BACKGROUND OF THE INVENTION
FIELD OF THE INVENTION
[0001] The present invention relates to a method of stably observing the temperature and/or
composition of molten iron, including molten steel, in a refining furnace by detecting
electromagnetic waves, which are radiated from molten metal, at an end of a single
tube under a non-contact state, via a tube penetrating refractories on a furnace wall
and/or a furnace bottom of the molten iron refining furnace such as a converter, an
AOD and an RH.
DESCRIPTION OF THE PRIOR ART
[0002] Conventionally, there is provided a method of observing the temperature and composition
of molten iron in a refining furnace, which is represented by a converter, via a tube
penetrating refractories on a furnace wall and/or a furnace bottom.
[0003] For example, the following methods are provided. Concerning the temperature of molten
iron in a refining furnace, there is provided a method in which an image fiber is
used as disclosed in Japanese Unexamined Patent Publication No. 11-142246. Concerning
the composition of molten iron in a refining furnace, there is provided a method in
which laser beams are used as disclosed in Japanese Unexamined Patent Publication
No. 60-42644.
[0004] In the above techniques, it is necessary for a tuyere used for observation to be
opened at all times. In general, in the case where gas is supplied from a tuyere to
molten iron, a piece of solid iron, which is referred to as a mushroom, is created
by coagulation at an end of the tuyere. Due to the creation of this mushroom, it becomes
impossible to observe the temperature and composition of molten iron. In the case
where the end of the tuyere is opened by an exothermic reaction which is caused by
supplying oxygen gas, the front side of the tuyere is heated to a high temperature
by the heat created in the process of oxidation. Therefore, it becomes impossible
to measure the temperature. Further, it becomes impossible to measure the content
of light elements, because they are absorbed by oxygen gas. The creation of the mushroom
is greatly affected by not only the composition and flow rate of the gas supplied
from a tube but also the temperature and the components of the molten steel. However,
there is provided no knowledge to make the appropriate control condition clear. As
described above, according to the prior art, no knowledge about now to keep open the
tuyere used for observation at all times is known. Therefore, it is impossible to
stably observe the inside of the furnace in the process of refining.
SUMMARY OF THE INVENTION
[0005] It is an object of the present invention to provide a method of stably observing
the temperature and/or composition of molten iron, including molten steel, in a refining
furnace by keeping a tuyere used for observation open at all times, according to the
state of refining. It is another object of the present invention to provide a tuyere
used for observation in the method. The invention will be described as follows.
(1) A method of observing the inside of a molten metal refining furnace comprising
the steps of: using a single tube tuyere for observing the temperature and/or composition
of molten iron in the refining furnace via a tube penetrating refractories of a furnace
wall and/or furnace bottom of the molten iron refining furnace by detecting electromagnetic
waves radiated from molten metal at a forward end of the tube under a non-contact
state; and using an inert gas or an oxidizing gas alone, or mixed with each other,
according to the opening condition of the forward end of the tube. In this case, the
inert gas is Ar, nitrogen or CO, and the oxidizing gas is oxygen, air or CO2.
(2) A method of observing the inside of a molten metal refining furnace according
to item (1), wherein a mixed gas of an inert gas with an oxidizing gas or only an
oxidizing gas is supplied (the opening period) in the case where the ratio (%) of
opening of the tube is not higher than α which is calculated by the inner diameter
r (mm) of the tuyere according to Equation (1), and only inert gas is supplied (the
steady period) in the case where the ratio of opening is higher than α.
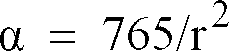
In this case, the opening period is judged and completed when the temperature of molten
iron at the forward end of the tube to be measured is not lower than 1800°C. Although
the upper limit of the rate of opening is not particularly prescribed, it is preferable
that the upper limit of the rate of opening is not more than 95% so as to prevent
the fusion of the tuyere.
(3) A method of observing the inside of a molten metal refining furnace comprising
the steps of: using a single tube tuyere for observing the temperature and/or composition
of molten iron in the refining furnace via a tube penetrating refractories of a furnace
wall and/or furnace bottom of the molten iron refining furnace, by detecting electromagnetic
waves radiated from molten metal, at a forward end of the tube under a non-contact
state; and controlling a flow rate of an inert gas according to the opening condition
of the forward end of the tube. In this case, the inert gas is Ar, nitrogen or CO.
(4) A method of observing the inside of a molten metal refining furnace according
to item (3), wherein the flow rate of an inert gas is controlled according to the
temperature and composition of the molten iron so that the ratio (%) of opening of
the single tube can be not less than α, which is calculated by the inner diameter
r (mm) of the tube according to Equation (1), and not more than 95%.
(5) A tuyere for observing the inside of a molten metal refining furnace having a
single tube for observing the temperature and/or composition of molten iron in the
refining furnace, via a tube penetrating refractories of a furnace wall and/or furnace
bottom of the molten iron refining furnace, by detecting electromagnetic waves radiated
from molten metal at a forward end of the tube under a non-contact state, the tuyere
for observing the inside of a molten metal refining furnace comprising a control function
by which an inert gas or an oxidizing gas can be used alone, or mixed with each other,
according to the state of the opening of the forward end of the tube, the inner diameter
of which is 2 to 6 mm.
(6) A method of observing the inside of a molten metal refining furnace in which the
temperature and/or composition of the molten iron in the molten iron refining furnace
is observed via a tube penetrating refractories of a furnace wall and/or furnace bottom
of the molten metal refining furnace, in a non-contact state, by detecting electromagnetic
waves radiated from molten iron at the forward end of the tube, the method of observing
the inside of the molten metal refining furnace comprising the steps of: using a twin
tube tuyere; detecting a ratio of opening of the forward end of the inner tube tuyere;
and controlling a size of a mushroom at the forward end tuyere by changing gas flow
rate and/or gas composition which is supplied through the inner and the outer tube
according to a change in the ratio of opening so as to keep the ratio of opening necessary
for observation.
(7) A method of observing the inside of a molten metal refining furnace according
to item (6), further comprising the steps of: estimating the size of the mushroom
at the forward end of tuyere according to the temperature and composition of molten
iron; and controlling the size of the mushroom at the forward end of tuyere by changing
the gas flow rate of and/or gas composition of LPG inert gas, inert gas and oxidizing
gas which are supplied through the outer tube according to the result of the estimation
so as to keep the ratio (%) of opening of the inner tube in a range from not less
than α (%), which is calculated by Equation (5), to not more than 95%.

where r is an inner diameter (mm) of the inner tube.
(8) A method of observing the inside of a molten metal refining furnace according
to item (6), further comprising the steps of: supplying a mixed gas, in which an inert
gas and an oxidizing gas are mixed with each other, or only an oxidizing gas from
the inner tube, so as to increase the ratio of opening in a tube opening period in
the case where the ratio of opening of the inner tube is lower than α (%) in Equation
(5); and supplying only inert gas from the inner tube in a period except for the tube
opening period.
(9) A method of observing the inside of a molten metal refining furnace according
to one of items (6) to (8), further comprising the steps of: supplying an inert gas
from the inner tube at all times; supplying a mixed gas, in which inert gas and oxidizing
gas are mixed with each other, or only an oxidizing gas, from the outer tube so as
to increase the ratio of opening of the inner tube in a tube opening period in the
case where the ratio of opening of the inner tube is lower than α (%) in Equation
(5); and supplying tuyere cooling gas, or inert gas alone, through the outer tube
or supplying mixed gas, in which tuyere cooling gas and inert gas are mixed, from
the outer tube in a period except for the tube opening period.
(10) A tuyere for observing the inside of a molten metal refining furnace, which is
a double tube tuyere for observing the temperature and/or composition of molten iron
in the refining furnace via a tube penetrating refractories of a furnace wall and/or
a furnace bottom of the molten iron refining furnace by detecting electromagnetic
waves radiated from molten metal at a forward end of the tube under a non-contact
state, -the tuyere for observing the inside of a molten metal refining furnace comprising:
a piping structure; and a control system capable of independently controlling a gas
flow rate and/or gas composition which is supplied through each of the inner and the
outer tube.
(11) A tuyere for observing the inside of a molten metal refining furnace according
to claim 10, wherein inner diameter r of the inner tube is 5 to 20 mm.
BRIEF DESCRIPTION OF THE DRAWINGS
[0006]
Fig. 1 is a view showing a relation between the diameter (K) of an opening section
of a tuyere for observation, the diameter (M) of a mushroom created at a forward end
of the tuyere, and inner diameter (r) of the inner tube.
Fig. 2 is a view showing a result of an experiment which shows a relation between
parameter α, inner diameter r of a tube and the accuracy of measurement of temperature
by radiation.
Fig. 3 is a view showing a relation between a ratio of an opening and the accuracy
of measurement of temperature by radiation in the case where a tube, the inner diameter
of which is 10 mm, is used.
Fig. 4 is a view showing a model of a single tube for observation of the present invention.
Fig. 5 is a view showing a model of a twin tube for observing the inside of a furnace
of the present invention.
DESCRIPTION OF THE MOST PREFERRED EMBODIMENT
[0007] The present invention has been accomplished according to the new knowledge that the
opening area of a tuyere for observation and the size of a mushroom created at a forward
end of the tube are correlated to each other and the opening area can be controlled
when the mushroom size is controlled. Fig. 1 is a graph showing a detailed result
of an experiment made by the present inventors in which a melting furnace, the capacity
of which was 1 ton, was used. As shown in Fig. 1, M/r and K/r are strongly correlated
to each other wherein r is an inner diameter of an inner tube of a tuyere, K is a
diameter of an opening section of the tuyere for observation, and M is a diameter
of a mushroom created at a forward end of the tube. That is, in order to control the
ratio of opening of the tube to be a value necessary for observation, it is necessary
to control the mushroom size by changing the gas flow rate and gas composition.
[0008] In this case, the electromagnetic wave is a generic name for emitted energy such
as light used for radiant measurement and light used for laser beam emission analysis,
the wave-length of which is peculiar to each component. The reason why the single
tube is adopted in the present invention is that gas is supplied to the single tube
from a single gas generation system, so that the equipment investment is small. The
reason why the twin tube tuyere is adopted in the present invention is that the composition
and gas flow rate can be independently controlled by the twin tube tuyere. Gas used
for the inner and outer tube is a tuyere cooling gas, such as LPG inert gas, an inert
gas and an oxidizing gas which are used alone or mixed. Concerning the tuyere cooling
gas of the outer tube, by which the cooling effect can be positively provided when
the gas is decomposed. Concerning the inert gas of the outer tube, Ar, nitrogen or
carbon monoxide gas is used. Concerning the oxidizing gas of the outer tube, oxygen,
air or carbon dioxide is used. Concerning the inert gas used for the inner tube, Ar,
nitrogen or carbon monoxide gas is used. Concerning the oxidizing gas used for the
inner tube, oxygen, air or carbon dioxide is used.
[0009] The first item of the present invention is a method of observing the inside of a
molten metal refining furnace represented by a converter, an electric furnace or an
AOD comprising the steps of: using a single tube for observing the temperature and/or
composition of molten iron in the refining furnace via a tube penetrating refractories
of a furnace wall and/or furnace bottom of the molten iron refining furnace by detecting
electromagnetic waves radiated from molten metal at a forward end of the tube under
a non-contact state; and using inert gas or oxidizing gas alone or mixed according
to the opening condition of the forward end of the tube.
[0010] In the single tube, according to the state of opening at a forward end of the tube,
inert gas and oxidizing gas are used alone or mixed. That is, observation is conducted
by detecting an electromagnetic wave radiated from an interface formed between a molten
iron face at the forward end of the tube and bubbles of gas blown out from the tuyere.
The ratio of opening of the forward end of the tube is controlled according to the
composition of gas so that an intensity of electromagnetic waves can be controlled
to be a sufficiently high value prescribed according to the method of observation.
In this case, the inert gas is Ar, nitrogen or CO. The oxidizing gas is oxygen, air
or CO
2. In the case where the ratio of opening at the forward end of the tube is too low,
the accuracy of observation is deteriorated. Therefore, oxidizing gas is mixed with
inert gas, so that the mushroom created at the forward end of the tube is melted.
On the contrary, in the case where the ratio of opening at the forward end of the
tube is too high, the fusion of the tuyere is great, so that inert gas is used alone
and the mushroom is created as long as the accuracy of observation is not deteriorated.
[0011] The second item of the present invention prescribes a specific control method in
the first invention. In this case, the area of opening necessary for observation of
temperature in which an intensity of electromagnetic waves is high is different from
the area of opening necessary for observation in the case of laser emitted light for
composition analysis in which an intensity of light is low. Further, the area of opening
necessary for observation is different according to the inner diameter and length
of the tuyere. In general, when consideration is given to the thickness of refractories
of a large-scale converter, the length of the tuyere is approximately 1 to 2 m. In
this case, the area of observation of 6 mm
2 is required, which is experimentally known. This knowledge is organized into Equation
(1). Accordingly, the second item of the present invention provides a method of observing
the inside of a molten metal refining furnace, wherein a mixed gas of an inert gas
with an oxidizing gas, or only an oxidizing gas, is supplied (in the opening period)
in the case where the ratio (%) of opening of the tube is not higher than α which
is calculated by the inner diameter r of the tube according to Formula (1), and only
inert gas is supplied (in the steady period) in the case where the ratio of opening
is higher than α.
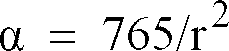
[0012] In this case, the ratio of opening is defined as a value obtained when an area of
the opening, at the forward end of the tube not covered with the mushroom, is divided
by a cross-sectional area of the tube, wherein this ratio of opening is expressed
by percent. In the case where a relation between the ratio of opening and the back
pressure is previously measured, it is possible to detect the ratio of opening by
a change in the back pressure of gas. Further, it is possible to directly detect the
ratio of opening by the observation conducted by an image fiber arranged at the forward
end of the tuyere on the shell side.
[0013] Fig. 2 is a graph showing an example in which the present invention is applied to
the measurement of radiation in which an image fiber is used. The accuracy of the
vertical axis corresponds to 2σ (σ is a standard deviation) of the measured temperature.
Due to the foregoing, it is understood that the temperature can be observed with accuracy
when α × r
2 is not lower than 765. However, when α × r
2 is lower than 765, the visual field is decreased because of a block in the opening.
Accordingly, the accuracy of observation is deteriorated.
[0014] Specifically, control is conducted as follows. In the case where the ratio of opening
of the tube is lower than the critical value necessary for observation, the value
of α × r
2 of which is 765, one of or two and more of the rate of flow of oxidizing gas of oxygen,
air and CO
2 and the flow rate of inert gas of Ar, nitrogen and CO are adjusted according to the
inner diameter of the tube, the temperature of the molten iron and the concentration
of carbon in the molten iron, so that the rate of opening can be controlled.
[0015] The diameter of the mushroom formed at the forward end of the tube, which is an index
of control, can be calculated according to the heat balance of each item described
below. When a relation between the diameter of the mushroom and the rate of opening
is experimentally found, it is possible to conduct control.
(1) Index (v1) of cooling by sensible heat of gas: function of specific heat of gas
(2) Index (v2) of cooling by latent heat of gas: function of reaction heat of gas
(3) Index (k) of receiving heat of the mushroom from molten iron
[0016] When the mushroom is assumed to be a hemisphere, the following heat balance is established.

[0017] In the above Equation (2), a, b and n are constants, Q is a flow rate of total gas
(Nm
3/h/t), T is a temperature (°C) of molten iron, and Ts is a solid line temperature
(°C). In this case, v1 and v2 can be calculated when a ratio of contribution to the
creation of the mushroom is determined by an experiment according to the physical
property and reaction heat of the used gas. Ts can be found by the phase diagram.
When these are put into Equation (2) and the constants are determined so that they
can agree with the mushroom diameter obtained by an experiment, it is possible to
obtain a formula of estimation of the mushroom diameter when an actual device is used.
In this connection, concerning the ratio of contribution of reaction heat, the present
inventors found the following by an experiment. In the case of oxygen (including a
component of oxygen in air), the ratio of contribution is 70 to 80% of the latent
heat of forming reaction of FeO calculated by the reaction of 2Fe + O
2 = FeO. However, in the case of CO
2, the ratio of contribution is only 2 to 5% of the latent heat calculated by the reaction
of CO
2 +[C] =2CO. Further, according to the experiment made by the present inventors, diameter
M (mm) of the mushroom, the inner diameter r (mm) of the tube and the diameter K (mm)
of the opening section equivalent to a circle have a relation expressed by the following
Equation (3).

[0018] In the above equation, β is in a range from 1.0 to 1.3.
[0019] The third item of the present invention is a method of observing the inside of a
molten metal refining furnace comprising the steps of: using a single tube for observing
the temperature and/or composition of molten iron in the refining furnace via a tube
penetrating refractories of a furnace wall and/or furnace bottom of the molten iron
refining furnace by detecting electromagnetic waves radiated from molten metal at
a forward end of the tube under a non-contact state; and controlling a flow rate of
inert gas according to the opening condition of the forward end of the tube. According
to the method, the mushroom size is controlled when the flow rate of inert gas is
controlled. When the ratio of opening at the forward end of the tube is too low, the
accuracy of observation is deteriorated. Therefore, when the flow rate of inert gas
is decreased so as to decrease the cooling capacity given by the sensible heat of
gas, the mushroom created at the forward end of the tube is melted. On the contrary,
when the ratio of opening at the forward end of the tube is too high, the tube is
greatly melted. Therefore, when the flow rate of inert gas is increased so as to increase
the cooling capacity given by the sensible heat of gas, the mushroom is created as
long as the accuracy of observation is not deteriorated.
[0020] This is necessary when the inside of the tube must be kept in an atmosphere of inert
gas at all times so that the emitted light can be transmitted without causing attenuation
in the case where light of a short wave-length, which has been emitted from carbon
or phosphorus by laser beams, is observed. The present inventors found that the ratio
of opening can be controlled even if the inside of the tube is kept in an atmosphere
of inert gas at all times.
[0021] The fourth and the fifth item of the present invention prescribe a specific control
method of the third invention. The fourth item of the present invention provides a
method of observing the inside of a molten metal refining furnace, in which a flow
rate of inert gas is controlled according to the temperature and composition of molten
iron so that the ratio (%) of opening of the single tube can be not less than α, which
is calculated by the inner diameter r (mm) of the tube according to Equation (1),
and not more than 95%. When the ratio of opening is higher than 95%, the size of the
mushroom created at the forward end of the tube is too small. Therefore, it is impossible
to protect the tube, and the life of the tube is short.
[0022] In the fifth item of the present invention, the carbon concentration can be estimated
by a method in which the carbon concentration is calculated from the quantity of oxygen
to be supplied and the decarbonizing efficiency, which is experimentally known, on
the basis of the carbon concentration of molten iron to be charged. Further, the carbon
concentration can be estimated by a method in which the carbon concentration is estimated
from the exhaust gas analysis and the result of direct sampling of molten iron. Alternatively,
the carbon concentration can be estimated by the combination of the above methods.
The temperature can be estimated by a direct continuous measurement method or a semi-continuous
measurement method. Further, the temperature can be estimated by a method in which
the temperature is calculated from the temperature rising efficiency which is experimentally
known. Alternatively, the temperature can be estimated by the combination of the above
methods. The reason why the flow rate of inert gas is controlled according to the
temperature and composition of molten iron is that the size of the mushroom is greatly
affected by a difference between the temperature of molten iron and the temperature
of the solid phase line of molten iron. Also, the reason why the flow rate of inert
gas is controlled according to the temperature and composition of molten iron is that
it is necessary to detect a difference between the temperature of molten iron and
the temperature of the solid phase line which is determined by the molten iron composition
(the carbon concentration) and also it is necessary to increase and decrease the flow
rate according to the value of difference.
[0023] Also, in this case, the diameter of the mushroom at the forward end of the tube,
which is an index of control, can be calculated by the heat balance of each item.
It is possible to control when an experimental relation between the diameter of the
mushroom and the ratio of opening is found.
(1) Index (v1) of cooling by sensible heat of gas: function of specific heat of gas
(2) Index (k) of receiving heat of the mushroom from molten iron
[0024] When the mushroom is assumed to be a hemisphere, the following heat balance is established.

[0025] In the above Equation (4), a, b and n are constants, Q is a flow rate of total gas
(Nm
3/h/t), T is a temperature (°C) of molten iron, and Ts is a solid line temperature
(°C). In this case, v1 can be calculated according to the physical property of the
used gas. Ts can be found according to the phase diagram. When these are put into
Equation (4) the constants are determined so that they can agree with the mushroom
diameter obtained by an experiment. In this way, it is possible to obtain a formula
of estimation of the mushroom diameter when an actual device is used. The relation
between diameter M of the mushroom and diameter K of the equivalent circle of the
opening section can be calculated by Equation (3).
[0026] Concerning the tuyere, as shown by an embodiment in Fig. 4, the present invention
provides a tuyere for observing the inside of a molten metal refining furnace which
is a single tube for observing the temperature and/or composition of molten iron in
the refining furnace via a tube penetrating refractories of a furnace wall and/or
furnace bottom of the molten iron refining furnace by detecting electromagnetic waves
radiated from molten metal at a forward end of the tube under a non-contact state,
the tuyere for observing the inside of a molten metal refining furnace comprising
a control function by which inert gas or oxidizing gas can be used alone or mixed
according to a state of opening of the forward end of the tube.
[0027] In this case, concerning the inner diameter of the tube for observation, the inner
diameter of the tube pipe is 2 to 6 mm. In the case where the inner diameter of the
tube is smaller than 2 mm, it is impossible to create a mushroom when the opening
area necessary for observation is ensured. Therefore, the life of the tuyere is short.
In the case where the inner diameter of the tube is larger than 6 mm, the flow rate
of gas is increased and the cost is raised, which is not economical.
[0028] Next, explanations will be made into a case in which the twin tube tuyere of the
present invention is adopted.
[0029] According to the sixth item of the present invention, electromagnetic waves are detected
which are emitted from an interface formed between the molten iron surface at the
forward end of the tube and the bubbles of gas which has been blown into the tuyere.
In this case, it is necessary to control the ratio of opening at the forward end of
the inner tube by the composition and flow rate of gas in the inner and the outer
tube so that an intensity of the electromagnetic waves emitted from the interface
can be sufficiently high for the intensity required by the method of observation.
Therefore, the ratio of opening is detected by the change in the back pressure of
gas and the result of observation conducted by an image fiber. According to the thus
detected ratio of opening, the flow rate and/or composition of gas in the inner and
the outer tube is changed so as to change the size of the mushroom. In this way, the
ratio of opening necessary for observation is kept.
[0030] The seventh item of the present invention is a specific control method of the above
item 6 of the present invention. According to the seventh item of the present invention,
when the cooling capacity of the outer tube is controlled according to the temperature
and composition of molten iron, the ratio of opening of the tuyere is kept to be a
value higher than the critical value necessary for observation at all times. When
the gas flow rate and/or gas composition which are supplied through each of the tuyere,
inert gas and oxidizing gas of the outer tube is changed according to the mushroom
size which is estimated according to the temperature and composition of molten iron,
the ratio (%) of opening of the tube is kept in a range not less than α (%) and not
more than 95%.
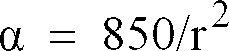
where r is an inner diameter (mm) of the inner tube. Since it is preferable that
r is not less than 3 mm, α is set at a value lower than 95%. Further, it is preferable
that inert gas is supplied into the inner tube at all times. In this case, the ratio
of opening is defined as a value (%) which is obtained when an area of the opening
region at the forward end of the tube not covered with the mushroom is divided by
a cross-sectional area of the tuyere.
[0031] The critical value of the ratio of opening, in the case where the intensity of electromagnetic
waves is high such as a case in which the temperature is observed, is different from
the critical value of the ratio of opening, in the case where the intensity of electromagnetic
waves is low such as a case of light emitted by a laser used for component analysis.
Further, the critical value of the ratio of opening is different according to the
inner diameter and the length of the tube. In general, when consideration is given
to the thickness of refractories of a large-scale converter, the length of the tube
is approximately 1 to 2 m. In this case, the area for observation not less than 6
mm
2 is required, which is experimentally known. This knowledge is organized into Equation
(5). In the tube, the inner diameter of which is r (mm), in order to provide an area
R mm
2 for observation at the forward end of the tube, the ratio of opening must be a value
not less than α calculated by Equation (6).

[0032] In this case, when a value not less than 6 mm
2 is substituted into R, Equation (5) can be obtained. In the case where the ratio
of opening is lower than α, the accuracy of observation is deteriorated because the
area of the opening at the forward end of the tube is small. In the case where the
ratio of opening is higher than 95%, since the size of the mushroom created at the
forward end of the tube is too small, it is impossible to protect the tuyere. Therefore,
the life of the tuyere is short. Fig. 3 is a view showing an example of the accuracy
of measurement of temperature by radiation in which an image fiber, the inner diameter
of which was 10 mm, was used. The accuracy of the vertical axis corresponds to 2σ
(σ is a standard deviation) of the measured temperature. Due to the foregoing, it
can be understood that the temperature can be accurately observed when the ratio of
opening is not less than 8.5% (corresponding to α in Equation (5)). However, when
the ratio of opening is lower than 8.5%, the visual field is decreased due to blocking
by the tuyere. Therefore, the accuracy of observation is deteriorated. On the contrary,
when the ratio of opening is higher than 95%, the ratio of opening is so high that
the mushroom cannot be sufficiently created, and the tuyere is damaged by fusion.
[0033] The present invention has been accomplished according to the new knowledge that the
size of the mushroom created at the forward end of the tube, which is closely related
to the opening area of the tuyere for observation, is more affected by the outer tube
gas than by the inner tube gas. Accordingly, in order to control the ratio of opening
of the tube, the flow rate and/or composition of the outer tube is controlled. An
example of the tuyere cooling gas of the outer tube is LPG. Examples of the inner
gas are Ar, nitrogen and carbon monoxide gas. Examples of oxidizing gas are oxygen,
air and carbon dioxide gas. Specifically, in order to make the ratio of opening to
be higher than α, one of the following actions (1) to (4) is executed so as to raise
the temperature of the forward end of the outer tube of the tuyere, so that the mushroom
is melted. In this case, the inner tube is filled with inert gas at all times. Therefore,
no problems are caused in the measurement of electromagnetic waves.
(1) The flow rate of inert gas is decreased.
(2) Oxidizing gas is mixed with inert gas.
(3) In the mixed gas in which inert gas and oxidizing gas are mixed with each other,
while the total flow rate is being kept constant, the mixing ratio of oxidizing gas
is increased, or while the flow rate of inert gas is being kept constant, the flow
rate of oxidizing gas is increased.
(4) Only oxidizing gas is blown into the tuyere.
[0034] On the contrary, when the ratio of opening is made to be not more than 95%, at least
one of the following actions (1) to (3) is executed so as to decrease the temperature
at the forward end of the outer tube of the tuyere, so that the mushroom is created
and the tuyere is protected. In this case, the inner tube is filled with inert gas
at all times. Therefore, no problems are caused in the measurement of electromagnetic
waves.
(1) The flow rate of inert gas is increased.
(2) Tuyere cooling gas is mixed with inert gas.
(3) In the mixed gas in which inert gas and tuyere cooling gas are mixed with each
other, while the total flow rate is being kept constant, the mixing ratio of tuyere
cooling gas is increased, or while the flow rate of inert gas is being kept constant,
the flow rate of tuyere cooling gas is increased.
[0035] Since the behavior of creation of the mushroom is greatly affected by the composition
and temperature of molten iron, it is necessary to control according to the composition
and temperature of molten iron. It is most reasonable that the results of measurement
of the composition and temperature of molten iron, which have been measured according
to the electromagnetic waves obtained through the tuyere for observation, are used.
However, it is possible to estimate the carbon concentration by the method in which
the carbon concentration is calculated from the quantity of oxygen to be supplied
and the decarbonizing oxygen efficiency, which is experimentally known, on the basis
of the carbon concentration of charged molten iron. Also, it is possible to estimate
the carbon concentration by the method in which the carbon concentration is estimated
from the results of exhaust gas analysis or direct sampling of molten iron. The carbon
concentration can be estimated by one of the above methods or the combination of the
above methods. Further, the temperature can be estimated by the method in which the
temperature is calculated from the temperature rising efficiency, which is experimentally
known, on the basis of the temperature of the charged molten iron.
[0036] Specifically, according to the relation shown in Fig. 1, diameter M of the mushroom
created at the forward end of the tube is controlled as M/r. Diameter M of the mushroom
can be estimated in such a manner that diameter M of the mushroom is calculated by
the heat balance of each of the following items (1) to (4).
(1) Cooling index (v1) by sensible heat of outer tube gas: function of specific heat
of outer tube gas
(2) Cooling index (v2) by latent heat of outer tube gas: function of reaction heat
of outer tube gas
(3) Cooling index (v3) by sensible heat of inner tube gas: function of specific heat
of inner tube gas
(4) Heat receiving index (k) from molten iron of mushroom
[0037] When the mushroom is assumed to be a hemisphere, the following heat balance is established.

[0038] In the above Equation (7), a, b and n are constants, Q is a flow rate of total gas
(Nm
3/h/t), T is a temperature (°C) of molten iron, and Ts is a solid line temperature
(°C) determined by the composition of the molten iron. In this case, v1, v2 and v3
can be calculated when a ratio of contribution to the creation of the mushroom is
determined by an experiment according to the physical property and reaction heat of
the used gas. Ts can be found according to the phase diagram. When these are put into
Equation (7) and the constants are determined so that they can agree with the mushroom
diameter obtained by an experiment. In this way, it is possible to obtain a formula
for estimating the mushroom diameter when an actual device is used.
[0039] The eighth item of the present invention provides a method of opening a tuyere by
supplying oxidizing gas from the inner tube when the tuyere is blocked. That is, the
present invention provides a method of observing the inside of a molten metal refining
furnace, further comprising the steps of: supplying a mixed gas, in which an inert
gas and an oxidizing gas are mixed, or containing only an oxidizing gas, from the
inner tube so as to increase the ratio of opening in a tuyere opening period in the
case where the ratio of opening of the tube is lower than α (%) in Equation (5); and
supplying only inert gas from the inner tube in a period except for the tuyere opening
period. In this case, the tuyere opening period is defined as a period from the point
in time at which the ratio of opening becomes lower than α so that the action to open
the opening is executed to the point in time at which the ratio of opening becomes
a value not less than 95%. According to the knowledge of the inventors, in the case
where the ratio of opening cannot be measured because the temperature of the forward
end of the tube is high, it can be judged that the tuyere has been opened when the
temperature of the forward end of the tube is raised to a temperature not lower than
1800°C, and the tuyere opening period can be ended. Concerning the action to open
the opening, one of the following actions (1) and (2) or both of the following actions
(1) and (2) may be executed, so that the temperature of the forward end of the tube
is raised so as to melt the mushroom.
(1) The inner tube is filled with mixed gas in which inert gas and oxidizing gas are
mixed with each other. While the total flow rate is being kept constant, the mixing
ratio of oxidizing gas is increased. Alternatively, while the flow rate of the inert
gas is being kept constant, the flow rate of oxidizing gas is increased.
(2) Only oxidizing gas is blown from the inner tube.
[0040] In this case, the reason why the action to open the opening is conducted in the inner
tube is that it is possible to increase the flow rate of gas so that opening can be
positively conducted in a short period of time. Specifically, as can be seen in Fig.
1, when M/r is not more than 2, K/r becomes not less than 1. The fact that K/r is
1 means that the opening diameter and the tuyere diameter coincide with each other.
That is, the tuyere is completely open. Accordingly, in the case where the tuyere
is blocked, the action is taken by which M/r becomes not more than 2, so that the
tuyere can be opened since K/r is made to be not less than 1. Estimation of diameter
M of the mushroom can be calculated by the heat balance described in each of the following
items.
(1) Cooling index (v1') by sensible heat of outer tube gas: function of specific heat
of outer tube gas
(2) Cooling index (v2') by latent heat of outer tube gas: function of reaction heat
of outer tube gas
(3) Cooling index (v3') by sensible heat of inner tube gas: function of specific heat
of inner tube gas
(4) Cooling index (v4') by latent heat of inner tube gas: function of reaction heat
of inner tube gas
(5) Heat receiving index (k') from molten iron of mushroom
[0041] When the mushroom is assumed to be a hemisphere, the following heat balance is established.

[0042] In the above Equation (8), a', b' and n are constants, Q is a flow rate of total
gas (Nm
3/h/t), T is a temperature (°C) of molten iron, and Ts is a solid line temperature
(°C) determined by the composition of molten iron. In this case, v1' v2', v3' and
v4' can be calculated when a ratio of contribution to the creation of the mushroom
is determined by an experiment according to the physical property and reaction heat
of the used gas. Ts can be found according to the phase diagram. When these are put
into Equation (8) and the constants are determined so that they can agree with the
mushroom diameter obtained by an experiment. It is possible to obtain a equation of
estimation of the mushroom diameter when an actual device is used. According to the
investigation made by the present inventors, the following were found. The ratio of
contribution of the heating value by inner tube oxygen to the diameter of the mushroom
was only 3%, and the ratio of contribution of the sensible heat of inner tube gas
to the diameter of the mushroom was only 30%.
[0043] The ninth item of the present invention shows another method of opening used when
the tuyere is blocked. The method of observing the inside of a molten metal refining
furnace comprises the steps of: supplying inert gas from the inner tube at all times;
supplying a mixed gas, in which inert gas and oxidizing gas are mixed, or only supplying
oxidizing gas, from the outer tube, so as to increase the ratio of opening in the
tuyere opening period in the case where the ratio of opening of the tuyere is lower
than α (%) shown in Equation (5); and supplying tuyere cooling gas or inert gas alone
from the outer tube or supplying mixed gas, in which tuyere cooling gas and inert
gas are mixed with each other, from the outer tube in a period except for the tuyere
opening period. Concerning the action to open the tuyere, one of the following actions
(1) to (3) is executed, so that the temperature at the forward end of the tuyere is
raised and the mushroom is melted.
(1) Oxygen gas is mixed with inert gas in the outer tube.
(2) Tuyere cooling gas in the outer tube is changed over to oxidizing gas.
(3) Only oxidizing gas is supplied to the outer tube.
[0044] The reason why inert gas is supplied to the inner tube at all times and the opening
is made by outer tube gas is described as follows. For example, when light of short
wave-length, which is emitted by carbon or phosphorus by the action of the laser,
is observed, the emitted light is greatly absorbed by oxygen in the tube. Therefore,
in order to transmit the emitted light without being attenuated, it is necessary to
fill the inner tube with an inert gas at all times. According to the investigation
made by the present inventors, it was found that even when an inert gas is supplied
from the inner tube at all times, the tuyere can be opened when the composition of
gas supplied from the outer tube is controlled.
[0045] Specifically, in the same manner as that of the invention described in the above
item (8), according to the relation shown in Fig. 1, diameter M of the mushroom created
at the forward end of the tuyere is controlled as M/r, which is made to be not more
than 2. Diameter M of the mushroom can be estimated in such a manner that diameter
M of the mushroom is calculated by the heat balance of each of the following items
(1) to (4).
(1) Cooling index (v1") by sensible heat of outer tube gas: function of specific heat
of outer tube gas
(2) Cooling index (v2") by latent heat of outer tube gas: function of reaction heat
of outer tube gas
(3) Cooling index (v3") by sensible heat of inner tube gas: function of specific heat
of inner tube gas
(4) Heat receiving index (k") from molten iron of mushroom
[0046] When the mushroom is assumed to be a hemisphere, the following heat balance is established.

[0047] In the above Equation (9), a", b" and n are constants, Q is a flow rate of total
gas (Nm
3/h/t), T is a temperature (°C) of molten iron, and Ts is a solid line temperature
(°C) determined by the composition of molten iron. In this case, v1", v2" and v3"
can be calculated when a ratio of contribution to the creation of the mushroom is
determined by an experiment according to the physical properties and the reaction
heat of the gas used. Ts can be found according to the phase diagram. When these are
put into Equation (9) and the constants are determined so that they can agree with
the mushroom diameter obtained by an experiment, it is possible to obtain a formula
of estimation of the mushroom diameter when an actual device is used. According to
the investigation made by the present inventors, the following were found. The ratio
of contribution of the heating value by outer tube oxygen to the diameter of the mushroom
was 75%, and the ratio of contribution of the sensible heat of outer tube gas to the
diameter of the mushroom was 100%.
[0048] The tenth item of the present invention provides a tuyere for executing a method
of observing the inside of a molten metal refining furnace of the present invention.
The reason why a double tube tuyere for observing the temperature is adopted is that
the composition and flow rate of gas in the inner and the outer tube are independently
controlled. In this double tube tuyere, the ratio of opening at the forward end of
the inner tube tuyere is detected, and the flow rate and/or composition of gas in
the inner and the outer tube is controlled according to the information obtained by
the detection. In order to enable the above operation, the tuyere is composed as shown
in Fig. 5. The tuyere is composed of a concentric double tube structure including
an inner tube 1 and an outer tube 2 penetrating refractories of a refining furnace.
In this structure, the inner tube 1 and the outer tube 2 are independent from each
other.
The flow rate and/or composition of gas can be independently controlled via the inner
tube gas supply pipe 9 and the outer tube gas supply pipe 10 which are independently
connected with the control unit to control the composition and flow rate of gas. In
this case, the inner diameter of the tuyere for observation is prescribed to be 5
to 20 mm. In the case where the inner diameter of the tuyere for observation is smaller
than 5 mm, it is impossible to create a mushroom when an opening area necessary for
observation is ensured, and the life of the tuyere is shortened. In the case where
the inner diameter of the tuyere for observation is larger than 20 mm, the flow rate
of gas is increased, and the cost is raised, which is not economical.
EXAMPLE
[0049] In the example, a top-blow oxygen converter, the capacity of which was 3 ton, was
used. A single tube tuyere, the diameter of which was 4 mm, which was arranged at
the furnace bottom, was used as the tuyere for observation. (In this case, α in Formula
(1) is 47.8.) Nitrogen was supplied alone from the tuyere. Alternatively, a mixed
gas in which Ar and oxygen were mixed with each other was supplied. Molten iron of
[C]: 4.2%, [Mn]: 0.16%, [Si]: 0.21% and [P]: 0.085% was charged into the furnace,
and oxygen was supplied to the furnace for decarbonization. When the supply of oxygen
was started, the temperature of molten iron was 1315°C. In this case, % means mass
percent, which is the same in the following descriptions. The composition at the time
of blowout was [C]: 0.04%, [Mn]: 0.07%, [Si]: 0.01% and [P]: 0.017%, and the temperature
was 1657°C. The measurement of temperature with radiation was executed by an image
fiber through the tuyere for observation. At the same time, laser beams were irradiated
via the tuyere concerned, and light emitted from carbon was observed so as to measure
the carbon concentration. The ratio of the opening was measured by an image obtained
in the image fiber observation. According to a change in the ratio of opening, the
composition and flow rate of gas were controlled.
EXAMPLE 1
[0050] Under the condition shown on Table 1, the flow rate of Ar was controlled for each
carbon concentration and temperature. As a result, it was possible to make an accurate
measurement of temperature and an analysis of carbon concentration all through the
refining period.
Table 1
Carbon (%) |
Temperature (°C) |
Inner tube: Nm3/s |
Ratio of opening % |
Time of measurement 2σ |
|
|
Ar |
Oxygen |
|
|
4 - 2.5 |
1350 - 1425 |
0.0035 - 0.0050 |
0 |
68 - 76 |
2.5 - 3.1 |
2.5 - 1.0 |
1425 - 1525 |
0.0036 - 0.0050 |
0 |
75 - 88 |
2.2 - 3.3 |
1.0 - 0.5 |
1525 - 1600 |
0.0027 - 0.0036 |
0 |
79 - 90 |
1.9 - 2.9 |
0.5 - 0.05 |
1600 - 1650 |
0.0024 - 0.0027 |
0 |
60 - 72 |
2.1 - 3.1 |
EXAMPLE 2
[0051] The temperature rising rate was low at the beginning. Therefore, the tuyere was blocked
at the point of time of [C] = about 0.05% and temperature = 1600°C (as shown by (1)
on Table 2). Therefore, the composition and flow rate of gas were controlled under
the condition shown by (2) on Table 2. As a result, the tuyere was opened again. After
that, it was possible to make an accurate measurement of temperature and an analysis
of carbon concentration all through the refining period.
Table 2
|
Carbon
(%) |
Temperature
(°C) |
Inner tube: Nm3/s |
Ratio of opening % |
Time of measurement
2σ |
|
|
|
Ar |
Oxygen |
|
|
(1)
Comparative Example |
0.05 |
1600 |
0.0024 |
0 |
42 -0 |
Impossibility of measurement |
(2)
Present Invention |
0.05 |
1600 |
0.0024 |
0.00012 |
84 - 93 |
2.2 - 3.5 |
COMPARATIVE EXAMPLE 1
[0052] In Comparative Example 1, operation was performed under the condition shown on Table
3 while the flow rate of Ar was kept constant irrespective of the carbon concentration
and temperature. As a result, the ratio of opening was decreased at the end of refining,
and it became impossible to make observations.
Table 3
Carbon
(%) |
Temperature
(°C) |
Inner tube: Nm3/s |
Ratio of opening
% |
Time of measurement
2σ |
|
|
Ar |
Oxygen |
|
|
4 - 2.5 |
1350 - 1425 |
0.0050 |
0 |
78 - 98 |
2.4 - 3.3 |
2.5 - 1.0 |
1425 - 1525 |
0.0050 |
0 |
68 - 82 |
2.9 - 3.6 |
1.0 - 0.5 |
1525 - 1600 |
0.0050 |
0 |
43 - 61 |
4.8 - 8.5 |
0.5 - 0.05 |
1600 - 1650 |
0.0050 |
0 |
39 - 0 |
Impossibility of measurement |
EXAMPLE 3
[0053] In Example 3, a top-blow oxygen converter, the capacity of which was 3 ton, was used.
A double tube tuyere, the inner diameter of the inner tube tuyere of which was 10
to 15 mm and the interval between the inner and the outer tube of which was 1 mm,
which was arranged at the furnace bottom, was used as the tuyere for observation.
Nitrogen and/or oxygen was supplied from the inner tube, and one of nitrogen, oxygen
and LPG or not less than two of them were supplied from the outer tube. Molten iron
of [C]: 4.2%, [Mn]: 0.16%, [Si]: 0.21% and [P]: 0.085% was charged into the furnace,
and oxygen was supplied to the furnace for decarbonization. When the supply of oxygen
was started, the temperature of molten iron was 1315°C. In this case, % means mass
percent. The composition at the time of blowout was [C]: 0.04%, [Mn]: 0.07%, [Si]:
0.01% and [P]: 0.017%, and the temperature was 1657°C. The measurement of temperature
with radiation was executed by an image fiber through the tuyere for observation.
At the same time, laser beams were irradiated via the inner tube, and light emitted
from carbon was observed so as to measure the carbon concentration. The ratio of opening
was measured by an image obtained in the image fiber observation in the inner tube.
According to a change in the ratio of opening, the composition and flow rate of gas
in the inner and outer tube were changed so as to control the size of the mushroom
at the forward end of the tuyere of the inner tube.
[0054] A double tube tuyere, the inner diameter of the inner tube tuyere of which was 15
mm, was used. Under the condition shown on Table 4, according to a change in the measured
ratio of opening, while the mushroom size was being estimated for each carbon concentration
and temperature, the flow rate of nitrogen in the outer tube was appropriately controlled.
As a result, it was possible to make an accurate measurement of temperature (showing
2 × σ on the table) and an analysis of carbon concentration all through the refining
period. In-this connection, the flow rate of the inner tube was kept constant at a
value 1.5 times as high as the critical flow rate. In this connection, α in Formula
(5) is 3.8% because the inner diameter is 15 mm.
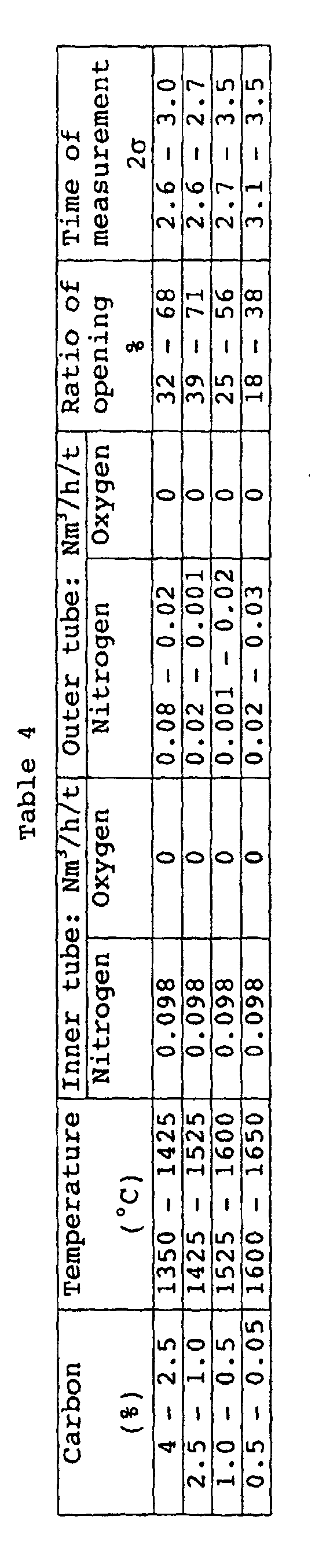
[0055] In this case, the critical flow rate (F: Nm
3/h) was calculated by the following formula.

[0056] In the above formula, ρ
g is gas density (kg/m
3), ρ
1 is molten iron density (kg/m
3), and H is a bath depth (m).
EXAMPLE 4
[0057] In Example 4, the precondition was set to be the same as that of Example 3, and a
double tube tuyere, the inner diameter of the inner tube tuyere of which was 10 mm,
was used. Under the conditions shown on Table 5, according to the change of the ratio
of opening that was measured, the composition and flow rate of outer tube gas were
appropriately controlled while the mushroom size was being estimated for each carbon
concentration and temperature. As a result, it was possible to make an accurate measurement
of temperature and analysis of carbon concentration through all the refining period.
In this connection, the inner tube flow rate was set at a constant value which was
1.5 times as high as the critical flow rate. In Formula (5), α was 8.5% because the
inner diameter was 10 mm.
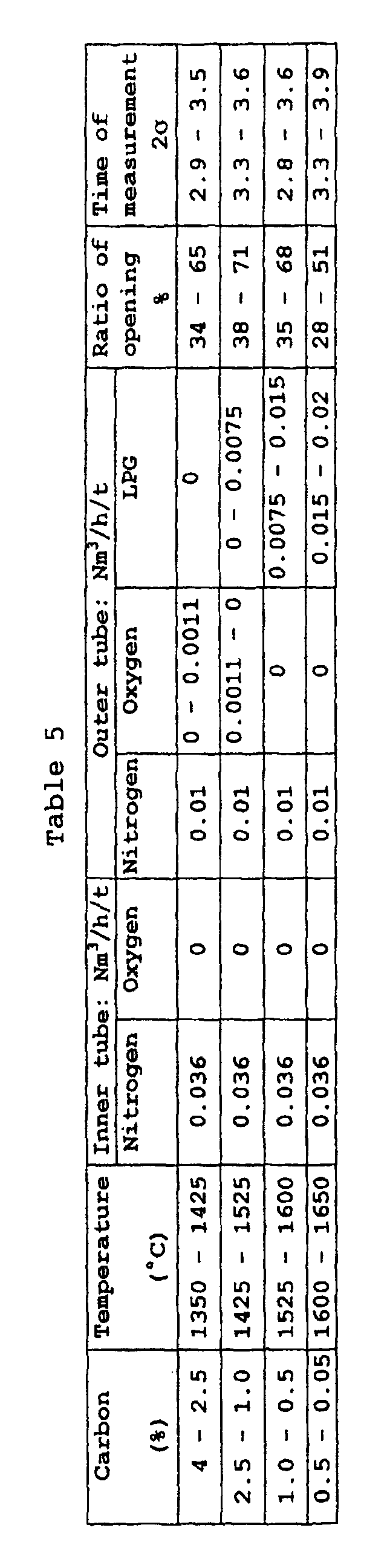
EXAMPLE 5
[0058] In Example 5, the precondition was set to be the same as that of Example 3, and a
double tube tuyere, the inner diameter of the inner tube tuyere of which was 10 mm,
was used. However, the temperature rising rate was low at the beginning, and the tuyere
was blocked at the point of time of [C] = about 2.4% and temperature = about 1400°C
(shown by (1) on Table 6). Therefore, the composition and flow rate of outer tube
gas were changed under the condition of (1) or (2) shown on Table 6, and the size
of the mushroom at the forward end of the inner tube tuyere was controlled. As a result,
the tuyere was opened again. As a result, it was possible to make an accurate measurement
of temperature and an analysis of carbon concentration all through the refining period.

COMPARATIVE EXAMPLE 2
[0059] In Comparative Example 2, a double tube tuyere, the inner diameter of the inner tube
tuyere of which was 15 mm, was used, and operation was performed under the condition
shown on Table 7 wherein the flow rate of nitrogen in the outer tube was kept constant
irrespective of the carbon concentration and temperature. As a result, in the middle
of refining, the ratio of opening was decreased, so that it became impossible to make
observations. Further, at the end of refining, the mushroom was melted and the tuyere
for observation was damaged by fusion.
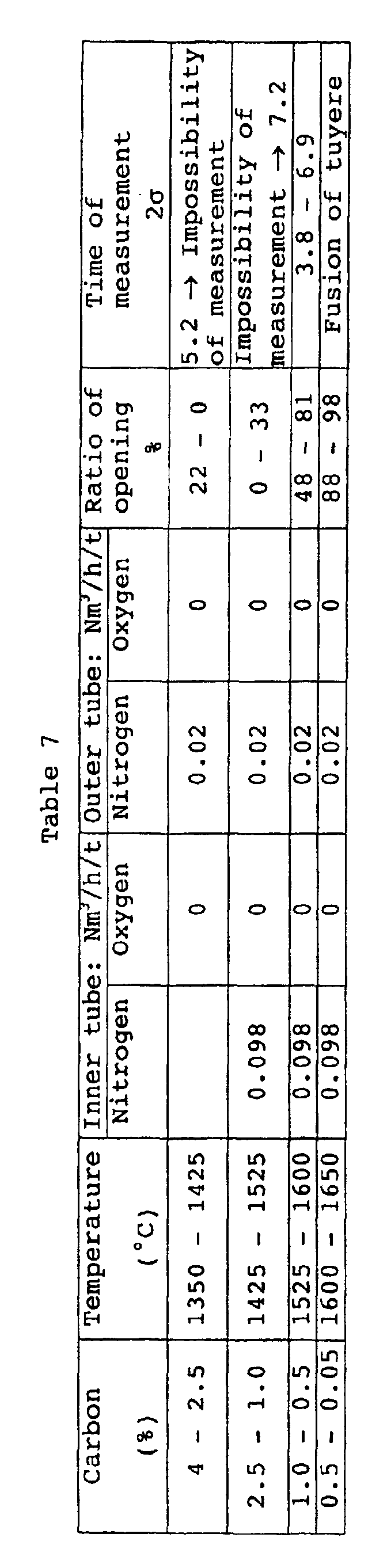
INDUSTRIAL POSSIBILITY
[0060] According to the present invention, it is possible to stably observe the temperature
and/or composition of molten iron in a refining furnace by opening a tuyere for observation,
at all times, according to the state of refining.