(19) |
 |
|
(11) |
EP 2 216 149 B1 |
(12) |
EUROPÄISCHE PATENTSCHRIFT |
(45) |
Hinweis auf die Patenterteilung: |
|
23.03.2011 Patentblatt 2011/12 |
(22) |
Anmeldetag: 02.02.2010 |
|
(51) |
Internationale Patentklassifikation (IPC):
|
|
(54) |
Verfahren zur Herstellung von Spanplatten
Method for manufacturing chipboards
Procédé de fabrication de panneaux de particules
|
(84) |
Benannte Vertragsstaaten: |
|
AT BE BG CH CY CZ DE DK EE ES FI FR GB GR HR HU IE IS IT LI LT LU LV MC MK MT NL NO
PL PT RO SE SI SK SM TR |
(30) |
Priorität: |
04.02.2009 DE 102009000623
|
(43) |
Veröffentlichungstag der Anmeldung: |
|
11.08.2010 Patentblatt 2010/32 |
(73) |
Patentinhaber: GLUNZ AG |
|
49716 Meppen (DE) |
|
(72) |
Erfinder: |
|
- Wiemann, Dieter
32756, Detmold (DE)
|
(74) |
Vertreter: Rehberg, Bernhard Frank |
|
Rehberg Hüppe + Partner
Nikolausberger Weg 62 37073 Göttingen 37073 Göttingen (DE) |
(56) |
Entgegenhaltungen: :
EP-A1- 1 033 212 DE-A1- 2 934 212 DE-A1- 19 751 326
|
WO-A1-03/095167 DE-A1- 19 622 421 US-A- 4 035 120
|
|
|
|
|
|
|
|
|
Anmerkung: Innerhalb von neun Monaten nach der Bekanntmachung des Hinweises auf die
Erteilung des europäischen Patents kann jedermann beim Europäischen Patentamt gegen
das erteilte europäischen Patent Einspruch einlegen. Der Einspruch ist schriftlich
einzureichen und zu begründen. Er gilt erst als eingelegt, wenn die Einspruchsgebühr
entrichtet worden ist. (Art. 99(1) Europäisches Patentübereinkommen). |
TECHNISCHES GEBIET DER ERFINDUNG
[0001] Die Erfindung bezieht sich auf ein Verfahren zur Herstellung von Spanplatten unter
Verwendung von Altholz und Frischholz mit den Merkmalen des Oberbegriffs des unabhängigen
Patentanspruchs 1.
[0002] Die geeigneten Ressourcen für Frischholz für die Herstellung von Holzwerkstoffen
sind begrenzt. Es wird daher notwendig, für die Herstellung von Holzwerkstoffprodukten
zunehmend auf Alt- oder Recyclingholz zurückzugreifen, dabei wird hier und im Folgenden
der Begriff Altholz für Holz verwendet, das bereits zuvor einmal zu einem Produkt
verarbeitet wurde.
[0003] Die Erfindung befasst sich mit einer möglichst weitgehenden Verwendung von Altholz
für die Herstellung von Spanplatten, ohne deren technologischen Eigenschaften zu beeinträchtigen.
STAND DER TECHNIK
[0004] In der Spanplattenindustrie ist eine sogenannte zwei-strängige Spanaufbereitung bekannt.
Hierbei werden Späne aus frischem Holz, in der Regel Schneidspäne und/oder Gatterspäne,
und Späne aus Altholz in separaten Linien getrocknet und danach in separaten Siebeinrichtungen
fraktioniert. Dabei werden die Späne in beiden Linien in vier Fraktionen aufgeteilt:
(1) übergroße Späne, die zurück zur Zerkleinerung geführt werden, (2) Späne für die
Mittelschicht der Spanplatten, (3) Späne für die Deckschichten der Spanplatten und
(4) Staub, der in begrenztem Umfang den Deckschichten zugeschlagen werden kann und
ansonsten verbrannt wird. Dabei kann die Ausbeute der einzelnen Fraktionen neben der
Art der Generierung der Späne durch die Maschenweite der Siebbespannungen beeinflusst
werden. In jedem Fall entstehen in beiden Linien grobe Späne, die in der Mittelschicht
der Spanplatten eingesetzt werden können, und feine Späne für die Deckschichten der
Spanplatten. Falls in den Sieben der Fraktion (3) nicht ausreichend Späne für die
Deckschichten anfallen, werden Späne der Fraktion (2) der Mittelschicht zu Deckschichtspänen
nachzerkleinert. Bei der bekannten zwei-strängigen Spanaufbereitung werden die Späne
nach der individuellen Aufbereitung von Spänen aus Frischholz und Spänen aus Altholz
fraktionsweise zusammengeführt, beleimt und danach mit je einem Streuaggregat für
die untere Deckschicht, die Mittelschicht und die obere Deckschicht gestreut. Als
Streuaggregate werden typischerweise entweder Windstreukammern (Absetzkammern) oder
Rollensiebe eingesetzt. Windstreukammern fraktionieren nach der Flugeigenschaft der
Späne, also nach Größe und Gewicht. Dabei fallen große, aber auch kleine schwere Teile
vor den kleinen leichten Teilen aus dem Luftstrom aus. Rollensiebe mit einem Rollenbett
fraktionieren nach der Größe der Späne. Dadurch entsteht ein Schichtaufbau von fein
nach grob. Auch wenn die Fraktion (3) der Altholzlinie, d. h. die Deckschichtfraktion
der Späne aus Altholz, nach dem Sieben beispielsweise in einem Steigsichter nachgereinigt
wird, kann nicht verhindert werden, dass sich in den Deckschichten Störstoffe aus
dem Altholz wiederfinden, zu denen beispielsweise Mineralien, feiner Sand, Glas und
Kunststoffe zählen. Diese Störstoffe behindern das Schleifen der Oberflächen der Spanplatten.
Sie erzeugen Ausbrüche an Schnittkanten beim Zerteilen der Spanplatten in kleinere
Formate. Ferner erreicht die Plattenoberfläche aufgrund der Störstoffe nicht die Qualität
einer Feinstschichtoberfläche einer ausschließlich aus Frischholz hergestellten Spanplatte.
Erfahrungsgemäß sind auch die Standzeiten der Schleifbänder wesentlich kürzer, wenn
in den Deckschichten viel Altholz enthalten. Die geschilderten Mängel treten besonders
deutlich hervor, wenn die Deckschichten der Spanplatten mit Rollensieben hergestellt
werden.
[0005] Aus der
DE 197 51 326 A1 ist ein Verfahren zur Herstellung von Holzwerkstoffen, einschließlich Spanplatten,
unter Verwendung von Altholz und Frischholz mit den Merkmalen des Oberbegriffs des
unabhängigen Patentanspruchs 1 bekannt. Speziell soll dabei aminoplasthaltiges Altholz
zum Einsatz kommen. Das zerkleinerte Altholz wird mit den in üblichen Zusatzmengen
mit Aminoplast beleimten Frischspänen gemischt und so als Deckschicht- oder Mittelschichtmaterial
bei der üblichen Herstellung von Spanplatten eingesetzt.
[0006] Aus der
DE 196 22 421 A1 ist ein Verfahren zur Aufbereitung von Altholz bekannt, um Hackschnitzel für die
Herstellung von Spanplatten zu gewinnen.
[0007] Aus der
DE 29 34 212 A1 ist eine Kombiplatte bekannt, bei der Deckschichten aus Holz und eine Mittelschicht
aus anderen Materialarten, wie z. B. Hanf, Flachs, Bagasse, Reisstroh, Stroh usw.,
ggf. unter Zusatz von Holz, ausgebildet werden, um statt des knapper werdenden Rohstoffs
Holz Abfallstoffe in der Mittelschicht einzusetzen. Dabei erfolgt die Aufbereitung
der Holzspäne für die Deckschichten und der Materialien für die Mittelschicht in getrennten
Spanaufbereitungssträngen.
AUFGABE DER ERFINDUNG
[0008] Der Erfindung liegt die Aufgabe zugrunde, ein Verfahren mit den Merkmalen den Oberbegriffs
des unabhängigen Patentanspruchs 1 aufzuzeigen, mit dem unter möglichst weitreichender
Verwendung von Altholz hochwertige Spanplatten mit besten technologischen Eigenschaften
und hochwertiger Oberfläche herstellbar sind.
LÖSUNG
[0009] Erfindungsgemäß wird die Aufgabe durch ein Verfahren mit den Merkmalen des unabhängigen
Patentanspruchs 1 gelöst. Die abhängigen Patentansprüche 2 bis 12 betreffen bevorzugte
Ausführungsformen des neuen Verfahrens. Der Patentanspruch 13 ist auf eine nach dem
neuen Verfahren hergestellte Spanplatte gerichtet.
BESCHREIBUNG DER ERFINDUNG
[0010] Bei dem neuen Verfahren zur Herstellung von Spanplatten unter Verwendung von Altholz
und Frischholz werden neben den Spänen für die Mittelschicht auch die Späne für jeweils
zwei Deckschichten auf jeder Seite der Spanplatten getrennt aufbereitet. Das heißt,
auf jeder Seite der Spanplatten gibt es eine äußere Deckschicht, für die die Späne
zumindest überwiegend aus Frischholz aufbereitet werden, und eine innere Deckschicht,
für die die Späne zumindest überwiegend aus Altholz aufbereitet werden. Die Späne
für die äußeren und die inneren Deckschichten werden bei der Herstellung der Spanplatte
durchgängig getrennt voneinander gehalten und auch separat beleimt und gestreut. So
sind die Späne aus Frischholz in den äußeren Deckschichten konzentriert, während die
Späne aus Altholz in den inneren Deckschichten und in der Mittelschicht konzentriert
sind. Auf diese Weise wird der maximal mögliche Nutzen aus dem eingesetzten Frischholz
gezogen. Sowohl die positiven Auswirkungen des Frischholzes auf die technologischen
Eigenschaften der Spanplatten als auch auf deren Oberflächenqualität wirken sich in
den äußeren Deckschichten maximal aus. So entspricht die Qualität der Plattenoberfläche
einer erfindungsgemäß hergestellten Spanplatte der Qualität der Oberfläche einer Spanplatte,
die insgesamt ausschließlich aus Frischholz hergestellt ist. Späne aus Frischholz
können wesentlich länger und schlanker als Späne aus Altholz ausgebildet werden. Dadurch
kann bei Erzielung gleicher Festigkeitswerte weniger Bindemittel in den äußeren Deckschichten
eingesetzt werden. Die Festigkeit einer Spanplatte wird im Wesentlichen durch ihre
Biegefestigkeit bestimmt. Die Biegefestigkeit wiederum wird durch die Spanqualität,
d. h. den Schlankheitsgrad, und den Beleimungsgrad insbesondere der äußeren Deckschichten
bestimmt. Aus diesen Gründen können bei Erzielung vergleichbarer Festigkeitseigenschaften
auch die Späne aus Altholz in den inneren Deckschichten, die bei einer erfindungsgemäß
hergestellten Spanplatte unter den biegefesten äußeren Deckschichten liegen, mit weniger
Bindemittel beleimt werden. Bekanntlich haben feine Späne aus Altholz eine etwa kubische
Struktur und damit eine wesentlich größere Oberfläche bezogen auf das Gewicht als
Späne aus Frischholz und benötigen deshalb normalerweise entsprechend mehr Bindemittel.
Hierdurch wird üblicherweise ein Teil des Kostenvorteils von Altholz gegenüber Frischholz,
das als solches teurer ist und zum Trocknen mehr Energie erfordert, kompensiert. Bei
dem erfindungsgemäßen Verfahren kann jedoch ein maximaler Kostenvorteil durch den
Einsatz des Altholzes erzielt werden, da es mit einem relativ geringen Bindemittelanteil
verwendet wird. So können u.a. Platten mit einem sehr hohen Altholzanteil hergestellt
werden, deren Oberflächen direkt lackier- und bedruckbar sind.
[0011] Wenn auch bei dem erfindungsgemäßen Verfahren nur wenig Frischholz zum Einsatz kommt,
so werden doch die äußeren Deckschichten vorzugsweise nur aus Frischholz zusammengesetzt,
um ihre Oberflächenqualität zu maximieren. Dabei kann Schleifstaub vom Schleifen der
erfindungsgemäß hergestellten Spanplatten zurückgeführt und den Deckschichten zugesetzt
werden. Dieser Schleifstaub ist im vorliegenden Fall wie Frischholz zu bewerten, da
er durch Schleifen der ausschließlich aus Frischholz bestehenden Deckschichten entsteht
und entsprechend keine Störstoffe enthält.
[0012] Demgegenüber können bei dem neuen Verfahren die inneren Deckschichten ebenso wie
die Mittelschicht der Spanplatten ausschließlich aus Altholz zusammengesetzt werden.
Entsprechend ist es bei dem neuen Verfahren bevorzugt, alle aus dem Frischholz gewonnenen
Späne auf eine Größe zu zerkleinern, die sie für die Verwendung in den äußeren Deckschichten
geeignet macht. Grundsätzlich kann die Mittelschicht bei dem erfindungsgemäßen Verfahren
auch aus Spänen aus Altholz und Spänen aus Frischholz gestreut werden.
[0013] Weil die Späne aus Frischholz erfindungsgemäß nur oder doch zumindest weit überwiegend
für die Deckschichten eingesetzt werden, ist für deren Trocknung nur eine vergleichsweise
kleine Trocknungseinrichtung erforderlich.
[0014] Die vollständig getrennte Aufbereitung der Späne für die inneren und äußeren Deckschichten
macht es auch möglich, die Beleimung der verschiedenen Deckschichten in Hinblick auf
die enthaltenen Späne und ihre Funktion zu optimieren. Hierfür können unterschiedliche
Bindemittelmengen oder auch Bindemittelzusammensetzungen zur Anwendung kommen.
[0015] Um den Bindemittelbedarf bei dem neuen Verfahren ohne Nachteile für die hergestellten
Spanplatten möglichst klein zu halten, können die Späne für die inneren Deckschichten
grundsätzlich gröber als die Späne für die äußeren Deckschichten ausgebildet werden.
[0016] Konkret können die Späne für die äußeren Deckschichten durch ein Sieb mit einer Maschenweite
im Bereich von 1,3 bis 1,6 mm fallen und von einem Sieb mit einer Maschenweite von
0,3 bis 0,6 mm im Wesentlichen zurückgehalten werden, während die Späne für die inneren
Deckschichten durch ein Sieb mit einer Maschenweite im Bereich von 1,6 bis 1,8 mm
fallen und von einem Sieb mit einer Maschenweite von 0,5-0,75 mm im Wesentlichen zurückgehalten
werden können.
[0017] Vorzugsweise weisen die Späne für die äußeren Deckschichten einen relativ hohen Schlankheitsgrad
von 1 : 2,5 bis 5 auf.
[0018] Weiter ist es bevorzugt, wenn zwischen den inneren und den äußeren Deckschichten
und auch zu der Mittelschicht hin keine Trennschichten vorgesehen sind, wie sie sich
durch große Sprünge bei den Spangrößen an den Rändern der Schichten ausbilden. Der
Spangrößenverlauf innerhalb der einzelnen Schichten ist durch die Gestaltung und die
Einstellung der Streueinrichtungen einstellbar.
[0019] Wie wenig Frischholz für die erfindungsgemäße Herstellung von Spanplatten benötigt
wird, wird daraus deutlich, dass die Dicke der inneren Deckschichten größer sein kann
als diejenige der äußeren Deckschichten. So kann die Dicke der inneren Deckschichten
auf 1 bis 3 mm eingestellt werden, während eine Dicke der äußeren Deckschichten von
nur 0,5 bis 1,5 mm ausreichend ist. Diese Angabe bezieht sich jedoch auf die Dicke
der äußeren Deckschichten nach dem Schleifen.
[0020] Bei einer erfindungsgemäß hergestellten Spanplatte ist der mindestens fünfschichtige
Aufbau aus äußeren Deckschichten, inneren Deckschichten und Mittelschicht, wobei nur
die äußeren Deckschichten überwiegend aus Frischholz bestehen, leicht nachweisbar.
[0021] Vorteilhafte Weiterbildungen der Erfindung ergeben sich aus den Patentansprüchen,
der Beschreibung und den Zeichnungen. Die in der Beschreibungseinleitung genannten
Vorteile von Merkmalen und von Kombinationen mehrerer Merkmale sind lediglich beispielhaft
und können alternativ oder kumulativ zur Wirkung kommen, ohne dass die Vorteile zwingend
von erfindungsgemäßen Ausführungsformen erzielt werden müssen. Weitere Merkmale sind
den Zeichnungen - insbesondere den dargestellten Geometrien und den relativen Abmessungen
mehrerer Bauteile zueinander sowie deren relativer Anordnung und Wirkverbindung -
zu entnehmen. Die Kombination von Merkmalen unterschiedlicher Ausführungsformen der
Erfindung oder von Merkmalen unterschiedlicher Patentansprüche ist ebenfalls abweichend
von den gewählten Rückbeziehungen der Patentansprüche möglich und wird hiermit angeregt.
Dies betrifft auch solche Merkmale, die in separaten Zeichnungen dargestellt sind
oder bei deren Beschreibung genannt werden. Diese Merkmale können auch mit Merkmalen
unterschiedlicher Patentansprüche kombiniert werden. Ebenso können in den Patentansprüchen
aufgeführte Merkmale für weitere Ausführungsformen der Erfindung entfallen.
KURZBESCHREIBUNG DER FIGUREN
[0022] Die Erfindung wird im Folgenden anhand konkreter Ausführungsbeispiele unter Bezugnahme
auf die beigefügten Zeichnungen näher erläutert und beschrieben.
- Fig. 1
- ist ein Querschnitt durch den Schichtaufbau einer erfindungsgemäß hergestellten Spanplatte.
- Fig. 2
- gibt den Verlauf der mittleren Spangröße über die Dicke einer ersten Ausführungsform
der erfindungsgemäß hergestellten Spanplatte wieder, und
- Fig. 3
- gibt den Verlauf der mittleren Spangröße über die Dicke einer zweiten Ausführungsform
einer erfindungsgemäß hergestellten Spanplatte wieder.
[0023] Die Figuren sind dabei ausdrücklich als Prinzipdarstellungen zu verstehen und nicht
unbedingt maßstabsgerecht.
FIGURENBESCHREIBUNG
[0024] Eine erfindungsgemäß hergestellte Spanplatte 1 gemäß
Fig. 1 weist zwei äußere Deckschichten 2, zwei innere Deckschichten 3 und eine Mittelschicht
4 auf. Die Mittelschicht 4 kann zusätzlich in weitere Teilschichten unterteilt sein.
Die äußeren Deckschichten 2 bestehen ausschließlich aus Spänen aus Frischholz und
Schleifstaub vom Planschleifen zuvor hergestellter Spanplatten 1. Dazu wird Frischholz
getrennt aufbereitet, um Späne einer einzigen Siebfraktion zu erhalten, die typischerweise
durch ein Sieb mit einer Maschenweite von 1,3 bis 1,6 mm hindurchfällt, aber von einem
Sieb mit einer Maschenweite von 0,3 bis 0,6 mm zurückgehalten wird. Gröbere Späne
werden nachzerkleinert. Feinere Späne können in begrenztem Umfang wie der bereits
erwähnte Feinschliff als Füllstoff für die äußeren Deckschichten 2 verwendet werden.
Ansonsten werden sie verbrannt. Die Späne aus Frischholz der beschriebenen Siebfraktion
weisen vorzugsweise einen hohen Schlankheitsgrad von ca. 1 : 2,5 bis 5 auf, was es
erlaubt, mit einem relativ geringen Bindemittelanteil eine hohe Biegefestigkeit der
Spanplatte 1 über deren äußere Deckschichten 2 einzustellen. Überdies sind die ausschließlich
aus Frischholz ausgebildeten äußeren Deckschichten 2 frei von Störstoffen. Ihr Planschleifen
ist daher problemlos, ebenso wie ein Zerteilen der Spanplatte 1 in gewünschte Formate.
Außerhalb der äußeren Deckschichten 2 kann die Spanplatte 1 vollständig auf der Basis
von Altholz ausgebildet sein. Hierzu werden aus zerkleinertem Altholz Holzspäne von
zwei Siebfraktionen für die inneren Deckschichten 3 einerseits und die Mittelschicht
4 andererseits aufbereitet. Die Späne aus Altholz der inneren Deckschichten 3 sind
dabei typischerweise etwas gröber als die der äußeren Deckschichten 2. Trotz der typischerweise
kubischen Abmessungen dieser Späne aus Altholz können sie auch bei hohen technologischen
Anforderungen an die Spanplatte 1 mit vergleichsweise wenig Bindemittel beleimt sein,
weil sie Biegefestigkeit der Spanplatte 1 durch die äußere Deckschichten 2 bereitgestellt
wird. Auch in der Mittelschicht 4 aus noch gröberen Spänen aus Altholz reicht ein
vergleichsweise geringer Bindemittelanteil aus. Dabei kann das Bindemittel grundsätzlich
über alle Schichten zwei bis vier der Spanplatte 1 dasselbe sein. Es ist aber auch
möglich, unterschiedliche Bindemittel zu verwenden und beispielsweise in den äußeren
Deckschichten 2 und ggf. auch in den inneren Deckschichten 3 im Gegensatz zu der Mittelschicht
4 ein formaldehydfreies Bindemittel einzusetzen. Hier hat der Fachmann Optimierungsmöglichkeiten,
bei denen er sinnvoller Weise auch die unterschiedlichen Zusammensetzungen der äußeren
Deckschichten 2 einerseits und der inneren Deckschichten 3 und der Mittelschicht 4
andererseits aus Spänen aus Frischholz bzw. Altholz berücksichtigt.
[0025] Fig. 2 skizziert eine mögliche Verteilung der mittleren Spangröße G über der Dicke d einer
erfindungsgemäß hergestellten Spanplatte 1 gemäß Fig. 1. Die Späne für die äußeren
Deckschichten 2 werden typischerweise mit zur Plattenmitte hin gröber werdenden Spänen
gestreut. Die Späne für die inneren Deckschichten 3 und die Mittelschicht 4 können
wie hier angedeutet auch mit homogener Verteilung über der Dicke d gestreut werden.
[0026] Bevorzugt ist jedoch eine in
Fig. 3 angedeutete Spangrößenverteilung G über der Dicke d, bei der Sprünge in den Spangrößen
zwischen den einzelnen Schichten 2 bis 4 gezielt vermieden werden. Kleinere Sprünge
in der Spangrößenverteilung sind zwar unkritisch. Größere Sprünge können aber als
Grenzflächen oder Trennschichten wirken, an denen eine erhöhte Gefahr der Auflösung
des Verbunds der Schichten 2 bis 4 besteht. Die nachstehende Tabelle gibt mögliche
Bemaßungen der verschiedenen Schichten 2 bis 4 einer Spanplatte 1 gemäß Fig. 1 für
unterschiedliche Dicken der Spanplatte 1 wieder. Hieraus ergibt sich, dass die Deckschichten
1 mit einer typischen Schleifzulage von jeweils 0,3 mm hergestellt werden. Außerdem
sind die mittleren Rohdichten der einzelnen Schichten angegeben, die mit der Spangröße
in den einzelnen Schichten korrelieren.
Tabelle 1
|
ca.mm |
ca.kg/m3 |
|
ca.mm |
ca.kg/m3 |
|
ca.mm |
ca.kg/m3 |
|
ca.mm |
ca.kg/m3 |
Plattendicke ungeschliffen |
8 |
|
|
10,6 |
703 |
|
13,6 |
|
|
16,6 |
|
Abschliff |
0,6 |
|
|
0,6 |
|
|
0,6 |
|
|
0,6 |
|
Plattendicke geschliffen |
8 |
|
|
10 |
692 |
|
13 |
|
|
16 |
|
|
|
|
|
|
|
|
|
|
|
|
|
DS außen ungeschliffen |
0,85 |
860 |
|
0,85 |
850 |
|
0,85 |
830 |
|
0,9 |
820 |
DS außen geschliffen |
0,55 |
860 |
|
0,55 |
850 |
|
0,55 |
830 |
|
0,60 |
820 |
DS innen |
1.2 |
810 |
|
1,3 |
805 |
|
1.8 |
790 |
|
1,75 |
775 |
Mittelschicht |
4.5 |
650 |
|
6,3 |
640 |
|
8,3 |
625 |
|
11,3 |
615 |
DS innen |
1,2 |
810 |
|
1,3 |
805 |
|
1,8 |
790 |
|
1,75 |
775 |
DS außen geschliffen |
0,55 |
860 |
|
0,55 |
850 |
|
0,55 |
830 |
|
0.60 |
820 |
DS außen ungeschliffen |
0.85 |
860 |
|
0.85 |
850 |
|
0,85 |
830 |
|
0.9 |
820 |
Plattendicke ungeschliffen |
18,6 |
|
|
28,6 |
|
|
38,6 |
|
|
|
|
Abschliff |
0,6 |
|
|
0,6 |
|
|
0,6 |
|
|
|
|
Plattendicke geschliffen |
18 |
|
|
28 |
|
|
38 |
|
|
|
|
|
|
|
|
|
|
|
|
|
|
|
|
DS außen ungeschliffen |
0,9 |
815 |
|
1,1 |
795 |
|
1,35 |
785 |
|
|
|
DS außen geschliffen |
0,60 |
815 |
|
0,80 |
795 |
|
1,05 |
785 |
|
|
|
DS innen |
1,9 |
770 |
|
2,55 |
750 |
|
2,7 |
730 |
|
|
|
Mittelschicht |
13 |
610 |
|
21,3 |
580 |
|
30,5 |
565 |
|
|
|
DS innen |
1,9 |
770 |
|
2,55 |
750 |
|
2.7 |
730 |
|
|
|
DS außen geschliffen |
0,60 |
815 |
|
0.80 |
795 |
|
1,05 |
785 |
|
|
|
DS außen ungeschliffen |
0,9 |
815 |
|
1,1 |
795 |
|
1,35 |
785 |
|
|
|
[0027] Um das neue Verfahren zur Herstellung einer Spanplatte aus Frischholz und Altholz
durchzuführen, werden neben mindestens drei Aufbereitungslinien für die Späne aus
Frischholz für die äußeren Deckschichten 2, für die Späne aus Altholz für die inneren
Deckschichten 3 und für die Späne aus Altholz für die Mittelschicht 4 insgesamt fünf
Streueinheiten benötigt. Mit jeweils einer Streueinheit werden die Späne aus Frischholz
für die äußeren Deckschichten 2 gestreut. Mit zwei weiteren Streueinheiten werden
die Späne aus Altholz für die inneren Deckschichten 3 gestreut; und mit mindestens
einer weiteren Streueinheit werden die Späne aus Altholz für die Mittelschicht 4 gestreut.
Wenn dabei eine symmetrische Verteilung der Spangrößen auch über die Mittelschicht
erreicht werden soll, wie dies in Fig. 3 gezeigt ist, müssen auch für die Mittelschicht
zwei in unterschiedlicher Orientierung nacheinander geschaltete Streueinheiten eingesetzt
werden.
[0028] Die Streueinheiten für die äußeren Deckschichten können Windstreukammern oder Rollensiebe
sein. Für die Herstellung der inneren Deckschichten werden vorzugsweise Rollenstreuköpfe
mit zwei übereinander angeordneten Rollenbetten eingesetzt. Bei entsprechender Einstellung
können mit diesen Einrichtungen wahlweise homogene Schichten, Schichten mit einer
"fein /grob" Selektierung und auch Kombinationen aus " von homogen nach fein" erzeugt
werden. Für eine homogene Spangrößenverteilung in der Mittelschicht können Streuköpfe
mit sogenannten Fächerwalzen (cage-former) oder Rollensiebe mit zwei übereinander
angeordneten Rollenbetten eingesetzt werden. Auch eine Spangrößenverteilung, die eine
Kombination der in den Fig. 2 und 3 gezeigten Spangrößenverteilungen darstellt, ist
möglich. So können zwar die Spangrößen der Mittelschicht 4 die symmetrische Verteilung
gemäß Fig. 3 aufweisen, aber die Spangrößen der inneren Deckschichten 3 homogen verteilt
sein. Hierdurch treten in aller Regel keine so großen Sprünge der Spangrößen an den
Übergängen zu der Mittelschicht 4 und den äußeren Deckschichten 2 auf, dass hierdurch
Trennschichten ausgebildet würden.
[0029] Die für die Umsetzung der vorliegenden Erfindung erforderlichen Maschineninvestitionen
werden dadurch schnell kompensiert, dass hochwertige Spanplatten, insbesondere mit
hochwertiger Oberfläche unter Verwendung nur eines geringen Anteils an Frischholz
und entsprechend relativ geringen Kosten für das Holz und dessen Trocknung hergestellt
werden können.
BEZUGSZEICHENLISTE
[0030]
- 1
- Spanplatte
- 2
- äußere Deckschicht
- 3
- innere Deckschicht
- 4
- Mittelschicht
1. Verfahren zur Herstellung von Spanplatten (1) unter Verwendung von Altholz und Frischholz,
wobei Späne für eine Mittelschicht (4) und Späne für Deckschichten (2, 3) der Spanplatten
(1) getrennt aufbereitet werden, dadurch gekennzeichnet, dass die Späne für äußere Deckschichten (2) zumindest überwiegend aus dem Frischholz aufbereitet
werden, dass die Späne für innere Deckschichten (3) zumindest überwiegend aus dem
Altholz aufbereitet werden und dass die Späne für die äußeren Deckschichten (2) und
die inneren Deckschichten (3) separat gestreut werden.
2. Verfahren nach Anspruch 1, dadurch gekennzeichnet, dass die äußeren Deckschichten (2) nur aus Spänen aus Frischholz gestreut werden.
3. Verfahren nach Anspruch 1 oder 2, dadurch gekennzeichnet, dass den Spänen aus Frischholz für die äußeren Deckschichten (2) Schleifstaub zugesetzt
wird.
4. Verfahren nach einem der Ansprüche 1 bis 3, dadurch gekennzeichnet, dass die inneren Deckschichten (3) nur aus Spänen aus Altholz gestreut werden.
5. Verfahren nach einem der Ansprüche 1 bis 4, dadurch gekennzeichnet, dass die Mittelschicht (4) nur aus Spänen aus Altholz gestreut wird.
6. Verfahren nach einem der Ansprüche 1 bis 5, dadurch gekennzeichnet, dass die Späne für die inneren Deckschichten (3) und die äußeren Deckschichten (2) unterschiedlich
beleimt werden.
7. Verfahren nach einem der Ansprüche 1 bis 6, dadurch gekennzeichnet, dass die Späne für die inneren Deckschichten (3) so aufbereitet werden, dass sie gröber
als die Späne für die äußeren Deckschichten (2) sind.
8. Verfahren nach einem der Ansprüche 1 bis 7, dadurch gekennzeichnet, dass die Späne für die äußeren Deckschichten (2) durch ein Sieb mit einer Maschenweite
im Bereich von 1,3 bis 1,6 mm fallen und von einem Sieb mit einer Maschenweite von
0.3 bis 0,6 mm im Wesentlichen zurückghalten werden.
9. Verfahren nach einem der vorhergehenden Ansprüche, Dadurch gekennzeichnet, dass die Späne für die äußeren Deckschichten (2) einen Schlankheitsgrad von 1 : 2,5 bis
5 aufweisen.
10. Verfahren nach einem der vorangehenden Ansprüche, dadurch gekennzeichnet, dass zwischen den inneren Deckschichten (3) und den äußeren Deckschichten (2) sowie der
Mittelschicht (4) keine Trennschichten ausgebildet werden, an denen sich die Größe
der Späne sprungartig ändert.
11. Verfahren nach einem der vorangehenden Ansprüche, dadurch gekennzeichnet, dass die Dicke der inneren Deckschichten (3) auf 1 bis 3 mm eingestellt wird.
12. Verfahren nach einem der vorangehenden Ansprüche, dadurch gekennzeichnet, dass die Dicke der äußeren Deckschichten (2) auf 0,5 bis 1,5 mm nach dem Schleifen eingestellt
wird.
13. Hotzplatte hergestellt nach dem Verfahren nach einem der vorangehenden Ansprüche 1
bis 12, mit einer Mittelschicht (4) und Deckschichten (2, 3) aus Spänen aus Altholz
und Frischholz, dadurch gekennzeichnet, dass die Späne von äußeren Deckschichten (2) zumindest überwiegend aus Frtschholz und
die Späne von inneren Deckschichten (3) zumindest überwiegend aus Althotz bestehen.
1. Method for manufacturing chipboards (1) using old wood and new wood, wherein chips
for a middle layer (4) and chips for cover layers (2, 3) of the chipboard (1) are
prepared separately, characterized in that the chips for outer cover layers (2) are at least predominantly prepared of the fresh
wood, that the chips for inner cover layers (3) are at least predominantly prepared
of the old wood, and that the chips for the outer cover layers (2) and the inner cover
layers (3) are spread separately.
2. Method of claim 1, characterized in that the outer cover layers (2) are only spread of chips of fresh wood.
3. Method of claim 1 or 2, characterized in that abrasive dust is added to the chips of fresh wood for the outer cover layers (2).
4. Method of any of the claims 1 to 3, characterized in that the inner cover layers (3) are only spread of chips of old wood.
5. Method of any of the claims 1 to 4, characterized in that the middle layer (4) is only spread of chips of old wood.
6. Method of any of the claims 1 to 5, characterized in that the chips for the inner cover layers (3) and the outer cover layers (2) are glued
differently.
7. Method of any of the claims 1 to 6, characterized in that the chips for the inner cover layers (3) are prepared in such way that they are more
coarse than the chips for the outer cover layers (2).
8. Method of any of the claims 1 to 7, characterized in that the chips for the outer cover layers (2) pass through a sieve having a mesh size
in a range of 1,3 to 1,6 mm and are essentially retained by a sieve having a mesh
size of 0,3 to 0,6 mm.
9. Method of any of the preceding claims, characterized in that the chips for the outer cover layers (2) have a slenderness ratio of 1 to 2,5 to
5.
10. Method of any of the preceding claims, characterized in that no separation layers, at which the size of the chips changes abruptly, are formed
between the inner cover layers (3) and the outer cover layers (2) or the middle layer
(4).
11. Method of any of the preceding claims, characterized in that the thickness of the inner cover layers (3) is adjusted to 1 to 3 mm.
12. Method of any of the preceding claims, characterized in that the thickness of the outer cover layers (2) is adjusted to 0,5 to 1,5 mm after sanding.
13. Wood board manufactured according to the method of any of the preceding claims 1 to
12 having a middle layer (4) and cover layers (2, 3) of chips of old wood and new
wood, characterized in that the chips of outer cover layers (2) at least predominantly consist of new wood and
the chips of inner cover layers (3) at least predominantly consist of old wood.
1. Procédé pour fabriquer des panneaux de particules (1) en utilisant du bois ancien
et du bois récent, des copeaux destinés à une couche centrale (4) et des copeaux destinés
à des couches de revêtement (2, 3) des panneaux de particules (1) étant traités séparément,
caractérisé en ce que les copeaux destinés à des couches de revêtement (2) extérieures sont traités au
moins principalement à partir du bois récent, en ce que les copeaux destinés à des couches de revêtement (3) intérieures sont traités au
moins principalement à partir du bois ancien et en ce que les copeaux destinés aux couches de revêtement (2) extérieures et aux couches de
revêtement (3) intérieures sont dispersés séparément.
2. Procédé selon la revendication 1, caractérisé en ce que les couches de revêtement (2) extérieures uniquement à base de copeaux de bois récent
sont dispersées.
3. Procédé selon la revendication 1 ou 2, caractérisé en ce que de la poussière de ponçage est ajoutée aux copeaux de bois récent pour les couches
de revêtement (2) extérieures.
4. Procédé selon l'une quelconque des revendications 1 à 3, caractérisé en ce que les couches de revêtement (3) intérieures uniquement à base de copeaux de bois ancien
sont dispersées.
5. Procédé selon l'une quelconque des revendications 1 à 4, caractérisé en ce que la couche centrale (4) uniquement à base de copeaux de bois ancien est dispersée.
6. Procédé selon l'une quelconque des revendications 1 à 5, caractérisé en ce que les copeaux pour les couches de revêtement (3) intérieures et les couches de revêtement
(2) extérieures sont collées différemment.
7. Procédé selon l'une quelconque des revendications 1 à 6, caractérisé en ce que les copeaux pour les couches de revêtement (3) intérieures sont traitées de telle
sorte qu'ils sont plus grossiers que les copeaux pour les couches de revêtement (2)
extérieures.
8. Procédé selon l'une quelconque des revendications 1 à 7, caractérisé en ce que les copeaux pour les couches de revêtement (2) extérieures tombent à travers un tamis
présentant une largeur de maille de l'ordre de 1,3 à 1,6 mm et sont retenus pour l'essentiel
par un tamis présentant une largeur de maille de 0,3 à 0,6 mm.
9. Procédé selon l'une quelconque des revendications précédentes, caractérisé en ce que les copeaux pour les couches de revêtement (2) extérieures présentent un degré d'élancement
de 1:2,5 à 5.
10. Procédé selon l'une quelconque des revendications précédentes, caractérisé en ce que, entre les couches de revêtement (3) intérieures et les couches de revêtement (2)
extérieures ainsi que la couche centrale (4), on ne trouve pas de couches de séparation
sur lesquelles la grandeur des copeaux varie brusquement.
11. Procédé selon l'une quelconque des revendications précédentes, caractérisé en ce que l'épaisseur des couches de revêtement (3) intérieures est réglée sur 1 à 3 mm.
12. Procédé selon l'une quelconque des revendications précédentes, caractérisé en ce que l'épaisseur des couches de revêtement (2) extérieures est réglée sur 0,5 à 1,5 mm
après le ponçage.
13. Panneau en bois fabriqué selon le procédé selon l'une quelconque des revendications
1 à 12, comprenant une couche centrale (4) et des couches de revêtement (2, 3) à base
de copeaux provenant de bois ancien et de bois récent, caractérisé en ce que les copeaux des couches de revêtement (2) extérieures sont au moins principalement
à base de bois récent et les copeaux de couches de revêtement (3) intérieures au moins
principalement à base de bois ancien.
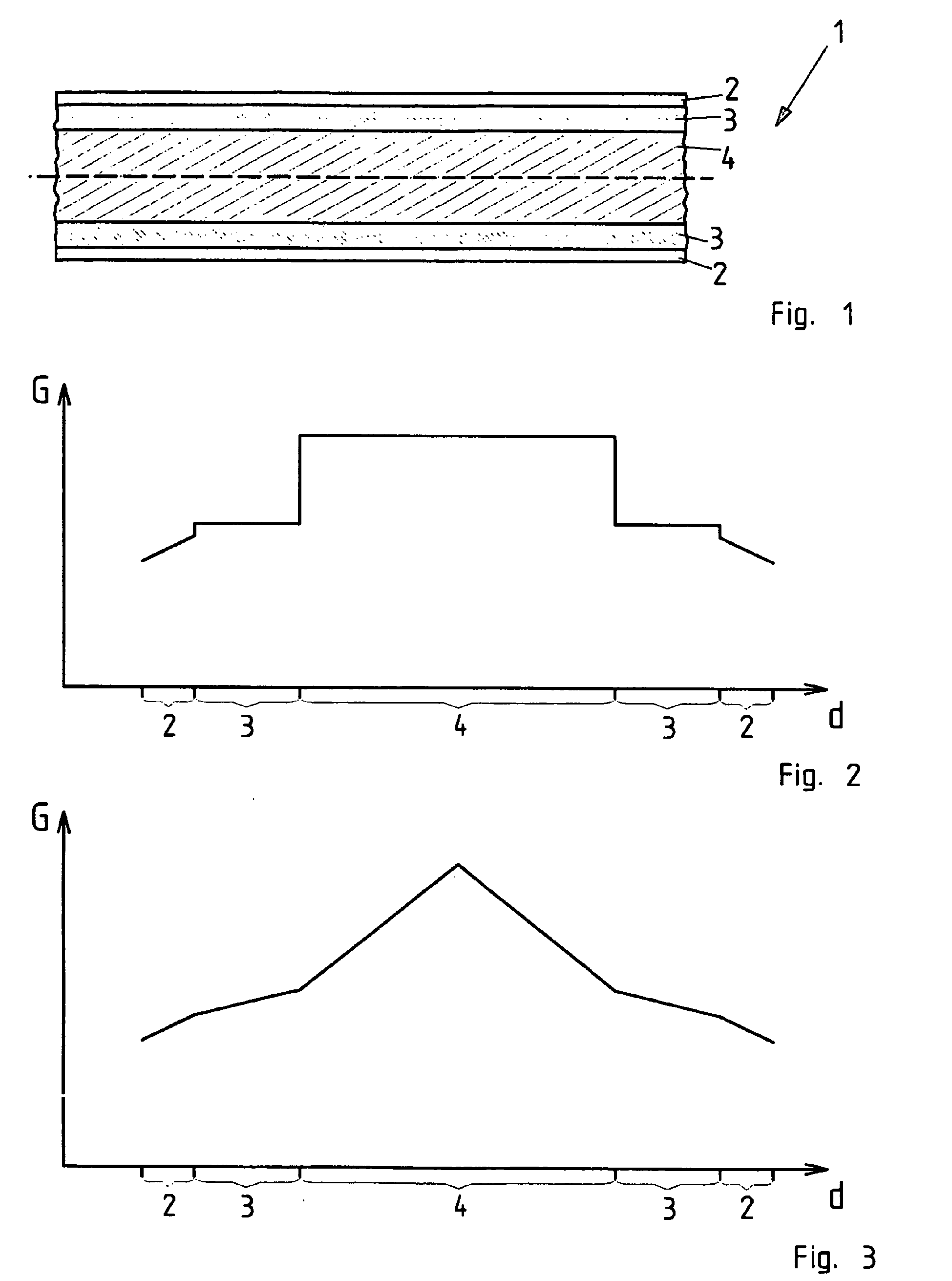
IN DER BESCHREIBUNG AUFGEFÜHRTE DOKUMENTE
Diese Liste der vom Anmelder aufgeführten Dokumente wurde ausschließlich zur Information
des Lesers aufgenommen und ist nicht Bestandteil des europäischen Patentdokumentes.
Sie wurde mit größter Sorgfalt zusammengestellt; das EPA übernimmt jedoch keinerlei
Haftung für etwaige Fehler oder Auslassungen.
In der Beschreibung aufgeführte Patentdokumente