(19) |
 |
|
(11) |
EP 1 316 423 B1 |
(12) |
EUROPÄISCHE PATENTSCHRIFT |
(45) |
Hinweis auf die Patenterteilung: |
|
25.01.2006 Patentblatt 2006/04 |
(22) |
Anmeldetag: 29.11.2001 |
|
(51) |
Internationale Patentklassifikation (IPC):
|
|
(54) |
Rasterwalze und Verfahren zu ihrer Herstellung und Wiederaufbereitung
Engraved roller and method for its production and reprocessing
Rouleau tramé et méthode pour sa production et retraitement
|
(84) |
Benannte Vertragsstaaten: |
|
DE ES FR GB IT |
(43) |
Veröffentlichungstag der Anmeldung: |
|
04.06.2003 Patentblatt 2003/23 |
(73) |
Patentinhaber: FISCHER & KRECKE GMBH & CO. |
|
33609 Bielefeld (DE) |
|
(72) |
Erfinder: |
|
- Kolbe, Wilfried, Dr.
21483 Gülzow (DE)
- Schirrich, Klaus
33729 Bielefeld (DE)
- Steinmeier, Bodo
33739 Bielefeld (DE)
- Brusdeilins, Wolfgang
33659 Bielefeld (DE)
|
(74) |
Vertreter: TER MEER - STEINMEISTER & PARTNER GbR |
|
Artur-Ladebeck-Strasse 51 33617 Bielefeld 33617 Bielefeld (DE) |
(56) |
Entgegenhaltungen: :
EP-A- 0 791 477
|
EP-A- 1 132 209
|
|
|
|
|
|
|
|
|
Anmerkung: Innerhalb von neun Monaten nach der Bekanntmachung des Hinweises auf die
Erteilung des europäischen Patents kann jedermann beim Europäischen Patentamt gegen
das erteilte europäischen Patent Einspruch einlegen. Der Einspruch ist schriftlich
einzureichen und zu begründen. Er gilt erst als eingelegt, wenn die Einspruchsgebühr
entrichtet worden ist. (Art. 99(1) Europäisches Patentübereinkommen). |
[0001] Die Erfindung betrifft ein Verfahren zur Herstellung einer Rasterwalze, insbesondere
für Flexodruckmaschinen, mit einem zylindrischen Kern und einem einem lösbar auf dem
Kern gehaltenen Sleeve, das an seiner Oberfläche eine Rasterschicht mit einem Näpfchenraster
aufweist. Weiterhin bezieht sich die Erfindung auf eine nach diesem Verfahren hergestellte
Rasterwalze und ein Verfahren zur Wiederaufbereitung derselben.
[0002] Beim Flexodruck wird die Druckfarbe mit Hilfe einer Rasterwalze auf den Druckzylinder
aufgetragen. Die Oberfläche der Rasterwalze läuft dabei durch eine Kammerrakel, in
der sich die feinen Näpfchen des Näpfchenrasters mit Druckfarbe füllen. Wenn die Rasterwalze
dann an einer anderen Umfangsstelle mit dem Druckzylinder in Berührung kommt, so wird
die Druckfarbe auf die drukkenden Teile des Druckzylinders übertragen.
[0003] Bekannte Rasterwalzen weisen zumeist einen formstabilen zylindrischen Kern aus Metall
auf, der an beiden Enden mit Achsstummeln versehen oder lösbar auf einer durchgehenden
Achse befestigt ist, so daß er drehantreibbar im Gestell der Druckmaschine gelagert
werden kann. Bei der Herstellung wird die Oberfläche des zylindrischen Kerns mit einer
Grundierungsschicht versehen, auf der dann unmittelbar die aus Keramikmaterial bestehende
Rasterschicht aufgebracht wird. Die einzelnen Näpfchen werden schließlich mit Hilfe
eines Lasers in der Oberfläche der Rasterschicht ausgebildet.
[0004] Wenn die Rasterwalze nach längerem Gebrauch wiederaufbereitet werden soll, weil die
Rasterschicht beschädigt oder verschlissen ist, so muß die gesamte Rasterschicht und
ggf. auch die Grundierungsschicht abgeschliffen werden, bevor nach erneuter Grundierung
wieder eine neue Rasterschicht aufgetragen und durch Laserbearbeitung mit dem Näpfchenraster
versehen werden kann. Dieses Wiederaufbereitungsverfahren ist sehr aufwendig und teuer.
[0005] Aus EP-A-1 132 209 ist eine Rasterwalze bekannt, bei der der zylindrische Kern nicht
aus Metall, sondern aus mit Kohlefasern verstärktem Kunststoff besteht und somit bei
gleicher Stabilität ein geringeres Gewicht hat. Dadurch wird zwar die Handhabung der
Rasterwalze erleichtert und die Laufruhe verbessert, doch ist die Wiederaufbereitung
der Rasterwalze ähnlich aufwendig wie bei Rasterwalzen aus Metall.
[0006] Andererseits sind, beispielsweise aus EP 0 791 477 A2. Rasterwalzen der eingangs
genannten Art bekannt, die auf der sogenannten "Sleeve-Technik" beruhen. Bei diesen
Rasterwalzen ist die Rasterschicht nicht direkt auf dem zylindrischen Kern, sondern
auf einem hohlzylindrischen Sleeve angebracht, das dann auf den zylindrischen Kern
aufgeschoben wird. Bei dieser Technik ist es möglich, das Sleeve wieder vom Kern abzuziehen
und durch ein neues Sleeve zu ersetzen.
[0007] Häufig weist der Kern ein Druckluftsystem auf, mit dem es möglich ist, Druckluft
an auf der Oberfläche des Kerns verteilten Stellen abzugeben und so das Sleeve aufzuweiten,
damit es sich leichter aufschieben und abziehen läßt. Diese Vorgehensweise setzt jedoch
einen speziellen und relativ aufwendigen Aufbau des Sleeves voraus. Bei der Druckluftbeaufschlagung
soll sich nämlich nach Möglichkeit nur der Innendurchmesser des Sleeves vergrößern,
während der Außendurchmesser möglichst unverändert bleiben sollte, weil sonst die
aus Keramikmaterial bestehende Rasterschicht rissig werden und/oder abplatzen könnte.
Folglich muß das Sleeve auf der Innenseite einer möglichst formstabilen Schicht, beispielsweise
aus glasfaserverstärktem Kunststoff, eine kompressible Schicht aufweisen, die beim
Aufweiten des Innendurchmessers komprimiert werden kann. Damit der pneumatische Druck
gleichmäßig auf die innere Oberfläche des Sleeves verteilt wird, sollte unter der
kompressiblen Schicht wieder eine sehr dünne Innenschicht aus steiferem Material vorgesehen
sein.
[0008] Für eine einwandfreie Druckqualität ist es erforderlich, daß das Sleeve sehr gute
Rundlaufeigenschaften aufweist. Dieses Erfordernis läßt sich jedoch bei Sleeves mit
dem oben beschriebenen Aufbau nur schwer erfüllen, weil durch das Vorhandensein der
kompressiblen Schicht die direkte Abstützung der steiferen Außenschicht auf dem formstabilen
Kern verlorengeht. Die Außenschicht des Sleeves muß deshalb in sich eine hohe Eigenstabilität
aufweisen. Dies läßt sich nur durch entsprechend große Schichtdicken erreichen, so
daß sich ein erhöhter Materialverbrauch und erhöhte Kosten ergeben. Die große Wanddicke
des Sleeves, beispielsweise in der Größenordnung von 25 mm oder mehr, erschwert insbesondere
bei größeren Druckbreiten die Handhabung des Sleeves und vergrößert die träge Masse
des Sleeves und damit die Gefahr einer Unwucht, so daß die gewünschte Laufruhe nur
schwer zu erreichen ist. Die große Wanddicke desSleeves erschwert auch die Einhaltung
der Rahmenbedingungen für den Außendurchmesser der Rasterwalze und für deren Innendurchmesser,
d.h. für den Außendurchmesser des Kerns. Der Außendurchmesser der Rasterwalze muß
den Einbaubedingungen im Farbwerk der Druckmaschine sowie Überlegungen Rechnung tragen,
die mit dem Druckprozeß zusammenhängen, beispielsweise Trocknungszeit der Druckfarbe.
Fliehkraft am Umfang der Rasterwalze, Konstruktion der Kammerrakel etc.. Andererseits
entstehen bei einer Verkleinerung des Innendurchmessers erhöhte Kosten für den Kern,
der dann bei kleinerem Außendurchmesser die gleichen Stabilitätsanforderungen erfüllen
muß.
[0009] Ein weiterer Nachteil der Sleeve-Technik besteht darin, daß es beim Aufschieben des
Sleeves auf den Kern häufig zu einer Beschädigung der Rasterschicht an den Enden des
Sleeves kommt.
[0010] Wenn die Rasterschicht beschädigt oder verschlissen ist, so ist der Austausch des
kompletten Sleeves wegen der relativ hohen Kosten für das Sleeve unwirtschaftlich.
Das Abtragen der alten Rasterschieht auf dem Sleeve und der Aufbau einer neuen Rasterschicht
ist ähnlich aufwendig wie bei den herkömmlichen Rasterwalzen, bei denen die Rasterschicht
direkt auf dem Kern angebracht ist.
[0011] Aufgabe der Erfindung ist es, ein Verfahren anzugeben, das eine einfache und kostengünstige
Herstellung und Wiederaufbereitung der Rasterwalzen ermöglicht
[0012] Diese Aufgabe wird bei einem Verfahren der eingangs genannten Art dadurch gelöst,
daß das Sleeve aus einem im wesentlichen Inkompressiblen Material besteht, welches
sich direkt auf dem Kern abstützt, daß zunächst das Sleeve auf dem Kern angebracht
wird und erst dann die Rasterschicht auf dem Sleeve ausgebildet wird, so daß das Sleeve
mit der Rasterschicht nur unter vorübergehender Vergrößerung des Außendurchmessers
des Sleeves aufweitbar ist und damit unter Zerstörung der Rasterschiebt entfernbar
ist.
[0013] Bei der Herstellung der Rasterschicht sitzt somit das Sleeve bereits fest auf dem
Kern, so daß das Sleeve nicht mehr aufgeweitet und auf den Kern aufgeschoben zu werden
braucht und somit keine Gefahr einer Beschädigung der Rasterschicht besteht. Da das
Sleeve folglich auch keine kompressive Schicht aufzuweisen braucht, läßt sich seine
Wanddicke beträchtlich reduzieren, so daß Material und Kosten eingespart werden. Zudem
kann sich das verhältnismäßig steife Material des Sleeves direkt auf dem starren Kern
abstützen, so daß auch bei einem sehr dünnen Sleeve ein einwandfreier Rundlauf der
Rasterwalze gewährleistet werden kann. Insoweit hat die nach dem erfindungsgemäßen
Verfahren hergestellte Rasterwalze ähnliche Vorteile wie herkömmliche Rasterwalzen
ohne Sleeve. Der wesentliche Vorteil gegenüber den sleevelosen Rasterwalzen besteht
darin, daß eine Wiederaufbereitung der Rasterschicht bei Beschädigung oder Verschleiß
wesentlich geringeren Aufwand und geringere Kosten verursacht. Da nämlich das Sleeve
lösbar auf dem Kern gehalten ist, kann, wenn eine Wiederaufbereitung erforderlich
ist, einfach das alte Sleeve mit der darauf sitzenden Rasterschicht entfernt und entsorgt
werden. Anstelle des alten Sleeves wird dann ein neues Sleeve aufgezogen, was wegen
der geringen Wanddicke und dem einfachen Aufbau des Sleeves nur geringe Kosten verursacht,
und auf dem neuen Sleeve wird dann, wenn es wieder fest auf dem Kern sitzt, die neue
Rasterschicht aufgebaut. Damit erübrigt sich das aufwendige Abschleifen der alten
Rasterschicht, so daß der Zeit- und Arbeitsaufwand für das Wiederaufbereiten der Rasterwalze
erheblich reduziert wird.
[0014] Vorteilhafte Ausgestaltungen der Erfindung ergeben sich aus den Unteransprüchen.
[0015] Der Kern kann wie bei der bekannten Sleeve-Technik ein Druckluftsystem aufweisen,
das das Aufschieben des Sleeves auf den Kern und das spätere Entfernen des Sleeves
vom Kern erleichtert. Da das Sleeve beim Aufschieben auf den Kern noch keine Rasterschicht
trägt, ist es unschädlich, wenn sich der Außendurchmesser des Sleeves durch die Druckluftbeaufschlagung
vorübergehend vergrößert. Da das Sleeve erfindungsgemäß nur dann wieder vom Kern abgezogen
wird, wenn ohnehin ein Neuaufbau der Rasterschicht erforderlich ist, kann eine Zerstörung
der Rasterschicht beim Abziehen des alten Sleeves hingenommen werden.
[0016] Die Wanddicke und das Material des Sleeves sind vorzugsweise so aufeinander abgestimmt,
daß die Eigenelastizität des Sleeves ein Aufschieben auf den Kern - ggf. unterstützt
durch das Druckluftsystem - zuläßt und dann einen festen Sitz des Sleeves auf dem
Kern gewährleistet. Eine etwaige anfängliche oder beim Aufschieben auf den Kern entstehende
Unrundheit des Sleeves kann anschließend durch Abdrehen oder eine sonstige Oberflächenbearbeitung
des Sleeves auf dem Kern beseitigt werden, bevor die Rasterschicht aufgetragen wird.
Das Auftragen der Rasterschicht kann in ähnlicher Weise wie bei herkömmlichen Rasterwalzen
ohne Sleeve erfolgen, indem zunächst eine Grundierungsschicht und dann eine Keramikschicht
aufgetragen wird, die beim Auftragen oder durch Nachbearbeitung eine sehr gleichmäßige
Dicke erhält und auf deren Oberfläche dann mit Hilfe eines Lasers die Näpfchen des
Näpfchenrasters gebildet werden. Erforderlichenfalls kann durch eine Nachbearbeitung
das Obertlächefinish verbessert werden.
[0017] Bei der erfindungsgemäßen Rasterwalze hat das Sleeve vorzugsweise nur eine Dicke
von 2-5 mm, und es besteht, abgesehen von der Keramikschicht und ggf. der Grundierungsschicht,
nur aus einer einzigen Materiallage, vorzugsweise aus glasfaserverstärktem Kunststoff.
[0018] Im folgenden wird ein Ausführungsbeispiel der Erfindung anhand der Zeichnung näher
erläutert.
[0019] Es zeigen:
- Fig. 1
- eine Ansicht eines Kerns und, teilweise aufgebrochen, eines Sleeves in einer Anfangsphase
bei der Herstellung einer Rasterwalze;
- Fig. 2
- eine Teilansicht der Rasterwalze nach dem Aufschieben des Sleeves auf den Kern;
- Fig. 3 bis 6
- vergrößerte Darstellungen des Schichtaufbaus der Rasterwalze in verschiedenen Stadien
der Herstellung; und
- Fig. 7
- eine teilweise aufgebrochene Ansicht der nach dem erfindungsgemäßen Verfahren hergestellten
Rasterwalze.
[0020] Figur 1 zeigt (nicht maßstäblich) eine Ansicht eines Kerns 10 einer Rasterwalze.
Der Kern 10 hat die Form eines Hohlzylinders und besteht aus einem formstabilen und
dabei möglichst leichten Material, beispielsweise aus Stahl. Aluminium oder vorzugsweise
aus kohlefaserverstärktem Kunststoff. An beiden Enden des Kerns 10 sind Achsstummel
12 ausgebildet, die zur Lagerung der Rasterwalze in einer nicht gezeigten Druckmaschine
dienen. Wahlweise kann anstelle der Achsstummel 12 auch eine durchgehende Achse vorgesehen
sein, auf der der Kern 10 mit Hilfe eines nicht gezeigten Hydrauliksystems lösbar
aufgespannt ist. Im Inneren des Kerns 10 und in einem der Achsstummel 12 ist ein an
sich bekanntes, nicht näher dargestelltes Druckluftsystem untergebracht, über das
Druckluft zugeführt werden kann, die über mehrere auf der Oberfläche des Kerns 10
verteilte Öffnungen 14 austritt. Die Öffnungen 14 bilden mindestens einen auf dem
Umfang des Kerns 10 umlaufenden Kranz 16, der in geringem Abstand zu dem Ende des
Kerns 10 liegt (rechts in Figur 1), von dem aus ein Sleeve 18 auf den Kern aufgeschoben
wird.
[0021] Das Sleeve 18 ist in Figur 1 rechts neben dem Kern 10 dargestellt und besteht aus
einem dünnwandigen, einlagigen Rohr aus glasfaserverstärktem Kunststoff, das eine
Wanddicke von beispielsweise 2 mm hat und dessen Innendurchmesser mit dem Außendurchmessers
des Kerns 10 übereinstimmt. Wenn das Sleeve 18 auf den Kern 10 aufgeschoben wird,
so wird das Druckluftsystem aktiviert, so daß Druckluft aus den Öffnungen 14 austritt
und das Sleeve 18 aufweitet, sobald es auf ein Ende des Kerns aufgeschoben worden
ist. Nach dem vollständigen Aufschieben des Sleeves 18 auf den Kern 10 wird das Druckluftsystem
abgeschaltet, so daß das Sleeve 18 elastisch schrumpft und dann fest auf dem Kern
10 sitzt. Dieser Zustand ist in Figur 2 dargestellt.
[0022] Figur 3 zeigt in einer Ausschnittsvergrößerung zu Figur 2 die einlagige Wand des
Sleeves 18, die sich unmittelbar auf der Umfangsfläche des Kerns 10 abstützt. Erforderlichenfalls
kann die Umfangsfläche des auf dem Kern 10 sitzenden Sleeves 18, beispielsweise auf
einer Drehbank, nachbearbeitet werden, so daß eine exakt zylindrische und auf die
Achse des Kerns 10 zentrlerte Form der Umfangsfläche des Sleeves 18 erreicht wird.
Etwaige geringfügige Verformungen des Sleeves, die beim Aufschieben auf den Kern 10
eingetreten sein mögen, werden auf diese Weise beseitigt.
[0023] Anschließend wird auf der Umfangsfläche des Sleeves 18 eine Grundierungsschicht 20
aufgetragen (Figur 4), auf der dann mit bekannten Verfahren eine Keramikschicht 22
(Figur 5) aufgebracht wird, deren Dicke sehr präzise eingestellt wird, so daß auch
die Umfangsfläche der Keramikschicht 22 exakt zylindrisch ist.
[0024] Mit Hilfe eines Lasers wird dann in die Umfangsfläche der Keramikschicht 22 ein feines
Raster aus Näpfchen 24 eingebrannt, wie in Figur 6 gezeigt ist.
[0025] Auf diese Weise erhält man als Endprodukt die in Figur 7 dargestellte Rasterwalze
26. Da sich bei dieser Rasterwalze die mit dem Näpfchenraster 26 versehene Keramikschicht
22 unmittelbar über die verhältnismäßig dünne und im wesentlichen inkompressible Schicht
aus glasfaserverstärktem Kunststoff, die das Sleeve 18 bildet, auf dem starren Kern
10 abstützt, ergeben sich ausgezeichnete Laufeigenschaften der Rasterwalze 26, die
bei gegebener Stabilität ein geringes Gewicht und ein entsprechend geringes Trägheitsmoment
aufweist und bei der ein sehr günstiges Verhältnis zwischen dem Außendurchmesser und
dem Durchmesser des Kerns 10 besteht.
[0026] Das nur aus einer einzigen Kunststoffschicht bestehende Sleeve 18 läßt sich mit geringem
Materialeinsatz kostengünstig herstellen.
[0027] Wenn die das Näpfchenraster 24 bildende Keramikschicht 22 (Rasterschicht) verschlissen
oder beschädigt ist, wird das Sleeve 18 vom Kern 10 gelöst und entsorgt. Zu diesem
Zweck wird vorübergehend wieder das Druckluftsystem aktiviert, so daß sich das Sleeve
mühelos von dem Kern 10 abziehen läßt. Anschließend wird auf die gleiche Weise wie
in Figur 1 ein neues Sleeve 18 aufgeschoben, und die in Figuren 3 bis 6 dargestellten
Schritte werden wiederholt, so daß man mit geringem Arbeitsaufwand eine neuwertige
Rasterwalze erhält.
1. Verfahren zur Herstellung einer Rasterwalze (26), insbesondere für Flexodruckmaschinen,
mit einem zylindrischen Kern (10) und einem lösbar auf dem Kern gehaltenen Sleeve
(18), das an seiner Oberfläche eine Rasterschicht (22) mit einem Näpfchenraster (24)
aufweist, dadurch gekennzeichnet, daß das Sleeve (18) aus einem im wesentlichen inkompressiblen Material besteht, welches
sich direkt auf dem Kern (10) abstützt, daß zunächst das Sleeve (18) auf dem Kern
(10) angebracht wird und erst dann die Rasterschicht (22) auf dem Sleeve (18) ausgebildet
wird, so daß das Sleeve (18) mit der Rasterschicht (22) nur unter vorübergehender
Vergrößerung des Außendurchmessers des Sleeves (18) aufweitbar ist und damit unter
Zerstörung der Rasterschicht (22) entfernbar ist.
2. Verfahren nach Anspruch 1, dadurch gekennzeichnet, daß das Sleeve (18) axial auf den Kern (10) aufgeschoben und dabei mittels Druckluft,
die über Öffnungen (14) in der Umfangsfläche des Kerns (10) austritt, vorübergehend
aufgeweitet wird.
3. Rasterwalze, insbesondere für Flexodruckmaschinen, mit einem zylindrischen Kern (10)
und einem lösbar auf dem Kern gehaltenen Sleeve (18), das an seiner Oberfläche eine
Rasterschicht (22) mit einem Näpfchenraster (24) aufweist, dadurch gekennzeichnet, daß das Sleeve (18) aus einem im wesentlichen inkompressiblen Material besteht, welches
sich direkt auf dem Kern (10) abstützt, und daß das Sleeve (18) mit der Rasterschicht
(22) nur unter vorübergehender Vergrößerung des Außendurchmessers des Sleeves (18)
aufweitbar ist und damit unter Zerstörung der Rasterechicht (22) entfernbar ist.
4. Rasterwalze nach Anspruch 3, dadurch gekennzeichnet, daß das Sleeve (18) aus glasfaserverstärktem Kunststoff besteht.
5. Rasterwalze nach einem der Ansprüche 3 bis 4, dadurch gekennzeichnet, daß das Sleeve (18) aus einer einzigen Materiallage besteht, die die Rasterschicht (22)
und ggf. eine zwischen der Rasterschicht und der einzigen Materiallage eingefügte
Grundierungsschicht (20) trägt.
6. Rasterwalze nach einem der Ansprüche 3 bis 5, dadurch gekennzeichnet, daß die Wanddicke des Sleeves (18) einschließlich der Rasterschicht (22) nicht mehr als
10 mm beträgt, bei einer Druckbreite der Rasterwalze von 1,5 bis 2 m oder mehr.
7. Rasterwalze nach einem der Ansprüche 3 bis 6. dadurch gekennzeichnet, daß der Kern (10) aus kohlefaserverstärktem Kunststoff besteht.
8. Verfahren zur Wiederaufbereitung einer Rasterwalze, die nach Anspruch 1 oder 2 hergestellt
ist, oder einer Rasterwalze nach einem der Ansprüche 3 bis 7, dadurch gekennzeichnet, daß das Sleeve (18) vom Kern (10) abgezogen wird und an seiner Stelle ein neues Sleeve
(18) ohne Rasterschicht auf den Kern (10) aufgeschoben wird, welches Sleeve (18) aus
einem im wesentlichen inkompressiblen Material besteht, welches sich direkt auf dem
Kern (10) abstützt, und daß dann auf dem neuen Sleeve eine neue Rasterschicht (22)
ausgebildet wird, so daß das neue Sleeve (18) mit der neuen Rasterschicht (22) nur
unter vorübergehender Vergrößerung des Außendurchmessers des Sleeves (18) aufweitbar
ist und damit unter Zerstörung der Rasterschicht (22) entfernbar ist.
1. Procédé de fabrication d'un rouleau tramé (26), en particulier pour machine d'impression
flexographique, avec un mandrin cylindrique (10) et un manchon (18) maintenu de manière
amovible sur le mandrin et qui présente à sa surface une couche tramée (22) avec une
trame de godets (24), caractérisé en ce que le manchon (18) est constitué d'un matériau sensiblement incompressible qui s'appuie
directement sur le mandrin (10), en ce que l'on place d'abord le manchon (18) sur le mandrin (10) puis après seulement la couche
tramée (22) est réalisée sur le manchon (18), ce qui fait que le manchon (18) avec
la couche tramée (22) ne peut être élargi que moyennant une augmentation temporaire
du diamètre extérieur du manchon (18), et peut ainsi être enlevé moyennant une destruction
de la couche tramée (22).
2. Procédé selon la revendication 1, caractérisé en ce que le manchon (18) est enfilé axialement sur le mandrin (10) et est temporairement élargi
au moyen d'air comprimé qui sort par des orifices (14) de la surface périphérique
du mandrin (10).
3. Rouleau tramé, en particulier pour machine d'impression flexographique, avec un mandrin
cylindrique (10) et un manchon (18) maintenu de manière amovible sur le mandrin et
qui présente à sa surface une couche tramée (22) avec une trame de godets (24), caractérisé en ce que le manchon (18) est constitué d'un matériau sensiblement incompressible qui s'appuie
directement sur le mandrin (10), et en ce que le manchon (18) avec la couche tramée (22) ne peut être élargi que moyennant une
augmentation temporaire du diamètre extérieur du manchon (18), et peut ainsi être
enlevé moyennant une destruction de la couche tramée (22).
4. Rouleau tramé selon la revendication 3, caractérisé en ce que le manchon (18) est constitué d'une matière plastique renforcée par des fibres de
verre.
5. Rouleau tramé selon l'une des revendications 3 ou 4, caractérisé en ce que le manchon (18) est constitué d'une seule couche d'un matériau, qui porte la couche
tramée et éventuellement une couche d'apprêt (20) insérée entre la couche tramée et
l'unique couche de matériau.
6. Rouleau tramé selon l'une des revendications 3 à 5, caractérisé en ce que l'épaisseur de la paroi du manchon (18) y compris de la couche tramée (22) n'est
pas supérieure à 10 mm, dans le cas d'une largeur d'impression du rouleau tramé de
1,5 à 2 m ou plus.
7. Rouleau tramé selon l'une des revendications 3 à 6, caractérisé en ce que le mandrin (10) est constitué d'une matière plastique renforcée par des fibres de
carbone.
8. Procédé de retraitement d'un rouleau tramé, qui est fabriqué selon la revendication
1 ou 2, ou d'un rouleau tramé selon l'une des revendications 3 à 7, caractérisé en ce que le manchon (18) est retiré du mandrin (10) et on enfile à sa place sur le mandrin
(10) un nouveau manchon (18) sans couche tramée, lequel manchon (18) est constitué
d'un matériau sensiblement incompressible qui s'appuie directement sur le mandrin
(10), et en ce que sur le nouveau manchon on réalise une nouvelle couche tramée (22), ce qui fait que
le nouveau manchon (18) avec la nouvelle couche tramée (22) ne peut être élargi que
moyennant une augmentation provisoire du diamètre extérieur du manchon (18), et peut
ainsi être enlevé moyennant une destruction de la couche tramée (22).
1. A method of manufacturing an anilox roller, in particular for a flexographic printing
press, the anilox roller comprising a cylindrical core (10) and a sleeve (18) detachably
held on the core and having at its surface an anilox layer (22) with a grid pattern
(24) of pits, characterised in that the sleeve (18) consists of an essentially incompressible material which is supported
directly on the core (10), that, at first, the sleeve (18) is mounted on the core
(10), and only then the anilox layer (22) is formed on the sleeve (18), so that the
sleeve (18) can be expanded only with temporary increase of the outer diameter of
the sleeve (18) and can thus be removed while the anilox layer (22) is destroyed.
2. The method of claim 1, characterised in that the sleeve (18) is axially thrust onto the core (10), while preliminarily widening
the sleeve by means of compressed air discharged through openings (14) in the peripheral
surface of the core (10).
3. An anilox roller, in particular for a flexographic printing press, comprising a cylindrical
core (10) and a sleeve (18) which is detachably held on the core and has at its surface
an anilox layer (22) with a grid pattern of pits (24), characterised in that the sleeve consists of an essentially incompressible material which is supported
directly on the core (10), and that the sleeve (18) having the anilox layer (22) is
removable only with temporary increase of the outer diameter of the sleeve (18) and
hence with destruction of the anilox layer (22).
4. The anilox roller of claim 3, characterised in that the sleeve (18) is made of glass fibre-reinforced synthetic resin.
5. The anilox roller of claim 3 or 4, characterised in that the sleeve (18) consists of a single layer of material carrying the anilox layer
(22) and, optionally, a primer layer (20) interposed between said single layer and
said anilox layer.
6. The anilox roller of any of the claims 3 to 5, characterised in that the wall thickness of the sleeve (18), including the anilox layer (22), is not larger
than 10 mm, for a printing width of the anilox roller of 1.5 to 2 m or more.
7. The anilox roller of any of the claims 3 to 6, characterised in that the core (10) is made of carbon fibre-reinforced synthetic resin.
8. A method of recycling an anilox roller obtained by the method according to claim 1
or 2, or an anilox roller of any of the claims 3 to 7, characterised in that the sleeve (18) is withdrawn from the core (10) and, in its place, a new sleeve (18)
without anilox layer is thrust onto the core (10), the sleeve (18) consisting of an
essentially incompressible material which is supported directly on the core (10),
and that, then, a new anilox layer (22) is formed on the new sleeve (18), so that
the new sleeve (18) having the new anilox layer (22) can be expanded only with temporary
increase of the outer diameter of the sleeve (18) and can thus be removed while the
anilox layer (22) is destroyed.
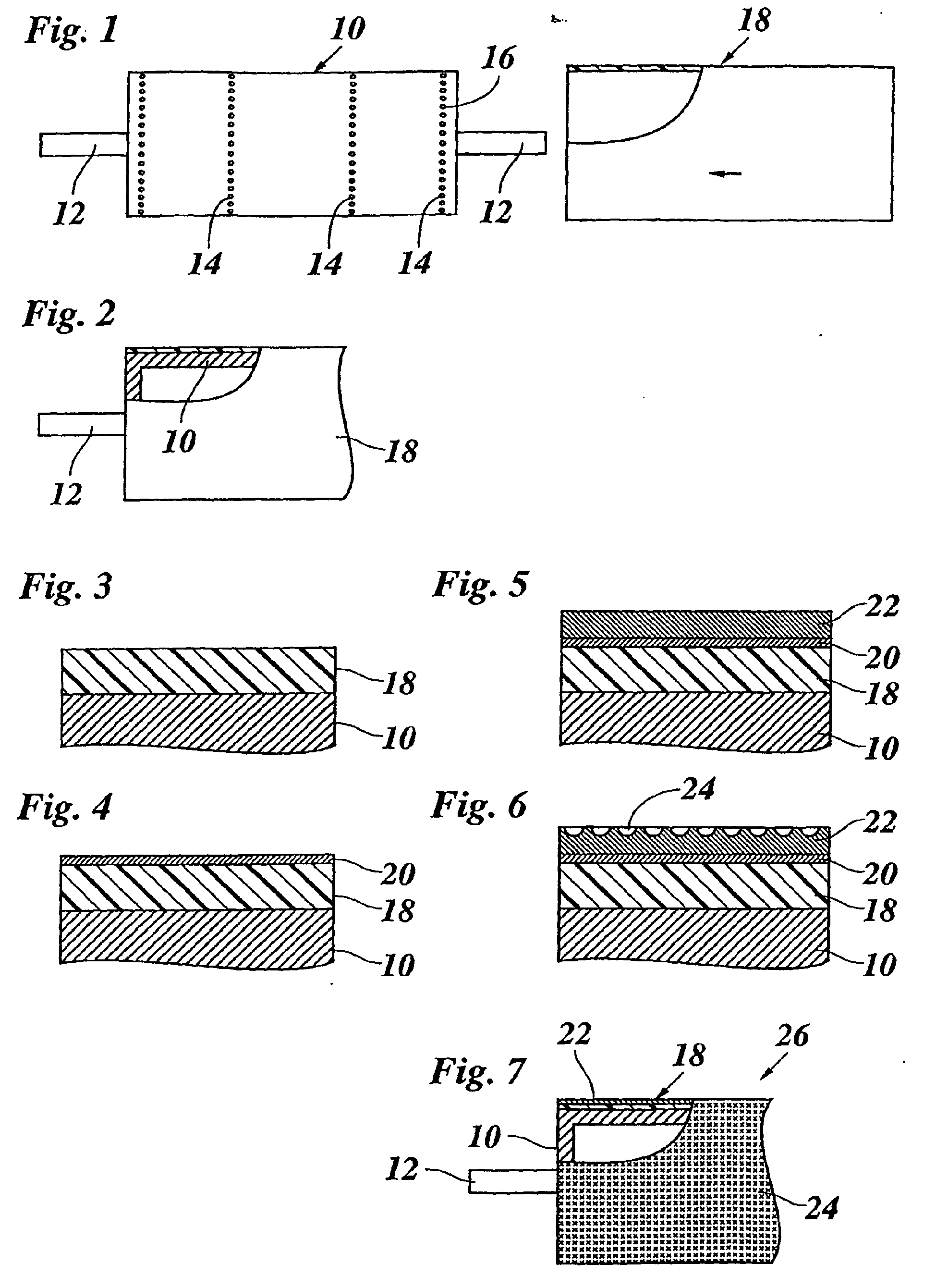