(19) |
 |
|
(11) |
EP 1 061 321 B1 |
(12) |
EUROPÄISCHE PATENTSCHRIFT |
(45) |
Hinweis auf die Patenterteilung: |
|
05.11.2003 Patentblatt 2003/45 |
(22) |
Anmeldetag: 25.03.2000 |
|
|
(54) |
Plattenreaktor
Plate reactor
Réacteur à plaques
|
(84) |
Benannte Vertragsstaaten: |
|
DE FR GB IT |
(30) |
Priorität: |
18.06.1999 DE 19927924
|
(43) |
Veröffentlichungstag der Anmeldung: |
|
20.12.2000 Patentblatt 2000/51 |
(73) |
Patentinhaber: Ballard Power Systems AG |
|
73230 Kirchheim / Teck-Nabern (DE) |
|
(72) |
Erfinder: |
|
- Haug, Lothar
73730 Esslingen (DE)
- Weisser, Marc
73277 Owen/Teck (DE)
|
(74) |
Vertreter: Beyer, Andreas, Dr. et al |
|
Wuesthoff & Wuesthoff,
Patent- und Rechtsanwälte,
Schweigerstrasse 2 81541 München 81541 München (DE) |
(56) |
Entgegenhaltungen: :
EP-A- 0 347 961 WO-A-86/05866
|
EP-A- 0 702 201 DE-A- 3 613 596
|
|
|
|
|
|
|
|
|
Anmerkung: Innerhalb von neun Monaten nach der Bekanntmachung des Hinweises auf die
Erteilung des europäischen Patents kann jedermann beim Europäischen Patentamt gegen
das erteilte europäischen Patent Einspruch einlegen. Der Einspruch ist schriftlich
einzureichen und zu begründen. Er gilt erst als eingelegt, wenn die Einspruchsgebühr
entrichtet worden ist. (Art. 99(1) Europäisches Patentübereinkommen). |
[0001] Die Erfindung betrifft einen Plattenreaktor gemäß dem Oberbegriff des Patentanspruchs
1 Ein derartiger Platten reaktor ist zum Beispiel aus der EP-A1-0 347 961 bekannt.
[0002] Aus der DE 36 13 596 A1 ist ein Plattenreaktor in Form eines Wärmetauschers bekannt,
der aus einem Stapel von Metallplatten besteht. In den Metallplatten sind Vertiefungen
zur Ausbildung von Strömungskanälen vorgesehen. In Stapelrichtung erstrecken sich
Verteiler- beziehungsweise Sammelkanäle durch den Plattenstapel. In diese Verteiler-
beziehungsweise Sammelkanäle sind die entsprechenden Zu- beziehungsweise Abführleitungen
gesteckt und durch einen Lötvorgang gasdicht verbunden.
[0003] Die EP 0 347 961 A1 offenbart einen Plattenwärmetauscher, der eine Mehrzahl von übereinander
gestapelten Wärmetauscherplatten sowie zwei den Plattenstapel begrenzende Endplatten
aufweist. Eine unmittelbar benachbart zu einer oberen Endplatte angeordnete Platte
des Plattenstapels weist in zwei einander gegenüberliegenden Ecken jeweils eine kreisförmige
Vertiefung mit einem ringförmigen Randabschnitt sowie einer von dem ringförmigen Randabschnitt
begrenzten Durchflussöffnung auf. In den anderen beiden einander gegenüberliegenden
Ecken der Platte sind jeweils kreisförmige Durchflussöffnungen ausgebildet. Die Endplatte
weist entlang zweier einander gegenüberliegender Seiten jeweils eine oval geformte
Ausbuchtung auf, in der zu den in der Platte ausgebildeten Durchflussöffnungen korrespondierende
Öffnungen ausgebildet sind, wobei die Durchmesser aller in der Platte ausgebildeten
Durchflussöffnungen und die Durchmesser aller in die Endplatte eingebrachten Öffnungen
identisch sind. Der Plattenwärmetauscher umfasst ferner erste und zweite Zu- beziehungsweise
Abführleitungen, die zwischen der Endplatte und der zu der Endplatte benachbarten
Platte des Plattenstapels festgelegt sind. Die Zu- beziehungsweise Abführleitungen
weisen jeweils einen zylindrischen Leitungsabschnitt sowie einen zweistufigen Sockelabschnitt
auf. Der zweistufige Sockelabschnitt der ersten Zu- beziehungsweise Abführleitungen
wird mit dem ringförmigen Randabschnitt der in der Platte ausgebildeten Vertiefung
verbunden, während der zweistufige Sockelabschnitt der zweiten Zu- beziehungsweise
Abführleitungen auf der flachen Oberfläche der Platte befestigt wird, so dass die
Sockelabschnitte der ersten und zweiten Zu- beziehungsweise Abführleitungen zwischen
der Platte und der in der Endplatte ausgebildeten Ausbuchtung festgelegt werden. Der
zylindrische Leitungsabschnitt erstreckt sich durch die in der Endplatte ausgebildeten
Öffnungen, wobei der Außendurchmesser des zylindrischen Leitungsabschnitts im Wesentlichen
dem Innendurchmesser der in den Endplatten ausgebildeten Öffnungen bzw. der in die
Platte eingebrachten Durchflussöffnungen entspricht.
[0004] Es ist die Aufgabe der Erfindung, einen kostengünstig herstellbaren Plattenreaktor
mit verbesserter Anschlussbefestigung zu schaffen.
[0005] Diese Aufgabe wird durch einen Plattenreaktor mit den Merkmalen des Patentanspruchs
1 gelöst.
[0006] Durch die Ausbildung der Endplatten aus mehreren dünnen Teilplatten kann eine kostengünstige
Herstellung erreicht werden. Vorzugsweise können die normalen Platten des Plattenreaktors
als Teilplatten für die Endplatten verwendet werden. Somit ist lediglich eine Art
von Platten notwendig und dennoch kann eine ausreichende mechanische Stabilität des
Plattenreaktors gewährleistet werden. Durch die Anordnung von mindestens einer Erhebung
am Außenumfang der Zu- beziehungsweise Abführleitung und zumindest einer entsprechenden
Vertiefung an zumindest einer der Teilplatten kann eine Verzahnung zwischen der Zu-
beziehungsweise Abführleitung und der Endplatte erreicht werden.
[0007] Dadurch erhöht sich zum einen die Fügefläche, wodurch beim anschließenden Lötvorgang
eine bessere Dichtigkeit gewährleistet werden kann. Zum anderen wird die Montage verbessert,
da durch die Verzahnung eine exakte Positionierung möglich ist.
[0008] Weiter Vorteile und Ausgestaltungen der Erfindung gehen aus den Unteransprüchen und
der Beschreibung hervor. Die Erfindung ist nachstehend anhand einer Zeichnung näher
beschrieben, die einen Schnitt durch einen Plattenreaktor im Bereich eines Anschlußrohres
zeigt.
[0009] Der insgesamt mit 1 bezeichnete, in der Zeichnung jedoch nur teilweise und im Schnitt
dargestellte Plattenreaktor besteht aus einem Stapel von Platten 2, der durch eine
insgesamt mit 3 bezeichnete Endplatte abgeschlossen wird. Die Endplatte 3 im gezeigten
Ausführungsbeispiel besteht aus vier Teilplatten 4. An die eine in der Zeichnung gezeigte
Platte 2 schließen sich beliebig viele weitere Platten an. Der Stapel wird auf der
der Endplatte 3 gegenüberliegenden Seite durch eine weitere, ebenfalls nicht dargestellte
Endplatte abgeschlossen. Hierbei kann es sich um eine herkömmliche Endplatte oder
eine ebenfalls aus mehreren Teilplatten aufgebaute Endplatte handeln. Die Zahl der
Teilplatten 3 ist sowohl bei der Endplatte 3 als auch bei der gegenüberliegenden Endplatte
frei wählbar.
[0010] Plattenreaktoren sind aus dem Stand der Technik allgemein bekannt und werden daher
hier nur noch kurz und soweit für das Verständnis der Erfindung notwendig beschrieben.
Unter Plattenreaktoren in dem hier gebrauchten Sinn werden Vorrichtungen zur Durchführung
von chemischen Reaktionen, Vorrichtungen zur Übertragung von thermischer Energie zwischen
verschiedenen Medien, aber auch Kombinationen davon verstanden: In den Platten 2 sind
in der Zeichnung nicht dargestellte Vertiefungen, Räume oder Kanäle zur Führung von
Medien vorgesehen. Im folgenden wird zur Vereinfachung nur noch von Kanälen gesprochen.
Es können sowohl identische Platten 2 als auch für die verwendete Medien unterschiedliche
Platten 2 verwendet werden. Die einzelnen Platten 2 können hierbei seriell und/oder
parallel von den Medien durchströmt werden. Außerdem können in den Kanälen geeignete
Katalysatormaterialien in beliebiger Form - zum Beispiel als Schüttung, Beschichtung
usw. - zur Unterstützung der chemischen Reaktion vorgesehen werden.
[0011] Zur Zu- beziehungsweise Abführung der Medien zu beziehungsweise aus den einzelnen
Kanälen in den Platten 2 sind Verteiler- beziehungsweise Sammelkanäle 5 vorgesehen.
Diese werden vorzugsweise durch Bohrungen in den einzelnen Platten 2 beziehungsweise
in der Endplatte 3 gebildet, welche bei der Montage in Stapelrichtung deckungsgleich
übereinander zum Liegen kommen. In der Zeichnung ist lediglich ein solcher Verteilerkanal
5 gezeigt. Bei einem kompletten Plattenreaktor 1 können jedoch jeweils ein oder auch
mehrere Verteiler- beziehungsweise Sammelkanäle 5 vorgesehen werden.
[0012] In den Verteilerkanal 5 hinein ragt eine Zuführleitung 6, welche zur Zufuhr eines
Mediums gasdicht mit dem Verteilerkanal 5 verbunden ist. In dem gezeigten Ausführungsbeispiel
ist die Zuführleitung 6 als kreisrundes Rohr dargestellt, was auch eine bevorzugte
Ausführungsform darstellt. Es ist jedoch auch möglich, andere Querschnittsformen für
die Zuführleitung 6 zu wählen, wobei in diesem Fall anstelle der Bohrungen in den
Platten 2 beziehungsweise in der Endplatte 3 entsprechend geformte Durchbrechungen
vorgesehen sind. Die Zuführleitung 6 weist an ihrem Außenumfang 7 einen Ringbund 8
auf. Korrespondierend dazu weisen die beiden mittleren Teilplatten 4m eine vergrößerte
Bohrung auf, deren Durchmesser im wesentlichen dem Außendurchmesser des Ringbundes
8 entspricht. Darüber hinaus entspricht die axiale Breite b des Ringbundes 8 im wesentlichen
der Dicke d der beiden mittleren Teilplatten 4m. Die Teilplatten 4 weisen in dem bevorzugten
Ausführungsbeispiel alle gleiche Dicken auf, die auch der Dicke der Platten 2 entspricht.
Selbstverständlich ist es auch möglich, unterschiedlich dicke Teilplatten 4 zu verwenden,
wobei in diesem Falle die axiale Breite b des Ringbundes 8 der Dicke d derjenigen
Platten mit vergrößerter Bohrung entspricht.
[0013] Vorzugsweise entspricht der Durchmesser der Bohrungen in den Teilplatten 4 im wesentlichen
dem Außendurchmesser der Zuführleitung 6, während der Durchmesser der Bohrungen in
den Platten 2 im wesentlichen dem Innendurchmesser der Zuführleitung 6 entspricht.
Dies hat zur Folge, daß nach der Montage die Medienführung in der Zuführleitung 6
als auch im Verteilerkanal 5 den gleichen Querschnitt aufweist. Die axiale Position
des Ringbundes 8 wird vorzugsweise so gewählt, daß das axiale Ende 9 der Zuführleitung
6 nach der Montage mit dem der Platte 2 zugewandten Rand der Endplatte 3 abschließt.
Dies bedeutet, daß der axiale Abstand des Ringbundes 8 von dem axialen Ende 9 der
Zuführleitung 6 im wesentlichen gleich der Dicke der innersten Teilplatte 4i ist.
Dadurch wird verhindert, daß die Zuführleitung 6 die Versorgung der Kanäle in der
Platte 2 beeinflußt oder gar behindert.
[0014] Bei der Herstellung des Plattenreaktors 1 werden die Platten 2 aufeinander gestapelt
und anschließend die innerste Teilplatte 4i oben auf diesen Stapel gelegt. Anschließend
wird die Zuführleitung 6 in den Verteilerkanal 5 gesteckt, wobei der Ringbund 8 auf
der Oberfläche der innersten Teilplatte 4i aufliegt. Anschließend werden die beiden
mittleren Teilplatten 4m über die Zuführleitung 6 gestülpt. Durch die übereinstimmende
Dimensionierung der beiden mittleren Teilplatten 4m und des Ringbundes 8 bilden die
Oberfläche der nun obersten Teilplatte 4m und des oberen Randes des Ringbundes 8 eine
im wesentlichen ebene Fläche. Daraufhin wird dann die äußerste Teilplatte 4a ebenfalls
über die Zuführleitung 6 gestülpt. Schließlich wird auf die äußerste Teilplatte 4a
am Außenumfang der Zuführleitung 6 Lotmaterial gegeben, welches beim anschließenden
Lötvorgang in die Fügestellen zwischen der Zuführleitung 6 mit Ringbund 8 und den
Bohrungen der Teilplatten 4 gezogen wird und bilden eine gasdichte Verbindung. Zusätzlich
kann auch noch Lotmaterial zwischen den Teilplatten 4 oder direkt an den Fügestellen
zwischen Zuführleitung 6 mit Ringbund 8 und den Bohrungen der Teilplatten 4 vorgesehen
werden.
[0015] Durch die Anordnung des Ringbundes 8 werden im wesentlichen zwei Vorteile erreicht.
Zum einen wird die Fügefläche zwischen Zuführleitung 6 mit Ringbund 8 und den Bohrungen
der Teilplatten 4 erhöht, so daß sowohl die mechanische Stabilität als auch die Dichtigkeit
verbessert wird. Zum anderen wird die Zuführleitung 6 sowohl in axialer als auch in
radialer Richtungen fixiert, so daß bei der Herstellung kein Fehler bei der Positionierung
auftreten kann. Für den Fall, daß die Zubeziehungsweise Abführleitung 6 nicht rotationssymmetrisch
ist und es daher auf die Drehrichtung ankommt, kann anstelle des normalen durchgehenden
Ringbundes 8 der Außenumfang der Zubeziehungsweise Abführleitung 6 auch nur teilweise
mit einem Bund versehen werden, wobei dann in den Teilplatten 4 wiederum eine korrespondierende
Durchbrechung eingebracht werden muß. Prinzipiell ist hier jede Form einer Erhebung
und der zugehörigen Durchbrechung möglich, wobei jedoch auf eine möglichst einfache
Herstellung zu achten ist. Anstelle des dargestellten Ringbundes 8 kann beispielsweise
an der Zuführleitung 6 ein kleiner Einstich vorgesehen werden, in den dann anschließend
ein Draht- oder Sprengring eingelegt wird. Als weiteres Ausführungsbeispiels ist es
auch möglich, anstelle des Ringbundes 8 die Zuführleitung 6 nach außen aufzuweiten,
wodurch wiederum eine Erhebung entsteht.
[0016] Obwohl in der Zeichung lediglich eine Zuführleitung 6 mit zugehörigem Verteilerkanal
5 dagestellt und beschrieben ist, soll der Patentschutz nicht darauf beschränkt werden.
Die Erfindung betrifft allgemein einen Plattenreaktor, bei dem zumindest eine der
Zu- und/oder Abführleitungen 6 mit der beschriebenen Befestigung versehen ist, unabhängig
davon, ob noch weitere Zu- und/oder Abführleitungen 6 mit herkömmlicher Befestigung
vorgesehen sind.
1. Plattenreaktor (1) mit einem von Endplatten (3) begrenzten Stapel von Platten (12)
zur Ausbildung von Reaktions- und/oder Wärmetauscherräumen, mit sich im Wesentlichen
in Stapelrichtung durch die Endplatten (3) beziehungsweise Platten (12) erstreckenden
und durch Durchbrechungen gebildeten Verteiler- und/oder Sammelkanälen (5) und mit
einer Zu- beziehungsweise Abführleitung (6), die mit einem Verteiler- beziehungsweise
Sammelkanal (5) in Strömungsverbindung steht, wobei die Zu- beziehungsweise Abführleitung
(6) teilweise in den Verteiler- beziehungsweise Sammelkanal (5) gesteckt wird, wobei
der Außendurchmesser der Zubeziehungsweise Abführleitung (6) im Wesentlichen dem Innendurchmesser
des Verteiler- beziehungsweise Sammelkanals (5) entspricht und die Zu- beziehungsweise
Abführleitung (6) gasdicht mit dem Verteiler- beziehungsweise Sammelkanal (5) verbunden
wird, und wobei die Zu- beziehungsweise Abführleitung (6) an ihrem Außenumfang zumindest
eine Erhebung (8) aufweist,
dadurch gekennzeichnet, dass die Endplatte (3) aus mehreren Teilplatten (4) gebildet ist, und dass zumindest eine
von der äußersten Teilplatte (4a) abweichende Teilplatte (4m) eine zu der zumindest
einen Erhebung (8) korrespondierende Durchbrechung aufweist, so dass die äußerste
Teilplatte (4a) und eine von dieses äußersten Teilplatte (4a) abweichende Teilplatte
(4m) Durchbrechungen mit unterschiedlichen Durchmessern aufweisen.
2. Plattenreaktor nach Anspruch 1,
dadurch gekennzeichnet,
daß die Zu- beziehungsweise Abführleitung (6) und der Verteiler- beziehungsweise Sammelkanal
(5) zylinderförmig ausgebildet sind und daß die Durchbrechung in der zumindest einen
zugehörigen Teilplatte (4m) durch eine Bohrung gebildet ist, deren Durchmesser im
wesentlichem dem Außendruchmesser der Erhebung (8) entspricht.
3. Plattenreaktor nach Anspruch 1,
dadurch gekennzeichnet,
daß die Breite (b) der Erhebung (8) in Richtung der Längsächse der Zu- beziehungsweise
Abführleitung (6) im wesentlichen der Dicke (d) einer oder mehrerer Teilplatten (4m)
entspricht.
4. Plattenreaktor nach Anspruch 1,
dadurch gekennzeichnet,
daß vier Teilplatten (4) vorgesehen sind, wobei die beiden mittleren Teilplatten (4m)
einen vergrößerten Durchmesser aufweisen, und wobei die Erhebung (8) derart an der
Zubeziehungsweise Abführleitung (6) angeordnet ist, daß im zusammengebauten Zustand
die Zu- beziehungsweise Abführleitung (6) sich lediglich bis in den Bereich der vierten
Teilplatte (4i) ersteckt.
5. Plattenreaktor nach Anspruch 1,
dadurch gekennzeichnet,
daß die zumindest eine Erhebung (8) ein Ringbund ist
6. Plattenreaktor nach Anspruch 1,
dadurch gekennzeichnet,
daß die zumindest eine Erhebung (8) ein Draht- oder Sprengring ist, der in einen zugehörigen
Einstich am Außenumfang der Zuführleitung (6) eingelegt ist.
7. Plattenreaktor nach Anspruch 1,
dadurch gekennzeichnet,
daß die zumindest eine Erhebung (8) durch Aufweiten der Zuführleitung (6) nach außen
gebildet wird.
1. Plate reactor (1), with a stack of plates (12), which is limited by end plates (3),
for the formation of reaction and/or heat exchanger spaces, with distributing and/or
collecting ducts (5) extending essentially in the stack direction through the end
plates (3) or the plates (12) and formed by perforations, and with a supply or discharge
line (6) which is flow-connected to a distributing or collecting duct (5), the supply
or discharge line (6) being partially plugged into the distributing or collecting
duct (5), the outside diameter of the supply or discharge line (6) corresponding essentially
to the inside diameter of the distributing or collecting duct (5), and the supply
or discharge line (6) being connected in a gas-tight manner to the distributing or
collecting duct (5), and the supply or discharge line (6) having at least one elevation
(8) on its outer circumference, characterized in that the end plate (3) is formed from a plurality of part-plates (4), and in that at least one part-plate (4m) differing from the outermost part-plate (4a) has a perforation
matching the at least one elevation (8), so that the outermost part-plate (4a) and
a part-plate (4m) differing from this outermost part-plate (4a) have perforations
with different diameters.
2. Plate reactor according to Claim 1, characterized in that the supply or discharge line (6) and the distributing or collecting duct (5) are
designed cylindrically, and in that the perforation in the at least one associated part-plate (4m) is formed by a bore,
the diameter of which corresponds essentially to the outside diameter of the elevation
(8).
3. Plate reactor according to Claim 1, characterized in that the width (b) of the elevation (8) in the direction of the longitudinal axis of the
supply or discharge line (6) corresponds essentially to the thickness (d) of one or
more part-plates (4m).
4. Plate reactor according to Claim 1, characterized in that four part-plates (4) are provided, the two middle part-plates (4m) having an enlarged
diameter, and the elevation (8) being arranged on the supply or discharge line (6)
in such a way that, in the assembled state, the supply or discharge line (6) extends
only into the region of the fourth part-plate (4i).
5. Plate reactor according to Claim 1, characterized in that the at least one elevation (8) is an annular collar.
6. Plate reactor according to Claim 1, characterized in that the at least one elevation (8) is a wire ring or spring ring which is inserted into
an associated recess on the outer circumference of the supply line (6).
7. Plate reactor according to Claim 1, characterized in that at least one elevation (8) is formed by means of the outward expansion of the supply
line (6).
1. Réacteur à plaques (1) avec un empilement de plaques (12) limité par des plaques d'extrémité
(3) pour la formation de zones d'échange thermique et/ou de réaction, comportant des
canaux de répartition et/ou de collecte (5) formés par des perforations et s'étendant
essentiellement dans l'alignement de l'empilement par les plaques d'extrémités (3)
ou les plaques (12), et avec une conduite d'amenée ou d'évacuation (6) reliée au flux
par un canal de répartition ou de collecte (5), la conduite d'amenée ou d'évacuation
(6) étant partiellement emboîtée dans le canal de répartition ou de collecte (5),
le diamètre extérieur de la conduite d'amenée ou d'évacuation (6) correspondant essentiellement
au diamètre intérieur du canal de répartition ou de collecte (5) et le raccordement
de la conduite d'amenée ou d'évacuation (6) au canal de répartition ou de collecte
(5) étant étanche au gaz et la conduite d'amenée ou d'évacuation (6) comportant à
son périmètre extérieur au moins une élévation (8),
caractérisé en ce que la plaque d'extrémité (3) est formée de plusieurs plaques partielles (4) et en ce qu'au moins une plaque partielle (4m) différente de la plaque partielle la plus extrême
(4a) comporte une perforation correspondant à au moins une élévation (8), de telle
façon que la plaque partielle la plus extrême (4a) et l'une de ces plaques partielles
(4m) différente de cette plaque partielle la plus extrême (4a) comportent des perforations
de diamètres différents.
2. Réacteur à plaques selon la revendication 1,
caractérisé en ce que la conduite d'amenée ou d'évacuation (6) et le canal de répartition ou de collecte
(5) sont de forme cylindrique et que la perforation dans au moins une plaque partielle
correspondante (4m) est formée par un perçage dont le diamètre correspond essentiellement
au diamètre extérieur de l'élévation (8).
3. Réacteur à plaques selon la revendication 1,
caractérisé en ce que la largeur (b) de l'élévation (8) dans la direction de l'axe longitudinal de la conduite
d'amenée ou d'évacuation (6) correspond essentiellement à l'épaisseur (d) d'une ou
plusieurs plaques partielles (4m).
4. Réacteur à plaques selon la revendication 1,
caractérisé en ce que quatre plaques partielles (4) sont prévues, les deux plaques partielles médianes
(4m) présentant un diamètre supérieur et l'élévation (8) étant agencée de telle façon
au niveau de la conduite d'amenée ou d'évacuation (6) qu'une fois montée, la conduite
d'amenée ou d'évacuation (6) s'étendant uniquement jusqu'à la zone de la quatrième
plaque partielle (4i).
5. Réacteur à plaques selon la revendication 1,
caractérisé en ce qu'au moins une des élévations (8) est un collet annulaire.
6. Réacteur à plaques selon la revendication 1,
caractérisé en ce qu'au moins une des élévations (8) est une bague de retenue ou une couronne de fil logée
dans une entaille correspondante sur le pourtour extérieur de la conduite d'amenée
(6).
7. Réacteur à plaques selon la revendication 1,
caractérisé en ce qu'au moins une des élévations (8) est formée par évasement vers l'extérieur de la conduite
d'amenée (6).
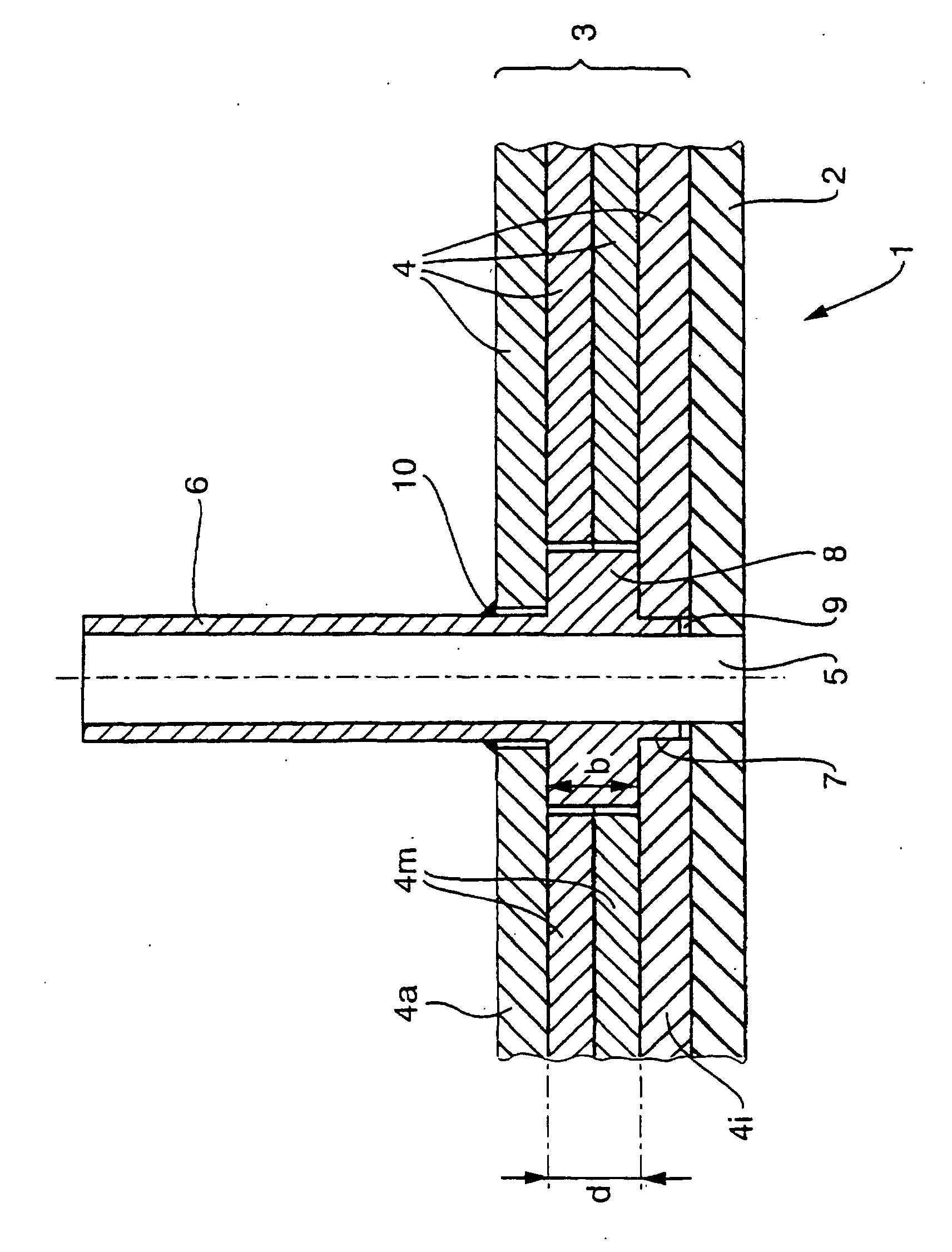