[0001] This invention relates to aqueous dispersions of epoxy resins and to a process to
prepare them. In one aspect, the invention relates to improved aqueous dispersions
of epoxy resins, which provide improved coating properties.
[0002] Aqueous dispersions of epoxy resins have been known for many years. However, the
performance of these dispersions as elements of coatings has been viewed as inferior
to their solvent borne counterparts. It is known that the surfactants employed to
render the epoxy component emulsifiable such as nonylphenol ethoxylates, alkylphenol
initiated poly(oxyethylene) ethanols, alkylphenol initiated poly(oxypropylene) poly(oxyethylene)
ethanols, and block copolymers containing an internal poly(oxypropylene) block and
two external poly(oxyethylene) ethanol blocks readily migrate to surface interfaces
where, it is speculated, they deleteriously affect film performance.
[0003] Further as aqueous dispersions of epoxy resins have become more widely used in industry,
improved handling properties such as storage stability, uniformity, small particle
size, higher inversion temperature, viscosity reproducibility, and ease of transferring
the dispersions become more desirable. Therefore, there is a growing need for aqueous
dispersions of epoxy resins that have improved, user friendly handling properties.
[0004] WO 96 06876 A describes a process for preparing self-dispersing curable epoxy resin
comprising a reduced particle size mixture comprised of a self-dispersing curable
epoxy resin based on polyxyalkyleamine, water and an organic cosolvent and removing
at least a major amount of the said organic cosolvent from the said mixture after
said reducing. This process has the drawback that the organic solvent has to be removed
from the dispersion and this provides a limitation for the development this technology.
[0005] With the use of reactive diluents in accordance with the prior art dispersion process
it is possible to produce different epoxy resin or epoxy-polyacrylate dispersions
which are always of low solvent content up to 10% such as disclosed in EP 0 770 635
A, however the use of reactive diluent implies lower film properties of the cured
coating composition.
[0006] According to the invention an aqueous dispersion is provided, comprising:
a) water;
b) at least one epoxy resin having a functionality of greater than 0.8 epoxide group
per molecule;
c) from 0.1 to 20 weight percent, based on the epoxy resin, of at least one epoxy
functional polyoxyalkylene surfactant which has been prepared by reacting i) an amidoamine
having one of the structures:
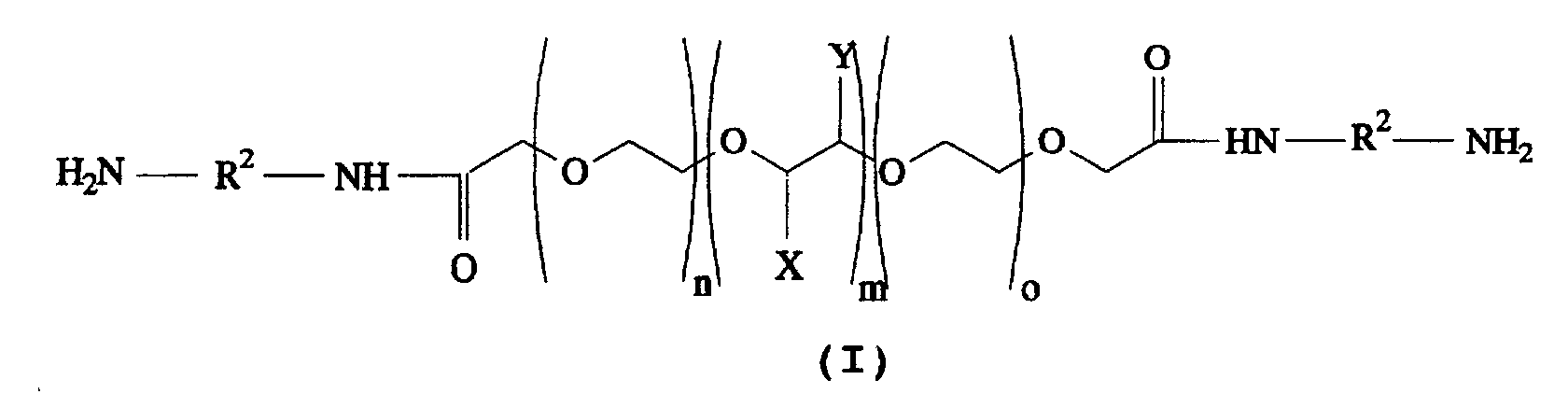
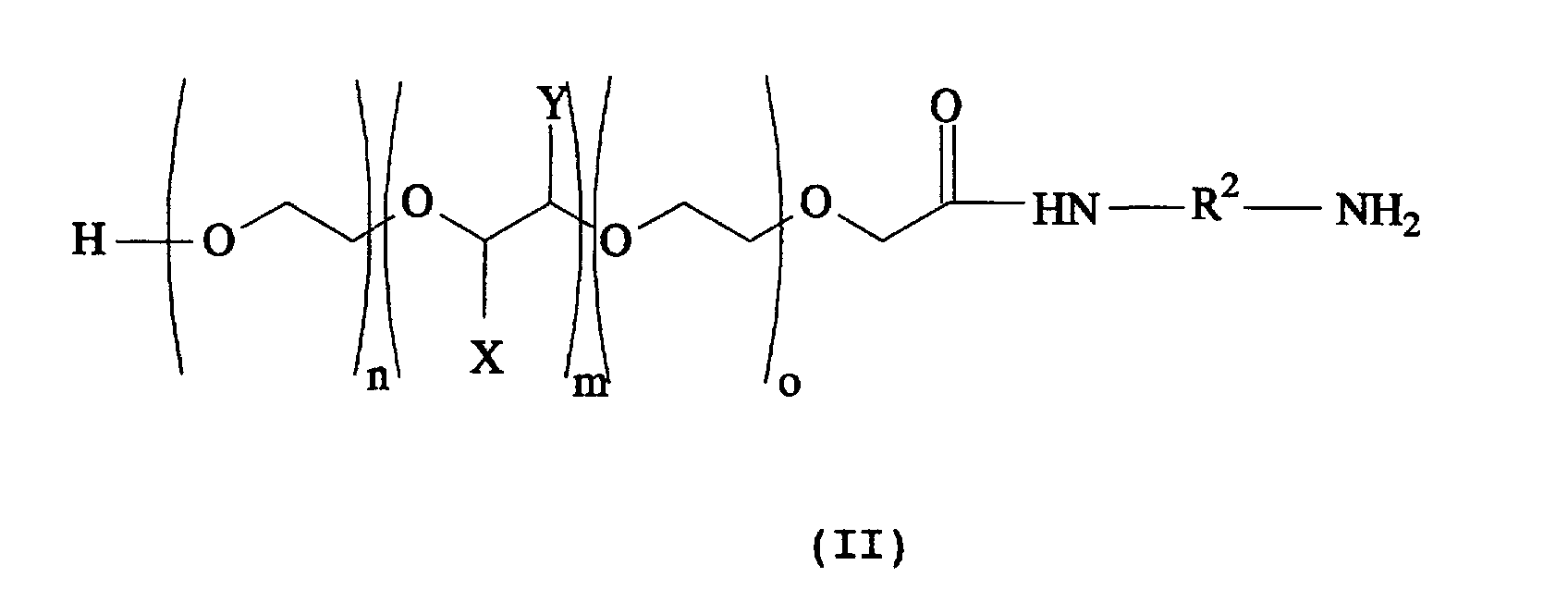
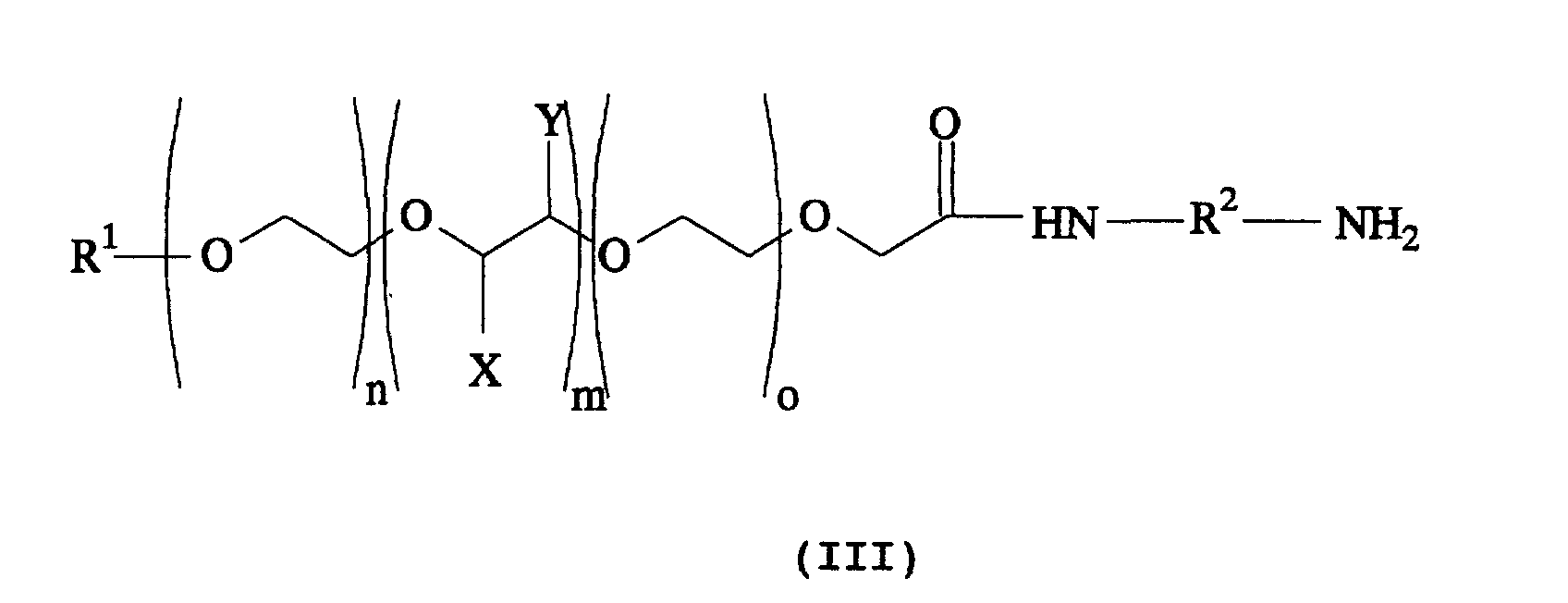
wherein R1 is an alkyl, aryl, or arylalkyl group or mixtures thereof having 1 to
15 carbon atoms, R2 is aliphatic, cycloaliphatic, or aromatic group having 2 to 18
carbon atoms optionally containing non-reactive oxygen or at most an average of 4
secondary and/or tertiary nitrogen atoms per structure in the backbone, X and Y are
independently a hydrogen, methyl or ethyl group with the provision that if X is methyl
or ethyl, Y is hydrogen or if Y is methyl or ethyl, X is hydrogen, and n+m+o is a
real number from 40 to 400, and n+o is a real number of at least 15 wherein the ratio
of (I) to (II) by weight is in the range of 100:0 to 0:100, the ratio of (I) to (III)
by weight in the range of 100:0 to 0:100, and the ratio of (II) to (III) by weight
in the range of 100:0 to 0:100, and ii) at least one epoxy resin having a functionality
of from greater than 0.8 epoxide group per molecule in an amine to epoxy equivalent
ratio of at least 1:2; said surfactant being present in an amount effective to provide
resin emulsification.
d) at least one solvent mixture comprising (i) acetone and (ii) a non-volatile hydrophobic
liquid resin or resin modifier; and
e) an acetone-free solvent solution to produce a resin-surfactant emulsion.
[0007] It has been found that by using above solvent combination in above process with an
epoxy functional polyoxyalkylene surfactant an effective aqueous epoxy resin dispersion
can be formed. The process of the invention provides an epoxy resin dispersion having
a relatively uniform particle size, and an average particle size of generally less
than 1µ that has good shelf-life and handling properties. These dispersions are stable,
retaining consistent viscosity and epoxy functionality for suitable periods of time
and provides good gloss for the coating compositions. Further, it has been found that
process time can be reduced substantially by using the process of the invention.
As said, the epoxy-functional surfactant is prepared by reacting (i) at least one
amidoamine having the structures:

wherein R1 is an alkyl, aryl, or alkylaryl group having 1 to 15 carbon atoms, preferably
C1-C4 alkyl or nonylphenyl, most preferably methyl, R2 is aliphatic, cycloaliphatic,
or aromatic group having 2 to 18 carbon atoms optionally containing non-reactive oxygen
or nitrogen atoms in the backbone, X and Y are independently a hydrogen, methyl or
ethyl group with the provision that if X is methyl or ethyl, Y is hydrogen or if Y
is methyl or ethyl, X is hydrogen and n+m+o is a real number from 40 to 400, m is
a real number from 0 to 70, preferably from 0 to 50, most preferably 0, and n+o is
a real number in an amount effective to provide resin emulsification which is at least
15 and in a ratio of (I) to (II) by weight in the range of 100:0 to 0:100, a ratio
of (I) to (III) by weigh in the range of 100:0 to 0:100, and a ratio of (II) to (III)
by weight in the range of 100:0 to 0:100, and (ii) at least one epoxy resin having
a functionality greater than 0.8 epoxide group per molecule. The epoxy-functional
amidoamine surfactant preferably has a molecular weight within the range of from 1,700
to 40,000, preferably to 20,000. In formula (I), preferably m is a real number from
0 to 70 and n and o are independently a real number from 5 to 395. In formula (II),
preferably m is a real number from 0 to 70, n is a real number from 0 to 395, and
o is a real number from 0 to 400, preferably from 10 to 390 and more preferably from
20 to 380. In formula (III), preferably m is a real number from 0 to 70, n is a real
number from 0 to 395, and o is a real number from 0 to 400, preferably from 10 to
390 and more preferably from 20 to 380. In all of the above formulae (I), (II), and
(III), n+o must be a real number in an amount effective to provide resin emulsification
which is typically at least 15, preferably at least 35. In one preferred embodiment,
m is 0.
[0008] In one of the preferred embodiments, the epoxy-functional surfactant can be prepared
by reacting amidoamine of structures (I) and (II) in a ratio of (I) to (II) by weight
in the range of 99:1 to 1:99, preferably in the range of 20:80 to 80:20, and at least
one epoxy resin.
[0009] For the epoxy-functional surfactant, the amidoamine is contacted with the epoxy resin
under conditions effective to react the amine group and the epoxide group.
Typically, the equivalent ratio of the amine to epoxy is at least 1:2, preferably
in the range of from 1:6 to 1:500. The reaction is typically carried out at a temperature
from ambient temperature to an elevated temperature sufficient to react the amine
group and the epoxide group preferably in the range of from 50 °C to 150 °C for a
time effective to produce the reaction products. The progress of the reaction can
be monitored and targeted to produce the desired product by measuring the amine equivalent
weight and the epoxy equivalent weight of the reactant mixture. Generally, the reaction
mixture is heated until the epoxy equivalents equal to the amine equivalents added
are consumed which is generally one hour or greater. stepwise or at the same time
in any order. If desired the surfactant can be recovered from the reaction mixture
or made "in-situ". More than one epoxy resin can be reacted with the amidoamine. The
preferred amidoamine can be prepared by reacting an acid-terminated polyalkylene glycol-containing
compound having the formula
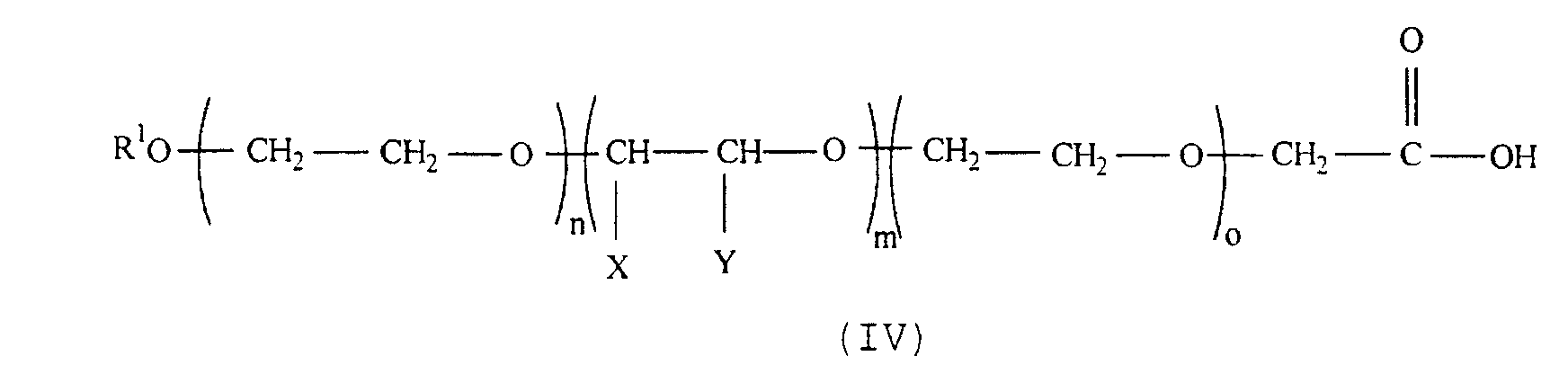
or
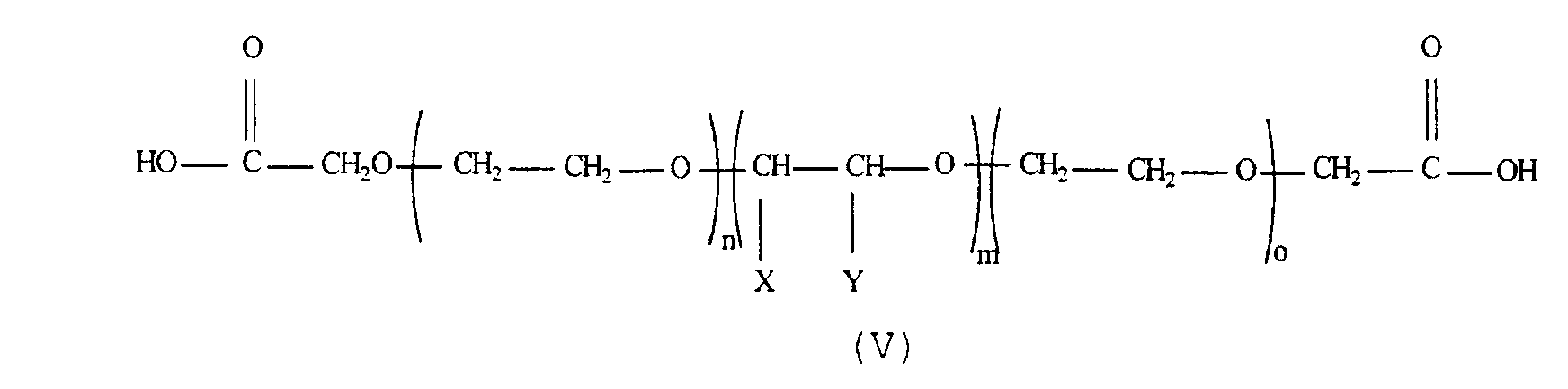
or
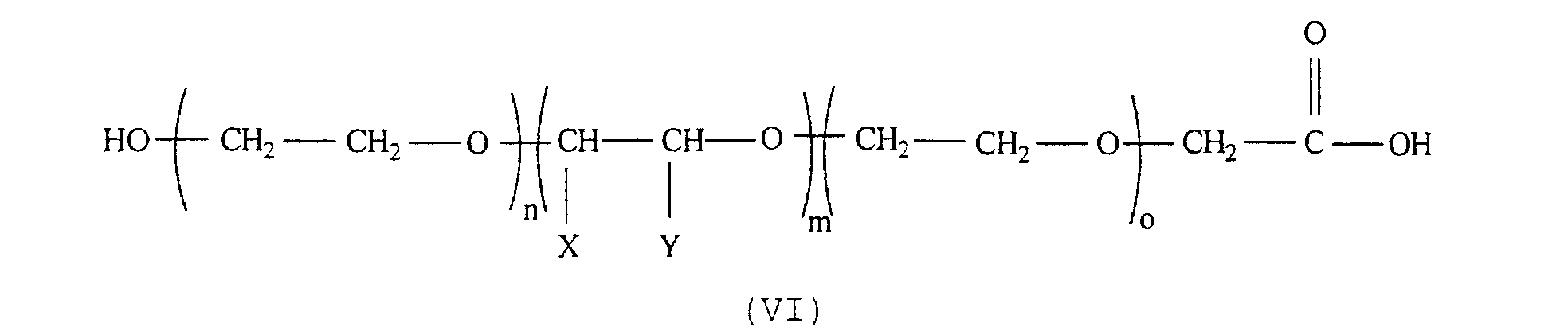
wherein R
1 is an alkyl, aryl, or arylalkyl group having 1 to 15 carbon atoms, n, m, and o are
as described above, and at least one diamine in an amine to acid equivalent ratio
of 6:1 to 25:1. Preferred diamine has the formula:
H
2N―R
2―NH
2 (VII)
wherein R
2 is as defined above. Examples of suitable diamines include for example, m-xylylenediamine,
1,3-bis-aminomethylcyclohexane, 2-methyl-1,5-pentanediamine, 1-ethyl-1,3-propanediamine,
ethylenediamine, diethylenetriamine, triethylenetetramine, polyoxy-propylenediamines,
2,2(4),9-trimethyl-1,6-hexanediamine, isophorone diamine, 2,9(6)-toluenediamine, 1,6-hexanediamine,
and 1,2-diaminocyclohexane.
[0010] The acid-terminated polyalkylene glycol-containing compound or oxidized polyalkylene
glycol can be produced by oxidation of a polyethylene glycol monoalkylether or a monoalkylether
of a block copolymer of ethylene oxide and propylene oxide or butylene oxide ("polyalkylene
glycol") or by at least a partial oxidation of a polyethylene glycol, or a block copolymer
of ethylene oxide and propylene oxide or polybutylene oxide ("polyalkylene glycol").
[0011] The acid-terminated polyalkylene glycol-containing compounds or oxidized polyalkylene
glycol can be produced by oxidation of the polyalkylene glycols including, but not
limited to, the processes described in U.S. Patent Nos. 5,250,727 and 5,166,423. Generally,
oxygen-containing gas is added to the polyalkylene glycol in the presence of a free
radical (e.g., 2,2,6,6-tetramethyl-1-piperidinyloxy) and an inorganic acid (e.g.,
nitric acid) to produce the carboxylic acid until at least one hydroxyl group per
molecule, or if diacid-terminated polyalkylene glycol is desired substantially all
of the alcohol groups, are oxidized to carboxylic acid groups. Acid-terminated polyalkylene
glycol-containing compound can also be made by Williamson ether synthesis where a
polyalkylene glycol is reacted with chloroacetic acid and/or esters in the presence
of a base.
[0012] The epoxy resins useful in producing the surfactants can be any reactive epoxy resin
having a 1,2-epoxy equivalency (functionality) preferably, on the average, greater
than 0.8 epoxide group per molecule, in some application preferably at least 1.5,
to preferably 6.5 epoxide groups per molecule. The epoxy resin can be saturated or
unsaturated, linear or branched, aliphatic, cycloaliphatic, aromatic or heterocyclic,
and may bear substituents which do not materially interfere with the reaction with
the carboxylic acid. Such substituents can include bromine or fluorine. They may be
monomeric or polymeric, liquid or solid, but are preferably liquid or a low melting
solid at room temperature. Suitable epoxy resins include glycidyl ethers prepared
by reacting epichlorohydrin with a compound containing at least 1.5 aromatic hydroxyl
groups carried out under alkaline reaction conditions. Examples of other epoxy resins
suitable for use in the invention include monoepoxies, diglycidyl ethers of dihydric
compounds, epoxy novolacs and cycloaliphatic epoxies. Generally epoxy resins contain
a distribution of compounds with a varying number of repeat units. Further, the epoxy
resin can be a mixture of epoxy resins. In one such embodiment, the epoxy resin can
comprise a monoepoxide resin and a di-and/or a multi-functional epoxy resin, preferably
an epoxy resin having a functionality of from 0.7 to 1.3 and an epoxy resin having
a functionality of at least 1.5, preferably at least 1.7, more preferably from 1.8
to 2.5. The mixture can be added or reacted with the amidoamine stepwise or simultaneously.
[0013] Commercial examples of preferred epoxy resins include, for example, EPON Resins DPL-862,
828, 826, 825, 1001, 1002, EPONEX Resin 1510, HELOXY Modifiers 32, 62, 63, 64, 65,
67, 68, 71, 107, 116, EPON Resin DPS155, EPON Resin HPT 1050, CARDURA Resin E-10 and
ERL-4221, -4289, -4299, - 4234 and -4206 epoxy resins (EPON, EPONEX, HELOXY, CARDURA
and ERL are trademarks).
[0014] The epoxy resin component can be any epoxy resin having a functionality of greater
than 0.8 epoxide group per molecule, preferably at least 1.2 epoxide group per molecule,
preferably at most to 6.5 epoxide group per molecule. These epoxy resins include those
mentioned above for use in preparing the surfactant. Suitable epoxy resins include
glycidyl ethers prepared by reacting epichlorohydrin with a compound containing, on
the average, greater than one hydroxyl group carried out under alkaline reaction conditions.
Examples of epoxy resins suitable for use in the invention include in addition to
the epoxy resins mentioned above, polyglycidyl esters of polycarboxylic acids, and
glycidylmethacrylate-containing acrylic resin. Polyglycidyl esters of polycarboxylic
acids are mentioned below.
[0015] In a typical process to prepare the aqueous dispersion, the amount of the epoxy resin
component ii) is from 20 to 75 percent by weight, preferably from 55 to 65 percent
by weight, based on the total dispersion. Generally, i) water and ii) an epoxy resin
having a functionality of greater than 0.8 epoxide group per molecule are mixed under
conditions effective to provide an oil-in-water emulsion in the presence of iii) from
0.1, preferably from 0.5, more preferably from 1, to 20, most preferably to 6 weight
percent, based on the epoxy resin of at least one polyoxyalkylene surfactant mentioned
above and iv) an acetone-free solvent solution to produce a resin-surfactant emulsion.
To this emulsion, a solvent mixture comprising i) acetone and ii) a non-volatile hydrophobic
liquid resin or resin modifier is added to produce the aqueous dispersion. It has
been found that by adding the solvent mixture after the formation of the emulsion
(inversion) accelerates the time to provide a aqueous dispersion having the suitable
particle size of less than 1µ and consistency to provide good gloss for the final
coating product. Thus, it is beneficial to add the solvent before it reaches the target
particle size to reduce process time.
[0016] Acetone is preferably present in an amount of from 0.5, more preferably from 1, up
to preferably 5, more preferably up to 3% of the total aqueous dispersion. The non-volatile
hydrophobic liquid resin or resin modifier is present in an amount of 1 to 25%, preferably
1 to 3%, based on the total amount of components a)ii), a)iii), and b)ii).
[0017] The hydrophobic liquid resin or resin modifier can be any non-volatile, hydrophobic
compound which is liquid, flowable at room temperature, whether neat or in a hydrophobic
solution such as xylene or butanol. A substance is non-volatile when it meets the
definition according to ASTM D 2369-93 or ASTM D 3960-93. For a coating composition,
the hydrophobic liquid resin or resin modifier must be compatible (e.g. does not detract
from corrosion resistance, or high gloss, etc.) with the curing agents in the coating
composition, for example, such as amine curing agents. Preferable hydrophobic liquid
resin or resin modifier includes, for example, an aliphatic monoglycidylether, urea
formaldehyde resin or an aliphatic monoglycidylester. Preferable hydrophobic liquid
resin or resin modifier can be, for example, HELOXY 7 Modifier (alkyl C
8-C
10 glycidyl ether), HELOXY 9 Modifier (C
10-11 alkyl glycidylether) available from Shell Chemical Company and BEETLE 216-10 Resin
(BEETLE is a trademark for alkylated urea formaldehyde high solids solution).
[0018] These dispersions can be made by adding the surfactant and water to the epoxy resin
to be dispersed or by producing the surfactant "in-situ" as described above. These
dispersions can also be made by adding the epoxy resin to the amidoamine precursor
and water. The surfactant can be produced in-situ by adding amidoamine precursor to
the epoxy resin at an effective temperature to react the amidoamine and epoxy resin,
or by adding the amidoamine precursor to a difunctional epoxy resin and dihydric phenol
before or during the advancement reaction as described above.
[0019] The epoxy resin coating composition of the invention may include other additives,
such as elastomers, stabilizers, extenders, plasticizers, pigments, pigment pastes,
antioxidants, leveling or thickening agents, defoaming agents and/or cosolvents, wetting
agents, cosurfactants, reactive diluents, fillers, catalysts, and the like. The aqueous
dispersion can contain a monoepoxide diluent as reactive diluent.
[0020] Preferable monoepoxide diluents are those which contain a water-immiscible glycidated
C
8-20 aliphatic alcohol, C
1-18 alkylphenol glycidylether, or glycidated VERSATIC acid (VERSATIC is a trademark).
The monoepoxide component can contain alicyclic and aromatic structures, as well as
halogen, sulfur, phosphorus, and other such heteroatoms. Reactive diluents can be,
for example, epoxidized unsaturated hydrocarbons such as decene and cyclohexene; glycidyl
ethers of monohydric alcohols such as 2-ethylhexanol, dodecanol and eicosanol; glycidyl
esters of monocarboxylic acids such as hexanoic acid; acetals of glycidaldehyde; and
the like. The preferred reactive diluent is glycidyl ether of monohydric C
8-14 aliphatic alcohols.
[0021] Useful coating compositions can be obtained by mixing an amine-functional epoxy resin
curing agent with the aqueous epoxy resin dispersion mentioned above.
[0022] The epoxy resin curing agent can be any curing agent effective to cure (or crosslink)
the epoxy resin dispersed in the aqueous solution. These curing agents are generally
water compatible (i.e., dilutable and/or dispersible). Suitable curing agents for
use with the dispersions include those typically employed with epoxy resins, such
as aliphatic, araliphatic and aromatic amines, polyamides, amidoamines and epoxy-amine
adducts. They exhibit varying levels of compatibility with water, depending upon the
nature of the starting materials employed for their preparation. In many cases, partial
ionization with acetic acid, propionic acid and the like is required to effect or
improve water compatibility or emulsifiability.
[0023] Preferably for curing at room temperature or lower temperatures an epoxide equivalent
to amine hydrogen equivalent ratio of from 1:0.75 to 1:1.5 is employed and more preferably
from 1:0.9 to 1:1.25. Suitable polyalkylene amines curing agents are those which are
soluble or dispersible in water and which contain more than 2 active hydrogen atoms
per molecule such as diethylenetriamine, triethylenetetramine, tetraethylenepentamine,
etc. Other suitable curing agents include, for example, 2,2,4- and/or 2,4,4-trimethyl-hexamethylene-diamine,
1,6-hexanediamine, 1-ethyl-1,3-propanediamine, 2,2(4),4-trimethyl-1,6-hexanediamine,
bis(3-aminopropyl)-piperazine, N-aminoethylpiperazine, N,N-bis(3-aminopropyl)ethylenediamine,
2,4(6)-toluenediamine and also cycloaliphatic amines such as 1,2-diaminocyclohexane,
1,4-diamino-3,6-diethylcyclohexane, 1,2-diamino-4-ethylcyclohexane, 1,4-diamino-3,6-diethyl-cyclohexane,
1-cyclohexyl-3,4-diamino-cyclohexane, isophoronediamine, norboranediamine, 4,4'-diamino-dicyclohexylmethane,
4,4'-diaminodicyclohexylmethane, 4,4'-diaminodicyclohexylpropane, 2,2-bis(4-aminocyclo-hexyl)-propane,
3,3'-dimethyl-4,4'-diaminodicyclohexyl-methane, 3-amino-1-cyclohexaneaminopropane,
1,3- and 1,4-bis(amino-methyl)-cyclohexane. As araliphatic amines, in particular those
amines are employed in which the amino groups are present on the aliphatic radical
for example m- and p-xylylene-diamine or their hydrogenation products. The amines
may be used alone or as mixtures.
[0024] Suitable amine-epoxide adducts are, for example, reaction products of diamines such
as, for example, ethylenediamine, diethylenetriamine, triethylenetetramine, m-xylylenediamine
and/or bis(aminomethyl)cyclohexane with terminal epoxides such as, for example, polyglycidyl
ethers of polyhydric phenols listed above.
[0025] Polyamidoamine curing agents can be obtained, for example by reacting polyamines
with polycarboxylic acids such as dimerized fatty acids. In addition to the above
polyamines, the water-soluble polyoxypropylene-diamines with molecular weights of
190 to 2,000 and also the readily water-dispersible curing agents, such as are described
in the German Auslegeschrift 2,332,177 and the European Patent 0,000,605, for example,
modified amine adducts are preferably employed. To cure the coating to completion,
the coatings obtainable from these dispersions may also be heated for 30 to 120 minutes
at an elevated temperature, preferably within the range of 50 °C to 120 °C.
[0026] For higher temperature cure applications, aminoplast resins can be used as curing
agents for epoxy resins having a high equivalent weight, e.g. greater than 700. Generally,
from 5, preferably from 10, to 40, preferably to 30 weight percent of aminoplast resins,
based on the combined weight of the epoxy resin and aminoplast resin, is used. Suitable
aminoplast resins are the reaction products of ureas and melamines with aldehydes
further etherified in some cases with an alcohol. Examples of aminoplast resin components
are urea, ethylene urea, thiourea, melamine, benzoguanamine and acetoguanamine. Examples
of aldehydes include formaldehyde, acetaldehyde and propionaldehyde. The aminoplast
resins can be used in the alkylol form but, preferably, are utilized in the ether
form wherein the etherifying agent is a monohydric alcohol containing from 1 to 8
carbon atoms. Examples of suitable aminoplast resins are methylol urea, dimethoxymethylol
urea, butylated polymeric urea-formaldehyde resins, hexamethoxymethyl melamine, methylated
polymeric melamine-formaldehyde resins and butylated polymeric melamine-formaldehyde
resins.
[0027] Commercial examples of water-compatible curing agents include EPI-CURE 8535, 8536,
8537, 8290 and 8292 Curing Agents, ANQUAMINE 401, CASAMID 360 and 362 curing agents;
EPILINK 381 and DP660 curing agents; Hardener HZ350, Hardeners 92-113 and 92-116 (Ciba
Geigy); BECKOPOX EH659W, EH623W, VEH2133W curing agents and EPOTUF 37-680 and 37-681
curing agents (EPICURE, ANQUAMINE, CASAMID, EPILINK, BECKOPOX and EPOTUF are trademarks).
[0028] The curable epoxy resin composition can be cured at a temperature within the range
of from 5 °C, preferably from 20 °C, to 200 °C, preferably to 175 °C for a time effective
to cure the epoxy resin.
[0029] Preferred embodiments of the aqueous dispersions of the present invention are formed
by those wherein the acetone is present in an amount of 0.5 to up to 5 %wt of the
total aqueous dispersion. Preferably the non-volatile hydrophobic liquid resin or
resin modifier is present in an amount of 1 to 25 %wt based on the total amounts of
components a) ii), a) iii), and b) ii), and more preferably in an amount of from 1
to 10 %wt.
[0030] The non-volatile hydrophobic liquid resin or resin modifier more preferably is an
aliphatic monoglycidyl ether, urea formaldehyde resin or an aliphatic monoglycidyl
ester.
[0031] More preferred aqueous dispersions of the present invention comprise a surfactant
containing a polyoxyethylene or polyoxyethylene-oxypropylene block copolymer segment.
Most preferably this surfactant is an addition product comprising diglycidyl ether
of dihydric phenol, dihydric phenol and a diglycidyl ether of polyoxyalkylene glycol.
[0032] The aqueous dispersions of the instant invention and curing agents described above
can serve as components of paints and coatings for application to substrates such
as, for example, metal and cementitious structures. To prepare such paints and coatings,
these resins are blended with primary, extender and anti-corrosive pigments, and optionally,
additives such as surfactants, antifoam agents, rheology modifiers and mar and slip
reagents. The selection and amount of these pigments and additives depends on the
intended application of the paint and is generally recognized by those skilled in
the art.
[0033] Examples of primary pigments include rutile titanium dioxide, such as KRONOS 2160
and TI-PURE R-960, buff titanium dioxide, red iron oxide, yellow iron oxide and carbon
black. Examples of extender pigments include calcium meta silicate, such as 10ES WOLLASTOKUP,
barium sulfate, such as SPARMITE and aluminum silicate, such as ASP 170 (KRONOS, TI-PURE,
WOLLASTOKUP, SPARMITE and ASP are trademarks). Examples of anticorrosive pigments
include calcium strontium phosphosilicate, such as HALOX SW111, zinc ion modified
aluminum triphosphate, such as K-WHITE 84 and basic aluminum zinc phosphate hydrate,
such as HEUCOPHOS ZPA (HALOX, K-WHITE and HEUCOPHOS are trademarks).
[0034] Additional surfactants can be included in waterborne epoxy paints and coatings to
improve both pigment and substrate wetting. Such surfactants are typically nonionic,
examples of which include TRITON X-100 and TRITON X-405, PLURONIC F-88 and SURFYNOL
104 (TRITON, PLURONIC and SURFYNOL are trademarks).
[0035] Anti-foam agents and defoamers suppress foam generation during manufacture of the
paint or coating. Useful defoamers include DREWPLUS L-475, DE FO PF-4 Concentrate
and BYK 033 (DREWPLUS, DE FO and BYK are trademarks).
[0036] Rheological additives are employed to obtain proper application properties. There
are three types of additives that provide the desired thickening and shear thinning
required for waterborne epoxy coatings; namely, hydroxyethylcellulose, organically
modified hectorite clays and associative thickeners. NATROSOL 250 MBR and NATROSOL
Plus are examples of modified hydroxyethyl-cellulosics and BENTONE LT is representative
of a hectorite clay (NATROSOL and BENTONE are trademarks). ACRYSOL QR-708 is an often
useful associative thickener (ACRYSOL is a trademark).
[0037] Mar and slip agents improve early resistance to abrasion from scrubbing or light
foot traffic. Polydimethylsiloxanes and polyethylene waxes are used in this regard.
An example of a commercially available wax is MICHEM LUBE 182 (MICHEM LUBE is a trademark).
[0038] The curable paint and coating compositions can be applied to a substrate by brush,
spray, or rollers.
[0039] The aqueous dispersions produced by the instant invention can also be used as components
of adhesives and fibre sizing.
[0040] The following illustrative embodiments describe the process of the invention and
are provided for illustrative purposes and are not meant as limiting the invention.
[0041] Examples A-E demonstrate the process of the invention. The formation of the aqueous
dispersion is compared with where acetone is added prior to the emulsification in
the comparative examples.
[0042] EPON Resin 828 (a diglycidyl ether of dihydric phenol having epoxy equivalent weight
of 187-188) and EPON Resin 1001F (an epoxy resin formed by advancing a diglycidyl
ether of dihydric phenol with bisphenol-A having epoxy equivalent weight of 525-550),
HELOXY Modifier 62 (ortho-cresol glycidyl ether), HELOXY Modifier 7 (alkyl C
8-C
10 glycidyl ether), HELOXY Modifier 9 (C
10-11 alkyl glycidylether) or liquid epoxy diluent were obtained from Shell Chemical Company
Polyethylene glycol monomethyl ether and polyethylene glycol were obtained from Aldrich
Chemical Co. 2-methyl-1,5-pentanediamine (DYTEK A) was obtained from DuPont (DYTEK
is a trademark).
I. Viscosity Viscosities were determined on the obtained emulsion or dispersion by means of a
BROOKFIELD SYNCHRO LECTRIC Viscometer from Brookfield Engineering Laboratories (BROOKFIELD
SYNCHRO LECTRIC is a trademark).
II. Particle Size The determination of emulsion and dispersion particle sizes was accomplished with
a by a COULTER LS230 particle size analyzer (Area mean) (COULTER is a trademark).
All particle size data is reported in microns, µ.
III. Percent Solids The percent solids of all products were measured by spreading a 0.5 gram sample of
the product onto aluminum foil, placing the coated foil into a forced draft oven,
held at 120 °C, for 10 minutes, determining the residual weight of the film by rationing
the residual weight to the total weight and multiplying by 100.
IV. Weight per Epoxide The weight per epoxide (WPE or EEW) of all products was determined by drying a weighed
amount of sample by means of azeotropic distillation with methylene chloride then
titrating the residue by known methods and correcting for percent solids to determine
the WPE at 100% solids content.
Example 1 (Referential)
Preparation of alpha-(2-carboxymethyl)-omega-methoxypoly-(oxy-1,2-ethanediyl)
[0043] To a 3000 ml, four neck flask, fitted with a stirrer, thermocouple, air sparge tube,
condenser and addition funnel, was added 495.6 grams (0.099 equiv.) of polyethylene
glycol monomethyl ether of approximately 5000 Mn (Aldrich Chemical Co.), 15.4 grams
(0.099 equiv) of 2,2,6,6-tetramethyl-1-piperidinyloxy, free radical (Aldrich Chemical
Co., TEMPO, free radical) and 1000 grams of dichloromethane. The mixture was heated
to reflux, then air was introduced into the mixture through the sparge tube. Next,
concentrated nitric acid (15.4 grams) was then added over 15 minutes and the mixture
was held at reflux for 19 hours. Volatiles were then removed by means of a rotary
evaporator. The residue solidified upon cooling. It was ground to a powder, washed
with 2-propanol and dried in a vacuum oven at 40 °C to constant weight. NMR Analysis
confirmed conversion of hydroxyl to carboxyl functionality. The solid possessed an
acid equivalent weight of 5025.
Example 2 (Referential)
Preparation of Partially End Capped Amidoamine
[0044] Poly(ethylene glycol), 4,600 average molecular weight was oxidized to the corresponding
acid using 4-Hydroxy - 2,2,6,6-teramethyl-1-piperidinyloxy free radical in a similar
manner to that described in Example 1. The resulting material had a weight per equivalent
acid of 2735. This material was then amidified with 10 equivalents of primary amine
per equivalent acid using DYTEK A amine. This amido amine was isolated; 25% of the
primary amine was capped with CARDURA E-10 epoxy and then diluted to approximately
65 %NV with deionized water.
Example A
Epoxy resin dispersion using surfactant from Example 2
[0045] To a 3-liter resin flask were added 532.76 grams EPON Resin 828, 196.82 grams bisphenol
A and 0.27 grams of ethyltriphenylphosphonium iodide. This catalyzed epoxy was then
advanced to an epoxy equivalent weight of 675 at 170-191 °C. This batch was allowed
to cool to 149 °C and the following additions were made in respective order; 80.53
grams of EPON Resin 828, 24.55 grams of ARCOSOLV PM glycol ether and 89.12 grams of
the surfactant solution described in Example 2 above (ARCOSOLV is a trademark). The
batch solution was allowed to cool to 104 °C over 2 hours and then 110.19 grams of
deionized water was added over 10 minutes with good mixing. Then the batch was mixed
for an additional 30 minutes while the temperature dropped to 90 °C. During this time
the resin became emulsified in the aqueous continuous phase. After an additional 10
minutes of mixing the emulsion particle size was measured by a COULTER LS230 particle
size analyzer. At this point the surface area mean particle size was 1.026 microns
with 90% <2.502 and 99% <4.753 microns. To this emulsion was added 16.35 grams of
HELOXY 9 liquid epoxy diluent and 27.76 grams of acetone over 10 minutes at 76-84
°C. The particle size was measured again 25 minutes after this addition and it was
surface area mean particle size 0.621 microns, 90% <1.332 and 99% <2.529. After the
batch was mixed 55 minutes (from the addition of HELOXY 9/acetone) at 76-81 °C the
surface area mean particle size was 0.526 micron with 90% <0.923 and 99% <2.234. The
batch was then thinned with additional 475 grams deionized water while allowing the
temperature to drop to 85 °C. The final properties of this batch measured at 25 °C
after filtering through an 80 mesh polyester filter were 42,000 cp. viscosity, 57.4%
NV and surface area mean particle size 0.411 microns, 90% <0.572 and 99% <0.865. As
shown in Table I below, the invention process time saving was 60 minutes.
Example B
Epoxy resin dispersion using surfactant from Example 2
[0046] The same composition as Example A was scaled up to 41,635 liters (11 gallons) using
the same invention process. The particle size dropped very quickly after the HELOXY
9 liquid epoxy diluent and acetone were added (B-1) at 17 hours after inversion reaching
a particle size of 0.73 microns in 22 hours and (B-2) 1 hour after inversion reaching
a particle size of 0.52 microns in 22 hours.
Example C-E
Epoxy resin dispersions using PLURONIC F88, glycidated polyoxyalkylene glycol
[0047] Epoxy resin dispersions using the surfactants; PLURONIC F-88 (polyoxyethylene oxypropylene
glycol from BASF having MW of 10,000), an addition product of diglycidyl ether of
dihydric phenol, dihydric phenol and a diglycidyl ether of polyoxyalkylene glycol
as described in Example 1 of U.S. Patent No. 4,315,044; surfactant from Example 2
as Examples C, D, and E, respectively, were made in a similar manner to Example A
except the surfactants were replaced weight per weight and for Example E, the HELOXY
9 Modifier was replaced by BEETLE 216-10 Resin from Cytec Industries (Urea-formaldehyde
resin) on a non-volatile weight per weight basis. The results are listed in the Table
III below.
Table I
EXAMPLE NO. |
Particle Size BEFORE Solvent ADD |
Particle Size AFTER ADD |
Particle Size AFTER ADD |
FINAL Particle Size |
Example C |
1.60 |
45 minutes 1.20 |
|
0.83 |
Example D |
2.782 |
35 minutes 0.761 |
|
0.786 |
Example E |
1.222 |
25 minutes 0.878 |
40 minutes 0.739 |
Final 0.708 |
Comparative Example A
Preparation of a dispersion without using the process of the invention
[0048] The same composition as Example A was made where acetone and HELOXY 9 Modifier were
added before any water was added to emulsify the batch. EPON Resin 828, 613.29 grams
is advanced with 196.82 grams of Bisphenol A to an epoxy equivalent weight of 535.
ARCOSOLV PM glycol ether, 24.55 grams is added to the resin. This resin solution is
then allowed to react with the Example 2 surfactant solution, 89.12 grams for one
hour at 102 °C (215 °F). Then a blend of HELOXY 9 Modifier, 16.35 grams and acetone
27.76 grams are admixed into the batch while allowing the batch to cool to 77 °C (170
°F). The resin is then allowed to emulsify by mixing in 119.11 grams of deionized
water. After the resin is emulsified it is mixed for 25 minutes at ∼73 °C (∼165 °F)
and then checked for particle size. The mean surface area particle size at this point
is 0.784 microns. After an additional 2 hours 25 minutes of mixing the mean surface
area particle size is 0.734 microns. As shown in the table immediately below, the
comparative process does not reach as low as particle size as the process of the invention
even with double the particle size reduction processing time. The final properties
of this standard process batch were: 8,640 cP, 54.3% NV and mean average surface area
particle size of 0.82.
Table II
|
10 mins |
25 mins |
50 mins |
85 mins |
145 mins |
Final |
Time Saved |
Comparative Example A |
|
0.784 |
|
|
0.734 |
0.82 |
|
Example A |
1.021 |
|
0.621 |
0.526 |
|
0.41 |
60 mins |
All listed data were determined as COULTER LS230 surface area mean particle size |
Comparative Example B
Preparation of an dispersion without using the process of the invention
[0049] This batch was made with the same composition as comparative Example A: the acetone
and HELOXY 9 Modifier were added before any water was added to emulsify the resin.
This batch, (Comparative Example B-1) required greater than 20 hours of mixing to
lower the Dn to <1.0 micron particle size. In a second attempt (Comparative Example
B-2), to reach a particle size epoxy dispersion that would allow paints to be made
with acceptable gloss it took over 50 hours to process. The results are shown in Table
III below.
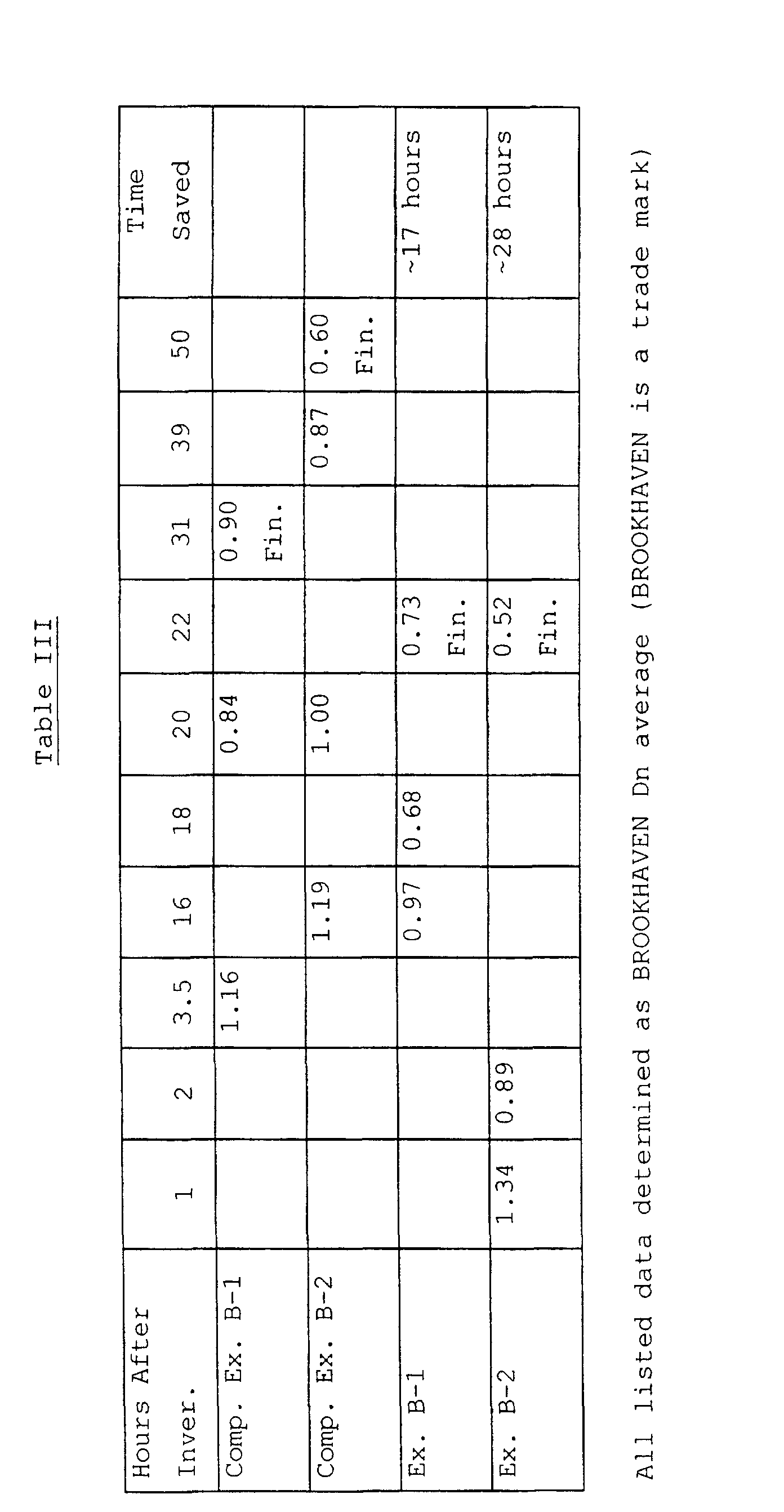
Example I
Two Component Paint Formulations
[0050] This white enamel paint performance as shown for Example B-2 epoxy dispersion with
the curing agent E, described below, was obtained by dispersing the titanium dioxide
into the curing agent to which acetic acid, pigment wetter and defoamer were added.
The acetic acid was used at a level that was 0.12 equivalents acetic acid per total
equivalents of titrateable nitrogen of the curing agent. The pigment to binder ratio
in this paint was 0.7:1.0; the VOC was 1.2 pounds per gallon (composed of acetone
and dipropylene glycol normal butyl ether in a weight ratio of 1:1 and the existing
VOC introduced into the paint by the Example B-2 epoxy dispersion); and the combining
ratio of equivalents of epoxy to amine hydrogen was 1.1 to 1.0.
[0051] Curing Agent E is a curing agent dispersion described as follows:
[0052] A 4 necked round-bottomed glass flask was equipped with a condensor having a water
trap, a nitrogen inlet, a resin solution inlet and the amine inlet. The flask was
flushed with nitrogen.
[0053] The amine (triethylenetetramine) (468.72 g) was charged into the reactor and heated
to 93 °C. At 93 °C a metered addition of the resin solution EPON Resin 1001-X-75 (670
g) to the amine was started at such a rate that the temperature of the reaction mixture
did not exceed 121 °C.
[0054] After completion of the addition, the mixture is kept at 93 °C for additional 60
minutes. Excess amine and xylene were distilled off at about 140 °C under about 1.5
mmHg. The reaction product had an amine value of about 300 mg KOH/g. Subsequently
the reaction mixture was cooled to 121 °C and 80.63 g of acid terminated polyalkylene
glycol surfactant (in solid form), representing a final surfactant level of about
3.2% on solids resin weight, were charged into the flask and heated to about 200 °C
for 2 hours. The acid value of the reaction mixture was measured after 2 hours of
reaction and a value of 2 mg KOH/g was found indicating that the reaction was completed.
[0055] Subsequently the reaction mixture was cooled to 93 °C, after which 176.5 g of HELOXY
62 modifier, representing about 1 equivalent of epoxy per primary amine on the amine
adduct, were added to the reaction vessel at a rate such that the maximum temperature
did not exceed 121 °C. After completion of the addition, the reaction was held at
93 °C for 60 minutes. The reaction mixture was allowed to cool to about 78 °C. Water
was dropwise added until the reaction mixture was inverted from a water in oil to
an oil in water emulsion. Further water was added to a total amount of 882.37 g to
obtain a final solids content of 45% by weight. The average particle size was 0.5µ.
[0056] Also shown in Table IV, the paint performance using the process of the invention
with a curing agent dispersion which illustrates the excellent development of the
paint protective performance properties of this invention.
Table IV
Epoxy |
Curing Agent |
Set to Touch |
Cure at RT |
60° Gloss% |
Pencil Hardness |
MEK D. Rubs |
Example B-2 |
|
E 0.5 hour |
5 days |
95 |
F |
60 |
[0057] The gloss for paint formulations using dispersions made by Examples B-1, B-2 and
Comparative Examples B-1 and B-2 in a similar manner is shown below in Table V.
Table V
* 20 degree/60 degree @ |
0.5 hours |
4 hours |
6 hours |
Comparative Example B-1 |
80/100 |
48/91 |
22/71 |
Example B-1 |
85/102 |
59/95 |
37/83 |
+ 20 degree/60 degree @ |
0.5 hours |
2.5 hours |
3.5 hours |
Comparative Example B-2 |
34/78 |
34/78 |
26/73 |
Example B-2 |
64/95 |
60/92 |
47/87 |
* 3 mil wet films |
+ 5 mil wet films |