[0001] This invention relates to a steel cord used as a reinforcing member for rubber articles
such as pneumatic tires, industrial belts and the like, and more particularly to steel
cords having an excellent durability.
[0002] Pneumatic tires as a typical example of the rubber articles, particularly tires for
construction vehicles are mounted onto a large-size dump truck or the like used on,
for example, large-scale civil engineering site or ore working site and subjected
to severer service conditions on wasteland surface under heavy loading. In general,
this type of the tire has a structure that a carcass is toroidally extended between
a pair of bead cores as a casing skeleton and a belt of plural layers is disposed
on an outside of the carcass in a radial direction of the tire.
[0003] Since the above tire for construction vehicle is run on considerably uneven places
under heavy loading, the tread is subjected to a large deformation and hence bottoms
of grooves formed in the tread such as lug grooves and the like are repeatedly subjected
to a large compression force. When the large compression force is applied to the bottom
of the groove formed in the tread, compression strain is created in an outermost belt
layer constituting the belt near to the tread. Such a compression strain is repeatedly
created during the running of the tire over a long time, whereby fatigue is particularly
stored in cords of the outermost belt layer to induce cord breaking. By such a cord
breaking is decreased the strength of the tire, so that there is a possibility that
the tire is broken in the riding on projection such as rock or the like.
[0004] It is, therefore, an object of the invention to provide steel cords capable of developing
a sufficient durability even in the use under the severe condition subjected to repetitive
compression deformation as well as a pneumatic tire having an excellent durability.
[0005] In the belt of the tire for construction vehicle, it is usual that the steel cord
constituting the belt layer adopts so-called strand construction formed by twisting
plural strands each being formed by twisting plural steel filaments see e.g. US-A-3
911662. Particularly, steel cords of the strand construction having 1 x n structure,
wherein the cord is formed by twisting n-strands of a layer construction formed by
twisting plural steel filaments around a core of one or more steel filaments, are
preferably used in the outermost belt layer constituting the belt of the tire for
construction vehicle in order that the outermost belt layer is followed to the tread
deformation when the tread rides on the projection during the running of the tire.
[0006] As a result of the inventors' studies, it has been confirmed that when the cords
of the above strand construction are subjected to compression strain, sheath filaments
of each strand are precedentially broken or a large compression strain is caused in
the sheath filaments of the strand. And also, it has been confirmed that once the
sheath filament is broken, the large compression strain is caused even in the remaining
filaments and hence these filaments are successively broken to finally bring about
the cord breaking. Furthermore, the cords of the outermost belt layer are successively
broken by successively causing the above course of cord breaking in the other cords
to bring about the lowering of the tire strength. When the tire is subjected to large
shock at the above state in the riding over projections, there is increased a risk
of causing the tire breakage.
[0007] As seen from the above, the breakage of the cord having the strand construction results
from the fact that the large compression strain is caused in the sheath filament constituting
the strand to precedentially break the sheath filament. For this end, the inventors
have made various studies with respect to means for controlling the large compression
strain produced in the sheath filament and found that it is very effective to adequately
define a twisting angle of the sheath filament for improving the fatigue resistance
of the cord.
[0008] Moreover, since the outermost belt layer of the belt is apt to cause corrosion due
to incorporation of water passed through cut damage or the like in the tire into the
inside of the cord constituting the belt layer, it is important to arrange the filaments
of the cord so as to surely penetrate rubber into a gap between the filaments.
[0009] The invention is based on the above knowledge and lies in a steel cord for the reinforcement
of rubber article formed by twisting 4-5 strands, each strand being formed by twisting
a sheath of 4-5 steel filaments around a core of a single steel filament, characterized
in that a ratio of diameter d
S of the steel filament constituting the sheath to diameter d
C of the steel filament constituting the core is within a range of 1.00-1.75, and a
twisting direction of the sheath in the strand is the same as a twisting direction
of the strand in the cord, and a twisting angle α of the sheath in the strand with
respect to an axis of the cord as calculated by the following equation (1) is within
a range of 30-52°:
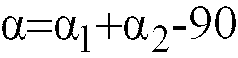
wherein
α1 = tan-1{P1/π·(dC + dS)}
α2 = tan-1{P2/π·(A - dC - 2dS)}
P1: twisting pitch of strand (mm),
P2: twisting pitch of cord (mm),
A: cord diameter (mm).
[0010] Moreover, the twisting angle α is represented by an average in a longitudinal direction
of the cord.
[0011] Further, the invention lies in a pneumatic tire comprising a carcass toroidally extended
between a pair of bead cores as a casing skeleton and a belt of plural layers disposed
on an outside of the carcass in a radial direction of the tire, wherein the above
defined steel cords are applied to at least an outermost belt layer in the belt.
[0012] The invention will be described with reference to the accompanying drawings, wherein:
Fig. 1 is a diagrammatically section view of a steel cord having a twisting structure
of 5 x (1 + 4) according to the invention; and
Fig. 2 is a diagrammatically partial section view of an embodiment of the pneumatic
tire according to the invention.
[0013] In the steel cord for the reinforcement of rubber article according to the invention,
when the cord has a basic structure of m x (1 + n), the number of strands m is 4 to
5 and the number of filaments n in the sheath is 4 to 5.
[0014] When the number of strands m is 3 or less, if the cord is used as a cord in an outermost
belt layer constituting a belt for a large-size tire such as construction vehicle
tire or the like, it is necessary to make the diameter of the filament in order to
obtain a given tire strength, and as the filament diameter becomes thick, strain on
the surface of the filament becomes large due to local bending between the filaments
when the cord is subjected to bending deformation by riding on the projection, and
hence it is easy to cause the cord breaking. On the other hand, when the number of
strands m is 6 or more, it is difficult to arrange the strands on a concentric circle
and the twisting property is degraded to make a breaking load of the cord small.
[0015] The reason why the core in the strand is made of a single filament is due to the
fact that the number of filaments in the core is naturally 1 or 2 in order to penetrate
rubber into the inside of the cord, but when two filaments are used in the core, poor
twisting is apt to be caused due to the difference of twisting shrink amount between
the core and the sheath in the step of producing the cord by twisting the strands.
[0016] When the diameters of the core filament and sheath filament are within the ranges
defined in the invention as mentioned below, if the number of filaments n for the
sheath is 3 or less, the gap between the filaments in the sheath is too large and
the twisting shape become unstable, while when it is 6 or more, the gap enough to
penetrate rubber can not be ensured.
[0017] A typical example of the cord having a basic structure of m x (1 + n) according to
the invention is sectionally shown in Fig. 1. This cord has a twisting construction
of 5 x (1 + 4) formed by twisting five strands 1 of 1+4 structure. Each strand 1 is
formed by twisting four steel filaments arranged adjacent to each other as a sheath
3 around a core 2 made of a single steel filament.
[0018] In the cord according to the invention, it is necessary that the twisting direction
of m strands or the twisting direction of the cord is the same as the twisting direction
of sheath filaments in the strand or the twisting direction of the strand. Because,
when the twisting direction of the cord is different from the twisting direction of
the strand, the filaments between the strands contact at a point and hence the twisting
loss or the lowering ratio of the breaking load of the cord when a sum of breaking
loads of the filaments is 100% becomes large, and as a result, even when the breaking
load of the cord is made large, it can not be developed.
[0019] In the cord according to the invention, the ratio d
S/d
C of diameter of the filament d
S constituting the sheath to diameter of the filament d
C constituting the core is within a range of 1.00-1.75, preferably 1.5-1.75. When the
ratio d
S/d
C is less than 1.00, the core is protruded from the strand due to the difference of
the twisting shrink amount between the core and the sheath in the step of producing
the cord by twisting the strands, while when the ratio d
S/d
C exceeds 1.75, the arrangement of the sheath filaments is eccentric and the twisting
property in the cord becomes ununiform.
[0020] Finally, it is important that the twisting angle a of the sheath in each strand with
respect to the axis of the cord as calculated by the equation (1) is within a range
of 30-52°, preferably 35-45°. When the twisting angle α is less than 30°, the twisting
pitch should be made considerably short, and hence the filament is unavoidably subjected
to strong work in the production step of the cord and troubles such as breakage and
the like are apt to be caused, while when the twisting angle a exceeds 52°, the fatigue
life of the cord becomes shorter than that of steel cord of 4 × (1 + 5 × 0.25) frequently
used in an outermost layer of the belt in the tire for construction vehicle and hence
there is a risk of causing tire breakage in a short time.
[0021] Then, the cords according to the invention are used for the reinforcement of the
carcass by arranging a plurality of the cords side by side and embedding in a rubber
sheet to form a rubberized belt layer for a belt of the tire. As the structure of
the tire, it is sufficient to have the same as in the conventional pneumatic tire
for the construction vehicle. For example, the belt structure shown in Fig. 2 is advantageously
adaptable. In Fig. 2, numeral 4 is a carcass toroidally extending between a pair of
bead cores (not shown) and turned around the bead core from an inside of the tire
toward the outside thereof, numeral 5 a belt disposed on the carcass 4 and comprised
of 4-6 belt layers, a belt of 6 belt layers in the illustrated embodiment, numeral
6 a tread disposed on the belt, and numeral 7 a lug groove.
[0022] The belt 5 has a structure that 6 belt layers each containing many steel cords arranged
at a certain inclination angle, preferably angle of 50-80° with respect to the cord
in the carcass 4 are lain one upon the other so as to cross the cords of these layers
with each other. The cords according to the invention are applied to at least an outermost
belt layer of the belt.
[0023] The following examples are given in illustration of the invention and are not intended
as limitations thereof.
[0024] At first, the durability is measured with respect to steel cords having a construction
shown in Table 1. That is, a fatigue test of repeatedly causing a given compression
strain in a direction of cord axis is carried out with respect to each of these cords
to measure the repetitive number of compression strain until the breakage of any one
of the filaments constituting the cord. The measured results are also shown in Table
1.
[0025] Further, each of the steel cords shown in Table 1 is used in an outermost belt layer
among 6 belt layers constituting a belt of an off-the-road radial tire having a tire
size of 40.00R57 at an end count of 13.1 cords/5 cm. Moreover, steel cords of 7 ×
(3 + 9 × 0.32 mm) are used in two middle belt layers among the remaining five belt
layers and steel cords of 7 × (3 + 9 × 0.23 mm) are used in three inner belt layers.
Each of the tires is inflated under an inner pressure of 7.0 kgf/cm
2 and actually run on road till the tread is completely worn. Thereafter, the tire
is cut to take out 50 cords and the number of broken filaments is measured to obtain
results as shown in Table 1 wherein the tire durability is represented by an index
on the basis that the conventional example is 100.
Table 1
|
Conventional
Example |
Comparative
Example 1 |
Comparative
Example 2 |
Example 1 |
Example 2 |
Cord construction |
4 × (1+5) |
4 × (1+4) |
5 × (1+4) |
5 × (1+4) |
5 × (1+4) |
Filament diameter in core dC (mm) |
0.25 |
0.18 |
0.21 |
0.21 |
0.21 |
Filament diameter in sheath dS (mm) |
0.25 |
0.285 |
0.34 |
0.34 |
0.34 |
dS/dC |
1.00 |
1.58 |
1.62 |
1.62 |
1.62 |
Twisting pitch of strand P1 (mm) |
5.02 |
4.98 |
6.83 |
5.24 |
5.02 |
Twisting pitch in cord P2 (mm) |
11.26 |
8.13 |
12.20 |
12.25 |
11.26 |
Twisting direction |
S/S/S |
Z/Z/Z |
Z/Z/Z |
Z/Z/Z |
Z/Z/Z |
Cord diameter A (mm) |
1.687 |
1.702 |
2.201 |
2.555 |
2.658 |
Twisting angle of sheath with respect to axis of strand α1 |
72.5° |
73.6° |
75.8° |
71.7° |
71.0° |
Twisting angle of strand with respect to axis of cord α2 |
70.0° |
69.9° |
71.4° |
66.9° |
63.7° |
Twisting angle of sheath with respect to axis of cord α |
52.5° |
53.5° |
57.2° |
48.6° |
44.7° |
Compression strain: 4.0% |
34175 |
39678 |
4995 |
286730 |
255000 |
Compression strain: -6.0% * |
7875 |
8048 |
3945 |
34315 |
41175 |
Compression strain: -8.0% * |
2993 |
1974 |
1985 |
10640 |
16763 |
Evaluation of cord durability** |
- |
Δ |
× |
○ |
○ |
Evaluation of tire durability |
100 |
103 |
66 |
no breakage |
no breakage |
*: Repetitive number until the breakage of filament (times) |
*: Superiority or inferiority with respect to conventional example
○ ··· superior
Δ ··· equal
× ··· inferior |
[0026] According to the invention, there can be provided steel cords capable of developing
the sufficient durability even in the use under severe condition repeatedly subjected
to compression deformation. Therefore, when such steel cords are applied to at least
an outermost belt layer in a belt of a tire, the durability against compression strain
particularly concentrated in the groove bottom of the tread is considerably improved
and hence it is possible to provide a tire having an excellent tire durability.
1. A steel cord for the reinforcement of rubber articles formed by twisting 4-5 strands,
each strand (1) being formed by twisting a sheath (3) of 4-5 steel filaments around
a core (2) of a single steel filament,
characterized in that a ratio of diameter d
S of the steel filament constituting the sheath to diameter d
C of the steel filament constituting the core is within a range of 1.00-1.75, and a
twisting direction of the sheath in the strand is the same as a twisting direction
of the strand in the cord, and a twisting angle α of the sheath in the strand with
respect to an axis of the cord as calculated by the following equation (1) is within
a range of 30-52°:

wherein
α1 = tan-1 {P1/π·(dC + dS)}
α2 = tan-1 {P2/π·(A - dC - 2dS)}
P1 : twisting pitch of strand (mm),
P2 : twisting pitch of cord (mm),
A: cord diameter (mm).
2. A steel cord as claimed in claim 1, characterized in that the said ratio dS/dC of diameter of the filament dS constituting the sheath (3) to diameter of the filament dc constituting the core
(2) is within a range of 1.5 -1.75.
3. A steel cord as claimed in claim 1 or 2, characterized in that the said twisting angle α as calculated by the equation (1) is 35 - 45°.
4. A pneumatic tire comprising a carcass (4) toroidally extended between a pair of bead
cores as a casing skeleton and a belt (5) of plural layers disposed on an outside
of the carcass in a radial direction of the tire, characterized in that steel cords as claimed in any of claims 1 to 3 are applied to at least an outermost
belt layer in the belt.
1. Stahlcordfaden zur Verstärkung von Gummierzeugnissen, der durch Verdrillen von 4-5
Litzendrähten gebildet wird, wobei jeder Litzendraht (1) durch Verdrillen eines Mantels
(3) aus 4-5 Stahlfilamenten um einen Kern (2) aus einem einzigen Stahlfilament gebildet
wird,
dadurch gekennzeichnet, daß das Verhältnis des Durchmessers d
s des Stahlfilaments, das den Mantel bildet, zu dem Durchmesser d
c des Stahlfilaments, das den Kern bildet, in dem Bereich von 1,00-1,75 liegt, und
die Verdrillrichtung des Mantels bei dem Litzendraht die gleiche ist wie die Verdrillrichtung
des Litzendrahtes bei dem Cordfaden, und der Verdrillwinkel α des Mantels bei dem
Litzendraht bezüglich der Achse des Cordfadens innerhalb des Bereichs von 30-52° liegt,
wobei der Verdrillwinkel α mittels der folgenden Gleichung (1):
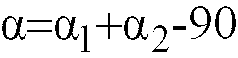
berechnet wird,
wobei:
α1 = tan-1 {P1/π(dc + ds)}
α2 = tan-1 {P2/π·(A - dc -2ds)}
P1: Verdrillsteigung des Litzendrahtes (mm)
P2: Verdrillsteigung des Cordfadens (mm),
A: Cordfadendurchmesser (mm).
2. Stahlcordfaden wie in Anspruch 1 beansprucht, dadurch gekennzeichnet, daß das Verhältnis ds/dc des Durchmessers ds des Filaments, das den Mantel (3) bildet, zu dem Durchmesser dc des Filaments, das den Kern (2) bildet, in dem Bereich von 1,5-1,75 liegt.
3. Stahlcordfaden wie in Anspruch 1 oder 2 beansprucht, dadurch gekennzeichnet, daß der mittels der Gleichung (1) berechnete Verdrillwinkel α 35-45° ist.
4. Luftreifen, aufweisend eine Karkasse (4), die sich als ein Mantelgerüst toroidförmig
zwischen zwei Wulstkernen erstreckt, und einen Gürtel (5) aus mehreren Schichten,
die in der radialen Richtung des Reifens außerhalb der Karkasse angeordnet sind, dadurch gekennzeichnet, daß die in irgendeinem der Ansprüche 1 bis 3 beanspruchten Stahlcordfäden bei dem Gürtel
bei mindestens der äußersten Gürtelschicht verwendet werden.
1. Câblé en acier pour le renforcement d'articles en caoutchouc formé par torsion de
4 à 5 torons, chaque toron (1) étant formé par torsion d'une gaine (3) composée de
4 à 5 filaments d'acier autour d'une âme (2) composée d'un seul filament d'acier,
caractérisé en ce qu'un rapport entre le diamètre d
s du filament d'acier constituant la gaine et le diamètre d
c du filament d'acier constituant l'âme est compris dans un intervalle allant de 1,00
à 1,75, une direction de torsion de la gaine dans le toron étant identique à une direction
de torsion du toron dans le câblé, un angle de torsion α de la gaine dans le toron
par rapport à un axe du câblé, calculé selon l'équation suivante (1), étant compris
dans un intervalle allant de 30 à 52°:
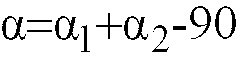
où
α1 = tan-1 {P1/π·(dc + ds)}
α2 = tan-1 {P2/π·(A - de - 2ds)}
P1: pas de torsion du toron (mm)
P2: pas de torsion du câblé (mm)
A: diamètre du câblé (mm).
2. Câblé en acier selon la revendication 1, caractérisé en ce que ledit rapport ds/dc entre diamètre du filament ds constituant la gaine (3) et le diamètre du filament dc constituant l'âme (2) est compris dans un intervalle allant de 1,5 à 1,75.
3. Câblé en acier selon les revendications 1 ou 2, caractérisé en ce que ledit angle de torsion α calculé selon l'équation (1) est compris entre 35 et 45°.
4. , Bandage pneumatique comprenant une carcasse (4) s'étendant toroïdalement entre une
paire de tringle comme squelette d'enveloppe et une ceinture (5) composée de plusieurs
nappes, agencée sur un côté externe de la carcasse dans une direction radiale du bandage
pneumatique, caractérisé en ce que des câblées en acier comme revendiqué dans l'une quelconque des revendications 1
à 3 sont appliqués sur au moins la nappe de ceinture la plus externe de la ceinture.