[0001] Die vorliegende Erfindung betrifft Chrom(VI)freie, Chrom(III)-haltige im wesentlichen
zusammenhängende Konversionsschichten gemäß Anspruch 1, ein Verfahren zu deren Herstellung
gemäß Anspruch 4, sowie eine Verwendung von Passivierungslösungen gemäß Anspruch 10.
[0002] Metallische Werkstoffe insbesondere Eisen und Stahl werden verzinkt oder verkadmet,
um sie vor korrosiven Umwelteinflüssen zu schützen. Der Korrosionsschutz des Zinks
beruht darauf, daß es noch unedler ist als das Grundmetall und deshalb den korrosiven
Angriff zunächst ausschließlich auf sich zieht, es fungiert als Opferschicht. Das
Grundmetall des betreffenden verzinkten Bauteils bleibt unversehrt, solange es noch
durchgehend mit Zink bedeckt ist, und die mechanische Funktionalität bleibt über längere
Zeiträume erhalten als bei unverzinkten Teilen. Dicke Zinkschichten gewähren natürlich
einen höheren Korrosionsschutz als dünne Schichten - der korrosive Abtrag von dicken
Schichten dauert eben länger.
[0003] Der korrosive Angriff auf die Zinkschicht ihrerseits kann durch das Aufbringen einer
Chromatierung stark verzögert werden, und somit wird auch die Grundmetallkorrosion
noch weiter hinausgezogen als durch eine Verzinkung alleine. Der Korrosionsschutz
durch das Schichtsystem Zink/Chromatierung ist erheblich höher als nur durch eine
gleichdicke Zinkschicht. Ferner wird durch eine Chromatierung auch die optische Beeinträchtigung
eines Bauteils durch Umwelteinflüsse hinausgezogen - auch die Korrosionsprodukte von
Zink, der sogenannte Weißrost, wirken sich störend auf das Aussehen eine Bauteils
aus.
[0004] Die Vorteile einer aufgebrachten Chromatierung sind so groß, daß fast jede galvanisch
verzinkte Oberfläche zusätzlich auch chromatiert wird. Der Stand der Technik kennt
vier nach ihren Farben benannte Chromatierungen, die jeweils durch Behandeln (Tauchen,
Spritzen, Rollen) einer verzinkten Oberflache mit der entsprechenden wäßrige Chromatierungslösung
aufgebracht werden. Ferner sind Gelb- und Grünchromtierungen für Aluminium bekannt,
die auf analoge Weise hergestellt werden. Es handelt sich jedenfalls um unterschiedlich
dicke Schichten aus im wesentlichen amorphem Zink/Chromoxid (bzw. Aluminium/Chromoxid)
mit unstöchiometrischer Zusammensetzung, einem gewissen Wassergehalt und eingebauten
Fremdionen. Bekannt und nach DIN 50960 Teil 1 in Verfahrensgruppen eingeteilt sind:
1) Farblos- und Blauchromatierungen, Gruppen A und B
[0005] Die Blauchromatierungsschicht ist bis zu 80 nm dick, schwach blau in der Eigenfarbe
und weist je nach Schichtdicke eine durch Lichtbrechung erzeugte goldene, rötliche,
bläuliche, grünliche oder gelbe Irisierfarbe auf. Sehr dünne Chromatschichten fast
ohne Eigenfarbe werden als Farbloschromatierungen (Gruppe A) eingestuft. Die Chromatierungslösung
kann in beiden Fällen sowohl aus sechswertigen als auch aus dreiwertigen Chromaten
sowie Gemischen aus beiden, ferner aus Leitsalzen und Mineralsäuren bestehen. Es gibt
fluoridhaltige und fluoridfreie Varianten. Die Anwendung der Chromatierungslösungen
erfolgt bei Raumtemperatur. Der Korrosionsschutz von unverletzten Blauchromatierungen
beläuft sich auf 10-40 h im Salzsprühschrank nach DIN 50021 SS bis zum ersten Auftreten
von Korrosionsprodukten. Die Mindestforderung für die Verfahrensgruppen A und B nach
DIN 50961 Kapitel 10 Tabelle 3 beträgt 8 h für Trommelware und 16 h für Gestellware.
2) Gelbchromatierungen, Gruppe C
[0006] Die Gelbchromatierungsschicht ist etwa 0,25-1 µm dick, goldgelb gefärbt und häufig
stark rotgrün irisierend. Die Chromatierungslösung besteht im wesentlichen aus in
Wasser gelösten sechswertigen Chromaten, Leitsalzen und Mineralsäuren. Die gelbe Farbe
rührt von dem signifikanten Anteil (80-220 mg/m2) sechswertigen Chroms her, das neben
dem bei der Schichtbildungsreaktion durch Reduktion erzeugten dreiwertigen Chrom,
eingebaut wird. Die Anwendung der Chromatierungslösungen erfolgt bei Raumtemperatur.
Der Korrosionsschutz von unverletzten Gelbchromatierungen beläuft sich auf 100-200
h im Salzsprühschrank nach DIN 50021 SS bis zum ersten Auftreten von Korrosionsprodukten.
Die Mindesfforderung für die Verfahrensgruppe C nach DIN 50961 Kapitel 10 Tabelle
3 beträgt 72 h für Trommelware und 96 h für Gestellware.
3) Olivchromatierungen, Gruppe D
[0007] Die typische Olivchromatierungsschicht ist bis zu 1,5 µm dick, deckend olivgrün bis
olivbraun. Die Chromatierungslösung besteht im wesentlichen aus in Wasser gelösten
sechswertigen Chromaten, Leitsalzen und Mineralsäuren, insbesondere Phosphaten bzw.
Phosphorsaure und kann auch Formiate enthalten. In die Schicht werden erhebliche Mengen
von Chrom(VI) (300-400 mg/m2) eingelagert. Die Anwendung der Chromatierungslösungen
erfolgt bei Raumtemperatur. Der Korrosionsschutz von unverletzten Olivchromatierungen
beläuft sich auf 200-400 h im Salzsprühschrank nach DIN 50021 SS bis zum ersten Auftreten
von Korrosionsprodukten. Die Mindestforderung für die Verfahrensgruppe D nach DIN
50961 Kapitel 10 Tabelle 3 beträgt 72 h für Trommelware und 120 h für Gestellware.
4) Schwarzchromatierungen, Gruppe F
[0008] Die Schwarzchromatierungsschicht ist im Grunde eine Gelb- oder Olivchromatierung,
in die kolloidales Silber als Pigment eingelagert ist. Die Chromatierungslösungen
haben in etwa die gleiche Zusammensetzung wie Gelb- oder Olivchromatierungen und enthalten
zusätzlich Silberionen. Auf Zinklegierungsschichten wie Zn/Fe, Zn/Ni oder Zn/Co lagert
sich bei geeigneter Zusammensetzung der Chromatierungslösung Eisen-, Nickel- oder
Cobaltoxid als Schwarzpigment in die Chromatschicht ein, so daß in diesen Fällen Silber
nicht erfoderlich ist. In die Chromatschichten werden erhebliche Mengen Chrom(VI)
eingebaut, und zwar je nach dem, ob eine Gelb- oder eine Olivchromatierung die Basis
darstellt zwischen 80 und 400 mg/m2. Die Anwendung der Chromatierungslösungen erfolgt
bei Raumtemperatur. Der Korrosionsschutz von unverletzten Schwarzchromatierungen auf
Zink beläuft sich auf 50-150 h im Salzsprühschrank nach DIN 50021 SS bis zum ersten
Auftreten von Korrosionsprodukten. Die Mindestforderung für die Verfahrensgruppe E
nach DIN 50961 Kapitel 10 Tabelle 3 beträgt 24 h für Trommelware und 48 h für Gestellware.
Schwarzchromatierungen auf Zinklegierungen liegen erheblich oberhalb der genannten
Werte.
5) Grünchromatierungen für Aluminium, Gruppe E
[0009] Die Grünchromatierung auf Aluminium (bekannt auch als Alugrün) ist mattgrün und nicht
irisierend. Die Chromatierungslösung besteht im wesentlichen aus in Wasser gelösten
sechswertigen Chromaten, Leitsalzen und Mineralsäuren sowie insbesondere aus Phosphaten
und Silicofluoriden. Die sich bildende Chromat-/Phosphatschicht ist, wie lod/Stärketests
zeigen, entgegen der landläufigen Meinung nicht immer 100%ig Chrom(VI)frei. Die Herstellung
von Alugrün in Chromatierungslösungen auf der Basis von ausschließlich Chrom(III)
ist unbekannt.
[0010] Nach dem Stand der Technik lassen sich dicke Chromatschichten mit hohem Korrosionsschutz
> 100 h im Salzsprühschrank nach DIN 50021 SS bzw. ASTM B 117-73 bis zum Auftreten
von ersten Korrosionsprodukten nach DIN 50961 (Juni 1987) Kapitel 10, insbesondere
Kapitel 10.2.1.2, ohne Versiegelung und weitere besondere Nachbehandlung (DIN 50961,
Kapitel 9) nur durch Behandlung mit gelösten ausgesprochen giftigen Chrom(VI)-Verbindungen
herstellen. Dementsprechend enthalten die Chromatschichten mit den genannten Anforderungen
an den Korrosionsschutz noch diese ausgespochen giftigen und karzinogenen Chrom(VI)Verbindungen,
die zudem nicht vollständig in der Schicht immobilisert sind. Die Chomatierung mit
Chrom(VI)-Verbindungen ist hinsichtlich Arbeitsschutz problematisch. Der Gebrauch
von verzinkten und mit Chrom(VI)-Verbindungen hergestellten Chromatierungen wie z.B.
die weitverbreiteten Gelbchromatierungen z.B. auf Schrauben stellt ein Gefahrdungspotential
der Bevölkerung dar und erhöht das allgemeine Krebsrisiko.
[0011] Die US 43 84 902, insbesondere mit den Beispielen 1, 2, 4 und 5 beschreibt Konversionsschichten,
die den Anforderungen im Salzsprühtest genügen. Es handelt sich dabei in allen Fällen
um eine Cer-haltige Schicht, die eine durch das Cer(IV)-lon hervorgehobene
gelbliche Färbung aufweist. Die Beispiele enthalten in der Badlösung nur Cer(III) sowie Wasserstoffperoxid
als Oxidationsmittel. In der Beschreibung ist diskutiert, daß Wasserstoffperoxid im
Sauren zwar kein Oxidationsmittel für Ce(III) darstellt, das jedoch an der Oberfläche
während der Abscheidung der pH-Wert so weit ansteigt, daß eine ausreichende Menge
Ce(IV) entstehen kann. Die gelbliche Farbe, die mit der vorliegenden Badzusammensetzung
erreicht worden ist, deutet in der Tat darauf hin, daß eine Oxidation stattgefunden
hat. Aber nur eine Oxidation von Ce(III) zu Ce(IV). Vierwertiges Cer ist ein noch
stärkeres Oxidationsmittel als sechswertiges Chrom, weshalb Ce(IV) aus Cr(III) das
zu vermeidende Cr(VI) erzeugen wird. Cr(VI) hat eine sehr starke gelbe Farbe und ist
als Korrosionsschutzmittel bekannt. Die in der US 43 84 902 beschriebene Schicht ist
somit nicht frei von sechswertigem Chrom.
[0012] Die erfindungsgemäße Schicht ist jedoch ohne Oxidationsmittel hergestellt und daher
frei von sechswertigem Chrom. Das ist insbesondere daran zu erkennen, daß die erfindungsgemäße
Schicht nicht gelb ist.
[0013] Selbst wenn die gelbe Farbe und der erhöhte Korrosionsschutz allein von Ce(IV) erzeugt
worden sein sollte, so bietet die erfindungsgemäße Schicht auch ohne diesen teuren
und seltenen Zusatz den gewünschten Korrosionsschutz.
[0014] US 43 59 348 beschreibt ebenfalls Konversionsschichten, die den oben genannten Anforderungen
im Salzsprühtest genügen. Auch hier handelt es sich in allen Fällen an eine Cer-haltige
Schicht, die eine durch das Cer(IV)-lon hervorgehobene gelbliche Färbung aufweist.
Dieses Dokument geht daher nicht über die US 43 84 902 hinaus.
[0015] Darüberhinaus offenbart Database WPI, Derwent Publications Ltd., London, GB; AN 94-014365
& SU-A-1781316, daß Cr
3+ zusammen mit Kaliumnitrat und Kaliumhypophosphit und einem nicht näher definierten
"joiner's glue" eine anorganische Korrosionsbeschichtung zum Schützen von zinkbeschichteten
Stahl ergeben soll.
[0016] Ferner offenbart GB-A-2 097 024 die Behandlung von Metalloberflächen zur Verbesserung
der Korrosionsschutzes auf Zink und Zinklegierungsoberflächen mit einer wäßrigen sauren
Lösung, einem Oxidationsmittel und wenigstens einem Metall, ausgewählt aus der Gruppe
bestehend aus Kobalt, Nickel, Molybdän, Mangan, Aluminium, Lanthan, Lanthaniden-Mischungen
oder Cerionen oder Mischungen davon oder anstelle davon Eisen- und Kobaltionen. Ferner
offenbart die GB-A-2 097 024 die Verwendung von dreiwertigen Chromionen und Eisenionen
in Kombination mit einem zusätzlichen Metall ausgewählt aus der Gruppe bestehend aus
den oben genannten oder Cerionen, jedoch werden hauptsächlich Kombinationen von Chrom(III)
in Kombination mit einem Oxidationsmittel und Cer- oder Lanthanionen beschrieben.
[0017] EP-A-337 411 offenbart saure Chrom(III)-haltige und fluoridhaltige Passivierungsbäder
für Oberflächen aus Zink und Zinklegierungen unter Verwendung von Chromfluorokomplexen,
wobei es sich bei der Chromatierung gemäß der EP-A-337 411 um eine Blauchromatierung
handelt, welche Fluoridionen einsetzt.
[0018] DE-A-4 135 524 offenbart ein Verfahren zur Chromatierung von Zink mit einer Lösung
vom pH 1,2-3, die 0,1-50g/l Chrom(III)-Onalat-Komplex enthält.
[0019] Daher ist es Aufgabe der vorliegenden Erfindung, eine chrom(VI)freie, dicke Konversionsschicht
mit hohem Chromanteil auf Zink oder Zinklegierungen zur Verfügung zu stellen.
[0020] Die Lösung dieser Aufgabe erfolgt bezüglich einer Schicht durch die Merkmale des
Anspruchs 1, verfahrenstechnisch durch die Merkmale des Anspruchs 4 und hinsichtlich
einer Verwendung durch die Merkmale des Anspruchs 10.
Die Unteransprüche 2 bis 3, 5 bis 9 und 11 bis 18 stellen bevorzugte Ausführungsformen
der vorliegenden Erfindung dar.
[0021] Die Anmelderin hat für die Zwecke der vorliegenden Erfindungen den Begriff "Chromitierung"
geprägt, um die vorliegende Erfindung von den im Stand der Technik üblichen Chromatierungen
abzugrenzen und klar zu machen, daß weder die erhaltene Konversionsschicht, hoch die
erfindungsgemäßen Zusammensetzungen (Konzentrate/Passivierungsbäder) mit welcher man
die Beschichtungen herstellt, das toxische Chrom (VI) enthalten, der erreichte Korrosionsschutz
jedoch denjenigen der Gelbchromatierung übertrifft.
[0022] EP 00 34 040 A1 beschreibt zwar eine Vielzahl von Schichten, von deren größerer Gruppe
(unter den von Barnes/Ward dargelegten Standardbedingungen erzeugt) die Farbe nicht
genannt, jedoch als klar bezeichnet wird. Zwei Beispiele, nämlich Nr. 16 und 17, beschreiben
eine grünliche Borat-haltige Schicht, die als wolkig-stumpf bis undurchsichtig bezeichnet
wird.
[0023] Beispiel 14 beschreibt eine Schicht mit einem Korrosionsschutz von nur
4 Stunden.
[0024] Die Unteransprüche stellen bevorzugte Ausführungsformen der vorliegenden Erfindung
dar.
[0025] Bezüglich der Merkmale von Anspruch 2 ist folgendes festzustellen:
[0026] Einige Elemente konnten bei der Glimmentladungsspektrometrie nicht erfaßt, andere
nicht kalibriert werden. Deshalb wurden die Phasen Chrom/(Chrom+Zink) miteinander
verglichen. Der Chromindex ist der durchschnittliche Chromgehalt in Dezimalprozent
(%/100) in der Schicht > 1% Cr, multipliziert mit der Schichtdicke in nm (vgl. Fig.37).
Der Chrom-Index ist proportional zur Chrommenge auf der Oberfläche (mg/m
2).
[0027] Weitere Vorteile und Merkmale der vorliegenden Erfindung ergeben sich aufgrund der
Beschreibung von Ausführungsbeispielen sowie anhand von theoretischen Uberlegungen,
die einerseits nicht bindend sind und andererseits in Kenntnis der vorliegenden Erfindung
von den Erfindern angestellt wurden und anhand der Zeichnung.
[0028] Es zeigt:
Fig. 1: Einen Vergleich der vorliegenden Erfindung mit Blau- und Gelbchromatierung;
Fig.2: Eine Rasterelektronenmikroskopische Aufnahme, Vergrößerung 40000-fach, die
einen Vergleich der vorliegenden Erfindung ("Chromitierung") mit Blau- und Gelbchromatierung
zeigt.
Fig.3: Ein Farbfoto, welches die Bandbreite der Irisfarbe gemäß der vorliegenden Erfindung
auf Zinkoberflächen zeigt;
Fig.4: Beschichtungen des Standes der Technik der EP 0 034 040;
Fig. 5 bis Fig. 36 Tiefenprofilanalysen von erfindungsgemäßen Schichten und Schichten,
wie sie sich aus den herkömmlichen Blau- und Gelbchromatierungen ergeben, wobei die
Tiefenprofilanalysen durch Glimmentladungsspektrometrie gemessen wurden (Spektrometer:
JY5000RF); und
Fig. 37 eine Tabelle mit der Auswertung der Tiefenprofilanalysen aus den Fig. 5 bis
36.
Beispiel 1
[0029] Es wurde folgendes Experiment durchgeführt:
[0030] Kleine Stahlteile wurden elektrolytisch glanzverzinkt (15 µm) und nach der Verzinkung
einzeln getaucht in eine kochende (100 °C), wäßrige Lösung enthaltend:
100 g/l CrCl3 · 6 H2O (dreiwertiges Chromsalz)
100 g/l NaNO3
15,75 g/l NaF
26,5 g/l Citronensäure · 1 aq
die zuvor mit Natronlauge auf einen pH-Wert von 2,5 eingestellt wurde. Die Tauchzeit
betrug 30 s. Die Teile wurden daraufhin mit Wasser gespült und im Luftstrom getrocknet.
Auf den Teilen hatte sich eine grünliche stark irisierende Schicht, wie sich später
herausstellte, aus Zink/Chromoxid gebildet. Überraschenderweise zeigte sich beim Korrosionstest
im Salzsprühschrank nach DIN 50021 SS, daß die ausgebildete Chromatchicht einen Korrosionsschutz
bis zum Auftreten von ersten Korrosionsprodukten nach DIN 50961 Kapitel 10, insbesondere
Kapitel 10.2.1.2 von sensationellen 1000 h aufwies.
[0031] Die neue grünliche Chromatschicht hatte eine Schichtdicke von ca. 800 nm und wurde
auf chrom(VI)freiem Wege erzeugt und war nachweislich chrom(VI)frei.
[0032] Die Herstellungsmethode nach Beispiel 1 für die neue grünliche chrom(VI)freie Chromatierung
ist für konventionelle Anlagen wegen der relativ hohen Temperatur der Prozeßlösung
nicht sehr wirtschaftlich. Weitere theoretische Überlegungen zur chrom(VI)freien Chromatierung
und weitere Versuche führten schließlich zu wirtschaftlichen Herstellungsbedingungen.
Theoretische Überlegungen zur chrom(VI)freien Chromatierung
[0033] Die Chromatierung von Zink geschieht durch die Ausbildung einer sogenannten Konversionsschicht
auf der Zinkoberfläche, d. h. die Zinkoberfläche reagiert chemisch mit der Chromatierungslösung
und wird in eine Chromatschicht konvertiert. Die Ausbildung von Konversionsschichten
ist ein dynamischer Prozeß jenseits vom chemischen Gleichgewicht. Zur Beschreibung
der zugrundeliegenden Prozesse muß man sich deshalb der chemischen Kinetik bedienen.
Mit dem speziell aufgestellten kinetischen Modell ließen sich Ansatzpunkte zur Optimierung
der vorliegenden Erfindung gewinnen.
[0034] Die Konversionsschichtbildung in einer Chromatierungslösung auf der Basis von Chrom
(III) läßt sich anhand von zwei Reaktionsgleichungen beschreiben:
[0035] I Elementares Zink geht durch Säureangriff in Lösung:

[0036] II und fällt zusammen mit Chrom(III) als Zinkchromoxid auf der Zinkoberfläche aus:

[0037] Das kinetische Modell muß Differentialgleichungen für die Konzentrationsverläufe
von Zn
2, H
+, Cr
(III) und für das Dickenwachstum der ZnCrO-Schicht umfassen. In den Reaktionsgeschwindigkeitsansätzen
wurde durch Einfügung des Terms 1/(1+
p1·
mZnCrO)
2 berücksichtigt, daß Reaktion I durch die aufwachsende Passivschicht zunehmend gebremst
wird. P1 ist ein Maß für die Dichtigkeit der Schicht.
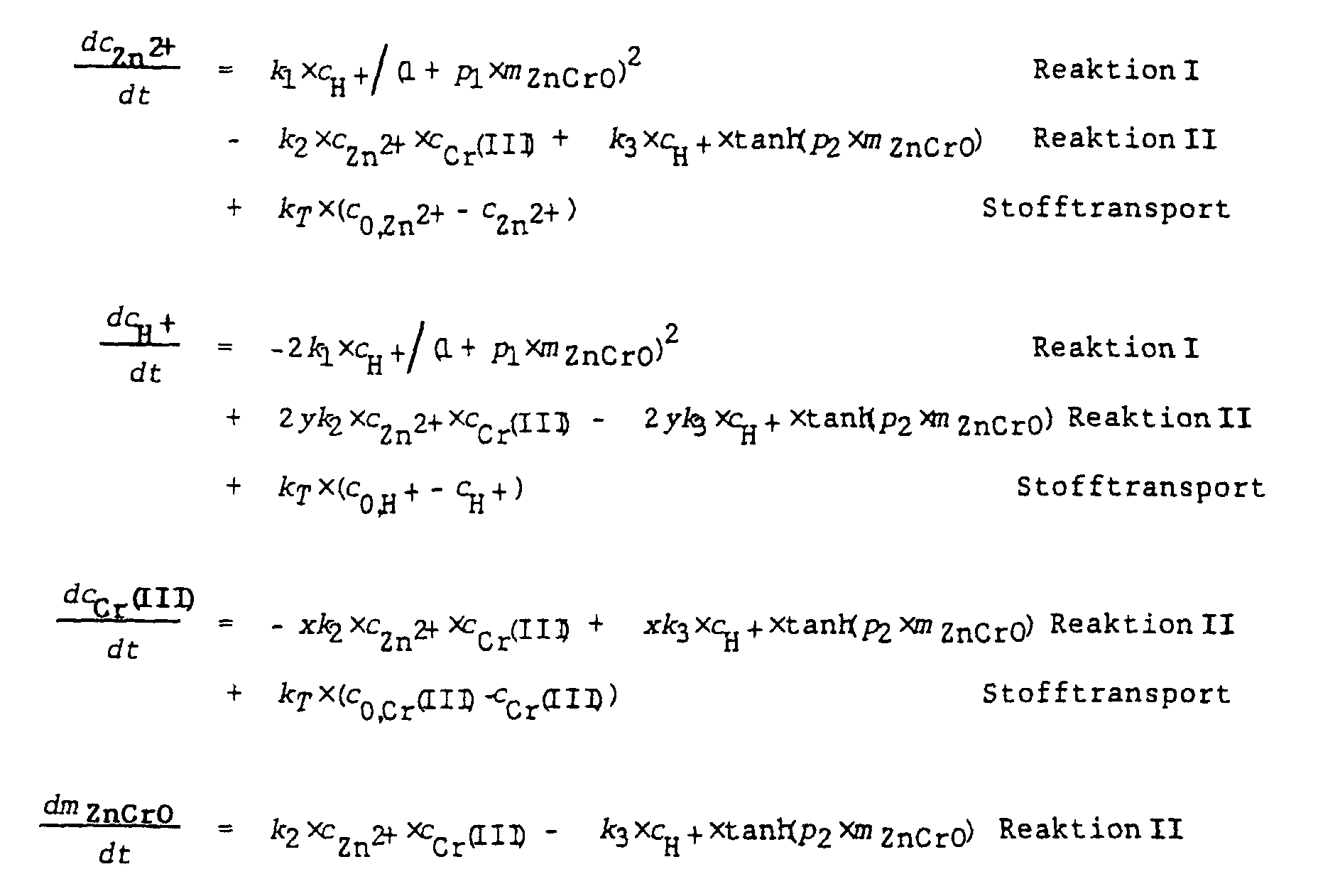
[0038] Der Term tanh
p2·
mZnCrO steht für die zwingende Voraussetzung der Rückreaktion 11, nämlich das Vorhandensein
von ZnCrO. Die tanh-Funktion sorgt für einen gleitenden übergang von 0 auf 1, der
sich mit P2 einstellen läßt. Das Differentialgleichungssystem wurde mittels Computer
numerisch gelöst. Als Ergebnis wurden der Schichtdickenverlauf und die Konzentrationsverläufe
über die Zeit erhalten. Als Anfangswerte zur Zeit t
0 = 0 dienten:
c0,Zn2+ = |
0 |
|
c0,H+ = |
10-2 mol/l |
(pH 2) |
c0,Cr(III) = |
0,5 mol/l |
|
m0,ZnCrO = |
0 |
|
[0039] In Bild 1 sind die Schichtdickenverläufe für verschiedene Werte der Geschwindigkeitskonstanten
kj dargestellt. Für einen guten Korrosionsschutz sollte die Passivschicht so dick und
gleichzeitig so kompakt wie möglich sein.
[0040] Fig. 38 (ursprüngliches Bild 1) zeigt eine Computersimulation des kinetischen Modells
zur Chromatierung von Zink für verschiedene Geschwindigkeitskonstanten.
[0041] Je schneller die anfängliche Zinkauflösung (Geschwindigkeitskonstante k
1) und je schneller das gelöste Zink mit dem Chrom(III) ausfällt {Geschwindigkeitskonstante
k
2), umso dicker wird die Chromatschicht. Das Schichtwachstum wird stark begünstigt,
wenn bereits gelöstes Zink im Bad vorliegt, das ergaben Simulationen mit
c0,Zn2+ > 0. Ein niedriger pH-Wert begünstigt die Zinkauflösung, sorgt aber auch für eine
verstärkte Rücklösung der Schicht.
[0042] Aus dem Modell lassen sich im Grunde zwei Forderungen für die Herstellung einer möglichst
dicken Chromatschicht aufstellen. Die Reaktion I und die Hinreaktion II müssen so
schnell wie möglich ablaufen, die Rückreaktion II muß langsam bleiben. Hierfür ergeben
sich folgende Ansatzpunkte:
Reaktion I
[0043]
- a
- pH-Optimierung
- b
- Vermeidung von Inhibitoreinschleppung aus dem Zinkbad
- c
- Zugabe von Oxidationsmitteln zur Beschleunigung der ZinkaufLösung
- d
- Beschleunigung der Zinkauflösung durch Bildung von galvanischen Elementen
Hinreaktion II
[0044]
- e
- Die Geschwindigkeitskonstante k2 sollte so groß wie möglich sein. Chrom(III)-Komplexe haben allgemein eine langsame
Kinetik. Durch Einsatz geeigneter Liganden sollte sich die Reaktionsgeschwindigkeit
beschleunigen lassen.
- f
- Bei Verwendung weitere Übergangsmetalikationen in der Chromatierungslösung ergeben
sich i. a. auch höhere Geschwindigkeitskonstanten als für Cr(III). Ferner können diese
Übergangsmetallkationen als Katalysatoren beim Ligandenaustausch am Chrom(III) wirken.
Rückreaktion II
[0045]
- g
- Einbau von schwer rücklösbaren Hydroxiden, z. b. Nickel-, Cobalt- und/oder Kupferhydroxid.
[0046] Es wurden Reihenversuche durchgefüht. Die Ansatzpunkte a und b sind dem Fachmann
bekannt. Die Beschleunigung der Zinkauflösung über die Punkte c und d führte zwar
auch zu dicken, allerdings gelblichen Überzügen mit einem Chrom/ZinkVerhältnis von
1:4 bis 1:3, die nur einen geringen Korrosionsschutz aufwiesen. Es zeigte sich, daß
gute Korrosionsschutzwerte erst bei Chrom/Zink-Verhältnissen oberhalb von 1:2 erreichbar
sind.
[0047] Ein höheres Chrom/Zink-Verhältnis bei gleichzitig dickeren Chromatschichten erhalt
man bei Erhöhung der Geschwindigkeitskonstante k
2 (Ansatzpunkt e) bzw. Beschleunigung der Hinreaktion II. Nachdem die Erfinder der
vorliegenden Anmeldung erkannt hatten, daß heiße Chrom(III)-Lösungen zu überraschenden
Passivschichten führen, gibt es im Zusammenhang mit den theoretischen Überlegungen
der Erfinder folgende Moglichkeiten:
- Erhöhung der Temperatur der Chromatierungslösung und/oder der Teiloberfläche
- Erhöhung der Chrom(lll)-Konzentration in der Prozeßlösung
[0048] Beschleunigung der Ligandenaustauschkinetik am Chrom(lll). Hierzu muß man wissen,
daS Chrom(III) in wäßrigen Lösungen im wesentlichen in Form von hexagonalen Komplexen
vorliegt, die im allgemeinen eine hohe kinetische Stabilität aufweisen und ferner,
daß der Ligandenaustausch der geschwindigkeitsbestimmende Schritt in Hinreaktion II
ist. Durch Auswahl geeigneter Komplexliganden, mit denen das Chrom(III) kinetisch
weniger stabile Komplexe bildet, wird demnach k
2 erhöht.
- Zusatz von Elementen in die Chromatierungslösung, die auf den Ligandenautausch katalytisch
wirken.
[0049] In Reihenversuchen erwiesen sich Chelatliganden (wie Di- und Tricarbonsäuren sowie
Hydroxydi- und Hdroxytricarbonsäuren) als solche, die kinetisch weniger stabile Komplexe
mit Chrom(III) bildeten. Wohingegen die Fluoridkomplexe kinetisch sehr stabil sind.
Bei Verwendung nur solcher Chelatliganden zur Komplexierung des Chrom(III) und Verzicht
auf Fluorid in der Passivierungslösung wurden ausgezeichnete Resultate auch bei einer
Behandlungstemperatur von nur 60 °C erzielt, wie die Beispiele 2 und 3 zeigen.
Beispiel 2
[0050] Elektrolytisch glanzverzinkte (15 µm) Stahlteile wurden in eine wäßrige Chromatierungslösung
enthaltend:
50 g/l CrCl3 · 6 H2O (dreiwertiges Chromsalz)
100 g/l NaNO3
31,2 g/l Malonsäure
getaucht, die zuvor mit Natronlauge auf einen pH-Wert von 2,0 eingestellt wurde.
Die Tauchzeit betrug 60 s. Nach Spülung und Trocknung ergab sich im Salzsprühschrank
nach DIN 50021 SS ein Korrosionsschutz von 250 h bis Erstangriff nach DIN 50961.
[0051] Malonsäure ist ein Ligand, der am Chrom (III) eine schnellere Ligandenaustauschkinetik
ermöglicht als das Fluorid aus Beispiel 1. Ein guter Korrosionsschutz, der die Mindestanforderung
von DIN 50961 für die Verfahrensgruppe C (Gelbchromatierung) bei weitem übertrifft,
läßt sich somit schon bei 60 °C erreichen.
Beispiel 3
[0052] Elektrolytisch glanzverzinkte (15 µm) Stahlteile wurden in eine wäßrige Chromatierungslösung
bestehend aus:
50 g/l CrCl3 · 6 H2O (dreiwertiges Chromsalz)
3 g/l Co(NO3)2
100 g/l NaNO3
31,2 g/l Malonsäure
getaucht, die zuvor mit Natronlauge auf einen pH-Wert von 2,0 eingestellt wurde.
Die Tauchzeit betrug 60 s. Nach Spülung und Trocknung ergab sich im Salzsprühschrank
nach DIN 50021 SS ein Korrosionsschutz von 350 h bis Erstangriff nach DIN 50961.
[0053] Cobalt ist ein Element, daß nach der Modellvorstellung den Ligandenaustausch katalysieren
und ferner durch Einbau von kinetisch stabilen Oxiden in die Chromatschicht die Rückreaktion
II reduzieren konnte, so daß die Chromatschicht insgesamt dicker werden sollte. Auch
in diesem Punkt wird die für die vorliegende Erfindung aufgestellte Modelivorstellung
durch die Praxis gestützt. Der Korrosionsschutz ließ sich allein durch Zusatz von
Cobalt in die Chromatierungslösung nochmals im Vergleich zu Beispiel 3 deutlich steigern.
[0054] Neue grünliche Chromatierungsschichten auf Zink wurden analog zu Beispiel 2 bei 40,
60, 80 und 100 °C hergestellt. Die Schichtdicken der jeweiligen Chromatschichten wurden
mittels Rutherford-Rückstreu-Experimenten (RBS = Rutherford-Backscattering) ermittelt.
In der Tabelle aufgeführt sind zusätzlich die korrespondierenden Korrosionsschutzwerte
in Stunden Salzsprühschrank nach DIN 50021 SS bis Erstangriff nach DIN 50961 Kapitel
10.
J/°C |
d/nm |
Korr.-Schutz/h |
40 |
100 |
50-60 |
60 |
260 |
220-270 |
80 |
400 |
350 450 |
100 |
800 |
800-1200 |
[0055] Je nach dem verwendeten Komplexliganden, in Beispiel 2 und 3 Malonat, lassen sich
zum Teil noch erheblich höhere Schichtdicken und Korrosionsschutzwerte erzielen. Mit
Komplexliganden, bei denen die komplexierende funktionelle Gruppe Stickstoff, Phosphor
oder Schwefel enthält (-NR
2, -PR
2 wobei R unabhängig voneinander ein organischer, insbesondere aliphatischer Rest und/oder
H ist, und/oder -SR, wobei R ein organischer, insbesondere aliphatischer Rest oder
H, ist), ist es möglich, die aufgezeigten Schichteigenschaften in Grenzen auch bei
Raumtemperatur zu erzeugen.
Beispiel 4
[0056] Elektrolytisch mit einer Zink/Eisenlegierung (0,4-0,6% Eisen) beschichtete Stahlteile
wurden bei 60° C in folgende wäßrige Chromatierungslösung getaucht:
50g/l CrCl3. 6 H2O
100g/l NaNO3
31,2 g/l Malonsäure
[0057] Die Lösung wurde zuvor mit NaOH auf einen pH-Wert von 2,0 eingestellt. Die Tauchzeit
betrug 60s. Nach Spülung und Trocknung zeigte sich auf dem Zink/Eisen eine transparente,
grünliche, leicht graue, stark irisierende Schicht. Im Salzsprühschrank nach den oben
genannten DIN- und ASTM-Normen ergab sich ein Korrosionsschutz von 360 h bis Erstangriff
nach DIN 50961.
Beispiel 5
[0058] Elektrolytisch mit einer Zink/Nickellegierung (8-13% Nickel) beschichtete Stahlteile
wurden bei 60° C in folgende wäßrige Chromatierungslösung getaucht:
50g/l CrCl3. 6 H2O
100g/l NaNO3
31,2 g/l Malonsäure
[0059] Die Lösung wurde zuvor mit NaOH auf einen pH-Wert von 2,0 eingestellt. Die Tauchzeit
betrug 60s. Nach Spülung und Trocknung zeigte sich auf dem Zink/Nickel eine transparente,
grünliche, dunkelgraue, stark irisierende Schicht. Im Salzsprühschrank nach den oben
genannten DIN- und ASTM-Normen ergab sich ein Korrosionsschutz von 504 h bis Erstangriff
nach DIN 50961.
[0060] Weitere vorteilhafte Liganden ergeben sich aus der Aufzählung gemäß Anspruch 9 und
11.
[0061] Die neue grünliche chrom(VI)freie Chromatschicht ist demnach je nach Herstellungstemperatur
zwischen 100 und 1000 nm dick, schwach grün in der Eigenfarbe und rotgrün irisierend.
Die Chromatierungslösung besteht aus dreiwertigen Chromaten, ferner aus Leitsalzen
und Mineralsäuren. Die Anwendung der Chromatierungslösungen erfolgt in der Regel bei
Temperaturen oberhalb 40 °C. Der Korrosionsschutz von unverletzten grünlichen chrom(VI)freien
Chromatierungen beläuft sich je nach Herstellungstemperatur auf 100-1200 h im Salzsprühschrank
nach DIN 50021 SS bis zum ersten Auftreten von Korrosionsprodukten. Damit erfüllt
die neue Chromatierung die Mindestforderungen an den Korrosionsschutz für die Verfahrensgruppen
C und D nach DIN 50961 (Kapitel 10, Tabelle 3) und zwar ohne Chrom(VI) weder bei der
Herstellung noch im Produkt.
[0062] Die vorliegende Erfindung ermöglicht es erstmals, Chrom(VI)-freie Konversionsschichten
beziehungsweise Passivschichten, basierend auf Chrom(III) zur Verfügung zu stellen,
welche jedoch den Korrosionsschutz der im Stand der Technik üblichen Gelbchromatierungen
- also Chrom(VI)-haltige Passivschichten erbringen.
[0063] Dies ist ein einzigartiges Novum in der gesamten Galvanisierungsbranche.
[0064] Bisher waren auf Chrom(III)-Basis lediglich klare bis blaue Schichten bekannt, in
Fachkreisen Blaupassivierung genannt, welche in der Praxis vielfältige Anwendungen
finden.
[0065] Ferner sind gelblich-transparente Schichten mit Cer-Zusatz bekannt, die in der Praxis
jedoch nicht eingesetzt werden aufgrund des sehr teuren Cer-Zusatzes und ihren schlechten
Korrosionsschutzeigenschaften.
[0066] Darüberhinaus sind pulvrig-grünliche Schichten bekannt für die der Anmelderin - selbst
eine der führenden Firmen im Bereich der Oberflächentechnik - keine praktischen Anwendungen
bekannt sind.
[0067] Bereits der farbliche Unterschied der Konversionsschichten der vorliegenden Erfindung
wird aufgrund der Figur 1 deutlich, wobei drei Behandlungsverfahren auf verzinkten
Schrauben durchgeführt wurden.
[0068] Das in der Abbildung gemäß Figur 1 linke Schraubenhäufchen wurde einer klassischen
Blauchromatierung - wie auf Seite 2 der Beschreibung unter Ziffer 1 dargelegt - unterzogen.
[0069] Das auf dem Foto gemäß Figur 1 rechte Schraubenhäufchen wurde einer konventionellen
Gelbchromatierung gemäß Seite 2, Nummer 2 der vorliegenden Beschreibung unterzogen.
[0070] Das mittlere Schraubenhäufchen zeigt das Ergebnis, wenn die Schrauben mittels des
erfindungsgemäßen Verfahrens passiviert werden.
[0071] Es handelt sich somit um eine grünlich-irisierende transparente Konversions- beziehungsweise
Passivschicht.
[0072] Es handelt sich ferner bei den in Figur 1 wiedergegeben Farben um die realen Farben,
was daraus folgt, daß zum Zwecke der neutralen Farbwiedergabe einerseits eine Farbkarte
und andererseits ein Graukeil mitfotografiert wurde.
[0073] Wie sich aus dem weißen Testfeld "White" sowie dem entsprechenden Feld mit der Dichte
".00" aus dem Graukeil ergibt, sind beide Testfelder rein weiß, wodurch die neutrale
Ausfilterung und die damit realistische Farbwiedergabe evident ist.
[0074] In Figur 2 sind rasterelektronenmikroskopische (REM) Aufnahmen der Konversionsschichten
einer Gelbchromatierung und einer Blauchromatierung gemäß dem Stand der Technik im
Vergleich zur "Chromitierung" gemäß der vorliegenden Erfindung gezeigt.
[0075] Die Schichtproben stammten von dem in Figur 2, untere Bildhälfte gezeigten entsprechend
passivierten verzinkten Eisenschrauben.
[0076] Die erfindungsgemäß (durch (Chromitierung") behandelten Proben wiesen eine Chrom(VI)-freie
Konversionsschicht mit einer Dicke von ca. 300 nm auf. Bei den Aufnahmen der Figur
2 ist zu berücksichtigen, daß die Schichten unter einem Betrachtungswinkel von 40°
fotographiert wurden, wobei sich eine Verkürzung um cos (40°) = 0,77 ergibt.
[0077] Aufgrund der REM-Aufnahmen der erfindungsgemäßen Chromitierungsschicht ergibt sich
somit, daß Konversionsschichtdicken wie bei der Gelbchromatierung erreicht werden,
jedoch mit dem Unterschied, daß die erfindungsgemäße Konversionsschicht kein toxisches
Chrom(VI) enthält.
[0078] Das Farbfoto der Figur 3 zeigt darüberhinaus die Bandbreite der Irisfarbe der erfindungsgemäßen
Passivschicht in der Praxis.
[0079] Bereits aus den Fotos der Figuren 1 und 3 kann man erkennen, daß die erfindungsgemäße
Passivschicht keine Chrom(VI)-lonen enthält, da ihr die typisch gelbe Farbe (vgl.
rechtes Schraubenhäufchen des Farbfotos der Anlage 1), fehlt.
[0080] Gegenstände gemäß dem Foto der Figure 1 und 3 sowie verzinkte Stahlbleche, die mit
dem erfindungsgemäßen Verfahren passiviert wurden, wurden nach DIN50021SS beziehungsweise
ASTM B 117-73 bis zu Auftreten von ersten Korrosionsprodukten nach DIN50961 Kapitel
10 im Salzsprühschrank getestet. Hierbei stellte sich überraschend heraus, daß die
Passivschichten der vorliegenden Erfindung und somit die mit dem vorliegenden Verfahren
passivierten Gegenstände dem Korrosionsschutz von Chrom(VI)-Passivierungen, also Gelbchromatierungen,
erfüllten, obwohl sie kein Chrom(VI) enthalten.
[0081] Hierbei ist es erwähnenswert, daß die typische Gelbchromatierung des Standes der
Technik 100 Stunden Salzwasserexposition gemäß der oben angeführten DIN- beziehungsweise
ASTN-Norm standhält, während mit den Passivschichten der vorliegenden Erfindung sogar
der zehnfache Korrosionsschutz erreicht wurde.
[0082] Die Schichten der vorliegenden Erfindung sowie die Verfahren zur Herstellung dieser
Schicht beziehungsweise des Verfahrens zur Passivierung von Metalloberflächen erfüllt
somit den lange in der Technik bestehenden Bedarf an Konversionsschichten, welche
ohne toxische und cancerogene Chrom(VI)-Verbindungen auskommen, und dennoch den Korrosionsschutz
der Gelbchromatierungen aufweisen und in der Regel sogar übertreffen.
[0083] EP 00 34 040 A1 beschreibt zwar eine Vielzahl von Schichten, von deren größerer Gruppe
(unter den von Barnes/Ward dargelegten Standardbedingungen erzeugt) die Farbe nicht
genannt, jedoch als klar bezeichnet wird. Zwei Beispiele, nämlich Nr. 16 und 17, beschreiben
eine grünliche Borat-haltige Schicht, die als wolkig-stumpf bis undurchsichtig bezeichnet
wird.
[0084] Beispiel 14 beschreibt eine Schicht mit einem Korrosionsschutz von nur
4 Stunden.
[0085] In Beispiel 15 der EP 00 34 040 wird eine Aluminium-haltige Schicht beschrieben,
die einen Korrosionsschutz von 100 Stunden erreicht. Dies wird, vergleicht man mit
den anderen Beispielen, allein durch den Korrosionsschutzzusatz Aluminium, der der
vorliegenden Erfindung fehlt, erreicht. Aluminiumfreie Schichten aus gleichen oder
ähnlichen Bädern weisen jedoch nur geringen Korrosionsschutz auf. Die erfindungsgemäße
Schicht bietet auch ohne diesen Zusatz einen signifikant höheren, nämlich bis zu 1000
h Korrosionsschutz.
[0086] Beispiele
16 und
17 beschreiben Schichten mit einem Korrosionsschutz von 300 bzw. 200 Stunden im Salzsprühtest,
also in dem von der Anmelderin beanspruchten Bereich. Aus der Beschreibung Seite 19,
Zeile 7 geht hervor, daß für einen guten Korrosionsschutz Schichten von größer 1000
nm erforderlich seien. Daher ist es auch verständlich, daß diese Schichten, die im
übrigen stets aus Borsäure-haltigen Lösungen erzeugt worden sind, als wolkig und eher
undurchsichtig beschrieben werden (Seite 14, Zeile 10). Der gesteigerte Korrosionsschutz
ist nach Seite 15, Zeilen 1-5 auf den Einbau Borat-haltiger Spezies zurückzuführen.
[0087] Dagegen bietet die erfindungsgemäße Schicht auch ohne diesen Zusatz einen hohen (und
auch noch höheren) Korrosionsschutz.
[0088] Es gibt jedoch noch einen weiteren patentrechtlichen sowie für die praktische Anwendung
bedeutenden Unterschied: die in Bsp. 16 und 17 der EP 00 34 040 beschriebenen Schichten
sind nämlich, weich und abwischbar und erfordern demnach eine Art Härtungsprozeß als
Nachbehandlung (Seite 17, Zeilen 12-21).
[0089] Die vorliegenden erfindungsgemäßen Schichten sind auch
ohne Härtungsprozeß hart und wischfest. Abwischbare, nicht auf dem Substrat haftende,
Korrosionsschutzschichten sind in der Praxis unbrauchbar.
[0090] In Figur 4 ist als Vergleichsbeispiel ein Foto gezeigt.Dieses Foto stellt das Ergebnis
von Vergleichsversuchen dar, die die Anmelderin im Vergleich zur EP 00 34 040 durchgeführt
hat. Insbesondere hat die Anmelderin die in diesem Stand der Technik angegebenen Beispiele
16 und 17 nachgearbeitet. Hierbei wurden verzinkte Stahlbleche in die in den Beispielen
16 und 17 der EP 00 34 040 beschriebenen Lösungen eingetaucht und die entsprechenden
Behandlungszeiten eingehalten. Figur 4 zeigt die gemäß dem Stand der Technik erhaltenen
Schichten auf den Substratoberflächen, und zwar von oben nach unten jeweils das erste
und das zweite Blech, das nacheinander durch Eintauchen behandelt worden ist.
[0091] Das Foto der Figur 4 zeigt von links nach rechts in der oberen Bildhälfte ein Läppchen
mit dem die Schicht, erzeugt gemäß Beispiel 16 - Stand der Technik - abgewischt wurde,
ein gemäß Beispiel 16 behandeltes verzinktes Stahlblech, daneben ein gemäß Beispiel
17 - Stand der Technik - behandeltes verzinktes Stahlblech und ganz rechts ebenfalls
ein Läppchen mit dem die Schicht aus Beispiel 17 abgewischt wurde. In der zweiten
Zeile ist links - neben dem Hinweis auf Beispiel 16 und rechts daneben (neben dem
Hinweis auf Beispiel 17) jeweils ein - gemäß Stand der Technik - beschichtetes verzinktes
Stahlblech gezeigt.
[0092] Sichtbar ist eine milchige, weiß-grünliche pulverige Beschichtung, die bereits ohne
besonderen Druck mit einem weichen Lappen abwischbar (siehe Figur 4, obere Bildhälfte)
ist. Das Beschichtungsverfahren des Standes der Technik selbst legt nahe, daß es sich
bei dieser Schicht nicht um eine dem Substratblech fest anhaftende kompakte oxidische
Zink/Chrom-Konversionsschicht, sondern um einen im wesentlichen aus Chrom-Hydroxid
bestehenden, locker aufliegenden Überzug handelt. Der pH-Wert muß für diese Beschichtung
so hoch sein, daß die Ausfällungsgrenze für Chrom-Hydroxide bereits überschritten
ist (Seite 26, Zeile 12 der EP 0034 040). Die Ausfällung von Chromhydroxid ist kinetisch
gehemmt und wird durch das Eintauchen einer mehr oder weniger rauhen Oberfläche gefördert.
Daß der Schichtbildungsmechanismus ein anderer sein muß als bei den anderen Beispielen,
kann man auch daran erkennen, daß
mit (Bsp. 16 Stand der Technik) oder
ohne (Bsp. 17) Komplexbildner mehr oder weniger das gleiche Ergebnis erzielt wurde. Beim
praktischen Nachvollziehen der Beispiele 16 und 17 des Standes der Technik wurde auch
festgestellt, daß die Schicht umso dicker, weicher und pulveriger wurde, je mehr Bleche
in der Lösung beschichtet wurden. Es fiel auch im Bad immer mehr Chromhydroxid aus,
was die Lebensdauer einer solchen Beschichtungslösung auf wenige Stunden begrent.
Die erfindungsgemäße Schicht hingegen wird nur aus geeigneten "schnellen" Komplexen
erzeugt und dies in einem deutlich sauren pH-Bereich. Die Lösung ist über Monate,
vermutlich sogar Jahre hinweg stabil.
[0093] Die den Figuren 5 bis 36 zugrundeliegenden Messungen wurden mit einem Glimmentladungsspektrometer
durchgeführt.
[0094] Das Element F und die Anionen konnten mit dieser Methode nicht analysiert werden.
O,H,Cl und K konnten nicht quantifiziert werden.
[0095] In folgender Tabelle ist ersichtlich, für welche Konzentrationsbereiche die Kalibration
Gültigkeit aufweist:
Element |
Konzentration min. in |
Konzentration max. in |
C |
0.0067 |
3.48 |
S |
0.0055 |
0.168 |
Cr |
0.0001 |
99.99 |
Ni |
0.0001 |
99.99 |
Co |
0.0001 |
7.00 |
Zn |
0.0001 |
99.99 |
Na |
0.0001 |
0.0068 |
N |
0.0001 |
6.90 |
B |
0.0001 |
0.040 |
Fe |
0.0005 |
99.91 |
[0096] Die Probenzuordnung bei den Figuren 5 bis 36 ergibt sich aufgrund folgender Tabelle:
Probe Nr |
Beschichtung |
Bedingungen |
Meßpunkt |
1 |
Chromitierung auf Zn (gem. Erfind.) |
60°C, 1 min, pH 2 |
A |
|
|
|
B |
2 |
|
60°C, 2min, pH 2 |
A |
|
|
|
B |
3 |
|
60°C, 1min, pH 2,5 |
A |
4 |
|
60°C, 1,5min, pH 2,5 |
A |
5 |
|
60°C, 2min, pH 2,5 |
A |
6 |
|
100°C, 1min, pH 2 |
A |
|
|
|
B |
|
|
|
C |
|
|
|
D |
7 |
Chromitierung auf Zn/Fe |
60°C, 1min, pH 2 |
A |
|
|
|
B |
8 |
Blauchromatierung auf Zn |
20°C, 30s, pH 1,8 |
A |
9 |
Gelbchromatierun g auf Zn |
20°C, 45s, pH 1,8 |
A |
|
|
|
B |
[0097] Fig. 37 zeigt eine Tabelle mit der Auswertung der Tiefenprofilmessungen, aus der
hervorgeht, daß sämtliche erfindungsgemäßen (Chromitierungs) Schichten eine Dicke
von über 100 nm haben.
1. Chrom(VI)-freie , Chrom (III)-haltige und im wesentlichen zusammenhängende Konversionsschicht
auf Zink oder Zinklegierungen,
dadurch gekennzeichnet, daß
sie bereits ohne Silikat, Cer, Aluminium und Borat im Salzsprühtest nach DIN 50021
SS bzw. ASTM B 117-73 bis Erstangriff nach DIN 50961 Kapitel 10 einen Korrosionsschutz
von 100 bis 1000 h aufweist;
sie klar, transparent, farblos und grünlich-bunt irisierend ist;
sie eine Schichtdicke von 100 nm bis 1000 nm aufweist; und
sie hart, haftfest und wischfest ist; und
sie über die Konversionsschichtdicke bis zu einem Chromgehalt von 1%, bezogen auf
Zink und Chrom in der Konversionsschicht, einen durchschnittlichen Chromgehalt über
5% aufweist;
eine chromreiche Zone > 20% Chrom, bezogen auf Zink und Chrom in der Konversionsschicht,
von mehr als 15 nm aufweist; und
einen Chrom-Index > 10 aufweist, wobei der Chromindex definiert ist als der durchschnittliche
Chromgehalt in %/100 in der Schicht > 1% Cr, multipliziert mit der Schichtdicke in
nm.
2. Konversionsschicht nach Anspruch 1,
dadurch gekennzeichnet, daß sie zur weiteren Steigerung des Korrosionsschutzes noch zusätzliche Komponenten enthält
welche ausgewählt werden aus der Gruppe bestehend aus: Silikat, Cer, Aluminium und
Borat;
zusätzlichen Metallverbindungen, insbesondere 1- bis 6-wertigen Metallverbindungen,
beispielsweise Verbindungen aus Na, Ag, Al, Co, Ni, Fe, Ga, In, Lanthaniden, Zr, Sc,
Ti, V, Mn, Cu, Zn, Y, Nb, Mo, Hf, Ta, W; und
Anionen, insbesondere Halogenidionen, insbesondere Chloridionen; schwefelhaltige lonen,
insbesondere Sulfationen, Nitrationen; phosphorhaltige Ionen, insbesondere Phosphationen,
Diphosphationen, lineare und/oder cyclische Oligophosphationen, lineare und/oder cyclische
Polyphosphationen, Hydrogenphosphationen; Carbonsäureanionen; und siliziumhaltige
Anionen, insbesondere Silikatanionen; und
Polymeren, insbesondere organischen Polymeren, Korrosionsinhibitoren; Kieselsäuren,
insbesondere kolloidalen oder dispergierten Kieselsäuren; Tensiden; Diolen, Triolen,
Polyolen; organischen Säuren, insbesondere Monocarbonsäuren; Aminen; Kunststoffdispersionen;
Farbstoffen, Pigmente, insbesondere Ruß, Pigmentbildner, insbesondere metallische
Pigmentbildner; Aminosäuren, insbesondere Glycin; Siccativen, insbesondere Cobaltsiccativen;
Dispergierhilfsstoffen; sowie
Mischungen aus diesen.
3. Konversionsschicht nach einem der Ansprüche 1 oder 2, dadurch gekennzeichnet, daß sie Farbstoffe oder Farbpigmente enthält.
4. Verfahren zum Herstellen von chrom(VI)-freien Konversionsschichten wenigstens mit
dem Korrosionsschutz von herkömmlichen chrom(VI)-haltigen Gelbchromatierungen, wobei
man eine Metalloberfläche mit einer Lösung aus wenigstens einem Chrom(III)-Komplex
sowie wenigstens einem Salz behandelt;
dadurch gekennzeichnet, daß
Chrom(III) in einer Konzentration von 5 bis 100 g/l vorliegt; und
man einen Chrom(III)-Komplex mit einer Chelatligandenaustauschkinetik einsetzt, die
schneller als die Fluoridaustauschkinetik in Chrom(III)-Fluorokomplexen ist.
5. Verfahren nach Anspruch 4, dadurch gekennzeichnet, daß die Metalloberfläche eine solche von Zink oder Zinklegierungen, insbesondere mit
Eisen, ist.
6. Verfahren nach Anspruch 4 oder 5, dadurch gekennzeichnet, daß man bei einer Temperatur von 20 bis 100°C, vorzugsweise 20 bis 80° C, bevorzugt 30
bis 60° C, besonders bevorzugt 40 bis 60° C, behandelt.
7. Verfahren nach einem der Ansprüche 4 bis 6,
dadurch gekennzeichnet, daß die Chelatliganden des Chrom(III)-Komplexes ausgewählt werden aus der Gruppe bestehend
aus:
Dicarbonsäuren, Tricarbonsäuren, Hydroxycarbonsäuren, insbesondere Oxal-, Maton-,
Bernstein-, Glutar-, Adipin-, Pimelin-, Kork-, Azelain-, Sebazinsäure; und
ferner, Maleinsäure, Phthalsäure, Terephthalsäure, Weinsäure, Citronensäure, Äpfelsäure,
Ascorbinsäure; und
Acetylaceton, Harnstoff, Hamstoffderivate; sowie
deren geeignete Mischungen, sowohl untereinander als auch in gemischten Komplexen
mit anorganischen Anionen und H2O und/oder
das Verfahren mehrfach auf der zu passivierenden Oberfläche durchgeführt wird.
8. Verfahren nach einem der Ansprüche 4 oder 7, dadurch gekennzeichnet, daß es ein bei 20 bis 100°C arbeitendes Chromatierungsverfahren mit Spülwasserrückführung
über wenigstens 2 kaskadierte Spülstufen ist.
9. Verfahren nach Anspruch 8, dadurch gekennzeichnet, daß in einer der Spülstufen eine Blauchromatierung erfolgt.
10. Verwendung von Chrom(III)-haltigen Lösungen, wobei das Chrom(III) in Form wenigstens
eines Komplexes mit einer Chelatligandenaustauschkinetik vorliegt, die schneller als
die Fluoridaustauschkinetik in Chrom(III)-Fluorokomplexen ist; und
Chrom(III) in einer Konzentration von 5 bis 100 g/l vorliegt,
als Passivierungsbad für Oberflächen aus Zink oder Zinklegierungen, wobei es als passivierende
Komponente im wesentlichen Chrom(III) enthält.
11. Verwendung nach Anspruch 10, dadurch gekennzeichnet, daß die Zinklegierungen solche mit Eisen sind.
12. Verwendung nach Anspruch 10 oder 11,
dadurch gekennzeichnet, daß der Chrom(III)-Komplex ausgewählt wird aus Komplexen mit Chrom (III) und wenigstens
einem Chelatliganden aus der Gruppe bestehend aus:
Dicarbonsäuren, Tricarbonsäuren, Hydroxycarbonsäuren, insbesondere Oxal-, Malon-,
Bernstein-, Glutar-, Adipin-, Pimelin-, Kork-, Azelain-, Sebazinsäure; und
ferner, Maleinsäure, Phthalsäure, Terephthalsäure, Weinsäure, Citronensäure, Äpfelsäure,
Ascorbinsäure; und
weiteren Chelatliganden wie Acetylaceton, Harnstoff, Hamstoffderivate; sowie
deren geeignete Mischungen, sowohl untereinander als auch in gemischten Komplexen
mit anorganischen Anionen und H2O.
13. Verwendung nach einem der Ansprüche 10 bis 12,
dadurch gekennzeichnet, daß die Lösungen weitere Zusätze enthalten, die ausgewählt sind aus der Gruppe bestehend
aus: Versiegelungen, Dewatering-Fluids; und
zusätzlichen Metallverbindungen, insbesondere 1- bis 6-wertigen Metallverbindungen,
beispielsweise Verbindungen aus Na, Ag, Al, Co, Ni, Fe, Ga, In, Lanthaniden, Zr, Sc,
Ti, V, Mn, Cu, Zn, Y, Nb, Mo, Hf, Ta, W; und
Anionen, insbesondere Halogenidionen, insbesondere Chloridionen; schwefelhaltige lonen,
insbesondere Sulfationen, Nitrationen; phosphorhaltige lonen, insbesondere Phosphationen,
Diphosphationen, lineare und/oder cyclische Oligophosphationen, lineare und/oder cyclische
Polyphosphationen, Hydrogenphosphationen; Carbonsäureanionen; und siliziumhaltige
Anionen, insbesondere Silikatanionen; und
Polymeren, insbesondere organische Polymeren, Korrosionsinhibitoren; Kieselsäuren,
insbesondere kolloidalen oder dispergierten Kieselsäuren; Tensiden; Diolen, Triolen,
Polyolen; organischen Säuren, insbesondere Monocarbonsäuren; Aminen; Kunststoffdispersionen;
Farbstoffen, Pigmente, insbesondere Ruß, Pigmentbildner, insbesondere metallische
Pigmentbildner; Aminosäuren, insbesondere Glycin; Siccativen, insbesondere Cobaltsiccativen;
Dispergierhilfsstoffen; sowie
Mischungen aus diesen.
14. Verwendung nach einem der Ansprüche 10 bis 13, dadurch gekennzeichnet, daß Chrom(III) in einer Konzentration von 5 g/l bis 80 g/l, insbesondere von 5 g/l bis
60 g/l, besonders bevorzugt von 10 g/l bis 30 g/l, vorzugsweise 20 g/l, vorliegt.
15. Verwendung nach einem der Ansprüche 10 bis 14, dadurch gekennzeichnet, daß die Lösungen einen pH-Wert zwischen 1,5 und 3 aufweisen.
16. Verwendung nach einem der Ansprüche 10 bis 15, dadurch gekennzeichnet, daß die Lösungen 20 g/l Chrom(III) enthalten und einen pH-Wert von 2 bis 2,5 aufweisen.
17. Verwendung nach einem der Ansprüche 10 bis 16, dadurch gekennzeichnet, daß die Lösungen eine Badtemperatur von 20 bis 100°C, vorzugsweise 20 bis 80° C, bevorzugt
30 bis 60° C, besonders bevorzugt 40 bis 60° C aufweisen.
18. Verwendung nach einem der Ansprüche 10 bis 17, dadurch gekennzeichnet, daß die zu behandelnden Gegenstände zwischen 15 und 200 Sekunden, insbesondere zwischen
15 und 100 Sekunden, vorzugsweise 30 Sekunden in die Chrom(III)-haltigen Lösungen
eingetaucht werden.
1. A chromium(VI)-free, chromium(III)-containing and substantially coherent conversion
layer on zinc or zinc alloys,
characterised in that
even in the absence of silicate, cerium, aluminum and borate it presents a corrosion
protection of approx. 100 to 1000 h in the salt spray test according to DIN 50021
SS or ASTM B 117-73 until first attack according to DIN 50961 Chapter 10;
it is clear, transparent, colorless and presents a greenish, multicolored iridescence;
it has a layer thickness of 100 nm to 1000 nm; and
it is hard, adheres well and is resistant to wiping; and
it has across the conversion layer thickness a chromium content of up to approx. 1
%, in relation to zinc and chromium in the conversion layer an average chromium content
of more than approx. 5%;
it has a chromium-rich zone > 20% chromium, in relation to zinc and chromium in the
conversion layer, of more than approx. 15 nm; and
it has a chromium index > 10, wherein the chromium index is defined as the average
chromium content in %/100 in the layer > 1% Cr, multiplied by the layer thickness
in nm.
2. A conversion layer according to claim 1,
characterised in that it contains, for further enhanced corrosion protection, additional components selected
from the group consisting of: silicate, cerium, aluminum and borate;
additional metal compounds, in particular 1- to 6-valent metal compounds, for example
compounds of Na, Ag, Al, Co, Ni, Fe, Ga, In, lanthanides, Zr, Sc, Ti, V, Mn, Cu, Zn,
Y, Nb, Mo, Hf, Ta, W; and
anions, in particular halide ions, in particular chloride ions; sulfurous ions, in
particular sulfate ions, nitrate ions; phosphoric ions, in particular phosphate ions,
diphosphate ions, linear and/or cyclic oligophosphate ions, linear and/or cyclic polyphosphate
ions, hydrogen phosphate ions; carboxylic acid anions; and silicon-containing anions,
in particular silicate anions; and
polymers, in particular organic polymers, corrosion inhibitors; silicic acids, in
particular colloidal or disperse silicic acids; surfactants; diols, triols, polyols;
organic acids, in particular monocarboxylic acids; amines; plastics dispersions; dyes,
pigments, in particular carbon black, chromogenic agents, in particular metallic chromogenic
agents; amino acids, in particular glycin; siccatives, in particular cobalt siccatives;
dispersing agents; and
mixtures thereof.
3. A conversion layer according to any one of claims 1 or 2, characterised in that it contains dyes or color pigments.
4. A method for producing chromium(VI)-free conversion layers affording at least the
corrosion protection of conventional chromium(VI)-containing yellow chromations, wherein
a metallic surface is treated with a solution of at least one chromium(III) complex
and at least one salt;
characterised in that
chromium(III) is present in a concentration of 5 to 100 g/l; and
a chromium(III) complex is used having chelate ligand replacement kinetics more rapid
than the fluoride replacement kinetics in chromium(III)-fluorocomplexes.
5. A method according to claim 4, characterised in that said metallic surface is one of zinc or zinc alloys, in particular with iron.
6. A method according to claim 4 or 5, characterised in that treatment is carried out at a temperature of 20 to 100°C, preferably 20 to 80°C,
in a preferred manner 30 to 60°C, in a particularly preferred manner 40 to 60°C.
7. A method according to any one of claims 4 to 6,
characterised in that the chelate ligands of the chromium(III) complex are selected from the group consisting
of:
dicarboxylic acids, tricarboxylic acids, hydroxycarboxylic acids, in particular oxalic,
malonic, succinic, glutaric, adipic, pimelic, suberic, azelaic, sebacic acid; and
furthermore, maleic acid, phthalic acid, terephthalic acid, tartaric acid, citric
acid, malic acid, ascorbic acid; and
acetylacetone, urea, urea derivatives; as well as
suitable mixtures thereof, among each other as well as in mixed complexes with inorganic
anions and H2O and/or
the method is performed repeatedly on the surface to be passivated.
8. A method according to any one of claims 4 or 7, characterised in that it is a it is a chromate coating method operating at 20 to 100°C with rinsing water
recycling over at least 2 cascaded rinsing stages.
9. A method according to claim 8, characterised in that a blue chromation is performed in one of the rinsing stages.
10. Use of chromium(III)-containing solutions, wherein the chromium(III) is present in
the form of at least one complex having chelate ligand replacement kinetics more rapid
than the fluoride replacement kinetics in chromium(III)-fluorocomplexes; and
chromium(III) is present in a concentration of 5 to 100 g/l,
as a passivation bath for surfaces of zinc or zinc alloys, wherein it substantially
contains chromium(III) as a passivating component.
11. Use according to claim 10, characterised in that the zinc alloys are zinc alloys with iron.
12. Use according to claim 10 or 11,
characterised in that the chromium(III) complex is selected from complexes with chromium(III) and at least
one chelate ligand from the group consisting of:
dicarboxylic acids, tricarboxylic acids, hydroxycarboxylic acids, in particular oxalic,
malonic, succinic, glutaric, adipic, pimelic, suberic, azelaic, sebacic acid; and
furthermore, maleic acid, phthalic acid, terephthalic acid, tartaric acid, citric
acid, malic acid, ascorbic acid; and
further chelate ligands such as acetylacetone, urea, urea derivatives; as well as
suitable mixtures thereof, among each other as well as in mixed complexes with inorganic
anions and H2O.
13. Use according to any one of claims 10 to 12,
characterised in that the solutions contain further additives selected from the group consisting of: sealers,
dewatering fluids; and
additional metal compounds, in particular 1- to 6-valent metal compounds, for example
compounds of Na, Ag, Al, Co, Ni, Fe, Ga, In, lanthanides, Zr; Sc, Ti, V, Mn, Cu, Zn,
Y, Nb, Mo, Hf, Ta, W; and
anions, in particular halide ions, in particular chloride ions; sulfurous ions, in
particular sulfate ions, nitrate ions; phosphoric ions, in particular phosphate ions,
diphosphate ions, linear and/or cyclic oligophosphate ions, linear and/or cyclic polyphosphate
ions, hydrogen phosphate ions; carboxylic acid anions; and silicon-containing anions,
in particular silicate anions; and
polymers, in particular organic polymers, corrosion inhibitors; silicic acids, in
particular colloidal or disperse silicic acids; surfactants; diols, triols, polyols;
organic acids, in particular monocarboxylic acids; amines; plastics dispersions; dyes,
pigments, in particular carbon black, chromogenic agents, in particular metallic chromogenic
agents; amino acids, in particular glycin; siccatives, in particular cobalt siccatives;
dispersing agents; as well as
mixtures thereof.
14. Use according to any one of claims 10 to 13, characterised in that chromium(III) is present in a concentration of 5 g/l to 80 g/l, in particular of
5g/l to 60 g/l, in a particularly preferred manner of 10 g/l to 30 g/l, preferably
20 g/l.
15. Use according to any one of claims 10 to 14, characterised in that the solutions have a pH between 1.5 and 3.
16. Use according to any one of claims 10 to 15, characterised in that the solutions contain 20 g/l chromium(III) and have a pH of 2 to 2.5.
17. Use according to any one of claims 10 to 16, characterised in that the solutions have a bath temperature of 20 to 100°C, preferably 20 to 80°C, in a
preferred manner 30 to 60°C, in a particularly preferred manner 40 to 60°C.
18. Use according to any one of claims 10 to 17, characterised in that the objects to be treated are immersed into the chromium(III)-containing solutions
for between 15 and 200 seconds, in particular between 15 and 100 seconds, preferably
30 seconds.
1. Couche de conversion exempte de chrome(VI), contenant du chrome (III) et substantiellement
cohérente sur zinc ou alliages de zinc,
caractérisée en ce que
celle-ci présente une protection à la corrosion de 100 à 1000 h, même en l'absence
de silicate, de cérium, d'aluminium et de borate, dans l'essai au brouillard salin
d'après les normes DIN 50021 SS ou ASTM B 117-73 jusqu'à la première attaque d'après
la norme DIN 50961 chapitre 10;
elle est claire, transparente, sans couleur et présente une irisation multicolore
verte;
elle possède une épaisseur de couche de 100 nm à 1000 nm; et
elle est dure, adhère bien et résiste au frottement; et
elle présente, à travers l'épaisseur de la couche de conversion, une teneur en chrome
allant jusqu'à environ 1%, par rapport au zinc et au chrome dans la couche de conversion
une teneur moyenne en chrome de plus de 5%;
elle présente une zone riche en chrome > 20% de chrome, par rapport au zinc et au
chrome dans la couche de conversion, de plus de 15 nm; et
elle présente un index de chrome > 10, où l'index de chrome est défini de telle sorte
que la teneur moyenne en chrome en %/100 dans la couche > 1% Cr, multiplié par l'épaisseur
en nm.
2. Couche de conversion selon la revendication 1,
caractérisée en ce qu'elle contient, pour augmenter encore plus la protection contre la corrosion, des composantes
supplémentaires sélectionnées du groupe composé de: silicate, cérium, aluminium et
borate;
des composés de métaux supplémentaires, en particulier ceux de valence 1 à 6 comme
par exemple les composés de Na, Ag, Al, Co, Ni, Fe, Ga, In, lanthanides, Zr, Sc, Ti,
V, Mn, Cu, Zn, Y, Nb, Mo, Hf, Ta, W; et
des anions, en particulier des ions d'halogénures, en particulier des ions de chlorures;
des ions sulfureux, en particulier des ions de sulfates, des ions de nitrates; des
ions phosphorés, en particulier des ions de phosphates, des ions de diphosphates,
des ions d'oligophosphates linéaires et/ou cycliques, des ions de polyphosphates linéaires
et/ou cycliques, des ions de phosphates d'hydrogène; des anions d'acides carboxyliques;
et des anions silicieux, en particulier des anions de silicates; et
des polymères, en particulier des polymères organiques, des inhibiteurs de corrosion;
des acides siliciques, en particulier des acides siliciques colloïdaux ou dispersés;
des tensioactifs; des diols, des triols, des polyols; des acides organiques, en particulier
des acides monocarboxyliques; des amines; des dispersions plastiques; des colorants,
des pigments, en particulier le noir de carbone, des agents chromogènes, en particulier
des agents chromogènes métalliques; des aminoacides, en particulier la glycine; des
siccatifs, en particulier des siccatifs au cobalt; des agents de dispersion; ainsi
que
des mélanges de ceux-ci.
3. Couche de conversion selon l'une des revendications 1 ou 2, caractérisée en ce qu'elle contient des colorants ou des pigments de couleur.
4. Procédé pour la production de couches de conversion exemptes de chrome(VI) procurant
au moins la protection anti-corrosion des chromatations jaunes conventionnelles contenant
du chrome(VI), où
une surface métallique est traitée avec une solution d'au moins un complexe de chrome(III)
et d'au moins un sel;
caractérisé en ce que
le chrome(III) est présent dans une concentration de 5 à 100 g/l; et
l'on utilise un complexe de chrome(III) ayant une cinétique de remplacement des ligands
de chélate plus rapide que la cinétique de remplacement de fluoride dans les complexes
fluorés de chrome(III).
5. Procédé selon la revendication 4, caractérisé en ce que la surface métallique est de zinc ou d'un alliage de zinc, en particulier avec du
fer.
6. Procédé selon la revendication 4 ou 5, caractérisé en ce que le traitement est effectué à une température entre 20 et 100°C, de préférence entre
20 et 80°C, de manière préférentielle entre 30 et 60°C, de manière particulièrement
préférée entre 40 et 60°C.
7. Procédé selon l'une des revendications 4 à 6,
caractérisé en ce que les ligands de chélate du complexe de chrome(III) sont choisis du groupe composé
:
d'acides dicarboxyliques, d'acides tricarboxyliques, d'acides hydroxycarboxyliques,
en particulier d'acide oxalique, malonique, succinique, glutarique, adipique, pimélique,
subérique, azélaique, sébacique; et
en outre d'acide maléique, d'acide phtalique, d'acide téréphtalique, d'acide tartrique,
d'acide citrique, d'acide malique, d'acide ascorbique; et
d'acétyl-acétone, d'urée, des dérivés d'urée ainsi que
de leurs mélanges appropriés, non seulement entre eux, mais aussi dans des complexes
mélangés avec des anions inorganiques et H2O et/ou
le procédé est appliqué plusieurs fois sur la surface à rendre passive.
8. Procédé selon l'une des revendications 4 ou 7, caractérisé en ce que celui-ci est un procédé de chromatation opérant à des températures de 20 à 100°C
qui retraite l'eau de rinçage en passant par au moins 2 phases de rinçage en cascade.
9. Procédé selon la revendication 8, caractérisé en ce qu'il se produit une chromatation bleue dans l'une des phases de rinçage.
10. Utilisation de solutions contenant du chrome(III), où le chrome(III) est présent sous
la forme d'au moins un complexe ayant une cinétique de remplacement des ligands de
chélate qui est plus rapide que la cinétique de remplacement de fluoride dans les
complexes fluorés de chrome(III); et
le chrome(III) est présent dans une concentration de 5 à 100 g/l,
en tant que bain de passivation pour des surfaces de zinc ou des alliages de zinc,
où il contient essentiellement du chrome(III) comme composante passivante.
11. Utilisation selon la revendication 10, caractérisée en ce que les alliages de zinc sont des alliages avec du fer.
12. Utilisation selon la revendication 10 ou 11,
caractérisée en ce que le complexe de chrome(III) est sélectionné à partir de complexes ayant du chrome(III)
et au moins un ligand de chélate du groupe composé:
d'acides dicarboxyliques, d'acides tricarboxyliques, d'acides hydroxycarboxyliques,
en particulier d'acide oxalique, malonique, succinique, glutarique, adipique, pimélique,
subérique, azélaique, sébacique; et
en outre d'acide maléique, d'acide phtalique, d'acide téréphtalique, d'acide tartrique,
d'acide citrique, d'acide malique, d'acide ascorbique; et
d'autres ligands de chélate tels que l'acétyl-acétone, l'urée, les dérivés d'urée;
ainsi que
de leurs mélanges appropriés, non seulement entre eux mais aussi dans des complexes
mélangés avec des anions inorganiques et H2O.
13. Utilisation selon l'une des revendications 10 à 12,
caractérisée en ce que les solutions contiennent d'autres additifs sélectionnés du groupe composé: de revêtements
scellants, de liquides déshydratants; et
des composés de métaux supplémentaires, en particulier ceux de valence 1 à 6 comme
par exemple des composés de Na, Ag, Al, Co, Ni, Fe, Ga, In, lanthanides, Zr, Sc, Ti,
V, Mn, Cu, Zn, Y, Nb, Mo, Hf, Ta, W; et
des anions, en particulier des ions d'halogénures, en particulier des ions de chlorures;
des ions sulfureux, en particulier des ions de sulfates, des ions de nitrates; des
ions phosphorés, en particulier des ions de phosphates, de diphosphates, des ions
d'oligophosphates linéaires et/ou cycliques, des ions de polyphosphates linéaires
et/ou cycliques, des ions de phosphates d'hydrogène; des anions d'acides carboxyliques;
et des anions silicieux, en particulier des anions de silicates; et
des polymères, en particulier des polymères organiques, des inhibiteurs de corrosion;
des acides siliciques, en particulier des acides siliciques colloïdaux ou dispersés;
des tensioactifs; des diols, des triols, des polyols; des acides organiques, en particulier
des acides monocarboxyliques; des amines; des dispersions plastiques; des colorants,
des pigments, en particulier le noir de carbone, des agents chromogéniques, en particulier
des agents chromogéniques métalliques; des aminoacides, en particulier la glycine;
des siccatifs, en particulier des siccatifs au cobalt; des agents de dispersion; ainsi
que
des mélanges de ceux-ci.
14. Utilisation selon l'une des revendications 10 à 13, caractérisée en ce que le chrome(III) est présent dans une concentration de 5 g/l à 80 g/l, particulièrement
de 5 g/l à 60 g/l, de manière particulièrement préférée de 10 g/l à 30 g/l, de manière
préférentielle de 20 g/l.
15. Utilisation selon l'une des revendications 10 à 14, caractérisée en ce que les solutions présentent un pH compris entre 1,5 et 3.
16. Utilisation selon l'une des revendications 10 à 15, caractérisée en ce que les solutions contiennent 20 g/l de chrome(III) et ont un pH de 2 à 2,5.
17. Utilisation selon l'une des revendications 10 à 16, caractérisée en ce que les solutions présentent une température de bain de 20 à 100°C, préférablement de
20 à 80°C, de manière préférée de 30 à 60°C, de manière particulièrement préférée
de 40 à 60°C.
18. Utilisation selon l'une des revendications 10 à 17, caractérisée en ce que les objets à traiter sont immergés dans les solutions contenant du chrome(III) pendant
un laps de temps compris entre 15 et 200 secondes, en particulier entre 15 et 100
secondes, préférablement de 30 secondes.