[0001] Für die Herstellung von Werkzeugen, die im praktischen Einsatz korrosiven Medien
ausgesetzt sind und an die gleichzeitig hohe Anforderungen an ihre Härte gestellt
werden, werden martensitische, korrosionsbeständige Werkzeugstähle verwendet.
[0002] Spanende Fertigungsverfahren sind ein wesentlicher Bestandteil der industriellen
Produktionstechnologie und ein Hauptkostenträger bei der Herstellung von Werkzeugen
für die Kunststoffverarbeitung. Die wirtschaftliche Verwendbarkeit von Stählen der
eingangs genannten Art hängt daher wesentlich von ihrer Zerspanbarkeit und ihrer Korrosionsbeständigkeit
ab, welche wiederum entscheidend durch den Chromgehalt der Stähle beeinflußt wird.
Unter dem Begriff "Zerspanbarkeit" wird in diesem Zusammenhang die Eigenschaft eines
Werkstoffes verstanden, sich unter bestimmten Bedingungen spanend bearbeiten zu lassen.
[0003] Besondere Anforderungen an die Korrosionsbeständigkeit von Werkzeugen, die aus Stählen
der voranstehend erwähnten Art hergestellt sind, ergeben sich im Bereich der kunststoffverarbeitenden
Industrie. So führen Kontakte mit den dort eingesetzten Kühl- und Reinigungsmitteln,
der Umgebungsatmosphäre sowie mit den verarbeiteten Kunststoffen selbst in vielen
Fällen zu einer korrosiven Beanspruchung des jeweiligen Werkzeugs.
[0004] Ein rostfreier martensitischer Stahl mit guter Bearbeitbarkeit ist aus der EP 0 721
513 B1 bekannt. Der bekannte Stahl enthält 10 bis 14 Mass.-% Chrom. Zur Verbesserung
seiner Zerspanbarkeit weist er zudem mindestens 0,15 % Schwefel und 1,0 bis 3,5 %
Kupfer auf. Die Zugabe von Kupfer hat zusätzlich einen positiven Einfluß auf die Härte
der Legierung.
[0005] Neben dem in der erwähnten Europäischen Patentschrift beschriebenen Stahl ist eine
Vielzahl chromlegierter, korrosionsbeständiger Stähle bekannt, deren Chromgehalt zwischen
11,0 und 17,0 Mass.-% liegt. Es sind dies beispielsweise die mit den Werkstoffnummern
1.2080, 1.2082, 1.2083, 1.2085, 1.2201, 1.2314, 1.2316, 1.2319, 1.2361, 1.2376, 1.2378,
1.2379, 1.2380, 1.2436, 1.2601 in der StahlEisen-Liste bezeichneten Stähle. Regelmäßig
sind diese Stähle mit Kohlenstoff, Silizium und Mangan legiert. Wahlweise enthalten
sie außerdem Carbidbildner wie Molybdän, Vanadium oder Wolfram.
[0006] Die Verarbeitung der bekannten Stähle erfolgt in Abhängigkeit vom jeweiligen Kohlenstoff-
und Carbidgehalt. So werden die Stähle der in Rede stehenden Art zum einen vom Werkzeughersteller
im vergüteten Zustand mit einer Härte von 285 bis 325 HB verwendet. Bei dieser Härte
ist eine zerspanende Bearbeitung des Werkstoffs noch möglich. Zum anderen werden die
Stähle im weichgeglühten Zustand verarbeitet, wobei die Härte der Stähle dann maximal
250 HB beträgt. Derart weniger harte Stähle lassen sich zwar besser verarbeiten. Es
muß allerdings nach der Bearbeitung noch eine Wärmebehandlung durchgeführt werden,
um die üblicherweise erforderliche Einbauhärte von 46 bis 60 HRC zu erreichen. Anschließend
ist eine Fertigbearbeitung erforderlich.
[0007] Eine spanende Bearbeitung läßt sich bei den von den Anwendern geforderten hohen Endhärten
bei den bekannten Stählen nicht mehr wirtschaftlich durchführen. Dieses Problem wird
zwar durch die Verarbeitung im weichgeglühten Zustand mit nachgeschalteter Wärmebehandlung
gelöst. Ein Nachteil der abschließenden Wärmebehandlung besteht jedoch neben den für
diesen zusätzlichen Arbeitsgang anfallenden Kosten darin, daß es dabei zur Rißbildung
und zum Verzug des Bauteils infolge der Erwärmung kommen kann.
[0008] Ein weiterer Nachteil der bekannten, in der StahlEisen-Liste verzeichneten Stähle
ist ihre aufgrund des Kohlenstoffgehalts und der Legierungszusammensetzung verschlechterte
Schweißbarkeit. Eine gute Verschweißbarkeit ist jedoch gerade im Bereich der Kunststoffverarbeitung
unabdingbar. Häufig ist es in Folge von nachträglichen Änderungen der Gestaltung und
wegen erforderlich werdender Reparaturen notwendig, Schweißarbeiten an den Werkzeugen
vorzunehmen.
[0009] Zusätzlich erschwert wird die Bestimmung eines den Anforderungen in der Praxis, insbesondere
den sich bei der Kunststoffverarbeitung stellenden Problemen gerechtwerdenden Stahls
dadurch, daß ein solcher Stahl nicht nur korrosionsbeständig, gut zerspanbar und gut
schweißbar, sondern auch in ausreichendem Maße zäh sein muß, um die im praktischen
Betrieb auftretenden Kräfte aufnehmen zu können. Andernfalls besteht die Gefahr, daß
die auftretenden hohen Biege-, Torsions-, Druck- und Zugkräfte ebenfalls Risse verursachen.
[0010] Es hat sich gezeigt, daß die bekannten Stähle allen diesen Anforderungen gleichzeitig
nicht gerecht werden. So weisen aufgrund eines höheren Schwefelgehaltes gut zerspanbare
Stähle eine zu geringe Zähigkeit auf, während bei infolge einer Erhöhung des Kohlenstoffgehaltes
härteren Stählen die Korrosionsbeständigkeit vermindert ist. JP-A-01 215 489 offenbart
einen Stahl bestehend aus 0.05-0.17 % C, 0.01-1.5 % Si, 0.01-2% Mr, ≤ 0.025 % P, ≤
0.015% S, 8-12 % Cr, ≤ 0.8% Ni, 0.5-3% Mo, 0.5-3% W, 0.1-0.2% Nb, ≤ 0.04% Al, 0.03-0.05%
N, ≤ 0.010 and 0.0005-0.01 Ca, Rest Eisen.
[0011] Die Aufgabe der Erfindung besteht darin, einen insbesondere für die Herstellung von
Werkzeugen für die kunststoffverarbeitende Industrie geeigneten Stahl zu finden, der
bei hoher Härte und Korrosionsbeständigkeit eine den praktischen Anforderungen gerechtwerdende
Zähigkeit, Zerspanbarkeit und Schweißbarkeit aufweist. Darüber hinaus soll ein Verfahren
zur Herstellung von Zwischenprodukten aus einem solchen Stahl angeben werden. Unter
dem Begriff "Zwischenprodukt" werden in diesem Zusammenhang auch Langprodukte, Flachprodukte
oder andere Gegenstände verstanden, die anschließend einer weiteren Verarbeitung zugeführt
werden.
[0012] In Bezug auf den Werkstoff wird diese Aufgabe durch einen Stahl für insbesondere
korrosionsbeanspruchte Werkzeuge gelöst, der folgende Zusammensetzung aufweist (in
Mass.-%) :
- C:
- mindestens 0,02 und höchstens 0,12 %,
- Si:
- höchstens 1,5 %,
- Mn:
- mehr als 1,0 - 2,50 %,
- P:
- höchstens 0,035 %,
- S:
- mindestens 0,04 % und weniger als 0,15 %,
- Cr:
- mehr als 8,0 % und weniger als 12 %,
- Mo:
- mehr als 0,0 % und höchstens 0,20 %,
- V:
- mehr als 0,0 % und höchstens 0,25 %,
- Nb:
- mehr als 0,1 % und höchstens 0,5 %,
- N:
- mindestens 0,02 und höchstens 0,12 %,
- Ni:
- höchstens 0,5 %
- B:
- höchstens 0,005 %,
- Cu:
- höchstens 0,3 %,
- Al:
- höchstens 0,035 %,
- Sn:
- höchstens 0,035 %,
- As:
- höchstens 0,02 %,
mindestens eines der Elemente Ca, Mg oder Ce, wobei die Summe der Gehalte an diesen
Elementen mehr als 0,0002 % und höchstens 0,015 % beträgt,
Rest Eisen und unvermeidbare Verunreinigungen.
[0013] Der erfindungsgemäße nioblegierte Werkzeugstahl weist eine optimierte Kombination
von Zerspanbarkeit, Härte, Korrosionsbeständigkeit, Schweißbarkeit und Zähigkeit auf.
Er erreicht Härtelagen, die zwischen 300 und 450 HB liegen. Trotz des relativ hohen
Schwefelgehalts weist er eine für Stähle der gattungsgemäßen Art gute Zähigkeit auf,
die den in der Praxis sich stellenden Anforderungen genügt.
[0014] Zur Verbesserung der Zerspanbarkeit sind erfindungsgemäße Stähle schwefellegiert,
dessen Anteil jeweils weniger als 0,15 Mass.-% beträgt. Vorzugsweise weist der Stahl
dabei mindestens 0,04 Mass.-% auf, wodurch eine gute Zerspanbarkeit sicher gewährleistet
werden kann. Noch bessere Zerspanbarkeiten können bei Berücksichtigung der sonstigen
an die Zusammensetzung gestellten Bedingungen dann erreicht werden, wenn erfindungsgemäßer
Stahl mindestens 0,07 Mass.-% Schwefel enthält.
[0015] Trotz eines derart bemessenen Schwefelanteils weist erfindungsgemäßer Stahl eine
gute Zähigkeit auf. Dies wird dadurch erreicht, daß der Stahl zusammen mit dem Schwefel
wenigstens eines der Elemente Calcium, Mangan oder Cer in Mengen enthält, deren Summe
mehr als 0,0002 jedoch höchstens 0,015 Mass.-% beträgt. Diese Elemente ermöglichen
die Einformung von Sulfiden in die Matrix des Stahls und führen so zur Verbesserung
seiner Zähigkeit. Erreichen läßt sich dies beispielsweise zielsicher dann, wenn der
erfindungsgemäße Stahl 0,001 - 0,009 Mass.-% Calcium enthält.
[0016] Durch die Verwendung niedriger Kohlenstoffgehalte von maximal 0,12 Mass.-% sowie
niedriger Stickstoffgehalte von höchstens 0,12 Mass.-% und eines Niobgehalt von 0,11
bis 0,5 Mass.-% werden bei erfindungsgemäßem Stahl Hartphasen gebildet, welche zur
erreichten Härte von 300 bis 450 HB beitragen. Gleichzeitig werden die betreffenden
Hartphasen in besonders feiner und gleichmäßiger Verteilung ausgeschieden, was einen
positiven Einfluß auf die Zähigkeitseigenschaften hat.
[0017] Besonders deutlich machen sich diese vorteilhaften Eigenschaften des Legierens mit
Niob bemerkbar, wenn der Niobgehalt so eingestellt wird, daß der Härtefaktor H
f bei erfindungsgemäßem Stahl folgende Bedingung erfüllt:

wobei sich der Härtefaktor H
f nach der Formel

berechnet und mit %Nb der jeweilige Nb-Gehalt des Stahls bezeichnet ist. Bei einer
solchen Bemessung des Niobgehaltes wird der vorhandene Kohlenstoff und Stickstoff
durch das Element Niob weitgehend zu Hartphasen abgebunden, so daß das bei erfindungsgemäßem
Stahl mit einem Gehalt von weniger als 12 % in der Matrix enthaltene Chrom voll zur
Bildung von korrosionshemmenden Passivschichten zur Verfügung steht. Auf diese Weise
weist erfindungsgemäßer Stahl trotz der relativ geringen Chromgehalte bei gleichzeitig
hoher Härte eine hervorragende Korrosionsbeständigkeit auf.
[0018] Bei erfindungsgemäßem Stahl sind zudem die Gehalte an solchen Elementen, die zur
Rißbildung in der Schweißnaht führen könnten, auf ein Minimum abgesenkt. Eine optimale
Schweißbarkeit von erfindungsgemäßem Stahl läßt sich dabei dadurch gewährleisten,
daß der sich nach der Formel

berechnende Schweißfaktor S
f bei erfindungsgemäßem Stahl folgende Bedingung erfüllt:
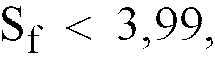
wobei mit %C, %B, %Cu, %P, %S, %Mo, %Cr, %Mn die jeweiligen C-, B- ,Cu- , P-, S-,
Mo-, Cr-, Mn-Gehalte des Stahls bezeichnet sind.
[0019] Die Zähigkeit der eingangs genannten bekannten Werkzeugstähle wird durch den Kohlenstoff-
und Carbidgehalt sowie durch die Höhe des Schwefelgehaltes, die Verteilung und die
Morphologie der Sulfide negativ beeinflußt. Erfindungsgemäßer Stahl enthält nur maximal
0,12 % Kohlenstoff. Auf diese Weise ist auch sein Carbidgehalt beschränkt. Zusätzlich
ist bei einem erfindungsgemäßen Stahl dadurch, daß in ihm die Gehalte an korngrenzwirksamen
Elementen auf ein Minimum reduziert ist, die Zähigkeit gegenüber anderen schwefellegierten
Stählen erhöht.
[0020] Es wurde festgestellt, daß die korngrenzwirksamen Elemente in Stählen der in Rede
stehenden Art während des Erstarrungsvorganges sowie während der Warmumformung und
/oder während einer Wärmebehandlung bei bestimmten Temperaturen an den Korngrenzen
seigern. Diese Seigerungen führen zu einer Verminderung der Kohäsion und bilden so
bevorzugt die Quelle der Entstehung von Rissen. Indem bei einem erfindungsgemäßen
Stahl der Versprödungsfaktor KG
f die folgende Bedingung erfüllt, kann der negative Einfluß der korngrenzenwirksamen
Elemente und damit einhergehend die Gefahr der Entstehung von Rissen zielgerichtet
minimiert werden:
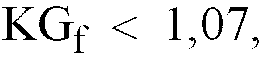
wobei sich der Versprödungsfaktor KG
f nach der Formel

berechnet und mit %Cu, %Sn, %As, %Al, %P und %N die jeweiligen Cu-, Sn-, As-, Al-,
P- und N-Gehalte des Stahls bezeichnet sind.
[0021] In Bezug auf das Verfahren zum Erzeugen eines Zwischenprodukts für die Herstellung
von Bauteilen, insbesondere für die Herstellung eines korrosionsbeanspruchten Werkzeugs,
aus erfindungsgemäß zusammengesetztem Stahl wird die oben angegebene Aufgabe gelöst,
indem mindestens folgende Herstellungsschritte durchlaufen werden:
- Erschmelzen eines erfindungsgemäßen Stahls,
- Vergießen des Stahls zu einem Vormaterial, wie Blöcken, Brammen, Stranggußriegeln,
Dünnbrammen oder gegossenem Band,
- Diffusionsglühen des Vormaterials bei einer 1200 - 1280 °C betragenden Temperatur,
- Warmumformen des geglühten Vormaterials zu dem Bauelement.
[0022] Durch das im erfindungsgemäß gewählten Temperaturbereich durchgeführte Diffusionsglühen
des Vormaterials wird ein Ausgleich der erstarrungsbedingten Seigerungen herbeigeführt,
so daß eine gleichmäßige Verteilung der enthaltenen Legierungselemente erzielt wird.
Bei der anschließenden Warmumformung des Vormaterials zu dem Zwischenprodukt wird
die Gefügestruktur und die Werkstoffisotropie beeinflußt. Eine verbesserte Struktur
des Gefüges und eine höhere Isotropie des Werkstoffs kann dabei dadurch erreicht werden,
daß die Warmverformung unter Anwendung eines Umformgrades ϕ von mindestens 1,5 durchgeführt
wird.
[0023] Im Rahmen des erfindungsgemäßen Verfahrens kann die Warmumformung als Schmieden oder,
zur Herstellung größerer Abmessungen, als Warmwalzen durchgeführt werden. Die Warmumformung
findet dabei bevorzugt bei Temperaturen von 850 °C - 1100 °C durchgeführt. In diesem
Temperaturbereich weist der erfindungsgemäß verwendete Werkstoff eine niedrige Fließspannung
und eine hohe Zähigkeit auf, so daß eine optimale Umformbarkeit gegeben ist. Die Warmumformung
läßt sich somit schnell, kostengünstig und mit hoher Ausbringung durchführen.
[0024] Das erfindungsgemäß erzeugte Werkstück wird nach der Warmumformung aus der Umformhitze
vorzugsweise an Luft abgelegt. Bei der Ablage an Luft wird der Werkstoff langsam und
vollständig vom austenitischen in den martensitischen Zustand überführt. Durch eine
solche langsame Abkühlung wird einerseits die gewünschte Härte des Werkstoffes von
bis zu 450 HB eingestellt. Andererseits werden Wärme- und Umwandlungsspannungen weitgehend
vermieden, so daß keine Verzüge oder Spannungsrisse am fertigen Zwischenprodukt auftreten.
[0025] Durch eine gegebenenfalls zusätzlich durchzuführende Wärmebehandlung bei Temperaturen
von 850 °C - 1050 °C mit nachfolgendem kontrollierten Abkühlen an einem Abkühlungsmedium,
wie Luft, Öl, Wasser oder einem Polymer, auf das vorzugsweise ein Anlassen bei Temperaturen
zwischen 400 °C und 650 °C folgt, kann eine Härte des erzeugten Zwischenprodukts hergestellt
werden, die sich von der nach der Ablage an Luft aus der Umformhitze vorliegenden
Härte unterscheidet. Insbesondere lassen sich über diese Wärmebehandlung auch niedrigere
Härtewerte bis zu einer Untergrenze von 300 HB erzielen.
[0026] Nachfolgend wird die Erfindung anhand von Ausführungsbeispielen näher erläutert.
Es zeigen:
- Diag. 1
- den Schneidenverschleiß im Bohrversuch aufgetragen über den Bohrweg,
- Diag. 2
- die für verschiedene Stähle ermittelte Schlagbiegearbeit aufgetragen über den Versprödungsfaktor
KGf.
[0027] In Tabelle 1 sind die Legierungen erfindungsgemäßer Stähle A,B,C den Zusammensetzungen
von vier außerhalb der Erfindung liegenden Vergleichsstählen D,E,F,G gegenübergestellt.
In Tabelle 2 sind zusätzlich die zu den Stählen A bis G gehörenden Brinell-Härtewerte
sowie die Härte- (H
f), Schweiß- (S
f), und Versprödungsfaktoren (KG
f) angegeben.
[0028] Zur Überprüfung der Zerspanbarkeit der Stähle A - G wurden an aus diesen Stählen
erzeugten Bauelementen Bohrversuche mit unbeschichteten Wendelbohrern aus dem Schnellarbeitsstahl
mit der Werkstoffnummer 1.3343 durchgeführt. Zu diesem Zweck wurden 24 mm tiefe Löcher
in die mit einer Härte von 300 bis 400 HB vorliegenden Stähle gebohrt. Die Schnittgeschwindigkeit
betrug jeweils 12 m/min und der Vorschub 0,12 mm/U.
[0029] Nach einem Gesamtbohrweg von 200, 1200 und 2400 mm wurde der an den Wendelbohrern
aufgetretene Verschleiß der Schneidkanten ausgemessen. Es zeigte sich, daß die erfindungsgemäßen
Stähle A, B und C trotz ihrer höheren Härte weniger Verschleiß an den Schneidkanten
der Bohrer erzeugen (Diag. 1). Ihre Zerspanbarkeit ist somit deutlich gegenüber der
der herkömmlichen, außerhalb der Erfindung liegenden Stähle D, E, F und G verbessert.
[0030] Zur Bestimmung der Zähigkeit von Werkzeugstählen wurde der Schlagbiegeversuch nach
Stahl-Eisen-Prüfblatt 1314 durchgeführt. In diesem Versuch wird als Maß für die Zähigkeit
eines Werkstoffes die zum Zerschlagen von ungekerbten Proben notwendige Schlagbiegearbeit
ermittelt. Die verwendeten Proben mit der Abmessung 7 x 10 x 55 mm wurden aus der
Verformungsrichtung der überprüften Stähle A - G entnommen, die mit einer Härte von
300 bis 400 HB vorlagen.
[0031] Die Prüfung erfolgte bei Raumtemperatur. Wie die im Diag. 2 zusammengefaßten Werte
für die Schlagbiegearbeit (Mittelwerte aus 3 geprüften Einzelproben) zeigen, kann
mit zunehmendem Versprödungsfaktor KG
f ein deutliches Absinken der gemessenen Schlagbiegearbeit festgestellt werden. Die
erfindungsgemäßen Stähle A, B und C weisen mit Werten deutlich oberhalb von 200 J
das gewünschte hohe Zähigkeitsniveau auf, während bei den zum Vergleich aufgeführten
Stählen D, E, F und G mit zunehmendem Versprödungsfaktor lediglich Werte zwischen
50 und 150 J gemessen werden konnten, ihre Zähigkeit daher deutlich niedriger war.
[0032] Um die Korrosionsbeständigkeit der in Tabelle 1 aufgeführten Stähle zu überprüfen,
wurden Eintauchversuche in einer 0,5 % wässrigen Natriumchloridlösung durchgeführt.
Nach einer Tauchdauer von 1 h wurden die Proben jeweils eine halbe Stunde lang an
Luft getrocknet und dann erneut eingetaucht. Nach insgesamt neun Tauch- und Trockenzyklen
wurde das Aussehen der ehemals fein geschliffenen Proben beurteilt.
[0033] Nach Beendigung der Versuche war bei den erfindungsgemäßen Stählen A bis C so gut
wie kein Rostbefall auf der Oberfläche der Proben feststellbar, was auf eine ausreichende
Korrosionsbeständigkeit hindeutet. Die zum Vergleich aufgeführten Stähle D, E und
G zeigten dagegen einen starken Angriff durch die Prüflösung, so daß der größte Teil
der Oberfläche nach den durchgeführten Prüfzyklen bereits korrodiert war. Lediglich
der Vergleichsstahl F war aufgrund seines hohen Chromgehaltes und wegen des Fehlens
von Schwefel korrosionsbeständiger. Aufgrund des Fehlens von Schwefel in der Zusammensetzung
wies dieser Stahl F jedoch die bei weitem schlechteste Zerspanbarkeit aller untersuchten
Stähle auf.
[0034] Die erläuterten Beispiele belegen, daß erfindungsgemäßer Stahl einerseits die angestrebte
Härte von 300 HB bis 450 HB sicher erreicht und andererseits gut zerspanbar ist. Bei
außerhalb der Erfindung liegenden Stählen, welche die für den Härtefaktor H
f erfindungsgemäß zu beachtenden Bedingungen nicht erfüllen, wird diese Eigenschaftskombination
dagegen nicht erreicht.
[0035] Vergleichbares erweist sich im Zusammenhang mit dem für den Schweißbarkeitsfaktor
S
f erfindungsgemäßer Stähle einzuhaltenden Wert. So weisen die Vergleichsstähle, deren
Schweißfaktor S
f jeweils oberhalb des erfindungsgemäß vorgesehenen Grenzwertes liegen, ein deutlich
schlechteres Schweißverhalten auf als erfindungsgemäße Stähle. Dies zeigt sich insbesondere
in dem Auftreten von Schweißrissen, zu deren Vermeidung bei den nicht erfindungsgemäßen
Stählen eine aufwendige Vorwärmung und Nachbehandlung notwendig ist.
[0036] Schließlich belegen die Beispiele, daß durch die erfindungsgemäße Beschränkung der
Gehalte an korngrenzenwirksamen Elementen, wie Cu, Sn, As, Al, P und N bei den Stählen
A, B, C der jeweilige Versprödungsfaktor KG
f niedrig gehalten und damit einhergehend eine für Stähle der in Rede stehenden Art
gute Zähigkeit erreicht worden ist.
Tabelle 2
Erfindung |
Stahl |
Härte
[HB] |
Sf |
KGf |
Hf |
A |
395 |
3,28 |
0,76 |
0,0889 |
B |
380 |
3,04 |
0,42 |
0,0646 |
C |
370 |
3,54 |
0,69 |
0,0552 |
Vergleich |
Stahl |
Härte
[HB] |
Sf |
KGf |
Hf |
D |
330 |
5,12 |
2,95 |
0,1099 |
E |
300 |
5,10 |
1,09 |
0,1099 |
F |
315 |
4,99 |
0,98 |
0,1099 |
G |
325 |
6,48 |
4,06 |
0,0005 |
1. Stahl für insbesondere korrosionsbeanspruchte Werkzeuge, welcher folgende Zusammensetzung
aufweist (in Mass. -%) :
C: mindestens 0,02 und höchstens 0,12 %,
Si: höchstens 1,5 %,
Mn: mehr als 1,0 - 2,50 %,
P: höchstens 0,035 %,
S: mindestens 0,04 % und weniger als 0,15 %,
Cr: mehr als 8,0 % und weniger als 12 %,
Mo: mehr als 0,0 % und höchstens 0,20 %,
V: mehr als 0,0 % und höchstens 0,25 %,
Nb: mehr als 0,1 % und höchstens 0,5 %,
N: mindestens 0,02 und höchstens 0,12 %,
Ni: höchstens 0,5 %,
B: höchstens 0,005 %,
Cu: höchstens 0,3 %,
Al: höchstens 0,035 %,
Sn: höchstens 0,035 %,
As: höchstens 0,02 %,
mindestens eines der Elemente Ca, Mg oder Ce, wobei die Summe der Gehalte an diesen
Elementen mindestens 0,0002 % und höchstens 0,015 % beträgt,
Rest Eisen und unvermeidbare Verunreinigungen.
2. Stahl nach Anspruch 1, dadurch gekennzeichnet, daß er 0,001 - 0,009 Mass.-% Ca enthält.
3. Stahl nach einem der Ansprüche 1 oder 2,
dadurch gekennzeichnet, daß sein Härtefaktor H
f folgende Bedingung erfüllt:

wobei

und mit %Nb der jeweilige Nb-Gehalt des Stahls bezeichnet ist.
4. Stahl nach einem der voranstehenden Ansprüche,
dadurch gekennzeichnet, daß sein Schweißfaktor S
f folgende Bedingung erfüllt:
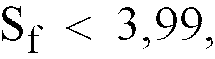
wobei

und mit %C, %B, %Cu, %P, %S, %Mo, %Cr, %Mn die jeweiligen C-, B- ,Cu- , P-, S-, Mo-,
Cr-, Mn-Gehalte des Stahls bezeichnet sind.
5. Stahl nach einem der voranstehenden Ansprüche,
dadurch gekennzeichnet, daß sein Versprödungsfaktor KG
f folgende Bedingung erfüllt:
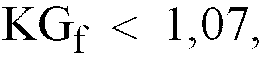
wobei

und mit %Cu, %Sn, %As, %Al, %P und %N die jeweiligen Cu-, Sn-, As-, Al-, P- und N-Gehalte
des Stahls bezeichnet sind.
6. Stahl nach einem der voranstehenden Ansprüche,
dadurch gekennzeichnet, daß er mindestens 0,05 Mass.-% Schwefel enthält.
7. Stahl nach einem der voranstehenden Ansprüche,
dadurch gekennzeichnet, daß er mindestens 0,07 Mass.-% Schwefel enthält.
8. Verfahren zur Erzeugung eines Zwischenprodukts für die Herstellung von Bauelementen,
insbesondere für die Herstellung von korrosionsbeanspruchten Werkzeugen, aus einem
gemäß einem der Ansprüche 1 bis 7 zusammengesetzten Stahl umfassend folgende Schritte:
- Erschmelzen des Stahls,
- Vergießen des Stahls zu einem Vormaterial, wie Blöcken, Brammen, Stranggußriegeln,
Dünnbrammen oder gegossenem Band,
- Diffusionsglühen des Vormaterials bei einer 1200 - 1280 °C betragenden Temperatur,
- Warmumformen des geglühten Vormaterials zu dem Zwischenprodukt.
9. Verfahren nach Anspruch 8, dadurch gekennzeichnet, daß die Warmumformung als Schmieden durchgeführt wird.
10. Verfahren nach Anspruch 8, dadurch gekennzeichnet, daß die Warmumformung als Warmwalzen durchgeführt wird.
11. Verfahren nach einem der Ansprüche 7 bis 10, dadurch gekennzeichnet, daß das Zwischenprodukt nach der Warmumformung an Luft abgelegt wird.
12. Verfahren nach einem der Ansprüche 7 bis 11, dadurch gekennzeichnet, daß die Warmumformung bei Temperaturen von 850 °C - 1150 °C durchgeführt wird.
13. Verfahren nach einem der Ansprüche 7 bis 12, dadurch gekennzeichnet, daß das Zwischenprodukt im Anschluß an die Warmumformung bei Temperaturen von 850 °C
- 1050 °C wärmebehandelt und nach der Wärmebehandlung an einem Abkühlmedium, wie Luft,
Öl, Wasser oder einem Polymer kontrolliert abgekühlt wird.
14. Verfahren nach Anspruch 13, dadurch gekennzeichnet, daß nach der Abkühlung ein Anlassen bei Temperaturen von 400 °C - 650 °C durchgeführt
wird.
15. Verwendung eines gemäß einem der Ansprüche 1 bis 6 zusammengesetzten Stahls zur Herstellung
von Werkzeugen für die Kunststoffverarbeitung.
1. A steel, in particular for tools exposed to corrosion, of the following composition
(in mass-%):
C: min. 0.02 and max. 0.12 %;
Si: max. 1.5 %;
Mn: more than 1.0 - 2.50 %;
P: max. 0.035 %;
S: min. 0.04 % and less than 0.15 %;
Cr: more than 8.0 % and less than 12 %;
Mo: more than 0.0 % and max. 0.20 %;
V: more than 0.0 % and max. 0.25 %;
Nb: more than 0.1 % and max. 0.5 %;
N: at least 0.02 % and max. 0.12 %;
Ni: max. 0.5 %;
B: max. 0.005 %;
Cu: max. 0.3 %;
Al: max. 0.035 %;
Sn: max. 0.035 %;
As: max. 0.02 %;
at least one of the element Ca, Mg or Ce, wherein the sum of the contents of these
elements is more than 0.0002 % and max. 0.015%;
with the remainder being iron and unavoidable impurities.
2. The steel according to claim 1, characterised in that it contains 0.001 - 0.009 mass-% of Ca.
3. The steel according to one of claims 1 or 2,
characterised in that its hardness factor Hf meets the following condition:

wherein

with %Nb designating the respective Nb content of the steel.
4. The steel according to one of the preceding claims,
characterised in that its weld factor Sf meets the following condition:
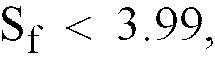
wherein

and wherein %C, %B, %Cu, %P, %S, %Mo, %Cr, %Mn designate the respective contents
of C, B, Cu, P, S, Mo, Cr and Mn of the steel.
5. The steel according to one of the preceding claims,
characterised in that its embrittlement factor KGf meets the following condition:
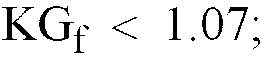
wherein

with %Cu, %Sn, %As, %Al, %P and %N designating the respective contents of Cu,
Sn, As, Al, P and N of the steel.
6. The steel according to any one of the preceding claims, characterised in that it comprises at least 0.05 mass-% of sulphur.
7. The steel according to any one of the preceding claims, characterised in that it comprises at least 0.07 mass-% of sulphur.
8. A method for producing an intermediate product for the production of components, in
particular for the production of tools exposed to corrosion, made from a steel with
a composition according to any one of claims 1 to 7, comprising the following steps:
- melting the steel;
- casting the steel to form a raw material such as ingots, slabs, continuous-cast
bars, thin slabs or cast strip;
- diffusion annealing of the raw material at a temperature between 1200 and 1280 °C;
and
- hot forming the annealed raw material to form the intermediate product.
9. The method according to claim 8, characterised in that hot forming is carried out by way of forging.
10. The method according to claim 8, characterised in that hot forming is carried out by way of hot rolling.
11. The method according to any one of claims 7 to 10, characterised in that following hot forming, the intermediate product is held where it is exposed to air.
12. The method according to any one of claims 7 to 11, characterised in that hot forming takes place at temperatures between 850 °C and 1150 °C.
13. The method according to any one of claims 7 to 12, characterised in that following hot forming, the intermediate product is heat treated at temperatures between
850 °C and 1050 °C and after heat treatment is subjected to controlled cooling with
the use of a cooling medium such as air, oil, water or a polymer.
14. The method according to claim 13, characterised in that after cooling, tempering at temperatures between 400 °C and 650 °C is carried out.
15. The use of a steel with a composition according to any one of claims 1 to 6 for the
production of tools for plastics processing.
1. Acier, en particulier pour des outils sollicités par la corrosion, qui présente la
composition suivante (en % en poids) :
C : au minimum 0,02 % et au maximum 0,12 %
Si : au maximum 1,5 %
Mn : supérieur à 1,0 - 2,50 %,
P : au maximum 0,035 %,
S : au minimum 0,04 % et inférieur à 0,15 %,
Cr: supérieur à 8,0 % et inférieur à 12 %,
Mo : supérieur à 0,0 % et au maximum 0,20 %,
V : supérieur à 0,0 % et au maximum 0,25 %,
Nb : supérieur à 0,1 % et au maximum 0,5 %,
N : au minimum 0,02 % et au maximum 0,12 %,
Ni : au maximum 0,5 %,
B : au maximum 0,005 %,
Cu : au maximum 0,3 %,
Al : au maximum 0,035 %,
Sn : au maximum 0,035 %,
As : au maximum 0,02 %,
au moins un des éléments Ca, Mg ou Ce, la somme des teneurs de ces éléments étant
égale au minimum à 0,0002 % et au maximum à 0,015 %,
le reste étant du fer et des impuretés inévitables.
2. Acier selon la revendication 1, caractérisé en ce qu'il contient 0,001 à 0,009 % en poids de Ca.
3. Acier selon la revendication 1 ou 2,
caractérisé en ce que son facteur de dureté H
f remplit la condition suivante :

sachant que

et % Nb désigne la teneur respective en Nb de l'acier.
4. Acier selon l'une quelconque des revendications précédentes,
caractérisé en ce que son facteur de soudabilité S
f remplit la condition suivante :
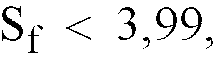
sachant que

et % C, % B, % Cu, % P, % S, % Mo, % Cr, % Mn désignent dans chaque cas les teneurs
respectives en C, en B, en Cu, en P, en S, en Mo, en Cr, en Mn de l'acier.
5. Acier selon l'une quelconque des revendications précédentes,
caractérisé en ce que son facteur de fragilité KG
f remplit la condition suivante :
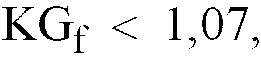
sachant que

et % Cu, % Sn, % As, % Al, % P, % N désignent les teneurs respectives en Cu, en Sn,
en As, en Al, en P et en N de l'acier.
6. Acier selon l'une quelconque des revendications précédentes, caractérisé en ce qu'il contient au minimum 0,05 % en poids de soufre.
7. Acier selon l'une quelconque des revendications précédentes, caractérisé en ce qu'il contient au minimum 0,07 % en poids de soufre.
8. Procédé de préparation d'un demi-produit pour la fabrication d'éléments de construction,
en particulier pour la construction d'outils sollicités par la corrosion, à partir
d'un acier ayant la composition selon l'une quelconque des revendications 1 à 7, comprenant
les étapes suivantes :
- fusion de l'acier,
- coulée de l'acier pour obtenir un produit de départ, tel que des lingots, des brames,
des barres de coulée continue, des brames minces ou un feuillard coulé,
- homogénéisation du produit de départ à une température de 1 200 à 1 280°C,
- formage à chaud du produit de départ ayant subi une homogénéisation, en vue d'obtenir
le demi-produit.
9. Procédé selon la revendication 8, caractérisé en ce que le formage à chaud effectué est un forgeage.
10. Procédé selon la revendication 8, caractérisé en ce que le formage à chaud effectué est un laminage à chaud.
11. Procédé selon l'une quelconque des revendications 7 à 10, caractérisé en ce que, après le formage à chaud, le demi-produit est stocké à l'air.
12. Procédé selon l'une quelconque des revendications 7 à 11, caractérisé en ce que le formage à chaud est effectué à des températures de 850°C à 1 150°C.
13. Procédé selon l'une quelconque des revendications 7 à 12, caractérisé en ce que le demi-produit, à la suite du formage à chaud, subit un traitement thermique à des
températures de 850°C à 1 050°C et, après le traitement thermique, est refroidi de
manière contrôlée avec un milieu de refroidissement, tel que l'air, l'huile, l'eau
ou un polymère.
14. Procédé selon la revendication 13, caractérisé en ce que, à l'issue du refroidissement, est effectué un traitement de revenu à des températures
de 400°C à 650°C.
15. Utilisation d'un acier ayant la composition selon l'une quelconque des revendications
1 à 6, destiné à la construction d'outils pour la transformation des matières plastiques.