BACKGROUND OF THE INVENTION
[0001] The present invention relates to an automatic transmission having an oil filter that
is attached to a transmission casing.
[0002] In a related art, an automatic transmission through which oil discharged from an
oil pump through a control valve unit is circulated in a transmission casing as lubricating
oil after passing through an oil cooler and an oil filter has been known. For example,
such an automatic transmission is disclosed in Japanese Patent Provisional Publication
No.
2003-106415 (hereinafter is referred to as "
JP2003-106415").
[0003] In this related art automatic transmission, an opening end surface of a filter case
having therein the oil filter is contiguous with or touches the transmission casing,
and a circumferential edge portion of this opening end surface is fixed with a plurality
of screws. Further, a seal member is provided on a contact surface between the transmission
casing and the filter case, and thereby preventing oil leakage.
SUMMARY OF THE INVENTION
[0004] In the related art automatic transmission in
JP2003-106415, however, because the circumferential edge portion of the opening end surface is
fixed with the plurality of screws, there is a need to secure space for arranging
each screw around the filter case, and an installation position of the filter case
is thus limited.
[0005] In addition, in a case where looseness of any of the plurality of screws occurs,
a pressing force that presses the filter case against the transmission casing, i.e.
a surface pressure that acts on the contact surface between the transmission casing
and the filter case, becomes weak. This causes decrease in a sealing performance by
the seal member, and the oil leakage might occur.
[0006] For these problems, it is therefore an object of the present invention to provide
an automatic transmission which is capable of reducing fixing points of the filter
case while securing the sealing performance between the transmission casing and the
filter case.
[0007] According to one aspect of the present invention, an automatic transmission comprises:
a transmission casing which houses therein a transmission mechanism, the transmission
casing having (a) a concave portion with which at least an oil inlet or an oil outlet
communicates at an inside of the concave portion and (b) an overhanging portion which
is positioned close to the concave portion and extends along a surface of the transmission
casing with a clearance provided between the surface and the overhanging portion,
and a filter case which is attached to the transmission casing and has therein an
oil filter, the filter case having (c) a case body which is inserted into the concave
portion, (d) a seal member which fits onto an outer circumference of the case body
and seals a boundary between an outer circumferential surface of the case body inserted
into the concave portion and an inside surface of the concave portion, (e) a first
brim portion which protrudes from the outer circumferential surface of the case body
and is fixed to the surface of the transmission casing and (f) a second brim portion
which protrudes from the outer circumferential surface of the case body and is inserted
into the clearance.
[0008] The other objects and features of this invention will become understood from the
following description with reference to the accompanying drawings.
BRIEF DESCRIPTION OF THE DRAWINGS
[0009] FIG. 1 is a schematic system diagram showing a power train in which an automatic
transmission of an embodiment 1 is mounted.
[0010] FIG. 2 is a sectional development showing the automatic transmission of the embodiment
1.
[0011] FIG. 3 is a schematic circuit diagram showing a hydraulic circuit in the automatic
transmission of the embodiment 1.
[0012] FIG. 4 is a side view of a transmission case of the automatic transmission of the
embodiment 1.
[0013] FIG. 5 is a sectional view of A-A in FIG. 4.
[0014] FIG. 6 is a sectional view of B-B in FIG. 4.
[0015] FIG. 7A is a side view of a case body of a filter case. FIG. 7B is a top view of
the case body. FIG. 7C is a sectional view of C-C in FIG. 7B.
[0016] FIG. 8A is a sectional view showing a main part in an automatic transmission of a
comparative example. FIG. 8B is a top view of the main part in the automatic transmission
of the comparative example.
[0017] FIG. 9 is a side view of a transmission casing, showing a state before the filter
case is fixed.
DETAILED DESCRIPTION OF THE INVENTION
[0018] According to an automatic transmission of the present invention, a case body is inserted
into a concave portion that is formed at an transmission casing, and a boundary between
an outer circumferential surface of the case body and an inside surface of the concave
portion is sealed with a seal member which fits onto an outer circumference of the
case body. With this, a sealing performance by the seal member is secured by a difference
in dimension between an outside diameter of the case body and an inside diameter of
the concave portion. And even if the case body rattles, the sealing performance by
the seal member can be secured. As a result, the oil leakage from the boundary between
the outer circumferential surface of the case body and the inside surface of the concave
portion can surely be prevented.
[0019] Further, since the sealing performance is secured by the difference in dimension
between the outside diameter of the case body and the inside diameter of the concave
portion, there is no need to press a filter case against the transmission casing.
Further, a first brim portion is fixed to the transmission casing and a second brim
portion is inserted into a clearance between a surface of the transmission casing
and an overhanging portion, and attachment of the case body to the transmission casing
can be achieved. As a consequence, fixing points of the filter case to the transmission
casing can be reduced. In addition, even in a case where the first brim portion comes
off from the transmission casing, since the second brim portion interferes with the
overhanging portion, the filter case does not fall out and the sealing performance
is not impaired. Hence, it is possible to reduce the fixing points of the filter case
while securing the sealing performance between the transmission casing and the filter
case.
[0020] Embodiments of the present invention will now be explained below with reference to
the drawings.
[Embodiment 1]
[0021] First, a system in the present invention will be explained. A power train shown in
Fig. 1 has an engine 1 that is a drive source, a torque converter 2 that is connected
with and driven by the engine 1, an automatic transmission 3 that is connected with
and driven by the torque converter 2, and wheels 6, 6 to which a power is transmitted
and outputted from the automatic transmission 3 through a drive shaft 6a. The automatic
transmission 3 is controlled by a transmission control section 7 having a continuously
variable transmission control section (a CVT control section) 7a that controls an
after-mentioned continuously variable transmission mechanism (CVT mechanism) 20 and
a multi-range (or a geared) transmission control section 7b that controls an after-mentioned
multi-range (or geared) transmission mechanism 30. The automatic transmission 3 has
a transmission mechanism TM that is housed in a transmission casing 8.
[0022] As shown in Fig. 2, the transmission casing 8 has a converter housing 8a, a transmission
case 8c, a transmission cover 8b, and a bearing retainer 8d. Further, a filter case
50 having therein an oil filter F is externally attached to the transmission casing
8, and an oil passage Y (see Figs. 5 and 6) is formed in the transmission casing 8.
[0023] The converter housing 8a has a concave portion 81a in which the torque converter
2 is installed. The converter housing 8a forms an outer surface of the transmission
casing 8 on a torque converter side. The converter housing 8a is provided with an
input shaft penetration opening 82a into which an output shaft 2a of the torque converter
2 is inserted, and also provided with a drive shaft penetration opening 83a from which
the drive shaft 6a protrudes. The input shaft penetration opening 82a is formed in
the center of the concave portion 81a. In addition, an output bearing 84a for supporting
a transmission output shaft 4 is provided at an inside surface of the converter housing
8a.
[0024] The transmission case 8c is combined with the converter housing 8a, and forms an
outer surface or shell of the transmission casing 8. The transmission case 8c is provided
therein with an input shaft bearing 81c for supporting the output shaft 2a of the
torque converter 2, and also provided with a primary pulley bearing 82c for supporting
an input shaft of a primary pulley 21, further provided with a secondary pulley bearing
83c for supporting an output shaft of a secondary pulley 22. Moreover, the transmission
case 8c is provided with a drive shaft penetration opening 84c from which the drive
shaft 6a protrudes. In addition, the transmission case 8c has a concave portion 85c
in which the multi-range transmission mechanism 30 is installed, and has a valve unit
case portion 86c that houses a control valve unit 71.
[0025] As shown in Figs. 5 and 6, on an outer surface 90c of the transmission case 8c (on
a surface 90c of the transmission casing), a cover attachment surface 87c to which
the transmission cover 8b is attached, a filter concave portion (a concave portion)
88c into which the filter case 50 is inserted, and a screw hole 89c into which a fixing
screw N1 for fixing the filter case 50 is screwed, are provided. On the cover attachment
surface 87c, a plurality of screw holes (not shown) into which a fixing screw N2 (see
Fig. 4) for fixing the transmission cover 8b is screwed are provided.
[0026] Here, the transmission cover 8b attached to the cover attachment surface 87c and
the valve unit case portion 86c are placed on upper and lower sides of a filter attachment
area S (see Figs. 4 and 5) where the filter concave portion 88c and the screw hole
89c are provided. Further, the transmission cover 8b and the valve unit case portion
86c protrude or extend in an axial direction as compared with the filter attachment
area S (conversely, the filter attachment area S is placed in a depressed or hollow
position in the axial direction). As can be seen in Fig. 6, the filter attachment
area S has concave and convex surfaces, and a position in which the screw hole 89c
is provided protrudes in the axial direction as compared with a position in which
the filter concave portion 88c is provided.
[0027] As shown in Figs. 5 and 6, an oil inlet 60 and an oil outlet 61 open in an inside
of the filter concave portion 88c. Each of these oil inlet and outlet 60 and 61 communicates
with the oil passage Y formed in the transmission case 8c. With this, the oil flowing
in the oil passage Y flows into the filter concave portion 88c from the oil inlet
60, and flows out from the oil outlet 61 to the oil passage Y.
[0028] The oil inlet 60 opens at a side surface of the filter concave portion 88c, and the
oil outlet 61 opens at a bottom surface of the filter concave portion 88c. The oil
outlet 61 is formed at a top end of a tube part 62 that protrudes from the bottom
surface.
[0029] Returning to Fig. 2, the transmission cover 8b covers axial direction end surfaces
of the primary pulley 21 and the secondary pulley 22 of the CVT mechanism 20. The
transmission cover 8b forms the outer surface of the transmission casing 8 on a CVT
mechanism side. The transmission cover 8b is provided with a primary pulley bearing
81b for supporting the primary pulley 21, and also provided with a secondary pulley
bearing 82b for supporting the secondary pulley 22. Further, a primary pulley rotation
speed sensor KS1 that detects the number of revolutions of the primary pulley 21 and
a secondary pulley rotation speed sensor KS2 that detects the number of revolutions
of the secondary pulley 22 penetrate and are fixed to the transmission cover 8b.
[0030] On a circumferential edge portion of the transmission cover 8b, a contact surface
(not shown) that is contiguous with or touches the cover attachment surface 87c of
the transmission case 8c and a plurality of attachment screw penetration holes (not
shown) where the fixing screw N2 penetrates are provided. Additionally, as shown in
Figs. 4 and 6, the transmission cover 8b is provided, on the circumferential edge
portion, with an overhanging portion 83b that is positioned close to the filter concave
portion 88c of the transmission case 8c.
[0031] The overhanging portion 83b extends or sticks out along and over the outer surface
90c of the transmission case 8c with a clearance K (see Fig. 6) provided between the
outer surface 90c and the overhanging portion 83b.
[0032] The bearing retainer 8d is so fixed as to cover the concave portion 85c of the transmission
case 8c. The bearing retainer 8d is provided with an output shaft bearing 81d for
supporting the transmission output shaft 4 that is connected with and driven by the
multi-range transmission mechanism 30.
[0033] Next, the transmission mechanism TM will be explained. As shown in Figs. 1 and 2,
the transmission mechanism TM has a transmission gear mechanism 10, the CVT mechanism
20, the multi-range transmission mechanism 30, and a final drive gear mechanism 40.
[0034] The transmission gear mechanism 10 has a drive gear 11 that is secured to the output
shaft 2a of the torque converter 2 and a driven gear 12 that is secured to the input
shaft of the primary pulley 21 of the CVT mechanism 20. Here, a transmission ratio
is arbitrarily set by a gear ratio between the drive gear 11 and the driven gear 12.
[0035] The CVT mechanism 20 is an existing belt-drive CVT having the primary pulley 21,
the secondary pulley 22 and a belt 23 that is wound around these both pulleys 21 and
22. The driven gear 12 is secured to the input shaft of the primary pulley 21, and
the power from the transmission gear mechanism 10 is inputted to the primary pulley
21. An output shaft of the secondary pulley 22 connects with the multi-range transmission
mechanism 30 and drives the multi-range transmission mechanism 30. The primary pulley
21 and the secondary pulley 22 are each supplied with oil (fluid), and each pulley
width of the primary and secondary pulleys 21, 22 can be freely varied according to
their respective fluid pressures. In this CVT mechanism 20, by controlling these fluid
pressures supplied to the primary and secondary pulleys 21, 22, the transmission ratio
can be continuously varied.
[0036] The multi-range transmission mechanism 30 has a ravigneaux planetary gear mechanism.
As can be seen in Fig. 1, a combined sun gear 31 of the ravigneaux planetary gear
mechanism is connected to and driven by the secondary pulley 22 of the CVT mechanism
20, and the combined sun gear 31 acts as an input of the ravigneaux planetary gear
mechanism. A carrier 32 connects with and drives the transmission output shaft 4,
and the carrier 32 acts as an output of the ravigneaux planetary gear mechanism. The
combined sun gear 31 is fixed to the transmission casing 8 through a low brake (a
1
st speed selection brake) L/B. The carrier 32 meshes with and is driven by a ring gear
33 through a high clutch (a 2
nd speed selection clutch) H/C. Further, the ring gear 33 is fixed to the transmission
casing 8 through a reverse brake R/B.
[0037] In the multi-range transmission mechanism 30, the low brake L/B, the high clutch
H/C and the reverse brake R/B are also supplied with oil (fluid), and their engagement/disengagement
can be controlled according to the respective supplied fluid pressures. With this
fluid pressure control, the forward 1
st speed, the forward 2
nd speed and a reverse 1
st speed of the multi-range transmission mechanism 30 can be selected.
[0038] When selecting the forward 1
st speed, only the low brake L/B is engaged. When selecting the forward 2
nd speed, only the high clutch H/C is engaged. Further, when selecting the reverse 1
st speed, the reverse brake R/B is engaged. A relationship of the engagement/disengagement
of each brake and clutch L/B, H/C, R/B when controlling the multi-range transmission
mechanism 30 is shown in a following Table 1. In the table, "O" denotes "engagement",
"x" denotes "disengagement (release)".
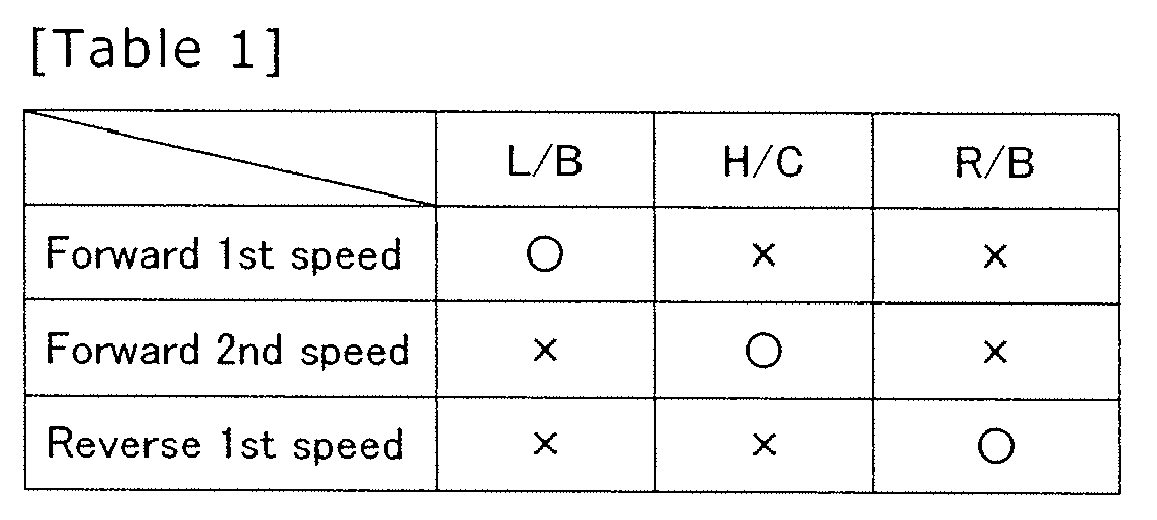
[0039] When carrying out gear shift in the multi-range transmission mechanism 30, by performing
a cooperative shift control between the CVT mechanism 20 and the multi-range transmission
mechanism 30, a shift shock is suppressed.
[0040] The final drive gear mechanism 40 has a drive gear 41 which is secured to the transmission
output shaft 4 protruding from the bearing retainer 8d toward the converter housing
8a and a driven gear 42 which is secured to the drive shaft 6a penetrating the converter
housing 8a and the transmission case 8c and connects with the wheels 6, 6 through
the drive shaft 6a. Here, a speed reduction ratio is arbitrarily set by a gear ratio
between the drive gear 41 and the driven gear 42.
[0041] In Fig. 2, reference sign 70 is an oil pump, reference sign 71 is a control valve
unit, reference sign 72 is an oil pan. The oil pump 70 is connected to the output
shaft 2a of the torque converter 2 through a chain CH, and is driven by rotation of
the output shaft 2a. The control valve unit 71 controls or regulates the oil (working
fluid) discharged from the oil pump 70 to a proper fluid pressure, and supplies it
to the transmission mechanism TM.
[0042] In Fig. 3, a schematic hydraulic circuit in the automatic transmission 3 is shown.
When the oil pump 70 is driven by the rotation of the output shaft 2a of the torque
converter 2, the oil stored in the oil pan 72 is pumped up by the oil pump 70 through
a strainer 70a and is supplied to the control valve unit 71. The oil supplied to the
control valve unit 71 is regulated to the proper fluid pressure, and supplied to the
primary pulley 21, the secondary pulley 22, the low brake L/B, the high clutch H/C,
the reverse brake R/B, a torque converter fluid pressure chamber (a torque converter
release pressure chamber) 2b and a lock-up fluid pressure chamber (a torque converter
applier chamber) 2c.
[0043] Remaining oil that is not supplied to each component (e.g. the pulley) from the control
valve unit 71 serves as lubricating oil, and is supplied to an oil cooler C, then
is cooled through a cooling medium such as cooling water. The oil cooled in the oil
cooler C is supplied to the oil filter F through the oil passage formed in the transmission
casing 8. The oil filter F filters out foreign matter or contaminant such as sputtering
residue and metal shavings (or filings). Part of the filtered oil is sprayed to each
part in the transmission casing 8 as casing-inside lubrication, and part of the filtered
oil is sprayed to the belt 23 of the CVT mechanism 20 as belt lubrication.
[0044] The filter case 50 has, as shown in Fig. 5 and 6, a closed-bottomed cylindrical-shaped
case body 51 whose one side opens, an O-ring (a seal member) 52 fitting onto an outer
circumference of the case body 51, a fixing brim portion (a first brim portion) 53
that sticks out from a case body outer circumferential surface 51a, and an inserting
brim portion (a second brim portion) 54.
[0045] The case body 51 has a cup-shape whose size allows the oil filter F to be inserted
into the case body. On an inner side of a bottom of the case body 51, a ring-shaped
protrusion 51b that touches the oil filter F is formed. Further, on the outer circumferential
surface 51a on the opening end side, an annular groove 51c into which the O-ring 52
fits is formed throughout an entire circumference of the outer circumferential surface
51a, close to the opening end. This opening end side is inserted into the filter concave
portion 88c.
[0046] The O-ring 52 is positioned between the oil inlet and outlet 60, 61 and an opening
of the filter concave portion 88c when the case body 51 is inserted into the filter
concave portion 88c, and seals a boundary between the case body outer circumferential
surface 51a inserted into the filter concave portion 88c and an inside surface of
the filter concave portion 88c. Here, by fitting the O-ring 52 into the annular groove
51c, movement or deviation in an axial direction, of the case body 51 is prevented.
[0047] The fixing brim portion 53 is provided with a screw penetration hole 53a where the
fixing screw N1 penetrates. As can be seen in Fig. 6, the fixing brim portion 53 touches
the outer surface 90c of the transmission case 8c when the case body 51 is inserted
into the filter concave portion 88c.
[0048] The inserting brim portion 54 is a plate portion that is inserted into the clearance
K between the transmission case 8c and the overhanging portion 83b with clearances
provided between the inserting brim portion 54 and the transmission case 8c and also
between the inserting brim portion 54 and the overhanging portion 83b, when the case
body 51 is inserted into the filter concave portion 88c. That is, a thickness of the
inserting brim portion 54 is set to be smaller (thinner) than the clearance K between
the outer surface 90c of the transmission case 8c and the overhanging portion 83b.
In addition, as shown in Figs. 7A and 7B, the inserting brim portion 54 is provided
with a whirl-stop protrusion (a rib) 54a which protrudes from the case body 51 in
the axial direction and touches a side surface of the overhanging portion 83b when
inserted into the clearance K.
[0049] The oil filter F is made of material such as nonwoven fabric whose both ends open
and which has a hollow cylindrical shape. Both opening ends of the oil filter F are
covered with a disc-shaped first cover member 55a and a disc-shaped second cover member
55b which are made of iron. These first and second cover members 55a and 55b prevent
the oil from being impregnated into the oil filter F from the both ends. The second
cover member 55b is provided with an opening portion 55c which faces or corresponds
to a center space of the oil filter F. Furthermore, a cylindrical packing 55d, both
ends of which open and one end of which is provided with a flange, is inserted into
the opening portion 55c. The flange portion of the cylindrical packing 55d touches
the second cover member 55b when the cylindrical packing 55d is inserted into the
opening portion 55c.
[0050] Regarding insertion of the oil filter F, as shown in Figs. 5 and 6, one end of the
oil filter F to which the first cover member 55a is attached is inserted toward the
bottom of the case body 51, then the oil filter F is inserted into the case body 51.
When inserted, the first cover member 55a touches the protrusion 51b, and space is
created between a circumferential surface of the oil filter F and an inner circumferential
surface of the case body 51. On the other hand, the other end of the oil filter F
to which the second cover member 55b is attached protrudes from the opening end of
the case body 51.
[0051] When the filter case 50 is fixed to the transmission case 8c, the tube part 62 protruding
from the bottom surface of the filter concave portion 88c is inserted into the center
space of the oil filter F. Here, the cylindrical packing 55d is previously inserted
into this center space through the opening portion 55c of the second cover member
55b. Because of this, the tube part 62 is inserted into the cylindrical packing 55d,
and a gap between the tube part 62 and the oil filter F is sealed with the cylindrical
packing 55d.
[0052] Next, operation or working will be explained. First, [Fixing structure of the related
art filter case and its problem] will be explained. Subsequently, operation or working
of the automatic transmission of the embodiment 1 will be explained in [Achievement
of prevention of oil leakage] and [Achievement of reduction of fixing points]
[0053] [Fixing structure of the related art filter case and its problem]
Figs. 8A and 8B are a sectional view and a top view of a fixing structure of the related
art filter case. In this fixing structure of the related art filter case, an oil passage
Y having an oil outlet 61 is formed in the transmission case TC, and a filter case
FC having therein an oil filter F is fixed to the transmission case TC so as to be
over this oil outlet 61 (or so as to cover this oil outlet 61). In addition, the filter
case FC is provided with an oil inlet 60, and the oil inlet 60 is connected to an
oil passage (not shown).
[0054] The filter case FC has a contact flange surface 100 that touches the transmission
case TC. This contact flange surface 100 is formed throughout an entire circumference
of an opening end of the filter case FC. Further, a plurality of bolt fixing holes
101 (in four positions in the drawing) are arranged at certain intervals so as to
surround the entire circumference of the filter case FC. The contact flange surface
100 is provided with a groove portion 102a into which an O-ring (a seal member) 102
fits.
[0055] The O-ring 102 fitting into the groove portion 102a is in absolute contact with the
transmission case TC when the filter case FC is fixed to the transmission case TC,
and seals a contact surface between the transmission case TC and the filter case FC.
[0056] On the other hand, fixing bolts B are inserted into the bolt fixing holes 101 and
screwed, then the filter case FC is fixed to the transmission case TC. With a fixing
force by the plurality of fixing bolts B, i.e. with a pressing force that acts on
the filter case FC by the fixing bolts B, a sealing performance by the O-ring 102
is secured.
[0057] This fixing structure of the related art filter case is configured so that the oil
flowing into the filter case FC from the oil inlet 60 formed in the filter case FC
is impregnated into the oil filter F and flows out to the oil passage Y formed in
the transmission case TC from the oil outlet 61 that is inserted into a center space
of the oil filter F.
[0058] In this fixing structure of the related art filter case, because the filter case
FC is fixed to the transmission case TC with the plurality of fixing bolts B arranged
so as to surround the entire circumference of the filter case FC, there is a need
to secure space for arranging each fixing bolt B around the filter case FC, and there
is a problem that an installation position of the filter case FC is limited. Furthermore,
because the contact surface between the transmission case TC and the filter case FC
is sealed, if asperities exist on the contact surface, it is difficult to secure the
sealing performance. For this reason, in this case, it is required that the contact
surface be flat.
[0059] That is to say, the fixing structure of the related art filter case requires not
only the annular flat surface on the transmission case TC side which is in absolute
contact with the contact flange surface 100 of the filter case FC, but also the space
that allows the fixing bolts B to be arranged at constant intervals around its entire
circumference is needed. For this reason, a problem that size reduction of the transmission
casing is difficult arises.
[0060] Moreover, if looseness of any of the plurality of fixing bolts B that secure the
filter case FC to the transmission case TC occurs, the pressing force which acts on
the contact surface between the transmission case TC and the filter case FC and presses
the O-ring 102 against the transmission case TC decreases. The sealing performance
by this O-ring 102 is therefore decreased, and there is a risk that the oil leakage
from the contact surface will occur. Further, if the oil leakage occurs, an oil quantity
in the automatic transmission 3 will be reduced and reduction in the fluid pressure
will arise, and this might cause a situation where a vehicle is unable to travel.
[0061] [Achievement of prevention of oil leakage] In the automatic transmission 3 in the
embodiment 1, the oil, which flows into the filter concave portion 88c from the oil
inlet 60 formed in the transmission case 8c, is impregnated into the oil filter F
from the outer circumferential surface of the oil filter F toward the center space,
and flows out to the oil passage Y from the oil outlet 61. With this oil flow, the
oil is filtered by the oil filter F.
[0062] As explained above, the filter case 50 into which the oil filter F is inserted is
inserted into the filter concave portion 88c, and the boundary between the case body
outer circumferential surface 51a and the inside surface of the filter concave portion
88c is sealed with the O-ring 52 fitting into the annular groove 51c formed on the
outer circumferential surface 51a of the case body 51. With this, the oil leakage
from a contact surface between the filter case 50 and the transmission case 8c is
prevented. Here, the sealing performance by the O-ring 52 is secured by a difference
in dimension between an outside diameter of the case body 51 and an inside diameter
of the filter concave portion 88c.
[0063] Further, since the sealing performance by the O-ring 52 is secured by the difference
in dimension between the outside diameter of the case body 51 and the inside diameter
of the filter concave portion 88c, for example, even if the case body 51 rattles,
the sealing performance by the O-ring 52 between the case body outer circumferential
surface 51a and the inside surface of the filter concave portion 88c is not impaired.
Thus, regardless of the rattling of the case body 51, the sealing performance can
be secured, and the oil leakage from the contact surface between the filter case 50
and the transmission case 8c can surely be prevented.
[0064] Furthermore, in the automatic transmission 3 in the embodiment 1, the O-ring 52 is
positioned between the opening of the filter concave portion 88c and the oil inlet
and outlet 60, 61 which communicate with this filter concave portion 88c when the
filter case 50 is inserted into the filter concave portion 88c.
[0065] With this, the leakage of the oil flowing into the filter concave portion 88c from
the oil inlet 60 and flowing out from the oil outlet 61 through the oil filter F,
from the contact surface between the filter concave portion 88c and the filter case
50 can surely be prevented.
[0066] [Achievement of reduction of fixing points] In the automatic transmission 3 in the
embodiment 1, in order to fix the filter case 50 to the transmission case 8c, first,
the oil filter F is attached to the filter concave portion 88c of the transmission
case 8c. At this time, the first and second cover members 55a and 55b are previously
attached to the both ends of the oil filter F, also the cylindrical packing 55d is
previously inserted into the opening portion 55c of the second cover member 55b. And
the tube part 62 protruding from the bottom surface of the filter concave portion
88c is inserted into the cylindrical packing 55d, then the oil filter F is fixed in
the filter concave portion 88c.
[0067] Next, the oil filter F fixed in the filter concave portion 88c is covered by the
filter case 50. At this time, the O-ring 52 is previously fitted into the annular
groove 51c of the case body 51 of the filter case 50. And the opening end of the case
body 51 is inserted into the filter concave portion 88c, then the oil filter F is
covered by the filter case 50. Here, when the filter case 50 covers the oil filter
F, the ring-shaped protrusion 51b touches the first cover member 55a, and this prevents
the first cover member 55a from floating.
[0068] Further, when covering the oil filter F by the filter case 50, as shown in Fig. 9,
the inserting brim portion 54 of the filter case 50 is set so as not to overlap with
the overhanging portion 83b of the transmission cover 8b. In this positioning, a position
of the screw hole 89c formed on the transmission case 8c and a position of the screw
penetration hole 53a formed on the fixing brim portion 53 do not match.
[0069] When rotating the filter case 50 in a direction indicated by arrows in Fig. 9 about
the case body 51, the position of the screw hole 89c formed on the transmission case
8c and the position of the screw penetration hole 53a formed on the fixing brim portion
53 match, and also the inserting brim portion 54 is inserted into the clearance K
between the transmission case 8c and the overhanging portion 83b. As mentioned above,
since the inserting brim portion 54 is provided with the whirl-stop protrusion 54a
protruding from the case body 51 in the axial direction and this whirl-stop protrusion
54a touches the overhanging portion 83b, an extra rotation of the case body 51 is
prevented, and the position of the screw hole 89c and the position of the screw penetration
hole 53a can easily match. In addition, since the inserting brim portion 54 inserted
into the clearance K between the transmission case 8c and the overhanging portion
83b is set with the clearances provided between the inserting brim portion 54 and
the transmission case 8c and also between the inserting brim portion 54 and the overhanging
portion 83b (i.e. with the clearances provided above the transmission case 8c and
also below the overhanging portion 83b), the inserting brim portion 54 can be inserted
smoothly.
[0070] Finally, the fixing screw N1 is inserted into the screw penetration hole 53a and
is screwed into the screw hole 89c. With this, the filter case 50 is fixed to the
transmission case 8c, and the filter case 50 does not fall out and does not rotate
about the case body 51.
[0071] On the other hand, after the inserting brim portion 54 is inserted between the transmission
case 8c and the overhanging portion 83b, the inserting brim portion 54 overlaps with
the overhanging portion 83b in the axial direction of the case body 51. Therefore,
for instance, even if the fixing screw N1 loosens or comes out, the inserting brim
portion 54 interferes with the overhanging portion 83b, and the movement in the axial
direction of the case body 51 can be prevented, namely that the case body 51 can be
prevented from falling out of the filter concave portion 88c.
[0072] With respect to the sealing performance, since the sealing performance by the O-ring
52 is secured by the difference in dimension between the outside diameter of the case
body 51 and the inside diameter of the filter concave portion 88c, when preventing
the case body 51 from falling out of the filter concave portion 88c, the sealing performance
can be secured. That is, the sealing performance by the O-ring 52 does not depend
on the pressing force of the filter case 50 against the transmission case 8c.
[0073] As explained above, there is no need to press the filter case 50 against the transmission
case 8c, and when preventing the case body 51 from falling out of the filter concave
portion 88c, the sealing performance can be secured. Thus, the fixing brim portion
53 is not required to be arranged throughout the entire circumference of the filter
case 50. This can achieve the reduction of the fixing points, and even when an installation
space of the filter case 50 is narrow, it is possible to install the filter case 50.
[0074] In particular, in the case of the automatic transmission 3 in the embodiment 1, as
shown in Figs. 4 and 5, the filter attachment area S is located between the transmission
cover 8b and a control valve case (the valve unit case portion) 86c, and further the
filter attachment area S is located in the depressed or hollow position in the axial
direction as compared with the transmission cover 8b and the control valve case 86c.
Because of this, the filter attachment area S is extremely narrow. Besides, it is
difficult to secure space where tools used for fixing the filter case 50 are inserted.
[0075] However, in the automatic transmission 3 in the embodiment 1, as described above,
since the fixing point of the filter case 50 is only the fixing brim portion 53, even
though the filter attachment area S is narrow, the filter case 50 can be easily fixed.
[0076] Further, even if the fixing screw N1 loosens and the filter case 50 moves in the
axial direction, the inserting brim portion 54 interferes with the overhanging portion
83b, and the case body 51 is prevented from falling out of the filter concave portion
88c. As a consequence, reduction in the sealing performance does not occur, and an
undesirable situation where the fluid pressure is decreased and the vehicle is unable
to travel can be prevented.
[0077] Furthermore, in the automatic transmission 3 in the embodiment 1, the thickness of
the inserting brim portion 54 that serves to prevent the filter case 50 from falling
out in the axial direction is set to be smaller (thinner) than the clearance K into
which this inserting brim portion 54 is inserted. Thus, even in a case where a dimension
error occurs in the clearance K and the inserting brim portion 54 or an assembly error
occurs, it is possible to surely insert the inserting brim portion 54 into the clearance
K.
[0078] Moreover, in the automatic transmission 3 in the embodiment 1, as shown in Fig. 7B,
the fixing brim portion 53 and the inserting brim portion 54 are positioned on substantially
opposite sides of a center of the case body 51 and protrude in the substantially opposite
directions. With this structure, well-balanced installation of the case body 51 is
achieved, which prevents the falling out of the case body 51. Also, even though the
fixing point is reduced, this structure reduces a tendency for the case body 51 to
come off (or to fall out).
[0079] In addition, in the automatic transmission 3 in the embodiment 1, since the whirl-stop
protrusion 54a serving as a rotation stopper of the case body 51 is formed on the
inserting brim portion 54, the position of the screw hole 89c formed on the transmission
case 8c and the position of the screw penetration hole 53a formed on the fixing brim
portion 53 can easily match. This facilitates the attachment of the filter case 50.
[0080] Next, effects of the present invention will be explained. In the automatic transmission
of the embodiment 1, the following effects can be obtained.
[0081] (1) The automatic transmission 3 has: the transmission casing 8 which houses therein
the transmission mechanism TM, the transmission casing 8 having: (a) the concave portion
88c with which at least the oil inlet 60 or the oil outlet 61 communicates at the
inside of the concave portion (the filter concave portion) 88c; and (b) the overhanging
portion 83b which is positioned close to the concave portion 88c and extends along
the surface (the outer surface) 90c of the transmission casing 8 with the clearance
K provided between the outer surface 90c and the overhanging portion 83b, and the
filter case 50 which is attached to the transmission casing 8 and has therein the
oil filter F, the filter case 50 having; (c) the case body 51 which is inserted into
the concave portion 88c; (d) the seal member (the O-ring) 52 which fits onto the outer
circumference of the case body 51 and seals the boundary between the outer circumferential
surface 51a of the case body 51 inserted into the concave portion 88c and the inside
surface of the concave portion 88c; (e) the first brim portion (the fixing brim portion)
53 which protrudes from the outer circumferential surface 51a of the case body 51
and is fixed to the outer surface 90c of the transmission casing 8; and (f) the second
brim portion (the inserting brim portion) 54 which protrudes from the outer circumferential
surface 51a of the case body 51 and is inserted into the clearance K.
With this, it is possible to reduce the fixing points of the filter case 50 while
securing the sealing performance between the transmission casing 8 and the filter
case 50.
[0082] (2) The thickness of the second brim portion (the inserting brim portion) 54 is set
to be thinner than the clearance K.
With this, even in a case where the dimension error or an assembly error occurs, it
is possible to surely insert the second brim portion (the inserting brim portion)
54 into the clearance K, and performance of assembly of the filter case 50 can be
improved.
[0083] (3) The seal member (the O-ring) 52 is positioned between the opening of the concave
portion 88c and the oil inlet 60 or the oil outlet 61 communicating with the concave
portion 88c.
With this, the sealing performance between the transmission casing 8 and the filter
case 50 can be secured.
[0084] (4) The first brim portion (the fixing brim portion) 53 and the second brim portion
(the inserting brim portion) 54 are positioned on substantially opposite sides of
the center of the case body 51 and protrude in substantially opposite directions.
With this, despite less fixing point of the filter case 50, the filter case 50 can
be fixed with stability.
[0085] (5) The second brim portion (the inserting brim portion) 54 has the rib (the whirl-stop
protrusion) 54a that serves as a rotation stopper of the case body 51 by touching
the overhanging portion 83b of the transmission casing 8 when the filter case 50 is
rotated.
With this, the extra rotation of the case body 51 is prevented when fixing the filter
case 50 in assembly, and this facilitates the attachment of the filter case 50.
[0086] Although the present invention has been described above, it is not limited to the
above embodiment.
[0087] In the automatic transmission 3 in the embodiment 1, the overhanging portion 83b
is provided on the circumferential edge portion of the transmission cover 8b. However,
instead of the overhanging portion 83b, for instance, a part of the transmission case
8c or a part of the control valve case 86c could be the overhanging portion.
[0088] Further, in the automatic transmission 3 in the embodiment 1, as the seal member
that fits onto the outer circumference surface of the filter case 50, the O-ring 52
is used. However, instead of the O-ring 52, an annular lip packing, which has a pressure-receiving
surface (an inner circumferential surface of the filter concave portion 88c) side
lip structure, could be employed.
[0089] Furthermore, in the automatic transmission 3 in the embodiment 1, one fixing brim
portion 53 and one inserting brim portion 54 are provided. In the present invention,
at least one fixing brim portion and at least one inserting brim portion are needed.
Therefore, two or more fixing brim portion and two or more inserting brim portion
might be provided, depending on the installation position of the filter case 50.
[0091] Although the invention has been described above by reference to certain embodiments
of the invention, the invention is not limited to the embodiments described above.
Modifications and variations of the embodiments described above will occur to those
skilled in the art in light of the above teachings. The scope of the invention is
defined with reference to the following claims.