BACKGROUND OF THE INVENTION
[0001] The present invention relates to a swing type excavator in which a front attachment
is swingable in the horizontal direction.
[0002] It is generally essential for small-sized hydraulic excavators to have a function
capable of digging a side ditch in a near position transversely of the excavator without
changing the body direction. This function is achieved by the swing type excavator.
[0003] As disclosed in JP-U-4-46149 and JP-U-5-47798, for example, the swing type excavator
is of a structure that a swing post being able to swing horizontally is disposed in
a front central portion of an upper structure forwardly of a cab, and a front attachment
is mounted to the swing post. A side ditch digging can be performed by turning the
upper structure and swinging the swing post so that the whole of the front attachment
is swung in the horizontal direction. It is usual that a boom of the swing type excavator
comprises a mono-boom bent at a certain angle for the purpose of deep digging.
[0004] Further, in conventional swing type excavator, as disclosed in JP-U-547798, a horizontal
pin (boom foot pin) as a coupling point between a boom and a swing post is positioned
forwardly of a swing pin as the swing center of the swing post toward a front attachment
(hereinafter referred to as first prior art).
[0005] Meanwhile, to enable digging work to be performed in a narrow space, there has recently
been developed an excavator which can realize the so-called undercarriage-width turn
that not only an upper structure is turned generally within the width of an undercarriage,
but also a front attachment, including a bucket, an arm and a boom, can be turned
together generally within the undercarriage width while assuming a posture where the
front attachment is folded above the upper structure (hereinafter referred to as a
turning posture). Such an excavator is called an ultra-small turn hydraulic shovel
or excavator. Since the ultra-small turn hydraulic excavator can take any directions
within a circle of which diameter is given by the undercarriage width, it can perform
desired work in any narrow place so long as the place has a width enough to allow
an excavator body to pass there. For example, when construction work is executed in
one lane of a two-lane road, the work can be performed while traffic is blocked not
in both lanes, but in only one lane, which results in a minimum extent of traffic
restriction.
[0006] Meanwhile, there is an offset type excavator as an excavator other than the swing
type which has a function capable of digging a side ditch in a near position transversely
of the excavator without changing the body direction.
[0007] As disclosed in JP-A-2-120427 and JP-A-2-213525, for example, the offset type excavator
is of a structure that a boom is divided into a lower boom and an upper boom, the
upper boom being horizontally tiltable with respect to the lower boom, and a parallel
link mechanism and a cylinder for driving the parallel link mechanism are disposed
between the lower boom and the upper boom. Upon operation of the cylinder, an arm
is translated with respect to the lower boom through an action of the parallel link
mechanism. When digging a side ditch, therefore, the ditch can be dug in a desired
position transversely of the excavator body within the undercarriage width with no
need of turning the upper structure.
[0008] As the ultra small turn hydraulic excavator, there has hitherto been practiced offest
type one (hereinafter referred to as second prior art). The reason is as follows.
A boom usually has the form bent at a certain angle. To realize an ultra-small turn
of the excavator having such a boom, one end of the boom is required to be supported
to a position near the longitudinal center of an upper structure. However, if the
excavator employs the swing type in combination with the construction that one end
of the boom is supported to a position near the longitudinal center of the upper structure,
the boom would interfere with a cab and a front attachment could not be swung to the
same side as the cab, when the front attachment is horizontally swung with respect
to the upper structure in an attempt at work of side ditch digging. Accordingly, the
offset type excavator in which the arm is horizontally tiltable with respect to the
boom must have been practiced to prevent an interference between the front attachment
and the cab.
[0009] Another ultra-small turn hydraulic excavator which has also been practiced employs,
based on the above offset type, a boom provided between an upper boom and a lower
boom with an additional mechanism which enables the upper boom to be also vertically
tiltable with respect to the lower boom, an opening angle between the two booms being
changed by action of a cross link (hereinafter referred to as third prior art).
[0010] JP-U-2-84857 discloses a swing type excavator in which a boom comprises a lower boom
vertically tiltable with respect to a swing post, and an upper boom vertically tiltable
with respect to the lower boom (hereinafter referred to as fourth prior art). In this
prior art, an opening angle between the two booms is changed by action of a cross
link depending on a tilt angle of the lower boom so that when the lower boom is maximally
tilted up (i.e., erected), the-upper boom is straightly extended in the direction
of extension of the lower boom, and when the lower boom is maximally tilted down (i.e.,
flattened), the upper boom is bent at a proper angle with respect to the lower boom.
A swing post is disposed in a front central portion of an upper structure.
SUMMARY OF THE INVENTION
[0011] However, the prior art excavators have problems as follows.
[0012] In the case where the coupling point between the boom and the swing post is positioned
forwardly of the swing center of the swing post twoard the front attachment like the
above-described first prior art, the position of the swing post on the upper structure
must be moved rearwardly with respect to the front attachment so that the whole of
the front attachment comes closer to the turn center of the upper structure, for achieving
a reduction in the minimum turn radius. This results in the following problems.
(1) If the swing post is positioned closer to the turn center of the upper structure
to reduce the minimum swing radius in the turning posture, the distance between the
swing center of the front attachment and the turn center of the upper structure is
shortened and, therefore, the front attachment is entirely moved toward the turn center
of the upper structure when a side ditch is dug by turning the upper structure and
swinging the whole of the front attachment in the opposite direction. Accordingly,
the side ditch distance from an outer lateral surface of the undercarriage to an outer
wall surface of the side ditch is reduced and the side ditch cannot be dug in a position
transversely spaced from the longitudinal center of the excavator body by a distance
comparable to that conventionally achieved.
(2) If the swing post is positioned closer to the turn center of the upper structure,
a maximum tilt-down angle of the boom is required to be smaller than conventionally
to avoid an interference between a blade provided to project forwardly from the excavator
body and the boom or the boom cylinder. This reduces the maximum digging depth.
[0013] Further, in the offset type excavator as the second prior art, because the complex
parallel link mechanism and the cylinder for driving it are required to be provided
on the front attachment, the weight of the front attachment is increased, which is
disadvantageous in the following points.
(1) The front attachment is so very heavy that the center of gravity is deviated toward
its distal end and the excavator has poor stability depending on a posture of the
front attachment.
(2) Corresponding to the increased weight of the front attachment, it is also required
to use a heavier counterweight. Therefore, the weight of the whole excavator becomes
comparable to that of one which has a digging capability in a level one class higher
than excavators being of not offset type but standard type. This pushes up a transportation
cost. Furthermore, the size of the upper structure is increased, which is an obstacle
in realizing an ultra-small turn.
(3) Since the weight of the excavator body is increased, an engine ouput must be enlarged.
Hence a manufacture cost and a running cost are pushed up.
In addition, the offset type excavator has problems below because the arm and the
bucket are offset parallel to the boom.
(4) A vertical pin is employed to couple the lower boom and the upper boom to each
other, and it may be curved or broken when extremely large impact forces or vibrations
are generated in the digging direction while crushing work is performed by using a
breaker or the like as the front attachment.
(5) When digging a side ditch deeply, there is a possibility that a lower portion
of the parallel link mechanism may interfere with the ground surface. Accordingly,
the offset type excavator cannot achieve a digging depth comparable to that obtainable
with standard type excavators.
(6) Because of using the complex parallel link mechanism, the manufacture cost is
increased and maintenance work is more frequently required.
(7) When the arm and the bucket are offset to the side opposite to the cab, the field
of view is obstructed by the boom, giving an operator difficulty in viewing the digging
position from the cab.
(8) When the arm and the bucket are offset to the same side as the cab, there is a
possibility that the bucket positioned in front of the cab may badly interfere with
the cab. To avoid such a possibility, means for preventing the interference must be
provided. However, an interference preventing device required for that purpose is
complicated in its entire structure, including sensor means for detecting tilt angles
of the lower boom and the arm making up the front attachment and an offset amount,
as well as arithmetic means. This results in a higher manufacture cost.
[0014] The third prior art accompanies similar problems to those described above because
of employing the same offset type as in the second prior art.
[0015] Meanwhile, in the swing type excavator, the foot end of the boom cannot be supported
to a position near the longitudinal center of the upper structure, and hence the excavator
cannot be constructed in such a manner as enabling the whole of the front attachment
to turn within the undercarriage width, as described before. Stated otherwise, in
the swing type excavator, the foot end of the boom is supported by the swing post
disposed substantially centrally in front of the cab, and a mono-boom vertically bent
at a certain angle is employed as the boom. Therefore, if the bent angle of the boom
is set so as to enable deep digging when the boom is maximally tilted down, a part
of the front attachment would project out of the undercarriage width upon the upper
structure being turned even in a posture where the boom is maximally tilted up. Additionally,
since the swing post is disposed substantially centrally in front of the cab, the
cab has to be shifted rearwardly on the narrow upper structure in order that the boom
has a large tilt angle when it is maximally tilted up. This implies a difficulty in
designing layout of the cab.
[0016] In the above-described fourth prior art, since the opening angle between the lower
boom and the upper boom is changed by action of the cross link depending on a tilt
angle of the lower boom, the upper boom is bent with respect to the lower boom so
as to enable deep digging when the lower boom is maximally tilted down, and the upper
boom is straightly extended with respect to the lower boom when the lower boom is
maximally tilted up, enabling the bucket to be raised to a higher level. However,
because the swing post is disposed in the front central portion of the upper structure
as with general swing type excavators, the lower boom would hit against the cab if
the lower boom is attempted to tilt rearwardly beyond its vertical posture. Hence
the maximum tilt-up angle of the lower boom cannot be set to a large value. This results
in a limitation in reducing a minimum turn radius of the front attachment given when
the lower boom is maximally tilted up. Thus, the third prior art also has similar
problems to those in the above swing type excavator having the mono-boom.
[0017] A first object of the present invention is to provide a swing type excavator which
can realize the undercarriage-width turn without reducing not only the side ditch
distance but also the maximum digging depth in a deep digging posture.
[0018] A second object of the present invention is to provide a swing type excavator which
can realize the undercarriage-width turn with a simple construction without using
a complex link mechanism, i.e., without so increasing weight of a front attachment.
[0019] A third object of the present invention is to provide a swing type excavator which
can realize the undercarriage-width turn with a simple construction, and can easily
avoid an interference between the front attachment and a cab when the front attachment
is swung.
[0020] To achieve the above first object, according to the present invention, there is provided
a swing type excavator comprising an undercarriage, an upper structure mounted on
the undercarriage in a turnable manner, and a cab and a front attachment, including
a bucket, an arm and a boom, both mounted on the upper structure, the upper structure
being provided with a swing post which supports the boom of the front attachment in
such a manner as able to swing the whole of the front attachment horizontally, wherein
a coupling point between the boom and the swing post is positioned rearwardly of the
swing center of the swing post away from the front attachment.
[0021] Preferably, said boom is a mono-boom.
[0022] Said boom may e a two-piece boom having a lower boom vertically tiltable by a boom
cylinder with respect to said swing post and an upper boom vertically tiltable with
respect to said lower boom.
[0023] Further, to achieve the above first to third objects, according to the present invention,
there is provided a swing type excavator having said two-piece boom wherein said front
attachment includes opening angle adjustment means for changing a vertical opening
angle between said lower boom and said upper boom depending on a vertical tilt angle
of said lower boom, and that said swing post is mounted on said upper structure through
a swing pin in a position forwardly and laterally of said cab so that said lower boom
can be tilted rearwardly up to a position beyond a line laterally extending from a
front part of said cab.
[0024] Preferably, said opening angle adjustment means comprises a cross link having one
end coupled to said swing post through a horizontal pin and the other end coupled
to said upper boom through a horizontal pin such that said cross link intersects a
line connecting the coupling point between said lower boom and said swing post and
a coupling point between said lower boom and said upper boom.
[0025] Preferably, said opening angle adjustment means comprises a hydraulic cylinder having
one end coupled to said swing post or said lower boom through a horizontal pin and
the other end coupled to said upper boom through a horizontal pin, and means for controlling
extension and contraction of said hydraulic cylinder such that the opening angle between
said lower boom and said upper boom is changed depending on the vertical tilt angle
of said lower boom.
[0026] In the present invention concerning the above first object, the coupling point between
the boom and the swing post is positioned rearwardly of the swing center of the swing
post away from the front attachment. Therefore, the vertical tilt point of the boom
and hence the front attachment comes closer to the turn center of the upper structure,
and the minimum turn radius in the turning posture is reduced. Also, since the position
of the swing post (i.e., the swing center) with respect to the upper structure is
not required to be changed, the front attachment is not shifted toward the turn center
of the upper structure when a side ditch is dug by turning the upper structure and
swinging the whole of the front attachment in the opposite direction to the upper
structure, and hence the same side ditch distance as in the pior art is ensured. Further,
since the position of the swing post is not changed, the maximum tilt-down angle of
the boom in the deep digging posture is also not changed and the same maximum digging
depth as in the prior art is obtained.
[0027] Additionally, as a result of the vertical tilt center of the front attachment coming
closer to the turn center of the upper structure, the maximum digging reach length
from the turn center to the tip end of the bucket is shortened and hence the tipping
moment in the maximum digging reach position is reduced to increase stability of the
excavator.
[0028] In the present invention concerning the first to third objects, the boom is divided
into the lower boom and the upper boom, and the opening angle between the lower boom
and the upper boom (hereinafter referred to as the boom-to-boom opening angle) is
changed by the opening angle adjustment means depending on the vertical tilt angle
of the lower boom so that the boom-to-boom opening angle is maximized in a turning
posture where the lower boom is fully tilted up and the front attachment is folded.
Also, the swing post is disposed on the upper structure in a position forwardly and
laterally of the cab, allowing the lower boom to take an increased maximum tilt-up
angle with no need of greatly changing layout, such as shifting the cab rearwardly,
while preventing interference of the lower boom with the cab. Therefore, the minimum
turn radius of the front attachment is so reduced as to enable the undercarriage-width
turn. Thus, an ultra-small turn excavator capable of realizing the undercarriage-width
turn can be obtained by employing a simple structure of the swing type, without using
a complex parallel link mechanism. Also, if the swing post is only disposed in a position
forwardly and laterally of the cab, there still exists a possibility that the bucket
may hit against the cab when the boom is tilted up and the arm is folded in a condition
where the swing post and the front attachment are swung perpendicularly to the cab
on the same side. By increasing the boom-to-boom opening angle with tilting-up of
the lower boom by the opening angle adjustment means, the bucket passes above the
cab, thus eliminating a possibility that the bucket may hit against the cab.
[0029] With such a feature that the opening angle adjustment means comprises a cross link
having one end coupled to the swing post through a horizontal pin and the other end
coupled to the upper boom through a horizontal pin, the cross link being arranged
to intersect a line connecting the coupling point between the lower boom and the swing
post and the coupling point between the lower boom and the upper boom, the boom-to-boom
opening angle in the maximum tilt-up position of the lower boom is so enlarged that
the front attachment can take the turning posture narrower than the undercarriage
width in that position of the lower boom.
[0030] In the above form, by setting the position of the coupling point between the cross
link and the swing post to be rearwardly of the position of the coupling point between
the lower boom and the swing post away from the front attachment, the boom-to-boom
opening angle in the maximum digging reach position is reduced and a maximum digging
reach length from the turn center to the tip end of the bucket is shortened. Furthermore,
the boom-to-boom opening angle in the maximum tilt-down position of the lower boom
is increased to enable deep digging.
[0031] As an alternative, the position of the coupling point between the cross link and
the swing post is set to be forwardly of the position of the coupling point between
the lower boom and the swing post toward the front attachment. This feature provides
the following advantage in addition to the advantages described above. Since the coupling
position at one end of the cross link is located on the swing post forwardly of the
coupling position of the lower boom, the longitudinal length of the swing post can
be shortened and the entire size of the swing post itself can be reduced. Correspondingly,
the degree of freedom in design is increased.
[0032] With another feature that the opening angle adjustment means comprises a hydraulic
cylinder having one end coupled to the swing post or the lower boom through a horizontal
pin and the other end coupled to the upper boom through a horizontal pin, and means
for controlling extension and contraction of the hydraulic cylinder such that the
opening angle between the lower boom and the upper boom is changed depending on the
vertical tilt angle of the lower boom, the boom-to-boom opening angle can be changed
depending on the vertical tilt angle of the lower boom. Additionally, in this case,
the extension and contraction of the hydraulic cylincer can be changed at any desired
rate, and hence the boom-to-boom opening angle can also be changed at any desired
rate.
[0033] The term "generally within the undercarriage width" used in the specification means
that the upper structure including the front attachment turns "within the undercarriage
width" in a practical sense and, though depending on the machine size, it is allowed
for the turning components to protrude from the undercarriage width (i.e., side ends
of the undercarriage) on the order of several tens millimeters during use.
BRIEF DESCRIPTION OF THE DRAWINGS
[0034]
Fig. 1 is a side view showing a construction of a swing type excavator according to
one embodiment of the present invention.
Fig. 2 is a plan view of the excavator of Fig. 1.
Fig. 3 is a view for explaining operation of a front attachment in the excavator of
Figs. 1 and 2, in which a cab is omitted and only its outer contour is indicated by
two-dot-chain lines for the sake of simplicity.
Fig. 4 is a plan view of the excavator in a turning posture in Fig. 3.
Fig. 5A is an enlarged view of a swing post in the excavator of Figs. 1 and 2, and
Fig. 5B is a view showing a comparative example in which a horizontal pin is positioned
forwardly of a swing pin toward the front attachment.
Fig. 6 is a view for comparatively showing motions of the front attachments mounted
to the respective swing posts in Figs. 5A and 5B, the view illustrating the cab in
the simplified form as with Fig. 3.
Figs. 7A and 7B are plan views showing a condition of side ditch digging in which;
Fig. 7A represents the case of the embodiment shown in Fig. 5A and Fig. 7B represents
the case of the comparative example shown in Fig. 5B.
Fig. 8 is a side view showing a construction and operation of a swing type excavator
according to another embodiment of the present invention, the view illustrating the
cab in the simplified form as with Fig. 3.
Fig. 9 is a side view showing a construction and operation of a swing type excavator
according to still another embodiment of the present invention, the view illustrating
the cab in the simplified form as with Fig. 3.
Fig. 10 is a block diagram of principal parts of a hydraulic circuit for an upper
boom cylinder in Fig. 9.
Fig. 11 is a block diagram showing a configuration of a controller in Fig. 10.
Fig. 12 is a flowchart for control of an upper boom cylinder to be performed in the
controller of Fig. 10.
Fig. 13 is a side view showing a modification of the excavator in Fig. 9 wherein an
upper boom cylinder is coupled between a lower boom and an upper boom, the view illustrating
the cab in the simplified form as with Fig. 3.
Fig. 14 is a view, similar to Fig. 1, showing an embodiment in which the present invention
is applied to excavator having a canopy type cab.
Fig. 15 is a side view showing a construction of a swing type excavator according
to yet another embodiment of the present invention.
Fig. 16A is an enlarged view of a swing post in the excavator of Fig. 15, and Fig.
16B is a view showing a comparative example in which a horizontal pin is positioned
forwardly of a swing pin toward a front attachment.
Fig. 17 is a view for comparatively showing motions of the front attachments mounted
to the respective swing posts in Figs. 16A and 16B, in which a cab is omitted and
only its outer contour is indicated by two-dot-chain lines for the sake of simplicity.
Figs. 18A and 18B are plan views showing a condition of side ditch digging in which;
Fig. 18A represents the case of the embodiment shown in Fig. 16A and Fig. 18B represents
the case of the comparative example shown in Fig. 16B.
DETAILED DESCRIPTION OF THE PREFERRED EMBODIMENTS
[0035] One embodiment of a swing type excavator according to the present invention will
be described with reference to Figs. 1 to 7. The excavator of this embodiment is a
ultra-small turn hydraulic shovel which can realize an undercarriage-width turn.
[0036] First, a construction of the excavator of this embodiment will be described. In the
excavator of this embodiment, as shown in Figs. 1 and 2, an upper structure 11 is
mounted on an undercarriage 10 which travels to move an excavator body, and a cab
12 is mounted on the upper structure 11 in its one side. A swing post 13 is attached
by a swing pin 30, as a vertical pin, to the upper structure 11 at a position forwardly
and laterally of the cab 12. A front attachment 1, including a bucket 22, an arm 19,
an upper boom 17, a lower boom 14 and a cross link 15, is mounted to the swing post
13. The swing post 13 is swingable in the horizontal direction about the swing pin
30. As well known, a seat, various control levers and so on are installed in the cab
12.
[0037] The upper structure 11 has such a size that it can swing generally within a width
of the undercarriage 10, and is operated by a turning mechanism (not shown) so as
to turn horizontally. In addition to the cab 12, the swing post 13 and the front attachment
1 mentioned above, all kinds of equipment necessary for a typical hydraulic shovel
or excavator, e.g., hydraulic devices such as hydraulic pumps and valves for driving
a boom cylinder 16, an arm cylinder 18, a bucket cylinder 20 and a swing cylinder
23, which will be described later, an engine, etc. are also mounted on the upper structure
11.
[0038] The boom is divided into two parts, i.e., the lower boom 14 and the upper boom 17.
The lower boom 14 has a foot end coupled to the swing post 13 by a horizontal pin
31, and a distal end coupled to the upper boom 17 by a horizontal pin 32. Also, the
boom cylinder 16 has a bottom-side end coupled to the swing post 13 by a horizontal
pin 16A, and a rod distal end coupled to the lower boom 14 by a horizontal pin 16B,
thereby tilting the lower boom 14 vertically upon its extension and contraction. Thus,
the boom cylinder 16 serve as a power source to tilt the lower boom 14. On the other
hand, the upper boom 17 has a bottom end coupled to the lower boom 14 by the horizontal
pin 32 as mentioned above, and a distal end coupled to the arm 19 by a horizontal
pin 33. Additionally, the cross link 15, described later, is coupled to the upper
boom 17 by a horizontal pin 34.
[0039] Here, a tilt angle of the lower boom 14 is maximized in the upward direction when
the boom cylinder 16 is extended to a maximum, and is maximized in the downward direction
when the boom cylinder 16 is contracted to a minimum. Also, as the tilt angle in the
upward direction is increased, the lower boom 14 is gradually inclined rearwardly
beyond its vertical posture. In the conventional swing type excavator, since the swing
post is mounted centrally of the upper structure in front of the cab, there is a possibility
that the lower boom 14 may hit against the cab when the lower boom 14 is inclined
rearwardly beyond its vertical posture. Therefore, the maximum tilt-up angle of the
lower boom 14 has been limited to such an extent that the lower boom 14 will not be
inclined rearwardly up to a position of the cab. In this embodiment, since the swing
post 13 is disposed in a position forwardly and laterally of the cab 12, the lower
boom 14 will not hit against the cab 12 even when the lower boom 14 is inclined rearwardly
to a large extent. Accordingly, the maximum tilt-up angle of the lower boom 14 given
when the boom cylinder 16 is maximally extended is set in this embodiment so that
the lower boom 14 may be inclined up to a position where it interferes with the cab
12 in the prior art, i.e., the lower boom 14 may be inclined rearwardly up to a position
exceeding a line laterally extended from the cab 12. That setting is realized by properly
designing a maximum stroke of the boom cylinder 16 given when it is maximally extended,
and its mount relation with respect to the swing post 13.
[0040] In the swing post 13, the horizontal pin 31 as a coupling point between the lower
boom 14 and the swing post 13 is positioned rearwardly of the swing pin 30 as the
swing center of the swing post 13 away from the front attachment 1.
[0041] The cross link 15 is a member constituting an opening angle adjustment means, and
has one end coupled to the swing post 13 by a horizontal pin 35, and the other end
coupled to the upper boom 17 by the horizontal pin 34. In the swing post 13, the horizontal
pin 35 at one end of the cross link 15 is positioned rearwardly of the horizontal
pin 31 at the foot end of the lower boom 14 away from the front attachment 1. In the
posture shown in Fig. 1, the cross link 15 intersects a straight line connecting the
horizontal pin 32 by which the upper boom 17 and the lower boom 14 are coupled to
each other and the horizontal pin 31 by which the lower boom 14 and the swing post
13 are coupled to each other.
[0042] The cross link 15 serves to, as described later in detail, change an opening angle
between the upper boom 17 and the lower boom 14 to be maximized when the lower boom
14 is maximally tilted up such that the lower boom 14 is inclined rearwardly beyond
the line laterally extended from the cab 12. That maximum opening angle is set so
as to provide the minimum turn radius of the front attachment 1 which is generally
equal to or smaller than the width of the undercarriage 10 on condition that the lower
boom 14 is inclined rearwardly beyond the line laterally extended from the cab 12.
[0043] The arm 19 is vertically tiltably coupled to the distal end of the upper boom 17
by the horizontal pin 33 as described above, and the bucket 22 is vertically tiltably
coupled to a distal end of the arm 19 through bucket links 21. The arm cylinder 18
is attached between the upper boom 17 and the arm 19 by horizontal pins 36, 37. An
opening angle between the arm 19 and the upper boom 17 is changed upon the arm cylinder
18 being extended and contracted. Also, the bucket cylinder 20 is attached between
the arm 19 and the bucket links 21 by horizontal pins 38, 39. The bucket links 21
are moved with extension and contraction of the bucket cylinder 20, whereupon the
bucket 22 is angularly moved about its coupling point to the arm 19 to thereby dig
earth and sand, etc. Thus, the arm cylinder 18 and the bucket cylinder 20 serve as
power sources to angularly move the arm 19 and the bucket 22, respectively.
[0044] Furthermore, the swing cylinder 23 has a rod distal end coupled to the swing post
13 by a vertical pin 23a, and a bottom-side end coupled to a predetermined position
on the upper structure 11 by a vertical pin 23b. When the swing cylinder 23 is extended
and contracted as indicated by broken lines in Fig. 23, the swing post 13 is swung
correspondingly as indicated by broken lines, and the front attachment 1 is also swung
with respect to the upper structure 11 (see Fig. 2). When digging a side ditch by
the excavator of this embodiment, the upper structure 11 is turned and the swing cylinder
23 is selectively extended or contracted, thereby swinging the swing post 13 and hence
the front attachment 1 in the opposite direction to the upper structure 11, as with
conventional swing type excavators.
[0045] Operation of the excavator of this embodiment will be described-below with reference
to Figs. 3 and 4 while focusing primarily on action of the cross link 15.
[0046] In Fig. 3, when the boom cylinder 16 is extended and contracted, the lower boom 14
is vertically tilted about the horizontal pin 31 as its coupling point to the swing
post 13. Since the upper boom 17 is coupled to the lower boom 14 by the horizontal
pin 32 and the cross link 15 is coupled to the upper boom 17 by the horizontal pin
32, the opening angle between the upper boom 17 and the lower boom 14 is changed depending
on movement of the lower boom 14.
[0047] The horizontal pin 32 at the distal end of the lower boom 14 moves along a path A
which is a circle (indicated by one-dot-chain line in Fig. 3) with the horizontal
pin 31 at the foot end of the lower boom 14 as the center, and the horizontal pin
34 at the distal end of the cross link 15 moves along a path B which is a circle (indicated
by two-dot-chain line in Fig. 3) with the horizontal pin 35 at one end of the cross
link 15 as the center. For reference, a path C of the horizontal pin 33 coupling the
upper boom 17 and the arm 19 is also shown in Fig. 3. The cross link 15 is designed
such that the cross link 15 intersects the straight line connecting the horizontal
pin 32 and the horizontal pin 31 in the posture of Fig. 1, and the path A of the horizontal
pin 32 at the distal end of the lower boom 14 is overlapped with the path B of the
horizontal pin 34 at the distal end of the cross link 15 as shown in Fig. 3. With
this arrangement, when the path B of the horizontal pin 34 at the distal end of the
cross link 15 is positioned outside the path A of the horizontal pin 32 at the distal
end of the lower boom 14, the boom-to-boom opening angle is increased as the spacing
between the paths A and B is enlarged. Conversely, when the path B of the horizontal
pin 34 at the distal end of the cross link 15 is positioned inside the path A of the
horizontal pin 32 at the distal end of the lower boom 14, the boom-to-boom opening
angle is reduced as the spacing between the paths A and B is enlarged. By so setting
the positional relationship between the cross link 15 and the lower boom 14, the boom-to-boom
opening angle can be controlled to a desired value.
[0048] More specifically, in a region (indicated by I in Fig. 3) including the maximum tilt-up
angle of the lower boom 14 given when the boom cylinder 16 is extended to a maximum,
the boom-to-boom opening angle is increased as the lower boom 14 is tilted upwardly.
Also, in a region (indicated by II in Fig. 3) including the maximum tilt-down angle
of the lower boom 14 given when the boom cylinder 16 is contracted to a minimum, the
boom-to-boom opening angle is increased as the lower boom 14 is tilted downwardly.
The boom-to-boom opening angle is minimized when the tilt angle of the lower boom
14 is a predetermined angle φ from the horizontal direction, i.e., at the boundary
between the first region and the second region. In Fig. 3, the tilt angle of the lower
boom 14 in a maximum digging reach position, where the front attachment 1 is maximally
extended along the ground surface, is in the vicinity of the predetermined angle φ.
[0049] Assuming now in Fig. 3 that the boom-to-boom opening angle in the turning posture
where the lower boom 14 takes the maximum tilt-up angle is α, the boom-to-boom opening
angle in the maximum digging reach position, where the front attachment is maximally
extended along the ground surface is β, and the boom-to-boom opening angle in a deep
digging posture where the upper boom 17 is substantially vertical to the ground surface
is γ, there holds a relationship of:
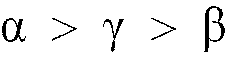
[0050] Therefore, when the lower boom 14 is pivotally raised to assume the turning posture,
the boom-to-boom opening angle is increased by the action of the cross link 15 so
that the lower boom 14 and the upper boom 17 are gradually angularly spaced above
the upper structure 11. At this time, when the boom cylinder 16 is maximally extended
to maximize the tilt-up angle of the lower boom 14, the boom-to-boom opening angle
is also maximized by the action of the cross link 15. Then, since the lower boom 14
is inclined rearwardly beyond the vertical position as described above, the front
attachment 1 is accommodated within the width of the undercarriage 10 by extending
the arm cylinder 18 and the bucket cylinder 20 to such an extent that the arm 19 and
the bucket 22 are folded to locate near the upper boom 17 as shown. Fig. 4 shows the
excavator in this condition as viewed from above. When the lower boom 14 is pivotally
lowered from the turning position, the boom-to-boom opening angle is gradually reduced
by the action of the cross link 15 and, in the maximum digging reach position, the
maximum digging reach length from the turn center to a tip end of the bucket 22 is
shortened. Accordingly, the tipping moment in the maximum digging reach position is
reduced to increase stability of the excavator. In the deep digging posture where
the lower boom 14 is further pivotally lowered, the boom-to-boom opening angle is
increased again and the bucket 22 is moved to a deeper position for deep digging.
[0051] While, in this embodiment, the tilt angle β of the lower boo 14 in the maximum digging
reach position of the front attachment 1 is not coincident with the predetermined
angle φ where boom-to-boom the opening angle is minimized, these angles may be set
to be substantially equal to each other. By so setting, the maximum digging reach
length takes a minimum value and the effect of improving stability is maximized.
[0052] In the swing post 13 of the excavator of this embodiment, as described above, the
coupling point between the lower boom 14 and the swing post 13 is positioned rearwardly
of the swing center of the swing post 13 away from the front attachment 1. Fig. 5A
is an enlarged view showing such an arrangement. On the contrary, Fig. 5B is an enlarged
view showing a comparative example in which a horizontal pin 31a as the coupling point
between a lower boom 14a and a swing post 13a is positioned forwardly of a swing pin
30a as the swing center of the swing post 13a toward a front attachment. Note that
the swing post 13a is disposed on the upper structure in the same position as the
swing post 13. In both the cases of Figs. 5A and 5B, the horizontal pins 16A, 16C
coupling the bottom-side ends of the boom cylinders 16, 16a to the swing posts 13,
13a are positioned forwardly of the swing pins 30, 30a. In the conventional swing
type excavator, as with the case of Fig. 5A, the coupling point between the boom and
the swing post is positioned forwardly of the swing center of the swing post toward
the front attachment.
[0053] Fig. 6 comparatively shows motions of the front attachments mounted to the swing
posts in Figs. 5A and 5B. In Fig. 6, solid lines represent the motion of the front
attachment in this embodiment of Fig. 5A and two-dot-chain lines represent the motion
of the front attachment in the comparative example of Fig. 5B. With the arrangement
of this embodiment that the vertical tilt center of the lower boom 14 is positioned
rearwardly of the swing center of the swing post 13 away from the front attachment
1, the vertical tilt center of the front attachment 1, including the lower boom 14,
comes closer to the turn center of the upper structure 11. Accordingly, the minimum
turn radius is reduced in the amount corresponding to a shortened length a shown in
Fig. 6. Further, corresponding to the shortened length a, an increase in the boom-to-boom
opening angle necessary for keeping the front attachment 1 within the undercarriage
width is reduced and the burden imposed on the cross link is diminished. Moreover,
as a result of the vertical tilt center of the front attachment 1 coming closer to
the turn center of the upper structure 11, the maximum digging reach length from the
turn center to the tip end of the bucket 22 is reduced by a shortened length b shown
in Fig. 6. Therefore, the tipping moment in the maximum digging reach position is
further reduced to ensure higher stability of the excavator.
[0054] Figs. 7A and 7B show the excavator in a condition of side ditch digging in which;
Fig. 7A represents the case of this embodiment shown in Fig. 5A and Fig. 7B represents
the case of the comparative example shown in Fig. 5B. For any case, in the illustrated
condition, the upper structure 11 is turned 90° clockwise on the drawing and the front
attachment is swung 90° counterclockwise on the drawing to dig a side ditch in a limit
position maximally shifted in the direction of the undercarriage width. Note that,
in Fig. 7B, identical members to those in Fig. 7A are denoted by the same reference
numerals. While the vertical tilt center of the lower boom 14 (i.e., the position
of the horizontal pin 31 or 31a) is located on the drawing lower in this embodiment
of Fig. 7A than in the comparative example of Fig. 7B, the swing center of the swing
post 13 (i.e., the position of the swing pin) is in the same position. Accordingly,
the side ditch distance δ is the same in both the cases of Figs. 7A and 7B. Thus,
since the swing center position of the swing post 13 is not changed, the side ditch
can be dug in a position transversely spaced from the longitudinal center of the excavator
body by a distance comparable to that achieved in the prior art, and hence the side
ditch distance is not sacrificed.
[0055] Additionally, as seen from Fig. 6, since the vertical tilt center of the lower boom
14 is positioned closer to the turn center of the upper structure 11 and the lower
boom 14 is allowed to move rearwardly up to a position more away from the front attachment
1, a space left open in front of the lower boom is increased. Therefore, when loading
dug earth and sand, etc. on a dump track or the like from the bucket 22, the earth
and sand, etc. can be more easily loaded.
[0056] It is to be noted that the positional relationship between the horizontal pin 16A
at the foot end of the boom cylinder 16 and the swing pin 30 is not limited to that
shown in Figs. 5A and 5B, but may be optionally set.
[0057] With this embodiment described above, the boom comprises the lower boom 14 and the
upper boom 17, and the boom-to-boom opening angle is changed by the action of the
cross link 15 depending on the tilt angle of the lower boom 14 so that the opening
angle is maximized in the turning posture where the lower boom 14 is tilted up to
a maximum. Also, since the swing post 13 is disposed in a position forwardly and laterally
of the cab 12, the lower boom can take an increased maximum tilt-up angle with no
need of shifting the cab 12 rearwardly, while preventing interference of the lower
boom 14 with the cab 12. Therefore, the minimum turn radius of the front attachment
1 is so reduced as to enable the undercarriage-width turn. Thus, a ultra-small turn
excavator capable of realizing the undercarriage-width turn can be obtained by employing
a simple structure of the swing type, without using a complex parallel link mechanism.
Also, in realizing the undercarriage-width turn, the degree of freedom in designing
layout of the cab 12 on the narrow upper structure 11 can be increased. For example,
the cab 12 may be installed in a more forward position than usual. This is advantageous
in that the engine size can be increased correspondingly, which provides a greater
allowance in design of the upper structure.
[0058] If the swing post is only disposed in a position forwardly and laterally of the cab,
there still exists a possibility that the bucket may hit against the cab when the
boom is tilted up and the arm is folded in a condition where the swing post and the
front attachment are swung perpendicularly to the cab on the same side. However, this
embodiment is also effective to avoid such a possibility. More specifically, since
the cross link 15 is provided in such a manner as to increase the opening angle between
the upper boom 17 and the lower boom 14 with tilting-up of the lower boom 14, the
bucket 22 passes above the cab 12 when the lower boom 14 is tilted up and the arm
19 is folded in the condition where the swing post 13 and the front attachment 1 are
swung perpendicularly to the cab 12 on the same side. As a result, a possibility that
the bucket 22 may hit against the cab 12 is eliminated.
[0059] Further, since the cross link 15 is arranged such that one end thereof is coupled
to the swing post 13 through the horizontal pin 35, the distal end thereof is coupled
to the upper boom 17 through the horizontal pin 32, and it intersects the straight
line connecting the horizontal pin 32 and the horizontal pin 31, the boom-to-boom
opening angle in the maximum tilt-up position of the lower boom 14 is so enlarged
that the front attachment can take the turning posture narrower than the undercarriage
width in that position of the lower boom.
[0060] Since the horizontal pin 35 at one end of the cross link 15 is disposed rearwardly
of the horizontal pin 31 at the foot end of the lower boom 14 away from the front
attachment 1, the boom-to-boom opening angle is reduced in the maximum digging reach
position where the lower boom 14 is tilted down, and the tipping moment in the maximum
digging reach position is reduced to increase stability of the excavator. Additionally,
in the deep digging posture where the lower boom 14 is further pivotally lowered,
the boom-to-boom opening angle is increased so as to enable deep digging.
[0061] Since the coupling point between the lower boom 14 and the swing post 13 is positioned
rearwardly of the swing center of the swing post 13 away from the front attachment
1, the minimum turn radius is further reduced and an increase in the boom-to-boom
opening angle necessary for keeping the front attachment 1 within the undercarriage
width is reduced correspondingly to diminish the burden imposed on the cross link
15. Also, the maximum digging reach length is shortened and the tipping moment in
the maximum digging reach position is further reduced to ensure higher stability of
the excavator. Moreover, since the swing center of the swing post 13 is not changed,
the side ditch distance is not sacrificed. Additionally, when loading dug earth and
sand, etc. on a dump track or the like from the bucket 22, the earth and sand, etc.
can be more easily loaded because of an increased space left open in front of the
lower boom.
[0062] Since this embodiment of the swing type does not employ a heavy mechanism required
for the offset type, the weight of the front attachment is reduced and the stability
is increased. Also, since the counterweight can be made smaller correspondingly, it
is possible to reduce the total weight of the excavator body and hence a transportation
cost. The reduced weight of the excavator body results in other advantages of reducing
a necessary engine output, cutting down a manufacture cost and a running cost, and
improving fuel economy.
[0063] Further, since this embodiment is not of the offset type, the number of connection
points where vertical pins are used is reduced, whereby the front attachment is not
subject to such restrictions as imposed on conventional offset type excavators and
application fields are widened. Additionally, since there is no fear of interference
between a lower portion of the parallel link mechanism and the ground surface during
side ditch digging, the digging depth can be increased as compared with standard type
excavators. As a result of using no complex parallel link mechanism, the manufacture
cost is reduced and maintenance work is less frequently required.
[0064] In offset type excavators, when the arm and the bucket are offset to the side opposite
to the cab, the field of view may be obstructed by the boom, giving an operator difficulty
in viewing the digging position from the cab. However, since this embodiment is of
the swing type that the front attachment 1 is mounted to the swing post 13, the field
of view from the cab 12 is widened, thus allowing the operator to surely look at the
bucket. Accordingly, the operator can perform work with confidence and hence safety
is improved as compared with the offset type excavators.
[0065] In addition, since this embodiment is not of the offset type, there is no possibility
that the front attachment 1 may badly interfere with the cab 12. Only when the front
attachment 1 is swung to the side opposite to the cab 12 and the lower boom 14 is
tilted upwardly, there is a possibility that the front attachment 1 slightly interferes
with the cab 12, but an interference preventing area can be easily calculated just
by detecting a vertical tilt angle and a swing angle of the lower boom 14. Unlike
the conventional offset type excavators, therefore, an inexpensive and highly reliable
interference preventing device can be realized with no need of detecting angles of
all components of the front attachment in the ultra-small turn excavator.
[0066] Next, another embodiment of the swing type excavator according to the present invention
will be described with reference to Fig. 8. Note that, in Fig. 8, identical members
to those in Figs. 1 to 3 are denoted by the same reference numerals.
[0067] As shown in Fig. 8, in a swing post 13A of this embodiment, since a horizontal pin
35A at one end of a cross link 15A is positioned rearwardly of a horizontal pin 31A
at a foot end of a lower boom 14A and, in the posture shown in Fig. 8, the cross link
15A intersects a straight line connecting a horizontal pin 32A by which the upper
boom 17 and the lower boom 14A are coupled to each other and the horizontal pin 31A
at which the lower boom 14 and the swing post 13A are coupled to each other.
[0068] The horizontal pin 32A at the distal end of the lower boom 14A moves along a path
which is a circle (indicated by one-dot-chain line in Fig. 8) with the horizontal
pin 31A as the center, and the horizontal pin 34A at the distal end of the cross link
15A moves along a path which is a circle (indicated by two-dot-chain line in Fig.
8) with the horizontal pin 35A as the center. In this embodiment, the path of the
horizontal pin 32A at the distal end of the lower boom 14A is overlapped with the
path of the horizontal pin 34A at the distal end of the cross link 15A as shown in
Fig. 8. As with the embodiment of Fig. 3, therefore, when the path of the horizontal
pin 34A at the distal end of the cross link 15A is positioned outside the path of
the horizontal pin 32A at the distal end of the lower boom 14A, the boom-to-boom opening
angle is gradually increased. In the region where the positional relationship is reversed
to the above, the boom-to-boom opening angle is gradually reduced.
[0069] Accordingly, when the lower boom 14 is pivotally raised to assume the turning posture,
the boom-to-boom opening angle is gradually increased by the action of the cross link
15A and, when it is pivotally lowered from the turning position, the boom-to-boom
opening angle is gradually reduced by the action of the cross link 15. In this embodiment,
the opening angle α in the turning posture, the opening angle β in the maximum digging
reach position, and the opening angle γ in the deep digging posture are related to
each other as follows:
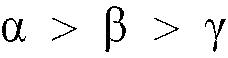
[0070] As with the above embodiment, when the lower boom 14 is pivotally lowered from the
turning position, the boom-to-boom opening angle is gradually reduced and, in the
maximum digging reach position, the maximum digging reach length from the turn center
to the tip end of the bucket 22 is shortened. Therefore, the tipping moment in the
maximum digging reach position is reduced to increase stability of the excavator.
Note that, so long as the boom-to-boom opening angle is increased in the turning posture,
the magnitude relationship among α, β and γ may be optionally set to prolong the maximum
digging reach length, for example, by adjusting the position of the horizontal pin
35 of the cross link 15 and the length of the cross link 15.
[0071] With this embodiment thus arranged, since the coupling position (i.e., the horizontal
pin 35A) at one end of the cross link 15A is positioned forwardly of the coupling
position (i.e., the horizontal pin 31A) of the lower boom 14A to the swing post 13A,
the longitudinal length of the swing post 13A can be shortened. Thus, the size of
the swing post 13A itself is reduced and the degree of freedom in design is increased
correspondingly.
[0072] Further, in the maximum digging reach position, the maximum digging reach length
is shortened and the tipping moment is reduced to increase stability of the excavator
like the above embodiment.
[0073] Next, still another embodiment of the swing type excavator according to the present
invention will be described with reference to Figs. 9 to 12. Note that, in Fig. 9,
identical members to those in Fig. 1 are denoted by the same reference numerals.
[0074] As shown in Fig. 9, in this embodiment, an upper boom cylinder 40 is employed as
opening angle adjustment means instead of the cross link in Figs. 1 and 8. Specifically,
the upper boom cylinder 40 is coupled between the swing post 13 and the upper boom
17 to generate force, when extended and contracted, for changing the opening angle
between the upper boom 17 and the lower boom 14 (hereinafter referred to as the boom-to-boom
opening angle). The remaining construction is the same as in Figs. 1 and 8.
[0075] Fig. 10 is a block diagram of principal parts of a hydraulic circuit as means for
controlling extension and contraction of the upper boom cylinder 40 in this embodiment.
In Fig. 10, a sensor 41 detects an elevation angle (vertical tilt angle) θ of the
lower boom, and a sensor 42 detects a boom-to-boom opening angle ε. A controller 43
receives the angles θ and ε from the sensors 41 and 42, respectively, and applies
to an amplifier 44 a voltage signal 43a corresponding to a flow rate supplied to the
upper boom cylinder 40. The amplifier 44 converts the voltage signal 43a into a current
signal 44a, and the shift position of a directional control valve 45 is determined
by the current signal 44a. Depending on the shift position of the directional control
valve 45, a hydraulic fluid delivered under pressure from a reservoir 46 by a hydraulic
pump 47 is supplied at a certain rate to a rod-side port 40a or a bottom-side port
40b of the upper boom cylinder 40, thereby contracting or extending the upper boom
cylinder 40. Also, a certain back pressure is applied to the circuit by a back pressure
valve 48.
[0076] As shown in Fig. 11, the controller 43 comprises an arithmetic unit 43A, a first
memory 43B and a second memory 43C. The first memory 43B stores the value of a boom-to-boom
opening angle θ
0 at the start of work, and the second memory 43C is a function memory for storing
a function table which represents the relationship between the angles θ and ε. In
the controller 43, the detected angles θ and ε are input to the arithmetic unit 43A
which calculates the voltage signal 43a corresponding to a flow rate supplied to the
upper boom cylinder 40 while transferring data with respect to the first memory 43B
and the second memory 43C.
[0077] A control flow for the upper boom cylinder 40 to be executed in the controller 43
will now be described with reference to Fig. 12. It is to be noted that the following
calculation and control procedures are executed by slicing a period of time, during
which the excavator is operating, into a predetermined sampling time Δt. First, in
step S1, an initial value of the elevation angle of the lower boom 14 prior to starting
to operate the lower boom 14 is input and stored as θ
0 in the first memory 43B beforehand. Then, it is determined in step S2 whether the
time Δt has elapsed or not after the start of operation. If Δt has elapsed, the control
flow goes to next step S3.
[0078] In step S3, the elevation angle θ of the lower boom 14 and the boom-to-boom opening
angle ε are detected by the sensors 41 and 42, respectively, and the arithmetic unit
43A reads both the angles. Then, in step S4, the arithmetic unit 43A reads the previous
elevation angle θ
0 of the lower boom 14 (before the time Δt) from the first memory 43B. Subsequently,
in step S5, an elevation angle (hereinafter denoted by [θ]) after Δt from the current
time is calculated. Here, [θ] is expressed by:
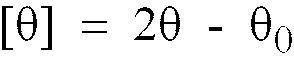
This equation is resulted as follows. Given an elevation angular speed of the lower
boom 14 being θ
*, since θ
* is expressed by;
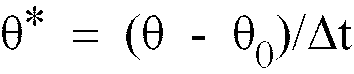
the following equation is obtained:

[0079] Thereafter, in step S6, the arithmetic unit 43A reads [ε] corresponding to the above
[θ], i.e., a boom-to-boom opening angle after Δt from the current time, from the function
table in the second memory 43C. In step S7, θ
0 in the first memory 43B is replaced by θ which is stored as new θ
0. Then, in step S8, a boom-to-boom opening angular speed [ε
*] after Δt from the current time is calculated from:

[0080] In next step S9, an extending or contracting speed of the upper boom cylinder 40
is calculated from [ε
*] by utilizing a geometrical relation formula. This geometrical relation formula is
uniquely determined by the lengths and positions of the upper boom cylinder 40 and
the lower boom 14, the coupling positions of the upper boom cylinder 40 and the lower
boom 14 to the swing post 13, etc., and is stored in the arithmetic unit 43A. In next
step S10, a flow rate of the hydraulic fluid to be supplied to the upper boom cylinder
40 is calculated from the extending or contracting speed of the upper boom cylinder
40, followed by outputting the calculated result (i.e., the voltage signal 43a) to
the amplifier 44 in step S11. It is then determined in step S12 whether the operation
is to be completed or not. If so, the control flow is ended, but if not so, it is
returned to step S1 to repeat the same procedures as described above.
[0081] With this embodiment thus arranged, the boom-to-boom opening angle is changed depending
on the vertical tilt angle of the lower boom 14 by means of the upper boom cylinder
40, the controller 43 for controlling extension and contraction of the cylinder 40,
and so on. Additionally, the extension and contraction of the upper boom cylinder
40 can be changed at any desired rate, and hence the boom-to-boom opening angle can
also be changed at any desired rate.
[0082] As a modification of the above embodiment, an upper boom cylinder 50 may be coupled
between the lower boom 14 and the upper boom 17 as shown in Fig. 13. This modification
can also provide similar advantages. Note that, in Fig. 13, identical members to those
in Fig. 9 are denoted by the same reference numerals.
[0083] While, in the foregoing embodiments, the present invention is applied to the excavator
having the closed type cab, it is also applicable to an excavator having a canopy
type cab which is partly open. Fig. 14 shows such an embodiment in which a cab 12A
is of the canopy type having only a roof 12B and being open to both sides. In the
canopy type cab 12A, a seat, various control levers and so on are similarly installed
in a space below the roof 12A. In the excavator of Fig. 14, the remaining construction
is the same as in the embodiment of Fig. 1. This modification can also provide similar
advantages to those in the embodiment of Fig. 1.
[0084] In each of the embodiments described before, the swing post 13 is disposed on the
upper structure 11 in a position forwardly and laterally of the cab 12. This, however,
is only illustrative and the arrangement may be modified such that the right front
corner of the cab is cut-away so as to provide a space for accommodating the swing
post 13. The present invention can be applied also to such a modification, without
impairing the advantages described before.
[0085] A swing type excavator according to yet another embodiment of the present invention
will be described with reference to Figs. 15 to 18. The excavator of this embodiment
is a hydraulic shovel which can realize the ultra-small turn.
[0086] In Fig. 15, the excavator of this embodiment comprises an undercarriage 110 which
travels to move an excavator body, and an upper structure 111 which is mounted on
the undercarriage 110, with a closed type cab 112 mounted on the upper structure 111.
A swing post 113 is attached by a swing pin 130, as a vertical pin, to the upper structure
111 at a central position forwardly of the cab 112 in a horizontally swingable manner.
A front attachment 101, including a bucket 122, an arm 119 and a boom 114, is mounted
to the swing post 113. A blade 102 is provided so as to project forwardly of the undercarriage
110. The cab 112 may be of the canopy type having only a roof. As well known, a driving
seat, various control levers and so on are installed in the cab 112.
[0087] The upper structure 111 is able to turn horizontally on the undercarriage 110 by
a turning mechanism (not shown). In addition to the cab 112, the swing post 113 and
the front attachment 101 mentioned above, all kinds of equipment necessary for a typical
hydraulic shovel or excavator, e.g., hydraulic devices such as hydraulic pumps and
valves for driving a boom cylinder 116, an arm cylinder 118, a bucket cylinder 120
and a swing cylinder 123, which will be described later, an engine, etc. are also
mounted on the upper structure 111.
[0088] The boom 114 is a mono-boom vertically bent at a certain angle, and has a foot end
coupled to the swing post 113 by a horizontal pin 131. Also, the boom cylinder 116
has a bottom-side end coupled to the swing post 113 by a horizontal pin 116A, and
a rod-side end coupled by a horizontal pin 116B to a bracket 114A which is fixed to
an inner bent portion of the boom 14, thereby tilting the lower boom 114 vertically
upon its extension and contraction. Thus, the boom cylinder 116 serve as a power source
to tilt the boom 114.
[0089] The arm 119 is vertically tiltably coupled to a distal end of the boom 114 by a horizontal
pin 133, and the bucket 122 is vertically tiltably coupled to a distal end of the
arm 119 through bucket links 121. The arm cylinder 118 is attached between a bracket
114B fixed to an outer bent portion of the boom 114 and the arm 119 by horizontal
pins 136, 137. An angle formed between the arm 119 and the boom 114 is changed upon
the arm cylinder 118 being extended and contracted. Also, the bucket cylinder 120
is attached between the arm 119 and the bucket links 121 by horizontal pins 138, 139.
The bucket links 121 are moved with extension and contraction of the bucket cylinder
120, whereupon the bucket 122 is angularly moved about its coupling point to the arm
119 to thereby dig earth and sand, etc. Thus, the arm cylinder 118 and the bucket
cylinder 120 serve as power sources to angularly move the arm 119 and the bucket 122,
respectively.
[0090] In the swing post 113, the horizontal pin 131 as a coupling point between the boom
114 and the swing post 113 is positioned rearwardly of the swing pin 130 as the swing
center of the swing post 113 away from the front attachment 101.
[0091] Furthermore, the swing cylinder 123 has a rod-side end coupled to the swing post
113 by a vertical pin 123a, and a bottom-side end coupled to a predetermined position
on the upper structure 111 by a vertical pin 123b (see Fig. 17). When the swing cylinder
123 is extended and contracted, the swing post 113 is swung correspondingly and the
front attachment 101 is entirely swung in the horizontal direction with respect to
the upper structure 111. When digging a side ditch, the upper structure 111 is turned
and the swing cylinder 123 is extended or contracted depending on the direction of
the turn, thereby swinging the swing post 113 and hence the front attachment 101 in
the opposite direction to the upper structure 111.
[0092] Operation of the thus-constructed excavator of this embodiment will be described
below. In the swing post 113 of the excavator of this embodiment, as mentioned above,
the coupling point between the boom 114 and the swing post 113 is positioned rearwardly
of the swing center of the swing post 113 away from the front attachment 101. Fig.
16A is an enlarged view showing the swing post 113 and thereabout in this embodiment,
whereas Fig. 16B is an enlarged view showing a swing post and thereabout in the prior
art as a comparative example. In the comparative example, a horizontal pin 131a as
the coupling point between a boom 114a and a swing post 113a is positioned forwardly
of a swing pin 130a as the swing center of the swing post 113a toward a front attachment.
Note that, in both the cases of Figs. 16A and 16B, the horizontal pins 116A, 116C
coupling the bottom-side ends of the boom cylinders 116, 116a to the swing posts 113,
113a are positioned forwardly of the swing pins 130, 130a.
[0093] Fig. 17 shows motions of the front attachments mounted to the swing posts in Figs.
16A and 16B. In Fig. 17, solid lines represent the motion of the front attachment
in this embodiment of Fig. 16A and two-dot-chain lines represent the motion of the
front attachment in the comparative example of Fig. 16B. As will be seen from Fig.
17, with the arrangement of this embodiment that the vertical tilt center of the boom
114 is positioned rearwardly of the swing center of the swing post 113 away from the
front attachment 101, the vertical tilt center of the front attachment 101, including
the boom 114, comes closer to the turn center of the upper structure 111. Accordingly,
the minimum turn radius of the front attachment in its turning posture is reduced
in the amount corresponding to a shortened length a shown in Fig. 17.
[0094] Also, as shown in Fig. 16, the swing pin 130 of this embodiment is disposed on the
upper structure in the same position as the swing pin 130a of the prior art. Therefore,
even when the maximum tilt-down angle of the boom 114 in the deep digging posture
is set to a value equal to that in the prior art, the boom cylinder 116 will not interfere
with the blade 102 and, as seen from Fig. 17, the same maximum digging depth as in
the prior art is obtained. Moreover, as a result of the vertical tilt center of the
front attachment 101 coming closer to the turn center of the upper structure 111,
the maximum digging reach length from the turn center to a tip end of the bucket 122
is reduced by a shortened length b shown in Fig. 17. Therefore, the tipping moment
in the maximum digging reach position is reduced to increase stability of the excavator.
[0095] Figs. 18A and 18B show the excavator in a condition of side ditch digging in which;
Fig. 18A represents the case of this embodiment shown in Fig. 16A and Fig. 18B represents
the case of the comparative example shown in Fig. 16B. For any case, in the illustrated
condition, the upper structure 111 is turned 90° clockwise on the drawing and the
front attachment is swung 90° counterclockwise on the drawing to dig a side ditch
in a limit position maximally shifted in the direction of the undercarriage width.
[0096] In this embodiment shown in Fig. 18A, the vertical tilt center of the front attachment
101 is closer to the turn center of the upper structure 111 and, therefore, the vertical
tilt center of the boom 114 (i.e., the position of the horizontal pin 131) is located
on the drawing lower than in the comparative example of Fig. 18B. But, since the swing
center of the swing post 113 (i.e., the position of the swing pin) is in the same
position, the front attachment itself does not move toward the turn center of the
upper structure 111 in the condition of side ditch digging. Accordingly, the side
ditch distance δ from an outer lateral surface of the undercarriage 110 to an outer
wall surface of the side ditch is the same in both the cases of Figs. 18A and 18B.
Thus, with this embodiment, the side ditch can be dug in a position transversely spaced
from the longitudinal center of the excavator body by a distance comparable to that
achieved in the prior art.
[0097] Additionally, in the posture shown in Fig. 17, since the vertical tilt center of
the boom 114 is positioned closer to the turn center of the upper structure 111 and
the front attachment 101 is allowed to entirely move toward the turn center of the
upper structure 111, a space left open in front of the boom 114 when it is tilted
up is increased. Therefore, when holding dug earth and sand, etc. in the bucket 122
and loading them on a dump track or the like by tilting up the boom 114, the earth
and sand, etc. can be more easily loaded because of a larger spacing between the boom
114 and the dump track.
[0098] It is to be noted that the positional relationship between the horizontal pin 116A
at the foot end of the boom cylinder 116 and the swing pin 130 is not limited to that
shown in Fig. 16, but may be optionally set.
[0099] With this embodiment described above, since the coupling point between the boom 114
and the swing post 113 is positioned rearwardly of the swing center of the swing post
113 away from the front attachment 101, the minimum turn radius in the turning posture
can be so reduced as to realize the ultra-small turn. Also, since the position of
the swing post 113 is not changed, the same side ditch distance as in the prior art
is ensured and, in the deep digging posture, the same maximum digging depth as in
the prior art is obtained.
[0100] Further, since the maximum digging reach length is shortened, the tipping moment
is reduced to increase stability of the excavator.
[0101] Additionally, when the front attachment 101 is directed forwardly, a wider space
is left open in front of the boom 114. Therefore, when loading dug earth and sand,
etc. on a dump track or the like from the bucket 122, the earth and sand, etc. can
be more easily loaded because of the wider space left open in front of the boom.
[0102] Since the horizontal pin 131 is positioned rearwardly of the swing post 113 away
from the front attachment 101, a front upper portion of the swing post 113 can be
made smaller and hence the entire size of the swing post 113 itself can be reduced.
[0103] While the swing post 113 is disposed on the upper structure 111 in a central position
forwardly of the cab 112 in the above embodiment, the present invention is not limited
to such an arrangement. For example, the swing post may be disposed in a position
forwardly and laterally of the cab, or in a space formed by cutting out a right-side
corner forwardly of the cab. As another alternative, the swing post may be disposed
laterally of the cab. In any case, similar advantages can be obtained by setting a
position of the coupling point between the boom and the swing post in a like manner
to that in the above embodiment.