 700 °C unterworfen wird.
1. Fil métallique en alliage de type invar ayant une grande ténacité, une grande résistance
mécanique et de faibles propriétés de dilatation thermique, contenant, comme éléments
d'alliage principaux, Fe et Ni, où la taille moyenne de grains dans la direction transversale
dudit fil métallique dans une taille de fil métallique finale est située dans un domaine
de 1 à 5 µm ; où le rapport surfacique des précipités existant aux joints des grains
dudit fil métallique dans ladite taille de fil métallique finale est d'au plus 4 %
et où les impuretés contenues dans ledit alliage sont d'au plus 0,01 % en masse de
P, d'au plus 0,004 % en masse de S, d'au plus 0,005 % en masse de O et d'au plus 0,008
% en masse de N.
2. Fil métallique en alliage de type invar selon la revendication 1, où le rapport surfacique
desdits précipités est d'au plus 2 %.
3. Fil métallique en alliage de type invar selon la revendication 1, où la taille moyenne
de grains dans la direction transversale dudit fil métallique dans ladite taille de
fil métallique finale est située dans un domaine de 1,5 à 4 µm.
4. Fil métallique en alliage de type invar selon la revendication 1, où une partie de
Ni dans ledit alliage de type invar est remplacée par Co.
5. Fil métallique en alliage de type invar selon la revendication 1, où ledit alliage
de type invar contient en outre, comme élément renforçant, au moins un élément parmi
Mo, Cr, C, W, Nb, Ti, V et Si.
6. Fil métallique en alliage de type invar selon la revendication 1, où ledit alliage
de type invar contient en outre, comme désoxydant, au moins un élément parmi Mn, Al,
Mg, Ti et Ca.
7. Fil métallique en alliage de type invar selon la revendication 1, où les impuretés
contenues dans ledit alliage sont d'au plus 0,005 % en masse de P, d'au plus 0,002
% en masse de S, d'au plus 0,003 % en masse de O et d'au plus 0,006 % en masse de
N.
8. Procédé de fabrication d'un fil métallique en alliage de type invar ayant une grande
ténacité, une grande résistance mécanique et de faibles propriétés de dilatation thermique,
comprenant les étapes de :
préparation d'un alliage de type invar contenant, comme éléments principaux, Fe et
Ni, où les impuretés contenues dans ledit alliage sont d'au plus 0,01 % en masse de
P, d'au plus 0,004 % en masse de S, d'au plus 0,005 % en masse de O et d'au plus 0,008
% en masse de N ;
mise en oeuvre d'un travail à chaud et d'un traitement thermique en combinaison pour
fixer le rapport surfacique des précipités existant aux joints des grains dudit alliage
à au plus 2 % et pour fixer la taille moyenne de grains dans la direction longitudinale
d'une forme de barre formée par ledit travail à chaud et ledit traitement thermique
dans un domaine de 5 à 40 µm, puis mise en oeuvre d'un travail à froid et d'un traitement
thermique en combinaison pour fixer le rapport surfacique des précipités existant
aux joints des grains dudit alliage dans la taille de fil métallique finale dudit
fil métallique à au plus 4 % et pour fixer la taille moyenne de grains dans la direction
transversale dudit fil métallique dans ladite taille de fil métallique finale dans
un domaine de 1 à 5 µm.
9. Procédé de fabrication d'un fil métallique en alliage de type invar selon la revendication
8, où le rapport surfacique desdits précipités après ledit travail à chaud et ledit
traitement thermique en combinaison est fixé à au plus 1 % et le rapport surfacique
desdits précipités dans ladite taille de fil métallique finale est fixé à au plus
2 %.
10. Procédé de fabrication d'un fil métallique en alliage de type invar selon la revendication
8, où ledit alliage est soumis à un premier travail à froid à un degré de mise en
forme d'au plus 70 % après ledit travail à chaud, puis soumis à au moins un traitement
thermique à une température située dans un domaine de 600 à 700°C.