(19) |
 |
|
(11) |
EP 1 147 836 B1 |
(12) |
EUROPÄISCHE PATENTSCHRIFT |
(45) |
Hinweis auf die Patenterteilung: |
|
13.10.2004 Patentblatt 2004/42 |
(22) |
Anmeldetag: 07.04.2001 |
|
|
(54) |
Giessform, umfassend Aussenformteile und darin eingelegte Formstoffkerne
Casting mould comprising outer mould parts and cores of moulding material inserted
into these parts
Moule comprenant pièces de forme extérieure ansi que noyaux en sable disposés dans
celles-ci
|
(84) |
Benannte Vertragsstaaten: |
|
AT BE CH CY DE DK ES FI FR GB GR IE IT LI LU MC NL PT SE TR |
|
Benannte Erstreckungsstaaten: |
|
RO |
(30) |
Priorität: |
19.04.2000 DE 10019310
|
(43) |
Veröffentlichungstag der Anmeldung: |
|
24.10.2001 Patentblatt 2001/43 |
(73) |
Patentinhaber: Hydro Aluminium Mandl&Berger GMBH |
|
4030 Linz (AT) |
|
(72) |
Erfinder: |
|
- Willfort, Peter
4040 Linz (AT)
- Bohn, Horst
4030 Linz (AT)
|
(74) |
Vertreter: COHAUSZ & FLORACK |
|
Patent- und Rechtsanwälte
Postfach 10 18 30 40009 Düsseldorf 40009 Düsseldorf (DE) |
(56) |
Entgegenhaltungen: :
EP-A- 0 280 675 DE-A- 19 531 551 US-A- 5 704 413
|
EP-B- 0 234 877 DE-C- 19 607 805
|
|
|
|
|
|
|
|
|
Anmerkung: Innerhalb von neun Monaten nach der Bekanntmachung des Hinweises auf die
Erteilung des europäischen Patents kann jedermann beim Europäischen Patentamt gegen
das erteilte europäischen Patent Einspruch einlegen. Der Einspruch ist schriftlich
einzureichen und zu begründen. Er gilt erst als eingelegt, wenn die Einspruchsgebühr
entrichtet worden ist. (Art. 99(1) Europäisches Patentübereinkommen). |
[0001] Die Erfindung betrifft eine Gießform, umfassend Außenformteile und darin eingelegt
Formstoffkerne, die miteinander einen Formhohlraum bilden. Die Aüßenformteile können
Teile einer Dauergießform und/oder Formstoffteile/Außenkerne sein.
[0002] Zur Darstellung komplizierter Gußstücke, beispielsweise von Zylinderköpfen, werden
notwendigerweise Formstoffkerne in die Außenformteile eingelegt. Hierbei ist es bereits
bekannt, auch Außenkerne aus Formstoff zu verwenden, so daß wesentliche Teile der
Gußstückaußenflächen nicht von einer metallischen Kokillenwand, sondern von Außenkernen
aus Formstoff abgebildet werden. Dies eignet sich besonders für das Gießen von Aluminium-
und Magnesiumlegierungen.
[0003] Aus der DE 195 31 551 A1 ist ein Verfahren zum Herstellen von Gußstücken aus Leichtmetall
sowie eine dafür vorgesehene verlorene Form auf Basis von Sand bekannt. Die bekannte,
einen Formhohlraum für das Gußstück abbildende verlorene Gießform weist Formaußenteile,
mindestens einen Kern und einen Deckelkern mit mindestens einem Speiser für mindestens
eine Druckmassel auf. Der Deckelkern wird mit einer Kernschlichte behandelt und oberflächlich
abgedichtet. Unmittelbar nach Beendigung des Füllens der Form mit Metallschmelze werden
die Druckmasseln mit einem Druck von bis zu etwa 1 bar beaufschlagt. Auf diese Weise
soll die Qualität des hergestellten Gußstücks verbessert und das Volumen des Speisermaterials
(Druckmassel) reduziert werden. Allerdings sind die in DE 195 31 551 A1 offenbarte
Vorrichtung und das entsprechende Verfahren nicht zum Rotationsgießen geeignet.
[0004] Aus DE 196 07 805 C1 sind ein Verfahren und eine Vorrichtung zum Schmelzen und Gießen
von Metallen in Formen mittels eines Drehgießverfahrens bekannt. Sowohl das Schmelzen
als auch das Gießen findet in einem den Schmelztiegel und die Gießform umfassenden
Vakuum statt. Durch diese Maßnahme soll insbesondere die Möglichkeit geschaffen werden,
auch große Gußteile aus reaktiven Werkstoffen gleichzeitig unter Luftabschluß und
ohne Unterbrechung des Vakuums zeitsparend herzustellen. Die Abbildung komplizierter
Gußstücke mit Hilfe von aufwendig gestalteten, insbesondere aus mehreren Teilen bestehenden
Gießformen ist mit diesem bekannten Verfahren bzw. mit der bekannten Vorrichtung in
der Praxis schwierig.
[0005] Der vorliegenden Erfindung liegt die Aufgabe zugrunde, eine Gießform für das Drehgießen
bereitzustellen, die für komplizierte Gußstücke verwendbar ist.
[0006] Die erfindungsgemäße Lösung hierfür besteht in einer gemäß Anspruch 1 ausgebildeten
Gießform. Erfindungsgemäß kann auf darüberhinausgehende Mittel zur Fixierung der Formstoffkerne
in den Außenformkernen und zwischen den Formstoffkernen untereinander verzichtet werden.
Der Aufbau in mehreren Schichten erlaubt eine komplizierte Formgebung. Die Verwendung
des abschließenden Deckkerns aus Formstoff erlaubt ein Andocken eines Gießbehälters
(Kontaktgießen) und schafft in Verbindung mit der um eine horizontale Achse drehbaren
Aufhängung der Gießform die Voraussetzung für ein Rotationsgießen. Der Deckkern weist
hierzu vorzugsweise zumindest eine Eingußöffnung und zumindest eine Gasaustrittsöffnung
auf.
[0007] Die Seitenteile können insbesondere zwei gegenüber der Grundplatte vom Formhohlraum
entgegengesetzt nach außen wegschiebbare Längsseitenteile und/oder zumindest ein gegenüber
der Grundplatte vom Formhohlraum nach außen wegschwenkbares Stirnseitenteil umfassen.
Durch diese Maßnahme ist ein problemloser Aufbau der in mehreren Schichten aufgestapelten
Innenkerne möglich. Die Seitenteile können hierbei an den Innenseiten Formvorsprünge
aufweisen, die einzelne der Innenkerne zusätzlich gegenüber der Grundplatte festhalten.
Zur Festlegung des Deckkernes können an der Grundplatte oder an zumindest zwei Seitenteilen
verschiebbare Riegel oder schwenkbare Klauen angeordnet sein, die das Paket der Formstoffkerne
innerhalb der Gießform in einer Weise sichern, daß auch beim Drehen der Gießform Verschiebungen
zwischen den Innenkernen ausgeschlossen sind.
[0008] In einer besonders günstigen Art der Verwendung einer erfindungsgemäßen Gießform
wird diese zunächst auf der Grundplatte stapelnd aufgebaut, dann um 180° um eine horizontale
Achse gedreht, so daß der Deckkern, der eine Eingußöffnung aufweist, nach untern zu
liegen kommt. An den Deckkern wird sodann ein Gießbehälter, der mit Schmelze für einen
Gießvorgang gefüllt ist, angedockt. Beim erneuten Drehen um 180° um die horizontale
Achse fließt die Schmelze über die Eingußöffnung im Deckkern in den Formhohlraum.
Anschließend wird der Schmelzebehälter entfernt und es kommt zur Erstarrung des Gußteils,
wonach die Gießform entformt werden kann. Die Gießform wird vorzugsweise jeweils um
eine zu ihrer Längserstreckung parallele Achse gedreht.
[0009] Die Grundplatte ist als Dauerformteil aus Metall ausgebildet; die Außenformteile
können ebenfalls Dauerformteile sein, die mit der Grundplatte mechanisch verbunden
sind, oder Formstoffteile sein, die mit mechanischen Spannmitteln von den Seiten und
von oben auf der Grundplatte zusammen und aufgespannt werden.
[0010] Ein Ausführungsbeispiel der Erfindung ist in den Zeichnungen dargestellt und wird
nachstehend beschrieben.
- Figur 1
- zeigt eine erfindungsgemäße Gießform in einer ersten Stellung nach dem Aufbau;
- Figur 2
- zeigt eine erfindungsgemäße Gießform in einer zweiten Stellung vor dem Beginn eines
Gießvorgangs.
[0011] Die Figuren 1 und 2 werden weitgehend gemeinsam beschrieben. Eine erfindungsgemäße
Gießform 11 umfaßt eine mehrteilige Grundplatte 12, Seitenteile 13, 14, jeweils als
Dauerformteile, eine Mehrzahl von Innenkernen 15, die in mehreren Schichten übereinander
auf der Grundplatte 12 aufgebaut sind, sowie einen Deckkern 16, jeweils aus Formstoff
bestehend. Die mehreren Innenkerne 15 sind in durchgehendem Kraftfluß zwischen der
Grundplatte 12 und dem Deckkern 16 eingespannt. An den Seitenteilen 13, 14 sind Formvorsprünge
17, 18 erkennbar, die einzelne der Innenkerne 15 zusätzlich gegen die Grundplatte
12 halten. Die Seitenteile 13, 14 sind durch Stellzylinder 19, 20 gegenüber der Grundplatte
12 entgegengesetzt gerichtet verschiebbar. Hierbei sind sie gegenüber der dargestellten
Position voneinander entfernbar. Danach kann der stapelnde Aufbau der Innenkerne 15
auf der Grundplatte 12 erfolgen. Danach sind die Seitenteile 13, 14, wie durch entgegengesetzt
gerichtete Pfeile angedeutet, wieder schließbar, um erneut die dargestellte Position
zu erreichen. Danach wird der Deckkern 16 aufgelegt. Auf den Seitenteilen 13, 14 sind
Riegel 21, 22 angeordnet, die zur Montage gegenüber den Seitenteilen 13, 14 zurückgeschoben
werden können und nach dem Auflegen des Deckkerns 16 in die dargestellte Position
vorgeschoben werden können, in der sie den Deckkern 16 gegenüber den Innenkernen 15
und den Seitenteilen 13, 14 halten. In der Grundplatte 12 sind Ausstoßer 23, 24 erkennbar,
die zum Entformen mittels eines Stellzylinders 25 betätigbar sind. Die Grundplatte
12 und damit die gesamte Gießform 11 ist um eine horizontale senkrecht zur Zeichnungsebene
liegende Achse 27 drehbar. Dies gilt in gleicher Weise für eine Säule 27, auf der
ein Schwenkarm 28 gelagert ist, der einen Gießbehälter 29 trägt, der mit einem Stellzylinder
30 parallel zur Säule 27 auf dem Schwenkarm 28 verschoben werden kann.
[0012] In Figur 1 ist die fertig aufgebaute Gießform 11 in ihrer Position unmittelbar nach
dem stapelnden Aufbau gezeigt. Der Gießbehälter 29 hängt überkopf, ist über den Stellzylinder
30 von der Gießform 11 entfernt und durch den Schwenkarm 28 auf der Säule 27 um 90°
gegenüber der Gießform verschwenkt.
[0013] In Figur 2 ist die Gießform 11 mit Säule 27 und Gießbehälter 29 um 180° um die Achse
26 gedreht dargestellt. Der Gießbehälter 29 befindet sich noch in gleicher Relativposition
zur Gießform 11 wie in Figur 1, ist jedoch jetzt nach oben offen und wird mittels
eines Dosierlöffels 31 gerade mit Schmelze 32 für einen Gießvorgang befüllt.
[0014] Nach dem Befüllen des Gießbehälters 29 wird der Schwenkarm 28 um 90° relativ zur
Säule 27 geschwenkt, so daß der Gießbehälter 29 unter der Gießform 11 vor der Säule
27 zu liegen kommt. Sodann wird der Gießbehälter 29 mittels des Zylinders 30 gegen
die Gießform 11 gehoben, bis der Gießbehälter 29 abdichtend an dem Deckkern 16 anliegt.
In der damit erreichten Position wird die Gießform 11 mit angedocktem Gießbehälter
29 wiederum um die Achse 26 um 180° weitergedreht. Die auf den Formhohlraum abgemessene
Schmelze 32 fließt dabei über den Einguß 33 in den Formhohlraum, wobei Gas aus dem
Gasaustritt 34 in den Gießbehälter 29 entweichen kann. Nach Beendigung des Drehvorganges
und damit des Gießvorganges, in der wieder die Stellung der Gießform 11 nach Figur
1 erreicht ist, wird der Gießbehälter 29 mit dem Stellzylinder 30 von der Gießform
11 abgehoben und mittels des Schwenkarms 28 in die in Figur 1 dargestellte Position
zurückgedreht. Nach dem Erstarren kann das Entformen durch Zurückziehen der Seitenteile
13, 14 und Betätigen der Ausstoßer 23, 24 erfolgen.
[0015] Die Seitenteile 13, 14 könnten auch aus Formstoff bestehen, wobei anstelle der Riegel
21, 22 dann mit der Grundplatte verbundene Niederhalter treten würden.
Bezugszeichenliste
[0016]
- 11
- Gießform
- 12
- Grundplatte
- 13
- Seitenteil
- 14
- Seitenteil
- 15
- Innenkern
- 16
- Deckkern
- 17
- Formvorsprung
- 18
- Formvorsprung
- 19
- Stellzylinder
- 20
- Stellzylinder
- 21
- Riegel
- 22
- Riegel
- 23
- Ausstoßer
- 24
- Ausstoßer
- 25
- Stellzylinder
- 26
- Drehachse
- 27
- Säule
- 28
- Schwenkarm
- 29
- Gießbehälter
- 30
- Stellzylinder
- 31
- Dosierlöffel
- 32
- Schmelze
- 33
- Einguß
- 34
- Gasaustritt
1. Gießform, umfassend Außenformteile, darin eingelegte Innenkerne (15) aus Formstoff
und einen abschließenden Deckkern (16) aus Formstoff,
- wobei die Oberflächen der Außenform (12,13,14) und die Oberflächen der Innenkerne
(15) und des Deckkerns (16) miteinander einen Formhohlraumbilden, ,
- wobei die Innenkerne (15) in mehreren Lagen aufeinandergeschichtet sind und in durchgehendem
Kraftfluss zwischen den Außenformteilen (12,13,14) und dem abschließenden Deckkern
(16) eingespannt sind,
- wobei die Außenformteile (12,13,14) eine Grundplatte (12) und mechanisch mit dieser
verbundene und gegenüber dieser bewegliche Seitenteile (13,14) umfassen, und
- wobei die Gießform (11) um eine horizontale Achse (26) drehbar aufgehängt ist.
2. Gießform nach Anspruch 1,
dadurch gekennzeichnet,
daß die Seitenteile (13, 14) zwei gegenüber der Grundplatte (12) vom Formhohlraum entgegengesetzt
nach außen wegschiebbare Längsseitenteile umfassen.
3. Gießform nach Anspruch 1 oder 2,
dadurch gekennzeichnet,
daß die Seitenteile zumindest ein gegenüber der Grundplatte (12) vom Formhohlraum nach
außen wegschwenkbares Stirnseitenteil umfassen.
4. Gießform nach einem der Ansprüche 1 bis 3,
dadurch gekennzeichnet,
daß an der Grundplatte oder an mindestens zwei Seitenteilen (13, 14) verschiebbare Riegel
(21, 22) zur Halterung des Deckkerns (16) angeordnet sind.
5. Gießform nach einem der Ansprüche 1 bis 3,
dadurch gekennzeichnet,
daß an der Grundplatte oder an zumindest zwei Seitenteilen (13, 14) schwenkbare Klauen
zur Halterung des Deckkerns (16) angeordnet sind.
6. Gießform nach einem der Ansprüche 1 bis 5,
dadurch gekennzeichnet,
daß an den Innenseiten der Seitenteile (13, 14) Formvorsprünge (17, 18) vorgesehen sind,
die einzelne Innenkerne (15) zusätzlich gegenüber der Grundplatte (12) festhalten.
7. Gießform nach einem der Ansprüche 1 bis 6,
dadurch gekennzeichnet,
daß in der Grundplatte (12) Ausstoßer (23, 24) angeordnet sind.
8. Gießform nach einem der Ansprüche 1 bis 7,
dadurch gekennzeichnet,
daß im Deckkern (16) zumindest eine Eingußöffnung (33) und zumindest eine Gasaustrittsöffnung
(34) vorhanden ist.
9. Verwendung einer Gießform nach einem der Ansprüche 1 bis 8,
dadurch gekennzeichnet,
daß die Gießform (11) nach dem stapelnden Aufbau auf der Grundplatte (12) um 180° um
eine horizontale Achse (26) gedreht wird,
daß ein Schmelze (32) für einen Gießvorgang enthaltender Gießbehälter (29) von unten
mit seiner Öffnung abdichtend gegen den Deckkern (16) gesetzt wird,
daß die Gießform (11) mit dem anliegenden Gießbehälter (29) erneut um die genannte horizontale
Achse (26) um 180° gedreht wird, wobei die Schmelze (32) durch einen Einguß (33) im
Deckkern (16) in die Gießform gelangt, und daß dann der Gießbehälter (29) nach oben
von der Gießform (11) entfernt wird.
10. Verwendung einer Gießform nach Anspruch 1,
dadurch gekennzeichnet,
daß die Gießform (11) jeweils um eine parallel zu ihrer Längserstreckung liegende horizontale
Achse (26) gedreht wird.
1. Casting mould, comprising outer mould parts, inner cores (15) inserted therein consisting
of moulding material and a closing cover core (16) consisting of moulding material,
- wherein the surfaces of the outer mould (12,13,14) and the surfaces of the inner
cores (15) and the cover core (16) form a mould cavity with one another,
- wherein the inner cores (15) are placed one above the other one in several layers
and clamped in continuous force flow between the outer mould parts (12,13,14) and
the closing cover core (16),
- wherein the outer mould parts (12,13,14) comprise a base-plate (12) and side parts
(13, 14) mechanically connected to this and movable in relation to this, and
- wherein the casting mould (11) is suspended rotatable around a horizontal axis (26).
2. Casting mould according to Claim 1, characterised in that the side parts (13, 14) comprise two longitudinal side parts, which in relation to
the base-plate (12) can be slid away outwards in the opposing direction from the mould
cavity.
3. Casting mould according to Claim 1 or 2, characterised in that the side parts comprise at least one face part, which in relation to the base-plate
(12) can be pivoted away outwards from the mould cavity.
4. Casting mould according to any one of Claims 1 to 3, characterised in that movable locking bars (21, 22) are arranged on the base-plate or on at least two side
parts (13, 14) for holding the cover core (16).
5. Casting mould according to any one of Claims 1 to 3, characterised in that pivotable claws are arranged on the base-plate or on at least two side parts (13,
14) for holding the cover core (16).
6. Casting mould according to any one of Claims 1 to 5, characterised in that mould projections (17, 18) are provided on the insides of the side parts (13, 14),
which additionally hold some of the inner cores (15) in relation to the base-plate
(12).
7. Casting mould according to any one of Claims 1 to 6, characterised in that ejectors (23, 24) are arranged in the base-plate (12).
8. Casting mould according to any one of Claims 1 to 7, characterised in that at least one sprue (33) and at least one gas outlet (34) is present in the cover
core (16).
9. Use of a casting mould according to any one of Claims 1 to 8, characterised in that the casting mould (11) is rotated by 180° around a horizontal axis (26) after being
built up stacked on the base-plate (12),
that a casting vessel (29) containing melt (32) for a casting operation is placed
with its opening forming a seal against the cover core (16) from below,
that the casting mould (11) with the casting vessel (29) in close contact is again
rotated by 180° around the horizontal axis (26) mentioned, whereby the melt (32) gets
into the casting mould through a sprue (33) in the cover core (16) and that the casting
vessel (29) is then removed upwards from the casting mould (11).
10. Use of a casting mould according to Claim 1, characterised in that the casting mould (11) is rotated in each case around a horizontal axis (26) lying
parallel to its longitudinal direction.
1. Moule comprenant des parties de moule extérieures, des noyaux internes (15) en matière
de moule disposés dans celles-ci et un noyau de recouvrement (16) en matière de moule
assurant la fermeture, dans lequel moule les surfaces de moule extérieures (12, 13,
14) et les surfaces des noyaux internes (15) et du noyau de recouvrement (16) forment
ensemble une cavité de moulage, dans lequel les noyaux internes (15) sont superposés
en plusieurs couches et sont enserrés par un flux de force continu entre les parties
de moule extérieures (12, 13, 14) et le noyau de recouvrement (16) assurant la fermeture,
dans lequel les parties de moule extérieures (12, 13, 14) comportent une plaque de
base (12) et des parties latérales (13, 14) assemblées mécaniquement à celle-ci et
mobiles par rapport à celle-ci, et dans lequel le moule (11) est suspendu de manière
rotative autour d'un axe horizontal (26).
2. Moule selon la revendication 1, caractérisé en ce que les parties latérales (13, 14) comprennent deux parties latérales longitudinales
mobiles par rapport à la plaque de base (12) en s'écartant vers l'extérieur dans le
sens opposé à la cavité de moulage.
3. Moule selon la revendication 1 ou 2, caractérisé en ce que les parties latérales comprennent au moins une partie latérale frontale pouvant pivoter
par rapport à la plaque de base (12) en s'écartant vers l'extérieur à partir de la
cavité de moulage.
4. Moule selon l'une quelconque des revendications 1 à 3, caractérisé en ce que des verrous (21, 22) destinés à maintenir le noyau de recouvrement (16), sont disposés
de manière mobile en coulissement contre la plaque de base ou contre au moins deux
parties latérales (13, 14).
5. Moule selon l'une quelconque des revendications 1 à 3, caractérisé en ce que des griffes destinées à maintenir le noyau de recouvrement (16), sont disposées de
manière pivotante contre la plaque de base ou contre au moins deux parties latérales
(13, 14).
6. Moule selon l'une quelconque des revendications 1 à 5, caractérisé en ce que des saillies (17, 18) sont prévues sur les faces intérieures des parties latérales
(13, 14), par lesquelles des différents noyaux internes (15) sont en plus retenus
par rapport à la plaque de base (12).
7. Moule selon l'une quelconque des revendications 1 à 6, caractérisé en ce que des éléments d'éjection (23, 24) sont disposés contre la plaque de base (12).
8. Moule selon l'une quelconque des revendications 1 à 7, caractérisé en ce que le noyau de recouvrement (16) comporte au moins un orifice d'admission (33) et au
moins un orifice d'évacuation du gaz (34).
9. Utilisation d'un moule selon l'une quelconque des revendications 1 à 8, caractérisé en ce que le moule (11) après son montage empilé sur la plaque de base (12) est entraîné en
rotation sur 180° autour d'un axe horizontal (26), en ce qu'une cuve (29) contenant une matière en fusion (32) pour le processus de moulage est
montée par le bas de manière étanche avec son ouverture contre le noyau de recouvrement
(16), en ce que le moule (11) avec la cuve (29), montée contre celui-ci, est à nouveau entraîné en
rotation sur 180° autour dudit axe horizontal (26), moyennant quoi la matière en fusion
(32) pénètre dans le moule par l'intermédiaire d'un orifice d'admission (33) ménagé
dans le noyau de recouvrement (16), et en ce que la cuve (29) est ensuite retirée par le haut pour s'écarter du moule (11).
10. Utilisation d'un moule selon la revendication 1, caractérisé en ce que le moule (11) est dans chaque cas entraîné en rotation autour d'un axe horizontal
(26) disposé parallèlement à la dimension longitudinale dudit moule.

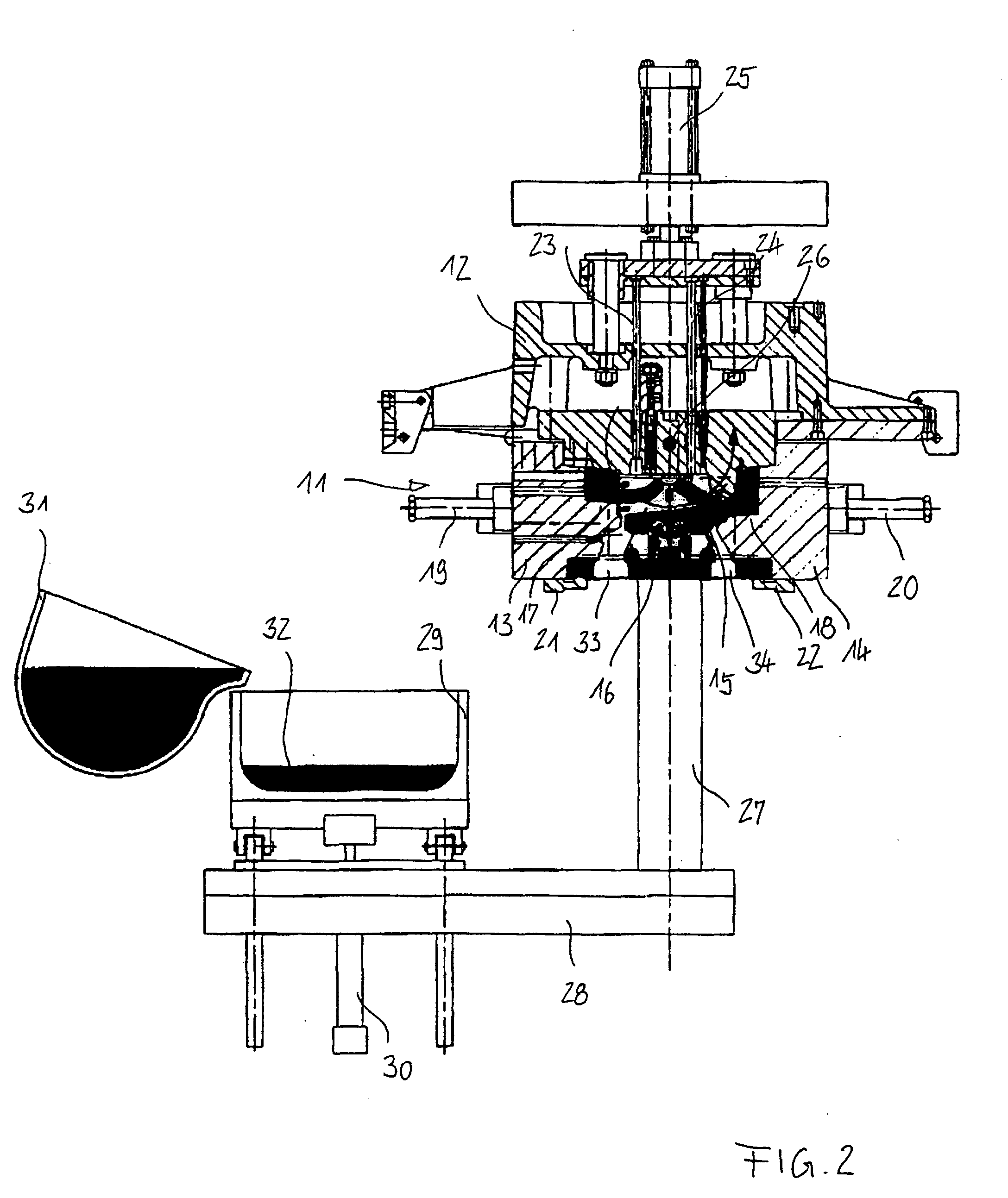