(19) |
 |
|
(11) |
EP 1 525 947 B1 |
(12) |
FASCICULE DE BREVET EUROPEEN |
(45) |
Mention de la délivrance du brevet: |
|
12.04.2006 Bulletin 2006/15 |
(22) |
Date de dépôt: 23.10.2003 |
|
|
(54) |
Procédé de polissage de finition
Verfahren zum abschliessenden Polieren
Method for finish-polishing
|
(84) |
Etats contractants désignés: |
|
AT BE BG CH CY CZ DE DK EE ES FI GB GR HU IE IT LI LU MC NL PT RO SE SI SK TR |
(43) |
Date de publication de la demande: |
|
27.04.2005 Bulletin 2005/17 |
(73) |
Titulaire: SOCIETE EUROPEENNE DE SYSTEMES OPTIQUES S.E.S.O. |
|
13792 Aix-en-Provence Cedex 3 (FR) |
|
(72) |
Inventeur: |
|
- Fermé, Jean-Jacques
13800 Velaux (FR)
|
(74) |
Mandataire: Jacquard, Philippe Jean-Luc et al |
|
Cabinet ORES,
36,rue de St Pétersbourg 75008 Paris 75008 Paris (FR) |
(56) |
Documents cités: :
DE-A- 3 801 969 US-A1- 2002 102 925
|
FR-A- 2 843 711
|
|
|
|
|
|
|
|
|
Il est rappelé que: Dans un délai de neuf mois à compter de la date de publication
de la mention de la délivrance de brevet européen, toute personne peut faire opposition
au brevet européen délivré, auprès de l'Office européen des brevets. L'opposition
doit être formée par écrit et motivée. Elle n'est réputée formée qu'après paiement
de la taxe d'opposition. (Art. 99(1) Convention sur le brevet européen). |
[0001] La présente invention a pour objet un procédé de polissage de finition d'une surface
à l'aide d'un élément de polissage et d'un abrasif.
[0002] Il est déjà connu de réaliser un polissage de finition d'une surface à l'aide d'un
élément de polissage, par exemple un feutre, et d'un abrasif, par exemple de la silice
colloïdale. La technique généralement utilisée consiste à coller le feutre sur un
outil métallique en intercalant éventuellement un matériau souple par exemple de type
mousse. Cette technique présente l'inconvénient de déformer la surface à polir, ce
qui fait que les résultats obtenus ne sont pas optimaux.
[0003] Le document US-A-2002102925 divulgue un procédé de polissage de finition d'une surface
à l'aide d'un élément de polissage et d'un support déformable. Dans une première étape,
le support est mis en contact avec la surface à polir pour en épouser le contour,
ensuite l'élément de polissage est interposé entre la surface du support durci et
la surface à polir et mis en mouvement par rapport à ces deux surfaces de manière
à effectuer un polissage de finition.
[0004] La présente invention a pour objet un procédé qui permette de remédier au moins en
partie au problème précité.
[0005] L'invention concerne ainsi un procédé de polissage de finition d'une surface à l'aide
d'un élément de polissage et d'un abrasif, caractérisé en ce qu'il met en oeuvre :
a) avant ledit polissage, le collage de l'élément de polissage sur un support en un
matériau déformable de manière permanente et ;
b) l'application d'une pression sur le support déformable une fois que l'élément de
polissage est en contact avec la surface à polir de sorte que l'élément de polissage
soit mis en forme pour épouser un contour de ladite surface,
c) réaliser le polissage de finition à l'aide de l'élément de polissage ainsi mis
en forme.
[0006] Ledit matériau est avantageusement déformable par fluage et/ou durcissable. Il peut
s'agir par exemple de poix qui est chauffée à une température qui permet son fluage
et qui, après b et avant c, est ensuite refroidie pour obtenir un durcissement, ou
bien encore d'une colle qui se présente sous forme d'un gel et qui, après b, et avant
c est durcie par exemple par polymérisation ou application d'un rayonnement notamment
ultra-violet. Le matériau peut être également du plâtre..
[0007] L'élément de polissage peut être un feutre ou tout matériau de polissage convenant
à un polissage de finition conduisant à de faibles rugosités (de l'ordre de 1Å à quelques
Å par exemple). Le matériau de polissage est avantageusement porté par un support
de polissage.
[0008] Le polissage de finition peut être en particulier réalisé à l'aide d'une machine
assurant un déplacement relatif de translation entre l'élément de polissage et la
surface à polir selon deux directions perpendiculaires et éventuellement de rotation
autour d'un axe parallèle à une desdites directions perpendiculaires. Le polissage
de finition s'applique particulièrement bien au cas de surfaces ayant une génératrice,
la surface étant disposée de manière telle que la direction de la génératrice soit
parallèle à celle des deux directions précitées qui est parallèle à l'axe de rotation.
[0009] Le procédé s'applique notamment à des surfaces qui avant polissage de finition, ont
été préalablement soumises à un pré-polissage (ou polissage dit grossier) et à un
polissage proprement dit.
[0010] Après le polissage proprement dit qui peut être réalisé notamment par toute technique
connue, la surface présente une rugosité comprise par exemple entre 3Å et 15Å, alors
après polissage de finition, la rugosité peut être comprise entre 1Å et 5Å, et plus
particulièrement entre 1Å et 3Å pour des surfaces en verre, en silice, en silicium
et en céramique (voire entre 1Å et 2Å pour des surfaces en verre ou en silice) et
entre 3Å et 5Å pour une surface en nickel revêtant une surface métallique.
[0011] D'autres caractéristiques et avantages de l'invention apparaîtront mieux à la lecture
de la description ci-après, donnée à titre d'exemple non limitatif, en liaison avec
les dessins dans lesquels :
- les figures 1a et 1b illustrent en coupe la mise en oeuvre du procédé de polissage
de finition selon l'invention,
- la figure 2 représente une machine assurant le polissage de finition d'une surface
dans le cadre de la présente invention et les figures 3a et 3b d'une part et 4a et
4b d'autre part illustrent deux modes de mise en oeuvre de la machine.
[0012] L'invention se rapporte au polissage de finition de surfaces à basse rugosité (notamment
des miroirs) dont la forme est par exemple rectangulaire. Il repose sur l'utilisation
de machines de polissage ayant une cinématique à 2 axes linéaires perpendiculaires.
[0013] Les formes générées sur des surfaces peuvent être des plans, des sphères, des cylindres
suivant leur grande dimension (cylindre méridional) ou leur petite dimension (cylindre
sagittal), des miroirs à profil méridional elliptique ou parabolique, des miroirs
paraboliques ou elliptiques représentant un morceau d'un miroir de révolution.
[0014] Une des applications de ces surfaces est la réalisation de miroirs utilisés pour
mettre en forme et focaliser les faisceaux de lumière X émis par les sources de lumière
de type synchrotron ou laser à électrons libres.
[0015] Les différentes étapes sont par exemple :
- 1. Ebauche : cette étape est conventionnelle pour le travail des matériaux de type
verre ou céramique ou silicium et elle consiste à mettre en forme le support sur lequel
sera réalisée la surface à basse rugosité.
Pour cela on utilise des fraiseuses ou des centres d'usinage équipés d'outils spécifiques
au travail de ces matériaux. Ces outils sont constitués habituellement d'un laiton
sur lequel sont déposées de fines particules de diamant fixées sur l'outil par un
liant. Ces opérations se font sous arrosage d'eau ou d'autres liquides en fonction
des matériaux usinés. La mise en forme de la surface est aussi réalisée par cette
technique.
- 2. Doucissage : on utilise pour cela des outils ayant la forme de plans ou de cylindre
ou d'un profil complémentaire de la surface à polir.
Les dimensions de ces outils sont proches de celle de la surface à polir. Ces outils
peuvent être obtenus par un usinage traditionnel en mécanique. La matière utilisée
peut être de l'aluminium, du laiton, et dans certains cas des morceaux de verre recollés
sur un support mécanique.
On procède à l'aide d'une machine de polissage ayant une cinématique à 2 axes linéaires,
à la mise en forme relative de l'outil et de la surface à polir.
Pour cela, on applique la surface à doucir sur l'outil et on induit un mouvement relatif
entre la surface et l'outil parallèle à la grande longueur de la surface et un mouvement
perpendiculaire pour la largeur.
Soit l'outil soit la surface sont fixes et la pièce complémentaire est mobile et entraînée
par les deux mouvements de translation. Alternativement l'outil est entraîné selon
un mouvement de translation et la surface est entraînée selon le mouvement de translation
perpendiculaire. De plus soit l'outil, soit la surface est libre de rotuler autour
d'un axe parallèle à la grande longueur.
L'opération de rodage utilise des abrasifs classiques de doucissage et l'on fait décroître
la taille du grain jusqu'à obtenir une surface ayant l'aspect d'un douci fin.
Durant toute cette phase, l'outil est retouché jusqu'à ce que l'on obtienne sur la
surface à polir la forme géométrique finale à quelques microns près.
- 3. Pré-polissage à la poix ou au feutre de polissage grossier et un abrasif de polissage
classique tel que l'oxyde de cérium en utilisant la machine décrite précédemment.
Le mouvement suivant la longueur (direction X) a une amplitude comprise par exemple
entre 5 et 200 mm, et suivant la largeur (direction Y), il a une amplitude comprise
par exemple entre 1 et 100 mm.
- 4. Polissage proprement dit avec correction itérative de la forme jusqu'à obtenir
les spécifications d'écart par rapport à la forme théorique. Le matériau de polissage
est de la poix qui est coulée sur l'outil puis mise en forme avec la surface à polir
par chauffage.
Des dégarnis de la poix sont effectués localement là où des bosses on été mesurées.
L'abrasif utilisé est par exemple de l'oxyde de cérium. Les pressions de polissage
sont comprises entre 5 et 100 grammes par centimètre carré. Ce polissage est terminé
lorsque la surface à polir a la bonne forme et qu'il n'y a plus de points ou de défauts
correspondant aux étapes précédentes. La rugosité à ce stade est comprise entre 3
et 15Å pour des zones carré d'analyse de 1 à 1000 microns de largeur.
- 5. La finition super polie est faite en utilisant un abrasif de type silice colloïdale
associé à un feutre.
Cette opération, si elle est réalisée de manière classique, déforme généralement la
surface à polir.
Selon l'invention, on colle directement le feutre sur la poix et on met à profit son
fluage pour mettre en forme la surface du feutre de façon à ce qu'elle soit complémentaire
de la surface à polir. La mise en forme est effectuée en chauffant la poix, l'outil
ou le substrat de la surface à polir, le moule étant la surface à polir elle-même.
Ce chauffage est réalisé à une température de l'ordre de 60°C à laquelle la poix a
une viscosité suffisante pour se déformer en fluant sans couler. Les mouvements et
les pressions appliqués sont similaires à celles mises en oeuvre lors du polissage
proprement dit (étape 4 ci-dessus), c'est-à-dire entre 5 et 100 g/cm2.
L'état de l'art normalement connu pour cette phase est de coller le feutre sur un
outil métallique en intercalant éventuellement un matériau souple de type par exemple
mousse. L'avantage du procédé selon l'invention est de disposer d'un outil dur (poix
à la température de 20°C) ayant un contour qui épouse la forme de la surface à polir.
A ce stade, la rugosité obtenue est généralement comprise entre 1 et 2Å sur les matières
de type verre et silice. Elle est généralement comprise entre 1Å et 3Å sur le silicium
et les céramiques, et entre 3Å et 5Å sur les surfaces métalliques revêtues de nickel.
[0016] Selon la figure 1a, qui concerne le cas d'une pièce optique 1 à polir qui est un
cylindre ou un tore, l'élément de polissage 2 (d'épaisseur par exemple entre 0,1 mm
et 2 mm) est collé sur de la poix 3 qui est solidaire d'un support 4 par exemple cylindrique
qui sert d'outil de polissage. L'élément de polissage 2 peut être un matériau poreux
tel qu'un feutre, notamment une mousse de polyuréthane microcellulaire de la Société
RHODES (Bierkeek - Belgique) ou un matériau synthétique poreux (« Finishing Pad »)
de la Société -RODEL, ou des supports (ou « drops -») de polissage de la Société BUEHLER.
Après chauffage de la poix jusqu'à lui conférer une viscosité lui permettant de fluer
sans couler (par exemple en la chauffant à une température de l'ordre de 60°C), on
appuie l'outil 4 sur une surface à polir 6 de la pièce optique 1 avec une pression
suffisante pour que la déformation par fluage de la poix permette au feutre 2 en contact
avec la surface 6 d'épouser localement la forme de la surface 6. Le feutre 2 qui peut
être en un ou plusieurs morceaux a de préférence une surface 5 égale, à plus ou moins
20% à celle de la surface 6.
[0017] La pression P appliquée lors du polissage de finition est de l'ordre de 5 à 100 grammes/cm
2.
[0018] La figure 1b illustre le procédé dans le cas d'une surface plane ou d'un miroir ayant
une génératrice G dans le plan de coupe.
[0019] La figure 2 représente une machine utilisable pour la mise en oeuvre du procédé de
polissage de finition, ainsi que pour les étapes précédentes de doucissage, de pré-polissage
et de polissage proprement dit.
[0020] Elle présente deux barres de coulissement parallèles 11 et 12 le long de laquelle
peuvent se translater dans une première direction X deux coulisseaux 14 et 15 reliés
par une barre d'attelage 16. Chacun des coulisseaux porte un bras 17 et 18 s'étendant
par exemple dans une direction Y perpendiculaire à la direction X, avec un réglage
en hauteur 17', 18' selon Z (perpendiculaire à X et Y).
[0021] Chacun des bras présente un logement 19 et 20 permettant de recevoir un axe de rotation
21 et 22 d'un porte-pièce 23 portant la pièce 1
[0022] dont la surface 6 doit être soumise au polissage de finition. L'outil 4 est disposé
sur un support 25 solidaire d'une table 27 présentant des moyens de translation de
l'outil 4 et donc du feutre 2 dans la direction Y perpendiculaire à la direction X.
Ces moyens de translation sont par exemple des glissières 26.
[0023] Les vitesses de polissage dans chacune des directions X et Y peuvent être choisies
par exemple entre 0,05 m/s et 0,5 m/s.
[0024] Les figures 3a et 3b d'une part et 4a et 4b d'autre part illustrent deux modes de
mise en oeuvre du polissage de finition (après durcissement du support en matériau
déformable par exemple de la poix ou de la colle). Le déplacement selon X (par exemple
entre 5 et 200 mm) permet un polissage parallèle à la direction des génératrices de
la surface, alors que le mouvement de translation selon Y (par exemple entre 1 et
100 mm) et la rotation selon l'axe (21, 22) permet à la surface 6 à polir de suivre
en tournant l'élément de polissage 2 au fur et à mesure du déplacement selon Y. Ainsi,
la combinaison de ces trois mouvements (translation X, translation Y et rotation)
permet d'assurer le polissage de la surface sur son contour et sur toute sa longueur.
[0025] Selon les figures 3a et 3b, la pièce 1 de section cylindrique ou plane est portée
par le porte-pièce 23 et l'outil 4 est solidaire du support 25. Selon les figures
4a et 4b, la pièce 1 cylindrique ou plane est solidaire du support 25 et c'est l'outil
4 qui est porté par le porte-pièce 23.
[0026] Le procédé s'applique également à des surfaces ne présentant pas de génératrice.
La mise en forme de l'élément 2 améliore les performances par rapport à la surface
ayant la génératrice la plus proche.
1. Procédé de polissage de finition d'une surface (6) à l'aide d'un élément de polissage
(2) et d'un abrasif,
caractérisé en ce qu'il met en oeuvre :
a) avant ledit polissage, le collage de l'élément de polissage (2) sur un support (3,
4) en un matériau déformable de manière permanente et ;
b) l'application d'une pression sur le support (3, 4) déformable une fois que l'élément
de polissage (2) est en contact avec la surface (6) à polir de sorte que l'élément
de polissage (2) soit mis en forme pour épouser un contour de ladite surface (6).
c) réalisation du polissage de finition à l'aide de l'élément de polissage (2) ainsi
mis en forme.
2. Procédé selon la revendication 1, caractérisé en ce que ledit matériau (3) est déformable par fluage et/ou durcissable.
3. Procédé selon la revendication 2, caractérisé en ce que ledit matériau (3) est de la poix qui est chauffée à une température permettant son
fluage et qui après mise en forme de l'élément de polissage (2) est ensuite refroidie
pour obtenir un durcissement.
4. Procédé selon la revendication 2, caractérisé en ce que ledit matériau (3) est une colle de type gel qui après mise en forme de l'élément
de polissage (2) est durcie par exemple par polymérisation ou application d'un rayonnement,
notamment ultra-violet.
5. Procédé selon la revendication 2 caractérisé en ce que le matériau (3) est du plâtre.
6. Procédé selon une des revendications précédentes, caractérisé en ce que l'élément de polissage (2) est un feutre.
7. Procédé selon une des revendications précédentes, caractérisé en ce que ledit matériau déformable (3) est porté par un support de polissage (4).
8. Procédé selon une des revendications précédentes, caractérisé en ce que le polissage de finition est réalisé à l'aide d'une machine comportant un dispositif
de déplacement assurant un mouvement relatif entre l'élément de polissage (2) et la
surface (6) à polir selon deux directions (X, Y) perpendiculaires.
9. Procédé selon la revendication 8, caractérisé en ce que le dispositif de déplacement est agencé pour produire également un mouvement de rotation
relatif autour d'un axe (21, 22) parallèle à l'une desdites deux directions perpendiculaires.
10. Procédé selon une des revendications 8 ou 9, caractérisé en ce que la surface (6) présente une génératrice dont la direction est parallèle à l'une desdites
deux directions perpendiculaires.
11. Procédé
caractérisé en ce que la surface (6) sur laquelle le polissage de finition est réalisé a été préalablement
soumise à :
- un pré-polissage ou polissage grossier
- un polissage.
12. Procédé selon la revendication 11 caractérisé en ce qu'après polissage, la surface (6) présente une rugosité entre 3Å et 15Å et après polissage
de finition, une rugosité entre 1Å et 5Å.
13. Procédé selon la revendication 12, caractérisé en ce que ladite rugosité après polissage de finition est comprise entre 1Å et 3Å pour les
surfaces (6) en verre, en silice, en silicium et en céramique, et entre 3Å et 5Å pour
une surface (6) en nickel revêtant une surface métallique.
1. Verfahren zum Feinpolieren einer Oberfläche (6) mit Hilfe eines Polierelementes (2)
und eines Abrasivs,
dadurch gekennzeichnet, daß es anwendet:
a) vor dem Polieren das Aufkleben des Polierelementes (2) auf einen Träger (3, 4)
aus einem permanent verformbaren Material, und;
b) Anwenden eines Druckes auf den verformbaren Träger (3, 4), sobald sich das Polierelement
(2) in Anlage an der zu polierenden Oberfläche (6) befindet, wodurch das Polierelement
(2) so geformt wird, daß es sich an eine Kontur der Oberfläche (6) anpaßt,
c) Durchführen des Feinpolierens mit Hilfe des auf diese Weise geformten Polierelementes
(2).
2. Verfahren nach Anspruch 1, dadurch gekennzeichnet, daß das Material (3) durch Fließen verformbar und/oder aushärtbar ist.
3. Verfahren nach Anspruch 2, dadurch gekennzeichnet, daß das Material (3) Pech ist, das auf eine Temperatur erwärmt wird, die sein Fließen
ermöglicht, und das nach dem Formen des Polierelementes (2) anschließend abgekühlt
wird, um eine Aushärtung zu erzielen.
4. Verfahren nach Anspruch 2, dadurch gekennzeichnet, daß das Material (3) ein Klebstoff vom Gel-Typ ist, das nach dem Formen des Polierelementes
(2) beispielsweise durch Polymerisieren oder durch Anwenden einer Strahlung, insbesondere
Ultraviolett-Strahlung, ausgehärtet wird.
5. Verfahren nach Anspruch 2 dadurch gekennzeichnet, daß das Material (3) Gips ist.
6. Verfahren nach einem der vorhergehenden Ansprüche, dadurch gekennzeichnet, daß das Polierelement (2) ein Filz ist.
7. Verfahren nach einem der vorhergehenden Ansprüche, dadurch gekennzeichnet, daß das verformbare Material (3) von einem Polierträger (4) getragen ist.
8. Verfahren nach einem der vorhergehenden Ansprüche, dadurch gekennzeichnet, daß das Feinpolieren mit Hilfe einer Maschine durchgeführt wird, die eine Bewegungsvorrichtung
aufweist, welche eine Relativbewegung zwischen dem Polierelement (2) und der zu polierenden
Oberfläche (6) in zwei zueinander senkrechten Richtungen (X, Y) ausführt.
9. Verfahren nach Anspruch 8, dadurch gekennzeichnet, daß die Bewegungsvorrichtung dazu ausgelegt ist, des weiteren eine Relativdrehbewegung
um eine Achse (21, 22) zu erzeugen, die zu einer der beiden zueinander senkrechten
Richtungen parallel ist.
10. Verfahren nach einem der Ansprüche 8 oder 9, dadurch gekennzeichnet, daß die Oberfläche (6) eine Generatrix aufweist, deren Richtung zu einer der beiden zueinander
senkrechten Richtungen parallel ist.
11. Verfahren,
dadurch gekennzeichnet, daß die Oberfläche (6), an der das Feinpolieren vorgenommen wird, vorausgehend
- einem Vorpolieren oder Grobpolieren
- einem Polieren
unterzogen wurde
12. Verfahren nach Anspruch 11, dadurch gekennzeichnet, daß die Oberfläche (6) nach dem Polieren eine Rauhigkeit von zwischen 3 Å und 15 Å aufweist,
und nach dem Feinpolieren eine Rauhigkeit von zwischen 1 Å und 5 Å aufweist
13. Verfahren nach Anspruch 12, dadurch gekennzeichnet, daß die Rauhigkeit nach dem Feinpolieren bei Oberflächen (6) aus Glas, aus Silica, aus
Silizium und aus Keramik zwischen 1 Å und 3 Å liegt, und bei einer Oberfläche (6)
aus Nickel, die eine metallische Oberfläche bedeckt, zwischen 3 Å und 5 Å liegt.
1. A method of finishing polishing a surface (6) using a polishing element (2) and an
abrasive, the method being
characterized in that it implements the following steps:
a) prior to said polishing, sticking the polishing element (2) in permanent manner
on a support (3, 4) of deformable material;
b) applying pressure on the deformable support (3, 4) once the polishing element (2)
is in contact with the surface (6) to be polished so that the polishing element (2)
is shaped to match an outline of said surface (6); and
c) performing finishing polishing using the polishing element (2) shaped in this way.
2. A method according to claim 1, characterized in that said material (3) is deformable in creep and/or is hardenable.
3. A method according to claim 2, characterized in that said material (3) is pitch which is heated to a temperature enabling it to creep
and which, once the polishing element (2) has been shaped, is sufficiently cooled
in order to harden it.
4. A method according to claim 2, characterized in that said material (3) is an adhesive of the gel type which, once the polishing element
(2) has been shaped, is hardened, e.g. by being polymerized or by applying radiation,
in particular ultraviolet radiation.
5. A method according to claim 2, characterized in that the material (3) is plaster.
6. A method according to any preceding claim, characterized in that the polishing element (2) is a felt.
7. A method according to any preceding claim, characterized in that said deformable material (3) is carried by a polishing support (4).
8. A method according to any preceding claim, characterized in that the finishing polishing operation is performed using a machine comprising a displacement
device for imparting relative movement between the polishing element (2) and the surface
(6) to be polished along two mutually perpendicular directions (X, Y).
9. A method according to claim 8, characterized in that the displacement device is arranged also to produce relative rotary movement about
an axis (21, 22) parallel to one of said two perpendicular directions.
10. A method according to claim 8 or claim 9, characterized in that the surface (6) presents a generator line of direction parallel to one of said two
perpendicular directions.
11. A method,
characterized in that the surface (6) on which the finishing polishing is performed has previously been
subjected to:
- pre-polishing or coarse polishing; and
- polishing.
12. A method according to claim 11, characterized in that after polishing, the surface (6) presents roughness lying in the range 3 Å to 15
Å, and after finishing polishing it presents roughness in the range 1 Å to 5 Å.
13. A method according to claim 12, characterized in that said roughness after finishing polishing lies in the range 1 Å to 3 Å for surfaces
(6) of glass, silica, silicon, or ceramic, and in the range 3 Å to 5 Å for a nickel
coating on a metal surface.

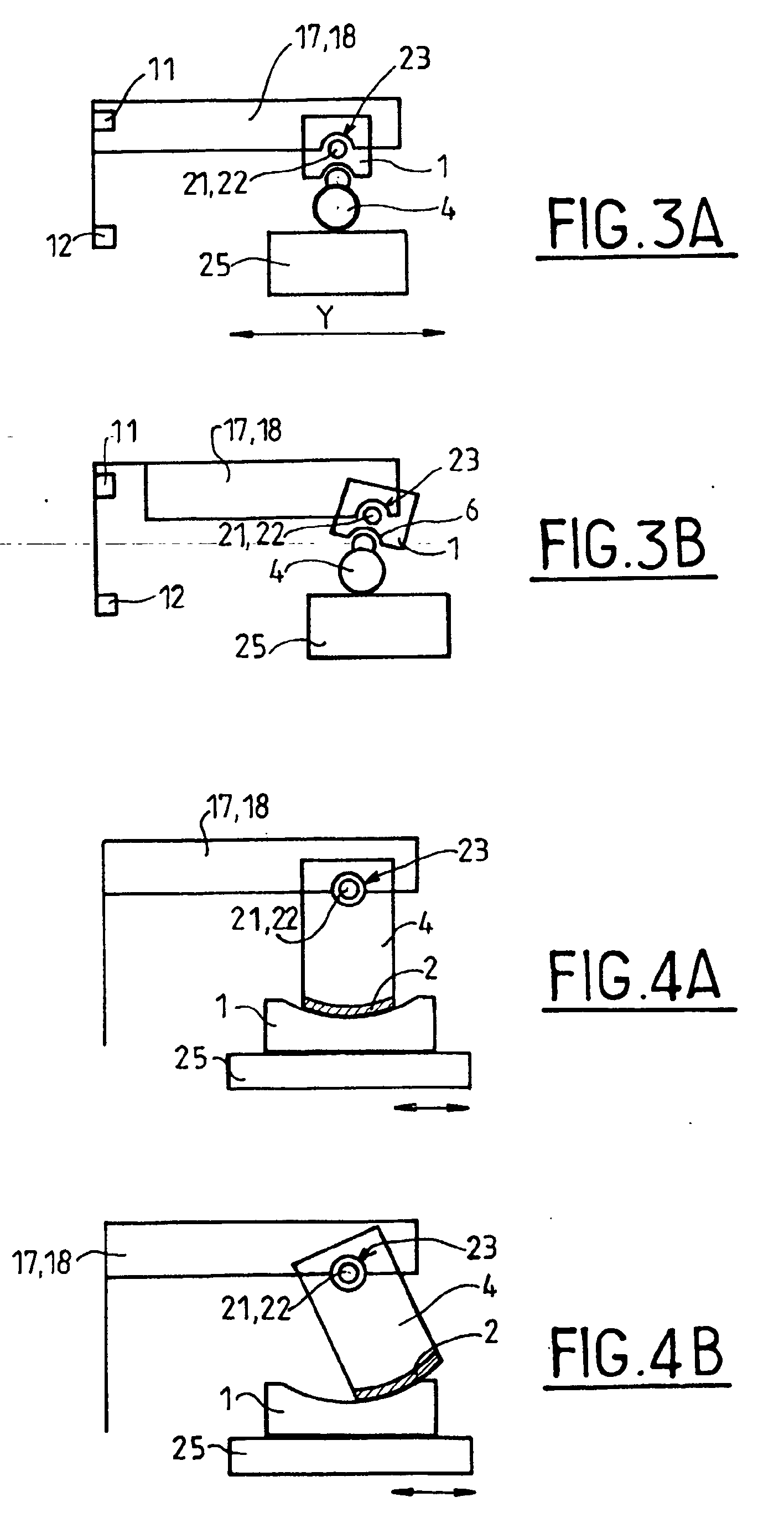