TECHNICAL FIELD
[0001] The present invention relates to a heat treatment method and device for heating,
cooling or drying a steel strip by blowing a jet of gas onto the steel strip.
BACKGROUND ART
[0002] Conventionally, there is provided a heac treatment device for heating or cooling
a steel strip by blowing a jet of gas onto the steel strip. However, since gas is
used as a thermal medium for conducting heat transfer in a conventional heac treatment
device, the heat transfer coefficient α is low. Therefore, a sufficiently high performance
can not be necessarily provided by the conventional heat treatment device, so that
a demand for a high heating or cooling rate, which must be accomplished from the viewpoint
of metallurgy, can not be satisfied. For example, the present inventors have proposed
a cooling device for cooling a steel strip by blowing a jet of gas onto the steel
strip, which is disclosed in Japanese Examined Patent Publication No. 2-16375. In
the above cooling device for cooling a steel strip, it is assumed that the heat transfer
coefficient is in a region of α ≤ 400 kcal/m
2Hr°C. In the case where the heat transfer coefficient is in the above region, it is
possible to attain a cooling rate of 100°C/sec when the thickness of the steel strip
is 0.6 mm. However, when thickness of the steel strip is 1.0 mm, only a cooling rate
of 63°C/sec can be actually attained. For the above reasons, when it is necessary
to accomplish a higher heat transfer coefficient, a roll cooling method is used, in
which a water-cooled roll is made to come into solid contact wich a steel strip, or
alternatively a gas-water cooling method is used, in which gas and water are mixed
with each other and a steel strip is cooled by the mixture. However, the above roll
cooling method is disadvantageous in that the roll comes into solid contact with the
steel strip. Therefore, it is difficult to make the water-cooled roll come into contact
with the steel strip uniformly. Therefore, the steel strip can not be cooled uniformly,
which causes a deterioration in a profile of the steel strip. On the other hand, the
gas-water cooling method is disadvantageous in that a surface of the steel strip is
oxidized by dissolved oxygen contained in water because water is used for cooling
in this method. Therefore, when the above gas-water cooling method is used, it becomes
necessary to conduct acid cleaning again on the strip after the completion of heat
treatment.
SUMMARY OF THE INVENTION
[0003] In order to enhance the heat transfer coefficient in the heat treatment device for
heating or cooling a steel strip by blowing a jec of gas onto the steel strip, it
is preferable to increase the flow velocity of gas blown onto the steel strip. According
to the experiment made by the present inventors, it has been found that the heat transfer
coefficient can be enhanced substantially in proportion to an increase in the flow
velocity of gas blown onto the strip. However, in accordance with the increase in
the flow velocity of gas, a pressure loss in the piping is sharply increased, and
it becomes necessary to provide a very large capacity of blower in order to obtain
a predetermined heat transfer coefficient.
[0004] An object of the present invention is to reduce the amount of power required for
a heat treatment device for conducting heat treatment on a steel strip by blowing
a jet of gas onto the steel strip while the heating rate or cooling rate is maintained
high.
[0005] In order to accomplish the above object, the heat treatment device for conducting
heat treatment on a steel strip by blowing a jet of gas onto the steel strip of the
present invention is characterized as described in the following items (1) to (3).
(1) A method for conducting heat treatment on a steel strip by blowing a jet of gas
onto the steel strip from a nozzle which vertically protrudes from a plane surface
of a header up to a height h from the said surface, wherein the outlet opening of
the nozzle is in a distance z from the steel strip of up to 70 mm, in order to heat,
cool or dry the steel strip by blowing the jet of gas is characterized in that an
inequality of W/4 ≤ h is satisfied, wherein W is a quantity of gas (density of quantity
of gas) blown onto a unit area in m3/min·m2 and h is in mm.
(2) A heat treatment device for performing the method of the invention is characterized
in that a roll insertion space, in which presser rolls are alternately arranged at
regular intervals along the proceeding direction of the steel strip, is provided in
a gas blowing space in which the nozzles for blowing jets of gas are arranged, so
as to prevent the steel strip from fluttering; and nozzles for blowing jets of gas
are arranged in the roll insertion space on che opposite side to the roll insertion
side with respect to the steel strip so as to extend the gas blowing space.
(2) The hear treatment device can be further
characterized in that: a roll insertion space, in which support rolls are alternately
arranged at regular intervals along the proceeding direction of the steel strip, is
provided in a gas blowing space in which the nozzles for blowing jets of gas are arranged,
so as to prevent the steel strip from fluttering; the support rolls are cooled in
the case of cooling the steel strip; and the support rolls are heated in the case
of heating or drying the steel strip.
(3) The heat treatment device can be further
characterized in that a heat exchanger for cooling gas is arranged at least on the
downstream side of a gas compressor such as a blower.
BRIEF DESCRIPTION OF THE DRAWINGS
[0006]
Fig. 1 is a graph showing a relation between the density of quantity of gas and the
heat transfer coefficient and also showing a range of the experiment made in the present
invention.
Figs. 2(a), 2(b), 2(c) and 2(d) are views respectively showing a nozzle of the heat
treatment device for conducting heat treatment on a steel strip by blowing a jet of
gas of the present invention.
Figs. 3(a) and 3(b) are views respectively showing a state of a jet of gas at a forward
end of a nozzle.
Fig. 4 is a graph showing a heat transfer characteristic of a nozzle.
Fig. 5 is a graph showing a relation between a ratio of a projection area of a baffle
body to an area of a cross-section of a nozzle, and a heat transfer coefficient at
a position immediately under the nozzle.
Fig. 6 is a graph showing a relation between a ratio of baffle plate length/nozzle
diameter and a heat transfer coefficient immediately under a nozzle.
Fig. 7 is a view showing a positional relationship between a nozzle and a steel strip.
Figs. 8 (a) and 8(b) are views respectively showing a conventional nozzle.
Fig. 9 is a view showing an example of the heat treatment device of the present invention
in which an opening for releasing gas to the back side is provided.
Figs. 10(a), 10 (b) and 10(c) are views respectively showing an example of the nozzle
arrangement of the heat treatment device of the present invention.
Fig. 11 is a view showing a relation between opening portion area S1 and nozzle opening
area S2 of a heat treatment device for conducting heat treatment on a steel strip
by blowing a jet of gas.
Fig. 12 is a graph showing a relationship between a ratio of an area of the opening
portion to an area of the nozzle opening, and a ratio of the heat transfer coefficient
of a heat treatment device for conducting heat treatment on a steel strip by blowing
a jet of gas.
Figs. 13(a) and 13(b) are views respectively showing a flow of gas in a heat treatment
device for conducting heat treatment on a steel strip by blowing a jet of gas.
Fig. 14 is a view showing a portion in which a rising gas flow is generated between
the cooling nozzles in a heat treatment device for conducting heat treatment on a
steel strip by blowing a jet of gas.
Figs. 15(a) and 15(b) are views respectively showing a structure of the nozzle periphery
of a heat treatment device for conducting heat treatment on a steel strip by blowing
a jet of gas of the present invention.
Fig. 16 is a graph showing an influence given to the heat transfer coefficient by
the ratio of nozzle protruding length h to nozzle inner diameter D in a heat treatment
device for conduccing heat treatment on a steel strip by blowing a jet of gas.
Fig. 17 is a view showing a relation between the gas blowing header having no opening
portion and the nozzle in a heat treatment device for conducting heat treatment on
a steel strip by blowing a jet of gas.
Fig. 18 is a graph showing a relation between the density of quantity of gas and the
ratio of the heat transfer coefficient when a nozzle protruding length h is changed
in a heat treatment device for conduccing heat treatment on a steel strip by blowing
a jet of gas.
Fig. 19 is a view showing an arrangement of the support roll and the gas blowing device
in a conventional heat treatment device for conducting heat treatment on a steel strip
by blowing a jet of gas.
Fig. 20 is a view showing an arrangement of the support roll and the gas blowing device
in a heat treatment device for conducting heat treatment on a steel strip by blowing
a jet of gas of the present invention.
Fig. 21 is a cross-sectional view of the advancing and retracting mechanism and the
heating and cooling mechanism of a support roll in a heat treatment device for conducting
heat treatment on a steel strip by blowing a jet of gas.
Fig. 22(a) is a view showing an arrangement of the conventional heat exchanger in
a heat treatment device for conducting heat treatment on a steel strip by blowing
a jet of gas.
Fig. 22(b) is a view showing an arrangement of the heat exchanger in a heat treatment
device for conducting heat treatment on a steel strip by blowing a jet of gas of the
present invention.
Fig. 23 is a graph showing a relation between the ratio of blower power and the gas
blowing temperature when a steel strip is cooled in a heat treatment device for conducting
heat treatment on a steel strip by blowing a jet of gas.
THE MOST PREFERRED EMBODIMENT
[0007] The present invention will be explained in detail as follows. In this connection,
the present inventors have investigated various fields in order to solve the problems.
In the present invention, problems have been solved from the viewpoints of nozzle
formation, gas discharge, ratio of effective gas blowing length, and blowing gas temperature,
and these will be successively explained below.
[0008] First, concerning the nozzle formation, in order to optimize the nozzle diameter
and nozzle pitch, various experiments were made and the results of the experiments
were compared with each other. As a result of the experiments, it was confirmed that
the nozzle diameter and nozzle pitch defined by Japanese Examined Patent Publication
No. 2-16375 proposed by the present inventors were most effective even if the flow
velocity of gas was increased. Fig. 1 shows a range of the experiment made in the
present invention and a range of the experiment made in Japanese Examined Patent Publication
No. 2-16375. It can be seen in Fig. 1 that a relation between the density of a quantity
of gas and the heat transfer coefficient is on an extension line on the graph even
in a region wherein the heat transfer coefficient is not lower than 400 kcal/m
2Hr°C, and that problems with respect to the exhaust of the gas are avoided.
[0009] A stagnation point, which is caused when a jec of gas collides with an object, deteriorates
the heat transfer coefficient. Therefore, it is well known that facilitating a turbulence
at this stagnation point is effective as a means for enhancing the heat transfer coefficient
of gas emitted from the nozzle. For example, as shown in Figs. 8(a) and 8(b), Japanese
Unexamined Utility Model Publication No. 61-40155 discloses a structure in which a
baffle plate 3 or a spiral line 6 is arranged in the nozzle 1 so as to facilitate
a turbulent flow.
[0010] However, in order to arrange the cross baffle plate 3 as described in Japanese Unexamined
Utility Model Publication No. 61-40155, the nozzle length must be long so that two
or three baffle plates can be arranged in the nozzle. Therefore, it is difficult to
industrially manufacture a large number of nozzles having such a structure. When the
spiral line 6 is incorporated into the nozzle as described above, gas is agitated
and emitted by a centrifugal force. Therefore, this structure is not effective.
[0011] As described before, the intensity of turbulence is low at the center of gas flow.
Accordingly, in order to enhance the heat transfer coefficient effectively, it is
necessary to increase an intensity of turbulence at the center of gas flow. According
to the present invention, as a means for facilitating a turbulence at the center of
gas flow, which can be easily put into practical use from the industrial viewpoint,
the present inventors proposed a structure in which a baffle body 2 or a baffle plate
3 is arranged at the center of the forward end of the nozzle 1 as shown in Fig. 2.
Due to the above structure of the nozzle 1, as shown in Figs. 3(a) and 3(b), there
is formed a turbulent flow 5, in which a vortex row is developed, at the rear of the
baffle body 2 or the baffle plate 3. Therefore, it becomes possible to make a turbulent
flow in the central region of the gas flow 4. In this connection, the cross-section
of the baffle body 2 is not limited to a circle, but the cross-section of the baffle
body 2 may be formed into a polygon or other shape.
[0012] Secondly, the present inventors made investigation into a method of discharging exhaust
gas emitted from the nozzle. As described before, in order to enhance the heat transfer
coefficient, a flow velocity of gas blown onto a steel strip may be increased. In
other words, a quantity of gas blown onto the steel strip may be increased. However,
when gas discharge is not sufficiently conducted, gas once blown onto the steel strip
remains on a surface of the steel strip and interferes with new gas blown onto the
steel strip. As a result, the heat transfer coefficient cannot be greatly enhanced.
On the graph of Fig. 1, a solid line expresses an example in which gas discharge is
conducted in a good condition, and a dotted line expresses an example in which gas
discharge is not conducted in a good condition. When gas discharge is not conducted
in a good condition, an increase in the heat transfer coefficient is deteriorated
in a region in which the density of air quantity is higher than a predetermined value.
For the above reasons, in order to enhance the heat transfer coefficient effectively,
it is very important to smoothly discharge gas which has been blown onto a steel strip.
In order to solve the above problems, the present inventors found the following two
solutions.
[0013] As a result of the investigation of gas flow after the collision of gas with a steel
strip, it was found that a jet of gas, which had been emitted from the nozzle, collided
with a steel strip and flowed along a surface of the steel strip and then collided
with a jet of gas, which had been emitted from the adjacent nozzle, and then flowed
in a direction so that gas could be separated from the steel strip. This rising current
of gas which rose between the nozzles was generated in the hatched portion in Fig.
14. A flow rate of this rising current of gas was 20 to 40% of the flow rate of the
jet of gas emitted from the nozzle 1.
[0014] Therefore, according to the present invention, there is provided an opening portion
or a clearance, from which gas is discharged, the area of which is sufficiently large
to form a rising current of exhaust gas after a jet of gas emitted from a nozzle collides
with a jet of gas emitted from an adjacent nozzle. In this connection, Fig. 12 shows
a relation between opening portion area S
1 and nozzle opening area S
2.
[0015] As shown in Fig. 13(a), after a jet of gas emitted from the nozzle 1 has collided
with the steel strip 7, it flows on the steel strip 7 and then collides with a jet
of gas emitted from the adjacent nozzle and rises upward. As shown in Fig. 13(a),
this rising current flows to an end portion of the steel strip in the width direction
when no forced ventilation is conducted. Therefore, this rising current is not sufficiently
exhausted. Accordingly, it turns back at a surface of the gas blowing header 8 and
is mixed with a jet of gas emitted from the nozzle 1. As a result, temperature of
the jet of gas emitted from the nozzle 1 is increased when the steel strip must be
cooled, and decreased when the steel strip must be heated. Therefore, it is impossible
to obtain a predetermined capacity of heating or cooling. Since gas remains between
the steel strip 7 and the blowing header 8, a flow velocity of a sheet-shaped gas
flow on the steel strip 7 is lowered. Accordingly, the cooling capacity is deteriorated
in the periphery of the colliding portion of the jet of gas emitted from the nozzle
1.
[0016] In the device according to the present invention, there is provided an opening portion
10 between the gas blowing headers 8 as shown in Fig. 13(b). The rising current flows
into this opening portion 10. Consequently, the jet of gas emitted from the nozzle
1 reaches a surface of the steel strip while it is seldom affected by the rising current
of gas which has turned back. Therefore, the steel strip can be effectively cooled
or heated. Since no gas remains between the steel strip 7 and the gas blowing header
8, gas can flow smoothly along the steel strip 7. Therefore, deterioration of the
cooling or heating capacity of gas can be mitigated.
[0017] An example of the structure of the nozzle periphery of the heat treatment device
of the present invention is shown in Fig. 15. As shown in Fig. 15(a), the nozzle 1
is a protruding nozzle, the forward end of which protrudes more than the forward end
portion of the gas blowing header 8. Therefore, when gas is discharged from the opening
portion 10, a portion of the jet of gas emitted from the nozzle 1 is prevented from
being directly exhausted without colliding with the steel strip. In the example shown
in Fig. 15(b), although the forward end of the nozzle 1 is located at the same level
as that of the forward end surface of the gas blowing header 8, a profile of the forward
end portion of the gas blowing header 8 is tapering, that is, a cross-sectional area
of the gas passage is gradually reduced in the gas blowing direction. Therefore, an
entrance portion of exhaust gas between the gas blowing headers 8 is capering. Accordingly,
it is possible that a portion in the exhaust gas passage, the area of which is smallest,
is assumed to be the opening portion in the case shown in Fig. 15(a). Consequently,
it is possible to provide the same effect as that of the structure shown in Fig. 15
(a) .
[0018] Next, the second gas exhausting method by which gas can be exhausted smoothly will
be explained below. According to the first gas exhausting method, gas is released
to the rear of the nozzles through the opening portion between the gas blowing headers.
However, the first gas exhausting method is disadvantageous in that the gas blowing
header is divided into a plurality of portions by the space of the opening portion.
For the above reasons, the equipment cost is raised although the first gas exhausting
method is ideal. Therefore, according to the second gas exhausting method, the opening
portion communicated with the rear side of the nozzle is eliminated, and the nozzle
is protruded by an appropriate protruding height. That is, when the nozzle protruding
height h shown in Fig. 17 is ensured, interference with blowing gas is eliminated,
and no gas remains because a space into which gas is released is formed not at the
rear of the nozzle but in the direction parallel to the steel strip. The above method
has already been proposed by the present inventors in Japanese Examined Patent Publication
No. 2-16375. According to the above Japanese Examined Patent Publication No. 2-16375,
the distance Z from the steel strip to the forward end of the nozzle is defined to
be a value noc more than 70 mm, and nozzle protruding length h is defined to be a
value not less than (100 - Z) mm. However, as described before, the above values are
determined on the assumption that an estimated region of the heat transfer coefficient
is α ≤ 400 kcal/m
2Hr°C. Experiments were made this time as to a region in which the heat transfer coefficient
was higher than the aforementioned value, and the following results were found. The
definition is not sufficient, in which the nozzle protruding length h is not less
than (100 - Z) mm in accordance with an increase in the quantity of gas. Unless a
term of the quantity (density) W of blown gas per unit of area in m
3/min·m
2 is added to the evaluation, it is impossible to make an appropriate evaluation reference.
That is, the present inventors found that it is important from the physical viewpoint
to define a gas discharge space in accordance with a quantity of gas to be blown.
[0019] Therefore, the present inventors made an experiment in which the nozzle protruding
height h was changed and a heated steel strip was cooled, so that the relationship
between the density of quantity of gas and the ratio of the heat transfer coefficient
was found. In this case, the ratio of the heat transfer coefficient was defined as
a ratio of the heat transfer coefficient when a heat transfer coefficient was determined
to be a reference value. This relation is shown in Fig. 18. According to Fig. 18,
when the nozzle protruding height h is 200 mm, the ratio of the heat transfer coefficient
is increased substantially in proportional to an increase in the density of a quantity
of gas. When the nozzle protruding height h is small, an increase in the ratio of
the heat transfer coefficient is suppressed from a certain density of a quantity of
gas, and emitted gas remains and interferes with newly emitted gas. This tendency
occurs in a region in which the density of quantity of gas is low when the nozzle
protruding height h is small. From the above relationship, the following expression
can be obtained,
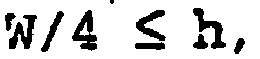
where W is the density of a quantity of gas in m
3/min·m
2, and h is the necessary nozzle protruding height in mm.
[0020] In this connection, concerning the density W of quantity of gas, of course, calculation
is conducted with the maximum density of quantity of gas so that the function can
be effectively exhibited in all regions of the performance of the device. Concerning
the nozzle protruding height h, it is possible to find the smallest height according
to the above basis. However, when the height h is unnecessarily extended, a pressure
loss in the nozzle is increased and the manufacturing cost of the device is increased.
Therefore, it is preferable to select the smallest height which is necessary.
[0021] Thirdly, the present inventors made investigation into a ratio of the effective gas
blowing length. Usually, in the case of cooling, the cooling rate is defined as Δt/T°C/sec,
wherein a cooling temperature difference is Δt°C and a period of time required for
cooling is T sec. In the case of heating, the heating rate is defined in the same
manner as that of the cooling rate. From the metallurgical viewpoint, the cooling
and the heating rate are important. In order to enhance the cooling and the heating
rate, the present inventors devised the equipment. In the heat treatment device for
conducting heat treatment by blowing a jet of gas, in order to enhance the heating
rate or the cooling rate, an interval between the nozzle and the steel strip was reduced,
so that a decrease in the flow velocity of gas emitted from the nozzle could be prevented
as much as possible. In order to suppress the warp and flutter of a steel strip, the
support rolls 16, 17 were made to come into contact with the steel strip 7 at a certain
interval as shown in Fig. 19, so that the warp and flutter of the steel strip could
be corrected and an interval between the nozzle 1 and the steel strip 7 could be reduced.
[0022] However, for the reasons of conducting operation, these support rolls 16, 17 are
provided with roll supporting devices 18, 19 so that these support rolls 16, 17 can
be advanced and retracted in operation. Due to the foregoing, it is necessary to provide
support roll insertion spaces in the device, and it is impossible to blow gas into
these spaces, that is, the support roll insertion spaces become a useless region from
the viewpoint of heat treatment. Due to the existence of these spaces, the heating
and the cooling rate are partially lowered, which is disadvantageous from the metallurgical
viewpoint. It is important to increase an average heating rate or an average cooling
rate in metallurgy. In order to increase these values, it is effective to enhance
the efficiency of the gas blowing space, and it is also effective to reduce the support
roll insertion space as much as possible.
[0023] In Fig. 19, an effective gas blowing length ratio is defined as a ratio of the length
in which gas is actually blown out, to the length L1 from the start to the end of
blowing gas. In the conventional case of a continuous annealing apparatus for annealing
a steel strip continuously, the effective cooling length ratio was approximately 80%.
In order co improve the above circumstances, the present inventors made investigation
into a method in which heating or cooling is conducted even in the support roll insertion
space. The support roll insertion space shown in Fig. 19 is divided into two sides.
One is a side onto which the roll is inserted, and the other is a side which is opposed
to the steel strip wherein no roll is arranged on this side. When an extension 22
of the gas blowing device is arranged on the side on which no roll is arranged as
shown in Fig. 20, it is possible to change this side into a gas blowing space. On
the side on which the roll is arranged, there is arranged a roll supporting device
for advancing and retracting the support roll 16, 17. Therefore, it is difficult to
arrange the gas blowing device on this side. Even if the gas blowing device is arranged
on this side, it is difficult to make the gas blowing device approach a steel strip.
Therefore, the efficiency is lowered. Accordingly, the present inventors devised a
device in which the support roll itself is heated or cooled so as to conduct roll
heating or roll cooling. Due to the foregoing, the support roll insertion region,
which was conventionally a useless region with respect to heating or cooling, can
be made very small, and even in the roll insertion region, heating or cooling can
be conducted. Due to the foregoing, it becomes possible to enhance the average heating
or cooling rate.
[0024] Fourthly, the present inventors made investigation into the optimization of blowing
gas temperature in the case of cooling a steel strip. In general, there is a tendency
that the power required for a blower is decreased when the blowing gas temperature
is decreased. However, when the blowing gas temperature is decreased to a value lower
than a predetermined value, in order to decrease the blowing gas temperature, a difference
in temperature, between the refrigerant used in the heat exchanger and the blowing
gas is reduced. Therefore, although a pressure loss in the heat exchanger is increased,
the temperature of blowing gas is not decreased so much. As a result, power required
for the blower is on the contrary, increased. The present inventors made investigation
into the blowing gas temperature in detail. As a result, they found the following.
The most appropriate blowing gas temperature, that is, a point at which power required
for the blower becomes smallest was approximately in a range from 60°C to 200°C. The
present inventors also found that this point fluctuated in accordance with the heat
transfer coefficient, the steel strip temperature on the entry side of the heat treatment
device, the steel strip temperature on the delivery side of the heat treatment device,
and the temperature of refrigerant used in the heat exchanger. The present inventors
also made detailed investigation into a region in which the heat transfer coefficient
is high. As a result of the investigation, the following were found. In the region
in which the heat transfer coefficient was high, the most appropriate point was shifted
to a low blowing gas temperature side compared with the conventional region in which
the heat transfer coefficient was low, and the blowing gas temperature greatly affected
the power required for the blower as shown in Fig. 23.
[0025] Therefore, the present inventors made investigation into a method by which the blowing
gas temperature can be effectively decreased. In a heat treatment device in which
a steel strip is cooled when a non-oxidizing gas is circulated and blown onto the
steel strip, a heat exchanger in which water is used as refrigerant is commonly used
as a cooling method for cooling gas. From the viewpoint of protecting the blower from
heat, the heat exchanger is conventionally arranged on the entry side of the blower.
In this case, in order to decrease the blowing gas temperature, the capacity of the
heat exchanger may be increased. However, when a difference in temperature between
refrigerant and gas is decreased, the heat exchanging efficiency is deteriorated and
a pressure loss is increased when gas flows in the heat exchanger.
However, irrespective of the increase in the pressure loss, the blowing gas temperature
is not decreased. As a result, as shown in Fig. 23, when the blowing gas temperature
is decreased too much, the power required for the blower is, on the contrary, increased.
Therefore, the present inventors aimed at an increase in temperature of blowing gas
in the case of increasing the pressure of blowing gas by the blower. In accordance
with that, the present inventors devised an arrangement in which the heat exchanger
is arranged on the delivery side of the blower. That is, instead of installing more
heat exchangers on the entry side of the blower, more heat exchangers are installed
on the delivery side of the blower. Due to the foregoing, a difference in temperature
between gas and refrigerant can be increased, so that the heat exchanging efficiency
can be enhanced. Due to the above arrangement, even in the case of the same heat transfer
coefficient (α), the same blowing gas temperature can be obtained by a blower power
which is lower than that of the conventional arrangement. Especially when an increase
in pressure of the blower is enlarged so that the gas blowing velocity onto a steel
strip can be increased, the effect can be made remarkable because the gas temperature
is greatly increased at the blower.
EXAMPLES
[0026] Examples are successively explained as follows. First, a baffle plate attached to
the nozzle will be explained below. Heat transfer characteristics of single nozzles
shown in Figs. 2(a) and 2(b) were investigated, wherein a baffle body 2 was attached
to a single nozzle shown in Fig. 2(a) and a baffle plate 3 was attached to a single
nozzle shown in Fig. 2(b). In this case, air was used as a cooling refrigerant. A
nozzle diameter was set at 10.5 mm, a velocity of air emitted from the nozzle was
set at 150 m/s, and a distance from the forward end of the nozzle to the object to
be cooled was set at 50 mm.
[0027] The characteristic of the nozzle, to the forward end of which the above baffle body
was attached, was investigated when a plate at high temperature was cooled with this
nozzle. The result of the investigation is shown in Fig. 4. The heat transfer coefficient
was enhanced at a position immediately below the nozzle center as shown in Fig. 4.
[0028] Concerning the baffle body, a ratio of the projection area of the baffle body to
the cross-section of the nozzle under the above cooling condition is shown in Fig.
5. As can be seen in Fig. 5, the effect of enhancing the heat transfer coefficient
can be provided when the ratio of the projection area of the baffle body to the cross-section
of the nozzle is not lower than 3%. When the ratio of the projection area of the baffle
body to the cross-section of the nozzle is not lower than 12%, a pressure loss at
the forward end of the nozzle caused by installing the baffle body is increased. Therefore,
the amount of power required for the blower is increased. Therefore, an arrangement
in which the ratio of the projection area of the baffle body to the cross-section
of the nozzle is not lower than 12% is not economical. For the above reasons, the
ratio of the projection area of the baffle body to the cross-seccion of the nozzle
was determined to be 3 to 12%.
[0029] In the same manner, with respect to the baffle plate, the thickness of which was
smaller than 3% of the cross-section of the nozzle, the length of the plate in the
axial direction of the nozzle was investigated. As a result of the investigation,
it was confirmed that the heat transfer coefficient was enhanced when length of the
plate was not less than 50% with respect to the nozzle diameter. Concerning the thickness
of the baffle plate, when the thickness was not less than 3%, a pressure loss of blowing
gas was increased because of the length of the baffle plate in the axial direction
of the nozzle compared with the baffle body described before. Therefore, in order
to reduce the amount of power required for the blower, it is advantageous that the
thickness of the baffle plate is smaller than 3%.
[0030] Secondarily, an example of the gas exhausting method by which gas is smoothly emitted
from the nozzle will be described as follows. Fig. 9 is a cross-sectional view of
the heat treatment device of the present invention. There are provided nozzles 1 which
are protruded being opposed to the steel strip 7 running in the direction of an arrow.
Jets of gas are blown out from the nozzles 1 onto the steel strip 7 so that the steel
strip 7 can be heat-treated. In this case, this heat treatment device is used as a
heating device when the blowing gas is heated, and this heat treatment device is used
as a cooling device when the blowing gas is cooled. In order to prevent the oxidation
of the steel strip, in many cases, the heat treatment chamber 12 is filled with non-oxidizing
atmosphere, in which hydrogen is mixed with nitrogen. However, even when a gas such
as air is used, the same effect can be provided. The arrows shown in Fig. 9 represent
currents of gas.
[0031] Gas is continuously supplied from the blower 9. Then, gas is sent to the divided
gas blowing headers 3 via a gas distribution header (not shown). A jet of gas, which
has been emitted from each nozzle 1 and has collided with the steel strip 7, takes
heat away from the steel strip 7. Then, the jet of gas is turned back and exhausted
from the opening portion 10. That is, gas is exhausted to the rear side of the nozzle
1 with respect to the steel strip 7. After gas has been exhausted, it is sent to the
blower 9 again via the suction gas header 11. The pressure of gas is increased by
the blower 9, and then it is recycled.
[0032] Although not shown in Fig. 9, a device for heating or cooling gas is arranged before
or after the blower 9. In the arrangement shown in Fig. 9, only gas which has passed
through the opening portion 10 via the suction gas header 11 is circulated again,
however, it is possible to suck gas from a portion of the heat treatment chamber without
providing the suction gas header 11. In this case, a jet of gas emitted from each
nozzle 1 collides with the steel strip 7, and then it passes through the opening portion
only under the force of a rising current formed by a jet of gas which has been turned
back. In Fig. 9, the cross-section of the gas blowing header 8 is rectangular. However,
for the reasons of manufacturing the gas blowing header 8, the cross-section of the
gas blowing header 8 may be circular, elliptical or polygonal, or, alternatively,
the cross-section of the gas blowing header 8 may be a combined shape.
[0033] Fig. 10 is a view showing an arrangement of the nozzles 1 and the gas blowing headers
3, wherein this view is taken on the side of the steel strip. As shown in Fig. 10(a),
the nozzles 1 may be arranged in a zigzag manner. Further, as shown in Fig. 10(b),
sets of nozzles 1 may be arranged, in a zigzag manner, wherein each sec of nozzles
1 is composed of 3 to 7 rows of nozzles 1. When one gas blowing header is arranged
for each row of nozzles, the equipment cost is raised. Therefore, as shown in Fig.
10(c), when one gas blowing header is arranged for a plurality of rows of nozzles,
it is possible to reduce the number of opening portions. However, in the above case,
there is a possibility that the exhaust of gas cannot be performed completely. Accordingly,
it is necessary to adjust the nozzle protruding height h in accordance with an area
of the opening portion.
[0034] Using the heat treatment device of the present invention shown in Figs. 9 and 10,
a steel strip 7, the thickness of which was 1.0 mm, was cooled by blowing a jet of
gas wherein a mixed gas of nitrogen and hydrogen was used as a refrigerant. In this
case, the cooling nozzle protruding length h was set at 20 mm. In Fig. 12, there is
shown a heat transfer coefficient ratio when a ratio of the area of the opening portion
to the area of the nozzle opening was changed under the condition of a constant blower
power. On Table 1, the nozzle diameter, the nozzle pitch and others are shown. On
the graph shown in Fig. 12, a cooling capacity for cooling the steel strip is evaluated
by the average heat transfer coefficient in the width direction of the steel strip.
The result of a comparative example is shown at the points where ratios of the area
of the opening portion to the area of the nozzle opening are 0, 3.4 and 17.3. In this
case, when the ratio of the area is 0, all the opening portions are closed. The result
of the example is shown in a range from the point where the ratio of the area of the
opening portion to the area of the nozzle opening is 5.8, to the point where the ratio
of the area of the opening portion to the area of the nozzle opening is 15.7. In a
range from the point where the ratio is 5, to the point where the ratio is 17, the
ratio of the heat transfer coefficient of the example is higher than that of the comparative
example. That is, when the ratio of the area of the opening portion to the area of
the nozzle opening is 5 to 17, the cooling capacity for cooling a steel strip by blowing
a jet of gas is enhanced.
Table 1
|
No. |
Distance Z (mm) from nozzle to steel strip |
Nozzle diameter (inner diameter) D (mm) |
Distance (mm) from nozzle to nozzle |
Ratio of area of opening portion to area of nozzle opening |
Comparative Example |
1 |
50 |
9.4 |
50 |
0 |
|
2 |
50 |
9.4 |
25 |
3.6 |
Inventive Example |
3 |
50 |
10.5 |
25 |
5.8 |
|
4 |
50 |
9.4 |
25 |
7.2 |
|
5 |
50 |
12.7 |
50 |
7.9 |
|
6 |
50 |
10.5 |
50 |
11.6 |
|
7 |
50 |
9.4 |
50 |
14.4 |
|
8 |
50 |
7.8 |
25 |
15.7 |
Comparative Example |
9 |
50 |
10.5 |
50 |
17.3 |
[0035] It is preferable that the protruding length h of the nozzle 1 is not more than 5
times of the inner diameter D of the nozzle 1. The reason is that the heat transfer
coefficient is remarkably lowered, as shown in Fig. 16, when the protruding length
h of the nozzle 1 exceeds 5 times of the inner diameter D of the nozzle. The reason
why the heat transfer coefficient is remarkably lowered is thought to be that, when
the nozzle protruding length h is large, the flow velocity of gas is decreased until
a rising current of gas reaches the opening portion 10 between the gas blowing headers
8 when the nozzle protruding length h is large, so that it becomes difficult for gas
to be exhausted.
[0036] Next, an example is shown in which gas is exhausted while the opening portion of
the gas blowing header is eliminated and the nozzle protruding height h is set at
an appropriate value. This example is shown in Fig. 17. In this arrangement, no openings
are provided between the nozzles 1, and the gas blowing header 8 is formed into a
box-shaped gas blowing header in which a certain number of nozzles are arranged. In
this connection, concerning the distance Z between the forward end of the nozzle and
the steel strip 7, as disclosed in Japanese Examined Patent Publication No. 2-16375,
it is common that distance Z is set at a value not more than 70 mm.
[0037] Next, referring to Fig. 17, a current 14 of gas will be explained below. After a
jet of gas has been emitted from the nozzle 1, it collides with the steel strip 7.
Then the jet of gas flows along the steel strip 7. In a short time, the jet of gas
collides with a jet of gas emitted from an adjacent nozzle. Therefore, the jet of
gas flows in a direction opposite to the direction of the jet of gas emitted from
the nozzle, that is, the jet of gas flows from the steel strip 1 toward the gas blowing
header 8. After that, this jet of gas collides with the gas blowing header and flows
along the gas blowing header. In a short time, this jet of gas passes through a region
interposed between the gas blowing header 8 and the steel strip 7 and is exhausted
outside. At this time, when the density of the gas is low, a current of gas flowing
along the gas blowing header flows in a region of the nozzle protruding height h.
However, when the density of the gas is increased, this region is not sufficiently
large, so that the current of gas, which has already collided with the steel strip,
flows into a region between the steel strip 7 and the forward end of the nozzle 1.
In the above state, the current of gas, which has once collided with the steel strip,
is involved in a jet of gas emitted from the nozzle. For example, when the steel strip
is cooled, a jet of gas emitted from the nozzle is cooled, however, when a current
of gas of high temperature, which has already collided with the steel strip, is involved
in the jet of gas emitted from the nozzle, the temperature of the jet of gas colliding
with the steel strip is raised, so that the cooling efficiency is lowered. In this
connection, concerning the gas blowing header, when the height h of the nozzle is
determined to be not lower than a predetermined value, gas can be smoothly discharged,
however, the gas blowing header may be appropriately divided so that spaces can be
formed between the divided gas blowing headers and gas can be discharged through the
spaces. Especially when the width of the steel strip is large or the length of the
gas blowing header is large in the longitudinal direction, that is, when the size
of the gas blowing header is large, it is effective to divide the gas blowing header.
[0038] Thirdly, an example will be shown in which a ratio of the effective gas blowing length
is enhanced. Fig. 19 is a view showing a conventional heat treatment device for conducting
heat treatment by blowing a jet of gas. The steel strip 7 and the nozzle 1 are made
to be close to each other in this arrangement so that the efficiency of a jet of gas
can be enhanced. In order to prevent the nozzle from coming into contact with the
steel strip when the steel strip flutters or warps, the steel strip is alternately
pressed by the left support roll 16 and the right support roll 17. However, no gas
is blown into the left support roll insertion space 23 and the right support roll
insertion space 24. Accordingly, although cooling or heating is conducted in the range
of L1, useless portions, in which cooling or heating is not conducted, are included
in the range of L1. As a result, it is impossible to obtain a high cooling or heating
rate. That is, the conventional heat treatment device is in a state in which the ratio
of the effective gas blowing length is small.
[0039] Referring to Fig. 20, an example of the present invention will be explained below.
In the arrangement shown in Fig. 20, there was provided an extension 22 of the gas
blowing device on the opposite side to the support roll with respect to the steel
strip 7. Due to the above arrangement, length L2 from the starting position to the
ending position of gas blowing was shortened. The actual gas blowing length shown
in Fig. 19 is the same as the actual gas blowing length shown in Fig. 20, however,
when length L1 is compared with length L2, length L2 is shorter than length L1, that
is, the ratio of the effective gas blowing length was enhanced. In this case, a period
of time required for heating or cooling was shortened by (Ll - L2)/V seconds, wherein
a moving speed of the steel strip 7 is V m/sec. Concerning the heating or the cooling
rate, it is possible to increase the heating or the cooling rate in accordance with
that. In this connection, when the present invention was applied to an actual continuously
annealing device for annealing a steel strip continuously, the ratio of the effective
gas blowing length was increased from 82% to 90%.
[0040] As described before, when the support roll is heated or cooled, the heating or the
cooling capacity can be enhanced, so that the heating or the cooling rate can be further
increased. However, as described before, the heat treatment device, in which the support
rolls are directly contacted with a steel strip so as to conduct heating or cooling,
since it is generally difficult to make the rollers come into contact with the steel
strip uniformly, the heat treatment device is disadvantageous in that the temperature
of the steel strip becomes nonuniform. However, according to an experiment made by
the present inventors, the diameters of the support rolls are usually not more than
300 mmφ, that is, diameters of the support rolls are usually small. Therefore, a surface
pressure of the support roll is higher than that of a commonly used heating or cooling
roll, the diameter of which is 1000 mmφ,
wherein the surface pressure is defined as a pressure by which the steel strip is
pressed against the roll. Therefore, it was found that no problems were caused with
respect to nonuniform temperature in the case of heating or cooling.
[0041] Fig. 21 is a cross-sectional view showing the right support roll portion. In this
connection, the structure of the left support roll portion is substantially the same
as that of the right support roll portion. Therefore, only the right support roll
is explained here. In this example, the support roll is a water-cooled roll. As shown
in Fig. 21, the right support roll 17 is arranged between both side walls of the heat
treatment chamber wall 13 and rotatably supported by bearings 26 which can be slid
on the side walls in the longitudinal direction. In this case, the gas blowing headers
and the nozzles are arranged in a clearance on the left of the steel strip 7, however,
they are omitted in the drawing for simplification. One end of the right support roll
17, the inside of which is formed into a jacket structure, is connected with a motor
27 for rotating the support roll. On the other hand, a bearing 29 arranged on the
opposite side has a rotary joint structure, and a water feed pipe 28 and a drain pipe
29 are connected with the rotary joint. In this case, the bearing 26 is arranged in
such a manner that it can slide. Therefore, the bearing 26 can be advanced and retracted
by a motor for moving the support roll via a power transmission shaft 31 and a distributor
32.
[0042] Due to the above structure, cooling water can be supplied to the right support roll
17 via the water supply pipe 28, and waste water is discharged outside through the
drain pipe 29. In this explanation, the support roll is used as a cooling roll, however,
when heated fluid is used, it is possible to use the support roll as a heating roll.
Even in the case of cooling, it is possible to use fluid other than water. Further,
in the case of heating, instead of using fluid, electric power may be supplied to
the roll, so that the roll can be used as an electrically heated roll. It is possible
to control a heating or cooling capacity by controlling a temperature or quantity
of fluid to be supplied or by controlling an electric current to be supplied to the
roll.
[0043] Fourthly, an example will be shown in which the gas blowing temperature is effectively
decreased. Fig. 22(a) is a view showing a conventional example of the heat treatment
device in which a non-oxidizing gas is circulated and a jet of non-oxidizing gas is
blown onto a steel strip so that the steel strip can be cooled. In Fig. 22(a), reference
numeral 7 is a steel strip which is an object to be cooled. The steel strip 7 is cooled
in non-oxidizing gas (not shown) inside the heat treatment chamber wall 13. Reference
numeral 9 is a blower for sucking and blowing the non-oxidizing gas in the heat treatment
chamber. This blower 9 sucks gas from the heat treatment chamber via a duct 34. In
the middle of this duct 34, there is provided a heat exchanger 35 for cooling gas,
and the thus cooled gas is boosted by the blower 9. The thus boosted gas is introduced
again into the heat treatment chamber via the duct 34 and blown onto the steel strip
7 via the gas blowing header 8 and the nozzle 1. Therefore, the steel strip 7 can
be quickly cooled. Concerning the position of the heat exchanger 35, according to
the conventional arrangement, in order to protect the blower 9 from heat, after gas
in the heat treatment chamber has been cooled by the heat exchanger, it is sucked
by the blower. That is, the heat exchanger is arranged on the upstream side of the
blower. In the conventional heat treatment device, an estimated region of the heat
transfer coefficient for cooling a steel strip is low.
Therefore, the flow velocity at the nozzle end is not high. Accordingly, a high boosting
pressure is not required for the blower, and the increase in the gas temperature is
small in the blower. For the above reasons, no problems are caused in practical use.
However, when the heat transfer coefficient is raised in the cooling of a steel strip,
it becomes necessary to increase the flow velocity at the nozzle end, and a high boosting
pressure is required for the blower. For the above reasons, an increase in temperature
caused in the process of boosting can not be neglected. As a result, the cooling efficiency
can be enhanced when the heat exchanger 35 is also arranged after the blower 9 as
shown in Fig. 22(b), that is, the cooling efficiency can be enhanced when the heat
exchanger 35 is also arranged on the downstream side of the blower 9. That is, when
an amount of decrease in the temperature of atmosphere gas is set to be constant,
a capacity of the heat exchanger in the arrangement shown in Fig. 22(b) can be made
smaller than that of the heat exchanger in the arrangement shown in Fig. 22 (a) .
As a result, a pressure loss in the heat exchanger is reduced, and a capacity of the
blower can be made smaller. In this connection, in the arrangement shown in Fig. 22(b),
the heat exchangers are arranged before and after the blower. However, if no problems
are caused in the blower from the viewpoint of heat resistance, the heat exchanger
arranged on the upstream side may be removed, and the heat exchanger may be arranged
only on the downstream side.
INDUSTRIAL AVAILABILITY
[0044] According to the present invention, in the heat treatment device for heating, cooling
or drying a steel strip by blowing a jet of gas onto the steel strip, it is possible
to enhance the heat transfer coefficient by facilitating a turbulence at the center
of the jet of gas, and it is also possible to smoothly exhaust gas which has been
blown onto the steel strip and it is possible to prevent the interference of this
exhausted gas with gas newly blown onto the steel strip. Due to the foregoing, the
heat transfer coefficient can be enhanced.
[0045] According to the present invention, in the heat treatment device for heating, cooling
or drying a steel strip by blowing a jet of gas onto the steel strip, the length of
useless running sections in the insertion spaces of the right and the left rolls can
be shortened, that is, length of sections not contributing to heating, cooling or
drying a steel strip can be shortened. Therefore, the total length of the heat treatment
device can be reduced. Due to the foregoing, it is possible to reduce a period of
time for heating, cooling or drying a steel strip, so that the heating rate, cooling
rate or drying rate for heating, cooling or drying a steel strip can be enhanced.
Further, the heat exchanger for cooling gas is arranged on the delivery side of a
gas compressor such as a blower. Due to the foregoing, it becomes possible to effectively
lower the temperature of blowing gas. As a result, the cooling efficiency can be enhanced,
and power required for a gas compressor such as a blower can be reduced.
[0046] Consequently, it is possible to ensure a heating or cooling rate required from the
viewpoint of metallurgy without providing an excessively large capacity of blower
or duct. Also, it become possible to shorten the length of the apparatus. Therefore,
the apparatus can be made compact and an intensity of power of the blower can be made
greatly smaller than that of the blower of the conventional arrangement. Accordingly,
from the viewpoint of reducing the running cost, it is possible to provide a great
merit. Further, according to the cooling system of the present invention, cooling
is conducted without causing problems of nonuniform temperature of a steel strip,
and also without causing deterioration of a profile of the steel strip and oxidation
of a surface of the steel strip caused in the process of cooling with gas and water,
which are caused in the roll cooling of the conventional cooling system in which the
heat transfer coefficient is α ≥ 400 kcal/m
2Hr°C. Therefore, it is possible to enhance the quality of the steel strip, and it
is unnecessary to provide an acid cleaning device for removing an oxide film. Therefore,
the apparatus can be simplified.
DESCRIPTION OF REFERENCE NUMERALS
[0047]
- 1
- Nozzle
- 2
- Baffle body
- 3
- Baffle plate
- 4
- Jet of gas
- 5
- Turbulent flow
- 6
- Spiral line
- 7
- Steel strip
- 8
- Gas blowing header
- 9
- Blower
- 10
- Opening portion
- 11
- Suction gas header
- 12
- Heat treatment chamber
- 13
- Heat treatment chamber wall
- 14
- Gas current
- 15
- Upper conveyance roll
- 16
- Left support roll
- 17
- Right support roll
- 18
- Left roll supporting device
- 19
- Right roll supporting device
- 20
- Lower conveyance roll
- 21
- Gas blowing device
- 22
- Extension of gas blowing device
- 23
- Left supporting roll insertion space
- 24
- Right supporting roll insertion space
- 25
- Gas blowing space
- 26
- Bearing
- 27
- Support roll driving motor
- 28
- Water supply pipe
- 29
- Drain pipe
- 30
- Bellows
- 31
- Transmission shaft
- 32
- Distributor
- 33
- Supporting roll retracting motor
- 34
- Duct
- 35
- Heat exchanger