(19) |
 |
|
(11) |
EP 1 899 494 B1 |
(12) |
EUROPÄISCHE PATENTSCHRIFT |
(45) |
Hinweis auf die Patenterteilung: |
|
28.07.2010 Patentblatt 2010/30 |
(22) |
Anmeldetag: 23.06.2006 |
|
(51) |
Internationale Patentklassifikation (IPC):
|
(86) |
Internationale Anmeldenummer: |
|
PCT/EP2006/063516 |
(87) |
Internationale Veröffentlichungsnummer: |
|
WO 2007/000422 (04.01.2007 Gazette 2007/01) |
|
(54) |
VERFAHREN ZUM HERSTELLEN VON KERAMISCHEN SCHICHTEN
METHOD FOR PRODUCING CERAMIC LAYERS
PROCEDE DE FABRICATION DE COUCHES CERAMIQUES
|
(84) |
Benannte Vertragsstaaten: |
|
CH DE FR GB IT LI NL |
(30) |
Priorität: |
28.06.2005 DE 102005031101
|
(43) |
Veröffentlichungstag der Anmeldung: |
|
19.03.2008 Patentblatt 2008/12 |
(73) |
Patentinhaber: SIEMENS AKTIENGESELLSCHAFT |
|
80333 München (DE) |
|
(72) |
Erfinder: |
|
- KRÜGER, Ursus
14089 Berlin (DE)
- ULLRICH, Raymond
14621 Schönwalde (DE)
|
(56) |
Entgegenhaltungen: :
EP-A- 0 939 143 FR-A1- 2 850 649
|
WO-A-87/06627 US-A- 6 139 913
|
|
|
|
|
- PETROVICOVA E ET AL: "Thermal spraying of polymers" INTERNATIONAL MATERIALS REVIEWS
INST. MATER UK, Bd. 47, Nr. 4, August 2002 (2002-08), Seiten 169-190, XP001248250
ISSN: 0950-6608
- SCHADLER L S ET AL: "Microstructure and mechanical properties of thermally sprayed
silica/nylon nanocomposites" JOURNAL OF THERMAL SPRAY TECHNOLOGY ASM INT USA, Bd.
6, Nr. 4, Dezember 1997 (1997-12), Seiten 475-485, XP001248384 ISSN: 1059-9630 in
der Anmeldung erwähnt
- VILLAFUERTE J: "COLD SPRAY: A NEW TECHNOLOGY" WELDING JOURNAL, AMERICAN WELDING SOCIETY,
MIAMI, FL, US, Bd. 84, Nr. 5, Mai 2005 (2005-05), Seiten 24-29, XP001237822 ISSN:
0043-2296
|
|
|
|
Anmerkung: Innerhalb von neun Monaten nach der Bekanntmachung des Hinweises auf die
Erteilung des europäischen Patents kann jedermann beim Europäischen Patentamt gegen
das erteilte europäischen Patent Einspruch einlegen. Der Einspruch ist schriftlich
einzureichen und zu begründen. Er gilt erst als eingelegt, wenn die Einspruchsgebühr
entrichtet worden ist. (Art. 99(1) Europäisches Patentübereinkommen). |
[0001] Die Erfindung betrifft ein Verfahren zum Herstellen von keramischen Schichten, bei
dem Partikel mittels einer Düse auf die zu beschichtende Oberfläche gespritzt werden
und dort haften bleiben.
[0002] Die Herstellung von keramischen Schichten durch thermisches Spritzen ist beispielsweise
bekannt aus einer Veröffentlichung des US-Verteidigungsministeriums (
The AMPTIAC Newsletter, Frühling 2002, Vol. 6 No. 1). Danach können Mikropartikel, die die keramischen Bestandteile der zu erzeugenden
keramischen Beschichtung enthalten, in einem thermischen Spritzprozess auf die zu
beschichtende Oberfläche gespritzt werden. Durch die thermische Spritzpistole wird
ein Plasmastrahl erzeugt, in den die Mikropartikel des Keramikwerkstoffes eingespeist
werden und dadurch zumindest teilweise aufgeschmolzen werden. Hierdurch bildet sich
bei dem Auftreffen der Mikropartikel auf das zu beschichtende Substrat bzw. die im
Aufbau befindliche Schicht ein keramisches Gefüge aus, welches evtl. durch eine thermische
Nachbehandlung fertig gestellt wird.
[0003] In jüngerer Vergangenheit ist eine neue Klasse keramischer Materialien - die so genannten
Polymer-Keramiken - entwickelt worden. Zu dieser neuen keramischen Klasse wird beispielsweise
durch den Lehrstuhl für Glas und Keramik an der Universität Erlangen auf der Internetseite
www.presse.unierlangen.de\ Aktuelles\Keram%20Material.html (verfügbar am 06.09.2004)
ausgeführt, dass Polymerkeramiken nicht im traditionellen Verfahren des Hochtemperaturglühens
(Sintern) von pulverförmigen Rohstoffen hergestellt werden können, da die keramischen
Rohmaterialien (Precursor) als Polymere für dieses Verfahren eine zu hohe thermische
Empfindlichkeit aufweisen. Stattdessen muss ein stark von chemischen Techniken geprägter
Verfahrensansatz verfolgt werden, bei dem die siliziumhaltigen Kunststoffe, die auch
als präkeramische Polymere bezeichnet werden (beispielsweise Polycarbosilane, Polysilazane
und Poysiloxane), durch eine thermische Zersetzung (Pyrolyse) in keramische Hochleistungsmaterialien
überführt werden. Wegen der niedrigeren Prozesstemperaturen sind jedoch thermische
Spritzverfahren der Herstellung von Polymerkeramiken nicht zugänglich.
[0006] Die Aufgabe der Erfindung besteht darin, ein Verfahren zum Herstellen von keramischen
Schichten mittels Spritzens anzugeben, welches der Herstellung von polymerkeramischen
Schichten zugänglich ist.
[0007] Diese Aufgabe wird mit dem eingangs genannten Verfahren erfindungsgemäß dadurch gelöst,
dass als Partikel Vorstufen einer Polymerkeramik (die auch als präkeramische Polymere
bezeichnet werden) verwendet werden und als Düse eine Kaltspritzdüse unter Einsatz
des Kaltspritzens verwendet wird. Die Anwendung des Kaltspritzverfahrens hat den Vorteil,
dass im Unterschied zu thermischen Spritzverfahren die zur Bildung der Beschichtung
notwendige Energie aufgrund einer starken Beschleunigung der Beschichtungsteilchen
im Kaltgasstrahl (bevorzugt auf mehrfache Schallgeschwindigkeit) erzeugt wird.
[0008] Kaltspritzverfahren sind grundsätzlich beispielsweise aus der
DE 102 24 780 A1 bekannt. Die zum Betrieb des Verfahrens notwendige Vorrichtung weist beispielsweise
eine Vakuumkammer auf, in der ein Substrat vor einer so genannten Kaltspritzdüse platziert
werden kann. Zur Durchführung der Beschichtung wird die Vakuumkammer evakuiert und
mittels der Kaltspritzdüse (auch Kaltgasspritzpistole genannt) ein Gasstrahl erzeugt,
in dem Partikel zur Beschichtung des Werkstücks eingeschleust werden können. Diese
werden durch den Kaltgasstrahl stark beschleunigt, so dass ein Anhaften der Partikel
auf der Oberfläche des zu beschichtenden Substrates durch Umwandlung der kinetischen
Energie der Partikel erreicht wird. Die Partikel können zusätzlich erwärmt werden,
wobei deren Erwärmung derart begrenzt wird, dass die Schmelztemperatur der Partikel
nicht erreicht wird (dieser Umstand trägt namensgebend zum Begriff Kaltgasspritzen
bei).
[0009] Der Energieeintrag in die Beschichtungsteilchen, d. h. die Vorstufen der Polymerkeramik,
kann durch Einstellen der Geschwindigkeit des Kaltgasstrahls sowie durch eventuell
zusätzliche Einbringung thermischer Energie in den Kaltgasstrahl verändert werden.
Er muss so bemessen werden, dass die Vorstufen der Polymerkeramik, die in Partikelform
auf die Oberfläche des zu beschichtenden Substrates beschleunigt werden, zumindest
haften bleiben (hierzu im Folgenden mehr). Hierdurch lässt sich eine Beschichtung
aus Polymerkeramik durch Spritzen erzeugen, deren Eigenschaften nicht durch eine thermische
Überbeanspruchung der zu verspritzenden Teilchen gefährdet werden.
[0010] Gemäß einer vorteilhaften Ausführung der Erfindung ist es möglich, dass weitere Partikel
als Füllstoff dem durch die Düse erzeugten Kaltgasstrahl zugeführt werden. Hierbei
besteht vorteilhaft die Möglichkeit, Füllstoffe zu verwenden, deren thermische Empfindlichkeit
einen Zusatz zum Plamastrahl eines thermischen Spritzverfahrens nicht erlauben würde.
Da die bei thermischen Spritzverfahren verwendeten Keramiken im Allgemeinen einen
sehr hohen Schmelzpunkt aufweisen, ist der Zusatz von Füllstoffen bei konventionellen
keramischen Verfahren nämlich so gut wie ausgeschlossen.
[0011] Es ist beispielsweise vorteilhaft, wenn Metalle, insbesondere Zirkon (Zr) Titan (Ti)
oder Aluminium (A1) oder Metalllegierungen insbesondere aus dem genannten Materialien
zugeführt werden, die bei der Schichtbildung mit den Vorstufen der Polymerkeramik
reagieren. Hierbei entsteht die Möglichkeit, die Zusammensetzung der Polymerkeramiken
mittels Zugabe von aktiven Füllstoffen zu beeinflussen.
[0012] Weiterhin kann beispielsweise vorteilhaft auch ein Anteil an passiven Füllstoffen
zugegeben werden, beispielsweise Siliziumoxid (SiO
2), Siliziumkarbit (SiC), Siliziumnitrid (SiN), Bohrnitrid (BN) oder Korund. Weiterhin
können passivierte oder inaktive Metalllegierungen oder Metalle zugegeben werden.
Passivierte Metalle sind inaktiv, da sie eine oxidierte Oberfläche aufweisen, die
keramische Eigenschaften aufweist. Inaktive Metalle weisen im Allgemeinen einen genügend
hohen Schmelzpunkt auf, damit sie an den bei der Bildung der Polymerkeramik beteiligten
Reaktionen nicht beteiligt sind. Vorrangig kommen edle Metalle wie Gold (Au) oder
Platin (Pt) infrage.
[0013] Die Füllstoffe können zur Steigerung der Reaktivität vorzugsweise nanopartikulär
in dem Kaltspritzprozess eingebunden werden. Damit eine Verarbeitung mit dem Kaltgasspritzen
möglich wird, müssen die Nanopartikel aufgrund ihrer sehr geringen Trägheit an größere
Partikel gebunden werden. Beispielsweise können die Füllstoffe als Nanopartikel in
eine Matrix präkeramisches Polymere als Vorstufen der Polymerkeramik eingebettet werden,
wobei die Vorstufen jeweils Mikropartikel bilden, die sich mit dem Kaltgasspritzen
verarbeiten lassen. Die Einbettung in die Matrix der Vorstufen ist insbesondere bei
reaktiver Füllstoffen besonders vorteilhaft, da diese wegen ihrer guten Verteilung
und großen Oberfläche dann vollständig bei dem Bildungsprozess der Polymerkeramik
reagieren können. Ein Verfahren zur Herstellung von Mikropartikeln mit in einer Matrix
als Mikroverkapselung eingebetteten Nanopartikeln wird beispielsweise durch die Firma
Capsulation® angeboten.
[0014] Gemäß einer anderen Ausgestaltung der Erfindung ist vorgesehen, dass der Energieeintrag
in den Kaltgasstrahl derart bemessen wird, dass die Reaktion der Vorstufen der Polymerkerämik
während der Schichtbildung vollständig abgeschlossen wird. Dies bedeutet, dass die
Vorstufen der Polymerkeramik beim Auftreffen auf die Unterlage (Substrat bzw. sich
im Aufbau befindliche Schicht) vollständig in die Polymerkeramik umgewandelt werden
und dabei Füllstoffe gleichzeitig eingebaut werden bzw. mit den Vorstufen der Polymerkeramik
reagieren. Hierdurch lässt sich vorteilhaft ein sehr wirtschaftliches Verfahren verwirklichen,
weil eine Nachbehandlung der polymerkeramischen Schicht nicht notwendig ist. Eventuell
kann ein thermischer Nachbehandlungsschritt erfolgen, der beispielsweise zum Abbau
von Eigenspannungen benötigt wird.
[0015] Es ist jedoch auch möglich, dass der Energieeintrag in den Kaltgasstrahl derart bemessen
wird, dass eine Haftung der Partikel gewährleistet ist, jedoch die Reaktion der Vorstufen
der Polymerkeramik nicht abgeschlossen wird und anschließend eine Nachbehandlung erfolgt.
Mit der Nachbehandlung kann vorteilhaft gezielt eine Umwandlung in Polymerkeramiken
erfolgen, wobei dies in dem gesamten erzeugten Schichtverbund geschieht, wodurch der
Aufbau von fertigungsbedingten Spannungen vorteilhaft vermindert oder sogar ausgeschlossen
werden kann. Als Nachbehandlung soll in diesem Zusammenhang auch eine direkt nach
dem Auftreffen der Vorstufen der Polymerkeramik eingeleitete Behandlung verstanden
werden, die bereits während des Schichtaufbaus den gebildeten Anteil der Beschichtung
mit zusätzlicher Energie beaufschlagt.
[0016] In diesem Zusammenhang ist es vorteilhaft, wenn die Nachbehandlung beispielsweise
durch den Energieeintrag elektromagnetischer Strahlung, insbesondere von Laserlicht
in die sich bildende Schicht erfolgt. Der Laser kann vorteilhaft auf die Auftreffstelle
des Kaltgasstrahls ausgerichtet werden, wodurch erreicht wird, dass der Energieeintrag
in die Schicht genauso lokal erfolgt, wie dies durch den Kaltgasstrahl erreicht wird.
Auf diese Weise lässt sich die Polymerkeramik in der Beschichtung auch fertig stellen,
wenn aufgrund der Anforderungen des Prozesses der Energieeintrag in den Kaltgasstrahl
begrenzt ist.
[0017] Der Verfahrensparameter des Energieeintrags in den Kaltgasstrahl kann außerdem vorteilhaft
dazu genutzt werden, um die Haftung der Schicht auf dem Substrat günstig zu beeinflussen.
Dies geschieht dadurch, dass der Energieeintrag in den Kaltgasstrahl bei der Beschichtung
des noch unbeschichteten Substrates derart bemessen wird, dass die Partikel eine Verbindung
mit dem Werkstoff des Substrates eingehen. Hierbei ist der Umstand zu berücksichtigen,
dass die Partikel aufgrund ihrer kinetischen Energie beim Auftreffen auf das noch
unbeschichtete Substrat eine Verbindung mit diesem eingehen können, wobei diese beispielsweise
aus kovalenten Bindungen bestehen können. Hierdurch wird die Schichthaftung vorteilhaft
verbessert, was bei einer mechanischen Beanspruchung der erzeugten keramischen Schicht
beispielsweise die Gefahr ihres Abplatzens verringert.
[0018] Weitere Einzelheiten der Erfindung werden im Folgenden anhand der Zeichnung beschrieben.
Die einzige Figur stellt eine Vorrichtung zum Kaltgasspritzen dar. Diese weist einen
Vakuumbehälter 11 auf, in dem einerseits eine Kaltspritzdüse 12, die auch als Kaltgasspritzpistole
bezeichnet werden kann, und andererseits ein Substrat 13 angeordnet ist (Befestigung
nicht näher dargestellt). Durch eine erste Leitung 14 kann ein Prozessgas der Kaltgasspritzpistole
12 zugeführt werden. Diese weist, wie durch die Kontur angedeutet, eine Lavalform
auf, durch die das Prozessgas entspannt und in Form eines Gasstrahls (Pfeil 15) zu
einer Oberfläche 16 des Substrates 13 hin beschleunigt wird. Das Prozessgas kann beispielsweise
als reaktives Gas Sauerstoff 17 enthalten. Weiterhin kann das Prozessgas in nicht
dargestellter Weise erwärmt werden, wodurch sich in dem Vakuumbehälter 12 eine geforderte
Prozesstemperatur einstellt.
[0019] Durch eine zweite Leitung 18 können der Kaltspritzdüse 12 Partikel 19 zugeführt werden,
die als Matrix präkeramische Polymere 19a mit Füllstoffen 19b für die zu bildende
Polymerkeramik ausgeführt sein können. Diese Partikel werden in dem Gasstrahl beschleunigt
und treffen auf der Oberfläche 16 auf. Die kinetische Energie der Partikel führt zu
einem Anhaften derselben auf der Oberfläche 16, wobei auch der Sauerstoff 17 in die
sich ausbildende Schicht 20 eingebaut wird bzw. an den pyrolytischen Reaktionen der
präkeramischen Polymere beteiligt wird. Außerdem können weitere Füllstoffpartikel
19c, die als Mikropartikel ausgeführt sind, dem Kaltgasstrahl zugemischt werden, die
ebenfalls in die Schicht 21 eingebaut werden.
[0020] Zur Ausbildung der Schicht kann das Substrat 13 in Richtung des Doppelpfeils 21 vor
der Kaltspritzdüse 12 hin und her bewegt werden. Alternativ ist es auch möglich, in
nicht dargestellter Weise die Kaltspritzdüse 12 schwenkbar auszuführen. Während des
Beschichtungsprozesses wird das Vakuum in der Vakuumkammer 11 durch die Vakuumpumpe
22 ständig aufrechterhalten, wobei das Prozessgas vor der Durchleitung durch die Vakuumpumpe
22 durch einen Filter 23 geführt wird, um Partikel auszufiltern, die beim Auftreffen
auf die Oberfläche 16 nicht an diese gebunden wurden.
[0021] In einem Grenzbereich 24, der kreuzschraffiert dargestellt ist und sich auf den an
die Oberfläche 16 angrenzenden Teil des Gefüges des Substrates 13 und die an die Oberfläche
angrenzenden Partikel der sich ausbildenden Schicht bezieht, kann durch geeignete
Einstellung der Prozessparameter der Energieeintrag in die sich bildende Schicht derart
gesteuert werden, dass eine gute Haftung zwischen der Schicht 20 und dem Substrat
13 bewirkt wird. Hierbei werden bevorzugt kovalente Bindungen ausgenutzt, die sich
zwischen den auftreffenden Partikeln 19 und dem Substrat 13 ausbilden, ohne dass die
Oberfläche 16 des Substrates 13 aufgeschmolzen wird. Hierdurch kann verhindert werden,
dass Bestandteile des Substrates 13 in ungewünschter Weise in die sich bildende Schicht
20 eingebaut werden und andersherum.
[0022] Um die Schicht 20 nach der Herstellung einer geeigneten Wärmebehandlung zum Abschluss
der in der Schicht 20 ablaufenden Reaktionen unterwerfen zu können, ist in dem Vakuumbehälter
11 weiterhin eine Heizung 25 vorgesehen. Mit dieser können während des Ablaufes des
Beschichtungsprozesses auch die in der Vakuumkammer geforderten Temperaturen erreicht
werden. Weiterhin ist zur Einbringung eines lokalen Energieeintrags in die Schicht
in Form von elektromagnetischer Strahlung ein Laser in dem Vakuumbehälter 11 untergebracht,
der sich mittels einer schwenkbaren Aufhängung bewegen lässt. Insbesondere kann dieser,
wie in der Figur dargestellt, auf den Auftreffpunkt des Kaltgasstrahls 15 ausgerichtet
werden, wodurch während des Schichtbildungsprozess ein zusätzlicher externer Energieeintrag
erfolgen kann, der unabhängig vom Energieeintrag in den Kaltgasstrahl 15 ist.
1. Verfahren zum Herstellen von keramischen Schichten (20), bei dem Partikel (19) mittels
einer Düse auf die zu beschichtende Oberfläche (16) gespritzt werden und dort haften
bleiben,
dadurch gekennzeichnet,
dass als Partikel als präkeramische Polymere ausgebildete Vorstufen (19a) einer Polymerkeramik
verwendet werden und als Düse eine Kaltspritzdüse (12) unter Einsatz des Kaltgasspritzens
verwendet wird.
2. Verfahren nach Anspruch 1,
dadurch gekennzeichnet,
dass weitere Partikel als Füllstoff (19b, 19c) dem durch die Düse erzeugten Kaltgasstrahl
(15) zugeführt werden.
3. Verfahren nach Anspruch 2,
dadurch gekennzeichnet,
dass Metalle oder Metalllegierungen als aktive Füllstoffe (19b, 19c) zugeführt werden,
die bei der Schichtbildung mit den Vorstufen (19a) der Polymerkeramik reagieren.
4. Verfahren nach Anspruch 2 oder 3,
dadurch gekennzeichnet,
dass Keramiken oder inaktive oder passivierte Metalllegierungen oder Metalle, als passive
Füllstoffe (19b, 19c) zugeführt werden, die bei der Schichtbildung an der Reaktion
der Vorstufen (19a) der Polymerkeramik unbeteiligt bleiben.
5. Verfahren nach einem der vorstehenden Ansprüche,
dadurch gekennzeichnet,
dass der Energieeintrag in den Kaltgasstrahl (15) derart bemessen wird, dass die Reaktion
der Vorstufen (19a) der Polymerkeramik während der Schichtbildung vollständig abgeschlossen
wird.
6. Verfahren nach einem der Ansprüche 1 bis 3,
dadurch gekennzeichnet,
dass der Energieeintrag in den Kaltgasstrahl (15) derart bemessen wird, dass eine Haftung
der Partikel (19) gewährleistet ist, jedoch die Reaktion der Vorstufen (19a) der Polymerkeramik
nicht abgeschlossen wird und anschließend eine Nachbehandlung erfolgt.
7. Verfahren nach Anspruch 6,
dadurch gekennzeichnet,
dass die Nachbehandlung durch den Energieeintrag elektromagnetischer Strahlung in die
sich bildende Schicht erfolgt.
8. Verfahren nach einem der vorstehenden Ansprüche,
dadurch gekennzeichnet,
dass der Energieeintrag in den Kaltgasstrahl (15) bei der Beschichtung des noch unbeschichteten
Substrates (13) derart bemessen wird, dass die Partikel (19) eine Verbindung mit dem
Werkstoff des Substrates (13) eingehen.
1. Process for producing ceramic layers (20), in which a nozzle is used to spray particles
(19) onto the surface (16) to be coated, where they remain adhering,
characterized
in that the particles used are precursors (19a) of a polymer ceramic which are in the form
of preceramic polymers, and the nozzle used is a cold spraying nozzle (12) using cold
spraying.
2. Process according to Claim 1,
characterized
in that further particles are fed as filler (19b, 19c) to the cold gas jet (15) produced
by the nozzle.
3. Process according to Claim 2,
characterized
in that the active fillers (19b, 19c) fed in are metals or metal alloys which react with
the precursors (19a) of the polymer ceramic during the layer formation.
4. Process according to Claim 2 or 3,
characterized
in that the passive fillers (19b, 19c) fed in are ceramics or inactive or passivated metal
alloys or metals which do not become involved in the reaction of the precursors (19a)
of the polymer ceramic during the layer formation.
5. Process according to one of the preceding claims,
characterized
in that the amount of energy introduced into the cold gas jet (15) is such that the reaction
of the precursors (19a) of the polymer ceramic is completed during the layer formation.
6. Process according to one of Claims 1 to 3,
characterized
in that the amount of energy introduced into the cold gas jet (15) is such that adhesion
of the particles (19) is ensured, but the reaction of the precursors (19a) of the
polymer ceramic is not completed and this is followed by after-treatment.
7. Process according to Claim 6,
characterized
in that the after-treatment is carried out by means of the introduction of energy from electromagnetic
radiation into the layer which forms.
8. Process according to one of the preceding claims,
characterized
in that the amount of energy introduced into the cold gas jet (15) during coating of the
still uncoated substrate (13) is such that the particles (19) enter into a bond with
the material of the substrate (13).
1. Procédé de production de couches ( 20 ) en céramique, dans lequel on pulvérise des
particules ( 19 ) au moyen d'une buse sur la surface ( 16 ) à revêtir et on les y
laisse adhérer,
caractérisé
en ce qu'on utilise comme particules des précurseurs ( 19a ) d'une céramique polymère constituée
sous la forme de polymères pré-céramiques et on utilise, comme buse, une buse ( 12
) de projection à froid en mettant en oeuvre la projection de gaz froid.
2. Procédé suivant la revendication 1,
caractérisé
en ce que l'on apporte d'autres particules comme charge ( 19b, 19c ) au jet ( 15 ) de gaz froid
produit par la buse.
3. Procédé suivant la revendication 2,
caractérisé
en ce que l'on apporte des métaux ou des alliages de métaux comme charge ( 19b, 19c ) active,
qui réagissent lors de la formation de la couche sur les précurseurs ( 19a ) de la
céramique polymère.
4. Procédé suivant la revendication 2 ou 3,
caractérisé
en ce que l'on apporte des céramiques ou des alliages métalliques ou des métaux inactifs ou
passivés comme charge ( 19a, 19c ) passives qui, lors de la formation de la couche,
restent sans participer à la réaction des précurseurs ( 19a ) de la céramique polymère.
5. Procédé suivant l'une des revendications précédentes,
caractérisé
en ce qu'on proportionne l'apport d'énergie au jet ( 15 ) de gaz froid, de manière à exclure
complètement la réaction des précurseurs ( 19a ) de la céramique polymère pendant
la formation de la couche.
6. Procédé suivant l'une des revendications 1 à 3,
caractérisé
en ce que l'on proportionne l'apport d'énergie au jet ( 15 ) de gaz froid, de manière à assurer
une adhérence des particules ( 19 ), mais à ne pas exclure la réaction des précurseurs
( 19a ) de la céramique polymère et on effectue ensuite un post-traitement.
7. Procédé suivant la revendication 6,
caractérisé
en ce que l'on effectue le post-traitement par l'apport d'énergie de rayonnement électromagnétique
à la couche qui se forme.
8. Procédé suivant l'une des revendications précédentes,
caractérisé
en ce que l'on proportionne l'apport d'énergie au jet ( 15 ) de gaz froid lors du revêtement
du substrat ( 13 ) qui n'est pas encore revêtu, de manière à ce que les particules
( 19 ) entrent en liaison avec le matériau du substrat ( 13 ).
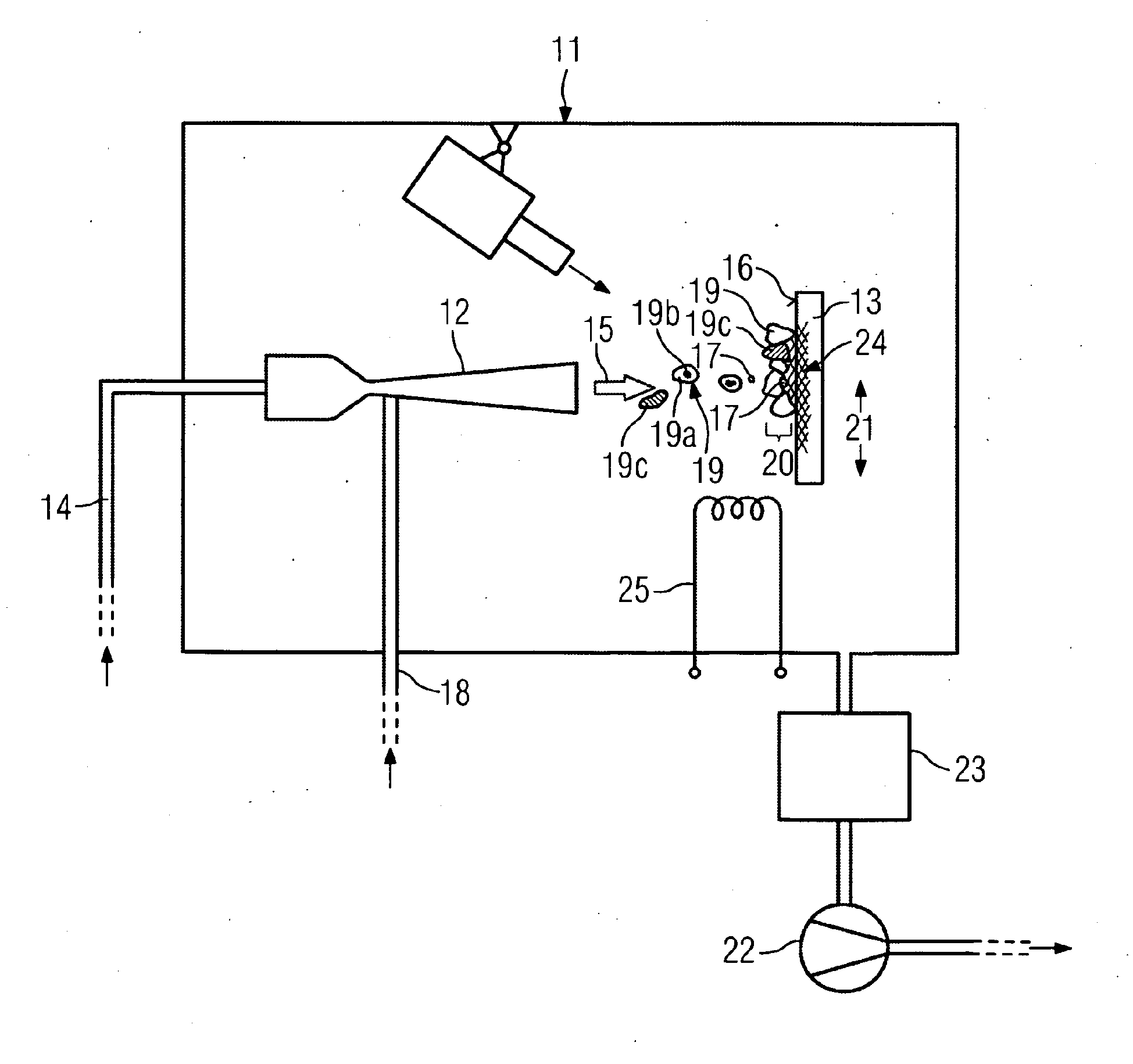
IN DER BESCHREIBUNG AUFGEFÜHRTE DOKUMENTE
Diese Liste der vom Anmelder aufgeführten Dokumente wurde ausschließlich zur Information
des Lesers aufgenommen und ist nicht Bestandteil des europäischen Patentdokumentes.
Sie wurde mit größter Sorgfalt zusammengestellt; das EPA übernimmt jedoch keinerlei
Haftung für etwaige Fehler oder Auslassungen.
In der Beschreibung aufgeführte Patentdokumente
In der Beschreibung aufgeführte Nicht-Patentliteratur
- The AMPTIAC NewsletterFrühling, 2002, vol. 6, 1 [0002]
- O. GoerkeCeramic coatings processed by spraying of siloxane precursors (polymerspraying)Journal
of the European Ceramic Society, 2004, vol. 24, 2141-2147 [0004]
- L. S. SchadlerMicrostructure and Mechanical Properties of Thermally Sprayed Silica/Nylon NanocompositesJournal
of Thermal Spray Technology, 1997, vol. 6, 475-485 [0005]