(19) |
 |
|
(11) |
EP 1 119 429 B1 |
(12) |
EUROPÄISCHE PATENTSCHRIFT |
(45) |
Hinweis auf die Patenterteilung: |
|
02.07.2003 Patentblatt 2003/27 |
(22) |
Anmeldetag: 28.07.1999 |
|
(51) |
Internationale Patentklassifikation (IPC)7: B22F 3/22 |
(86) |
Internationale Anmeldenummer: |
|
PCT/DE9902/343 |
(87) |
Internationale Veröffentlichungsnummer: |
|
WO 0000/6327 (10.02.2000 Gazette 2000/06) |
|
(54) |
VERFAHREN ZUR HERSTELLUNG VON BAUTEILEN DURCH METALLPULVERSPRITZGUSS
METHOD FOR PRODUCING COMPONENTS BY METALLIC POWDER INJECTION MOULDING
PROCEDE DE PRODUCTION DE COMPOSANTS PAR UN PROCEDE DE MOULAGE PAR INJECTION DE POUDRE
METALLIQUE
|
(84) |
Benannte Vertragsstaaten: |
|
AT BE CH CY DE DK ES FI FR GB GR IE IT LI LU MC NL PT SE |
(30) |
Priorität: |
29.07.1998 DE 19834237
|
(43) |
Veröffentlichungstag der Anmeldung: |
|
01.08.2001 Patentblatt 2001/31 |
(73) |
Patentinhaber: |
|
- GKSS-FORSCHUNGSZENTRUM GEESTHACHT GMBH
21502 Geesthacht (DE)
- Tricumed Medizintechnik GmbH
24143 Kiel (DE)
|
|
(72) |
Erfinder: |
|
- HARTWIG, Thomas
D-27721 Ritterhude (DE)
- EBEL, Thomas
D-24147 Klausdorf (DE)
- GERLING, Rainer
D-21465 Reinbek (DE)
|
(74) |
Vertreter: Tönnies, Jan G. et al |
|
Boehmert & Boehmert
Anwaltssozietät
Niemannsweg 133 24105 Kiel 24105 Kiel (DE) |
(56) |
Entgegenhaltungen: :
EP-A- 0 065 702 EP-A- 0 671 231 US-A- 5 911 102
|
EP-A- 0 427 379 US-A- 5 284 329
|
|
|
|
|
- D.EYLON ET AL: "Titanium P/M products" 1990 , METALS HANDBOOK, ASM, 10TH EDITION,
VOL. 2, PAGE(S) 647-660 , US, OHIO, METALS PARK XP002128526 Seite 651, Spalte 3, Zeile
7 - Zeile 13
|
|
|
|
Anmerkung: Innerhalb von neun Monaten nach der Bekanntmachung des Hinweises auf die
Erteilung des europäischen Patents kann jedermann beim Europäischen Patentamt gegen
das erteilte europäischen Patent Einspruch einlegen. Der Einspruch ist schriftlich
einzureichen und zu begründen. Er gilt erst als eingelegt, wenn die Einspruchsgebühr
entrichtet worden ist. (Art. 99(1) Europäisches Patentübereinkommen). |
[0001] Die Erfindung betrifft ein Verfahren zur Herstellung von Bauteilen durch Metallpulverspritzguß
von mit Binder überzogenen Metallpulverteilen mit den Merkmalen der in dem Oberbegriff
des Anspruchs 1 beschriebenen Gattung.
[0002] Komplex geformte Bauteile werden in mittleren und hohen Stückzahlen seit langem im
Kraftfahrzeugsbau, in der Luftfahrt als bewegte Teile und in der Off-Shore-Anwendung
und ferner in der Medizintechnik beispielsweise für Implantate benötigt. Es handelt
sich dabei um komplex geformte Bauteile mit Abmaßen, die bis in den Millimeterbereich
gehen können. In der Regel werden derartig kompliziert geformte Bauteile mit spanabhebenden
Verfahren hergestellt, wie etwa durch Fräsen, durch Drehen und durch Schleifen. Als
Materialien kommen beispielsweise niedriglegierte, hochlegierte oder korrosionsbeständige
Stähle, Schnellarbeitsstähle, Superlegierungen, Legierungen mit magnetischen Eigenschaften,
Hartmetalle und weitere nicht aufgezählte Materialien infrage. Bei der Anwendung eines
spanabhebenden Verfahrens zur Herstellung von komplex geformten Bauteilen, insbesondere
bei der Verwendung von harten, hochfesten Werkstoffen für das Bauteil, besteht beim
Fräsen, Drehen und Schleifen der Nachteil, daß ein hoher Werkzeugverschleiß bei der
Herstellung entsteht und damit entsprechende Kosten. Komplexe Bauteilgeometrien fordern
einen hohen Arbeitsaufwand, damit steigt der Stückpreis. Gewisse komplizierte Strukturen
sind nur mit Hilfe von extremem Aufwand zu realisieren. Dies trifft insbesondere auf
dünne Teile zu, wie beispielsweise dünne Achsen zu, die wegen der mechanischen Belastung
beim Fräsen, Drehen und Schleifen des Teiles der Gefahr einer Beschädigung unterliegen.
Bei Anwendung einer Fertigungstechnik, wie dem Fräsen, Drehen und Schleifen entsteht
generell ein hoher Materialverlust und damit entsprechende Kosten. Ferner ist die
Oberfläche der fertiggestellten komplex geformten Bauteile mit einer nicht akzeptablen
Rauhigkeit der Oberfläche versehen, die spezielle Techniken zur Nachbehandlung erfordert,
um eine Oberfläche mit geringer Rauhigkeit zu erreichen.
[0003] Eine weitere Herstellungsmethode zur Erzeugung eines komplex geformten Bauteiles
mit geringen Dimensionen besteht in der Anwendung des Feingusses. Bei dem Feinguß
ist für jedes hergestellte Bauteil eine Formfertigung erforderlich, deren Herstellung
einen erheblichen Arbeitsaufwand erfordert. Mit Hilfe des Feingusses lassen sich komplex
geformte Bauteile mit kleinen und kleinsten Strukturen, die im Bereich von Zentelmillimeter
liegen, nicht mehr mit Sicherheit reproduzieren. Darüber hinaus reagiert aufgrund
der Temperatur des flüssigen Gusses in der Regel die Oberfläche des hergestellten
komplex geformten Bauteils mit der Wandfläche der Gußform. Die so entstandene Reaktionsschicht
auf der Oberfläche des komplex geformten Bauteils muß zur Herstellung einer einwandfreien
Oberfläche beispielsweise abgebeizt werden. Dieses Abbeizen führt wiederum dazu, daß
enge Toleranzen nicht mehr eingehalten werden können. Ferner sind die mechanischen
Eigenschaften des Gußgefüges, die mittels Feinguß hergestellt werden, den mechanischen
Eigenschaften unterlegen, wenn das komplex geformte Bauteil mit Hilfe der Schmiedetechnik
hergestellt worden ist.
[0004] Es ist ferner bekannt, komplex geformte Bauteile auf dem Wege der Funkenerosion herzustellen.
Die Herstellung von Bauteilen mit der Funkenerosion geht nur langsam und zeitaufwendig
vor sich und ist auch mit erheblichen Kosten verbunden. Beschränkungen bei der Herstellung
von komplex geformten Bauteilen durch Funkenerosion ergeben sich auch dadurch, daß
nicht alle Geometrien des Bauteils mittels Funkenerosion hergestellt werden können.
Darüber hinaus ist naturgemäß der Materialverlust bei der Herstellung eines Bauteils
auf dem Wege der Funkenerosion hoch, Zwangsweise wird durch die Herstellung eines
Bauteils auf dem Wege der Funkenerosion auch die Oberflächenschicht des für das komplex
geformte Bauteil verwendete Materials unbrauchbar und muß mit entsprechenden Verfahren
entfernt und geglättet werden. Die Herstellung einer Oberfläche mit geringer Rauhigkeit
erfordert nicht nur einen zusätzlichen Arbeitsgang, sondern wirkt sich auch negativ
auf die Einhaltung einer hohen Reproduziergenauigkeit und Maßhaltigkeit aus.
[0005] Ein weiteres Verfahren zur Herstellung von komplex geformten Bauteilen mit geringer
Dimension ist in der elektrochemischen Bearbeitung für die Herstellung solcher Bauteile
gegeben. Die elektrochemische Bearbeitung hat den Nachteil, daß manche Bauteilgeometrien
nicht gestaltet werden können und daß grundsätzlich keine scharfen Kanten erzeugt
werden können. Auch bei elektrochemischer Bearbeitung wird bei dem hochwertigen Material
für die Herstellung von komplex geformten Bauteilen ein hoher Anteil abgetragen und
damit ist der Materialverlust erheblich.
[0006] Lassen sich komplex geformte Bauteile aufgrund ihrer speziellen Anforderungen an
die Bauteilgeometrie mit den geschilderten Verfahren nach dem Stand der Technik, wie
Fräsen, Drehen, Schleifen, Feinguß, Funkerosion und elektrochemischen Bearbeitung
nicht herstellen, so wird in der Regel auf einen anderen Werkstoff ausgewichen oder
man wählt ein anderes Design, um dennoch eine Fertigung des komplex geformten Bauteiles
zu erreichen. Wählt man deshalb ein anderes Design des komplex geformten Bauteiles,
das mit einer der geschilderten Techniken nach dem Stand der Technik dann doch gefertigt
werden kann, so erzwingt dies einen Verzicht auf die für den jeweiligen Zweck des
komplex geformten Bauteiles erforderliche optimale Geometrie des Bauteils. Weicht
man zur Fertigung des komplex geformten Bauteils auf einen für die Fertigung nach
dem Stand der Technik besser geeigneten Werkstoff aus, so handelt man sich den Nachteil
ein, daß wegen der veränderten und teilweise mangelhaften Werkstoffeigenschaften des
geänderten Werkstoffes das Bauteil beispielsweise größer dimensioniert werden muß,
als dies für seine optimale Eigenschaft erforderlich wäre, gegebenenfalls müssen Einschränkungen
bezüglich der funktionellen Eigenschaften des Bauteils hingenommen werden oder es
müssen beispielsweise im Fall von Bauteilen, die für die Medizintechnik vorgesehen
sind, Materialeigenschaften eines Werkstoffes akzeptiert werden, die beispielsweise
eine schlechtere Biokompatilität des Bauteils bei einem Implantat bedeutet, wie dies
bei dem Ersatz eines gut verträglichen Titanwerkstoffes durch einen anderen bei einem
Implantat der Fall ist. Jede einzelne der vorstehend genannten Einschränkungen bei
der Wahl eines anderen Designs oder eines anderen Werkstoffes kann für den jeweiligen
Anwendungsfall für sich allein bereits unakzeptabel sein.
[0007] Seit langem ist es bekannt, das Spritzgießverfahren für Bauteile mit komplizierten
Geometrien aus den unterschiedlichsten Kunststoffen anzuwenden, um solche Teile herzustellen.
Für höhere Eigenschaften, wie sie beispielsweise beim Maschinenbau, in der Medizintechnik
und anderen Gebieten erforderlich sind, ließen sich die im Spritzgießverfahren verwendeten
thermo- und/oder duroplastischen Materialien praktisch nicht anwenden, da sie keine
ausreichenden mechanischen Eigenschaften aufwiesen. Eine Verbesserung der mechanischen
Eigenschaften wurde dadurch erzielt, daß man pulverförmige Füllstoffe, beispielsweise
aus Metall beim Spritzgießverfahren verwendet hatte und den Metallanteil in der Spritzgießmasse
so groß wie möglich ausgeführt hat, so daß nun ein Metallbauteil erzeugt wurde, bei
dem der pulverförmige Binder durch Mischen die Metallpulverteile umschließt und durch
diesen Binder zunächst zusammengehalten wird, wobei das geschilderte Verfahren als
Metallpulverspritzgußverfahren bezeichnet wird. Das mit Binder versehene Metallpulver
wird mit einer Spritzgußmaschine in eine Form gespritzt, danach wird zumindest teilweise
der Binder aus dem erhaltenen Bauteilgrünling entfernt und einem Sintern unterzogen.
Um mit dem Metallpulverspritzgußverfahren eine extrem hohe Reproduziergenauigkeit
und Maßhaltigkeit zu erreichen, ferner mechanische Eigenschaften der Bauteile, die
denen von geschmiedeten Bauteilen vergleichbar sind, und
[0008] um ein homogenes Gefüge beim Werkstoff des Bauteils zu erzielen und damit bei der
nachfolgender Wärmebehandlung des Bauteils kein Verzug stattfindet, wurden bereits
Titanpulver zum Erzeugen von hochbeanspruchbaren Bauteilen, wie beispielsweise im
Kraftfahrzeugbau usw. verwendet. Besonders vorteilhaft ist als Werkstoff Titan für
kompliziert geformte Bauteile mit geringer Dimension auf dem Gebiet der Medizintechhik,
da derartige Bauteile als Implantat eine besonders gute Biokompatibilität aufweisen.
Mit Titanpulver lassen sich zwar die erforderlichen Festigkeitswerte von Bauteilen
mit komplex geformeter Struktur erreichen, jedoch fehlt beispielsweise im sicherheitsrelevanten
Bereichen sowohl bei Maschinen wie auch bei Implantaten eine Sicherheitsreserve des
aus Titanpulver hergestellten Bauteils bezüglich der Funktionsfähigkeit und gegen
irreparable Schäden bei Überbelastung und gegen Bruch. Komplex geformte aus Titanpulver
und mit dem Metallpulverspritzgußverfahren hergestellte Bauteile, brechen bei Erreichen
der Festigkeitsgrenze ohne vorherige plastische Verformung sofort (Sprödbruch), was
jedoch im überwiegenden Teil der Anwendungsfälle nicht toleriert werden kann. Dieser
wesentliche Nachteil der nach dem Stand der Technik aus Titanpulver hergestellten
komplex geformten Bauteile resultiert im wesentlichen daher, daß während der Herstellung
dieser Bauteile erhebliche Mengen von Verunreinigungsstoffen, wie Sauerstoff, Kohlenstoff,
Stickstoff und dergleichen in den Werksktoff des Titanbauteils aufgenommen werden.
Damit erlangen aus Titanpulver hergestellte komplex geformte Bauteile bei Anwendung
des Metallpulverspritzgußverfahrens nicht die Eigenschaften, die das gleiche Bauteil
hat, wenn es auf dem Wege des Schmiedeverfahrens hergestellt worden ist.
[0009] Aus der DE 44 08 304 A1 sind Sinterteile aus sauerstoffempfindlichen, nicht reduzierbaren
Pulvern und ihre Herstellung über Spritzgießen bekannt, bei dem Metallpulverteile
aus Titan zur Herstellung von komplex geformten Bauteilen dienen, die Erzeugung oxidfreien
Pulvers unter Luftausschluss und die Feedstockherstellung mit einem Binder unter Schutzgas
erfolgt und bei dem sich ferner die Entbinderung und das Sintern unter Luft- und Feuchtausschluss
vollziehen.
[0010] Der Erfindung liegt die Aufgabe zugrunde, ein preiswertes und für die Massenfertigung
geeignetes Verfahren zur Herstellung von komplex geformten Bauteilen zu schaffen,
das insbesondere eine Sicherheitsreserve des gesinterten Bauteils vor Funktionsunfähigkeit
und gegen irreparable Schäden bei Überbelastung und gegen Bruch ermöglicht, das eine
Minimierung der Aufnahme von Verunreinigungsstoffen in das Material der Bauteile während
der Herstellung der Bauteile bis zur Fertigstellung zuläßt, das für das vorgefertigte
Bauteil ein homogenes Gefüge, eine extrem hohe Reproduziergenauigkeit und Maßhaltigkeit
aufweist, das eine Nachbearbeitung der hergestellten Bauteile vermeidet, das eine
geringe Oberflächenrauhigkeit des fertigen Bauteils ermöglicht, und das während der
Herstellung der komplex geformten einen Verzug der Bauteile ausschließt.
[0011] Die Vorteile der Erfindung liegen insbesondere darin, daß einzelne der Abschnitte
des Verfahrens nach der Erfindung zur Herstellung von komplex geformten Bauteilen
unter striktem Einhalten einer hochreinen Schutzatmosphäre aus Schutzgas und/oder
Luftausschluß und/oder Vakuum stattfindet. Auf diese Weise wird verhindert, daß während
des Herstellprozesses der komplex geformten Bauteile Verunreinigungsstoffe in bezug
auf die vorgegebenen Leistungsdaten des Bauteils in nicht mehr tolerierbarem Umfang
von dem Bauteil aufgenommen werden. Diese einzelnen Herstellabschnitte sind jedoch
teilweise nochmals in Unterabschnitte gegliedert, wobei diese Unterabschnitte ebenfalls
dazu beitragen, daß die Aufnahme von Verunreinigungsstoffen in das Material des Bauteils
stets einem Minimum zugeführt wird, wie beispielsweise die Metallpulverteile der gewählten
Titanlegierung und die Bestandteile des Binders in ihrer Zusammensetzung derart ausgewählt
werden, daß jeder Werkstoffeinzelbestandteil im Ausgangszustand an sich bereits die
Eigenschaft hat, arm an Verunreinigungsstoffen zu sein. Durch diese Auswahl der Bestandteile
der Titanlegierung und des Binders wird der Anteil der unerwünschten Verunreinigungsstoffe
auf den denkbar geringsten Ausgangsbasiswert gesetzt, so daß sich die während des
Verfahrens unvermeidliche Erhöhung der Verunreinigungsstoffe des Material des Bauteils
in der Endsumme ensprechend der gewählten niedrigen Basisverunreinigung der Bestandteile
der Titanlegierung und des Binders verringert. Es findet also die Herstellung der
Metallpulverteile, ferner die Mischung der Metallpulverteile mit den Binderbestandteilen
zur Feedstockherstellung unter dem Einfluß von hochreinem Schutzgas, wie beispielsweise
Argon statt. Die Sinterung selbst erfolgt unter einem Vakuum und die Entbinderung
erfolgt in einem kommerziellen Entbinderbad, beispielsweise mit Hexan und damit unter
Ausschluß der Anwesenheit von Luft und damit von Sauerstoff, Kohlenstoff, Stickstoff
und dergleichen als Verunreinigungsstoffe.
[0012] Jeder einzelne Abschnitt des Herstellverfahrens der komplex geformten Bauteile ist
dem Ziel unterworfen, eine geringst mögliche Anreicherung von Verunreinigungsstoffen
bei jedem Herstellschritt zu erreichen, sowie dies bei der Erzeugung der Metallpulverteile
gemäß der Erfindung erfolgt ist. Für die hochwertige Beanspruchung der erzeugten Bauteile
wurde eine Titanlegierung gewählt, die die Zusammensetzung Ti-6Al-7Nb hat. Die an
Verunreinigungsstoffen armen Metallpulverteile dieser Titanlegierung können durch
zwei Verfahren erzeugt werden, nämlich das Electrode Induction Melting Guiding Gasatomization-Verfahren
oder das Plasma Melting Induction Guiding Gasatomazation-Verfahren. Die Erzeugung
der Metallpulverteile für die genannte Titanlegierung erfolgt durch eine Verdüsungsanlage
mit Argoninertgaszerstäubung, in der die inertgasverdüsten Metallpulverteile in der
gasdicht an die Verdüsungsanlage angeflanschten Pulverkanne aufgefangen werden. Die
Pulverkanne selbst ist dabei gasdicht verschließbar ausgeführt und wird in ein Handschuhboxensystem
eingeschleußt, das selbst wiederum mit Argongas betrieben wird, so daß bei der Herstellung
der Metallpulverteile eine absolut geringe Erhöhung der Verunreinigungsstoffe, wie
Sauerstoff, Kohlenstoff, Stickstoff usw. während dieses Herstellungsabschnittes in
den Pulverbestandteilen des Bauteiles erreicht wird.
[0013] Für das bei der Feedstockherstellung unter Schutzgaseinfluß erfolgende Mischen der
erzeugten Metallpulverteile mit dem Binder ist ebenfalls eine spezielle Zusammensetzung
des Binders zur Minimierung einerseits der Aufnahmemöglichkeit von Verunreinigungsstoffen
während der Feedstockherstellung und andererseits zur Beeinflussung der verbleibenden
Binderreste in dem gesinterten Bauteil durch die Zusammensetzung der Binderbestandteile
bezüglich ihrer Reaktion auf eine Temperaturerhöhung in dem Bauteil ausgewählt worden.
Zur Durchführung einer Teilentbinderung der komplex geformten Bauteile werden Binderbestandteile
mit niedrigen Schmelz-, Zersetzungs- und/oder Verdampfungstemperatur in einem Anteil
dem Binder beigemischt, der größer als die Hälfte der Gesamtbinderanteile ist. Der
Rest des gesamten Gemisches an Binderbestandteilen besteht aus auf höhere Schmelz-,
Zersetzungs- und/oder Verdampfungstemperatur reagierende Binderanteile gegenüber den
niedrigschmelzenden Binderanteilen. Die Metallpulveranteile der Titanlegierung werden
mit Binderbestandteilen aus thermoplastischen oder duroplastischen Polymeren, mit
thermogelierenden Substanzen, mit Wachsen oder oberflächenaktiven Substanzen oder
daraus erhaltenen Mischungen überzogen. Zur Herstellung der erfindungsgemäßen Bauteile
ist ein spezieller Binder ausgewählt worden, der zur Verringerung des Eintrags von
Verunreinigungsstoffen, wie Sauerstoff und zur Verminderung des Restbinders in dem
Bauteil beiträgt.
[0014] Eine weitere Verfahrensmaßnahme bei der Herstellung von hochkompliziert gebauten
Bauteilen besteht darin, daß während der Sinterung diese Bauteile beim Schrumpfen
keine Verbindung mit ihrer Unterlage eingehen dürfen und auch nicht durch Verunreinigungsstoffe
verändert werden sollen, die die Unterlage abscheidet, auf der die Bauteile beim Sintern
liegen, wobei dieselben Bedingungen und Voraussetzungen bei der Unterlage für das
heißisostatische Pressen gelten, das bei den Bauteilen nach der Sinterung noch durchgeführt
werden kann. Um zu verhindern, daß eine Reaktion zwischen den komplex geformten Bauteilen
und der Unterlage stattfindet, ist deshalb die Sinterunterlage für die Bauteile derart
ausgeführt, daß während der Durchführung des Sinterns der Bauteile die freie Gleitfähigkeit
der Oberfläche der Sinterunterlage für die aufliegenden Bauteile unverändert erhalten
bleibt, was beispielsweise durch Ausgestaltung der Oberfläche der Sinterunterlage
mit einem gegen das Material der Bauteile reduktionsbeständigen Werkstoff wie z.B.
Keramikoxyden ggeschieht. Gleichzeitig wird der Werkstoff der Oberfläche der Sinterunterlage
so gewählt, daß der Werkstoff bei Sintertemperatur keine Verunreinigungsstoffe abgibt.
Diese Ausgestaltung der Sinterunterlage ist ein besonderer Vorteil der Erfindung,
um zu vermeiden, daß sich die komplex aufgebauten Bauteile mit oft sehr minimaler
Struktur auf der Sinterunterlage und auch beim heißisostatischen Pressen nicht durch
Verkleben mit der Oberfläche verziehen oder brechen und auch nicht durch Verunreinigungsstoffe
mit der jeweiligen Unterlage kontaminiert werden.
[0015] Ein weiterer Vorteil der vorliegenden Erfindung ist ferner durch das gewählte Herstellverfahren
des Metallpulverspritzgusses gegeben, bei dem das Mischen der Metallpulverteile mit
den Binderbestandteilen zur Feedstockherstellung und auch das Metallformspritzen des
Feedstockes in der Spritzmaschine jeweils bei niedrigen Temperaturen erfolgt, so daß
keine Reaktion des Feedstockes bzw. der Binder- und Metallanteile des Feedstocks mit
dem Mischer selbst oder insbesondere nicht mit der Spritzform in der Spritzgußmaschine
erfolgt, so daß an den komplex geformten Bauteilen keine Oberflächen entstehen, die
mit der Form bzw. mit Geräteteilen reagieren und deshalb auch nicht nachbehandelt
werden müssen, das heißt daß sich die Oberfläche bereits in einem einwandfreien Zustand
befindet, wodurch eine extrem hohe Reproduziergenauigkeit und Maßhaltigkeit und damit
eine endformnahe Herstellung eines hochfesten Bauteils ermöglicht wird. Durch die
Auswahl einer Titanlegierung zur Herstellung nach dem Metallpulverspritzgußverfahren
für komplexe Bauteile, wobei die gewählte Titanlegierung Ti-6Al-7Nb mittels ihrer
Bestandteile die für das herzustellende komplex geformte Bauteile erforderlichen Materialeigenschaften
aufweist, gelingt es mit Hilfe des erfindungsgemäßen Verfahrens, diese Legierungseigenschaften
während der Herstellung in Abschnitten und Unterabschnitten bis zu Fertigstellung
des Endzustandes des Bauteils nahezu unverändert zu erhalten, während es nach dem
Stand der Technik bei dem Herstellverfahren des Metallpulverspritzgusses in der Regel
zu erheblicher Aufnahme von Verunreinigungsstoffen kommt und damit zu einer nicht
tolerierbaren Veränderung der Materialeigenschaften des herzustellenden Bauteils im
Vergleich zu den Ursprungseigenschaften des ausgewählten Materials zur Herstellung
von Metallpulver.
[0016] Nachstehend wird die Erfindung anhand eines Ausführungsbeispiels und von Zeichnungen
noch näher erläutert.
[0017] Es zeigen:
- Fig. 1
- Schaubildform einer Prinzipdarstellung des Verfahrens zur Herstellung komplex geformter
Bauteile mit dem Metallpulverspritzgußverfahren,
- Fig. 2
- die Wiedergabe eines Zugstabes, der nach der Metallpulverspritzgußtechnik hergestellt
ist, vor und nach einem Zugversuch und
[0018] Aus Figur 1 ist in Form eines Schaubildes lediglich skizzenhaft und in Teildarstellung
die Fertigung eines komplex geformten Bauteiles von der Herstellung der Metallpulverteile
über die Feedstockherstellung, das Metallformpritzen, die Entbinderung und die Sinterung
mit zum fertigen Bauteil dargestellt. In Figur 1, 2 und auch bei den Ergebnissen in
Figur 3 wurde bewußt auf die Darstellung eines komplex geformten Bauteiles verzichtet,
um die Übersichtlichkeit zu fördern und um eindeutige Meßergebnisse erzielen zu können.
Komplex geformte Bauteile sind jedoch für ihre Anwendung im Kraftfahrzeugbau, der
Luftfahrt, bei Off-Shore-Anwendungen und in der Medizintechnik, z.B. in Form von Implantaten
erforderlich. Die Metallpulverteile als Material zur Formung von Bauteilen nach der
Erfindung kann auf unterschiedlichen Wegen hergestellt werden. Es kann einmal Pulver
verwendet werden, das durch mechanisches Legieren oder mechanisches Zerkleinern hergestellt
worden ist. Erforderlich ist jedoch, die Werkstoffeinzelbestandteile der Titanlegierung
in ihrer Zusammensetzung derart auszuwählen, daß jeder Werkstoffeinzelbestandteil
im Ausgangszustand an sich bereits die Eigenschaft besitzt, arm an Verunreinigungen
zu sein. Die geforderte Reinheit von Werkstoffeinzelbestandteilen richtet sich nach
den Anforderungen, die an das fertiggestellte Endprodukt Bauteil bei seiner Verwendung
gestellt werden. Jeder Werkstoffeinzelbestandteil der Metallpulverteile muß also die
für das herzustellende Bauteil erforderlichen Materialeigenschaften bereits aufweisen.
Während vorstehend die direkte Pulvermischung als erste Möglichkeit der Herstellung
von Metallpulverteilen geschildert wurde, geht das Ausführungsbeispiel in Figur 1
davon aus, daß vorlegiertes Pulver verwendet wird, also bespielsweise eine in Form
eines Stabes ausgeführte Fertiglegierung. Auch mit dieser Fertiglegierung lassen sich
Metallpulverteile zur Herstellung von komplex gebauten Bauteilen oder einem Prüfkörper
durchführen und zwar in einer Verdüsungsantage mittels einer Argoninertgaszerstäubung.
Es wurde eine Verdüsungsanlage verwendet, die speziell für die Herstellung hochreiner
Titanlegierungspulver konzipiert worden ist. Die Zerstäubung des in einer Fertiglegierung
vorlegierten Titanlegierungspulvers erfolgt unter strikter Einhaltung einer hochreinen
Schutzatmosphäre aus Schutzgas wie beispielsweise Argon. Dadurch und durch die spezielle
Konstruktion der Verdüsungsanlage wird die Aufnahme von Verunreinigungsstoffen wie
Kohlenstoff, Sauerstoff und Stickstoff während des Zerstäubungsprozesses sehr gering
gehalten. Mit der von der Anmelderin verwendeten Anlage wird ein Kohlenstoff- und
Sauerstoffgehalt des Titanlegierungspulvers mit Kohlenstoff: 0,01 Gew.%, Sauerstoff:
0,21 Gew.% erzielt, wobei diese Werte nur knapp oberhalb derjenigen Werte liegen,
die jeder Werkstoffeinzelbestandteil im Ausgangszustand bereits hatte, nämlich bei
Kohlenstoff: 0,01 Gew.% und bei Sauerstoff: 0,2 Gew.%.
[0019] Wenn die Erzeugung der Metallpulverteile für die Titanlegierung mittels einer Verdüsungsanlage
mit Argoninertgaszerstäubung erfolgt, so ist es vorteilhaft, daß die in inertverdüsten
Metallpulverteile in einer gasdicht an der Verdüsungsanlage angeflanschten Pulverkanne
aufgefangen werden. Diese Pulverkanne selbst ist dabei gasdicht verschließbar ausgeführt
und die Pulverkanne wird dann in ein Handschuhboxensystem eingeschleust, das selbst
wiederum mit dem Schutzgas Argon betrieben wird. Diese Maßnahmen werden ergriffen,
um eine Minimierung der Aufnahme von Verunreinigungsstoffen in das Metallpulver bei
der Herstellung zu erzielen. Die Reinheit von Verunreinigungsstoffen der benutzten
Metallpulverteile für die Titanlegierung ist für die Erfüllung der erforderlichen
Materialeigenschaften des fertiggestellten Bauteils sehr wesentlich. Die Pulverbestandteile
müssen weniger verunreinigt sein als das Endprodukt, da im Herstellprozeß des Bauteils
zwar eine Minimierung der aufgenommen Verunreinigungsstoffe in das Bauteil vorgenommen
werden kann, jedoch eine völlige Vermeidung der Aufnahme von Verunreinigungsstoffen
während des Herstellverfahrens des Bauteils praktisch nicht möglich ist. Um das Ziel
hochreiner Metallpulverteile zu erreichen, wurden zwei verschiedene Verfahren zur
Herstellung von Metallpulverteilen für die Titanlegierung verwendet. Zum einen wurde
das Electrode Induction Melting Gasatomization-Verfahren angewandt, und zum anderen
das Plasma-Melting Induction Guiding Gasatomization -Verfahren. Unterschiedliche Ergebnisse
bezüglich der Schadstoffsumme bei der Herstellung der Metallpulverteile werden auch
dadurch verursacht, daß bei Verwendung eines vorlegierten Pulvers in Form eines fertiglegierten
Stabes nach der DIN-Norm der Sauerstoffgehalt mit 2000 µg/g schon im Fertigprodukt
vorgegeben ist, wobei sich auf die vorgegebene Menge der Sauerstoffverunreinigung
noch diejenigen Gew.% an Sauerstoffverunreinigung und natürlich auch anderer Verunreinigungsstoffe
aufaddieren, die während der Herstellung der Metallpulverteile entstehen. Aufgrund
der bei Fertiglegierung enthaltenen nach der DIN-Norm zulässigen Verschmutzung mit
Verunreinigungsstoffen ist es vorteilhaft, selbst die Werkstoffeinzelbestandteile
der Titanlegierung zusammenzustellen, um so durch besondere Sorgfalt bei der Auswahl
und der Behandlung der Einzelbestandteile im Ausgangszustand ein besseres Ergebnis
zu erzielen, d.h. ein Ergebnis das bereits bei der Herstellung der Metallpulverteile
eine Minimierung beispielsweise der Sauerstoffkonzentration im Ausgangszustand ermöglicht.
[0020] Bei der Anwendung der Inertgaszerstäubung zur Herstellung von Metallpulverteilen
entstehen Metallpulverteile in ausgeprägter Kugelform. Die Kugelform ist für die Sinterung
vorteilhaft, da eine hohe Packungsdichte der Metallpulverteile aufgrund der Kugelform
des Pulvers erreicht werden kann und damit eine geringe Restporosität des gesinterten
komplex aufgebauten Bauteils erzielt wird.
[0021] Die erzeugte Metallpulvermenge wird dann mittels einer Siebkette nach der Teilchengröße
der Metallpulverteile gesiebt. Für die Herstellung der komplex geformten Bauteile
ist die Verwendung von Metallpulverteilen mit der Teilchengröße < 100µm geeignet.
Besonders günstige Ergebnisse werden erzielt, wenn man vorzugsweise eine Teilchengröße
< 45 µm verwendet. Der dabei entstehende Materialverlust bei der Metallpulvererzeugung
liegt bei einer Verwendung von Metallpulverteilen mit der Teilchengröße < 45 µm bei
etwa 70 bis 75% der hergestellten Metallpulverteile im Gegensatz zu den häufig 90%
Materialverlust bei der Herstellung der komplex geformten Bauteile mittels spanabhebender
Verfahren. Die gesiebten Metallpulverteile mit einer Teilchengröße > 45 µm lassen
sich für andere Zwecke verwenden, so daß sich der Materialverlust noch verringern
läßt. Bei dem eigentlichen Metallpulverspritzgußverfahren und -vorgang wird eine praktisch
hundertprozentige Materialausnutzung erreicht, da dann eventuell anfallende Feedstockreste
weiter verwendet werden können. Die Oberflächenrauhigkeit des fertiggestellten komplex
geformten Bauteils ist von der Pulvergröße abhängig und beträgt bei Verwendung von
Metallpulverteilen mit einer Teilchengröße < 45 µm typischerweise 1 µm. Dies bedeutet,
die Oberfläche des fertiggestellten komplex geformten Bauteils ist grundsätzlich ohne
Nachbeabeitung zu verwenden.
[0022] Aus der Figur 1a) ist beispielhaft die Titanlegierung in Stabform 1 dargestellt,
die mittels Inertgasverdüsung zu Metallpulverteilen 2 verarbeitet wird, wobei bereits
geschildert wurde, daß dies nur eine Möglichkeit der Herstellung der Metallpulverteile
darstellt. In Figur 1b) folgt die Feedstockherstellung, d.h. das Mischen der Metallpulverteile
2 mit dem Binder 3 in einem Kneter 4 zu dem Feedstock 5. Danach folgt gemäß Figur
1c) das Metallformspritzen des Feedstocks mittels einer hier nur schematisch in Blockdarstellung
angedeuteten Spritzgußmaschine 6, der der Feedstock 5 zugeführt wird und unter Druck
in die Spritzform 7 in die Form des Bauteils 8 eingespritzt wird. Der so entstandene
Grünling des Bauteils 8 wird in der Entbinderung in der Figur 1d) in einem Entbinderungsbad
9 teilentbindet und danach gemäß Figur 1e) in der Kammer 10 des Sinterofens gesintert,
bis das fertige Bauteil 8 entstanden ist, was aus den bereits geschilderten Gründen
der Vereinfachung als Zugstab ausgebildet ist, der gleichzeitig für die später noch
dargestellten Zugversuche verwendet wird. Wie der Übersichtsdarstellung in Figur 1
zu entnehmen ist, folgt nach der Herstellung der Metallpulverteile, die Vermischung
dieser Metallpulverteile mit einem Binder 3. Diese beiden Komponenten werden in einem
Kneter 4 vermischt und zu einem Feedstock verarbeitet. Der Feedstock ist also die
Mischung aus den Metallpulverteilen und den Binderbestandteilen, die in dem anschließen
Metallformspritzgußprozeß als Spritzmasse verwendet werden. Als Binderbestandteile
werden thermoplastische oder duroplastische Polymere, thermogelierende Substanzen,
Wachse oder oberflächenaktive Substanzen oder daraus erhaltene Mischungen zugegeben.
Als Binderbestandteile können dabei Polyamide, Polyoxymethylen, Polycarbonat, Styrol-Acrylnitril-Copolymerisat,
Polyimid, natürliche Wachse und Öle, Duroplaste, Cyanate, Polypropylene, Polyacetate,
Polyäthylene, Äthylen-Vinyl-Acetate, Polyvinyl-Alkohole, Polyvinyl-Chloride, Polystyrene,
Polymethyl-Methacrylate, Aniline, Wasser, Mineralöle, Agar, Glycerin, Polyvinyl-Butyryle,
Polybutyl-Methacrylate, Cellulose, Ölsäuren Phtalate, Paraffin-Wachse, Carnauba-Wachs,
Ammonium-Polyacrylate, Digylcerid-Stearate und -Oleate, Gylceryl-Monostearate, Isopropyl-titanate
Lithlum-Stearate, Monoglyceride, Formaldehyde, Octyl-Säure-Phosphate, Olefin-Sulfonate,
Phosphat-Ester oder Stearinsäure verwendet werden.
[0023] Das Mischen der beiden Komponenten des Feedstocks , also der Metallpulverteile 2
und der Binderbestandteile geschieht bei erhöhter Temperatur, so daß die Binderbestandteile
flüssig werden und die Pulverpartikel umhüllen können. In der Regel müssen auch Gleitmittel
zugefügt werden, um ein Verkleben der Binderbestandteile und der Metallpulverteile
zu verhindern. Es muß mit dem Kneter 4 für eine ausreichend homogene Vermischung gesorgt
werden, ohne daß sich die Bestandteile verklumpen. Durch geeignete Auswahl der Mischtemperatur
und der Bestandteile des Binders findet auch keine chemische Reaktion zwischen Binder
und dem Metallpulver während der Vermischung statt. Der Binder 3 muß auch in seinen
Bestandteilen so ausgewählt werden, daß während des Metallspritzgusses keine Zersetzung
des Binders stattfindet. Darüber hinaus muß der Binder auch sehr leicht aus dem mittels
Metallpulverspritzguß hergestellten Bauteils entfernt werden können, da er nur zum
vorübergehenden Zusammenhalt der Metallpulverbestandteile nach dem Metallformspritzen
dient. Der stets aus mehreren Bestandteilen bestehende Binder muß derart ausgeführt
sein, daß jeder Werkstoffeinzelbestandteil im Ausgangszustand an sich bereits die
Eigenschaft besitzt, arm an Verunreinigungsstoffen wie Sauerstoff, Stickstoff und
Kohlenstoff zu sein. Ganz wesentlich für die Herstellung eines komplex geformten Bauteils
ist auch bezüglich des Binders und seiner Bestandteile, daß diese dazu beitragen,
die geforderten Materialeigenschaften des Bauteils bis zur Fertigstellung des Bauteils
zu erhalten und nicht durch zusätzliche Aufnahme von Verunreinigungsstoffen zu verändern.
Aus diesem Grunde ist der Kneter und/oder die Knetkammer vorzugsweise mit hochreinem
Schutzgas wie beispielsweise Argon gefüllt, um eine Kontamination der beiden Komponenten
des Feedstocks beispielsweise mit Sauerstoff und Stickstoff aus der Luft zu verhindern.
Infolge des Zugebens von äußeren Gleitmitteln bildet der Binder eine Hülle um jedes
einzelne Metallpulverteil. Bei der Erzeugung des Feedstocks müssen Schervorgänge sicherstellen,
daß jedes Metallpulverteil mit Binder bedeckt ist. Dies geschieht meistens in sogenannten
Z-Schaufelmischern oder auch in Planetenmischern. Der Feedstock weist meist einen
Anteil von etwa 30 bis 40 Vol.% Binder auf.
[0024] Das Mischen der Metallpulverteile der Titanlegierung und der Bestandteile des Binders
bei der Feedstockherstellung wird in einem niedrigen Temperaturbereich durchgeführt.
Der Temperaturbereich bei der Feedstockherstellung liegt dabei zwischen 50 Grad und
200 Grad Celsius. Die Bestandteile des Binders sind mit einer unterschiedlichen Schmelz-,
Zersetzungs- und/oder Verdampfungstemperatur versehen. Es überwiegen dabei diejenigen
Binderbestandteile, die einen niedrigen Schmelz-, Zersetzungs- und/oder Verdampfungstemperatur
haben gegenüber denjenigem Anteil an Binderbestandteilen des Gemisches, die eine höhere
unterschiedliche Schmelz-, Zersetzungs- und/oder Verdampfungstemperatur aufweisen.
Ein an Verunreinigungsstoffen armer Binder, dessen Werkstoffeinzelbestandteile im
Ausgangszustand an sich bereits die Eigenschaft besitzen, arm an Verunreinigungsstoffen
zu sein, besteht aus Polyäthylen, Stearinsäure, Paraffin- und Carnauba-Wachs.
[0025] Es schließt sich gemäß Figur 1c) das Metallformspritzen des Bauteils 8 in einer Spritzgußmaschine
6 in der Spritzform 7 an. Für das Metallformspritzen werden in der Regel die in der
Kunststoffindustrie üblichen Spritzgußmaschinen eingesetzt. Der Feedstock wird in
der Regel pelletiert und als Pellet bei Bedarf in die Spritzgußmaschine eingeführt.
Die genauen Parameter beim Metallformspritzen wie Druck und Temperatur hängen von
der Geometrie des komplex geformten Bauteils und den Fließeigenschaften des Feedstocks
ab. Der Druck bewegt sich in dem Bereich von 30 bis 50 bar. Das Metallformspritzen
weist die Vorteile auf, eine kostengünstige und ausgezeichnete Reproduzierbarkeit
der komplex geformten Bauteile bei geringen Toleranzen zu ermöglichen und ist besonders
für mittlere bis hohe Stückzahlen geeignet. Diese Vorteile sind insbesondere auf die
außerordentlich lange Lebensdauer der Metallspritzgußform zurückzuführen, die nahezu
keiner Abnützung unterliegt, so daß eine Veränderung der Bauteilgeometrie mit der
Zeit- und Benutzungsdauer nicht zu erwarten ist. Die Spritzform wird konventionell
hergestellt. Da diese Herstellung aber nur einmal erforderlich ist, kann der dazu
nötige Arbeitsaufwand hoch sein ohne sich wesentlich auf einen mittleren bis hohen
Stückzahlpreis auszuwirken. Eine automatische Herstellung großer Stückzahlen von Bauteilen
mit derartigen Maschinen ist ohne irgendein Problem leicht durchzuführen. Es lassen
sich auch komplexe Formen, wie beipielsweise Gewinde, Bohrungen und dergleichen nur
mit einem einzigen Spritzvorgang herstellen.
[0026] Das Metallformspritzen des komplex geformten Bauteils zur Herstellung des Grünlings
erfolgt in einem niedrigen Temperaturbereich. Dieser Temperaturbereich liegt beim
Metallformspritzen zwischen 60 Grad und 200 Grad Celsius. Dieser niedrige Temperaturbereich
ermöglicht es, bei der Auswahl der Binderbestandteile zu verhindern, daß die Oberfläche
des gespritzten Grünlings in der Spritzgußmaschine mit der Fläche der Spritzform 7
reagiert, weshalb die Oberfläche glatt ist und nach der Fertigstellung des Bauteils
nicht nochmals bearbeitet werden muß. Dies gilt auch, wie bereits geschildert, für
den in einem ähnlichen niedrigen Temperaturbereich liegenden Herstellungsprozeß bei
der Feedstockherstellung, der sich zwischen 50 Grad und 200 Grad Celsius bewegt. Auch
hier kann es zu keiner Reaktion der Oberfläche des Kneters mit dem enstehenden Feedstock
kommen und deshalb kommt es auch nicht zu Störungen in der Fertigung. An das Metallformspritzen
schließt sich die Entbinderung des Bauteils 8 an, siehe dazu Figur 1d). Es wird zunächst
eine Teilentbinderung vorgenommen, z.B. durch thermisches Austreiben oder in einem
kommerziellen Entbinderbad, das beispielsweise mit Hexan unter Luftausschuß bei leicht
erhöhter Temperatur in der Größenordnung von 40 Grad Celsius für einige Stunden durchgeführt
wird. Dabei werden große Anteile des Bindergehalts bei leicht erhöhter Temperatur
mit Hilfe des Lösungsmittels entfernt. Dieses Aufheizen muß sehr vorsichtig geschehen,
um Verzug und Zerstörung am komplex geformten Bauteil zu vermeiden. Deshalb ist auch
der Binder aus verschiedenen Komponenten zusammengesetzt, die bei unterschiedlichen
Temperaturen verdampfen. Es werden bei der Teilentbinderung unter Einfluß des Lösungsmittels
Hexan etwa 75% des Binders aus dem Grünling herausgelöst, der dann als teilentbindertes
Bauteil Bräunling genannt wird. Das Lösungsmittel Hexan sorgt dafür, daß die Entbinderung
unter völligem Ausschluß von Luft, ferner von Verunreinigungsstoffen wie Kohlenstoff,
Sauerstoff, Stickstoff stattfindet und so eine Anreicherung von Verunreinigungsstoffen
in dem gespritzten Bauteil verhindert. Eine weitere Entfernung des Restbinders, der
sich erst bei höherer Temperatur entfernen läßt und bisher das Auseinanderhalten des
Bauteils verhinderte, erfolgt durch thermische Zersetzung. Vorzugsweise erfolgt die
thermische Zersetzung im Hochvakuum, sie kann jedoch auch in einer reinen Schutzgasatmosphäre
wie beispielsweise Argon stattfinden. Nach der Extraktion findet ein Trocknen in Argongas
statt. Die Handhabung der gespritzten Bauteile in Form eines Grünlings und der teilentbinderten
Bauteile in Form eines Bräunlings muß vorsichtig erfolgen, um einen Verzug oder einen
Bruch zu vermeiden. Der Grad und die Homogenität der Entbinderung sind entscheidend
für die weitere Geometrietreue, den erfolgreichen Verlauf der Sinterung und einer
geringen Kontamination des Bauteils mit Restbinderbestandteilen. Zur Durchführung
einer Teilentbinderung des komplex geformten Bauteils werden also zunächst diejenigen
Binderbestandteile mit niedriger Schmelz-, Zersetzungs- und/oder Verdampfungstemperatur
bei leicht erhöhter Temperatur entfernt.
[0027] Als nächster Schritt zur Fertigstellung der komplex geformten Bauteile erfolgt die
Sinterung, wie aus Figur 1e) ersichtlich ist. Bei dem Sintern erfährt der Bräunling
des Bauteils eine Wärmebehandlung, in der die einzelnen Metallpulverteile metallurgische
Kontakte in Form einer Schweißdiffusion miteinander erhalten. Ein erfolgreicher Sinterprozeß
bei Titanlegierungen und die Erzielung einer einwandfreien Materialeigenschaft des
Bauteils ist nur durch die Vermeidung der Aufnahme zusätzlicher Verunreinigungsstoffe
wie Sauerstoff, Kohlenstoff und Stickstoff während des Sinterprozesses in das Metallpulver
zu erreichen. Deshalb muß die Atmosphäre der Kammer des Sinterofens mit einem ausgezeichneten
Vakuum in der Größenordnung < 10
-5 mbar besitzen, wobei die hohen Temperaturen beim Sintern ungünstig für die Erhaltung
guter Materialeigenschaften sind, da bei diesen hohen Temperaturen eine besonders
gute Aufnahme von Verunreinigungen in den Metallpulverteilen stattfindet. Der Temperaturintervall
beim Sintern liegt zwischen 1100 Grad und 1400 Grad Celsius. Versuche bei der Herstellung
haben gezeigt, daß vorzugsweise die Temperatur von 1300 Grad Celsius ein optimales
Ergebnis bezüglich der Eigenschaften des gefertigten Bauteils erbringt. Weiter ist
es erforderlich, Verunreinigungen durch in dem Bräunling noch enthaltende Binderrückstände
zu vermeiden, was dadurch geschieht, daß eine der Verdampfungsrate des in dem Bräunling
des Bauteils noch enthaltenen Restbinders angepaßte Aufheizrate wie z.B. 5 K/min gewählt
wird, wodurch während des Aufheizvorganges in der Sinterkammer der Restbinder thermisch
ausgetrieben wird. Das nach dem Sintern fertiggestellte komplex geformte Bauteil weist
eine Dichte nahe der theoretischen Dichte auf, nämlich bei 96%. Die mechanischen Eigenschaften
des fertiggestellten Bauteils sind sehr ähnlich denen von geschmiedetem Material mit
vergleichbarer Zusammensetzung.
[0028] Eine wichtige Rolle zur einwandfreien Herstellung der komplex geformten Bauteile
hat während des Sintervorgangs die Sinterunterlage. Die Sinterunterlage für die komplex
geformten Bauteile ist deshalb derart ausgeführt, daß während der Durchführung des
Sinterns der Bauteile die freie Gleitfähigkeit der Oberfläche der Sinterunterlage
für die aufliegenden Bauteile unverändert erhalten bleibt. Der Werkstoff der Sinterunterlage
wird deshalb so gewählt, daß bei der Sintertemperatur die Oberfläche der Sinterunterlage
aus gegen das Material der Bauteile reduktionsbeständigem Werkstoff besteht, wie dies
beispielsweise bei Keramikoxyden der Fall ist. Darüber hinaus wird ein Werkstoff der
Sinterunterlage verwendet, der bei der Sintertemperatur keine Verunreinigungsstoffe
abgibt. Durch diese Auswahl der Werkstoffe der Sinterunterlage wird bei der Lagerung
der komplex geformten Bauteile auf der Sinterunterlage und bei dem während des Sinterns
auftretenden Schrumpfungsprozeß ein Verzug der Bauteile und ein eventueller Bruch
vermieden.
[0029] Nach dem Sintern kann durch eine anschließende heißisostatische Preßbehandlung erreicht
werden, daß die Restporosität des gesinterten Teils auf Null gebracht werden kann,
um damit alle theoretisch möglichen mechanischen Eigenschaften aus dem Werkstoff des
Bauteils herauszuholen. Deshalb werden die gesinterten Bauteile in eine mit hochreinem
Schutzgas wie beispielsweise Argon ausgestatte Kammer gegeben und bei einer Temperatur
von etwa 850 Grad Celsius und 2000 bar Gasdruck für einige Stunden heißisostatisch
gepreßt. Das hochreine Schutzgas Argon ist deshalb erforderlich, weil bei diesen hohen
Temperaturen die Neigung der Titanlegierung groß ist, Fremdstoffe aufzunehmen, was
jedoch verhindert werden muß. Aus dem gleichen Grund ist deshalb auch bei dem Material
der Auflagefläche für die Bauteile bei dem isostatischen Pressen darauf zu achten,
daß diese Auflage die freie Gleitfähigkeit durch Ausbildung aus geeignetem Material
wie beispielsweise Keramikoxyden während des Pressens beibehält und daß das Material
der Auflagefläche bei der Temperatur des isostatischen Pressens keine Verunreinigungsstoffe
in die Kammer und an die Bauteile abgibt. Der heißisostatische Preßprozeß wird nur
dann ausgeführt, wenn entweder das Material im Innern der Bauteile keine Porosität
aufweisen darf oder, wenn die höchstmöglichen Festigkeiten mit einer Dichte von 100%
und die bestmöglichen Duktilitäten für die jeweilige Anwendung erforderlich sind und
deshalb die dafür entstehenden zusätzlichen Kosten in Kauf genommen werden.
[0030] Die bisherige Beschreibung der Herstellung des komplex geformten Bauteils gemäß der
Erfindung und die nachstehend noch beschriebenen und in der Tabelle unten zusammengefaßten
Werte und Auswertungen von Versuchen an einem als Zugstab ausgebildeten Bauteil zeigen,
daß es mit dem erfindungsgemäßen Verfahren möglich ist nicht nur die hohe Festigkeit
des Titans als Bestandteil der Titanlegierung für die Extremanforderungen bei den
Anwendungen in der Medizintechnik, z.B. als Implantat, in der Kraftfahrzeug- und Luftfahrtechnik
und bei Off-shore-Anwendungen von dem Ausgangszustand des Materials für das Bauteil
und seinen Eigenschaften in diesem Ausgangszustand bis zur Fertigstellung des mit
Metallpulverteilen im Sinterverfahren hergestellten komplex geformten Bauteils zu
erhalten, sondern auch gleichzeitig, was ganz wesentlich ist, die der Ursprungstitanlegierung
Ti-6Al-7Nb bereits eigene hohe Duktilität bis zum Erhalt des fertig hergestellten
komplex geformten Bauteils mittels Sintern zu erhalten. Die Titanlegierung Ti-6Al-7Nb
wurde auch bisher schon anderweitig verwendet, konnte jedoch nicht sinnvoll bei einem
Metallpulverspritzgußverfahren verwendet werden, ohne daß die Eigenschaft der Dehnbarkeit
durch die Aufnahme von Verunreinigungsstoffen während des Herstellungsprozesses wieder
verloren ging, so daß dem gewonnenen Endprodukt die Sicherheitsreserve des gesinterten
Bauteils bezüglich der Funktionsfähigkeit und gegen irreparable Schäden bei einer
Überbelastung des Bauteils und gegen Bruch bei dem Stand der Technik fehlte. Das nach
dem Stand der Technik mit Titan hergestellte Bauteil kann zwar hohe Festigkeit aufweisen,
verhält sich aber bei der Dehnbarkeit nicht wie ein Metall, es ist elastisch nicht
aber plastisch verformbar. Nur durch die erfindungswesentliche Kombination der Merkmale
der Auswahl der Titanlegierung Ti-6Al-7Nb zusammen mit den weiter hier aufgezählten
Merkmalen des Bestehens einer hochreinen Schutzatmosphäre beim Herstellen des Metallpulvers,
bei der Feedstockherstellung, der Entbinderung und der Sinterung mit Hilfe von Schutzgas
und/oder Luftausschluß und/oder Vakuum zusammen mit der Auswahl von Metalllpulverteilen
und Binder, die an Verunreinigungsstoffen arm ausgebildet sind, den Herstellverfahren
an Verunreinung armen Metallpulverteilen der Titanlegierung durch das Electrode Induction
Melting Gasatomization- oder das Plasma Melting Induction Guiding Gasatomization-Verfahren,
der Anwendung eines niedrigen Temperaturbereiches beim Herstellen der Mischung des
Feedstocks und beim Metallformspritzen und ferner der Beschaffenheit der Sinterunterlage
mit der freien Gleitfähigkeit ihrer Oberfläche und der Erzeugung der Metallpulverteile
für die Titanlegierung durch eine mit Argon betriebene Verdüsungsanlage mit der nachgeschalteten
Vorrichtung zum Weitertransport der Metallpulverteile in einer Schutzatmosphäre. Nur
durch die Kombination dieser Merkmale läßt sich die beispielsweise in Figur 2 dargestellte
Duktilität des Zugstabes bis zum Abschluß der Fertigung nach dem Sintern erhalten.
In Figur 2a) ist der Zugstab 8 nach der Fertigstellung zu sehen. In Figur 2b) ist
eine Dehnung mit dem Zugstab 8 durchgeführt worden bis er auseinanderbrach. Aus der
Figur 2b ist deutlich ersichtlich, daß sich der durch Sintern hergestellte Zugstab
wie normales Metall verhalten hat, indem er sich vor dem Auseinanderbrechen plastisch
verformt hat, d.h. länger geworden ist bevor er auseinander- brach. Die Fähigkeit,
neben der Elastizität auch eine Plastizität aufzuweisen, schafft die für die Anwendung
erforderliche Sicherheitsreserve beim Einbau von komplex geformten Bauteilen, die
nach dem erfindungsgemäßen Verfahren hergestellt sind.
[0031] Aus Figur 3 sind die Meßergebnisse von mechanischen Versuchen bei der Herstellung
von Zugproben des Zugstabes 8 ersichtlich. Bei der Herstellung der Zugproben wurden
die Sintertemperatur von 1250 Grad Celsius und 1300 Grad Celsius und die Oberflächenbehandlung
geschliffen oder nicht geschliffen variiert. Bei einigen Proben des Zugstabes wurde
zusätzlich noch ein heißisostatischer Prozeß angeschlossen, um eine hundertprozentige
Dichte zu erreichen, bei der anderen Proben lag die Dicht bei etwa 96%. In Figur 3
sind Zugproben von Zugstäben zusammengefaßt, die folgende unterschiedliche Behandlung
erfuhren:
- Sintertemperatur 1250° C, keine weiteren Behandlungen
- Sintertemperatur 1300° C, ebenfalls keinerlei zusätzliche Behandlungen
- Sintertemperatur 1300° C, anschließende heißisostatische Preßbehandlung unter Argon,
850° C/2000 bar, keine weitere Oberflächenbehandlung
- Sintertemperatur 1250 °C, heißisostatischer Preßprozeß, Oberfläche geschliffen
- Sintertemperatur 1300 °C, heißisostatischer Preßprozeß, Oberfläche geschliffen
- Sintertemperatur 1250 °C, heißisostatischer Preßprozeß, anschließende Wärmebehandlung
bei 900° C /1h/in Wasser abgeschreckt + 540° C / 8h/ unter Schutzgas gekühlt. Diese
Temperung entspricht der üblichen Aushärtebehandlung einer Ti-AI-V-Legierung.
In der Tabelle der Figur 3 sind die Ergebnisse für die Streckgrenze R
p,
0,2, die Zugfestigkeit R
m, die Dehnung A, Sauerstoffgehalt und Dichte, geordnet nach Behandlungsvariation aufgeführt.
Die Zugversuche zeigten eine Steigerung der Festigkeit bei steigender Sintertemperatur
und Dichte. Die bei 1300 Grad Celsius gesinterten und anschließend einem heißisostatischen
Preßprozeß unterzogenen Proben zeigten Festigkeitswerte bei Raumtemperatur vergleichbar
zu denen der geschmiedeten oder gewalzten Legierung (Streckgrenze ca. 1000 Mpa, Zugfestigkeit
ca. 1060 Mpa, Dehnung ca. 17%).
[0032] Der Sauerstoffgehalt liegt bei ca. 0,25 Gew.%, der Kohlenstoffgehalt bei etwa 0,06
%. Die Ausgangslegierung, die für die Metallpulvererzeugung verwendet wurde, wies
bereits einen Sauerstoffgehalt von 0,2% bzw. einen Kohlenstoffgehalt von 0,01 % auf.
Der jeweilige Zuwachs ist durch die Handhabung und vor allem durch den Sinterprozeß
bedingt.
[0033] Die Gefügeuntersuchungen zeigten ein homogenes, feinlamellares Gefüge aus α- und
β-Phase mit einer mittleren Korngröße von etwa 150 µm. Die Poren haben eine Größe
von maximal 10 µm, im Fall der einem heißisostatischen Preßprozeß unterzogenen Proben
sind keine Poren vorhanden. Zusätzlich sind zum Vergleich Proben mit der Geometrie
des Zugstabes, der nach dem erfindungsgemäßen Verfahren hergestellt wurde, spanabhebend
aus geschmiedeten Material gefertigt worden. Dieses Material diente ebenfalls als
Ausgangslegierung für die Metallpulverherstellung. Bei der Oberflächenbehandlung handelt
es sich nicht um eine Politur, sondern nur um einen Schliff, der eventuelle Oberflächenkerben
beseitigen sollte. Da das Material duktil ist, sollte der Einfluß der Oberflächenqualität
bei den Versuchen keine allzu große Rolle spielen. Auf eine Elektropolitur wurde deshalb
verzichtet.
[0034] Das Gefüge im Fall des geschmiedeten Materials ist feinkörnig globular, während das
nach der Erfindung hergestellte Material des Zugstabes eine feinlamellare Struktur
aufweist. Der Kohlenstoffgehalt liegt jeweils bei ca. 0,06 Gew.%, die Zunahme gegenüber
der Ausgangslegierung beträgt etwa 0,05 Gew..%. Der Sauerstoffgehalt nimmt maximal
um 0,06 Gew..% zu, dabei wies die Ausgangslegierung bereits 0,19 Gew.% auf. Die Ergebnisse
der Zugversuche an dem Zugstab 8 lassen sich wie folgt interpretieren. Alle Proben
zeigen eine hervorragende Festigkeit. Bis auf den Fall der wärmebehandelten Probe
ist die gemessene Dehnung bei den nach der Erfindung hergestellten Proben des Zugstabes
deutlich höher als in der geschmiedeten Ausführung. Die bei 1300 Grad Celsius gesinterten
Proben zeigen im Durchschnitt etwas bessere Resultate als die bei 1250 Grad Celsius
gesinterten Zugstäbe. Eine Ausführung des heißisostatischen Preßprozesses an den Proben
verbessert die Festigkeit nocheinmal über 100 MPa. Die Festigkeitswerte, der einem
heißisostatischen Preßprozeß unterzogenen Proben des Zugstabes sind vergleichbar mit
denen des geschmiedeten Ausgangsmaterials in Form eines Zugstabes. Die Aushärtungsbehandlung
führt zwar zu deutlich höherer Festigkeit, gleichzeitig aber nur zu einer sehr kleinen
Dehnung. Zusammengefaßt heißt das, daß die nach dem erfindungsgemäßen Verfahren angefertigten
Proben des Zugstabes bei geeigneter Auswahl der vorgenommenen Verfahrensmerkmale eine
mit den Schmiedeteilen vergleichbare Festigkeit bei gleichzeitig höherer Duktilität
aufweisen.
Bezugszeichenliste
[0035]
- 1
- Titanlegierung in Stabform
- 2
- Metallpulverteile
- 3
- Binder
- 4
- Kneter
- 5
- Feedstock
- 6
- Spritzgußmaschine
- 7
- Spritzform
- 8
- Bauteil
- 9
- Entbinderbad
- 10
- Kammer des Sinterofens
Proben |
Rp 0,2 [MPa] |
Rm [MPa] |
A [%] |
Sauerstoff gehalt (Gew.%] |
Dichte [in % der theoretischen Dichte] |
geschmiedetes Material |
981 |
1034 |
5.0 |
0,19 |
100 |
|
1250°C Sintertemperatur |
796 |
897 |
12.8 |
0,25 |
96.0 |
|
1300°C Sintertemperatur |
846 |
917 |
14.4 |
0,25 |
96,0 |
|
1300°C, HIP |
1016 |
1059 |
17.8 |
0,25 |
100 |
|
1250°C, HIP, geschliffen |
963 |
1061 |
17.2 |
0,25 |
100 |
|
1300°C, HIP, geschliffen |
934 |
1019 |
20.5 |
0,25 |
100 |
|
1250°C, HIP, Wärmebeh., geschl. |
1050 |
1115 |
1.0 |
0,25 |
100 |
|
1. Verfahren zur Herstellung von Bauteilen durch Metallpulverspritzguß von mit Binder
überzogenen Metallpulverteilen in einer Spritzform, wobei anschließend eine Entbinderung
und Sinterung der erzeugten Bauteile erfolgt, bei dem die Metallpulverteile einer
Titanlegierung zur Herstellung der komplex geformten Bauteile dienen, wobei jeder
der folgenden Abschnitte der Herstellung der Bauteile von der Erzeugung der Metallpulverteile
für die Titanlegierung, der Feedstockherstellung mit einem Binder, der Entbinderung,
und dem Sintern ausschließlich unter Bestehen einer hochreinen Schutzzatmosphäre aus
Schutzgas und/oder Luftausschluß und/oder Vakuum stattfindet, und wobei die Metallpulverteile
und der Binder arm an Verunreinigungsstoffen ausgebildet sind,
dadurch gekennzeichnet dass
eine Nachverdichtung der komplex geformten Bauteile durch heißisostatisches Pressen
der gesinterten Bauteile in einer mit Schutzgas gefüllten Kammer durchgeführt wird,
dass die Auflagefläche für die Bauteile während des heißisostatischen Pressens eine
freie Gleitfähigkeit durch Ausbildung aus geeignetem Material beibehält,und dass das
Material der Auflagefläche bei der Temperatur des isostatischen Pressens keine Verunreinigungsstoffe
abgibt.
2. Verfahren nach Anspruch 1, dadurch gekennzeichnet, däß die Werkstoffeinzelbestandteile der Titanlegierung und des Binders in ihrer Zusammensetzung
derart ausgewählt werden, daß jeder Werkstoff Einzelbestandteil im Ausgangszustand
an sich bereits die Eigenschaft besitzt, arm an Verunreinigungsstoffen zu sein.
3. Verfahren nach einem oder mehreren der Ansprüche 1 bis 2, dadurch gekennzeichnet, daß den Metallpulverteilen als Binderbestandteile thermoplastische oder duroplastische
Polymere, thermogelierende Substanzen, Wachse oder oberflächenaktive Substanzen oder
daraus erhaltene Mischungen zugegeben werden.
4. Verfahren nach einem oder mehreren der Ansprüche 1 bis 3, dadurch gekennzeichnet, daß für den Binder Polyamide, Polyoxymethylen, Polycarbonat, Styrol-Acrylnitril-Copolymerisat,
Polyimid, natürliche Wachse und Öle, Duroplaste, Cyanate, Polypropylene, Polyacetate,
Polyäthylene, Äthylen-Vinyl-Acetate, Polyvinyl-Alkohoie, Polyvinyl-Chloride, Polystyrene,
Polymethyl-Methacrylate, Aniline, Wasser, Mineralöle, Agar, Glycerin, Polyvinyl-Butyryle,
Polybutyl-Methacrylate, Cellulose, Ölsäuren Phtalate, Paraffin-Wachse, Carnauba-Wachs,
Ammonium-Polyacrylate, Digylcerid-Stearate und - Oleate, Gylceryl-Monostearate, Isopropyl-titanate,
Lithium-Stearate, Monoglyceride, Formaldehyde, Octyl-Säure-Phospate, Olefin-Sulfonate,
Phospat-Ester oder Stearinsäure verwendet werden.
5. Verfahren nach einem oder mehreren der Ansprüche 1 bis 4 dadurch gekennzeichnet, daß zur Durchführung einer Teilentbinderung der komplex geformten Bauteile diejenigen
Binderbestandteile mit niedriger Schmelz-, Zersetzungs- und/oder Verdampfungstemperatur
einen überwiegenden Anteil an dem gesamten Gemisch der Binderbestandteile gegenüber
denjenigen Binderbestandteilen des Gemisches haben, die eine höhere Schmelz-, Zersetzungs-
und/oder Verdampfungstemperatur aufweisen.
6. Verfahren nach einem oder mehreren der Ansprüche 1 bis 5 dadurch gekennzeichnet, daß der Binder aus Polyäthylene, Stearinsäure, Paraffin und Carnauba-Wachs zusammengesetzt
ist.
7. Verfahren nach einem oder mehreren der Ansprüche 1 bis 6 dadurch gekennzeichnet, daß die an Verunreinigungsstoffen armen Metal/pulverteile der Titanlegierung durch das
Electrode-Induction Melting Gasatomization-Verfahren erzeugt werden.
8. Verfahren nach einem oder mehreren der Ansprüche 1 bis 7 dadurch gekennzeichnet, daß die an Verunreinigungsstoffen armen Metallpulverteile durch das Plasma Melting Induction
Guiding Gasatomization-Verfahren erzeugt werden.
9. Verfahren nach einem oder mehreren der Ansprüche 1 bis 8 dadurch gekennzeichnet, daß die Erzeugung der Metallpulverteile für die Titanlegierung durch eine Verdüsungsanlage
mit Inertgaszerstäubung erfolgt.
10. Verfahren nach einem oder mehreren der Ansprüche 1 bis 9, dadurch gekennzeichnet, daß die inertgasverdüsten Metallpulverteile in einer gasdicht an der Verdüsungsanlage
angeflanschten Pulverkanne aufgefangen werden, daß dabei die Pulverkanne selbst gasdicht
verschließbar ausgeführt ist und daß die Pulverkanne in ein Handschuhboxensystem eingeschleust
wird, das mit Argongas betrieben ist.
11. Verfahren nach einem oder mehreren der Ansprüche 1 bis 10 dadurch gekennzeichnet, daß die Teilchengröße der Metallpulverteile der Titanlegierung in dem Bereich kleiner
als 100 µm ausgeführt ist.
12. Verfahren nach einem oder mehreren der Ansprüche 1 bis 11 dadurch gekennzeichnet, daß die Teilchengröße der Metallpufverteile der Titanlegierung vorzugsweise kleiner als
45 µm ausgeführt ist.
13. Verfahren nach einem oder mehreren der Ansprüche 1 bis 10 dadurch gekennzeichnet, daß das Metallformspritzen der Bauteile mit Spritzgußmaschinen ausgeführt wird.
14. Verfahren nach einem oder mehreren der Ansprüche 1 bis 10 dadurch gekennzeichnet, daß das Mischer der Metallpulverteile der Titanlegierung und des Binders bei der Feedstockherstellung
und das Metallformspritzen des Bauteils jeweils in einem niedrigen Temperaturbereich
durchgeführt wird.
15. Verfahren nach einem oder mehreren der Ansprüche 1 bis 10, 14 dadurch gekennzeichnet, daß der Temperaturbereich bei der Feedstockherstellung sich zwischen 50 Grad und 200
Grad Celsius bewegt.
16. Verfahren nach einem oder mehreren der Ansprüche 1 bis 10, 13, 14 dadurch gekennzeichnet, daß der Temperaturbereich beim Metallformspritzen zwischen 60 Grad und 200 Grad Celsius
liegt.
17. Verfahren nach einem oder mehreren der Ansprüche 1 bis 16, dadurch gekennzeichnet, daß die Titantegierung aus Ti-6Al-7Nb besteht.
18. Verfahren nach einem oder mehreren der Ansprüche 1 bis 17, dadurch gekennzeichnet, daß die Sinterunterlage für die Bauteile derart ausgeführt ist, daß während der Durchführung
des Sinterns der Bauteile die freie Gleitfähigkeit der Oberfläche der Sinterunterlage
für die aufliegenden Bauteile unverändert erhalten bleibt.
19. Verfahren nach einem oder mehreren der Ansprüche 1 bis 18 dadurch gekennzeichnet, daß der Werkstoff der Sinterunterlage bei der Sintertemperatur keine Verunreinigungsstoffe
abgibt.
20. Verfahren nach einem oder mehreren der Ansprüche 1 bis 19 dadurch gekennzeichnet, daß bei der Sintertempatur die Oberfläche der Sinterunterlage aus gegen das Material
der Bauteile reduktionsbeständigem Werkstoff, wie z.B. Keramikoxyden besteht.
21. Verfahren nach einem oder mehreren der Ansprüche 1 bis 20 dadurch gekennzeichnet, daß die kompiex geformten Bauteile der Sinterung in einem Temperarurintervall von 1100
Grad Celsius bis 1400 Grad Celsius unterzogen werden.
22. Verfahren nach einem oder mehreren der Ansprüche 1 bis 21 dadurch gekennzeichnet, daß die komplex geformten Bauteile vorzugsweise bei einer Temperatur von 1300 Grad Celsius
gesintert werden.
1. Method for the manufacture of components by metal powder die casting from metal powder
parts coated with binder in a die, followed by a binder removal and sintering of the
components produced, where the metal powder parts of a titanium alloy are used for
the manufacture of the complexly shaped components, each of the following sections
in the manufacture of the components of producing the metal powder parts for the titanium
alloy, feedstock production with a binder, binder removal and sintering take place
exclusively under a high-purity inert atmosphere of inert gas and/or air exclusion
and/or vacuum and the metal powder parts and binder have a law impurity level, characterized in that a subsequent compaction of the complexly shaped components takes place by hot isostatic
pressing of the sintered, components in an inert gas-filled chamber, that the bearing
surface for the components during hot isostatic pressing maintains a free sliding
capacity by construction from a suitable material and that the material of the bearing
snrface at the isostatic pressing temperatures does not give off imparities.
2. Method according to claim 1, characterized in that the individual material constituents of the titanium alloy and the binder have a
composition such that each individual material constituent in the starting state already
has the characteristic of a low impurity level.
3. Method according to one or more of the claims 1 to 2, characterized in that to the metal powder parts are added as binder constituents thermoplastic or duroplastic
polymers, thermogelling substances, waxes or surfactants or mixtures obtained therefrom.
4. Method according to one or more of the claims 1 to 3, characterised in that for the binder are used polyamides, polyoxymethylene, polycarbonate, styrene-acrylonitrile
copolymer, polyimide, natural waxes and oils, duroplastics, cyanates, polypropylenes,
polyacetates, polyethylenes, ethylene-vinyl acetates, polyvinyl alcohols, polyvinyl
chlorides, polystyrenes, polymethyl methacrylates, aniline, water, mineral oils, agar,
glycerol, polyvinyl butyryls, polybutyl methacrylates, cellulose, oleic scuds, phthalates,
paraffin waxes, carnauba wax, ammonium polyacrylates, diglyceride stearates and oleates,
glycerol monostearates, isopropyl titanates, lithium stearates, monoglycerides, formaldehyde,
octanoic acid phosphates, olefin sulphonates, phosphate esters or stearic acid.
5. Method according to one or more of the claims 1 to 4, characterized in that for carrying out a partial binder removal with respect to the complexly shaped components
those binder constituents with a low melting, decomposing and/or evaporation temperature
preponderate in the total binder constituent mixture compared with those mixture binder
constituents with a higher melting, decomposing and/or evaporation temperature.
6. Method according to one or more of the claims 1 to 5, characterized in that a binder is composed of polyethylenes, stearic acid, paraffin, and carnauba wax.
7. Method according to one or more of the claims 1 to 6, characterized in that the low imparity metal powder parts of the titanium alloy are produced by the electrode
induction metal gas atomization process.
8. Method according to one or more of the claims 1 to 7, characterized in that the low impurity metal powder parts are produced by the plasma melting induction
guiding gas atomization process.
9. Method according to one or more of the claims 1 to 8, characterized, in that the metal powder parts for the titanium alloy are produced by an atomizing apparatus
with inert gas atomization.
10. Method according to one or more of the claims 1 to 9, characterized in that the inert gas-atomized metal powder parts are corrected in a gastight powder can
flanged to the atomizing apparatus, the powder can being itself constructed in a gas-tight
sealable form and that the powder can is introduced into a glovebox system operated
with argon gas.
11. Method according to one or more of the claims 1 to 10, characterized in that the particle size of the metal powder parts of the titanium alloy is in the range
smaller than 100 µm.
12. Method according to one or more of the claims 1 to 11, characterized in that the particle size of the metal powder parts of the titanium alloy is preferably smaller
than 45 µm.
13. Method according to one or more of the claims 1 to 10, characterized in that the die casting of the components takes place with die casting machines.
14. Method according to one or more of the claims 1 to 10, characterized in that the mixing of the metal powder parts of the titanium alloy and the binder during
feedstock production and metal die casting of the component in each case take place
in a low temperature range.
15. Method according to one or more of the claims 1 to 10 and 4, characterized in that the temperature range during feedstock production is between 50 and 200°C.
16. Method according to one or more of the claims 1 to 10, 13 and 14, characterized in that the temperature range during metal die casting is between 60 and 200°C.
17. Method according to one or more of the claims 1 to 16, characterised in that the titanium alloy is Ti-6Al-7Nb.
18. Method according to one or more of the claims 1 to 17, characterized in that the sintering substrate for the components is constructed in such a way that during
the sintering of the components the free sliding capacity of the surface of the sintering
substrate for the components resting thereon remains unchanged.
19. Method according to one or more of the claim 1 to 18, characterized in that the sintering substrate material gives off no impurities at the sintering temperature.
20. Method according to one or more of the claims 1 to 19, characterized in that at the sintering temperature, the sintering substrate surface is made from a material,
such as e.g. ceramic oxides redaction-resistant to the material of the components.
21. Method according to one or more of the claims 1 to 20, characterized in that the complexly shaped components undergo sintering in a temperature range 1100 to
1400°C.
22. Method according to one or more of the claims 1 to 21, characterized in that the complexly shaped components are preferably sintered at a temperature of 1300°C.
1. Procédé pour la fabrication de pièces par moulage par injection de particules de poudres
métalliques enrobées de liant, dans un moule à injection, les pièces fabriquées étant
soumises ensuite à une élimination du liant et à un frittage, procédé dans le cadre
duquel les particules de poudres métalliques servent d'alliage au titane pour la fabrication
des pièces de forme complexe, chacune des étapes suivantes de la fabrication des pièces,
de la production des particules de poudres métalliques pour l'alliage au titane, de
la fabrication de la matière première avec un liant, de l'élimination du liant et
du frittage ayant lieu, exclusivement, dans une atmosphère de protection de grande
pureté consistant en gaz protecteur et / ou en l'absence d'air et /ou sous vide, et
les particules de poudres métalliques et le liant présentant une faible teneur en
impuretés, caractérisé en ce qu'une densification ultérieure des pièces de forme complexe, par compression isostatique
à chaud des pièces frittées, est exécutée dans une chambre remplie de gaz protecteur,
que la surface d'appui des pièces conserve, pendant la compression isostatique, une
libre aptitude au glissement en raison d'une exécution en matière appropriée, et que
la matière de la surface d'appui, à la température de compression, ne dégage pas d'impuretés.
2. Procédé selon la revendication 1, caractérisé en ce que les différents éléments constitutifs de la matière première de l'alliage au titane
et du liant sont sélectionnés, quant à leur composition, de sorte que chacun des composants
de la matière première, à l'état initial, possède déjà, en soi, la propriété d'une
faible teneur en impuretés.
3. Procédé selon l'une ou plusieurs des revendication 1 à 2, caractérisé en ce que des polymères thermoplastiques ou thermodurcissables, des substances thermogélifiantes,
des cires ou des substances tensioactives ou des mélanges de celles-ci, sont ajoutés
aux particules de poudres métalliques, en tant que composants du liant.
4. Procédé selon l'une ou plusieurs des revendications 1 à 3, caractérisé en ce que, pour le liant, on utilise des polyamides, des polyoxyméthylènes, des polycarbonates,
des copolymères de styrène-acrylonitrile, des polyimides, des cires et des huiles
naturelles, des résines thermodurcissables, des cyanates, des polypropylènes, des
polyacétates, des polyéthylènes, des acétates d'éthyle et de vinyle, des alcools de
polyvinyle, des chlorures de polyvinyle, des polystyrènes, des polyméthacrylates de
méthyle, des anilines, de l'eau, des huiles minérales, de l'agar, de la glycérine,
des polybutyryles de vinyle, des polyméthacrylates de butyle, de la cellulose, des
acides oléiques, des phtalates, des cires de paraffine, de la cire de carnauba, des
polyacrylates d'ammonium, des stéarates et des oléates de diglycéride, des monostéarates
de glycéryle, des titanates d'isopropyle, des stéarates de lithium, des monoglycérides,
des aldéhydes formiques, des phosphates d'acide octylique, des sulfonates d'oléfines,
des esters phosphatiques ou de l'acide stéarique.
5. Procédé selon l'une ou plusieurs des revendications 1 à 4, caractérisé en ce que, pour l'élimination partielle du liant des pièces de forme complexe, les composants
du liant ayant une température de fusion, de décomposition et / ou d'évaporation inférieure
présentent une part prédominante du mélange des composants du liant, par rapport aux
composants du mélange dont la température de fusion, de décomposition et / ou d'évaporation
est plus élevée.
6. Procédé selon l'une ou plusieurs des revendications 1 à 5, caractérisé en ce que le liant est composé de polyéthylènes, d'acide stéarique, de paraffine et de cire
de carnauba
7. Procédé selon l'une ou plusieurs des revendications 1 à 6, caractérisé en ce que les particules de poudres métalliques de l'alliage au titane présentant une faible
teneur en impuretés sont fabriquées selon le procédés d'atomisation de gaz par fusion
par induction d'électrode.
8. Procédé selon l'une ou plusieurs des revendications 1 à 7, caractérisé en ce que les particules de poudres métalliques à faible teneur en impuretés sont fabriquées
selon le procédé d'atomisation de gaz par fusion au plasma et guidage par induction
9. Procédé selon l'une ou plusieurs des revendications 1 à 8, caractérisé en ce que la fabrication des particules de poudres métalliques pour l'alliage au titane est
effectuée à l'aide d'une installation d'atomisation avec désintégration par gaz inertes.
10. Procédé selon l'une ou plusieurs des revendications 1 à 9, caractérisé en ce que les particules de poudres métalliques atomisées par gaz inerte sont collectées dans
un récipient à poudre étanche aux gaz, qui est monté sur l'installation d'atomisation,
en ce que, ce faisant, ledit récipient à poudre est lui-même conçu façon à pouvoir être fermé
de manière étanche aux gaz, et que ledit récipient à poudre est amené dans un système
de boîte à gants qui est exploité à l'argon.
11. Procédé selon l'une ou plusieurs des revendications 1 à 10, caractérisé en ce que la granulométrie des particules de poudres métalliques de l'alliage au titane est
située dans la gamme inférieure à 100µ.
12. Procédé selon l'une ou plusieurs des revendications 1 à 11, caractérisé en ce que la granulométrie des particules de poudres métalliques de l'alliage au titane est
de préférence inférieure à 45µ.
13. Procédé selon l'une ou plusieurs des revendications 1 à 10, caractérisé en ce que le moulage par injection du métal est effectué avec des presses d'injection.
14. Procédé selon l'une ou plusieurs des revendications 1 à 10, caractérisé en ce que le mélange des particules de poudres métalliques de l'alliage au titane et du liant,
lors de la fabrication, et le moulage par injection de la pièce sont effectués, chacun,
dans un domaine de températures basses.
15. Procédé selon l'une ou plusieurs des revendications 1 à 10, 14, caractérisé en ce que le domaine de températures est situé entre 50 et 200 degrés Celsius, lors de la fabrication
de la matière première.
16. Procédé selon l'une ou plusieurs des revendications 1 à 10, 13, 14, caractérisé en ce que le domaine de températures est situé entre 60 et 200 degrés Celsius, lors du moulage
par injection.
17. Procédé selon l'une ou plusieurs des revendications 1 à 16, caractérisé en ce que l'alliage au titane consiste en Ti-6Al-7Nb.
18. Procédé selon l'une ou plusieurs des revendications 1 à 17, caractérisé en ce que le support de frittage pour les pièces est exécutée de telle sorte que, pendant l'exécution
du frittage des pièces, l'aptitude au glissement libre de la surface du support de
frittage, qui supporte les pièces, demeure inchangée.
19. Procédé selon l'une ou plusieurs des revendications 1 à 18, caractérisé en ce que la matière du support de frittage ne dégage pas d'impuretés à la température de frittage.
20. Procédé selon l'une ou plusieurs des revendications 1 à 19, caractérisé en ce que la surface du support de frittage, à la température de frittage, consiste en une
matière première résistant à une réduction par la matière des pièces, comme, par exemple,
des oxydes céramiques.
21. Procédé selon l'une ou plusieurs des revendications 1 à 20, caractérisé en ce que les pièces de forme complexe sont soumis au frittage dans un domaine de températures
de 1100 à 1400 degrés Celsius
22. Procédé selon l'une ou plusieurs des revendications 1 à 21, caractérisé en ce que les pièces de forme complexe sont frittées, de préférence à une température de 1300
degrés Celsius.
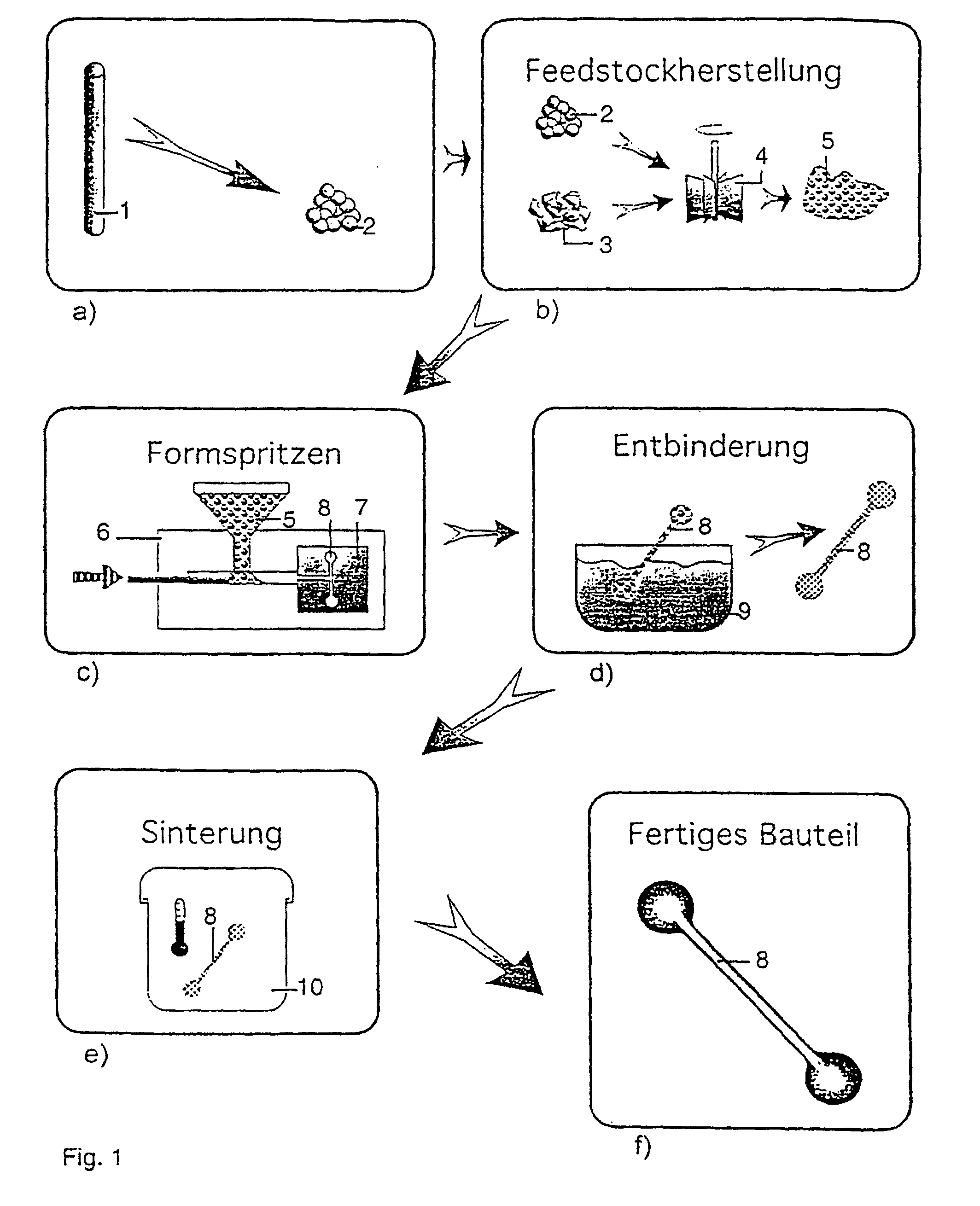
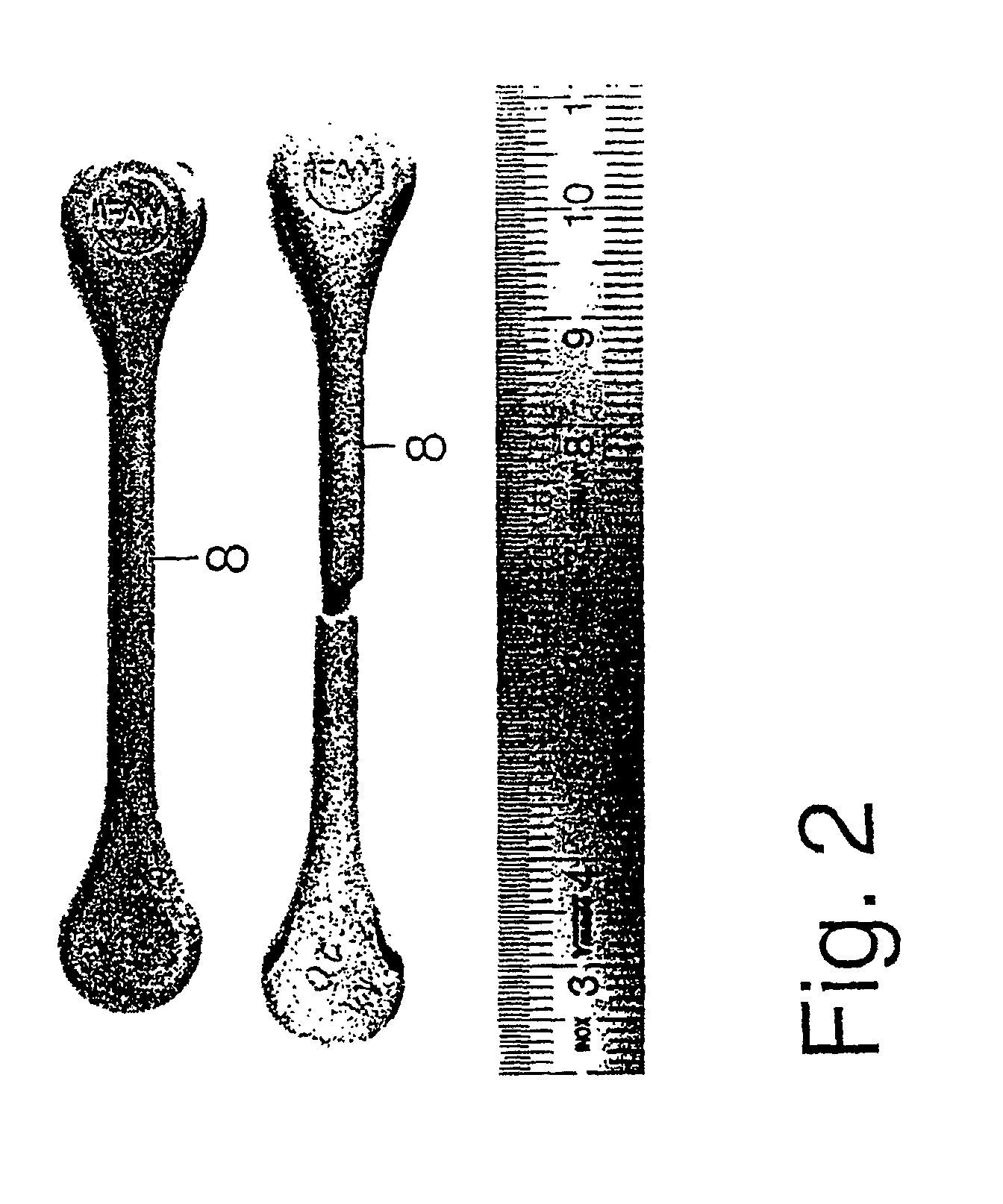