FIELD OF THE INVENTION AND PRIOR ART
[0001] The present invention relates to a lorry according to the preamble of claim 1 and
a method for regulating the maximum allowed lifting moment of a hydraulic lorry crane.
[0002] In order to avoid overloading of a hydraulic crane, it is known to establish a, with
respect to the strength of the crane, maximum allowed value for the lifting moment
of the crane. The expression "base value" is in the following used as a denomination
for this maximum allowed value for the lifting moment of the crane established based
on the strength properties of the crane. This base value may be a fixed value which
takes into account the position of the crane boom system which, with respect to strength,
is the most critical one among the allowed positions for the crane boom system of
the crane, or a variable value established instantaneously in dependence on the swing-out
angle of the inner boom of the crane and possibly further variables defining the prevailing
position of the crane boom system of the crane. The value for the maximum allowed
lifting moment is normally converted into a corresponding value for the maximum allowed
working pressure for the lifting cylinder of the crane, and by limiting this working
pressure it is secured that the lifting moment of the crane will not exceed the maximum
allowed lifting moment.
[0003] For a lorry crane, i.e. a crane mounted on a lorry, the value of the maximum allowed
lifting moment also has to be adapted in dependence on the stability of the lorry,
to thereby avoid a tipping of the lorry due to inappropriate manoeuvring of the crane.
To prevent the lorry from tipping, the tipping moment presently exerted on the lorry
by the crane and by the load carried by the crane has to be lower than the stabilizing
moment given by the weight of the lorry without cargo in combination with the weight
of the possible load located on the lorry. The magnitude of the tipping moment and
the stabilizing moment depends i.a. on the position of the tipping line over which
the crane boom system of the crane presently extends. In dependence on the position
of the support legs of the lorry and the horizontal slewing position of the crane,
this tipping line may extend between two vehicle wheels, between two support legs
or between one vehicle wheel and one support leg. The position of the tipping line
can be established based on information about the slewing angle of the column of the
crane and information about the horizontal extension length of the support legs of
the lorry. When the position of the tipping line of the lorry is known, the perpendicular
distance between the tipping line and the centre of gravity of the lorry without cargo
can be calculated, which in its turn makes it possible to calculate the stabilizing
moment given by the weight of the lorry without cargo. When the position of the tipping
line, the slewing angle of the column of the crane and the lifting radius of the crane
are known, the perpendicular distance between the tipping line and the load suspension
point of the crane can be calculated, which in its turn makes it possible to estimate
the tipping moment exerted by the crane when the lifting moment of the crane corresponds
to the above-mentioned base value for the maximum allowed lifting moment.
[0004] A lorry normally lacks a sensor for establishing the prevailing wheel force of the
load-bearing vehicle wheels of the lorry, which implies that there is no possibility
to calculate the stabilizing moment given by the load presently located on the lorry.
In the automatic stability monitoring of a conventional lorry crane, only the stabilizing
moment given by the weight of the lorry without cargo is therefore taken into account,
and it will thereby not be possible to adapt the lifting capacity of the crane in
dependence on the stabilizing moment given by the weight of the possible load presently
located on the lorry. When the crane of the lorry is manoeuvred with a load located
on the lorry, the value for the maximum allowed lifting moment of the crane will therefore
often be lower than what would have been possible if also the stabilizing moment from
the load had been taken into account, which consequently implies that the lifting
capacity of the crane is limited to a greater extent than actually required with respect
to the stability.
[0005] According to a known principle for stability monitoring of a lorry crane, the tipping
moment
Mo exerted by the crane when the lifting moment of the crane corresponds to the above-mentioned
base value
Mc,bas for the maximum allowed lifting moment and the stabilizing moment
Ms given by the weight of the lorry without cargo are calculated in the manner described
above. Thereafter, it is checked whether a predetermined stability condition is fulfilled
with these tipping and stabilizing moments, namely whether the ratio between the stabilizing
moment
Ms and the tipping moment
Mo is equal to or larger than the value of a given stability constant
κ (Ms/
Mo≥k). If the stability condition is fulfilled, i.e. if
Ms/
Mo≥k, said base value
Mc,bas is used as an upper limit for the allowed lifting moment of the crane. If the stability
condition is not fulfilled, i.e.
Ms/
Mo<k, a reduction factor κ is established, and a reduced value
Mc,red for the maximum allowed lifting moment of the crane is established as the product
of the base value
Mc,bas and the reduction factor κ, i.e.
Mc,red=MC,bas·κ
. The reduction factor
κ is calculated as the quotient between the stabilizing moment
Ms and the product of the stability constant
κ and the tipping moment
Mo, i.e. κ=
MS/
(k·
Mo). The reduced value
Mc,red is then used as an upper limit for the maximum allowed lifting moment of the crane.
OBJECT OF THE INVENTION
[0006] The object of the present invention is to provide a new and favourable manner for
regulating the maximum allowed lifting moment of a hydraulic lorry crane.
SUMMARY OF THE INVENTION
[0007] According to the present invention, said object is achieved by means of a lorry having
the features defined in claim 1 and a method having the features defined in claim
7.
[0008] With the solution according to the invention, it will be possible, when establishing
the maximum allowed lifting moment of a hydraulic crane, to take advantage of the
stabilizing moment given by the load presently located on the lorry, so that the reduction
of the maximum allowed lifting moment of the crane required in certain situations
in view of the stability of the crane can be limited while maintaining a proper safety
against a tipping of the lorry.
[0009] Preferred embodiments of the invention will appear from the dependent claims and
the following description.
BRIEF DESCRIPTION OF THE DRAWINGS
[0010] The invention will in the following be more closely described by means of embodiment
examples, with reference to the appended drawings. It is shown in:
- Fig 1
- a schematic rear view of a lorry provided with support legs and a hydraulic crane;
- Fig 2
- a schematic planar view of the lorry, the support legs and the crane according to
Fig 1;
- Fig 3
- a schematic perspective view of a manoeuvring unit with a number of manoeuvring members
for controlling different crane functions; and
- Fig 4
- a schematic illustration of an embodiment of a crane included in a lorry according
to the present invention.
DETAILED DESCRIPTION OF PREFERRED EMBODIMENTS
[0011] Figs 1 and 2 show a lorry 1 provided with load-bearing vehicle wheels 2
1-2
4 and a chassis 3 supported by the vehicle wheels. In the illustrated example, the
lorry is provided with two rear wheels 2
1, 2
2 and two front wheels 2
3, 2
4, but the lorry could also be provided with a larger number of load-bearing vehicle
wheels than here illustrated. A hydraulic crane 20 is mounted on and carried by the
chassis 3. Two horizontally extendable support legs 4
1, 4
3 are arranged on one side of the longitudinal axis of the vehicle, and two horizontally
extendable support legs 4
2, 4
4 are arranged on the opposite side of the longitudinal axis of the vehicle. The lorry
could alternatively be provided with a larger or smaller number of support legs than
here illustrated. The respective support leg 4
1-4
4 has a first force member 5, suitably in the form of a hydraulic cylinder, by means
of which the support leg is horizontally displaceable from a retracted position close
to the chassis 3 to an extended position at a distance from the chassis 3. Alternatively,
the respective support leg 4
1-4
4 could be manually displaceable horizontally from a retracted position close to the
chassis 3 to an extended position at a distance from the chassis 3. The support legs
4
1-4
4 are shown in the extended position in Figs 1 and 2. Furthermore, the respective support
leg 4
1-4
4 has a second force member 6, by means of which the support leg is manoeuvrable to
an active support position in contact with the ground or other underlayer. The support
legs 4
1-4
4 are shown in the active support position in Figs 1 and 2. In its active support position,
the respective support leg rests against the underlayer through a support leg foot
7 arranged at the lower end of a telescopically lowerable lower support leg part 8
of the support leg. In the illustrated example, the second force member 6 consists
of a hydraulic cylinder, by means of which the lower support leg part 8 of the support
leg is displaceable upwards and downwards in relation to an upper support leg part
9.
[0012] The lorry 1 comprises means 10 (schematically indicated in Fig 4) for establishing
the horizontal extension length of the respective support leg 4
1-4
4. These means 10 comprise sensors which sense the displacement position of the horizontally
displaceable part 12 of the respective support leg or the displacement position of
the movable part of said first force member 5 of the respective support leg.
[0013] Furthermore the lorry 1 comprises means 11 (schematically indicated in Fig 4) for
establishing the force
F exerted by the second force member 6 of the respective support leg 4
1-4
4 when the support leg is in the active support position. This force corresponds to
the contact force exerted by the support leg against the underlayer and consequently
the normal force acting on the support leg from the underlayer. When the second force
member 6 of the respective support leg 4
1-4
4 consists of a hydraulic cylinder, the means 11 comprise pressure sensors for sensing
the differential pressure of each one of these hydraulic cylinders.
[0014] The hydraulic lorry crane 20 comprises:
- a column 21, which is rotatable in relation to the chassis 3 about an essentially
vertical axis of rotation A1 by means of a not shown rotating device;
- a liftable and lowerable crane boom 22, here denominated inner boom, which is articulately
fastened to the column 21 in such a manner that it is turnable in relation to the
column about an essentially horizontal axis of rotation A2; and
- a hydraulic cylinder 23, here denominated lifting cylinder, for lifting and lowering
the inner boom 22 in relation to the column 21.
[0015] The slewing angle θ of the column 21 in relation to the chassis 3 is established
by means of a sensor 14 (schematically indicated in Fig 4), which continuously senses
the slewing position of the column.
[0016] In the example illustrated in Fig 1, the crane 20 also comprises a liftable and lowerable
crane boom 24, here denominated outer boom, which is articulately fastened to the
inner boom 22 in such a manner that it is turnable in relation to the inner boom about
an essentially horizontal axis of rotation A3. A hydraulic cylinder 25, here denominated
outer boom cylinder, carries out the lifting and lowering of the outer boom 24 in
relation to the inner boom 22. In this case, the crane boom system 29 of the crane
is formed by the inner boom 22 and the outer boom 24.
[0017] In the illustrated example, the lifting cylinder 23 comprises a cylinder part 23a
which is articulately fastened to the column 21, and a piston which is received in
this cylinder part and displaceable in relation to it, the piston being provided with
a piston rod 23b, which is articulately fastened to the inner boom 22. The outer boom
cylinder 25 comprises a cylinder part 25a which is articulately fastened to the inner
boom 22, and a piston which is received in this cylinder part and displaceable in
relation to it, the piston being provided with a piston rod 25b, which is articulately
fastened to the outer boom 24.
[0018] In the illustrated example, the outer boom 24 comprises two crane boom sections 24a,
24b which are mutually displaceable in the longitudinal direction of the outer boom
for adjustment of the extension length of the outer boom. The crane boom sections
24a, 24b are displaceable in relation to each other by means of a hydraulic cylinder
26 carried by the outer boom 24. In the illustrated example, a rotator 27 is articulately
fastened to the outer end of the outer boom, which rotator in its turn carries a lifting
hook 28. In order to perform lifting operations requiring a great range, a liftable
and lowerable crane boom in the form of a so-called jib may be mounted to the outer
end of the outer boom 24.
[0019] The crane 20 further comprises an electronic regulating device 30 (schematically
indicated in Fig 4), which is adapted to check whether one or more predetermined stability
conditions for the lorry are fulfilled with a lifting moment of the crane corresponding
to a, with respect to the strength of the crane, maximum allowed value
Mc,bas, here denominated base value, for the lifting moment of the crane. This base value
Mc,bas may be a given fixed value which takes into account the position of the crane boom
system which, with respect to strength, is the most critical one among the allowed
positions for the crane boom system 29 of the crane, or a variable value established
by the regulating device 30 in dependence on the swing-out angle of the inner boom
22 of the crane in the vertical plane and possibly further variables defining the
prevailing position of the crane boom system of the crane.
[0020] If the regulating device 30 will establish that said stability condition is not fulfilled,
the regulating device 30 is adapted to establish a reduced value
Mc,red for the maximum allowed lifting moment of the crane, the regulating device 30 being
adapted, when establishing this reduced value
Mc,red, to take into account the horizontal extension length of the respective support leg
4
1-4
4 that is in the active support position, the slewing angle θ of the column 21 in relation
to the chassis 3 in the horizontal plane, and the force
Fi exerted by the second force member 6 of the respective support leg that is in the
active support position and is not included in the prevailing tipping line of the
lorry. A preferred implementation of this will be described in the following. As a
lorry 1 has a considerable weight, the support legs 4
1-4
4 are not designed to carry the entire weight of the lorry when the crane 20 is used.
When the crane 20 is used, the main part of the weight of the lorry is carried by
the vehicle wheels 2
1-2
4, whereas the support legs 4
1-4
4 that are in the active support position only carry a minor part of the weight of
the lorry. When all the support legs 4
1-4
4 are in the active support position, there are consequently six different possible
tipping lines for the lorry 1 illustrated in Fig 2, namely:
- a first possible tipping line between the contact points against the underlayer of
the rear support legs 41, 42;
- a second possible tipping line between the contact points against the underlayer of
the right rear support leg 41 and the right front support leg 43;
- a third possible tipping line between the contact points against the underlayer of
the right front support leg 43 and the right front wheel 23;
- a fourth possible tipping line between the contact points against the underlayer of
the right front wheel 23 and the left front wheel 24;
- a fifth possible tipping line between the contact points against the underlayer of
the left front wheel 24 and the left front support leg 44; and
- a sixth possible tipping line between the contact points against the underlayer of
the left front support leg 44 and the left rear support leg 42.
[0021] The position of the prevailing tipping line L
o (see Fig 2), i.e. the position of the tipping line over which the lorry 1 presently
runs the risk of tipping in case of an overloading of the crane 20, depends on the
prevailing slewing position of the crane boom system 29 in the horizontal plane and
the horizontal extension length of the support legs 4
1-4
4 that are in the active support position. By establishing the slewing angle θ of the
column 21 in relation to the chassis 3 and the horizontal extension length of the
respective support leg 4
1-4
4, it will consequently be possible to establish the position of the prevailing tipping
line L
o. Based on the thus established position of the prevailing tipping line L
o and the slewing angle θ of the column 21 in relation to the chassis 3, the angle
θ' between the crane boom system 29 and the normal to the tipping line can then be
established, as well as the perpendicular distance
H between the vertical axis of rotation A1 of the crane and the prevailing tipping
line L
o.
[0022] The tipping moment
Mo of the crane 20 with respect to the prevailing tipping line L
o and with a lifting moment of the crane corresponding to the above-mentioned base
value
Mc,bas is given by the following formula:

where
R is the lifting radius of the crane, i.e. the horizontal distance from the vertical
axis of rotation A1 of the crane to the load suspension point P. The lifting radius
R can be calculated based on measured values on the variables defining the prevailing
position of the crane booms 22, 24 of the crane. The lifting radius
R may alternatively be set to a fixed value representing the largest possible lifting
radius of the crane.
[0023] Equilibrium of moments about the tipping line L
o with a lifting moment of the crane corresponding to the above-mentioned base value
Mc,bas will give the following relationship:

where
Fi is the support leg force of the active support leg
i, which corresponds to the force exerted by the second force member 6 of the support
leg,
Di is the perpendicular distance between the contact point of the support leg
i against the underlayer and the prevailing tipping line L
o,
Ri is the wheel force of the vehicle wheel
i, di is the perpendicular distance between the contact point of the vehicle wheel i against
the underlayer and the prevailing tipping line L
o,
mv is the mass of the lorry without cargo,
g is the gravitational constant,
hv is the perpendicular distance between the centre of gravity G
v of the lorry without cargo and the prevailing tipping line L
o,
me is the mass of the possible load 13 presently located on the lorry, and
he is the perpendicular distance between the centre of gravity G
e of said load 13 and the prevailing tipping line L
o.
[0024] In the above-mentioned relationship of equilibrium of moments, n

consequently represents the moment from the support m leg forces,
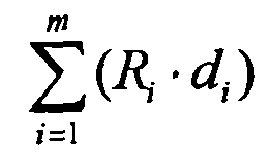
represents the moment from the unknown wheel forces,
mv · g · hv represents the moment from the known mass of the unloaded lorry, and
me · g · he represents the moment from the unknown mass of the possible load.
[0025] Considering that the wheel forces
Ri are unknown but always positive, the above-mentioned equilibrium relationship is
changed into the following inequality:

[0026] In any case, a stabilizing moment
(mv · g · hv) is obtained by the mass of the lorry in itself, and when a load is located on the
lorry, a supplementary stabilizing moment
(me · g · he) is also obtained by the mass of this load. The stabilizing moment
Ms is consequently equal to the sum of the moment from the mass of the unloaded lorry
and the moment from the mass of the possible load located on the lorry, i.e.
MS =
mv · g · hv +
me · he. From this it follows that
MS ≥ mv · g · hv. From the inequality (1) above, it also follows that

[0027] The conventional stability condition that the ratio between the stabilizing moment
MS and the tipping moment
MO is to be larger than or equal to the value on a stability constant κ with a given
value higher than 1, for instance 1.2, may be used as stability condition. This stability
condition can consequently be written in the following manner:
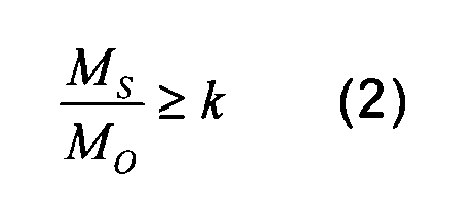
When checking whether the stability condition (2) is fulfilled or not, the stabilizing
moment
Ms may now be made to assume the highest of the values
mv · g · hv and

[0028] If the stability condition (2) is not fulfilled, the regulating device 30 is adapted
to establish the above-mentioned reduced value
MC,red for the maximum allowed lifting moment of the crane as the product of the base value
MC,bas and a reduction factor
κ which is established by the regulating device and has a value lower than 1. In this
case, the regulating device 30 is adapted to make said reduction factor κ assume a
basic value κ
bas when

i.e. when the stabilizing moment
Ms has had the value
mv · g · hv in connection with the establishment that the stability condition (2) is not fulfilled.
This basic value κ
bas for the reduction factor is suitably established according to the following formula:
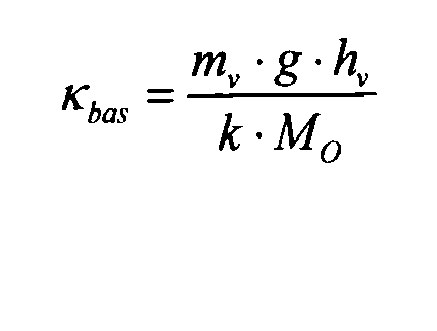
[0029] When
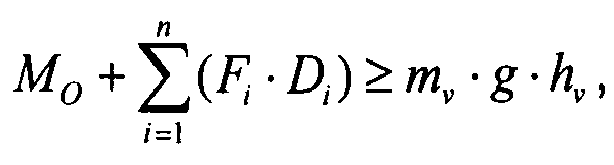
, i.e. when the stabilizing moment
Ms has had the value
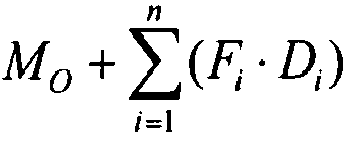
in connection with the establishment that the stability condition (2) is not fulfilled,
the regulating device 30 is adapted to make said reduction factor κ assume an increased
value κ
eh, which is higher than said basic value κ
bas. This increased value κ
eh for the reduction factor is suitably established according to the following formula:
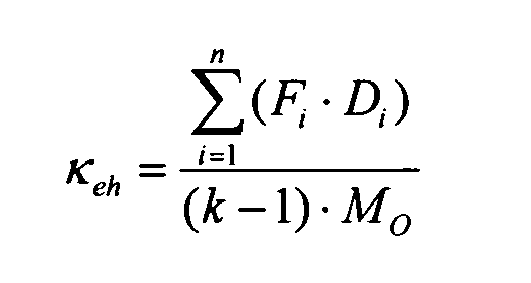
[0030] The last-mentioned formula follows from the fact that the stability condition in
the last-mentioned case can be written as:
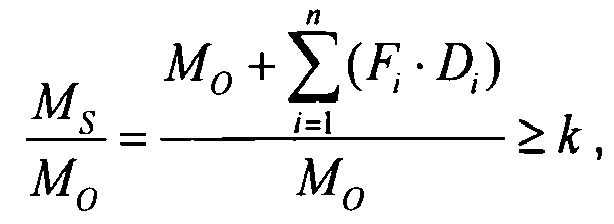
, which can be reformulated into the following condition:

[0031] The regulating device 30 is in a conventional manner adapted to convert the prevailing
value
(MC,bas or
MC,red) for the maximum allowed lifting moment of the crane 20 into a corresponding value
for the maximum allowed working pressure for the lifting cylinder 23.
[0032] The control system for controlling the different crane functions, i.e. lifting/lowering
by means of the lifting cylinder 23, tilting by means of the outer boom cylinder 25,
extension/retraction by means of the hydraulic cylinder 26 etc, comprises a pump 40
(see Fig 4), which pumps hydraulic fluid from a reservoir 41 to a directional-control-valve
block 42. The directional-control-valve block 42 comprises a directional-control-valve
section 43 for each of the hydraulic cylinders 23, 25 and 26 of the crane boom system,
to which hydraulic cylinders hydraulic fluid is supplied in a conventional manner
in dependence on the setting position of the slide member in the respective directional-control-valve
section 43. The setting position of the slide members in the directional-control-valve
sections 43 is controlled either through a number of manoeuvring members, for instance
in the form of manoeuvring levers 44, each of which being connected to its own slide
member, or by remote control through a manoeuvring unit 45 (see Fig 3) comprising
a manoeuvring member S1-S6 for each slide member. In the case of remote control, the
control signals are transmitted through cable or a wireless connection from the manoeuvring
unit 45 to an electronic control unit, for instance in the form of a microprocessor,
which in its turn controls the setting position of the slide members in the valve
sections 43 of the directional-control-valve block 42 in dependence on the magnitude
of the respective control signal from the manoeuvring unit 45.
[0033] Each individual directional-control-valve section 43 consequently controls the magnitude
and the direction of the flow of hydraulic fluid to a specific hydraulic cylinder
and thereby controls a specific crane function. For the sake of clarity, only the
directional-control-valve section 43 for the lifting cylinder 23 is illustrated in
Fig 4.
[0034] The directional-control-valve block 42 further comprises a shunt valve 46, which
pumps excessive hydraulic fluid back to the reservoir 41, and an electrically controlled
dump valve 47, which can be made to return the entire hydraulic flow from the pump
40 directly back to the reservoir 41.
[0035] In the shown embodiment example, the directional-control-valve block 42 is of load-sensing
and pressure-compensating type, which implies that the magnitude of the hydraulic
flow supplied to a hydraulic cylinder is always proportional to the position of the
slide member in the corresponding directional-control-valve section 43, i.e. proportional
to the setting position of the manoeuvring lever 44. The directional-control-valve
section 43 comprises a pressure limiter 48, a pressure compensator 49 and a directional-control-valve
50. Directional-control-valve blocks and directional-control-valve sections of this
type are known and available on the market. Also other types of valve devices than
the one here described may of course be used in the crane 20 in question.
[0036] A load holding valve 51 is arranged between the respective hydraulic cylinder and
the associated directional-control-valve section 43, which load holding valve makes
sure that the load will remain hanging when the hydraulic system runs out of pressure
when the dump valve 47 is made to return the entire hydraulic flow from the pump 40
directly back to the reservoir 41.
[0037] The crane further comprises a pressure sensor 52 arranged to measure the hydraulic
pressure on the piston side of the lifting cylinder 23. The regulating device 30 is
connected to the pressure sensor 52 in order to receive measuring signals from this
sensor related to said hydraulic pressure.
[0038] The regulating device 30 continuously reads the output signal from the pressure sensor
52 and compares this output signal with the established value for the maximum allowed
working pressure for the lifting cylinder 23. If the pressure sensed by the pressure
sensor 52 exceeds the established maximum allowed working pressure for the lifting
cylinder 23, the regulating device 30 delivers a signal to the dump valve 47 which
dumps the hydraulic flow directly to the reservoir 41, which results in that the hydraulic
system runs out or pressure and the load is held in its position by means of the load
holding valve 51. In this situation, the control system is adapted to allow only moment
reducing crane movements.
[0039] In the example described above, the regulating device 30 is adapted to let the maximum
allowed working pressure for the lifting cylinder 23 represent the maximum allowed
hydraulic pressure on the piston side of the lifting cylinder. However, the regulating
device 30 could alternatively be adapted to let the maximum allowed working pressure
for the lifting cylinder 23 represent the maximum allowed differential pressure in
the hydraulic cylinder. This differential pressure is defined as the hydraulic pressure
on the piston side of the lifting cylinder minus the hydraulic pressure on its piston
rod side divided by the cylinder ratio. In the last-mentioned case, the regulating
device 30 is also arranged to receive measuring signals from a pressure sensor 53
which measures the hydraulic pressure on the piston rod side of the lifting cylinder
23 so as to thereby be able to establish the prevailing differential pressure in the
hydraulic cylinder and compare this differential pressure with the established value
on the maximum allowed working pressure for the lifting cylinder. The expression "working
pressure" as used in this description and the following claims, consequently refers
either to the hydraulic pressure on the piston side of the lifting cylinder or the
differential pressure in the lifting cylinder.
[0040] The invention is of course not in any way limited to the embodiments described above.
On the contrary, several possibilities to modifications thereof should be apparent
to a person skilled in the art without thereby deviating from the basic idea of the
invention as defined in the appended claims. The control system of the crane may for
instance have another design than the control system which is illustrated in Fig 4
and described above.
1. A lorry provided with load-bearing vehicle wheels (2
1-2
4), a chassis (3) supported by the vehicle wheels, a hydraulic crane (20) carried by
the chassis and two or more support legs (4
1-4
4) connected to the chassis, the respective support leg having a force member (6) by
means of which the support leg is manoeuvrable to an active support position in contact
with the ground or other underlayer, wherein the crane (20) comprises:
- a column (21), which is rotatable in relation to the chassis (3) about an essentially
vertical axis;
- a liftable and lowerable crane boom (22), here denominated inner boom, which is
articulately fastened to the column (21);
- a hydraulic cylinder (23), here denominated lifting cylinder, for lifting and lowering
the inner boom (22) in relation to the column (21); and
- an electronic regulating device (30), which is adapted to check whether one or more
predetermined stability conditions for the lorry are fulfilled with a lifting moment
of the crane corresponding to a, with respect to the strength of the crane, maximum
allowed value (MC,bas), here denominated base value, for the lifting moment of the crane, the regulating
device (30) being adapted to establish a reduced value (MC,red) for the maximum allowed lifting moment of the crane if said one or more stability
conditions are not fulfilled,
characterized in that the regulating device (30), when establishing said reduced value (MC,red), is adapted to take into account the horizontal extension length of the respective
support leg (41-44) that is in the active support position, the slewing angle (θ) of the column (21)
in relation to the chassis (3), and the force (Fi) exerted by the force member (6) of the respective support leg that is in the active
support position and is not included in the prevailing tipping line of the lorry.
2. A lorry according to claim 1, characterized in that the regulating device (30) is adapted to establish said reduced value (MC,red) as the product of said base value (MC,bas) and a reduction factor (κ), which is established by the regulating device and has
a value lower than 1.
3. A lorry according to claim 2,
characterized in:
- that the regulating device (30) is adapted to make said reduction factor (κ) assume a
basic value (κbas) when the following condition (I) is fulfilled:

where mv is the mass of the lorry without cargo, g is the gravitational constant, hv is the perpendicular distance between the centre of gravity of the lorry without
cargo and the prevailing tipping line, MO is the tipping moment of the crane (20) with respect to the prevailing tipping line
and with a lifting moment of the crane corresponding to said base value (MC,bas), Fi is the force exerted by the force member (6) of the active support leg i and Di is the perpendicular distance between the contact point of the active support leg
i against the underlayer and the prevailing tipping line, and
- that the regulating device (30) is adapted to make said reduction factor (κ) assume an
increased value (κeh), which is higher than said basic value (κbas), when said condition (I) is not fulfilled.
4. A lorry according to claim 3,
characterized in that the regulating device (30) is adapted to establish said basic value (κ
bas) for the reduction factor according to the following formula:
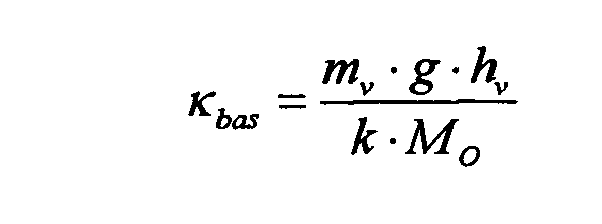
where κ
bas is said basic value,
mv, g, hv and
Mo are as above and κ is a stability constant with a given value higher than 1.
5. A lorry according to claim 4,
characterized in that the regulating device (30) is adapted to establish said increased value (κ
eh) for the reduction factor according to the following formula:

where κ
eh is said increased value and
Fi,
Di, Mo and κ are as above.
6. A lorry according to any of claims 1-5, characterized in that the regulating device (30) is adapted to convert the prevailing value (MC,bas or MC,red) for the maximum allowed lifting moment of the crane into a corresponding value for
the maximum allowed working pressure for the lifting cylinder (23).
7. A method for regulating the maximum allowed lifting moment of a hydraulic crane (20)
which is mounted on a chassis (3) of a lorry (1), which chassis is supported by load-bearing
vehicle wheels (2
1-2
4), where the lorry comprises two or more support legs (4
1-4
4) connected to the chassis (3), the respective support leg having a force member (6),
by means of which the support leg is manoeuvrable to an active support position in
contact with the ground or other underlayer, and the lorry (20) comprises:
- a column (21), which is rotatable in relation to the chassis (3) about an essentially
vertical axis;
- a liftable and lowerable crane boom (22), here denominated inner boom, which is
articulately fastened to the column (21);
- a hydraulic cylinder (23), here denominated lifting cylinder, for lifting and lowering
the inner boom (22) in relation to the column (21);
the method comprising the steps:
- to check by means of an electronic regulating device (30) whether one or more predetermined
stability conditions for the lorry are fulfilled with a lifting moment of the crane
corresponding to a, with respect to the strength of the crane, maximum allowed value
(MC,bas), here denominated base value, for the lifting moment of the crane; and
- to establish a reduced value (MC,red) for the maximum allowed lifting moment of the crane by means of said regulating device
(30) if said one or more stability conditions are not fulfilled, the horizontal extension
length (Li) of the respective support leg (41-44) that is in the active support position, the slewing angle (θ) of the column (21)
in relation to the chassis (3) and the force (Fi) exerted by the force member (6) of the respective support leg that is in the active
support position and is not included in the prevailing tipping line of the lorry being
taken into account when establishing said reduced value (MC,red).
8. A method according to claim 7, characterized in that said reduced value (MC,red) is established as the product of said base value (MC,bas) and a reduction factor (κ) with a value lower than 1.
9. A method according to claim 8,
characterized in:
- that said reduction factor (κ) is made to assume a basic value (κbas) when the following condition (I) is fulfilled:

where mv is the mass of the lorry without cargo, g is the gravitational constant, hv is the perpendicular distance between the centre of gravity of the lorry without
cargo and the prevailing tipping line, Mo is the tipping moment of the crane (20) with respect to the prevailing tipping line
and with a lifting moment of the crane corresponding to said base value (MC,bas), Fi is the force exerted by the force member (6) of the active support leg i, and Di is the perpendicular distance between the contact point
of the active support leg i against the underlayer and the prevailing tipping line, and
- that said reduction factor (κ) is made to assume an increased value (κeh), which is higher than said basic value (κbas), when said condition (I) is not fulfilled.
10. A method according to claim 9,
characterized in that said basic value (κ
bas) for the reduction factor is established according to the following formula:
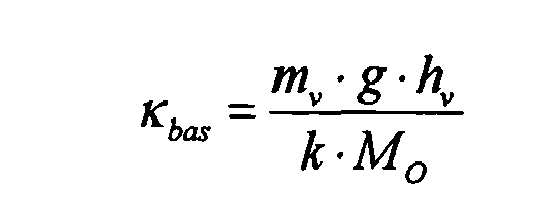
where κ
bas is said basic value,
mv, g,
hv and
Mo are as above, and κ is a given stability constant with a value higher than 1.
11. A method according to claim 10,
characterized in that said increased value (κ
eh) for the reduction factor is established according to the following formula:
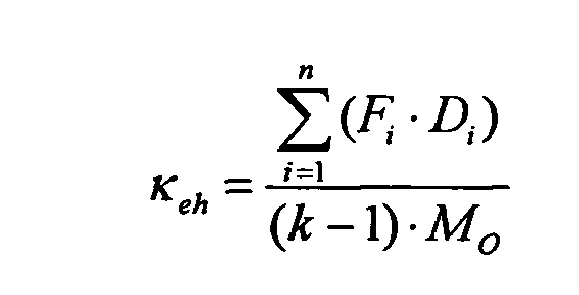
where κ
eh is said increased value, and
Fi, Di, Mo and κ are as above.
12. A method according to any of claims 7-11, characterized in that the prevailing value (MC,bas or MC,red) for the maximum allowed lifting moment of the crane is converted into a corresponding
value for the maximum allowed working pressure for the lifting cylinder (23).