[0001] L'invention concerne la fabrication de tôles laminées à froid et recuites d'aciers
dits « dual-phase » présentant une très haute résistance et une aptitude à la déformation
pour la fabrication de pièces par mise en forme, en particulier dans l'industrie automobile.
Les aciers dual-phase, dont la structure comprend de la martensite, éventuellement
de la bainite, au sein d'une matrice ferritique, ont connu un grand développement
car ils allient une résistance élevée à des possibilités importantes de déformation.
A l'état de livraison, leur limite d'élasticité est relativement basse comparée à
leur résistance à la rupture, ce qui leur confère un rapport (limite d'élasticité/résistance)
très favorable lors des opérations de formage. Leur capacité de consolidation est
très grande, ce qui permet une bonne répartition des déformations dans le cas d'une
collision et l'obtention d'une limite d'élasticité nettement plus importante sur pièce
après formage. On peut réaliser ainsi des pièces aussi complexes qu'avec des aciers
conventionnels, mais avec des propriétés mécaniques plus élevées, ce qui autorise
une diminution d'épaisseur pour tenir un cahier des charges fonctionnel identique.
De la sorte, ces aciers sont une réponse efficace aux exigences d'allègement et de
sécurité des véhicules. Dans le domaine des tôles laminées à chaud (d'épaisseur allant
par exemple de 1 à 10mm) ou laminées à froid (épaisseur allant par exemple de 0,5
à 3 mm), ce type d'aciers trouve notamment des applications pour des pièces de structures
et de sécurité pour les véhicules automobile, telles que les traverses, longerons,
pièces de renfort, ou encore les voiles de roues.
[0002] Les exigences récentes d'allègement et de réduction de la consommation d'énergie
ont conduit à une demande accrue d'aciers dual-phase à très haute résistance, c'est
à dire dont la résistance mécanique R
m est comprise entre 980 et 1100MPa. Outre ce niveau de résistance, ces aciers doivent
présenter une bonne soudabilité et une bonne aptitude à la galvanisation en continu
au trempé. Ces aciers doivent également présenter une bonne aptitude au pliage.
[0003] La fabrication d'aciers Dual Phase à haute résistance est par exemple décrite dans
le document
EP1201780 A1 relatif à des aciers de composition : 0,01-0,3%C. 0,01-2%Si, 0,05-3%Mn, <0,1%P, <0,01%S,
0,005-1%Al, dont la résistance mécanique est supérieure à 540MPa, qui présentent une
bonne résistance à la fatigue et une aptitude à l'expansion de trou. Cependant, la
plupart des exemples présentés dans ce document révèlent une résistance inférieure
à 875 MPa. Les rares exemples dans ce document allant au delà de cette valeur sont
relatifs à des aciers à forte teneur en carbone (0,25 ou 0,31%) pour lesquelles l'aptitude
au soudage et à l'expansion de trou n'est pas suffisante.
[0004] Le document
EP0796928A1 décrit par ailleurs des aciers Dual Phase laminés à froid dont la résistance est
supérieure à 550MPa, de composition 0,05-0,3%C, 0,8-3%Mn, 0,4-2,5%Al, 0,01-0,2%Si.
La matrice ferritique contient de la martensite, de la bainite et/ou de l'austénite
résiduelle. Les exemples présentés montrent que la résistance ne dépasse pas 660MPa,
même pour une teneur en carbone élevée (0,20-0,21 %)
[0005] Le document
JP11350038 décrit des aciers Dual Phase dont la résistance est supérieure à 980MPa, de composition
0,10-0,15%C, 0,8-1,5%Si, 1,5-2,0%Mn, 0,01-0,05%P, moins de 0,005%S, 0,01-0,07%Al en
solution, moins de 0,01%N, contenant en outre un ou plusieurs éléments : 0,001-0,02%Nb,
0,001-0,02%V, 0,001-0,02%Ti. Cette résistance élevée est cependant obtenue au prix
d'une addition importante de silicium qui permet certes la formation de martensite,
mais peut néanmoins conduire à la formation d'oxydes superficiels qui détériorent
la revêtabilité au trempé.
[0006] Le but de la présente invention est de proposer un procédé de fabrication de tôles
d'aciers dual-phase à très haute résistance, laminées à froid, nues ou revêtues, ne
présentant pas les inconvénients mentionnés précédemment.
[0007] Elle vise à mettre à disposition des tôles d'acier Dual Phase présentant une résistance
mécanique comprise entre 980 et 1100 MPa conjointement avec un allongement à rupture
supérieur à 9% et une bonne aptitude au formage, notamment au pliage
[0008] L'invention vise également à mettre à disposition un procédé de fabrication dont
de faibles variations des paramètres n'entraînent pas de modifications importantes
de la microstructure ou des propriétés mécaniques.
[0009] L'invention vise également à mettre à disposition une tôle d'acier aisément fabricable
par laminage à froid, c'est à dire dont la dureté après l'étape de laminage à chaud
est limitée de telle sorte que les efforts de laminage restent modérés lors de l'étape
de laminage à froid.
[0010] Elle vise également à disposer d'une tôle d'acier apte au dépôt d'un revêtement métallique,
en particulier par galvanisation au trempé selon les procédés usuels.
[0011] Elle vise encore à disposer d'un acier présentant une bonne aptitude au soudage au
moyen des procédés d'assemblage usuels tels que le soudage par résistance par points.
[0012] L'invention vise également à mettre à disposition un procédé de fabrication économique
en évitant l'addition d'éléments d'alliage coûteux.
[0013] A cet effet, l'invention a pour objet une tôle d'acier Dual Phase laminée à froid
et recuite de résistance comprise entre 980 et 1100MPa, d'allongement à rupture supérieur
à 9 %, dont la composition comprend, les teneurs étant exprimées en poids : 0,055%
≤C ≤ 0,095%, 2% ≤Mn ≤2,6%, 0,005% ≤ Si≤ 0,35%, S≤0,005%, P ≤0,050%, 0,1 ≤Al ≤ 0,3%,
0,05% ≤Mo ≤0,25%, 0,2%≤Cr≤0,5%, étant entendu que Cr+2Mo≤0.6%, Ni≤ 0,1%, 0,010≤Nb
≤0,040%, 0,010≤Ti ≤0,050%, 0,0005 ≤B ≤0,0025%, 0,002%≤N≤0,007%, le reste de la composition
étant constitué de fer et d'impuretés inévitables résultant de l'élaboration.
[0014] Préférentiellement, la composition de l'acier contient, la teneur étant exprimée
en poids : 0,12% ≤Al≤0.25%.
[0015] Selon un mode préféré, la composition de l'acier contient, la teneur étant exprimée
en poids : 0,10% ≤ Si ≤ 0,30%.
[0016] La composition de l'acier contient à titre préférentiel :0.15% ≤ Si ≤ 0,28%.
[0017] Selon un mode préféré, la composition contient : P ≤0,015%.
[0018] La microstructure de la tôle contient préférentiellement 35 à 50% de martensite en
proportion surfacique.
[0019] Selon un mode particulier, le complément de la microstructure est constitué de 50
à 65% de ferrite en proportion surfacique.
[0020] Selon un autre mode particulier, le complément de la microstructure est constitué
de 1 à 10% de bainite et de 40 à 64% de ferrite en proportion surfacique.
[0021] La fraction surfacique de ferrite non recristallisée rapportée à la totalité de la
phase ferritique est préférentiellement inférieure ou égale à 15%.
[0022] La tôle d'acier possède préférentiellement un rapport entre sa limite d'élasticité
R
e et sa résistance R
m tel que : 0,6≤Re/R
m ≤0,8.
[0023] Selon un mode particulier, la tôle est galvanisée en continu.
[0024] Selon un autre mode particulier, la tôle comporte un revêtement galvannealed.
[0025] L'invention a également pour objet un procédé de fabrication d'une tôle d'acier Dual
Phase laminée à froid et recuite
caractérisé en ce qu'on approvisionne un acier de composition selon l'une quelconque des caractéristiques
ci-dessus, puis
- on coule l'acier sous forme de demi-produit, puis
- on porte le demi-produit à une température 1150°C≤TR≤1250°C, puis
- on lamine à chaud le demi-produit avec une température de fin de laminage TFL ≥Ar3 pour obtenir un produit laminé à chaud, puis
- on bobine le produit laminé à chaud à une température 500°C ≤Tbob≤ 570°C, puis on décape le produit laminé à chaud, puis on effectue un laminage à
froid avec un taux de réduction compris entre 30 et 80% pour obtenir un produit laminé
à froid, puis
- on chauffe le produit laminé à froid à une vitesse 1°C/s≤VC≤5°C/s jusqu'à une température de recuit TM telle que: Ac1+40°C≤TM≤Ac3-30°C où l'on effectue un maintien pendant une durée : 30s≤tM≤300s de façon à obtenir un produit chauffé et recuit avec une structure comprenant
de l'austénite, puis
- on refroidit le produit jusqu'à une température inférieure à la température Ms avec une vitesse V suffisante pour que l'austénite se transforme totalement en martensite.
[0026] L'invention a également pour objet un procédé de fabrication d'une tôle d'acier Dual
Phase laminée à froid, recuite et galvanisée
caractérisé en ce qu'on approvisionne le produit chauffé et recuit avec une structure comprenant de l'austénite
selon la caractéristique ci-dessus puis,
- on refroidit le produit chauffé et recuit avec une vitesse VR suffisante pour éviter la transformation de l'austénite en ferrite, jusqu'à atteindre
une température proche de la température TZn de galvanisation au trempé, puis
- on galvanise en continu le produit par immersion dans un bain de zinc ou d'alliage
de Zn à une température 450°C≤TZn≤480°C pour obtenir un produit galvanisé, puis
- on refroidit le produit galvanisé jusqu'à la température ambiante avec une vitesse
V'R supérieure à 4°C/s pour obtenir une tôle d'acier laminée à froid, recuite et galvanisée.
[0027] L'invention a également pour objet un procédé de fabrication d'une tôle d'acier Dual
Phase laminée à froid et galvannealed,
caractérisé en ce qu'on approvisionne le produit chauffé et recuit avec une structure comprenant de l'austénite
selon la caractéristique ci-dessus, puis,
- on refroidit le produit chauffé et recuit avec une vitesse VR suffisante pour éviter la transformation de ladite austénite en ferrite, jusqu'à
atteindre une température proche de la température TZn de galvanisation au trempé, puis
- on galvanise en continu le produit par immersion dans un bain de zinc ou d'alliage
de Zn à une température 450°C≤TZn≤480°C pour obtenir un produit galvanisé, puis
- on chauffe le produit galvanisé à une température TG comprise entre 490 et 550°C pendant une durée tG comprise entre 10 et 40 s pour obtenir un produit galvannealed, puis
- on refroidit le produit galvannealed jusqu'à la température ambiante à une vitesse
V"R supérieure à 4°C/s, pour obtenir une tôle d'acier laminée à froid et galvannealed.
[0028] L'invention a également pour objet un procédé de fabrication selon l'une des caractéristiques
ci-dessus,
caractérisé en ce que la température T
M est comprise entre 760 et 830°C.
[0029] Selon un mode particulier, la vitesse de refroidissement V
R est supérieure ou égale à 15°C/s.
[0030] L'invention a également pour objet l'utilisation d'une tôle d'acier selon l'une quelconque
des caractéristiques ci-dessus, ou fabriquée par un procédé selon l'une quelconque
des caractéristiques ci-dessus, pour la fabrication de pièces de structures ou de
sécurité pour véhicules automobiles.
[0031] D'autres caractéristiques et avantages de l'invention apparaîtront au cours de la
description ci-dessous, donnée à titre d'exemple et faite en référence aux figures
annexées ci-jointes selon lesquelles :
- La figure 1 présente un exemple de microstructure d'une tôle d'acier selon l'invention
- Les figures 2 et 3 présentent des exemples de microstructure de tôles d'acier non
conforme à l'invention.
[0032] L'invention va maintenant être décrite de façon plus précise, mais non limitative,
en considérant ses différents éléments caractéristiques :
[0033] En ce qui concerne la composition chimique de l'acier, le carbone joue un rôle important
sur la formation de la microstructure et sur les propriétés mécaniques : au-dessous
de 0,055% en poids, la résistance devient insuffisante. Au-delà de 0,095%, un allongement
de 9% ne peut plus être garanti. La soudabilité est également réduite.
[0034] Outre un effet durcissant par solution solide, le manganèse est un élément qui augmente
la trempabilité et réduit la précipitation de carbures. Une teneur minimale de 2%
en poids est nécessaire pour obtenir les propriétés mécaniques désirées. Cependant,
au-delà de 2,6%, son caractère gammagène conduit à la formation d'une structure en
bandes trop marquée.
[0035] Le silicium est un élément participant à la désoxydation de l'acier liquide et au
durcissement en solution solide. Cet élément joue en outre un rôle important dans
la formation de la microstructure en empêchant la précipitation des carbures et en
favorisant la formation de martensite qui entre dans la structure des aciers Dual
Phase. Il joue un rôle effectif au-delà de 0,005%. Une addition de silicium en quantité
supérieure à 0,10%, préférentiellement supérieure à 0,15%, permet d'atteindre les
plus hauts niveaux de résistance visés par l'invention. Cependant, une augmentation
de la teneur en silicium dégrade l'aptitude au revêtement au trempé en favorisant
la formation d'oxydes adhérents à la surface des produits : sa teneur doit être limitée
à 0,35% en poids, et préférentiellement à 0,30% pour obtenir une bonne revêtabilité.
En outre, le silicium diminue la soudabilité : une teneur inférieure à 0,28% permet
d'assurer simultanément une très bonne aptitude au soudage ainsi qu'une bonne revêtabilité.
[0036] Au-delà d'une teneur en soufre de 0,005%, la ductilité est réduite en raison de la
présence excessive de sulfures tels que MnS qui diminuent l'aptitude à la déformation,
en particulier lors d'essais d'expansion de trou.
[0037] Le phosphore est un élément qui durcit en solution solide mais qui diminue la soudabilité
par points et la ductilité à chaud, particulièrement en raison de son aptitude à la
ségrégation aux joints de grains ou à la co-ségrégation avec le manganèse. Pour ces
raisons, sa teneur doit être limitée à 0,050%, et préférentiellement à 0,015% afin
d'obtenir une bonne aptitude au soudage par points.
[0038] L'aluminium joue un rôle important dans l'invention en empêchant la précipitation
des carbures et en favorisant la formation des constituants martensitiques au refroidissement.
Ces effet sont obtenus lorsque la teneur en aluminium est supérieure à 0,1%, et préférentiellement
lorsque la teneur en aluminium est supérieure à 0,12%.
[0039] Sous forme d'AlN, l'aluminium limite la croissance du grain lors du recuit après
laminage à froid. Cet élément est aussi utilisé pour la désoxydation de l'acier liquide
en quantité usuellement inférieure à environ 0,050%. On considère en effet habituellement
que des teneurs plus importantes accroissent l'érosion des réfractaires et le risque
de bouchage des busettes. En quantité excessive, l'aluminium diminue la ductilité
à chaud et augmente le risque d'apparition de défauts en coulée continue. On cherche
également à limiter les inclusions d'alumine, en particulier sous forme d'amas, dans
le but de garantir des propriétés d'allongement suffisantes. Or les inventeurs ont
mis en évidence, en liaison avec les autres éléments de la composition, qu'une quantité
d'aluminium allant jusqu'à 0,3% en poids pouvait être ajoutée sans effet néfaste vis-à-vis
des autres propriétés requises, en particulier vis-à-vis de l'aptitude à la déformation,
et permettait également d'obtenir les propriétés microstructurales et mécaniques visées.
Au delà de 0,3%, il existe un risque d'interaction entre le métal liquide et le laitier
lors de la coulée continue, qui conduit à l'apparition éventuelle de défauts. Une
teneur en aluminium allant jusqu'à 0,25% en poids permet d'assurer la formation d'une
microstructure fine sans îlots martensitiques de grande taille qui joueraient un rôle
néfaste sur la ductilité.
[0040] Les inventeurs ont montré que, d'une manière surprenante, il était possible d'obtenir
un niveau de résistance élevé, compris entre 980 et 1100MPa, même en dépit de la limitation
des additions d'aluminium et de silicium. Ceci est obtenu par la combinaison particulière
des éléments d'alliage ou de microalliage selon l'invention en particulier grâce aux
additions de Mo, Cr, Nb,Ti, B.
[0041] En quantité supérieure à 0,05% en poids, le molybdène joue un rôle efficace sur la
trempabilité et retarde le grossissement de la ferrite et l'apparition de la bainite.
Cependant, une teneur supérieure à 0,25% accroît excessivement le coût des additions.
[0042] En quantité supérieure à 0,2%, le chrome, par son rôle sur la trempabilité, contribue
également à retarder la formation de ferrite proeutectoïde. Au delà de 0,5%, le coût
de l'addition est là aussi excessif.
[0043] Les effets conjoints du chrome et du molybdène sur la trempabilité sont pris en compte
dans l'invention selon leurs caractéristiques propres ; selon l'invention, les teneurs
en chrome et en molybdène sont telles que : Cr+(2 x Mo) ≤0,6%. Les coefficients dans
cette relation traduisent l'influence respective de ces deux éléments sur la trempabilité
en vue de favoriser l'obtention d'une structure ferritique fine.
[0044] Le titane et le niobium sont des éléments de microalliage utilisés conjointement
selon l'invention :
- En quantité comprise entre 0,010 et 0,050%, le titane se combine essentiellement à
l'azote et au carbone pour précipiter sous forme de nitrures et/ou de carbonitrures.
Ces précipités sont stables lors d'un réchauffage des brames à 1150-1250°C avant le
laminage à chaud, ce qui permet de contrôler la taille du grain austénitique. Au delà
d'une teneur en titane de 0,050%, il existe un risque de former des nitrures de titane
grossiers précipités dès l'état liquide, qui tendent à réduire la ductilité.
- En quantité supérieure à 0,010%, le niobium est très efficace pour former de fins
précipités de Nb(CN) dans l'austénite ou dans la ferrite lors du laminage à chaud,
ou encore lors du recuit dans une gamme de température voisine de l'intervalle de
transformation intercritique. Il retarde la recristallisation lors du laminage à chaud
et lors du recuit et affine la microstructure. Cependant, une quantité excessive en
niobium diminuant la soudabilité, il convient de limiter celle-ci à 0,040%.
[0045] Les teneurs en titane et en niobium ci-dessus permettent de faire en sorte que l'azote
soit entièrement piégé sous forme de nitrures ou de carbonitrures, si bien que le
bore se trouve sous forme libre et peut jouer un rôle efficace sur la trempabilité.
[0046] La teneur minimale en bore pour assurer une trempabilité efficace est de 0,0005%.
Au delà de 0,0025%, l'effet sur la trempabilité est saturé et on constate un effet
néfaste sur la revètabilité et sur la ductilité à chaud.
[0047] Afin de former une quantité suffisante de nitrures et de carbonitrures, une teneur
minimale de 0,002% en azote est requise. La teneur en azote est limitée à 0,007% pour
éviter la formation de BN qui diminuerait la quantité de bore libre nécessaire au
durcissement de la ferrite.
[0048] Une addition optionnelle de nickel peut être réalisée de façon à obtenir un durcissement
supplémentaire de la ferrite. Cette addition est cependant limitée à 0,1 % pour des
raisons de coût.
[0049] La mise en oeuvre du procédé de fabrication d'une tôle laminée selon l'invention
est la suivante :
- On approvisionne un acier de composition selon l'invention
- On procède à la coulée d'un demi-produit à partir de cet acier. Cette coulée peut
être réalisée en lingots ou en continu sous forme de brames d'épaisseur de l'ordre
de 200mm. On peut également effectuer la coulée sous forme de brames minces de quelques
dizaines de millimètres d'épaisseur ou de bandes minces entre cylindres d'acier contra-rotatifs.
[0050] Les demi-produits coulés sont tout d'abord portés à une température T
R supérieure à 1150 °C pour atteindre en tout point une température favorable aux déformations
élevées que va subir l'acier lors du laminage. Cependant, si la température T
R est trop importante, les grains austénitiques croissent de façon indésirable. Dans
ce domaine de température, les seuls précipités susceptibles de contrôler efficacement
la taille du grain austénitique sont les nitrures de titane, et il convient de limiter
la température de réchauffage à 1250°C afin de maintenir un grain austénitique fin
à ce stade.
[0051] Naturellement, dans le cas d'une coulée directe de brames minces ou de bandes minces
entre cylindres contra-rotatifs, l'étape de laminage à chaud de ces demi-produits
débutant à plus de 1150°C peut se faire directement après coulée si bien qu'une étape
de réchauffage intermédiaire n'est pas nécessaire dans ce cas.
[0052] On lamine à chaud le demi-produit dans un domaine de température où la structure
de l'acier est totalement austénitique : si T
FL est inférieure à la température de début de transformation de l'austénite au refroidissement
A
r3, les grains de ferrite sont écrouis par le laminage et la ductilité est réduite.
Préférentiellement, on choisira une température de fin de laminage supérieure à 850°C.
[0053] On bobine ensuite le produit laminé à chaud à une température T
bob comprise entre 500 et 570°C : cette gamme de température permet d'obtenir une transformation
bainitique complète pendant le maintien quasi-isotherme associé au bobinage. Lorsque
la température de bobinage est trop basse, la dureté du produit est augmentée, ce
qui augmente les efforts nécessaires lors du laminage à froid à froid ultérieur.
[0054] On décape le produit laminé à chaud selon un procédé connu en lui-même, puis on effectue
un laminage à froid avec un taux de réduction compris préférentiellement entre 30
et 80%.
[0055] On chauffe ensuite le produit laminé à froid, préférentiellement au sein d'une installation
de recuit continu, avec une vitesse moyenne de chauffage Vc comprise entre 1 et 5'C/s.
En relation avec la température de recuit T
M ci-dessous, cette gamme de vitesse de chauffage permet d'obtenir une fraction de
ferrite non recristallisée inférieure ou égale à 15%.
[0056] Le chauffage est effectué jusqu'à une température de recuit T
M comprise entre la température A
c1 (température de début de transformation allotropique au chauffage)+40°C, et A
c3 (température de fin de transformation allotropique au chauffage) - 30°C, c'est à
dire dans une gamme de température particulière du domaine intercritique : lorsque
T
M est inférieure à (A
c1+40°C), la structure peut comporter encore des zones de ferrite non recristallisées
dont la fraction surfacique peut atteindre 15%. Cette proportion de ferrite non recristallisée
est évaluée de la façon suivante : après avoir identifié la phase ferritique au sein
de la microstructure, on quantifie le pourcentage surfacique de ferrite non recristallisée
rapportée à la totalité de la phase ferritique. On a mis en évidence que ces zones
non recristallisées jouent un rôle néfaste sur la ductilité et ne permettent pas d'obtenir
les caractéristiques visées par l'invention. Une température de recuit T
M selon l'invention permet d'obtenir une quantité d'austénite suffisante pour former
ultérieurement au refroidissement de la martensite en quantité telle que les caractéristiques
désirées soient atteintes. Une température T
M inférieure à (A
c3 - 30°C) permet également d'assurer que la teneur en carbone des îlots d'austénite
formés à la température T
M conduit bien à une transformation martensitique ultérieure : lorsque la température
de recuit est trop élevée, la teneur en carbone des îlots d'austénite devient trop
faible, ce qui conduit à une transformation ultérieure en bainite ou en perlite non
favorable. De plus, une température trop élevée conduit à un accroissement de la taille
des précipités de niobium qui perdent une partie de leur capacité de durcissement.
La résistance mécanique finale est alors diminuée.
[0057] On choisira préférentiellement à cet effet une température T
M comprise entre 760°C et 830°C.
[0058] Une durée de maintien minimale t
M de 30s à la température T
M permet la dissolution des carbures, une transformation partielle en austénite est
réalisée. L'effet est saturé au delà d'une durée de 300 s. Un temps de maintien supérieur
à 300s est également difficilement compatible avec les exigences de productivité des
installations de recuit continu, en particulier la vitesse de défilement. La durée
de maintien t
M est comprise entre 30 et 300s.
[0059] Les étapes suivantes du procédé différent selon que l'on fabrique une tôle d'acier
non revêtue, ou galvanisée en continu au trempé, ou galvannealed :
- Dans le premier cas, à la fin du maintien de recuit, on effectue un refroidissement
jusqu'à une température inférieure à la température Ms (température de début de formation de la martensite) avec une vitesse de refroidissement
V suffisante pour que l'austénite formée lors du recuit se transforme totalement en
martensite.
[0060] Ce refroidissement peut être effectué à partir de la température T
M en une seule ou en plusieurs étapes et peut faire intervenir dans ce dernier cas
différents modes de refroidissement tels que des bains d'eau froide ou bouillante,
des jets d'eau ou de gaz. Ces éventuels modes de refroidissement accéléré peuvent
être combinés de façon à obtenir une transformation martensitique complète de l'austénite.
Après cette transformation martensitique, le tôle est refroidie jusqu'à la température
ambiante.
[0061] La microstructure de la tôle nue refroidie est alors constituée d'une matrice ferritique
avec des îlots de martensite dont la proportion surfacique est comprise entre 35 et
50%, et est exempte de bainite.
- Dans le cas où l'on souhaite fabriquer une tôle galvanisée en continu au trempé, à
la fin du maintien de recuit, on refroidit le produit jusqu'à atteindre une température
proche de la température TZn de galvanisation au trempé, la vitesse de refroidissement VR étant suffisamment rapide pour éviter la transformation de l'austénite en ferrite.
A cet effet, la vitesse de refroidissement VR est préférentiellement supérieure à 15°C/s. On effectue la galvanisation au trempé
par immersion dans un bain de zinc ou d'alliage de zinc dont la température TZn est comprise entre 450 et 480°C. Une transformation partielle de l'austénite en bainite
intervient à ce stade, qui conduit à la formation de 1 à 10% de bainite, cette valeur
étant exprimée en proportion surfacique. Le maintien dans cette gamme de température
doit être inférieur à 80s de façon à limiter la proportion surfacique de bainite à
10% et obtenir ainsi une proportion suffisante de martensite. On refroidit ensuite
le produit galvanisé à une vitesse comprise V'R supérieure à 4°C/s jusqu'à la température ambiante dans le but de transformer complètement
la fraction d'austénite restante en martensite : on obtient de la sorte une tôle d'acier
laminée à froid, recuite et galvanisée contenant en proportion surfacique 40-64% de
ferrite, 35-50% de martensite et 1-10% de bainite.
- Dans le cas où l'on souhaite fabriquer une tôle d'acier Dual Phase laminée à froid
et « galvannealed », c'est à dire galvanisée-alliée, on refroidit le produit à la
fin du maintien de recuit jusqu'à atteindre une température proche de la température
TZn de galvanisation au trempé, la vitesse de refroidissement VR étant suffisamment rapide pour éviter la transformation de l'austénite en ferrite.
A cet effet, la vitesse de refroidissement VR est préférentiellement supérieure à 15°C/s. On effectue la galvanisation au trempé
par immersion dans un bain de zinc ou d'alliage de zinc dont la température TZn est comprise entre 450 et 480°C. Une transformation partielle de l'austénite en bainite
intervient à ce stade, qui conduit à la formation de 1 à 10% de bainite, cette valeur
étant exprimée en proportion surfacique. Le maintien dans cette gamme de température
doit être inférieur à 80s de façon à limiter la proportion de bainite à 10%. Après
la sortie du bain de zinc, on chauffe le produit galvanisé à une température TG comprise entre 490 et 550°C pendant une durée tG comprise entre 10 et 40s. On provoque ainsi l'interdiffusion du fer et de la fine
couche de zinc ou d'alliage de zinc déposée lors de l'immersion, ce qui permet d'obtenir
un produit galvannealed. On refroidit ce produit jusqu'à la température ambiante avec
une vitesse V"R supérieure à 4°C/s: on obtient de la sorte une tôle d'acier galvannealed à matrice
ferritique, contenant en proportion surfacique 40-64% de ferrite, 35-50% de martensite
et 1-10% de bainite. La martensite se trouve typiquement sous forme d'îlots de taille
moyenne inférieure à 4 micromètres, voire deux micromètres, ces îlots présentant majoritairement,
pour plus de 50% d'entre eux, une morphologie massive plutôt qu'une morphologie allongée.
La morphologie d'un îlot donné est caractérisée par le rapport entre sa taille maximale
Lmax et minimale Lmjn. Un îlot donné est considéré comme possédant une morphologie massive lorsque son
rapport
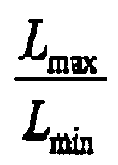
est inférieur ou égal à 2.
[0062] La présente invention va être maintenant illustrée à partir des exemples suivants
donnés à titre non limitatif :
Exemple:
[0063] On a élaboré des aciers dont la composition figure au tableau ci-dessous, exprimée
en pourcentage pondéral, Outre les aciers IX à IZ ayant servi à la fabrication de
tôles selon l'invention, on a indiqué à titre de comparaison la composition d'un acier
R ayant servi à la fabrication de tôles de référence.
Tableau 1 Compositions d'aciers (% poids). R= Référence Valeurs soulignées : Non conformes
à l'invention.
Acier |
C (%) |
Mn (%) |
Si (%) |
S (%) |
P (%) |
Al (%) |
Mo (%) |
Cr (%) |
Cr+2Mo (%) |
Ni (%) |
Nb (%) |
Ti (%) |
B (%) |
N (%) |
IX |
0,071 |
2,498 |
0,275 |
0.003 |
0,011 |
0,150 |
0,104 |
0.304 |
0,512 |
0,022 |
0,039 |
0,025 |
0,0024 |
0.004 |
IY |
0,076 |
2,430 |
0.3 |
0,003 |
0,012 |
0,120 |
0.09 |
0,33 |
0,51 |
0,030 |
0,024 |
0.024 |
0,0018 |
0,0035 |
IZ |
0,062 |
2,030 |
0,163 |
0,003 |
0,011 |
0,125 |
0,055 |
0,27 |
0,38 |
0,020 |
0,011 |
0,015 |
0,0011 |
0,004 |
R |
0.143 |
1.910 |
0,23 |
0,002 |
0.012 |
0.035 |
0.1 |
0,24 |
0,44 |
. |
: |
: |
: |
0,004 |
[0064] Des demi-produits coulés correspondant aux compositions ci-dessus ont été réchauffés
à 1230°C puis laminés à chaud jusqu'à une épaisseur de 2,8-4 mm dans un domaine où
la structure est entièrement austénitique. Les conditions de fabrication de ces produits
laminés à chaud (température de fin de laminage T
FL, température de bobinage T
bob) sont indiquées au tableau 2.
Tableau 2 Conditions de fabrication des produits laminés à chaud
Acier |
TFL(°C) |
Ar3 (°C) |
Tbob(°C) |
IX |
890 |
705 |
530 |
IY |
880 |
715 |
540 |
IZ |
880 |
735 |
530 |
R |
880 |
700 |
550 |
[0065] Les produits laminés à chaud ont été ensuite décapés puis laminés à froid jusqu'à
une épaisseur de 1,4 à 2 mm soit un taux de réduction de 50%. A partir d'une même
composition, certains aciers ont fait l'objet de différentes conditions de fabrication.
Les références IX1, IX2 et IX3 désignent par exemple trois tôles d'aciers fabriquées
selon des conditions différentes à partir de la composition d'acier IX. Les tôles
ont été galvanisées au trempé dans un bain de zinc à une température T
Zn de 460°C, d'autres ont fait en outre l'objet d'un traitement de galvannealing. Le
tableau 3 indique les conditions de fabrication des tôles recuites après laminage
à froid :
- Vitesse de chauffage Vc
- Température de recuit TM.
- Temps de maintien au recuit tM
- Vitesse de refroidissement après recuit VR
- Vitesse de refroidissement après galvanisation V'R
- Température de galvannealing TG
- Durée de galvannealing tG
- Vitesse de refroidissement V"R après traitement de galvannealing
[0066] Les températures de transformation A
c1 et A
c3 ont été également portées au tableau 3.
Tableau 3 Conditions de fabrications des tôles laminées à froid et recuites Valeurs
soulignées : non conformes à l'invention
Tôle d'acier |
Vc (°C/s) |
TM (°C) |
Ao1-Ac2 (°C) |
tM (s) |
VR (°C/s) |
V'R (°C/s) |
TQ (°C) |
tG (s) |
V'R (°C/s) |
IX1 Invention |
2 |
800 |
710-870 |
90 |
20 |
18 |
- |
- |
- |
IX2 Invention |
2 |
780 |
710-870 |
90 |
20 |
18 |
- |
- |
- |
IX3 Référence |
2 |
740 |
710-870 |
100 |
17 |
15 |
- |
- |
- |
IX4 Invention |
2 |
800 |
710-870 |
100 |
20 |
- |
520 |
10 |
10 |
IX5 Référence |
2 |
850 |
710-870 |
100 |
20 |
- |
520 |
10 |
10 |
IX6 Référence |
2 |
745 |
710-870 |
100 |
20 |
- |
520 |
10 |
10 |
IX7 Référence |
2 |
800 |
710-870 |
100 |
10 |
- |
520 |
10 |
10 |
IY1 Exemple 2 |
2 |
780 |
710-865 |
90 |
20 |
18 |
- |
- |
- |
IY2 Exemple |
2 |
800 |
710-865 |
100 |
20 |
- |
520 |
10 |
10 |
IZ Example |
2 |
800 |
710-865 |
100 |
20 |
- |
520 |
10 |
10 |
R Référence |
2 |
800 |
715-810 |
90 |
20 |
18 |
- |
- |
- |
[0067] Les propriétés mécaniques de traction obtenues (limite d'élasticité Re, résistance
Rm, allongement à rupture A ont été portées au tableau 4 ci-dessous. Le rapport Re/Rm
a été également indiqué.
[0068] On a également déterminé la microstructure des aciers, dont la matrice est ferritique.
Les fractions surfaciques de bainite et de martensite ont été quantifiées après attaque
aux réactifs Picral et LePera respectivement, suivies par une analyse d'image grâce
au logiciel Aphelion
™. On a également déterminé la fraction surfacique de ferrite non recristallisée grâce
à des observations en microscopie optique et électronique à balayage où l'on a identifié
la phase ferritique, puis quantifié la fraction recristallisée au sein de cette phase
ferritique. La ferrite non recristallisée se présente en général sous forme d'îlots
allongés par le laminage.
[0069] L'aptitude au pliage a été quantifiée de la façon suivante : des tôles ont été pliées
à bloc sur elles-mêmes en plusieurs tours. De la sorte, le rayon de pliage diminue
à chaque tour. L'aptitude au pliage est ensuite évaluée en relevant la présence de
fissures à la surface du bloc plié, la cotation étant exprimée de 1 (faible aptitude
au pliage) à 5 (très bonne aptitude) Des résultats cotés 1-2 sont considérés comme
non satisfaisants.
Tableau 4 Résultats obtenus sur les tôles laminées à froid et recuites Valeurs soulignées
: non conformes à l'invention
Tôle d'acier |
Fraction de ferrite (%) |
Fraction de bainite (%) |
Fraction de martensite (%) |
Fraction de ferrite non recristallisée (%) |
Re (MPa) |
Rm (MPa) |
Re/Rm |
A (%) |
Aptitude au pliage |
IX1 Invention |
50 |
6 |
44 |
0 |
720 |
1020 |
0,71 |
11 |
3 |
IX2 Invention |
52 |
2 |
46 |
0 |
680 |
1030 |
0,66 |
10 |
3 |
IX3 référence |
48 |
0 |
52 |
25 |
700 |
1120 |
0.62 |
6 |
1 |
IX4 Invention |
50 |
8 |
42 |
0 |
760 |
1030 |
0,74 |
10 |
3 |
IX5 référence |
55 |
12 |
33 |
0 |
780 |
950 |
0.82 |
12 |
3 |
IX6 référence |
46 |
1 |
53 |
20 |
750 |
1130 |
0,66 |
7 |
1 |
IX7 référence |
56 |
11 |
33 |
0 |
755 |
955 |
0.79 |
12 |
3 |
IY1 Exemple |
52 |
2 |
46 |
0 |
650 |
1030 |
0,63 |
13 |
4 |
IY2 Exemple |
50 |
7 |
43 |
0 |
680 |
1020 |
0,67 |
12 |
4 |
IZ Exemple |
48 |
6 |
46 |
0 |
630 |
1025 |
0,61 |
14 |
4 |
R référence |
72 |
3 |
25 |
0 |
490 |
810 |
0,60 |
18 |
2 |
[0070] Les tôles d'aciers selon l'invention présentent un ensemble de caractéristiques microstructurales
et mécaniques permettant la fabrication avantageuse de pièces, notamment pour des
applications structurales :
résistance comprise entre 980 et 1100Pa, rapport Re/Rm compris entre 0,6 et 0,8, allongement à rupture supérieur à 9%, bonne aptitude au
pliage. La figure 1 illustre la morphologie de la tôle d'acier IX1, où la ferrite
est totalement recristallisée.
[0071] Les tôles selon l'invention présentent une bonne aptitude au soudage, notamment par
résistance, le carbone équivalent étant inférieur à 0,25.
[0072] Par comparaison, les tôles de référence n'offrent pas ces mêmes caractéristiques
:
[0073] Les tôles d'acier IX3 (galvanisée) et IX6 (galvannealed) ont été recuites à une température
T
M trop faible : en conséquence, la fraction de ferrite non recristallisée est excessive
ainsi que la fraction de martensite. Ces caractéristiques microstructurales sont associées
à une diminution de l'allongement et de l'aptitude au pliage. La figure 2 illustre
la microstructure de la tôle d'acier IX3 : on note la présence de ferrite non recristallisée
sous forme d'îlots allongés (repérés (A)) coexistant avec la ferrite recristallisée
et la martensite, ce dernier constituant apparaissant plus foncé sur la micrographie.
Une micrographie en Microscopie Electronique à Balayage (figure 3) permet de distinguer
finement les zones de ferrite non recristallisée (A) de celles recristallisées (B).
[0074] La tôle IX5 est une tôle galvannealed recuite à une température T
M trop élevée : la teneur en carbone de l'austénite à haute température devient alors
trop faible et l'apparition de la bainite est favorisée au détriment de la formation
de martensite. On assiste également à une coalescence des précipités de niobium, ce
qui provoque une perte de durcissement. La résistance est alors insuffisante, le rapport
Re/R
m étant trop élevé.
[0075] La tôle IX7 galvannealed a été refroidie à une vitesse V
R trop lente après l'étape de recuit : la transformation de l'austénite formée en ferrite
se produit alors dans cette étape de refroidissement de façon excessive, la tôle d'acier
contenant au stade final une proportion de bainite trop importante et une proportion
de martensite trop faible, ce qui conduit à une résistance insuffisante.
[0076] La composition de la tôle d'acier R ne correspond pas à l'invention, sa teneur en
carbone étant trop importante, et sa teneur en manganèse, aluminium, niobium, titane,
bore étant trop faibles. En conséquence, la fraction de martensite est trop faible
si bien que la résistance mécanique est insuffisante. Les tôles d'aciers selon l'invention
seront utilisées avec profit pour la fabrication de pièces de structures ou de sécurité
dans l'industrie automobile.
2. Tôle d'acier selon la revendication. 1,
caractérisée en ce que la composition dudit acier contient, la teneur étant exprimée en poids :
3. Tôle d'acier selon la revendication 1 ou 2,
caractérisée en ce que la composition dudit acier contient, la teneur étant exprimée en poids :
4. Tôle d'acier selon la revendication 1 ou 2,
caractérisée en ce que la composition dudit acier contient, la teneur étant exprimée en poids :
5. Tôle d'acier selon l'une quelconque des revendications 1 à 4,
caractérisée en ce que la composition dudit acier contient, la teneur étant exprimée en poids :
6. Tôle d'acier selon l'une quelconque des revendications 1 à 5, caractérisée en ce que sa microstructure contient 35 à 50% de martensite en proportion surfacique
7. Tôle d'acier selon la revendication 6, caractérisée en ce que le complément de ladite microstructure est constitué de 50 à 65% de ferrite en proportion
surfacique
8. Tôle d'acier selon la revendication 6, caractérisée en ce que le complément de ladite microstructure est constitué de 1 à 10% de bainite et de
40 à 64% de ferrite en proportion surfacique
9. Tôle d'acier selon l'une quelconque des revendications 1 à 8 caractérisée en ce que sa fraction surfacique de ferrite non recristallisée rapportée à la totalité de la
phase ferritique, est inférieure ou égale à 15%
10. Tôle d'acier selon l'une quelconque des revendications 1 à 9 caractérisée en ce que le rapport entre sa limite d'élasticité Re et sa résistance Rm est tel que : o,6≤Re/Rm ≤0,8
11. Tôle d'acier selon l'une quelconque des revendications 1 à 6 ou 8 à 10, caractérisée qu'elle est galvanisée en continu
12. Tôle d'acier selon l'une quelconque des revendications 1 à 6 ou 8 à 10, caractérisée qu'elle comporte un revêtement galvannealed
13. Procédé de fabrication d'une tôle d'acier Dual Phase laminée à froid et recuite
caractérisé en ce qu'on approvisionne un acier de composition selon l'une quelconque des revendications
1 à 5, puis
- on coule ledit acier sous forme de demi-produit, puis
- on porte ledit demi-produit à une température 1150°C≤TR≤1250°C, puis
- on lamine à chaud ledit demi-produit avec une température de fin de laminage TFL ≥Ar3 pour obtenir un produit laminé à chaud, puis
- on bobine ledit produit laminé à chaud à une température Tbob telle que : 500°C ≤Tbob≤ 570°C, puis
- on décape ledit produit laminé à chaud, puis
- on effectue un laminage à froid avec un taux de réduction compris entre 30 et 80%
pour obtenir un produit laminé à froid, puis
- on chauffe ledit produit laminé à froid à une vitesse 1°C/s≤VC≤5°C/s jusqu'à une température de recuit TM telle que : Ac1+40°C≤TM≤Ac3-30°C où l'on effectue un maintien pendant une durée : 30s≤tM≤300s de façon à obtenir un produit chauffé et recuit avec une structure comprenant
de l'austénite, puis
- on refroidit ledit produit jusqu'à une température inférieure à la température Ms avec une vitesse V suffisante pour que ladite austénite se transforme totalement
en martensite
14. Procédé de fabrication d'une tôle d'acier Dual Phase laminée à froid, recuite et galvanisée
caractérisé en ce qu'on approvisionne ledit produit chauffé et recuit avec une structure comprenant de
l'austénite selon la revendication 13 puis,
- on refroidit ledit produit chauffé et recuit avec une vitesse VR suffisante pour éviter la transformation de ladite austénite en ferrite, jusqu'à
atteindre une température proche de la température TZn de galvanisation au trempé, puis
- on galvanise en continu ledit produit par immersion dans un bain de zinc ou d'alliage
de Zn à une température 450°C≤TZn≤480°C pour obtenir un produit galvanisé, puis
- on refroidit ledit produit galvanisé jusqu'à la température ambiante avec une vitesse
V'R supérieure à 4°C/s pour obtenir une tôle d'acier laminée à froid, recuite et galvanisée
15. Procédé de fabrication d'une tôle d'acier Dual Phase laminée à froid et galvannealed,
caractérisé en ce qu'on approvisionne ledit produit chauffé et recuit avec une structure comprenant de
l'austénite selon la revendication 13 puis,
- on refroidit ledit produit chauffé et recuit avec une vitesse VR suffisante pour éviter la transformation de ladite austénite en ferrite, jusqu'à
atteindre une température proche de la température TZn de galvanisation au trempé, puis
- on galvanise en continu ledit produit par immersion dans un bain de zinc ou d'alliage
de Zn à une température 450°C≤TZn≤480°C pour obtenir un produit galvanisé, puis
- on chauffe ledit produit galvanisé à une température TG comprise entre 490 et 550°C pendant une durée tG comprise entre 10 et 40 s pour obtenir un produit galvannealed, puis
- on refroidit ledit produit galvannealed jusqu'à la température ambiante à une vitesse
V"R supérieure à 4°C/s, pour obtenir une tôle d'acier laminée à froid et galvannealed
16. Procédé de fabrication selon l'une quelconque des revendications 13 à 15, caractérisé en ce que ladite température TM est comprise entre 760 et 830°C
17. Procédé de fabrication selon la revendication 14 ou 15, caractérisé en ce que ladite vitesse de refroidissement VR est supérieure ou égale à 15°C/s
18. Utilisation d'une tôle d'acier selon l'une quelconque des revendications 1 à 12, ou
fabriquée par un procédé selon l'une quelconque des revendications 13 à 17, pour la
fabrication de pièces de structures ou de sécurité pour véhicules automobiles