(19) |
 |
|
(11) |
EP 1 563 925 B1 |
(12) |
EUROPÄISCHE PATENTSCHRIFT |
(45) |
Hinweis auf die Patenterteilung: |
|
28.05.2008 Patentblatt 2008/22 |
(22) |
Anmeldetag: 27.01.2005 |
|
(51) |
Internationale Patentklassifikation (IPC):
|
|
(54) |
Verfahren zur Herstellung von Durchzügen in Sammelrohren und Vorrichtung zur Durchführung
des Verfahrens
Method of making openings in collecting tubes and apparatus for doing so
Procédé de fabrication d' ouvertures dans des tubes collecteurs et moyen pour sa mise
en oeuvre
|
(84) |
Benannte Vertragsstaaten: |
|
DE ES FR IT |
(30) |
Priorität: |
16.02.2004 DE 102004007686
|
(43) |
Veröffentlichungstag der Anmeldung: |
|
17.08.2005 Patentblatt 2005/33 |
(73) |
Patentinhaber: Behr GmbH & Co. KG |
|
70469 Stuttgart (DE) |
|
(72) |
Erfinder: |
|
- Demuth, Walter, Dipl.-Ing. (FH)
71229 Leonberg (DE)
- Geiger, Wolfgang
71642 Ludwigsburg (DE)
- Kranich, Michael, Dipl.-Ing.
74354 Besigheim (DE)
- Staffa, Karl-Heinz, Dipl.-Ing.
70567 Stuttgart (DE)
- Walter, Christoph, Dipl.-Ing.
70469 Stuttgart (DE)
|
(56) |
Entgegenhaltungen: :
EP-A- 1 188 498 US-A- 5 202 543
|
DE-A1- 1 808 050
|
|
|
|
|
- PATENT ABSTRACTS OF JAPAN Bd. 009, Nr. 213 (M-408), 30. August 1985 (1985-08-30) &
JP 60 072620 A (MIYAGI SEIKI KK), 24. April 1985 (1985-04-24)
|
|
|
|
Anmerkung: Innerhalb von neun Monaten nach der Bekanntmachung des Hinweises auf die
Erteilung des europäischen Patents kann jedermann beim Europäischen Patentamt gegen
das erteilte europäischen Patent Einspruch einlegen. Der Einspruch ist schriftlich
einzureichen und zu begründen. Er gilt erst als eingelegt, wenn die Einspruchsgebühr
entrichtet worden ist. (Art. 99(1) Europäisches Patentübereinkommen). |
[0001] Die Erfindung betrifft ein zweistufiges Verfahren zur Herstellung von Durchzügen
in dickwandigen Sammelrohren nach dem Oberbegriff des Patentanspruches 1 sowie eine
Vorrichtung zur Durchführung des Verfahrens nach dem Oberbegriff des Patentanspruches
7. Ein solches Verfahren sowie eine solche Vorrichtung ist aus der
EP-A-1188498 bekannt.
[0002] Verfahren zur Herstellung von Durchzügen in dickwandigen und dünnwandigen Rohren
unterscheiden sich unter anderem dadurch, dass bei dickwandigen Rohren die Herstellung
des Durchzuges nicht in einem Arbeitsgang, z. B. durch Reißen mit einem Stempel möglich
ist. Vielmehr hat es sich als vorteilhaft erwiesen, die Durchzüge in dickwandigen
Rohren in zwei Verfahrensschritten, d. h. einem zweistufigen Verfahren herzustellen.
Derartige Durchzüge, sei es in Längsrichtung oder in Querrichtung des Rohres, werden
insbesondere bei Sammelrohren von Wärmeübertragern benötigt, die von einem überkritischen
Kältemittel wie C02 (R744) mit relativ hohen Drücken (bis zu 130 bar) beaufschlagt
werden. In diese Durchzüge werden Flachrohre, meistens Mehrkammerrohre, eingesetzt
und verlötet, sodass sich ein Wärmeübertrager hoher Innendruckfestigkeit ergibt.
[0003] Durch die
DE-A 199 45 223 der Anmelderin wurde ein Verfahren zur Herstellung von Durchzügen in einem doppelwandigen
Sammelrohr bekannt, welches für Innendrücke über 100 bar, also auch für den Betreib
mit dem Kältemittel C02 ausgelegt ist. Das bekannte Verfahren erzeugt in einem ersten
Verfahrenschritt durch Sägen mittels eines Sägeblattes einen Schlitz in einem ersten
dickwandigen Rohr, sodass das Rohr geöffnet ist. Anschließend wird ein dünnwandiges
Rohr über das dickwandige, geschlitzte Rohr geschoben und mit diesem durch einen Pressverband
verbunden. Schließlich werden mittels eines Stempels Durchzüge in das äußere dünnwandige
Rohr "gerissen", wobei das dickwandige Rohr als Innenmatrize fungiert. Nachteilig
bei diesem Verfahren ist, dass beim Sägen des Schlitzes Späne in das Innere des Rohres
und damit in den Kältemittelkreislauf gelangen können.
[0004] In der
DE-A 101 03 176 der Anmelderin wurde daher vorgeschlagen, dass beim Herstellen eines Schlitzes durch
Sägen nicht die gesamte Wandstärke des dickwandigen Rohres zerspant wird, sondern
dass jeweils eine Mindestwandstärke auf der Innenseite des Rohres erhalten bleibt.
Damit wird verhindert, dass infolge des Sägens anfallende Späne ins Innere des Sammelrohres
gelangen. Durch das Sägen wird die Wandstärke des dickwandigen Rohres soweit geschwächt,
dass anschließend eine konventionelle Herstellung eines Durchzuges mittels Durchzugsstempel
möglich ist. Dabei wird beim Eindringen des Stempels in die Rohrwandung Material nach
außen und innen verdrängt, sodass sich eine hinreichende Anlagefläche für die zu verlötenden
Flachrohre ergibt. Das bekannte zweistufige Verfahren ermöglicht die Herstellung von
in Längsrichtung des Rohres verlaufenden Schlitzen bzw. Durchzügen als auch von quer
zur Längsrichtung verlaufenden Schlitzen zum Einstecken von Flachrohren. Der erste
Verfahrensschritt, das Sägen ist somit spangebend, und der zweite Verfahrensschritt,
das Stanzen eine spanlose Umformung. Nachteilig hierbei ist der Verfahrensschritt
des Sägens, für welchen spezielle Sägeblätter und Sägevorrichtungen benötigt werden.
[0005] Es ist Aufgabe der vorliegenden Erfindung, ein Verfahren der eingangs genannten Art
dahingehend zu verbessern, dass es einfacher und kostengünstiger wird und damit auch
die Herstellkosten des durch das Verfahren hergestellten Erzeugnisses gesenkt werden.
Insbesondere soll durch das Verfahren eine günstige Gestaltung des Durchzuges erreicht
werden. Ferner ist es Aufgabe der Erfindung, eine geeignete Vorrichtung zur Durchführung
des Verfahrens bereitzustellen.
[0006] Diese Aufgabe wird durch die Merkmale des Patentanspruches 1 gelöst. Erfindungsgemäß
ist vorgesehen, dass der erste Verfahrensschritt des zweistufigen Verfahrens durch
Stoßen, Schälen oder Hobeln ausgeführt wird. In den Ansprüchen wird für diese Zerspanung
der Sammelbegriff "Stoßen" verwendet. Dabei wird ein entsprechender Stempel, Meißel
oder Schälmesser quer zur Längsrichtung des Sammelrohres geführt, um einen Teil der
Rohrwandstärke spangebend abzutragen. Bei dieser gezielten Materialschwächung bleibt
eine Mindestrohrwandstärke stehen, sodass das Rohr nach innen nicht geöffnet wird.
Mit dem erfindungsgemäßen Stoßvorgang wird eine Verfahrensvereinfachung erreicht,
wobei die gewünschte Reduzierung der Rohrwandstärke in einem oder mehreren Stoß- oder
Schälschritten erfolgen kann (einmaliger oder mehrmaliger Vorschub). Ferner ergibt
sich durch die verbleibende Mindestwandstärke der Vorteil, dass keine Späne in das
Rohrinnere und damit möglicherweise in den Kältemittelkreislauf gelangen. Während
beim Stoßen der Meißel am Werkstück (Sammelrohr) vorbeigeführt wird, bewegt sich beim
Hobeln das Werkstück gegenüber dem feststehenden Meißel. Das Hobeln ist daher ein
alternativer erster Verfahrensschritt.
[0007] Nach einer vorteilhaften Ausgestaltung der Erfindung liefert der Stoßvorgang eine
Schnittlänge L, die eine Kreissehne im Rohrquerschnitt bildet. Vorzugsweise ist die
Schnittlänge gleich dem oder kleiner als der Innendruchmesser des Sammelrohres. Damit
ergibt sich der Vorteil einer maximalen Durchzugslänge, d. h. das Verhältnis von Außendurchmesser
des Sammelrohres zur Tiefe der Flachrohre ist maximal.
[0008] In weiterer vorteilhafter Ausgestaltung der Erfindung wird in das Sammelrohr eine
Nut gestoßen, welche unterschiedliche Querschnitte aufweisen kann, z. B. einen Rechteck-
oder einen Dreiecksquerschnitt. Diese unterschiedliche Querschnittsgestaltung kann
durch Wahl eines entsprechenden Stempels oder Stoßmeißels bewirkt werden. Ein derartiges
Werkzeug kann leicht und schnell ausgetauscht werden.
[0009] Nach der Erfindung wird in der zweiten Stufe des Verfahrens ein Durchzugsstempel
quer zur vorangegangenen Stoßbewegung in das Rohr gestoßen, womit die endgültige Durchzugsform
durch Reißen und Materialverdrängung hergestellt wird. Bei diesem zweiten Verfahrensschritt
wird das Rohr also geöffnet, allerdings fallen bei diesem zweiten Schritt keine Späne
an, sodass auch keine Verunreinigung des Rohrinneren auftreten kann. Durch die Materialschwächung
im ersten Verfahrensschritt kann der Durchzug ohne Innenmatrize und ohne Verformung
der Rohrwandung hergestellt werden. In Abhängigkeit von der oben erwähnten Mindestwandstärke
nach dem ersten Verfahrensschritt werden die Wandungen des Durchzuges ausgebildet,
welche die Flachrohrenden umfassen.
[0010] Die Aufgabe der Erfindung wird auch durch eine Vorrichtung mit den Merkmalen des
Patentanspruches 7 gelöst, wobei erfindungsgemäß ein geteiltes Werkzeug mit einer
Öffnung zur Aufnahme eines Sammelrohres vorgesehen ist. Das Sammelrohr wird somit
fest im Werkzeug verspannt. Darüber hinaus weist das Werkzeug erfindungsgemäß einen
etwa tangential zum Sammelrohr verlaufenden ersten Kanal zur Führung des Stempels
oder Schälmessers auf. Das Schneidewerkzeug, welches den ersten spangebenden Verfahrensschritt
ausführt, ist somit über den gesamten Arbeitshub geführt, sodass eine saubere Spanbildung
und ein definierter Spanauswurf erfolgt. Erfindungsgemäß weist die Vorrichtung ferner
einen senkrecht zum ersten Kanal angeordneten zweiten Kanal zur Führung eines Durchzugsstempels
auf, welcher in einem zweiten Verfahrensschritt, d. h. anschließend an den Stoßvorgang
in das Rohrmaterial eindringt. Somit sind die für die Herstellung mindestens eines
Durchzuges erforderlichen Werkzeuge in einer Vorrichtung angeordnet und geführt. Dabei
können vorteilhafterweise mehrere Kanäle in Längsrichtung des Rohres vorgesehen werden,
in welchen Schälmesser und Durchzugsstempel geführt und betätigt werden. Damit können
sämtliche an einem Sammelrohr vorgesehen Durchzüge gleichzeitig, d. h. in aufeinander
folgenden Verfahrensschritten hergestellt werden. Danach wird das Werkzeug geöffnet
und das fertige Sammelrohr mit Durchzügen entnommen.
[0011] Ein Ausführungsbeispiel der Erfindung ist in der Zeichnung dargestellt und wird im
Folgenden näher beschrieben. Es zeigen
- Fig. 1
- eine Vorrichtung zur Durchführung des erfindungsgemäßen Verfahrens,
- Fig. 2
- einen Querschnitt eines Sammelrohres nach Durchführung des ersten Verfahrensschrittes
und
- Fig. 3
- eine Ausbildung eines Schälmessers mit unterschiedlichen Schälbreiten.
[0012] Fig. 1 zeigt eine Vorrichtung 1 zur Herstellung von Durchzügen an einem dickwandigen Sammelrohr
2, welches in die Vorrichtung 1 eingelegt ist. Die Vorrichtung 1 umfasst ein geteiltes
Werkzeug 3, welches aus einem Unterteil 3a und einem Oberteil 3b besteht und eine
an den Querschnitt des Sammelrohres 2 angepasste Aufnahmeöffnung 4 aufweist. Beide
Werkzeugteile 3a, 3b sind durch nicht näher dargestellte Spannmittel miteinander verspannt,
sodass das Sammelrohr 2 fest im Werkzeug 3 aufgenommen ist. Das Werkzeug 3 weist im
Bereich der Aufnahmeöffnung 4, die hier einen kreisförmigen Querschnitt aufweist,
einen in der Zeichnung senkrecht verlaufenden ersten Kanal 5 für einen Schälstempel
6 auf, welcher in dem Kanal 5 in Längsrichtung geführt wird. Der Schälstempel 6 weist
eine nicht dargestellte Schneidkante auf, welche in das Material des Sammelrohres
2 einschneidet und einen Span abtrennt. Der erste Kanal 5 weist eine Längsachse m
auf, die etwa tangential zum Außenumfang des Sammelrohres 2 verläuft. Senkrecht zum
ersten Kanal 5 ist ein zweiter Kanal 7 zur Führung eines Schlitzstempels 8 im Werkzeug
3 angeordnet, und zwar mit einer Kanalachse n, die senkrecht zur Kanalachse m des
ersten Kanals 5 verläuft. Der Schlitzstempel 8 ist an sich bekannt und weist einen
hier nicht dargestellten länglichen Querschnitt auf, welcher der Form der herzustellenden
Durchzüge bzw. der in die Durchzüge einzusetzenden Flachrohrenden entspricht. Insbesondere
weist der Schlitzstempel 8 frontseitig eine Schneide 8a auf, welche in das Rohrmaterial
des Sammelrohres 2 eindringt.
[0013] Das erfindungsgemäße Verfahren zur Herstellung von Durchzügen wird im Folgenden anhand
der oben beschriebenen Vorrichtung 1 erläutert. Der erste Verfahrensschritt besteht
darin, dass der Schälstempel 6 entlang der Längsachse m durch den ersten Kanal 5 gestoßen
wird, dabei mit seiner nicht dargestellten Schneidkante einen Span vom Umfang des
Sammelrohres 2 abhebt und am Ende des Kanals 5 (in der Zeichnung unten) auswirft.
Nach dem Auswurf wird der Schälstempel 6 in seine in der Zeichnung dargestellte Ausgangslage
zurückgezogen. Durch den Stoß- bzw. Schälvorgang ist am Umfang des Sammelrohres 2,
welches größtenteils schraffiert dargestellt ist, eine in tangentialer Richtung verlaufende
Nut 9 entstanden, die als nicht schraffiertes Kreissegment 9 dargestellt ist. Während
das Sammelrohr 2 generell eine Wandstärke s
0 aufweist, beträgt die Wandstärke an der schwächsten Stelle im Bereich der Tangentialnut
9 s
min, d. h. das Sammelrohr 2 ist im Bereich der Tangentialnut 9 nach innen geschlossen.
Die Wandstärke s
0 liegt bei Aluminiumrohren im Bereich von mehreren Millimetern, dagegen beträgt s
min wenige Zehntel Millimeter. Diese Mindestwandstärke verhindert einerseits das Eindringen
von Spänen in das Rohrinnere und ist andererseits zur Bildung einer Durchzugswand
in dem nachfolgenden Verfahrensschritt erforderlich. Der zweite Verfahrensschritt
besteht darin, dass der Schlitzstempel 8 in Richtung der Kanalachse n auf das Sammelrohr
2 zubewegt wird, bis die Schneide 8a in die Nut 9 eintritt und auf das Sammelrohr
2 mit der reduzierten Mindestwandstärke S
min trifft. Die weitere Bewegung des Stempels 8 in Richtung des Rohrmittelpunktes M führt
zunächst zu einem Aufreißen der verbleibenden Wandstärke und einer anschließenden
Materialverdrängung, sodass ein Durchzug entsprechend der Form des Stempels 8 im Sammelrohr
2 gebildet wird. Die Erstreckung des Schlitzstempels 8 entspricht etwa dem Innendurchmesser
des Sammelrohres 2. Der Schlitzstempel 8 wird nach dem "Reißen" des in seiner Endform
nicht dargestellten Durchzuges wieder in seine in der Zeichnung dargestellte Ausgangsposition
zurückgezogen. Damit ist der zweite Verfahrensschritt beendet und die Endform des
nicht dargestellten Durchzuges im Sammelrohr 2 hergestellt. Das Sammelrohr 2 weist
bei einer Verwendung als Wärmeübertrager, z. B. als Gaskühler einer mit C02 betriebenen
Kraftfahrzeug-Klimaanlage eine Vielzahl von Durchzügen auf, die mit der zuvor beschriebenen
Vorrichtung gleichzeitig hergestellt werden können, sofern die in Fig. 1 dargestellten
ersten und zweiten Kanäle 5, 7 im Abstand der Durchzüge im Werkzeug 3 angeordnet sind.
Bei einer derartigen Ausbildung der Vorrichtung 1 können die Stempel 6 und 8 jeweils
gleichzeitig und hintereinander betätigt werden, sodass sämtliche Durchzüge gleichzeitig
in einer Werkzeugeinspannung hergestellt werden können.
[0014] Fig. 2 zeigt einen Querschnitt durch das Sammelrohr 2 nach Durchführung des ersten Verfahrensschrittes,
d. h. nach Stoßen der tangentialen Nut 9. Die Nut 9 weist im Schnitt ein Kreissegment
mit einer Sehne der Länge L auf, wobei L die Schnittlänge der Nut 9 darstellt. Das
dickwandige Sammelrohr 2 weist einen Innendurchmesser DI auf. Zur Herstellung eines
optimalen Durchzuges soll die maximale Schnittlänge L
max das Maß des Innendruchmessers DI nicht überschreiten.
[0015] Fig. 3 zeigt einen Schälstempel 10 in zwei Ansichten mit unterschiedlichen Schälbreiten
H1 und H2, wobei H2 < H1 ist. H1 entspricht dabei der Höhe eines nicht dargestellten
Flachrohres, welches in den nicht dargestellten Durchzug gesteckt wird. Bei einer
Schälbreite von H2 < H1 ergeben sich nach dem Ausformen der Durchzüge mit dem Schlitzstempel
8 höhere Wände für den Durchzug, während bei einer Schälbreite von H1 die Wände des
Durchzuges infolge geringer Materialverdrängung relativ niedrig sind. Durch die Schälbreite
H1, H2 der Tangentialnut 9 kann somit Einfluss auf die Höhe der Durchzugswände genommen
werden.
1. Zweistufiges Verfahren zur Herstellung von Durchzügen in dickwandigen Sammelrohren
von Wärmeübertragern, wobei die Durchzüge als sich quer zur Längsachse des Sammelrohres
(2) erstreckende Schlitze zur Aufnahme von Flachrohren ausgebildet sind, wobei in
einer ersten Stufe des Verfahrens eine Reduzierung der Rohrwandstärke s0 im Bereich der Durchzüge mittels eines spangebende Verfahrensschrittes und in einer
zweiten Stufe des Verfahrens eine Materialverdrängung durch Eindringen eines Durchzugsstempels
(8) in den Bereich reduzierter Wandstärke erfolgt, und die Spanabhebung in der ersten
Stufe durch Stoßen ausgeführt wird, dadurch gekennzeichnet, dass der reißende und Materialverdrängende Durchzugsstempel (8) in der zweiten Stufe des
Verfahrens quer zur Richtung der Stoßbewegung der ersten Stufe geführt wird, derart,
dass bei diesem zweiten Schritt keine Späne anfallen.
2. Verfahren nach Anspruch 1, dadurch gekennzeichnet, dass das Stoßen mittels eines quer zur Längsachse des Sammelrohres (2) geführten Stempels
(6) erfolgt.
3. Verfahren nach Anspruch 1 oder 2, dadurch gekennzeichnet, dass die Spanabhebung, ausgehend von einer anfänglichen Wandstärke s0, nur bis zu einer minimalen Wandstärke smin durchgeführt wird.
4. Verfahren nach Anspruch 1, 2 oder 3, dadurch gekennzeichnet, dass durch den Vorgang des Stoßens eine Kreissehne mit einer Schnittlänge L erzeugt wird,
die kleiner als der oder gleich dem Innendurchmesser DI des Sammelrohres (2) ist.
5. Verfahren nach einem der Ansprüche 1 bis 4, dadurch gekennzeichnet, dass im Sammelrohr (2) mindestens eine querverlaufende Nut (Tangentialnut 9) erzeugt wird,
die einen rechteck- oder dreieckförmigen Querschnitt mit einer Schälbreite H aufweist.
6. Verfahren nach Anspruch 1, dadurch gekennzeichnet, dass durch das Eindringen des Durchzugsstempels (8) die Endform der Durchzüge hergestellt
wird.
7. Vorrichtung zur Durchführung des Verfahrens nach einem der Ansprüche 1 bis 6, gekennzeichnet durch ein geteiltes Werkzeug (3, 3a, 3b) mit einer Aufnahmeöffnung (4) für das Sammelrohr
(2), einem tangential zur Aufnahmeöffnung (4) angeordneten ersten Kanal (5) zur Führung
eines Schälstempels (6) und mit einem senkrecht zum ersten Kanal (5) angeordneten
zweiten Kanal (7) zur Führung des reißenden und Materialverdrängenden Durchzugsstempels
(8).
1. Two-stage method for the production of openings in thick-walled collecting tubes of
heat exchangers, the said openings being formed as slots that extend transversely
to the longitudinal axis of the collecting tube (2) to receive flat tubes, such that
in a first stage of the method the tube wall thickness s0 is reduced in the area of the openings by a machining process step and in the second
stage of the method material is displaced by the penetration of a perforating ram
(8) in the area of reduced wall thickness, and the machining in the first stage is
carried out by slotting, characterised in that in the second stage of the method the perforating ram (8) is moved transversely to
the direction of the slotting movement in the first stage, in such manner that in
the second stage no machining chips are produced and the final shape of the opening
is created by rupturing and displacing the material.
2. Method according to Claim 1, characterised in that the slotting is carried out by a punch (6) that is moved transversely to the longitudinal
axis of the collecting tube (2).
3. Method according to Claims 1 or 2, characterised in that starting with an initial wall thickness of s0, machining is only carried out down to a minimum wall thickness of smin.
4. Method according to Claims 1, 2 or 3, characterised in that by the slotting process a chord of a circle is produced, whose cut length L is smaller
than or equal to the inside diameter DI of the collecting tube (2).
5. Method according to any of Claims 1 to 4, characterised in that at least one transversely extending groove (tangential groove 9) is produced in the
collecting tube (2), which has a rectangular or triangular cross-section with width
of cut H.
6. Method according to Claim 1, characterised in that the final shape of the opening is produced by the penetration of the perforating
ram (8).
7. Device for implementing the method according to any of Claims 1 to 6, characterised in that it comprises a split die (3, 3a, 3b) with a holding aperture (4) for the collecting
tube (2), with a first channel (5) arranged tangentially to the said holding aperture
(4) which guides a slotting punch (6) and with a second channel (7) arranged perpendicularly
to the first channel (5) which guides the perforating ram (8), in such manner that
the final shape of the opening is produced by rupturing and displacing the material.
1. Procédé en deux étapes pour la fabrication de passages dans des tubes collecteurs,
à parois épaisses, d'échangeurs de chaleur, où les passages sont configurés comme
des fentes s'étendant de façon transversale par rapport à l'axe longitudinal du tube
collecteur (2) et servant au logement de tubes plats où, au cours d'une première étape
du procédé, il se produit, dans la zone des passages, une diminution de l'épaisseur
s0 des parois tubulaires, au moyen d'une étape du procédé se produisant par enlèvement
de copeaux et, au cours d'une deuxième étape du procédé, il se produit un refoulement
de matière par pénétration d'un poinçon (8) de formation de passages dans la zone
d'épaisseur de paroi réduite, et l'enlèvement de copeaux se produisant au cours de
la première étape est réalisé par mortaisage,
caractérisé en ce que le poinçon (8) de formation des passages est guidé, au cours de la deuxième étape
du procédé, de façon transversale par rapport à la direction du mouvement de mortaisage
se produisant au cours de la première étape, de manière telle qu'au cours de cette
deuxième étape, il ne se forme aucun copeau, et que la forme définitive des passages
soit réalisée par rupture et par refoulement de matière.
2. Procédé selon la revendication 1, caractérisé en ce que le mortaisage est réalisé au moyen d'un poinçon (6) guidé de façon transversale par
rapport à l'axe longitudinal du tube collecteur (2).
3. Procédé selon la revendication 1 ou 2, caractérisé en ce que l'enlèvement de copeaux est réalisé à partir d'une épaisseur de paroi initiale s0, jusqu'à une épaisseur de paroi minimale smin.
4. Procédé selon les revendications 1, 2 ou 3, caractérisé en ce qu'une corde de cercle ayant une longueur de coupe L est produite par le processus du
mortaisage, longueur de coupe qui est inférieure ou égale au diamètre intérieur DI
du tube collecteur (2).
5. Procédé selon l'une quelconque des revendications 1 à 4, caractérisé en ce qu'au moins une rainure s'étendant transversalement (rainure tangentielle 9) est produite
dans le tube collecteur (2), rainure qui présente une section de forme rectangulaire
ou triangulaire, ayant une largeur d'écroûtage H.
6. Procédé selon la revendication 1, caractérisé en ce que la forme définitive des passages est réalisée par la pénétration du poinçon (8) de
formation des passages.
7. Dispositif de mise en oeuvre du procédé selon l'une quelconque des revendications
1 à 6, caractérisé par un outil divisé (3, 3a, 3b) comprenant une ouverture de logement (4) pour le tube
collecteur (2), un premier conduit (5) disposé de façon tangentielle par rapport à
l'ouverture de logement (4) et servant au guidage d'un poinçon d'écroûtage (6), et
comprenant un deuxième conduit (7) disposé perpendiculairement au premier conduit
(5) et servant au guidage du poinçon (8) de formation des passages, de manière telle
que la forme définitive des passages soit réalisée par rupture et par refoulement
de matière.
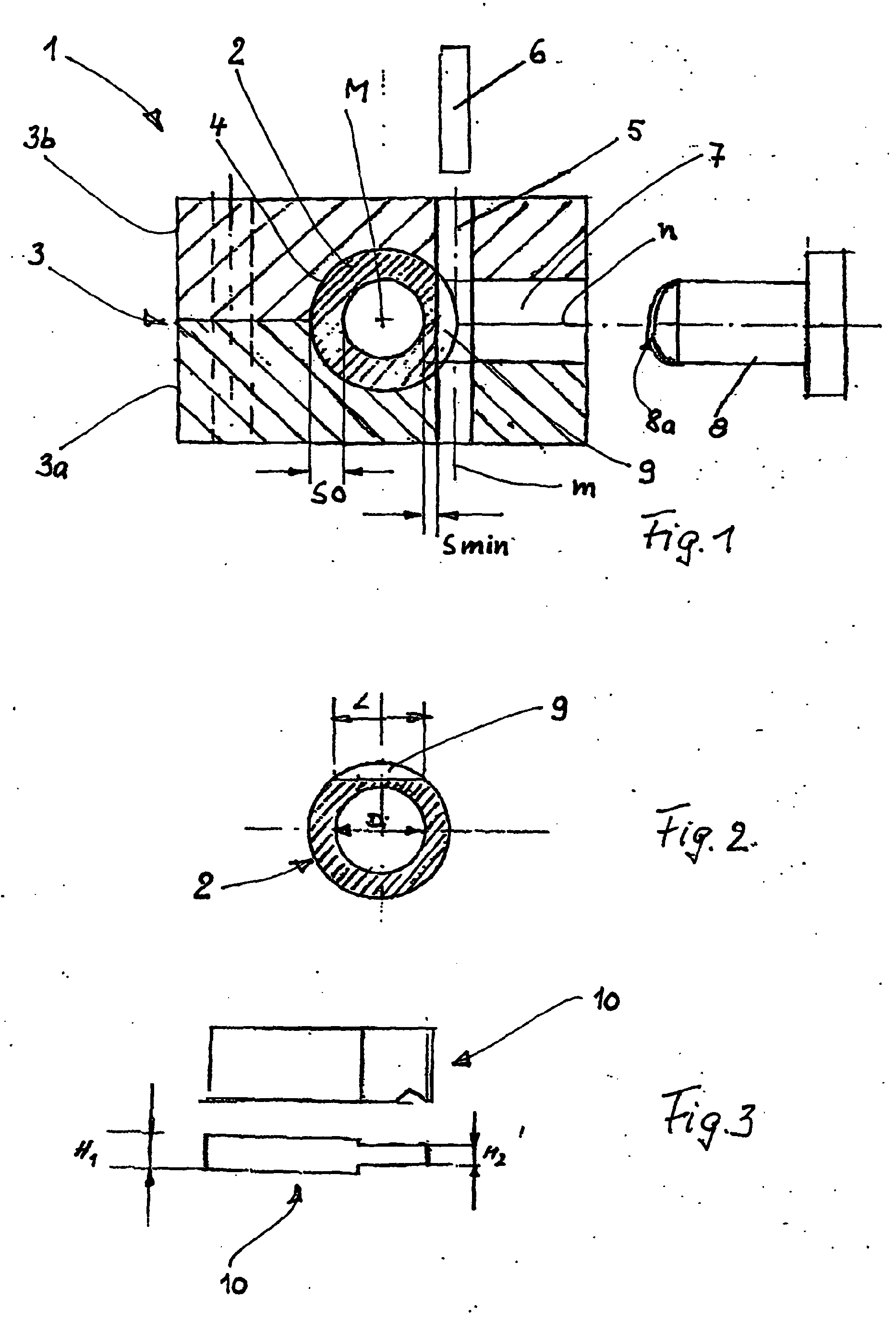
IN DER BESCHREIBUNG AUFGEFÜHRTE DOKUMENTE
Diese Liste der vom Anmelder aufgeführten Dokumente wurde ausschließlich zur Information
des Lesers aufgenommen und ist nicht Bestandteil des europäischen Patentdokumentes.
Sie wurde mit größter Sorgfalt zusammengestellt; das EPA übernimmt jedoch keinerlei
Haftung für etwaige Fehler oder Auslassungen.
In der Beschreibung aufgeführte Patentdokumente