[0001] The present invention relates to a sample tube, for instance for use in a PCR thermal
cycler.
[0002] Such a tube is known from US patent 6,015,534. During use, the known sample tube
is filled with a sample. The sample may contain, for instance, DNA. In that case,
the sample tube may be used in combination with a thermal cycler, to perform a polymerase
chain reaction (PCR) to amplify the DNA, wherein a certain liquid reaction mixture
is cycled through a PCR protocol including several different temperature incubation
periods. In many appliances, it is desired to submit a relatively large number of
samples to the same treatment, using a respective number of sample tubes. For example,
in US 6,015,534, 96 sample tubes are used at the same time, in a microtiter plate
format, for performing PCR reactions.
[0003] The sample tube known from US 6,015,534 is a thin walled disposable tube, having
a conical section, for decreasing the delay between changes in the temperature of
a sample block and corresponding changes in temperature of the reaction mixture. Particularly,
this known sample tube is made of polypropylene such as Himont PD701 with a wall thickness
in the range of 0.009 to 0.012 inches, corresponding to 226 - 301 µm. A problem of
the sample tube shown in US 6,015,534 is, that a delay between changes in the temperature
of an environment of the tube on the one hand and corresponding changes in temperature
of a sample contained therein on the other hand are still relatively large. Therefore,
it is relatively difficult to bring the sample within a desired period of time to
a desired treatment temperature during use. Consequently, the throughput of any temperature
dependent process using this known sample tubes, is relatively low. It is also difficult
to achieve a desired accurate, identical temperature control of numerous samples,
when using a large number of the known sample tubes. This may hamper the process,
leading to undesired results thereof.
[0004] From US 6,140, 631, a cylindrical sample container is known, made of metal having
a thickness in the range from 0.02 mm to 1.0 mm, further having a resin layer having
a thickness ranging from 1µm to 100 µm. More specifically, US 6,140,631 discloses
one example of an aluminium container, having a bottomed cylindrical shape and a wall
thickness of 0.29 mm, further having a polypropylene layer of 0.01 mm. According to
US 6,140,631, this example of an aluminium sample container had a 40% of increase
of speed of temperature rise, whereas a delay of temperature rise is decreased, in
comparison with one mainly constituted of polypropylene. A disadvantage of this example
of an aluminium sample container is, that its utilisation still leads to relatively
long delays in the thermal control of a sample contained therein. Besides, the thin
wall of this aluminium sample container is relatively weak, which makes the handling
of that container difficult. Also, aluminium is relatively vulnerable to higher temperatures,
so that the aluminium sample container may not be so durable during a certain thermal
process.
[0005] The present invention aims to provide a durable sample tube, suitable for a precise
control of the temperature of a sample contained therein, wherein a sample can be
brought to one or more desired temperatures relatively fast.
[0006] According to one aspect of the invention, there is provided a sample tube, for instance
for use in a PCR thermal cycler, wherein the tube comprises a steel wall.
[0007] Surprisingly, the sample tube according to the invention provides for relatively
short delays between changes in the temperature of an environment of the tube on the
one hand and corresponding temperature changes of a sample contained in the tube on
the other hand. Therefore, a precise control of the sample temperature can be achieved
during use of the present sample tube. For instance, any desired warming up of contents
of the present sample tube can be achieved relatively fast, so that said contents
may undergo any thermal process relatively fast, resulting in a high throughput and/or
short analysis times. Similarly, any desired cooling down of a sample contained in
the tube can be achieved relatively fast.
[0008] The steel wall has a relatively homogeneous thickness distribution, particularly
in respect to the wall thickness of a known polypropylene sample tube. Because of
the relatively homogeneous thickness distribution of the present sample tube wall,
heat conductivity through the tube wall can be controlled more effectively, leading
to an increased chance of success of a temperature dependent treatment, reaction and/or
process which takes place in the sample tube during use. Also, because of the homogeneous
thickness distribution of the steel tube wall, any results concerning samples which
have been treated using a number of the present sample tubes at the same time, will
be more reliable.
[0009] Furthermore, the sample tube according to the present invention is durable. Particularly,
the steel tube wall can be made relatively thin, for instance in the below-mentioned
range of about 50-200 µm whilst remaining sufficiently robust for use. The present
sample tube can be handled conveniently and at high speed, for instance using robot
handlers or the like, wherein the risk is low that the tube is deformed or broken.
[0010] Also, the sample tube according to the present invention is relatively resistant
to temperature changes and to high temperatures, depending on the polymer used, of
up to 200°C. Consequently, the tube wall may substantially retain its shape and its
size during a thermal process, also retaining said desired homogeneous wall thickness
distribution, so that a desired temperature control of the contents of the sample
tube can be upheld.
[0011] The present invention is based, amongst others, on the notion, that steel has a relatively
high heat transfer coefficient. Besides, steel has a relatively low heat capacity,
for instance with respect to polypropylene and aluminium. The application of steel
in the wall of a sample tube brings a fast and efficient heat transfer between the
tube environment and a sample contained in the tube. Until the present invention,
apparently to use steel as a sample tube wall material was unknown.
[0012] According to an embodiment of the invention, at least part of said steel wall forms
a conical section. The conical section is suitable for holding a relatively small
sample within a confined space, so that the sample may be thermally controlled in
a well-defined manner. Besides, such a conical section can make good thermal contact
with, for instance, a surrounding heat exchanger. The volume of said conical section
may be, for instance, in the range of about 0.01-0.50 ml, for instance about 100 µl.
[0013] According to a further aspect of the invention, the inner surface of said steel wall
comprises a polymer coating.
[0014] Such a coating prevents direct contact between the sample and the steel wall. The
polymer coating may prevent certain samples from sticking to the steel wall. Besides,
the coating may protect samples which may be adversely affected by direct contact
with steel. Furthermore, the polymer coating avoids interference between the sample
and the steel wall. A suitable coating material comprises a polypropylene or a polyester.
[0015] Preferably, the polymer coating is relatively thin. For instance, said polymer coating
may have a thickness which is less than the thickness of said steel wall. Therefore,
the overall tube wall, comprising the steel wall and said polymer coating, has a relatively
high heat transfer coefficient for providing precise and fast control of the sample
temperature.
[0016] According to a preferred embodiment of the invention, the said steel wall has a thickness
in the range of about 50-200 µm, more preferably 70-140 µm.
[0017] The heat capacity of such a sample tube is relatively low, which leads to desired
high rates of heat transfer between the tube environment and the tube contents. Thus,
the temperature of the tube contents can be controlled efficiently.
[0018] According to a further aspect of the invention, the internal volume of the tube is
less than about 1 ml.
[0019] In that case, the tube is particularly suitable for thermally controlling small samples,
for instance for sample treatment and/or sample testing purposes. For instance, the
internal volume of the sample tube may be in the range of about 0,1-0,5 ml.
[0020] According to an other aspect of the invention, there is provided a method for manufacturing
a sample tube, particularly a sample tube according to the invention, wherein a blank
is cut from steel sheet and the blank is drawn to a tube. The blank may be of polymer
coated steel sheet or alternatively, draw forming may take place in a so-called polymer
injection forming process.
[0021] Embodiments of the invention will now be described, by way of example only, with
reference to the accompanying schematic drawing.
Fig. 1 is a cross-section of a sample tube;
fig. 2 shows an application of the embodiment of fig. 1.
[0022] In the present application, any value which is provided with a term such as 'circa',
'about' or 'substantially', is to be construed as indicating a range from minus 10%
to plus 10% of that value.
[0023] Figure 1 shows a cross-section of a sample tube 1, for instance for use in a PCR
thermal cycler. Particularly, the sample tube 1 has an upper, substantially cylindrical
section 4 and an integral lower, conical section 5 having a rounded tip. During use,
a sample can be held in a relatively small space, in the lower part of the conical
section 5.
[0024] According to the present invention, the wall 2 of the tube 1 is made from steel.
In an embodiment, the inner surface of the tube wall 2 is coated with a plastic layer
3. Preferably, the coating 3 comprises of polypropylene. Depending on the desired
application of the sample tube, different coating materials may be used.
[0025] The overall internal volume of the tube 1, which is surrounded by the surface of
said coating 3, is less than about 1 ml. For instance, the internal volume of the
sample tube is in the range of about 0.1-0.5 ml, particularly about 0.2 ml. Besides,
the volume I of said conical section 5 is preferably less than 0.2 ml, for instance
about 100 µl, for receiving relatively small samples during use.
[0026] At least part of said steel wall 2 has a thickness in the range of circa 50-100 µm.
In the present embodiment, at least the conical section 5 has such a wall thickness
in the range of circa 50-100 µm, measured in a direction perpendicular to said conical
section, which direction has been indicated with a dashed line X in fig. 1. The first,
cylindrical section 4 may have a similar wall thickness, or for instance a somewhat
greater thickness.
[0027] Said coating 3 has a thickness which is less than the thickness of said steel wall
2. Preferably, the thickness of the coating 3 is less than about 50 µm, particularly
less than about 25 µm.
[0028] During use, the sample tube 1 is filled with a sample S. Then, the temperature of
the tube 1 is being controlled, for instance by heating or cooling the tube wall 2,
for controlling the temperature of the sample S.
[0029] Fig. 2 shows a particular embodiment of the use of a number of sample tubes 1. Herein,
the sample tubes 1 are positioned in suitable apertures 6 of a metal block H. Said
apertures 6 are substantially conical for receiving the conical sections 5 of the
sample tubes 1. The temperature of the metal block H is controlled for controlling
the temperatures of the sample tubes 1 and the respective samples S. For instance,
a method for performing a polymerase chain reaction may be carried out, using sample
tubes 1 in combination with the metal block H.
[0030] Because the sample tubes 1 comprise relatively thin steel walls 2 having thin coatings
3, the temperatures of the samples S can be controlled homogeneously, precisely, efficiently
and fast. This is particularly ascribed to the application of steel tube walls 2,
since steel has a relatively low heat capacity and a relatively high thermal conductivity.
[0031] Furthermore, the substantially steel sample tubes 1 are relatively durable, mechanically
as well as thermally. The present sample tubes 1 are robust, as well as relatively
resistant against temperature changes. Thus, a thermal process utilizing the sample
tubes 1, as has been shown in fig. 2, can be performed relatively safely, wherein
chances of deformation or breakage of any of the tubes 1 are relatively low. The robustness
of the tubes 1 also allows a fast and safe handling of the tubes 1, for instance transportation
to and from the metal block H.
Example:
[0032] The following example compares thermal aspects of various sample tubes, having tube
walls comprising different materials. A first tube I comprises a polyethylene wall,
such as disclosed in US patent 6,015,534 . A second tube II comprises an aluminium
wall and a polypropylene coating, similar to the one disclosed in US 6,140,613. A
third tube III is a tube according to the present invention, comprising a thin, robust
steel wall and a polypropylene coating.
[0033] Tube III according to the invention, may be made by cutting a circular blank with
a diameter of 14.0 mm from a polymer coated steel sheet. The blank is drawn to a cup
of 8.0 mm diameter having a height of 4.1 mm in a first drawing step and to a cup
of 5.5 mm diameter and 7.5 mm height in a successive drawing step. In further successive
operations the bottom of the cup is drawn to a conical shape. Finally the tube is
cut to the required height to remove earing that may result from the forming operations.
[0034] For simplicity, each tube I, II, III is assumed to be just conical, having a height
H of 10 mm and an overall base plane diameter Db of 5.5 mm. Dimensions H, Db, Do,
Di of the tubes have been indicated in fig. 1.
[0035] In the first tube I, having a polypropylene wall only, the inner surface of the polyethylene
wall encloses a cone having the base plane diameter Di of 5.0 mm. The volume V
I of this polyethylene wall is about 1.5*E-8 m
3.
[0036] The second tube II has an aluminium wall 2 with a thickness of 0.29 mm, combined
with a 0.01 mm layer 3 of polypropylene. The volume of the aluminium wall 2 is about
1.8*E-8 m
3. The volume of the polyethylene coating 3 is about 5.3*E-10 m
3.
[0037] In the third tube III, the steel wall has a thickness of 0.135 mm. The polymer layer
3 has a thickness of 0.015 mm. The volume of the steel wall is about 5.8*E-9 m
3, whereas the volume of the coating is about 9.7*E-10 m
3.
[0038] Materials properties density ρ and heat capacity c
p of steel, polypropylene (PP) and aluminium are depicted in table I.
Table I - materials properties
|
ρ (kg/m3) |
cp (J/kg.K) |
steel |
7870 |
46.9 |
PP |
906 |
1700 |
Al |
2700 |
922 |
[0039] The amount of energy, necessary to heat up a substance by a certain amount of degrees
ΔT (K), is given by the following formula:
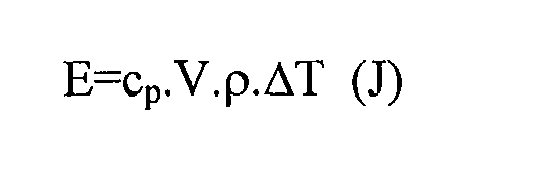
wherein E is the energy (J), c
p is the heat capacity (J/kg.K), V is the volume of the material (m
3) and ρ is the specific density (kg/m
3).
[0040] Table II gives the results for E, for uncoated and internally polymer coated tubes
(values in brackets) respectively, following from the above formula for the tube variants
I, II, III, in case a temperature rise of 40K is desired.
Table II - results
|
wall thickness (mm) and material |
coating thickness (mm) and material |
E(J) |
tube I |
0.22 mm PP |
- |
0.92 (-) |
tube II |
0.29 mm Al |
(0.01 mm PP) |
1.77 (1.81) |
tube III |
0.08 mm steel |
(0.015 mm PP) |
0.86 (0.92) |
[0041] From table II, it follows that the tube according to the present invention, being
the third tube III, has a somewhat lower heat capacity compared to the first tube
I, which is made completely from polypropylene. The heat capacity of the second tube
II, which has an aluminium wall, is significantly higher than the third tube III.
The third tube will provide a relatively fast and precise thermal control of the contents
thereof, because of the relatively high heat conductivity of steel.
[0042] While a specific embodiment of the invention has been described above, it will be
appreciated that the invention may be practised otherwise than as described, within
the scope of the accompanying claims.
[0043] Said plastic coating may comprise one or more plastics, for instance polypropylene
and/or other suitable plastics.
[0044] Furthermore, each sample tube may be disposable, to prevent cross-contamination.
Also, the sample tube may be provided with a cover.
[0045] Further, a number of sample tubes may be provided in an assembly of tubes, for instance
in a rod-like assembly, plate-like assembly, in a microtiter plate format, and the
like.
[0046] Besides, various means can be used for controlling the temperature of the sample
tube and its contents. For instance, to that aim, a heat exchanger, a thermal cycler,
metal sample block, liquid bath, gas flow or airflow, oven etcetera can be used.
[0047] Also, an upper sample section 4 may be provided with handling means, for instance
a rim, flange or the like, for handling purposes.
[0048] Each sample tube may have various shapes and dimensions.
1. Sample tube, for instance for use in a PCR thermal cycler, wherein the tube (1) comprises
a steel wall (2).
2. Sample tube according to claim 1, wherein at least part of said steel wall (2) has
a thickness in the range of circa 50-200 µm, preferably 70-140 µm.
3. Sample tube according to claim 1 or 2, wherein at least part of said steel wall forms
a conical section.
4. Sample tube according to claims 2 and 3, wherein the conical section has a wall thickness
in the range of circa 50-100 µm.
5. Sample tube according to claim 4 or 5, wherein the volume (I) enclosed by said conical
section is in the range of about 0.05-0.5 ml, for instance about 100 µl.
6. Sample tube according to any of the preceding claims, wherein the inner surface of
said steel wall (2) comprises a polymer coating.
7. Sample tube according to claim 6, wherein the coating (3) comprises polypropylene.
8. Sample tube according to claim 6 or 7, wherein the coating (3) comprises polyester.
9. Sample tube according to claim 6, 7 or 8 wherein said coating (3) has a thickness
which is less than the thickness of said steel wall (2).
10. Sample tube according to any of claims 6-9, wherein the thickness of said polymer
coating (3) is less than about 50 µm, particularly less than about 20 µm.
11. Sample tube according to any of the preceding claims, wherein the internal volume
of the tube (1) is less than about 1 ml.
12. Sample tube according to any of the preceding claims, wherein the internal volume
of the sample tube is in the range of about 0.1-0.5 ml, for instance about 0.2 ml.
13. Method for manufacturing a sample tube, particularly a sample tube according to any
of the preceding claims, wherein a blank is cut from steel sheet and the blank is
drawn to a tube.
14. Use of at least one sample tube (1) according to any of claims 1-12, wherein the at
least one sample tube (1) is provided with at least one sample (S), wherein the temperature
of the at least one tube (1) is being controlled for controlling the temperature of
the at least one sample (S).
15. Method for performing a polymerase chain reaction, using at least one sample tube
according to any of claims 1-12.