Field of the invention
[0001] The present invention relates to modified linen fibers, in particular modified linen
slivers and yarns, having an allomorph I content of at least 40% and a solubility
in cuproethylendiamine (Cued) 0.5 M lower than 1.4 g/l, as well as to a process for
their preparation.
Background of the invention
[0002] The main constituent of linen fibers is cellulose I. From a chemical point of view,
cellulose is a beta-1,4-linked polymer of D-glucopyranose and it occurs in several
distinct crystalline forms known as allomorphs, such as for instance cellulose I,
II, III and IV [see A. Sarko in New developments of industrial polysaccharides, page
87, Ed. V. Crescenzi, I.C.M.]. Cellulose allomorphs can be identified by a variety
of analytical techniques, such as spectroscopic (IR, Raman or solid state
13C-NMR spectroscopy) and diffractional (electron, neutron or x-ray diffraction) techniques.
[0003] Cellulose I and cellulose II are the commercially dominant allomorphs of cellulose.
[0004] Cellulose I ("native cellulose") is the naturally occurring form in nearly all plants
while cellulose II, also known as "hydrate" cellulose, is mainly produced by treatment
of cellulose I with strong basic agents such as concentrated aqueous potassium or
sodium hydroxides. Such a treatment, known as mercerization, is commonly used for
removing the non-cellulosic components, such as lignin and hemicelluloses, from raw
materials containing cellulose. It causes the irreversible transition of cellulose
I to the thermodynamically more stable cellulose II.
[0005] Fibers made of cellulose I are characterized, in the dry state, by a greater breaking
load resistance and, most of all, by a typical brightness and luster that are particularly
appreciated in the textile field.
[0006] On the contrary, mercerized cellulose fibers and fabrics are deprived of the beauty
and resistance of natural materials.
[0007] Nevertheless natural cellulose I fibers show a significant drawback, that is they
loose much of their strength when wet. In fact the hydrogen bonds between hydroxyls
of neighboring fibers, which are very strong in a dry state, are considerably weakened
by water. This inconvenient can limit the applicability of natural fibers, especially
in those fields in which a high breaking resistance, even in a wet state, is required.
[0008] Furthermore another aspect of the same problem is represented by the low wet and
dry crease resistance of linen.
[0009] In this case, linen fabrics do not spontaneously recover the initial arrangement
after washing and drying and, unavoidably, an additional ironing step is required
in order to return to the original shape.
[0010] With the aim to improve wet strength and crease recovery of raw cellulosic materials,
and optionally, to confer new additional advantageous properties, some cross-linking
processes are performed on natural fibers, in particular etherification reactions.
[0011] The known processes for preparing cellulose ethers are generally carried out in two
stages, with the preparation of the "alkali cellulose" taking place first followed
by its etherification. Alkali cellulose is, in turn, prepared by mixing cellulose,
as homogeneously as possible, with water and alkali metal hydroxides in suitable industrial
units. The etherification stage is usually carried out by reacting the alkali cellulose
produced in the first stage together with an etherifying agent (United States patent
n. 5,493,013 - Hoechst Aktiengesellschaft).
[0012] Etherification cross-linking processes, by linking together hydroxyl groups of different
cellulose chains with strong covalent bonds instead of weak hydrogen bonds, can improve
several properties of the final products, such as wet strength or crease resistance.
Nevertheless, the rather drastic aqueous alkaline conditions can irreversibly alter
the appearance and the crystalline structure of cellulosic materials and, therefore,
not always, they applies to textiles.
[0013] For instance, a cellulose cross-linking process that provides superabsorbent articles
is described in the International patent application WO96/15154 [The Procter & Gamble
Company]. However the reported reaction conditions, that confer good absorbing properties
to those cellulose materials, would not be usable in the textile field in that they
would spoil the look and the resistance of cellulose natural fibers.
[0014] A cellulose cross-linking process carried out in organic solvents which prevents
the original compact and rigid structure of native cellulose is described in the International
patent application WO89/09643 [Grandics]. However, the patent does not mention the
possible application of the process to substrates different from microcrystalline
cellulose.
[0015] There are a few examples of cross-linking reactions performed on fabrics and, very
often, they use formaldehyde as cross-linking agent. For instance, a cross-linking
treatment of cellulose fabrics with formaldehyde is claimed in the United States patent
n. 3,663,974 [Toyo Spinning Co Ltd.]. Nevertheless a significant drawback of those
derivatives is the scarce stability of the resultant bonds that slowly degrade and
release formaldehyde.
[0016] Some different cross-linking reagents for cellulose textiles have been investigated
but they generally require high temperatures or aqueous basic conditions that can
damage the native structure of cellulose [see, as an example, the cross-linking process
claimed in US 6,036,731 in the name of Ciba SC Holding AG].
[0017] US 3,567,362 discloses a process by which conditioned and wet crease recovery can
be imparted to cotton fabrics. Fabrics are treated with aqueous soda and then with
butadienediepoxide in carbon tetrachloride solution, obtaining crosslinking of the
fabric fibers. When using low amounts of soda solution, cotton maintains the allomorph
I configuration.
[0018] It would be highly desirable to provide modified linen fibers in which the allomorph
I content, the strength and the beautiful appearance of the natural fibers are maintained
and the crease resistance increased.
Description of the invention
[0019] We have now surprisingly found that it is possible to increase crease resistance
while maintaining the allomorph I content, the strength and the beautiful appearance
of the natural fibers by a cross-linking process on linen slivers and yarns.
[0020] In particular, the cross-linked linen slivers and yarns according to the invention
have an allomorph I content measured by solid state
13C NMR of at least 40%, preferably at least 45%, and a solubility in cuproethylendiamine
(Cued) 0.5 M lower than 1.4 g/l.
[0021] The low solubility in Cued indicates the presence of cross-linking between cellulose
chains which is stable to the strong basic conditions of Cued. Untreated linen slivers
and yarns have a solubility in Cued 0.5 M much higher than 1.4 g/l, since Cued is
able to destroy the chain to chain interactions present in linen fibers. If the cross-linking
is obtained by formation of an ester bond, the cross-linked cellulose is also dissolved
in Cued because of the hydrolysis of the ester bonds under these conditions. However,
basic conditions are also applied in standard laundry washings. This is why fibers
cross-linked by formation of ester bonds loose their crease-resistance properties
in time. On the contrary, the low solubility of the products according to the invention
proves that they do not hydrolyze in the presence of bases and, consequently, are
likely to have increased crease resistance even after repeated washes.
[0022] Another object of the present invention is a process for preparing modified linen
slivers and yarns, by reacting linen slivers and yarns with a cross-linking agent
in the presence of a base in a non-aqueous medium
[0023] In a preferred embodiment, the cross-linking reaction is performed by formation of
an ether bond between the hydroxyls of cellulose chains.
[0024] Preferably, the number of hydroxyls per glucose unit of cellulose that can be cross-linked
ranges from 0.0001 to 3, more preferably from 0.001 to 1; most preferably, from 0.005
to 0.15.
[0025] As far as the position of hydroxyls of cellulose involved in the cross-linking process
is concerned, any possible isomer is encompassed within the scope of the present invention.
[0026] In addition, as the present cross-linking reaction is an heterogeneous reaction,
the final distribution of cross-linking can be irregular. In particular the extent
of cross-linking could be higher on the surface of the fiber and negligible inside.
However it is within the scope of the present invention any composition comprising
modified linen slivers and yarns, having allomorph I content of at least 40% and a
solubility in cuproethylendiamine (Cued) 0.5 M lower than 1.4 g/l, optionally together
with not modified linen slivers and yarns.
[0027] Preferred cross-linking reagents suited for the present process include compounds
of formula
X-A-X' (I)
wherein
X and X' are reactive groups, i.e. moieties capable of reacting with hydroxyl groups
of cellulose, rather than undergoing self-polymerization.
[0028] Such reactive groups include, for example, detachable groups, activated unsaturated
groups, formyl, aziridino and epoxy groups.
[0029] Example of detachable groups, also known as leaving groups, are halogens, cyano,
triflate, mesylate, tosylate, trifluoroacetate, ammonium, sulphate, p-nitrobenzoate,
phosphato, acetoxy, propionyloxy and the like. Halogens are preferred leaving groups.
Chloro is particularly preferred.
[0030] Activated unsaturated groups are for example vinyl, halovinyl, styryl, acryloyl or
methacryloyl groups.
[0031] Further reactive groups according to the present invention are formyl, comprising
masked formyls, aziridino and epoxy groups, such as for instance ethylene or propylene
oxides, and the like. Preferred cross-linking reagents contain glycidyl residues.
[0032] A is a bivalent bridging radical comprising from 1 to 100 carbon atoms and, optionally,
from 1 to 50 heteroatoms selected among halogens, oxygen, nitrogen, sulfur, boron,
phosphorus and silicon.
[0033] With the term "a bivalent bridging radical A" an aliphatic, aromatic or heteroaromatic
radical linking X and X' is intended.
[0034] The bivalent radical A includes linear, branched or cyclic aliphatic radicals such
as methylene, ethylidene, propylidene, isopropylidene, butylidene, pentylidene, hexylidene,
heptylidene, octylidene, nonylidene, decylidene, dodecylidene, tetradecylidene, hexadecylidene,
heptadecylidene, octadecylidene, cyclohexylidene and the like. Preferred bivalent
aliphatic radicals A are C
1-C
18 aliphatic linear radicals.
[0035] Radical A may optionally include double or triple bonds and from 1 to 50 heteroatoms
selected from halogens, oxygen, nitrogen, sulphur, boron, phosphorus and silicon.
These heteroatoms can alternate with carbon atoms along the bridging chain or can
represent side functional groups linked to the bridging chain. Examples of heterogroups
linked to the bridging chain are halogens, amino or hydroxyl groups.
[0036] Examples of preferred heteroatom-containing radicals A are poly(oxyethylene), poly(oxypropylene),
poly(vinylchloride), poly(ethyleneimine), poly(propyleneimine), optionally substituted
by one or more hydroxyl groups.
[0037] Bivalent radicals A comprising aromatic systems, such as benzene, naphthalene, anthracene,
phenantrene, fluorene and the like, or heterocyclic rings such as furan, pyrrole,
thiophene, pyrazole, imidazole, triazole, thiazole, isothiazole, oxazole, isoxazole,
pyridine, pyrimidine, pyrazine, pyridazine, quinoline, isoquinoline, tetrahydrofuran,
dioxane, tetrahydropyran, piperidine, dihydropyran, dihydropyridine, optionally benzo-condensed,
and the like are also included in the present invention.
[0038] A preferred group of cross-linking reagents comprises compounds in which A is selected
among poly(oxyethylene), poly(oxypropylene), poly(ethyleneimine) or poly(propyleneimine).
[0039] When X and X' are identical, they are preferably selected from 1,2-epoxyethyl, vinyl
and chloro.
[0040] A preferred group of cross-linking reagents according to the present invention is
represented by diglycidyl reagents.
[0041] A particularly preferred reagent is poly(propylene glycol)diglycidyl ether.
[0042] Other preferred cross-linking reagents have X different from X', in particular X
is a halogen and X' is 1,2-epoxyethyl.
[0043] Among these reagents epichlorohydrin is particularly preferred.
[0044] By the use of cross-linking agents of formula (I), the obtained cross-linked linen
fibers have the following formula (II):
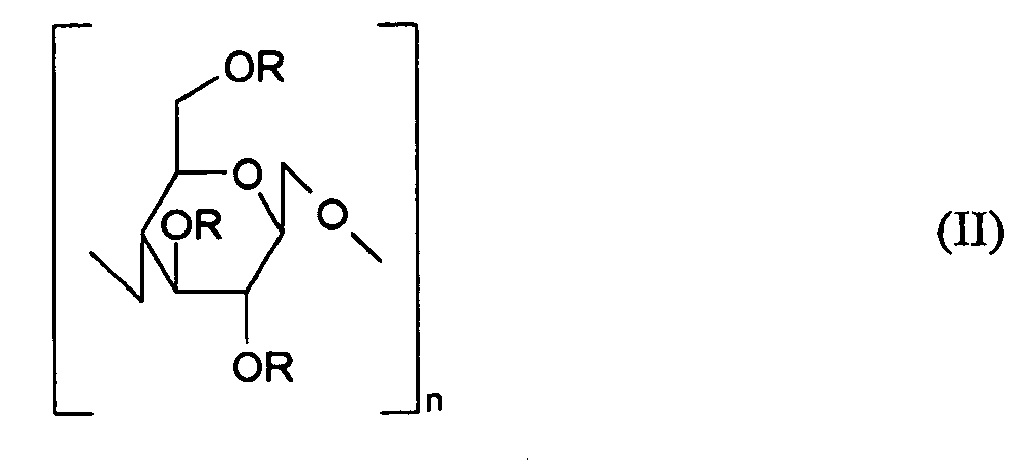
wherein
n is an integer from 100 to 100,000
R is a hydrogen, a group of formula AR" in which A is a bivalent bridging radical
comprising from 1 to 100 carbon atoms and, optionally, from 1 to 50 heteroatoms selected
from halogens, oxygen, nitrogen, sulphur, boron, phosphorus and silicon, and
R" is an O-cellulose I radical derived from formula II;
provided that AR" groups are present in a AR"/n ratio from 0.0001 to 3.
[0045] The present process is particularly mild and a relevant advantage is that it does
not significantly alter the appearance, the strength and the allomorph I content of
starting linen slivers and yarns.
[0046] In a preferred embodiment the process for preparing cross-linked linen sliver and
yarns comprises the steps of:
a) applying an cross-linking reagent to linen sliver and yarns and
b) treating with a base in a non-aqueous medium.
[0047] It is possible to apply the two steps in any order, i.e. first step a) and then step
b) or first step b) followed by step a). The linen slivers and yarns, starting materials
used in the present invention, contain an average content of water of about 14% and
according to the present process, linen slivers and yarns do not generally need any
previous dehydrating step, but can be used as such.
[0048] The application of the cross-linking reagent generally comprises the imbibition of
the linen slivers and yarns, with the commercial grade reagent, and the removal of
the exceeding reagent by centrifugation or squeeze.
[0049] The cross-linking reagent can be used as such or can be previously dissolved in a
suitable solvent.
[0050] The imbibition of step a) of the present process is generally performed at a mild
temperature and for the time needed to saturate the starting material.
[0051] Step b) of the process, according to the present invention, comprises the treatment
of linen slivers and yarns, previously processed according to step a), with a base
in a non-aqueous medium.
[0052] With the term "base" any basic reagent which is able to activate the hydroxyl groups
of cellulose towards cross-linking etherification is meant. Suitable bases are both
organic and inorganic bases. Examples of organic base are nitrogen-containing compounds
such as amines, pyridines and the like. Examples of inorganic bases are alkaline hydroxides
and ammonia. Other suitable basic reagents are, for instance, quaternary ammonium
hydroxides, alkaline alcoholates or carbanions. They are commercially available or
can be prepared by known methods.
[0053] Preferred bases for the process of the present invention are alkaline hydroxides
and alcoholates. Among them sodium and potassium hydroxide, sodium methoxide and ethoxide
are the most preferred.
[0054] As already stated, step b) of the process, according to the present invention, comprises
the treatment of linen slivers and yarns previously processed according to step a),
with a base in a non-aqueous medium.
[0055] With the term "non aqueous medium" a polar solvent with a low content of water is
intended. The absence of water is important for the present process, however commercially
available "pure grade" solvents can successfully be used without any further dehydrating
treatment.
[0056] Polar solvents suitable for the present process are able to dissolve or to suspend
the base without giving side reactions or irreversibly altering the cellulose crystalline
structure.
[0057] However, it is also possible to add a suitable dissolving agent in order to dissolve
the selected base, such as for instance a phase transfer catalyst and the like.
[0058] Solvents particularly suited for the present purpose are, for instance, alcohols,
such as methanol, ethanol, n-propanol, i-propanol, n-butanol, ter-butanol and the
like.
[0059] Methanol, ethanol and i-propanol are preferred. I-propanol is particularly preferred
from an industrial point of view.
[0060] The base is usually dissolved in the selected solvent and then the resultant solution
is used in step b). The concentration of non-aqueous basic solutions used in step
b) of the present invention can vary. Suitable values of concentration are those sufficient
to activate hydroxyl groups of cellulose towards cross-linking etherification. Examples
of usable ranges of concentration are 1-30% (w/v) for alkaline hydroxides and 0.01-5M
for alcoholates.
[0061] In a preferred embodiment, the linen slivers and yarns processed according to step
a), are dipped into the non-aqueous basic solution above described, at a temperature
and for a time needed to complete the reaction.
[0062] After completion of the cross-linking reaction, the linen slivers and yarns are repeatedly
washed, at first with the same solvent selected for step b) and then with water up
to neutral pH.
[0063] In another preferred embodiment, the process comprises a step b) of the process,
according to the present invention, followed by a step a) of the process, according
to the present invention.
[0064] According to the process of the present invention, it is possible to improve the
properties of linen slivers and yarns without loosing the qualities of native cellulose.
[0065] In particular the modified linen slivers and yarns of the present invention maintain
the allomorph I content, the strength and the beautiful appearance of the natural
fibers and increase the crease resistance.
[0066] A further advantage of the present process is that it can be performed as a continuous
process.
[0067] All these aspects make the present invention particularly attractive from an industrial
viewpoint.
[0068] In order to better illustrate the present invention, without limiting it, the following
examples are now given.
Evaluation methods
[0069] The allomorph I content of the samples was evaluated by solid state
13C-NMR spectroscopy (CP/MAS and MAS techniques).
[0070] The solubility in cuproethylendiamine 0.5M was measured in the following way:
70 mg of linen sample are dipped in 25 ml of distillate water for 1 hour, then 25
ml of cuproethylendiamine 1M are added with a burette and finally mixed for 4 hours.
At the end of this procedure the sample is visually observed. The presence of undissolved
linen fibers indicates solubility in Cued 0.5 M lower than 1.4 g/l. Complete dissolution
of the sample implies solubility in Cued 0.5 M equal to or higher than 1.4 g/l
[0071] Breaking-load test (g/tex) was performed according to ASTM D 1445/2524.
General procedure 1
[0072] A linen sliver was dipped in the selected cross-linking reagent for a proper time
(contact time) and at a suitable temperature. It was then centrifuged for about 10
minutes at 1000 r.p.m. The procedure can be repeated twice (double imbibition).
[0073] The sliver was then dipped into a non-aqueous basic solution, at the reported temperature,
and left for the indicated contact time. The final product was washed first with the
same solvent used for the basic solution and then with water up to neutral pH.
Example 1. Cross-linking reaction with epichlorohydrin
[0074] Experiments 3-4 (table 1) were carried out according to the general procedure 1.
Epichlorohydrin (Aldrich) was used as cross-linking reagent. Step a) was performed
at 50°C and for a contact time of 30 minutes while step b) at 50°C and for a contact
time of 60 minutes.
[0075] Comparative experiment 1 represents the unmodified linen sliver.
[0076] Comparative experiment 2 is a cross-linking reaction according to general procedure
1 but performed in an aqueous base.
Table 1
|
Step B |
|
|
|
Exp. n. |
Base |
Solvent |
Conc. |
Solubility in Cued 0.5M (g/l) |
Resistance g/tex |
Allomorph I content (%) |
1 (comp.) |
- |
- |
- |
≥ 1.4 |
29 |
58 |
2 (comp.) |
NaOH |
H2O |
24% |
<1.4 |
14 |
n. d. |
3 |
CH3ONa |
CH3OH |
0.2M |
< 1.4 |
28 |
57 |
4 |
CH3ONa |
CH3OH |
1.0M |
<1.4 |
29 |
56 |
Example 2. Alkylating reaction with poly(propylene glycol)diglycidyl ether
[0077] The experiments (table 2) were carried out according to general procedure 1. Poly(propylene
glycol)diglycidyl ether (Aldrich, average molecular weight by number -380) was used
as cross-linking reagent. Step a) was performed at 50°C and for a contact time of
30 minutes while step b) at 50°C and for a contact time of 60 minutes.
[0078] Comparative experiment 1 represents the unmodified linen sliver.
[0079] Comparative experiment 5 is a cross-linking reaction according to general procedure
1 but performed in an aqueous base.
Table 2
|
Step B |
|
|
|
Exp. n. |
Base |
Solvent |
Conc. |
Solubility in Cued 0.5M (g/l) |
Resistance g/tex |
Allomorph I content (%) |
1(comp.) |
- |
- |
- |
≥ 1.4 |
29 |
58 |
5 (comp.) |
NaOH |
H2O |
24% |
<1.4 |
12 |
n. d. |
6 |
CH3ONa |
CH3OH |
0.2M |
<1.4 |
26 |
57 |
7* |
CH3ONa |
CH3OH |
0.2M |
<1.4 |
25 |
62 |
8 |
CH3ONa |
CH3OH |
1M |
<1.4 |
29 |
57 |
* double imbibition n. d.= not detectable |
General procedure 2
[0080] A linen sliver or yarn is dipped into a non-aqueous basic solution, at the reported
temperature, and left for the indicated contact time.
[0081] The sliver or yarn is then dipped in the selected cross-linking reagent for a proper
time (contact time) and at a suitable temperature. The final product is washed first
with the same solvent used for the basic solution and then with water up to neutral
pH.
Example 3. Cross-linking reaction with epichlorohydrin / i-propanol 1/1 (v/v)
[0082] The following experiments were carried out on linen sliver (table 3) and on linen
yarn (table 4) according to general procedure 2. Epichlorohydrin (Aldrich) was used
as cross-linking reagent. It was previously dissolved in i-propanol achieving a ratio
epichlorohydrin / i-propanol 1/1 (v/v).
[0083] Step a) and step b) ware performed at 50°C and for a contact time of 15 minutes.
[0084] Young module was measured to test crease resistance of the yarn. The values of untreated
yarn are reported as comparative experiment 11 in table 4. The sharp reduction of
Young module of the cross-linked sample is an indication of an improvement in crease
resistance.
Table 3
|
Step B |
|
|
|
Exp. n. |
Base |
Solvent |
Conc. |
Solubility in Cued 0.5M (g/l) |
Resistance g/tex |
Allomorph I content (%) |
9 |
NaOH |
CH3OH |
24% |
<1.4 |
26 |
59 |
10 |
KOH |
i-C3H7OH |
8% |
< 1.4 |
26 |
50 |
Table 4
|
Step B |
|
|
|
Exp. n. |
Base |
Solvent |
Conc. |
Solubility in Cued 0.5M (g/l) in |
Young Module (N/tex) |
Allomorph I content (%) |
11 (comp.) |
- |
- |
- |
≥ 1.4 |
16.1 |
57 |
12 |
KOH |
i-C3H7OH |
8% |
< 1.4 |
5.4 |
49 |
1. Modifizierte Leinenfasern und Garne, die einen Allomorph I-Gehalt von mindestens 40%
haben, der mit Festkörper-13C-NMR gemessen wurde, und die durch eine Löslichkeit von weniger als 1,4 g/l in 0,5
m Kupferethylendiamin (Cued) charakterisiert sind.
2. Modifizierte Leinenfasern und Garne nach Anspruch 1, worin die Leinenfasern durch
die Bildung einer Etherbindung zwischen den Hydroxylgruppen der Celluloseketten vernetzt
sind.
3. Modifizierte Leinenfasern und Garne nach Anspruch 1, worin der Allomorph I-Gehalt
mindestens 45% beträgt.
4. Modifizierte Leinenfasern und Garne nach den Ansprüchen 1 - 3, die die folgende Formel
besitzen:
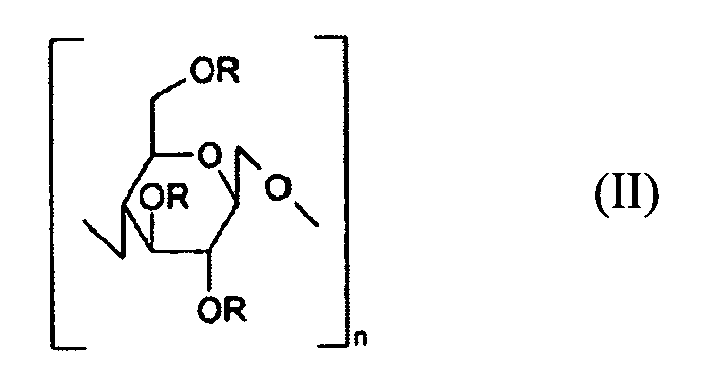
worin
n eine ganze Zahl von 100 bis 100.000 ist,
R ein Wasserstoff oder eine Gruppe der Formel AR" ist, in der A ein zweiwertiges Brückenradikal
ist, das 1 bis 100 Kohlenstoffatome und wahlweise 1 bis 50 Heteroatome, ausgewählt
aus Halogenen, Sauerstoff, Stickstoff, Schwefel, Bor, Phosphor und Silizium, enthält,
und R" ein O-Cellulose I-Radikal ist, das sich von der Formel I ableitet; vorausgesetzt,
dass die AR"-Gruppen in einem AR"/n-Verhältnis von 0,0001 bis 3 vorliegen.
5. Modifizierte Leinenfasern und Garne nach Anspruch 4, worin A ein lineares aliphatisches
C1-C18-Radikal ist, das wahlweise durch eine oder mehrere Hydroxylgruppen substituiert ist.
6. Modifizierte Leinenfasern und Garne nach Anspruch 4, worin A Polyoxyethylen, Polyoxypropylen,
Polyethylenimin und Polypropylenimin ist, das wahlweise durch eine oder mehrere Hydroxylgruppen
substituiert ist.
7. Ein Verfahren zur Herstellung von modifizierten Leinenfasern und Garnen nach den Ansprüchen
1 - 6, enthaltend die Schritte:
a) Anwendung eines Vemetzungsreagenzes auf die Leinenfasern und Garne und
b) Behandlung mit einer Base in einem nichtwässrigen Medium.
8. Ein Verfahren nach Anspruch 7, worin Schritt a) vor Schritt b) durchgeführt wird.
9. Ein Verfahren nach Anspruch 7, worin Schritt b) vor Schritt a) durchgeführt wird.
10. Ein Verfahren nach den Ansprüchen 7 - 9, worin das Vernetzungsreagenz eine Verbindung
der Formel
X'-A-X (I)
ist und X und X' reaktive Gruppen sind, z. B. Komponenten, die eher mit Hydroxylgruppen
von Cellulose reagieren können als eine Selbstpolymerisation zu durchlaufen;
A ein zweiwertiges Brückenradikal ist, das 1 bis 100 Kohlenstoffatome und wahlweise
1 bis 50 Heteroatome, ausgewählt aus Halogenen, Sauerstoff, Stickstoff, Schwefel,
Bor, Phosphor und Silicium, enthält.
1. Rubans de fibres et fils de lin modifiés, ayant une teneur en allomorphe I mesurée
par RMN 13C à l'état solide d'au moins 40% et caractérisés par une solubilité dans la cuproéthylènediamine (Cued) 0,5 M inférieure à 1,4 g/l.
2. Rubans de fibres et fils de lin modifiés selon la revendication 1, dans lesquels le
lin est réticulé par formation d'une liaison éther entre les groupes hydroxyle de
chaînes de cellulose.
3. Rubans de fibres et fils de lin modifiés selon la revendication 1, dans lesquels la
teneur en allomorphe I est d'au moins 45%.
4. Rubans de fibres et fils de lin modifiés selon l'une des revendications 1 à 3, ayant
la formule suivante :

dans laquelle :
- n représente un entier de 100 à 100 000 ;
- R représente un hydrogène ou un groupe de formule AR" dans laquelle A représente
un radical pontant bivalent comprenant de 1 à 100 atomes de carbone et, facultativement,
de 1 à 50 hétéroatomes choisis parmi les halogènes, l'oxygène, l'azote, le soufre,
le bore, le phosphore et le silicium, et R'' représente un radical O-cellulose I dérivé
de la formule I ; à la condition que les groupes AR'' soient présents dans un rapport
AR''/n de 0,0001 à 3.
5. Rubans de fibres et fils de lin modifiés selon la revendication 4, dans lesquels A
représente un radical aliphatique linéaire en C1-C18, facultativement substitué par un ou plusieurs groupes hydroxyle.
6. Rubans de fibres et fils de lin modifiés selon la revendication 4, dans lesquels A
représente les radicaux poly(oxyéthylène), poly(oxypropylène), poly(éthylèneimine)
et poly(propylèneimine), facultativement substitués par un ou plusieurs groupes hydroxyle.
7. Procédé de fabrication des rubans de fibres et des fils de lin modifiés tels que définis
à l'une des revendications 1 à 6, comprenant les étapes consistant à :
(a) appliquer un réactif de réticulation aux rubans de fibres et fils de lin ; et
(b) traiter par une base dans un milieu non-aqueux.
8. Procédé selon la revendication 7, dans lequel l'étape (a) est effectuée avant l'étape
(b).
9. Procédé selon la revendication 7, dans lequel l'étape (b) est effectuée avant l'étape
(a).
10. Procédé selon l'une des revendications 7 à 9, dans lequel le réactif de réticulation
est un composé de formule :
X'-A-X (I)
- X et X' sont des groupes réactifs, c'est-à-dire des fractions capables de réagir
avec des groupes hydroxyle de cellulose, plutôt que de subir une auto-polymérisation
;
- A représente un radical pontant bivalent comprenant de 1 à 100 atomes de carbone
et, facultativement, de 1 à 50 hétéroatomes choisis parmi les halogènes, l'oxygène,
l'azote, le soufre, le bore, le phosphore et le silicium.