TECHNICAL FIELD
[0001] The present invention relates to a knitted fabric having a triple knit ply structure.
More particularly, the present invention relates to a knitted fabric having a the
triple knit ply structure constituted from a front surface knit ply, a back surface
knit ply and an intermediate knit ply arranged between the front and back surface
knit plies and formed from hollow filament stitching yarns through which the front
and back surface knit plies are tuck-stitched together. The knitted fabric having
a triple knit ply structure of the present invention is appropriately used for underwear
which a high lightness (light weight property) and must have a high warmth (warm-keeping
property).
TECHNICAL BACKGROUND
[0002] Generally, it is known that a knitted fabric having a triple knit ply structure constituted
by tuck-stitching front and back surface knit plies with stitching yarns, as disclosed
by, for example, Japanese Unexamined Patent Publication No. 6-158483-A, has excellent
bulkiness, warmth and a good appearance and thus is widely used for sport wear such
as, for example, training wear, and casual clothes for children and women. In the
case where the knitted fabric having a triple knit ply structure is used for underwear,
it must have a further enhanced warmth and lightness.
[0003] Conventional knitted fabrics for underwear, which are produced from knitting yarns
comprising natural fibers such as cotton fibers or a combination of natural fibers
and synthetic fibers (for example, polyester or nylon fibers) or regenerated fibers
(for example, rayon fibers) or semisynthetic fibers (for example, cellulose triacetate
fibers), are widely used. In the conventional knitted fabric for underwear as mentioned
above, in the case where a further enhancement of the warmth is required, the front
or back surface of the knitted fabric is nap-raised or, for knitting yarns, functional
fibers, containing a substance capable of absorbing far infrared rays and/or near
infrared rays and mixed into a fiber-forming polymer, or other functional fibers capable
of generating heat by absorbing moisture in the ambient air, are used, to realize
an enhancement of the warmth of the knitted fabric. However, when a nap-raising procedure
is applied, the thickness of the knitted fabric may significantly increase. Also,
when the above-mentioned functional fibers are utilized, a disadvantage that the enhancement
in the warm-keeping property of the knitted fabric is unsatisfactory, such that it
becomes necessary to increase the thickness of the knitted fabric and therefore the
mass of the resultant knitted fabric becomes too large, may occur.
SUMMARY OF THE INVENTION
[0004] An object of the present invention is to provide a knitted fabric having a triple
knit ply structure, exhibiting high lightness and warmth and useful for knitted clothes.
[0005] The above-mentioned object can be attained by the knitted fabric having a triple
knit ply structure of the present invention.
[0006] The knitted fabric having a triple knit ply structure of the present invention comprises
a front surface knit ply having a yarn knit structure, a back surface knit ply having
a yarn knit structure and a binding intermediate knit ply formed from stitching yarns
through which the yarn knit structure of the front surface knit ply and the yarn knit
structure of the back surface knit ply are tuck-stitched together,
the stitching yarns being constituted from hollow fibers.
[0007] In the knitted fabric having a triple knit ply structure of the present invention,
the stitching yarns are preferably polyester multifilament yarns having a thickness
of 20 to 170 dtex, and a thickness of individual filaments of 1 to 10 dtex, the individual
filaments preferably having a percentage of hollowness of 10 to 55%.
[0008] The knitted fabric having a triple knit ply structure of the present invention, preferably
has a thickness of 0.5 to 1.5 mm and a basis mass of 80 to 200 g/m
2.
[0009] In the knitted fabric having a triple knit ply structure of the present invention,
the binding intermediate knit ply preferably has a basis mass of 25 to 60 g/m
2.
[0010] The knitted fabric having a triple knit ply structure of the present invention preferably
has a heat-insulation efficiency (α) of 18% or more.
[0011] In the knitted fabric having a triple knit ply structure of the present invention,
the yarns from which the front surface knit ply is formed are preferably bulky polyester
multifilament yarns having a thickness of 20 to 17 dtex, and a thickness of individual
filaments of 0.1 to 20 dtex.
[0012] In the knitted fabric having a triple knit ply structure of the present invention,
the yarns from which the back surface knit ply is formed are preferably constituted
from at least one type of fibers selected from natural fibers, synthetic fibers, regenerated
fibers and semisynthetic fibers.
[0013] The knitted fabric having a triple knit ply structure of the present invention, preferably
has a tubular knit structure.
BRIEF DESCRIPTION OF THE DRAWINGS
[0014]
Fig. 1 shows an explanatory cross-sectional profile of an embodiment of the knitted
fabric having a triple knit ply structure,
Fig. 2 is a photographic of a cross-section of an embodiment of the knitted fabric
having a triple knit ply structure of the present invention,
Fig. 3 is a diagram showing a knit design of an embodiment of the knitted fabric having
a triple knit ply structure of the present invention, and
Fig. 4 shows an explanatory cross-sectional view of a dry-contact heating apparatus
for the measurement of the heat-insulation efficiency α of the knitted fabric having
a triple knit ply structure of the present invention.
BEST MODE OF CARRYING OUT THE INVENTION
[0015] The knitted fabric having a triple knit ply structure is constituted from front and
back surface knit plies formed from yarns knitted into knit ply structures and a binding
intermediate knit ply formed from stitching yarns through which the yarn knit structure
of the front surface knit ply and the yarn knit structure of the back surface knit
ply are tuck-stitched together, and the stitching yarn from which the binding intermediate
knit ply is formed are constituted from hollow fibers.
[0016] In the present invention, each of the hollow fibers comprises a peripheral shell
portion extending along the longitudinal axis of the hollow fiber and having an annular
cross-sectional profile and a hollow space surrounded by the peripheral shell and
extending along the longitudinal axis of the hollow fiber.
[0017] In the case where the knitted fabric having a triple knit ply structure is formed
into an underwear cloth, the resultant knitted underwear cloth having the triple knit
ply structure is used in the manner such that the back surface knit ply faces the
skin surface and the front surface knit ply is exposed to the ambient air atmosphere.
In this case, the back surface knit ply, in most cases, comes into contact with the
skin of the user, and thus must have a good warmth and a high absorption of perspiration
and moisture and must exhibit a good touch and hand; the front surface knit ply must
exhibit a good appearance, and an appropriate sliding property on a coat superimposed
on the underwear cloth; and the binding intermediate knit ply must have a firm tuck-stitching
property, a good form-retaining property resistance to compression, and a high warmth.
[0018] Referring to Fig. 1, the knitted fabric 1 having a triple knit ply structure is constituted
from
(a) a front surface knit ply 2 constituted from yarns 2a knitted into a knit structure,
(b) a back surface knit ply 3 constituted from yarns 3a knitted into a knit structure,
and
(c) a binding intermediate knit ply 4 constituted from stitching hollow fiber yarns
4a which are tuck-stitched with the yarns 2a and 3a from which the knit structures
of the front and back surface knit plies 2 and 3 are formed, to bind the front and
back surface knit plies together through the intermediate knit ply 4.
[0019] Fig. 2 shows a photograph of a cross-section of an embodiment of the knitted fabric
having a triple knit ply structure of the present invention. In Fig. 2, yarns 2a,
from which the knit structure of the front surface knit ply 2 is constituted and yarns
3a from which the knit structured the back surface knit ply 3 is constituted, are
tuck stitched by stitching yarns 4a of the binding intermediate knit ply 4. In Fig.
2, the stitching yarn 4a constituted from filaments. The filaments are hollow filaments
of which the hollow cross-sectional profiles clearly appears in Fig. 2.
[0020] Fig. 3 shows a knit design of an embodiment of the knitted fabric having a triple
knit ply structure of the present invention. Fig. 3, the knit designs (1) and (4)
are of a front surface knit ply, the knit designs (2) and (5) are of a back surface
knit ply, and the knit designs (3) and (6) are of a binding intermediate knit ply.
[0021] In the knitted fabric having a triple knit ply structure of the present invention,
there is no limitation to the type of the stitching yarns usable for the binding intermediate
knit ply. For example, the stitching yarns are preferably hollow multi-filament yarns.
In this case, preferably, the hollow multifilament yarns have a thickness of 20 to
170 dtex, more preferably 20 to 100 dtex; the individual filaments have a thickness
of 1 to 10 dtex, more preferably 2 to 5 dtex, and a percentage of hollowness of 10
to 50%, more preferably 30 to 55%. The percentage of hollowness of the hollow filaments
refers to a percentage of the cross-sectional area of hollow portion of an individual
hollow filament on the basis of the whole cross-sectional area of the individual hollow
filament. The stitching yarns may be spun yarns comprising hollow staple fibers (preferably
having a thickness of 1 to 10 dtex and a percentage of hollowness of 10 to 55%) and
preferably having a thickness of 20 to 170 dtex.
[0022] There is no specific limitation to the type of the hollow fibers for constituting
the stitching yarns. Usually, the hollow fibers are preferably selected from organic
fibers for clothes, for example, hollow polyester filaments, hollow nylon filaments,
hollow polyester staple fibers, hollow nylon staple fibers and composite fibers of
these polymers. Among them, hollow polyester filaments are preferably used for the
present invention.
[0023] In the knitted fabric having a triple knit ply structure of the present invention,
the binding intermediate knit ply preferably has a basis mass of 25 to 60 g/m
2, more preferably 30 to 50 g/m
2. When the basis mass is within the above-mentioned range, the resultant knitted fabric
having a triple knit ply structure of the present invention exhibits high warmth and
lightness.
[0024] The front surface knit ply of the knitted fabric having a triple knit ply structure
of the present invention is preferably formed from bulky yarns, for example, false
twist-textured yarns, spun yarns, air jet-interlaced filament yarns and yarns comprising
two or more types of fibers or filaments different in shrinkage from each other. In
this case, the resultant knitted fabric exhibit a high warmth. Also, to improve the
hand of the knitted fabric, and to prevent undesirable projections of stitching yarns
from the outermost surface of the front surface knit ply when the stitching yarns
tuck-stitch with the yarns from which the front surface knit ply is formed, to form
the binding intermediate knit ply, the yarns for forming the front surface knit ply
preferably have a thickness of 20 to 170 dtex, more preferably 50 to 150 dtex, and
the individual fibers for the yarns preferably have a thickness of 0.1 to 20 dtex,
more preferably 2 to 5 dtex. There is no limitation to the type of the fibers from
which the front surface knit ply is formed. For example, fibers of polyesters, nylons,
cellulose acetates, acrylic resins, rayon, cotton, wool and/or silk or composite fibers
thereof may be used for the front surface knit ply. Among them, the polyester fibers
are preferably employed. The fiber yarns as mentioned above are preferably selected
from false twist-textured multifilament yarns, more preferably false twist-textured
polyester multifilament yarns. The front surface knit ply preferably has a basis mass
of 20 to 60 g/m
2, more preferably 30 to 50 g/m
2.
[0025] In the knitted fabric having a triple knit ply structure of the present invention,
the yarns from which the knit structure of the back surface knit ply is formed preferably
comprises at least one type of fibers selected from natural fibers (for example, wool
and silk fibers), synthetic fibers (for example, polyester, nylon and acrylic fibers),
regenerated fibers (for example, rayon and cupra fibers), and semisynthetic fibers
(for example, cellulose triacetate fibers). In the case where the knitted fabric having
a triple knit ply structure of the present invention is used for clothes, the fiber
yarns for the back surface knit ply are preferably selected from those exhibiting
high comfort when the cloth is worn by a user, for example, cotton, rayon, polyester,
and nylon yarns and composite yarns of the above-mentioned yarns. The yarns for the
back surface knit ply may be selected from multifilament yarns and spun yarns. The
multifilament yarns may be texturized bulky multifilament yarns. The yarns for the
back surface knit ply preferably have a thickness of 40 to 300 dtex (130 to 20 yarn
number count), more preferably 70 to 200 dtex. The back surface knit ply preferably
has a basis mass of 30 to 100 g/m
2, more preferably 40 to 70 g/m
2.
[0026] There are no limitations to the thickness and the basis mass of the knitted fabric
having a triple knit ply structure of the present invention. Usually, to realize both
the high warmth and lightness, the knitted fabric having a triple knit ply structure
preferably has a thickness of 0.5 to 1.5 mm, more preferably 0.6 to 0.8 mm, and a
basis mass of 80 to 200 g/m
2, more preferably 110 to 150 g/m
2.
[0027] The knitted fabric having a triple knit ply structure of the present invention preferably
exhibits a heat-insulation efficiency of 18% or more, more preferably 20% or more,
determined by the following measurement.
[0028] In the measurement, referring to Fig. 4, a heating device 5 (large size BT-box, made
by KATOTEC K.K., model: THERMOLABO II) is placed in air controlled to a uniform temperature
of 20°C, in which device only a heating surface (dimensions: 10 cm × 10 cm) is exposed
to the atmosphere and other surface are heat-insulated, and the temperature of the
heating surface is maintained at a uniform temperature of 65°C. A sample of a knitted
fabric b having dimensions of 10 cm × 10 cm is placed on the heating surface. Then,
an electric power consumption W, in W needed to maintain the temperature of the heating
surface at 65°C for one minute is measured. For the purpose of comparison, an electric
power consumption W
0 needed to maintain the temperature of the heating surface, on which no knitted fabric
sample is placed, at 65°C for one minute is measured.
[0029] The heat-insulation efficiency α of the knitted fabric sample is calculated in accordance
with the following equation.

[0030] In the production of the knitted fabric having a triple knit ply structure of the
present invention, for example, a circular knitting machine is used, yarns for forming
the knit structure of the front surface knit ply and yarns for forming the knit structure
of the back surface knit ply are respectively supplied into the circular knitting
machine through a cylinder side and a dial side of the machine and knitted into, for
example, knit structures, as shown in Fig. 3 and, simultaneously, the knit structures
of the front and back surface knit plies are tuck-stitched with stitching yarns, to
form a binding intermediate knit ply.
EXAMPLES
[0031] The knitted fabric having a triple knit ply structure of the present invention will
be further illustrated by the following examples, which are not intended to limit
the scope of the present invention in any way.
Example 1
[0032] A 23G double circular knitting machine was employed to produce a knitted fabric having
a triple knit ply structure of the present invention.
[0033] The front surface knit ply was formed from false twist-textured polyethylene terephthalate
filament yarns having a yarn count of 56 dtex/36 filaments, and the back surface knit
ply was formed from spun cotton yarns having a thickness of 98 dtex (60 yarn number
count). The binding intermediate knit ply was formed from stitching yarns consisting
of hollow polyethylene terephthalate filament yarns having a percentage of hollow
of hollow filaments of 35% and a yarn count of 40 dtex/12 filaments. The knit structures
of the front and back surface knit piles are tuck-stitched by the stitching hollow
filament yarns. A knitted fabric having a triple knit ply structure as shown in Fig.
3 was obtained. Table 1 shows the thickness, basis mass and heat-insulation efficiency
α of the resultant knitted fabric.
[0034] The resultant knitted fabric exhibited lightness, an excellent warmth and a soft
surface touch. No projection or exposure of the stitching yarns of the binding intermediate
layer to the outside of the front surface knit ply were found. Thus the resultant
knitted fabric exhibited a good appearance and dignity.
Comparative Example 1
[0035] A knitted fabric having a triple knit ply structure as shown in Fig. 3 was produced
by using the same 23G double circular knitting machine as in Example 1, from false
twist-textured polyethylene terephthalate filament yarns having a yarn count of 56
dtex/36 filaments for the front surface knit ply, spun cotton yarns having a thickness
of 98 dtex (60 yarn number count) for the back surface knit ply and non-hollow polyethylene
terephthalate filament yarns, having a yarn count of 56 dtex/24 filaments as stitching
yarns for the binding intermediate knit ply. Table 1 shows the thickness, basis mass
and heat-insulation efficiency of the resultant knitted fabric.
[0036] The knitted fabric having a triple knit ply structure of Comparative example 1 had
similar appearance, elegance, thickness and basis mass to that of the Example 1, but
had an insufficient heat-insulation efficiency α.
Comparative Example 2
[0037] A knitted fabric having a circular rib knit structure was produced from spun cotton
yarns having a thickness of 147 dtex (40 yarn number count) by using a circular knitting
machine. Table 1 shows the thickness, basis mass and heat-insulation efficiency α
of the resultant knitted fabric.
[0038] The resultant knitted fabric exhibited a significantly poor heat insulation efficiency
α, while the thickness and the basis weight of the resultant knitted fabric were higher
than those of Example 1.
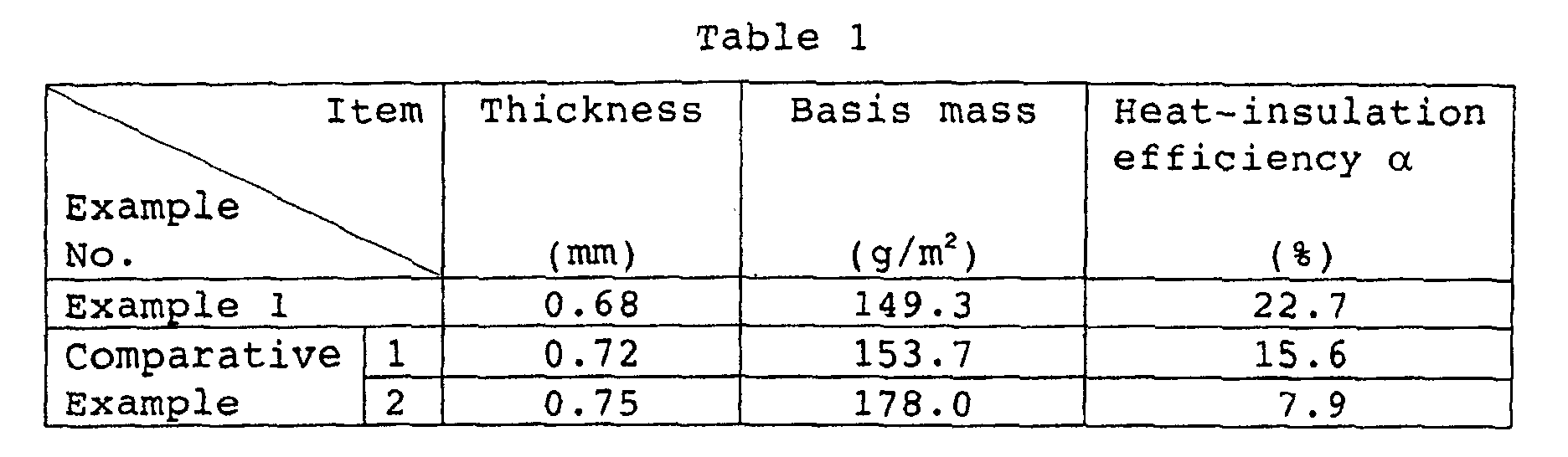
INDUSTRIAL APPLICABILITY OF THE INVENTION
[0039] The knitted fabric having a triple knit ply structure of the present invention exhibits
an excellent warmth in relation to the thickness and basis mass thereof, an excellent
lightness in relation to the thickness and the warmth thereof and thus is an appropriate
textile material for the use in underwear which need high lightness and warmth.
1. A knitted fabric having a triple knit ply structure, comprising a front surface knit
ply having a yarn knit structure, a back surface knit ply having a yarn knit structure
and a binding intermediate knit ply formed from stitching yarns through which the
yarn knit structure of the front surface knit ply and the yarn knit structure of the
back surface knit ply are tuck-stitched together,
the stitching yarns being constituted from hollow fibers.
2. The knitted fabric having a triple knit ply structure as claimed in claim 1, wherein
the stitching yarns are polyester multifilament yarns having a thickness of 20 to
170 dtex, and a thickness of individual filaments of 1 to 10 dtex, the individual
filaments having a percentage of hollowness of 10 to 55%.
3. The knitted fabric having a triple knit ply structure as claimed in claim 1, having
a thickness of 0.5 to 1.5 mm and a basis mass of 80 to 200 g/m2.
4. The knitted fabric having a triple knit ply structure as claimed in claim 1, wherein
the binding intermediate knit ply has a basis mass of 25 to 60 g/m2.
5. The knitted fabric having a triple knit ply structure as claimed in claim 1, having
a heat-insulation efficiency (α) of 18% or more.
6. The knitted fabric having a triple knit ply structure as claimed in claim 1, wherein
the yarns from which the front surface knit ply is formed are bulky polyester multifilament
yarns having a thickness of 20 to 17 dtex, and a thickness of individual filaments
of 0.1 to 20 dtex.
7. The knitted fabric having a triple knit ply structure as claimed in claim 1, wherein
the yarns from which the back surface knit ply is formed are constituted from at least
one type of fibers selected from natural fibers, synthetic fibers, a regenerated fibers
and semisynthetic fibers.
8. The knitted fabric having a triple knit ply structure as claimed in claim 1, having
a tubular knit structure.