[0001] L'invention concerne un procédé de production d'essence à faible teneur en soufre
comprenant au moins une étape de transformation des composés soufrés consistant en
une alkylation des composés soufrés, au moins un fractionnement de l'essence obtenue
à l'étape A en au moins deux fractions, au moins une étape de traitement en présence
d'un catalyseur acide et au moins un traitement de désulfuration d'au moins une partie
de la fraction lourde. Ce procédé permet de valoriser une coupe essence comprenant
éventuellement en outre des hydrocarbures à deux trois ou quatre atomes de carbone,
en réduisant la teneur en soufre total de ladite coupe à de très faibles niveaux compatibles
avec les spécifications actuelles ou à venir. Cette désulfuration est par ailleurs
effectuée sans diminution sensible du rendement en essence et en minimisant la diminution
de l'indice d'octane.
Art antérieur :
[0002] La production d'essences reformulées répondant aux nouvelles normes d'environnement
nécessite notamment que l'on diminue faiblement leur concentration en oléfines mais
de façon importante leur concentration en aromatique (surtout le benzène) et en soufre.
Les essences de craquage catalytique, qui peuvent représenter 30 à 50 % du pool essence,
présentent des teneurs en oléfines et en soufre élevées. Le soufre présent dans les
essences reformulées est imputable, à près de 90 %, à l'essence de craquage catalytique
(FCC, « Fluid Catalytic Cracking » ou craquage catalytique en lit fluidisé). La désulfuration
(l'hydrodésulfuration) des essences et principalement des essences de FCC est donc
d'une importance évidente pour l'atteinte des spécifications.
[0003] L'hydrotraitement (hydrodésulfuration) de la charge envoyée au craquage catalytique
conduit à des essences contenant typiquement 100 ppm de soufre. Les unités d'hydrotraitement
de charges de craquage catalytique opèrent cependant dans des conditions sévères de
température et de pression, ce qui suppose une consommation importante d'hydrogène
et un investissement élevé. De plus, la totalité de la charge doit être désulfurée,
ce qui entraîne le traitement de volumes de charge très importants.
[0004] L'hydrotraitement (ou hydrodésulfuration) des essences de craquage catalytique, lorsqu'il
est réalisé dans des conditions classiques connues de l'homme du métier permet de
réduire la teneur en soufre de la coupe. Cependant, ce procédé présente l'inconvénient
majeur d'entraîner une chute très importante de l'indice d'octane de la coupe, en
raison de la saturation de l'ensemble des oléfines au cours de l'hydrotraitement.
[0005] D'autre part, le brevet
US-A- 4 131 537 enseigne l'intérêt de fractionner l'essence en plusieurs coupes, de préférence trois,
en fonction de leur point d'ébullition, et de les désulfurer dans des conditions qui
peuvent être différentes et en présence d'un catalyseur comprenant au moins un métal
du groupe VIB et/ou du groupe VIII. Il est indiqué dans ce brevet que le plus grand
bénéfice est obtenu lorsqu'on fractionne l'essence en trois coupes, et lorsque la
coupe présentant des points d'ébullition intermédiaires est traitée dans des conditions
douces.
[0006] La demande de brevets
EP-A-0 755 995 décrit un procédé de désulfuration d'essences de FCC comprenant au moins deux étapes.
La première est une hydrodésulfuration catalytique à une température comprise entre
200 et 350°C, avec un taux de désulfuration compris entre 60 et 90 % et est effectuée
en présence d'une charge contenant moins de 0,1 % en volume de sulfure d'hydrogène
(H2S). La deuxième, ainsi qu'éventuellement les suivantes, sont également des étapes
d'hydrodésulfuration catalytique opérées entre 200 et 300°C et en présence d'une charge
comprenant moins de 0,05 % en volume d'H2S. Le taux de désulfuration est compris entre
60 et 90 % dans cette étape. Dans ce procédé, la concentration en H2S doit être maintenue
à un niveau très faible. En cas de recyclage de l'hydrogène excédentaire il est donc
en général nécessaire d'éliminer l'H2S, par exemple au moyen d'une étape d'absorption
aux amines, après la deuxième étape et les suivantes, afin que le gaz de recycle convienne
moins de 0,1 % volume d'H2S. Il est également préféré d'éliminer l'H2S entre la première
et la deuxième étape afin de respecter la teneur maximale en H2S en entrée de la deuxième
étape (0,05 % volume). Pour les essences chargées en soufre, une telle élimination
est donc nécessaire compte tenu du taux de desulfuration supérieur à 60 % en première
étape
[0007] La demande de brevet
EP-A-0 725 126 décrit un procédé d'hydrodésulfuration d'une essence de craquage dans lequel l'essence
est séparée en une pluralité de fractions comprenant au moins une première fraction
riche en composés faciles à désulfurer et une seconde fraction riche en composés difficiles
à désulfurer. Avant d'effectuer cette séparation, il faut au préalable déterminer
la distribution des composés soufrés au moyen d'analyses. Ces analyses sont nécessaires
pour sélectionner l'appareillage et les conditions de séparation.
[0008] Dans cette demande il est ainsi indiqué qu'une fraction légère d'essence de craquage
voit sa teneur en oléfines et son indice d'octane chuter de manière importante lorsqu'elle
est désulfurée sans être fractionnée. Par contre, le fractionnement de ladite fraction
légère en 7 à 20 fractions suivi d'analyses des teneurs en soufre et en oléfines de
ces fractions permet de déterminer la ou les fractions les plus riches en composés
soufrés qui sont ensuite désulfurées simultanément ou séparément et mélangées aux
autres fractions désulfurées ou non. Une telle procédure est complexe et doit être
reproduite à chaque changement de la composition de l'essence à traiter.
[0009] Dans le brevet français
2 785 908, il est enseigné l'intérêt de fractionner l'essence en une fraction légère et une
fraction lourde puis d'effectuer un hydrotraitement spécifique de l'essence légère
sur un catalyseur à base de nickel, et un hydrotraitement de l'essence lourde sur
un catalyseur comprenant au moins un métal du groupe VIII et/ou au moins un métal
du groupe VIb.
[0010] Il a également été proposé, par exemple dans le brevet
US-A-5 290 427, des procédés d'hydrotraitement des essences consistant à fractionner l'essence,
puis à introduire les fractions à différents niveaux d'un réacteur d'hydrodésulfuration
et à convertir les fractions désulfurées sur une zéolithe ZSM-5, afin de compenser
la perte d'octane enregistrée au moyen d'une isomérisation. Cette isomérisation est
accompagnée d'un craquage de l'essence vers des composés plus légers.
[0011] Dans ces procédées, les essences à traiter présentent en général un point initial
supérieur à 70°C, et il est nécessaire de traiter séparément l'essence légère (fraction
correspondant aux composés de point d'ébullition compris entre les C5 hydrocarbures
à 5 atomes de carbone et 70°C) par exemple au moyen d'un adoucissement.
[0012] Le brevet
US-A-5 318 690 propose un procédé comprenant un fractionnement de l'essence et un adoucissement
de l'essence légère, tandis que l'essence lourde est désulfurée, puis convertie sur
une zéolithe ZSM-5 et désulfurée à nouveau dans des conditions douces. Cette technique
est basée sur une séparation de l'essence brute de façon à obtenir une coupe légère
de préférence pratiquement dépourvue de composés soufrés autres que les mercaptans.
Ceci permet de traiter ladite coupe uniquement au moyen d'un adoucissement qui enlève
les mercaptans.
[0013] De ce fait, les oléfines, présentes en quantité relativement importante dans la coupe
lourde, sont en partie saturées lors de l'hydrotraitement. Pour compenser la chuté
de l'indice d'octane liée à l'hydrogénation des oléfines, le brevet préconise un craquage
sur zéolithe ZSM-5 qui produit des oléfines, mais au détriment du rendement. De plus,
ces oléfines peuvent se recombiner avec l'H
2S présent dans le milieu pour reformer des mercaptans. Il est alors nécessaire d'effectuer
un adoucissement ou une hydrodésulfuration supplémentaire.
[0014] La demande de brevet
WO 00/15319 décrit un procédé permettant de réaliser simultanément le fractionnement et le traitement
d'un naphta léger. Dans ce procédé, la coupe lègère contient des mercaptans allant
généralement du methyl-mercaptan aux hexyl-mercaptan. Ces composés soufrés ne sont
éliminés de la fraction légère que dans le cas où la colonne de fractionnement contient
une section d'hydrodésulfuration en tête de colonne. En l'absence de cette section,
il n'est donc pas possible d'éliminer les mercaptans qui soit se retrouvent dans l'essence
désulfurée lorsque la fraction légère est recombinée avec la fraction lourde désulfurée,
soit peuvent être éliminés avec l'ensemble de la fraction légère, ce qui engendre
une perte du rendement en essence après désulfuration.
[0015] Le brevet
US 6,083,379 décrit un procédé de déulfuration et d'amélioration de l'indice d'octane des essences
comprenant un fractionnement de l'essence en au moins deux coupes, le traitement de
la fraction légère en présence d'une zéolithe, un fractionnement de la fraction lègère
ainsi traitée, le mélange des fractions lourdes obtenues lors des deux étapes de fractionnement
et l'hydrodésulfuration du mélange de ces fractions.
[0016] La demande de brevet
WO 94/22980 décrit un procédé de désulfuration d'essence comprenant un fractionnement en deux
coupes, la coupe la plus lourde est désulfurée dans un réacteur d'hydrodésulfuration
puis traitée en présence d'un catalyseur acide qui permet de compenser la perte d'octane.
La coupe la plus légère est également désulfurée au moyen d'une extraction non-hydrogénante
des mercaptans.
[0017] Le brevet
US 5,968,346 décrit un procédé d'hydroconversion d'une charge hydrocarbonnée, permettant d'enlever
des impuretés telles que des composés comprenant des hétéroatomes. Ce procédé comprend
une première étape d'hydroconversion de l'ensemble de la charge, suivie d'une séparation
du liquide et de la vapeur présents dans l'effluent de cette première étape et d'un
contactage du gaz avec un liquide. Le mélange des deux fractions liquides issues du
contactage et du fractionnement est ensuite traité dans une seconde étape d'hydroconversion
en présence d'un catalyseur.
Résumé de l'invention :
[0018] La présente invention concerne un procédé de production d'essences à faible teneur
en soufre, qui permet de valoriser la totalité d'une coupe essence contenant du soufre,
de préférence une coupe essence de craquage catalytique ou de cokage (coking selon
la terminologie anglosaxonne), ou de pyrolyse, ou encore de viscoréduction (visbreaking
selon la terminologie anglosaxonne), et de réduire les teneurs en soufre dans ladite
coupe essence à de très faibles niveaux, sans diminution sensible du rendement en
essence tout en minimisant la diminution de l'indice d'octane due à l'hydrogénation
des oléfines. La charge du procédé selon l'invention peut également éventuellement
comprendre en plus d'une coupe essence, une coupe C4
- comprenant des hydrocarbures à deux, trois ou quatre atomes de carbone.
[0019] Le procédé selon l'invention est un procédé de production d'essence à faible teneur
en soufre, à partir d'une coupe essence contenant du soufre (essence initiale). Il
comprend au moins les étapes suivantes:
A) au moins une étape de transformation des composés soufrés présents dans l'essence.
Dans le procédé selon l'invention, l'étape de transformation des composés soufrés
est une étape d'alkylation des composés soufrés choisis dans le groupe constitué par
le thiophène, les composés thiophéniques et les mercaptans, de préférence les mercaptans
ayant 1 à 6 atomes de carbone. Cette étape A est disposée avant l'étape E décrite
ci-après.
B) au moins une étape de traitement en présence d'un catalyseur acide située avant
l'étape A ou avant ou après les étapes C, ou D et après l'étape E, éventuellement
simultanément à l'étape C. Le traitement en présence d'un catalyseur acide permet
d'obtenir un effluent présentant un indice d'octane plus élevée que la charge de cette
étape. Les réactions qui interviennent au cours de cette étape sont essentiellement
des réactions de craquage et/ou d'isomérisation qui conduisent à des oléfines ou des
paraffines branchés contribuant à une augmentation de l'indice d'octane. Tout type
de catalyseur acide peut éventuellement être utilisé, mais on emploiera de préférence
un catalyseur comprenant un alumino-silicate et de manière plus préférée une zéolithe.
C) au moins un traitement de désulfuration d'au moins une partie de l'essence traitée
à l'étape B, ou fractionnée à l'étape E ou hydrogénée à l'étape D en présence d'au
moins un catalyseur d'hydrodésulfuration.
E) au moins un fractionnement de l'essence obtenue à l'étape A en au moins deux fractions
(ou coupes), une fraction légère de préférence pratiquement dépourvue de soufre et
contenant les oléfines les plus légères de l'essence initiale (essence légère ou fraction
légère), et une fraction lourde dans laquelle de préférence la majeure partie des
composés soufrés initialement présents dans l'essence initiale est concentrée (essence
ou fraction lourde). Il est également possible de séparer l'essence obtenue à l'étape
A en plus de deux fractions, c'est-à-dire par exemple une fraction légère, au moins
une fraction intermédiaire et une fraction lourde.
[0020] Le procédé selon l'invention peut également comprendre en outre :
D) éventuellement au moins une hydrogénation sélective des dioléfines située avant
ou après les étapes A, B, ou E.
F) éventuellement une étape de mélange de la fraction légère obtenue après l'une des
étapes D ou E et éventuellement d'au moins une fraction intermédiaires issue de l'une
des étapes B, C ou E avec la fraction lourde désulfurée issue de l'une des étapes
B, C,ou E. Dans cette étape, de préférence, la totalité de ladite fraction lourde
désulfurée est mélangée à ladite fraction légère, sans séparation du liquide et du
gaz contenu dans l'essence lourde après désulfuration, éventuellement un simple strippage
par un gaz inerte peut être effectué pour éliminer l'H2S de l'essence lourde totalement
désulfurée. Dans certains cas spécifiques, la valorisation de l'essence légère, de
l'essence lourde désulfurée, et éventuellement d'au moins une essence intermédiaire,
s'effectue de manière séparée. Il est alors inutile de réaliser cette étape F.
[0021] La charge du procédé selon l'invention est une coupe essence contenant du soufre,
de préférence une coupe essence issue d'une unité de craquage catalytique, de cokage
ou de viscoréduction ou de pyrolyse, dont la gamme de points d'ébullition s'étend
typiquement depuis environ les points d'ébullitions des hydrocarbures à 2 ou 3 atome
de carbone (C2 ou C3) jusqu'à environ 250°C, de préférence depuis environ les points
d'ébullitions des hydrocarbures à 5 atomes de carbone (C2 ou C3) jusqu'à environ 220°C.
Le point final de la coupe essence dépend de la raffinerie dont elle est issue et
des contraintes du marché, mais reste généralement dans les limites indiquées ci-avant.
Description détaillée l'invention
[0022] Il est décrit dans la présente invention un procédé permettent l'obtention d'une
essence préférentiellement issue d'une unité de craquage catalytique; de cokage ou
de viscoréduction ou de pyrolyse et présentant une teneur en soufre limitée. Ledit
procédé comprend au moins une étape de transformation des composés soufrés consistant
en une alkylation, au moins un fractionnement de l'essence obtenue en au moins deux
fractions : essence légère et essence lourde, au moins une étape de traitement en
présence d'un catalyseur acide et aux moins un traitement due désulfuration d'au moins
une partie de l'essence. Le procédé selon l'invention peut également comprendre éventuellement
au moins une étape d'hydrogénation sélective des dioléfines.
[0023] La présence simultanée des étapes A de transformation des composés soufrés et B de
traitement acide permet d'obtenir à l'étape C une désulfuration très poussée de l'essence
sans diminution excessive du rendement en essence et tout en maintenant un indice
d'octane élevé.
[0024] Grâce à ce procédé, des taux de désulfuration importants sont atteints, dans des
conditions opératoires raisonnables précisées ci-après. Le point de fractionnement
de l'essence est de préférence limité afin de limiter la présence de composés soufrés,
notamment des composés thiophèniques dans l'essence légère. En particulier, le thiophène
qui forme des azéotropes avec un certain nombre d'hydrocarbures, ne peut pas être
facilement séparé des oléfines en C5 et/ou C6.
[0025] Un fractionnement est présent, pour permettre de recouvrer une fraction légère comprenant
une proportion importante des oléfines légères présentes dans l'essence tout en limitant
la teneur en soufre de cette friction, il est préféré de traiter la charge dans des
conditions et sur des catalyseurs qui permettent de transformer les composés soufrés
(étape A). Ainsi, les composés soufrés légers et/ou thiophèniques peuvent être transformés
en composés soufrés de point d'ébullition plus élevés se retrouvant après la séparation
dans au moins une fraction intermédiaire ou dans l'essence lourde. Ces coupes intermédiaires
et/ou lourde peuvent ensuite être aiséments désulfurées.
[0026] L'hydrotraitement des essences et en particulier l'hydrodésulfuration s'effectue
en présence d'hydrogène dans des conditions telles qu'au moins une partie des oléfines
présentes dans la charge à hydrotraiter sont hydrogénées. Ceci entraine une chute
plus ou moins importante de l'indice d'octane de la coupe essence. Le procédé selon
l'invention permet au moyen de l'étape A de limiter la teneur en composés soufrés
dans la fraction légère de la charge. Il permet donc d'éviter l'hydrodésulfuration
de cette fraction. Toutefois, il est parfois préféré de ne traiter que certaines coupes
issues du fractionnement. De plus, il reste des oléfines dans les fractions intermédiaires
et lourdes de l'essence qui peuvent être hydrogénées lors de l'étape de désulfuration.
Pour toutes ces raisons, lorsqu'un indice d'octane très élevé est recherché, il est
interessant de compenser la diminution de l'indice d'octane enregistrée lors de la
désulfuration au moyen d'une étape de traitement acide en présence d'un catalyseur
acide, tel que par exemple une zéolithe.
[0027] La teneur en soufre des coupes essences produites par craquage catalytique (FCC)
dépend de la teneur en soufre de la chargé traitée au FCC, de la présence ou non d'un
prétraitement de la charge du FCC, ainsi que du point final de la coupe. Généralement,
les teneurs en soufre de l'intégralité d'une coupe essence, notamment celles provenant
du FCC, sont supérieures à 100 ppm en poids et la plupart du temps-supérieures à 500
ppm en poids. Pour des essences ayant des points finaux supérieurs à 200°C, les teneurs
en soufre sont souvent supérieures à 1000 ppm en poids, elles peuvent même dans certains
cas atteindre des valeurs de l'ordre de 4000 à 5000 ppm en poids.
[0028] Lé procédé selon l'invention s'applique notamment lorsque des taux de désulfuration
élevés des l'essence sont requis, c'est à dire lorsque l'essence désulfurée doit contenir
au plus 10 % du soufre de l'essence initiale et éventuellement au plus 5 % voire au
plus 2 % du soufre de l'essence initiale ce qui correspond à des taux de désulfuration
supérieurs à 90 % voire supérieurs à 95 ou encore supérieur à 98 %.
[0029] Il s'applique plus particulièrement lorsque ces taux de désulfuration doivent être
obtenus tout en limitant la diminution des indices d'octane recherche et moteur. Ainsi,
les indices d'octane recherche et moteur (octane numbér selon la terminologie anglosaxone
et ci-après appelés ON) de l'essence obtenue après traitement au moyen du procédé
selon l'invention ont une valeur généralement proche ou supérieure de celle de l'essence
non-traité. De manière préférée, l'essence issue du procédé selon l'invention présente
un indice d'octane recherche ou moteur tel que ON ≥ (ON)
O-1, de manière plus préférée ON ≥ (ON)
O-0,7, de manière très préférée ON ≥ (ON)
O-0,5, et de manière encore plus préférée ON ≥ (ON)
O, (ON)
O représentant la valeur de l'indice d'octane recherche ou moteur de la charge (essence
initiale ou non-traitée).
[0030] Le procédé selon l'invention comprend au moins les étapes suivantes:
A) Cette étape consiste en au moins une étape de transformation des composés soufrés
présents dans l'essence. Dans le procédé selon l'invention, l'étape de transformation
des composés soufrés est une étape d'alkylation des composés soufrés choisis dans
le groupe constitué par le thiophène, les composés thiophéniques et les mercaptans,
de préférence les mercaptans ayant 1 à 6 atomes de carbone. Cette étape A est disposée
avant l'étape E et avant l'étape C de désulfuration.
B) au moins une étape de traitement en présence d'un catalyseur acide située avant
l'étape A ou avant ou après les étapes C, ou D et aprés l'étape E éventuellement réalisée
simultanément à l'étape C. Le traitement en présence d'un catalyseur acide permet
d'obtenir un effluent présentant un indice d'octane plus élevée que la charge de cette
étape. Les réactions qui interviennent au cours de cette étape sont essentiellement
des réactions de craquage et/ou d'isomérisation qui conduisent à des oléfines ou des
paraffines branchés contribuant à une augmentation de l'indice d'octane. Tout type
de catalyseur acide peut éventuellement être utilisé, mais on emploiera de préférence
un catalyseur comprenant un alumino-silicate et de manière plus préférée une zéolithe.
C) au moins un traitement de désulfuration d'au moins une partie de l'essence traitée
à l'étape B, ou fractionnée à l'étape E ou hydrogénée à l'étape D en présence d'au
moins un catalyseur d'hydrodésulfuration.
E) au moins un fractionnement de l'essence initiale, ou de l'essence obtenue à l'étape
A ou B ou D, en au moins deux fractions (ou coupes), une fraction légère de préférence
pratiquement dépourvue de soufre et contenant les oléfines les plus légères de l'essence
initiale (essence légère ou fraction légère), et une fraction lourde dans laquelle
de préférence la majeure partie des composés soufrés initialement présents dans l'essence
initiale est concentrée (essence où fraction lourde). Il est également possible de
séparer l'essence obtenue à l'étape A ou B ou directement la charge non traitée en
plus de deux fractions, c'est-à-dire par exemple une fraction lègère, au moins une
fraction intermédiaire et une fraction lourde.
[0031] Le procédé selon l'invention peut également comprendre en outre :
D) éventuellement au moins une hydrogénation sélective des dioléfines située avant
ou après les étapes A, B, C ou E.
F) éventuellement une étape de mélange de la fraction légère obtenue après l'une des
étapes B, C, D ou E de préférence de l'une des étapes B, C ou E, et de manière plus
préférée de l'étape C, ou à l'issue d'un fractionnement additionnel et éventuellement
d'au moins une fraction intermédiaire issue de l'une des étapes B à E, de préférence
de l'étape C ou d'un fractionnement additionnel, avec la fraction lourde désulfurée
issue de l'une des étapes B à E, de préférence de l'étape C. Dans cette étape, de
préférence, la totalité de ladite fraction lourde désulfurée est mélangée à ladite
fraction légère, sans séparation du liquide et du gaz contenu dans l'essence lourde
après désulfuration, éventuellement un simple strippage par un gaz inerte peut être
effectué pour éliminer l'H2S de l'essence lourde totalement désulfurée. Dans certains
cas spécifiques, la valorisation de l'essence légère, de l'essence lourde désulfurée,
et éventuellement d'au moins une essence intermédiaire, s'effectue de manière séparée.
Il est alors inutile de réaliser cette étape F.
[0032] Selon une variante du procédé selon l'invention, il est possible d'associer au moins
une section réactionnelle à une colonne de fractionnement selon l'étape E. Ladite
ou lesdites sections réactionnelles opèrent alors sur au moins une fraction prélevée
à l'intérieur de la colonne de fractionnement et l'effluent de la section réactionnelle
est renvoyé vers ladite colonne. La ou les sections réactionnelles ainsi couplées
à la colonne de fractionnement de l'étape E peuvent être choisies dans le groupe constitué
par les sections réactionnelles des étapes suivantes : traitement acide (étape B),
désulfuration (étape C), hydrogénation des dioléfines (étape D).
[0033] De tels dispositifs comprenant une colonne de fractionnement associés à un réacteur
externe et utilisables dans le procédé selon l'invention ont été par exemple décrits
pour des applications dans le domaine du raffinage et de la pétrochimie dans les brevets
US 5,1777,283,
US 5,817,227 et
US 5,888,355
[0034] Selon d'autres variantes du procédé selon l'invention, il est également possible
d'utiliser une colonne réactive à la place de la colonne de fractionnement, c'est-à-dire
de placer au moins une desdites sections réactionnelles dans la colonne de fractionnement
(section réactionnelle interne à la colonne), de préférence dans une zone ou la concentration
en réactif est maximale.
[0035] Selon une variante préférée du procédé selon l'invention, la section réactionnelle
interne à la colonne est choisie dans le groupe constitué par les sections réactionnelles
suivantes : traitement acide (étape B), désulfuration (étape C), hydrogénation des
dioléfines (étape D)
[0036] De telles colonnes réactives sont connues de l'homme du métier et ont été par exemple
décrites dans les brevets ou demandes de brevet
US 5,368,691,
US 5,523,062,
FR 2,737 131,
FR 2,737,132,
EP-A-0 461 855.
[0037] Une autre variante du procédé selon l'invention consiste à la fois à utiliser une
colonne réactive comprenant au moins une section réactionnelle et un réacteur externe
couplé ou non à la dite colonne. De telles variantes sont par exemple décrites dans
la demande de brevet
WO 00/15319.
[0038] Les variantes décrites précédemment ne sont que des illustrations des variantes possibles
du procédé selon l'invention. Le procédé selon l'invention peut en effet être mis
en oeuvre en combinant des sections réactionnelles soit associé(s) à la colonne de
fractionnement, soit interne(s) à ladite colonne, soit externe(s) et non-couplée(s)
à ladite colonne en ce sens que l'effluent de ladite ou desdites section(s) réactionnelle(s)
n'est pas recyclé vers la colonne de fractionnement.
[0039] Dans le procédé selon l'invention, l'essentiel des oléfines est maintenu dans la
fraction légère, eventuellement dans au moins une fraction intermédiaire ne nécessitant
pas de désulfuration trop importante. La teneur en composés soufrés de la fraction
lègère obtenue après fractionnement est généralement inférieure à 100 ppm, de préférence
inférieure à 30 ppm, de manière plus préférée inférieure à 20 ppm et de manière très
préférée inférieure à 10 ppm.
[0040] Un autre avantage réside dans le fait que la teneur résiduelle en composés soufrés
de l'essence désulfurée au moyen du procédé selon l'invention est particulièrement
basse, et que l'indice d'octane de l'essence est maintenu à un niveau élevé.
[0041] Les étapes du procédé selon l'invention sont décrites plus en détail ci après.
- transformation des composés soufrés (étape A):
[0042] Cette étape consiste à faire passer la charge, éventuellement hydrogénée à l'étape
D sur un catalyseur présentant une fonction acide qui permet de réaliser essentiellement
la réaction d'alkylation du thiophène et des dérivés thiophèniques par les oléfines
l'addition des composés soufrés sous forme de mercaptans sur les oléfines. Les conditions
d'opération sont ajustées pour réaliser la transformation désirée avec des taux de
conversion du thiophéne et/ou des thiophèniques et/ou des mercaptans légers, de préférence
des mercaptans ayant de 1 à 6 atomes de carbone, supérieurs à 80 %poids, de préférence
supérieurs à 90 %poids, de manière très préférée supérieurs à 95 %poids. D'autres
composés tels que COS ou CS2 peuvent éventuellement également être convertis.
[0043] Pour minimiser l'activité oligomérisante du catalyseur acide éventuellement utilisé,
l'essence peut être additivée d'un composé connu pour inhiber l'activité oligomérisante
des catalyseurs acides tel que les alcools, les éthers ou l'eau.
[0044] Cette transformation peut être par exemple conduite selon les procédures et en utilisant
les schémas décrits dans les demandes de brevet français n°
00/08113, et n°
00/10233.
[0045] Selon cette variante de l'étape A, l'essence éventuellement hydrogénée est traitée
dans une section permettant de transformer, par alkylation, les composés choisis dans
le groupe constitué par le thiophène, les composés thiophèniques et les mercaptans.
Lors de l'alkylation, les composés thiophéniques contenus dans la coupe 60°C-160°C
vont réagir avec des taux de conversion supérieurs à 80 %poids, de préférence supérieurs
à 90 %poids, avec les oléfines pour former des alkyls thiophènes selon la réaction
suivante pour lé thiophène :
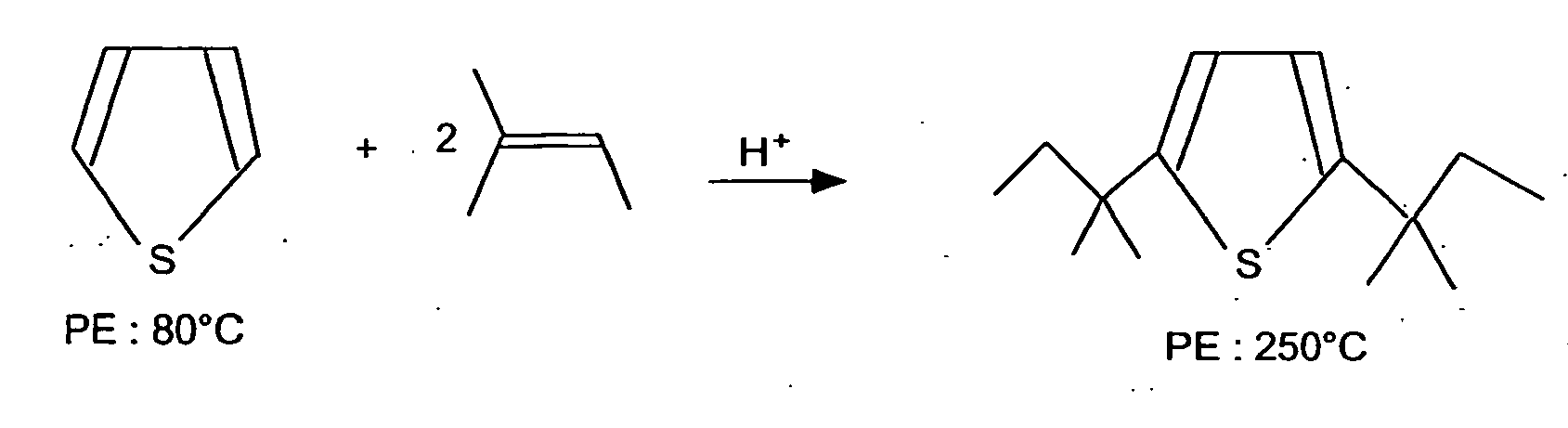
[0046] Une partie ou la totalité du benzène peut également être éliminée par alkylation
avec les oléfines. Ces composés de poids moléculaires plus élevés sont surtout caractérisés
par des températures d'ébullition plus élevées que celles qu'ils avaient avant alkylation.
Ainsi la température théorique d'ébullition qui est de 80°C se trouve déplacée vers
250°C pour les alkyls thiophènes.
[0047] Cette étape d'alkylation est effectuée en présence de catalyseur acide. Ce catalyseur
peut être indifféremment une résine, une zéolithe, une argile, toute silice fonctionalisée
ou tout silico-aluminate présentant une acidité, ou tout support greffé de groupes
fonctionnels acides. Le rapport du volume de charge injecté sur le volume de catalyseur
est compris entre 0,1 et 10 litre/litre/heure et de préférence entre 0,5 et 4 litre/litre/heure.
Plus précisément, cette étape d'alkylation est effectuée en présence d'au moins un
catalyseur acide choisi dans le groupe constitué par les silicoaluminates les titanosilicates,
les mixtes alumine titane, les argiles, les résines, les oxydes mixtes obtenus par
greffage d'au moins un composé organométallique organosoluble ou aquosoluble (choisi
dans le groupe constitué par les alkys. et/ou les alcoxy. métaux d'au moins un élément
tels que titane, zirconium silicium, germanium, étain, tantale, niobium...) sur au
moins un oxyde tel que l'alumine (formes gamma, delta, éta, seules ou en mélange)
la silice, les silices-alumines, les silices-titane, les silices-zircone ou tout autre
solide présentant une acidité quelconque. Un mode particulier de l'invention peut
consister à mettre en oeuvre un mélange physique d'au moins deux des catalyseurs ci-avant
dans des proportions variant de 95/5 à 5/95, préférentiellement de 85/15 à 15/85 et
très préférentiellement de 70/30 à 30/70.
[0048] La température pour cette étape est généralement comprise entre 10 et 350°C selon
le type de catalyseur ou la force de l'acidité. Ainsi pour une résine acide de type
échangeuse d'ions, la température est généralement comprise entre 50 et 150°C de préférence
entre 50 et 120°C.
[0049] Le rapport molaire oléfine sur composés thiophèniques est compris entre 0,1 et 1000
mole/mole de préférence entre 0,5 et 500 mole/mole.
[0050] La pression opératoire de cette étape est généralement comprise entre 0,1 et 3 MPa
et de préférence telle que la charge se trouve sous forme liquide dans les conditions
de température et de pression, soit à une pression supérieure à 0,5 MPa.
[0051] L'effluent issu de l'étape A; d'alkylation des composés soufrés, peut éventuellement
être mélangé au moins en partie à une coupe lourde issue du fractionnement à l'étape
E.
- traitement en présence d'un catalyseur acide (étape B) :
[0052] Cette étape permet de compenser la perte d'octane due à l'étape de désulfuration
de l'essence totale ou d'une coupe essence (étape C). Elle est placée soit avant ladite
étape C de désulfuration, soit après ladite étape. Elle peut éventuellement être mise
en oeuvre sur la totalité de l'essence avant l'étape d'alkylation des composés soufrés
(étape A). De manière préférée, elle est située après fractionnement (étape E), et
de manière plus préférée juste avant ou juste après l'étape de désulfuration (étape
C). Il est enfin possible de réaliser l'étape B simultanément à l'étape C, soit en
disposant un catalyseur acide et un catalyseur d'hydrodésulfuration dans le même réacteur,
soit en utilisant un catalyseur bifonctionnel comprenant une phase active en désulfuration
telle que décrite à l'étape C, dispersée sur un support comprenant un solide acide
tel que par exemple une zéolithe.
[0053] Lorsque l'étape de désulfuration est réalisée dans deux réacteurs séparés, il est
parfois préféré de disposer l'étape B de traitement acide entre les deux réacteurs
de l'étape C. En effet, le second réacteur de désulfuration permet d'enlever les mercaptans
éventuellement formés dans l'étape B par recombinaison des oléfines formés dans cette
étape avec des composés soufrés. Cette seconde étape de désulfuration peut alors être
une hydrodésulfuration catalytique ou un adoucissement, par exemple un adoucissement
extractif.
[0054] Lorsque l'étape de traitement acide est placée après l'étape de désulfuration, le
catalyseur acide choisi pour l'étape de traitement acide présente une acidité controlée
de manière à limiter le degré de crackage des hydrocarbures. De ce fait, la réaction
de craquage est essentiellement limitée aux composés présentant un faible indice d'octane.
[0055] De préférence, cette étape de traitement acide réalise un craquage limité des paraffines
de faible indice d'octane pour former des produits d'indicé d'octane plus élevé. Les
réactions misent en jeu sont d'une part le craquage des parrafines présentant les
points d'ébullition les plus élevés en paraffines de plus faible point d'ébullition,
et le craquage des paraffines de faible indice d'octane. Des oléfines sont également
formées lors de ces réactions, ainsi que des parrafines ramifiées via des réactions
d'isomérisation. L'ensemble de ces réactions permet donc de compenser la diminution
de l'indice d'octane due à l'étape de désulfuration, voire dans certains cas à augmenter
cet indice au-delà de l'indice de la coupe ou de l'essence avant désulfuration.
[0056] Afin de limiter la désactivation du catalyseur par dépôt d'hydrocarbures, on injecte
généralement de l'hydrogène dans le réacteur de traitement acide. Il est également
possible d'admettre l'excés d'hydrogène issue d'une étape précédente (par exemple
une étape de désulfuration) à l'entrée de cette étape, avec éventuellement un complément
d'hydrogène apporté par une alimentation séparée.
[0057] Les conditions opératoires de cette étape sont généralement les suivantes: la température
est généralement comprise entre 140°C et 500°C, préférentiellement entre 170°C et
480°C ; la pression est généralement comprise entre 0,5 et 15 MPa, de préférence entre
1 et 10MPa, de manière plus préférée entre 2 et 8 MPa ; la vitesse spatiale exprimée
en volume de charge par volume de catalyseur et par heure est généralement comprise
entre 0,3 et 15 h-1, de préférence entre 0,5 et 10 h-1 ; le rapport volumique hydrogène
sur charge hydrocarbonnée est généralement compris entre 0 et 1000 litres par litres,
de préférence entre 10 et 800 litres par litres, de manière plus préférée entre 20
et 500 litres par litres.
[0058] Parmi les catalyseurs préférés pour cette étape, on peut citer les silicates, aluminosilicate,
les borosillicates, les gallosilicates, et d'une façon générale les metallosilicates.
Parmi les aluminosilicates, ceux appartenant à la famille des ZSM (par exemple ZSM-5,
ZSM-12, ZSM 22) ou MCM (par exemple MCM-22) sont préférées, ainsi que la zéolithe
Y, la mordénite, la zéolithe béta ou les faujasites. Afin de régler l'acidité de ces
matériaux, ils peuvent être éventuellement au moins partiellement désaluminés, ou
synthétisés en milieu fluorure.
[0059] Les catalyseurs de cette étape peuvent également comprendre un métal actif en hydrogénation,
de façon à faciliter l'élimination des composés susceptibles d'empoisonner le catalyseur
et notemment sa fonction acide. De préférence, un métal du groupe VIII de l'ancienne
classification périodique (groupes 8,9,10 de la nouvelle classification) est employé,
par exemple un métal noble ou le nickel..
- désulfuration (étape C):
[0060] Cette étape peut par exemple être une étape d'hydrodésulfuration réalisée par passage
de l'essence lourde ou intermédiaire, en présence d'hydrogène, sur au moins un catalyseur
comprenant au moins un élément du groupe VIII et/ou au moins un élément du groupe
Vlb au moins en partie sous forme sulfure, à une température comprise entre environ
210°C et environ 350°C, de préférence entre 220°C et 320°C, sous une pression généralement
comprise entre environ 1 et environ 4 MPa, de préférence entre 1,5 et 3 MPa. La vitesse
spatiale du liquide est comprise entre environ 1 et environ 20 h
-1 (exprimée en volume de liquide par volume de catalyseur et par heure), de préférence
entre 1 et 10 h-1, de manière très préférée entre 3 et 8 h-1. Le rapport H
2/HC est compris entre 100 à 600 litres par litre et préférentiellement entre 300 et
600 litres par litre.
[0061] La teneur en métal du groupe VIII exprimée en oxyde est généralement comprise entre
0,5 et 15 % poids, préférentiellement entre 1 et 10 % poids. La teneur en métal du
groupe Vlb est généralement comprise entre 1,5 et 60 % poids, préférentiellement entre
3 et 50 % poids.
[0062] L'élément du groupe VIII, lorsqu'il est présent, est de préférence le cobalt, et
l'élément du groupe Vlb, lorsqu'il est présent, est généralement le molybdène ou le
tungstène. Des combinaisons telles que cobalt-molybdène sont préférées. Le support
du catalyseur est habituellement un solide poreux, tel que par exemple une alumine,
une silice-alumine ou d'autres solides poreux, tels que par exemple de la magnésie,
de la silice ou de l'oxyde de titane, seuls ou en mélange avec de l'alumine ou de
la silice-alumine. Le catalyseur selon l'invention présente de préférence une surface
spécifique inférieure à 190 m2/g, de manière plus préférée inférieure à 180m2/g, et
de manière très préférée inférieure à 150 m2/g.
[0063] Après introduction du ou des éléments et éventuellement mise en forme du catalyseur
(lorsque cette étape est réalisée sur un mélange contenant déjà les éléments de base),
le catalyseur est dans une première étape activé. Cette activation peut correspondre
soit à une oxydation puis à une réduction, soit à une réduction directe, soit à une
calcination uniquement. L'étape de calcination est généralement réalisée à des températures
allant d'environ 100 à environ 600 °C et de préférence comprises entre 200 et 450
°C, sous un débit d'air. L'étape de réduction est réalisée dans des conditions permettant
de convertir au moins une partie des formes oxydées du métal de base en métal. Généralement,
elle consiste à traiter le catalyseur sous un flux d'hydrogène à une température de
référence au moins égale à 300 °C. La réduction peut aussi être réalisée en partie
au moyen de réducteurs chimiques.
[0064] Le catalyseur est de préférence utilisé au moins en partie sous sa forme sulfurée.
L'introduction du soufre peut intervenir avant ou après toute étape d'activation,
c'est-à-dire de calcination ou de réduction. De préférence, aucune étape d'oxydation
du catalyseur n'est réalisée lorsque le soufre ou un composé soufré a été introduit
sur le catalyseur. Le soufre ou un composé soufré peut être introduit
ex situ, c'est-à-dire en dehors du réacteur où le procédé selon l'invention est réalisé, ou
in situ, c'est-à-dire dans le réacteur utilisé pour le procédé selon l'invention. Dans ce
dernier cas, le catalyseur est de préférence réduit dans les conditions décrites précédemment,
puis sulfuré par passage d'une charge contenant au moins un composé soufré, qui une
fois décomposé conduit à la fixation de soufre sur le catalyseur. Cette charge peut
être gazeuse ou liquide, par exemple de l'hydrogène contenant de l'H
2S, ou un liquide contenant au moins un composé soufré.
[0065] D'une façon préférée, le composé soufré est ajouté sur le catalyseur
ex situ. Par exemple, après l'étape de calcination, un composé soufré peut être introduit
sur le catalyseur en présence éventuellement d'un autre composé. Le catalyseur est
ensuite séché, puis transféré dans le réacteur servant à mettre en oeuvre le procédé
selon l'invention. Dans ce réacteur, le catalyseur est alors traité sous hydrogène
afin de transformer au moins une partie du métal principal en sulfure. Une procédure
qui convient particulièrement à l'invention est celle décrite dans les brevets
FR-B- 2 708 596 et
FR-B- 2 708 597.
[0066] La désulfuration de l'essence lourde et/ou d'au moins une essence intermédiaire peut
également être réalisée au moyen d'un absorbeur comprenant une masse absorbante, par
exemple à base d'oxyde de zinc. Ladite désulfuration peut également être réalisée
au moyen d'une combinaison entre une section d'hydrodésulfuration et un absorbeur,
de préférence situé après la section d'hydrodésulfuration.
[0067] La section de désulfuration peut éventuellement comprendre au moins deux réacteurs
en série, avec éventuellement une séparation du gaz contenant de l'H2S et du liquide
entre les deux réacteurs. Il est également possible d'employer deux catalyseurs identiques
ou différents disposés dans au moins deux lits à l'intérieur d'un seul réacteur ou
dans deux réacteurs comportant un seul ou plusieurs lits de catalyseur. Un ajout intermédiaire
d'hydrogène (également appellé quench selon la terminologie anglosaxonne), est également
possible entre lesdits réacteur et/ou entre deux lits.
[0068] Par exemple, il est possible d'utiliser un catalyseur comprenant du cobalt et du
molybdène ou du tungstène associé à un catalyseur comprenant du nickel dans le même
réacteur ou dans deux réacteurs différents disposés en série. De préférence lesdits
catalyseurs sont sulfurés.
[0069] Un des modes préférés de désulfuration d'au moins une coupe intermédiaire ou lourde
ou de l'essence totale consiste par exemple à opérer en deux étapes : une première
étape réalisant essentiellement l'hydrogénation des composés soufrés insaturés et
une seconde étape réalisant une décomposition des composés soufrés saturés, selon
l'un des modes opératoires enseignés dans la demande de brevet
EP-A-1 031 622.
[0070] Il est également possible, de préférence pour les coupes les moins riches en composés
soufrés, notamment la coupe légère obtenue après l'étape optionnelle de fractionnement
de réaliser un simple adoucissement au moyen de tout procédé d'adoucissement connu
de l'homme du métier. Il est ainsi possible d'utiliser un procédé d'adoucissement
par oxydation à l'air, éventuellement en présence de cuivre, ou encore par un procédé
extractif par contact liquide/liquide, par exemple par une solution de soude. D'autres
procédés de conversion catalytique des mercaptans en disulfure peuvent également être
utilisés, en combinaison si nécessaire avec un fractionnement supplémentaire après
adoucissement.
- hydrogénation des dioléfines (étape D optionnelle) :
[0071] L'hydrogénation des diènes est une étape optionnelle qui permet d'éliminer, avant
hydrodésulfuration, la presque totalité des diènes présents dans la coupe essence
contenant du soufre à traiter. Elle se déroule préférentiellement en première étape
du procédé selon l'invention, ou éventuellement sur au moins l'une des coupes obtenues
juste après fractionnement à l'étape E. Elle est généralement effectuée en présence
d'un catalyseur comprenant au moins un métal du groupe VIII, de préférence choisi
dans le groupe constitué par le platine, le palladium et le nickel, et un support.
On emploiera par exemple un catalyseur à base de nickel ou de palladium déposé sur
un support inerte, tel que par exemple de l'alumine, de la silice ou un support contenant
au moins 50 % d'alumine.
[0072] La pression employée est suffisante pour maintenir plus de 60 %, de préférence 80
%, et de manière plus préférée de 95 % en poids de l'essence à traiter en phase liquide
dans le réacteur ; elle est le plus généralement comprise entre environ 0,4 et environ
5 MPa et de préférence supérieure à 1 MPa, de manière plus préférée comprise entre
1 et 4 MPa. La vitesse spatiale horaire du liquide à traiter est comprise entre environ
1 et environ 20 h
-1 (volume de charge par volume de catalyseur et par heure), de préférence entre 2 et
10 h
-1, de manière très préférée entre 3 et 8 h
-1. La température est comprise le plus généralement entre environ 50 et environ 250
°C, et de préférence entre 80 et 220 °C, et de manière plus préférée entre 100 et
200 °C, pour assurer une conversion suffisante des dioléfines. De façon très préférée
elle est limitée à 180°C. Le rapport hydrogène sur charge exprimé en litre est généralement
compris entre 1 et 50 litres par par litre, de préférence entre 3 et 30 litres, de
manière plus préférée entre 8 et 25 litres par litre.
[0073] Le choix des conditions opératoires est particulièrement important. On opérera le
plus généralement sous pression et en présence d'une quantité d'hydrogène en faible
excès par rapport à la valeur stoechiométrique nécessaire pour hydrogéner les dioléfines.
L'hydrogène et la charge à traiter sont injectés en courants ascendants ou descendants
dans un réacteur comprenant de préférence un lit fixe de catalyseur. Un autre métal
peut être associé au métal principal pour former un catalyseur bimétallique, tel que
par exemple le molybdène ou le tungstène. L'utilisation de telles formules catalytiques
a par exemple été revendiquée dans le brevet
FR 2 764 299. L'essence de craquage catalytique peut contenir jusqu'à quelques % poids de dioléfines.
Après hydrogénation, la teneur en dioléfines est généralement réduite à moins de 3000
ppm, voire moins de 2500 ppm et de manière plus préférée moins de 1500 ppm. Dans certains
cas, il peut être obtenu moins de 500 ppm. La teneur en diènes après hydrogénation
sélective peut même si nécessaire être réduite à moins de 250 ppm.
[0074] Selon une réalisation particulière du procédé selon l'invention, l'étape d'hydrogénation
des diènes se déroule dans un réacteur catalytique d'hydrogénation qui comprend une
zone réactionnelle catalytique traversée par la totalité de la charge et la quantité
d'hydrogène nécessaire pour effectuer les réactions désirées.
- séparation de l'essence en au moins deux fractions (étape E):
[0075] Selon une première variante du procédé selon l'invention, l'essence est fractionnée
en deux fractions :
- une fraction légère contenant une teneur en soufre résiduelle limitée, de préférence
inférieure à environ 100 ppm, de manière plus préférée inférieure à environ 50 ppm,
de manière très préférée inférieure à environ 20 ppm, et permettant d'utiliser cette
coupe sans effectuer autre traitement visant à diminuer sa teneur en soufre, sauf
éventuellement une transformation des composés soufrés selon l'étape A, ou un simple
adoucissement.
- une fraction lourde dans laquelle de préférence la majeure partie du soufre initialement
présent dans là charge est concentrée.
[0076] Cette séparation est réalisée de préférence au moyen d'une colonne de distillation
classique appelée aussi splitter. Cette colonne de fractionnement doit permettre de
séparer une fraction légère de l'essence contenant une faible fraction du soufre et
une fraction lourde contenant de préférence la majeure partie du soufre initialement
présent dans l'essence initiale.
[0077] Cette colonne opère généralement à une pression comprise entre 0,1. et 2 MPa et de
préférence entre 0,2 et 1 MPa. Le nombre de plateaux théoriques de cette colonne de
séparation est généralement compris entre 10 et 100 et de préférence entre 20 et 60.
Le taux de reflux, exprimé comme étant le rapport du débit liquide dans la colonne
divisé par lé débit de distillat exprimé en kg/h, est généralement inférieur à l'unité
et de préférence inférieur à 0,8.
[0078] L'essence légère obtenue à l'issue de la séparation contient généralement au moins
l'ensemble des oléfines en C5, de préférence les composés en C5 et au moins 20 % des
oléfines en C6. Généralement, cette fraction légère présente une faible teneur en
soufre, c'est à dire qu'il n'est pas en général nécessaire de traiter la coupe légère
avant de l'utiliser comme carburant.
[0079] Selon une deuxième variante du procédé selon l'invention, l'essence est fractionnée
en au moins 3 fractions : une fraction légère, une fraction lourde et au moins une
fraction intermédiaire.
[0080] Dans le procédé selon l'invention, l'essence est de préférence fractionnée en au
moins deux coupes présentant les propriétés suivantes :
- une coupe dite légère (coupe L) dont les points d'ébullition sont de préférence inférieurs
à environ 60°C. Cette température est donnée à titre indicatif, il s'agit de préférence
de la température maximale pour laquelle la teneur en thiophène est inférieure à 5
ppm,
- au moins une coupe dite lourde (coupe H1) dont les points d'ébullition sont supérieurs
à environ 60°C.
[0081] La coupe légère L est de préférence injectée dans un ballon de séparation gaz liquide
afin de séparer l'hydrogène non consommé, et éventuellement l'H2S présent, des oléfines
possédant généralement de 5 à 7 atomes de carbone.
[0082] La coupe dite lourde H1 c'est-à-dire la coupe dont les températures sont supérieures
à environ 60°C est envoyée dans une colonne de distillation ou tout autre procédé
de séparation capable de séparer cette coupe en au moins deux coupes:
- une coupe intermédiaire 12 dont les points d'ébullition à titre d'exemple sont au
minimum de 60°C et au maximum d'environ 120°C voire environ 160°C. Cette coupe peut
être traitée à l'étape A et éventuellement B et/ou C du procédé selon l'invention.
- une coupe plus lourde H2 dont les points d'ébullition sont généralement supérieurs
à environ 160°C ou à environ 120°C.
[0083] La coupe lourde H2 dont les températures d'ébullition sont généralement supérieures
à environ 150°C voire environ 180°C est envoyée l'étape C de désulfuration.
[0084] Dans une autre version du procédé selon l'invention, il est également possible de
fractionner directement l'essence en au moins trois coupes une coupe légère (L), au
moins une coupe intermédiaire (12) et au moins une coupe lourde (H2) présentant les
propriétés décrites ci-avant.
[0085] La coupe intermédiaire 12 dont les points d'ébullition sont compris entre environ
60°C et environ 120°C ou environ 160°C peut être envoyée dans l'unité de transformation
des composés soufrés selon l'étape A.
[0086] Après l'étape A, les coupes 12 peuvent à nouveau être fractionnées en une coupe intermédiaire
I3 et une coupe lourde H3. La couple H3 ainsi obtenue peut éventuellement être mélangée
à la coupe H2, de préférence avant désulfuration.
[0087] Dans la figure 1, le procédé n'est pas selon l'invention car il ne comprend pas d'étape
de fractionnement. La charge 1 est tout d'abord éventuellement et de préférence envoyée
dans l'unité 2 d'hydrogénation selon l'étape D. Cette section réactionnelle peut éventuellement
comprendre un catalyseur capable à la fois d'hydrogéner les dioléfines (étape D) et
d'alourdir les composés soufrés, notamment les mercaptans légers par addition sur
les oléfines. L'effluent issu de cette section 2 ou la charge, lorsque la section
2 est absente, est envoyée par la conduite 3 vers une section réactionnelle 4 permettant
de réaliser l'alkylation des composés thiophèniques (étape A). L'effluent de la section
4 est ensuite envoyé via la conduite 5 vers une section 6 contenant un catalyseur
d'hydrodésulfuration. L'effluent désulfuré issu de cette section (7) est enfin envoyé
dans une section réactionnelle contenant un catalyseur acide (section 8) et permettant
de réaliser essentiellement un léger craquage et d'autres réaction décrites selon
l'étape B, afin d'augmenter l'indice d'octane de l'essence désulfurée. L'hydrogène
nécessaire aux sections 2, 6 et 8, peut être ammené respectivement par les conduites
10, 12 et 13. Il est éventuellement possible d'amener via la ligne 11 1 une coupe
hydrocarbonée riche en oléfines issues d'un autre procédé, pour faciliter l'alkylation
des composés thiophéniques dans la section 4. L'effluent 9 issu de ce traitement peut
être utilisé dans un pool essence car il présente une basse teneur en composés soufrés
et un indice d'octane élevé.
[0088] Dans la figure 2, le procédé selon l'invention comprend une étape de fractionnement.
La charge 1 est tout d'abord éventuellement et de préférence envoyée dans l'unité
2 d'hydrogénation selon l'étape D. Cette section réactionnelle peut éventuellement
comprendre un catalyseur capable à la fois d'hydrogéner les dioléfines (étape D) et
d'alourdir les composés soufrés, notamment les mercaptans légers. L'effluent issu
de cette section 2 ou la charge, lorsque la section 2 est absente, est envoyé par
la conduite 3 vers une section réactionnelle 4 permettant de réaliser l'alkylation
des composés thiophèniques (étape A). L'effluent de la section 4 est ensuite envoyé
via la conduite 5 vers une section 6 de fractionnement (étape E) en trois coupes:
une fraction légère non traitée et récupérée via la conduite 12, une fraction intermédiaire
récupérée via la conduite 13 puis traitée, une fraction lourde récupérée via la conduite
7 puis traitée. Le traitement de la fraction intermédiaire (13) consiste tout d'abord
en un traitement acide (étape B) dans la section 14, puis en une hydrodésulfuration
en présence d'un catalyseur dans la section 16 (étape C) de l'effluent issu de la
section 14 (effluent 15). Le traitement de la coupe lourde consiste en une hydrodésulfuration
en présence d'un catalyseur dans la section 8 (étape C), puis en un traitement acide
de l'effluent désulfuré 9 dans la sections 10 (étape B). L'hydrogène nécessaire aux
sections 2, 8, 10, 14 et 16 peut être ammené respectivement via les conduites 19,
21, 22, 23 et 24. Il est également possible d'amener via la ligne 20 une coupe hydrocarbonnée
riche en oléfine issue d'un autre procédé, pour faciliter l'alkylation des composés
thiophéniques dans la section 4. Les coupes intermédiaires et lourdes ainsi désulfurées
et présentant un indice d'octane élevé grace au traitement acide sont récupérée respectivement
via les conduites 17 et 11 et mélangées à la coupe légère 12 pour former une essence
désulfurée 18 présentant un haut indice d'octane.
[0089] En résumé, l'invention concerne un procédé de production d'essence à faible teneur
en soufre comprenant au moins une étape d'alkylation des composés soufrés (étape A),
au moins une étape de traitement en présence d'un catalyseur acide (étape B) et au
moins un traitement de désulfuration d'au moins une partie de l'essence (étape C).
Ledit procédé peut éventuellement comprendre en outre au moins une étape d'hydrogénation
sélective des dioléfines (étape D). Il comprend en outre au moins une étape de fractionnement
de l'essence issue de l'étape A (étape E) en au moins deux fractions ou en au moins
trois fractions.
[0090] Selon un mode plus préféré, ladite étape consiste essentiellement en une alkylation
des composés thiophèniques. Selon un mode très préféré, l'étape de transformation
dss composés soufrés (étape A) comprend à la fois une alkylation des composés thiophèniques
et une addition des mercaptans sur les oléfines réalisées dans deux sections réactionnelles
séparées. Eventuellement, l'étape d'alourdissement des composés soufrés (étape A)
est réalisée dans la même section réactionnelle que l'étape d'hydrogénation des dioléfines
(étape D).
[0091] Le procédé selon l'invention peut en outre comprendre une étape de mélange (étape
F) de la fraction légère obtenue après l'une des étapes B à E et éventuellement d'au
moins une fraction intermédiaire issue de l'une des étapes B à E avec la fraction
lourde désulfurée issue de l'une des étapes B à E.
[0092] Selon une variante préférée du procédé selon l'invention, l'essence lourde est désulfurée
en présence d'au moins un catalyseur d'hydrodésulfuration ou d'un absorbant. Selon
une autre variante, l'essence lourde est désulfurée dans deux réacteurs d'hydrodésulfuration
disposés en série et comprenant un catalyseur d'hydrodésulfuration. Dans ce cas, l'H2S
est de préférence strippé entre les deux réacteurs d'hydrodésulfuration. Selon une
autre variante du procédé selon l'invention, une étape de traitement acide (étape
B) est intercalée entre les deux réacteurs d'hydrodésulfuration. Eventuellement, l'essence
lourde désulfurée au moyen de l'une quelconque des variantes décrites est strippée
au moyen d'un gaz inerte.
[0093] Eventuellement, au moins une section réactionnelle du procédé selon l'invention est
interne à la section de fractionnement et choisie dans le groupe constitué par les
sections réactionnelles suivantes, traitement acide (étape B), désulfuration (étape
C), hydrogénation des dioléfines (étape D).
[0094] Eventuellement, au moins une section réactionnelle est couplée à la section de fractionnement
et choisie dans le groupe constitué par les sections réactionnelles suivantes : traitement
acide (étape B), désulfuration (étape C), hydrogénation des dioléfines (étape D).