(19) |
 |
|
(11) |
EP 1 930 498 B1 |
(12) |
EUROPÄISCHE PATENTSCHRIFT |
(45) |
Hinweis auf die Patenterteilung: |
|
23.03.2011 Patentblatt 2011/12 |
(22) |
Anmeldetag: 17.10.2007 |
|
(51) |
Internationale Patentklassifikation (IPC):
|
|
(54) |
Bespannung für eine Maschine zur Herstellung von Bahnmaterial und Verfahren zur Herstellung
einer derartigen Bespannung
Fabric for a production machine for sheet material and method for manufacturing such
a fabric
Habillage pour une machine de fabrication de matériau en bande et procédé de fabrication
d'une telle habillage
|
(84) |
Benannte Vertragsstaaten: |
|
AT BE BG CH CY CZ DE DK EE ES FI FR GB GR HU IE IS IT LI LT LU LV MC MT NL PL PT RO
SE SI SK TR |
(30) |
Priorität: |
05.12.2006 DE 102006057228
|
(43) |
Veröffentlichungstag der Anmeldung: |
|
11.06.2008 Patentblatt 2008/24 |
(73) |
Patentinhaber: Voith Patent GmbH |
|
89522 Heidenheim (DE) |
|
(72) |
Erfinder: |
|
- Jeffrey, John
Blackburn, Lancashire BB18RJ (GB)
- Payne, Justin Alan
Blackburn, Lancashire BB2 5HG (GB)
- Ponton, David Stuart
Blackburn, Lancashire BB12AY (GB)
|
(56) |
Entgegenhaltungen: :
EP-A- 0 695 827
|
WO-A-2004/061213
|
|
|
|
|
|
|
|
|
Anmerkung: Innerhalb von neun Monaten nach der Bekanntmachung des Hinweises auf die
Erteilung des europäischen Patents kann jedermann beim Europäischen Patentamt gegen
das erteilte europäischen Patent Einspruch einlegen. Der Einspruch ist schriftlich
einzureichen und zu begründen. Er gilt erst als eingelegt, wenn die Einspruchsgebühr
entrichtet worden ist. (Art. 99(1) Europäisches Patentübereinkommen). |
[0001] Die vorliegende Erfindung betrifft ein Verfahren zur Herstellung einer bandartigen
Bespannung für eine Maschine zur Herstellung von Bahnmaterial, insbesondere Papier
oder Karton. Weiter betrifft die vorliegende Erfindung ein Verfahren, mit welchem
eine derartige bandartige Bespannung in eine Maschine zur Herstellung von Bahnmaterial
eingegliedert werden kann, sowie eine bandartige Bespannung für eine Maschine zur
Herstellung von Bahnmaterial.
[0002] In Maschinen zur Herstellung von Bahnmaterial, also beispielsweise Maschinen zur
Herstellung von Papier oder Karton, werden in verschiedenen Bereichen langgestreckte,
endlos arbeitende Bänder bzw. Bespannungen eingesetzt, welche die Funktion des Transports
des zu fertigenden Bahnmaterials bzw. auch der Bearbeitung, insbesondere auch der
Entwässerung in Presssektionen, haben. Dazu werden häufig Bänder bzw. Bespannungen
mit bandartigen Substraten eingesetzt, die eine offene, also porige Struktur haben.
Gewebebänder bzw. Spiralgliederbänder, auch als "spiral linc fabrics" oder "spiral
fabrics" bekannt, haben sich hier als besonders vorteilhaft erwiesen. Um die Oberflächeneigenschaft
bzw. auch die Permeabilität lokal beeinflussen zu können, ist es bekannt, auf bzw.
in derartige bandartige Substrate einen Auftrag mit kontinuierlichem oder diskretem
Muster aufzubringen.
[0003] Beispielsweise schlägt die
EP 1 690 981 A1 zum Aufbringen eines derartigen Auftrags in Form eines topographischen Musters vor,
ein Rotationssieb zu verwenden, um das Muster mit der gewünschten Form und Qualität
erzeugen zu können.
[0004] Die
EP 0 695 827 offenbart ein nahtbares Transferband, bei dem die den Nahtbereich überbrückende Polymerschicht
im Nahtbereich durchtrennt ist.
[0005] Die
EP 1 690 982 A1 schlägt zur Erzeugung eines topographischen Musters vor, dieses in einem Polymerextrusionsverfahren
aufzutragen, wobei ein das Polymermaterial abgebender Extrusionskopf über die Oberfläche
des zu bearbeitenden bandartigen Substrates hinweg bewegt wird und dabei das Muster
mit der gewünschten Formgebung aufträgt.
[0006] Die
WO 2004/061213 offenbart ein Verfahren zur Herstellung eines mit Auftragmaterial beschichteten bzw.
imprägnierten endlosen Bandes, das in Presssektionen einer Papiermaschine eingesetzt
werden kann. Das polymerische Auftragmaterial wird in allen drei Raumrichtungen mit
der gewünschten Struktur aufgetragen.
[0007] Problematisch ist der Einsatz dieser aus dem Stand der Technik bekannten Vorgehensweise
dann, wenn die zu beschichtende Bespannung in einer Papiermaschine oder dergleichen
zwar in Endloskonfiguration arbeitet, jedoch nicht in Endloskonfiguration hergestellt
ist, sondern zumindest einen Nahtbereich aufweist. An einem derartigen Nahtbereich
können die beiden dort liegenden Endbereiche der Bespannung voneinander gelöst werden,
um auf diese Art und Weise die offene, also nicht in Endloskonfiguration vorliegende
Bespannung in eine Papiermaschine oder dergleichen einzubauen. Nach erfolgtem Einbau
werden die beiden Endbereiche wieder miteinander verbunden, beispielsweise durch ein
langgestrecktes Verbindungselement. Dies bedeutet, dass das Trennen der beiden Endbereiche
auch dann möglich sein muss, wenn auf dem Substrat der Bespannung Auftragmaterial
vorgesehen ist. Im Allgemeinen bedeutet dies, dass das Muster des Auftrags so gewählt
sein muss, dass es den Nahtbereich frei lässt, um dort die Endbereiche voneinander
trennen bzw. wieder miteinander verbinden zu können.
[0008] Es ist die Aufgabe der vorliegenden Erfindung, ein Verfahren zur Herstellung einer
bandartigen Bespannung für eine Maschine zur Herstellung von Bahnmaterial, insbesondere
Papier oder Karton, vorzusehen, mit welchem auch bei einem mit wenigstens einem Nahtbereich
versehenen bandartigen Substrat ein beliebiges Auftragsmuster erzeugbar ist.
[0009] Erfindungsgemäß wird diese Aufgabe gelöst durch ein Verfahren zur Herstellung einer
bandartigen Bespannung insbesondere für eine Maschine zur Herstellung von Bahnmaterial,
insbesondere Papier oder Karton, umfassend die Maßnahmen:
- a) Bereitstellen eines bandartigen Substrates mit wenigstens einem im Wesentlichen
in Substratquerrichtung sich erstreckenden Nahtbereich,
- b) Aufbringen eines Auftrags auf das bandartige Substrat derart, dass der Auftrag
sich über wenigstens einen Nahtbereich hinweg erstreckt, wobei der Auftrag mit einem
kontinuierlichen oder/und diskreten sich über den Nahtbereich erstreckenden Auftragsmuster
auf das bandartige Substrat aufgetragen wird.
- c) Durchtrennen des Auftrags entlang wenigstens eines Nahtbereichs.
[0010] Bei der erfindungsgemäßen Vorgehensweise wird also der Auftrag nach dessen Aufbringen
auf das bandartige Substrat und ggf. nach einem Aushärtvorgang durchtrennt, und zwar
dort, wo das bandartige Substrat möglicherweise aufgetrennt werden muss, um die so
hergestellte bandartige Bespannung in eine Maschine zur Herstellung von Bahnmaterial
eingliedern zu können. Damit wird es möglich, bei der Maßnahme b) den Auftrag mit
einem beliebigen und sich vor allem auch über den Nahtbereich hinweg erstreckenden
Muster aufzubringen. Es muss nicht darauf geachtet werden, dass der Nahtbereich freigehalten
wird. Dies hat den Vorteil, dass beim Einsatz einer so hergestellten bandartigen Bespannung
auch in dem zu fertigenden Bahnmaterial keine durch eine Unterbrechung des Auftrags
im Nahtbereich generierte Strukturierung erzeugt wird. Dazu trägt insbesondere auch
bei, dass das Durchtrennen des Auftrags im Nahtbereich nach dem Öffnen und Wiederverschließen
des Nahtbereichs zu einer Konfiguration führt, bei welcher die aneinander unmittelbar
angrenzenden Bereiche des durchtrennten Auftrags so vorhanden sind, als wären sie
tatsächlich nicht getrennt.
[0011] Völlig unabhängig davon, mit welcher Struktur dieses Muster ausgebildet ist, kann
es in beliebiger Art und Weise über den wenigstens einen Nahtbereich hinweg geführt
sein.
[0012] Der Auftrag kann beispielsweise mit Polymermaterial aufgebaut sein.
[0013] Um eine stabile Verbindung mit dem bandartigen Substrat zu erzielen und auch den
gewünschten Effekt, beispielsweise der Beeinflussung der Permeabilität, erzeugen zu
können, wird vorgeschlagen, dass der Auftrag mit einer eindringenden Tiefe von 5%
bis 100% in das bandartige Substrat eindringt.
[0014] Bei dem in dem erfindungsgemäßen Verfahren einzusetzenden bandartigen Substrat kann
beispielsweise vorgesehen sein, dass der Nahtbereich in den im Nahtbereich liegenden
Endbereichen des bandartigen Substrates einander überlappend positionierte Schleifen
umfasst, durch welche ein sich im Wesentlichen in der Substratquerrichtung erstreckendes,
langgestrecktes Verbindungselement zum Verbinden der beiden Endbereiche hindurchgeführt
ist. Um dies zu erzielen, kann das bandartige Substrat in verschiedenster Weise aufgebaut
sein. Beispielsweise kann es als Spiralgliederband, auch bekannt als "spiral linc
fabric", oder als gewebtes Band ausgebildet sein. Sowohl beim Spiralgliederband, als
auch beim gewebten Band sind an den Endbereichen Verbindungsschleifen vorhanden, entweder
gebildet durch Gewebeschleifen oder gebildet durch schleifenartige Bereiche der Spiralbandglieder.
[0015] Die Maßnahme c) kann das Durchtrennen des Auftrags entlang des langgestreckten Verbindungselements
umfassen. Um dies mit hoher Präzision realisieren zu können, wird vorgeschlagen, dass
der Verlauf des langgestreckten Verbindungselements optisch erfasst wird und dass
eine Durchtrenneinrichtung beruhend auf dem Ergebnis der optischen Erfassung entlang
des langgestreckten Verbindungselements geführt wird.
[0016] Die vorliegende Erfindung betrifft weiterhin ein Verfahren zum Einbau einer erfindungsgemäß
hergestellten bandartigen Bespannung in eine Maschine zur Herstellung von Bahnmaterial,
wobei dieses Verfahren die folgenden Maßnahmen umfasst:
- A) Entfernen eines langgestreckten Verbindungselements aus einem Nahtbereich des bandartigen
Substrates,
- B) Eingliedern der offenen Bespannung in eine Maschine zur Herstellung von Bahnmaterial,
- C) Schließen des Nahtbereichs durch Einführen eines langgestreckten Verbindungselements
in die einander überlappend positionierten Schleifen in den miteinander zu verbindenden
Endbereichen des bandartigen Substrates.
[0017] Um den mit der erfindungsgemäß hergestellten bandartigen Bespannung angestrebten
Effekt einer möglichst nicht vorhandenen Unterbrechung des Auftrags in einem Nahtbereich
noch ausgeprägter erhalten zu können, wird weiter vorgeschlagen, dass das Verfahren
eine Maßnahme D) umfasst zum Wiederverbinden des im Bereich wenigstens einen Nahtbereichs
durchtrennten Auftrags nach der Durchführung der Maßnahme C). Dieses Wiederverbinden
kann beispielsweise durch Verkleben, Verschmelzen oder Ultraschallschweißen des aufgetrennten
Auftrags umfassen.
[0018] Gemäß einem weiteren Aspekt betrifft die vorliegende Erfindung eine bandartige Bespannung,
insbesondere für eine Maschine zur Herstellung von Bahnmaterial, insbesondere Papier
oder Karton, umfassend ein bandartiges Substrat mit wenigstens einem sich im Wesentlichen
in einer Substratquerrichtung erstreckenden Nahtbereich, in welchem Endbereiche des
bandartigen Substrates durch ein langgestrecktes und durch einander überlappend angeordnete
Schleifen der Endbereiche hindurchgeführtes Verbindungselement miteinander verbunden
oder zu verbinden sind, wobei auf dem bandartigen Substrat ein sich über wenigstens
einen Nahtbereich hinweg erstreckender und entlang wenigstens eines Nahtbereichs durchtrennter
Auftrag vorgesehen ist, wobei der Auftrag mit einem kontinuierlichen oder/und diskreten
sich über den Nahtbereich erstreckenden Auftragsmuster auf das bandartige Substrat
aufgetragen ist.
[0019] Der Auftrag kann beispielsweise aus Polymermaterial gebildet sein.
[0020] Das bandartige Substrat kann eine Vielzahl von im Wesentlichen in einer Substratquerrichtung
verlaufenden, helixartig gewundenen Gliedern umfassen, welche mit schleifenartigen
Bereichen einander überlappend angeordnet sind und durch ein durch die einander überlappend
angeordneten schleifenartigen Bereiche hindurchgeführtes, langgestrecktes Verbindungselement
miteinander verbunden sind.
[0021] Alternativ ist es selbstverständlich möglich, dass das bandartige Substrat ein Gewebesubstrat
mit in den im Nahtbereich miteinander zu verbindenden Endbereichen vorgesehenen Gewebeschleifen
umfasst.
[0022] Um bei einer in eine Maschine zur Herstellung von Bahnmaterial integrierten bandartigen
Bespannung auch dann, wenn ein zum Einbau geöffneter Nahtbereich wieder geschlossen
ist, im Bereich des Auftrags eine vollständig geschlossene Struktur bereitzustellen,
wird weiter vorgeschlagen, dass der im Bereich wenigstens eines Nahtbereichs durchtrennte
Auftrag vorzugsweise durch Verkleben, Verschmelzen oder Ultraschallschweißen wieder
verbunden ist.
[0023] Die vorliegende Erfindung wird nachfolgend mit Bezug auf die beiliegenden Zeichnungen
detailliert beschrieben. Es zeigt:
- Fig. 1
- ein mit einem Auftrag versehenes bandartiges Substrat in einer Zwi- schenphase der
Herstellung einer Bespannung für eine Maschine zur Herstellung von Bahnmaterial;
- Fig. 2
- eine spätere Phase des Herstellungvorgangs.
[0024] In Fig. 1 ist ein kurzer Abschnitt eines bandartigen Substrates 10 für eine bahnartige
Bespannung für eine Maschine zur Herstellung von Bahnmaterial, wie z.B. Papier oder
Karton, gezeigt. Bei dem in Fig. 1 erkennbaren Aufbau ist das bandartige Substrat
10 als so genanntes Spiralgliederband, auch als "spiral link fabric" bezeichnet, aufgebaut.
Dieses Spiralgliederband umfasst eine Vielzahl von mit ihrer helixartigen bzw. schraubenartig
gewundenen Struktur in einer Bandquerrichtung CMD langgestreckten Gliedern 12. Die
helixartige bzw. schraubenartige Struktur ist abgeflacht, so dass die einzelnen Windungs-
bzw. Schraubengänge an ihren beiden in der Bandlängsrichtung bzw. Laufrichtung MD
gelegenen Endbereichen jeweils Schleifen 14, 16 bilden. Die in der Bandquerrichtung
CMD unmittelbar benachbart liegenden Schleifen 14 bzw. 16 weisen einen auch durch
die Ganghöhe der Windung definierten gegenseitigen Abstand auf, der mindestens der
Materialstärke der einzelnen Glieder 12 entspricht. Auf diese Art und Weise wird es
möglich, die Schleifen 14 von einem der Glieder 12 eingreifend jeweils zwischen Schleifen
16 eines anderen Glieds 12 zu positionieren. In die so einander überlappend angeordneten
Glieder 12 kann ein beispielsweise aus Drahtmaterial oder dergleichen aufgebautes
und in Fig. 1 anhand einer Strichlinie schematisch angedeutetes, langgestrecktes Verbindungselement
18 eingeführt werden. Durch dieses Verbindungselement 18 wird also eine scharnierartige
bzw. gelenkige Verbindung unmittelbar benachbarter Glieder 12 erzeugt. Der gegenseitige
Abstand derartiger Verbindungselemente 18 in der Bandlängsrichtung MD, der etwas kleiner
ist als die Länge der einzelnen Glieder 12 in dieser Richtung, kann im Bereich von
etwa 3 mm bis 4 mm, vorzugsweise bei etwa 3,5 mm liegen.
[0025] Um die Eigenschaften der mit einem derartigen Substrat aufgebauten Bespannung für
eine Maschine zur Herstellung von Bahnmaterial beeinflussen zu können, kann beispielsweise
an derjenigen Seite des bandartigen Substrates, mit welcher auch das zu fertigende
Bahnmaterial bzw. das Ausgangsmaterial dafür in Kontakt kommen soll, ein Auftrag 20
vorgesehen sein. Dieser beispielsweise mit Polymer- bzw. allgemein Elastomermaterial
aufgebaute Auftrag 20 kann in an sich bekannter Art und Weise in einem Siebdruckverfahren,
beispielsweise mit einem Rotationssieb, oder in einem Extrusionsverfahren mit beliebigem
Muster aufgetragen werden. Dabei kann die Menge bzw. auch die Viskosität des Materials
für den Auftrag 20 so gewählt werden, dass es in definierter Art und Weise in die
offene Struktur des bandartigen Substrates 10 eindringt, beispielsweise mit einer
Eindringtiefe von 5% bis 100%. Ein nicht vollständiges Durchdringen des bandartigen
Substrates 10 ermöglicht es, dass sich an der Rückseite des Auftrags 10 bzw. innerhalb
des mit an sich offener Struktur ausgebildeten bandartigen Substrates 10 ein Luftstrom
ausbilden kann.
[0026] Das Muster, mit welchem der Auftrag 20 auf das bandartige Substrat 10 aufgetragen
wird, ist beliebig. Es kann, wie in Fig. 1 erkennbar, ein kontinuierliches Muster,
beispielsweise mit der gezeigten netzartigen Konfiguration, verwendet werden. Selbstverständlich
können auch diskrete Muster, wie z.B. punktartige Bereiche, gewählt werden.
[0027] Man erkennt in Fig. 1, dass der Auftrag 20 auch in demjenigen Bereich liegt, in dem
ein durch die einander überlappend angeordneten Schleifen 14, 16 und das in diese
eingeführte Verbindungselement generierter Nahtbereich 22 des bandartigen Substrates
10 vorhanden ist. Es sei hier darauf hingewiesen, dass bei einem derartigen bandartigen
Substrat 10, das mit den in der Fig. 1 erkennbaren Gliedern 12 aufgebaut ist, im Prinzip
jedes der langgestreckten Verbindungselemenet so aufgebaut bzw. in die zugehörigen
Schleifen eingeführt sein kann, dass es zum Öffnen des ansonsten beispielsweise in
endloser Konfiguration bereitgestellten Substrates 10 herausgezogen werden kann. Es
ist selbstverständlich, dass das bandartige Substrat 10 auch in anderer Art und Weise,
beispielsweise in einem Webverfahren hergestellt werden kann, wobei dann ein jeweiliger
Nahtbereich gebildet ist durch in den miteinander zu verbindenden Endbereichen des
bandartigen Substrates 10 gebildete Schleifen. Auch das Wickeln eines derartigen bandartigen
Substrates 10 um jeweilige die Schleifen in den Endbereichen bildende Wickeldorne
ist möglich. Tatsächlich ist darauf hinzuweisen, dass die nachfolgend noch detaillierter
erläuterte erfindungsgemäße Vorgehensweise bei jedwedem bandartigen Substrat 10 eingesetzt
werden kann, bei dem ein Nahtbereich gebildet ist, in dem zwei miteinander zu verbindende
Endbereiche des Substrates 10 vorhanden sind und beispielsweise durch Einsatz eines
langgestreckten Verbindungselements miteinander verbunden bzw. bei Entfernen dieses
Verbindungselements voneinander gelöst werden können.
[0028] Bei der erfindungsgemäßen Vorgehensweise wird also der Auftrag 20 mit seiner gewünschten
Struktur aufgebracht, beispielsweise in einem Zustand, in welchem das Substrat 10
in seiner geschlossenen, also endlosen Konfiguration in eine Auftragestation eingebaut
ist. Nach dem Aufbringen des Auftrags 20 mit beliebigem Muster kann beispielsweise
zunächst das Material des Auftrags 20 möglicherweise auch unter Wärmeeinfluss ausgehärtet
werden. Nachfolgend wird dann durch ein in Fig. 1 schematisch angedeutetes Durchtrennwerkzeug
24 der Auftrag 20 im Nahtbereich 22 durchtrennt. Dazu kann vorzugsweise so vorgegangen
werden, dass vermittels optischer Erfassungssysteme, beispielsweise optischen Detektoren
oder Kameras, der Verlauf des langgestreckten Verbindungselements 18 bzw. des Nahtbereichs
22 exakt ermittelt wird und das Werkzeug 24 dann bezüglich des mit dem Auftrag 20
versehenen Substrates 10 so geführt wird, dass der Auftrag 20 direkt über dem Nahtbereich
22 bzw. dem darin sich erstreckenden langgestreckten Verbindungselement 18 durchtrennt
wird. Dazu wird das Werkzeug 24 dann in einer Schnittrichtung S, welche im Wesentlichen
auch der Bandquerrichtung CMD entsprechen wird, bewegt. Dieses Durchtrennen, also
beispielsweise Durchschneiden, erfolgt weiterhin so, dass nur der Auftrag 20 durchtrennt
wird, jedoch das darunter liegende bandartige Substrat 10 nicht beschädigt wird.
[0029] Nachdem auf diese Art und Weise also das bandartige Substrat 10 bzw. die damit aufgebaute
Bespannung hergestellt worden ist, kann zum Eingliedern derselben in eine Maschine
zur Herstellung von Bahnmaterial der Nahtbereich 22 oder zumindest einer der Nahtbereiche
22 geöffnet werden. Dazu kann, wie in Fig. 2 erkennbar, das langgestreckte Verbindungselement
18 aus dem Bereich der sich überlappend positionierten Schleifen 14, 16 herausgezogen
werden, so dass die beiden in Fig. 2 erkennbaren Endbereiche 26, 28 der Bespannung
bzw. des Substrates 10 voneinander weg bewegt werden können und somit der zuvor gebildete
Durchtrennungsbereich bzw. Schnitt im Auftrag 20 erkennbar wird.
[0030] Nachdem die nunmehr in offener Konfiguration vorliegende Bespannung in eine Maschine
zur Herstellung von Bahnmaterial eingegliedert worden ist, können die beiden Endbereiche
26, 28 wieder so bezüglich einander positioniert werden, dass die Schleifen 14, 16
der Glieder 12 ineinander eingreifen bzw. sich überlappen und den Raum zur Aufnahme
des langgestreckten Verbindungselements 18 bereitstellen. Dieses kann in diesen Raum
dann wieder eingeführt werden, um auf diese Art und Weise wieder die geschlossene,
endlose Konfiguration der Bespannung zu erzeugen. In diesem Zustand liegen die beiden
zuvor getrennten Bereiche 30, 32 des Auftrags 20 wieder unmittelbar einander gegenüber
und berühren sich ggf.. Die bedeutet, dass trotz des Durchtrennens der Auftrags 20
im Arbeitszustand der so hergestellten Bespannung ein faktisch ununterbrochenes Auftragsmuster
des Auftrags 20 vorhanden sein wird. Um diesen Effekt noch stärker auszuprägen, kann
nach dem Eingliedern der Bespannung in eine Maschine zur Herstellung von Bahnmaterial
und dem Wiederverbinden der Endbereiche 26, 28 der Auftrag 20 in seinen unmittelbar
benachbart liegenden Bereichen 30, 32 auch wieder verbunden werden. Dies kann beispielsweise
durch Verkleben oder insbesondere bei Einsatz thermoplastischer Materialien durch
Verschmelzen oder Ultraschallschweißen erfolgen.
[0031] Es ist dann eine völlig geschlossene Struktur sowohl des bandartigen Substrates 12,
als auch des Auftrags 20 vorhanden.
[0032] Aus der vorangehenden Beschreibung erkennt man, dass bei der erfindungsgemäßen Vorgehensweise
bzw. der erfindungsgemäßen Bespannung ein Auftrag mit beliebigem Muster und selbstverständlich
auch aus beliebigem Material vorgesehen sein kann. Wie bereits erwähnt, ist es vorteilhaft,
Elastomermaterial bzw. Polymermaterial einzusetzen, das wahlweise hydrophobe Eigenschaften,
hydrophile Eigenschaften oder lokal unterschiedliche hydrophobe und hydrophile Eigenschaften
aufweisen kann und vorzugsweise Temperaturen von mindestens bis zu 250°C aushalten
sollte.
[0033] Bei einer alternativen Vorgehensweise zum Eingliedern einer mit einem Auftrag 20
auf einem bandartigen Substrat 10 aufgebauten Bespannung in eine Maschine zur Herstellung
von Bahnmaterial kann so vorgegangen werden, dass die Bespannung in geschlossener,
also endloser Konfiguration eingegliedert wird, wenn dies beispielsweise auf Grund
der konstruktiven Auslegung der betroffenen Maschine zur Herstellung von Bahnmaterial
vorteilhaft ist. Es ist dann ggf. auch nicht erforderlich, den Auftrag 20 in einem
Nahtbereich zu durchtrennen, bevor die Bespannung in eine derartige Maschine eingegliedert
wird. Soll jedoch dann zu Wartungszwecken die Bespannung herausgenommen und wieder
in die Maschine integriert werden, kann vor dem Herausnehmen durch ein geeignetes
Werkzeug der Auftrag 20 in einem Nahtbereich 22 durchtrennt werden, um die Bespannung
herausnehmen zu können und sie ggf. dann in der vorangehend beschriebenen Art und
Weise wieder in die Maschine eingliedern zu können. Dies bedeutet, dass die erfindungsgemäße
Maßnahme c) auch erst bei einer in eine Maschine integrierten bandartigen Bespannung
durchgeführt werden kann.
[0034] Es ist hier darauf hinzuweisen, dass vorangehend die besonderen Vorteile der erfindungsgemäßen
Vorgehensweise bzw. der erfindungsgemäßen Bespannung in Verbindung mit dem Einsatz
bei einer Maschine zur Herstellung von Bahnmaterial beschrieben wurde. Es ist selbstverständlich,
dass die vorliegende Erfindung nicht nur für bandartige Bespannungen derartiger Maschinen
zur Herstellung von Bahnmaterial, also beispielsweise Papiermaschinen, Anwendung finden
kann. Selbstverständlich kann sie bei jedweder anderen industriellen Anwendung, in
welcher derartige langgestreckte und im Allgemeinen in Endloskonfiguration arbeitende
Bespannungen Einsatz finden, zur Anwendung kommen.
1. Verfahren zur Herstellung einer bandartigen Bespannung insbesondere für eine Maschine
zur Herstellung von Bahnmaterial, insbesondere Papier oder Karton, umfassend die Maßnahmen:
a) Bereitstellen eines bandartigen Substrates (10) mit wenigstens einem im Wesentlichen
in Substratquerrichtung (CMD) sich erstreckenden Nahtbereich (22),
b) Aufbringen eines Auftrags (20) auf das bandartige Substrat (10) derart, dass der
Auftrag (20) sich über wenigstens einen Nahtbereich (22) hinweg erstreckt,
c) Durchtrennen des Auftrags (20) entlang wenigstens eines Nahtbereichs (22),
dadurch gekennzeichnet, dass der Auftrag (20) mit einem kontinuierlichen oder/und diskreten sich über den Nahtbereich
erstreckenden Auftragsmuster auf das bandartige Substrat (10) aufgetragen wird.
2. Verfahren nach Anspruch 1, dadurch gekennzeichnet, dass der Auftrag (20) mit Polymermaterial aufgebaut ist.
3. Verfahren nach einem der Ansprüche 1 und 2, dadurch gekennzeichnet, dass der Auftrag (20) mit einer eindringenden Tiefe von 5% bis 100% in das bandartige
Substrat (10) eindringt.
4. Verfahren nach einem der Ansprüche 1 bis 3, dadurch gekennzeichnet, dass der wenigstens eine Nahtbereich (22) des bandartigen Substrates (10) in den im Nahtbereich
(22) liegenden Endbereichen (26, 28) desselben einander überlappend positionierte
Schleifen (14, 16) umfasst, durch welche ein sich im Wesentlichen in der Substratquerrichtung
(CMD) erstreckendes, langgestrecktes Verbindungselement (18) zum Verbinden der beiden
Endbereiche (26, 28) hindurchgeführt ist.
5. Verfahren nach Anspruch 4, dadurch gekennzeichnet, dass als bandartiges Substrat (10) ein Spiralgliederband oder ein gewebtes Band mit Verbindungsschleifen
(14, 16) an den im Nahtbereich (22) zu verbindenden Endbereichen (26, 28) verwendet
wird.
6. Verfahren nach Anspruch 4 oder 5, dadurch gekennzeichnet, dass die Maßnahme c) das Durchtrennen des Auftrags (20) entlang des langgestreckten Verbindungselements
(18) umfasst.
7. Verfahren nach Anspruch 6, dadurch gekennzeichnet, dass der Verlauf des langgestreckten Verbindungselements (18) optisch erfasst wird und
dass eine Durchtrenneinrichtung (24) beruhend auf dem Ergebnis der optischen Erfassung
entlang des langgestreckten Verbindungselements (18) geführt wird.
8. Verfahren zum Einbau einer nach dem Verfahren der Ansprüche 1 bis 7 hergestellten
bandartigen Bespannung in eine Maschine zur Herstellung von Bahnmaterial, umfassend
die Maßnahmen:
A) Entfernen eines langgestreckten Verbindungselements (18) aus einem Nahtbereich
(22) des bandartigen Substrates (10),
B) Eingliedern der offenen Bespannung in eine Maschine zur Herstellung von Bahnmaterial,
C) Schließen des Nahtbereichs (22) durch Einführen eines langgestreckten Verbindungselements
(18) in die einander überlappend positionierten Schleifen (14, 16) in den miteinander
zu verbindenden Endbereichen (26, 28) des bandartigen Substrates (10).
9. Verfahren nach Anspruch 8, dadurch gekennzeichnet, dass das Verfahren eine Maßnahme D) umfasst zum Wiederverbinden des im Bereich wenigstens
einen Nahtbereichs (22) durchtrennten Auftrags (20) nach der Durchführung der Maßnahme
C).
10. Verfahren nach Anspruch 9, dadurch gekennzeichnet, dass die Maßnahme D) das Verkleben, Verschmelzen oder Ultraschallschweißen des aufgetrennten
Auftrags (20) umfasst.
11. Bandartige Bespannung, insbesondere für eine Maschine zur Herstellung von Bahnmaterial,
insbesondere Papier oder Karton, umfassend ein bandartiges Substrat (10) mit wenigstens
einem sich im Wesentlichen in einer Substratquerrichtung (CMD) erstreckenden Nahtbereich
(22), in welchem Endbereiche (26, 28) des bandartigen Substrates (10) durch ein langgestrecktes
und durch einander überlappend angeordnete Schleifen (14, 16) der Endbereiche (26,
28) hindurchgeführtes Verbindungselement (18) miteinander verbunden oder zu verbinden
sind, wobei auf dem bandartigen Substrat (10) ein sich über wenigstens einen Nahtbereich
(22) hinweg erstreckender und entlang wenigstens eines Nahtbereichs (22) durchtrennter
Auftrag (20) vorgesehen ist, dadurch gekennzeichnet, dass der Auftrag (20) mit einem kontinuierlichen oder/und diskreten sich über den Nahtbereich
erstreckenden Auftragsmuster aufgetragen ist.
12. Bandartige Bespannung nach Anspruch 11, dadurch gekennzeichnet, dass der Auftrag (20) aus Polymermaterial gebildet ist.
13. Bandartige Bespannung nach einem der Ansprüche 11 bis 12, dadurch gekennzeichnet, dass das bandartige Substrat (10) eine Vielzahl von im Wesentlichen in einer Substratquerrichtung
(CMD) verlaufenden, helixartig gewundenen Gliedern (12) umfasst, welche mit schleifenartigen
Bereichen (14, 16) einander überlappend angeordnet sind und durch ein durch die einander
überlappend angeordneten schleifenartigen Bereiche (14, 16) hindurchgeführtes, langgestrecktes
Verbindungselement (18) miteinander verbunden sind.
14. Bandartige Bespannung nach einem der Ansprüche 11 bis 13, dadurch gekennzeichnet, dass das bandartige Substrat (10) ein Gewebesubstrat mit in den im Nahtbereich miteinander
zu verbindenden Endbereichen vorgesehenen Gewebeschleifen umfasst.
15. Bandartige Bespannung nach einem der Ansprüche 11 bis 14, dadurch gekennzeichnet, dass der im Bereich wenigstens eines Nahtbereichs durchtrennte Auftrag (20) vorzugsweise
durch Verkleben, Verschmelzen oder Ultraschallschweißen wieder verbunden ist.
1. Method for producing a belt-like fabric, in particular for a machine for producing
web material, in particular paper or cardboard, comprising the following measures:
a) provision of a belt-like substrate (10) with at least one seam region (22) which
extends substantially in the substrate transverse direction (CMD),
b) application of a coat (20) to the belt-like substrate (10) in such a way that the
coat (20) extends over at least one seam region (22),
c) severing of the coat (20) along at least one seam region (22),
characterized in that the coat (20) is applied to the belt-like substrate (10) with a continuous and/or
discrete coat pattern which extends over the seam region.
2. Method according to Claim 1, characterized in that the coat (20) is built up with polymer material.
3. Method according to either of Claims 1 and 2, characterized in that the coat (20) penetrates into the belt-like substrate (10) with a penetrating depth
from 5% to 100%.
4. Method according to one of Claims 1 to 3, characterized in that the at least one seam region (22) of the web-like substrate (10) comprises loops
(14, 16) which are positioned so as to overlap one another in those end regions (26,
28) of the said belt-like substrate (10) which lie in the seam region (22), through
which loops (14, 16) an elongate connecting element (18) which extends substantially
in the substrate transverse direction (CMD) is guided in order to connect the two
end regions (26, 28).
5. Method according to Claim 4, characterized in that a helical-link belt or a woven belt with connecting loops (14, 16) at the end regions
(26, 28) to be connected in the seam region (22) is used as belt-like substrate (10).
6. Method according to Claim 4 or 5, characterized in that measure c) comprises severing the coat (20) along the elongate connecting element
(18).
7. Method according to Claim 6, characterized in that the course of the elongate connecting element (18) is sensed optically, and in that a severing device (24) is guided along the elongate connecting element (18) based
on the result of the optical sensing operation.
8. Method for installing a belt-like fabric which is produced according to the method
of Claims 1 to 7 in a machine for producing web material, comprising the following
measures:
A) removal of an elongate connecting element (18) from a seam region (22) of the belt-like
substrate (10),
B) integration of the open fabric into a machine for producing web material,
C) closing of the seam region (22) by insertion of an elongate connecting element
(18) into the loops (14, 16) which are positioned so as to overlap one another in
those end regions (26, 28) of the belt-like substrate (10) which are to be connected
to one another.
9. Method according to Claim 8, characterized in that the method comprises a measure D) for re-connecting the coat (20) which has been
severed in the region of at least one seam region (22), after measure C) has been
carried out.
10. Method according to Claim 9, characterized in that measure D) comprises the adhesive bonding, fusing or ultrasound welding of the severed
coat (20).
11. Belt-like fabric, in particular for a machine for producing web material, in particular
paper or cardboard, comprising a belt-like substrate (10) having at least one seam
region (22) which extends substantially in a substrate transverse direction (CMD)
and in which end regions (26, 28) of the belt-like substrate (10) are connected to
one another or are to be connected to one another by an elongate connecting element
(18) which is guided through loops (14, 16) of the end regions (26, 28), which loops
(14, 16) are arranged so as to overlap one another, a coat (20) which extends over
at least one seam region (22) and has been severed along at least one seam region
(22) being provided on the belt-like substrate (10), characterized in that the coat (20) is applied with a continuous and/or discrete coat pattern which extends
over the seam region.
12. Belt-like fabric according to Claim 11, characterized in that the coat (20) is formed from polymer material.
13. Belt-like fabric according to either of Claims 11 and 12, characterized in that the belt-like substrate (10) comprises a multiplicity of helically wound links (12)
which extend substantially in a substrate transverse direction (CMD), are arranged
so as to overlap one another with loop-like regions (14, 16), and are connected to
one another by an elongate connecting element (18) which is guided through the loop-like
regions (14, 16) which are arranged so as to overlap one another.
14. Belt-like fabric according to one of Claims 11 to 13, characterized in that the belt-like substrate (10) comprises a woven-fabric substrate with woven-fabric
loops which are provided in the end regions which are to be connected to one another
in the seam region.
15. Belt-like fabric according to one of Claims 11 to 14, characterized in that the coat (20) which has been severed in the region of at least one seam region is
preferably re-connected by adhesive bonding, fusing or ultrasound welding.
1. Procédé de fabrication d'une toile en forme de bande, en particulier pour une machine
de fabrication de matériau en nappe, en particulier du papier ou du carton, le procédé
comportant les étapes qui consistent à :
a) prévoir un support (10) en forme de bande qui présente au moins une zone de soudage
(22) qui s'étend essentiellement dans la direction transversale (CMD) du support,
b) appliquer un revêtement (20) sur le support (10) en forme de bande de telle sorte
que le revêtement (20) s'étende au-delà d'au moins une zone de soudage (22),
c) découper le revêtement (20) sur au moins une zone de soudage (22),
caractérisé en ce que
le revêtement (20) est appliqué selon un motif d'application qui s'étend en continu
et/ou de manière distincte sur la zone de soudage du support (10) en forme de bande.
2. Procédé selon la revendication 1, caractérisé en ce que le revêtement (20) est constitué d'un matériau polymère.
3. Procédé selon l'une des revendications 1 et 2, caractérisé en ce que le revêtement (20) pénètre dans le support (10) en forme de bande sur une profondeur
de 5 % à 100 %.
4. Procédé selon l'une des revendications 1 à 3, caractérisé en ce que la ou les zones de soudage (22) du support (10) en forme de bande comprennent des
boucles (14, 16) placées en superposition mutuelle dans les parties d'extrémité (26,
28) situées dans la zone de soudage (22) et traversées par un élément de liaison (18)
allongé qui s'étend essentiellement dans la direction transversale (CMD) du support
pour relier les deux régions d'extrémité (26, 28).
5. Procédé selon la revendication 4, caractérisé en ce qu'il utilise comme support (10) en forme de bande une bande d'éléments en spirale ou
une bande tissée dotée de boucles de liaison (14, 16) sur les parties d'extrémité
(26, 28) qui doivent être reliées dans la zone de soudage (22).
6. Procédé selon les revendications 4 ou 5, caractérisé en ce que la disposition c) comporte la séparation du revêtement (20) le long de l'élément
de liaison (18) allongé.
7. Procédé selon la revendication 6, caractérisé en ce que la forme de l'élément allongé de liaison (18) est détectée optiquement et en ce qu'un dispositif de séparation (24) est guidé le long de l'élément allongé de liaison
(18) sur base du résultat de la détection optique.
8. Procédé d'incorporation d'une toile en forme de bande réalisée avec le procédé selon
les revendications 1 à 7 dans une machine de fabrication de matériau en nappe, le
procédé comportant les dispositions qui consistent à :
A) enlever un élément allongé de liaison (18) d'une zone de soudage (22) du support
(10) en forme de bande,
B) placer la toile ouverte dans une machine de fabrication de matériau en nappe,
C) fermer la zone de soudage (22) en introduisant un élément allongé de liaison (18)
dans les boucles (14, 16) placées en superposition mutuelle dans les parties d'extrémité
(26, 28), qui doivent être reliées l'une à l'autre, du support (10) en forme de bande.
9. Procédé selon la revendication 8, caractérisé en ce que le procédé comprend une étape D) qui relie de nouveau le revêtement (20) séparé dans
la zone occupée par au moins une zone de soudage (22) après l'exécution de l'étape
C).
10. Procédé selon la revendication 9, caractérisé en ce que l'étape D) comporte le collage, la fusion ou le soudage par ultrasons du revêtement
(20) découpé.
11. Toile en forme de bande, en particulier pour machine de fabrication de matériau en
nappe, en particulier de papier ou de carton, comprenant un support (10) en forme
de bande qui présente au moins une zone de soudage (22) qui s'étend essentiellement
dans une direction (CMD) transversale par rapport au support et dans laquelle des
parties d'extrémité (26, 28) du support (10) en forme de bande sont reliées ou doivent
être reliées l'une à l'autre par un élément allongé de liaison (18) qui traverse des
boucles (14, 16), disposées en superposition mutuelle, des parties d'extrémité (26,
28), un revêtement (20) qui s'étend au-delà d'au moins une zone de soudage (22) et
découpé le long d'au moins une zone de soudage (22) étant prévu sur le support (10)
en forme de bande,
caractérisée en ce que
le revêtement (20) est appliqué selon un motif d'application continu et/ou discontinu
qui s'étend au-dessus de la zone de soudage.
12. Toile en forme de bande selon la revendication 11, caractérisée en ce que le revêtement (20) est formé d'un matériau polymère.
13. Toile en forme de bande selon l'une des revendications 11 à 12, caractérisée en ce que le support (10) en forme de bande comporte plusieurs éléments (12) enroulés en hélice
et s'étendant essentiellement dans une direction (CMD) transversale par rapport au
support, disposés en superposition mutuelle avec les zones (14, 16) en forme de boucle
et reliés les uns aux autres par un élément allongé de liaison (18) qui traverse les
zones (14, 16) en forme de boucle disposées en superposition mutuelle.
14. Toile en forme de bande selon l'une des revendications 11 à 13, caractérisée en ce que le support (10) en forme de bande comprend un support tissé qui présente des boucles
tissées prévues dans les parties d'extrémité qui doivent être reliées l'une à l'autre
dans la zone de la soudage.
15. Toile en forme de bande selon l'une des revendications 11 à 14, caractérisée en ce que le revêtement (20) découpé dans la zone d'au moins une zone de soudage est de nouveau
relié, de préférence par collage, fusion ou soudage par ultrasons.
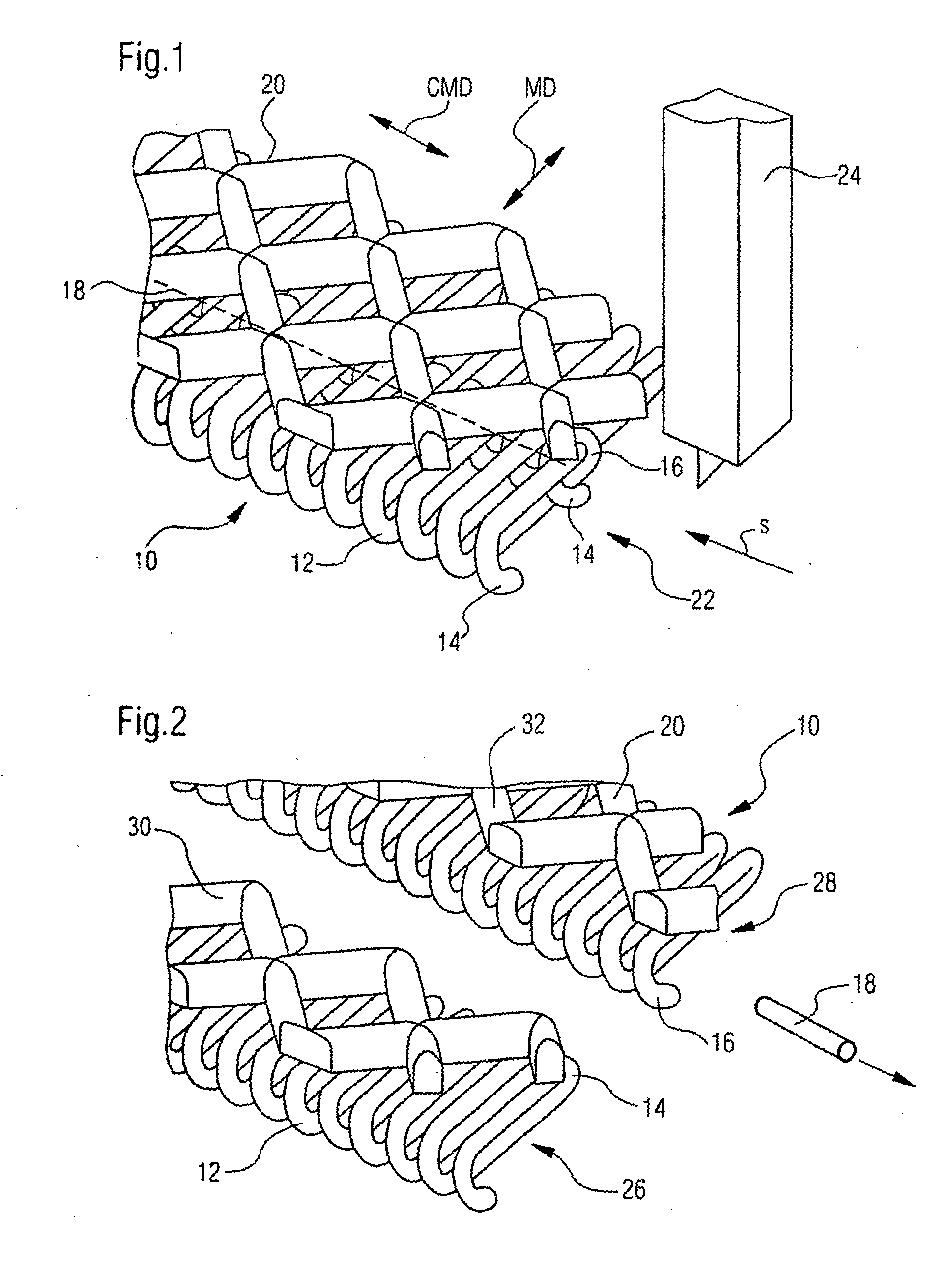
IN DER BESCHREIBUNG AUFGEFÜHRTE DOKUMENTE
Diese Liste der vom Anmelder aufgeführten Dokumente wurde ausschließlich zur Information
des Lesers aufgenommen und ist nicht Bestandteil des europäischen Patentdokumentes.
Sie wurde mit größter Sorgfalt zusammengestellt; das EPA übernimmt jedoch keinerlei
Haftung für etwaige Fehler oder Auslassungen.
In der Beschreibung aufgeführte Patentdokumente