[0001] Die Erfindung betrifft ein Verfahren zur Herstellung von Papier, Pappe und Karton
mit hoher Trockenfestigkeit durch Zugabe von kationischer, anionischer und/oder amphoterer
Stärke als Trockenfestigkeitsmittel zum Papierstoff und Entwässern des Papierstoffs
unter Blattbildung.
[0002] Zur Erhöhung der Trockenfestigkeit von Papier, ist z.B. aus Ullmanns Encyklopädie
der technischen Chemie, 4. Auflage, Verlag Chemie, Weinheim - New York, 1979, Band
17, Seite 581, bekannt, wäßrige Anschlämmungen von nativen Stärken, die durch Erhitzen
in eine wasserlösliche Form überführt werden, als Massezusatz bei der Herstellung
von Papier zu verwenden. Die Retention der in Wasser gelösten Stärken an die Papierfasern
im Papierstoff ist jedoch gering. Eine Verbesserung der Retention von Naturprodukten
an Cellulosefasern bei der Herstellung von Papier ist beispielsweise aus der US-A-3
734 820 bekannt. Darin werden Pfropfcopolymerisate beschrieben, die durch Pfropfen
von Dextran, einem in der Natur vorkommenden Polymerisat mit einem Molekulargewicht
von 20.000 bis 50 Millionen, mit kationischen Monomeren, z.B. Diallyldimethylammoniumchlorid,
Mischungen aus Diallyldimethylammoniumchlorid und Acrylamid oder Mischungen aus Acrylamid
und basischen Methacrylaten, wie Dimethylaminoethylmethacrylat, hergestellt werden.
Die Pfropfpolymerisation wird vorzugsweise in Gegenwart eines Redoxkatalysators durchgeführt.
[0003] Aus der US-A-4 097 427 ist ein Verfahren zur Kationisierung von Stärke bekannt, bei
dem man die Stärkekochung in einem alkalischen Medium in Gegenwart von wasserlöslichen
quaternären Ammoniumpolymerisaten und eines Oxidationsmittels durchführt. Als quaternäre
Ammoniumpolymerisate kommen u.a. auch quaternisierte Diallyldialkylaminopolymerisate
oder quaternisierte Polyethylenimine in Betracht. Als Oxidationsmittel verwendet man
beispielsweise Ammoniumpersulfat, Wasserstoffperoxid, Natriumhypochlorit, Ozon oder
tert.-Butylhydroperoxid. Die auf diese Weise herstellbaren modifizierten kationischen
Stärken werden als Trockenverfestigungsmittel bei der Herstellung von Papier dem Papierstoff
zugegeben. Jedoch wird das Abwasser durch einen sehr hohen CSB-Wert (chemischer Sauerstoff-Bedarf)
belastet.
[0004] Aus der US-A-4 146 515 ist ein Verfahren zur Herstellung von kationischer Stärke
bekannt, die für Oberflächenleimung und Beschichtung von Papier- und Papierprodukten
verwendet wird. Gemäß diesem Verfahren wird eine wäßrige Anschlämmung von oxidierter
Stärke zusammen mit einem kationischen Polymeren in einem kontinuierlichen Kocher
aufgeschlossen. Als kationische Polymere kommen Kondensate aus Epichlorhydrin und
Dimethylamin, Polymerisate von Diallyldimethylammoniumchlorid, quaternisierte Reaktionsprodukte
von Ethylenchlorid und Ammoniak sowie quaternisiertes Polyethylenimin in Betracht.
[0005] Aus der US-A-3 467 608 ist ein Verfahren zur Herstellung einer kationischen Stärke
bekannt, bei dem man eine Aufschlämmung von Stärke in Wasser zusammen mit einem Polyalkylenimin
oder Polyalkylenpolyamin mit einem Molekulargewicht von mindestens 50.000 etwa 0,5
bis 5 Stunden lang auf eine Temperatur von etwa 70 bis 110°C erhitzt. Die Mischung
enthält 0,5 bis 40 Gew.-% Polyalkylenimin oder Polyalkylenpolyamin und 99,5 bis 60
Gew.-% Stärke. Gemäß Beispiel 1 wird ein Polyethylenimin mit einem durchschnittlichen
Molekulargewicht von etwa 200.000 in verdünnter wäßriger Lösung mit Kartoffelstärke
2 Stunden lang auf eine Temperatur von 90°C erhitzt. Die modifizierte Kartoffelstärke
kann in einer Mischung aus Methanol und Diethylether ausgefällt werden. Die in der
US-A-3 467 608 beschriebenen Reaktionsprodukte aus Stärke und Polyethylenimin bzw.
Polyalkylenpolyaminen werden als Flockungsmittel verwendet.
[0006] Aus der EP-A-0 282 761 und der DE-A-3 719 480 sind Herstellungsverfahren für Papier,
Pappe und Karton mit hoher Trockenfestigkeit bekannt. Bei diesem Verfahren werden
als Trockenverfestiger Umsetzungsprodukte eingesetzt, die durch Erhitzen von nativer
Kartoffelstärke mit kationischen Polymeren wie Vinylamin-, N-Vinylimidazolin- oder
Diallyldimethylammonium-Einheiten enthaltenden Polymeren bzw. Polyethylenimine in
wäßrigem Medium auf Temperaturen oberhalb der Verkleisterungstemperatur der Stärke
in Abwesenheit von Oxidationsmitteln, Polymerisationsinitiatoren und Alkali erhältlich
sind.
[0007] Aus der EP-B-0 301 372 ist ein ebensolcher Prozeß bekannt, bei dem entsprechend modifizierte,
enzymatisch abgebaute Stärken zum Einsatz kommen. Unter den dort angegebenen Aufschlußbedingungen
für native Stärke wird neben einem unvollständigen Aufschluß (spektroskopische Untersuchungen
zeigen ungelöste, teilweise nur angequollene Stärkekörner) auch eine größere Menge
an Abbauprodukten (Abbauraten > 10 %) gefunden.
[0008] Aus der US-A-4 880 497 und der US-A-4 978 427 ist ein Verfahren zur Herstellung von
Papier mit hoher Trocken- und Naßfestigkeit bekannt, bei dem man entweder auf die
Oberfläche des Papiers oder zum Papierstoff vor der Blattbildung ein hydrolysiertes
Copolymerisat als Verfestigungsmittel zusetzt, das durch Copolymerisieren von N-Vinylformamid
und ethylenisch ungesättigten Monomeren, wie beispielsweise Vinylacetat, Vinylpropionat
oder Alkylvinylether und Hydrolysieren von 30 bis 100 mol-% der Formylgruppen des
Copolymerisats unter Bildung von Aminogruppen erhältlich ist. Die hydrolysierten Copolymeren
werden in Mengen von 0,1 bis 5 Gew.-%, bezogen auf trockene Fasern, eingesetzt.
[0009] Aus der DE-A-4 127 733 sind hydrolysierte Pfropfpolymerisate von N-Vinylformamid
und Saccharidstrukturen enthaltenden Naturstoffen bekannt, die als Trocken- und Naßverfestigungsmittel
Anwendung finden. Die Hydrolyse der Pfropfpolymeren unter sauren Bedingungen hat jedoch
einen starken Molekulargewichtsabbau der Polysaccharide zur Folge.
[0010] Aus der WO-A-96/13525 ist ein Verfahren zur kationischen Modifizierung von Stärke
durch Umsetzung von Stärke mit Polymeren, die Amino- und/oder Ammoniumgruppen enthalten
in wäßrigem Medium bei Temperaturen 115 bis 180°C unter erhöhtem Druck bekannt, wobei
höchstens 10 Gew.-% der eingesetzten Stärke abgebaut werden.
[0011] H.R. Hernandez beschreibt in EUCEPA 24
th Cont.Proc.Pap.Technol., May 1990, Seiten 186 - 195 die Verwendung von kationischer
oder amphoterer Stärke zusammen mit kationischen oder anionischen Retentionsmitteln
bei der Herstellung von Papier. In einem Papiermaschinenversuch erfolgt die Papierherstellung
im alkalischen pH-Bereich mit Alkenylbernsteinsäureanhydrid, Alaun, amphoterer Wachsmaisstärke
und einem anionischen Retentionsmittel.
[0012] Wenn man zum Papierstoff eine kationisch modifizierte Stärke als Trockenverfestigungsmittel
zusetzt, tritt eine unerwünschte Erniedrigung der Entwässerungsgeschwindigkeit des
Papierstoffs ein. Gleichzeitig beobachtet man einen Anstieg des CSB-Werts im Abwasser
der Papiermaschine. Dieser Anstieg des CSB-Werts tritt vor allem bei stark salzhaltigen
Papiermaschinenabwässern ein.
[0013] Der Erfindung liegt daher die Aufgabe zugrunde, ein Verfahren zur Herstellung von
Papier, Pappe und Karton mit hoher Trockenfestigkeit zur Verfügung zu stellen, wobei
man eine erhöhte Retention von Stärke im Papier und somit geringere CSB-Werte im Papiermaschinenabwasser
erreicht und wobei außerdem gegenüber dem Stand der Technik eine Beschleunigung der
Entwässerungsgeschwindigkeit erzielt wird.
[0014] Die Aufgabe wird erfindungsgemäß gelöst mit einem Verfahren zur Herstellung von Papier,
Pappe und Karton mit hoher Trockenfestigkeit durch Zugabe von kationischer, anionischer
und/oder amphoterer Stärke als Trockenfestgkeitsmittel zum Papierstoff und Entwässern
des Papierstoffs in Gegenwart von Retentionsmitteln unter Blattbildung, wenn man für
Stärke mindestens ein kationisches Polymer aus der Gruppe der
- Vinylamineinheiten enthaltende Polymere
- Polyethylenimine
- vernetzte Polyamidoamine
- mit Ethylenimin gepfropfte und vernetzte Polyamidoamine
- Polydiallyldimethylammoniumchloride
- N-Vinylimidazolineinheiten enthaltende Polymere
- Dialkylaminoalkylacrylat- oder Dialkylaminoalkylmethacrylat enthaltende Polymere
- Dialkylaminoalkylacrylamid-Einheiten oder Dialkylaminoalkylmethacrylamid-Einheiten
enthaltende Polymere und
- Polyallylamine
einsetzt.
[0015] Gegenstand der Erfindung ist außerdem die Verwendung von kationischen polymeren Retentionsmitteln
aus der Gruppe der
- Vinylamineinheiten enthaltenden Polymere
- Polyethylenimine
- vernetzten Polyamidoamine
- mit Ethylenimin gepfropften und vernetzten Polyamidoamine
- Polydiallyldimethylammoniumchloride
- N-Vinylimidazolineinheiten enthaltenden Polymere
- Dialkylaminoalkylacrylat- oder Dialkylaminoalkylmethacrylat enthaltende Polymere
- Dialkylaminoalkylacrylamid-Einheiten oder Dialkylaminoalkylmethacrylamid-Einheiten
enthaltenden Polymere und
- Polyallylamine
zur Erhöhung der Retention von Trockenfestigkeitsmitteln aus kationischer, anionischer
und/oder amphoterer Stärke bei der Herstellung von Papier, Pappe und Karton. Besonders
bevorzugt ist die Verwendung von hydrolysierten Homo- oder Copolymerisaten von N-Vinylformamid
mit einem Hydrolysegrad von 1 bis 100 % und einem K-Wert von mindestens 30 (bestimmt
nach H. Fikentscher in wäßriger Lösung bei einer Polymerkonzentration von 0,5 Gew.-%,
einer Temperatur von 25°C und einem pH-Wert von 7) in Mengen von 0,01 bis 0,3 Gew.-%,
bezogen auf trockenen Papierstoff, als Retentionsmittel für kationische, anionische
und/oder amphotere Stärke.
[0016] Als Faserstoffe zur Herstellung der Pulpen kommen sämtliche dafür gebräuchlichen
Qualitäten in Betracht, z.B. Holzstoff, gebleichter und ungebleichter Zellstoff sowie
Papierstoffe aus allen Einjahrespflanzen. Zu Holzstoff gehören beispielsweise Holzschliff,
thermomechanischer Stoff (TMP), chemothermomechanischer Stoff (CTMP), Druckschliff,
Halbzellstoff, Hochausbeute-Zellstoff und Refiner Mechanical Pulp (RMP). Als Zellstoffe
kommen beispielsweise Sulfat-, Sulfit und Natronzellstoffe in Betracht. Geeignete
Einjahrespflanzen zur Herstellung von Papierstoffen sind beispielsweise Reis, Weizen,
Zuckerrohr und Kenaf. Zur Herstellung der Pulpen wird auch Altpapier allein oder in
Mischung mit anderen Fasern verwendet. Zu Altpapier gehört auch sogenannter gestrichener
Ausschuß, der aufgrund des Gehalts an Bindemittel für Streich- und Druckfarben Anlaß
für den White Pitch gibt. Anlaß zur Bildung von sogenannten Stickies geben die aus
Haftetiketten und Briefumschlägen stammenden Kleber sowie Klebstoffe aus der Rückenleimung
von Büchern sowie sogenannte Hotmelts.
[0017] Die genannten Faserstoffe können allein oder in Mischung untereinander verwendet
werden. Die Pulpen der obenbeschriebenen Art enthalten wechselnde Mengen an wasserlöslichen
und wasserunlöslichen Störstoffen. Die Störstoffe können beispielsweise mit Hilfe
des CSB-Wertes oder auch mit Hilfe des sogenannten kationischen Bedarfs quantitativ
erfaßt werden. Unter kationischem Bedarf wird dabei diejenige Menge eines kationischen
Polymeren verstanden, die notwendig ist, um eine definierte Menge des Siebwassers
zum isoelektrischen Punkt zu bringen. Da der kationische Bedarf sehr stark von der
Zusammensetzung des jeweils für die Bestimmung verwendeten kationischen Polymeren
abhängt, verwendet man zur Standardisierung ein gemäß Beispiel 3 der DE-B-2 434 816
erhaltenes Kondensationsprodukt, das durch Pfropfen eines Polyamidoamins aus Adipinsäure
und Diethylentriamin mit Ethylenimin und anschließender Vernetzung mit einem Polyethylenglykoldichlorhydrinether
erhältlich ist. Die Störstoffe enthaltenden Pulpen haben beispielsweise CSB-Werte
von 300 bis 40 000, vorzugsweise 1 000 bis 30 000 mg Sauerstoff pro kg der wässrigen
Phase und einen kationischen Bedarf von mehr als 50 mg des genannten kationischen
Polymeren pro Liter Siebwasser.
[0018] Kationische, anionische und amphotere Stärken sind bekannt und im Handel erhältlich.
Kationische Stärken werden beispielsweise durch Umsetzung von nativen Stärken mit
Quaternisierungsmitteln wie 2,3-(Epoxypropyl)trimethylammoniumchlorid hergestellt.
Stärke und Stärkederivate werden beispielsweise ausführlich beschrieben in dem Buch
von Günther Tegge, Stärke und Stärkederivate, Behr's-Verlag, Hamburg 1984.
[0019] Besonders bevorzugt werden als Trockenverfestigungsmittel Stärken eingesetzt, die
durch Umsetzung von nativer, kationischer, anionischer und/oder amphoterer Stärke
mit synthetischen kationischen Polymeren erhältlich sind. Als native Stärken kann
man beispielsweise Maisstärke, Kartoffelstärke, Weizenstärke, Reisstärke, Tapiokastärke,
Sagostärke, Sorghumstärke, Maniokstärke, Erbsenstärke, Roggenstärke oder Mischungen
der genannten nativen Stärken einsetzen. Als Stärke kommt auch Roggenmehl sowie andere
Mehle in Betracht. Außerdem eignen sich Proteine enthaltende Stärken aus Roggen, Weizen
und Hülsenfrüchten. Für die kätionische Modifizierung mit Polymeren kommen auch solche
nativen Stärken in Betracht, die einen Amylopektingehalt von mindestens 95 Gew.-%
haben. Bevorzugt sind Stärken mit einem Gehalt an Amylopektin von mindestens 99 Gew.-%.
Solche Stärken können beispielsweise durch Stärkefraktionierung üblicher nativer Stärken
oder durch Züchtungsmaßnahmen aus Pflanzen gewonnen werden, die praktisch reine Amylopektinstärke
produzieren. Stärken mit einem Amylopektingehalt von mindestens 95, vorzugsweise mindestens
99 Gew.-% sind auf dem Markt erhältlich. Sie werden beispielsweise als Wachsmaisstärke,
Wachskartoffelstärke oder Wachsweizenstärke angeboten. Die nativen Stärken können
entweder allein oder auch in Mischung mit kationischen Polymeren modifiziert werden.
[0020] Die Modifizierung der nativen Stärken sowie von kationischer, anionischer und/amphoterer
Stärke mit synthetischen kationischen Polymeren erfolgt nach bekannten Verfahren durch
Erhitzen von Stärken in wäßrigem Medium in Gegenwart von kationischen Polymeren auf
Temperaturen oberhalb der Verkleisterungstemperatur der Stärken. Verfahren dieser
Art sind beispielsweise aus den zum Stand der Technik genannten Literaturstellen EP-B-0
282 761 und der WO-A-96/13525 bekannt. Zur kationischen Modifizierung der oben genannten
Stärken kommen alle synthetischen Polymeren in Betracht, die Amino- und/oder Amomniumgruppen
enthalten. Diese Verbindungen werden im folgenden als kationische Polymere bezeichnet.
[0021] Als kationische Polymerisate eignen sich beispielsweise Vinylamineinheiten enthaltende
Homo- und Copolymerisate. Polymerisate dieser Art werden nach bekannten Verfahren
durch Polymerisieren von N-Vinylcarbonsäureamiden der Formel
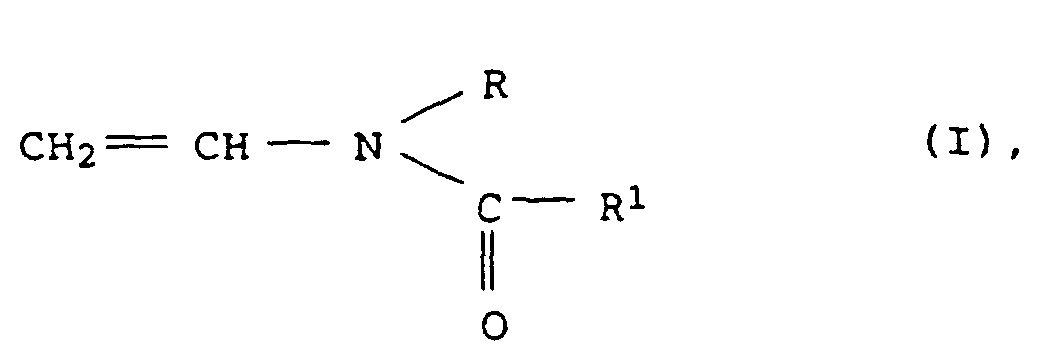
in der R und R
1 gleich oder verschieden sind und H oder C
1- bis C
6-Alkyl bedeuten, allein oder in Gegenwart von anderen damit copolymerisierbaren Monomeren
und Hydrolyse der entstehenden Polymerisate mit Säuren oder Basen unter Abspaltung
der Gruppierung

und unter Bildung von Einheiten der Formel
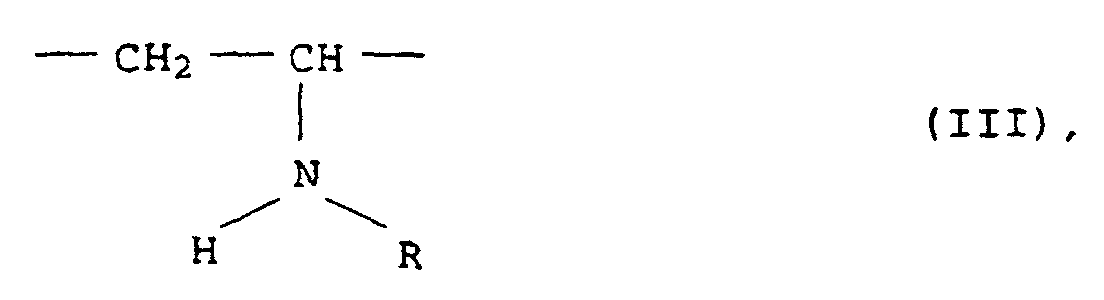
in der R die in Formel (I) angegebene Bedeutung hat, hergestellt.
[0022] Geeignete Monomere der Formel (I) sind beispielsweise N-Vinylformamid, N-Vinyl-N-methylformamid,
N-Vinyl-N-ethylformamid, N-Vinyl-N-propylformamid, N-Vinyl-N-isopropylformamid, N-Vinyl-N-butylformamid,
N-Vinyl-N-sek.butylformamid, N-Vinyl-N-tert.butylformamid, N-Vinyl-N-pentylformamid,
N-Vinylacetamid, N-Vinyl-N-ethylacetamid und N-Vinyl-N-methylpropionamid. Vorzugsweise
setzt man bei der Herstellung von Polymeren, die Einheiten der Formel (III) einpolymerisiert
enthalten, N-Vinylformamid ein. Die hydrolysierten Polymerisate, die Einheiten der
Formel (III) enthalten, haben K-Werte von 15 bis 300, vorzugsweise 30 bis 200, bestimmt
nach H. Fikentscher in wäßriger Lösung bei pH 7, einer Temperatur von 25°C und einer
Polymerkonzentration von 0,5 Gew.-%. Copolymerisate der Monomeren (I) enthalten beispielsweise
1) 99 bis 1 Mol-% N-Vinylcarbonsäureamide der Formel (I) und
2) 1 bis 99 Mol-% andere, damit copolymerisierbare monoethylenisch ungesättigte Monomere,
wie beispielsweise Vinylester von gesättigten Carbonsäuren mit 1 bis 6 Kohlenstoffatomen,
z.B. Vinylformiat, Vinylacetat, Vinylpropionat und Vinylbutyrat. Geeignet sind auch
ungesättigte C
3- bis C
6-Carbonsäuren, wie z.B. Acrylsäure, Methacrylsäure, Maleinsäure, Crotonsäure, Itaconsäure
und Vinylessigsäure sowie deren Alkalimetall- und Erdalkalimetallsalze, Ester, Amide
und Nitrile, beispielsweise Methylacrylat, Methylmethacrylat, Ethylacrylat und Ethylmethacrylat
oder mit Glykol- bzw. Polyglykolestern ethylenisch ungesättigter Carbonsäuren, wobei
jeweils nur eine OH-Gruppe der Glykole und Polyglykole verestert ist, z.B. Hydroxyethylacrylat,
Hydroxyethylmethacrylat, Hydroxypropylacrylat, Hydroxybutylacrylat, Hydroxypropylmethacrylat,
Hydroxybutylmethacrylat sowie die Acrylsäuremonoester von Polyalkylenglykolen eines
Molgewichts von 1.500 bis 10.000. Weiterhin sind geeignet die Ester von ethylenisch
ungesättigten Carbonsäuren mit Aminoalkoholen, wie z.B. Dimethylaminoethylacrylat,
Dimethylaminoethylmethacrylat, Diethylaminoethylacrylat, Diethylaminoethylmethacrylat,
Dimethylaminopropylacrylat, Dimethylaminopropylmethacrylat, Diethylaminopropylacrylat,
Diethylaminopropylmethacrylat, Dimethylaminobutylacrylat und Diethylaminobutylacrylat.
Die basischen Acrylate werden in Form der freien Basen, der Salze mit Mineralsäuren
wie z.B. Salzsäure, Schwefelsäure und Salpetersäure, der Salze mit organischen Säuren
wie Ameisensäure oder Benzolsulfonsäure, oder in quaternisierter Form eingesetzt.
Geeignete Quaternisierungsmittel sind beispielsweise Dimethylsulfat, Diethylsulfat,
Methylchlorid, Ethylchlorid oder Benzylchlorid.
[0023] Außerdem eignen sich als Comonomere 2) ungesättigte Amide wie beispielsweise Acrylamid,
Methacrylamid sowie N-Alkylmono- und - diamide mit Alkylresten von 1 bis 6 C-Atomen
wie z.B. N-Methylacrylamid, N,N-Dimethylacrylamid, N-Methylmethacrylamid, N-Ethylacrylamid,
N-Propylacrylamid und tert.Butylacrylamid sowie basische (Meth)acrylamide, wie z.B.
Dimethylaminoethylacrylamid, Dimethylaminoethylmethacrylamid, Diethylaminoethylacrylamid,
Diethylaminoethylmethacrylamid, Dimethylaminopropylacrylamid, Diethylaminopropylacrylamid,
Dimethylaminopropylmethacrylamid und Diethylaminopropylmethacrylamid.
[0024] Weiterhin sind als Comonomere geeignet N-Vinylpyrrolidon, N-Vinylcaprolactam, Acrylnitril,
Methacrylnitril, N-Vinylimidazol sowie substituierte N-Vinylimidazole wie z.B. N-Vinyl-2-methylimidazol,
N-Vinyl-4-methylimidazol, N-Vinyl-5-methylimidazol, N-Vinyl-2-ethylimidazol, und N-Vinylimidazoline
wie z.B. Vinylimidazolin, N-Vinyl-2-methylimidazolin, und N-Vinyl-2-ethylimidazolin.
N-Vinylimidazole und N-Vinylimidazoline werden außer in Form der freien Basen auch
in mit Mineralsäuren oder organischen Säuren neutralisierter oder in quaternisierter
Form eingesetzt, wobei die Quaternisierung vorzugsweise mit Dimethylsulfat, Diethylsulfat,
Methylchlorid oder Benzylchlorid vorgenommen wird.
[0025] Außerdem kommen als Comonomere 2) Sulfogruppen enthaltende Monomere wie beispielsweise
Vinylsulfonsäure, Allylsulfonsäure, Methallylsulfonsäure, Styrolsulfonsäure oder Acrylsäure-3-sulfopropylester
in Frage.
[0026] Bei der Verwendung von basischen Comonomeren 2) wie z.B. basischen Acrylestern und
-amiden kann oftmals auf eine Hydrolyse der N-Vinylcarbonsäureamide verzichtet werden.
Die Copolymerisate umfassen Terpolymerisate und solche Polymerisate, die zusätzlich
mindestens ein weiteres Monomer einpolymerisiert enthalten.
[0027] Bevorzugte kationische Polymere sind hydrolysierte Copolymerisate aus
1) N-Vinylformamid und
2) Vinylformiat, Vinylacetat, Vinylpropionat, Acrylnitril und N-Vinylpyrrolidon sowie
hydrolysierte Homopolymerisate von N-Vinylformamid mit einem Hydrolysegrad von 2 bis
100, vorzugsweise 30 bis 95 Mol-%.
[0028] Bei Copolymerisaten, die Vinylester einpolymerisiert enthalten, tritt neben der Hydrolyse
der N-Vinylformamideinheiten eine Hydrolyse der Estergruppen unter Bildung von Vinylalkoholeinheiten
ein. Einpolymerisiertes Acrylnitril wird ebenfalls bei der Hydrolyse chemisch verändert,
wobei z.B. Amid-, cyclische Amidin- und/oder Carboxylgruppen entstehen. Die hydrolysierten
Poly-N-vinylformamide können gegebenenfalls bis zu 20 Mol-% an Amidinstrukturen enthalten,
die durch Reaktion von Ameisensäure mit zwei benachbarten Aminogruppen im Polyvinylamin
oder durch Reaktion einer Formamidgruppe mit einer benachbarten Aminogruppe entstehen.
[0029] Als kationische Polymere kommen weiterhin Ethylenimin-Einheiten einpolymerisiert
enthaltende Verbindungen in Betracht. Vorzugsweise handelt es sich hierbei um Polyethylenimine,
die durch polymerisieren von Ethylenimin in Gegenwart von sauren Katalysatoren wie
Ammoniumhydrogensulfat, Salzsäure oder chlorierten Kohlenwasserstoffen wie Methylchlorid,
Ethylenchlorid, Tetrachlorkohlenstoff oder Chloroform, erhältlich sind. Solche Polyethylenimine
haben beispielsweise in 50 gew.-%iger wäßriger Lösung eine Viskosität von 500 bis
33.000, vorzugsweise 1.000 bis 31.000 mPa·s (gemessen nach Brookfield bei 20°C und
20 UPM). Zu den Polymeren dieser Gruppe gehören auch mit Ethylenimin gepfropfte Polyamidoamine,
die gegebenenfalls noch durch Umsetzung mit einem mindestens bifunktionellen Vernetzer
vernetzt sein können. Produkte dieser Art werden beispielsweise durch Kondensieren
einer Dicarbonsäure wie Adipinsäure mit einem Polyalkylenpolyamin wie Diethylentriamin
oder Triethylentetramin, gegebenenfalls Pfropfen mit Ethylenimin und Reaktion mit
einem mindestens bifunktionellen Vernetzer, z.B. Bischlorhydrinether von Polyalkylenglykolen
hergestellt, vgl. US-A-4 144 123 und US-A-3 642 572.
[0030] Weiterhin kommen zur Stärkemodifizierung Poly-Diallyldimethylammoniumchloride in
Betracht. Polymerisate dieser Art sind bekannt. Unter Polymerisaten des Diallyldimethylammoniumchlorids
sollen in erster Linie Homopolymerisate sowie Copolymerisate mit Acrylamid und/oder
Methacrylamid verstanden werden. Die Copolymerisation kann dabei in jedem beliebigen
Monomerverhältnis vorgenommen werden. Der K-Wert der Homo- und Copolymerisate des
Diallyldimethylammoniumchlorids beträgt mindestens 30, vorzugsweise 95 bis 180.
[0031] Als kationische Polymerisate eignen sich auch Homo- und Copolymerisate von gegebenenfalls
substituierten N-Vinylimidazolinen. Es handelt sich hierbei ebenfalls um bekannte
Stoffe. Sie können beispielsweise nach dem Verfahren der DE-B-1 182 826 dadurch hergestellt
werden, daß man Verbindungen der Formel

in der R
1, R
2=H, C
1- bis C
18-Alkyl, Benzyl, Aryl, R
3, R
4=H, C
1- bis C
4-Alkyl und X
- ein Säurerest bedeutet, gegebenenfalls zusammen mit Acrylamid und/oder Methacrylamid
in wäßrigem Medium bei pH-werten von 0 bis 8, vorzugsweise von 1,0 bis 6, 8 in Gegenwart
von Polymerisationsinitiatoren, die in Radikale zerfallen, polymerisiert.
[0032] Vorzugsweise setzt man bei der Polymerisation 1-Vinyl-2-imidazolin-Salze der Formel
(V) ein,
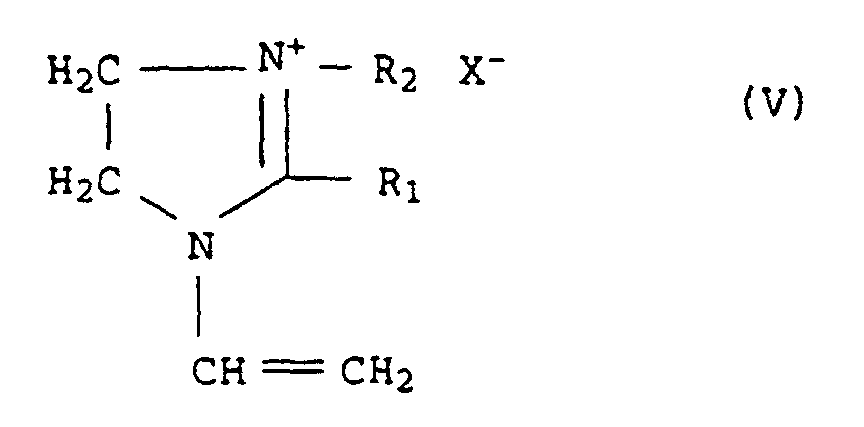
in der R
1, R
2=H, CH
3, C
2H
5, n- und i-C
3H
7, C
6H
5 und X
- ein Säurerest ist. X
- steht vorzugsweise für Cl
-, Br
-, SO
42-, CH
3-O-SO
3-, R-COO
- und R
2=H, C
1- bis C
4-Alkyl und Aryl.
[0033] Der Substituent X- in den Formeln (IV) und (V) kann prinzipiell jeder beliebige Säurerest
einer anorganischen sowie einer organischen Säure sein. Die Monomeren der Formel (IV)
werden erhalten, indem man die freien Basen, d.h. 1-vinyl-2-imidazoline, mit der äquivalenten
Menge einer Säure neutralisiert. Die Vinylimidazoline können auch beispielsweise mit
Trichloressigsäure, Benzolsulfonsäure oder Toluolsulfonsäure neutralisiert werden.
Außer Salzen von 1-Vinyl-2-imidazolinen kommen auch quaternisierte 1-Vinyl-2-imidazoline
in Betracht. Sie werden hergestellt, indem man 1-Vinyl-2-imidazoline, die gegebenenfalls
in 2-, 4- und 5-Stellung substituiert sein können, mit bekannten Quaternisierungsmitteln
umsetzt. Als Quaternisierungsmittel kommen beispielsweise C
1- bis C
18-Alkylchloride oder -bromide, Benzylchlorid oder -bromid, Epichlorhydrin, Dimethylsulfat
und Diethylsulfat in Frage. Vorzugsweise verwendet man Epichlorhydrin, Benzylchlorid,
Dimethylsulfat und Methylchlorid.
[0034] Zur Herstellung der wasserlöslichen Homopolymerisate werden die Verbindungen der
Formeln (IV) oder (V) vorzugsweise in wäßrigem Medium polymerisiert.
[0035] Da die Verbindungen der Formel (IV) relativ teuer sind, verwendet man aus ökonomischen
Gründen vorzugsweise als kationische Polymerisate Copolymerisate von Verbindungen
der Formel (IV) mit Acrylamid und/oder Methacrylamid. Diese Copolymerisate enthalten
die Verbindungen der Formel (IV) dann lediglich in wirksamen Mengen, d.h. in einer
Menge von 1 bis 50 Gew.-%, vorzugsweise 10 bis 40 Gew.-%. Für die Modifizierung nativer
Stärken besonders geeignet sind Copolymerisate aus 60 bis 85 Gew.-% Acrylamid und/oder
Methacrylamid und 15 bis 40 Gew.-% N-Vinylimidazolin oder N-Vinyl-2-methylimidazolin.
Die Copolymerisate können weiterhin durch Einpolymerisieren von anderen Monomeren
wie Styrol, N-Vinylformamid, Vinylformiat, Vinylacetat, Vinylpropionat, C
1- bis C
4-Alkylvinylether, N-Vinylpyridin, N-Vinylpyrrolidon, N-Vinylimidazol, ethylenisch
ungesättigten C
3- bis C
5-Carbonsäuren sowie deren Ester, Amide und Nitrile, Natriumvinylsulfonat, Vinylchlorid
und Vinylidenchlorid in Mengen bis zu 25 Gew.-% modifiziert werden. Beispielsweise
kann man für die Modifizierung nativer Stärken Copolymerisate einsetzen, die
1) 70 bis 97 Gew.-% Acrylamid und/oder Methacrylamid,
2) 2 bis 20 Gew.-% N-Vinylimidazolin oder N-Vinyl-2-methylimidazolin und
3) 1 bis 10 Gew.-% N-Vinylimidazol
einpolymerisiert enthalten. Diese Copolymerisate werden durch radikalische Copolymerisation
der Monomeren 1), 2) und 3) nach bekannten Polymerisationsverfahren hergestellt. Sie
haben K-Werte im Bereich von 80 bis 150 (bestimmt nach H. Fikentscher in 5 %iger wäßriger
Kochsalzlösung bei 25°C und einer Polymerkonzentration von 0,5 Gew.-%).
[0036] Als kationische Polymerisate kommen des weiteren Copolymerisate aus 1 bis 99 Mol-%,
vorzugsweise 30 bis 70 Mol-% Acrylamid und/oder Methacrylamid und 99 bis 1 Mol-%,
vorzugsweise 70 bis 30 Mol-% Dialkylaminoalkylacrylaten und/oder -methacrylaten in
Frage, z.B. Copolymerisate aus Acrylamid und N,N-Dimethylaminoethylacrylat oder N,N-Diethylaminoethylacrylat.
Basische Acrylate liegen vorzugsweise in mit Säuren neutralisierter oder in quaternisierter
Form vor. Die Quaternisierung kann beispielsweise mit Methylchlorid oder mit Dimethylsulfat
erfolgen. Die kationischen Polymerisate haben K-Werte von 30 bis 300, vorzugsweise
100 bis 180 (bestimmt nach H. Fikentscher in 5 %iger wäßriger Kochsalzlösung bei 25°C
und einer Polymerkonzentration von 0,5 Gew.-%). Bei einem pH-Wert von 4,5 haben sie
eine Ladungsdichte von mindestens 4 mVal/g Polyelektrolyt.
[0037] Geeignet sind auch Copolymerisate aus 1 bis 99 Mol-%, vorzugsweise 30 bis 70 Mol-%
Acrylamid und/oder Methacrylamid und 99 bis 1 Mol-%, vorzugsweise 70 bis 30 Mol-%
Dialkylaminoalkylacrylamid und/oder -methacrylamid. Die basischen Acrylamide und Methacrylamide
liegen ebenfalls vorzugsweise in mit Säuren neutralisierter oder in quaternisierter
Form vor. Als Beispiele seien genannt N-Trimethylammoniumethylacrylamidchlorid, N-Trimethylammoniumethylmethacrylamidchlorid,
Trimethylammoniumethylacrylamidmethosulfat, Trimethylammoniumethylmethacrylamidmethosulfat,
N-Ethyldimethylammoniumethylacrylamidethosulfat, N-Ethyldimethylammoniumethylmethacrylamidethosulfat,
Trimethylammoniumpropylacrylamidchlorid, Trimethylammoniumpropylmethacrylamidchlorid,
Trimethylammoniumpropylacrylamidmethosulfat, Trimethylammoniumpropylmethacrylamidmethosulfat
und N-Ethyldimethylammoniumpropylacrylamidethosulfat. Bevorzugt ist Trimethylammoniumpropylmethacrylamidchlorid.
[0038] Als kationische Polymere kommen auch Polyallylamine in Betracht. Polymerisate dieser
Art werden erhalten durch Homopolymerisation von Allylamin, vorzugsweise in mit Säuren
neutralisierter oder in quaternisierter Form oder durch Copolymerisieren von Allylamin
mit anderen monoethylenisch ungesättigten Monomeren, entsprechend der zuvor beschriebenen
Copolymeren mit N-Vinylcarbonsäureamiden.
[0039] Zur erfindungsgemäßen kationischen Modifizierung von Stärke wird beispielsweise eine
wäßrige Suspension mindestens einer Stärkesorte mit einem oder mit mehreren der kationischen
Polymeren auf Temperaturen oberhalb der Verkleisterungstemperatur der nativen bzw.
der modifizierten Stärken erhitzt, z.B. auf Temperaturen von 90 bis 180°C, vorzugsweise
115 bis 145°C. Bei Temperaturen oberhalb des Siedepunkts von Wasser wird die Umsetzung
unter erhöhtem Druck durchgeführt, wobei die Reaktion in der Weise vorgenommen wird,
daß bei höchstens 10 Gew.-% der Stärke ein Molgewichtsabbau eintritt. Wäßrige Aufschlämmungen
von Stärke enthalten beispielsweise auf 100 Gew.-Teile Wasser 0,1 bis 10, vorzugsweise
2 bis 6 Gew.-Teile Stärke. Auf 100 Gew.-Teile Stärke setzt man z.B. 0,5 bis 10 Gew.-Teile
mindestens eines kationischen Polymerisats ein. Als kationische Polymere kommen dabei
vorzugsweise partiell oder vollständig hydrolysierte Homo- oder Copolymerisate von
N-Vinylformamid, Polyethylenimine, mit Ethylenimin gepfropfte und vernetzte Polyamidoamine
und/oder Polydiallyldimethylammoniumchloride in Betracht.
[0040] Beim Erhitzen der wäßrigen Stärkesuspensionen in Gegenwart von kationischen Polymeren
wird zunächst die Stärke aufgeschlossen. Unter Stärkeaufschluß versteht man die Überführung
der festen Stärkekörner in eine wasserlösliche Form, wobei Überstrukturen (Helixbildung,
intramolekulare Wasserstoffbrücken usw.) aufgehoben werden, ohne daß es zum Abbau
von den, die Stärke aufbauenden Amylose- und/oder Amylopektineinheiten zu Oligosacchariden
oder Glukose kommt. Die wäßrigen Stärkesuspensionen, die ein kationisches Polymer
gelöst enthalten, werden bei der Umsetzung auf Temperaturen oberhalb der Verkleisterungstemperatur
der Stärken erhitzt. Bei dem erfindungsgemäßen Verfahren wird die eingesetzte Stärke
zu mindestens 90, vorzugsweise zu >95 Gew.-% aufgeschlossen und mit dem kationischen
Polymerisat modifiziert. Die Stärke ist dabei klar gelöst. Vorzugsweise kann man nach
der Umsetzung der Stärke aus der Reaktionslösung bei Verwendung einer Celluloseacetatmembran
mit einem Porendurchmesser von 1,2 µm keine unumgesetzte Stärke mehr abfiltrieren.
[0041] Die Umsetzung erfolgt vorzugsweise bei erhöhtem Druck. Hierbei handelt es sich üblicherweise
um den Druck, den das Reaktionsmedium in dem Temperaturbereich oberhalb der Siedepunkte
von Wasser, z.B. bei 115 bis 180°C entwickelt. Er liegt beispielsweise bei 1 bis 10,
vorzugsweise 1,2 bis 7,9 bar. Während der Umsetzung wird das Reaktionsgemisch einer
Scherung unterworfen. Falls man die Umsetzung in einem Rührautoklaven durchführt,
rührt man das Reaktionsgemisch beispielsweise mit 100 bis 2.000, vorzugsweise 200
bis 1.000 Umdrehungen/Minute. Die Reaktion kann praktisch in allen Apparaturen durchgeführt
werden, in denen Stärke in der Technik aufgeschlossen wird, z.B. in einem Jetkocher.
Die Verweilzeiten des Reaktionsgemisches bei den obengenannten Temperaturen von 115
bis 180°C betragen beispielsweise 0,1 Sekunden bis 1 Stunde und liegen vorzugsweise
in dem Bereich von 0,5 Sekunden bis 30 Minuten.
[0042] Unter diesen Bedingungen werden mindestens 90 % der eingesetzten Stärke aufgeschlossen
und modifiziert. Vorzugsweise werden dabei weniger als 5 Gew.-% der Stärke abgebaut.
[0043] Die nativen Stärketypen können auch einer Vorbehandlung unterworfen werden, z.B.
oxidativ, hydrolytisch oder enzymatisch abgebaut oder auch chemisch modifiziert werden.
Auch hier sind die Wachsstärken, wie Wachskartoffelstärke und Wachsmaisstärke von
besonderem Interesse.
[0044] Die so erhältlichen Umsetzungsprodukte haben beispielsweise bei einer Feststoffkonzentration
von 3,5 Gew.-% eine Viskosität von 50 bis 10.000, vorzugsweise 80 bis 4.000 mPa·s,
gemessen in einem Brookfield-Viskosimeter bei 20 Umdrehungen/Minute und einer Temperatur
von 20°C. Der pH-Wert der Reaktionsmischungen liegt beispielsweise in dem Bereich
von 2,0 bis 9,0, vorzugsweise 2,5 bis 8.
[0045] Die so erhältlichen mit kationischen Polymeren modifizierten Stärken werden als Trockenverfestigungsmittel
dem Papierstoff in Mengen von beispielsweise 0,5 bis 10, vorzugsweise 0,5 bis 3,5
und besonders bevorzugt 1,2 bis 2,5 Gew.-%, bezogen auf trockenen Papierstoff, zugesetzt.
Gemäß der Erfindung dosiert man zum Papierstoff zusätzlich ein kationisches Polymer
als Retentionsmittel für die oben beschriebenen Stärken, wie kationische Stärke, vorzugsweise
solche Stärken, die mit einem Polymer modifiziert wurden, anionische und/oder amphotere
Stärken. Vorzugsweise dosiert man zunächst die Trockenverfestiger und danach die Retentionsmittel.
Es ist jedoch auch möglich, Trockenverfestiger und Retentionsmittel gleichzeitig dem
Papierstoff zuzusetzen, wobei Trockenverfestiger und Retentionsmittel voneinander
getrennt dosiert werden. Ebenso ist es möglich, eine Mischung aus Trockenverfestiger
und Retentionsmittel zum Papier zu dosieren. Solche Mischungen können beispielsweise
dadurch hergestellt werden, daß man das Retentionsmittel der aufgeschlossenen Stärke
nach Abkühlen auf 50°C oder darunter zusetzt. Das Retentionsmittel kann jedoch auch
vor Zugabe der modifizierten Stärke zum Papierstoff zugesetzt werden. Von dieser Reihenfolge
der Zugabe macht man beispielsweise bei der Verarbeitung von Papierstoffen Gebrauch,
die einen hohen Störstoffgehalt aufweisen.
[0046] Als kationische Polymere, die als Retentionsmittel für Stärke in Betracht kommen,
können sämtliche kationischen Polymeren eingesetzt werden, die oben bereits zur kationischen
Modifizierung von nativer Stärke beschrieben sind, und zwar
- Vinylamineinheiten enthaltende Polymere
- Polyethylenimine
- vernetzte Polyamidoamine
- mit Ethylenimin gepfropfte und vernetzte Polyamidoamine
- Polydiallyldimethylammoniumchloride
- N-Vinylimidazolineinheiten enthaltende Polymere
- Dialkylaminoalkylacrylat- oder Dialkylaminoalkylmethacrylat enthaltende Polymere
- Dialkylaminoalkylacrylamid-Einheiten oder Dialkylaminoalkylmethacrylamid-Einheiten
enthaltende Polymere und
- Polyallylamine.
[0047] Außerdem eignen sich Kondensate aus Dimethylamin und Epichlorhydrin, Kondensate aus
Dimethylamin und Dichloralkanen wie Dichlorethan oder Dichlorpropan sowie Kondensationsprodukte
aus Dichlorethan und Ammoniak.
[0048] Bei einer bevorzugten Ausführungsform des erfindungsgemäßen Verfahrens setzt man
eine kationische Stärke in Kombination mit kationischen Polymeren ein, die Vinylamineinheiten
enthalten und die K-Werte von mindestens 30 (bestimmt nach H. Fikentscher in wäßriger
Lösung bei einer Polymerkonzentration von 0,5 Gew.-%, einer Temperatur von 25°C und
einem pH-Wert von 7) haben.
[0049] Als Trockenverfestigungsmittel setzt man bevorzugt eine kationische Stärke ein, die
erhältlich ist durch Umsetzung von 100 Gew.-Teilen einer nativen, kationischen, anionischen
und/oder amphoteren Stärke mit 0,5 bis 10 Gew.-Teilen eines Vinylamineinheiten enthaltenden
Polymeren mit einem K-Wert von 60 bis 150 bei Temperaturen oberhalb der Verkleisterungstemperatur
der Stärke. Als Vinylamineinheiten enthaltende Polymere werden z.B. hydrolysierte
Homo- und Copolymerisate von N-Vinylformamid mit einem Hydrolysegrad von mindestens
60 % bevorzugt eingesetzt. Diese Homo- und Copolymerisate werden nicht nur zur Kationisierung
von Stärke sondern ebenso dem Papierstoff als Retentionsmittel für die kationisch
modifizierten Stärken zugesetzt.
[0050] Die als Retentionsmittel für Stärke in Betracht kommenden hydrolysierten Homo- und
Copolymerisate von N-Vinylformamid können allgemein einen Hydrolysegrad von 1 bis
100 % aufweisen.
[0051] Andere bevorzugt in Betracht kommende kationische Stärken sind beispielsweise erhältlich
durch Umsetzung von 100 Gew.-Teilen einer nativen, kationischen, anionischen und/oder
amphoteren Stärke mit 0,5 bis 10 Gew.-Teilen
- Polydiallyl-dimethylammoniumchlorid
- wasserlöslichen, mit Epichlorhydrin vernetzten Polyamidoaminen
- wasserlöslichen, mit Ethylenimin gepfropften und mit Bis-chlorhydrinethern von Polyalkylenglykolen
vernetzten Polyamidoaminen
und/oder
- wasserlöslichen Polyethyleniminen und wasserlöslichen, vernetzten Polyethyleniminen
bei Temperaturen oberhalb der Verkleisterungstemperatur der Stärken bis 180°C.
[0052] Bevorzugt eingesetzte handelsübliche kationische Stärken haben z.B. einen Substitutionsgrad
D.S. von bis zu 0,15. Die als Trockenverfestigungsmittel einzusetzenden Stärken werden
in Mengen von 0,5 bis 10, vorzugsweise 1 bis 5 Gew.-%, bezogen auf trockenen Papierstoff
eingesetzt. Die Entwässerung des Papierstoffs erfolgt erfindungsgemäß immer in Gegenwart
mindestens eines Retentionsmittels für Stärke, wobei die Retentionsmittel in Mengen
von 0,01 bis 0,3 Gew.-%, bezogen auf trockenen Papierstoff eingesetzt werden. Man
erhält dadurch gegenüber den bekannten Verfahren eine beträchtlich verbesserte Retention
der Stärke und eine Erhöhung der Entwässerungsgeschwindigkeit des Papierstoffs auf
der Papiermaschine.
[0053] Als Retentionsmittel für Stärke kann man auch sogenannte Mikropartikel-Systeme verwenden,
wobei man zum Papierstoff ein hochmolekulares kationisches synthetisches Polymer zufügt,
die gebildeten Makroflocken durch Scheren des Papierstoffs zerteilt und anschließend
Bentonit zugibt. Dieses Verfahren ist beispielsweise aus der EP-A-0 335 575 bekannt.
Für ein solches Mikropartikelsystem kann man beispielsweise als kationische Polymere
eine Mischung aus einem Vinylamineinheiten enthaltendem Polymeren, z.B. Polyvinylamin
und einem kationischen Polyacrylamid, z.B. einem Copolymerisat aus Acrylamid und Dimethylaminoethylacrylatmethochlorid
einsetzen und nach der Scherstufe Bentonit zusetzen. Weitere bevorzugte Kombinationen
von kationischen Polymeren als Retentionsmittel für Stärken sind Mischungen aus Vinylamineinheiten
enthaltenden Polymeren und mit Ethylenimin gepfropften vernetzten Polyamidoaminen
sowie Mischungen aus Vinylamineinheiten enthaltenden Polymeren mit Polydiallyldimethylammoniumchloriden.
[0054] Falls nicht anders angegeben, bedeuten die Prozentangaben in den Beispielen Gewichtsprozent.
Die K-Werte wurden nach H. Fikentscher, Cellulose-Chemie, Band 13, 58 bis 64 und 71
bis 74 (1932) bei einer Temperatur von 25°C in wäßriger Lösung bei einer Polymerkonzentration
von 0,5 Gew.-% bestimmt.
Beispiele
[0055] Folgende kationische Polymere wurden verwendet:
Polymer 1:
[0056] Polyamidoamin aus Adipinsäure und Diethylentriamin, das mit .. Ethylenimin gepfropft
und anschließend mit Polyethylenglykoldichlorhydrinether gemäß den Angaben in Beispiel
3 der DE-B-2 434 816 vernetzt wurde.
Polymer 2:
[0057] Hydrolysiertes Polyvinylformamid mit einem K-Wert von 90 und einem Hydrolysegrad
von 95 mol-%.
Polymer 3:
[0058] Hydrolysiertes Polyvinylformamid mit einem K-Wert von 90 und einem Hydrolysegrad
von 75 mol-%.
Polymer 4:
[0059] Hydrolysiertes Polyvinylformamid mit einem K-Wert von 90 und einem Hydrolysegrad
von 50 mol-%.
Verfestiger 1
[0060] Eine wäßrige Suspension von nativer Kartoffelstärke wurde in einem Laborjetkocher
der Fa. Werkstättenbau GmbH bei einer Temperatur von 130°C und einem Druck von 2,3
bar kontinuierlich in Gegenwart von 1,5 % Polymer 2 gekocht.
Beispiele 1 bis 4
[0061] Man stellte einen Papierstoff mit einer Stoffdichte von 7,6 g/l aus einem aufgeschlagenen
fertigen handelsüblichen Wellenrohstoff auf Altpapierbasis her. Der pH-Wert des Papierstoffs
betrug 8,0. Um die Stärkeretention zu ermitteln wurden zu Proben dieses Papierstoffs
jeweils die in Tabelle 1 angegebenen Mengen an Verfestiger 1 und den Polymeren 1-4
nacheinander zugesetzt. Nach dem Durchmischen des Papierstoffs mit den Additiven wurde
abgenutscht und der Stärkegehalt aus der Extinktionsmessung des Stärke-Jod-Komplexes
bestimmt. Die dabei erhaltenen Ergebnisse sind in Tabelle 1 angegeben. Ein weiterer
Teil des Papierstoffes wurde nach dem Dosieren von Verfestiger 1 und den jeweils in
Tabelle 1 angegebenen Polymeren mit Hilfe eines Schopper-Riegler-Geräts entwässert.
Man bestimmte die Entwässerungszeit nach DIN ISO 5267 für 700 ml Filtrat. Die Ergebnisse
sind in Tabelle 1 angegeben.
Vergleichsbeispiel 1
[0062] Das Beispiel 1 wurde mit der Ausnahme wiederholt, daß man zum Papierstoff lediglich
Verfestiger 1 in einer Menge von 2 %, bezogen auf trockenen Papierstoff, dosierte.
Stärkegehalt des Filtrats und die Entwässerungszeit sind in Tabelle 1 angegeben.
Tabelle 1
Beispiel |
Zusatz zum Papierstoff, bezogen auf trockenen Papierstoff |
Stärkegehalt im Filtrat
[mg/l] |
Entwässerungszeit
[sec/700 ml] |
1 |
2 % Verfestiger 1 + 0,08 % Polymer 1 |
38 |
92 |
2 |
2 % Verfestiger 1 + 0,08 % Polymer 2 |
34 |
49 |
3 |
2 % Verfestiger 1 + 0,08 % Polymer 3 |
30 |
55 |
4 |
2 % Verfestiger 1 + 0,08 % Polymer 4 |
30 |
67 |
Vergleichsbeispiel |
|
|
|
1 |
2 % Verfestiger 1 |
50 |
136 |
Beispiel 5
[0063] Ein aufgeschlagener fertiger handelsüblicher Wellenrohstoff auf Altpapierbasis mit
einer Stoffdichte von 0,76 % wurde zunächst mit 2 % Verfestiger 1 und anschließend
mit 0,08 % Polymer 3 als Retentionsmittel für kationische Stärke versetzt. Nach Zugabe
von Verfestiger und Polymer wurde der Papierstoff jeweils durchmischt. Ein Teil dieses
Papierstoffs wurde abgenutscht. Aus dem Filtrat wurde der CSB-Wert und die Stärkeretention
durch enzymatischen Abbau zu Glucose mittels HPLC bestimmt. Aus dem anderen Teil des
Papierstoffs ermittelte man mit Hilfe eines Schopper-Riegler-Geräts die Entwässerungszeit
für 500 ml Filtrat. Die Ergebnisse sind in Tabelle 2 angegeben.
Vergleichsbeispiele 2 bis 4
[0064] Das Beispiel 5 wurde mit den aus Tabelle 2 ersichtlichen Änderungen wiederholt. Die
Ergebnisse sind in Tabelle 2 angegeben.
Tabelle 2
Beispiel |
Zusatz zum Papierstoff, bezogen auf trockenen Papierstoff |
CSB-Wert
[mgO2/l] |
Stärkeretention
(enzymatische Methode) |
Entwässerungszeit
[sec/500 ml] |
5 |
2 % Verfestiger 2 + 0,08 % Polymer 3 |
134 |
93 |
20 |
Vergleichsbeispiel |
|
|
|
|
2 |
2 % Verfestiger 1 |
313 |
43 |
72 |
3 |
2 % handelsübliche kationische Stärke D.S. 0,035 |
162 |
92 |
78 |
4 |
- |
135 |
|
68 |
Beispiel 6
[0065] Ein aufgeschlagener fertiger handelsüblicher Wellenrohstoff auf Altpapierbasis mit
einer Stoffkonzentration von 0,76 % wurde nacheinander mit 2 % Verfestiger 2 und 0,08
% Polymer 3 versetzt. Nach dem Durchmischen stellt man auf einem Rapid-Köthen-Blattbildner
Papierblätter mit einem Flächengewicht von 120 g pro m
2 her. Die Blätter wurden auf ihre Trockenfestigkeit geprüft, und zwar die Trockenreißlänge
nach DIN ISO 1924, Trockenberstdruck nach DIN ISO 2758 und Flachstauchwiderstand CMT
nach DIN EN 23035 gleich ISO 3035. Die Ergebnisse sind in Tabelle 3 angegeben.
Vergleichsbeispiele 5 bis 7
[0066] Zunächst wurde Beispiel 6 mit den aus Tabelle 3 ersichtlichen Änderungen wiederholt,
wobei man in Abwesenheit von Polymer 3 arbeitete (Vergleichsbeispiel 5). In weiteren
Tests verwendete man handelsübliche kationische Stärke (Vergleichsbeispiel 6) und
ermittelte den Nullwert (Vergleichsbeispiel 7). Die Ergebnisse sind in Tabelle 3 angegeben.
Tabelle 3
Beispiel |
Zusatz zum Papierstoff, bezogen auf trockenen Papierstoff |
Trockenreißlänge
[m] |
Trockenberstdruck
[kPa] |
CMT
[N] |
6 |
2 % Verfestiger 1 + 0,08 % Polymer 3 |
4433 |
296 |
209 |
Vergleichsbeispiel |
|
|
|
|
5 |
2 % Verfestiger 1 |
4353 |
278 |
190 |
6 |
2 % handelsübliche kationische Stärke D.S. 0,035 |
4488 |
296 |
194 |
7 |
- |
3757 |
241 |
160 |
Polymer 5:
[0067] Hydrolysiertes Poly-N-Vinylformamid mit einem K-Wert von 90 und einem Hydrolysegrad
von 30 %.
Polymer 6:
[0068] Handelsübliches modifiziertes PEI mit einer Ladungsdichte von 14,7 bei pH 4,5 bzw.
10,8 bei pH 7 und einem mittleren Molekulargewicht von ca. 700 000 D.
Polymer 7:
[0069] Hochmolekulares, kationisches Polyacrylamid mit einer Ladungsdichte von 1,7 bei pH
4,5 und einem mittleren Molekulargewicht von 8,5 Mio D.
Beispiel 7
[0070] Ein Papierfarbstoff auf Altpapierbasis mit einem CSB-Wert von 8000 mg Sauerstoff/l
und einer Stoffkonzentration von 1 % wurde nacheinander mit 2 % Verfestiger 1, mit
0,245 % Polymer 6 und 0,02 % Polymer 7 versetzt. Nach dem Durchmischen stellt man
auf dem Rapid-Köthen-Blattbildner Papierblätter mit einem Flächengewicht von ca. 110
g/m
2 her. Die Blätter wurden auf ihre Trockenfestigkeit geprüft, und zwar der Streifenstauchwiderstand
(SCT) Wert nach DIN 54518 (ISO 9895), Trockenberstdruck nach DIN ISO 2758 und Flachstauchwiderstand
CMT nach DIN EN 23035 (ISO 3035). Die Ergebnisse sind in Tabelle 4 angegeben.
Beispiel 8
[0071] Ein Papierstoff auf Altpapierbasis mit einem CSB-Wert von 8000 mg Sauerstoff/l und
einer Stoffkonzentration von 1 % wurde nacheinander mit 2 % Verfestiger 1, mit 0,12
% Polymer 2 und 0,02 % Polymer 7 versetzt. Nach dem Durchmischen stellt man auf dem
Rapid-Köthen-Blattbildner Papierblätter mit einem Flächengewicht von ca. 110 g/m
2 her. Die Blätter wurden nach den in Beispiel 7 angegebenen Methoden auf ihre Trockenfestigkeit
geprüft. Die Ergebnisse sind in Tabelle 4 angegeben.
Beispiel 9
[0072] Ein Papierstoff auf Altpapierbasis mit einem CSB-Wert von 8000 mg Sauerstoff/l und
einer Stoffkonzentration von 1 % wurde nacheinander mit 2 % Verfestiger 1, mit 0,12
% Polymer 3 und 0,02 % Polymer 7 versetzt. Nach dem Durchmischen stellt man auf dem
Rapid-Köthen-Blattbildner Papierblätter mit einem Flächengewicht von ca. 110 g/m
2 her. Die Blätter wurden nach den in Beispiel 7 angegebenen Methoden auf ihre Trockenfestigkeit
geprüft. Die Ergebnisse sind in Tabelle 4 angegeben.
Beispiel 10
[0073] Ein Papierstoff auf Altpapierbasis mit einem CSB-Wert von 8000 mg Sauerstoff/l und
einer Stoffkonzentration von 1 % wurde nacheinander mit 2 % Verfestiger 1, mit 0,13
% Polymer 4 und 0,02 % Polymer 7 versetzt. Nach dem Durchmischen stellt man auf dem
Rapid-Köthen-Blattbildner Papierblätter mit einem Flächengewicht von ca. 110 g/m
2 her. Die Blätter wurden nach den in Beispiel 7 angegebenen Methoden auf ihre Trockenfestigkeit
geprüft. Die Ergebnisse sind in Tabelle 4 angegeben.
Beispiel 11
[0074] Ein Papierstoff auf Altpapierbasis mit einem CSB-Wert von 8000 mg Sauerstoff/l und
einer Stoffkonzentration von 1 % wurde nacheinander mit 2 % Verfestiger 1, mit 0,13
% Polymer 5 und 0,02 % Polymer 7 versetzt. Nach dem Durchmischen stellt man auf dem
Rapid-Köthen-Blattbildner Papierblätter mit einem Flächengewicht von ca. 110 g/m
2 her. Die Blätter wurden nach den in Beispiel 7 angegebenen Methoden auf ihre Trockenfestigkeit
geprüft. Die Ergebnisse sind in Tabelle 4 angegeben.
Vergleichsbeispiel 8
[0075] Ein Papierstoff auf Altpapierbasis mit einem CSB-Wert von 8000 mg Sauerstoff/l und
einer Stoffkonzentration von 1 % wurde nacheinander mit 2 % Verfestiger 1 und 0,02
% Polymer 7 versetzt. Nach dem Durchmischen stellt man auf dem Rapid-Köthen-Blattbildner
Papierblätter mit einem Flächengewicht von ca. 110 g/m
2 her. Die Blätter wurden nach den in Beispiel 7 angegebenen Methoden auf ihre Trockenfestigkeit
geprüft. Die Ergebnisse sind in Tabelle 4 angegeben.

1. Verfahren zur Herstellung von Papier, Pappe und Karton mit hoher Trockenfestigkeit
durch Zugabe von kationischer, anionischer und/oder amphoterer Stärke als Trockenfestigkeitsmittel
zum Papierstoff und Entwässern des Papierstoffs in Gegenwart von Retentionsmitteln
unter Blattbildung,
dadurch gekennzeichnet, daß man als Retentionsmittel für Stärke mindestens ein kationisches Polymer aus der Gruppe
der
- Vinylamineinheiten enthaltende Polymere
- Polyethylenimine
- vernetzte Polyamidoamine
- mit Ethylenimin gepfropfte und vernetzte Polyamidoamine
- Polydiallyldimethylammoniumchloride
- N-Vinylimidazolineinheiten enthaltende Polymere
- Dialkylaminoalkylacrylat- oder Dialkylaminoalkylmethacrylat enthaltende Polymere
- Dialkylaminoalkylacrylamid-Einheiten oder Dialkylaminoalkylmethacrylamid-Einheiten
enthaltende Polymere und
- Polyallylamine
einsetzt.
2. Verfahren nach Anspruch 1, dadurch gekennzeichnet, daß man eine kationische Stärke in Kombination mit kationischen Polymeren einsetzt, die
Vinylamineinheiten enthalten und die K-Werte von mindestens 30 (bestimmt nach H. Fikentscher
in wäßriger Lösung bei einer Polymerkonzentration von 0,5 Gew.-%, einer Temperatur
von 25°C und einem pH-Wert von 7) haben.
3. Verfahren nach Anspruch 1 oder 2, dadurch gekennzeichnet, daß man eine kationische Stärke einsetzt, die erhältlich ist durch Umsetzung von 100
Gew.-Teilen einer nativen, kationischen, anionischen und/oder amphoteren Stärke mit
0,5 bis 10 Gew.-Teilen eines Vinylamineinheiten enthaltenden Polymeren mit einem K-Wert
von 60 bis 150 bei Temperaturen oberhalb der Verkleisterungstemperatur der Stärke.
4. Verfahren nach Anspruch 3, dadurch gekennzeichnet, daß man als Vinylamineinheiten enthaltende Polymere hydrolysierte Homo- oder Copolymerisate
von N-Vinylformamid mit einem Hydrolysegrad von mindestens 60 % einsetzt.
5. Verfahren nach einem der Ansprüche 1 bis 4, dadurch gekennzeichnet, daß man als Retentionsmittel für Stärke hydrolysierte Homo- oder Copolymerisate von N-Vinylformamid
mit einem Hydrolysegrad von 1 bis 100 % einsetzt.
6. Verfahren nach einem der Ansprüche 1 bis 5, dadurch gekennzeichnet, daß man eine kationische Stärke mit einem Substitutionsgrad D.S. von bis zu 0,15 einsetzt.
7. Verfahren nach einem der Ansprüche 1 bis 6, dadurch gekennzeichnet, daß man die Trockenfestigkeitsmittel in Mengen von 0,5 bis 10 Gew.-%, bezogen auf trockenen
Papierstoff, einsetzt.
8. Verfahren nach einem der Ansprüche 1 bis 7, dadurch gekennzeichnet, daß man die Trockenfestigkeitsmittel in Mengen von 1 bis 5 Gew.-%, bezogen auf trockenen
Papierstoff, einsetzt.
9. Verfahren nach einem der Ansprüche 1 bis 8, dadurch gekennzeichnet, daß man die Retentionsmittel für Stärke in Mengen von 0,01 bis 0,3 Gew.-%, bezogen auf
trockenen Papierstoff, einsetzt.
10. Verfahren nach Anspruch 1 oder 2,
dadurch gekennzeichnet, daß man eine kationische Stärke einsetzt, die erhältlich ist durch Umsetzung von 100
Gew.-Teilen einer nativen, kationischen, anionischen und/oder amphoteren Stärke mit
0,5 bis 10 Gew.-Teilen
- Polydiallyl-dimethylammoniumchlorid,
- wasserlöslichen, mit Epichlorhydrin vernetzten Polyamidoaminen
- wasserlöslichen, mit Ethylenimin gepfropften und mit Bis-chlorhydrinethern von Polyalkylenglykolen
vernetzten Polyamidoaminen
und/oder
- wasserlöslichen Polyethyleniminen und wasserlöslichen vernetzten Polyethyleniminen
bei Temperaturen oberhalb der Verkleisterungstemperatur der Stärke bis 180°C.
11. Verwendung von kationischen polymeren Retentionsmitteln aus der Gruppe der
- Vinylamineinheiten enthaltenden Polymere
- Polyethylenimine
- vernetzten Polyamidoamine
- mit Ethylenimin gepfropften und vernetzten polyamidoamine
- Polydiallyldimethylammoniumchloride
- N-Vinylimidazolineinheiten enthaltenden Polymere
- Dialkylaminoalkylacrylat- oder Dialkylaminoalkylmethacrylat enthaltende Polymere
- Dialkylaminoalkylacrylamid-Einheiten oder Dialkylaminoalkylmethacrylamid-Einheiten
enthaltenden Polymere und
- Polyallylamine
zur Erhöhung der Retention von Trockenfestigkeitsmitteln aus kationischer, anionischer
und/oder amphoterer Stärke bei der Herstellung von Papier, Pappe und Karton.
12. Verwendung nach Anspruch 11, dadurch gekennzeichnet, daß man als Retentionsmittel hydrolysierte Homo- oder Copolymerisate von N-Vinylformamid
mit einem Hydrolysegrad von 1 bis 100 % und einem K-Wert von mindestens 30 (bestimmt
nach H. Fikentscher in wäßriger Lösung bei einer Polymerkonzentration von 0,5 Gew.-%,
einer Temperatur von 25°C und einem pH-Wert von 7) in Mengen von 0,01 bis 0,3 Gew.-%
einsetzt.
1. A process for the production of paper, board and cardboard having high dry strength
by the addition of cationic, anionic or amphoteric starch as a dry strength agent
to the paper stock and drainage of the paper stock in the presence of retention aids
with sheet formation, wherein at least one cationic polymer from the group consisting
of
- polymers containing vinylamine units
- polyethyleneimines
- crosslinked polyamidoamines
- ethyleneimine-grafted and crosslinked polyamidoamines
- polydiallyldimethylammonium chlorides
- polymers containing N-vinylimidazoline units
- polymers containing dialkylaminoalkyl acrylate or dialkylaminoalkyl methacrylate
- polymers containing dialkylaminoalkylacrylamide units or dialkylaminoalkylmethacrylamide
units and
- polyallylamines
is used as a retention aid for starch.
2. A process as claimed in claim 1, wherein a cationic starch is used in combination
with cationic polymers which contain vinylamine units and have K values of at least
30 (determined according to H. Fikentscher in aqueous solution at a polymer concentration
of 0.5 % by weight, at 25°C and at a pH of 7).
3. A process as claimed in claim 1 or 2, wherein a cationic starch which is obtainable
by reacting 100 parts by weight of a natural, cationic, anionic or amphoteric starch
with from 0.5 to 10 parts by weight of a polymer containing vinylamine units and having
a K value of from 60 to 150 at above the glutinization temperature of the starch is
used.
4. A process as claimed in claim 3, wherein hydrolyzed homo- or copolymers of N-vinylformamide
having a degree of hydrolysis of at least 60 % are used as the polymers containing
vinylamine units.
5. A process as claimed in any of claims 1 to 4, wherein hydrolyzed homo- or copolymers
of N-vinylformamide having a degree of hydrolysis of from 1 to 100 % are used as retention
aids for starch.
6. A process as claimed in any of claims 1 to 5, wherein a cationic starch having a degree
of substitution D.S. of up to 0.15 is used.
7. A process as claimed in any of claims 1 to 6, wherein the dry strength agents are
used in amounts of from 0.5 to 10 % by weight, based on dry paper stock.
8. A process as claimed in any of claims 1 to 7, wherein the dry strength agents are
used in amounts of from 1 to 5 % by weight, based on dry paper stock.
9. A process as claimed in any of claims 1 to 8, wherein the retention aids for starch
are used in amounts of from 0.01 to 0.3 % by weight, based on dry paper stock.
10. A process as claimed in claim 1 or 2, wherein a cationic starch which is obtainable
by reacting 100 parts by weight of a natural, cationic, anionic or amphoteric starch
with from 0.5 to 10 parts by weight of
- polydiallyl-dimethylammonium chloride,
- water-soluble polyamidoamines crosslinked with epichlorohydrin
- water-soluble ethyleneimine-grafted polyamidoamines crosslinked with bischlorohydrin
ethers of polyalkylene glycols
or
- water-soluble polyethyleneimines and water-soluble crosslinked polyethyleneimines
at from above the glutinization temperature of the starch to 180°C is used.
11. The use of a cationic polymeric retention aid from the group consisting of
- polymers containing vinylamine units
- polyethyleneimines
- crosslinked polyamidoamines
- ethyleneimine-grafted and crosslinked polyamidoamines
- polydiallyldimethylammonium chlorides
- polymers containing N-vinylimidazoline units
- polymers containing dialkylaminoalkyl acrylate or dialkylaminoalkyl methacrylate
- polymers containing dialkylaminoalkylacrylamide units or dialkylaminoalkylmethacrylamide
units and
- polyallylamines.
for increasing the retention of dry strength agents comprising cationic, anionic
or amphoteric starch in the production of paper, board and cardboard.
12. The use as claimed in claim 11, wherein hydrolyzed homo- or copolymers of N-vinylformamide
having a degree of hydrolysis of from 1 to 100 % and a K value of at least 30 (determined
according to H. Fikentscher in aqueous solution at a polymer concentration of 0.5
% by weight, at 25°C and at a pH of 7) are used as retention aids in amounts of from
0.01 to 0.3 % by weight.
1. Procédé de préparation de papier, de carton-pâte et de carton présentant une haute
stabilité à sec par addition d'amidon cationique, anionique et/ou amphotère, comme
agent de stabilité à sec, à la pâte de papier et par déshydratation de la pâte de
papier en présence d'un agent de rétention, avec formation de feuille,
caractérisé en ce que, comme agent de rétention pour de l'amidon, on met en oeuvre au moins un polymère
cationique du groupe
- des polymères contenant des unités vinylamine,
- des polyéthylèneimines,
- des polyamidoamines réticulées,
- des polyamidoamines greffées avec de l'éthylèneimine et réticulées,
- des chlorures de polydiallyldiméthylammonium,
- des polymères contenant des unités N-vinylimidazoline,
- des polymères contenant de l'acrylate de dialkylaminoalkyle ou du méthacrylate de
dialkylaminoalkyle,
- des polymères contenant des unités dialkylaminoalkylacrylamide ou des unités dialkylaminoalkylméthacrylamide,
et
- des polyallylamines.
2. Procédé suivant la revendication 1, caractérisé en ce qu'on met en oeuvre un amidon cationique en combinaison avec des polymères cationiques
qui contiennent des unités vinylamine et qui ont des valeurs K d'au moins 30 (déterminées
d'après H. Fikentscher en solution aqueuse à une concentration en polymère de 0,5%
en poids, à une température de 25°C et à une valeur de pH de 7).
3. Procédé suivant l'une des revendications 1 et 2, caractérisé en ce qu'on met en oeuvre un amidon cationique qui peut être obtenu par réaction de 100 parties
en poids d'un amidon cationique, anionique et/ou amphotère, naturel, avec 0,5 à 10
parties en poids d'un polymère contenant des unités vinylamine et ayant une valeur
K de 60 à 150, à des températures au-dessus de la température de gélification de l'amidon.
4. Procédé suivant la revendication 3, caractérisé en ce que, comme polymères contenant des unités vinylamine, on met en oeuvre des homopolymères
ou copolymères de N-vinylformamide ayant un degré d'hydrolyse d'au moins 60%.
5. Procédé suivant l'une des revendications 1 à 4, caractérisé en ce que, comme agent de rétention pour l'amidon, on met en oeuvre des homopolymères ou copolymères
hydrolysés de N-vinylformamide ayant un degré d'hydrolyse de 1 à 100%.
6. Procédé suivant l'une des revendications 1 à 5, caractérisé en ce qu'on met en oeuvre un amidon cationique présentant un degré de substitution D.S. de
jusqu'à 0,15.
7. Procédé suivant l'une des revendications 1 à 6, caractérisé en ce qu'on met en oeuvre l'agent de stabilité à sec en des quantités de 0,5 à 10% en poids,
par rapport à la pâte de papier sèche.
8. Procédé suivant l'une des revendications 1 à 7, caractérisé en ce qu'on met en oeuvre l'agent de stabilité à sec en des quantités de 1 à 5% en poids, par
rapport à la pâte de papier sèche.
9. Procédé suivant l'une des revendications 1 à 8, caractérisé en ce qu'on met en oeuvre l'agent de rétention pour amidon en des quantités de 0,01 à 0,3%
en poids, par rapport à la pâte de papier sèche.
10. Procédé suivant l'une des revendications 1 et 2,
caractérisé en ce qu'on met en oeuvre un amidon cationique qui peut être obtenu par réaction de 100 parties
en poids d'un amidon cationique, anionique et/ou amphotère, naturel, avec 0,5 à 10
parties en poids
- de chlorure de polydiallyldiméthylammonium,
- de polyamidoamines solubles dans l'eau, réticulées avec de l'épichlorhydrine,
- de polyamidoamines solubles dans l'eau, greffées avec de l'éthylèneimine et réticulées
avec des éthers de bis-chlorhydrine de polyalkylèneglycols,
et/ou
- de polyéthylèneimines solubles dans l'eau et de polyéthylèneimines réticulées solubles
dans l'eau,
à des températures supérieures à la température de gélification de l'amidon jusqu'à
180°C.
11. Utilisation d'agent de rétention polymère cationique du groupe
- des polymères contenant des unités vinylamine,
- des polyéthylèneimines,
- des polyamidoamines réticulées,
- des polyamidoamines greffées avec de l'éthylèneimine et réticulées,
- des chlorures de polydiallyldiméthylammonium,
- des polymères contenant des unités N-vinylimidazoline,
- des polymères contenant de l'acrylate de dialkylaminoalkyle ou du méthacrylate de
dialkylaminoalkyle,
- des polymères contenant des unités dialkylaminoalkylacrylamide ou des unités dialkylaminoalkylméthacrylamide,
et
- des polyallylamines,
pour augmenter la rétention des agents de stabilité à sec à partir d'amidon cationique,
anionique et/ou amphotère lors de la fabrication de papier, de carton-pâte et de carton.
12. Utilisation suivant la revendication 11, caractérisée en ce que, comme agent de rétention, on met en oeuvre des homopolymères ou copolymères hydrolysés
de N-vinylformamide ayant un degré d'hydrolyse de 1 à 100% et une valeur K d'au moins
30 (déterminée d'après H. Fikentscher en solution aqueuse à une concentration en polymère
de 0,5% en poids, à une température de 25°C et à une valeur de pH de 7) en des quantités
de 0,01 à 0,3% en poids.