[0001] The present invention refers to a device for operating a swing gate.
[0002] Operating devices for automating opening and closing of swing single- or double-leaf
gates are widely available on the market at present. Among said operating systems
for swing gates, linear actuators able to provide a reciprocating rectilinear movement
are known to the art.
[0003] Figure 1 illustrates diagrammatically the kinematic mechanism of a leaf of a swing
gate operated by means of a linear actuator. A gate indicated as whole with reference
numeral 1 comprises two swing leaves 2.
[0004] Each leaf 2 is hinged at one end, by means of a hinge N, to a respective post 4,
so as to be able to rotate around the hinge N. Near the free end of each leaf 2 there
is provided a stop 5, to block the leaves 2 in the closing position of the gate 1.
[0005] The leaf 2 of the gate is operated by a linear actuator 10. One end of the body of
the linear actuator 10 is hinged, in a pivot axis C, to a bracket 6 made integral
with the post 4 by means of a flange 7. The linear actuator 10 has a piston which
moves linearly with a reciprocating motion from a distal position with respect to
the pivot end C to a proximal position with respect to the pivot end C.
[0006] The piston of the linear actuator 10 is hinged, in a pivot axis 8, to a bracket 9
integral with the leaf 2 of the gate. In this manner, when the piston is in the distal
position, the free end of the leaf 2 abuts against the stop 5 and the leaf 2 of the
gate is closed. During the stroke of the piston towards the proximal position, the
leaf 2 and the linear actuator 10 make a rotation of about 90° around the respective
hinges N and C. Thus, when the piston is in the proximal position, as shown with the
dashed line in Figure 1, the leaf 2 of the gate is in the open position.
[0007] Figure 2 illustrates the structure of a linear actuator 10 of the prior art. The
linear actuator 10 comprises a substantially cylindrical body 11 delimited by a proximal
end flange 12 and a distal end flange 13. The proximal end flange 12 is integral with
a structural bracket 14 which supports an attachment 15 for fixing to the pivot C
of the bracket 6 of the post 4, whilst the distal end flange 13 is integral with a
covering hood 16.
[0008] A worm screw 17 is mounted to be axially rotatable inside the body 11. The proximal
end of the worm screw 17 is rotatably supported by thrust bearings 18 and connected
by means of a joint 19 to a gear reduction unit 20 operated by an electric motor 21.
The electric motor 21 can be provided with an electromagnetic engine brake 22.
[0009] The bearings 18, joint 19, reduction unit 20, electric motor 21 and electromagnetic
brake 22 are disposed inside a housing 23 formed inside the body 11 near the proximal
flange 12. The worm screw 17 extends to the distal flange 13 and the free end of the
worm screw 17 is rotatably supported by the distal flange 13.
[0010] A lead nut 24 acting as piston for the linear actuator 10 screws onto the worm screw
17. The lead nut 24 has a threaded connection 25 able to receive suitable fixing means
for engagement with the pivot 8 of the bracket 9 of the leaf 2. The connection 25
of the lead nut 24 is accessible from the outside of the body 11 of the linear actuator
10. For this purpose the body 11 of the linear actuator 10 has a longitudinal slot
26, which extends substantially for the entire length of the worm screw 17, through
which the connection 25 of the lead nut 24 can slide.
[0011] Operation of the linear actuator 10 is described hereunder. The electric motor 20
supplied with electric current turns in one direction or the other causing the worm
screw to rotate at a suitable speed through the reduction unit 20 and the joint 19.
Rotation of the screw 17 in one direction or the other, causes translation of the
lead nut 24 towards the proximal end or towards the distal end, allowing opening or
closing, respectively, of the leaf 2 of the gate.
[0012] In these applications the lock is generally not used. In fact, to block the leaf
2 of the gate, the ability of the lead nut 24 to be non-reversible in its movement
of translation on the screw 17 is generally exploited. That is to say, if the screw
17 is stopped, the lead nut 24 cannot translate thereon. In this manner, when the
lead nut 24 is at the end of its closing stroke, near the distal end flange 13, the
leaf 2 of the gate is automatically blocked.
[0013] This non-reversibility of the movement of translation of the lead nut 24 is obtained
by providing any one of the following solutions:
- worm screw 17 non-reversible;
- worm screw 17 reversible and reduction unit 20 non-reversible;
- worm screw 17 reversible, reduction unit 20 reversible, but electromagnetic brake
22 provided on motor 21;
- worm screw 17 reversible and provision of a mechanism 19, such as a joint or one-way
clutch, interposed between the motor 21 and the worm screw 17 able to make the movement
of the screw 17 non-reversible.
[0014] The first solution with a non-reversible worm screw results in a low performance,
below 50%, whereas the solutions with a reversible worm screw lead to structural complexities,
such as the non-reversible reduction unit, and the provision of additional elements,
such as the electromagnetic brake and the one-way clutch.
[0015] Furthermore, it must be considered that in any case these solutions must allow the
user to open and close the gate even in the event of a failure of the power supply
to the motor. In fact, to open and close the gate in the event of an electrical power
failure:
- if the linear actuator 10 uses a non-reversible worm screw 17, the lead nut 24 must
be disconnected from the bracket 9 of the leaf 2 of the gate;
- if, on the other hand, the linear actuator 10 uses a reversible worm screw 17 with
non-reversible transmission, it is necessary to act on the transmission upstream of
the screw 17 to eliminate the non-reversibility and allow the lead nut 24 to slide
along the screw.
[0016] In the first case, the operations of disconnection of the lead nut and subsequent
reconnection of the lead nut to the gate, when the supply of electrical power returns,
prove somewhat awkward and complex for the user.
[0017] In the second case also, the operations of disconnection of the non-reversible transmission
from the worm screw and subsequent reconnection of the transmission to the screw,
when the electrical power returns, are somewhat awkward and complex for the user.
Furthermore, in this case, manual movement of the gate is extremely difficult, precisely
because the lead nut must slide on the worm screw making it rotate and in this case
it generates a high friction during rotation of the worm screw.
[0018] As described above, the actuator 10 requires, at one end thereof, an articulated
restraint C which connects it to a fixed part which is generally the gatepost 4. The
point of restraint C of the actuator must be placed in a well defined position with
respect to the hinge N of the leaf of the gate.
[0019] With reference to Figure 1, the following parameters are defined:
L is the fixed distance between the hinge 8 (constraint between the piston of the
actuator 10 and the leaf 2) and the hinge N (constraint between the leaf 2 and the
post 4);
x is the horizontal axis passing through the hinge N,
y is the vertical axis passing through the hinge C (constraint between the actuator
10 and the post 4),
O is the point of intersection between the axis x and the axis y,
A is the distance between the hinge N and the point O,
B is the distance between the hinge C and the point O,
d is the distance between the hinge N and the end of the post 4 parallel to the axis
y, and
f is the distance between the axis x and the end of the post carrying the bracket
7.
[0020] As a result, the stroke necessary for the carriage of the piston hinged at 8 is given
by L + A - (L - B) = A + B.
This stroke equal to A + B must not be greater than that available (intrinsic characteristic
of the piston of the actuator 10).
[0021] However, values A and B are influence by the values d and f, which in fact already
exist at the time when the installer of the actuator 10 works on the gate to be motorized
(automated).
[0022] Therefore, there is the need to find a correct position of the restraint C so as
to have A + B < available stroke of the piston of the actuator 10.
At present the manufacturer of the actuator 10 also provides the elements for attachment
both to the leaf 2 of the gate and to the post 4.
[0023] For attachment to the post 4 various connecting systems have been devised with brackets
and supports that allow more than one position of the restraint C. However, in order
to position the restraint C correctly, the installer often has to intervene with cuts
and welding of said brackets and supports.
[0024] One of the most widely used connecting systems of the prior art is that shown in
figure 1, which provides for two separate pieces, that is, the bracket 6 destined
to be constrained at C to the actuator 10 and the flange 7, intended to be fixed to
the post 4. Both the bracket 6 and the flange 7 have a plurality of fixing holes,
so that the bracket 6 can be positioned correctly on the flange 7.
[0025] If after fixing of the flange 7 to the post 4 further adjustment is necessary, this
adjustment can be carried out in two directions at right angles by moving the bracket
6 on the flange 7 and ensuring that the holes of the bracket 6 and the flange 7 are
in register to receive bolt-type fixing means. It is often necessary to shorten the
bracket 6 with cuts that eliminate pairs of holes and in any case the adjustment positions
are limited to the combination of holes and are generally 12 in number.
[0026] It is obvious that said mounting system for an automatic gate with leaves presents
some drawbacks.
[0027] In fact the installer must calculate with good precision the position of the constraint
C according to the piston stroke (A + B) and the actual characteristics of the gate
and the post (d and f). This position cannot always be obtained with the brackets
and flanges provided (6 and 7), considering the variety of shapes and materials with
which gates and posts are made.
[0028] Very often it is necessary to make adaptations to the attachments provided and sometimes
to invent new attachments which do not always yield good results. Sometimes it is
even necessary to modify the posts in order to move the brackets away.
[0029] The object of the present invention is to overcome the drawbacks of the prior art
by providing a device for operating a swing gate that is reliable and at the same
time cheap and simple in structure and execution.
[0030] Another object of the present invention is to provide such an operating device for
a swing gate that is practical and simple for the user to use.
[0031] Yet another object of the present invention is to provide such an operating device
for a swing gate that is versatile and suitable to be applied to various types of
leaves of swing gates.
[0032] These objects are achieved according to the invention with the characteristics listed
in appended independent claim 1.
[0033] Advantageous embodiments of the invention are apparent from the dependent claims.
[0034] The operating device to drive a leaf of a swing gate according to the invention consists
of a linear actuator. The body of the actuator is constrained to a post of the gate
and driven by a worm screw set in rotation by an electric motor.
[0035] The peculiarity of the invention lies in the fact that the piston comprises a carriage
which slides axially on the worm screw without interfering with the thread of the
screw. Inside said carriage an insert or comb can slide transversally to engage/disengage
the worm screw.
[0036] In this manner, when the comb engages the thread of the worm screw, a rotation of
the worm screw causes longitudinal translation of the carriage together with the comb.
On the other hand, when the comb is disengaged from the thread of the screw, the user
can make the carriage slide longitudinally together with the comb, even if he holds
the worm screw still.
[0037] Such a solution presents various advantages. In fact for blocking of the gate a non-reversible
worm screw can be used, without problems of constraints of non-reversibility in the
transmission upstream of the screw.
[0038] Moreover, by simply disengaging the comb from the thread of the worm screw, easy
movement of the leaf of the gate is allowed, when the worm screw is stopped because
of a failure of the electrical power supply to the motor which sets it in rotation.
[0039] Moreover, in the present invention the actuator is associated with a device for connection
thereof to a post. Said connecting device comprises a flange intended to be mounted
in a fixed manner on the post and a bracket intended to be mounted to a hinge of the
actuator and to be connected in a fixed manner to the flange.
[0040] The connection between the flange and the bracket has at least one grooved or splined
coupling. In this manner the position of the hinge of the actuator can be adjusted
in a suitable manner, allowing the installer a greater ease of assembly, without the
need to modify the mechanical connecting elements at his disposal.
[0041] Further characteristics of the invention will be made clearer by the detailed description
that follows, referring to purely exemplary and therefore non limiting embodiments
thereof, illustrated in the appended drawings, wherein:
Figure 1 is a diagrammatic top plan view illustrating the kinematic mechanism of a
leaf of a swing gate operated by a linear actuator of the prior art, wherein the leaf
and the linear actuator in the open position are shown with a dashed line;
Figure 2 is an enlarged axial sectional view of the linear actuator of Figure 1;
Figure 3 is axial sectional view partially broken off and enlarged with respect to
Figure 2, illustrating the device for operating the swing gate according to the invention;
Figure 4 is a front view, partially sectional, illustrating a first embodiment of
a device for connecting the actuator according to the invention;
Fig. 5 is a side elevational view from the right of the connecting device of Figure
4, in which a fixing bolt has been omitted;
Figure 6 is front view, partially sectional, illustrating a second embodiment of the
connecting device according to the invention;
Figure 7 is a side elevational view from the right of the connecting device of Figure
6, in which two fixing bolts have been omitted;
Figure 8 is a side elevational view of a flange forming part of the connecting device
according to the first and second embodiment of the invention;
Figure 9 is a sectional view along the section of plane IX-IX of Figure 8;
Figure 10 is a plan view of a bracket forming part of the connecting devices according
the first and second embodiment;
Figure 11 is a sectional view along the section of plane XI-XI of Figure 10;
Figure 12 is a plan view of a bolt forming part of the connecting devices according
to the first and second embodiment;
Figure 13 is a view from the right of the bolt of Figure 12;
Figure 14 is a plan view of an intermediate bracket forming part of the connecting
device according to the second embodiment of the invention;
Figure 15 is a sectional view along the section of plane XV-XV of Figure 14; and
Figure 16 is a diagrammatic view illustrating the various positions of movement of
the connecting devices according to the first and second embodiment of the invention.
[0042] The operating device for a swing gate according to the invention, indicated as a
whole with reference numeral 110, is described with the aid of Figure 3.
[0043] The operating device 110 is substantially similar to the linear actuator 10 described
previously with reference to Figure 2 and can be applied to a gate 1, like that described
previously with reference to Figure 1. Consequently, like or corresponding elements
to those described are indicated with the same reference numerals and detailed description
thereof is omitted.
[0044] The operating device 110 comprises a substantially cylindrical body 11, wherein a
worm screw 17 is mounted to be axially rotatable, in a similar way to that described
previously with reference to Figure 2.
[0045] Inside the body 11 there is disposed a piston 124 in the form of a carriage or slide
that can longitudinally slide inside the body 11. For this purpose the carriage 124
consists of a cylindrical or parallelepiped block which has an axial through hole
130, not threaded, which receives the worm screw 17 with a certain clerance. Thus
the carriage 124 can slide axially without interfering with the thread of the worm
screw 17.
[0046] A peripheral portion of the carriage 124 has a transverse threaded hole 125 to receive
a fixing bolt 126 which makes integral with the carriage 124 a flange 108 able to
be hinged to the bracket 9 of the leaf of the gate.
[0047] In a central position in the carriage 124 there is defined a chamber or seat 131
communicating with the axial hole 130 and open towards the outside. The carriage 124
has a narrowing in the chamber 131 so as to define an abutment surface 133.
[0048] In the chamber 131 there is mounted transversally slidably an insert or comb 132,
substantially parallelepiped in shape and having an end engaging portion 135 provided
with teeth or a thread, able to screw with the thread of the worm screw 17. The comb
132 has an abutment surface 134 opposed to the abutment surface 133 of the carriage
124.
[0049] In this manner the comb 132, translating transversally in the chamber 131, can pass
from an engagement position in which its thread screws with the thread of the screw
17 to a non-engagement position in which its thread does not interfere with the thread
of the screw 17 and its abutment surface 134 abuts against the abutment surface 133
of the carriage 124. It should be noted that the abutment surface 134 of the comb
and the abutment surface 133 of the carriage act as a stop for the stroke of the comb
132 and prevent the comb 132 from leaving its seat 131.
[0050] The comb 132 has a flange 136 which protrudes radially outward on the opposite side
to the thread 135. The flange 136 of the comb 132 is hinged by means of a pivot 137
to a lever 138. One end of the lever 138 is hinged by means of a pivot 139 to the
carriage 124.
[0051] In this manner the lever 138, by rotating around its own end pivot 139 in the direction
of arrows F1, draws with it the comb 132 which performs a translation in the direction
of the arrows F2. Thus the comb 132, through operation in rotation of the lever 138,
can pass from its position of engagement with the thread of the screw 17 to its position
of disengagement.
[0052] The free end of the lever 138 has a lock 140 for clamping of the carriage 124. The
lock 140 has a bolt 141 which can engage in a closing relationship with a stop 142
integral with the carriage 124. The bolt 141 of the lock 140 can be operated by the
user for opening/closing by means of a key.
[0053] Clearly the comb 132 can be driven in the transverse translation by other operating
means similar or equivalent to the lever 138.
[0054] Operation of the operating device 110 according to the invention is described hereunder.
[0055] Generally the lever 138 of the operating device 110 is in the closed position, that
is to say, the thread of the comb 132 is in engagement in the thread of the screw
17 and the lock 140 is clamped in the stop 142. In this situation, for opening/closing
of the leaf 2 of the gate, the electric motor 21 which sets the worm screw 17 in rotation
in one direction or the other is operated. Consequently, the thread of the comb 132
screws with the thread of the worm screw 17 and thus the carriage 124, inside which
the comb 132 is contained, performs a translation on the worm screw 17.
[0056] In this case, the worm screw 17 can advantageously be of the non-reversible type,
so as to avoid translation of the comb, when the screw is stopped and the gate is
in the closed position.
[0057] In the case of failure of the electrical power supply to the motor 21, it is not
necessary to disconnect the leaf 2 of the gate from the drive system 110. In fact
the user must simply open the lock 140, manually move the lever 138 into the position
of disengagement in which the thread of the comb 132 does not interfere with the thread
of the worm screw 17 and then move the leaf of the gate without any effort, since
the carriage 124 can slide freely on the screw 17.
[0058] It should be noted that the operating system 110 according to the invention is not
only extremely practical and simple for the user to use in the event of failure of
the electrical power supply, but it also allows use of a non-reversible worm screw,
with the result of being able to eliminate the non-reversible constraints in the transmission
upstream of the worm screw.
[0059] A first embodiment of the connecting device according to the invention, denoted as
a whole with reference numeral 80, is described with the aid of Figures 4, 5 and 8-13.
[0060] The connecting device 80 serves to connect the end of the actuator 10 (Figure 1)
in which there is the hinge restraint C to the post 4. The connecting device 80 comprises
a flange 30 designed to be fixed to the post 4 and a bracket 40 connected to the flange
30 and designed to be constrained, by means of the hinge restraint C, to the end of
the actuator 10.
[0061] As shown better in Figures 8 and 9, the flange 30 comprises a base plate 31, substantially
rectangular, which has near the four comers four fixing holes 32 able to receive bolt
means for fixing to the post 4.
[0062] From the base plate 31 there rises in a central position a support 33 disposed at
right angles with respect to the base plate 31. The support 33 is shaped as a rectangular
plate with the end rounded and has a through hole 34 with its axis substantially parallel
to the plane of the base plate 31. The hole 34 has a female grooved profile 35, with
a plurality of teeth and grooves parallel to each other and disposed with a prefixed
pitch.
[0063] As better shown in Figures 10 and 11, the bracket 40 is shaped as a rectangular plate-shaped
bar with the two ends rounded. The bracket 40 has near its two ends two respective
through holes 41 and 42. The hole 41 has a female grooved profile 43 substantially
similar to the gooved profile 35 of the hole 34 of the flange 30. The hole 42 has
a smooth profile able to receive the hinge C of the actuator 10.
[0064] The grooved hole 41 of the bracket 40 is put in register with the grooved hole 34
of the flange 30 and then a bolt 50, better illustrated in Figures 12 and 13, is inserted
into the two holes. The bolt 50 has a head 51 and a shaft 54. The shaft 54 has a splined
male part 52 near the head 51 and a threaded part 53 at its free end.
[0065] The splined part 52 of the shaft of the bolt 50 has a plurality of grooves and teeth
parallel to each other, so that the male splined part 52 of the bolt can engage with
the female grooved profiles 35 and 43 of the holes 34 and 41, respectively, of the
flange 30 and the bracket 40. As shown in Figure 4, a nut 55 is screwed into the threaded
part 53 of the bolt 50 so as to fix the bracket 40 to the flange 30 and prevent any
relative movement of the bracket 40 with respect to the flange 30.
[0066] It should be noted that before locking the bracket 40 to the flange 30, by means
of the bolt 50, the bracket 40 can take on a plurality of angular positions with respect
to the axis of the holes 34, 41. These angular positions are given by the pitch of
the teeth of the grooved profiles 35 and 43.
[0067] To be exact the angle between one position and the other of the bracket 40 is given
by:
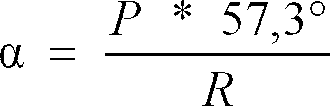
where P is the pitch of the teeth and R is the primitive radius of the teeth.
[0068] Therefore, for a grooved profile (commonly available commercially) having a pitch
P = 1 mm and a primitive radius R = 6.5 mm, α = 9° is obtained. With this α value,
as shown in Figure 14, the point of restraint C can theoretically take on 21 positions,
illustrated with (+), on an angle of 180°. However, as shown in Figure 16, beneath
the dashed line Z there are 6 positions of the point of restraint C that can not be
used because of the bulk and inclination of the actuator 10. Therefore 15 different
operative positions are obtained in which to be able to position the restraint C.
[0069] With reference to Figures 6, 7, 14 and 15, a second embodiment of a connecting device
according to the invention is described, indicated as a whole with reference numeral
180, in which like or similar elements to those already described are indicated by
the same reference numerals and detailed description thereof is omitted.
[0070] The connecting device 180 according to the second embodiment differs from the connecting
device 80 of the first embodiment only in the presence of a pair of intermediate brackets
60.
[0071] As shown better in Figures 14 and 15, each intermediate bracket 60 is in the form
of a rectangular plate-shaped bar with the two ends rounded. Each intermediate bracket
60 has near its two ends two respective through holes 61 and 62. The holes 61 and
62 both have a grooved profile 63 and 64, substantially similar to the grooved profile
35 of the hole 34 of the flange 30 and to the grooved profile 43 of the hole 41 of
the bracket 40.
[0072] As shown in Figure 6, the two intermediate brackets 60 are disposed on one side and
the other with respect to the support 33 of the flange 30 and with respect to one
end of the bracket 40 so that the holes 61 of the intermediate brackets 60 are in
register with the hole 34 of the flange 30 and the holes 62 of the intermediate brackets
60 are in register with the grooved hole 41 of the bracket 40.
[0073] At this point the intermediate brackets 60 are fixed to the flange 30 by inserting
a first splined bolt 50 into the grooved holes 61 and 34 of the two intermediate brackets
60 and the flange 30. On the other hand, the bracket 40 is fixed to the intermediate
brackets by inserting a second splined bolt 50 into the grooved holes 62 and 41 of
the two intermediate brackets 60 and of the end bracket 40.
[0074] Of course, instead of a pair of intermediate brackets 60 a single intermediate bracket
60 can be used.
[0075] With reference to Figure 7, H denotes the point of grooved coupling constraint between
the intermediate bracket 60 and the end bracket 40 and C again denotes the point of
hinged constraint between the end bracket 40 and the end of the actuator 10. With
reference to Figure 16, the point H, as seen previously, can move into 15 possible
positions, whilst the point C can move into 21 possible positions with respect to
the point H, on an angle of 180°. As a result the point C of constraint to the actuator
can take on
15 * 21 = 255 different possible positions indicated with (o).
[0076] Installation of the connecting devices 80 and 180 is described hereunder.
[0077] The installer, according to the stroke of the piston of the actuator 10 and the values
d and f, calculates the position of the point of restraint C. Having considered the
various positioning possibilities offered by the connecting device according to the
invention (in Figure 16 points indicated with (+) for the device 80 and points indicated
with (o) for the device 180), the installer can choose the point at which to fix the
flange 30 to the post 4 with greater ease.
[0078] Thus in the first instance the installer can attempt to use only the bracket 40,
exploiting the 15 positions offered thereby. If he does not obtain correct positioning
of the point of restraint C, he can also insert the intermediate brackets 60 to be
able to exploit the 255 admissible positions for point C.
[0079] As can be seen in Figure 16, in the case of use of grooved profiles with a pitch
of 1 mm between the teeth and of bars with a centre distance between the holes of
65 mm, the distance between one admissible position of the point of restraint C and
another is minimal. This facilitates calibration of the working position of the piston
after fixing of the flange 30.
[0080] Even if in the present description the connecting devices 80 180 have been described
applied to a traditional actuator 10, they are particularly suitable to be applied
to the operating device 110 according to the invention.
[0081] Numerous variations and modifications of detail within the reach of a person skilled
in the art can be made to the present embodiments of the invention, without departing
from the scope of the invention as set forth in the appended claims.
1. An operating device (110) for driving a leaf (2) of a swing gate (1), said operating
device (110) consisting of a linear actuator comprising:
- an elongated body (11) designed to be hinged to a bracket (6) integral with a fixed
post (4),
- a piston (124) longitudinally slidably mounted inside said body (11) and designed
to be hinged to a bracket (9) integral with said leaf (2) of the swing gate,
- a worm screw (17) that engages in said piston (124) to allow a reciprocating translating
movement of the piston (124) along the axis of the screw (17), and
- drive means (21) able to set said worm screw (17) in rotation around its own axis,
characterised in that
said piston comprises:
- a carriage or slide (124) longitudinally slidably mounted inside said body (11),
and
- an insert or comb (132) transversally slidably mounted inside said carriage (124)
to pass from an engagement position in which it engages with the thread of the screw
(17) to a disengagement position in which it does not interfere with the thread of
said screw (17).
2. An operating device (110) according to claim 1, characterised in that said comb (132) comprises a thread (135) able to screw with the thread of said worm
screw (17).
3. An operating device (110) according to claim 1 or 2, characterised in that said carriage (124) comprises a longitudinal through hole (130) able to receive said
worm screw (17) with clearance to allow easy sliding of the carriage (124).
4. An operating device (110) according to claim 3, characterised in that said carriage (124) comprises a transverse seat or chamber (131) communicating with
said longitudinal through hole (130) and able to receive said comb (132).
5. An operating device (110) according to any one of the preceding claims, characterised in that said comb (132) is connected to a lever (138) manually operable by the user to cause
transverse translation of the comb (132).
6. An operating device (110) according to claim 5, characterised in that one end of said lever (138) is hinged to the carriage (124) and a portion of said
lever is hinged to the comb (132) and that the free end of said lever (138) has a
lock (140) able to engage in a locking relationship with said carriage (124).
7. An operating device (110) according to any one of the preceding claims, characterised in that said worm screw (17) is of the reversible type.
8. An operating device (110) according to any one of the preceding claims,
characterised in that it is connected to a post (4), by means of a connecting device (80, 180) comprising:
- a flange (30) designed to be mounted in a fixed manner on said post (4), and
- a bracket (40) designed to be mounted to a hinge ( C ) of said actuator (10) and
to be connected in a fixed manner to said flange (30),
wherein the connection between said flange (30) and said bracket (40) provides for
at least one grooved or splined coupling.
9. An operating device (110) according to claim 8, characterised in that said flange (30) and said bracket (40) of the connecting device comprise respective
holes (34, 41) with respective female grooved profiles (35, 43) which have a plurality
of grooves ad a plurality of teeth parallel with each other, said grooved holes being
in register with each other and engaged by a splined bolt (50) which has a portion
of shaft (52) having a splined male profile with a plurality of grooves and teeth
parallel to each other.
10. An operating device (110) according to claim 9, characterised in that said flange (30) comprises a base plate (31) having a plurality of through holes
(32) to receive fixing bolts for fixing to the post and a supporting plate (33) which
rises in a central position from said base plate (31), said supporting plate having
said grooved hole (34) with its axis substantially parallel to the base plate.
11. An operating device (110) according to claim 9 or 10, characterised in that the shaft (54) of said splined bolt (50) has a threaded end part (53) able to receive
a nut (55) for fixing of said bracket (40) to the base plate (30).
12. An operating device (110) according to any one of claims 8 to 11, characterised in that said connecting device (180) comprises at least one intermediate bracket (60) coupled
by means of grooved coupling to said flange (30) and said bracket (40).
13. An automatic swing gate (1) characterised in that it comprises an operating device (110) and a connecting device (80, 180) according
to any one of the preceding claims.
14. A device (80, 180) for connecting an actuator (10; 110) of a leaf (2) of a swing gate
to a post (4) comprising:
- a flange (30) designed to be mounted fixedly on said post (4), and
- a bracket (40) designed to be assembled to a hinge ( C ) of said actuator (10) and
to be connected fixedly to said flange (30),
characterised in that the connection between said flange (30) and said bracket (40) provides at least one
grooved or splined coupling.
15. A connecting device (80, 180) according to claim 14, characterised in that said flange (30) and said bracket (40) of the connecting device comprise respective
holes (34, 41) with respective female grooved profiles (35, 43) which have a plurality
of grooves and a plurality of teeth parallel to each other, said grooved holes being
in register with each other and engaged by a splined bolt (50) which has a portion
of shaft (52) having a splined male profile with a plurality of grooves and teeth
parallel to each other.