TECHNICAL FIELD
[0001] The present invention relates to an air conditioner refrigerant circuit, and more
particularly to an air conditioner refrigerant circuit that connects an outdoor unit
refrigerant circuit that includes a compressor, a four way directional control valve,
and an outdoor heat exchanger that is disposed inside the outdoor device, with an
indoor heat exchanger that is disposed inside an indoor unit, by means of liquid line
piping and gas line piping.
BACKGROUND ART
[0002] An air conditioner refrigerant circuit is a system in which a compressor, a four
way directional control valve, and a outdoor heat exchanger disposed inside an outdoor
unit are connected, by means of refrigerant piping, to an indoor heat exchanger disposed
inside an indoor unit, and which forms a circulatory route for refrigerant.
[0003] In this type of air conditioner refrigerant circuit, during cooling, in order for
the outdoor heat exchanger to function as a condenser, and the indoor heat exchanger
to function as an vaporizer, the direction in which the refrigerant circulates is
controlled by the four way directional control valve. At this time, when a high pressure
receiver (hereinafter referred to as a "receiver") that temporarily stores liquid
refrigerant condensed by the outdoor heat exchanger is provided in the refrigerant
circuit, and the amount of refrigerant inside the outdoor heat exchanger that functions
as a condenser, and the amount of refrigerant inside the indoor heat exchanger that
functions as an vaporizer, changes, there are times when the refrigerant circuit is
constructed such that the change in the amount of refrigerant is absorbed by the receiver.
[0004] Normally, in the outdoor unit, a liquid line shut off valve is provided on the liquid
line piping that is connected to the outdoor heat exchanger, a gas line shut off valve
is provided on the gas line piping that is connected to the four way directional control
valve, and the receiver is serially disposed between the liquid line shut off valve
and the outdoor heat exchanger.
[0005] With a multi-type of air conditioner, in which one outdoor unit is connected to a
plurality of indoor units, in order for sufficient refrigerant to be distributed to
each indoor unit, a decompression circuit such as an electric valve or the like is
provided for each indoor heat exchanger.
[0006] In an air conditioner refrigerant circuit constructed in this manner, during cooling
operations, the amount of refrigerant supplied to each indoor heat exchanger can be
controlled at a suitable level by means of the decompression circuit provided for
each indoor heat exchanger. In addition, in situations in which the sum of the amount
of refrigerant in the outdoor heat exchanger and the amount of refrigerant in each
indoor heat exchanger fluctuates, the air conditioner refrigerant circuit is constructed
so that an adjustment in the amount of refrigerant takes place by means of the receiver,
and is returned to the compressor.
[0007] During heating, in order for the indoor heat exchangers to function as condensers,
and the outdoor heat exchanger to function as a vaporizer, the four way directional
control valve is operated and the refrigerant cycle takes place. At this time, because
the surplus refrigerant used during heating is stored in the receiver, it is necessary
to provide decompression circuits, such as electric valves or the like, between the
receiver and the indoor heat exchangers. Because of this, there is a danger that the
pressure differential before and after the decompression circuits used for distribution
that correspond to each indoor heat exchanger will become small, and that the flow
of refrigerant inside the indoor heat exchangers will worsen.
[0008] In particular, in situations in which each indoor device is provided on different
floors inside a building, there is a danger that vertical drift will develop due to
the differences in the elevation of each indoor heat exchanger, and that the flow
of refrigerant to the indoor heat exchanger on the lowest floor will cease. In order
to eliminate this, it is possible to enhance the capacity of the decompression circuit
provided on the outlet of the receiver in the outdoor device, and enlarge the pressure
differential before and after the decompression circuits used for distribution. For
example, it is possible to enlarge the diameter of an electric valve employed as a
decompression circuit on the receiver outlet. However, this is an expensive component,
and thus makes it difficult to reduce costs. An air conditioner refrigerating circuit
having the features defined in the preamble of claim 1 is known from
US-A-5,784,892.
[0009] It is an object of the present invention to reduce the occurrence of refrigerant
drift in situations in which there are differences in the elevation in which a plurality
of indoor devices are disposed, and to provide a refrigerant circuit in which cost
reductions can be achieved.
DISCLOSURE OF THE INVENTION
[0010] The air conditioner refrigerant circuit according to the present invention has the
features defined in the preamble of claim 1. Embodiments of the invention are named
in the dependent claims.
BRIEF DESCRIPTION OF THE DRAWINGS
[0011]
Fig. 1 is a schematic view of a first embodiment not comprising the claimed gas recovery
capillary.
Fig. 2 is a schematic view of a second embodiment not comprising the claimed gas recovery
capillary.
Fig. 3 is a schematic view of a third embodiment not comprising the claimed gas recovery
capillary.
Fig. 4 is a.schematic view of a fourth embodiment not comprising the claimed gas recovery
capillary.
Fig. 5 is a schematic view of a fifth embodiment according to the present invention.
Fig. 6 is a schematic view of a seventh embodiment according to the present invention.
Fig. 7 is a schematic view of a seventh embodiment according to the present invention.
Fig. 8 is a schematic view of a eighth embodiment according to the present invention.
Fig. 9 is a schematic view of a ninth embodiment according to the present invention.
Fig. 10 is a simplified descriptive view of an outdoor heat exchanger.
Fig. 11 is a view of a preferred embodiment.
Fig. 12 is a control flow chart during heating operations.
Fig. 13 is a descriptive view showing a working example during heating operations.
Fig. 14 is a descriptive view showing a working example during heating operations.
Fig. 15 is a descriptive view showing a working example during heating operations.
Fig. 16 is a descriptive view showing a working example during heating operations.
Fig. 17 is a control flow charge during cooling operations.
Fig. 18 is a descriptive view showing a working example during cooling operations.
Fig. 19 is a descriptive view showing a working example during cooling operations.
Fig. 20 is a descriptive view showing a working example during cooling operations.
Fig. 21 is a descriptive view showing a working example during cooling operations.
Fig. 22 is a descriptive view showing a working example during cooling operations.
Fig. 23 is a flow chart of the target discharge line temperature control by means
of the outdoor unit electric valves.
Fig. 24 is a flow chart of the target discharge line temperature control by means
of the outdoor unit electric valves.
Fig. 25 is a flow chart of a control condition ①.
Fig. 26 is a flow chart of a temporary target discharge line temperature calculation
during cooling.
Fig. 27 is a flow chart of a temporary target discharge line temperature calculation
during heating.
Fig. 28 is a flow charge of a target discharge line temperature calculation.
Fig. 29 is a flow charge of a control condition ②.
BEST MODE FOR CARRYING OUT THE INVENTION
[Overall construction of the invention]
[0012] In order to achieve the object of the present invention, embodiments that are considered
from a variety of viewpoints are shown below.
[First embodiment: Receiver disposed in a bypass circuit]
[0013] As shown in Fig. 1, we will consider a situation in which a plurality of indoor units
200A, 200B, etc. are connected to an outdoor unit 100 via branching units 300A, 300B,
etc.
[0014] The outdoor unit 100 is comprised of a compressor 101, a four way directional control
valve 102, an outdoor heat exchanger 103, an accumulator 105, and the like. A discharge
thermistor 109 for detecting the discharge line temperature is provided on the discharge
side of the compressor 101. Further, an outside air thermistor 111 for detecting the
outside air temperature, and an outdoor heat exchange thermistor 112 for detecting
the temperature of the outdoor heat exchanger 103, are provided in the outdoor unit
100. In addition, a fan 106 for drawing in outside air and exchanging heat between
the outside air and the refrigerant that flows inside the outdoor heat exchanger 103,
and a fan motor 104 for rotationally driving the fan 106, are provided.
[0015] In order to lead the refrigerant piping from the outdoor unit 100 to the indoor units,
a liquid line connector port 114 that is connected to the outdoor heat exchanger 103,
and a gas line connector port 115 that is connected to the four way directional control
valve 102, is provided in the outdoor unit 100. A liquid line shut off valve 116 and
a gas line shut off valve 117 are installed on the inside of each connecting port.
[0016] A receiver 121 is provided in the outdoor unit 121, which temporarily stores surplus
refrigerant liquid from the outdoor heat exchanger 103 when it functions as a condenser
during air conditioning. The receiver 121 comprises a liquid line connector 122 and
a gas line connector 123. The liquid line connector 122 is connected to liquid line
piping 131 between the outdoor heat exchanger 103 and the liquid line shut off valve
116, and the gas line connector 123 is connected to gas line piping 132 between the
four way directional control valve 102 and the gas line shut off valve 117.
[0017] A plurality of branching units 300A, 300B, etc. are connected to the liquid line
connector port 114 and the gas line connector port 115 on the outside unit 100. Because
the branching units 300A, 300B, etc. each have an identical construction, a description
of the branching unit 300A will be provided, and a description of the other branching
units will be omitted.
[0018] The branching unit 300A is comprised of an outdoor liquid line connector port 301
that is connected to the liquid line connector port 114 on the outdoor unit 100, and
an outdoor gas line connector port 303 that is connected to the gas line connector
port 115 on the outdoor unit 100. The branching unit 300A is comprised of a liquid
line branching circuit that branches on the inside of the outdoor liquid line connector
port 301, and on the other side thereof, indoor liquid line connector ports 302 are
provided which are connected to a number of indoor units. In addition, the branching
unit 300A is comprised of a gas line branching circuit that branches on the inside
of the outdoor liquid line connector port 303, and on the other side thereof, indoor
liquid line connector ports 304 are provided which are connected to a number of indoor
units. Here, indoor liquid line connector ports 302A, 302B, and 302C, and indoor gas
line connector ports 304A, 304B, and 304C are provided for three connected indoor
units.
[0019] Electric valves 305A - 305C for decompressing the pressurized refrigerant that passes
therethrough, and liquid line thermistors 306A - 306C for detecting the temperature
of the refrigerant temperature that passes therethrough, are each provided along the
branching circuit that spans between the outdoor liquid connector port 301 inside
the branching unit 300A to each indoor liquid line connector port 302A - 302C. Further,
gas line thermistors 307A - 307C for detecting the temperature of the refrigerant
that passes therethrough, are each provided along the branching circuit that spans
between the outdoor gas connector port 303 inside the branching unit 300A to each
indoor gas line connector port 304A - 304C.
[0020] A plurality of indoor units 200 are connected to each branching unit 300A, 300B,
etc. Here, there are 3 indoor units that can be connected to each branching unit 300A,
300B, etc., with the indoor units 200A - 200C connected to the branching unit 300A,
and the indoor units 200D - 200F connected to the branching unit 300B. Each indoor
unit 200A - 200F is an indoor unit for use with a multi unit, and any of them can
be used as a paired unit. Here, indoor device 200A will be described when used as
a paired unit.
[0021] Indoor unit 200A is comprised of an indoor heat exchanger 201, and refrigerant piping
connected to this indoor heat exchanger 201 is lead to the outdoor unit via a liquid
connector port 204 and a gas connector port 205. Further, this indoor device 200A
is comprised of a room temperature thermistor 202 for detecting the indoor temperature,
and an indoor heat exchange thermistor 203 for detecting the temperature of the indoor
heat exchanger 201.
[0022] Note that with the indoor units connected to branching units 300A, 300B, in situations
in which indoor units for multi unit use are employed, there are times when liquid
line thermistors are provided for detecting the temperature of the refrigerant that
flows inside the liquid line piping. In this case, the liquid line thermistors inside
the branching units 300A, 300B can be omitted.
[0023] Further, the gas line connector 123 of the receiver 121 can be constructed so that
it connects the gas line between the four way directional control valve 102 and the
accumulator 105.
[0024] In this embodiment, when the receiver 121 is provided in the bypass circuit that
connects the liquid line shut off valve 116 and the gas line shut off valve 117 in
the outdoor unit 100, surplus refrigerant can be collected in this receiver 121, and
refrigerant can be distributed during heating by means of the electric valves 305A
- 305C, 305D - 305F, etc. inside the branching units 300A, 300B, etc., there is a
lower occurrence of high-low drift due to the locations in which the indoor units
are disposed, and there is no longer any need to provide a large diameter electric
valve in the main refrigerant circuit of the outdoor device 100.
[Second embodiment: Provide a decompression circuit before and after the receiver]
[0025] In the first embodiment, it is possible to provide a decompression circuit on the
liquid line connector 122 and the gas line connector 123 of the receiver 121.
[0026] For example, as shown in Fig. 2, capillaries 124, 125 for decompression are respectively
installed on the liquid line connector 122 and the gas line connector 123 of the receiver
121. Electric valves for decompression may respectively provided thereon instead of
the capillaries 124, 125.
[0027] Due to this type of construction, the collection of surplus refrigerant in the receiver
121 can be smoothly performed.
[Third embodiment: Provide functional components that interrupt the flow of refrigerant
before and after the receiver]
[0028] In the first embodiment, it is possible to provide functional components that shut
off the flow of refrigerant to the liquid line connector 122 and the gas line connector
123 of the receiver 121. Here, as shown in Fig. 3, magnetic valves 126, 127 used as
refrigerant shut offs are installed on the liquid line connector 122 and the gas line
connector 123 of the receiver 121.
[0029] Due to this type of construction, surplus refrigerant can be reliably collected in
the receiver 121, refrigerant can be appropriately distributed by means of each magnetic
valve inside the branching units 300A, 300B, etc., and the occurrence of high-low
drift can be prevented.
[Fourth embodiment: Provide functional components before and after the receiver that
have a decompression function and a refrigerant shut off function]
[0030] In the first embodiment, it is possible to provide functional components that have
a decompression function and a refrigerant shut off function in the liquid line connector
121 and the gas line connector 122 of the receiver 121. For this type of functional
components, it is possible to employ a combination of electric valves or capillaries
that have a decompression function and a shut off function, and magnetic valves.
[0031] In Fig. 4, a liquid line electric valve (EVL) 128 is provided in the liquid line
connector 122 of the receiver 121, and a gas line electric valve (EVG) 129 is provided
in the gas line connector 123 of the receiver 121.
[0032] Due to this type of construction, there is no need to provide a large diameter electric
valve for decompression in the main circuit of the outdoor device 100, and refrigerant
can be appropriately distributed during heating operations. In addition, because a
main decompression circuit is not needed on the main circuit, the pressure differential
before and after the electric valves 305A - 305C, 305D - 305F, etc. in the branching
units 300A, 300B, etc. connected to each heat exchanger 201 can be maintained at a
high level, and the occurrence of high-low drift can be prevented. Moreover, it also
has the effect of making it possible to simultaneously control the SC control on the
outdoor heat exchanger 103 and the inlet superheating control on the compressor 101
during cooling operations, optimizing control of the refrigerating cycle, maintaining
reliability, improving COP, expanding the range of operational availability, and the
like.
[Fifth embodiment: Provide a gas recovery capillary on the receiver and the gas line
piping]
[0033] In the third and fourth embodiments, it is possible to provide a capillary for venting
gas between the receiver 121 and the gas line piping 132. In this case, as shown in
Fig. 5, a gas recovery capillary 130 can be provided which is connected with the gas
line piping 132 between the four way directional control valve 102 and the gas shut
off valve 117, and serves to collect gaseous refrigerant from the receiver 121.
[0034] In conventional refrigerant circuits, in order to improve the refrigerant collection
function during pump down operations, a gas recovery capillary is provided in the
piping between the four way directional control valve that becomes continuous low
pressure piping, and the accumulator. However, in this case, during normal operations
(cooling operations and heating operations), because refrigerant flows from the high
pressure side to the low pressure side, the result is that a decline in efficiency
is incurred during normal operations. Further, in situations in which surplus refrigerant
is handled by the receiver during heating operations, because the gas recovery capillary
is connected to a continuous low pressure line, the flow rate characteristics of the
capillary must be made smaller, and the result of this is that it becomes difficult
to improve refrigerant collection efficiency during pump down operations.
[0035] Due to the construction of this fifth embodiment, gas refrigerant inside the receiver
121 can return to the inlet of the accumulator via the gas recovery capillary 130
during pump down operations, it becomes easy to store liquid refrigerant in the receiver
121, and during normal operations, the flow of refrigerant from the gas recovery capillary
130 can be interrupted during cooling operations by shutting liquid line electric
valve 128. Further, high pressure can be maintained inside the receiver 121 during
heating operations, the back flow of refrigerant from the liquid line electric valve
128 can be prevented, and it becomes possible to handle surplus refrigerant during
heating operations.
[Sixth embodiment: Provide an auxiliary heat exchanger in the gas line connector]
[0036] In the embodiments described above, it is possible to provide an auxiliary heat exchanger
in the gas line connector 123 of the receiver 121. An example of this situation is
shown in Fig. 6.
[0037] In Fig. 6, a gas line electric valve 129 having a decompression function and a refrigerant
shut off function is provided on the gas line connector 123 of the receiver 121. An
auxiliary heat exchanger 133 is provided between the gas line electric valve 129 and
the portion that connects with the gas line piping 132.
[0038] When the refrigerant circuit in the first to fifth embodiments is employed and cooling
operations take place, when surplus refrigerant is discharged from the receiver, it
is necessary to control the speed of refrigerant discharge in order to prevent liquid
from suddenly backing up toward the accumulator. However, by providing this type of
auxiliary heat exchanger 133, it becomes possible to eliminate the occurrence of a
sudden liquid backup toward the accumulator, and improve the speed of refrigerant
discharge, because the liquid refrigerant vaporizes by means of this auxiliary heat
exchanger 133. In addition, during heating operations, because the auxiliary heat
exchanger 133 functions as a condenser, it becomes possible to improve the speed in
which surplus refrigerant is stored in receiver 121.
[0039] Further, by providing the liquid line electric valve 128 and the gas line electric
valve 129 connected to the receiver 121, and providing the auxiliary heat exchanger
133 between the liquid line electric valve 129 and the gas line electric valve 132,
it becomes possible to control the state of the refrigerant in the outlet of the outdoor
heat exchanger 103 (liquid line piping 131). Because of this, when the temperature
of the discharge pipe is high, the quantity of refrigerant discharged from the receiver
121 is made large in order to cool it, and when there is liquid refrigerant in the
accumulator 105, it becomes possible to control the discharge temperature by reducing
the quantity of refrigerant discharge from the receiver 121. In addition, because
it becomes possible to adjust the temperature of the surplus refrigerant stored during
heating operations, and because the condensing ability of the auxiliary heat exchanger
133 is variable, under conditions in which high pressure is easily raised during heating
overload operations, the condensing ability of the auxiliary heat exchanger 133 can
be enlarged by enlarging the opening of the gas line electric valve 129, and this
can contribute to a decrease in the high pressure.
[Seventh embodiment: Place an auxiliary heat exchanger on the lower portion of the
outdoor heat exchanger]
[0040] Like the sixth embodiment, when the auxiliary heat exchanger 133 is disposed on the
gas line connector 123 of the receiver 121, it is possible to provide the auxiliary
heat exchanger 133 inside the outdoor heat exchanger 103, and, it is possible to place
it on the lowermost portion of the outdoor heat exchanger 103. This seventh embodiment
is shown in Fig. 7.
[0041] In Fig. 7, the auxiliary heat exchanger 133 connected to the gas line connector 123
of the receiver 121 is provided inside the outdoor heat exchanger 103, and, is disposed
on the lowermost portion of the outdoor heat exchanger 103.
[0042] During heating operations in which the outdoor temperature is low, there is a danger
that water condensed after defrosting operations will refreeze in the lower frame
of the outdoor unit 100, will grow until it reaches the outdoor heat exchanger 103,
and a decrease in operational performance will result. Like this seventh embodiment,
by placing an auxiliary heat exchanger 133 in the lowermost portion of the outdoor
heat exchanger 103, and due to the refrigerant that flows inside the auxiliary heat
exchanger 133 during heating operations in low outdoor temperatures, condensed water
can be prevented from refreezing, and it becomes possible to prevent a decline in
the performance of the outdoor heat exchanger 103.
[Eighth embodiment: Place a subcooling heat exchanger adjacent to the auxiliary heat
exchanger]
[0043] The situation in which a subcooling heat exchanger is disposed on the liquid line
of a outdoor heat exchanger will be considered. This subcooling heat exchanger is
a device for placing refrigerant from the outlet of the outdoor heat exchanger into
the supercooled state during cooling. The configuration shown in Fig. 8 will be considered,
in which the auxiliary heat exchanger in the seventh embodiment is disposed in the
outdoor heat exchanger and is adjacent to the subcooling heat exchanger.
[0044] A subcooling heat exchanger 134 is disposed below the outdoor heat exchanger 103,
and below that, the auxiliary heat exchanger 133 is disposed on the lowermost portion
of the outdoor heat exchanger 103.
[0045] With this type of construction, due to the vaporizing abilities of the auxiliary
heat exchanger 133, cooling abilities can be increased by means of the subcooling
heat exchanger 134 disposed adjacent thereto, and the degree to which the refrigerant
from the outlet of the outdoor heat exchanger 103 is supercooled can be increased.
[Ninth embodiment: Place an auxiliary heat exchanger upwind of the subcooling heat
exchanger]
[0046] In the eighth embodiment, it is possible to place an auxiliary heat exchanger cooling
line upwind of a subcooling heat exchanger cooling line.
[0047] The outdoor heat exchanger 103, for example, as shown in Fig. 10, is composed of
a plurality of cooling lines 171 that have one end thereof bent back, and a plurality
of heat radiating fins 172, which are metallic plate members that have insertion holes
formed therein for inserting the cooling lines 171. Distributors 173, 174 are provided
on both ends of each cooling line 171. When each cooling line 171 functions as a vaporizer,
one end thereof serves as a refrigerant port, and when each cooling line 171 functions
as a condenser, the other end serves as a refrigerant port.
[0048] Fig. 9 shows an enlarged lateral view of only the lower portion of this type of outdoor
heat exchanger 103. Here, a pipe plate 175 that supports both ends of cooling lines
171 is provided on the side surface of the outdoor heat exchanger 103. This pipe plate
175 is formed into approximately the same shape as the heat radiating fins 172, and
has insertion holes 176 formed therein for inserting the cooling lines 171. The cooling
lines 171 disposed between the distributors 173, 174 are inserted into each insertion
hole 176.
[0049] The distributor 174 on the outdoor heat exchanger 103 is connected to the four way
directional control valve 102, and the distributor 173 is connected to the subcooling
heat exchanger 134. The subcooling heat exchanger 134 is comprised of an SC cooling
line 177, one end of which is connected to the distributor 173, and the other end
thereof is connected to the liquid shut off valve 116. Further, the auxiliary heat
exchanger 133 is comprised of an auxiliary cooling line 178, one end of which is connected
to the gas line electric valve 129, and the other end thereof is connected to the
gas line piping 132.
[0050] Here, if we assume that the direction of the wind generated by a fan 106 is that
shown by the arrow A in Fig. 9 (from right to left in Fig. 9), then the SC cooling
line 177 is disposed on the downwind side (the left side of Fig. 9), and the auxiliary
cooling line 178 is disposed on the upwind side (the right side of Fig. 9).
[0051] Due to this type of construction, heat exchange can not only occur by means of the
thermal conduction of the SC cooling line 177, the heat radiating fins 172, and the
auxiliary cooling line 178, but the heat radiated outward by the airflow produced
by the fan 106 can be used, the efficiency of the subcooling heat exchanger 134 is
increased, and refreezing in the lower portion of the outdoor heat exchanger 103 can
be prevented.
[Preferred Embodiment]
[0052] By appropriately combining the above described first through eighth embodiments,
it is expected that large efficiencies will be obtained. A preferred embodiment that
is a combination of these embodiments will be described below.
[0053] The preferred embodiment of the present invention is shown in Fig. 11.
[0054] The outdoor device 100 is comprised of an outdoor refrigerant circuit, which is comprised
of a compressor 101, a four way directional control valve 102, a heat exchanger 103,
an accumulator 105, and the like. A discharge pressure protection switch 108 for detecting
an abnormal rise in the discharge pressure is provided on the discharge side of the
compressor 101, and an inlet pressure sensor 110 for detecting the inlet pressure
is provided on the inlet side of the compressor 101.
[0055] Further, an oil separator 107 for separating the lubricating oil that is included
in the refrigerant and returning it to the accumulator 105 is provided on the discharge
side of the compressor 101. A discharge line thermistor 109 for detecting the temperature
on the discharge side of the compressor 101 is installed in the oil separator 107.
[0056] A discharge - intake capillary 141 for adjusting the discharge pressure and the inlet
pressure, and a discharge - intake electric valve (EVP) 142 for controlling capacity,
are provided in a discharge - intake bypass that connects the outlet side of the oil
separator 107 and the inlet side of the accumulator 105. In addition, an outside air
thermistor 111 for detecting the outside air temperature, and an outdoor heat exchange
thermistor 112 for detecting the temperature of the outdoor heat exchanger 103, are
provided in the outdoor unit 100. Further provided are fans 106 for drawing in air
from outside and exchanging heat between the refrigerant that flows inside the outdoor
heat exchanger 103 and the air drawn in, and fan motors 104 for rotationally driving
the fans 106.
[0057] In order to lead refrigerant piping from the outdoor unit 100 to the indoor units,
the outdoor unit 100 comprises a liquid line connector port 114 that is connected
to the outdoor heat exchanger 103, and a gas line connector port 115 that is connected
to the four way directional control valve 102. A liquid line shut off valve 116 and
a gas line shut off valve 117 are provided on the inner sides of each connector port.
[0058] A receiver 121 is provided in the outdoor unit 100, which temporarily stores surplus
refrigerant from the outdoor heat exchanger 103 when it functions as a condenser during
cooling operations. The receiver 121 is comprised of a liquid line connector 122 and
a gas line connector 123. The liquid line connector 122 is connected to liquid line
piping 131 between the outdoor heat exchanger 103 and the liquid line shut off valve
116, and the gas line connector 123 is connected to gas line piping 132 between the
four way directional control valve 102 and the gas line shut off valve 117.
[0059] A liquid line electric valve (EVL) 128 having a decompression function and a refrigerant
cut-off function is provided in the liquid line connector 122 on the receiver 121,
and a gas line electric valve (EVG) 129 is provided on the gas line connector 123
on the receiver 121.
[0060] An auxiliary heat exchanger 133 is provided in between the gas line electric valve
129 and a portion that connects to the gas line piping 132. As shown in Fig. 9, the
auxiliary heat exchanger 133 is constructed by placing an auxiliary cooling line 178
in the lowermost portion of the outdoor heat exchanger 103. A subcooling heat exchanger
134 is disposed on the liquid line outlet of the outdoor heat exchanger 103. As shown
in Fig. 9, the subcooling heat exchanger 134 can be constructed so that it is disposed
adjacent to the auxiliary heat exchanger 133, by positioning an SC cooling line 177
on the downwind side of the auxiliary cooling line 178 of the auxiliary heat exchanger
133.
[0061] A gas recovery capillary 130 for collecting gaseous refrigerant from the receiver
121 is provided, and is connected to the gas line piping 132 in between the four way
directional control valve 102 and the gas shut off valve 117.
[0062] A plurality of branching units 300A, 300B, etc. are connected to the liquid line
connector port 144 and the gas line connector port 115 on the outdoor unit 100. Because
each outdoor unit 300A, 300B, etc. are constructed identically, a description of the
branching unit 300A will be provided, and a description of the other branching units
will be omitted.
[0063] The branching unit 300A is comprised of an outdoor liquid line connector port 301
that is connected to the liquid line connector port 114 on the outdoor unit 100, and
an outdoor gas line connector port 303 that is connected to the gas line connector
port 115 on the outdoor unit 100. The branching unit 300A is comprised of a liquid
line branching circuit that branches on the inner side of the outdoor liquid line
connector port 301, and on the opposite end thereof, indoor liquid line connector
ports 302 for a number of connected indoor units are provided. Further, the branching
unit 300A is comprised of a gas line branching circuit that branches on the inner
side of the outdoor gas line connector port 303, and on the opposite end thereof,
indoor gas line connector ports 304 for a number of connected indoor units are provided.
Here, if we assume that there are three connected indoor units, then indoor liquid
line connector ports 302A, 302B, and 302C, and indoor gas line connector ports 304A,
304B, and 304C, will be provided. In addition, an electric valve 308 for use as a
bypass is provided between the outdoor liquid line connector port 301 and the outdoor
gas line connector port 303.
[0064] Electric valves 305A - 305C for decompressing the pressurized refrigerant that passes
therethrough, and liquid line thermistors 306A - 306C for detecting the temperature
of the refrigerant that passes therethrough, are each provided in the branching circuit
that spans between the outdoor liquid line connector port 301 inside the branching
unit 300A and each indoor liquid line connector port 302A - 302C. In addition, gas
line thermistors 307A - 307C for detecting the temperature of the refrigerant that
passes therethrough, are each provided in the branching circuit that spans between
the outdoor gas line connector port 303 inside the branching unit 300A and each indoor
gas line connector port 307A - 307C.
[0065] A plurality of indoor units 200 are connected to each branching unit 300A, 300B,
etc. As illustrated in the figure, three indoor units can be connected to each branching
unit 300A, 300B, etc., with the indoor units 200A - 200C connected to the branching
unit 300A, and the indoor units 200D - 200F connected to the branching unit 300B.
Each indoor unit 200A - 200F can be used either as an indoor unit for multi unit use,
or as an indoor unit for paired unit use. Here, the indoor unit 200A will be described
as an indoor unit for paired unit use.
[0066] The indoor device 200A is comprised of an indoor heat exchanger 201, and refrigerant
piping that is connected to this indoor heat exchanger 201 is lead to the outdoor
unit via a liquid line connector port 204 and a gas line connector port 205. Further,
a room temperature thermistor 202 for detecting the indoor room temperature, and an
indoor heat exchange thermistor 203 for detecting the temperature of the indoor heat
exchanger 201 are provided in the indoor unit 200A.
[0067] Note that when the indoor units connected to the branching units 300A, 300B are employed
as indoor units for multi unit use, there are times when a liquid line thermistor
for detecting the temperature of the refrigerant that flows inside the liquid line
piping is provided. In this situation, it is also possible to omit the liquid line
thermistor inside the branching units 300A, 300B.
[Refrigeration circuit control system]
[0068] In the refrigeration circuit described above, when the refrigerant capacity of the
indoor units is small (when the number of units operating is small, when the capacity
of the indoor heat exchangers used by the indoor units operating is small, etc.),
the discharge - intake bypass electric valve 142 is opened wide, a rise in the discharge
pressure during heating operations is prevented, and freezing of the low pressure
piping during cooling operations is prevented.
[0069] In addition, during heating operations, the overall system can be controlled with
the liquid line electric valve 128 by controlling the opening and closing thereof
when the gas line electric valve 129 is in the open state and there is surplus refrigerant
in the receiver 121. During cooling operations, the liquid line electric valve 128
distinguishes between the presence or absence of surplus refrigerant, and controls
the surplus refrigerant in the outdoor unit SC control.
[0070] Moreover, during heating operations, the gas line electric valve 129 stores surplus
refrigerant in the receiver 121 by opening to a predetermined aperture when it is
necessary to handle surplus refrigerant. During cooling operations, the gas line electric
valve 129 controls the overall system by controlling the opening and closing thereof
when the liquid line electric valve 128 is in the open state and there is surplus
refrigerant in the receiver 121.
[Control during heating operations]
[0071] A working example during heating operations is shown in Fig. 12.
[0072] In Fig. 12, it is determined in Step S1 whether or not there is not surplus refrigerant
in the refrigerant circuit, and whether or not there is no need to control capacity.
When there is no surplus refrigerant in the refrigerant circuit, and no need to control
capacity, the process moves to Step S2. In Step S2, the discharge - intake bypass
electric valve 142 is placed in the fully closed state, the liquid line electric valve
128 is placed in the fully open state, and the gas line electric valve 129 is placed
in the fully closed state.
[0073] As shown in Fig. 13, in the state in which there is no surplus refrigerant in the
refrigerant circuit and there is no need for capacity control, it is possible for
all of the connected indoor units 200A - 200F to operate.
[0074] In this situation, the outdoor heat exchanger 103 functions as a vaporizer, and each
indoor heat exchanger 201 in each indoor unit functions as a condenser. The electric
valves 305A - 305C, 305D - 305F that are inside the branching units 300A, 300B are
constructed such that the apertures thereof are respectively controlled in accordance
with the settings in each indoor unit, and refrigerant is distributed to each indoor
heat exchanger 201. Here, the electric valve 308 used as a bypass is in the fully
closed state.
[0075] Thus, the appropriate amount of refrigerant can be distributed to each indoor heat
exchanger 201 by means of the electric valves 305A - 305C, 305D - 305F disposed inside
the branching units 300A, 300B. Further, because surplus refrigerant is not produced
in the circuit, the receiver 121 is placed in the non-operational state, and control
of any of the discharge - intake bypass electric valve 142, the liquid line electric
valve 128, and the gas line electric valve 128 is not required.
[0076] In Step S3, it is determined whether or not there is surplus refrigerant in the refrigerant
circuit, and whether or not capacity control is unnecessary. When there is surplus
refrigerant in the refrigerant circuit, and capacity control is unnecessary, the process
moves to Step S4. At Step S4, the discharge - intake electric valve 142 is placed
in the fully closed position, the gas line electric valve 129 is opened a fixed amount,
and the liquid line electric valve 128 is controlled in response to the target discharge
line temperature.
[0077] For example, as shown in Fig. 14, in situations when only the indoor units 200A -
200C connected to the branching units 300A operate, it is possible for the outdoor
unit 100 to generate surplus refrigerant. In this situation, the refrigerant that
was condensed by the auxiliary heat exchanger 133 by opening the gas line electric
valve 129 a fixed amount, can be introduced and stored in the receiver 121. Because
the refrigerant that passes through the gas line electric valve 129 is condensed by
the auxiliary heat exchanger 133, the temperature thereof will not exceed the heat
resistant temperature of a standard electric valve, and it becomes possible to select
a gas line electric valve 129 that is inexpensive. In addition, by controlling the
aperture of the liquid line electric valve 128 in response to the target discharge
line temperature, the surplus refrigerant inside the receiver 121 can be adjusted,
and the overall system can be controlled by controlling the intake superheating.
[0078] At Step S5, it is determined whether or not there is surplus refrigerant in the refrigerant
circuit, and whether or not there is a need to control capacity. For example, when
there is surplus refrigerant in the refrigerant circuit, and the peak-cut control
is in the suspend zone even though the operational frequency of the compressor 101
is at the lower limit, it will be determined that that there is surplus refrigerant
and that capacity control is necessary, and the process will move to Step S6.
[0079] At Step S6, the discharge - intake electric valve 142 is maintained in the closed
state, and the aperture of the gas line electric valve 129 is controlled so that the
peak-cut control remains stable in a no-change zone. In addition, the aperture of
the liquid line electric valve 128 is controlled in response to the target discharge
line temperature.
[0080] For example, as shown in Fig. 15, when, from amongst the indoor units 200 connected
to the branching units 300A, 300B, only indoor unit 200C is operating, and this indoor
unit 200C is a large capacity indoor unit, it is possible for this type of operational
state to exist.
[0081] In this situation, the condensing capability of the auxiliary heat exchanger 133
is improved by opening the gas line electric valve 129, and the aperture of the gas
line electric valve 129 is controlled so that the peak-cut control remains stable
in a no-change zone. Because of this, refrigerant condensed via the auxiliary heat
exchanger 133 is introduced into the receiver 121, surplus refrigerant is collected
in the receiver 121, the high pressure refrigerant capacity is stabilized, and control
of the operational frequency of the compressor 101 is stabilized in the no-change
zone of the peak-cut control. In addition, because the gas line electric valve 129
is open, the control of the overall system (intake superheating control) occurs by
adjusting the surplus refrigerant inside the receiver 121 by controlling the aperture
of the liquid line valve 128 in response to the target discharge line temperature.
[0082] At Step S7, it is determined whether or not the peak-cut control is still in the
suspend zone even though the gas line electric valve 129 is completely open. When
the peak-cut control is in the suspend zone even though the number of operational
cycles of the compressor 101 is below a lower limit, and the peak-cut control is still
in the suspend zone even though the gas line electric valve 129 is completely open,
then the process moves to Step S8.
[0083] At Step S8, the aperture of the discharge - intake bypass electric valve 142 is controlled
so that the operational frequency of the compressor 101 remains stable in a no-change
zone of the peak-cut control. At this time. the gas line electric valve 129 is in
the fully open state, and the aperture of the liquid line electric valve 128 is controlled
in response to the target discharge line temperature.
[0084] For example, as shown in Fig. 16, when, from amongst the indoor units 200 that are
connected to the branching units 300A, 300B, only the indoor unit 200C is operating,
and the capacity of this indoor unit 200C is small, despite the fact that the gas
line electric valve 129 is completely open, it is possible for the peak-cut control
to be in the suspend zone. In this situation, capacity control occurs by controlling
the discharge - intake bypass electric valve 142, and stabilizing the operational
frequency of the compressor 101 in the no-change zone of the peak-cut control. In
addition, because the gas line electric valve 129 is open, the control of the overall
system (intake superheating control) occurs by adjusting the surplus refrigerant inside
the receiver 121 by controlling the aperture of the liquid line electric valve 128
in response to the target discharge line temperature.
[Control during cooling operations]
[0085] A working example during cooling operations is shown in Fig. 17.
[0086] In Fig. 17, it is determined at Step S11 whether or not there is surplus refrigerant
in the refrigerant circuit, and whether or not capacity control is unnecessary. When
it is determined that there is no surplus refrigerant in the refrigerant circuit,
and that capacity control is not necessary, the process moves to Step S12. At Step
S12, the discharge - intake bypass electric valve 142 is placed into the fully closed
state, the gas line electric valve 129 is placed in the fully open state, and the
liquid line electric valve 128 for conducting SC control by means of the subcooling
heat exchanger 134 is placed in the fully open state.
[0087] As shown in Fig. 18, in the state in which there is no surplus refrigerant in the
refrigerant circuit, and capacity control is not necessary, it is possible for all
of the connected indoor units 200A - 200F to be operating.
[0088] In this situation, the outdoor heat exchanger 103 functions as a condenser, and the
indoor heat exchangers 201 in each indoor unit function as vaporizers. The electric
valves 305A - 305C, 305D - 305F inside the branching units 300A, 300B are constructed
such that each respective aperture thereof is controlled in accordance with the settings
in each indoor unit, and refrigerant is distributed to each indoor heat exchanger
201. Here, the bypass electric valve 308 is placed in the fully open state.
[0089] Thus, refrigerant can be appropriately distributed to each indoor heat exchanger
201 by means of the electric valves 305A - 305C, 305D - 305F disposed inside the branching
units 300A, 300B. Further, because surplus refrigerant is not generated inside the
circuit, the receiver is placed into a non-operational state, and none of the discharge
- intake bypass electric valve 142, liquid line electric valve 128, or the gas line
electric valve 129 need be controlled.
[0090] In Step S13, it is determined whether or not there is surplus refrigerant in the
refrigerant circuit, and whether or not capacity control is unnecessary. When it is
determined that there is surplus refrigerant and capacity control is unnecessary,
the process moves to Step S14. At Step S14, the discharge - intake bypass electric
valve 142 is placed in the fully closed state, and the liquid line electric valve
128 is opened to a degree in which SC control by means of the subcooling heat exchanger
134 becomes possible (not fully open). Further, the aperture of the gas line electric
valve 129 is controlled, and the overall system is controlled (intake superheating
control), in order to place the discharge line temperature of the compressor 101 at
the desired temperature.
[0091] For example, as shown in Fig. 19, when only the indoor units 200A - 200C connected
to the branching unit 300A are operating, it is possible to generate surplus refrigerant
by means of the outdoor device 100. In this case, surplus refrigerant can be introduced
to and stored in the receiver 121 by opening the liquid line electric valve 128. In
addition, by controlling the aperture of the gas line electric valve 129 to correspond
with the target discharge line temperature, the surplus refrigerant inside the receiver
121 can be adjusted, and the overall system can be controlled due to the control of
intake superheating.
[0092] As shown in Fig. 20, when, from amongst the connected indoor units 200, only the
indoor unit 200C connected to the branching unit 300A is in the operational state,
and this indoor unit 200C has a large capacity, the identical operational state is
possible. In this case as well, the appropriate surplus refrigerant handling and system
control is make possible by means of the identical control shown in Fig. 19.
[0093] In Step S15, it is determined whether or not there is surplus refrigerant in the
refrigerant circuit, and whether or not capacity control is necessary. When it is
determined that there is surplus refrigerant and capacity control is necessary, the
process moves to Step S16. For example, when there are few indoor units operating,
there is a surplus of refrigerant, and the freezing prevention control is in the suspend
zone even though the operational frequency of the compressor 101 is at a lower limit,
it is determined that capacity control is necessary and the process moves to Step
S16.
[0094] At Step S16, the aperture of the discharge - intake bypass electric valve 142 is
controlled so that control of the number of cycles of the compressor 101 stabilizes
in an antifreeze control no-change zone. At this time, the aperture of the liquid
line electric valve 128 is controlled (not fully opened) in order to handle the surplus
refrigerant from the liquid line piping 131, and the liquid refrigerant is stored
in the receiver 121. In addition, because the liquid line electric valve 128 is open,
the amount of refrigerant inside the receiver 121 is adjusted by controlling the aperture
of the gas line electric valve 129 to correspond with the target discharge line temperature,
thereby controlling the overall system.
[0095] This type of operational state, for example, as shown in Fig. 21, will be attained
when, from amongst the connected indoor units 200C, only the indoor unit 200C is in
the operational state, and this indoor unit 200C has a small capacity. The aperture
of the electric valve 305C corresponding to the indoor heat exchanger 201 of the operational
indoor unit is controlled in response to the indoor temperature setting and the like,
and the other electric valves 305A, 305B, and the electric valves 305D - 305F inside
the branching unit 300B, are placed in the closed state. In this state, the aperture
of the discharge - intake bypass electric valve 142 can be controlled, the number
of cycles of the compressor 101 can be stabilized, surplus refrigerant can be handled
by adjusting the aperture of the liquid line electric valve 128, and the overall system
can be controlled by adjusting the aperture of the gas line electric valve 129.
[0096] At Step S17, it is determined whether or not the outside air temperature is lower
than a predetermined temperature. When the outside air temperature is below a predetermined
temperature, and when the liquid line electric valve 128 is placed in the fully closed
state, there is a danger that the pressure inside the receiver 121 will become lower
than the intake pressure of the compressor 101, and the liquid refrigerant stored
in the receiver 121 will not be able to drain out. In this situation, there is a danger
that a refrigerant shortage will occur in the refrigerant circuit. Thus, when it is
determined that this state will be created and that the outside air temperature is
lower than a predetermined temperature, the process moves to Step S18.
[0097] At Step S18, the pressure inside the receiver 121 is made higher than the pressure
inside the gas line piping 132 by opening the aperture of the liquid line electric
valve 128 to a predetermined degree, and the liquid refrigerant inside the receiver
121 is discharged into the auxiliary heat exchanger 133. Further, because the liquid
line electric valve 128 is open, by controlling the aperture of the gas line electric
valve 129, the target discharge line temperature can be controlled, and the overall
system can be controlled. Moreover, the intake pressure of the compressor 101 can
be increased by controlling the discharge - intake bypass electric valve 142 in order
to prevent freezing.
[0098] As shown in Fig. 22, even during times in which, from amongst the connected indoor
units 200, only the indoor unit 200C is operating, when the outside air temperature
is low, surplus refrigerant will not be generated. In this type of situation, it is
possible for the liquid line electric valve 128 to be placed in the fully closed state,
and liquid refrigerant not to be introduced into the receiver 121. However, when the
liquid line electric valve 128 is placed in the fully closed state, the temporarily
accumulated liquid refrigerant cannot be drained out. Thus, liquid refrigerant can
be discharged to the auxiliary heat exchanger 133, and the overall system can be controlled,
by opening the aperture of the liquid line electric valve 128 to a predetermined degree
and controlling the aperture of the gas line electric valve 129.
[0099] With regard to the antifreeze control, by controlling the aperture of the discharge
- intake bypass electric valve 142, the indoor unit vaporization temperature is stably
controlled in a no-change antifreeze control area.
[Operational control during defrosting]
[0100] When the outside air temperatures are low during the winter, there is a possibility
that the outdoor heat exchanger 103 of the outdoor device 100 will freeze. In this
situation, a defrost operation can be performed following cooling operations, and
the outdoor heat exchanger 103 can be thawed out.
[0101] Normally, as shown in Fig. 18, the discharge - intake bypass electric valve 142 is
placed in the fully closed state, the liquid line electric valve 128 is placed in
the fully closed state, the gas line electric valve is placed in the fully opened
state, the outside heat exchanger 103 is made to function as a condenser, and defrost
operations take place. When the defrost operation has run for a fixed period of time,
the outdoor heat exchanger 103 is presumed to be thawed out, and the defrost operation
ends. Heating operations will occur following this type of defrost operation, because
defrost operations generally occur in the wintertime.
[0102] In defrost operations, liquid refrigerant returns to the accumulator 105 because
the ventilation fan inside the indoor unit 200 stops, and because the indoor heat
exchanger 201 is not made to function as a vaporizer at the maximum level. In other
words, the liquid refrigerant accumulates and backs up. Thus, after the completion
of this type of defrost operation, it is difficult to promptly start heating operations,
and the startup capabilities of the heater worsen.
[0103] Because of this, the liquid line electric valve 128 is opened, and the aperture of
the gas line electric valve 129 is controlled so that the amount of refrigerant that
the compressor 101 takes in is equivalent thereto. Because of this, liquid refrigerant
can be introduced to and stored in the receiver 121, and will not accumulate and back
up in the accumulator 105. Thus, the startup capabilities of the heater after the
completion of defrost operations can be improved.
[Target discharge line temperature control]
[0104] As shown with the fourth to ninth embodiments, when the gas line electric valve 129
is provided in the gas line connector 123 of the receiver 121, by controlling the
opening and closing of the gas line electric valve 129, the surplus refrigerant in
the receiver 121 that is injected back into the compressor 101 as a liquid can be
adjusted. In this way, the discharge line temperature can be controlled. Further,
when the liquid line electric valve 128 is provided in the liquid line connector 122
of the receiver, and the gas line electric valve 129 is provided in the gas line connector
123 of the receiver, during both cooling and heating, the amount of liquid refrigerant
injected from the receiver 121 to the compressor 101 can be adjusted, and operational
efficiency can be improved.
[0105] Control of the target discharge line temperature will now be described in detail.
[0106] The target discharge line temperature is determined from the indoor heat exchanger
temperature and the outdoor heat exchanger temperature, and the apertures of the liquid
line electric valve 128 and the gas line electric valve 129 are adjusted so that the
actual discharge line temperature comes close to the target discharge line temperature.
[0107] For example, if we assume that the target discharge line temperature = α x condenser
temperature - β x vaporizer temperature + γ, then the amount of adjustment in the
liquid line electric valve 128 and the gas line electric valve 129 can be determined,
and each electric valve can be driven, from a table that corresponds the deviation
between the target discharge line temperature and the actual discharge line temperature
with the amount of change in the discharge temperature per unit of time. Here, the
table that corresponds the deviation between the target discharge line temperature
and the actual discharge line with the amount of change in the discharge temperature
per unit of time can be a fuzzy table.
[0108] In fact, because the fluctuation in the condenser temperature and the vaporizer temperature
is large due to disturbances, by using the average value of the previous target discharge
line temperature and the current target discharge line temperature, fluctuation in
the target discharge line temperature can be minimized.
[0109] An example of the control of the target discharge line temperature by controlling
the apertures of the liquid line electric valve 128 and the gas line electric valve
129 connected to the receiver 121 of the outside unit 100 will be described based
upon the flow charts shown in Figs. 23 and 24.
[0110] In Step S21, it is determined whether or not control condition ① is satisfied in
order to begin target discharge line temperature control by means of the outside electric
valves.
-BEGIN control condition ① determination flow
[0111] Control condition ① is determined based upon the flow chart shown in Fig. 25.
[0112] At Step S41, it is determined whether or not the air conditioner is operating normally.
If the air conditioner is in normal cooling operations or normal heating operations,
then the process moves to Step S44, and if not, then the process moves to Step S42.
[0113] At Step S42, it is determined whether or not the air conditioner is in a test mode.
When the air conditioner is in cooling test operation or in heating test operation,
the process moves to Step S44, and if not, the process moves to Step S43.
[0114] At Step S43, it is determined whether or not the air conditioner is in defrost preheating
operation. When the air conditioner is in defrost preheating operation, the process
moves to Step S44, and if not, the process moves to Step S49.
[0115] At Step S44, it is determined whether or not the electric valves 305 inside the branching
unit 300 are being controlled when the room in which heating or cooling is occurring
changes. When the electric valves 305 inside each branching unit 300 are being controlled
when the room in which heating or cooling is taking place is changed immediately after
any of the indoor units 200 begin operating, or immediately after any of the indoor
units 200 cease operation, then the process moves to Step S49, and if not, the process
moves to Step S45.
[0116] At Step S45, it is determined whether or not control is occurring during a change
in the operational frequency. When the air conditioning load changes in the indoor
units 200 during operation, and when control is occurring during a change in the number
of operational cycles of the compressor 101, the process moves to Step S49, and if
not, the process moves to Step S46.
[0117] At Step S46, it is determined whether or not discharge line high temperature control
is occurring. When the discharge temperature of the compressor 100 is above a predetermined
temperature, the apertures of the liquid line valve 128 and the gas line valve 129
open a fixed amount, and discharge line high temperature control occurs such that
the liquid refrigerant inside the receiver 121 backs up into the accumulator 103.
When this type of discharge line high temperature control occurs, the process moves
to Step S49, and if it does not, the process moves to Step S47.
[0118] As Step S47, it is determined whether or not discharge line thermistor removal control
is occurring. In situations in which the discharge temperature detected by the discharge
line thermistor 109 does not rise above a predetermined temperature, even though the
air conditioner runs for a fixed period of time from startup, there is a possibility
that the discharge line thermistor 109 has been removed, or that it is due to environmental
conditions, such as the outside air temperature being unusually cold. When the latter
is true, because it is not necessary to take the system down and inspect it, the discharge
temperature will be estimated from other temperature sensors and the like, a test
operation will be run, and it will be confirmed that the discharge line thermistor
109 has in fact not been removed. When this operational control instigates the discharge
line thermistor omission control, and this discharge line thermistor removal control
occurs, the process moves to Step S49. If not, the process moves to Step S48.
[0119] At Step S48, the apertures of the electric valves 128, 129 inside the outdoor device
100 are controlled, the target discharge line temperature control mode is set, and
at Step S49, a mode in which this control does not occur is set.
-END Control condition ① determination flow-
[0120] At Step S21, when control condition ① is satisfied, and the target discharge line
temperature control mode has been set by means of the outdoor unit electric valves,
the process moves to Step S23. When the mode in which this control does not occur
is set, the process moves to Step S22.
[0121] At Step S22, a flag that shows whether or not a sampling timer has started for the
first time is set initially to be on, and the process returns to the overall control
main routine.
[0122] In Step S23, the sampling timer is started. This sampling timer counts the sampling
timing of the discharge line temperature data in order to control the discharge line
temperature. At Step S24, it is determined whether or not the sampling time counted
exceeds a predetermined sampling time TTHS1. This sampling time TTHS1 can be set in
a range between 0 to 255 x 100 msec. For example, it can be set at 20 seconds.
[0123] In Step S24, when it is determined that the count value of the sampling timer exceeds
the sampling time TTHS1, the process moves to Step S25. At Step S25, the target discharge
line temperature DOSET is determined.
-BEGIN Target discharge temperature DOSET-
[0124] At the time the target discharge temperature DOSET is determined, as described above,
the average value of the previous target discharge line temperature and the current
target discharge line temperature is used (temporary target discharge line temperature)
in order to minimize fluctuations due to disturbances. The method of determining the
temporary target discharge line temperature DOSETN is shown in Fig. 26 and 27.
--BEGIN Temporary target discharge line temperature DOSETN during cooling operations--
[0125] First, the determination of the temporary discharge line temperature DOSETN during
cooling operations can be performed by means of the flow chart in Fig. 26.
[0126] At Step S51, it is determined whether or not the desired operational frequency FMK
for the compressor 101 exceeds a condensing temperature correction coefficient switching
frequency FEVFDC for calculating the target discharge line temperature during cooling
operations. When the desired frequency FMK > FEVFDC, then the process moves to Step
S52. If not, the process moves to Step S53.
[0127] At Step S52, a condensing temperature correction coefficient KEVFD is set to be a
condensing temperature correction coefficient KEVFDC for calculating the target discharge
line temperature during high frequency cooling. At Step S53, the condensing temperature
correction coefficient KEVFDC is set to be a condensing temperature correction coefficient
KEVFDC1 for calculating the target discharge line temperature during low frequency
cooling.
[0128] At Step S54, it is determined whether or not the lowest temperature of a indoor heat
exchanger operating in a room DCMNU is equal to or above a vaporizing temperature
threshold for calculating the target discharge line temperature during cooling DZC.
When the lowest temperature of a indoor heat exchanger operating in a room DCMNU is
equal to or above the vaporizing temperature threshold for calculating the target
discharge line temperature during cooling DZC, the process moves to Step S55. If not,
the process moves to Step S56.
[0129] At Step S55, the lowest temperature of a indoor heat exchanger operating in a room
DCMNU is set as a vaporizing temperature DZ. At Step S56, the current vaporizing temperature
DZ is set to be the vaporizing temperature threshold for calculating the target discharge
line temperature DZC.
[0130] At Step S57, based on the number of indoor units 200 currently operating, intercept
points DSHC are established for calculating the target discharge line temperature
during cooling. An intercept point DSHC1 for use when one room is being cooled, an
intercept point DSHC2 for use when two rooms are being cooled, and an intercept point
DSHC3 for use when three rooms are being cooled, are established in predetermined
memory regions. Any of these values are set as the value of DSHC in accordance with
the operating conditions at the time.
[0131] At Step S58, it is determined whether or not the aperture EVP of the discharge -
intake electric valve 142 is equal to or greater than a predetermined value EVPMIN.
When the aperture EVP of the discharge - intake electric valve 142 is equal to or
greater than the predetermined value EVPMIN, then the process moves to Step S59, and
if not, the process moves to Step S60.
[0132] At Step S59, a target discharge line temperature correction value DEVP is set to
be a target discharge line temperature value during cooling operations capacity control
DEVPC. At Step S60, the value of the target discharge line temperature correction
value DEVP is set to zero.
[0133] At Step S61, the value of the temporary target discharge line temperature DOSETN
is calculated from the condensing temperature correction coefficient for calculating
the target discharge line temperature KEVFD, the outdoor heat exchanger temperature
DE, a vaporizing temperature correction coefficient for calculating the target discharge
line temperature during cooling KEVFDEC, the minimum indoor heat exchanger temperature
(vaporizing temperature) DZ, the intercept points for calculating the target discharge
line temperature during cooling DSHC, and the target discharge line temperature correction
value DEVP. Here, DOSETN = KEVFD x DE - KEVFDEC x DZ + DSHC - DEVP.
--END Temporary target discharge line temperature during cooling operations DOSTN--
--BEGIN Temporary target discharge line temperature during heating operations DOSETN--
[0134] Next, the method of calculating a temporary target discharge line temperature during
heating operations DOSETN will be described based upon the flow chart in Fig. 27.
[0135] At Step S71, it is determined whether or not a desired operational frequency FMK
for the compressor 101 exceeds a condensing temperature correction coefficient switching
frequency for calculating the target discharge line temperature during heating operations
FEVFDW. When the desired frequency FMK > FEVFDW, then the process moves to Step S72.
If not, the process moves to Step S73.
[0136] At Step S72, a condensing temperature correction coefficient KEVFD is set to be a
condensing temperature correction coefficient for calculating the target discharge
line temperature during high frequency heating KEVFDW. At Step S73, the condensing
temperature correction coefficient KEVFD is set to be a condensing temperature correction
coefficient for calculating the target discharge line temperature during low frequency
heating KEVFDW1.
[0137] At Step S74, it is determined whether or not the outdoor heat exchanger temperature
DE is equal to or above a vaporizing temperature threshold for calculating the target
discharge line temperature during heating DZW. When the outdoor heat exchanger temperature
DE is equal to or above the vaporizing temperature threshold for calculating the target
discharge line temperature during heating DZW, the process moves to Step S75. If not,
the process moves to Step S76.
[0138] At Step S75, the lowest temperature of a indoor heat exchanger operating in a room
DCMNU is set as a vaporizing temperature DZ. At Step S76, the vaporizing temperature
DZ is set to be the vaporizing temperature threshold for calculating the target discharge
line temperature during heating DZW.
[0139] At Step S77, based on outdoor temperature DOA, an intercept point for calculating
the target discharge line temperature during heating DSHW is established. When the
outdoor temperature DOA is smaller than an intercept point switching outside air temperature
for calculating the target discharge line temperature during low temperature heating
DOASH1, the intercept point for calculating the target discharge line temperature
during heating DSHW is set as the intercept point for calculating the target discharge
line temperature during low temperature heating DSHW1. When the outdoor temperature
DOA is equal to or greater than the intercept point switching outside air temperature
for calculating the target discharge line temperature during low temperature heating
DOASH1, and the outdoor temperature DOA is under an intercept point switching outside
air temperature for calculating the target discharge line temperature during high
temperature heating DOASH2, the value of the intercept point for calculating the target
discharge line temperature during heating DSHW is set to be an intercept point for
calculating the target discharge line temperature during moderate temperature heating
DSHW2. When the outdoor temperature DOA is equal to or greater than the intercept
point switching outside air temperature for calculating the target discharge line
temperature during high temperature heating DOASH2, the value of the intercept point
for calculating the target discharge line temperature during heating DSHW is set to
be an intercept point for calculating the target discharge line temperature during
high temperature heating DSHW3.
[0140] At Step S78, it is determined whether or not the aperture EVP of the discharge -
intake electric valve 142 is equal to or greater than a predetermined value EVPMIN.
When the aperture EVP of the discharge - intake electric valve 142 is equal to or
greater than the predetermined value EVPMIN, then the process moves to Step S79, and
if not, the process moves to Step S80.
[0141] At Step S79, a target discharge line temperature correction value DEVP is set to
be a target discharge line temperature value during heating operations capacity control
DEVPW. At Step S80, the value of the target discharge line temperature correction
value DEVP is set to zero.
[0142] At Step S81, the value of the temporary target discharge line temperature DOSETN
is calculated from the condensing temperature correction coefficient for calculating
the target discharge line temperature KEVFD, the maximum indoor heat exchanger temperature
DCMXT, a vaporizing temperature correction coefficient for calculating the target
discharge line temperature during heating KEVFDEW, the vaporizing temperature DZ,
the intercept point for calculating the target discharge line temperature during heating
DSHC, and the target discharge line temperature correction value DEVP. Here, DOSETN
= KEVFD x DCMXT - KEVFDEW x DZ + DSHW - DEVP.
--END Temporary target discharge line temperature during heating operations DOSETN-
[0143] After the temporary discharge line temperature DOSETN is determined by the method
shown in the flow charts in Fig. 26 and Fig. 27, another method of calculating the
target discharge line temperature DOSET is shown in Fig. 28.
[0144] At Step S91, it is determined whether or not the first time flag is on. Because a
target discharge line temperature control mode is set by the outdoor unit electric
valves, the first time flag indicates the first time the value of the sampling timer
has exceeded the sampling time TTHS1. When the first time flag is on, the process
moves to Step S92, and when it is not, the process moves to Step S93.
[0145] At Step S92, the target discharge line temperature DOSET is set as the temporary
target discharge line temperature DOSETN. In addition, the previous target discharge
line temperature DOSETZ is set as the temporary target discharge line temperature.
DOSET = DOSETN
DOSETZ = DOSETN
[0146] At Step S93, the average of the temporary target discharge line temperature DOSETN
and the previous target discharge line temperature DOSETZ is calculated, and the target
discharge line temperature DOSET is set to this value. In addition, the previous target
discharge line temperature DOSETZ is set to the temporary target discharge line temperature.
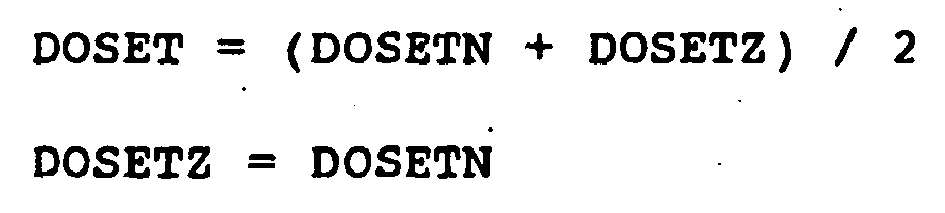
[0147] Note that in each operational mode, the largest and smallest values for the discharge
line temperature during normal operations are considered, and are set as the upper
and lower limits for the target discharge line temperature DOSETN. As described above,
the target discharge line temperature DOSET requested is controlled so as to be within
these upper and lower limits.
-END Target discharge line temperature DOSET-
[0148] At Step S26, the current discharge line temperature DO is detected. The current discharge
line temperature DO can be detected by reading the discharge line temperature thermistor
109. At Step S27, the variation in the discharge line temperature EDO is calculated.
Here, the discharge line temperature variation EDO = the target discharge line temperature
DOSET - the discharge line temperature DO. As Step S28, amount of change in the discharge
line temperature dDO is calculated. Here, the amount of change in the discharge line
temperature = the previous discharge line temperature DOZ - the current discharge
line temperature DO.
[0149] At Step S29, the discharge line temperature EDO and amount of change in the discharge
line temperature dDO is used to search the fuzzy table, and the value for the amount
of change in the electric valves PEVHN is determined.
[0150] As Step S32, it is determined whether or not the air conditioner is in cooling operation
mode. When the air conditioner is in cooling operation mode, the process moves to
Step S33, and if not, the process moves to Step S34. At Step S33, the amount of change
in the electric valves PEVHN is corrected by means of a cooling correction coefficient
KPOTD.

[0151] At Step S34, the electric valve cumulative pulse PHNA is calculated based upon the
amount of change in the electric valves PEVHN.

[0152] At Step S35, an integral part and fractional part of the electric valve cumulative
pulse PHNA are each calculated, with the integral part set as PHN and the fractional
part set as PHNA.
[0153] As Step S36, it is determined whether or not the control condition ② has been satisfied.
-BEGIN Control condition ②-
[0154] As Step S101, it is determined whether or not the operational mode is set to cooling
operations. When the operational mode is set to cooling operations, the process moves
to Step S102, and if not, the process proceeds in the direction of D (Step S37 of
Fig. 4).
[0155] At Step S102, it is determined whether or not an indicator signal has been received
from the connected branching unit 300 that indicates that the apertures of the electric
valves 305 are at a minimum, which corresponds to the air conditioning in all rooms
being halted. When an indicator signal has been received from the connected branching
unit 300 that indicates that the apertures of the electric valves 305 are at a minimum,
which corresponds to the air conditioning in all rooms being halted, the process proceeds
in the direction of C (Step S38 of Fig. 24). When the conditions of Step S102 are
not fulfilled, then the process moves to Step S103.
[0156] At Step S103, it is determined whether or not a gas line electric valve aperture
EVG is equal to or larger than a predetermined valve EVGMIN. When the gas line electric
valve aperture EVG is equal to or larger than the predetermined valve EVGMIN, the
process proceeds in the direction of C (Step S38 of Fig. 24), and if not, it proceeds
in the direction of D (Step S37 of Fig. 24).
-END Control condition ②-
[0157] As Step S37, the desired apertures of the electric valves are changed. When in the
cooling operation mode, the gas line electric valve aperture EVG = EVG - an electric
valve change pulse PHN, and when in the heating operation mode, the liquid line electric
valve aperture EVL = EVL - PHN.
[0158] At Step S38, the desired aperture of the gas line electric valve is changed. Here,
the gas line electric valve aperture EVG = EVG + the electric valve change pulse PHN.
[0159] At Step S39, the first time flag is placed in the off state, the sampling timer is
reset, and the process moves to Step S21.
[0160] In this way, it becomes possible to continuously control the liquid injection amount,
and the appropriate discharge line temperature of the compressor 101 can be set by
controlling the apertures of the liquid line electric valve 128 and the gas line electric
valve 129 connected to the receiver 121. In particular, by controlling not only the
gas line electric valve 129, but also the liquid line electric valve 128, the liquid
injection amount can be appropriately controlled during not only cooling but also
during heating, and it becomes possible to increase reliability and operational efficiency
regardless of the operational mode.
INDUSTRIAL APPLICABILITY
[0161] In the air conditioner refrigerant circuit according to the present invention, a
refrigerant circuit can be provided that minimizes the occurrence of refrigerant high-low
drift even though a plurality of indoor units are placed in different vertical intervals,
and in which cost reductions can be provided.
[0162] In addition, with the air conditioner of the present invention, by controlling the
refrigerant opening and closing means connected to the receiver, the discharge line
temperature of the compressor can be controlled, and reliability and operational efficiency
can be improved.